- Institute of Robotics and Mechatronics, German Aerospace Center (DLR), Wessling, Germany
For certain tasks in logistics, especially bin picking and packing, humans resort to a strategy of grasping multiple objects simultaneously, thus reducing picking and transport time. In contrast, robotic systems mainly grasp only one object per picking action, which leads to inefficiencies that could be solved with a smarter gripping hardware and strategies. Development of new manipulators, robotic hands, hybrid or specialized grippers, can already consider such challenges for multi-object grasping in the design stages. This paper introduces different hardware solutions and tests possible grasp strategies for the simultaneous grasping of multiple objects (SGMO). The four hardware solutions presented here are: an under-actuated Constriction Gripper, Linear Scoop Gripper suitable for deform-able object grasping, Hybrid Compliant Gripper equipped with mini vacuum gripper on each fingertip, and a Two-finger Palm Hand with fingers optimized by simulation in pybullet for maximum in-hand manipulation workspace. Most of these hardware solutions are based on the DLR CLASH end-effector and have variable stiffness actuation, high impact robustness, small contact forces, and low-cost design. For the comparison of the capability to simultaneously grasp multiple objects and the capability to grasp a single delicate object in a cluttered environment, the manipulators are tested with four different objects in an extra designed benchmark. The results serve as guideline for future commercial applications of these strategies.
1 Introduction
Robotic grasping has received a significant impulse thanks to artificial intelligence, especially in computer vision (Höfer et al., 2021; Durner et al., 2021) and grasp planning (Ichnowski et al., 2020; Mahler and Goldberg, 2017). In particular, for bin-picking, various solutions are now available as commercial products as well (UniversalRobots, 2023; Ocado 2023). These bin-picking solutions work well for packaged goods or grasping one object at a time. These approaches can only increase the number of picks by optimising the robot’s speed, which often leads to grasping errors and, in turn, reduces the number of successful picks. Another alternative to increase the number of picks is grasping multiple objects simultaneously (Harada and Kaneko, 1998).
For grasping objects in a plane using appropriate pre-grasp actions like push or squeeze using a traditional two-fingered gripper, Sakamoto et al. (2021) proposed a strategy for grasping two objects, while Agboh et al. (2022) proposed a strategy for grasping multiple objects simultaneously. In both cases, a significant increase in the number of picks was demonstrated compared to a single object grasp strategy. Yao and Billard (2023) proposed a multi-object grasp synthesis algorithm for a multi-fingered robotic hand, exploiting the kinematic redundancy and pairwise contacts on arbitrary contact surfaces. However, if such a generated grasp plan is actually feasible to be executed on a robotic platform in a realistic setting was not evaluated and tests were conducted on a upright mounted standalone hand, where a human places the objects between the fingers as per the generated grasp plan. Practical challenges such as, grasping a new object without disturbing the already grasped object in hand, the ability of the hand to grasp small objects, or the ability to simultaneously control all the fingers to perform a coordinate multi-grasp need to be addressed in parallel. Chen et al. (2021) used tactile sensing to estimate the number of objects that will remain stably within the hand after a caging grasp. In all cases, the performance is still low compared to the human hand, which is very well suited for grasping multiple objects in terms of its dexterity, passive compliance, soft fingertip or palm, and sensing capabilities. Sun et al. (2022) provides a taxonomy on multi-object grasping with human hand.
Robotic hands designs were also proposed specifically for multi-object grasping (Nguyen and Chow, 2023; Mucchiani and Yim, 2020; Gyeongji and Kahye, 2023). These solutions simplify multi-object grasping with its embedded mechanical intelligence, but are not very suitable for other manipulation actions or single-object grasping. A multi-purpose robotic hand is crucial to solve at-least both multi-object and single object grasping to cater to a wide variety of grasping use-cases like bin-picking, object sorting, household assistance robotics, and agriculture robotics. Jain et al. (2023) presented a solution suitable for both problems, but is not a fully integrated system, due to the valves, pump and sensors are not integrated in the gripper.
