- 1Department of Mechanical Engineering, National University of Technology, Islamabad, Pakistan
- 2Department of Mechanical Engineering, University of Engineering and Technology, Peshawar, Pakistan
- 3Department of Mechanical Engineering, Institute of Manufacturing, University of Engineering and Applied Sciences, Swat, Pakistan
- 4Industrial Engineering Department, College of Engineering, King Saud University, Riyadh, Saudi Arabia
- 5Department of Information and Communication Technology, University of Agder (UiA), Grimstad, Norway
- 6Mechanical Engineering Department, National University of Technology, Islamabad, Pakistan
The purpose of this research is to investigate the impact of moisture content, closing speed, and pressurizing speed of hot press on the density, uniformity of density distribution, and properties of Medium Density Fiberboard (MDF) products. Moisture content affects the plasticity, heat conductivity, and hydrolysis reaction of the fiber and appropriate moisture content ensures the quality of the board. Excessive moisture content can lead to defects such as pollution and bubbles on the surface of the board. Closing time and pressurizing speed affect the nature, quality, and section structure of the MDF. The section density of the board varies with the closing time, and the product properties, especially the strength differs largely. The pressurizing speed influences the density distribution and board properties. Fast pressurizing speed results in high Modulus of Rupture (MoR) and low Internal Bonding (IB), while slow pressurizing speed leads to low MoR and high IB. Pre-plasticizing layer can improve the quality of MDF by increasing the density and hardness of the board surface. The findings provide guidance for optimizing the MDF production process and improving the quality of MDF products. Applying a fast pressurizing speed during the manufacturing process of MDF has resulted in a 15.7% increase in the MoR, which is a measure of the material’s ability to withstand stress before breaking as compared to using a slow pressurizing speed. Additionally, using a fast pressurizing speed has led to a reduction of 17.4% in the IB, which is a measure of the ability of the board to resist internal separation or delamination. Therefore, a fast pressurizing speed is more effective in improving the mechanical properties of MDF.
1 Introduction
During the hot pressing process, the purpose of moisture in raw board is to increase the plasticity and heat conductivity of the fiber, involve in hydrolysis reaction of cellulose and hemicellulose promote the resignification of lignin and reduce the melting point (Zhou et al., 2013). Therefore, appropriate moisture content can ensure the good quality of board. Excessive moisture content will bring disadvantages to the dry method production, because no padding mesh is used in dry hot pressing method and a lot of steam is difficult to discharge, in which case strong hydrolysis will be caused to the fiber and the decomposition of organic acid will be increased, resulting in such defects as pollution and bubbles on the board surface (Magalhães et al., 2020a). In the production of MDF, the moisture content of the raw board in continuous hot pressing line shall be controlled about 5% (Lv et al., 2020). But for multi-layer press, the moisture content of raw board shall be controlled about 10% (Hasan et al., 2020). To enhance the heat transfer efficiency and increase the hardness of board surface, the fiber on the surface layer is allowed to have a moisture content 2% higher than the core layer (Ganev et al., 2005). For, multi-layer hot press, necessary auxiliary time exists in the hot pressing process. Such auxiliary time refers to closing time, pressurizing time, depressurizing time and opening time of hot press plate. Control over such time has significant influence on the nature, quality and section structure of the MDF (Zeng et al., 2018).
S Ganev et al. (2003) (Ganev et al., 2003) investigated the influence of medium density fiberboard (MDF) density and sorption state on sorption isotherms, as well as the impact of panel moisture content and density on the effective water conductivity and diffusion coefficient of MDF panels. A total of 39 laboratory-made MDF panels were produced, with dimensions of 650 mm × 650 mm x 12 mm, and were categorized into three density groups: 540 kg/m3, 650 kg/m3, and 800 kg/m3. The results indicated that moisture content had a more substantial effect on the effective water conductivity than density. In desorption, effective water conductivity increased as moisture content levels increased, while it decreased as moisture content increased in adsorption. Panels with a density of 540 kg/m3 had significantly higher effective water conductivity in desorption and diffusion coefficients in both desorption and adsorption compared to those with densities of 650 and 800 kg/m3. Additionally, in adsorption, the effective water conductivity of panels with a density of 540 kg/m3 was significantly higher than that of panels with a density of 800 kg/m3.
