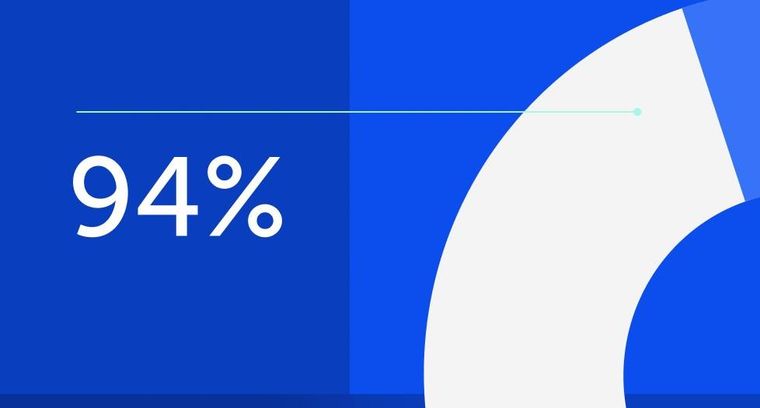
94% of researchers rate our articles as excellent or good
Learn more about the work of our research integrity team to safeguard the quality of each article we publish.
Find out more
POLICY BRIEF article
Front. Sustain. Food Syst., 27 August 2021
Sec. Sustainable Food Processing
Volume 5 - 2021 | https://doi.org/10.3389/fsufs.2021.675626
This article is part of the Research TopicFood Storage, Spoilage and Shelf Life: Recent Developments and InsightsView all 18 articles
Silo storage is considered the best option for wheat storage. However, the storage losses in warehouse storage are also equivalent to silo storage of wheat when proper storage management practices are adopted and the Food Corporation of India (FCI) is the best example of a sustainable food storage system with only 0.3% storage losses in 3 years of wheat storage. The wheat procurement, storage, and distribution system of FCI is unique in the world and handles about 85 million tons of food grains annually by procuring from farmers at the guaranteed Minimum Support Price that meets certain quality standards. This article discusses the role of FCI in food security, warehouse storage management practice as a model, and storage loss level of wheat during storage.
The post-harvest life and quality of agricultural produce depend mainly upon its quality at the time of harvest. However, after the harvest, several interrelated factors form complex interrelationships that may result in the deterioration of quality during storage. Although the harvest period of agricultural produce is relatively short, the demand for consumption extends throughout the year. Thus, the agricultural produce has to be stored safely using proper methods of preservation for consistent supply throughout the year. Cereals, as agricultural produce, occupy an important place in human food, as they are primary sources of energy to the majority of the global population. While farmers store cereals for the purpose of seed, feed, and their own consumption, marketing agencies and traders store them for economic gain. In many cases, Government agencies store food grains to ensure domestic food security, supply, and price stability in the market, and also to earn foreign exchange through export. Therefore, the dynamics of storage in terms of quality maintenance and losses form crucial components of economic and policy decisions. Storage losses are usually in the range of 1–2%, particularly in the developed countries, when grains are stored in well-managed silos with aeration and drying. However, it may be as high as 20–50% in the lesser developed countries, particularly in cover and plinth storage with poorly managed storage facilities (Jayas, 2012). The qualitative losses in wheat stored in jute bags may be as high as 6.6% and reduction of such loss can be brought down to 2% by storing in metal bins (Sinha and Sharma, 2004). Thus, savings of agricultural produce with proper storage is as good as additional production, which emphasizes the need for proper storage management (Jha et al., 2015). The factors responsible for storage losses are environmental, type of storage structure, duration, purpose of storage, treatment during storage, method of packaging and storing grains, etc. Environmental factors mainly consist of temperature, relative humidity (RH), rainfall, exposure to direct sun, air velocity, etc. Besides, biological factors responsible for storage losses are moisture content, insects, pests, microorganisms, and rodents. Before storing wheat grain, it must be dried to a proper level of moisture content; otherwise many problems such as germination and loss of eating quality may occur (Gu et al., 2000; Ueno, 2003). Fluctuations in environmental factors, such as temperature, dampness, and longevity result in significant nutrient losses (Kumar and Singh, 1984). Prolonged storage with high seed moisture percentage also causes a reduction in germination, seedling vigor, accelerated seed aging, increased germination time, electrical conductivity, insect infestation, and eventually loss in seed weight (Mersal et al., 2006). Extreme dry environmental conditions during storage result in faster seed aging, reducing longevity and quality (Labuza, 1980). However, it has been observed that losses during storage in the warehouses are not as high as perceived in the literature, particularly when proper storage management practices are adopted. The best example of proper warehouse storage management practices of food grains, mainly for wheat and rice in developing countries can be said to be of the Food Corporation of India (FCI), which has bare minimum losses in long-duration storage of food grains. FCI handles about 3% of total world cereal production every year. Furthermore, food security in India is largely maintained by them through efficient handling and distribution of food grains. This chapter deliberates on storage management practices of wheat in FCI in their warehouse system and the extent of storage losses due to different factors based on a recent study.