If we look on food handling, this review of robotic food handling Wang et al. (2022) suggests that there may be a need for specialised, cost-effective manipulators. It would be beneficial to consider that multiple object grasping could potentially reduce system costs by increasing picking rates, which is not really addressed in the review. Additionally, grasping from the bottom could be a useful approach for improving the handling of special objects like Daifuku, which remains an open challenge (Qiu et al., 2023). The demonstrated gripper design Bo et al. (2024) has the capability to grasp multiple foot objects and objects grasped from the bottom, however, there may be opportunities to enhance its target grasping performance due to its scoop size. This paper presents four different end-effectors developed at DLR for multi-object grasping (Section 2): Constriction Gripper (CG), a Linear Scoop Gripper (LSG), Hybrid Compliant Gripper (HCG) equipped with mini vacuum gripper fingertip, and a Two-finger Palm Hand (TPH) with inter-finger net support. HCG and TPH are based on the mechatronics developed for the CLASH hand Friedl and Roa (2020) and has variable stiffness. CG uses the same electronics as the CLASH hand but has no variable stiffness. LSG is actuated by
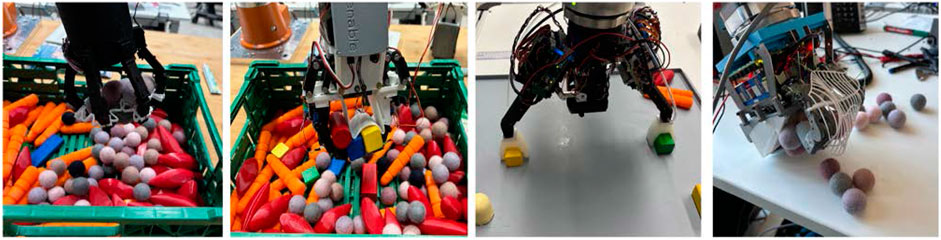
Figure 1. Multi-object grasping with different end-effectors. From left to right: Constriction Gripper, Linear Scoop Gripper, Hybrid Compliant Gripper, and Two Finger Palm Hand.
The requirements of the benchmark are inspired by the food handling use case to handle fruit and vegetable. Necessary materials as the mark paper, the benchmark sheets, the model of the grasp plate and the objects are given in the support material to reproduce the benchmark.The following requirements have to be fulfilled by the grippers:
These evaluations provide valuable insights into the capabilities of the end-effectors to perform different grasping strategies. They also provide baseline guidance (Section 4) for future hardware design aspects that need to be considered to successfully perform both single and multi-object grasping.
2 Hardware overview
The different characteristics of the four end-effectors (Figure 1) developed for this experimental study are summarized in Figure 2. They are discussed further in detail in the following sections.
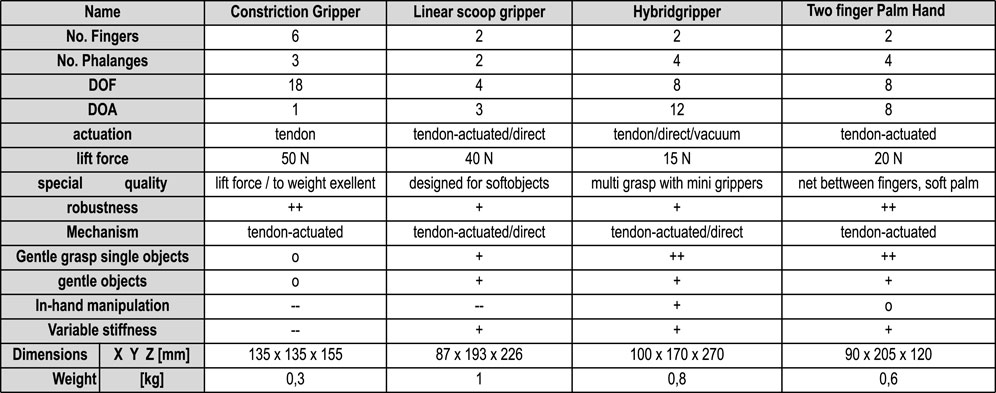
Figure 2. Hardware overview of different end-effectors for multi-object grasping (Explanation for rating symbols: = unsatisfactory; - = fair, o = satisfactory; + = well; ++ = excellent); Explanation: “In-hand manipulation” means, that the gripper can move an object in the hand with dexterity to bring it to a different position or orientation. Explanation dimension: Z ist vertical to the tool flange, X is vertical to the main finger motion (TPH: X to adduction direction).