Z Caiet.al (2006) (Cai et al., 2006) explored the influence of mat moisture content (MC) and panel density on the performance of medium density fiberboard (MDF) panels in terms of heat transfer, internal steam pressure, and pre-curing on the surface. The study systematically examined the effects of these factors, including pre-curing, on MDF panels. The findings indicated that both panel density and mat MC had significant impacts on internal bonding and internal steam pressure. Delamination was observed when the maximum internal steam pressure exceeded 100 kPa (15 psi). The optimized mat MC for internal bonding performance was found to be dependent on panel density, with a range of 12.1–15.3 percent for low-density panels (673 kg/m3), and a narrower and lower range for medium (769 kg/m3) and high (833 kg/m3) density panels. The results also suggested that panel density had a positive correlation with mechanical performance, internal steam pressure, and maximum core temperature, but it slowed down the rate of temperature increase in the core and reduced the pre-cure thickness gradient.
I Aliet.al (2014) (Ali et al., 2014) examined the influence of various factors, such as resin type, resin content, and moisture content, on the physical and mechanical properties of medium density fiberboard (MDF) panels made from kenaf (Hibiscus cannabinus L.) bast fibers. The study utilized the Taguchi method of experimental design to determine the optimal levels of the factors that produced desirable properties. The panels were manufactured with a target thickness of 9 mm and density of 700 kg/m3, using three different commercial resins, namely, urea formaldehyde (UF), phenol formaldehyde (PF), and melamine urea formaldehyde (MUF). The results of the study showed that resin type and moisture content had a significant impact on mechanical properties, while resin content had the least impact. Conversely, for physical properties, resin content and moisture content had a much lesser impact as compared to resin type. The study suggested that kenaf panels produced with MUF resin at a higher resin loading and an intermediate level of moisture content demonstrated elevated properties, according to the wood-based MDF standard ANSI A208.2-2009 for Grades 130 and 155.
MK Hong et al. (2017) (Hong et al., 2017) evaluated the impact of panel density and resin content on the properties of medium density fiberboard (MDF) and to gain insights into how MDF properties vary with panel density and resin content. MDF panels were manufactured with different panel densities (650, 700, 750, and 800 kg/m3) by adjusting the amount of wood fibers in the mat forming. Additionally, MDF panels were produced with a target density of 650 kg/m3 by spraying 8, 10, 12, and 14% of urea formaldehyde (UF) resins onto wood fibers in a drum-type mechanical blender. As the panel density and resin content increased, the internal bonding (IB) strength of MDF panels consistently increased. The modulus of rupture (MOR), modulus of elasticity (MOE), and screw withdrawal resistance (SWR) showed a similar trend to the IB strength. In terms of physical properties, both thickness swelling (TS) and water absorption (WA) decreased with an increase in panel density and resin content. However, formaldehyde emission (FE) increased as the panel density and resin content became greater.
P. Antov et al. (2019) (Antov et al., 2019) conducted a study to optimize the exploitation properties of eco-friendly medium density fiberboards (MDF) manufactured with lignosulfonate as a binder. The study focused on two main factors: lignosulfonate concentration and hot pressing temperature. Three levels of lignosulfonate concentration were tested: 20%, 30%, and 40%. Similarly, three temperature levels were tested: 200°C, 210°C, and 220°C. The MDFs were produced under laboratory conditions using D-optimal experimental design. The study developed regression models to determine the impact of the factors within the specified range of variation on the properties of the MDFs, including water absorption, swelling in thickness, bending strength, modulus of elasticity in bending, and internal bond strength of the panels. The researcher identified a promising method for producing environmentally-friendly MDF panels with no harmful free-formaldehyde emissions and to use lignosulfonate as an adhesive. By adjusting the concentration of lignosulfonate in the wood-fiber mass and the hot pressing temperature, the properties of the MDF panels can be effectively manipulated. The concentration of lignosulfonate has a greater impact on panel properties than the hot pressing temperature within the specified variation range, likely due to the high hot pressing temperature (over 200°C) and extended press time. When the concentration of lignosulfonate exceeds 35%, the strength properties of the panels deteriorate as the hot pressing temperature increases. Lowering the concentration to below 30% is not recommended, as it does not increase the utilization of lignosulfonate hydroxyl groups and necessitates a higher hot pressing temperature.
K. Sihag et al. (2022) (Sihag et al., 2022) optimized adhesive system, which consisted of unmodified hydrolysis lignin and reduced phenol formaldehyde (PF) resin content. In the laboratory, the researchers produced the fiberboard panels with a very low PF resin content ranging from 1% to 3.6% and hydrolysis lignin addition levels varying from 7% to 10.8% based on the dry wood fibers. They applied a specific two-stage hot-pressing regime, which involved initial low pressure of 1.2 Mpa and subsequent high pressure of 4 Mpa. The study investigated the effect of the binder content and PF resin content in the adhesive system on the fiberboards' primary properties, including water absorption, thickness swelling, bending strength, modulus of elasticity, and internal bond strength. Appropriate optimization was conducted to define the optimal content of PF resin and hydrolysis lignin to comply with European standards. The study concluded that the proposed technology was appropriate for manufacturing fiberboard panels that met the strictest EN standard. Notably, the researchers showed that, for this type of panel production, the minimum total content of binders should be 10.6%, and the PF resin content should be at least 14% of the adhesive system.
The present study examined how moisture content, closing speed, and pressurizing speed affect the density, uniformity of density distribution, and characteristics of Medium Density Fiberboard (MDF) products. The aim is to offer recommendations for enhancing the MDF production process and elevating the quality of MDF products by managing these variables.
2 Materials and methods
2.1 Materials
The research work utilizes various materials, including urea formaldehyde adhesive and Bio composite fibers (Populus Deltoides) Peshawar Forest Institute, Pakistan supplied bio composite fibers. The average length of these fibers is 0.75 mm, and they contain 8.5%–11% moisture content. These fibers are organic, plant-based, biodegradable, and sustainable. A commercial urea formaldehyde adhesive is used as the adhesive in the manufacturing process of MDF panels (Gul and Alrobei, 2021). The Wah Nobel Group of Companies, located in Taxila, Pakistan, supplied the urea formaldehyde resin, and its specifications are listed in Table 1. The viscosity (cps), density (g/cc), and pH values were measured at a temperature of 30°C, while the Gel time (seconds) was observed at a temperature of 105°C.
2.2 Methods
2.2.1 Preparation of MDF panels
To produce medium density fiberboard, wood is chipped and refined into fibers which are then mixed with glue and wax. The mixture is compressed under high temperature using a hot press, causing the glue to bond with the fibers and form the medium density fiberboard. Panels of the fiberboard were created with dimensions of 450 × 450 × 16 mm, and the density was varied between 700 and 750 kg/m3. To accomplish this, urea formaldehyde was sprayed onto fibers from Populus Deltuidess using a spray gun. A Hydraulic Hot Press (BURKLE, Bohemia, NY, United States) was then used to perform the hot pressing process at a temperature of 185°C and 150 bar pressure for 4 min on all four samples. After pressing, the panels were cooled horizontally in a cooling tower for 72 h.
Wood Chips ---> Fibers ---> Glue and Wax ---> Mixture ---> Hot Press ---> Raw MDF ---> Cooling Tower ---> Sanding ---> Final MDF Fibers ---> Glue and Wax ---> Mixture ---> Hot Press ---> Raw MDF ---> Cooling Tower ---> Sanding ---> Final MDF-->
2.2.2 Scanning electron microscopy of pure UF adhesive
The surface morphology of pure UF resin films with and without curing agent was examined using a SEM (MIRA3, TESCAN, Brno, Czech Republic). The resin film was produced by forming it on glass slides using the same temperature and time treatment. The film surface was then coated with a layer of gold and photographed. SEM analysis was conducted using an accelerated voltage of 10 kV.
2.2.3 X-ray diffraction of pure UF adhesive
The sample of UF Adhesive was cured at 110°C for 2 h to eliminate moisture from the resin. The powder samples were analyzed at 30°C using an X-ray diffractometer (MIRA3 TESCAN, Brno, Czech Republic) with scanning range was 20–80°, with a scanning step frequency of 0.04/min. The XRD spectrum was deconvolved to determine individual crystalline peaks and amorphous peaks, which allowed for the percentage of crystallinity of the UF resin (Li and Zhang, 2021).
2.2.4 Physical and mechanical properties of MDF panels
The MDF panels were characterized in terms of density (EN 323; British Standards Institution: London, UK, 1993) (BSI Standards Publication, 1993), modulus of elasticity and rupture (MoR) (EN 310; European Committee for Standardization: Brussels, Belgium, 1993) (European Committee for Standardization, 1993a) and internal bond (I.B) strength (EN 319; European Committee for Standardization: Brussels, Belgium, 1993) (European Committee for Standardization, 1993b) using standard test methods.
To assess the mechanical characteristics of medium density fiberboard, an assessment was performed using the Three-Point Bending Test. The samples were prepared in compliance with EN-310 with dimensions of 370 mm × 50 mm × 16 mm, and were subjected to a loading speed of 4 mm/min. The WDW-30 Electromechanical Universal Testing Machine, manufactured by JINAN Precision Testing Equipment Company Limited in Jinan, China, was utilized to test the samples. Eqs 1, 2 were employed to determine the mechanical properties.
The load and center deflection at the proportional limit, measured in N and mm respectively, are represented by the variables ‘P’ and ‘Y’. Meanwhile, the dimensions of the samples are denoted by ‘b’, ‘L’, and ‘d’, which correspond to their width, length, and depth, respectively, all of which are measured in mm.
A 50 mm by 50 mm specimen was bonded and subjected to a tensile test using the WDW-30 Electromechanical Universal Testing Machine, manufactured by JINAN Precision Testing Equipment Company Limited in Jinan, China, both perpendicular and parallel to its face. Internal bond strength, which is a crucial feature of composite boards, was measured using Eqs 3, 4 after applying a bonding agent to steel or aluminum alloy with similar dimensions.
Eqs 5, 6, (VII), and (VIII) were utilized to measure the physical properties. The specimens had dimensions of 150 mm by 100 mm by 16 mm, and three samples were tested for each physical property. The results presented are the average of the four values obtained. The water absorption and thickness swelling tests were conducted for a duration of 2 h and 24 h.
The variables m and V represent mass and volume, respectively, measured in kilograms and cubic meters. The variables b, L, and t denote the width, length, and thickness of the specimen, respectively, and are measured in millimeters.
3 Results and discussion
3.1 Scanning electron microscopy of pure UF adhesive
SEM analysis was conducted to examine the internal structure of cured urea formaldehyde (UF) resins as presented in Figure 1. The examination of the cured resin using cross-sectional analysis did not identify any specific structure that could be linked to the hydrolysis reaction triggered by the water produced during the high-temperature curing process of UF resins. The slight concavities observed as indicated by arrows were caused by the evaporation of moisture and formaldehyde, as previously reported (Johns and Dunker, 1986).
3.2 X-ray diffraction of pure UF adhesive
Based on the information provided, Figure 2 shows an X-ray diffraction (XRD) spectrum of pure UF adhesive. The spectrum displays one main peak at 2ϴ of 20.89, which weakens slightly after curing. However, further calculations revealed that the adhesive actually has an additional peak at 2ϴ of 23.94, 32.87, and 400, in addition to the sharp main peak at 2ϴ of 20.890. After curing, the main peak becomes sharper, the additional peak becomes visible, and the crystallinity of the adhesive increases.
XRD is a technique used to analyze the crystalline structure of materials by measuring the diffraction of X-rays by the atoms in a sample. The position and intensity of the peaks in an XRD spectrum can provide information about the crystal structure and composition of the material. In this case, the XRD spectrum of the UF adhesive suggests that it has a crystalline structure with one main peak at 2ϴ of 20.89 and an additional peak at 2ϴ of 23.94, 32.87, and 400, indicating the presence of specific crystal planes within the adhesive. After curing, the crystallinity of the adhesive increases, which may indicate a more ordered and stable structure (Liu et al., 2017).
