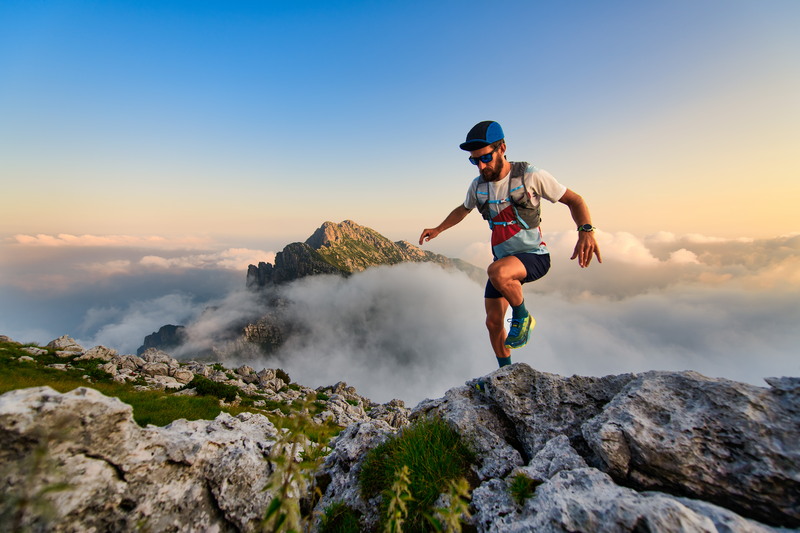
95% of researchers rate our articles as excellent or good
Learn more about the work of our research integrity team to safeguard the quality of each article we publish.
Find out more
REVIEW article
Front. Mater. , 03 January 2022
Sec. Ceramics and Glass
Volume 8 - 2021 | https://doi.org/10.3389/fmats.2021.814629
This article is part of the Research Topic Forming of Metallic Glasses and Their Functional Applications View all 6 articles
Ti-based metallic glasses (MGs) possess high specific strength, low elastic modulus, high elasticity, high wear and corrosion resistance, and excellent biocompatibility, which make them highly attractive as lightweight high-strength materials as well as biomaterials. However, the glass forming ability (GFA) of Ti-based MGs, particularly those bearing no toxic, noble, or heavy metals, that is, Be, Pd, or Cu alike, largely sets back their wide applications for the restricted critical glass forming size of these Ti-based MGs. In this review, the outlines in developing Ti-based MGs are delineated in order to provide an overall view on the efforts ever made to fabricate bulk size Ti-based MGs. The state of the art in the knowledge on the GFA of Ti-based MGs is briefly introduced, and possible directions for fabricating bulk size toxic and noble element free Ti-based MGs are discussed.
The disordered atomic packing in metallic glasses (MGs) makes them drastically different from conventional crystalline alloys and exhibit novel physical, chemical, and mechanical properties (Wang et al., 2004; Wang, 2009; Zhang et al., 2019). For the high specific strength, corrosion resistance, and biocompatibility of Ti element, Ti-based MGs have been attracting intensive attentions for their potential applications as lightweight high-strength materials (Jiang et al., 2015) and biomaterials (Li and Zheng, 2016). Early observations of non-crystalline phases in titanium alloys were made in binary TiCu and TiNi alloys in the late 1960s via splat quenching (Polk et al., 1978), for the large difference in atomic size between early transition metals (Ti) and late transition metals (Cu, Ni). Later on, lightweight Ti-based MG with a nominal composition of Ti50Be40Zr10 (i.e., METGLAS 2204) was first reported by Tanner and Ray in 1977 in the TiBeZr ternary system (Tanner and Ray, 1977). To date, hundreds of Ti-based MGs have been found (Gong et al., 2016) with improved glass forming ability (GFA) and intriguing mechanical and chemical properties, which effectively support the application of Ti-based MGs. The GFA of MGs generally refers to the lowest cooling rate required for the undercooled liquid to bypass crystallization and become a glass and is conveniently measured with the critical size of an MG sample (often the diameter of a rod) that could be cast into a fully amorphous state. However, those Ti-based MGs with excellent GFA (i.e., large critical diameter) (Gong et al., 2016) usually contain toxic element—Be, noble metal—Pd, or heavy late transition metals—Cu or Ni. The presence of these elements, to a certain extent, impairs the application prospects of Ti-based MGs. To summarize the achievements ever made and illuminate the directions for future research, the main development paths of Ti-based MGs are sorted out in this review. Based on the development paths of Ti-based MGs, 4 series of Ti-based MGs could be categorized according to the main composing elements, that is, TiCuNi series MGs, TiZrBe series MGs, TiZrCu series MGs, and TiZrSi series MGs.
In the following part, the successful preparation of each series of Ti-based MGs will be introduced in more detail, respectively. Here, we would like to emphasize that this review focuses mainly on the history of the observation of Ti-based MGs and the effect of alloying elements on the critical diameter of Ti-based MGs. Statistical data on the criteria of GFA for Ti-based MGs, such as the width of the supercooled liquid region ΔTx = Tx-Tg, the reduced glass transition temperature Trg = Tg/Tl, and the parameter γ = Tx/(Tg + Tl), are not focused on, where Tg is the glass transition temperature, Tx is the crystallization temperature, and Tl is the liquidus temperature. Moreover, the mechanical, physical, and chemical properties of Ti-based MGs are not encompassed either. For details on these aspects of Ti-based MGs, the readers are referred to more comprehensive reviews (Jiang et al., 2015; Gong et al., 2016; Li and Zheng, 2016). In the end, based on a global view on the development of Ti-based MGs, potential routes are discussed for the fabrication of new toxic and noble element free Ti-based MGs with bulk size.
In early days, glass formation and their structures of Ti-based MGs were mainly focused on to recognize these new glass materials. For example, early research studies on Ti (Cu, Fe) binary MGs were made based on their hydrogen absorption behaviors (Maeland et al., 1978; Rodmacq et al., 1988). Crystallization kinetics in amorphous TiCu and TiNi binary systems were examined by Buschow in 1983 (Buschow, 1983a; Buschow, 1983b) and in TiPt by Gao and Wang (Yi Qun Gao and Whang, 1985) in 1985, and later on, those of Ti74.8Ni13.1Cu12.1, Ti50Ni5Cu45, Ti70.8Ni13.3Cu12.3Ge3.6, and Ti66.6Cu12.5Ni13.6Ge7.3 MGs were also analyzed (Šušić et al., 1986; Gao et al., 1989). Chemical short range orders in TiNi MGs (Fukunaga et al., 1983; Fukunaga et al., 1984) were found to be analogous to that in corresponding crystalline compounds. Coexistence of two glass phases was observed in Ti61Cu23Ni16 and Ti62.5Cu12Ni23Si2.5 MGs (Duhaj et al., 1985). Electronic configurations in TiCu, TiCuAl, and TiCuSi MGs (Tanaka et al., 1988) were studied by Tanaka et al., and the results suggested that the chemical affinity of elements Si and Al for late and early transition metals is highly relevant to the GFA of these MGs.
Studies engaging in enhancing the GFA of Ti-based MGs rapidly emerged in the 1990s. Glass forming compositions in the ternary TiCuNi system with a wide supercooled liquid region (SLR) were reported in 1994 (Zhang et al., 1994). It was found that the glass forming composition range in the TiCuNi ternary system was with Ni from 0 to 50 at% and Cu from 0 to 75 at%, in which the Ti50Ni25Cu25 MG showed the widest SLR of 55 K. Since a wide SLR indicates high thermal stability of supercooled liquid and possibly good GFA (Inoue, 2000), great efforts were dedicated to the search for compositions with wider SLR. Ti65Ni25Al10 and Ti65Cu25Al10 MGs were also examined but to show no clear glass transition phenomenon before setting in of crystallization (Zhang et al., 1993). To widen the SLR of Ti-based MGs, different ternary systems Ti-Cu-(Ni, Co, Fe, and Si) were tried out (Inoue et al., 1994), whereas a quaternary Ti50Cu25Ni20Co5 MG was found to show an SLR of 90 K, but the GFA remained marginal. In 1998, the effects of Sn (and Zr) and Sb on the thermal stability of the ternary Ti50Cu25Ni20 system were examined (Zhang and Inoue, 1998). With 5 at% replacement of Ni by Sn, Ti50Cu25Ni20Sn5 MG showed an SLR of 60 K. The authors argued that the similar size of Sn (atomic radius 0.141 nm) to Ti (0.147 nm) enabled Sn to replace Ti in its compounds and the replacement of Sn to Ti altered the crystallization mode and stabilized the supercooled liquid. However, with 3 at% replacement of Ni by Sb also of a similar size (0.145 nm) to Ti, the SLR was reduced to 45 K for unclear reasons. Intriguingly, as shown in Figure 1, it was also found that by further alloying with Zr, the Ti50Cu25Ni15Sn5Zr5 MG showed a critical glass forming size of 6 mm rod diameter, indicating the crucial role of Zr in GFA. With slight composition variation, a Ti50Cu32Ni15Sn3 MG was found to show an SLR of 73 K and a critical diameter of 1 mm (Kim et al., 2001), suggesting the positive effect of Sn on GFA. In the meantime, for the smaller atomic sizes, metalloid elements Si (0.117 nm) and B (0.09 nm) were introduced to fabricate Ti50Cu20Ni24Sn3B1Si2 and Ti50Cu20Ni24B2Si4 MGs (Zhang and Inoue, 1999; Zhang and Inoue, 2001) with SLRs of 74 and 65 K in width, respectively. Ti50Cu20Ni24Sn3B1Si2 MG could also be cast into rods of a diameter of 1 mm. The authors believed that this was because the addition of B and Si enabled the 2 MGs to satisfy the 3 empirical rules of Inoue (Inoue, 2000) for glass formation, that is, (1) multicomponent with more than 3 main elements, 2) significant differences in atomic size above 12% of main elements, and 3) negative mixing heats among main elements.
FIGURE 1. Ti50Cu25Ni15Sn5Zr5 MG rods of 3 and 6 mm diameter (from Zhang et al. (Zhang and Inoue, 1998)).
In 2002, based on Ti50Cu32Ni15Sn3 MG, Kim et al. (2002), by replacing Cu (0.128 nm) with Be (0.113 nm) which is of smaller size and has larger mixing heat with Ti, prepared the Ti50Cu25Ni15Sn3Be7 MG with a critical diameter of 2 mm. The effects of Zr, Mo, and Ta on the glass formation of TiCuNiSn system were examined by He et al. (2003); He et al. (2004a); He et al. (2004b); He et al. (2006). However, mainly, amorphous ribbons could be fabricated. This was because the addition of Zr, Mo, and Ta lower the GFA by extending the melting interval and introducing nucleation sites for β-Ti solid solutions. Following Inoue’s rule, Kim et al. (2003); Kim et al. (2004); Park et al. (2004); Kim et al. (2007) further proposed to add Be and Zr into the quaternary TiCuNiSn system, and Ti45Cu25Ni15Sn3Be7Zr5 and Ti40Ni8Cu9Be18Zr25 MGs of critical diameters of 5 and 8 mm, but smaller SLR widths of 61 and 47 K were prepared. For the high content of Be and Zr, Ti40Ni8Cu9Be18Zr25 MG actually enters the TiZrBe series and suggests the potential high GFA of TiZrBe series MGs. It also seems that GFA does not agree well with the width of SLR, indicating the decoupling between GFA and thermal stability of undercooled liquid.
Similar to previous studies, in 2004, Ma et al. (2004a) examined the effect of Zr, Hf, and Si on the GFA of Ti50Cu42.5Ni7.5 MG and found that Ti41.5Cu42.5Ni7.5Zr2.5Hf5Si1 MG exhibits a critical diameter of 5 mm. The increased GFA was mainly because the addition of Zr moved the composition closer to the eutectic “valley” (lower liquid temperature and possibly higher Trg prone to glass formation) and the addition of Si stabilized the supercooled liquid, leading to the formation of local atomic structures. They (Ma et al., 2004b) also examined the effects of B, Al, and Zr on the glass formation in the TiCuNiSi system and reported Ti53Cu15Ni18Al7Zr3Si3B1 MG and Ti53Cu15Ni18.5Al7Zr3Si3B0.5 MG with a critical diameter of 2.5 mm. They found that small atom B was important in enhancing GFA for interactions with other elements and more efficient packing mode. Sun et al. also characterized the effect of small atom C (0.077 nm) on the GFA of Ti50Cu23Ni20Sn7 MG (Sun et al., 2005) but fabricated only MG composites. Later then, according to the topological glass formation model (Egami et al., 2007), early transition metals M (= Hf (0.160 nm), Zr (0.162 nm), and Sc (0.165 nm)) with large atomic sizes were introduced into Ti53Cu15Ni18.5Al7Si3B0.5M3 (Xia et al., 2005a; Xia et al., 2005b; Xia et al., 2005c; Xia et al., 2005d) to prepare new Ti-based BMGs with critical diameters of 2.5 mm, indicating no prominent effect of Hf and Sc on GFA. In 2007, based on Ma et al.’s work (Ma et al., 2004a). Huang et al. (2007) found that Ti41.5Cu37.5Ni7.5Zr2.5Hf5Si1Sn5 MG showed the best ever GFA in TiCuNi series MGs with a critical diameter of 6 mm, as shown in Figure 2, indicating the enhancement of GFA by Sn addition. Interestingly, with an equal atomic ratio, thst is, assisted by the high entropy effect (Greer, 1993) and the coexistence of Ti, Zr, and Be, TiCuNiZrHfBe MG shows a much increased critical diameter of 15 mm (Gong et al., 2015). However, TiNi (Al, Si, and Sn) ternary systems were re-examined to show limited GFA (Lu and Xu, 2008; Lu et al., 2009a; Lu et al., 2009b). By “3D pinpointing approach,” Wang et al. (Wang and Xu, 2008) found a series of quaternary (Ti, Zr) CuNi MGs with a critical diameter of 3 mm and proposed that the substitution of Zr for Ti increased GFA for its atomic size difference with Ti and negative mixing heat with Ni and Cu. Recently, Chen and Hsu also examined the effect of Sn on the GFA of a Ti44Cu40Ni16 alloy and reported a best glass former of Ti44Cu40Ni16Sn1 (Chen and Hsu, 2016) with a critical diameter of around 4 mm.
FIGURE 2. Thermograms for Ti41.5Zr2.5Hf5Cu37.5Ni7.5Si1Sn5 MG ribbon and rod (6 mm). The inset shows the SAED pattern of the rod of 6 mm diameter (from Huang et al. (2007)).
The development of TiCuNi series MGs was aimed at increasing the GFA and enlarging the SLR, that is, alloying with elements of large atomic size ratios, and attractive bonding nature to increase the difficulty in the redistribution of constituent elements for crystallization. This principle later developed into the 3 rules of Inoue. To enhance the GFA, C, Si, Sn, Sb, B, Zr, Hf, Sc, Be, Fe, Mo, Al, and Ta have been added into the TiCuNi system separately. The elements playing a positive role could be identified as Sn, Zr, Be, B, Si, and Hf. More importantly, as summarized before, coexistence of 2 or more elements would be crucial in enhancing the GFA of TiCuNi series MGs, for example, Zr + Sn (Zhang and Inoue, 1998; Wang and Xu, 2008), Zr + Be (Kim et al., 2003; Kim et al., 2004; Park et al., 2004; Kim et al., 2007), and Zr + Si (Ma et al., 2004a). This fact is worthy of further investigation for improving the GFA. However, the GFA of TiCuNi series MGs remains way small when compared to Zr-based (73 mm) (Lou et al., 2011) and Pd-based (85 mm) MGs (Nishiyama et al., 2012). On the other hand, the large amount of Cu and Ni largely lowers the specific strength of Ti-based MGs. To this situation, the TiZrBe series MGs with high GFA and lower density were rapidly developed in the past decades.
The fabrication of TiZrBe series MGs dates back to the synthesis of METGLAS 2204 (Tanner and Ray, 1977) by Tanner and Ray with high specific strength and a stable enough supercooled liquid state for the preparation of continuous ribbon. MG formation in binary TiBe and ZrBe systems was reported later in 1979, and it was found that glass formation compositions were near the eutectic point and that ZrBe exhibited better GFA than TiBe (Tanner and Ray, 1979). The formation of TiBe (Si, Al) (Tanner, 1978; Tanner et al., 1988) MGs and phase separation in the TiZrBe (Tanner and Ray, 1980) system were also studied. In 1993, with the preparation of Vitreloy 1 (Zr41.2Ti13.8Cu12.5Ni10Be22.5 MG) (Peker and Johnson, 1993), the first commercialized bulk metallic glass (BMG, referring to metallic glass that could be cast into a sample of over 1 mm in all 3 dimensions), the TiZrBe series MGs were under intensive study for bulk specimen forming compositions.
In 2002, for the small atomic size (0.113 nm) and negative mixing heat (−30 k J/mol) with Ti, Be was used in making Ti50Cu25Ni15Sn3Be7 MG with a critical diameter of 2 mm (Kim et al., 2002). In 2005, Guo et al. (2005), by tuning the Cu/Ni ratio, developed Ti40Zr25Be20Ni3Cu12 MG, with an enhanced glass forming critical diameter of 14 mm. This was because the high Cu content changed the competing phase in glass formation from quasi-crystalline to crystalline, indicating the key role of Cu in the GFA of TiZrBe series MGs. Then, Hao et al. (2006); Hao et al. (2009) examined the effect of Y on the GFA of Ti40Zr25Be20Ni3Cu12 and found that with 0.5 at% Y addition, an MG rod of 5 mm in diameter could be fabricated with low-purity raw materials as Y scavenged oxygen and impurities, leading to the formation of the Laves phase. The effect of Nb on the GFA of Ti40Zr25Be18Cu9Ni8 MG was investigated separately in Shan et al. (2008); Li et al., 2014), and no prominent enhancement was observed. Mei et al. examined the effect of Ta on the GFA of Ti40Ni8Cu9Be18Zr25 MG but found deterioration in GFA (Mei et al., 2007). For applications such as lightweight high-strength materials, Duan et al. (2008) reported the fabrication of lightweight Ti45Zr20Be35 (4.59 g/cm3) and Ti40Zr25Be30Cr5 (4.76 g/cm3) MGs containing no late transition metals with critical diameters of 6 and 8 mm. Following the path of TiZrBe series MGs, the best glass formers in Ti-based MG, Ti32.8Zr30.2Be22.7Ni5.3Cu9 MG by Tang et al. (2010) and Ti32.8Zr30.2Cu9Fe5.3Be22.7 MG by Zhang et al. (2015), were reported with a diameter over 50 mm comparable to the GFA of Zr-based (Lou et al., 2011) and Pd-based MGs (Nishiyama et al., 2012). Figure 3 shows the 50-mm rod of Ti32.8Zr30.2Cu9Fe5.3Be22.7 MG. The superior GFA was considered to be resulting from obedience to Inoue’s rules and the confusion effect induced by the 5 constituent elements (Greer, 1993).
FIGURE 3. Ti32.8Zr30.2Cu9Fe5.3Be22.7 MG rod with a diameter of 50 mm (from Zhang et al. (2015)).
Gong et al., 2012a; Gong et al., 2012b; Gong et al., 2012c; Gong et al., 2013a; Gong et al., 2013b; Gong et al., 2013c; Gong et al., 2018; Gong et al., 2020) developed the TiZrBe (Fe, Al, Fe + Cu, Al + Cu, Co.) MGs, Zhao et al. (2014); Zhao et al. (2015a); Zhao et al. (2015b); Zhao et al. (2016) fabricated TiZrBe (Cu, Ni, Ag) MGs, and Gu et al. (2017); Gu et al. (2019a); Gu et al. (2019b) developed the TiZrBeNi and TiZrBeNi (Fe, Cu) MGs with high GFA of a critical diameter of centimeters. The high GFA of these MGs are generally ascribed to obedience to Inoue’s rules and the large electronegativity of the composing elements. These MG systems largely enrich the family of TiZrBe series MGs. Lin et al. found that by adjusting the Ti/Zr ratio, the critical glass forming diameter of Ti32.8Zr30.2Be22.7Ni5.3Cu9 MG could be enhanced to 20 mm (Lin et al., 2018). Similar results were also observed in Ti35Zr30Be27.5Cu7 MG (Song et al., 2019). This was attributed to the fact that the addition of Zr increases the content of icosahedral quasi-crystalline clusters, which stabilize the undercooled melt.
With the inclusion of light metal Be of small atomic size (0.111 nm in diameter), TiZrBe series MGs usually possess excellent GFA and are readily developed for lightweight structural materials with high strength. More efficiently, with the addition of Cu and another late transition metal like Fe and Ni, that is, coexistence of Cu + Ni, Cu + Fe, the critical diameter of TiZrBe-series MG would be improved to several centimeters. As stated before, the competing phases in glass formation, the mixing heat, the confusion effect, electronegativity, the atomic size ratio, the short range order of melt, etc. have been adopted to rationalize the high GFA of TiZrBe series MGs. However, the fundamental physics underpinning the superior GFA of TiZrBe-based MGs remains less clear. On the other hand, for the biotoxicity of Be and Ni, despite the excellent GFA in TiZrBe series MGs, the application of these MGs encountered great difficulty in the field of biomaterials. Thereby, to meet the demand of biomaterials, Ti-based MGs bearing no Ni and no Be were developed.
TiZrCu series MGs as brazing filler metals were reported early in 1991 (Rabinkin et al., 1991). In 1994, by introducing Zr into the TiCuNi ternary system, Amiya et al., 1994) found that the TiZrCu ternary system and the TiZrCuNi quaternary system showed much improved thermal stability. For example, the amorphous Ti50Cu40Zr10 powders prepared by high-pressure gas atomization showed a clear supercooled liquid region of 47 K. This is due to the large atomic size of Zr and the negative mixing heat of Zr–Cu, which increased the difficulty in the redistribution of constituent elements for crystallization. By introducing Zr and Ni into the TiCu binary system, for the atomic size mismatch and strong interaction induced, Men et al. (2005) reported the formation of Ti45Zr5Cu45Ni5 MG, with a critical diameter of 3 mm. However, Ti45Zr5Cu45Ni5 MG is still not Ni-free. As Pd and Ni belong to the same family, Zhu et al. proposed to replace Ni (0.125 nm) with Pd (0.137 nm) in the Ti–Cu–Ni–Zr system and prepared a Ni-free Ti40Zr10Cu34Pd16 MG, with a glass forming critical diameter of 6 mm (Zhu et al., 2007a; Zhu et al., 2007b). The improved GFA is due to the atomic size difference and the negative mixing heat between Pd and Ti, and Zr and Cu. By replacing Cu with Sn in Ti40Zr10Pd14Cu36 MG, as shown in Figure 4, Zhu et al. reported Ti40Zr10Cu34Pd14Sn2 and Ti40Zr10Cu32Pd14Sn4 MGs with maximized GFA of a critical diameter of 12 mm in conjunction with high plasticity and strength (Zhu et al., 2008; Zhu et al., 2012a). This was also due to the atomic size difference and the negative mixing heat induced by Sn, proving the positive effect of Sn on Ti-based MGs. For the atomic size and mixing heat, Xie et al. (2010a) examined the effect of large atom Sn (0.141 nm) and small atom Ni (0.125 nm) on the GFA of Ti45Cu37.8Zr10Ni7.2 MG and found (Ti0.45Cu0.378Zr0.10Ni0.072)98Sn2 MG and Ti43.15Zr9.59Cu36.24Ni9.06Sn1.96 MG (Xie et al., 2010b) with increased GFA of a critical diameter of 2–3 mm.
FIGURE 4. XRD patterns of TiZrCuPdSn MGs. The inset is the 12 mm rod of Ti40Zr10Cu34Pd14Sn2 MG (from Zhu et al. (2012a)).