2.1 Constriction gripper
The first version of the Constriction Gripper (CG) was designed to be simple, energy efficient, and used for caging spherical objects and net bags (Figure 3, left). Most grippers or hands generate the needed torque to grasp objects in the base of the phalanges, and the required torque on the base motor increases with the length of the fingers. The constriction gripper generates the force in the fingertips with a circular chord that ties the fingertips together, and the tips of the chord are commanded from the base of the gripper. This prototype uses spring steel bars as fingers and a Ditex servo to move the tendon that closes or opens the hand. The tendon was guided in the top of the bars by printed parts with PTFE tube inserts to reduce friction. Initial tests showed a good weight to lift ratio of 40 g tare weight to over 6,000 g of load. For higher loads the bonding of the bars failed.
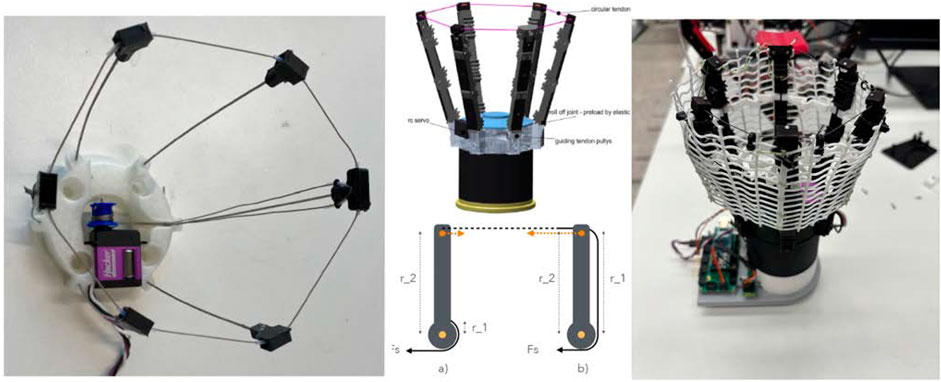
Figure 3. Constriction Gripper. Left: First version of gripper. Middle top: CAD model of updated second version of the gripper used in the experiments. Middle down: A simplified comparison of grip force generation between tendon actuated state of the art gripper a) and constriction gripper b). At a) the grip force is the ratio of
A second prototype of this gripper (Figure 3, right) was built to better adapt to the object’s form and be more robust against impacts.
The bars were replaced by 3D printed fingers with four phalanges. The joints are roll joints similar to Catalano et al. (2014) and have two elastic tendons to push back the finger. The last phalanges include a pulley for the circular tendon to reduce friction. Five of the six fingers are similar. The sixth finger has only three phalanges to include the routing pulleys to guide the tendon toward the actuator. Initial tests as grasping net bags and spherical fruits as well as pullout tests showed that the push-back force of the return springs in the fingers was not enough to pull the circular tendon back, if the actuator was released. Since the trade-off between good adaptation to the object and good gripper opening is not easy to achieve, an extra release actuator, which can pull back the fingers if needed, was included. The six pull-back tendons are collected on one winder and are loose in regular operation. With this modification, the gripper works well for net bags and spherical objects like apples and mangoes. For the multiple object grasp scenario, elastic structures were included between the second and third phalanges to hold small objects inside the gripper. Furthermore, a net was installed between the fingers. These adaptations allow sufficient contact with multiple objects so that even multi-curved objects like shallots can be securely gripped. Table 1 shows a comparative analysis of both versions of the constriction gripper to give insights of he improvements.
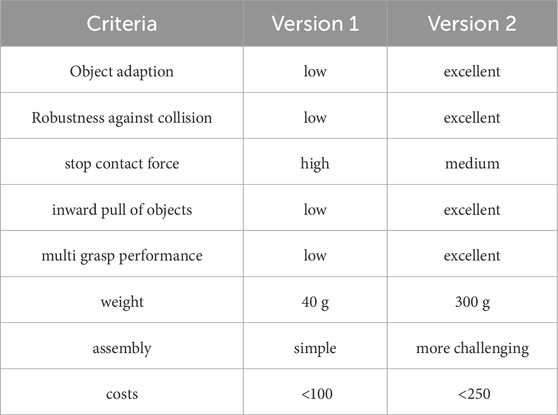
Table 1. Comparative analysis of both versions of the constriction gripper, Note the inward pull of objects, means that while closing the gripper multiple objects will automatically pulled inside the gripper.
