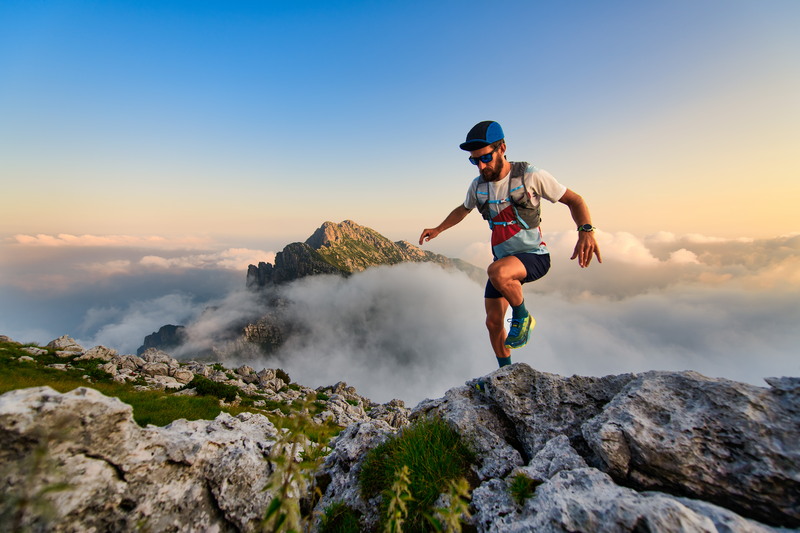
94% of researchers rate our articles as excellent or good
Learn more about the work of our research integrity team to safeguard the quality of each article we publish.
Find out more
BRIEF RESEARCH REPORT article
Front. Sustain. , 30 June 2023
Sec. Alternative Materials
Volume 4 - 2023 | https://doi.org/10.3389/frsus.2023.1169487
Toothbrush handles made from synthetic polymers like polypropylene and polyethylene accumulate in the environment at an annual rate of 1 billion devices per year and without significant degradation, resulting in severe burdens particularly in marine environments. Herein, we report a new process to generate these plastic handles using natural, biopolymer-based components using a direct thermoplastic molding approach, that also offers on-demand degradation of the materials. The materials are prepared directly from whole silk cocoons that are thermoplastically transformed into biodegradable plastic parts for consumer needs, here in the form of toothbrush handles; either with silk alone or in combination with other natural sourced materials such as cellulose, chitosan and hydroxyapatite. We demonstrate the on-demand degradation of these bioplastics in different ways, using natural exogenous protease digestion either offered through soil exposure of the silk based plastics or via unique on-demand activation of proteases sequestered in the plastic materials to drive the degradation on-demand (hydration). The approaches described here demonstrate a new approach to bio-plastic formation and degradation from biopolymers that offers widespread options for future consumer materials with a focus on sustainability.
Consumer plastics are prevalent in daily use and ubiquitous across a wide range of industries. The non-degradable nature of these synthetic plastics imposes huge environmental burdens to the world, with particular recent highlights of marine systems. An example of this challenges is evident in consumer-driven devices used in dentalcare. Dental cavities and tooth decay were one of the most prevalent medical conditions experienced in the US (Heng, 2016) as well as globally (Salari et al., 2022). A major contributor is the lack of proper oral hygiene practices. In addition, dental cavities among children are one of the most widespread non-communicable diseases serving as a major public health crisis (Moynihan, 2016). While there are many factors that play a role in dental cavity prevention and susceptibility, the invention of the bristle toothbrush helped to address this problem, resulting in a global toothbrush market of USD 6.78 billion in 2021 and expected to grow to USD 9.14 billion in 2029 (Toothbursh Market, 2022). Variations in bristle arrangement demonstrate that brushing can reduce plaque scores up to 42% on average, with a variation of 30–53% dependent on original plaque scores (Slot et al., 2012). Thus, both manual and electric toothbrushes remain a staple in societal norms when combating oral cavities.
