- 1Environmental Science and Sustainability Program, Harrisburg University of Science and Technology, Harrisburg, PA, United States
- 2Natural Resources Conservation Services, United States Department of Agriculture, Epping, NH, United States
- 3Civil and Environmental Engineering Department, University of New Hampshire, Durham, NH, United States
Coupled aquaponics is the integration of recirculating aquaculture systems (RAS) with hydroponic cropping systems (HCS) into a single system with shared water treatment units. Potential benefits of integration include water conservation, reduced reliance on finite mineral fertilizers, and intensive year-round location-independent production of lean proteins and fresh vegetables. However, coupled aquaponic practitioners have found minimal commercial success to date. This has been mostly due to the use of system designs which are not based on contemporary water treatment principles, especially those for commercial aquaculture. Instead, conventional coupled aquaponic system design has been based on a linear framework assuming fish wastes are readily utilized as plant fertilizers, with minimal emphasis on waste treatment or individual component hydraulic retention times. The result has been economic failures due to misbalancing the cost of inputs, the value of the outputs, and the time required to reach a marketable harvest size for both crops: fish and plants. This manuscript provides theoretical calculations based on existing standards in commercial RAS and HCS for sizing plant, fish, and biofiltration units focused on nitrogenous waste production from fish. Successful integration of HCS and RAS is defined as achieving industry standard production timelines for lettuce (seed to harvest time of 35 days) and Nile tilapia (fry to a 624 g average harvest weight in 35 weeks). Equations and examples to calculate lettuce yield, daily lettuce nitrogen requirement, fish feed rates to achieve specific nitrogen production rates, and fish tank and biofilter volumes are provided.
1. Introduction
Coupled aquaponics is the integration of a recirculating aquaculture system (RAS) and a hydroponic cropping system (HCS) where treated fish culture water is used as a nutrient solution for soilless plant production. Individually, RAS and HCS are prominent components of the controlled environment agriculture (CEA) industry where protected growing conditions are strictly manipulated to provide season-independent production to reduce water usage and increase yield in a minimized, location-independent growing area (Resh, 2013; Benke and Tomkins, 2017; Timmons et al., 2018). The CEA industry is an attractive option for decentralized urban food security, and it is expected to grow as the demand for food and agricultural water are projected to increase by 56 and 60% by 2050, respectively, to meet the needs of the growing global population (Smith and Stwalley, 2018; Boretti and Rosa, 2019; van Dijk et al., 2021). Proponents of aquaponics claim that the integration of RAS and HCS into a coupled system can further optimize CEA production and result in improved environmental sustainability through minimized water and fertilizer use with increased profitability through the sale of multiple locally grown commodities (Love et al., 2014; Goddek et al., 2015; Atique et al., 2022). Additionally, urban food distribution models indicate a market for aquaponics as consumer preference is shifting to regional hubs that provide year-round fresh food production (Feldmann and Hamm, 2015; Broad et al., 2022). Despite the proposed environmental benefits and potential consumer market, commercial-scaled success has been limited.
In practitioner surveys, it was found that the majority of aquaponic systems were not profitable, and that fish production was a substantial source of financial loss (Love et al., 2014, 2015; Pattillo et al., 2022). While aquaponic systems without nutrient supplementation has demonstrated leafy green vegetable production with similar or faster growth rates than hydroponics, it has also been found that the cost of nitrogen (N) and phosphorus (P) by mass were, respectively, up to 14 and 88 times more expensive in fish feed than in inorganic fertilizer salts used in hydroponics (Colt and Schuur, 2021; Atique et al., 2022). These reports suggest that aquaponic systems where fish production is not profitable and is managed predominantly to mineralize feed that is used as the sole nutrient source for plants will likely struggle to cover production costs. A more appropriate production model would meet the fish growth and harvest rates at standards demonstrated to be profitable in the RAS industry. The potential environmental and financial benefits of integrated production could then be achieved by using excess nutrients in culture water for leafy green production commensurate with the HCS industry. This manuscript provides a coupled aquaponic system design template derived from contemporary RAS design principles. This approach focuses on a parallel unit process design for individual fish, plant, and water treatment unit hydraulic retention optimization to maximize fish growth and N production, differing from the conventionally used linear water flow design found throughout much of the published literature on coupled aquaponics.
2. Scaling limitations of traditional coupled aquaponic designs
Many self-designed aquaponic systems are adapted from a template developed at the University of Virgin Islands (UVI) where a single process flow directs nutrients produced by fish to plants (Rakocy et al., 2006; Love et al., 2014). Scalable commercial application is limited since there is little opportunity for controlling water flow rate, nutrient mass loading rates, and organic carbon accumulation as the specific unit processes are not operated under optimal conditions to meet the individual requirements for ideal fish and crop production (Baßmann et al., 2017; Knaus and Palm, 2017; Yang and Kim, 2020). Optimization of an integrated production system requires a design which utilizes hydraulic retention times (HRTs) for waste treatment and crop production unit processes (fish and plants) based on established principles in the RAS and HCS industries (Davison, 1997; Chen et al., 2006; Rusten et al., 2006; Resh, 2013; Summerfelt et al., 2016). Many of the single, in-series culture water process flow systems used in published aquaponics research did not meet the individual requirements for each unit process and therefore would be ineffective for developing scalable production systems (Baßmann et al., 2017; Knaus and Palm, 2017; Yang and Kim, 2020; Ani et al., 2021; Dusci et al., 2021) (Figure 1). Utilizing a system design approach proven to be commercially effective for aquatic food production would allow greater scalability and optimization in coupled aquaponic systems.
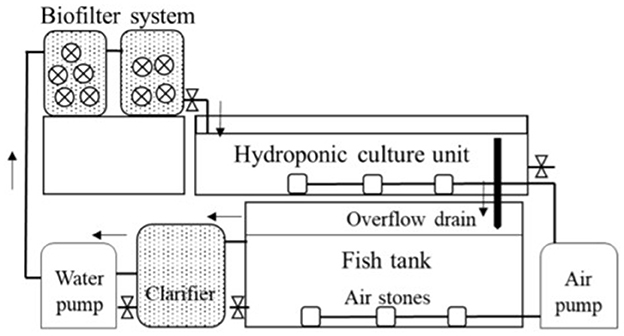
Figure 1. Basic single process flow design characterizing the UVI system design. Schematic of the single process flow system used in Yang and Kim (2020) where research was conducted to determine the effect of system retention time on water quality and fish and plant growth in coupled aquaponics. With a single loop design, only one water flow could be used in the system, preventing optimization of individual units.
3. Potential benefits of adopting contemporary RAS design principles
Applying contemporary RAS engineering principles to develop system design guidelines for consistent productivity is required to enhance economic viability of commercial coupled aquaponics. Adopting a parallel unit process design modeled from RAS engineering principles could separate fish and plant production into isolated, recirculating “loops” within one culture system that shares water treatment unit processes. This retains the benefits of integration while allowing independent unit scaling and operation at contemporary RAS and HCS industry standards (Figure 2). This manuscript provides theoretical calculations derived from existing RAS and hydroponic system design methodologies to size the primary components to estimate fish and crop production rates in an aquaponics system using a parallel unit process approach.
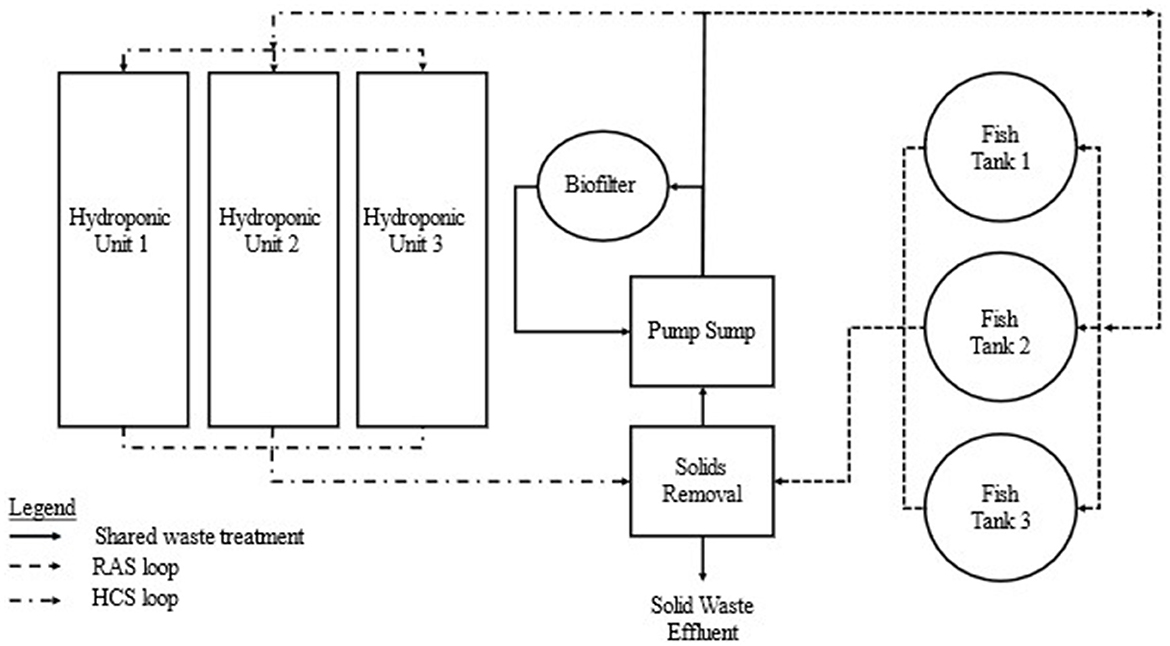
Figure 2. Basic components of a parallel unit process design. Flow schematic demonstrating the parallel “loops” used for individual fish tanks and hydroponic units with a shared waste treatment process for solids removal and biological nutrient conversion. Flow rate and HRT to each unit can be optimized to RAS and HCS industry standards and units can be added (or removed) as they are operated independently without affecting existing operating practices.
4. Designing a coupled aquaponics system with a parallel unit process approach
4.1. System surface area and design assumptions
Greenhouse systems are popular because modifications can be made to allow season-independent growth while harnessing natural light and heat. This design is based on commonly available commercial greenhouse dimensions of 29.26 m long and 9.14 m wide, with a total surface area of 267.6 m2. The floor area of the greenhouse is divided into four primary zones for efficient area utilization (Table 1). Most of the area is devoted to hydroponic production as this will provide the most consistent revenue source. Nile tilapia (Oreochromis niloticus) and lettuce (Lactuca sativa) are some of the most commonly grown fish and vegetable, respectively, according to recent aquaponic practitioner surveys and are the basis for all subsequent fish and plant management guidelines (Love et al., 2014; Pattillo et al., 2022). To ensure consistency in estimated yields, it is assumed that supplemental light, air temperature control, and water temperature control are used to maintain ideal growing conditions throughout the year.
4.2. Scalable hydroponic production
4.2.1. Deep water culture hydroponics
In deep water culture (DWC) hydroponics, plants float on polystyrene rafts in ponds that allow root systems to be fully submerged in nutrient-rich water (Resh, 2013). The ponds provide security against crop loss since sufficient standing water is retained in the event of equipment failure. Furthermore, supplemental lighting is simplified, and harvesting is streamlined in DWC because plants are easily accessible at a uniform elevation. Commercially available rafts are often 0.61 m wide and 1.22 m long, with a variety of options for spacing of grow holes.
