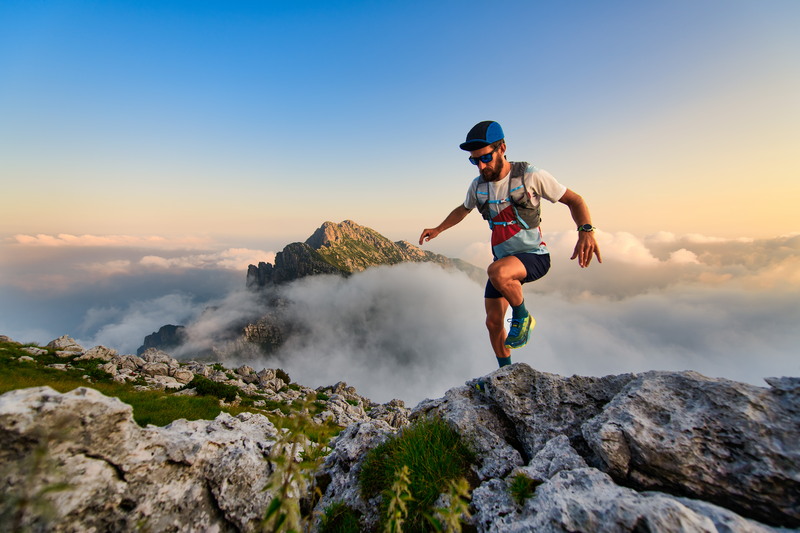
95% of researchers rate our articles as excellent or good
Learn more about the work of our research integrity team to safeguard the quality of each article we publish.
Find out more
ORIGINAL RESEARCH article
Front. Sustain. Food Syst. , 19 July 2024
Sec. Waste Management in Agroecosystems
Volume 8 - 2024 | https://doi.org/10.3389/fsufs.2024.1406962
This article is part of the Research Topic RAMIRAN 2023: Managing Organic Resources in a Changing Environment View all 15 articles
The ammonia (NH3) stripping process can recover nitrogen (N) from slurry and digestates as a mineral fertilizer, but it is currently expensive and difficult to manage at the farm level. Hence, a simple process is required. This study aimed to test a modular (based on farm N surplus) slow-release NH3 stripping process at a pilot plant scale. NH3 volatilization was promoted in a closed reactor, and then, the NH3 was removed by an air stream through the reactor headspace. The NH3-loaded air was purified in a scrubber, where NH3 reacted with sulfuric acid to form ammonium sulfate (AS). In total, 11 trials were conducted using pig slurry, dairy cattle slurry, and digestates: 7 trials were carried out with the reactors heated to 40°C, 2 trials were carried out at an ambient temperature, and the other 2 trials were carried out with the addition of sodium hydroxide (NaOH). To assess the technical–economic sustainability of the pilot plant, the total ammoniacal nitrogen (TAN) removal rate, electricity consumption, acid requirements, and AS quality and costs were evaluated. The pilot plant yielded TAN recovery amounts of 45% in 2 weeks with the reactors heated to 40°C, 64% in 1 week with NaOH addition, and 25% in 2 weeks at an ambient temperature. The N concentration in the AS solution reached 85.9 g kg−1, with an average value of 35.2 g kg−1. The electricity consumption, acid requirement, and operational costs in an optimized system were approximately 0.52 kWh kgN−1 recovered, 3.5 kg pure acid kgN−1 recovered, and 0.86 € kgN−1 recovered, respectively. Compared to other technologies, the simplified stripping process is slower but with similar removal efficiencies and lower energy consumption. Thus, this finding could be suitable for improving the N use in intensive livestock farms.
In a well-balanced system where nutrient inputs and crop requirements offset each other, livestock manure and digestates are valuable sources of crop nutrients. However, in regions with highly intensive livestock farming, there are high nitrogen (N) loads compared with the available land for proper livestock manure application in accordance with the Nitrates Directive (91/676/EEC) (Velthof et al., 2014). The increased livestock density has resulted in an excess of plant nutrients, particularly N, in European livestock farms. These surpluses pose environmental risks, such as ammonia (NH3) volatilization and nitrate (NO3−) leaching, leading to the potential eutrophication of ecosystems (Sommer, 2013).
To reduce these pollution phenomena, it is necessary to adopt treatment systems that reduce the N load of the effluents (EC DGE, 2016). In particular, there is an increasing need to reduce excess N in critical areas without eliminating N but by recovering it in a more easily manageable form within the same farm or in a form that is transportable to other areas (Huygens et al., 2020).
Nutrient recovery from slurry and digestates has been deemed feasible, with membrane technologies, struvite precipitation, and NH3 stripping as the most extensively studied processes (Rizzioli et al., 2023). Pressure-driven membrane technologies, including ultrafiltration and reverse osmosis, are gaining significance as crucial processes for nutrient recovery. Despite their non-selective nature, the primary limitation of these membrane processes is membrane fouling. This fouling hinders their widespread implementation on a large scale because of the challenges associated with effective management. Struvite precipitation is a method that enables the recovery of phosphorus and NH3 in the form of a magnesium (Mg) ammonium (NH4+) phosphate (PO43−) hexahydrate (6H2O) mineral. This process is primarily used in the municipal sector, particularly for treating anaerobic sewage sludge digestates. However, its application in the agricultural sector is relatively infrequent, as outlined by Rizzioli et al. (2023). NH3 stripping is the most developed technology in the European Union (EU) context, as noted by Rizzioli et al. (2023) It allows the removal of ammonia nitrogen (N-NH3) from the slurry by retaining it in an acid solution, usually sulfuric acid (H2SO4), to form ammonium sulfate (AS) (Vaneeckhaute et al., 2017; Pandey and Chen, 2021). Ammonia stripping is recognized as an effective technique, with N removal rates of up to 90–95% after treatment for a few hours (Flotats et al., 2011; Vaneeckhaute et al., 2017). This process is usually performed in packed-bed stripping towers to increase the available area for mass transfer, requiring a high removal rate of the solids in the slurry to avoid stripping column clogging, as well as the high demand for heat or chemical additives (Provolo et al., 2017; Pandey and Chen, 2021; Rizzioli et al., 2023).
Despite its applications in waste treatment plants (Brienza et al., 2021; Pigoli et al., 2021), the diffusion of NH3 stripping in livestock farms is still very limited (Rizzioli et al., 2023).
The driving forces of the NH3 stripping process are those that favor the volatilization of NH3 from the slurry, such as high temperature, pH, and airflow velocity, all of which are required to remove the released NH3 from the slurry (Flotats et al., 2011).
However, the electricity required to produce 1 kg of N as AS by treating digestates and slurry with stripping processes (at ambient temperature or recovering heat surplus from other processes, i.e., combined heat and power (CHP) engine of a biogas plant) is approximately 3.8–12 kWhel (Brienza et al., 2021, 2023). In comparison, the Haber–Bosch optimized process requires 9.5 kWhel to produce 1 kg of N as chemical fertilizer (Smith et al., 2020). Therefore, an optimized and/or simplified NH3 stripping process is required to produce renewable fertilizers more sustainably from digestates and slurry (Brienza et al., 2021; Vingerhoets et al., 2023).