2.2 Linear scoop gripper
Linear Scoop Gripper (LSG) was developed using the qbmove Advanced, a variable stiffness actuator. The finger kinematics and design enable soft fixture-based manipulation of deformable food items like fish, meat, and cheese slices, which is also the primary focus in the project SoftEnable, E. U., 2022. Traditional grippers, like the Soft Claw gripper qbrobotics (2023) from qbrobotics, have small opening width and do not generate parallel force when grasping bigger objects. Other traditional grippers like the robotiq 2F-85, a very common used gripper in research, needs a robot compensation movement for top grasp, that the fingers stay in contact with the surface during closing, which can lead to imprecise sliding of the scoopers under the object, if robot and gripper motion is not proper synchronised. And specially developed fish and meat grippers MarelFish (2020) are only suitable for gripping conveyor belts, where the objects are at a distance from each other. Hence a new mechanism was developed to overcome these drawbacks, which has simultaneous movement of the fingertips in one plane and small dimensions in the closed state. Each side of the gripper consists of two parallelograms placed behind each other, connected via gears. The inner parallelogram is pulled outward by a return spring, and due to the coupling, the second parallelogram follows at the same angle. A tendon on one side is connected to the actuator winder and guided by a pulley to the finger base on the other side. On actuation, the tendon pulls the two fingers in parallel. Each finger is equipped with a fingertip changer introduced in Friedl and Roa (2021), which allows one to easily change fingertips suitable for a specific task. A scrapper fingertip is ideal for caging deformable food items and multiple objects simultaneously as shown in a lot of papers He et al. (2021), Babin and Gosselin (2018). In contrast to these papers the idea of LSG, is to come very flat under the fish without extra arm movements and not to fold the fish by the closing motion. Gafer et al. (2020) shows a similar closing behavior, but cannot secure the objects against gravity or single pick objects in clutter scenes. The scrapper fingertip in LSG has a bi stable spring mechanism in its joint. Two small Bluebird A10 servos can actuate this joint and switch the scrapper between the two positions. The servos are connected to a sensor board based on Raspberry Pico, which can also be used to read different
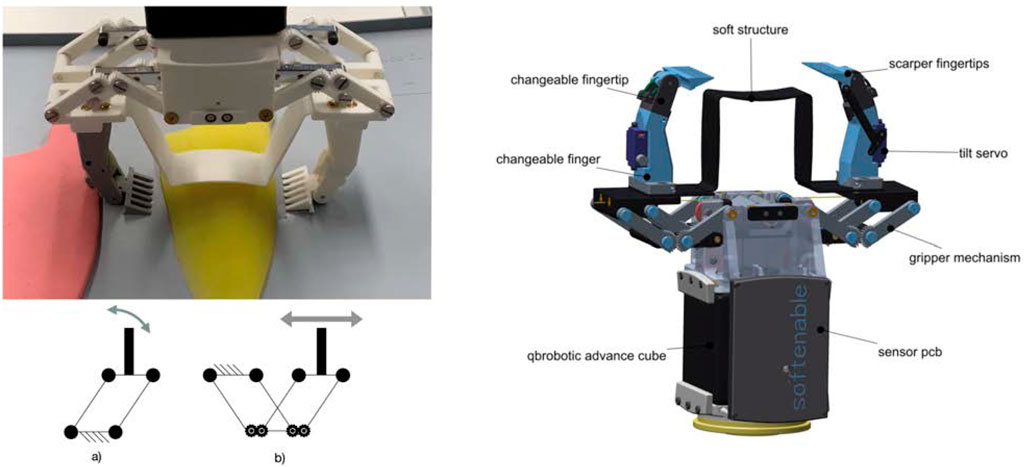
Figure 4. Linear Scoop Gripper. Left top: LSG grasping phantom fish. Left bottom: Schematic of parallel gripper vs. LSG mechanism. Right: Description of different components in LSG. Note that the fingers are easy to change, the grey finger is similar to the white one, build only with a different PLA color. In 2 a newer version of LSG with integrated sensors was used for the photo. For all test the version without sensors was used.
2.3 Hybrid compliant gripper
A two-finger gripper was developed based on the thumb models of CLASH hand as a platform for evaluating different tactile sensors in our previous work (Friedl and Roa, 2021). Basically the results out of the paper showed, that following adaptions allow to solve incomplete benchmark for the punnets, but still not perform as fast and simple, if suction cups are used. The fist change was an extra degree of freedom to tilt the modules, which increase the workspace and second are the special designed sensor fingertip, which gives extra information to the planner to found the right grasping points. In logistics areas, a lot of packaging with flat suction able surfaces are used. