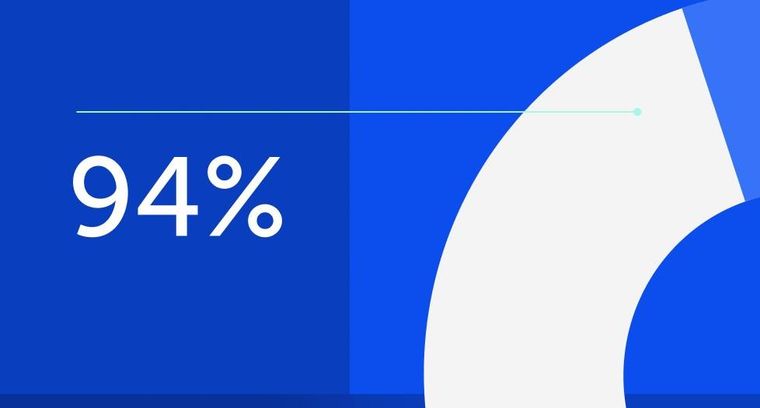
94% of researchers rate our articles as excellent or good
Learn more about the work of our research integrity team to safeguard the quality of each article we publish.
Find out more
ORIGINAL RESEARCH article
Front. Mater., 15 June 2023
Sec. Polymeric and Composite Materials
Volume 10 - 2023 | https://doi.org/10.3389/fmats.2023.1206918
This article is part of the Research TopicAdvancements in Composite Sandwich Materials: Fabrication, Characterization, Durability, Modeling and ApplicationsView all 5 articles
Graphene is an advanced material in the carbon group and offers greater mechanical, electrical, structural, and optical properties. Graphene oxide (GO) and reduced graphene oxide (rGO) nanoparticles were synthesized and characterized and their special effects on enhancing the physio-mechanical characteristics of medium density fiberboard (MDF) were assessed. GO and rGO nanoparticles were added to urea formaldehyde (UF) resin at different weight percentages (1.0, 2.0, and 3.0 wt%) during the dosing process. To manufacture the MDF, nanofillers were created by sonication and combination with natural wood fibers. To observe the behavior of nanoparticles in the nanofillers, microstructure characterizations were conducted. The manufactured nano MDF samples underwent physical and mechanical testing. The incorporation of GO and rGO nanoparticles into UF resin led to significant improvements in the physical and mechanical properties of the MDF. The addition of GO and rGO nanoparticles at different weight percentages (1.0, 2.0, and 3.0 wt%) resulted in a range of improvements in thickness swelling (up to 53.3% and 35.2% for GO and rGO nanoparticles, respectively), water absorption (up to 23.3% and 63.15%, respectively), and thermal conductivity (up to 42.16% and 27.7%, respectively). Additionally, the internal bond and rupture modulus of the MDF was enhanced by 59.0% and 70.0%, respectively, for GO and 41.4% and 48.5% for rGO. The highest value of the modulus of rupture (MoR) was observed at a concentration of 3.0% of rGO nanoparticles (44.7 MPa). The findings also showed that thickness swelling (Ts) and water absorption (WA) exhibited directly proportional relationships for 3.0% GO and rGO. These results suggested that incorporating GO and rGO nanoparticles into UF resin can significantly improve the physical and mechanical properties of nano MDF.
With the increase in technology and remarkable advancements in the field of materials science, new paths have been opened to meet daily technology needs and requirements. After the discovery of graphene, scientists, and engineers have turned to new and far better options to produce materials with desired properties. Graphene compounds have been used widely used to produce breakthrough composites in the world of science. Among these graphene compounds is graphite oxide, which, when combined with other materials, can be used to produce products that could easily and effectively replace traditional materials (Young et al, 2012).
Composite materials are important in developing the aerospace, automotive, and construction sectors in the current cutting-edge research age (Alabduljabbar et al, 2020a). Natural fiber composites offer unique qualities that make them the best-reinforced materials (Gul et al, 2017). Medium density fiberboard (MDF), the correct name for wood-based composite, comprises natural fibers and urea formaldehyde in a proportion of 10:90 percent by weight (Gul et al, 2019). While MDF has received much recent attention, its mechanical and physical strength remain severe drawbacks (Gul et al, 2021a). Scavengers, additives, and reactive agents have been used in several studies to enhance MDF’s mechanical and physical characteristics (Gul et al, 2020). To increase the efficacy of composites, a different team of researchers have proposed the concept of nanoparticles (Gul et al, 2021b). However, despite findings showing improvements in several MDF-related areas, there still appears to be more space for growth. Thus, the primary objective of the present study was to investigate the effects of adding graphene and reduced graphene oxide nanoparticles to urea formaldehyde resin on the mechanical and physical characteristics of MDF (Zhang et al, 2013; Gupta and Khatri, 2017).
Due to their excellent adsorption capacity, carbon-based nanomaterials are becoming more popular as adsorbents. Graphene is an effective adsorptive in nature as it offers a larger surface-to-volume ratio (2,630 m2g-1) and planar structure (Zhang et al, 2013). Recently, there has been much interest in the removal of organic contaminants and dyes from industrial effluents using graphene oxide (GO), chemically functionalized and reduced forms, and graphene nanocomposites.
According to Gupta and Khatri (2017) (Zhang et al, 2013), the GO and its composites with biopolymers are effective adsorbents for removing organic dyes. GO and its composites with biopolymers have many fantastic adsorption sites, especially those with negatively charged oxygen functions, which are good for cationic dye adsorption.
Because of its distinctive two-dimensional pattern structure, GO is an appealing adsorbent.
Since its groundbreaking discovery by Geim and others (De Silva, Huang et al, 2017) (Gupta and Khatri, 2017), graphene has gained notoriety in the nanomaterial community. Mechanical exfoliation, epitaxial growth, chemical vapor deposition, and chemical reduction of GO are only a few of the methods that have been employed to create graphene (Li, Zhuang et al, 2017) (De Silva et al, 2017).
Chemical reduction of graphene, including the acid-cutting reduction method, is one extensively employed method. According to Upadhyay et al (2015) (Li et al, 2017), the synthesis strategy entails the oxide formation of graphite using Hummers’ method, followed by the use of abrasive reductants such as hydrazine and NaBH4 (Upadhyay et al, 2015a). The requirement in the second step for dangerous chemical-reducing agents is a significant downside. Research is still being done to identify green reducing agents that are safe and kind to the environment. Recent research has used plant extracts, such as natural citrus fruits, amino acids, ascorbic acid, and other environmentally friendly reducing agents, to synthesize reduced graphene oxide (rGO) from GO. Due to their availability, affordability, and environmental friendliness, natural products are desirable replacements for harmful chemical reducing agents.
Nanofillers were created, and ZnO, SiO2, and Al2O3 nanoparticles were introduced to urea formaldehyde resin (UF) by Candan et al (2015). Hybrid nanoparticles were added in the amounts of 1.0%, 3.0%, and 0.0%, taking the UF filler content into account. All mechanical characteristics, including internal bonding, rupture modulus, and elasticity modulus, were significantly enhanced.
According to Taghiyari et al (2016) (Taghiyari and Jack, 2014), nanowollastonite nanoparticles have a second unique function. Nanowollostinite, UF resin, and camel thorn fibers with a maximum diameter of 1 μm were mixed together to create nanocomposites. These samples and their thicknesses, swelling, and other mechanical characteristics were examined. The mechanical and physical characteristics of the nanocomposites showed commendable improvements.
Nautiyal et al also described the mechanical and physical characteristics of nano MDF’ (2017) (Ismita and Chavan, 2017). In this investigation, three adsorptions of Na + nanoparticles—2, 4, and 6%—were introduced to the UF resin. The 6% condition showed improvements in mechanical characteristics, namely, the modulus of rupture and elasticity, by 34.1% and 66.0%, respectively, which demonstrated an increased mechanical integrity of the composite. The physical characteristics, such as thickness swelling, were only enhanced by 6.0% for the same nanofiller content.
Chen et al (2018) added C5H8O2 and CaCO3 nanoparticles to UF resin and observed improved thermo-mechanical behavior of the nanocomposites.
ZnO nanoparticles were included in both UF and MF resins by Da Silva et al (2019), who used them to evaluate the biological and physical performances of the nanocomposites. Wood fibers were combined with UF and MF nanofillers at concentrations of 0.0, 0.5, and 1.0%, and many samples were created. The findings showed the best biological and physical effects for 0.5% MU–ZnO nanofillers.
Alabduljabbar et al (2020b) explored the addition of different concentrations of alumina nanoparticles (1.5%, 3%, and 4.5% by weight) to urea formaldehyde (UF). Forest fibers such as Populus deltoids (Poplar) and Euamericana (Ghaz) were used as a composite reinforcement with Al2O3-UF as a matrix or nanofillers for making the desired nanocomposite specimens. Thermo gravimetric analysis (TGA) and differential scanning calorimetry (DSC) were used to analyze the thermal properties of the specimens. The results of the study indicated that increasing the percentage of alumina nanoparticles led to an increase in the total heat content. The study also investigated the mechanical properties of the specimens, including internal bonding (IB), modulus of elasticity (MOE), and modulus of rupture (MOR), as well as the physical properties such as density, water absorption (WA), and thickness swelling (TS). The experimental results of the study showed higher values for these properties for the new nano-MDF compared to the normal samples. The results also showed that increasing the concentration of alumina nanoparticles in the UF resin had a considerable effect on the mechanical properties of the panels. Overall, the study highlighted the potential of incorporating nanoparticles such as alumina in MDF to enhance its physical and mechanical properties, which could lead to improved performance and increased application of MDF in various industries.