Toothbrush handles are currently manufactured from polyethylene (PE) and polypropylene (PP). These polymers are among the most used plastics in consumer goods because they are thermoplastic, moldable, and cost-effective, with mature manufacturing infrastructure. For oral applications, they also have excellent physical, mechanical, and thermal properties. They are resistant to acids, bases, humidity, and are non-conductive. However, PE and PP are made from petroleum-based raw materials and have a tremendous carbon footprint when produced and used in commodity products. The widespread manufacturing of PP is suspected to contribute over 1 billion tons of CO2 over the next 30 years (Alsabri et al., 2022). These materials are also non-biodegradable, contributing huge environmental burdens. Approximately one billion toothbrushes are thrown away annually, ending up in the landfills, soil, ocean, and ecosystems. These petroleum products accumulate over time and if not disposed properly, can release toxic chemicals in the process of degradation (Royer et al., 2018; Borunda, 2019).
Recycling can be used to reduce the environmental impact of synthetic plastics, but this requires special recycling programs, separation of the different parts like the bristles and handles and are generally inefficient. In particular, PP waste contributes to environmental problems (Alsabri et al., 2022).
Using biodegradable, natural materials to replace synthetic plastics used for toothbrushes has attracted attention. Current commercially available alternatives include bamboo and wood. Bamboo has served as a sustainable material for centuries because it is durable and plentiful. In an appropriate context, bamboo is flexible and inexpensive. However, there are inherent flaws with bamboo toothbrushes that pose barriers to a sustainable impact. Depending on the individual manufacturer, the quality of the toothbrush handle can differ due to natural porous components within wood and bamboo. This loss of integrity over time can lead to blistering of the wood or bamboo, which leads to irritation of the brush head against the oral mucosa, as well as resulting in bristles falling out of the brush head. In addition to this problem, during manufacturing and machining of the toothbrush handles, the bamboo loses its natural antibacterial properties in the bark, leading to bacteria buildup on the handle and brush head (Admin, 2019). Consumers have also expressed concerns about improper grip placements or the lack of it leading to difficulties with handling the toothbrush. In addition, bamboo or wooden based toothbrush handles are composed mainly of cellulose. Cellulose is a hydrophilic biopolymer due to the abundant hydroxyl groups on the surface, thus, cellulose is prone to absorbing water, leading to structural changes of the handles.
Silk can be a good alternative material for toothbrush handles because silk is biodegradable and has excellent mechanical properties. Using silk to manufacture hard or dense materials can be achieved by the following methods: (1) direct assembly from regenerated silk aqueous solution (Li et al., 2016), (2) Hexafluoro-2-propanol (HFIP) solvent method (Perrone et al., 2014), and (3) regenerated silk amorphous powder thermoplastic molding (Guo et al., 2020b). For commodity plastic replacement that requires mass production, these methods have limitations. Regenerated silk production is costly and inefficient for commodity products requiring multiple processing steps including degumming dissolution, purification, and freeze drying (Rockwood et al., 2011). HFIP is a toxic solvent, thus processing requires extra costs to deal with the chemical. In addition, regenerated silk aqueous solutions require low temperature storage and transportation, which is particularly challenging when dealing with large quantities for commodity products. Direct thermoplastic molding of silk amorphous powders avoids dealing with the storage of large quantities of silk aqueous solution, yet, generating the regenerated powder is still time consuming and costly.
In this paper, we report the direct thermoplastic molding of whole silk cocoons to generate dense hard materials with mechanical strength comparable to commodity plastics such as polyvinyl chloride, polyethylene, and polystyrene. This method avoids the processing of regenerated silk solution and powder, making the production of silk-based commodity products organic solvent free, more efficient, and less expensive. The use of thermoplastic molding means that the consumer plastics industry has the option to directly utilize existing their thermoplastic molding infrastructure but now for sustainable plastics fabrication. The handles generated in this new manufacturing approach demonstrate suitable mechanical strength post-fabrication, biodegradability, and hydrophobicity comparable to commercial products. Furthermore, three different methods were pursued to demonstrate the versatile approaches to biodegradability of the toothbrush handles to achieve on-demand degradation.
