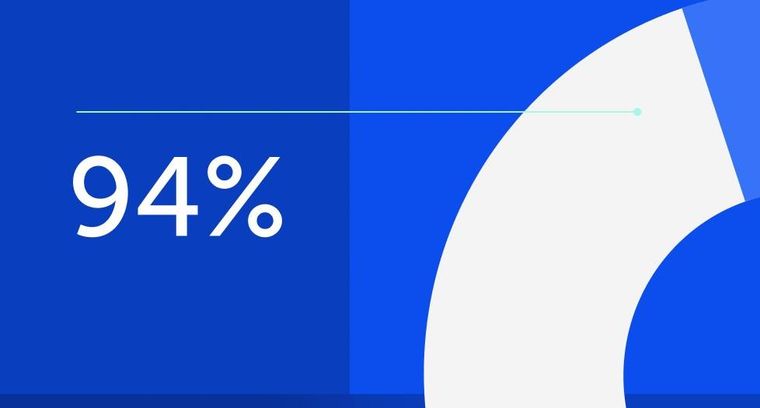
94% of researchers rate our articles as excellent or good
Learn more about the work of our research integrity team to safeguard the quality of each article we publish.
Find out more
ORIGINAL RESEARCH article
Front. Sustain. Food Syst., 12 June 2024
Sec. Water-Smart Food Production
Volume 8 - 2024 | https://doi.org/10.3389/fsufs.2024.1400274
Introduction: The agri-food sector has been identified as one of the most significant contributors to environmental degradation and emissions. Thus, in order to respond to the societal demand for cleaner and greener products, in recent years, the food industry has been striving to identify and apply more sustainable practices to minimize the negative impact on the environment. Within the agri-food sector, one of the industries requiring efforts to mitigate its environmental footprint is the tomato processing industry, which represents an important industry within the Italian industrial food processing sector. Efficient utilization of resources and adoption of innovative methods in the production lines of the tomato processing industry can be envisaged as strategic measures to increase sustainability. This study aims to discuss the results of the case study in which an Italian tomato processing company has been analyzed by applying the LCA methodology.
Method: Foreground data were obtained from the tomato processing facility located in southern Italy, and Ecoinvent database was the source of background data. The assessment was carried out by SimaPro software using ReCiPe 2016 (V1.03). The feasible conservation strategies in the production line have been evaluated through water-energy nexus simulation by SuperPro Designer® before the implementation, and different scenarios have been evaluated by SimaPro to decrease the environmental load.
Results and conclusion: This study demonstrates that the production of 1 kg of peeled tomatoes and tomato puree leads to greenhouse gas emissions of 0.083 kg CO2 eq and 0.135 kg CO2 eq, respectively. A deeper analysis to evaluate the contribution of the different tomato processing stages indicated that the thermal units are the main ones responsible for adverse effects on the environment, and any improvement in their performance can be seen as an unmissable opportunity. The conservation strategies identified resulted in considerable water (23.4%), electricity (14.7%), and methane (28.7%) savings and, consequently, in 16 and 19% reduction of global warming potential in peeled tomato and tomato puree production lines, respectively. These findings provide new insights for tomato processing companies wishing to adopt more sustainable processing practices, reducing their environmental impact to a considerable extent and improving their economic performance.
The agri-food sector plays a crucial role in global greenhouse gas (GHG) emissions, contributing to approximately 25% of the total emissions worldwide (Reavis et al., 2022). In Europe (EU-25), the agricultural sector is responsible for approximately 10–12% of global GHG emissions, while the food industry as a whole accounts for over 20% of all GHG emissions (Bevilacqua et al., 2007; Garnett, 2011). Additionally, the food processing sector contributes significantly to environmental burdens, with 20–30% of the global warming, ozone formation, and acidification and over 50% of eutrophication (European Commission, 2006). The impact of the agri-food sector extends beyond greenhouse gas emissions, encompassing considerable resource consumption as well. According to the EU Commission’s communication, the food and drink industry alone contributes to 28% of resource consumption in Europe (European Commission, 2011).
Thus, reducing the impacts of the agri-food sector is one of the foremost priorities within the European Sustainable Production and Consumption policies (Castillo-Díaz et al., 2023). To determine the sustainability of an agri-food network, it is essential to assess the environmental impact and resource usage throughout the product’s life cycle (Del Borghi et al., 2021). To address this problem, Life Cycle Assessment (LCA) is a widely accepted standard methodology in order to produce greener products (Ghnimi et al., 2021). LCA methodology comprehensively rates environmental impacts of a product or process by quantifying energy and material consumption, waste generation, and their respective environmental consequences (Jiménez-González et al., 2000). With this approach, the entire life cycle is taken into consideration from raw material production, processing, packaging, and transportation to end-of-life stages, such as recycling or disposing, which is commonly referred to as “cradle-to-grave” analysis (Roy et al., 2008). However, other approaches such as “from cradle to gate” (Anton et al., 2014), “from gate to gate” (Jiménez-González et al., 2000; De Marco et al., 2015), or “from gate to grave” (Rossi et al., 2014) are used to deeply analyze specific products. With these assessments, it is possible to restrict the assessment to part of the production processes. This provides a systematic way to evaluate and compare the potential routes for cleaner manufacturing (De Marco et al., 2017). This approach not only detects environmental burdens across a product’s life cycle but it can also constitute the basis for individuating and validating alternative scenarios to lessen environmental consequences throughout the supply chain using process simulation (Beccali et al., 2009).
Among the agricultural products, tomato is the most widely diffused vegetable undergoing industrial transformation (Eslami et al., 2023a). In 2023, approximately 44.2 million tons of tomatoes were utilized in the tomato processing sector to produce different types of tomato-based products (Tomato News, 2023). Italy is the third-largest tomato processor in the world, producing more than 5.4 million tons (12.2% of global production) of processed tomatoes, representing 52% of the European production (Anicav, 2023), being the Campania Region, in southern Italy, the main Italian production area (Eslami et al., 2023b). Generally, substantial amounts of water and energy in the cultivation, processing, packaging, and distribution phases are consumed to produce tomato-based products, and consequently, a significant environmental load is generated in each stage (Avellán et al., 2018; Stamou and Rutschmann, 2018; Liu et al., 2019; Pineda et al., 2020). The environmental impact of tomato cultivation has been extensively studied in many countries, such as Italy (Cellura et al., 2012; Garofalo et al., 2017; Ronga et al., 2019), Australia (Page et al., 2012), Canada (Ghasemi et al., 2020), Iran (Khoshnevisan et al., 2013; Pishgar-komleh and Shine, 2019), Albania (Canaj et al., 2019), Spain (Muñoz et al., 2007; Anton et al., 2014; Pérez et al., 2018), and Colombia (Ricardo et al., 2014), as reported in the comprehensive review by Pineda et al. (2020). Fewer studies are found in the literature discussing the environmental impact of the tomato processing industry on different products, such as tomato purée (Del Borghi et al., 2014; Manfredi and Vignali, 2014), tomato paste (Brodt et al., 2013; Winans et al., 2020), diced tomatoes (Brodt et al., 2013; Del Borghi et al., 2014; Winans et al., 2020), tomato sauce (Parajuli et al., 2021), ketchup (Wohner et al., 2020), and peeled tomato (Del Borghi et al., 2014), and to the best of our knowledge, an in-depth analysis of the processing phases of mashed tomato (De Marco et al., 2018) and peeled tomato (Garofalo et al., 2017; Arnal et al., 2018) is reported only in three studies. Most of these studies consider the tomato processing phase as a black box with the total inputs of water and energy, without investigating their effective consumption in the different processing stages. This lack of information makes it difficult to determine the specific contribution of each processing step or individual opportunity and corrective actions to decrease the environmental impact.