In India, there are ~146.5 million farming families who own 157.8 million ha agricultural land with an average landholding of 1.08 ha in 2015–2016 (Directorate of Economics Statistics (DES) et al., 2020). However, only about 5.7% of farmers have ≥4 ha land and own 29.23% of total agricultural land leaving the rest of them with much smaller landholdings. Therefore, the sustainability of farmers becomes an important issue, particularly in the form of distress sale of the cereals produced as they have very little holding capacity and need quick money for their sustenance.
In order to safeguard such a large number of small and marginal farmers, procurement of staple cereals such as wheat at the minimum support price (MSP) is an important policy tool that involves large scale procurement dispersed in wheat producing states like Punjab, Haryana, Uttar Pradesh, Madhya Pradesh Himachal Pradesh, Uttarakhand, and Bihar. The procurement of wheat involves massive handling of small quantities from a large number of individuals, a mammoth task as it has to be completed during the limited period of 3 months of Rabi harvesting, i.e., from April to June. FCI with other supporting state agencies play a vital role in the procurement of wheat. They procure about 33% of total wheat production in the country for the purpose of supporting farmers through minimum support price (MSP) to save them from distress sale, maintaining food security through the country-wide public distribution system (PDS), stocking reserves as a buffer to meet exigencies and to stabilize market prices through open sale of wheat in case of the steep rise of market prices.
FCI is the nodal agency for procurement, storage, transportation, and distribution of food grains, mainly wheat, rice, and some coarse grains. The storage system of FCI comprises of their owned warehouses, and hired warehouses of central warehousing corporation (CWC), state warehousing corporations (SWC), and privately owned warehouses for the storage of wheat. These agencies have a network of storage depots strategically located all over India. These depots have facility for short-term storage of wheat (<1 year), as well as longer-term storage (between 1 and 3 years). While short-term storage techniques developed by FCI with their experience is known as cover and plinth (CAP) storage system, the longer-term storage consists of covered warehouses and a small proportion in the silos. Such storage depots are located in almost all the states and union territories at more than 1,000 locations. Furthermore, FCI uses 2,085 warehouses and CAP systems for storage of cereals.
Under the contemporary socio-economic scenario, procurement has been showing an increasing trend and FCI along with allied state agencies have procured a record 85 million tons of food grains, i.e., wheat, rice, and coarse grains during the crop year 2019–2020. However, increasing procurement but almost constant off-take (distribution) of food grains under various schemes of the government has been pushing up the stock holding of the government leading to an increased average storage period of food grains. Average wheat procurement was about 36 million tons every year with an increasing trend. Furthermore, the MSP for wheat has been rising every year which had a positive impact on the production of wheat in subsequent years (Figure 1). As a result, the procurement of wheat in the central pool has also been increasing.
An important factor for the rise in stock holding is the ratio of off-take of procured wheat stock under various schemes run by the government of India to the total procured quantity during a given year. It may be seen that the procurement to off-take (O/P) ratio for wheat during the last decade has been declining and has been hovering around 0.80, which has resulted in stock built up of wheat. Under such a scenario the average storage period of stock becomes more than a year. This results in a higher cost of storage for every succeeding year resulting in increasing economic cost. In fact, a conservative estimate of 20% stock at the present level being held for another year would result in an additional cost of Rs 6,000 crores as storage cost.
However, the low off-take of wheat prior to 2020 has ensured enhanced supply of wheat to below poverty line families during the coronavirus disease of 2019 (COVID-19) pandemic lockdown free of cost and saved millions of people from food insecurity in India.
As per production, procurement, consumption, and storage period of wheat states and union territories can be segregated into three regions namely procuring regions, consuming regions, and transit regions. While wheat is procured mainly in surplus wheat-producing states, called procuring regions, the surplus is transported to consuming regions for distribution under National Food Security Act 2013 (NFSA) and other welfare schemes. So, while the storage period of wheat is longer in surplus and some of the consuming regions having adequate storage capacity, the period of storage is quite short in transit regions, mainly hill states with lower storage capacity. Important states under different categories are given in Table 1.
