- 1Department of Industrial Engineering, University of Salerno, Fisciano, Italy
- 2ProdAl Scarl – University of Salerno, Fisciano, Italy
With the rapid growth of today’s market, food processing industries are compelled to adopt advanced solutions to ensure product safety and quality, reduce costs amidst low-profit margins, guarantee timely delivery of an increased demand for product preferences, and enhance sustainability. To cope with these challenges, Digital Twin (DT) technology has emerged as a promising solution. Due to the relative novelty of this technology, research on its application within the food processing industry remains limited, necessitating additional studies to better understand its potential and multifaceted role from different perspectives. This review analyzes existing studies on DT applications in the food industry, discussing the concept, benefits, and challenges hindering its full adoption. On this basis, this study contributes to the existing body of knowledge on DT by identifying the state-of-the-art within the food processing industry and categorizing use cases from both industrial and academic contexts. Further, it explores the DT from a sustainability perspective, emphasizing its role in optimizing resource utilization for more efficient and sustainable food processing. Furthermore, the study examines its potential as a versatile tool to support sustainability initiatives within the industry. Lastly, it discusses the future impact of DT in shaping the evolution of food processing.
1 Introduction
The food processing industry is inherently complex and diverse, encompassing various food types, processing methods, preservation techniques, and distribution systems. This complexity gives rise to numerous challenges, including increased consumer demands, product diversification, and sustainability concerns (Karadeniz et al., 2019; Maheshwari et al., 2023; Ciano et al., 2021; Verboven et al., 2020; Wari and Zhu, 2019). Therefore, the industry is compelled to rethink approaches to enhance productivity, efficiency, quality, and sustainability, as well as meet consumer demands. Small and medium-sized food processing industries typically adopt a non-integrated approach to process optimization, dictated by their priorities, resources, and data availability (Klemeš et al., 2008). Further, many still rely on traditional process design methods driven by vendor management systems using unstructured data analysis and demand prediction (Maheshwari et al., 2023; Wari and Zhu, 2019). These traditional methods prioritize products over customers, emphasizing profit maximization rather than customer satisfaction by implementing short-term goal-seeking strategies rather than long-term comprehension (Leng et al., 2020; Marcello Braglia and Marrazzini, 2020). The food processing industry is characterized by high water and energy demand, contributing to significant waste generation and greenhouse gas emissions (Asgharnejad et al., 2021; Clairand et al., 2020; Garnett, 2013; Nikmaram and Rosentrater, 2019). According to the United Nations, globally about 12% of water resources are used for industrial use, with 56% of it being consumed by the food and beverage industry, and the global energy consumption of the food sector is about 200 EJ per year, with processing and distribution activities contributing to about 45% of this total (Eslami et al., 2023). In response to these challenges, current research explores innovative solutions such as the adoption of advanced technologies and digitalization (Clairand et al., 2020). Particularly, Digital Twin technology has emerged as a potential solution within the context of Industry 4.0 (Koulouris et al., 2021; Henrichs et al., 2022).
The concept of the Digital Twin (DT), or Digital Twins (DTs), was introduced by Grieves around 2002 in the context of Product Lifecycle Management (PLM). It was later adopted by NASA to describe the development of advanced, high-fidelity simulations for flight certification and testing (Udugama et al., 2021). In 2017, the advisory firm Gartner identified DT as one of the top 10 strategic technology trends, forecasting its widespread adoption among major industrial players (Melesse et al., 2020; Perno et al., 2022). Although DT has been defined in different ways by companies and researchers (Yu et al., 2022), a common definition is still lacking. Conceptually, DT is a living model that looks like, acts like and links-to a physical object or system that can continually be updated with incoming data from the operating environment to monitor the status and forecast future behaviors to improve or optimize decision-making for any time horizon (Melesse et al., 2020, 2021; Yu et al., 2022). DT can look like either a 1-D, 2-D, or 3-D representation of a physical object or a system. These models can either act like a single state (e.g., an average process system state), or discrete event – multiple steady states (e.g., multiple equilibrium process system states), or dynamic state (e.g., model predictive control), which directly or indirectly connect to a physical object or system. The connectivity of the DT (or level of integration) can be categorized based on the flow of data between the digital and physical layers (Bottani et al., 2020; Liu et al., 2021; Botín-Sanabria et al., 2022). For instance, when the digital layer is fully disconnected from the physical layer and no automated data exchange occurs, it is referred to as a digital model (DM). When the digital layer is partially connected, i.e., it only acquires data from sensors in the physical layer, it is termed a digital shadow (DS). Lastly, when there is full connectivity between the digital and physical layers, with data flowing bidirectionally via sensors, it is referred to as a DT (Liu et al., 2021). The unification of three features namely looks like, acts like and link-to, describes a paradigm shift in DT modeling, distinguishing DT from conventional representations that may capture only the appearance or behavior of a physical object or system without a strong linkage to the physical entity. While all three features are essential for optimal performance, the fidelity of each feature varies depending on the specific purpose and application of the DT (Yu et al., 2022).
DT can be classified based on application level, technique, and functionality (Figure 1). As far as application level is concerned, they may replicate individual units (resource-centric) (e.g., unit operation, equipment, product), the entire system (process-centric) (e.g., production line, packaging line), or a more complex system (hybrid-centric) (e.g., the shop-floor management system) (Park et al., 2020; Henrichs et al., 2022). Regarding techniques, DT models can be categorized as statistical (for process control, design, and product personalization), artificial intelligence (AI), or data-driven, (for monitoring, detection, calibration, verification, and validation), and physics-based (for Multiphysics modelling and simulation). The latter may incorporate mechanistic kinetics of biological and chemical processes. While mechanistic DTs are often capable of simulating the behavior of the real object realistically and comprehensively, the model parameters used in mechanistic DTs can be also quantified, verified, and validated with intelligent DTs using statistical methods and AI methods such as machine learning (ML). The technique is chosen considering the user’s needs and application complexity. In terms of DT functionality, each type of DT serves a specific purpose, including real-time monitoring, resource consumption analysis, system failure detection and prediction, process or product optimization, behavior analysis, technology integration, virtual testing, evaluation and validation, and virtual maintenance. These specific purposes, (Park et al., 2020), are grouped into four main technical functionalities.
1. Prognostic: DTs can be implemented to predict or forecast future states or behaviors of a process or system. It involves analyzing historical data, current conditions, and various factors to make informed predictions about future outcomes, forecasting the performance of unit operations, predicting insufficiency, and anticipating failures or issues before their occurrence.
2. Reactive simulation: DTs can enable responding to changes or events in real-time autonomously. Monitoring and dynamic reactions to deviations from expected behavior or predefined thresholds as well as controlling and adjusting the processing variables are the expected outcomes. Thus, it can recommend corrective and preventive actions using monitoring and prediction results.
3. Virtual Commissioning: For virtual commissioning through DTs testing and validation of new technologies or equipment can be performed in a simulated environment before its real implementation in the processing plants.
4. Synchronization-based Simulation Representation: utilization of DTs in the representation of synchronization-based simulation involves synchronizing the DT with a physical system to create a simulation model closely mirroring the real process. DT and the physical system are kept synchronized in real-time or near-real-time, allowing the accurate simulation and analysis of the process performance under various conditions. This application is valuable for testing scenarios, optimizing operations, and improving decision-making in complex systems such as transportation networks, energy grids, and smart cities.
Cyber-physical systems (CPS) play an important role in DT technology. In particular, CPS provides the foundation for the DT. It adds advanced capabilities to physical systems through computation and communication, interacting intensively with physical processes, which allows the accurate creation of virtual models or DTs. These DTs, in turn, leverage the capabilities of CPS to monitor, analyze, and control physical systems, leading to precise and efficient management and operation (Wang et al., 2015; Liu et al., 2017; Tao et al., 2019).