Head lettuce, such as Butterhead lettuce, is well-suited to DWC production because it has a lightweight head that can be easily supported by a raft and a relatively small root mass that will not clog the pond. A 5-week seed to harvest timeline for Butterhead lettuce has been established where seedlings are kept in a separate germination area for 2 weeks before being transplanted into a DWC system for 3 weeks (Breckner and Both, 2013; Rakocy and Ebeling, 2018, p. 663–707). Initial transplants require less space than mature plants, and staggering growth into three 1-week phases provides consistent production and efficient space utilization. Ideal spacing for lettuce growth is used to determine the total number of heads across the three different phases and weekly harvest estimates for a system. Each week, lettuce on the phase 3 rafts is harvested, and plants within each phase progress into the next phase growing area. Based on the established growing area and the recommended spacing for lettuce, a 200.67 m2 area could contain 11,067 plants and produce 3,689 heads per week or 191,828 heads per year (Table 2).
4.2.2. Nitrogen requirements
Nitrogen (N) is an essential macro-nutrient and is required for lettuce growth (Marschner, 2011). Smaller plants assimilate a smaller N mass each day while larger plants assimilate a greater mass each day. Maintaining a constant number of plants at each phase allows the calculation of an accurate average daily fish N production rate for ideal plant growing requirements using the following equation (Rakocy and Ebeling, 2018, p. 663–707):
where PN is the production of g N day−1 required for ideal lettuce growth, phases is the number of age-based growing sections, assimilationN is average g N day−1 required by a single lettuce plant, and SF is a safety factor to ensure an adequate nutrient mass is always available. The average N assimilation rate of a lettuce plant in a three-phased DWC growing method is 0.01837 g N plant−1 day−1 (Rakocy and Ebeling, 2018, p. 663–707). Based on this assimilation rate and the addition of a 20% safety factor to ensure sufficient nutrient supply, a DWC pond with 11,067 lettuce plants evenly separated across three age-based phases would require 244 g N day−1.
4.3. Scalable RAS production
4.3.1. Fish feed rate calculations
Fish waste contains high concentrations of total ammoniacal nitrogen (TAN) (Pulkkinen et al., 2019). A daily fish feed rate to produce a desired N loading rate from fish waste can be calculated using the following equation adapted from Timmons et al. (2018):
where g feed is g feed day−1 required to produce a specific N mass, PTAN is the specific production rate of N as g TAN day−1, PC is the protein content of the feed (%), and 0.092 is the average percent of the feed mass excreted as ammonia. A feed rate of 6.63 kg day−1 is required to provide 244 g N day−1 from feed with a 40% protein content.
4.3.2. Fish production schedule
Staggered tilapia production is used to ensure a constant feed and N production rates and to increase fish harvest frequency. DeLong et al. (2009) and McGinty and Rakocy (2015) provide estimates for tilapia growth rates under intensive aquaculture production standards from fry to harvest weight. A daily feed rate per fish was calculated using those growth rates in conjunction with the following equation from Timmons et al. (2018):
where g feed fish−1 is the average feed consumption day−1 fish−1 over a chosen timeframe, weightfinal is the average weight fish−1 in g at the end of this phase, weightinitialis the weight fish−1 in g at the start of this phase, FCR is the average feed conversion ratio at the given age range, agefinal is fish age in days at the end of the phase, and ageinitial is the fish age in days at the start of the phase. Phased production is determined by fish age, desired harvest frequency, or desired number of culture tanks. A five-phased production system can be utilized for a 7-week harvest interval with fry starting at 0.5 g and harvest when growth rates plateau and feed conversion ratio (FCR) increases upon reaching an average weight of 624 g (Losordo et al., 2000; McGinty and Rakocy, 2015) (Table 3).