3.3 Impact of mositure content in raw board onto product desnity
The moisture content of the raw board has an impact on the density distribution of the board. As illustrated in Figure 3, the moisture content varies significantly between the surface and core layer of the raw board, leading to variations in the density of the resulting board products. When the moisture content rises, the board’s compression resistance decreases, and the fiber becomes more malleable, softening under conditions of heat and pressure. This leads to a quick transition from elastic deformation to plasticity and compaction, resulting in an increased density of the surface layer. On the other hand, the core layer has low moisture content, high compression resistance, and low temperature, making it difficult to compact and resulting in increased density. The statement “the compression resistance is decreased with an increase in the moisture content” means that as the moisture content of a material increases, its ability to resist compression or external forces decreases. In the context of the material being discussed (raw board or fiberboard), an increase in moisture content causes the fibers to soften and become more plastic, which makes them easier to compress or deform. As a result, the material’s ability to resist compression decreases. This can have implications for the quality and durability of the final product, as a lower compression resistance may lead to the material being more susceptible to damage or deformation under pressure. Therefore, controlling the moisture content of the raw material during the manufacturing process is important to ensure that the final product has the desired properties and performance. Therefore, the moisture content in the fiber affects both the density of the board and the uniformity of the density distribution (Magalhães et al., 2020b).
For Figure 3, the labeling 1, 2 and 3 represents 3.5,3 and 2.5 MPa Pressure. There are total three layers (two surface and one middle) layers in the MDF. The moisture content in MDF usually is 9%–10% was measured through moisture meter model IR-3000FP MoistTech’s NIR (Near Infrared) United States. The statement “the compression resistance is decreased with an increase in the moisture content” means that as the moisture content of a material increases, its ability to resist compression or external forces decreases. In the context of the material being discussed (raw board or fiberboard), an increase in moisture content causes the fibers to soften and become more plastic, which makes them easier to compress or deform. As a result, the material’s ability to resist compression decreases. This can have implications for the quality and durability of the final product, as a lower compression resistance may lead to the material being more susceptible to damage or deformation under pressure. Therefore, controlling the moisture content of the raw material during the manufacturing process is important to ensure that the final product has the desired properties and performance.
3.4 Impact of closing time and pressuirizing speed in raw board onto product desnity
3.4.1 Closing time of hot press
As shown in Figure 4, to manufacture 9 mm MDF under a hot pressing temperature of 168°C, the raw boards No. 3, No. 7, No. 11 and No. 15 are pre-pressed under a pressure of 0.42 MPa and then be made into MDF product respectively at a pressure of 1.7, 3.4, 5.8 and 10.5 Mpa with density distribution curve as shown (in which No. 21 is not pre-stressed and the pressing condition is same as No. 15). The pressing pressure has a significant impact on the density of MDF boards. Generally, as the pressing pressure increases, the density of MDF also increases. This is because the high pressure compacts the fibers more tightly, resulting in a denser board.
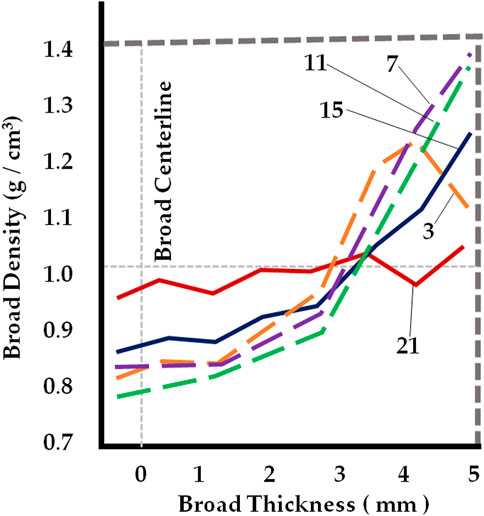
FIGURE 4. Relation between the closing time of press plate and distribution of board section density.