Although several composite material specialists have researched methods to improve the physio-mechanical strength of nanocomposites, there remains a gap to fill to achieve values closer to the ideal strength. Moreover, nanotechnology is the most cutting-edge method for creating nanocomposites with high strength and low weight. Thus, this study performed a thorough analysis of nano-MDF with varying concentrations (0.0%, 1.0%, 2.0%, and 3.0%) of GO and rGO nanoparticles based on the dry content of the resin. The physio-mechanical performance of MDF-infilled GO and rGO were the main goals of this investigation.
The study’s goal and research question were more explicitly constructed; i.e., the goal of this study was to investigate the effects of incorporating GO and rGO nanoparticles into UF resin on the physical and mechanical properties of MDF. The research question was as follows: How does the addition of GO and rGO nanoparticles at different weight percentages (1.0, 2.0, and 3.0 wt%) affect the thickness swelling, water absorption, modulus of rupture, internal bonding, and thermal stability of nano-MDF?
The UF resin was provided by Wah Nobel, Pakistan. GO was prepared in the synthesis lab of the National Centre for Physics, while the rGO was synthesized in the synthesis lab of the Institute of Space Technology. GO and rGO were synthesized in the synthesis lab at the National Centre for Physics, Islamabad. A SUND Defibrator machine set up at Ciel Woodworks Pvt. Ltd., Peshawar, Pakistan, was used to produce natural wood fibers. The average fiber length was 1.2 mm.
The resin underwent physical and mechanical testing in the lab. Table 1 summarizes the required attributes.
GO nanoparticles were produced and reduced from grapefruit using the modified Hummers’ method. Because of its outstanding yield, low cost, and compatibility with polymers due to its different surface chemistry, graphene is the most ideal filler material among all nanomaterials used in composite materials (Arduini et al, 2010). The GO nanoparticles have a size range of 14–17 nm.
Natural wood fibers were prepared in a SUND Defibrator machine installed at Ciel Woodworks Pvt., Ltd, Peshawar, Pakistan. The average fiber length was 1.2 mm.
The modified Hummers’ method was used to develop GO (Upadhyay, Soin, et al, 2015) (Upadhyay et al, 2015b). Typically, a conical flask containing 2 g of graphite and 46 mL of concentrated H2SO4 was used for the reaction, which was then put in an ice bath. The reaction mixture was constantly stirred at 0°C–5°C for another 30 min, while a total of 6 g of potassium permanganate was progressively added. Afterward, the flask was placed on a hot plate with a stirrer at 35 °C for 1 hour. After heating the reaction mixture for the specified amount of time, 92 mL of deionized water was added. After adding 20 mL of 30% H2O2 to the reaction mixture to stop the reaction, 280 mL of deionized water was added. The reaction mixture was then heated for an additional 30 min in a boiling water bath. After obtaining yellow-colored GO, it was repeatedly sieved and cleaned with 10% HCl.
Deionized water and ethanol. After being crushed, 80 g of grapefruit was added to a round bottom flask with 200 mL of deionized water. The reaction mixture was then heated to boiling and left to boil for 10 min. The temperature of the reaction mixture was raised, brought to room temperature, and then filtered to produce an extract with a red hue. To evenly distribute the 60 mg of GO throughout the 100 mL extract, the GO was added and quickly agitated. To this reaction mixture was added 360 L of aqueous NH3 solution, which caused it to become dark green instead of red in color. In an oil bath, the reaction mixture was heated to 95°C. The rGO samples were sieved, cleaned, and dehydrated in a vacuum oven up to 70°C once the heating phase was finished.
The procedures used to create and analyze reduced graphene oxide (rGO) and graphene oxide (GO) nanoparticles typically involve several steps. The following is a brief overview of these steps and potential sources of error:
Synthesis of GO: This typically involves the chemical oxidation of graphite, followed by exfoliation to produce graphene oxide sheets. Common oxidation agents include strong acids such as sulfuric acid and nitric acid. The resulting GO sheets typically have a high oxygen content and are hydrophilic.
Reduction of GO: The reduction of GO to rGO involves the removal of oxygen-containing functional groups, which results in a more hydrophobic material with improved electrical conductivity. Common reducing agents include hydrazine, sodium borohydride, and thermal annealing. The choice of reducing agent and reduction conditions can impact the resulting properties of the rGO.
Characterization of nanoparticles: Various techniques can be used to characterize the size, morphology, and composition of GO and rGO nanoparticles. The common techniques include transmission electron microscopy (TEM), scanning electron microscopy (SEM), X-ray diffraction (XRD), Fourier transform infrared (FTIR) spectroscopy, and Raman spectroscopy.
Potential sources of error: There are several potential sources of error in the synthesis and characterization of GO and rGO nanoparticles. For example, variations in the oxidation conditions can lead to differences in the resulting GO properties. The choice of reducing agent and reduction conditions can also impact the properties of the rGO. In addition, the choice of the characterization technique can influence the observed properties of the nanoparticles. It is important to carefully control the synthesis and characterization conditions to ensure accurate and reproducible results.
Nanocomposites containing UF-GO/rGO nanofillers synthesized in the lab with specific compositions are summarized in Table 2.
Four different compositions (0% w/v, 1% w/v, 2% w/v, and 3% w/v) of graphene oxide and reduced graphene oxide were selected as additives to the UF resin. The blends were mixed and homogenized using an ultrasonic processor (UP 400S, Hielscher Ultrasound Technology Company, USA) for 30 min. The samples were GO and rGO, and the subscripts S1, S2, S3, and S4 indicated the composition.
First, natural fibers were mixed with UF-GO/rGO nanofillers in a rotary drum with a nozzle. Then, raw MDF specimens measuring 460 × 460 × 18 mm3 were produced utilizing a hydraulic hot press, temperature, and time of 167 bar Pa, 175°C, and 4 minutes, respectively. The panel densities were maintained between 650 and 700 kg/m3. Three cooling days were spent in a panel treatment area on the raw nano-MDF. The produced prototypes were then finished by sanding and were cut to the desired dimensions of 440 × 440 × 16 mm3.
SEM experiments using scanning electron microscopy were performed to analyze the microstructure of UF-GO/rGO, GO, and rGO nanofillers. Following gold sputtering, SEM was performed using a MIRA3 TESCAN device (Czech Company) at a maximum of 15 kV and magnifications of ×50,000 and 700,00 X for GO nanoparticles, 500,00 X and 100,00 X for rGO nanoparticles, and 250,00 X for cured UF and UF-GO nanofillers and 500,00 X for UF-rGO Nanofillers. The samples were prepared and passed. Thermal conductivity was measured using Japan’s Kyoto electronics business device (model QTM500). The tester’s dimensions were 20 × 50 × 100 mm3 in accordance with ASTM C 1113–99 requirements (ASTM C 177/C 518, 1991; Sengupta et al, 1992). A WDW-30 (Precision Testing Company, Ltd.) electromechanical universal Testing Machine was used for tensile and bending tests.
a. Sample size: The study was conducted on a small scale in a laboratory. Therefore, the findings may not be representative of the behavior of nanoparticle-modified MDFs in larger production scales.
b. Variations in wood fibers: The wood fibers used in the study were sourced from a single wood species. Different wood species may have different properties that could affect the behavior of the nanoparticle-modified MDFs.
c. Variations in nanoparticle distribution: The distribution of nanoparticles in the MDF may not be uniform, which could result in variations in the physical and mechanical properties of the material.
d. Interactions between nanoparticles and wood fibers: The interactions between the nanoparticles and wood fibers were not analyzed in this study. These interactions could affect the mechanical and physical properties of the nanoparticle-modified MDFs.
e. Temperature and humidity: The study did not consider the effects of temperature and humidity on the behavior of the nanoparticle-modified MDF. These factors can affect the physical and mechanical properties of the material.
f. Manufacturing process: The manufacturing process used in this study may differ from the process used in large-scale production, which could affect the behavior of the nanoparticle-modified MDF.
g. Statistical analysis: The statistical analysis used in the study may have some limitations, and alternative statistical methods could lead to different conclusions.
h. Time-dependent effects: This study did not investigate the long-term behavior of the nanoparticle-modified MDFs. The mechanical and physical properties of the material may change over time, which could affect its performance.
Overall, the aforementioned limitations and potential sources of error should be considered when interpreting the study’s findings. Addressing these limitations in future research could lead to a better understanding of the behavior of nanoparticle-modified MDF and its potential applications.
Analysis of variance (ANOVA) with a single factor was applied for the statistical analysis of thickness swelling, water absorption, thermal conductivity, internal bonding, and modulus of rupture using origin 9, 64-bit software.
Figure 1 illustrates GO by scanning electron microscopy (SEM). According to Saleem et al (2018), the SEM findings demonstrate that the graphite peelings have a pattern-layered structure. The static GO exhibited a high-pitched, arbitrarily mutual crumpled-sheet structure. This showed that oxidation caused an imbalance in the orientated layered structure. Additionally, as stated by Wang and Hu (2011), the graphite leaves rubbed against one another to form monophonic or multi-layer graphene oxide (GO) costs.
The randomly oriented waves of silk-like rGO can be clearly viewed in Figure 2. The rGO sheets intertwined to create a sequence of small waves. The presence of Van der Wall contact causes rGO to exhibit a membranous fold structure. Additionally, rGO seemed more translucent and squashy (Worsley et al, 2010; Haneef et al, 2017).
The SEM images of GO and rGO nanoparticles showed that both materials had a layered structure; however, the oxidation of graphite caused an imbalance in the oriented structure of GO. The addition of GO and rGO nanoparticles to UF resin increased the strength of the composite due to the filling of extra gaps with the nanoparticles.
Figure 3 displays the SEM images of resins treated with pure UF and UF-GO. The resin’s yokes had an odd arrangement, and discernible tiny pits were examined. These ditches had a 3.0% GO absorption in the UF resin fence around them. Due to the additional filling of gaps by GO nanoparticles, the final composite achieved great strength. Scanning electron microscopy showed that GO was present in the visible leaves, while the dark area denoted resin made of UF.
Figure 5 The morphological analysis of the UF and the composite specimens was conducted using SEM images (Figure 4). Figure 3 a) shows the matrix material with additive, while Figure 4 b) displays the addition of rGO to the resin. The bright regions show the presence of rGO sheets. These ditches were visible due to the addition of 3.0% rGO nanoparticles to the UF resin. The final composite attained a high strength due to the filling of extra gaps using GO nanoparticles. The observable leaves in the SEM exhibit the presence of GO, while the dark region signifies the UF resin.
The crystalline nature of a material is one of its attractive properties for various applications. Here, GO showed a crystalline peak at 13.290, as confirmed in the literature. The calculated full width at half maximum (FWHM) value was 0.78720, while we obtained a 6.66 value of d-spacing. The Scherrer equation used to calculate the particle size produced a value of 10.2 nm (Muniz et al, 2016).
The rGO is a carbon-based material that shows an XRD peak at 26.50, as confirmed in Figure 5. The developed rGO showed crystallinity and offered better mechanical properties. The calculated FWHM was 0.09804, while we obtained d-spacing and particle size values of 3.36 and 83.3 nm, respectively. The developed nanoparticles were uniformly dispersed in water with an ultra-sonicator. The developed GO was hydrophilic, while rGO was hydrophobic.
The XRD plots showed that GO and rGO nanoparticles had crystalline structures. The rGO showed a crystalline peak at 26.50, while the GO had a crystalline peak at 13.290. The TGA curves of the nanoparticles showed that rGO had superior thermal stability compared to GO.
The TGA curves of developed nanoparticles are shown in Figure 6. The decrease in weight from 250°C to 450°C, which was seen in GO, was about 34.3 wt% and was caused by the vaporization of submerged water, the dissolution of O2 groups, and C oxidation. Complete decay of carbon may be envisaged before 630°C. The fact that rGO had a substantially superior thermal strength compared to GO before 450°C was also a source of relief. Due to the test specimen’s very low weight, the rGO decomposed at >630°C. The outcome is comparable to that of the earlier research published by Huang et al (2014).
The average values for the thickness swelling (TS) attribute are shown in Figure 7. EN-317 (European Committee for Standardization, 1993a) indicates that the standard thickness swelling value is 12%. Four different samples were fabricated, and the average TS values were reported. Average values of 30% and 28.5% were obtained for the 1%, 2%, and 3% GO and rGO samples. The recorded mean values for 1%, 2%, and 3% GO were 25.66%, 20%, and 14%, respectively, and 19.0%, 15.3%, and 10.5% for rGO. With increasing nanofiller absorption, the TS property of the nano-MDFs decreased. After adding nanofillers containing 3.0% nanoparticles, the TS property was successfully improved by a maximum of 53.3 for GO and 63.15% for rGO. The decrease in TS property could have occurred due to the nanofillers blocking the panel fiber apertures and by better UF resin curing during the heat transfer.
The average TS values of nano-MDF with GO and rGO were 30% and 28.5%, respectively, which were lower than the standard TS value of 12%. This suggests that the addition of GO and rGO nanoparticles can improve the dimensional stability of nano-MDF.
The water absorption (WA) property of the composite MDFs and the impact of the nanofillers can be seen in Figure 7. The standard value of WA,s according to ASTM D570 (ASTM International, 2010), is 45%. However, as the nanofiller absorption increases, the WA becomes less effective. The average values for 0.0%, 1.0%, 2.0%, and 3.0% GO were 85, 76.6, 63, and 55%, respectively. Similarly, the WA values for rGO were 83.0, 68, 57.4, and 48.0%. The addition of GO and rGO resulted in significant improvements in WA, with the greatest improvement of 35.2% and 42.16%, respectively. It is interesting to note that the WA of the MDF was improved due to the beneficial hot-pressing process, which led to better curing of the boards. Overall, these results suggested that the addition of nanofillers such as GO and rGO can significantly enhance the water resistance properties of MDFs.
Figure 8 displays the varied concentrations of GO and rGO in UF for the final MDF. The average thermal conductivity values were 0.131 and 0.133 W/mK for micro-MDF made with 0.0% GO and rGO, respectively. The average values were 0.136, 0.167, and 0.171 W/mK, respectively, for 1.0%, 2.0%, and 3.0% GO and 0.146, 0.172, and 0.184 w/mK for rGO micro MDF panels, corresponding to thermal conductivity enhancements of up to 23.3% and 27.7% for GO and rGO, respectively.