The average feed rate fish−1 day−1 across all phases is used to determine the total fish population required to consume a desired total feed rate to produce specific N mass each day, and can be calculated using the following equation:
where average g feed fish−1 is the average g feed fish−1 day−1 across all growth phases, n is the total number of growth phases, and phase is the g feed fish−1 day−1 for each phase. In the five-phased system described in Table 3, the average feed rate fish−1 across all phases is 3.96 g day−1. This average feed rate fish−1 and the total system feed rate from Equation 2 can be used to calculate the total fish population that must remain evenly distributed across all growth phases to fully consume the total system feed rate to produce the required daily N loading rate. The total fish population can be calculated using the following equation:
where fishtotal is the number of fish required across all growth phases to produce the desired mass of N day−1, feed ratesystem is the g feed day−1 required to produce the desired mass of N day−1, and average g feed fish−1 phase−1 is the average g feed fish−1 day−1 across all growth phases. A system feeding 6.63 kg day−1 with an average feed rate of 3.96 g feed fish−1 phase−1, would require 1,674 fish evenly distributed across all growth phases. A five-phased grow-out would require 335 fish phase−1. Each harvest would yield 209 kg of fish, for a yearly production of 1,553 kg.
4.3.3. Fish culture tank volume
The water volume of a tank can be calculated when the number of fish, final weight, and maximum stocking density are known using the following equation:
Where V is the volume of water required in a fish tank in m3, fishtank is the number of fish in each tank, densityfinal is the maximum desired stocking density in kg m−3, and weightharvest is the average weight in kg of fish at harvest. The tank volume for each of this five-phased production method will house 335 fish and a maximum stocking density of 40 kg m−3 and is shown in Table 4. A 20% safety factor for fish numbers in Phase 1 may be beneficial to account for higher juvenile mortality rates.
4.3.4. Moving bed biofilm reactor volume
Moving bed biofilm reactors (MBBR) are commonly used in RAS to transform fish lethal TAN into the safer nitrate using multiple heterotrophic bacteria whose growth is facilitated on aerated media (Pulkkinen et al., 2019). Growth media volume in an MBBR is dependent on daily TAN production rates from fish waste, and can be calculated using the following equation (Timmons et al., 2018):
where Vmedia is the volume of growth media in m3, PTAN is the daily TAN production in g day−1, SSAmedia is the specific surface area in m2 m−3 of the media for bacteria growth, and SF is a safety factor to ensure complete nitrification occurs. A system that produces 244 g N day−1, uses media with a 500 m2 m−3 SSA, and has a 20% safety factor would require 0.59 m3 of MBBR media. Research has demonstrated that MBBR is effective when 55% full of media (Timmons et al., 2018). An MBBR requiring 0.59 m3 of media would necessitate a total volume of 1.07 m3.
5. Discussion
Coupled aquaponic management improvements are often considered from only a fish or plant optimization perspective in systems designed with a single process flow (Yang and Kim, 2020; Ani et al., 2021). In an evaluation of tilapia stocking density on water quality, Ani et al. (2021) determined that lower densities resulted in more suitable dissolved oxygen (DO), TAN, nitrite, and nitrate conditions for ideal fish health than more densely stocked systems. These results have limited applicability to a CEA industry focused on intensive production and rapid yields. Based on diagrams in Ani et al. (2021), a single process flow system was used in the study and did not allow independent control over fish tank and biofilter HRTs, both of which have established parameters for maintaining appropriate DO, TAN, nitrite, and nitrate conditions in commercial RAS at stocking densities greater than any used in the study (Rusten et al., 2006; Summerfelt et al., 2016; Timmons et al., 2018; Ani et al., 2021).
For plant optimization, Yang and Kim (2020) compared three total system HRTs (6, 9, and 17 h) to determine ideal nutrient loading rates for crops in a single process flow system. The authors acknowledged that the HRTs were chosen based on DWC flow rates and would not be ideal for intensive fish production, again limiting commercial application where data suggest the fish production is key to financial success (Love et al., 2014; Yang and Kim, 2020; Colt and Schuur, 2021). The HRTs for optimal fish waste removal rates, DWC crop nutrient uptake, and TAN conversion are all different and a single process flow system cannot meet the requirements for each component within a coupled aquaponic system (Baßmann et al., 2017; Knaus and Palm, 2017; Yang and Kim, 2020; Ani et al., 2021; Dusci et al., 2021). These results demonstrate that scalability is limited and individual unit improvement without sacrificing optimization in a different unit is difficult to achieve in a linear approach.
In contrast, this work integrates principles proven to be effective in the RAS and HCS industries to provide practitioners with a design template from a N mass balance that permits individual unit control. The isolated loops in a parallel unit process design provide water flow rate control to each component, which can then be operated at ideal conditions regardless of scale (Table 5). Additional loops with different flow rates can be added, or removed, without affecting existing units. This allows multiple hydroponic methods to increase crop diversity and the opportunity to incorporate fingerling production with reduced flow rates, while maintaining the precise HRTs identified to meet differing fish and plant requirements.
6. Conclusions
Consumer interest in locally grown CEA produce combined with the growing limitations of traditional agricultural methods to meet vegetable and protein demands indicates the potential for a successful coupled aquaponics industry (Feldmann and Hamm, 2015; van Dijk et al., 2021; Broad et al., 2022). To date, minimal economic success has been achieved through aquaponics, especially if fish production fails to be profitable (Love et al., 2014; Colt and Schuur, 2021). Although RAS is one of the most prominent aquaculture methods, much of the recently published coupled aquaponics literature does not incorporate commercial RAS designs or operating standards into experimental systems when modeling production for practitioner application (Baßmann et al., 2017; Knaus and Palm, 2017; Food Agriculture Organization of the United Nations., 2020; Yang and Kim, 2020; Ani et al., 2021; Atique et al., 2022). This manuscript provides guidance on estimating plant and fish populations, yearly production, and unit volumes based on crop growing area, daily N mass requirements for lettuce in a 35-day seed to harvest schedule, and daily N mass production from tilapia in a 35-week fry to 624 g harvest schedule. A parallel unit process design adapted from RAS to incorporate an additional HCS loop is proposed to provide greater control over individual units. Unit volumes, HRTs, and fish feed and growth rates are calculated using established RAS production guidelines.
Additional research is required to further support the commercial aquaponics industry. Production data for yield estimates and comparisons to the individual RAS and HCS industries at commercial scale for additional fish species and vegetable varieties or cash crops would further de-risk practitioner adoption. Economic analysis to determine initial investment costs and potential return on investment is also required and may vary depending on environmental control costs by region as well as the fish and crop chosen. The optimization of aquaponic system design and operation is the first step to continue advancing a potential commercial industry.
Data availability statement
The original contributions presented in the study are included in the article/supplementary material, further inquiries can be directed to the corresponding author.
Author contributions
JT: conceptualization, investigation, data curation, writing—original draft, writing—review and editing, and project administration. RF: conceptualization, validation, writing—review and editing, and visualization. TG: conceptualization, writing—review and editing, and project administration. All authors contributed to the article and approved the submitted version.
Conflict of interest
The authors declare that the research was conducted in the absence of any commercial or financial relationships that could be construed as a potential conflict of interest.
Publisher's note
All claims expressed in this article are solely those of the authors and do not necessarily represent those of their affiliated organizations, or those of the publisher, the editors and the reviewers. Any product that may be evaluated in this article, or claim that may be made by its manufacturer, is not guaranteed or endorsed by the publisher.
References
Ani, J., Manyala, J., Masese, F., and Fitzsimmons, K. (2021). Effect of stocking density on growth performance of monosex Nile Tilapia (Oreochromis niloticus) in the aquaponic system integrated with lettuce (Lactuca sativa). Aquacult. Fish. 7, 328–335. doi: 10.1016/j.aaf.2021.03.002
Atique, F., Lindholm-Lehto, P., and Pirhonen, J. (2022). Is aquaponics beneficial in terms of fish and plant growth and water quality in comparison to separate recirculating aquaculture and hydroponic systems? Water 14, 1447. doi: 10.3390/w14091447
Baßmann, B., Brenner, M., and Palm, H. W. (2017). Stress and welfare of African catfish (Clarias gariepinus Burchell, 1822) in a coupled aquaponic system. Water 9, 504. doi: 10.3390/w9070504
Benke, K., and Tomkins, B. (2017). Future food-production systems: vertical farming and controlled-environment agriculture. Sustain. Sci. Pract. Policy 13, 13–26. doi: 10.1080/15487733.2017.1394054
Boretti, A., and Rosa, L. (2019). Reassessing the projections of the world water development report. npj Clean Water, 2, 15. doi: 10.1038/s41545-019-0039-9
Breckner, M., and Both, A. (2013). Hydroponic Lettuce Handbook. Cornell Controlled Environmental Agriculture. Available online at: https://cpb-us-e1.wpmucdn.com/blogs.cornell.edu/dist/8/8824/files/2019/06/Cornell-CEA-Lettuce-Handbook-.pdf (accessed September 17, 2022).
Broad, G., Marschall, W., and Ezzeddine, M. (2022). Perceptions of high-tech controlled environment agriculture among local food consumers: using interviews to explore sense-making and connections to good food. Agri. Hum. Val., 39, 417–433. doi: 10.1007/s10460-021-10261-7
Chen, S., Ling, J., and Blancheton, J.-P. (2006). Nitrification kinetics of biofilm as affected by water quality factors. Aquacult Eng. 34, 179–197. doi: 10.1016/j.aquaeng.2005.09.004
Colt, J., and Schuur, A. (2021). Comparison of nutrient costs from fish feeds and inorganic fertilizers for aquaponic systems. Aquacult. Eng. 95, 102205. doi: 10.1016/j.aquaeng.2021.102205
Davison, W. (1997). The effects of exercise training on teleost fish, a review of recent literature. Comp. Biochem. Physiol. A Physiol. 117, 67–75. doi: 10.1016/S0300-9629(96)00284-8
DeLong, D., Losordo, T., and Rakocy, J. (2009). Tank Culture of Tilapia. Stoneville, MS: USDA Southern Regional Aquaculture Center, SRAC Publication No. 282.
Dusci, J., Hager, J., Coyle, S., and Tidwell, J. (2021). Evaluation of freshwater prawn, Macrobrachium rosenbergii, for biological solids control in raft aquaponic systems and the protective effectiveness of root guards. J. World Aquacult. Soc. 53, 290–308. doi: 10.1111/jwas.12856
Feldmann, C., and Hamm, U. (2015). Consumers' perceptions and preferences for local food: a review. Food Qual. Pref. 40, 152–164. doi: 10.1016/j.foodqual.2014.09.014
Food and Agriculture Organization of the United Nations. (2020). The State of World Fisheries and Aquaculture 2020. Lima: CGIAR.
Goddek, S., Delaide, B., Mankasingh, U., Ragnarsdottir, K., Jijakli, H., and Thorarinsdottir, R. (2015). Challenges of sustainable and commercial aquaponics. Sustainability 7, 4199–4224. doi: 10.3390/su7044199
Knaus, U., and Palm, H. (2017). Effects of the fish species choice on vegetables in aquaponics under spring-summer conditions in northern Germany (Mecklenburg Western Pomerania). Aquaculture 473, 62–73. doi: 10.1016/j.aquaculture.2017.01.020
Losordo, T., Hobbs, A., and DeLong, P. (2000). The design and operational characteristics of the CP and L/EPRI fish barn: a demonstration of recirculating aquaculture technology. Aquacult. Eng. 22, 3–16. doi: 10.1016/S0144-8609(00)00029-7
Love, D., Fry, J., Genello, L., Hill, E., Frederick, J., Li, X., et al. (2014). An international survey of aquaponics practitioners. PLoS ONE 9, e102662. doi: 10.1371/journal.pone.0102662
Love, D., Fry, J., Li, X., Hill, E., Genello, L., Semmens, K., et al. (2015). Commercial aquaponics production and profitability: findings from an international survey. Aquaculture 435, 67–74. doi: 10.1016/j.aquaculture.2014.09.023
McGinty, A., and Rakocy, J. (2015). Cage Culture of Tilapia. Stoneville, MS:USDA Southern Regional Aquaculture Center, SRAC Publication No. 281.
Pattillo, D., Hager, J., Cline, D., Roy, L., and Hanson, T. (2022). System design and production practices of aquaponic stakeholders. PLoS ONE 17, e0266475. doi: 10.1371/journal.pone.0266475
Pulkkinen, J., Eriksson-Kallio, A., Aalto, S., Tiirola, M., Koskela, J., Kiuru, T., et al. (2019). The effects of different combinations of fixed and moving bed bioreactors on rainbow trout (Oncorhynchus mykiss) growth and health, water quality and nitrification in recirculating aquaculture systems. Aquacult. Eng. 85, 98–105. doi: 10.1016/j.aquaeng.2019.03.004
Rakocy, J., and Ebeling, J. (2018). Aquaponics – Integrating fish and plant culture. In: Timmons, M. B., Guerdat, T. C., and Vinci, B. J., editors. Recirculating Aquaculture. 4th ed. Ithaca, NY: Ithaca Publishing Company LLC.
Rakocy, J. E., Masser, M. P., and Losordo, T. M. (2006). Recirculating Aquaculture Tank Production Systems: Aquaponics—Integrating Fish and Plant Culture. Stoneville, MS: USDA Southern Regional Aquaculture Center, SRAC Publication No. 454.
Resh, H. M. (2013). Hydroponic Food Production: A Definitive Guidebook for the Advanced Home Gardener and the Commercial Hydroponic Grower. (7th ed.). Boca Raton, FL: CRC Press.
Rusten, B., Eikebrokk, B., Ulgenes, Y., and Lygren, E. (2006). Design and operations of the Kaldnes moving bed biofilm reactors. Aquacult. Eng. 34, 322–331. doi: 10.1016/j.aquaeng.2005.04.002
Smith, R., and Stwalley, R. (2018). A Scoping Review of Urban Agriculture: Trends, Current Issues, and Future Research. 2018 ASABE Annual International Meeting. St. Joseph, MI: American Society of Agricultural and Biological Engineers. Available online at: https://elibrary.asabe.org/abstract.asp?aid=49389
Summerfelt, S., Mathisen, F., Buran Holan, A., and Fyhn Terjesen, B. (2016). Survey of large circular and octagonal tanks operated at Norwegian commercial smolt and post-smolt sites. Aquacult. Eng. 74, 105–110. doi: 10.1016/j.aquaeng.2016.07.004
Timmons, M. B., Guerdat, T. C., and Vinci, B. J. (2018). Recirculating Aquaculture. 4th ed. Ithaca, NY: Ithaca Publishing Company LLC.
van Dijk, M., Morley, T., Rau, M., and Saghai, Y. (2021). A meta-analysis of projected global food demand and population at risk of hunger for the period 2010-2050. Nat. Food 2, 494–501. doi: 10.1038/s43016-021-00322-9
Keywords: aquaponics system design, recirculating aquaculture system (RAS), commercial aquaponics production, controlled environment agriculture (CEA), nutrient bioeconomy
Citation: Tetreault J, Fogle RL and Guerdat T (2023) Scalable coupled aquaponics design: Lettuce and tilapia production using a parallel unit process approach. Front. Sustain. Food Syst. 7:1059066. doi: 10.3389/fsufs.2023.1059066
Received: 30 September 2022; Accepted: 06 February 2023;
Published: 23 February 2023.
Edited by:
Kjell Inge Reitan, Norwegian University of Science and Technology, NorwayReviewed by:
Mohammad Mahfujul Haque, Bangladesh Agricultural University, BangladeshMd Abdus Salam, Bangladesh Agricultural University, Bangladesh
Copyright © 2023 Tetreault, Fogle and Guerdat. This is an open-access article distributed under the terms of the Creative Commons Attribution License (CC BY). The use, distribution or reproduction in other forums is permitted, provided the original author(s) and the copyright owner(s) are credited and that the original publication in this journal is cited, in accordance with accepted academic practice. No use, distribution or reproduction is permitted which does not comply with these terms.
*Correspondence: Joseph Tetreault, anRldHJlYXVsdEBoYXJyaXNidXJndS5lZHU=