Bombyx mori cocoons were shredded into small pieces using a paper shredding machine (bonsaii Cross Cut shredder 3S30 DIN P-4). The shredded pieces of cocoons were packed into predesigned molds, followed by hot pressing at 632 MPa and 145°C for 15 min. Glycerol as plasticizer (1–5%wt) was added to promote the thermoplastic process. After hot pressing, the samples were cooled to room temperature followed by machining to generate the desired shape as toothbrush handles. Enzyme-embedded toothbrush handles were prepared by mixing protease XIV powder (Millipore sigma) with silk cocoon pieces (1%wt) and thermoplastic molding followed by machining. The mixing of protease XIV powder with the silk cocoon pieces were achieved by sprinkling the protease powder on the silk cocoon pieces and packed in the mold upon thermoplastic molding. The mixing of cellulose, HAP, chitosan to make composite plastics with silk was achieved by mixing the material powders with silk cocoon pieces and packed in the mold upon thermoplastic molding.
Protease XIV was dissolved in DPBS solution as 1 and 5 mg/mL. The thermoplastic molded silk cocoon rods (without embedded enzyme) were immersed into the solution and incubated at 37°C. The weight of the silk cocoon rods was weighed before and after incubation at various time point. Digital images were taken to record the morphological changes of the rods within time. The degradation of protease-embedded silk cocoon rods was conducted by immersing the rods into DPBS solution and incubated at 37°C. The weight was measured before and after incubation at various time points. For a third demonstration, the degradation in plant soil was conducted by immersing the silk rods without embedded enzyme into plants with 160 mL of room temperature water added each week. The degradation was monitored by taking digital photos every week.
Figure 1A illustrates the process to generate biodegradable silk cocoon toothbrush handles by thermoplastic molding. The silk cocoons pieces are fed into a shredding machine to generate small pieces of cocoons. The smaller size of the cocoon, the easier to fill the mold for thermoplastic molding. To enable better thermoplastic molding, plasticizers like glycerol were added (1–5 wt%). This is a zero-waste process that directly utilizes the whole cocoon to make the bioplastics without pre-treatment or extraction. Roughly 60 silk cocoons are used per handle.
Figure 1. The process of making toothbrush handles from silk cocoons. (A) Illustration of the thermoplastic molding process. Silk cocoons were first shredded into small pieces and packed in mold followed by thermoplastic molding with glycerol added as plasticizer. (B–D) Digital images of toothbrush handles prepared from thermoplastic molded silk cocoons 163 × 12 × 7mm (right side of each image) compared with wooden toothbrush handles 192 × 13 × 8mm (left side).
Figures 1B–D shows silk toothbrush handles prepared through thermoplastic molding of silk cocoons with 5 wt% glycerol. The molded bars were machinable to desired shape. We compared these new silk handles with commercially available bamboo toothbrush handles. The silk handles were more hydrophobic, with similar density, and are nicely textured as shown in the picture.
The biodegradability of these silk toothbrush handles was demonstrated using three methods. In the first method (Figures 2A, B), the samples were immersed in protease XIV aqueous solutions at two concentrations, 1 mg/mL and 5 mg/mL. The morphology and weight changes were monitored over a month, and it was found that the handles were broken into soft fibers within a week and continued to demonstrate weight decrease over a month. Figures 2C, D shows the weight changes of the silk handles, where the weight initially increased over the first 10 days due to water absorption and swelling, followed by a significant weight decrease. Thus, the toothbrush handles can be degraded by immersion into protease solutions. In commercial use, a protease powder can be supplied with the product to customers to conduct degradation at the end of the product use cycle as one of the options.