FCI procures wheat mainly from major wheat surplus states of Punjab, Haryana, Uttar Pradesh, Rajasthan, and Madhya Pradesh, which are termed wheat-procuring states. The procurement of wheat is done through a structured procedure from the grain markets in which farmers bring their produce for sale during the harvest season. The duration of procurement lasts 2–3 months after the harvest. The quality parameters applied during procurement are called fair average quality (FAQ) determined by the Government of India. Samples from wheat stock brought by farmers are tested for quality in the mandi after cleaning the stock of foreign matters. Once the stock passes the FAQ parameters, the same is weighed after packing into bags. The quantity of the wheat after weighment is acknowledged through necessary documentation and receipts for payment to farmers. Wheat packed into new jute sacks/gunnies of 50 kg capacity is transported to the warehouses for storage using hired trucks. Storage of such wheat in gunny bags is done in covered warehouses (godowns) through an arrangement called stacking of bags. One stack contains around 3,200–3,300 bags. A substantial amount of wheat is stored in CAP storage as the limited covered godowns are used for storing rice which cannot be stored in CAP. Besides, a small quantity of wheat is also stored in modern silos in bulk form. All the warehouses are equipped with a weighing facility to ensure accurately measurement of weight of stock during operations.
Procured wheat from surplus states is transported to all other remaining states (consuming regions) for distribution under National Food Security Act and other schemes. The major share of transportation is undertaken by railways apart from transportation by road to nearby places and hill states. After the transportation from surplus regions wheat is stored in stacks in the warehouses of consuming regions until the same is issued for consumption following the First-in-First-out (FIFO) principle. Thus, wheat operations involve storage in the warehouses across the country, i.e., procuring as well as consuming regions.
The average duration of storage of wheat is more than 1 year in the warehouses. In order to maintain the good health of the stored wheat in bags, aeration, fumigation, and spraying are undertaken at certain intervals to keep the wheat stock free from insects and pests. For this purpose, samples are taken with a specified procedure as explained below.
The sampling procedures and analysis methods prescribed by the Bureau of Indian Standards (BIS) incorporating IS: 14818 (2000), IS: 2813 (1995), and IS: 4333 Part I Part II (2002) for food grains in respect of moisture content, 1,000-grain weight, and loss due to insect infestation are followed. The sampling is done at the time of initial receipt, periodical quality, and moisture rebuilding inspection and issue of the stock after 100% weighment. The analysis of samples is done in the FCI/CWC Depots laboratories specially set up in most of the depots. The sampling time and analysis procedure followed by FCI are as below:
a) Moisture content measurement: Measured at the time of stacking from the entire stack; fortnightly by taking samples from the periphery of the stacks; and at liquidation time by taking samples from the entire stack.
b) Quality parameters of stack, such as category of food grains (percentage of damaged, discolored, weevilled): Fortnightly by taking samples from the periphery of stacks.
c) Level of infestation: Monthly by taking samples from the periphery of stacks.
d) 1,000-grain weight: Monthly by taking samples from the periphery of stacks.
e) Incidences of rodents, birds, mites, monkey trouble during storage: Monthly by visual observations.
f) Number of spray/fumigation applied with name of the chemicals used: Prophylactic spray of malathion is done on the outer periphery of stacks fortnightly.
g) Recording of weight of spillage: The spilled grains are collected after every 15 days and placed in a bag attached with each stack (called palla bag).
h) Incidence of pilferage, if any: Depot officials report the information to authorized agency.
i) Microbial load in grain samples: Quarterly basis, if suspected.
j) Mycotoxins: Recorded only when suspected.
Losses during storage are unavoidable due to biotic and abiotic factors and such losses are quantified on the basis of weight difference between intake and off-take. The loss during storage of wheat stacked in a warehouse may take place because of a decrease in grain moisture content, reduction in total weight owing to environmental conditions (high temperature and less relative humidity), operational factors (spillage, sampling, weighing system errors, measurement errors, etc.), and dry matter losses due to biotic factors (insects, pests, rodents, respiration of grains, mycotoxins, etc.). Wheat also exhibits gain in weight, mainly due to an increase in moisture content to the equilibrium moisture content (EMC).
Thus, sources of losses are environmental, operational, and biotic factors. However, owing to the fact that nature of all other operations including the control measures for losses due to biotic factors being standardized across all the warehouses, variation of losses mainly occur due to number of times of stacking and de-stacking of wheat bags, i.e., whether it has been stacked first time after procurement (as undertaken in procuring region) or stacked second time after transportation from the procuring region, as done in consuming regions, and change in moisture content. The operational factors such as number of times of stacking becomes important as it has been observed that moisture in the peripheral bags of a given stack is different as compared with the core bags when stored for more than a quarter.
The main causes of damage and spoilage of wheat which are constantly monitored by FCI are summarized in Table 2.
Cover and pinth storage also called CAP storage in FCI is a scientific storage system for storing wheat and paddy. Under the CAP system, the storage site is made at a higher elevation than adjoining ground and away from drainage, canals, and flood-prone area to prevent flooding of the area. Normally, the plinth is made with brick and mortar, which is at least 450 mm above the ground level. Antitermite treatment is given at the time of construction to avoid termite attacks. Stacking of bags is done on dunnage material, usually, wooden crates (frames), placed on a raised platform (plinth), and the stack of food grain bags are covered with 800–1,000-gauge-thick polyethylene sheets (Figure 2).
Dunnage is an important aspect of the storage of bagged food grain that helps in the proper aeration of the bottom layer of food grain bags and prevents it from getting damaged. It can be made from wooden planks in general, on which the bags are stacked. Polyethylene sheet alone or sandwiched between two layers of mats, bamboo mats, ballies, are also used as dunnage for short-term storage. These days, plastic crates have also come into use in place of wooden crates. Wooden dunnage is made using timber planks in which the planks are one over the other and nailed. The lower member of dunnage is of 100 × 50 mm2 rectangular shape and 1 m long. In general, five planks at 362 mm distance from center to center are used. The upper member of dunnage is of 70 × 50 mm2 cross-section, 1.5 m long, and five planks are placed at 237 mm distance from center to center.
CAP storage system is used for short-term storage, usually less than a year. The need for CAP storage arises to store a high quantity of procured wheat and paddy, particularly immediately after the harvest period, at locations where covered storage capacity is not adequate, such as Punjab and Haryana.
A stack of 9.3 × 9.3 × 6.2 m is generally preferred in CAP storage by FCI. The height of the stack may go up to 15 bags. The top of the stack is made in an inverted “V” shape for easy flow of rainwater after covering. A layer of bags filled with straw may be suitable in some areas to minimize the damage due to rain, birds, temperature, and condensation.
After placing the polyethylene cover, the stack is lashed with ropes in some regions where wind velocity is generally high. Plastic net-type covers on the polyethylene cover are more convenient to tie the stacks.
Aeration of the stack becomes important to control temperature and moisture. Lifting the plastic cover is a common method of aeration in the CAP system and the frequency of aeration is once a week in general when the sky is clear. Curative treatments, such as fumigation are also in practice in some places.
The main disadvantages of CAP are that the fumigation is not very effective if the covers are damaged at the time of fumigation, especially due to strong wind, birds, and continued exposure to sun and rains.
FCI mainly uses warehouses for the storage of bagged grains to safeguard them from environmental factors. While wheat and paddy can be temporarily stored in a CAP system, rice has to be compulsorily stored in a covered storage godown. Covered storage godown is a very common grain storage method in many developing countries. Any type of shaded structure or building, such as stone structure, brick wall, walls of corrugated sheet, mud and wattle, walls with or without plaster, earthen walls, floor of stone or cemented with a corrugated sheet, slab, or thatched roof can be used for stacking of bagged grains. However, FCI constructs the warehouses as per their own standards and specifications (Figure 3).
The warehouse system for bagged storage of food grains requires a huge number of labor for making stacks at the time of initial storage and braking stacks at the time of liquidating the food grain bags. Thus, it incurs a high operational cost, especially if the labor charges are high. Losses due to pest attacks, spillage during handling, and operational difficulties are limited when standardized protocols are followed properly. Seepage of water may occur in poorly constructed godown floors and ventilators and may increase the RH inside the warehouse. However, bagged storage systems need less capital investment and sophisticated aeration systems are not required for aeration and fumigation.
The warehouse facility includes the structure, equipment for packaging of grains in bags, handling, ancillary facilities, quality evaluation equipment, and chemicals for pest control. The structures are constructed on a raised platform, well-drained locations, and away from flood-prone areas. The location of the warehouse should be at least 500 m away from waste management industries, such as bone-crushing mills, garbage dumping areas, slaughterhouses, tanneries, hide curing units, sewage water treatment plants, etc. The structures near a carriage head or the main road are preferred. Typically, a godown or warehouse of FCI is made of the dimensions given in Table 3.
The major requirements of a warehouse are as follows:
• Suitable foundation depending upon the site conditions.
• Damp proof and rigid floor, which should be free from cracks and crevices.
• Plinth at 800 mm above the ground level for truck loading and 1,060 mm for the rail fed.
• Platform width of 1,830 mm for road head and 2,440 mm for rail fed.
• Slope of platform 1:40 (minimum).
• Longitudinal walls of brick or stone masonry up to 5.6 m height from the plinth level and 230 mm thick.
• Steel ventilators of opening 1,494 × 594 mm2 placed near the top on the longitudinal walls.
• Air inlets steel ventilator of 620 × 620 mm2 placed at 600 mm above the floor level.
• Suitable number of steel ventilators glazed with fixed wire mesh on the gable walls.
• Single span structural steel or tubular trusses for roof.
• Cantilever trusses are fixed on to RCC columns at 4,000 mm height.
For movement of bags in a godown, a 3-m-wide gallery is kept along the width of the warehouse. A gangway of 2 m is kept along the length and in the center of the warehouse. For inspection of stacks, 1 m space around the entire stacking area should be kept. A typical stack arrangement in a godown is shown in Figure 4. A view of a typical stack inside an FCI godown is shown in Figure 5.
FCI has developed a protocol for wheat storage management in the warehouses. The protocol includes the methods of building a stack inside a warehouse, dunnage specifications, floor plan, prophylactic treatment procedures, fumigation treatment protocol, sampling procedure, and guidelines, dismantling process of the stacks, specifications for jute bags to be used, specifications for trucks to be used for transport, cleanliness, and hygiene protocol, warehouse ancillary equipment requirement, storage protocol for insecticides and chemicals, etc. All the operations are performed professionally by the trained manpower. Overall storage management practice of FCI may be used in any other country.
At present, FCI has a total storage capacity of 41.19 million tons. The warehouse storage capacity of FCI in 2020–2021 was 37.45 million tons (12.93 million tons owned by FCI and 24.52 million tons hired from other agencies and private warehouses). Furthermore, the silo storage capacity of FCI in the same period was 0.76 million tons, whereas storage under CAP is 3.32 million tons (2.57 million tons owned and 0.75 million tons hired). Thus, FCI stores the majority of procured cereals in warehouses (90.18%), whereas CAP storage is only 7.99% and silo storage is 1.83%. Therefore, warehouse management is the specialty of food grains storage by FCI in India.
FCI defines gain/loss during storage of food grains in a warehouse as the change (increase/decrease) in weight after a certain period of storage. However, the quantitative loss of food grains is defined as the reduction in dry matter weight during storage. Losses such as quality deterioration, loss of food value, goodwill or reputation, seed vigor loss, etc., are not a part of the quantitative loss. The trends of storage losses observed by FCI in the last decade are shown in Figure 6.
It may be observed that the storage losses of wheat decreased continuously in the last decade and gain was observed after 2014–2015. However, the gain in weight was due to the increase in moisture content mainly in prolonged storage. As a matter of fact, the dry matter mass decreases with the storage period even when external factors do not affect it. Therefore, a study on the extent of storage losses in wheat stored in the warehouses was conducted during 2013–2019.
A total of 30 depots of FCI were selected from different regions of the country. Multistage random sampling method was adopted to select stacks by taking depots as first-stage units, warehouse within each selected depot as second-stage units, a chamber in each of the selected warehouse as third-stage units, and stacks from each of selected chamber as fourth-stage units. At least two warehouses in each depot and two chambers in each warehouse were selected randomly for data collection. In one chamber, 12 wheat stacks were selected randomly for recording the losses. A set of four schedules were prepared for data collection. Altogether, 677 stacks of wheat (about 150 tons wheat in each stack having 3,000–3,200 bags) were taken in this study and continued for a storage period of 3 years. The stacks were built up, and initial parameters, such as weight, number of bags, moisture content, foreign matter, initial infestation level, broken grain, etc., were recorded. One stack from each chamber was liquidated randomly at 3 months interval, and their data were recorded including 100% weighment of the stack. After liquidation, the wheat was disposed of. All the norms and standards of storage management practices laid down by FCI were followed during the entire study. Samples were taken from each stack as described in section Storage Management. The observations on the physical parameters of the commodity were recorded fortnightly. Besides, environmental data inside the chamber were recorded on a daily basis and ambient environmental data of the locality were collected from the nearby meteorological station.
The sampling procedures and analysis methods prescribed by the Bureau of Indian Standards (BIS) incorporating IS: 14818 (2000), IS: 2813 (1995), and IS: 4333 Part I Part II (2002) for food grains in respect of moisture content, change in weight, 1,000-grain weight, and loss due to insect infestation were followed in this study.
The data were analyzed using MS Excel. The estimation of losses was carried out at depot level initially and pooled at the zone level. The t-test (dependent samples or paired t-test) was conducted to compare the difference in mean values of moisture content, storage loss, etc. at the time of stacking and liquidation. Standard deviation, standard errors, and ANOVA were done using Statistica Version-6 software.
Data collected in this study were scrutinized and matched with the records of depots as well as the hard copy records. The data, which were found unfit or could not get verified, were discarded. The remaining data were analyzed, and storage losses of wheat were estimated as discussed.