The internal bonding characteristics of MDFs made with UF and UF-GO/rGO resins are shown in Figure 9. According to EN-319 (European Committee for Standardization, 1993b), the standard IB value is 0.70.03 MPa. As can be seen in Figure 10, the 0.0% GO and rGO-based MDFs had average internal bonding values of 0.41, 0.53, 0.67, and 1.0 MPa and 0.48, 0.57, 0.8, and 1.6 MPa, respectively. The absorption of the aggregate nanofiller significantly improved the internal bond quality of the MDFs. The testers with 3.0% GO and rGO exhibited the greatest IB improvements of 59.0% and 70%, respectively.
The strengthening with graphene oxide nanoparticles enhanced the crosslink compactness of the UF resin, which improved the degree of heat transmission during the hot-pressing process of the MDF, which may have explained the better internal bond of the MDFs.
The average values for the reference and UF-GO/rGO-based testers at concentrations of 1.0, 2.0, and 3.0% are shown in Figure 11. According to EN-310 (European Committee for Standardization, 1993c; Gul, 2021), the standard value of MoR is 25 MPa. The average values for the GO tester were 24.0, 32.0, 36.0, and 41.0 MPa. During the same period, the average values for the rGO-based MDFs were 23.0, 35.0, 39.0, and 44.7 MPa. The greatest improvements for GO and rGO were 41.4% and 48.5%, respectively.
The findings of the study are consistent with those of previous studies that investigated the effects of GO on the physical and mechanical properties of composites. For instance, Ma et al (2019) demonstrated that the addition of GO to the adhesive resin of plywood could improve the mechanical and water resistance properties of the plywood. Similarly, Zhang et al (2018) showed that the addition of GO to the UF resin could improve the mechanical and thermal properties of the UF-GO composite.
This work produced 16-mm-thick nano MDF panels with four concentrations of graphene oxide and reduced graphene oxide nanoparticles (0.0, 1.0, 2.0, and 3.0%). The experimental findings might lead to the following conclusions.
1. The examination of the mechanical and physical characteristics of the resulting MDFs showed sufficient improvements for both GO- and rGO-based MDF samples.
2. The improvements in GO and rGO thickness swelling, water absorption, and thermal conductivity ranged from 53.3%–35.2%, 23.3%–63.15%, and to 42.16%–27.7%, respectively.
3. On the other hand, the internal bond and rupture modulus were enhanced by 59.0% and 70.0%, respectively, for GO and by 41.4% and 48.5% for rGO.
4. At a concentration of rGO nanoparticles of 3.0%, the highest value of the modulus of rupture (MoR) was 44.7 MPa.
5. The findings demonstrated that the Ts and WA exhibited direct proportional relationships for 3.0% GO and rGO.
6. By using different nanoparticles, further research may be done to examine the biological performances of MDF.
The observed improvements in MDF characteristics, such as the increased strength and decreased water absorption, can be attributed to the unique properties of graphene and graphene oxide nanoparticles.
Graphene and graphene oxide nanoparticles have high surface area-to-volume ratios, which can enhance the interaction between the nanoparticles and the MDF matrix. This can lead to improved adhesion between the particles and the MDF fibers, resulting in increased strength and stiffness.
Additionally, graphene and graphene oxide nanoparticles have excellent mechanical properties, such as high tensile strength and Young’s modulus. When these nanoparticles are incorporated into the MDF matrix, they can act as reinforcement agents, improving the mechanical properties of the resulting composite material.
Furthermore, the hydrophobic nature of graphene and graphene oxide nanoparticles can reduce the water absorption of the MDF, as evidenced by the lower thickness swelling values observed in this study. This can lead to the improved dimensional stability and durability of the resulting composite material.
Overall, the findings of the study demonstrated that the incorporation of graphene and graphene oxide nanoparticles into MDF can result in significant improvements in the mechanical and physical properties of the resulting composite material.
The raw data supporting the conclusions of this article will be made available by the authors, without undue reservation.
All authors listed have made a substantial, direct, and intellectual contribution to the work and approved it for publication.
This study received funding from King Saud University, Saudi Arabia through researchers supporting project number RSP 2023R145. Additionally, the APCs were funded by King Saud University, Saudi Arabia through researchers supporting project number RSP 2023R145.
The authors would like to thank King Saud University, Riyadh, Saudi Arabia, for researchers supporting project number RSP 2023R145.
The authors declare that the research was conducted in the absence of any commercial or financial relationships that could be construed as a potential conflict of interest.
All claims expressed in this article are solely those of the authors and do not necessarily represent those of their affiliated organizations, or those of the publisher, the editors, and the reviewers. Any product that may be evaluated in this article, or claim that may be made by its manufacturer, is not guaranteed or endorsed by the publisher.