Indeed, significant water and energy savings can be achieved through the implementation of conventional conservation measures that are economically and environmentally efficient. However, their subsequent impacts are often overlooked in research studies available in the literature, particularly within the context of LCA. To the best of our knowledge, no studies report the results of the LCA analysis of tomato processing lines, discussing reduction of the environmental impact on the implementation of conventional strategies to reduce water and energy consumption in the processing phases. Additionally, it is worth noting that there is a notable gap in the utilization of process simulators as benchmarking tools for water and energy analysis at the unit level in the tomato processing industry. This powerful tool could help to unveil the black box of the tomato processing phase, identifying the contribution of each processing step to the environmental impact and evaluating the effectiveness of conventional saving strategies before implementation. Within this context, only a few studies on other food processes specifically targeted the utilization of process simulators as benchmarking tools for water and energy analysis, evaluating the environmental burden and the costs associated with process optimization and introduction of conventional or new technologies to reduce energy and water consumption. For instance, Tomasula et al. (2013) assessed the environmental impact of milk powder production using SuperPro Designer process simulation software. They benchmarked greenhouse gas emissions by calculating the carbon footprint for the energy usage for each unit operation while also characterizing water usage in each step. The study revealed that process simulation effectively identified water and energy consumption in processing steps, highlighting major contributors to greenhouse gas emissions throughout the facility. The authors emphasized how the process simulator aided in identifying areas of high water and energy consumption within the unit operations, defining opportunities for resource efficiency improvements and reduced emissions. In 2014, the same research group expanded on this study using the process simulator to develop and assess the impact of alternative technologies for pasteurization and savings measures on overall process efficiency (Tomasula et al., 2014). Another study by Fritzson and Berntsson (2006) investigated energy efficiency in a slaughter and meat processing facility. The study aimed to identify potential energy savings (both electrical and thermal) within the plant. Employing a process integration approach, specifically, pinch analysis combined with process simulation using a HYSIS process simulator, the authors explored opportunities to decrease energy usage. The process simulator played a crucial role in modeling and simulating the refrigeration plant and investigating potential actions for energy savings (Fritzson and Berntsson, 2006).
Overall, these studies underscore the effectiveness of the process simulator as a powerful tool for characterizing water and energy use at the unit level across facilities. This approach enables pinpointing areas for improvement and testing alternative measures for cost-saving.
Intending to evaluate the sustainability of the tomato processing industry, this research reports the results of the LCA study, using SimaPro software with ReCiPe 2016 (V1.03) methodology at the level of the midpoint, of a tomato processing company located in southern Italy, starting with the analysis of water and energy consumptions in different stages of peeled tomato and tomato puree production lines to identify the hotspots in the processing phases. In this study, sensitivity analysis enabled comparing the different improvement scenarios following the implementation of suitable and feasible conservation measures to reduce water and energy consumption in this industry. The improvement scenarios in the processing phase were further examined by process simulation using software SuperPro Designer®. Finally, LCA analysis reconsidered the improved scenario, and the results were compared with the assessment of the current situation to determine the reduced environmental load of tomato processing when the suggested conservation measures are put in place.
The tomato processing company processes approximately 54,000 tons of tomatoes from July to September. 42 tons of tomatoes per hour enter the processing lines to produce peeled tomatoes in tinplate cans (300, 400, 3,000, and 3,400 g), and tomato puree in glass bottles (370, 500, and 690 g) of different weights. To evaluate the environmental impact of tomato processing, all the production steps must be analyzed, and water and energy (thermal, electrical) consumption precisely measured during production. The Current Value Stream Maps (CVSM) of tomato puree and peeled tomato production with information on water and energy consumption in each step are shown in Figure 1.
Figure 1. Current Value Stream Map (CVSM) for peeled tomato and tomato puree, with water [m3/FU], electricity [kWh/FU], and energy (thermal and electrical) [kWh/FU] consumption. (Functional Unit (FU) = 1 kg of product).
Fresh tomatoes are unloaded into a hydraulic flume and transported to the processing line. Tomatoes are washed in two washing channels and then sorted (manually and optically) before being subjected to thermophysical peeling. After washing, in the grading station consisting of a sorting belt, the operators manually remove the defective fruits and other undesired materials. This manual sorting is followed by automated optical sorting to remove green tomatoes. These wastes feed a reject conveyor, are transported to a collecting area, and are sold as cattle feed. The cleaned and sorted tomatoes then proceed through the thermophysical peeling step.
During the peeling stage, the tomato fruits are first blanched with pressurized steam (1.0–1.3 bar) and then vacuum-cooled before being conveyed onto pinch rollers for mechanical peeling. Then, peeled tomatoes undergo an optical and manual sorting step to remove tomato fruits not complying with the commercial standards due to color, presence of black spots or scars on the surface, or undersize.
Whole peeled tomatoes (~4.7–5 °Brix) are filled in cans of different weights that are conveyed through a juice filler to add tomato juice (~8°Brix). The latter is used to fill the voids between peeled tomato fruits to improve heat transfer during the following thermal treatment for pasteurization. The peeled tomato to juice ratio is approximately 60:40 (w/w). The average soluble solid concentration of the canned product is approximately 6.5 °Brix. After filling, the cans are sealed by seaming and then conveyed to the pasteurization unit.
The sealed cans are conveyed through two parallel pasteurization tunnels where cans are steam heated up to approximately 98–100°C and then cooled down to 45–50°C using water pumped from the wells. Finally, sterilized canned tomatoes are placed in an automatic palletizer for labeling and stored in bulk before delivering to customers.
The washing and sorting phases of tomato puree production are the same as for peeled tomato production and have been already described in section 2.1.1.1.
Washed/sorted tomatoes are fed in the chopping section, consisting of a special pump provided with a pre-feeding screw. Then, chopped tomatoes are heated with steam up to 80–85°C to inactivate pectolytic enzymes before undergoing juice extraction.
The juice extraction unit consists of a pulper and a refiner. Two streams come out from this processing step, namely, refined juice (approximately 5°Brix) undergoing concentration and peels and seeds, which are disposed of and then sold as cattle feed. The average extraction yield is approximately 94% and, generally, depends on pulp temperature (juice yield increases with increasing the temperature), tomato variety, and extractor technical features, such as type of sieves and rotation speed. The refined juice is collected in a holding tank constantly feeding the concentration units.
Tomato juice concentration is carried out in continuous triple-effect evaporators, where the refined juice, with an initial solid content of 4.7–5%, reaches a final concentration of up to approximately 8°Brix. Tomato juice is pumped to the two parallel evaporation units, each consisting of three evaporators operated in a series in a countercurrent mode. The entire concentration process, which is one of the most energy-intensive steps of the tomato puree processing line, takes place under vacuum at relatively low temperatures.
The concentrated tomato puree is pumped from the evaporation unit directly to the tube-in-tube pasteurization unit, where the puree is pre-heated up to 96°C. The hot juice is filled in bottles or cans and pasteurized at approximately 98–100°C in a pasteurization tunnel. In the final section of the tunnel, bottles are cooled utilizing cold water (45–50°C).
Finally, tomato puree cans or bottles are placed in an automatic palletizer for labeling and then stored in bulk in a warehouse.
Life cycle assessment is a standard methodology used to evaluate the environmental impacts of a product or service throughout its entire life cycle, from the acquisition of raw materials to the final disposal or treatment of waste, which is formally adopted by ISO standards 14,040 to 14,044 (ISO, 2006a,b). By using this method, all possible environmental impacts can be quantified, understood, evaluated, and analyzed. A comprehensive LCA analysis typically consists of the following four steps or sub-sections: definition of the goal and scope of the study, life cycle inventory (LCI), life cycle impact assessment (LCIA), and interpretation of results (Del Borghi et al., 2021).
Generally, LCA studies are classified into two main groups consequential (effect-orientated) and attributional (state-oriented) analyses (Bamber et al., 2020). In the former case, the objective is to identify the overall environmental effect in a steady state, whereas in the latter case, it is possible to determine how the environmental impact changes as the state changes. Since this study considered the current situation of the company with a focus on the improvement scenarios in the processing stage, an attributional analysis was considered (Hospido et al., 2010).