The density of MDF is an important parameter as it can affect the board’s mechanical properties, such as its strength and stiffness, and also its water absorption characteristics. Higher density MDF boards are generally stronger and more rigid, making them suitable for applications where strength and durability are important, such as furniture and flooring.
The section density of the board varies with the closing time, and the product property, especially the strength, differs largely.
3.4.2 Impact of closing time on modulus of elasticity
Shown in Figure 5 is the impact of different closing time on the MDF, Modulus of Elasticity (MoE). Studies have shown that with the extension of closing time, MoE tends to decline. This is because the longer the MDF is under pressure and heat, the more the fibers are compressed and rearranged, leading to a decrease in its stiffness and MoE. The reduction in MoE may also be due to the chemical changes that occur in the resin during the extended closing time.
Furthermore, the impact of closing time on MoE can be influenced by temperature. Similar results have been obtained under different temperature conditions, meaning that MoE tends to decline with an extension of closing time at both high and low temperatures. It is worth noting that the impact of closing time on MoE is not the only factor affecting the properties of MDF. Other factors such as the type of resin used, the density of the panel, and the thickness of the panel can also influence the MoE and other properties of MDF.
3.4.3 Pressurizing speed of hot press
After the press plate of the hot press is closed, the speed that the pressure rises from 0 to rated value is called pressurizing speed. The pressurizing speed has influence on both the property and section density of the board.
Shown in Figure 6 are two pieces A and B of MDF having the same nominal density as well as the distribution of their section density (C refers to nominal density). If the pressure of hot press plate rises fast, the density distribution (Curve A) as shown will be generated.
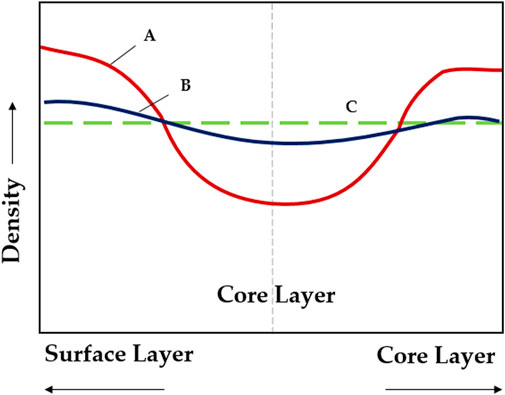
FIGURE 6. Distribution of Board Section Density (A and B are two pieces of products with same density, C is the average density).
If the pressure of hot press plate rises slowly, the distribution of board section density will be of small difference (Curve B).
The influence of pressurizing speed on board property can be seen from Table 2. If the pressure of the press rises fast, the MoR of the board will be high, the thickness of surface soft layer will be low and the quality of board surface will be good, but the board I. B will be low.
On the contrary, if the pressure of the press rises slowly, the MoR of the board will be reduced, the thickness of the surface soft layer will be increased and the quality of board surface will be poor, but the board Internal Bonding (I. B) will be enhanced. Under the test conditions as shown, fast pressurizing speed will result in increase of MoR by 15.7% and reduction of I.B by 17.4%, compared against the slow pressurizing speed.
3.4.4 Pre-plasticizing layer of product surface
The loose layer on the product surface is called pre-plasticizing layer (or soft layer) and it affects the quality and polish of the board surface. Therefore, it shall be sanded off in board trimming section, otherwise the decoration and processing of the products will be affected. The thicker the pre-plasticizing layer, the more it shall be sanded off (Zhang et al., 2018). This problem is particularly important for multi-layer hot pressing technique. Generally, it is required to remove 1–1.5 mm or even high up to 2 mm. Therefore, the loss on raw materials, auxiliary materials and energy (could potentially be referring to the energy required for sanding the board surface) will be high. So the thickness of pre-plasticizing layer should be minimized.
The raw board is affected by heats when the hot press plate is not closed yet, in which case the moisture in the surface fiber starts to vaporize, part of glue starts to agglomerate and solidify. That is, the surface fiber has been glued under a low pressure, so the surface is of low density and loose, on which pre-plasticizing layers generated as shown in Figure 7. Therefore, the slower the closing speed and pressurizing speed of the hot press plate, the higher the thickness of this layer.
4 Conclusion
In conclusion, this research has highlighted the crucial role of moisture content, closing speed, and pressurizing speed on the density, uniformity of density distribution, and properties of Medium Density Fiberboard (MDF) products. The appropriate moisture content is essential to ensure the quality of the board, while excessive moisture content can lead to defects. Closing and pressurizing speed have a significant impact on the nature, quality, and section structure of the board, affecting the product properties, particularly the strength, and quality of the board surface. The use of a pre-plasticizing layer can also improve the quality of the board. Applying a fast pressurizing speed during the manufacturing process of MDF can result in increased Modulus of Rupture (MoR), but a reduction in the internal bond (I. B). Controlling certain factors during the production of medium density fiberboard (MDF) is very important if you want to make high-quality MDF products. The factors mentioned could be things like temperature, humidity, or the type of raw materials used. By controlling these factors, we can improve the overall quality of the MDF and ensure that the final product meets certain standards. The sentence also suggests that these findings are important for the wood industry because they provide guidance on how to achieve the desired quality of the final MDF product.
Data availability statement
The original contributions presented in the study are included in the article/supplementary material, further inquiries can be directed to the corresponding author.
Author contributions
All authors listed have made a substantial, direct, and intellectual contribution to the work and approved it for publication. All authors contributed to the article and approved the submitted version.
Funding
This study received funding from King Saud University, Saudi Arabia through researchers supporting project number (RSP2023R145). Additionally, the APCs were funded by King Saud University, Saudi Arabia through researchers supporting project number (RSP2023R145).
Acknowledgments
The authors would like to thank King Saud University, Riyadh, Saudi Arabia, with researchers supporting project number (RSP 2023R145).
Conflict of interest
The authors declare that the research was conducted in the absence of any commercial or financial relationships that could be construed as a potential conflict of interest.
Publisher’s note
All claims expressed in this article are solely those of the authors and do not necessarily represent those of their affiliated organizations, or those of the publisher, the editors and the reviewers. Any product that may be evaluated in this article, or claim that may be made by its manufacturer, is not guaranteed or endorsed by the publisher.
References
Ali, I., Jayaraman, K., and Bhattacharyya, D. (2014). Effects of resin and moisture content on the properties of medium density fibreboards made from kenaf bast fibres. Industrial Crops Prod. 52, 191–198. doi:10.1016/j.indcrop.2013.10.013
Antov, P., Valchev, I., and Savov, V. (2019). Experimental and statistical modeling of the exploitation properties of eco-friendly MDF through variation of lignosulfonate concentration and hot pressing temperature. In Proceedings of the 2nd international congress of biorefinery of lignocellulosic materials. Sofia: IWBLCM, 104–109.
BSI Standards Publication (1993). Wood-based panels-determination of density in fiberboard; EN 323: 1993. London, UK: British Standards Institution.
Cai, Z., Muehl, J. H., and Winandy, J. E. (2006). Effects of panel density and mat moisture content on processing medium density fiberboard. For. Prod. J. 56 (10), 20.
European Committee for Standardization (1993). Particleboards and fiberboards, determination of tensile strength perpendicular to plane of the board; EN 319: 1993. Brussels, Belgium: European Committee for Standardization.
European Committee for Standardization (1993). Wood-based panels, determination of modulus of elasticity in bending and bending strength; EN 310: 1993. Brussels, Belgium: European Committee for Standardization.
Ganev, S., Cloutier, A., Beauregard, R., and Gendron, G. (2003). Effect of panel moisture content and density on moisture movement in MDF. Wood fiber Sci., 68–82.
Ganev, S., Gendron, G., Cloutier, A., and Beauregard, R. (2005). Mechanical properties of MDF as a function of density and moisture content. Wood fiber Sci., 314–326.
Gul, W., and Alrobei, H. (2021). Effect of graphene oxide nanoparticles on the physical and mechanical properties of medium density fiberboard. Polymers 13 (11), 1818. doi:10.3390/polym13111818
Hasan, S. A., Pitol, N. S., Shams, M. I., and Hannan, M. O. (2020). Scope of medium density fiberboard (MDF) from water hyacinth (Eichhornia crassipes). V (X), 123–127.