In digitally transformed food process operations, DT serves as a virtual replica of assets (i.e., equipment, unit operations), continuously synchronized with real systems via sensors (e.g., temperature and pH sensors) and advanced big data analytic tools (e.g., cloud computing and ML). This innovative approach enables real-time simulation and visualization of the food process operations, enhancing communication, collaboration, and decision-making. Different from conventional computer simulations, which rely on predefined models and scenarios and implement results after the simulation study, DT operates as a dynamic entity, continuously updating and implementing results through operational devices or personnel into real systems. This allows real-time adjustments and immediate actions in real scenarios for optimized processes and improved product quality. Furthermore, DT aims to extend computer simulations beyond their traditional scope of process or product design through virtual prototyping and optimization, offering comprehensive insights into processes and product development (Maheshwari et al., 2023; Verboven et al., 2020). This technology represents an effort to make simulation and data science tools available not only in the design phase (e.g., through what-if simulations) but also during real-time operations.
Existing studies on food-related DTs have discussed the concept of this technology, exploring various aspects, including its development, applications, utilization, potential benefits and limitations. Notably, these efforts have been predominantly focused on agricultural applications, with comparatively less attention given to other stages of the food system (Henrichs et al., 2022). Particularly, more research efforts on the application of DTs in food processing and manufacturing are needed, given the non-negligible contribution of this sector to the environmental impact. To the best of our knowledge, no prior reviews have comprehensively analyzed and discussed the implementation of DTs within the food processing industry from various aspects with a particular focus on sustainability.
To provide valuable insights for academia, industry, and policymakers to shape the future of digital transformation in the food industry, this review systematically analyzes existing studies on the applications of DT in the food industry, discussing its concept, benefits, and challenges to full adoption. Specifically, this work contributes to the existing body of knowledge on DT by identifying state-of-the-art applications and examining their adoption through both real-world use cases and findings from the literature. Further, it explores DT potential from a sustainability perspective, emphasizing its role in optimizing resource utilization for more efficient and sustainable food processing. Furthermore, it proposes a potential approach within the DT framework to serve as a general tool for supporting sustainability initiatives within the food processing industry. Lastly, it discusses the future impact of DT in shaping the evolution of food processing.
2 Methodology
Given the novelty of DT technology, the state-of-the-art application of DTs in the food processing industry is identified, and seminal works, use cases, existing gaps and the potential for future work in the area are discussed.
To ensure rigor and comprehensiveness, relevant works were selected based on the following criteria: (1) Primary Focus: The literature primarily focus is on DT applications in food processing. The initial inclusion and exclusion criteria were defined using keyword-based searches to filter publications based on their titles and abstracts. Exclusions included duplicates and studies not directly related to DT in the food industry; (2) Types of Literature: Sources included journal articles, conference papers, white papers, book chapters, and press releases. While these sources vary in depth and scientific rigor, they were included to provide a comprehensive overview of DT applications in food processing and capture broader research trends in the field; (3) Literature language: Only publications available in English were considered. (4) Implicit DT Applications: Studies discussing DT enabling technologies without explicitly using the term “Digital Twin” were also considered for inclusion, ensuring that relevant advancements were not overlooked; (5) Final inclusion and exclusion: To further refine the initial selections for the final set, papers that only mentioned DT in food processing in passing were excluded. Recent review papers’ references were examined to include studies that may not have been captured through the initial criteria. This step ensured more exhaustive coverage of literature.
All selected publications were categorized based on a predefined taxonomy (e.g., source type, food sector category, industrial case study and academic case study). Then, they underwent a detailed review, with identified applications systematically analyzed and discussed.
3 Results
A total of 43 case studies were identified from various sources. Figure 2 presents the distribution of these case study sources analyzed in this study. Most studies were published as journal articles (63%), followed by press releases (16%), which include web pages and company websites.
To better capture the current applications of DT in the food processing industry, case studies have been sorted according to the European Union’s classification of food processing. The food processing industry is classified into eight distinct categories: (1) meat products, (2) fish products, (3) fruit and vegetables, (4) edible oils, (5) dairy products, (6) grain mill products, (7) bakery, and (8) miscellaneous (e.g., sugar, tea, coffee, condiments, seasonings, snacks, and prepared and canned meals) (Asgharnejad et al., 2021). Within these categories, three main groups are identified: food preservation plants, food ingredient manufacturing plants, and food product manufacturing plants (Maroulis and Saravacos, 2008). Food Preservation facilities primarily utilize agricultural raw materials, often seasonal, employing preservation techniques such as thermal treatment, refrigeration, freezing, concentration, and dehydration. Food Ingredient Manufacturing facilities utilize bulk agricultural products or by-products of food processing to produce various ingredients (i.e., Sugars, starch, flour, oils, proteins, pectin, and gums). These facilities typically utilize operations and equipment units similar to traditional chemical processes. Food Product Manufacturing facilities often employ material transformation and preservation processes, in addition to packaging, to produce a diverse range of final products for consumers. Figure 3 depicts the application of DT technology across various food processing categories within the three main groups.
DT applications in the food processing within the miscellaneous category, encompassing products like, beverages (such as soft drinks beer, energy drink, fruit juices and water), food products (such as chocolate, French crêpe, honey, ice cream, starch-based foods, condiments), and food ingredients (such as sugar and syrup) (Siemens, 2018; Karadeniz et al., 2019; Bottani et al., 2020; Vignali and Bottani, 2020; Watson et al., 2021; Eppinger et al., 2021; Hong et al., 2021; Koulouris et al., 2021; McLean and Redmond, 2021; Vetter and Strube, 2022; Tshabalala and Kuriakose, 2023; Cabeza-Gil et al., 2023; Tancredi G. P. C. et al., 2023; Coca-Cola, 2023; Force Technology, 2024a, 2024b; George, 2021; Nestlé, n.d.; NVIDIA, n.d.; Siemens, n.d.) represent the most studied category of food processing, accounting for 58% of all categories examined. Within this category, approximately 84 and 16% of the case studies are concerned with food product manufacturing and food ingredient manufacturing groups, respectively, with the food preservation group being overlooked. The DT of fruit and vegetable products represents the second most studied category, constituting 16% of all categories examined. Within this category, both food preservation and food product manufacturing groups received almost equal attention, while food ingredient manufacturing was disregarded. DT applications in the grain, dairy, and meat product categories were studied at similar rates, representing 7, 9, and 7% of the total studies, respectively. Within these sectors, most of the case studies focused on food product manufacturing group, followed by food ingredient manufacturing, and food preservation groups. Finally, the bakery products category was the least explored, while no applications were found in the fish and edible oils categories.
The analysis further differentiated between practical DT applications (industrial case study) and research (academic case study) within the studies, providing insights into the current state of DT adoption at the industrial level (Figure 4). Notably, a clear disparity exists, with a significantly higher number of studies focusing on research compared to industrial use cases.
4 Discussion
4.1 Digital Twin in the food processing industry
4.1.1 Applications
The utilization of DT in the food processing industry has undoubtedly important advantages. It has been adopted across food sectors to optimize operations, enhance product quality, and improve consumers acceptability through the design of personalized products. However, the analyzed case studies revealed a clear lack of applications in the fish and edible oils sectors. This might be due to several factors, as discussed in the following. Indeed, DT technology has been adopted in food sectors where the high complexity of the processes makes streamlining useful to analyze the most critical phases affecting process performance and product quality. Moreover, regardless of whether production is carried out in batch or continuous processes, the utilization of DT technology is attractive for industries characterized by individualization-based manufacturing (e.g., personalized food products), multi-product manufacturing (e.g., condiments and breweries), and manufacturing of products for which slight changes in processing parameters highly affect the quality (e.g., sugar and dairy production). These industries often prioritize rapid recipe adjustments, efficient management of the productions based on multi-products, effective handling of production uncertainties, and precise control of the processing parameters.