The goal and scope of an LCA study is a critical step that determines the boundaries and purpose of the analysis of a system, considering all relevant stages and activities in the life cycle of the product. The scope of the LCA study should be defined clearly and transparently to ensure that the results are reliable, comparable, and useful for decision-making (Del Borghi et al., 2021). The goal of this study is to initially conduct a baseline LCA to evaluate the environmental impact generated in the processing phase of peeled tomato and tomato puree, manufacturing to identify the hotspots in tomato processing. Afterward, possible improvement scenarios in the processing phase were identified, and the effects of their implementation on water and energy saving were evaluated by simulation using SuperPro Designer® software. Furthermore, Life Cycle Assessment (LCA) was conducted again to assess the reduction in environmental burden using new data obtained from simulations via SuperPro Designer® software. These findings were then compared with the current situation to gauge the extent to which conservation strategies are effective in reducing the environmental impacts of the tomato processing phase.
In LCA, the functional unit (FU) is defined as a quantified description of the performance of a product, service, or process, which is being studied. It serves as a reference unit for standardizing inventory data (ISO, 2006a), facilitating the comparison of different products and services (ISO, 2006b). In the context of the food industry, the FU is typically defined based on the mass of products under analysis. All inputs and outputs associated with its production are evaluated on this basis (Del Borghi et al., 2021). In this study, 1 kg of peeled tomato in tomato juice (60% peeled tomato and 40% juice) and 1 kg of tomato puree (8 °Brix) are considered as FU.
LCA evaluation in the processing phase of tomato puree and peeled tomato production is the objective of this study. To this purpose, a “gate-to-gate” approach is proposed, considering solely the tomato processing stage in the analysis. This study considers the consumption of water, electrical energy, and methane during different stages of tomato processing, as well as the associated emissions into air, water, and soil, within the system boundaries of the study. Other stages, such as cultivation, packaging, and downstream processes (e.g., delivery of raw tomato, distribution of the final products, and end-of-life phase), as well as the eventual other ingredients used in the processing phase (e.g., salt), are excluded from the system boundaries of this study (Figure 2).
Figure 2. System boundaries in the tomato processing industry and consequent emissions to air, water, and soil.
During tomato processing, various types of by-products, including tomato waste (seeds, peels, and pomace), green tomatoes, leaves, branches, soil, and sludge are generated. According to the company, tomato waste is used as cattle feed, and other biowaste products are sent to the company to be modified and used as compost for agriculture purposes. Therefore, these by-products are not included in the system boundaries of the LCA, since they offer environmental benefits and do not have negative impacts (Del Borghi et al., 2014). Moreover, according to the “Polluter-Pays (PP) allocation method,” waste generators are responsible for carrying the full environmental impact of their actions until the point wastes are transported to a gate of the waste processing plant. As a result, system expansion and the avoided burdens from recycling are not taken into account in this particular study (European Court of Auditors, 2021).
Life Cycle Inventory (LCI) is a crucial step of LCA to quantify the inputs and outputs, including data on raw materials, energy consumption, and emissions throughout the product’s entire life cycle. LCI is a key stage being the validity of an LCA study completely contingent on the quality of data. It allows identifying the stages in a product’s life cycle with the most significant environmental impact, known as hotspots, and informing the decision-makers on how the environmental performance of a product can be improved (Rosenbaum et al., 2018).
As already underlined, in this study, only the tomato processing phase was considered, and the foreground data were collected from the company. Figure 1 provides a detailed life cycle inventory for peeled tomato and tomato puree production with information on water and energy consumption in the processing lines measured by different sensors installed in different units or evaluated through mass and energy balances in different units of the tomato processing line. The sensors allowed the accurate monitoring and measurement of the resources used at each production stage. However, the company generates various tomato-based products with some shared units and cannot provide specific information on the flows for each product. For this reason, the allocation issue was raised. In such a situation, the ISO (2006b) 14044 guidelines suggest using physical relationships between products to discriminate between inputs and outputs. Therefore, the consumption of resources for the common stages is allocated to the various products in proportion to the amount of tomato processed in the two different production lines (ISO, 2006b). According to the background data, the information regarding the production of electricity, methane, and water sources was obtained from the Ecoinvent database (V3.5) (Wernet et al., 2016). The information used in this study considers the Italian context whenever possible, and, in the case of lack of such information, the study relies on data broadly representing the European situation.
Regarding the related emissions to water during processing, the wastewater, considered as final waste flow in the assessment, is discharged into the municipal sewage system after being treated in a wastewater treatment unit. However, laboratory tests were conducted on samples collected from the company’s wastewater generated during tomato processing, and all the water pollutants generated were considered in this study. As far as air pollution is concerned, the company uses methane as fuel to provide thermal energy in the various stages of tomato processing. Table 1 presents the data on emissions from peeled tomato and tomato puree production, which is based on the information provided by the Environmental Protection Agency (EPA) on the emissions from methane combustion and their consequent impacts on the environment (Eastern Research Group, 1998).
Table 1. Direct emission values (g/FU) into the air for methane consumption in the processing phase of peeled tomato and tomato puree production.
The potential environmental effects associated with different types of resources are evaluated, and the subsequent emissions are presented using a set of indicators. In this study, ReCIPe 2016 (V1.03) method is used to assess the environmental impact of peeled tomato and tomato puree processing operations. This method, developed by the National Institute for Public Health and the Environment in the Netherlands (Huijbregts et al., 2017), involves 18 impact categories, as shown in Table 2.
Table 2. Environmental impact indicator values for peeled tomato (1 kg) and tomato puree (1 kg) production.
A commercial process simulation tool, SuperPro Designer (version 13; Intelligen Inc., Scotch Plains, NJ), is utilized to describe tomato processing lines. This process simulator contains models (unit procedures) for general unit operations and equipment, which can be linked to each other to develop a flow sheet diagram representing the entire process. Each model is a mathematical representation of the physical processes taking place in each unit. Once the models are constructed and connected via software connector lines, process data obtained from the plant operators and unit specifications are integrated, and mass and energy balances can be evaluated. Data considered in the process simulation base line are shown in Supplementary material.
The LCI analysis highlights significant resource consumption in various stages of peeled tomato and tomato puree production. In the former case, the washing and sorting stages consume most of the processing water (2.66E-03 m3/kg product), and the juice production stage uses the largest amount of energy which is 1.2E-01 kWh/kg product for the combined use of thermal and electrical energy. In the latter case, a more resource-intensive consuming process, washing, and sorting stages require the highest quantity of water (2.29E-03 m3/kg product), and the tomato juice concentration stage consumes the largest amount of energy which is 1.4E-01 kWh/ kg product, encompassing both thermal and electrical energy.
Data on the environmental impacts of the processing steps of peeled tomato and tomato puree are shown in Table 2 and Figures 3, 4.
Figure 3. Environmental impact contributions at the midpoint level of peeled tomato production (1 kg) in the different processing stages (other usages: blowers, cooling tower fans, and pumps for recirculating water).
Figure 4. Environmental impact contributions at the midpoint level of tomato puree production (1 kg) in the different processing stages (other usages: blowers, cooling tower fans, and pumps for recirculating water).
LCA analysis of peeled tomato production demonstrates that juice preparation (31.1–45.95%) and thermophysical peeling (14.1–38.3%) together have a contribution of over 57% in most of the environmental impact categories, except WD and MEP. The washing and sorting phases have a contribution to WD and MEP of 75.5 and 49.8%, respectively, related to the high water consumption and wastewater generation in the washing stage. The total GWP for producing 1 kg of peeled tomato is 8.30E-02 kg CO2 eq, of which the juice preparation process contributes approximately 45%. From these results, it can be concluded that the environmental impact of a processing step is directly proportional to its thermal and electrical energy consumption; the higher the amount of energy consumed, the greater the environmental impacts are generated. This information can be used to identify areas for improvement and can be considered as a guideline to develop more sustainable production practices for the tomato processing industry.
In tomato puree production, the concentration step has the highest environmental impact, contributing from 29 to 35.2% in all categories, except WD (71.1%) and MEP (30.5%), in which the washing and sorting phases have the highest contribution. According to GWP, tomato puree production (1 kg) is responsible for 1.35E-01 kg CO2 eq generation, being concentration the step with the highest contribution (35.2%). In both peeled tomato and tomato puree production, the canning, bottling, and palletization stages have the lowest energy consumption and, consequently, the lowest contribution to all categories of environmental impact (less than 4%).