The slow-release stripping system can be a valid solution to simplify the treatment, making it more easily applicable to livestock farms (Provolo et al., 2017; Heidarzadeh Vazifehkhoran et al., 2022). This system requires that volatilized NH3 is removed by an air stream through the headspace of the reactor without using a stripping tower. Thus, a reduced need for strong solid–liquid separation of the initial slurry/digestates and reduced risks of clogging and foam formation is observed. In addition, slow-release stripping can work at a process temperature of approximately 40°C, which can be maintained by taking advantage of the heat produced by a CHP engine in anaerobic digestion plants that are often dissipated to the environment. Furthermore, slow-release stripping takes advantage of the natural increase in pH taking place due to the fast carbon dioxide (CO2) volatilization (Hafner et al., 2012).
In the laboratory-scale trials conducted by Provolo et al. (2017) and Heidarzadeh Vazifehkhoran et al. (2022), an NH3 removal efficiency of 70–80% was obtained at 40°C after approximately 2 weeks of treatment. Ammonia removal efficiencies close to 90% were achieved by extending the treatment to 3 weeks (Heidarzadeh Vazifehkhoran et al., 2022) or adjusting the pH to 9 using sodium hydroxide (Provolo et al., 2017).
The strength of the NH3 stripping process is the production of AS, a mineral fertilizer regarded as a renewable substitute for synthetic fertilizers (Vaneeckhaute et al., 2013; Sigurnjak et al., 2016). AS has a higher N content compared to slurry or digestates: 4–7.4% (Pigoli et al., 2021) vs. 0.13–0.93%, for pig slurry and digestate, respectively (Finzi et al., 2015). The same amount of N is therefore contained in a lower volume, reducing the transport costs for AS.
The implementation of the slow-release NH3 stripping process on a farm scale will have important effects on the nutrient management of livestock slurries, which is in line with the objectives of the European Commission’s Farm to Fork strategy (reduce nutrient losses by at least 50% by 2030), and specifically with the principle of recycling of organic waste into renewable fertilizers.
To test the performance of the slow-release NH3 stripping process on a farm, the laboratory prototype tested by Provolo et al. (2017) and Heidarzadeh Vazifehkhoran et al. (2022) was upscaled to a farm-scale pilot plant with a reactor capacity of 30 m3. In this pilot plant, trials were conducted using different slurries (pig, cattle, and digestates) to assess the process performance by evaluating the amount of N recovered as mineral fertilizer, i.e., AS; the quality of the AS obtained in terms of N content; and the energy and (H2SO4) requirements of the process. A technical–economic sustainability assessment was also included.
Pilot plant functioning was based on the slow-release NH3 stripping process conducted under batch conditions. In this process, the recovery of NH3 from the slurry or digestates occurred in a reactor, where air was introduced into the headspace. The airflow served a dual purpose: to encourage the release of NH3 from the surface of the slurry or digestates and to carry it away. The NH3-laden airflow was then directed into a wet scrubber, where NH3 reacted with a (H2SO4) solution, resulting in the formation of AS.
The pilot plant (Figure 1) had a 30-m3 steel tank to receive the input slurry and digestates to be treated, from which a centrifugal pump (7.5 kW) sent the input slurry/digestates to a screw-press solid–liquid separator (SEPCOM Biogas Vertical—WAM Italia S.p.A, 4 kW, screen 0.25 mm) to remove coarse solids. The liquid fraction was collected in three 7.5-m3 high-density polyethylene (HDPE) tanks equipped with a radar sensor for electronic level measurement (VEGAPULS 31, Vega). A progressive cavity pump (C.M.O. Pompe s.n.c., 1.8 kW) loaded and emptied the liquid fraction into four 7.5-m3 HDPE stripping reactors. Each reactor was equipped with the following: a heating system using hot water circulated in a pipe exchanger inside the tank, a mechanical mixing system using an electric motor with a vertical paddle mixer (100 rpm), a temperature and pH sensor (B&C electronics PH 4326; probe B&C electronics SZ165), a slurry level sensor (VEGAPULS 31, Vega), and an effluent sampling valve. The hot water, which is used to heat the reactors, was produced by an electric boiler (36 kW) that simulates the available heat from a biogas plant. The reactors were half-filled at a volume of 3.75 m3, and the airflow necessary for NH3 recovery was ensured by a blower (Project Plast, Cremona, Italy, 2.2 kW, 2000 m3 h−1) that operated in a closed circuit and connected the reactors and scrubbers. The scrubber had a tank containing an acid solution for cleaning NH3-laden air from the reactors. As the acid was gradually neutralized to form AS, it became necessary to add more acid. This was done when the solution reached a pH of 1.5, as suggested by Sigurnjak et al. (2019). The pilot plant was monitored and controlled using a programmable logic controller (PLC), which could also be remotely accessed.
The experimental trials were conducted in the pilot plant under batch conditions (Table 1). Seven trials (i.e., Pig1, Pig2, Pig3, Dig1, Dig2, Cattle1, and Cattle2) were conducted by heating the stripping reactors at 40°C. Considering that an electric boiler was used for heating the reactors, an upscaling of the pilot plant is feasible only with a surplus heat to be valorized (i.e., from a CHP of a biogas plant). Otherwise, it is advisable to conduct the treatment at ambient temperature or with the addition of additives. For this reason, trials Pig4.at and Cattle3.at were conducted at ambient temperature, and trials Pig5.sh and Cattle4.sh were conducted at ambient temperature (at) with the addition of sodium hydroxide (i.e., sh; NaOH 30% w/w). NaOH 30% w/w was added to the reactor before starting the trial to increase the pH. It was necessary to add 30.4 kg and 59.4 kg of a previously prepared solution of NaOH 30% w/w per cubic meter of slurry to raise the pH to 10.7 for cattle slurry (Cattle4.sh) and pig slurry (Pig5.sh), respectively.
Table 1. Experimental conditions of the trials performed. sh = sodium hydroxide, NaOH 30% w/w; at = ambient temperature.
The trials were monitored using the following procedure:
• During the trials, every 5 min, the PLC recorded the pH, temperature, and level values of the reactors and the pH of the scrubber.
• The sampling of the slurry/digestates of each reactor and the AS solution in the scrubber was conducted at the start of the trial, during the trial every 72–96 h, and at the end of the trial.
Furthermore, during each sampling, the level of the AS solution inside the scrubber tank was manually measured and recorded. When the safety level for AS was exceeded, the AS solution was unloaded by a dosing pump (model BT-MA/AD, Etatron D.S., Rome – Italy), and if necessary, more acid (H2SO4 at 50% w/w) was added to the scrubber, by a dosing pump (model Tekna Evo AKL 803, SEKO, Rieti – Italy). Each acid/AS load/unload was measured and recorded by the operator.
• At each sampling, electricity consumption was recorded from the plant’s electricity meter.
A total of 196 samples were collected during the trials. The samples were stored at +4°C and analyzed within 24 h, to determine the content of total solids (TS), volatile solids (VS), ash, total Kjeldahl nitrogen (TKN), total ammoniacal nitrogen (TAN), pH, EC, phosphorus (P), and potassium (K). In particular, P and K were evaluated using the rapid tests NANOCOLOR 0–55 (REF 985055) and NANOCOLOR 0–45 (REF 985045), respectively. All parameters were analyzed using standard methods (APHA/AWWA/WEF, 2012). Otherwise, organic N was derived by subtracting the TAN content from the TKN content.
The concentrations of the major elements (Na, Mg, Ca, K, and P) and trace elements (Al, Cr, Mn, Fe, Co, Ni, Cu, Zn, As, Se, Mo, Cd, and Pb) in the AS solution were analyzed by inductively coupled plasma mass spectrometry (EPA, 2007; APHA/AWWA/WEF, 2012) using an ICP-MS (Bruker Aurora-M90).