It is worth noting that some implementations already exist in the food industry such as soft drinks manufacturing. The companies use DTs to manage the plant shopfloor and warehouses, as well as streamline processes (Coca-Cola, 2023; NVIDIA, n.d.). Further, other multi-product food companies leverage this technology to optimize operations, enable product personalization, and maintain high-quality standards (Nestlé, n.d.; Siemens, n.d.). The dairy industry uses this technology to maintain product quality, enhance resource efficiency and improve waste management (Force Technology, 2024b). The bakery product producers employs DT to facilitate the management and optimization of existing recipes, and the design of new products (Force Technology, 2024a). Similarly, the breweries employ the DTs for precise process control, ensuring consistent product quality (George, 2021). However, within the research domain, the number of case studies on the practical implementation of DT is lower compared to those focused on scientific studies. This could be attributed to the company’s concerns to publicly disclose the utilization of DT technology and its advancement to maintaining a competitive advantage. Additionally, the implementation of DT often involves the collection and analysis of sensitive data, which companies may be reluctant to share for confidentiality reasons. Furthermore, many DT applications are still in their early stages, and companies may prefer to achieve more robust results before their dissemination.
4.1.2 Purpose of use
The adoption of DT technology is driven by production and market factors, such as the need to meet increased demand or adapt to evolving market preferences, align with specific nutritional standards, and packaging sizes (Koulouris et al., 2021). Additionally, the increased competition in the business environment compels companies to look beyond cost reduction, and consider as key factors the improvement of product quality, productivity, and process efficiency (Perno et al., 2022). Further, food companies have to cope with low-profit margins while being challenged to face market changes by reducing time-to-market while developing new and flexible processes for a wide range of products (Koulouris et al., 2021). The employee-related factors play a role, with companies leveraging DTs to enhance creativity and cooperation between employees and offer virtual reality-based training programs and increase workplace safety by identifying potential hazards (Henrichs et al., 2022).
DT is deemed implemented when it incorporates as key elements the physical object or process that should be twinned, a virtual model representing the essential properties of the physical counterpart, and the connection between the two (Kritzinger et al., 2018; Xia et al., 2020; Ricci et al., 2021). It is worth mentioning that if there is lacking of or insufficient data available between the digital layer and its physical counterpart, it is not possible, by definition, to consider the model of the system as a DT. In the food processing industry, DTs have been implemented at different stages, using various enabling technologies for system architectures, each encompassing a specific purpose for their use. These stages are the design, processing, and service, and, in turn, are subdivided into sub-categories considering their specific purposes as follows.
4.1.2.1 Design stage
1. Optimization: DT utilization can assist in individuating the optimal design parameters to maximize process efficiency and minimize resource consumption. It can be employed to design new products, new processes and retrofitting the existing ones to enhance product quality, productivity, and efficient use of resources.
2. Data Generation: In situations where sufficient data for process design are lacking, for instance when only lab-scale data are available, DT can be employed to generate the necessary data. This can help in rebalancing datasets or estimating operating conditions or product characteristics, facilitating the setup of accurate models, through techniques such as ML, to be fed into optimization models.
3. Virtual Evaluation, Verification, and Validation: DTs serve as cost-effective tools for evaluating, verifying, and validating designed processes and products in a virtual environment.
4.1.2.2 Processing stage
1. Process monitoring: DTs could offer real-time monitoring by integrating essential data with visual models. It can combine historical, real-time, and predictive data to track past performances, monitor current operations, and forecast future outcomes. Thus, not only current data can be presented but DT could help in understanding situations and optimizing decisions.
2. Process control: Conventional methods for process control are based on physical measurements, and models should be used for predictive control. DTs, instead, enhance process control by leveraging the connection between virtual and physical components to eliminate disturbances and maintain quality specifications.
3. Process prediction: Variations in processing variables, such as raw material characteristics fluctuations, pose challenges. DTs predict how these variations impact processing conditions, leveraging soft sensing technologies like ML to forecast the trend of critical variables that are difficult or costly to be measured directly.
4. Process optimization and production planning: Conventional process optimization and production planning methods are affected by disturbances and uncertainties since they rely on static information. DTs vastly improve the effectiveness of optimization and planning processes by providing both monitored and predicted data.
4.1.2.3 Service stage
1. Fault Detection and Diagnosis: Fault locations can be pinpointed by comparing process variables from both virtual and physical processes. DTs facilitate fault diagnosis, enabling the identification of fault types and/or affected resources.
2. Virtual Testing: As a digital replica of the physical object, DTs allow testing operations in scenarios where failures could result in significant losses or damages. Unlike traditional simulation, DTs offer a highly realistic and accurate simulation environment. The identical virtual settings enable thorough exploration and testing without the inherent risks associated with physical systems.
3. Predictive maintenance: Like process prediction, predictive maintenance can be managed by DTs that can provide information on disturbances and uncertainties, thus providing more accurate maintenance times, such as cleaning-in-place scheduling.
Table 1 shows the results reported in the literature on the implementation of DTs in food processing, including the phases and specific purposes of their implementation and the main findings. For the sake of clarity, the specific purpose of each study is reported, regardless of the additional functionalities that might be achieved.
As shown in Table 1, the implementation of DT technology in food processing was mostly concerning the process phase, being control and prediction of the most targeted functionalities. As mentioned before, some studies achieved additional functionalities of DT applications besides the specific purpose for their use. For instance, to mention a few, Bottani et al. (2020) developed a DT for a fruit juice pasteurization unit to predict potential anomalies and enhance worker safety. Simultaneously, DT was used to control process parameter variations. In the study case of carrot slice drying conducted by Schemminger et al. (2024) the specific purpose of DT was the prediction of product quality, while monitoring and controlling were concurrently considered as functionalities of the DT. Thus, it can be highlighted that DT can be exploited for multiple functionalities simultaneously and fulfill the requirements of more controlled and efficient food processing operations.
4.1.3 Tools, methods and technologies for digital Twin system architecture
DT has been supported by various technologies and tools (from simulations to agents, from graphical representations to service platforms), each serving specific purposes aligned with the user’s ultimate goal (Crespi et al., 2023). Modeling and simulation are pivotal components of DT technology, particularly in complex processes. Commercial process simulator software, such as SuperPro Designer, Aspen Plus, Aspen HYSYS, etc., are widely employed for constructing virtual plants (Ureta and Salvadori, 2022). Typically, these process simulators utilize first-principles modeling, also known as white-box modeling, which relies on a deep understanding of physical–chemical phenomena underneath the process. Previous studies carried out for the food processing and chemical processing industry (Koulouris et al., 2021; Barbero-sánchez et al., 2024) have demonstrated the significant role of process simulators within the DT framework. These tools are characterized by standardized methodologies and robust technical support, ensuring the quality and reliability of DT applications in complex processes (Yu et al., 2022). Computational fluid dynamics (CFD) simulation tools (i.e., COMSOL Multiphysics, Ansys, etc.) also contribute significantly to DT frameworks. While these tools are inherently slow and cannot provide real-time or near-real-time simulation feedback, which is one of the key aspects of DT, they can be integrated with significant powerful tools, such as AI. For instance, ML models can be trained on a set of CFD-generated data to build quickly accessible models for real-time simulation, enabling faster predictions. This approach, explored in a case study for oven automation, was enabling real-time simulations for optimized thermal processing control (Kannapinn et al., 2022). In addition, CFD simulations can be launched in advance, building a database, which can then be used for real-time system control by comparing expected outcomes with sensor data to detect faults or anomalies, as discussed by Solari et al. (2023). Overall, these approaches allow for the creation of more efficient and responsive DT systems. Intelligent sensors and cloud platforms are advanced tools that enable the development and implementation of DT. These tools leverage data-driven (black-box) modeling, powered by big data analysis, IoT, and machine learning. While this approach is gaining traction in food processing in the context of Industry 4.0, hybrid modeling, combining white-box and black-box modeling approaches, is increasingly being considered in food-related DT studies. For example, (Tancredi et al., 2022) conducted a hybrid modeling study of a heat exchanger for monitoring and anomalies detection. Fundamental equations were incorporated in the model developed in LabVIEW environment for simulation. Additionally, Python was employed to develop an ML algorithm, enabling full process automation and autonomous fault detection, allowing real-time adjustments to optimize performance. Hybrid modeling approach offers a balanced integration of theoretical foundations and empirical data, providing a more robust and reliable DT function (Eppinger et al., 2021; Tancredi et al., 2022). Table 2 provides an overview of the diverse tools employed for DT construction within the analyzed food processing case studies.