Figure 2. Biodegradation of thermoplastic molded silk rods. (A, B) digital images of the biodegradation at two protease concentrations 1 and 5 mg/mL at 37°C. (C) Weight loss of the thermoplastic molded toothbrush handles in 1 and 5 mg/mL protease XIV DPBS solutions at 37°C. The weight was measured by taking the samples out of the degradation solution and the surface water was removed using a paper towel before weighing the sample. (D) Weight measurement of the thermoplastic molded toothbrush handles in 5 mg/mL protease XIV DPBS solutions at 37°C. The samples were collected from the degradation solution and rinsed with water several times and then dried overnight in the fume hood before the weight was measured. (E, F) Degradation of thermoplastic molded handles with protease XIV embedded in the handles in DPBS at 37°C at 1 and 5 wt%. (G) Weight loss of thermoplastic molded toothbrush handles with protease embedded at 1 and 5 wt% when immersed in DPBS at 37°C. The weight remaining was measured by taking the samples out of the degradation solution and the surface water was removed using a paper towel before weighing the sample. (H) Weight measurement of the thermoplastic molded toothbrush handles with 5% protease XIV embedded degrading at 37°C. The samples were collected from the degradation solution and rinsed with water several times and dried overnight in the fume hood before the weight was measured.
In the second method, rather than using a protease solution to promote biodegradation, the protease XIV powder was added into silk cocoons and using thermoplastic molding to entrap the protease in the silk bars. The silk bars maintained their integrity, texture and hydrophobicity as well as mechanical strength with the protease addition. Of particular note, the enzyme remains inactive in the molded silk parts due to the low water content—thus, the parts remain shelf-stable as long as needed, until on-demand degradation is activated via immersion in solution. This method enables the on-demand degradation after product usage with no need to offer a supply of enzyme powders. These protease-embedded silk bars showed significant degradation within a month (Figures 2E, F), thus, the protease activities were maintained after thermoplastic molding. Figures 2G, H shows the weight changes of the silk bars over time. The weight change shows similar trends as degradation in protease solution. The silk bars absorb water, and the weight reached the maximum at day 10 and then started decreasing mass. Using this method, no additional protease powder is needed for product degradation.
In the third method, we demonstrated that immersing silk cocoon toothbrush handles into plant soil induced biodegradation (Figure 3). The rods showed morphological changes within 3 weeks. This experiment shows that the biodegradation of silk cocoon-based toothbrush handles can be achieved at home by immersion of the devices in soil, taking advantage of natural enzymes in the soil environment for the degradation, providing an easy, rapid, instructive, and inexpensive method for bioplastics sustainability at home.
Figure 3. Degradation of thermoplastic molded rods in planted soil with 160 mL of room temperature water added each week.
Thermoplastic molding also enables the one-step process to make bioplastic composites via solid mixing, to further reduce costs. In this process, the secondary biopolymer like cellulose, HAP or chitosan solid materials can be directly mixed with the shredded cocoons and fed into the thermoplastic mold to generate composites via thermoplastic molding (Figure 4). The composites show good structural integrity with well fused structures. A wide range of doping concentration can be selected to match specific material needs. Thus, thermoplastic molding enables the making of bioplastic composites with a wide range of biopolymer choices, without limitations on solubility or reasonable doping concentrations. This approach also enables the incorporation of recycled biopolymers from waste to the bioplastic toothbrush handles.
Figure 4. Composites made from one-step solid mixing of silk cocoons. Examples include with (A) 20% cellulose, (B) 50% cellulose, (C) 10% HAP, (D) 20% HAP, and (E) 10% chitosan.
Herein, we introduced direct thermoplastic molding method to generate toothbrush handles using silk cocoons. The advantages of this process and system include: (1) zero-waste process with input of silk cocoons as well as other biopolymers that are naturally sourced, (2) no pre- or post-chemical treatment, thus, eco-friendly and sustainable, (3) introduction of recycled biopolymers to generate bioplastic composites and reduce costs further, (4) incorporation of bioactive ingredients such as proteases to achieve on demand/accelerated degradation of the materials.