The changes in moisture contents with storage periods are reported in Figure 7. The moisture contents of wheat at the time stacking in procuring region were 10.78 ± 0.42%, which were significantly lower (p < 0.05) than the stacking moisture content in the consuming region (11.34 ± 0.13%). Wheat is procured in peak summer season in India and stacking procuring region was done in summer months and hence lower moisture content was expected in procuring region. Furthermore, the wheat was transported from procuring region to the consuming regions in the monsoon season for further storage, and hence the wheat gained some moisture during storage in the procuring region.
Figure 7. Change in moisture content of wheat with storage period (A) consuming regions and (B) procuring regions.
The liquidation moisture content of wheat stored in consuming regions decreased significantly (p < 0.5) with the increase in storage period (Figure 7A) whereas it increased significantly (p < 0.0.5) in the procuring regions (Figure 7B). It may further be observed that the difference between stacking and liquidation moisture contents increased with the storage period and this difference varied according to the stacking moisture content in both regions. Thus, the wheat bags placed in the core of the stack gained/released moisture at a very slow rate and continuous alteration in environmental conditions of the warehouse affected the moisture of wheat in the periphery.
Wheat attained 11–11.50% moisture contents in both regions after 30–36 months of storage irrespective of the stacking moisture content. It indicated that the environmental conditions affected the rate of increase/decrease in moisture content. It may be inferred that the rate of gain/loss due to change in moisture content during storage is mainly dependent on the stacking moisture content.
A typical variation in weight gain/loss observed for the procuring region is shown in Figure 8, which explains the relationship between environmental conditions and moisture gain/losses. The procuring region was the subtropical region of India where all seasons prevail in a year.
Figure 8. Effect of stacking moisture content and season of storage on gain/losses during storage of wheat in procuring region.
The stacking moisture content of wheat in winter, summer, and monsoon seasons were 11.15 ± 0.43%, 10.11 ± 0.28%, and 11.69 ± 0.30%, respectively. The gains in weight of wheat were observed with increase in the storage periods only when storage was done in the summer and winter seasons when the moisture content was ≤ 11.15%. A slight gain in weight was also observed in monsoon-stored wheat up to 18 months storage and thereafter the weight loss was observed with an increase in storage period. It indicated that the moisture content of wheat might reduce in long-duration storage to attain equilibrium. Furthermore, the storage gain/losses increased with the increase in storage period irrespective of the season in which the wheat was stacked and liquidated. Thus, the weight gain/losses depended upon the moisture content at which stacking was done whereas the change in environmental conditions played a limited role.
Weevilled grain percentages were significantly higher in consuming regions in comparison with the procuring regions and increased with the storage period. Procuring region has subtropical climatic conditions whereas the majority of the consuming region has humid climates or coastal regions of India and hence the climatic conditions favored insect growth in the consuming region.
The infestation in food grains may cause loss of dry matter. However, such loss depends purely on the level of infestation. As per FCI norms, no insect per 500 g sample is considered “clear grain,” two insects per 500 g sample is considered “few infestation,” and more than two insects in 500 g sample is “heavy-infested grains.” The “heavy” infestation levels were observed in <2% of the stacks of consuming regions for the entire storage period whereas >74% stacks “clear” level of infestation during the entire storage period. Heavy infestations were observed in some specific locations of the consuming region where high rainfall was observed continuously for the longer duration and fumigation treatment failed repeatedly. In procuring region, the infestation level was clear in >80% stacks for the entire storage period. Curative measures were adopted immediately whenever >0 insect population was observed in any of the fortnightly sampling observations as per FCI norms. The insects do not cause any measurable loss in wheat when the insect population is three or less (Keskin and Ozkaya, 2015) for 1 month. The heavy infestation may cause dry matter loss of 0.03% in 1-month storage period in wheat (Keskin and Ozkaya, 2015).
No dry matter loss was observed in the consuming region up to 9 months of storage and highest loss of 0.12% was found after 18 months of storage due to heavy infestation in some specific depots. The dry matter loss in procuring region was up to 0.30% in 36 months of storage owing mainly due to spillage during heavy stock movement to the consuming regions.
The percentage changes in moisture of wheat were not consistent with storage period in consuming regions because the stacking moisture contents were different for stacks liquidated in different quarters as shown in Figure 7A. A reduction in dry matter weight of <0.18% was observed even after 36 months of storage whereas the net reduction in weight was up to 3% due to moisture decrease during long-term storage of wheat because the stacking was done at >11.5% moisture contents. The total loss during storage increased by the same level in addition to the decrease in moisture content in the same quarter. It may, therefore, be inferred that the total losses in consuming regions were contributed by the decrease in moisture content whereas dry matter loss due to biotic factors contributed up to 0.18% only.