Lately, Wang et al. (2013a) investigated the effect of Co. on the GFA of Ti40Zr10Pd14Cu36 MG and reported the Ti39Zr10Pd14Cu36Co1 MG and the (Ti0.39Zr0.10Pd0.14Cu0.36)99Co1 MG with critical diameters of 10 and 8 mm respectively. The increased GFA for the Co containing MG was attributed to the formation of network composed of Co,, Zr, and Pd atoms where the Co atoms connect with Zr and Pd atoms, as illustrated in Figure 5.
FIGURE 5. Atomic structures in Ti39Zr10Cu36Pd14 and Ti39Zr10Cu36Pd14Co1 MGs obtained from MD simulations (from Wang et al. (2013a)). (A) Total pair-distribution function; (B) arrangements of Pd and Zr in Ti39Zr10Cu36Pd14; (C) arrangements of Pd and Zr in Ti39Zr10Cu36Pd14Co1; (D) arrangements of Pd, Zr, and Co in Ti39Zr10Cu36Pd14Co1 MG.
In 2010, Zhao et al. investigated the effect of Si addition on the GFA of Ti43.89Cu43.60Zr6.75Ni5.76 MG with a deep eutectic character (Zhao et al., 2010) and found that small addition (0.5–1 at%) would improve GFA for the negative mixing heat, the confusion effect, and possibly the scavenging effect of Si on O, and the destabilizing effect of Si on the TiO2 cluster. By replacing Cu with Si, Zhu et al. found the formation of Ti40Cu33Zr10Pd14Sn2Si1 MG with increased thermal stability of an SLR of 80 K but reduced GFA (Zhu et al., 2012b). This was possibly due to the increase in the liquidus temperature induced by Si addition. Yi et al. also reported the preparation of Ti45.0Cu40.1Zr12.7Si2.2 MG, with a critical diameter of 3 mm (Yi, 2012). However, Tsai et al. studied the small addition effect of Si on the GFA of Ti40Zr10Pd14Cu36 MG (Tsai et al., 2015) and reported only slight variation in GFA. It is inferred that the effect of Si on TiZrCu series MGs is more prone to the enhancement of thermal stability.
In 2008, Qin et al. found that micro-addition of Nb in Ti40Zr10Pd14Cu36 MG would lead to the formation of in situ Pd3Ti nanoparticle MG composites (Qin et al., 2008). Oak et al. examined the effect of Nb and Ta addition on the GFA of Ti45Zr10Pd10Cu31Sn4 MG (Oak et al., 2009; Oak et al., 2011) and also found decreased GFA. Qin et al. found that the addition of Ta reduced the GFA of Ti40Zr10Pd14Cu36 MG but increased the corrosion resistance and plasticity (Qin et al., 2012). Fornell et al. investigated the effect of Nb on another Ti40Zr10Cu38Pd12 MG and found the formation of CuTi2 and CuTi nanoparticles (Fornell et al., 2013). Qin et al. (Qin et al., 2016) further explored the effects of Au, Pt, Nb, and Ta replacing Cu on the GFA of Ti40Zr10Pd14Cu34Sn2 MG and found decayed GFA with the precipitation of Pd3Ti nanoparticles. The authors attributed this fact to the decreased crystallization temperature after micro-addition of these elements. Yang et al. investigated the effect of Nb addition on the GFA of Ti40Zr10Cu33Pd14Sn3 and found the precipitation of β-Ti and Ti2Cu phases (Yang et al., 2017a). Wu et al. (2019) also observed decreased GFA in Ti40Zr10Cu33Pd14Sn3 MG with the addition of Nb. It is seen that the addition of Nb is detrimental to the GFA, and the resulting glass formation competing phases are complicated. The effect of Nb on GFA might be due to the positive mixing heat of Nb–Ti, Nb–Zr, and Nb–Cu.
Different attempts for new Ti-based MGs were also made, but the reason for the reduced GFA was not clear. In 2017, Oak et al. reported the preparation of Ti45Hf10Pd10Cu30Sn5 MG by replacing Zr with Hf in Ti45Zr10Pd10Cu30Sn5 MG, however with reduced GFA (Oak et al., 2017). Jia et al. (2018) studied the effect of Ni and Pt replacing Pd on the GFA of Ti41Cu36Zr10Pd13 and also found the degradation of GFA. By replacing Cu with Ag, Nicoara et al. designed and prepared Ti30Zr32Ag7Pd24Sn7 MG ribbons (Nicoara et al., 2018) with marginal GFA. Tantavisut et al. reported the fabrication of Ti44Zr10Pd10Cu6Co23Ta7, Ti44Zr10Pd10Cu10Co19Ta7, and Ti44Zr10Pd10Cu14Co15Ta7 MGs (Tantavisut et al., 2018). Bera et al. characterized the effect of Ga replacing Cu on the GFA of Ti40Zr10Pd14Cu36 MG and reported GFA in Ti40Zr10Cu34Pd14Ga2 and Ti40Zr10Cu32Pd14Ga4 MGs, with a diameter of 3 mm (Bera et al., 2019). They found that they could only obtain Ti40Zr10Pd14Cu36 MG of 2 mm diameter and attributed the GFA in Ti40Zr10Cu32Pd14Ga4 MG to the larger atomic size and more negative mixing heat of Ga.
To remove Ni from Ti47.4Cu42Zr5.3Ni5.3 MG, Seki et al. prepared Ti47.4Cu42Zr5.3TM5.3 (TM = Co., Fe) MGs but with decreased thermal stability (Seki et al., 2008) due to the difference in the electronic state between Ni and Co or Fe. Yin et al. examined the effect of Ni replacing Cu on Ti45.8Zr6.2Cu45Sn2Si1 MG and that of Zr replacing Ti on Ti52Cu40.9Ni5.1Sn2 MG and prepared MGs, with a critical diameter of 4 mm (Yin et al., 2013). They proposed that the GFA of these MGs showing multiple crystallization events correlated strongly with the onset temperature of the last crystallization event. Using the cluster-plus-glue-atom model, Wang et al. designed 2 TiZrCuSn MGs (i.e., (Ti7.2Zr1.8) (Cu8.72Sn0.28) and (Ti7.2Zr1.8) (Cu8.45Sn0.55)), with a critical glass forming diameter of 5 mm (Wang et al., 2013b), and later Ti40Zr10Cu56.94Sn3.06 and Ti45.71Zr11.43Cu39.29Sn3.57 MGs (Wang et al., 2016). However, for the high atomic fraction of Cu, they are more like Cu-based MGs, except for Ti45.71Zr11.43Cu39.29Sn3.57 MG. Based on Inoue’s rules and the effective atomic radius, Shirasawa et al. prepared TiZrCo ternary MGs around a predicted near eutectic Ti44Zr30Co26 MG (Shirasawa et al., 2014), as shown in Figure 6. These results provide possible routes for the design of new Ti-based MGs. Cao et al. studied the effect of nitrogen on the GFA of Ti42.5Cu40Zr10Ni5Sn2.5 and reported that the addition of N of 0.1 at% could facilitate the formation of glass by suppressing the formation of the competing eutectic structure (Cao et al., 2016). Kuball et al. reported the fabrication of a new class of sulfur-bearing Ti-based Ti75Ni17S8 and Ti40Zr35Cu17S8 MGs (Kuball et al., 2018; Kuball et al., 2019). The effect of S on GFA was interpreted with its smaller size, higher mixing heat with other elements, low solubility in intermetallics, and the tendency for formation of covalent bonds. Introducing small metalloid atoms could be new paths for the development of Ti-based MGs.
FIGURE 6. Design of TiZrCo ternary MGs (from Shirasawa et al. (2014)).
In 2014, Hu et al. reported Ti47Zr7.5Cu40Co2.5Sn2Si1 and Ti45Zr7.5Cu42Co2.5Sn2Si1 MGs, with a critical diameter of 3 mm (Hu et al., 2014). Coincidently, Wang et al. also studied the effect of Zr and Si on the GFA of Ti46Cu44Co7Sn3 MG and reported the Ti46Zr11.5Cu31.5Co7Sn3Si1 MG, with a critical diameter of 3 mm (Wang et al., 2015a). The improved GFA was due to the atomic size difference and mixing heat induced by Zr and Si. Later, they examined the effect of Ag replacing Cu on the GFA of Ti46Cu31.5Zr11.5Co7Sn3Si1 MG and found that Ti46Cu27.5Zr11.5Co7Sn3Si1Ag4 MG showed a critical diameter of 4 mm (Wang et al., 2015b). This was inspired by the fact that Pang et al. (2015) reported the preparation of Ti47Cu38Zr7.5Fe2.5Sn2Si1Ag2 MG with a diameter of 7 mm, as shown in Figure 7, the largest Ni-, Be-, and Pd-free Ti-based MG as the addition of silver promoted the formation of icosahedral clusters in the undercooled melt, which suppressed the nucleation of competing crystalline phases. Yan et al. investigated the effect of Nb replacing Cu on the GFA of Ti47Cu38Zr7.5Fe2.5Sn2Si1Ag2 MG, but observed reduced GFA of a critical diameter of 3 mm (Yan et al., 2018). This result was ascribed to the positive mixing heat of Nb–Ti, Nb–Zr, and Nb–Cu. The effect of (Ti + Zr)/Cu ratio on the glass formation in (TiZrCu)95Fe2.5Sn2Si1 MG was also studied and was found that Ti47Zr7.5Cu40Fe2.5Sn2Si1 MG exhibited good GFA, with a critical diameter of 3 mm (Liu et al., 2016a). Later, they examined the effect of Sc replacing Ti on the GFA of Ti47Cu40Zr7.5Fe2.5Sn2Si1 MG and reported best glass formers Ti45Cu40Zr7.5Fe2.5Sn2Si1Sc2 and Ti44Cu40Zr7.5Fe2.5Sn2Si1Sc3 MGs with a critical diameter of 6 mm (Liu et al., 2016b), for the scavenging effect of Sc and its negative mixing heat with Si, Sn, Zr, and Cu. They also found that Ta replacing Cu reduced the GFA of Ti47Cu38Zr7.5Fe2.5Sn2Si1Ag2 MG (Liu et al., 2020a) for the positive mixing heat of Ta-(Ti, Zr, Cu). Yang et al. from the same group also examined the GFA in (Ti, Cu, Zr)92.5Fe2.5Sn2Si1Ag2 alloys with composition adjustment between Ti, Cu, and Zr (Yang et al., 2021). Wang et al. examined the effect of Pd replacing Cu on the GFA of Ti47Cu38Zr7.5Fe2.5Sn2Si1Ag2 MG (Wang et al., 2021) and found reduced GFA for the increased liquidus temperature with Pd addition. However, the critical diameter was still no more than 7 mm.
FIGURE 7. XRD patterns of Ti47Cu38Zr7.5Fe2.5Sn2Si1Ag2 MG (from Pang et al. (2015)).
The search for Be-, Ni-, and Pd-free TiZrCu series MG with high GFA has been a hot topic up to now. In the past decades, great efforts have been made to reduce the content of Pd in Ti40Zr10Cu34Pd14Sn2 MG and increase the GFA. For this purpose, vastly different elements have been alloyed with TiZrCu series MGs, for example, Pd, Sn, Si, Ni, Nb, Hf, Ta, Fe, Ag, Co, N, S, and Sc. Also, coexistences of Pd + Sn and Pd + Co. would benefit glass formation. However, just like the situation in TiZrBe and TiCuNi series MGs, the fundamental physics underlying glass formation in Ti-based MGs remains elusive as vastly different concepts have been adopted to rationalize the intractable variation of GFA with the addition of alloying elements. Particularly, for the septenary and octonary alloys, understanding the GFA becomes increasingly difficult. On the other hand, the large atomic fraction of copper which would lead to adverse tissue reactions (Long and Rack, 1998) and also poses a disadvantage for the application of TiZrCu series MGs as biomaterials.