Hong, M. K., Lubis, M. A. R., and Park, B. D. (2017). Effect of panel density and resin content on properties of medium density fiberboard. J. Korean Wood Sci. Technol. 45 (4), 444–455.
Johns, W. E., and Dunker, A. K. (1986). Urea-formaldehyde resins. 2nd ed. Bergen, NJ, USA: Addison-Wesley, 126–148.
Li, J., and Zhang, Y. (2021). Morphology and crystallinity of urea-formaldehyde resin adhesives with different molar ratios. Polymers 13 (5), 673. doi:10.3390/polym13050673
Liu, M., Thirumalai, R. V. K., Wu, Y., and Wan, H. (2017). Characterization of the crystalline regions of cured urea formaldehyde resin. Rsc Adv. 7 (78), 49536–49541. doi:10.1039/c7ra08082d
Lv, Y., Liu, Y., Jing, W., Woźniak, M., Damaševičius, R., Scherer, R., et al. (2020). Quality control of the continuous hot pressing process of medium density fiberboard using fuzzy failure mode and effects analysis. Appl. Sci. 10 (13), 4627. doi:10.3390/app10134627
Magalhães, R., Nogueira, B., Costa, S., Paiva, N., Ferra, J. M., Magalhães, F. D., et al. (2020). Effect of panel moisture content on internal bond strength and thickness swelling of medium density fiberboard. Polymers 13 (1), 114. doi:10.3390/polym13010114
Magalhães, R., Nogueira, B., Costa, S., Paiva, N., Ferra, J. M., Magalhães, F. D., et al. (2020). Effect of panel moisture content on internal bond strength and thickness swelling of medium density fiberboard. Polymers 13 (1), 114. doi:10.3390/polym13010114
Sihag, K., Yadav, S. M., Lubis, M. A. R., Poonia, P. K., Negi, A., and Khali, D. P. (2022). Influence of needle-punching treatment and pressure on selected properties of medium density fiberboard made of bamboo (Dendrocalamus strictus Roxb. Nees). Wood Material Sci. Eng. 17 (6), 712–719. doi:10.1080/17480272.2021.1931440
Zeng, Q., Lu, Q., Zhou, Y., Chen, N., Rao, J., and Fan, M. (2018). Circular development of recycled natural fibers from medium density fiberboard wastes. J. Clean. Prod. 202, 456–464. doi:10.1016/j.jclepro.2018.08.166
Zhang, J., Ying, J., Cheng, F., Liu, H., Luo, B., and Li, L. (2018). Investigating the sanding process of medium-density fiberboard and Korean pine for material removal and surface creation. Coatings 8 (12), 416. doi:10.3390/coatings8120416
Keywords: medium density fiberboard, urea formaldehyde resin, moisture content, closing speed, pressurizing speed, modulus of rupture, internal bond
Citation: Gul W, Ahmad N, Mohammad S, Salah B, Sajid Ullah S, Khurram M and Khan R (2023) Impact of moisture content, closing speed, and pressurizing speed on the performance of medium density fiberboard (MDF). Front. Mater. 10:1195789. doi: 10.3389/fmats.2023.1195789
Received: 28 March 2023; Accepted: 27 April 2023;
Published: 09 May 2023.
Edited by:
Senthil Muthu Kumar Thiagamani, Kalasalingam University, IndiaReviewed by:
Lin Feng Ng, University of Technology Malaysia, MalaysiaNaveen J., Putra Malaysia University, Malaysia
Copyright © 2023 Gul, Ahmad, Mohammad, Salah, Sajid Ullah, Khurram and Khan. This is an open-access article distributed under the terms of the Creative Commons Attribution License (CC BY). The use, distribution or reproduction in other forums is permitted, provided the original author(s) and the copyright owner(s) are credited and that the original publication in this journal is cited, in accordance with accepted academic practice. No use, distribution or reproduction is permitted which does not comply with these terms.
*Correspondence: Waheed Gul, waheed.gul@nutech.edu.pk; Syed Sajid Ullah, syed.s.ullah@uia.no