The moisture content of wheat stored in procuring regions increased in all quarters of storage. The gain in moisture content in each quarter was consistent with the stacking moisture content shown in Figure 7B. When dry matter loss and gain in weight due to moisture content were put together, the total gain was consistent. The weevilled grains were 0.00–0.27% during the entire storage period. The dry matter loss up to 0.30% was observed and overall gain in weight of up to 1.25% were observed in the procuring regions.
From the study, it was evident that the final storage losses or gain were a function of moisture change and storage period. A longer period of storage shall always lead to higher net storage losses of wheat over a given period of time. However, the total dry matter loss during storage of wheat for 3 years was not more than 0.3%, which showed that the warehouse storage of food grains is a fairly good practice when proper storage management practices are followed.
FCI is the nodal agency to procure wheat from farmers at the MSP and distribution to the beneficiaries. The other agencies such as CWC, SWCs, and private godown owners hold the wheat on behalf of FCI until FCI transports the stock from surplus to deficient regions or issues for consumption under the National Food Security Act and other welfare schemes. The major responsibilities of FCI are procurement of wheat on MSP, storage, stock transportation, and allocation of wheat to the state governments. Whereas, the state governments identify the eligible families in their states for issuing Ration Cards and run Fair Price Shops (FPSs) through which the wheat is given to the poor families at subsidized rates. The government provides 35 kg wheat per family per month @ Rs. 2/kg to 23.7 million families (about 90 million persons) identified under Antyodaya Anna Yojana (AAY). Besides 703 million persons identified as Priority Households under AAY get 5 kg wheat/rice per person per month @ Rs. 2/kg for wheat and Rs. 3/kg for rice through the FPSs (Department of Food and Public Distribution, 2021). Furthermore, the government provided 5 kg wheat/rice per month free of cost to around 800 million persons in April–October 2020 and May–June 2021 as COVID-19 relief for poor, jobless, and migrant laborers. Thus, the buffer stock management of wheat by the FCI played a crucial role in managing the pandemic situation during 2019–2021 and ensuring no one will sleep without food in India.
The procurement system of FCI for wheat is open ended, i.e., the government guarantees to purchase any quantity of wheat from farmers at MSP, provided they meet the minimum prescribed quality standards. The MSP for wheat increased by 64.5%, i.e., from Rs. 1,170 in 2011–2012 to Rs. 1,925 in 2020–21. The FCI by its own and through state agencies purchased <35% of total wheat production prior to the year 2019–2020. However, during 2019–2020, the procurement increased to 43% of the total production as the COVID-19 relief package. Furthermore, in 2020–2021, the wheat procurement was more than 40% of total production as support to the farmers in COVID-19 situation. The role of FCI to meet any exigency has been visible in the COVID-19 pandemic during which The Government managed to provide food to all the population, particularly to the vulnerable population.
FCI operations of procurement, stack building, liquidation, transportation, distribution, etc. are helpful in providing employment opportunities, which may not be possible in the silo storage system. In the stack building or liquidation, a team of 14 persons works together. Each warehouse has eight teams on average and thus FCI provides employment to about 233 thousand persons annually besides FCI officials. Thus, the FCI not only ensures the food security of India but also provides employment to a large chunk of the population with efficient storage management and related operations of food grains. FCI has developed a sound and efficient storage management practice for the storage of food grains in its long journey of existence for the last 56 years. This model may be replicated in many developing countries for food security and the creation of employment for the poor population.
Prior to 2013, the storage losses of food grains were ≥0.22%. However, with better follow up of storage management practices, after commencement of the study, the storage losses have declined steadily. Furthermore, after 2014–2015, the total quantity delivered by FCI for distribution was more than the quantity stored in the beginning because of weight gain due to an increase in moisture content during storage (Anonymous, 2018). Thus, the study on storage losses of wheat in FCI warehouses helped in improving the implementation of stock management practices in the warehouses.
Food Corporation of India is a unique agency in the world that procures, stores, and distributes more than 70 million tons of cereals annually. The storage of wheat is now mainly done in warehouses with <0.3% dry matter loss after 3 years of storage. Furthermore, the losses of wheat in warehouse storage are not as high as perceived because the loss observed in this study was equivalent to the losses incurred in silo storage done in the developed world. Though this storage system demands huge recurring investment, it provides employment to a large number of rural populations. The warehouse storage management practices of FCI are exhaustive, practically applicable and sufficient to avoid the losses in long-duration storage when followed in a holistic manner. The storage losses of food grains have decreased substantially in FCI warehouses after the storage loss study commenced. Furthermore, the role of FCI food grain stock management was crucial in the COVID-19 pandemic due to which the Government of India managed to provide food to all the population, particularly to population below poverty line, jobless, and migrant laborers.