MGs composed merely of non-toxic elements are highly desirable for biomedical applications. The TiZrSi system (Whang et al., 1985), an important system in Ti-based crystalline alloys, was focused on to this motive. However, compared to other 3 series of Ti-based MGs, the TiZrSi series MGs are highly vulnerable in glass formation. Polk et al. (1978) examined the glass formation behaviors in TiSi and TiNi binary and TiNiSi ternary systems and reported a typical Ti60Ni30Si10 MG processable by melt spinning but with considerable Ni content. They proposed that low liquidus temperature, chemical difference, and size difference were critical to glass formation. In 1980, Suryanarayana et al. reported the formation of binary TiSi MG containing 15–20 at% Si (Suryanarayana et al., 1980). Inoue et al. reported the preparation of TiNb(Ta)Si(Mo, Rh, Ru, Ir, B, C, Ge) MG for the research on superconducting in MGs (Inoue et al., 1980a; Inoue et al., 1980b; Inoue et al., 1981). In 1992, Tarasova investigated the short range order of Ti64Zr22Si14 MG (Tarasova et al., 1992). Oak et al. prepared thin ribbon (TixZryTaz)85Si15 MGs and found that the Ti60Zr10Ta15Si15 MG ribbon of 20 µm in thickness exhibited both high ductility and ultimate strength (Oak and Inoue, 2007). In 2008, Oak et al. not only examined the glass formation in TiZrPdSi system but also prepared amorphous ribbons of 20 µm thickness (Oak and Inoue, 2008), despite the fact that the TiZrPdSi system obeyed Inoue’s 3 rules. The authors argued that the TiZrPdSi system would be a possible seed system for the development of Ti-based MGs bearing no toxic elements. Bai et al. prepared the biocompatible Ti70Zr6Fe7Si17 MG and Ti64Zr5Fe6Si17Mo6Nb2 MG and predicted that the addition of Mo and Nb should increase the GFA for the obedience to Inoue’s rules, but the specimen remained in the ribbon shape with a thickness of 80 µm (Bai et al., 2008). As shown in Figure 8, Calin et al. developed Ti75Zr10Si15 and Ti60Nb15Zr10Si15 MG ribbons of 30 µm in thickness with better biocompatibility and found that the addition of Nb increases the GFA for atomic mismatch and negative mixing heat of Nb-Si (Calin et al., 2013).
FIGURE 8. Composition design of TiZrSi MG (from Calin et al. (2013)).
Other alloys, for example, Ti64Zr10Si15Nb11 and Ti56Zr10Si15Nb19, were also prepared in ribbons but containing nanoparticles (Gabor et al., 2019). Huang et al. reported the fabrication of thin ribbon Ti42Zr40Si15Ta3 and Ti40Zr40Si15Cu5 MGs of 80–100 µm thickness (Huang et al., 2014; Huang et al., 2016) and found that for using as biomaterials, the content of Cu should be less than 5 at%, although it benefited GFA. Wu et al. investigated the effect of Sn on the GFA of Ti60Zr10Ta15Si15 MG (Wu et al., 2014) and found that the addition of Sn reduced the GFA. The authors attributed this fact to the relative decrease in the Si content with the addition of Sn, which reduces the atom pairs (Ti-Si) of negative mixing heat and is of great atomic size mismatch. Guo et al. fabricated the TiFeSi, TiFeSi(Zr,Pd,Ge) MGs (Guo et al., 2015) near the eutectic composition Ti65Fe30Si5 and found that small additions of Zr will ease glass formation, but the presence of Ge and Pd promotes crystallization for the atomic size mismatch. Abdi et al. studied the Ti75Zr10Si15 and Ti60Zr10Nb15Si15 alloys and found that by melt spinning only glassy matrix composites of 30–50 µm in thickness could be obtained (Abdi et al., 2016). These results suggest that the GFA of Ti75Zr10Si15 and Ti60Zr10Nb15Si15 MGs is not robust. Although poor GFA, the Ti60Nb15Zr10Si15 MG thin film was found to exhibit excellent biocompatibility (Thanka Rajan et al., 2019). Based on a design approach for high entropy alloys, Calin et al. (2021) prepared Ti20Zr20Nb20Hf20Si20, Ti30Zr25Nb25Si15Ga3B2, and Ti20Zr20Nb20Hf20Si15Ga3B2 alloys to obtain better glass former; however, slight crystalline phases precipitated in the glassy matrix.
Compared to the other 3 series of MGs, the GFA of TiZrSi series MGs is quite poor, as evidenced by the fact that only ribbon samples could be fabricated in the discovered compositions. This is largely because aiming for biomaterials, the development of TiZrSi series MGs excludes the presence of most late transition metals which are either adverse to the human body or noble. According to the empirical rules for glass formation, the late transition metals of medium atomic sizes compared to large early transition metal atoms and small metalloid atoms are critical in the GFA of MGs. As evidence suggests, the best glass formers in other MG systems are given in Table 1. It is seen that these alloy systems generally consist of early transition metals (ETMs), late transition metals (LTM), metal elements, and metalloids. More importantly, late transition metals (Cu, Ni, Co., Zn, Ag, Pd, etc.) are a prerequisite for their excellent GFA either as the base element or as the main constituents. As also observed in Zhao et al. (2015b), compared to electronegativity and mixing enthalpy, larger atomic size difference generally leads to higher GFA and seems more dominant for Ti-based MGs, whereas the mixing enthalpy and the electronegativity are also important. Thereby, to make a breakthrough and develop new TiZrSi series MGs, more advanced and instructive understandings on the GFA of Ti-based MGs is of top priority. On the other hand, as a compromise for the development of biomaterials, addition of expensive elements Pd, Hf, Ta, etc. would be tolerable on a condition that enough GFA could be achieved. Nevertheless, there is still a long journey before the fabrication of toxic element free Ti-based MGs.
In retrospect, on the development paths of Ti-based MGs, it is seen that the basic method for the design of MG forming compositions mainly includes the following 3 steps: i) according to the 3 empirical rules of Inoue, usually 3 main composing elements are chosen by their atomic sizes and the mixing heat between them; ii) the eutectic compositions are usually taken as guides for the base composition; and iii) the addition of minor alloying elements chosen by Inoue’s rules or substituting the main elements with similar elements by the confusion principle was performed to optimize the GFA of the base composition with trial and error.” However, the factors that play a non-trivial role on GFA are far more than those covered by the 3 empirical rules of Inoue—the eutectic composition, and the confusion principle. This fact significantly reduces the efficiency of the basic method. In this sense, in order to develop novel Ti-based MGs, as presented before, of top priority is to advance current understandings on the GFA of MGs—for instance, the coexistence of elements on GFA. More recently, the novel strong correlation between GFA and the full width at half maximum of the first diffraction peak of MGs (Li et al., 2021a) would help rapidly identify best glass formers.
On the other hand, based on the advances in artificial intelligence and manufacture technology, there could be 2 other ways around the aforementioned difficulty to fabricate bulk size Ti-based MGs. First is the machine learning approach (Sun et al., 2017). As outlined in Development paths of Ti-based MGs, large quantity of data on the glass formation behaviors of Ti-based MGs have been accumulated in the past half century. For the large number of Ti-based MG compositions observed and the many different alloying elements adopted, it is pretty difficult to manually establish a self-consistent GFA model compatible with all the data. In recent years, machine learning models for materials design boom up because of its ability in analyzing large-volume and high-dimension data and have proved to be a promising approach for finding MG compositions with good GFA (Sun et al., 2017; Liu et al., 2020b; Xiong et al., 2021). With machine learning models, based on the glass forming compositions and the non-glass forming compositions accumulated to date, potential Ti-based MGs with high GFA could be more conveniently found.
Second is the 3D printing technique (Zhang et al., 2021). It has been long noticed that the thermal stability and the GFA of MGs are usually decoupled. As the fundamental physics in glass formation is the suppression of crystal formation, a possible reason for the decoupling between GFA and thermal stability could arise from the discrepancy between the crystal nucleation activation energy and the crystal growth activation energy. We argue that those MGs with high thermal stability tend to have high crystal nucleation activation energy, which enables large undercooling of liquid, while those MGs with high GFA, besides high crystal nucleation activation energy, tend to have high crystal growth activation energy which suppresses the burst growth of crystal nuclei. This is partially validated by recent work on 3D printing of MGs (Ouyang et al., 2021). For the rapid cooling process in the 3D printing process, the thermal stability of MGs weighs much over the GFA. Thereby, by the 3D printing technique, with MG powders of excellent thermal stability, the size limit on the fabrication of Ti-based MGs would be ultimately relieved. A similar approach is the ultrasonic assisted forming (Ma et al., 2019), by which giant MGs are successfully prepared (Li et al., 2021b). This processing method also provides a potential way for the fabrication of bulk size Ti-based MGs containing no noble, no toxic, and no heavy metal elements as long as Ti-based MGs have high enough thermal stability to survive the processing period.
All authors have made substantial, direct, and intellectual contribution to the work and approved it for publication.
This work was financially supported by the National Nature and Science Foundation of China under grant No. 51701082, Guangzhou Science and Technology Plan Project under grant No.202102020821, and the Fundamental Research Funds for Central Universities.
The authors declare that the research was conducted in the absence of any commercial or financial relationships that could be construed as a potential conflict of interest.
All claims expressed in this article are solely those of the authors and do not necessarily represent those of their affiliated organizations, or those of the publisher, the editors, and the reviewers. Any product that may be evaluated in this article, or claim that may be made by its manufacturer, is not guaranteed or endorsed by the publisher.
Abdi, S., Oswald, S., Gostin, P. F., Helth, A., Sort, J., Baró, M. D., et al. (2016). Designing New Biocompatible Glass-Forming Ti75- X Zr10 Nb X Si15 (X = 0, 15) Alloys: Corrosion, Passivity, and Apatite Formation. J. Biomed. Mater. Res. 104, 27–38. doi:10.1002/jbm.b.33332
Amiya, K., Nishiyama, N., Inoue, A., and Masumoto, T. (1994). Mechanical Strength and thermal Stability of Ti-Based Amorphous Alloys with Large Glass-Forming Ability. Mater. Sci. Eng. A 179-180, 692–696. doi:10.1016/0921-5093(94)90294-1
Bai, L., Cui, C., Wang, Q., Bu, S., and Qi, Y. (2008). Ti-Zr-Fe-Si System Amorphous Alloys with Excellent Biocompatibility. J. Non-Crystalline Sol. 354, 3935–3938. doi:10.1016/j.jnoncrysol.2008.05.015
Bera, S., Ramasamy, P., Şopu, D., Sarac, B., Zálešák, J., Gammer, C., et al. (2019). Tuning the Glass Forming Ability and Mechanical Properties of Ti-Based Bulk Metallic Glasses by Ga Additions. J. Alloys Comp. 793, 552–563. doi:10.1016/j.jallcom.2019.04.173
Buschow, K. H. J. (1983). Stability and Electrical Transport Properties of Amorphous Ti1-xNixalloys. J. Phys. F: Met. Phys. 13, 563–571. doi:10.1088/0305-4608/13/3/006
Buschow, K. H. J. (1983). Thermal Stability of Amorphous Ti-Cu Alloys. Acta Metallurgica 31, 155–160. doi:10.1016/0001-6160(83)90075-5
Calin, M., Gebert, A., Ghinea, A. C., Gostin, P. F., Abdi, S., Mickel, C., et al. (2013). Designing Biocompatible Ti-Based Metallic Glasses for Implant Applications. Mater. Sci. Eng. C 33, 875–883. doi:10.1016/j.msec.2012.11.015
Calin, M., Vishnu, J., Thirathipviwat, P., Popa, M.-M., Krautz, M., Manivasagam, G., et al. (2021). Tailoring Biocompatible Ti-Zr-Nb-Hf-Si Metallic Glasses Based on High-Entropy Alloys Design Approach. Mater. Sci. Eng. C 121, 111733. doi:10.1016/j.msec.2020.111733
Cao, D., Wu, Y., Wang, H., Liu, X.-J., and Lu, Z. P. (2016). Effects of Nitrogen on the Glass Formation and Mechanical Properties of a Ti-Based Metallic Glass. Acta Metall. Sin. (Engl. Lett. 29, 173–180. doi:10.1007/s40195-016-0374-5
Chen, T.-H., and Hsu, Y.-K. (2016). Mechanical Properties and Microstructural of Biomedical Ti-Based Bulk Metallic Glass with Sn Addition. Comput. Mater. Sci. 117, 584–589. doi:10.1016/j.commatsci.2015.12.020
Duan, G., Wiest, A., Lind, M. L., Kahl, A., and Johnson, W. L. (2008). Lightweight Ti-Based Bulk Metallic Glasses Excluding Late Transition Metals. Scripta Materialia 58, 465–468. doi:10.1016/j.scriptamat.2007.10.040
Duhaj, P., Vlasák, G., and Svec, P. (1985). “The Study of Structural Changes in Ti-Based Metallic Glasses,” in Rapidly Quenched Metals. Editors S. Steeb, and H. Warlimont (Elsevier), 767–770. doi:10.1016/b978-0-444-86939-5.50184-6
Egami, T., Poon, S. J., Zhang, Z., and Keppens, V. (2007). Glass Transition in Metallic Glasses: A Microscopic Model of Topological Fluctuations in the Bonding Network. Phys. Rev. B 76, 024203. doi:10.1103/physrevb.76.024203
Fornell, J., Pellicer, E., Van Steenberge, N., González, S., Gebert, A., Suriñach, S., et al. (2013). Improved Plasticity and Corrosion Behavior in Ti-Zr-Cu-Pd Metallic Glass with Minor Additions of Nb: An alloy Composition Intended for Biomedical Applications. Mater. Sci. Eng. A 559, 159–164. doi:10.1016/j.msea.2012.08.058
Fukunaga, T., Hayashi, N., Kai, K., Watanabe, N., and Suzuki, K. (1983). Chemical Short-Range Structure of NixTi1−x (X = 0.26−0.40) alloy Glasses. Physica B+C 120, 352–356. doi:10.1016/0378-4363(83)90405-9
Fukunaga, T., Watanabe, N., and Suzuki, K. (1984). Experimental Determination of Partial Structures in Ni40Ti60 Glass. J. Non-Crystalline Sol. 61-62, 343–348. doi:10.1016/0022-3093(84)90572-6
Qin, F. X., Xie, G. Q., Zhu, S. L., and Dan, Z. H., 8th International Forum on Advanced Materials Science and Technology (IFAMST-8), Fukuoka Inst Technol, Fukuoka City, JAPAN, 2012, pp. 23–26.