The thermal units have significant environmental effects due to their large electricity and methane consumption. Moreover, fossil fuel combustion in thermal units results in the emission of greenhouse gases, such as carbon dioxide, nitrogen oxides (NOx), and sulphur oxides (SOx). These gases contribute to air pollution, smog, and acid rain formation, leading to negative effects on human health and ecosystems. The environmental impact of thermal units extends beyond their direct use. The extraction and production of fossil fuels contribute to habitat destruction, ecosystem disruption, and air and water pollution. Additionally, the transportation of these fuels over long distances further adds to the carbon footprint associated with thermal units (Eastern Research Group, 1998; Grubert and Brandt, 2019; IEA, 2023). Moreover, a significant portion of electricity worldwide is produced utilizing fossil fuels, such as coal, natural gas, and oil. The combustion of these fuels releases carbon dioxide (CO2) and other greenhouse gases into the atmosphere, contributing to climate change and global warming (Grubert and Brandt, 2019; IEA, 2023). Addressing this issue requires the development of more sustainable energy solutions and the implementation of effective environmental management practices to minimize the environmental burden of the tomato industry, as discussed in a more detailed manner in the following section.
To the best of our knowledge, only a few studies presenting the LCA of the processing stages of tomato-based products are available in the literature. Garofalo et al. discussed the environmental impact of peeled tomato production, analyzing and evaluating different impact categories. According to their results, juice production stage, together with pasteurization and peeling, has the highest environmental impact. These three stages are responsible for 90% of the total impact, as a consequence of their significantly high energy requirements (Garofalo et al., 2017). Arnal et al. also reported that thermophysical peeling and pasteurization have the highest environmental impact on all categories. However, it should be mentioned that the production of juice is not considered in their study (Arnal et al., 2018). Moreover, De Marco et al. evaluated the environmental impact of the processing stages of mashed tomato, and their results are coherent with those obtained in this study for tomato puree production. The authors reported that hot break, concentration, and pasteurization steps contribute to the highest extent to the majority of the midpoint categories (De Marco et al., 2018).
In the tomato processing industry, some opportunities for the improvement can reduce water and energy consumption and mitigate the environmental impacts of this processes. The LCA of the processing stages of peeled tomato and tomato puree production has been determined considering the current situation of the company. This allowed the identification of the hotspots of the two processing lines. Furthermore, conventional strategies for water and energy savings were individuated, and the development scenario was evaluated by SuperPro Designer® software, allowing simulation of how the implementation of the conventional conservation strategies hypothesized would affect the water mass balance and the energy balance in the processing lines. The results derived from process simulation and calculations employing a rule-of-thumb approach, as elaborated in the subsequent section, were utilized as new data for SimaPro to measure the environmental impact reduction that can be achieved in the new production scenario.
To advance sustainability within the tomato processing industry, this study employed two scenarios for sensitivity analysis during the processing phase of tomato puree and peeled tomato manufacturing. These scenarios simulated the implementation of conservation strategies in the tomato processing line.
CS: A baseline scenario that reflects the current situation for tomato puree and peeled tomato production.
SA.1: A scenario in which conventional conservation measures are considered in the processing phase of peeled tomato production.
SA.2: A scenario in which conventional conservation measures are considered in the processing phase of tomato puree production.
Based on the information obtained from analyzing in depth the processing plant of the company during the tomato production year 2023, an integrated technical assessment of the water-energy nexus (WEN) in the facility was performed. WEN is a concept when water and energy overlap in their use; heat is necessary to generate steam from water and water is involved upstream in the processing of electricity or natural gas. WEN assessment is a descriptive quantitative approach for characterizing the water and energy use of the facility (Peterson et al., 2022).
The data for the WEN assessment resulted from interviews with the plant operators, documents, and records available at the facility and through readings of the water flow meter sensors and monitoring devices installed on the key processing steps of both the tomato processing lines. These procedures enabled the collection of primary data, including the coefficient of usage for relevant equipment and unit operations. This technical assessment was integrated into the simulation tool SuperPro Designer® using the primary data as input to quantify the unknown streams and solve the mass and energy balances. The integrated technical WEN assessment allowed the development of the Current Value Stream Map (CVSM) based on accurate data on the amount and distribution of water, electricity, and thermal energy usage in the most relevant processing steps (Figure 1). Moreover, different scenarios were developed and simulated by SuperPro Designer®, considering the potential conventional measures for water and energy conservation through the different stages of tomato processing.
As the facility has already implemented a few conventional strategies, such as water reuse in units such as washing phases and cooling systems, there remains room for adopting additional solutions. In light of this, a set of feasible conservation measures have been considered, based on the information on the facility layout and productivity, such as maintenance actions, including improving the insulation of steam pipes and distribution systems, prevention of water overflow and leakage, process retrofitting, including the enhancement of the closed-loop system for cooling units, recovering and using waste heat from tomato evaporate condensate in the hot break unit, recovering heat from flue gas exiting the boilers, and integration in the processing units of well-established technological solution such as vapor recompression in the concentration systems, and Variable Frequency Drives (VFDs) on pumping systems, blowers, and cooling towers fans. A more detailed description of those improvements is reported in the following paragraphs.
Process simulation by SuperPro Designer® allowed the evaluation of how and to what extent the implementation of conventional measures could reduce water and energy consumption at the industrial facility examined. This integrated approach is considered powerful for compiling more detailed information on water-energy usage in each unit, thereby enhancing the resolution in LCA studies. The result of the process simulation is shown in Table 3, illustrating how the implementation of these conventional strategies in the tomato processing facility can provide considerable opportunity to reduce water consumption by approximately 23.4%, electrical energy consumption by approximately 14.7%, and methane consumption by approximately 28.7%. Afterward, to assess the feasibility of the envisaged strategies and their potential to reduce environmental impact on a tomato processing facility, an integrated approach was employed, utilizing process simulation and LCA to determine the new baseline after the implementation of process-specific measures that can decrease water and energy usage at the individual unit operation level, representing approximately 16 and 19% reduction in GWP in the peeled tomato and tomato puree production line of the case study company.
Table 3. Water, electrical energy and methane saving opportunities in the tomato processing industry.
The utilization of two software, namely, SuperPro Designer® and SimaPro, can provide data to decision-makers on improving the overall performance of the production plant in a controlled and cost-effective manner. This approach is useful to analyze many alternative processing scenarios before implementing corrective actions to reduce the environmental impact of the food processing industry, resulting in a significant saving of intellectual and economic resources.
Water overflow is a common issue in many food industries. In this case study, significant water overflows occur in three main units, namely, the washing flume, the cooling tower tank, and the water accumulation tank. The overflow of water is due to the lack of control of the water flow rate in the first unit and the lack of exploitation of intermediate water current reuse. For example, the condensate produced in the evaporation units in the tomato processing plant results in significant water discharge into the sewer. Therefore, the implementation of conventional strategies, such as the installation of VFD on the pumps feeding the water in the washing tunnels, could contribute to drastically limiting water overflow in this processing phase. Moreover, resizing the cooling tower tank and installing a level sensor on the accumulation tank should be considered to prevent excessive water overflows in these units. The potential water saving associated with these improvement measures was quantified via a process simulator, which allowed an estimation of the expected reduction in water consumption. The results from this endeavor indicate that the proposed saving measures could lead to a considerable reduction in water usage of approximately 6.5% of the total freshwater consumption.
Based on WEN analysis, the use of a single pass cooling unit for cans in the peeled tomato processing line represents an additional opportunity to improve the efficiency of water usage. Given that cooling is the second highest water-demanding step at the facility, substantial water savings could be obtained by implementing closed-loop recirculating cooling systems. The evaluation of the impact of this measure on water savings was achieved through process simulation. The results show that the implementation of a closed-loop system for can cooling units can reduce approximately 4% the total freshwater consumption. Even though the adoption of such systems introduces additional energy demand in cooling tower operations, the overall net benefits from both economic and environmental perspectives may offset the impact of the acquisition of an additional cooling tower.