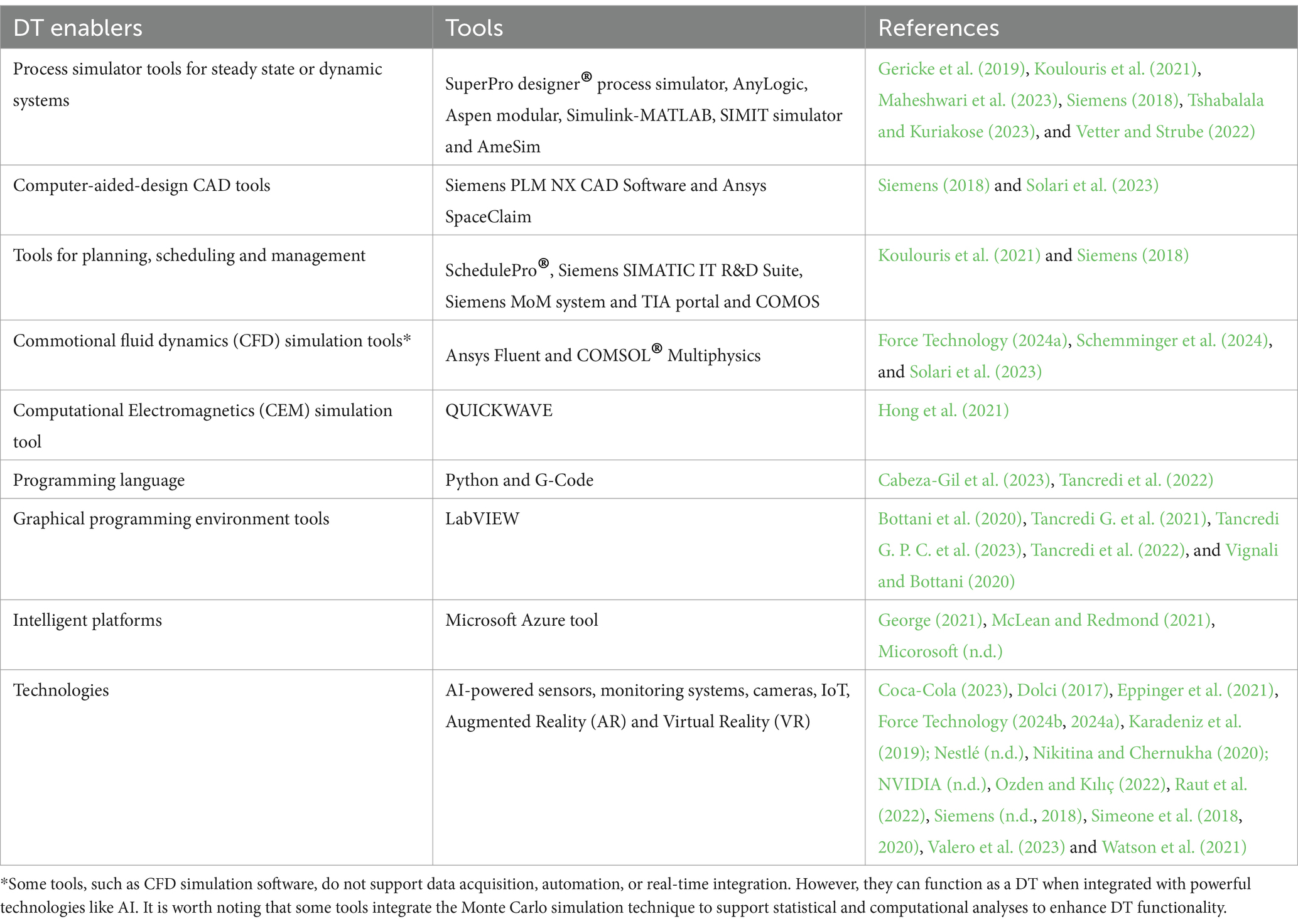
Table 2. A summary of different tools and technologies used in the case studies for constructing system architecture of DT technology.
4.1.4 Digital Twin for resource efficiency enhancement and waste management
The application of DT technology in the food sector can be crucial to meeting the societal demand for increased sustainability by improving resource efficiency and reducing water and energy consumption and emissions. Therefore, the driving factors for the use of DTs are not only the needs of the food industry to meet market demands and maintain competitiveness through the development of new products, quality enhancement, personalized food product design, and productivity improvement, but also a commitment to reduce its environmental footprint. Therefore, the use of DT technology can be seen as a significant advantage for the management of this last problem. For instance, DT facilitates precise control of production lines (Noor Hasnan and Yusoff, 2018; Clairand et al., 2020). This enables real-time monitoring of potential water and energy losses, allowing the implementation of solutions to prevent such losses (Clairand et al., 2020; Ojo et al., 2018). Measuring and analyzing specific variables and parameters of unit operations for water and energy usage through DT enables the identification and anticipation of potential issues. This proactive approach allows for the adjustment of process parameters, leading to improved water and energy efficiency and reduced waste. For example, in the ketchup processing industry (Eppinger et al., 2021), maintaining ketchup temperature above a certain threshold throughout the process is crucial to prevent bacterial proliferation, although at the cost of significant thermal energy consumption. DT technology can optimize thermal management systems, allowing for a reduction in the safety margin for target temperature settings. This not only decreases thermal energy consumption, leading to substantial cost savings but also preserves product quality. Similarly, in the milk powder industry (Eppinger et al., 2021), the drying process plays a pivotal role in determining end-product quality. Given its energy-intensive nature, optimizing the drying process typically requires empirical testing. By leveraging DT technology to adjust airflow directions and processing conditions, energy efficiency can be improved alongside product quality, while reducing the number of experimental trials. In the flour industry, precise control of the air velocity in pneumatic conveying systems is vital for both environmental safety and product quality (Tancredi G. P. C. et al., 2023). Optimizing this parameter can significantly improve the system’s energy efficiency. In honey-based product manufacturing (Watson et al., 2021), inefficient mixing can result in off-specification products and excessive energy consumption. The mixing process can leverage DT to predict the remaining time for complete mixing, enabling better scheduling of batch processes and enhancing productivity. Thus, preventing under-mixing and over-mixing, product rework or disposal is minimized, while excess energy usage is reduced. DT technology also contributes to water efficiency in Cleaning-In-Place (CIP) systems in the food industry (Simeone et al., 2018; Simeone et al., 2020). The food industry can leverage this technology for real-time monitoring and optimized planning of CIP processes. For example, in processes involving tanks of product concentrate, DT can evaluate fouling levels during cleaning, providing timely alerts to operators regarding cleaning adequacy within specified timeframes, thereby preventing both over cleaning and insufficient cleaning (Simeone et al., 2020). Furthermore, in the dairy industry, DTs can facilitate well-planned CIP by monitoring biofilm growth in the heat exchanger in real time during production and detecting potential sources of bacterial growth and pathogens. This approach ensures proper hygiene, maintained quality, and reduced downtime, while simultaneously improving water and energy efficiency (Force Technology, 2024b). Beyond water and energy use efficiency, DT can mitigate food waste during production. For example, DTs can be utilized for predictive maintenance of assets like pasteurizers, contributing to more efficient and less wasteful food production (Force Technology, 2024b). Furthermore, considering the variability of raw materials due to seasonal factors, DT technology offers an adaptive approach to adjusting processing parameters, such as machine settings, based on raw material quality or properties, thereby minimizing waste. Overall, DT could contribute to the growth of sustainable processes by optimizing the use of raw materials, water and energy, enabling food waste to be reduced (Eppinger et al., 2021; Watson et al., 2021).
4.2 Digital Twin as a general tool for supporting sustainability initiatives
In food processing, most design and optimization problems are aimed at several objectives, which can often be contradictory (Abakarov et al., 2013; Madoumier et al., 2019). Potential antagonistic effects can arise when optimizing multiple objectives, as maximizing one may lead to the minimization of one or several others (Rangaiah, 2009; Rangaiah et al., 2020). For instance, maximizing food product quality (texture, nutrient concentration, flavor, etc.,) often conflicts with process performance objectives, such as minimizing utility consumption, maximizing profit, or ensuring safety (Madoumier et al., 2019). Optimal solutions can be achieved through a multi-objective optimization (MOO) approach (Rangaiah, 2009; Rangaiah et al., 2020). MOO offers well-balanced solutions for the single-unit operation and the entire process, simultaneously investigating and estimating potential savings (Cerda-Flores et al., 2022). This approach can be integrated into the DT framework to serve as a versatile tool for implementing and assessing the effectiveness of sustainability initiatives in food processing. Recent studies in other disciplines have demonstrated the effectiveness of this approach in identifying optimal trade-offs between conflicting objectives within DT framework. For instance, Wang et al. (2023) investigated the scheduling optimization of laminar cooling water supply systems for hot rolling mills to enhance energy efficiency in the steel industry. The optimization model was designed to minimize multiple objectives simultaneously, primarily focusing on reducing the electrical energy usage in the pumping system while ensuring adequate water supply and operational efficiency. This optimization model was introduced in a DT framework, enabling a new mechanism for scheduling that includes virtual-real response, interaction, control, and iterative optimization. The proposed scheduling system significantly reduced energy consumption while ensuring the cooling requirements. This demonstrated the effectiveness of the DT model in optimizing resource use in industrial applications. Guo et al. (2024) proposed a novel DT model for geothermal heating systems to be utilized in buildings to address supply–demand mismatches. The authors integrated MOO within the DT framework to enable simultaneous optimization of the costs, geothermal energy utilization, and carbon emissions. This approach facilitated accurate heating demand prediction and optimal control of storage systems and heat pumps, maximizing geothermal energy use while minimizing both the costs and the emissions. The authors emphasized that this approach is an effective mean of enhancing energy sustainability. Therefore, in the perspective of a wider utilization of DT technology in the food processing industry, the integration of MOO into DT is highly valuable to enhance the usefulness and maximize the functionality of this model and enable more effective product and process design and optimization.
4.3 Challenges and limitations
While significant progress has been made in developing DT models for the food industry, large-scale deployment remains challenging. This is due, in part, to the need for advanced mathematical, numerical, and computational methodologies to ensure robustness and scalability (Bianco et al., 2022; Kannapinn et al., 2022). Beyond DT model development, recent research has highlighted general implementation challenges (Fuller et al., 2020; Henrichs et al., 2022; Melesse et al., 2020, 2021; Perno et al., 2022; Verboven et al., 2020; Wagner et al., 2019). For instance, Fuller et al. (2020), noted similarities between DT implementation challenges and those encountered in data analytics and the IoT, including data security, data acquisition, communication, storing, sorting, and analysis. Incorporating functional requirements into the DT including the monitoring of asset operations, the measurement of key performance indicators (KPIs), the materials data, the notification of unacceptable fluctuations and the use of simulation to identify potential adjustment actions, necessitates a vast amount of data, potentially hindering DT’s operational efficiency. Specifically, deep learning algorithms are considered highly energy-intensive tools, exacerbated by the increasing volumes of IoT data transmitted over networks (Yu et al., 2022). Further, a significant increase in computational requirements could lead to a trade-off between marginal benefits and the power consumed, which may counteract the intended purpose. Other studies have identified further implementation challenges, including the lack of a standardized methodology for information transfer between physical and virtual objects (Melesse et al., 2020, 2021; Perno et al., 2022), the need for a consistent framework (Henrichs et al., 2022; Wagner et al., 2019), and the complexity of model implementation given the intricate nature of food matrices (Verboven et al., 2020). Furthermore, the reluctance of some food companies to adopt emerging technologies, coupled with concerns over high investment costs and data security, also hinders widespread DT implementation within the food sector (Melesse et al., 2020, 2021; Verboven et al., 2020; Henrichs et al., 2022; Krupitzer et al., 2022; Perno et al., 2022). In Figure 5, the Ishikawa diagram is reported to highlight the factors that delay or hinder the full adoption of DT technology.
4.4 Related studies and future direction
Recent publications have investigated the prerequisites for developing and implementing DTs in the process industry, highlighting their potential benefits, challenges, and essential enabling technologies (Lee et al., 2013; Eisen et al., 2020; Verboven et al., 2020; Xia et al., 2020; Liu et al., 2021; Perno et al., 2022). DT concepts and capabilities are still evolving, and existing literature reviews offer valuable insights in this context, however, efficient resource management throughout the entire process operations have not been highly prioritized. For instance, Verboven et al. (2020) underlined that a comprehensive, multidisciplinary approach is required for a successful deployment and operation, highlighting the benefits of DTs in food processing operations. Nikitina and Chernukha (2020), whose work was focused on the utilization of DTs in food product development, underscored the efficiency and cost-saving benefits of DTs for testing new food product recipes virtually. Pylianidis et al. (2021) considered DT applications in food systems, focusing only on agriculture production, while Henrichs et al. (2022) reviewed DT applications in a broader context in the food industry, primarily focusing on the food supply chain. The latter highlighted the challenges and potentials of implementing this technology in the food industry with a focus on the supply chain. Kucha and Olaniyi (2024) studied the potential implementation of DTs in the meat industry utilizing the latest digital tools like IoT sensors for product quality improvement, highlighting the significance of this technology in the meat industry.
Differently from previous review papers, in this work, the applications of DTs in food industry have been thoroughly analyzed, with a specific focus on their potential and challenges to sustainability outcomes. The paper specifically targeted the food processing industry, providing a classification of the applications of DTs emphasizing the key elements, the model bases, functionalities and the purposes of their use (Table 3). It also sheds light on the technologies, commercial software and methods utilized for constructing the system architecture of DTs, offering insights into target units, products, and processes. The potential contribution of DTs in providing suggestions to increase the sustainability of the food processing industry, with particular attention on water and energy management, was analyzed and discussed. However, the limited number of publicly available industrial case studies did not allow fully capture the scope of DT adoption across the sector. Efforts are needed to get information on its implementation extent in the food industry as well as the factors that hinder its wider adoption.
Overall, being DT an emerging technology, standards and frameworks must be established and DT modeling methodology must be improved, enabling applications to enhance resource use efficiency and minimize waste generation in food processing operations.
DT can either replace current systems or be integrated into existing tools and methods to enhance their functionality beyond traditional limits, offering a powerful solution for managing complexity more effectively. From our perspectives, since DT can be applied at any system level and time horizon, it is particularly valuable in scenarios where human intervention requires significant intellectual and resource efforts.