However, there are also drawbacks of the system that require further investigation. For example, the silk cocoon-based toothbrush handles may still absorb some water, leading to product swelling, potentially compromising product quality and mechanical integrity. One relatively simple approach here is a waxy coating to prevent water ingress until on demand degradation is initiated, where the coating layer could be easily melted by heat, or alternatively, fluorination of the silk can be used to negate the water update as we have recently demonstrated (Fountain et al., 2022). Silk cocoons are animal derived products. For use as future sustainable products, ahimsa silk (a method of silk breeding and harvesting that does not kill the animal) can be considered as an alternative (Deshmukh, 2009). In our current study, 100% product break-down and degradation was not pursued, but this has been demonstrated in our prior work and that of others (Numata et al., 2010; Guo et al., 2020a,b). In terms of production costs, raw cocoons are estimated at around $20 per kg, thus, $0.3 is estimated as the cost of raw materials to make one toothbrush handle (15 g). Compared with regenerated silk solutions, the direct use of silk cocoons provides a significant price advantage (Guo et al., 2020b). Cellulose, chitosan or other biowaste components can be incorporated to further reduce costs, while maintaining degradability and sustainability. Although it remains a challenge to compete with the costs of current synthetic plastic toothbrush handles, the incentives of utilizing more environmentally friendly, more sustainable alternative materials should help to influence consumer choices that are less price sensitive. Further, a full lifecycle cost analysis would be helpful to provide further context and perhaps highlight the benefits to this new approach.
We demonstrated a new manufacturing method to generate biodegradable silk toothbrush handles through direct thermoplastic molding of silk cocoons. We show that the degradation of the handles can be achieved through different methods, all of which point to the sustainable production and degradation of the plastic in different environments. This method also enables the production of bioplastic composites, where the secondary biopolymer can be directly incorporated via solid mixing followed by thermoplastic molding, opening a new opportunity to introduce recycled materials from wastes into the system. The concept of embedding enzymes into the bioplastics via thermoplastic molding promotes on-demand degradation, but also presents a new method to incorporate active ingredients into bioplastics, as bioactive bioplastics for materials of the future. Clearly, the methodology demonstrated here is for toothbrush handles, but the approaches, materials, sustainability, and benefits can be considered for any dense, plastic-like parts used in consumer, environmental and other applications.
The raw data supporting the conclusions of this article will be made available by the authors, without undue reservation.
JW and CW organized the database. All authors contributed to conception and design of the study, manuscript revision, read, and approved the submitted version.
We thank the AFOSR (FA9550-20-1-0363) for support of this work.
We thank Scott J. MacCorkle from machine shop in Biomedical Engineering Department at Tufts University for mold machining.
The authors declare that the research was conducted in the absence of any commercial or financial relationships that could be construed as a potential conflict of interest.
All claims expressed in this article are solely those of the authors and do not necessarily represent those of their affiliated organizations, or those of the publisher, the editors and the reviewers. Any product that may be evaluated in this article, or claim that may be made by its manufacturer, is not guaranteed or endorsed by the publisher.
Admin (2019). Plastic vs. Bamboo Toothbrushes – Are They Really Better for the Environment? Greener Tywyn Gwyrdd.