The results obtained from the tests conducted in the pilot plant allowed us to evaluate its performance under different conditions, in terms of both the type of slurry treated (different animal species and farms; chemical and physical compositions) and the test conditions (warm and cold seasons, treatment duration). All the trials have been performed at least in duplicate, but a statistical analysis to compare the different trials has not been reported due to the mentioned different conditions. However, an in-depth evaluation of how such plants would work in practice has been performed.
Using both the results of the analyses on the samples and the data recorded during monitoring, the performance of the pilot plant was evaluated in terms of the TAN removal rate, TKN removal rate, and slurry volume reduction during the stripping treatment.
To determine the percentage of removal efficiencies achieved by the pilot plant, the difference between the effluent and influent masses of the above-mentioned parameters was considered.
The technical performances of the process were assessed by interpolating the TAN removal efficiency achieved in the pilot plant trials with heated reactors, to define a regression model over time considering the results of all trials performed. For the trials conducted at ambient temperature or with NaOH addition, the TAN removal efficiency was assessed by averaging the values obtained from the trials. The electricity consumption, acid requirement, and NaOH addition (when used) were then evaluated to determine the operational costs of the process and its economic sustainability.
Furthermore, the AS solution was evaluated in terms of quantity by assessing its N concentration and the mass of AS produced.
The electricity consumption recorded in each trial included the pretreatment of solid–liquid separation; reactor loading and unloading; reactor mixing, heating, and aeration; scrubber functioning; and PLC. Considering that electricity was used in the pilot plant to heat the reactors, the electricity consumption and thermal energy consumption have been analyzed separately. The H2SO4 requirement was the amount introduced into the scrubber during each trial, whereas the NaOH requirement was the amount added to the slurry or digestates in the reactors. The operational costs related to electricity consumption were 0.2297 € kWh−1 as determined from the annual report referred to in 2021 by the Italian Regulatory Authority for Energy, Networks, and Environment (ARERA). In the trials with reactors heated to 40°C, the costs do not include the electricity consumption resulting from heating, considering that an upscaling of the pilot plant is feasible only with a surplus heat to be valorized. The cost of pure H2SO4 and NaOH 30% w/w were, respectively, 0.21 and 0.21 € kg−1 (Vingerhoets et al., 2023). Consumption and costs were expressed per unit of N removed in each trial.
In addition to the treatment costs, it is worth noting that the AS solution produced has an economic value as a mineral fertilizer. Because there is no market for this product, the value of AS was considered a cost avoided in the purchase of mineral fertilizers based on the price of 1 kg of N as urea (46% N), with reference to the average market price in Europe in spring 2023 (March, April, and May) equal to 495 €/t, i.e., 1.08 € kgN−1 (WUR, 2024).
Based on the performance achieved in the pilot plant, a generalized mass and N balance was defined, considering the likely operating conditions of the upscaled process at full scale. The mass balance was based on the following 5 conditions: (1) setting a TAN removal rate that could be considered affordable; (2) the mass of the input slurry treated was equal to the treatment capacity of the pilot plant; (3) the mass of the output slurry was calculated considering a small volume reduction of the treated slurry, due to water evaporation; (4) the mass of the AS solution was obtained by calculating the amount of acid required to retain a given amount of TAN removed from the stripping reactors; (5) and the N in the output slurry was the difference between the N in the input slurry and that in the AS solution. The effect of input slurry dilution on the quality of the achievable AS solution was evaluated by comparing slurries with different initial TKN and TAN contents. Regarding upscaling the process, an assessment has been made based on the expected N removal performance and the associated electricity consumption, acid requirements, and operating costs.
The analyses reported in Table 2 refer to the mean values of the samples collected from each reactor at the beginning of each trial. The TS content of the treated slurries in trials Pig5.sh and Cattle4.sh also included the addition of NaOH.
The cattle slurry used in trials Cattle1 and Cattle2 had a high dilution with TS and lower nutrient content than that found in samples taken in the same area (Finzi et al., 2015). This was due to the consistent use of cooling systems based on the use of water (showers) during the period in which the slurry was treated in the pilot plant. The cattle slurry used in the trial in Cattle3.at was collected in a barn that did not have cooling systems with showers and therefore had a higher TS and nutrient content.
The digestates had a lower TS and nutrient content than that found in the same area (Finzi et al., 2015) probably because they were obtained from biogas plants fed mainly with livestock slurries (supplemented with small amounts of energy crop silage). In the Dig1 trial, the digestate used was from a biogas plant fed with pig slurry, while in the Dig2 trial, the digestate used was from a biogas plant fed with cattle slurry. Conversely, the pig slurry had a TS and nutrient content in line with (Pig1, Pig2, and Pig3) or higher (Pig4.at) than the values recorded in the same area (Finzi et al., 2015).
The results of the trials conducted (Table 3) showed TKN removal rates between 42 and 72% and TAN removal rates between 35 and 79% in the trial with reactors heated to 40°C; TKN removal rates between 3 and 26% and TAN removal rates between −5 and 25% in the trial with reactors kept at ambient temperature; and TKN removal rates between 50 and 67% and TAN removal rates between 76 and 82% in the trial with pH reactors adjusted to 10.7. The values depended on the treatment duration, which differed among trials. The TKN removal rate was lower than the TAN removal rate because the stripping treatment affected the amount of ammoniacal N. The TKN removal rate was higher than the TAN removal rate only in trials Pig2 and Cattle3.at. In trial Pig2, this removal effect could be due to a lower TAN/TKN ratio of the treated pig slurry compared with the expected values for this type of slurry (Finzi et al., 2015). The low TAN/TKN ratio could be due to the high content of organic N. A fraction of organic N had undergone a mineralization process (equal to 27% of the initial TKN content), producing TAN and leading to higher removal of TKN compared with TAN, the content of which was increased by the amount of organic N mineralized. In fact, organic N transformation to ammonium is temperature-dependent, as it is related to the transformation of organic matter. Sommer et al. (2007) observed the highest rates during the storage of pig slurry at 20°C in the initial period of 10–15 days when mineralization of organic N of approximately 19% (relative to the initial TKN content). In trial Cattle3.at, the removal effect could be due to the very slow TAN removal because the mineralization rate of organic N was 6%, consistent with the mean value of 10% found in other trials.
During the treatment, together with NH3, a part of the water in the effluent also evaporated. A slurry/digestates volume reduction from 3 to 23% was observed in the trials with reactors heated to 40°C. The reduction in the volume of the treated effluent was very variable and depends on the duration of the treatment. It may seem like an additional advantage to be able to reduce the volume of the effluent in addition to N, but this would be true if water exits the process. However, these results were only due to the absence of insulation of pipes and scrubbers in the pilot plant. The water vapor in the exhaust air from the reactors condensed in the pipes and scrubber, especially when the external temperature was significantly lower than that of the reactor. The volume reduction can be limited in an insulated installation, or when the external temperature is close to the temperature of the reactor. The volume reduction in trial Pig1 was 3% after 15 days of treatment, with an average difference of 13.6°C between the temperatures in the reactors and the external temperature. The trials carried out at ambient temperature, with a temperature difference of 3.7–4.3°C, had a volume reduction of 1–3% in a process of 15–21 days. A higher volume reduction (23%) occurred in trial Pig3 with a temperature difference of 27.2°C and a duration of 28 days.