CK: FCI organization setup, operations, and management. CR: quality control in warehouse management, handling, and operational guidelines. SJ: storage loss study in FCI godowns. RV: planning of paper, editing, storage study, FCI operations, and storage practices. All authors contributed to the article and approved the submitted version.
CK and CLR were employed by company Food Corporation of India.
The remaining authors declare that the research was conducted in the absence of any commercial or financial relationships that could be construed as a potential conflict of interest.
All claims expressed in this article are solely those of the authors and do not necessarily represent those of their affiliated organizations, or those of the publisher, the editors and the reviewers. Any product that may be evaluated in this article, or claim that may be made by its manufacturer, is not guaranteed or endorsed by the publisher.
Anonymous (2018). FCI Handbook-Food Storage Operations Management. Gurugram: Study Material, Institute of Food Security, 116.
Department of Food and Public Distribution (2021). Food Grain Bulletin. Available online at: https://dfpd.gov.in/writereaddata/Portal/Magazine/FBMar2021.pdf (acessed July 1, 2021).
Directorate of Economics Statistics (DES) Department of Agriculture Cooperation Farmers Welfare, Ministry of Agriculture, Farmers Welfare. Government of India. (2020). Agricultural Statistics at a Glance 2019. Available online at: https://eands.dacnet.nic.in/PDF/At%20a%20Glance%202019%20Eng.pdf (accessed July 2, 2021).
Gu, D., Sokhansanj, S., and Haghighi, K. (2000). Influence of floor air entry on grain moisture content, temperature, and bulk shrinkage during ambient air in-bin drying of wheat. Canad. Agric. Eng. 42, 185–193.
IS: 14818 (2000). Cereals and pulses and milled products- sampling of static batches. New Delhi: Bureau of Indian Standards.
IS: 4333 Part I and Part II. (2002). Methods of analysis for foodgrains. Bureau of Indian Standards. New Delhi: Manak Bhawan.
Jayas, D. S. (2012). Storing grains for food security and sustainability. Agric. Res. 1, 21–24. doi: 10.1007/s40003-011-0004-4
Jha, S. N., Vishwakarma, R. K., Ahmad, T., Rai, A., and Dixit, A. K. (2015). Report on Assessment of Quantitative Harvest and Post-harvest Losses of Major Crops and Commodities in India. Ludhiana: ICAR-All India Coordinated Research Project on Post-Harvest Technology.
Keskin, S., and Ozkaya, H. (2015). Effect of storage and insect infestation on the technological properties of wheat. J. Food 13, 134–139. doi: 10.1080/19476337.2014.919962
Kumar, R., and Singh, R. (1984). Levels of free sugars, intermediate metabolites and enzymes of sucrose-starch conversion in developing corn grains. J. Agric. Food Chem. 14, 231–235.
Labuza, T. P. (1980). The effect of water activity on reaction kinetics of food deterioration. Food Tech. 34, 36–59.
Mersal, I. F., El-Emam, A. A., and Amal, M. (2006). Effect of storage period, seed moisture content and insecticides treatment on wheat (Triticum aestivum L.) seed quality. Annals Agric. Sci. Moshtohor. 44, 111–124.
Sinha, M. K., and Sharma, P. D. (2004). Storage performance of wheat in different storage structures. J. Appld. Biol. 14, 83–85.
Keywords: wheat, warehouse storage management, storage loss, food security, Food Corporation of India
Citation: Kumar C, Ram CL, Jha SN and Vishwakarma RK (2021) Warehouse Storage Management of Wheat and Their Role in Food Security. Front. Sustain. Food Syst. 5:675626. doi: 10.3389/fsufs.2021.675626
Received: 03 March 2021; Accepted: 06 July 2021;
Published: 27 August 2021.
Edited by:
Shalini Gaur Rudra, Indian Agricultural Research Institute, IndiaReviewed by:
Francesco Facchini, Politecnico di Bari, ItalyCopyright © 2021 Kumar, Ram, Jha and Vishwakarma. This is an open-access article distributed under the terms of the Creative Commons Attribution License (CC BY). The use, distribution or reproduction in other forums is permitted, provided the original author(s) and the copyright owner(s) are credited and that the original publication in this journal is cited, in accordance with accepted academic practice. No use, distribution or reproduction is permitted which does not comply with these terms.
*Correspondence: R. K. Vishwakarma, cmt2Y2lwaGV0QGdtYWlsLmNvbQ==
Disclaimer: All claims expressed in this article are solely those of the authors and do not necessarily represent those of their affiliated organizations, or those of the publisher, the editors and the reviewers. Any product that may be evaluated in this article or claim that may be made by its manufacturer is not guaranteed or endorsed by the publisher.
Research integrity at Frontiers
Learn more about the work of our research integrity team to safeguard the quality of each article we publish.