Alsabri, A., Tahir, F., and Al-Ghamdi, S. G. (2022). Environmental impacts of polypropylene (PP) production and prospects of its recycling in the GCC region. Mater. Today Proceed. 56, 2245–2251. doi: 10.1016/j.matpr.2021.11.574
Deshmukh, G. (2009). Ahimsa Peace Silk-An innovation in silk manufacturing. Man-Made Text. India 52, p421–424. https://www.researchgate.net/publication/293416751_Ahimsa_Peace_Silk_-_An_innovation_in_silk_manufacturing
Fountain, J. N., Hawker, M. J., Hartle, L., Wu, J., Montanari, V., Sahoo, J. K., et al. (2022). Towards non-stick silk: tuning the hydrophobicity of silk fibroin protein. ChemBioChem 23, e202200429. doi: 10.1002/cbic.202200429
Guo, C., Li, C., and Kaplan, D. L. (2020a). Enzymatic degradation of bombyx mori silk materials: a review. Biomacromolecules 21, 1678–1686. doi: 10.1021/acs.biomac.0c00090
Guo, C., Li, C., Vu, H. V., Hanna, P., Lechtig, A., Qiu, Y., et al. (2020b). Thermoplastic moulding of regenerated silk. Nat. Mater. 19, 102–108. doi: 10.1038/s41563-019-0560-8
Li, C., Hotz, B., Ling, S., Guo, J., Haas, D. S., Marelli, B., et al. (2016). Regenerated silk materials for functionalized silk orthopedic devices by mimicking natural processing. Biomaterials 110, 24–33. doi: 10.1016/j.biomaterials.2016.09.014
Moynihan, P. (2016). Sugars and dental caries: evidence for setting a recommended threshold for intake. Adv. Nutr. 7, 149–156. doi: 10.3945/an.115.009365
Numata, K., Cebe, P., and Kaplan, D. L. (2010). Mechanism of enzymatic degradation of beta-sheet crystals. Biomaterials 31, 2926–2933. doi: 10.1016/j.biomaterials.2009.12.026
Perrone, G. S., Leisk, G. G., Lo, T. J., Moreau, J. E., Haas, D. S., Papenburg, B. J., et al. (2014). The use of silk-based devices for fracture fixation. Nat. Commun. 5, 3385. doi: 10.1038/ncomms4385
Rockwood, D. N., Preda, R. C., Yücel, T., Wang, X., Lovett, M. L., and Kaplan, D. L. (2011). Materials fabrication from Bombyx mori silk fibroin. Nature Protocols 6, 1612–1631. doi: 10.1038/nprot.2011.379
Royer, S.-J., Ferrón, S., Wilson, S. T., and Karl, D. M. (2018). Production of methane and ethylene from plastic in the environment. PLoS ONE 13, e0200574. doi: 10.1371/journal.pone.0200574
Salari, N., Darvishi, N., Heydari, M., Bokaee, S., Darvishi, F., and Mohammadi, M. (2022). Global prevalence of cleft palate, cleft lip and cleft palate and lip: a comprehensive systematic review and meta-analysis. J. Stomatol. Oral Maxillofac. Surg. 123, 110–120. doi: 10.1016/j.jormas.2021.05.008
Keywords: thermoplastic molding, silk cocoon, biodegradable, synthetic plastic replacement, sustainability
Citation: Wu J, Wiggins RD, Weaver CH, Kugel G and Kaplan DL (2023) Thermoplastic molding of silk protein composite plastic toothbrush handles with on-demand degradability. Front. Sustain. 4:1169487. doi: 10.3389/frsus.2023.1169487
Received: 19 February 2023; Accepted: 19 June 2023;
Published: 30 June 2023.
Edited by:
Elza Bontempi, University of Brescia, ItalyReviewed by:
Amal Bouich, Universitat Politècnica de València, SpainCopyright © 2023 Wu, Wiggins, Weaver, Kugel and Kaplan. This is an open-access article distributed under the terms of the Creative Commons Attribution License (CC BY). The use, distribution or reproduction in other forums is permitted, provided the original author(s) and the copyright owner(s) are credited and that the original publication in this journal is cited, in accordance with accepted academic practice. No use, distribution or reproduction is permitted which does not comply with these terms.
*Correspondence: David L. Kaplan, david.kaplan@tufts.edu
Disclaimer: All claims expressed in this article are solely those of the authors and do not necessarily represent those of their affiliated organizations, or those of the publisher, the editors and the reviewers. Any product that may be evaluated in this article or claim that may be made by its manufacturer is not guaranteed or endorsed by the publisher.
Research integrity at Frontiers
Learn more about the work of our research integrity team to safeguard the quality of each article we publish.