Alabduljabbar, H., Alyousef, R., Gul, W., Syed Riaz Akbar Shah, , Khan, A., Khan, R., et al. (2020). Effect of alumina nano-particles on physical and mechanical properties of medium density fiberboard. Materials 13, 4207. doi:10.3390/ma13184207
Arduini, F., Di Giorgio, F., Amine, A., Cataldo, F., Moscone, D., and Palleschi, G. (2010). Electroanalytical characterization of carbon black nanomaterial paste electrode: Development of highly sensitive tyrosinase biosensor for catechol detection. Anal. Lett. 43, 1688–1702. doi:10.1080/00032711003653932
Astm International, (2010). ASTM D570-98 (2010) e1-Standard Test Method for Water Absorption of Plastics. Pennsylvania, United States: ASTM.
Candan, Z., and Akbulut, T.(2015). Physical and mechanical properties of Nano reinforced particleboard composites. Maderas. Cienc. Tecnol. 17 (2), 0–334. doi:10.4067/s0718-221x2015005000030
Chen, Y., Cai, T., Dang, B., Wang, H., Xiong, Y., Yao, Q., et al. (2018). The properties of fiberboard based on nanolignocelluloses/CaCO 3/PMMA composite synthesized through mechano-chemical method. Sci. Rep. 8 (1), 1–9. doi:10.1038/s41598-018-23497-x
da Silva, A. P. S., Ferreira, B. S., Favarim, H. R., Silva, M. F. F., Silva, J. V. F., Azambuja, M. A., et al. (2019). Physical properties of medium density fiberboard produced with the addition of ZnO nanoparticles. Bio Resour. 14 (1), 1618–1625.
De Silva, K. K. H., Huang, H-H., Joshi, R. K., and Yoshimura, M. (2017). Chemical reduction of graphene oxide using green reductants. Carbon 119, 190–199. doi:10.1016/j.carbon.2017.04.025
European Committee for Standardization, (1993). Particleboards and fiberboards, determination of tensile strength perpendicular to plane of the board; EN 319: 1993. Brussels, Belgium: European Committee for Standardization.
European Committee for Standardization, (1993). Particleboards and Fiberboards. Particleboards and fiberboards, determination of swelling in thickness after immersion. Bruss. Belg. En. 317.
European Committee for Standardization, . Wood-based panels, determination of modulus of elasticity in bending and bending strength. EN 310, 1993.
Gul, W., Alrobei, H., Syed Riaz Akbar Shah, , and Khan, A. (2020). Effect of iron oxide nanoparticles on the physical properties of medium density fiberboard. Polymers 12, 2911. doi:10.3390/polym12122911
Gul, W., Alrobei, H., Syed Riaz Akbar Shah, , Khan, A., Hussain, A., Asiri, A. M., et al. (2021). Effect of embedment of MWCNTs for enhancement of physical and mechanical performance of medium density fiberboard. Nanomaterials 11 (1), 29. doi:10.3390/nano11010029
Gul, W., Syed Riaz Akbar Shah, , Khan, A., and Catalin, I. P. (2021). Characterization of zinc oxide-urea formaldehyde nano resin and its impact on the physical performance of medium-density fiberboard. Polymers 13 (3), 371. doi:10.3390/polym13030371
Gul, W., Akbar, S. R., Khan, A., and Ahmed, S. (2019). “Investigation of the surface morphology and structural characterization of MDF & HDF,” in Proceedings of the 5th International Conference on Advances in Mechanical Engineering, Istanbul, Turkey, 17–19 December 2019.
Gul, W. (2021). Effect of the embedment of nano particles on the manufacturing process parameters and the mechanical properties of medium density fiberboard (MDF). Peshawar, Pakistan: University of Engineering & Technology Peshawar (Pakistan).
Gul, W., Khan, A., and Shakoor, A. (2017). Impact of hot pressing temperature on medium density fiberboard (MDF) performance. Adv. Mater. Sci. Eng. 2017, 1–6. doi:10.1155/2017/4056360
Gupta, K., and Khatri, O. P. (2017). Reduced graphene oxide as an effective adsorbent for removal of malachite green dye: Plausible adsorption pathways. J. colloid interface Sci. 501, 11–21. doi:10.1016/j.jcis.2017.04.035
Haneef, M., Saleem, H., and Habib, A. (2017). Use of graphene Nano sheets and barium titanate as fillers in PMMA for dielectric applications. Synth. Met. 223, 101–106. doi:10.1016/j.synthmet.2016.12.006
Huang, L., Zhu, P., Li, G., Lu, D. D., Sun, R., and Wong, C. (2014). Core–shell SiO 2@ RGO hybrids for epoxy composites with low percolation threshold and enhanced thermo-mechanical properties. J. Mater. Chem. A 2 (43), 18246–18255. doi:10.1039/c4ta03702b
Ismita, N., and Chavan, L. (2017). Effects of different nanoclay loadings on the physical and mechanical properties of Melia composita particle board. Bois Forets des Tropiques 334, 7–12. doi:10.19182/bft2017.334.a31487
Li, C., Zhuang, Z., Jin, X., and Chen, Z. (2017). A facile and green preparation of reduced graphene oxide using Eucalyptus leaf extract. Appl. Surf. Sci. 422, 469–474. doi:10.1016/j.apsusc.2017.06.032
Ma, J., Ma, X., Zhang, X., and Li, Z. (2019). Effects of graphene oxide on the mechanical and water resistance properties of plywood adhesive resins. J. Adhesion Sci. Technol. 33 (18), 1965–1977.
Muniz, F. T. L., Miranda, M. A. R., dos Santos, C. M., and Sasaki, J. M. (2016). The Scherrer equation and the dynamical theory of X-ray diffraction. Acta Crystallogr. a Sect. A Found. Adv. 72 (3), 385–390. doi:10.1107/s205327331600365x
Saleem, H., Haneef, M., and Abbasi, H. Y. (2018). Synthesis route of reduced graphene oxide via thermal reduction of chemically exfoliated graphene oxide. Mater. Chem. Phys. 204, 1–7. doi:10.1016/j.matchemphys.2017.10.020
Sengupta, K., Das, R., and Banerjee, G. (1992). Measurement of thermal conductivity of refractory bricks by the nonsteady state hot-wire method using differential platinum resistance thermometry. J. Test. Eval. 20 (6), 454–459.
Taghiyari, H. R., and Jack, N. (2014). Effect of silver nanoparticles on hardness in medium-density fiberboard (MDF). iForest-Biogeosciences For. 8, 677–680. doi:10.3832/ifor1188-007
Upadhyay, R. K., Navneet Soin, , Bhattacharya, G., Saha, S., Barman, A., and Roy, S. S. (2015). Grape extract assisted green synthesis of reduced graphene oxide for water treatment application. Mater. Lett. 160, 355–358. doi:10.1016/j.matlet.2015.07.144
Wang, H., and Hu, Y. H. (2011). Effect of oxygen content on structures of graphite oxides. Industrial Eng. Chem. Res. 50 (10), 6132–6137. doi:10.1021/ie102572q
Worsley, M. A., Pauzauskie, P. J., Olson, T. Y., Juergen Biener, , Satcher, J. H., and Baumann, T. F. (2010). Synthesis of graphene aerogel with high electrical conductivity. J. Am. Chem. Soc. 132 (40), 14067–14069. doi:10.1021/ja1072299
Young, R. J., Kinloch, I. A., Gong, L., and Novoselov, K. S. (2012). The mechanics of graphene nanocomposites: A review. Compos. Sci. Technol. 72 (12), 1459–1476. doi:10.1016/j.compscitech.2012.05.005
Zhang, B.-T., Zheng, X., Li, H.-F., and Lin, J.-M. (2013). Application of carbon-based nanomaterials in sample preparation: A review. Anal. Chim. acta 784, 1–17. doi:10.1016/j.aca.2013.03.054
Keywords: graphene oxide (GO), reduced graphene oxide (rGO), nanocomposites, nanofabrication, medium density fiberboard
Citation: Gul W, Akbar Shah SR, Khan A, Ahmad N, Ahmed S, Ain N, Mehmood A, Salah B, Ullah SS and Khan R (2023) Synthesis of graphene oxide (GO) and reduced graphene oxide (rGO) and their application as nano-fillers to improve the physical and mechanical properties of medium density fiberboard. Front. Mater. 10:1206918. doi: 10.3389/fmats.2023.1206918
Received: 16 April 2023; Accepted: 25 May 2023;
Published: 15 June 2023.
Edited by:
Senthil Muthu Kumar Thiagamani, Kalasalingam University, IndiaReviewed by:
Hossein Ebrahimnezhad-Khaljiri, University of Zanjan, IranCopyright © 2023 Gul, Akbar Shah, Khan, Ahmad, Ahmed, Ain, Mehmood, Salah, Ullah and Khan. This is an open-access article distributed under the terms of the Creative Commons Attribution License (CC BY). The use, distribution or reproduction in other forums is permitted, provided the original author(s) and the copyright owner(s) are credited and that the original publication in this journal is cited, in accordance with accepted academic practice. No use, distribution or reproduction is permitted which does not comply with these terms.
*Correspondence: Waheed Gul, d2FoZWVkLmd1bEBudXRlY2guZWR1LnBr; Syed Sajid Ullah, c3llZC5zLnVsbGFoQHVpYS5ubw==
Disclaimer: All claims expressed in this article are solely those of the authors and do not necessarily represent those of their affiliated organizations, or those of the publisher, the editors and the reviewers. Any product that may be evaluated in this article or claim that may be made by its manufacturer is not guaranteed or endorsed by the publisher.
Research integrity at Frontiers
Learn more about the work of our research integrity team to safeguard the quality of each article we publish.