5 Conclusion
To conclude, Digital Twin (DT) technology holds a significant promise for revolutionizing the food processing industry. Its potential spans a range of holistic solutions, including real-time control, production scheduling, technology upgrades, asset diagnosis, maintenance, and optimization for more efficient and sustainable processes. However, open questions need to be addressed to ensure broad adoption across all food processing categories. Current DT case studies in the food processing industry remain limited, with a primary focus on investigating and demonstrating the feasibility of applications and use-cases. This review analyzed its applications across various food processing categories, distinguishing between its practical adoption and existing scientific literature. Key aspects, including functionalities, purpose of use, and challenges to full adoption, were discussed to provide insights into its status. The potential approach within the DT framework to serve as a general tool for supporting sustainability initiatives within the food processing industry was examined. Furthermore, the review emphasized the need for further research to bridge existing gaps. Standardization efforts, the development of a consistent framework, and advancements in modeling and simulation techniques are required to allow the growth and adoption of the DT within food sectors to achieve true digitalization within this complex industry. Addressing these challenges will be pivotal in unlocking the full potential of DT technology, paving the way for smarter, more sustainable food processing operations.
Author contributions
EA: Conceptualization, Data curation, Investigation, Visualization, Writing – original draft. GF: Conceptualization, Supervision, Writing – review & editing.
Funding
The author(s) declare that no financial support was received for the research and/or publication of this article.
Conflict of interest
The authors declare that the research was conducted in the absence of any commercial or financial relationships that could be construed as a potential conflict of interest.
The author(s) declared that they were an editorial board member of Frontiers, at the time of submission. This had no impact on the peer review process and the final decision.
Generative AI statement
The authors declare that no Gen AI was used in the creation of this manuscript.
Publisher’s note
All claims expressed in this article are solely those of the authors and do not necessarily represent those of their affiliated organizations, or those of the publisher, the editors and the reviewers. Any product that may be evaluated in this article, or claim that may be made by its manufacturer, is not guaranteed or endorsed by the publisher.
References
Abakarov, A., Sushkov, Y., and Mascheroni, R. H. (2013). A multi-criteria optimization and decision-making approach for improvement of food engineering processes. Int. J. Food Stud. 2, 1–21. doi: 10.7455/ijfs/2.1.2013.a1
Asgharnejad, H., Khorshidi Nazloo, E., Madani Larijani, M., Hajinajaf, N., and Rashidi, H. (2021). Comprehensive review of water management and wastewater treatment in food processing industries in the framework of water-food-environment nexus. Compr. Rev. Food Sci. Food Saf. 20, 4779–4815. doi: 10.1111/1541-4337.12782
Barbero-sánchez, J., Megía-ortega, A., Ferro, V. R., and Valverde, J. (2024). Exploring alternatives to create digital twins from and for process. Simulation 6, 16–30. doi: 10.30564/jcsr.v6i1.6168
Bianco, N., Mauro, A. W., Mauro, G. M., Pantaleo, A. M., and Viscito, L. (2022). A semi-empirical model for de-watering and cooling of leafy vegetables. Appl. Therm. Eng. 208:118227. doi: 10.1016/j.applthermaleng.2022.118227
Botín-Sanabria, D. M., Mihaita, S., Peimbert-García, R. E., Ramírez-Moreno, M. A., Ramírez-Mendoza, R. A., and Lozoya-Santos, J. d. J. (2022). Digital twin technology challenges and applications: A comprehensive review. Remote Sens. 14, 1–25. doi: 10.3390/rs14061335
Bottani, E., Vignali, G., and Carlo Tancredi, G. P. (2020). A digital twin model of a pasteurization system for food beverages: tools and architecture. Proceedings - 2020 IEEE International Conference on Engineering, Technology and Innovation, ICE/ITMC 2020.
Cabeza-Gil, I., Ríos-Ruiz, I., Martínez, M. Á., Calvo, B., and Grasa, J. (2023). Digital twins for monitoring and predicting the cooking of food products: A case study for a French crêpe. J. Food Eng. 359:111697. doi: 10.1016/j.jfoodeng.2023.111697
Cerda-Flores, S. C., Rojas-Punzo, A. A., and Nápoles-Rivera, F. (2022). Applications of multi-objective optimization to industrial processes: a literature review. PRO 10, 1–15. doi: 10.3390/pr10010133
Ciano, M. P., Pozzi, R., Rossi, T., and Strozzi, F. (2021). Digital twin-enabled smart industrial systems: a bibliometric review. Int. J. Comput. Integr. Manuf. 34, 690–708. doi: 10.1080/0951192X.2020.1852600
Clairand, J. M., Briceno-Leon, M., Escriva-Escriva, G., and Pantaleo, A. M. (2020). Review of energy efficiency technologies in the food industry: trends, barriers, and opportunities. IEEE Access 8, 48015–48029. doi: 10.1109/ACCESS.2020.2979077
Coca-Cola, HBC. (2023). At our bottling plant in Edelstal, Burgenland, we use numerous 4.0 technologies in production as well as in logistics for warehousing and supplying our customers with our 24/7 portfolio.
Dąbrowska, A., Giel, R., and Winiarska, K. (2022). Sequencing and planning of packaging lines with reliability and digital twin Concept considerations – a case study of a sugar production plant. Logforum 18, 321–334. doi: 10.17270/J.LOG.2022.762
Dolci, R. (2017). IoT solutions for precision farming and food manufacturing: artificial intelligence applications in digital food. Proc. Int. Comput. Softw. Appl. Conf. 2, 384–385. doi: 10.1109/COMPSAC.2017.157
Eisen, K., Eifert, T., Herwig, C., and Maiwald, M. (2020). Current and future requirements to industrial analytical infrastructure—part 1: process analytical laboratories. Anal. Bioanal. Chem. 412, 2027–2035. doi: 10.1007/s00216-020-02420-2
Eppinger, T., Longwell, G., Mas, P., Goodheart, K., Badiali, U., and Aglave, R. (2021). Increase food production efficiency using the executable digital twin (xDT). Chem. Eng. Trans. 87, 37–42. doi: 10.3303/CET2187007
Eslami, E., Abdurrahman, E., Ferrari, G., and Pataro, G. (2023). Enhancing resource efficiency and sustainability in tomato processing: a comprehensive review. J. Clean. Prod. 425:138996. doi: 10.1016/j.jclepro.2023.138996
Force Technology. (2024a). Digital twins of baking ovens - for design, development, management & optimisation. Available online at: https://forcetechnology.com/en/cases/haas-meincke-digital-twins-baking-ovens (Accessed February 15, 2025).
Force Technology. (2024b). Enabling better dairy production decisions. Available online at: https://forcetechnology.com/en/articles/better-dairy-production-decisions-with-ar-and-digital-twin (Accessed February 15, 2025).
Fuller, A., Fan, Z., Day, C., and Barlow, C. (2020). Digital twin: enabling technologies, challenges and open research. IEEE Access 8, 108952–108971. doi: 10.1109/ACCESS.2020.2998358
Garnett, T. (2013). Food sustainability: problems, perspectives and solutions. Proc. Nutr. Soc. 72, 29–39. doi: 10.1017/S0029665112002947
George, S. (2021). Converging the physical and digital with digital twins, mixed reality, and metaverse apps. Available online at: https://azure.microsoft.com/en-us/blog/converging-the-physical-and-digital-with-digital-twins-mixed-reality-and-metaverse-apps/ (Accessed November 1, 2024).