The TAN removal efficiencies achieved in the trials at 40°C were used to define a simple regression model over time that provides an achievable performance, regardless of the slurry characteristics and treatment duration (Figure 2). Each point on the graph corresponds to 1 sampling day and represents the removal of the TAN content from the start of the trial; 1 week after the start of treatment, a TAN removal rate of approximately 25% can be expected, 45% after 2 weeks, and 55% after 3 weeks. These average removal rates fit within a confidence interval, presenting an overall margin of variability of approximately ±15%, linked to the different operating conditions. The advantage of this process is the possibility of modulating the intensity of the treatment. The treatment can be stopped at any time once the necessary N removal level has been reached, based, for example, on the N surplus that a livestock farm has to manage. By observing the levels of TAN removal as a function of treatment time, the process highlights higher removal rates in the early stages. This means that longer treatment times allow higher levels of overall removal, but in the advanced stage of the process, the TAN release rate is lower than that in the initial stage. Therefore, each unit of N removed in this stage will have a higher unit cost.
Considering the trend in the removal of TAN, as shown in Figure 2, and based on the increased knowledge gained during the trials conducted in the pilot plant, a treatment duration of 2 weeks resulted as a tradeoff between the achievable N removal rate and consumption/costs. In detail, after 2 weeks of treatment, the performances shown in Figure 3 were achieved. In trials with reactors heated to 40°C, the digestates showed an average TAN removal rate of 54%, compared with 35% for cattle slurry and 34% for pig slurry. Without considering the Pig2 trial, which was characterized by high N mineralization, the average removal rate of TAN from pig slurry was 47%. The trials conducted at ambient temperature showed significant variability, with the Pig4.at trial close to 25% of TKN removal and the Cattle3.at trial characterized by high N mineralization. The trials with NaOH addition showed higher values than the other trials, with an average TAN removal rate of 76%. It should be noted that the addition of NaOH allowed a TAN removal rate of 64% to be achieved after just 1 week of treatment.
The amount and N concentration of the AS solution showed variability among the trials conducted, due to treatment duration and the ambient temperature during each trial.
In the trials with high slurry/digestates volume reduction, the water evaporated from the reactors condensed in the scrubber diluting the AS solution. The level of the scrubber tank also increased the necessity of emptying the AS solution before it became saturated with NH3 to prevent spilling liquid from the scrubber.
In trial Pig1 conducted with the heated reactors and low slurry volume reduction, the N concentration of the AS solution reached 69.7 g kg−1 (AS solution concentration of 33.2% w/w). Therefore, in the trials with high slurry volume reduction, the concentration of N in AS was low (5.7–44.0 g kg−1 of N).
Due to the high N removal rate of the Pig5.sh trial, conducted by adding NaOH and at ambient temperatures during the summer period (approximately 30°C of slurry temperature), the N concentration of the AS solution reached the maximum value of 85.9 g kg−1 (AS solution concentration of 40.9% w/w).
In addition to the N content, the AS solution was also characterized for total solids and major and trace element contents, which are reported in Table 4.
Table 4. Characteristics of the AS solution obtained, in terms of total solids, major elements, and trace elements.
The electricity consumption of the pilot plant related to electricity usage, such as reactor mixing, pumping, and airflow generation, was determined during the trials conducted at ambient temperature and was found to be an average of 0.25 kWhel m−3 treated per day. This consumption was considered for each trial.
Regarding the daily electricity consumption related to TKN removal, in the trials with the heated reactors, the electricity consumption ranged between 0.11 and 0.33 kWhel kgN−1 removed per day for the Dig1 and Cattle2 trials, respectively. The lowest value in the Dig1 trial was due to the high TKN removal efficiency (72%) of a digestate with a TKN of 3.05 g kg−1, compared with a TKN removal efficiency (46%) of a cattle slurry with a TKN of 1.67 g kg−1. In the trials at ambient temperature with the addition of NaOH, the electricity consumption ranged between 0.07 and 0.18 kWhel kgN−1 removed per day for the Pig5.sh and Cattle4.sh trials, respectively, due to the ambient temperature of approximately 26°C. In the trials conducted without the addition of NaOH, the electricity consumption ranged between 0.18 and 2.62 kWhel kgN−1 removed per day for the Pig4.at and Cattle3.at trials, respectively. This large difference was related to the higher removal of TKN in trial Pig4.at (26%) compared with the 3% found in trial Cattle3.at.
The energy required for heating the reactors was highly dependent on the season during which the trial was conducted. In the summer period with ambient temperatures from 23.2°C to 27.2°C (Pig1, Dig1, and Cattle1), the thermal energy consumption was within the range of 0.37–0.44 kWhth m−3 treated per day. The maximum value was obtained in trial Dig1, which lasted for 32 days, leading to a reduction in TKN of 72%, whereas the minimum value was obtained in trial Pig1, which lasted for 15 days, leading to a reduction in TKN of 42%. Increasing the treatment time to achieve higher N removal rates leads to higher electricity consumption expressed per unit of volume treated per day. This is because the TAN release rate slowed down as the treatment time increased (Figure 2).
The thermal energy consumption referred to daily N removal between 0.20 and 1.56 kWhth kgN−1 removed per day, where the minimum consumption was observed in Dig1 and Pig1 trials and the maximum was observed in Cattle1. In the Cattle1 trial, the initial TKN content of 1.25 g kg−1 was lower than that in the Dig1 and Pig1 trials with TKN contents of 3.05 and 4.25 g kg−1, respectively. This means that it is energetically prejudicial to treat diluted slurry.
In trials conducted with colder ambient temperatures between 11°C and 17°C (Cattle2, Dig2, Pig2, and Pig3), the heating electricity consumption ranged between 0.62 and 1.42 kWhth m−3 treated per day, respectively, for trials Pig2 (temperature 17.3°C, duration 28 days, and TKN removal rate of 44%) and Cattle2 (temperature 11°C, duration of 31 days, and TKN removal rate of 46%). Regarding the colder season, this resulted in consumption ranging from 0.60 to 1.88 kWhth kgN−1 removed per day for trial Pig2 and Cattle2, respectively. The lower temperature and the longer treatment time required in trial Cattle2 led to much higher energy consumption compared with trial Pig2.
Overall, regarding N removal, the electricity consumption varied between 2.69 and 55.01 kWhel kgN−1 removed in the trials at ambient temperature, 1.04–3.74 kWhel kgN−1 removed in the trials with NaOH addition, and 2.04–10.21 kWhel kgN−1 removed in the trials with the reactors heated, respectively, for trials Pig1 and Cattle2. The thermal energy consumption of all the trials with heated reactors ranged from 3.04 to 58.31 kWhth kgN−1 removed for trials Pig1 and Cattle2, respectively.
The acid requirement depends on both the amount of N retained and the amount of condensed water in the scrubber (see par. 3.1.2). The theoretical requirement calculated based on the stoichiometric ratio in the AS formation reaction is equal to 3.5 kg of H2SO4 for each kg of N removed.
The amount of acid used (expressed as pure acid) varied between 5.7 and 18.9 kg acid per kgN−1 removed or 5.0–20.2 kg acid m−3 treated in the trials with heated reactors and between 5.3 and 12.5 kg acid per kgN−1 removed or 11.6–12.3 kg acid m−3 treated in the trials with the reactors at ambient temperature and in the trials with NaOH addition.
The trials Pig1, Dig1, and Pig5.sh conducted at warm ambient temperatures (23.2°C–27.2°C) showed that the acid requirement per unit of N removed was between 5.3 (Pig5.sh) and 7.2 (Dig1) kg acid per kgN−1 removed compared with trial Cattle2, which had a requirement of 18.9 kg of acid per kgN−1 removed as the low ambient temperatures (11.4°C).
Overall, the treatment costs varied between 1.66 and 4.20 € kgN−1 removed in the tests with the reactors heated, between 0.93 and 12.80 € kgN−1 removed in the tests with the reactors at ambient temperature, and between 4.43 and 7.93 € kgN−1 removed in the tests with NaOH addition. The cost of the stripping process could be partially recovered from the sale of the AS solution. The obtainable benefit, expressed as the surrogate value of N recovered as AS solution, was assumed to be 1.08 € kgN−1. This income could even exceed the operating costs, making the treatment profitable. Specifically, in the Pig4.at trial, the potential profit was 0.15 € kgN−1.
Furthermore, the treatment costs have been split between electricity consumption and H2SO4 and NaOH requirements to evaluate the share of individual cost items on the overall cost.
The costs related to electricity consumption varied between 0.47 and 2.34 € kgN−1 removed in the trials with the reactors heated, between 0.62 and 12.64 € kgN−1 removed in the trials with the reactors at ambient temperature, and between 0.24 and 0.86 € kgN−1 removed in the trials with NaOH addition. Specifically, the lowest costs were obtained in trials Pig1, Pig4.at, and Pig5.sh, where a high efficiency in N removal was achieved within 2 weeks of treatment.
Regarding the H2SO4 requirements, the costs varied between 1.01 and 2.41 € kgN−1 removed in the trials with the reactors heated, between 0.17 and 0.31 € kgN−1 removed in the trials with the reactors at ambient temperature, and between 0.80 and 2.47 € kgN−1 removed in the trials with NaOH addition. The lowest costs were obtained in trials Pig2, Cattle3.at, and Pig5.sh.
The costs resulting from the use of NaOH varied between 3.40 (Pig5.sh) and 4.60 (Cattle4.sh) € kgN−1 removed.
The results of the trials conducted show TKN removal rates between 40 and 70% and TAN removal rates between 50 and 80%. These removal rates were similar to those found in other studies at the laboratory scale based on the slow-release stripping process. Provolo et al. (2017) found that the highest TAN removal efficiency (87%) was obtained at 40°C with pH adjusted to 9 using sodium hydroxide. However, at 40°C without pH adjustment, removal efficiencies of 69% for TAN and 47% for TKN were obtained in 10 days. Heidarzadeh Vazifehkhoran et al. (2022) reached TAN removal rates of 92, 83, and 67% with 20 days of hydraulic retention time (HRT) and 83, 60, and 41% with 12 days of HRT from the digestates, pig slurry, and dairy cattle slurry, respectively.
Regarding the stripping process at the pilot scale, there are studies in the literature (Baldi et al., 2018; Brienza et al., 2023; Vingerhoets et al., 2023), where the treatment was performed by treating the slurry in stripping towers. Vingerhoets et al. (2023) treated a liquid fraction of a digestate for 2-3 h and obtained significantly improved N removal efficiency, from 27% to 40%, by raising the pH from 8 to 10 at a temperature of 30°C and an airflow rate of 1,440 m3 h−1. At ambient temperature, Brienza et al. (2023) found a TKN removal rate of 21% (32% TAN removal) from a liquid fraction of anaerobically digested pig slurry with a pH of 8, treated during three periods between spring and autumn, in a pilot plant with the capacity to process approximately 1 ton per hour. In the present study, treating pig slurry with a pH of 7.9, a comparable TAN removal rate of 25% was obtained at ambient temperature of 30°C (Pig4.at), while a higher TAN removal rate of 82% (Pig5.sh) was obtained by increasing pH from 7.9 to 10.7 (Figure 3). In both cases, 2 weeks of treatment were necessary, much longer than the few hours reported by Brienza et al. (2023) and Vingerhoets et al. (2023).
Using our pilot plant, the addition of NaOH allowed TAN removal rates 1.9 times higher than those achieved when heating the reactors to 40°C, consistent with the findings of Baldi et al. (2018), who reported TAN removal rates of 1.6 times higher in trials with pH adjusted to 10.5 using NaOH addition, compared with trials without pH modification. Baldi et al. (2018) obtained on a full-scale plant a removal efficiency of 59–66% on digestate with pH increased to 10.5 by adding NaOH and treated for 6 h at 56°C–58°C in a continuous process, and they achieved a higher removal efficiency of 79% in a semi-batch process on digestate with pH increased to 10.1, treated for 6 h at 52°C. In the trials without NaOH addition, conducted at a temperature of 45–55°C and a pH of 9.2–9.5, they obtained a lower N removal rate (23–39%). A similar result was found by Bolzonella et al. (2018), who reached a removal efficiency of 22% when performing a stripping trial on digestates at a temperature of 60–70°C. In our study, the trials conducted at 40°C achieved TAN removal rates, ranging from 10% (Pig2) to 62% (Dig2), but after 2 weeks of treatment.
Compared to the pilot-scale slow-release stripping process tested in this study, the cited studies that treated slurry in stripping towers achieved comparable N removal rates, although with shorter treatment times. The main difference in the process was due to the lower surface of liquid exposed to air in the slow-stripping process, as the slurry was just mixed in the reactor without creating drops or enhancing the surface with packed beds. In fact, similar results were obtained but using a higher overall quantity of air. Considering the G/L ratio, defined by Palakodeti et al. (2021) as the ratio of the total volume of used gas to the volume of the stripped liquid, in our case, the value was approximately 44,000 compared to values well below 10,000 for packed beds (Palakodeti et al., 2021). The disadvantage of stripping towers is the treatment of slurry in columns with packed beds, which have a high risk of clogging and foaming, making this process more difficult to manage than the slow-release stripping process. Additionally, stripping towers require more intensive slurry solid/liquid separation to avoid clogging, increasing overall energy consumption and treatment costs.
The results obtained highlight the possibility of obtaining AS with 69.7 g kg−1 of TAN in the trial Pig1, with the heated reactors and 85.9 g kg−1 of TAN in the trial Pig5.sh, with the addition of NaOH. In the AS obtained in these trials, the sulfur trioxide (SO3) contents (stoichiometrically determined) were 199.2 and 245.6 g kg−1 for heated and NaOH-added trials, respectively. These AS solutions reached the compositional requirements of Fertilizing Product Regulation (EU) 1009/2019, which establishes rules for placing EU fertilizing products on the market (Regulation (EU) 1009, 2019). This regulation defines a liquid inorganic macronutrient fertilizer [PFC 1(C)(I)(b)(ii)] as a substance that contains only one declared main macroelement [N, phosphorus pentoxide (P2O5), or potassium oxide (K2O)] for at least 15 g kg−1 by mass and one or more declared secondary macroelements [calcium oxide (CaO), magnesium oxide (MgO), sodium oxide (Na2O), or sulfur trioxide (SO3)] for at least 7.5 g kg−1 by mass. The sum of all declared contents of major and minor macronutrients must be at least 70 g kg−1 by mass.