Gabor, C., Cristea, D., Velicu, I.-L., Bedo, T., Gatto, A., Bassoli, E., et al. (2019). Ti-Zr-Si-Nb Nanocrystalline Alloys and Metallic Glasses: Assessment on the Structure, Thermal Stability, Corrosion and Mechanical Properties. Materials 12, 1551. doi:10.3390/ma12091551
Gao, Y.-Q., Liu, X., Wang, W., Lo, Y.-B., and Yang, X.-Q. (1989). Crystallization Behavior of Ti66.6Ni13.6Cu12.5Ge7.3 Glass. Mater. Sci. Eng. A 108, 19–23. doi:10.1016/0921-5093(89)90401-2
Gong, P., Deng, L., Jin, J., Wang, S., Wang, X., and Yao, K. (2016). Review on the Research and Development of Ti-Based Bulk Metallic Glasses. Metals 6, 264. doi:10.3390/met6110264
Gong, P., Li, F., and Jin, J. (2020). Preparation, Characterization, and Properties of Novel Ti-Zr-Be-Co Bulk Metallic Glasses. Materials 13, 223. doi:10.3390/ma13010223
Gong, P., Wang, S., Liu, Z., Chen, W., Li, N., Wang, X., et al. (2018). Lightweight Ti-Based Bulk Metallic Glasses with superior Thermoplastic Formability. Intermetallics 98, 54–59. doi:10.1016/j.intermet.2018.04.019
Gong, P., Wang, X., Shao, Y., Chen, N., Liu, X., and Yao, K. F. (2013). A Ti-Zr-Be-Fe-Cu Bulk Metallic Glass with superior Glass-Forming Ability and High Specific Strength. Intermetallics 43, 177–181. doi:10.1016/j.intermet.2013.08.003
Gong, P., Yao, K.-F., Wang, X., and Shao, Y. (2012). Centimeter-sized Ti-Based Bulk Metallic Glass with High Specific Strength. Prog. Nat. Sci. Mater. Int. 22, 401–406. doi:10.1016/j.pnsc.2012.10.007
Gong, P., Yao, K., and Ding, H. (2013). Centimeter-Sized Ti-Based Quaternary Bulk Metallic Glass Prepared by Water Quenching. Int. J. Mod. Phys. B 27, 1350087. doi:10.1142/s0217979213500872
Gong, P., Yao, K. F., and Ding, H. Y. (2015). Crystallization Kinetics of TiZrHfCuNiBe High Entropy Bulk Metallic Glass. Mater. Lett. 156, 146–149. doi:10.1016/j.matlet.2015.05.018
Gong, P., Yao, K. F., and Shao, Y. (2012). Effects of Fe Addition on Glass-Forming Ability and Mechanical Properties of Ti-Zr-Be Bulk Metallic Glass. J. Alloys Comp. 536, 26–29. doi:10.1016/j.jallcom.2012.04.048
Gong, P., Yao, K. F., and Shao, Y. (2012). Lightweight Ti-Zr-Be-Al Bulk Metallic Glasses with Improved Glass-Forming Ability and Compressive Plasticity. J. Non-Crystalline Sol. 358, 2620–2625. doi:10.1016/j.jnoncrysol.2012.06.011
Gong, P., Yao, K., Wang, X., and Shao, Y. (2013). A New Centimeter-Sized Ti-Based Quaternary Bulk Metallic Glass with Good Mechanical Properties. Adv. Eng. Mater. 15, 691–696. doi:10.1002/adem.201200391
Gu, J.-L., Shao, Y., and Yao, K.-F. (2019). The Novel Ti-Based Metallic Glass with Excellent Glass Forming Ability and an Elastic Constant Dependent Glass Forming Criterion. Materialia 8, 100433. doi:10.1016/j.mtla.2019.100433
Gu, J.-L., Shao, Y., Zhao, S.-F., Lu, S.-Y., Yang, G.-N., Chen, S.-Q., et al. (2017). Effects of Cu Addition on the Glass Forming Ability and Corrosion Resistance of Ti-Zr-Be-Ni Alloys. J. Alloys Comp. 725, 573–579. doi:10.1016/j.jallcom.2017.07.165
Gu, J., Yang, X., Zhang, A., Shao, Y., Zhao, S., and Yao, K. (2019). Centimeter-sized Ti-Rich Bulk Metallic Glasses with superior Specific Strength and Corrosion Resistance. J. Non-Crystalline Sol. 512, 206–210. doi:10.1016/j.jnoncrysol.2018.10.034
Guo, F., Poon, S. J., and Shiflet, G. J. (2003). Metallic Glass Ingots Based on Yttrium. Appl. Phys. Lett. 83, 2575–2577. doi:10.1063/1.1614420
Guo, F., Wang, H.-J., Poon, S. J., and Shiflet, G. J. (2005). Ductile Titanium-Based Glassy alloy Ingots. Appl. Phys. Lett. 86, 091907. doi:10.1063/1.1872214
Guo, H., Zhang, W., Qin, C., Qiang, J., Chen, M., and Inoue, A. (2009). Glass-Forming Ability and Properties of New Au-Based Glassy Alloys with Low Au Concentrations. Mater. Trans. 50, 1290–1293. doi:10.2320/matertrans.me200809
Guo, Y., Bataev, I., Georgarakis, K., Jorge, A. M., Nogueira, R. P., Pons, M., et al. (2015). Ni- and Cu-free Ti-Based Metallic Glasses with Potential Biomedical Application. Intermetallics 63, 86–96. doi:10.1016/j.intermet.2015.04.004
Hao, G. J., Zhang, Y., Lin, J. P., Wang, Y. L., Lin, Z., and Chen, G. L. (2006). Bulk Metallic Glass Formation of Ti-Based Alloys from Low Purity Elements. Mater. Lett. 60, 1256–1260. doi:10.1016/j.matlet.2005.11.011
Hao, G., Ren, F., Zhang, Y., and Lin, J. (2009). Role of Yttrium in Glass Formation of Ti-Based Bulk Metallic Glasses. Rare Met. 28, 68–71. doi:10.1007/s12598-009-0013-7
He, G., Eckert, J., and Hagiwara, M. (2004). Glass-forming Ability and Crystallization Behavior of Ti-Cu-Ni-Sn-M (M=Zr, Mo, and Ta) Metallic Glasses. J. Appl. Phys. 95, 1816–1821. doi:10.1063/1.1643776
He, G., Eckert, J., and Hagiwara, M. (2006). Mechanical Properties and Fracture Behavior of the Modified Ti-Base Bulk Metallic Glass-Forming Alloys. Mater. Lett. 60, 656–661. doi:10.1016/j.matlet.2005.09.054
He, G., Eckert, J., and Löser, W. (2003). Stability, Phase Transformation and Deformation Behavior of Ti-Base Metallic Glass and Composites. Acta Materialia 51, 1621–1631. doi:10.1016/s1359-6454(02)00563-3
He, G., Löser, W., and Eckert, J. (2004). Devitrification and Phase Transformation of (Ti0.5Cu0.25Ni0.15Sn0.05Zr0.05)100−xMox Metallic Glasses. Scripta Materialia 50, 7–11. doi:10.1016/j.scriptamat.2003.09.049
Hu, Q., Zhang, M., Li, H., Yin, E., Pang, S., and Zhang, T. (2014) Formation, Bio-Corrosion Behavior and Mechanical Properties of Ti-Zr-Cu-Co-Sn-Si Bulk Metallic Glasses. J. Mater. Eng., 18–21. doi:10.11868/j.issn.1001-4381.2014.06.004
Huang, C. H., Huang, Y. S., Lin, Y. S., Lin, C. H., Huang, J. C., Chen, C. H., et al. (2014). Electrochemical and Biocompatibility Response of Newly Developed TiZr-Based Metallic Glasses. Mater. Sci. Eng. C 43, 343–349. doi:10.1016/j.msec.2014.06.040
Huang, C. H., Lai, J. J., Huang, J. C., Lin, C. H., and Jang, J. S. C. (2016). Effects of Cu Content on Electrochemical Response in Ti-Based Metallic Glasses under Simulated Body Fluid. Mater. Sci. Eng. C 62, 368–376. doi:10.1016/j.msec.2016.01.080
Huang, Y. J., Shen, J., Sun, J. F., and Yu, X. B. (2007). A New Ti-Zr-Hf-Cu-Ni-Si-Sn Bulk Amorphous alloy with High Glass-Forming Ability. J. Alloys Comp. 427, 171–175. doi:10.1016/j.jallcom.2006.03.006
Inoue, A., Kimura, H. M., Masumoto, T., Suryanarayana, C., and Hoshi, A. (1980). Superconductivity of Ductile Ti-Nb-Si Amorphous Alloys. J. Appl. Phys. 51, 5475–5482. doi:10.1063/1.327506
Inoue, A., Masumoto, T., Suryanarayana, C., and Hoshi, A. (1980). Superconductivity of Ductile Titanium-Niobium-Based Amorphous Alloys. J. Phys. Colloques 41, C8–758C758761. doi:10.1051/jphyscol:19808189
Inoue, A., Nishiyama, N., Amiya, K., Zhang, T., and Masumoto, T. (1994). Ti-based Amorphous Alloys with a Wide Supercooled Liquid Region. Mater. Lett. 19, 131–135. doi:10.1016/0167-577x(94)90057-4
Inoue, A. (2000). Stabilization of Metallic Supercooled Liquid and Bulk Amorphous Alloys. Acta Materialia 48, 279–306. doi:10.1016/s1359-6454(99)00300-6
Inoue, A., Takahashi, Y., Suryanarayana, C., Hoshi, A., and Masumoto, T. (1981). Crystallization-induced Superconductivity in Amorphous Ti-Ta-Si Alloys. J. Mater. Sci. 16, 3077–3086. doi:10.1007/bf00540315
Jia, H., Xie, X., Zhao, L., Wang, J., Gao, Y., Dahmen, K. A., et al. (2018). Effects of Similar-Element-Substitution on the Glass-Forming Ability and Mechanical Behaviors of Ti-Cu-Zr-Pd Bulk Metallic Glasses. J. Mater. Res. Tech. 7, 261–269. doi:10.1016/j.jmrt.2017.08.009
Jiang, J.-Z., Hofmann, D., Jarvis, D. J., and Fecht, H.-J. (2015). Low-Density High-Strength Bulk Metallic Glasses and Their Composites: A Review. Adv. Eng. Mater. 17, 761–780. doi:10.1002/adem.201400252
Jiang, Q. K., Zhang, G. Q., Yang, L., Wang, X. D., Saksl, K., Franz, H., et al. (2007). La-based Bulk Metallic Glasses with Critical Diameter up to 30mm. Acta Materialia 55, 4409–4418. doi:10.1016/j.actamat.2007.04.021
Kim, Y.-C., Kim, W. n. T., Kim, D.-H., and Kim, D.-H. (2002). Glass Forming Ability and Crystallization Behavior in Amorphous Ti50Cu32-xNi15Sn3Bex (X=0, 1, 3, 7) Alloys. Mater. Trans. 43, 1243–1246. doi:10.2320/matertrans.43.1243
Kim, Y.-C., Yi, S. H., Kim, W. T., and Kim, D. H. (2001). Glass Forming Ability and Crystallization Behaviors of the Ti-Cu-Ni-(Sn) Alloys with Large Supercooled Liquid Region. Msf 360-362, 67–72. doi:10.4028/www.scientific.net/msf.360-362.67
Kim, Y. C., Bae, D. H., Kim, W. T., and Kim, D. H. (2003). Glass Forming Ability and Crystallization Behavior of Ti-Based Amorphous Alloys with High Specific Strength. J. Non-Crystalline Sol. 325, 242–250. doi:10.1016/s0022-3093(03)00327-2
Kim, Y. C., Chang, H. J., Kim, D. H., Kim, W. T., and Cha, P. R. (2007). Unusual Glass-Forming Ability Induced by Changes in the Local Atomic Structure in Ti-Based Bulk Metallic Glass. J. Phys. Condens. Matter 19, 196104. doi:10.1088/0953-8984/19/19/196104
Kim, Y. C., Kim, W. T., and Kim, D. H. (2004). A Development of Ti-Based Bulk Metallic Glass. Mater. Sci. Eng. A 375-377, 127–135. doi:10.1016/j.msea.2003.10.115
Kuball, A., Gross, O., Bochtler, B., Adam, B., Ruschel, L., Zamanzade, M., et al. (2019). Development and Characterization of Titanium-Based Bulk Metallic Glasses. J. Alloys Comp. 790, 337–346. doi:10.1016/j.jallcom.2019.03.001