Preliminary auditing of the technicians of the tomato facility during the WEN assessment revealed that two fired-tube boilers lacked economizers, presenting an opportunity for significant energy efficiency improvement. Heat recovery from flue gas is often the best opportunity for heat recovery in steam systems (Dockrill and Friedrich, 2001). This involves using the heat from flue gas to preheat boiler feed water through an economizer. While this practice is common in large boilers, there is often room for additional heat recovery. A simulation trial was performed to quantify the fuel savings achievable with the implementation of an economizer. The results indicate that approximately 3.6% of fuel used in the boiler could be saved when the water makeup is preheated through the economizer from 41°C to approximately 65°C. This aligns with the general principle that approximately 1% of the fuel used is saved for every 25°C reduction in exhaust gas temperature (Masanet et al., 2008). While this strategy results in a modest decrease in the overall thermal energy percentage, its significance becomes more evident when considering the substantial volume of natural gas consumed at the facility.
In the tomato production facility, it was observed that the steam distribution systems were only partially insulated, and the steam condensate pipelines lacked insulation, leading to a significant loss of sensible heat. Furthermore, approximately 50% of the steam condensate was not recovered in the boiler, resulting in a significant demand for makeup water, which was supplemented with fresh water in a buffer tank. This further contributed to a considerable loss of sensible heat and therefore increased the amount of heating that occurs in the deaerators to heat the makeup water fed to the boiler at a temperature of approximately 41°C or even lower. Improving the thermal insulation of the steam distribution systems and steam condensate pipelines and reclaiming all recoverable steam condensates can result in a substantial thermal energy saving. Process simulation was used to quantify the savings obtained by applying these measures. The results demonstrated that reclaiming hot steam condensate to the boiler at 75°C allows saving approximately 6% of the total methane consumption. This increased temperature of the steam condensate can be achieved by properly insulating with suitable materials the pipelines in which the condensate streams are flowing. The reuse of all steam condensate in boilers not only enables lower fuel consumption but also allows reducing the amount of treated water to be fed to the boiler, with a saving of approximately ~5% of the total freshwater. This, in turn, lowers the electrical energy consumption of pumps for water makeup in the boiler and reduces the amount of chemicals used for makeup water treatment. The significant energy and cost savings associated with the measures described make the implementation of a return condensate piping system highly attractive.
The WEN assessment revealed that significant energy savings can be achieved in the concentration unit, the most energy-intensive operation in the tomato processing facility, by integrating vapor recompression technologies, such as Mechanical Vapor Recompression (MVR) and Thermal Vapor Recompression (TVR). This was considered in the process simulation, and the results showed that utilizing MVR in the triple-effect evaporator could significantly reduce thermal energy consumption, namely, steam usage, by approximately 81%. Instead, the utilization of TVR accounts for a 49% energy consumption reduction in the concentration unit. Single-effect evaporator with TVR is nearly as energy-efficient as a two-effect evaporator without TVR but at a considerably lower cost (Ahmetović et al., 2018). Additionally, a three-effect evaporator system with MVR can halve operating costs compared with a conventional seven-effect evaporator system with TVR (Ahmetović et al., 2018). The selection of the two alternative MVR or TVR technologies depends on several factors, such as facility layout, investment costs, steam production costs, and productivity (Ahmetović et al., 2018). In this case study, TVR is recommendable due to space limitation, production volume, and product concentration.
Thermal energy efficiency improvement in the concentration unit is an additional opportunity in the tomato processing facility. The majority of water evaporated from tomato juice exits the evaporation unit as condensate at a temperature of 71°C. This condensate is cooled down, partly fed to flume systems and partly discharged. The sensible heat in the TEC represents a potential heat resource for the hot break process, which has a significant thermal energy demand. Therefore, thermal energy reduction can be potentially achieved by recovering sensible heat from the tomato water condensate. To implement this strategy, the installation of an additional heat exchanger is required before the hot break step, transforming the hot break process into a two-stage operation. In this configuration, a fraction of the total thermal energy requirement in the hot break is accomplished with recovered sensible heat in the first stage, while the remaining heating is achieved with steam in the second stage. The heat transfer between the TEC and crushed tomatoes in the first stage of the hot break was modeled and simulated using process simulation software to predict the amount of energy that can be recovered (i.e., the potential energy savings gained by partially replacing steam heating). The results demonstrate that approximately 16% of steam demand in the hot break can be saved. Moreover, reduced electrical energy consumption from groundwater pumping, cooling tower use, and wastewater treatment can be accomplished with the reuse of TEC after heat recovery. While this strategy contributes only a modest reduction to the overall thermal and electrical energy consumption at WEN points, the high cost of natural gas in boilers and the increased electrical energy costs could encourage the adoption of this conservation measure.
The preliminary inspection of the electrical energy consumption conducted at the tomato processing facility revealed actions for energy saving. Certain pumps used to feed water from concentration units to flume systems for reuse were operating at their full speed continuously, despite intermittent process flow and water demand variations are likely to occur. Often, these pumps are oversized and are either throttled or bypassed to control the flow and pressure. In this situation, energy efficiency improvement is possible and the installation of VFD can be suggested. The overall energy saving resulting from the installation of VFD to adjust the speed of water pumps to match intermittent water demand was not feasible to be evaluated through process simulation. Alternatively, the evaluation of energy savings in the pumping system is fundamentally calculated by employing affinity laws. Nevertheless, due to constraints in conducting onsite audits, the assessment of energy savings in the pumping system of the facility was based on insights from previous studies. These studies indicate that the implementation of VFD can yield electrical energy savings ranging from 30 to 50% (Arun Shankar et al., 2016). Considering the average energy savings, it was evaluated that an electrical energy saving of 45% in the pumping systems translates into a reduction of the total electrical energy consumption in the facility of approximately 11%.
According to WEN analysis, cooling towers are the second most electrical energy-intensive unit in the tomato processing facility. Cooling towers are extensively used for cooling the TEC produced in the concentration units and the water leaving the cooling section of the pasteurization tunnel. Adjusting the airflow from fans through the installation of VFD when the ambient wet-bulb temperature is below the design conditions might lead to significant electrical energy savings. Just like in the pumping system, evaluating the energy savings achieved by VFD was not possible through process simulation. Furthermore, the application of fan laws, as outlined by Al-Bassam et al., was also not considered, given the auditing limitations and difficulty in identifying the average fan flow speed regulated by VFD in this particular case study (Al-Bassam and Alasseri, 2013). Consequently, the determination of electrical energy savings was carried out by employing a practical rule of thumb for achieving a 20% energy saving proposed by Owen and Carlson (2018), which is in line with the range (22–89%) reported by Saidur (2010). Therefore, to avoid overestimation, this approach assumed that the minimum achievable energy saving of approximately 20% of the cooling tower fan power load could be used to estimate the energy savings achieved by installing a VFD. In this study, the results obtained utilizing the above-mentioned approach indicate that the implementation of a VFD could lead to a saving of approximately 1.7% of the total electrical energy consumed at the facility. Although Trueblood et al. reported that implementing VDF on fans in cooling towers can result in a reduction between 42 and 63%, a range significantly higher than our simplified approach calculated, our results offer an initial estimation of the potential benefits of the proposed action (Trueblood et al., 2013).
The blowers providing the airflow for combustion to the boilers in the tomato processing plant are controlled by inlet vanes or dampers. Thus, additional energy saving can be obtained by substituting vanes/dampers with VFD. Similarly to the procedure described in the previous paragraph, the estimation of the overall electrical energy saving can be derived by installing VFD on boiler blowers, and a rule of thumb proposed by Owen et al. was applied (Owen and Carlson, 2018). The results showed that VFDs allow reducing the total energy consumption at the facility by approximately 0.4%.
Table 3 summarizes the conventional conservation measures that can be implemented in the processing stages of both peeled tomatoes and tomato puree production for energy and water saving.