Overall, the AS solutions obtained had a quality in line with Sigurnjak et al. (2019), who reported trials on two full-scale plants, where the NH3 was removed from biogas or digestates in the treatment plant or at the end-of-pipe pathway, in which AS with 53–74 g kg−1 of TAN was obtained. Similar results were reported by Ledda et al. (2013), who obtained AS with 51–61 g kg−1 of TAN in a digestate treatment plant characterized by sequential integration of solid–liquid separations, ultrafiltration, reverse osmosis, and cold NH3 stripping. Pigoli et al. (2021) obtained an AS with 71.7 g kg−1 of TAN in a full-scale plant where organic wastes were transformed by high-solid thermophilic anaerobic digestion coupled with N stripping technology.
The results obtained in this study are in line with the literature when considering the trials of limited water addition to the AS. As explained in the results, this condition was not achieved in some cases due mainly to the set-up of the pilot plant but could be easily improved in full-scale installations.
The average TS content (18.0% ± 7.9%) of the AS solution obtained in this study was consistent with literature findings of 20% ± 10% reported by Pigoli et al. (2021).
Contents of the major and trace elements in the AS solutions of all the trials were consistent with the data, as shown by Pigoli et al. (2021) and Brienza et al. (2021). In addition, the Cu and Zn contents of the AS solution were lower than the threshold established in Regulation (EU) 1009/2019 (Cu ≤600 mg kg−1 DW and Zn ≤1,500 mg kg−1 DW).
Regarding TOC content in the AS solutions of all the trials, its value was calculated as the difference between TS content attributable to AS and TS contents attributable to residual acid and was always under the threshold of Regulation (EU) 1009/2019 (≤10 g kg−1 FW).
The lowest electricity consumption found in the pilot plant trials (1.04–2.04–2.69 kWhel kgN−1 removal in the NaOH addition, heated reactors, and ambient temperature trials, respectively) was obtained when treating concentrated slurry. The highest electricity consumption (10.21–55.01 kWhel kgN−1 removal, respectively, in the trials with reactors heated and at ambient temperature) was obtained when diluted slurry was treated because the recoverable N is less than a concentrated slurry for the same treated volume and treatment time. The lowest electricity consumption values are lower than those reported in Flotats et al. (2011), which showed an energy consumption for the stripping column of approximately 28 kWh kg−1 of stripped N; or in Brienza et al. (2023) that showed a need for 12 kWhel kgN−1 recovered in a stripping plant operating at ambient temperature in different seasons; as well as in Brienza et al. (2021), which reported a need for approximately 3.8 kWhel and 59 kWhth to recover 1 kg of N as AS, through a stripping column operating at 90°C.
Regarding pure acid requirement in terms of N removed as AS, the pilot plant requirements were 5.3 and 7.2 kg acid per kgN−1 removed in the summer period (optimal conditions due to the limited condensate accumulation in the AS) or 11.1–18.9 kg acid per kgN−1 removed in the winter period (critical conditions due to the relevant condensate accumulation in the AS). Elsewhere, Vingerhoets et al. (2023) highlighted lower needs with 3.5 kg H2SO4 kgN−1 removed from digestate and cattle slurry by considering a H2SO4 concentrated at 98%.
Brienza et al. (2021) reported the use of 7.3 kg of 50% H2SO4 to recover 1 kg of N in different full-scale NH3 stripping units, which is slightly lower than the acid requirement of the pilot plant when it was operating in optimal conditions.
The operational costs achieved in the pilot plant in the optimal conditions were 1.66 € kgN−1 removed and 0.93 € kgN−1 removed for the trials conducted with reactors heated and with reactors at ambient temperature, respectively. These results were consistent with the findings of Brienza et al. (2021) who showed that the operational costs of the stripping treatment were 0.52 € kgN−1 removed from digestate processed in a full-scale plant operating at 47–76°C, in which, gypsum was used to recover NH3 in the scrubbing unit. In addition, Brienza et al. (2023) reported costs of 2.65 € kgN−1 removed, for a stripping unit treating digestate at ambient temperature in combination with an aerated constructed wetland. Bolzonella et al. (2018) provided a technical–economic assessment of a stripping system recovering less than 40% of the influent digestate N, indicating a processing operational cost of 3.34 € kgN−1 removed.
The operational costs of the trials with NaOH addition were 4.43–7.93 € kgN−1 removed for trials Pig5.sh and Cattle4.sh and were consistent with the findings of Vingerhoets et al. (2023) that reported costs within the range of 3.66–4.49 € kgN−1 removed. This was observed while treating cattle slurry with a comparable N removal rate, albeit with an increase in pH to 10. Considering the potential benefits, it might be valuable to assess alternative additives such as lime, which is cost-effective but requires proper management due to the sediment it generates (Cattaneo et al., 2019). Alternatively, given that the Pig5.sh and Cattle4.sh trials yielded comparable results to those with heated reactors but in just 1 week instead of 2, there is a potential to increase the pH less significantly. This approach would result in savings on NaOH usage and would extend the treatment duration. Another option to consider is the volatility of CO2 compared with NH3, with CO2 volatilization being approximately five times higher than NH3 volatilization within the first 4 h during aeration. Consequently, introducing NaOH a few hours after treatment initiation could reduce the required quantities as CO2 stripping contributes to a pH increase of 0.5–1 point (Husted et al., 1991).
The mass and N balance shown in Figure 4 describes an optimal operating condition considering a limited amount of water evaporated from the stripping reactors and condensed in the AS solution of no more than 1%. Based on the TAN removal trend shown in Figure 2, a TAN removal of 45% (corresponding to a treatment time of 2 weeks) was selected. Consequently, a TKN removal rate of 40% was assumed. Three types of slurry with different TKN contents of 1.5, 3, or 4.5 g kg-1 were considered for treatment in the pilot plant, while a fixed TAN/TKN ratio of 65% was considered regardless of the TKN concentration. Considering a 10% N mineralization of the initial TKN of the treated slurry (organic N converted to TAN), the resulting total removed TAN was higher than the TAN initially contained in the input slurry. Therefore, the sum of the TAN content in the starting slurry and the AS solution was 115%. With the same TAN removal rate, as the initial concentration of TKN increases, the concentration of N in the AS aqueous solution increases from 21.2 g kg−1 for the most diluted slurry to 59.6 g kg−1 for the most concentrated one.
Figure 4. Mass balance in optimal conditions by considering a specific condition: slurry with different N concentrations; TAN/TKN input slurry 65%; organic N mineralization 10%; volume reduction 1%.
Moreover, the European Commission proposal Ares (2024) 2885619–19/04/2024, to update the Nitrate Directive 91/676/EEC, considers the use of certain fertilizing materials from livestock manure, including AS, above the amount of 170 kg N per hectare per year up to an additional limit of 100 kg N per hectare per year. This applies if the AS has a mineral N to total N ratio of at least 90% and the fertilizing materials do not exceed 300 mg kg−1 dry matter and 800 mg kg−1 dry matter for Cu and Zn, respectively.
The target values to make the pilot plant technically and economically sustainable with the aim of its upscaling are shown in Table 5. The optimal conditions shown in Table 5 can be achieved by considering the following:
• To treat slurry or digestate with TKN content of approximately 4–5 g kg−1;
• The valorization of heat generated by the CHP engines of a biogas plant;
• An optimized acid requirement of 3.5 kg pure acid kgN−1 removed (Vingerhoets et al., 2023);
• Electricity consumption of 0.52 kWhel kgN−1 removed. This value has been obtained starting from the reduction in electricity consumption obtained from the upscaling of the slow-release NH3 stripping process from a laboratory scale equal to 2.1 kWhel kgN−1 removed, with the reactors filled to 0.04 m3 (Provolo et al., 2017), to pilot scale considering the lowest consumption achieved of 1.04 kWhel kgN−1 removed, with the reactors filled to 4 m3. Considering the same scale factors (halving the electricity consumption by increasing the treated volume by 100 times), the process upscaling at full scale will result in electricity consumption of 0.52 kWhel kgN−1 removed with reactors filled with 400 m3 of slurry/digestate.
From the perspective of the process upscaling, a possible reduction of the treatment times could be achieved by increasing the surface-to-volume ratio of the manure to accelerate NH3 release. The pilot plant had a surface-to-volume ratio of 10 cm2 dm−3, but by introducing a technical solution to increase this ratio to 60 cm2 dm−3, the NH3 removal in 14 days can reach 60% of the initial content (Trotta, 2020).
A full-scale plant with these characteristics could be a sustainable solution and competitive with other treatments, as the operating cost of 0.86 €/kg of N in the AS is similar to the market cost of mineral N. The process does not require any pretreatment of the slurry other than the usual separation of the coarse solid fraction and can be easily managed by the farmer as no special skills are required.
The slow-release NH3 stripping process has proven to be easily manageable at a pilot scale, allowing a TKN removal rate of up to 72%, confirming the expected performance based on laboratory tests. Moreover, the process is modular and enables the adjustment of the N removal rate according to the needs of the livestock farm.
Under optimal conditions, when slurry or digestates had a high TKN concentration (4–5 g kg−1) and by limiting the accumulation of condensed water in the scrubber, high-quality AS was obtained. It reached an N concentration between 69.7 and 85.9 g kg−1, classifying it as a mineral fertilizer according to the thresholds specified in EU Regulation 1009/2019.
The treatment studied can be economically sustainable. The operational cost (acid and electricity) of an optimized upscaled plant is 0.86 € kgN−1 removed, which is lower than case studies treating slurry or digestate in stripping towers. This holds true in situations where excess heat is available for valorization. Conversely, ambient temperature treatment with NaOH addition is sustainable by implementing management solutions that reduce the use of this additive (e.g., CO2 stripping or a minor pH increase compensated by a longer treatment time).
Introducing the treatment in farms with an N surplus or those needing to transport effluents over long distances improves overall effluent management. Within the same farm, AS becomes available, reducing the need for mineral fertilizers (if allowed by the threshold of the Nitrates Directive), and the separated solid can be applied in more distant fields. Alternatively, both products are more easily transportable to other farms compared with liquid manure.
The raw data supporting the conclusions of this article will be made available by the authors, without undue reservation.
AF: Data curation, Formal analysis, Investigation, Methodology, Writing – original draft, Writing – review & editing. OF: Data curation, Investigation, Writing – review & editing. ER: Data curation, Writing – review & editing. GP: Conceptualization, Funding acquisition, Methodology, Project administration, Supervision, Writing – review & editing.
The author(s) declare that financial support was received for the research, authorship, and/or publication of this article. This research was funded by the Lombardy Region as part of the Rural Development Program 2014–2020, Measure 16 – “Cooperation,” Sub-measure 16.1—“Support for the establishment and management of the EPI Operational Groups in the field of productivity and sustainability of agriculture,” Operation 16.1.01—“EPI Operational Groups.” Project “Conserva—Innovative Plant for the Conservative Removal of Nitrogen from Livestock Slurries and Digestate.” The authors acknowledge support from the University of Milan through the APC initiative.
The authors declare that the research was conducted in the absence of any commercial or financial relationships that could be construed as a potential conflict of interest.
All claims expressed in this article are solely those of the authors and do not necessarily represent those of their affiliated organizations, or those of the publisher, the editors and the reviewers. Any product that may be evaluated in this article, or claim that may be made by its manufacturer, is not guaranteed or endorsed by the publisher.
APHA/AWWA/WEF (2012). Standard methods for the examination of water and wastewater. in American Public Health Association (APHA); American Water Works Association (AWWA) and Water Environment Federation (WEF). 22nd edn. eds. E. W. Rice, R. B. Baird, A. D. Eaton, and L. S. Clesceri. Washington, DC, USA.
ARERA (2022). Relazione annuale sullo stato dei servizi anno 2021. Autorità di Regolazione per Energia Reti e Ambiente. Milan, Italy: Maggioli Editore.
Baldi, M., Collivignarelli, M. C., Abbà, A., and Benigna, I. (2018). The valorization of ammonia in manure digestate by means of alternative stripping reactors. Sustain. For. 10, 1–14. doi: 10.3390/su10093073
Bolzonella, D., Fatone, F., Gottardo, M., and Frison, N. (2018). Nutrients recovery from anaerobic digestate of agro-waste: techno-economic assessment of full scale applications. J. Environ. Manag. 216, 111–119. doi: 10.1016/j.jenvman.2017.08.026
Brienza, C., Donoso, N., Luo, H., Vingerhoets, R., de Wilde, D., van Oirschot, D., et al. (2023). Evaluation of a new approach for swine wastewater valorisation and treatment: a combined system of ammonium recovery and aerated constructed wetland. Ecol. Eng. 189:106919. doi: 10.1016/j.ecoleng.2023.106919
Brienza, C., Sigurnjak, I., Meier, T., Michels, E., Adani, F., Schoumans, O., et al. (2021). Techno-economic assessment at full scale of a biogas refinery plant receiving nitrogen rich feedstock and producing renewable energy and biobased fertilisers. J. Clean. Prod. 308:127408. doi: 10.1016/j.jclepro.2021.127408
Cattaneo, M., Finzi, A., Guido, V., Riva, E., and Provolo, G. (2019). Effect of ammonia stripping and use of additives on separation of solids, phosphorus, copper and zinc from liquid fractions of animal slurries. Sci. Total Environ. 672, 30–39. doi: 10.1016/j.scitotenv.2019.03.316
EPA (2007). “Method 3051A” in Microwave assisted acid digestion of sediments, Sludges, soils and oils (Washington, DC, USA: EPA).
Finzi, A., Oberti, R., Negri, A. S., Perazzolo, F., Cocolo, G., Tambone, F., et al. (2015). Effects of measurement technique and sample preparation on NIR spectroscopy analysis of livestock slurry and digestates. Biosyst. Eng. 134, 42–54. doi: 10.1016/j.biosystemseng.2015.03.015
Flotats, X., Foged, H. L., Bonmati, A., Palatsi, J., Magri, A., and Schelde, K. M. (2011). “Manure processing technologies” in Technical report no. II concerning “manure processing activities in Europe” to the European Commission, directorate-general environment (Tjele, Denmark: Agro Business Park).
Hafner, S. D., Meisinger, J. J., Mulbry, W., and Ingram, S. K. (2012). A pH-based method for measuring gaseous ammonia. Nutr. Cycl. Agroecosystems 92, 195–205. doi: 10.1007/s10705-012-9481-5
Heidarzadeh Vazifehkhoran, A., Finzi, A., Perazzolo, F., Riva, E., Ferrari, O., and Provolo, G. (2022). Nitrogen recovery from different livestock slurries with an innovative stripping process. Sustain. For. 14, 1–17. doi: 10.3390/su14137709
Husted, S., Jensen, L. S., and Jørgensen, S. S. (1991). Reducing ammonia loss from cattle slurry by the use of acidifying additives: the role of the buffer system. J. Sci. Food Agric. 57, 335–349. doi: 10.1002/jsfa.2740570305
Huygens, D., Orveillon, G., Lugato, E., Tavazzi, S., Comero, S., Jones, A., et al. (2020). Technical proposals for the safe use of processed manure above the threshold established for nitrate vulnerable zones by the nitrates directive (91/676/EEC), EUR 30363 EN. Luxembourg: Publications Office of the European Union.