Kuball, A., Gross, O., Bochtler, B., and Busch, R. (2018). Sulfur-bearing Metallic Glasses: A New Family of Bulk Glass-Forming Alloys. Scripta Materialia 146, 73–76. doi:10.1016/j.scriptamat.2017.11.011
Laws, K. J., Shamlaye, K. F., and Ferry, M. (2012). Synthesis of Ag-Based Bulk Metallic Glass in the Ag-Mg-Ca-[Cu] alloy System. J. Alloys Comp. 513, 10–13. doi:10.1016/j.jallcom.2011.10.097
Li, H. F., and Zheng, Y. F. (2016). Recent Advances in Bulk Metallic Glasses for Biomedical Applications. Acta Biomater. 36, 1–20. doi:10.1016/j.actbio.2016.03.047
Li, H., Li, Z., Yang, J., Ke, H. B., Sun, B., Yuan, C. C., et al. (2021). Interface Design Enabled Manufacture of Giant Metallic Glasses. Sci. China Mater. 64, 964–972. doi:10.1007/s40843-020-1561-x
Li, L., Liu, R., Zhao, J., Cai, H., and Yang, Z. (2014). Effects of Nb Addition on Glass-Forming Ability, Thermal Stability and Mechanical Properties of Ti-Based Bulk Metallic Glasses. Rare Metal Mater. Eng. 43, 1835–1838. doi:10.1016/s1875-5372(14)60141-7
Li, M.-X., Sun, Y.-T., Wang, C., Hu, L.-W., Sohn, S., Schroers, J., et al. (2021). Data-Driven Discovery of a Universal Indicator for Metallic Glass Forming Ability. Nat. Mater. doi:10.1038/s41563-021-01129-6
Lin, S., Liu, D., Zhu, Z., Li, D., Fu, H., Zhuang, Y., et al. (2018). New Ti-Based Bulk Metallic Glasses with Exceptional Glass Forming Ability. J. Non-Crystalline Sol. 502, 71–75. doi:10.1016/j.jnoncrysol.2018.06.038
Liu, X., Li, X., He, Q., Liang, D., Zhou, Z., Ma, J., et al. (2020). Machine Learning-Based Glass Formation Prediction in Multicomponent Alloys. Acta Materialia 201, 182–190. doi:10.1016/j.actamat.2020.09.081
Liu, Y., Pang, S., Li, H., Hu, Q., Chen, B., and Zhang, T. (2016). Formation and Properties of Ti-Based Ti-Zr-Cu-Fe-Sn-Si Bulk Metallic Glasses with Different (Ti + Zr)/Cu Ratios for Biomedical Application. Intermetallics 72, 36–43. doi:10.1016/j.intermet.2016.01.007
Liu, Y., Wang, G., Li, H., Pang, S., Chen, K., and Zhang, T. (2016). Ti Cu Zr Fe Sn Si Sc Bulk Metallic Glasses with Good Mechanical Properties for Biomedical Applications. J. Alloys Comp. 679, 341–349. doi:10.1016/j.jallcom.2016.03.224
Liu, Y., Wang, H.-J., Pang, S.-J., and Zhang, T. (2020). Ti-Zr-Cu-Fe-Sn-Si-Ag-Ta Bulk Metallic Glasses with Good Corrosion Resistance as Potential Biomaterials. Rare Met. 39, 688–694. doi:10.1007/s12598-018-1124-9
Long, M., and Rack, H. J. (1998). Titanium Alloys in Total Joint Replacement-A Materials Science Perspective. Biomaterials 19, 1621–1639. doi:10.1016/s0142-9612(97)00146-4
Lou, H. B., Wang, X. D., Xu, F., Ding, S. Q., Cao, Q. P., Hono, K., et al. (2011). 73 Mm-Diameter Bulk Metallic Glass Rod by Copper Mould Casting. Appl. Phys. Lett. 99, 051910. doi:10.1063/1.3621862
Lu, B.-c., Li, Y., and Xu, J. (2009). Optimal Glass-Forming Composition and its Correlation with Eutectic Reaction in the Ti-Ni-Al Ternary System. J. Alloys Comp. 467, 261–267. doi:10.1016/j.jallcom.2007.12.050
Lu, B.-C., Wang, Y.-L., and Xu, J. (2009). Revisiting the Glass-Forming Ability of Ti-Ni-Si Ternary Alloys. J. Alloys Comp. 475, 157–164. doi:10.1016/j.jallcom.2008.07.055
Lu, B.-c., and Xu, J. (2008). Glass Formation of Ti-Ni-Sn Ternary Alloys Correlated with TiNi-Ti3Sn Pseudo Binary Eutectics. J. Non-Crystalline Sol. 354, 5425–5431. doi:10.1016/j.jnoncrysol.2008.09.016
Ma, C., Ishihara, S., Soejima, H., Nishiyama, N., and Inoue, A. (2004). Formation of New Ti-Based Metallic Glassy Alloys. Mater. Trans. 45, 1802–1806. doi:10.2320/matertrans.45.1802
Ma, C., Soejima, H., Ishihara, S., Amiya, K., Nishiyama, N., and Inoue, A. (2004). New Ti-Based Bulk Glassy Alloys with High Glass-Forming Ability and Superior Mechanical Properties. Mater. Trans. 45, 3223–3227. doi:10.2320/matertrans.45.3223
Ma, J., Yang, C., Liu, X., Shang, B., He, Q., Li, F., et al. (2019). Sci. Adv. 5, eaax7256. doi:10.1126/sciadv.aax7256
Maeland, A. J. (1978). “Comparison of Hydrogen Absorption in Glassy and Crystalline Structures,” in Hydrides for Energy Storage. Editors A. F. Andresen, and A. J. Maeland (Pergamon), 447–462. doi:10.1016/b978-0-08-022715-3.50040-0
Mei, J., Li, J., Kou, H., Hu, R., Fu, H., and Zhou, L. (2007). Effects of Ta Addition on the Microstructure and Mechanical Properties of Ti40Zr25Ni8Cu9Be18 Amorphous alloy. J. Univ. Sci. Tech. Beijing Mineral, Metall. Mater. 14, 31–35. doi:10.1016/s1005-8850(07)60103-0
Men, H., Pang, S., Inoue, A., and Zhang, T. (2005). New Ti-Based Bulk Metallic Glasses with Significant Plasticity. Mater. Trans. 46, 2218–2220. doi:10.2320/matertrans.46.2218
Nicoara, M., Buzdugan, D., Locovei, C., Bena, T., and Stoica, M. (2018). About Thermostability of Biocompatible Ti-Zr-Ag-Pd-Sn Amorphous Alloys. J. Therm. Anal. Calorim. 133, 189–197. doi:10.1007/s10973-018-7031-3
Nishiyama, N., Takenaka, K., Miura, H., Saidoh, N., Zeng, Y., and Inoue, A. (2012). The World's Biggest Glassy alloy Ever Made. Intermetallics 30, 19–24. doi:10.1016/j.intermet.2012.03.020
Oak, J.-J., and Inoue, A. (2007). Attempt to Develop Ti-Based Amorphous Alloys for Biomaterials. Mater. Sci. Eng. A 449-451, 220–224. doi:10.1016/j.msea.2006.02.307
Oak, J.-J., and Inoue, A. (2008). Formation, Mechanical Properties and Corrosion Resistance of Ti-Pd Base Glassy Alloys. J. Non-Crystalline Sol. 354, 1828–1832. doi:10.1016/j.jnoncrysol.2007.10.025
Oak, J.-J., Louzguine-Luzgin, D. V., and Inoue, A. (2011). Fabrication of Ni-free Ti-Based Bulk-Metallic Glassy alloy Having Potential for Application as Biomaterial, and Investigation of its Mechanical Properties, Corrosion, and Crystallization Behavior. J. Mater. Res. 22, 1346–1353. doi:10.1557/jmr.2007.0154
Oak, J.-J., Louzguine-Luzgin, D. V., and Inoue, A. (2009). Investigation of Glass-Forming Ability, Deformation and Corrosion Behavior of Ni-free Ti-Based BMG Alloys Designed for Application as Dental Implants. Mater. Sci. Eng. C 29, 322–327. doi:10.1016/j.msec.2008.07.009
Oak, J. J., Kim, Y. H., Bae, K. C., and Park, Y. H. (2017). Effect of Hafnium and Zirconium to Glass Forming Ability, Thermal Stability, Plasticity Deformation and Crystallization of Ni-free Pentabasic Ti-Based Bulk Metallic Glasses. Arch. Metall. Mater. 62, 1081–1087. doi:10.1515/amm-2017-0158
Ouyang, D., Zhang, P. C., Zhang, C., and Liu, L. (2021), Understanding of crystallization behaviors in laser 3D printing of bulk metallic glasses. Appl. Mater. Today 23, 100988. doi:10.1016/j.apmt.2021.100988
Pang, S., Liu, Y., Li, H., Sun, L., Li, Y., and Zhang, T. (2015). New Ti-Based Ti-Cu-Zr-Fe-Sn-Si-Ag Bulk Metallic Glass for Biomedical Applications. J. Alloys Comp. 625, 323–327. doi:10.1016/j.jallcom.2014.07.021
Park, E. S., and Kim, D. H. (2004). Formation of Ca-Mg-Zn Bulk Glassy alloy by Casting into Cone-Shaped Copper Mold. J. Mater. Res. 19, 685–688. doi:10.1557/jmr.2004.19.3.685
Park, J. M., Kim, Y. C., Kim, W. T., and Kim, D. H. (2004). Ti-Based Bulk Metallic Glasses with High Specific Strength. Mater. Trans. 45, 595–598. doi:10.2320/matertrans.45.595
Peker, A., and Johnson, W. L. (1993). A Highly Processable Metallic Glass: Zr41.2Ti13.8Cu12.5Ni10.0Be22.5. Appl. Phys. Lett. 63, 2342–2344. doi:10.1063/1.110520
Polk, D. E., Calka, A., and Giessen, B. C. (1978). The Preparation and thermal and Mechanical Properties of New Titanium Rich Metallic Glasses. Acta Metallurgica 26, 1097–1103. doi:10.1016/0001-6160(78)90137-2
Qin, F.-X., Zhou, Y., Ji, C., Dan, Z.-H., Xie, G.-Q., and Yang, S. (2016). Enhanced Mechanical Properties, Corrosion Behavior and Bioactivity of Ti-Based Bulk Metallic Glasses with Minor Addition Elements. Acta Metall. Sin. (Engl. Lett. 29, 1011–1018. doi:10.1007/s40195-016-0468-0
Qin, F. X., Wang, X. M., Xie, G. Q., and Inoue, A. (2008). Distinct Plastic Strain of Ni-free Ti-Zr-Cu-Pd-Nb Bulk Metallic Glasses with Potential for Biomedical Applications. Intermetallics 16, 1026–1030. doi:10.1016/j.intermet.2008.05.004
Rabinkin, A., Liebermann, H., Pounds, S., Taylor, T., Reidinger, F., and Lui, S.-C. (1991). Amorphous TiZr - Base Metglas Brazing Filler Metals. Scripta Metallurgica et Materialia 25, 399–404. doi:10.1016/0956-716x(91)90200-k
Rodmacq, B., Lançon, F., Chamberod, A., and Maret, M. (1988). Large-angle Neutron Scattering Studies of Amorphous FexTi1−x Alloys and Hydrides. Mater. Sci. Eng. 97, 157–161. doi:10.1016/0025-5416(88)90032-8
Saini, J. S., Miska, J. P., Lei, F., AuYeung, N., and Xu, D. (2021). Hafnium Based Metallic Glasses with High Density and High Glass-Forming Ability. J. Alloys Comp. 882, 160896. doi:10.1016/j.jallcom.2021.160896
Saini, J. S., Palian, C., Lei, F., Dyall, A., AuYeung, N., McQuade, R., et al. (2020). Rare-earth and Precious-Metal Free Cu-Based Metallic Glasses with superior Glass-Forming Ability and Processability. Appl. Phys. Lett. 116, 011901. doi:10.1063/1.5131645
Schroers, J., and Johnson, W. L. (2004). Highly Processable Bulk Metallic Glass-Forming Alloys in the Pt-Co-Ni-Cu-P System. Appl. Phys. Lett. 84, 3666–3668. doi:10.1063/1.1738945
Seki, I., Kimura, H., and Inoue, A. (2008). Thermal Stability and Mechanical Properties of Ti47.4Cu42Zr5.3TM5.3(TM = Co, Fe) Metallic Glass Sheets Prepared by Twin-Roller Casting Method. Mater. Trans. 49, 498–501. doi:10.2320/matertrans.mbw200738
Shan, S.-F., Zhan, Z.-J., Fan, C.-Z., Jia, Y.-Z., Zhang, B.-Q., Liu, R.-P., et al. (2008). Chin. Phys. Lett. 25, 4165–4167.