To quantify the reduction in water, electrical energy, and methane consumption achievable through the implementation of all considered measures, it was necessary to develop an adjustable baseline model for simulating tomato processing. The results of these evaluations, presented in Table 3, showed that preventing water overflow and leakage in critical units, such as the washing flume, cooling tower tank, and water accumulation tank, represents a significant water conservation opportunity. The installation of VFD on water pumps and the resizing of cooling tower tanks could drastically reduce water overflow, with an estimated reduction of total freshwater consumption of approximately 6.5%. Additionally, improving a closed-loop system for the cooling unit is translated into a potential reduction in total freshwater consumption of 4%. The suggested thermal energy conservation measures, namely the recovery of heat from boiler flue gas, the harnessing of sensible heat from TEC in the hot break unit, the improvement of insulation of pipes and steam distribution systems, and the integration of vapor recompression systems in boilers, resulted in a reduction of methane consumption of about 3.6, 3.1, 6, and 16%, respectively. Furthermore, the installation of VFD on water pumps, cooling tower fans, and boiler blowers translates into approximately 13.1% savings on total electrical energy consumption. However, it is worth noting that the effects of conservation measures were evaluated in WEN points, thus they simultaneously affect each other, as shown in Table 3. The measures aimed at preventing overflow and leakage, as well as improving the closed-loop system, have a more pronounced impact on water conservation compared with other strategies and influence electrical energy consumption to a lower extent. Conversely, the installation of VFD on pumps, fans, and blowers is the most impactful strategy for reducing electrical energy consumption. Additionally, the integration of TVR is the most impactful strategy for methane savings, together with the improvement in insulation and condensate recovery, the latter being the least impactful on electrical energy consumption.
From a wider perspective, strategies focusing on the conservation of thermal energy, despite the lower savings achievable, play a pivotal role in a substantial reduction in the environmental burdens of tomato processing due to the complex and impactful extraction, production, transportation, and combustion processes of fossil fuels.
Overall, the suggested strategies yielded substantial savings, notably reducing water consumption by approximately 23.4%, electrical energy by approximately 14.7%, and methane by approximately 28.7%. These findings highlight that a multifaceted approach is needed for sustainable resource management in food processing industries, emphasizing the considerable impact of implementing conventional measures on water, electrical energy, and fuel savings.
To further assess the impact of the envisaged conservation strategies, a sensitivity analysis was conducted using SimaPro, incorporating the new data on water and energy consumption obtained through simulation. The results are shown in Table 4 and Figure 5.
Figure 5. Percentage variation of the environmental impacts in different categories for peeled tomato and tomato puree for sensitivity analysis.
The environmental benefits of employing these conservation strategies in both processing lines are clearly shown. For tomato puree production, environmental impact reductions ranging from 19 to 27% across various categories were observed. Similarly, for peeled tomatoes, the reduction spanned from 16 to 27%. Notably, compared with the base scenario, a significant decrease in global warming potential from 0.083 to 0.069 kg CO2 eq for peeled tomatoes and from 0.135 to 0.110 kg CO2 eq for tomato puree production was found. This accounts for 16 and 19% reduction of GWP, respectively. These reductions are attributed to diminished water, electricity, and methane consumption in the identified hotspots in the processing lines.
These findings highlight the critical role of embracing resource-efficient practices in the food industry to mitigate environmental impact and foster sustainable production. This research suggests that further exploration and implementation of such strategies can pave the way for a more environmentally conscious approach to food processing.
European sustainable production and consumption policies consider that agri-food has a top priority over other industrial sectors. Efficient resource utilization and adoption of innovative methods play a crucial role in mitigating the environmental impact and increasing the sustainability of the food industry. To enhance suitability in the tomato processing industry, an in-depth quantitative LCA analysis with a “gate to gate” approach was carried out, considering only the processing phases of peeled tomato and tomato puree production. The results of this study showed that to produce 1 kg of peeled tomato and 1 kg of tomato puree, the juice preparation in peeled tomato production and the concentration unit in tomato puree production have the highest contribution to global warming. In pursuit of advancing sustainability within the tomato processing sector, the development scenarios, defined through water-energy nexus simulation, reveal that the implementation of the conventional conservation measures identified in this study in the production lines of peeled tomato and tomato puree resulted in water (23.4%), electrical energy (14.7%), and methane (28.7%) savings, and consequently, environmental impact reduction in all categories subsequently led to tomato processing industry which is more sustainable. Some of these conservation measures can be easily applied in the processing plant analyzed in this study, being financially viable. For instance, the installation of insulation on water and steam pipelines is feasible. However, the most sustainable solution can be selected only if an assessment of the alternatives is carried out, considering Design for the Environment (DfE) methods in combination with Life Cycle Assessment (LCA) and Life Cycle Cost (LCC) for an economic evaluation.
However, to improve the accuracy and reliability of the LCA results, it will be necessary to conduct an extensive and accurate inputs and outputs data collection throughout the processing stages of peeled tomato and tomato puree production and carry out the analysis of uncertainties. This will provide a more complete picture of the environmental impacts associated with each stage. In view of improving the sustainability of the tomato processing industry, exploring the effect of introducing innovations, also through novel technologies, can be considered as an important further step along with the evaluation of social and economic life cycle assessments.
The original contributions presented in the study are included in the article/Supplementary material, and further inquiries can be directed to the corresponding author.
EE: Writing – original draft, Visualization, Software, Methodology, Investigation, Data curation, Conceptualization. EA: Writing – original draft, Software, Methodology, Investigation, Formal analysis, Data curation, Conceptualization. GP: Writing – review & editing, Supervision, Conceptualization. GF: Writing – review & editing, Validation, Supervision, Resources, Project administration, Funding acquisition, Conceptualization.
The author(s) declare that financial support was received for the research, authorship, and/or publication of this article. This study was supported by the research project Accelerating Water Circularity in Food and Beverage Industrial Areas around Europe (AccelWater, ID: 958266), Horizon 2020 (call H2020-LCCI-2020-EASME-single stage).
EE, EA, and GF were employed by ProdAl Scarl.
The remaining author declares that the research was conducted in the absence of any commercial or financial relationships that could be construed as a potential conflict of interest.
The author(s) declared that they were an editorial board member of Frontiers, at the time of submission. This had no impact on the peer review process and the final decision.
All claims expressed in this article are solely those of the authors and do not necessarily represent those of their affiliated organizations, or those of the publisher, the editors and the reviewers. Any product that may be evaluated in this article, or claim that may be made by its manufacturer, is not guaranteed or endorsed by the publisher.
The Supplementary material for this article can be found online at: https://www.frontiersin.org/articles/10.3389/fsufs.2024.1400274/full#supplementary-material
Ahmetović, E., Ibrić, N., Kravanja, Z., Grossmann, I. E., Maréchal, F., Čuček, L., et al. (2018). Simultaneous optimisation and heat integration of evaporation systems including mechanical vapour recompression and background process. Energy 158, 1160–1191. doi: 10.1016/j.energy.2018.06.046
Al-Bassam, E., and Alasseri, R. (2013). Measurable energy savings of installing variable frequency drives for cooling towers’ fans, compared to dual speed motors. Energ. Buildings 67, 261–266. doi: 10.1016/j.enbuild.2013.07.081
Anicav (2023). Anicav Numbers. Available at: https://anicav.it/ (Accessed December 15, 2023)
Anton, A., Torrellas, M., Nunez, M., Sevigne, E., Amores, M. J., Muñoz, P., et al. (2014). Improvement of agricultural life cycle assessment studies through spatial differentiation and new impact categories: case study on greenhouse tomato production. Environ. Sci. Technol. 48, 9454–9462. doi: 10.1021/es501474y
Arnal, J., Royo, P., Pataro, G., Ferrari, G., Ferreira, V., López-Sabirón, A., et al. (2018). Implementation of PEF treatment at real-scale tomatoes processing considering LCA methodology as an innovation strategy in the Agri-food sector. Sustain. For. 10, 979–995. doi: 10.3390/su10040979
Arun Shankar, V. K., Umashankar, S., Paramasivam, S., and Hanigovszki, N. (2016). A comprehensive review on energy efficiency enhancement initiatives in centrifugal pumping system. Appl. Energy 181, 495–513. doi: 10.1016/j.apenergy.2016.08.070
Avellán, T., Ardakanian, R., Perret, S. R., Ragab, R., Vlotman, W., Zainal, H., et al. (2018). Considering resources beyond water: irrigation and drainage Management in the Context of the water–energy–food Nexus. Irrig. Drain. 67, 12–21. doi: 10.1002/ird.2154
Bamber, N., Turner, I., Arulnathan, V., Li, Y., Zargar Ershadi, S., Smart, A., et al. (2020). Comparing sources and analysis of uncertainty in consequential and attributional life cycle assessment: review of current practice and recommendations. Int. J. Life Cycle Assess. 25, 168–180. doi: 10.1007/s11367-019-01663-1
Beccali, M., Cellura, M., Iudicello, M., and Mistretta, M. (2009). Resource consumption and environmental impacts of the agrofood sector: life cycle assessment of italian citrus-based products. Environ. Manag. 43, 707–724. doi: 10.1007/s00267-008-9251-y
Bevilacqua, M., Ciarapica, F. E., and Giacchetta, G. (2007). Development of a sustainable product lifecycle in manufacturing firms: a case study. Int. J. Prod. Res. 45, 4073–4098. doi: 10.1080/00207540701439941
Brodt, S., Kramer, K. J., Kendall, A., and Feenstra, G. (2013). Comparing environmental impacts of regional and national-scale food supply chains: a case study of processed tomatoes. Food Policy 42, 106–114. doi: 10.1016/j.foodpol.2013.07.004
Canaj, K., Mehmeti, A., Cantore, V., and Todorovi, M. (2019). LCA of tomato greenhouse production using spatially differentiated life cycle impact assessment indicators: an Albanian case study. Environ. Sci. Pollut. Res. 27, 6960–6970. doi: 10.1007/s11356-019-07191-7
Castillo-Díaz, F. J., Belmonte-Ureña, L. J., López-Serrano, M. J., and Camacho-Ferre, F. (2023). Assessment of the sustainability of the European Agri-food sector in the context of the circular economy. Sustain. Prod. Consum. 40, 398–411. doi: 10.1016/j.spc.2023.07.010
Cellura, M., Longo, S., and Mistretta, M. (2012). Life cycle assessment (LCA) of protected crops: an Italian case study. J. Clean. Prod. 28, 56–62. doi: 10.1016/j.jclepro.2011.10.021
De Marco, I., De Riemma, S., and Iannone, R. (2018). Uncertainty of input parameters and sensitivity analysis in life cycle assessment: an Italian processed tomato product. J. Clean. Prod. 177, 315–325. doi: 10.1016/j.jclepro.2017.12.258
De Marco, I., Miranda, S., Riemma, S., and Iannone, R. (2015). Environmental assessment of drying methods for the production of apple powders. Int. J. Life Cycle Assess. 20, 1659–1672. doi: 10.1007/s11367-015-0971-y
De Marco, I., Riemma, S., and Iannone, R. (2017). Environmental analysis of a mashed tomato production: an Italian case study. Chem. Eng. Trans. 57, 1825–1830. doi: 10.3303/CET1757305
Del Borghi, A., Gallo, M., Strazza, C., and Del Borghi, M. (2014). An evaluation of environmental sustainability in the food industry through life cycle assessment: the case study of tomato products supply chain. J. Clean. Prod. 78, 121–130. doi: 10.1016/j.jclepro.2014.04.083
Del Borghi, A., Moreschi, L., and Gallo, M. (2021). “Life cycle assessment in the food industry” in The interaction of food industry and environment. ed. C. Galanakis (London, UK: Elsevier), 63–118.
Dockrill, P., and Friedrich, F. (2001). Boilers and heaters: Improving energy efficiency. Ottawa: Natural Resources Canada.
Eastern Research Group (1998). Emission factor documentation for Ap-42 section 1.4 natural gas combustion. Morrisville, NC: Eastern Research Group.
Eslami, E., Abdurrahman, E., Ferrari, G., and Pataro, G. (2023a). Enhancing resource efficiency and sustainability in tomato processing: a comprehensive review. J. Clean. Prod. 425:138996. doi: 10.1016/j.jclepro.2023.138996
Eslami, E., Carpentieri, S., Pataro, G., and Ferrari, G. (2023b). A comprehensive overview of tomato processing by-product valorization by conventional methods versus emerging technologies. Food Secur. 12:166. doi: 10.3390/foods12010166
European Commission (2006). Environmental impact of products (EIPRO): Analysis of the life cycle environmental impacts related to the final consumption of the EU-25. Luxembourg. Available at: http://ec.europa.eu/environment/ipp/pdf/eipro_report.pdf
European Commission (2011). International reference life cycle data system (ILCD) handbook- general guide for life cycle assessment- provisions and action steps., first. Luxemburg: Joint Research Centre – Institute for Environment and Sustainability.
European Court of Auditors (2021). Special Report 12/2021: The Polluter Pays Principle: Inconsistent application across EU environmental policies and actions. Available at: https://www.eca.europa.eu/en/publications?did=58811
Fritzson, A., and Berntsson, T. (2006). Efficient energy use in a slaughter and meat processing plant-opportunities for process integration. J. Food Eng. 76, 594–604. doi: 10.1016/j.jfoodeng.2005.06.007
Garnett, T. (2011). Where are the best opportunities for reducing greenhouse gas emissions in the food system (including the food chain)? Food Policy 36, S23–S32. doi: 10.1016/j.foodpol.2010.10.010
Garofalo, P., Andrea, L. D., Tomaiuolo, M., Venezia, A., and Castrignan, A. (2017). Environmental sustainability of agri-food supply chains in Italy: The case of the whole-peeled tomato production under life cycle assessment methodology. J. Food Eng. 200, 1–12. doi: 10.1016/j.jfoodeng.2016.12.007
Ghasemi, S., Rahimi, A., Subramanian, S., and Smith, D. L. (2020). The environmental impacts of organic greenhouse tomato production based on the nitrogen- fi xing plant (Azolla). J. Clean. Prod. 245:118679. doi: 10.1016/j.jclepro.2019.118679
Ghnimi, S., Nikkhah, A., Dewulf, J., and Van Haute, S. (2021). Life cycle assessment and energy comparison of aseptic ohmic heating and appertization of chopped tomatoes with juice. Nature Publishing Group UK 11:13041. doi: 10.1038/s41598-021-92211-1
Grubert, E. A., and Brandt, A. R. (2019). Three considerations for modeling natural gas system methane emissions in life cycle assessment. J. Clean. Prod. 222, 760–767. doi: 10.1016/j.jclepro.2019.03.096
Hospido, A., Davis, J., Berlin, J., and Sonesson, U. (2010). A review of methodological issues affecting LCA of novel food products. Int. J. Life Cycle Assess. 15, 44–52. doi: 10.1007/s11367-009-0130-4
Huijbregts, M. A. J., Steinmann, Z. J. N., Elshout, P. M. F., Stam, G., Verones, F., Vieira, M., et al. (2017). ReCiPe2016: a harmonised life cycle impact assessment method at midpoint and endpoint level. Int. J. Life Cycle Assess. 22, 138–147. doi: 10.1007/s11367-016-1246-y
IEA (2023). Greenhouse Gas Emissions from Energy – Data product. Available at: https://www.iea.org/data-and-statistics/data-product/greenhouse-gas-emissions-from-energy (Accessed May 22, 2023)
ISO (2006a). ISO 14040:2006. Environmental Management-Life Cycle Assessment-Principles and Framework. Geneva: ISO.
ISO (2006b). ISO 14044, 2006. Environmental Management – Life Cycle Assessment – Requirements and Guidelines. Geneva: ISO.
Jiménez-González, C., Kim, S., and Overcash, M. R. (2000). Methodology for developing gate-to-gate life cycle inventory information. Int. J. Life Cycle Assess. 5, 153–159. doi: 10.1007/BF02978615
Khoshnevisan, B., Ra, S., Omid, M., Mousazadeh, H., and Clark, S. (2013). Environmental impact assessment of tomato and cucumber cultivation in greenhouses using life cycle assessment and adaptive neuro-fuzzy inference system. J. Cleaner Product. 30, 1–10. doi: 10.1016/j.jclepro.2013.09.057
Liu, C., Zhang, Z., Liu, S., Liu, Q., Feng, B., and Tanzer, J. (2019). Evaluating agricultural sustainability based on the water-energy-food nexus in the Chenmengquan irrigation district of China. Sustain. For. 11:5350. doi: 10.3390/su11195350
Manfredi, M., and Vignali, G. (2014). Life cycle assessment of a packaged tomato puree: a comparison of environmental impacts produced by different life cycle phases. J. Clean. Prod. 73, 275–284. doi: 10.1016/j.jclepro.2013.10.010
Masanet, E., Worrell, E., Graus, W., and Galitsky, C. (2008). Energy efficiency improvement and cost saving opportunities for the fruit and vegetable processing industry. Berkeley, CA: University of California.
Muñoz, P., Antón, A., Nuñez, M., Paranjpe, A., Ariño, J., Castells, X., et al. (2007). Comparing the environmental impacts of greenhouse versus open- field tomato production in the Mediterranean region. International symposium on high Technology for Greenhouse System Management, 1591–1596.
Owen, G., and Carlson, R. (2018). Benefits of a cooling tower VFD retrofit. Minnesota power systems conference (54th Annual MIPSYCON Conference). Minnesota, United States
Page, G., Ridoutt, B., and Bellotti, B. (2012). Carbon and water footprint tradeoffs in fresh tomato production. J. Clean. Prod. 32, 219–226. doi: 10.1016/j.jclepro.2012.03.036
Parajuli, R., Matlock, M. D., and Thoma, G. (2021). Cradle to grave environmental impact evaluation of the consumption of potato and tomato products. Sci. Total Environ. 758:143662. doi: 10.1016/j.scitotenv.2020.143662
Pérez, D., Soler, M., Delgado, M., and Reigada, A. (2018). Energy use and carbon footprint of the tomato production in heated multi-tunnel greenhouses in Almeria within an exporting Agri-food system context. Sci. Total Environ. 628-629, 1627–1636. doi: 10.1016/j.scitotenv.2018.02.127
Peterson, S. D., Amón, R., Wong, T., Spang, E. S., and Simmons, C. W. (2022). Material and energy flow analysis of craft brewing: a case study at a California microbrewery. Front. Sustain. Food Syst. 6:1028520. doi: 10.3389/fsufs.2022.1028520
Pineda, I. T., Lee, Y. D., Kim, Y. S., Lee, S. M., and Sub, K. (2020). Review of inventory data in life cycle assessment applied in production of fresh tomato in greenhouse. J. Clean. Prod. 282:124395. doi: 10.1016/j.jclepro.2020.124395
Pishgar-komleh, S. H., and Shine, P. (2019). Integration of life cycle assessment, artificial neural networks, and metaheuristic optimization algorithms for optimization of tomato-based cropping systems in Iran. Int. J. Life Cycle Assess. 25, 620–632. doi: 10.1007/s11367-019-01707-6
Reavis, M., Ahlen, J., Rudek, J., and Naithani, K. (2022). Evaluating greenhouse gas emissions and climate mitigation goals of the global food and beverage sector. Front. Sustain. Food Syst. 5, 1–10. doi: 10.3389/fsufs.2021.789499
Ricardo, C., Wyckhuys, K. A. G., and Schrevens, E. (2014). Life cycle assessment of Colombian greenhouse tomato production based on farmer-level survey data. J. Clean. Prod. 69, 26–33. doi: 10.1016/j.jclepro.2014.01.078
Ronga, D., Gallingani, T., Zaccardelli, M., Perrone, D., Francia, E., Milc, J., et al. (2019). Carbon footprint and energetic analysis of tomato production in the organic vs the conventional cropping systems in southern Italy. J. Clean. Prod. 220, 836–845. doi: 10.1016/j.jclepro.2019.02.111
Rosenbaum, R. K., Hauschild, M. Z., Boulay, A.-M., Fantke, P., Laurent, A., Núñez, M., et al. (2018). Life cycle assessment: theory and practice. Berlin: Spinger.
Rossi, V., Cleeve-edwards, N., Lundquist, L., Schenker, U., Dubois, C., Humbert, S., et al. (2014). Life cycle assessment of end-of-life options for two biodegradable packaging materials: sound application of the European waste hierarchy. J. Clean. Prod. 86, 132–145. doi: 10.1016/j.jclepro.2014.08.049
Roy, P., Nei, D., Okadome, H., Nakamura, N., Orikasa, T., and Shiina, T. (2008). Life cycle inventory analysis of fresh tomato distribution systems in Japan considering the quality aspect. J. Food Eng. 86, 225–233. doi: 10.1016/j.jfoodeng.2007.09.033
Saidur, R. (2010). A review on electrical motors energy use and energy savings. Renew. Sust. Energ. Rev. 14, 877–898. doi: 10.1016/j.rser.2009.10.018
Stamou, A. T., and Rutschmann, P. (2018). Pareto optimization of water resources using the Nexus approach. Water Resour. Manag. 32, 5053–5065. doi: 10.1007/s11269-018-2127-x
Tomasula, P. M., Datta, N., Yee, W. C. F., McAloon, A. J., Nutter, D. W., Sampedro, F., et al. (2014). Computer simulation of energy use, greenhouse gas emissions, and costs for alternative methods of processing fluid milk1. J. Dairy Sci. 97, 4594–4611. doi: 10.3168/jds.2013-7546
Tomasula, P. M., Yee, W. C. F., McAloon, A. J., Nutter, D. W., and Bonnaillie, L. M. (2013). Computer simulation of energy use, greenhouse gas emissions, and process economics of the fluid milk process. J. Dairy Sci. 96, 3350–3368. doi: 10.3168/jds.2012-6215
Tomato News (2023). Italy: 5.4 million tonnes processed in 2023. Available at: https://www.tomatonews.com/en/italy-54-million-tonnes-processed-in-2023_2_2169.html (Accessed December 16, 2023)
Trueblood, A. J., Wu, Y. Y., and Ganji, A. R. (2013). “Potential for energy, peak demand, and water savings in California tomato processing facilities” in Industrial energy technology conference 2013 (Bryan, TX: Energy Systems Laboratory).
Wernet, G., Bauer, C., Steubing, B., Reinhard, J., Moreno-Ruiz, E., and Weidema, B. (2016). The ecoinvent database version 3 (part I): overview and methodology. Int. J. Life Cycle Assess. 21, 1218–1230. doi: 10.1007/s11367-016-1087-8
Winans, K., Brodt, S., and Kendall, A. (2020). Life cycle assessment of California processing tomato: an evaluation of the effects of evolving practices and technologies over a 10-year (2005–2015) timeframe. Int. J. Life Cycle Assess. 25, 538–547. doi: 10.1007/s11367-019-01688-6
Keywords: process optimization, life cycle assessment, SimaPro, tomato processing industry, water-energy nexus, simulation, SuperPro Designer®
Citation: Eslami E, Abdurrahman E, Pataro G and Ferrari G (2024) Increasing sustainability in the tomato processing industry: environmental impact analysis and future development scenarios. Front. Sustain. Food Syst. 8:1400274. doi: 10.3389/fsufs.2024.1400274
Received: 18 March 2024; Accepted: 03 June 2024;
Published: 12 June 2024.
Edited by:
Ashish Rawson, National Institute of Food Technology, Entrepreneurship and Management, Thanjavur (NIFTEM-T), IndiaReviewed by:
Sumit Kumar, Jain University, IndiaCopyright © 2024 Eslami, Abdurrahman, Pataro and Ferrari. This is an open-access article distributed under the terms of the Creative Commons Attribution License (CC BY). The use, distribution or reproduction in other forums is permitted, provided the original author(s) and the copyright owner(s) are credited and that the original publication in this journal is cited, in accordance with accepted academic practice. No use, distribution or reproduction is permitted which does not comply with these terms.
*Correspondence: Giovanna Ferrari, Z2ZlcnJhcmlAdW5pc2EuaXQ=
†These authors have contributed equally to this work
Disclaimer: All claims expressed in this article are solely those of the authors and do not necessarily represent those of their affiliated organizations, or those of the publisher, the editors and the reviewers. Any product that may be evaluated in this article or claim that may be made by its manufacturer is not guaranteed or endorsed by the publisher.
Research integrity at Frontiers
Learn more about the work of our research integrity team to safeguard the quality of each article we publish.