Ledda, C., Schievano, A., Salati, S., and Adani, F. (2013). Nitrogen and water recovery from animal slurries by a new integrated ultrafiltration, reverse osmosis and cold stripping process: a case study. Water Res. 47, 6157–6166. doi: 10.1016/j.watres.2013.07.037
Palakodeti, A., Azman, S., Rossi, B., Dewil, R., and Appels, L. (2021). A critical review of ammonia recovery from anaerobic digestate of organic wastes via stripping. Renew. Sust. Energ. Rev. 143:110903. doi: 10.1016/j.rser.2021.110903
Pandey, B., and Chen, L. (2021). Technologies to recover nitrogen from livestock manure - a review. Sci. Total Environ. 784:147098. doi: 10.1016/j.scitotenv.2021.147098
Pigoli, A., Zilio, M., Tambone, F., Mazzini, S., Schepis, M., Meers, E., et al. (2021). Thermophilic anaerobic digestion as suitable bioprocess producing organic and chemical renewable fertilizers: a full-scale approach. Waste Manag. 124, 356–367. doi: 10.1016/j.wasman.2021.02.028
Provolo, G., Perazzolo, F., Mattachini, G., Finzi, A., Naldi, E., and Riva, E. (2017). Nitrogen removal from digested slurries using a simplified ammonia stripping technique. Waste Manag. 69, 154–161. doi: 10.1016/j.wasman.2017.07.047
Regulation (EU) 1009 (2019). Regulation (EU) 2019/1009 of the European Parliament and of the council of 5 June 2019 laying down rules on the making available on the market of EU fertilising products and amending regulation (EC) no 1069/2009 and (EC) no 1107/2009 and repealing Regulation. Off. J. Eur. Union.
Rizzioli, F., Bertasini, D., Bolzonella, D., Frison, N., and Battista, F. (2023). A critical review on the techno-economic feasibility of nutrients recovery from anaerobic digestate in the agricultural sector. Sep. Purif. Technol. 306:122690. doi: 10.1016/j.seppur.2022.122690
Sigurnjak, I., Brienza, C., Snauwaert, E., De Dobbelaere, A., De Mey, J., Vaneeckhaute, C., et al. (2019). Production and performance of bio-based mineral fertilizers from agricultural waste using ammonia (stripping-)scrubbing technology. Waste Manag. 89, 265–274. doi: 10.1016/j.wasman.2019.03.043
Sigurnjak, I., Michels, E., Crappé, S., Buysens, S., Tack, F. M. G., and Meers, E. (2016). Utilization of derivatives from nutrient recovery processes as alternatives for fossil-based mineral fertilizers in commercial greenhouse production of Lactuca sativa. L. Sci. Hortic. 198, 267–276. doi: 10.1016/j.scienta.2015.11.038
Smith, C., Hill, A. K., and Torrente-Murciano, L. (2020). Current and future role of Haber-Bosch ammonia in a carbon-free energy landscape. Energy Environ. Sci. 13, 331–344. doi: 10.1039/c9ee02873k
Sommer, S. G. (2013). Animal manure–from waste to raw materials and goods. in Manure Recycling: Treatment and Management. eds. S. G. Sommer, M. L. Christensen, T. Schmidt, and L. S. Jensen. doi: 10.1002/9781118676677
Sommer, S. G., Petersen, S. O., Sørensen, P., Poulsen, H. D., and Møller, H. B. (2007). Methane and carbon dioxide emissions and nitrogen turnover during liquid manure storage. Nutr. Cycl. Agroecosyst. 78, 27–36. doi: 10.1007/s10705-006-9072-4
Trotta, S. (2020). Rimozione dell’azoto dagli effluenti zootecnici mediante strippaggio: valutazione dell’influenza del rapporto superficie/volume. Thesis. Milano (Italy): Università degli Studi di Milano.
Vaneeckhaute, C., Lebuf, V., Michels, E., Belia, E., Vanrolleghem, P. A., Tack, F. M. G., et al. (2017). Nutrient recovery from Digestate: systematic technology review and product classification. Waste Biomass Valoriz 8, 21–40. doi: 10.1007/s12649-016-9642-x
Vaneeckhaute, C., Meers, E., Michels, E., Ghekiere, G., Accoe, F., and Tack, F. M. G. (2013). Closing the nutrient cycle by using bio-digestion waste derivatives as synthetic fertilizer substitutes: a field experiment. Biomass Bioenergy 55, 175–189. doi: 10.1016/j.biombioe.2013.01.032
Velthof, G. L., Lesschen, J. P., Webb, J., Pietrzak, S., Miatkowski, Z., Pinto, M., et al. (2014). The impact of the nitrates directive on nitrogen emissions from agriculture in the EU-27 during 2000-2008. Sci. Total Environ. 468–469, 1225–1233. doi: 10.1016/j.scitotenv.2013.04.058
Vingerhoets, R., Brienza, C., Sigurnjak, I., Buysse, J., Vlaeminck, S. E., Spiller, M., et al. (2023). Ammonia stripping and scrubbing followed by nitrification and denitrification saves costs for manure treatment based on a calibrated model approach. Chem. Eng. J. 477:146984. doi: 10.1016/j.cej.2023.146984
WUR . (2024). Database-Agrarische prijzen. https://agrimatie.nl/Prijzen.aspx?ID=15125/ (Accessed January 10, 2024).
Keywords: digestate, pig and cattle slurry, nitrogen recovery, ammonium sulfate, pilot plant
Citation: Finzi A, Ferrari O, Riva E and Provolo G (2024) Nitrogen recovery from intensive livestock farms using a simplified ammonia stripping process. Front. Sustain. Food Syst. 8:1406962. doi: 10.3389/fsufs.2024.1406962
Received: 25 March 2024; Accepted: 03 July 2024;
Published: 19 July 2024.
Edited by:
Fiona Nicholson, Agricultural Development Advisory Service, United KingdomReviewed by:
Rafael Clemente, CEBAS-CSIC, SpainCopyright © 2024 Finzi, Ferrari, Riva and Provolo. This is an open-access article distributed under the terms of the Creative Commons Attribution License (CC BY). The use, distribution or reproduction in other forums is permitted, provided the original author(s) and the copyright owner(s) are credited and that the original publication in this journal is cited, in accordance with accepted academic practice. No use, distribution or reproduction is permitted which does not comply with these terms.
*Correspondence: Alberto Finzi, YWxiZXJ0by5maW56aUB1bmltaS5pdA==
†ORCID: Alberto Finzi, https://orcid.org/0000-0002-7886-0057
Elisabetta Riva, https://orcid.org/0000-0003-0718-9291
Giorgio Provolo, https://orcid.org/0000-0002-7444-7118
Disclaimer: All claims expressed in this article are solely those of the authors and do not necessarily represent those of their affiliated organizations, or those of the publisher, the editors and the reviewers. Any product that may be evaluated in this article or claim that may be made by its manufacturer is not guaranteed or endorsed by the publisher.
Research integrity at Frontiers
Learn more about the work of our research integrity team to safeguard the quality of each article we publish.