Gericke, G. A., Kuriakose, R. B., Vermaak, H. J., and Mardsen, O. (2019). Design of Digital Twins for optimization of a water bottling plant. IECON Proc. 2019, 5204–5210. doi: 10.1109/IECON.2019.8926880
Guo, Y., Tang, Q., Darkwa, J., Wang, H., Su, W., Tang, D., et al. (2024). Multi-objective integrated optimization of geothermal heating system with energy storage using digital twin technology. Appl. Therm. Eng. 252:123685. doi: 10.1016/j.applthermaleng.2024.123685
Henrichs, E., Noack, T., Piedrahita, A. M. P., Salem, M. A., Stolz, J., and Krupitzer, C. (2022). Can a byte improve our bite? An analysis of digital twins in the food industry. Sensors 22:115. doi: 10.3390/s22010115
Hong, Y.-K., Stanley, R., Tang, J., Bui, L., and Ghandi, A. (2021). Effect of electric field distribution on the heating uniformity of a model ready-to-eat meal in microwave-assisted thermal sterilization using the FDTD method. Food Secur. 10:311. doi: 10.3390/foods10020311
Kannapinn, M., Pham, M. K., and Schäfer, M. (2022). Physics-based digital twins for autonomous thermal food processing: efficient, non-intrusive reduced-order modeling. Innov. Food Sci. Emerg. Technol. 81:103143. doi: 10.1016/j.ifset.2022.103143
Karadeniz, A. M., Arif, İ., Kanak, A., and Ergün, S. (2019). Digital twin of egastronomic things: A case study for ice cream machines. Proc. IEEE Int. Sympos. Circuits Syst. 2019, 1–4. doi: 10.1109/ISCAS.2019.8702679
Klemeš, J., Smith, R., and Kim, J.-K. (2008). Handbook of water and energy management. Cambridge: Woodhead Publishing Limited.
Koulouris, A., Misailidis, N., and Petrides, D. (2021). Applications of process and digital twin models for production simulation and scheduling in the manufacturing of food ingredients and products. Food Bioprod. Process. 126, 317–333. doi: 10.1016/j.fbp.2021.01.016
Kritzinger, W., Karner, M., Traar, G., Henjes, J., and Sihn, W. (2018). Digital twin in manufacturing: a categorical literature review and classification. IFAC 51, 1016–1022. doi: 10.1016/j.ifacol.2018.08.474
Krupitzer, C., Noack, T., and Borsum, C. (2022). Digital food twins combining data science and food science: system model, applications, and challenges. PRO 10:781. doi: 10.3390/pr10091781
Kucha, C., and Olaniyi, E. O. (2024). Applications of hyperspectral imaging in meat tenderness detection current research and potential for digital twin technology. Food Biosci. 58:103754. doi: 10.1016/j.fbio.2024.103754
Lee, J., Lapira, E., Bagheri, B., and Kao, H. (2013). Recent advances and trends in predictive manufacturing systems in big data environment. Manufact. Lett. 1, 38–41. doi: 10.1016/j.mfglet.2013.09.005
Leng, J., Liu, Q., Ye, S., Jing, J., Wang, Y., Zhang, C., et al. (2020). Digital twin-driven rapid reconfiguration of the automated manufacturing system via an open architecture model. Robot. Comput. Integr. Manuf. 63:101895. doi: 10.1016/j.rcim.2019.101895
Liu, M., Fang, S., Dong, H., and Xu, C. (2021). Review of digital twin about concepts, technologies, and industrial applications. J. Manuf. Syst. 58, 346–361. doi: 10.1016/j.jmsy.2020.06.017
Liu, Y., Peng, Y., Wang, B., Yao, S., Liu, Z., and Concept, A. (2017). Review on cyber-physical systems. J. Automat. Sinica 4, 27–40. doi: 10.1109/JAS.2017.7510349
Madoumier, M., Trystram, G., Sébastian, P., and Collignan, A. (2019). Trends in Food Science & Technology Towards a holistic approach for multi-objective optimization of food processes: a critical review. Trends Food Sci. Technol. 86, 1–15. doi: 10.1016/j.tifs.2019.02.002
Maheshwari, P., Kamble, S., Belhadi, A., Mani, V., and Pundir, A. (2023). Digital twin implementation for performance improvement in process industries- A case study of food processing company. Int. J. Prod. Res. 61, 8343–8365. doi: 10.1080/00207543.2022.2104181
Marcello Braglia, R. G., and Marrazzini, L. (2020). Rolling Kanban: a new visual tool to schedule family batch manufacturing processes with kanban. Int. J. Prod. Res. 58, 3998–4014. doi: 10.1080/00207543.2019.1639224
McLean, V., and Redmond, W. (2021). Mars and Microsoft work together to accelerate Mars’ digital transformation and reimagine business operations, Associate experience and consumer engagement. Available online at: https://news.microsoft.com/2021/05/13/mars-and-microsoft-work-together-to-accelerate-mars-digital-transformation-and-reimagine-business-operations-associate-experience-and-consumer-engagement/ (Accessed November 1, 2024).
Melesse, T. Y., Di Pasquale, V., and Riemma, S. (2020). Digital twin models in industrial operations: A systematic literature review. Proc. Manufact. 42, 267–272. doi: 10.1016/j.promfg.2020.02.084
Melesse, T. Y., Di Pasquale, V., and Riemma, S. (2021). Digital twin models in industrial operations: state-of-the-art and future research directions. IET Collab. Intellig. Manufact. 3, 37–47. doi: 10.1049/cim2.12010
Micorosoft. (n.d.). Microsoft azure digital twin. Available at: https://azure.microsoft.com/en-us/products/digital-twins/ (Accessed November 1, 2024).
Nestlé. (n.d.). Digital innovation. Available at: https://www.nestle.com/about/research-development/digital-innovation (Accessed February 16, 2025).
Nget, S., Mith, H., Boué, G., Curet, S., and Boillereaux, L. (2023). The development of a digital twin to improve the quality and safety issues of Cambodian Pâté: the application of 915 MHz microwave cooking. Food Secur. 12:187. doi: 10.3390/foods12061187
Nikitina, M., and Chernukha, I. (2020). Personalized nutrition and “Digital Twins” of food. Slovak J. Food Sci. 14, 264–270. doi: 10.5219/1312
Nikmaram, N., and Rosentrater, K. A. (2019). Overview of some recent advances in improving water and energy efficiencies in food processing factories. Front. Nutr. 6:20. doi: 10.3389/fnut.2019.00020
Noor Hasnan, N. Z., and Yusoff, Y. M. (2018). Short review: application areas of industry 4.0 Technologies in Food Processing Sector. 2018 IEEE 16th student conference on Research and Development. SCOReD 2018, 1–6. doi: 10.1109/SCORED.2018.8711184
NVIDIA. (n.d.). Warehouse digital twins. Available online at: https://docs.omniverse.nvidia.com/digital-twins/latest/warehouse-digital-twins/use-cases.html (Accessed February 16, 2025).
Ojo, O. O., Shah, S., Coutroubis, A., Jimenez, M. T., and Ocana, Y. M. (2018). Potential impact of industry 4.0 in sustainable food supply chain environment. 2018 IEEE International Conference on Technology Management, Operations and Decisions, ICTMOD 2018, 172–177.
Ozden, S., and Kılıç, F. (2022). Modeling of drying kinetics of Banana (Musa spp., Musaceae) slices with the method of image processing and artificial neural networks. Int. J. Comput. Intell. Appl. 21:171. doi: 10.1142/S1469026822500171
Park, K. T., Son, Y. H., and Noh, S. D. (2020). The architectural framework of a cyber physical logistics system for digital-twin-based supply chain control. Int. J. Prod. Res. 59, 5721–5742. doi: 10.1080/00207543.2020.1788738
Perno, M., Hvam, L., and Haug, A. (2022). Implementation of digital twins in the process industry: A systematic literature review of enablers and barriers. Comput. Ind. 134:103558. doi: 10.1016/j.compind.2021.103558
Pylianidis, C., Osinga, S., and Athanasiadis, I. N. (2021). Introducing digital twins to agriculture. Comput. Electron. Agric. 184:105942. doi: 10.1016/j.compag.2020.105942
Rangaiah, G. P., Feng, Z., and Hoadley, F., (2020). Multi-objective optimization applications in chemical process engineering: Tutorial and review. Processes. 8:508.
Raut, S., Schemminger, J., Von Gersdorff, J. E, Mellmann, J., and Sturm, B. (2022). Moving towards digital twin based smart drying systems for agricultural products. In 2022 ASABE Annual International Meeting American Society of Agricultural and Biological Engineers.
Ricci, R., Battaglia, D., and Neirotti, P. (2021). External knowledge search, opportunity recognition and industry 4.0 adoption in SMEs. Int. J. Prod. Econ. 240:108234. doi: 10.1016/j.ijpe.2021.108234
Schemminger, J., Raut, S., Sturm, B., and Defraeye, T. (2024). A hybrid digital shadow to assess biological variability in carrot slices during drying. Thermal Sci. Eng. Progress 50:102507. doi: 10.1016/j.tsep.2024.102507
Siemens. (2018). Customization in the food and beverage industry. Available online at: www.siemens.com/food-beverage (Accessed July 23, 2024).
Siemens. (n.d.). From outdated to trendsetting. Available online at: https://xcelerator.siemens.com/global/en/industries/food-beverage/smart-manufacturing/nestle-juuka-case-study.html?utm_campaign=2024-2-global-tac_900_069_gbl_cs_nestle_jukka_video_1&utm_source=siemens_amplify_2_0&utm_medium=social (Accessed February 19, 2025).
Simeone, A., Deng, B., Watson, N., and Woolley, E. (2018). Enhanced clean-in-place monitoring using ultraviolet induced fluorescence and neural networks. Sensors 18:742. doi: 10.3390/s18113742
Simeone, A., Woolley, E., Escrig, J., and Watson, N. J. (2020). Intelligent industrial cleaning: A multi-sensor approach utilising machine learning-based regression. Sensors 20:642. doi: 10.3390/s20133642
Solari, F., Lysova, N., and Montanari, R. (2023). Digital twin based on historical data and simulation results: fault detection and estimation of the remaining useful life of a cyclone bag filter. Appl. Sci. 13:8297. doi: 10.3390/app13148297
Tancredi, G., Bottani, E., and Vignali, G. (2021). Digital twin application for the temperature and steam flow monitoring of a food pasteurization pilot plant. Nantes, France: IFIP International Conference on Advances in Production Management Systems (APMS). 612–619. doi: 10.1007/978-3-030-85902-2_65
Tancredi, G. P. C., Bottani, E., and Vignali, G. (2023). Digital twin-enabled process control in the food industry: proposal of a framework based on two case studies. Int. J. Prod. Res. 62, 4331–4348. doi: 10.1080/00207543.2023.2260495
Tancredi, G. P., Vignali, G., and Bottani, E. (2022). Integration of digital twin, machine-learning and industry 4.0 tools for anomaly detection: an application to a food plant. Sensors 22:4143. doi: 10.3390/s22114143
Tao, F., Qi, Q., Wang, L., and Nee, A. Y. C. (2019). Digital twins and cyber–physical systems toward smart manufacturing and industry 4.0: correlation and comparison. Engineering 5, 653–661. doi: 10.1016/j.eng.2019.01.014
Tshabalala, P., and Kuriakose, R. B. (2023). “Designing an experimental setup for digital twins in modern manufacturing—A case study using a water bottling plant” in ICT Systems and Sustainability. eds. M. Tuba, S. Akashe, and A. Joshi (Cham: Springer Nature), 615–622.
Udugama, I. A., Lopez, P. C., Gargalo, C. L., Li, X., Bayer, C., and Gernaey, K. V. (2021). Digital twin in biomanufacturing: challenges and opportunities towards its implementation. Syst. Microbiol. Biomanufact. 1, 257–274. doi: 10.1007/s43393-021-00024-0
Ureta, M. M., and Salvadori, V. O. (2022). A review of commercial process simulators applied to food processing. J. Food Process Eng. 46:e14225. doi: 10.1111/jfpe.14225
Valero, M. R., Hicks, B. J., and Nassehi, A. (2023). “A conceptual framework of a digital-twin for a circular meat supply chain” in Lecture notes in mechanical engineering. eds. F. Chaari, F. Gherardini, V. Ivanov, and M. Haddar (Cham: Springer International Publishing).
Verboven, P., Defraeye, T., Datta, A. K., and Nicolai, B. (2020). Digital twins of food process operations: the next step for food process models? Curr. Opin. Food Sci. 35, 79–87. doi: 10.1016/j.cofs.2020.03.002
Vetter, F. L., and Strube, J. (2022). Enabling Total process digital twin in sugar refining through the integration of secondary crystallization influences. PRO 10:373. doi: 10.3390/pr10020373
Vignali, G., and Bottani, E. (2020). A tube-in-tube food pasteurizer modelling for a digital twin application. 6th international food operations and processing simulation workshop. Food OPS 2020, 30–36. doi: 10.46354/i3m.2020.foodops.005
Wagner, R., Schleich, B., Haefner, B., Kuhnle, A., Wartzack, S., and Lanza, G. (2019). Challenges and potentials of digital twins and industry 4.0 in product design and production for high performance products. PRO 84, 88–93. doi: 10.1016/j.procir.2019.04.219
Wang, F., Song, Y., Liu, C., He, A., and Qiang, Y. (2023). Multi-objective optimal scheduling of laminar cooling water supply system for hot rolling mills driven by digital twin for energy-saving. J. Process Control 122, 134–146. doi: 10.1016/j.jprocont.2023.01.004
Wang, L., Törngren, M., and Onori, M. (2015). Current status and advancement of cyber-physical systems in manufacturing. J. Manuf. Syst. 37, 517–527. doi: 10.1016/j.jmsy.2015.04.008
Wari, E., and Zhu, W. (2019). A constraint programming model for food processing industry: a case for an ice cream processing facility. Int. J. Prod. Res. 57, 6648–6664. doi: 10.1080/00207543.2019.1571250
Watson, N. J., Bowler, A. L., Rady, A., Fisher, O. J., Simeone, A., Escrig, J., et al. (2021). Intelligent sensors for sustainable food and drink manufacturing. Front. Sustain. Food Syst. 5:642786. doi: 10.3389/fsufs.2021.642786
Xia, K., Sacco, C., Kirkpatrick, M., Saidy, C., Nguyen, L., Kircaliali, A., et al. (2020). A digital twin to train deep reinforcement learning agent for smart manufacturing plants: environment, interfaces and intelligence. J. Manuf. Syst. 58, 210–230. doi: 10.1016/j.jmsy.2020.06.012
Keywords: food processing industry, digital model, digital shadow, Digital Twin, simulation tools, industry 4.0, sustainability
Citation: Abdurrahman EEM and Ferrari G (2025) Digital Twin applications in the food industry: a review. Front. Sustain. Food Syst. 9:1538375. doi: 10.3389/fsufs.2025.1538375
Edited by:
Jagadeesh Yeluripati, The James Hutton Institute, United KingdomReviewed by:
Orhan Korhan, Eastern Mediterranean University, CyprusKrist V. Gernaey, Technical University of Denmark, Denmark
Copyright © 2025 Abdurrahman and Ferrari. This is an open-access article distributed under the terms of the Creative Commons Attribution License (CC BY). The use, distribution or reproduction in other forums is permitted, provided the original author(s) and the copyright owner(s) are credited and that the original publication in this journal is cited, in accordance with accepted academic practice. No use, distribution or reproduction is permitted which does not comply with these terms.
*Correspondence: Giovanna Ferrari, Z2ZlcnJhcmlAdW5pc2EuaXQ=
†ORCID: Emadaldin Elfatih M. Abdurrahman, orcid.org/0009-0002-1581-9003