Shao, L., Xue, L., Luo, Q., Wang, Q., and Shen, B. (2019). The Role of Co/Al Ratio in Glass-Forming GdCoAl Magnetocaloric Metallic Glasses. Materialia 7, 100419. doi:10.1016/j.mtla.2019.100419
Shirasawa, N., Ito, R., Takigawa, Y., Uesugi, T., and Higashi, K. (2014). Prediction and Fabrication of Ti-Zr-Co Ternary Metallic Glasses Based on Effective Atomic Radius in Ti Solid Solution from First-Principles Calculations. J. Non-Crystalline Sol. 400, 67–71. doi:10.1016/j.jnoncrysol.2014.05.005
Song, X., Liu, X., Yang, Y., Feng, S., Lu, Y., and Kong, J. (2019). Glass Forming Ability and a Novel Method for Evaluating the Thermoplastic Formability of Zr Ti65-Be27.5Cu7.5 Alloys. Intermetallics 114, 106600. doi:10.1016/j.intermet.2019.106600
Sun, Y. F., Wang, Y. R., Wei, B. C., Li, W. H., and Shek, C. H. (2005). Effect of Quasicrystalline Phase on the Deformation Behavior of Zr62Al9.5Ni9.5Cu14Nb5 Bulk Metallic Glass. Trans. Nonferrous Met. Soc. China 15, 727–732. doi:10.1016/j.msea.2005.01.040
Sun, Y. T., Bai, H. Y., Li, M. Z., and Wang, W. H. (2017). Machine Learning Approach for Prediction and Understanding of Glass-Forming Ability. J. Phys. Chem. Lett. 8, 3434–3439. doi:10.1021/acs.jpclett.7b01046
Suryanarayana, C., and Inoue, A. (2013). Iron-based Bulk Metallic Glasses. Int. Mater. Rev. 58, 131–166. doi:10.1179/1743280412y.0000000007
Suryanarayana, C., Inoue, A., and Masumoto, T. (1980). Transformation Studies and Mechanical Properties of Melt-Quenched Amorphous Titanium-Silicon Alloys. J. Mater. Sci. 15, 1993–2000. doi:10.1007/bf00550625
Šušić, M. V., Budberg, P. B., and Alisova, S. P. (1986). Kinetics of thermal Devitrification (Crystallization) of a Titanium Amorphous alloy. Mater. Chem. Phys. 15, 1297–1300. doi:10.1007/bf00553266
Tanaka, K., Shibagaki, N., and Yamauchi, T. (1988). Electronic Structure and Local Environment of Non-transition Elements in Ternary Metallic Glasses. Mater. Sci. Eng. 99, 269–271. doi:10.1016/0025-5416(88)90337-0
Tang, M. Q., Zhang, H. F., Zhu, Z. W., Fu, H. M., Wang, A. M., Li, H., et al. (2010). TiZr-base Bulk Metallic Glass with over 50 Mm in Diameter. J. Mater. Sci. Tech. 26, 481–486. doi:10.1016/s1005-0302(10)60077-1
Tanner, L. E., Jacobson, L. A., and Wall, M. E. (1988). Formation and Crystallization of Amorphous Phases in the TiBeAl System. Mater. Sci. Eng. 97, 379–383. doi:10.1016/0025-5416(88)90078-x
Tanner, L. E. (1978). Physical Properties of TiBeSi Glass Ribbons. Scripta Metallurgica 12, 703–708. doi:10.1016/0036-9748(78)90312-5
Tanner, L. E., and Ray, R. (1979). Metallic Glass Formation and Properties in Zr and Ti Alloyed with Be-I the Binary Zr-Be and Ti-Be Systems. Acta Metallurgica 27, 1727–1747. doi:10.1016/0001-6160(79)90087-7
Tanner, L. E., and Ray, R. (1980). Phase Separation in ZrTiBe Metallic Glasses. Scripta Metallurgica 14, 657–662. doi:10.1016/0036-9748(80)90018-6
Tanner, L. E., and Ray, R. (1977). Physical Properties of Ti50Be40Zr10 Glass. Scripta Metallurgica 11, 783–789. doi:10.1016/0036-9748(77)90076-x
Tantavisut, S., Lohwongwatana, B., Khamkongkaeo, A., Tanavalee, A., Tangpornprasert, P., and Ittiravivong, P. (2018). The Novel Toxic Free Titanium-Based Amorphous alloy for Biomedical Application. J. Mater. Res. Tech. 7, 248–253. doi:10.1016/j.jmrt.2017.08.007
Tarasova, O. B., Smirnov, L. S., and Fykin, L. E. (1992). A Study of Short-Range Order in Amorphous Ti-Zr-Si Alloys. Phys. met. Metallogr 73, 177–180.
Thanka Rajan, S., Bendavid, A., and Subramanian, B. (2019). Cytocompatibility Assessment of Ti-Nb-Zr-Si Thin Film Metallic Glasses with Enhanced Osteoblast Differentiation for Biomedical Applications. Colloids Surf. B: Biointerfaces 173, 109–120. doi:10.1016/j.colsurfb.2018.09.041
Tsai, P. H., Hsu, K. T., Ke, J. H., Lin, H. C., Jang, J. S. C., and Huang, J. C. (2015). Mater. Tech. 30, A161–A165. doi:10.1179/17535557a15y.000000003
Wang, C., Hua, N., Liao, Z., Yang, W., Pang, S., Liaw, P. K., et al. (2021). Ti-Cu-Zr-Fe-Sn-Si-Ag-Pd Bulk Metallic Glasses with Potential for Biomedical Applications. Metall. Mater. Trans. A. 52, 1559–1567. doi:10.1007/s11661-021-06183-y
Wang, H., Park, E. S., Oak, J. J., Setyawan, A. D., Zhu, S. L., Wada, T., et al. (2013). Effect of Cobalt Microalloying on the Glass Forming Ability of Ti-Cu-Pd-Zr Metallic Glass. J. Non-Crystalline Sol. 379, 155–160. doi:10.1016/j.jnoncrysol.2013.08.001
Wang, T., Wu, Y. D., Si, J. J., Cai, Y. H., Chen, X. H., and Hui, X. D. (2015). Novel Ti-Based Bulk Metallic Glasses with superior Plastic Yielding Strength and Corrosion Resistance. Mater. Sci. Eng. A 642, 297–303. doi:10.1016/j.msea.2015.05.060
Wang, T., Wu, Y., Si, J., and Hui, X. (2015). Effects of Zr and Si on the Glass Forming Ability and Compressive Properties of Ti-Cu-Co-Sn Alloys. Metall. Mat Trans. A. 46, 2381–2389. doi:10.1007/s11661-014-2484-x
Wang, W. H. (2009). Bulk Metallic Glasses with Functional Physical Properties. Adv. Mater. 21, 4524–4544. doi:10.1002/adma.200901053
Wang, W. H., Dong, C., and Shek, C. H. (2004). Bulk Metallic Glasses. Mater. Sci. Eng. R: Rep. 44, 45–89. doi:10.1016/j.mser.2004.03.001
Wang, Y.-L., and Xu, J. (2008). Ti (Zr)-Cu-Ni Bulk Metallic Glasses with Optimal Glass-Forming Ability and Their Compressive Properties. Metall. Mat Trans. A. 39, 2990–2997. doi:10.1007/s11661-008-9647-6
Wang, Z., Dong, D., Qiang, J., Wang, Q., Wang, Y., and Dong, C. (2013). Ti-based Glassy Alloys in Ti-Cu-Zr-Sn System. Sci. China Phys. Mech. Astron. 56, 1419–1422. doi:10.1007/s11433-013-5104-7
Wang, Z. R., Qiang, J. B., Wang, Y. M., Wang, Q., Dong, D. D., and Dong, C. (2016). Composition Design Procedures of Ti-Based Bulk Metallic Glasses Using the Cluster-Plus-Glue-Atom Model. Acta Materialia 111, 366–376. doi:10.1016/j.actamat.2016.03.072
Whang, S. H., Lu, Y. Z., and Kim, Y. W. (1985). Microstructures and Age Hardening of Rapidly Quenched Ti-Zr-Si Alloys. J. Mater. Sci. Lett. 4, 883–887. doi:10.1007/bf00720529
Wu, X. Q., Wang, H. L., and Lin, J. G. (2014). Effects of Sn Content on thermal Stability and Mechanical Properties of the Ti60Zr10Ta15Si15 Amorphous alloy for Biomedical Use. Mater. Des. 63, 345–348. doi:10.1016/j.matdes.2014.06.045
Wu, X., Zhou, Y., Chen, F., and Qin, F. (2019). Effect of Nb Addition on Corrosion Behavior and Mechanical Properties of Ti-Based Metallic Glasses. Mater. Sci. Tech. 27, 73–80. doi:10.11951/j.issn.1005-0299.20180094
Xia, M.-x., Zheng, H.-x., Liu, J., Ma, C.-l., and Li, J.-g. (2005). Thermal Stability and Glass-Forming Ability of New Ti-Based Bulk Metallic Glasses. J. Non-Crystalline Sol. 351, 3747–3751. doi:10.1016/j.jnoncrysol.2005.09.033
Xia, M. X., Ma, C. L., Zheng, H. X., and Li, J. G. (2005). Preparation and Crystallization of Ti53Cu27Ni12Zr3Al7Si3B1 Bulk Metallic Glass with Wide Supercooled Liquid Region. Mater. Sci. Eng. A 390, 372–375. doi:10.1016/j.msea.2004.08.019
Xia, M. X., Zheng, H. X., Ma, C. L., and Li, J. G. (2005). Formation and Thermal Properties of Ti-Based Bulk Amorphous Alloy. Rare Metal Mater. Eng. 34, 1235–1238.
Xia, M. X., Zheng, H. X., Ma, C. L., and Li, J. G. (2005). Preparation and Properties of High Strength Bulk Metallic Glass Ti53Cu15Ni18.5Al7M3Si3B0.5 (M = Zr, Hf, Sc). Acta Metall. Sin. 41, 199–202.
Xie, K.-F., Yao, K.-F., and Huang, T.-Y. (2010). A Ti-Based Bulk Glassy alloy with High Strength and Good Glass Forming Ability. Intermetallics 18, 1837–1841. doi:10.1016/j.intermet.2010.02.036
Xie, K. F., Yao, K. F., and Huang, T. Y. (2010). Preparation of (Ti0.45Cu0.378Zr0.10Ni0.072)100−xSnx Bulk Metallic Glasses. J. Alloys Comp. 504, S22–S26. doi:10.1016/j.jallcom.2010.02.199
Xiong, J., Shi, S.-Q., and Zhang, T.-Y. (2021). Machine Learning Prediction of Glass-Forming Ability in Bulk Metallic Glasses. Comput. Mater. Sci. 192, 110362. doi:10.1016/j.commatsci.2021.110362
Xu, T., Pang, S., Li, H., and Zhang, T. (2015). Corrosion Resistant Cr-Based Bulk Metallic Glasses with High Strength and Hardness. J. Non-Crystalline Sol. 410, 20–25. doi:10.1016/j.jnoncrysol.2014.12.006
Yan, H.-M., Liu, Y., Pang, S.-J., and Zhang, T. (2018). Glass Formation and Properties of Ti-Based Bulk Metallic Glasses as Potential Biomaterials with Nb Additions. Rare Met. 37, 831–837. doi:10.1007/s12598-015-0664-5
Yang, B. J., Lu, W. Y., Zhang, J. L., Wang, J. Q., and Ma, E. (2017). Melt Fluxing to Elevate the Forming Ability of Al-Based Bulk Metallic Glasses. Sci. Rep. 7, 11053. doi:10.1038/s41598-017-11504-6
Yang, S., Li, D., Li, X. C., Zhang, Z. Z., Zhang, S. F., and He, L. (2017). Composition Dependence of the Microstructure and Mechanical Behavior of Ti-Zr-Cu-Pd-Sn-Nb Bulk Metallic Glass Composites. Intermetallics 90, 1–8. doi:10.1016/j.intermet.2017.06.006
Yang, W., Liu, Y., Hua, N., Pang, S., Li, Y., Liaw, P. K., et al. (2021). Formation and Properties of Biocompatible Ti-Based Bulk Metallic Glasses in the Ti-Cu-Zr-Fe-Sn-Si-Ag System. J. Non-Crystalline Sol. 571, 121060. doi:10.1016/j.jnoncrysol.2021.121060
Yi Qun Gao, G., and Whang, S. H. (1985). Crystallization Behavior of Binary Metallic Glasses Containing Pt. J. Non-Crystalline Sol. 70, 85–92. doi:10.1016/0022-3093(85)90095-x
Yin, E., Pang, S., Hui, X., Zhang, M., Zhuo, L., Chen, C., et al. (2013). Correlation of Glass-Forming Ability to thermal Properties in Ti-Based Bulk Metallic Glasses. J. Alloys Comp. 546, 7–13. doi:10.1016/j.jallcom.2012.07.037
Zeng, Y. Q., Yu, J. S., Tian, Y., Hirata, A., Fujita, T., Zhang, X. H., et al. (2020). Improving Glass Forming Ability of Off-Eutectic Metallic Glass Formers by Manipulating Primary Crystallization Reactions. Acta Materialia 200, 710–719. doi:10.1016/j.actamat.2020.09.042
Zhang, C., Ouyang, D., Pauly, S., and Liu, L. (2021). 3D Printing of Bulk Metallic Glasses. Mater. Sci. Eng. R: Rep. 145, 100625. doi:10.1016/j.mser.2021.100625
Zhang, L.-C., Jia, Z., Lyu, F., Liang, S.-X., and Lu, J. (2019). A Review of Catalytic Performance of Metallic Glasses in Wastewater Treatment: Recent Progress and Prospects. Prog. Mater. Sci. 105, 100576. doi:10.1016/j.pmatsci.2019.100576
Zhang, L., Tang, M. Q., Zhu, Z. W., Fu, H. M., Zhang, H. W., Wang, A. M., et al. (2015). Compressive Plastic Metallic Glasses with Exceptional Glass Forming Ability in the Ti-Zr-Cu-Fe-Be alloy System. J. Alloys Comp. 638, 349–355. doi:10.1016/j.jallcom.2015.03.120
Zhang, T., Inoue, A., and Masumoto, T. (1994). Amorphous (Ti,Zr, Hf)NiCu Ternary Alloys with a Wide Supercooled Liquid Region. Mater. Sci. Eng. A 181-182, 1423–1426. doi:10.1016/0921-5093(94)90877-x
Zhang, T., Inoue, A., and Masumoto, T. (1993). The Effect of Atomic Size on the Stability of Supercooled Liquid for Amorphous (Ti, Zr, Hf)65Ni25Al10 and (Ti, Zr, Hf)65Cu25Al10 Alloys. Mater. Lett. 15, 379–382. doi:10.1016/0167-577x(93)90100-c
Zhang, T., and Inoue, A. (1999). Preparation of Ti–Cu–Ni–Si–B Amorphous Alloys with a Large Supercooled Liquid Region. Mater. Trans. JIM 40, 301–306. doi:10.2320/matertrans1989.40.301
Zhang, T., and Inoue, A. (1998). Thermal and Mechanical Properties of Ti–Ni–Cu–Sn Amorphous Alloys with a Wide Supercooled Liquid Region before Crystallization. Mater. Trans. JIM 39, 1001–1006. doi:10.2320/matertrans1989.39.1001
Zhang, T., and Inoue, A. (2001). Ti-based Amorphous Alloys with a Large Supercooled Liquid Region. Mater. Sci. Eng. A 304-306, 771–774. doi:10.1016/s0921-5093(00)01592-6
Zhang, T., Yang, Q., Ji, Y., Li, R., Pang, S., Wang, J., et al. (2011). Centimeter-scale-diameter Co-based Bulk Metallic Glasses with Fracture Strength Exceeding 5000 MPa. Chin. Sci. Bull. 56, 3972–3977. doi:10.1007/s11434-011-4765-8
Zhao, L., Zhang, Z., Zhang, J., Pang, S., Ma, C., and Zhang, T. (2010). Composition Design and Glass-Forming Ability of Ti-Based Bulk Metallic Glasses. Int. J. Mod. Phys. B 24, 2326–2331. doi:10.1142/s0217979210064873
Zhao, S., Chen, N., Gong, P., and Yao, K. (2016). Centimeter-Sized Quaternary Ti-Based Bulk Metallic Glasses with High Ti Content of 50 at%. Adv. Eng. Mater. 18, 231–235. doi:10.1002/adem.201500165
Zhao, S. F., Chen, N., Gong, P., and Yao, K. F. (2015). New Centimeter-Sized Quaternary Ti-Zr-Be-Cu Bulk Metallic Glasses with Large Glass Forming Ability. J. Alloys Comp. 647, 533–538. doi:10.1016/j.jallcom.2015.05.214
Zhao, S. F., Gong, P., Li, J. F., Chen, N., and Yao, K. F. (2015). Quaternary Ti-Zr-Be-Ni Bulk Metallic Glasses with Large Glass-Forming Ability. Mater. Des. 85, 564–573. doi:10.1016/j.matdes.2015.07.032
Zhao, S. F., Shao, Y., Gong, P., and Yao, K. F. (2014). A Centimeter-Sized Quaternary Ti-Zr-Be-Ag Bulk Metallic Glass. Adv. Mater. Sci. Eng. 2014, 15. doi:10.1155/2014/192187
Zheng, Q., Xu, J., and Ma, E. (2007). High Glass-Forming Ability Correlated with Fragility of Mg-Cu(Ag)-Gd Alloys. J. Appl. Phys. 102, 113519. doi:10.1063/1.2821755
Zhou, Y., Zhao, Y., Qu, B. Y., Wang, L., Zhou, R. L., Wu, Y. C., et al. (2015). Remarkable Effect of Ce Base Element Purity upon Glass Forming Ability in Ce-Ga-Cu Bulk Metallic Glasses. Intermetallics 56, 56–62. doi:10.1016/j.intermet.2014.09.003
Zhu, S. L., Wang, X. M., and Inoue, A. (2008). Glass-forming Ability and Mechanical Properties of Ti-Based Bulk Glassy Alloys with Large Diameters of up to 1cm. Intermetallics 16, 1031–1035. doi:10.1016/j.intermet.2008.05.006
Zhu, S. L., Wang, X. M., Qin, F. X., Yoshimura, M., and Inoue, A. (2007). New TiZrCuPd Quaternary Bulk Glassy Alloys with Potential of Biomedical Applications. Mater. Trans. 48, 2445–2448. doi:10.2320/matertrans.mra2007086
Zhu, S. L., Wang, X. M., Qin., F. X., and Inoue, A. (2007). A New Ti-Based Bulk Glassy alloy with Potential for Biomedical Application. Mater. Sci. Eng. A 459, 233–237. doi:10.1016/j.msea.2007.01.044
Zhu, S. L., Xie, G. Q., Qin, F. X., and Wang, X. M. (2012). 8th International Forum on Advanced Materials Science and Technology (IFAMST-8). Fukuoka City, JAPAN: Trans Tech Publications Ltd, Fukuoka Inst Technol, 36–39.
Keywords: Ti-based metallic glasses, glass forming ability, biomaterials, lightweight high-strength materials, composition design
Citation: Zhang M, Song Y, Lin H, Li Z and Li W (2022) A Brief Introduction on the Development of Ti-Based Metallic Glasses. Front. Mater. 8:814629. doi: 10.3389/fmats.2021.814629
Received: 14 November 2021; Accepted: 03 December 2021;
Published: 03 January 2022.
Edited by:
Limin Wang, Yanshan University, ChinaReviewed by:
Pan Gong, Huazhong University of Science and Technology, ChinaCopyright © 2022 Zhang, Song, Lin, Li and Li. This is an open-access article distributed under the terms of the Creative Commons Attribution License (CC BY). The use, distribution or reproduction in other forums is permitted, provided the original author(s) and the copyright owner(s) are credited and that the original publication in this journal is cited, in accordance with accepted academic practice. No use, distribution or reproduction is permitted which does not comply with these terms.
*Correspondence: M. Zhang, m.zhangiwrm@jnu.edu.cn; Z. Li, lizu2020@gzhu.edu.cn
Disclaimer: All claims expressed in this article are solely those of the authors and do not necessarily represent those of their affiliated organizations, or those of the publisher, the editors and the reviewers. Any product that may be evaluated in this article or claim that may be made by its manufacturer is not guaranteed or endorsed by the publisher.
Research integrity at Frontiers
Learn more about the work of our research integrity team to safeguard the quality of each article we publish.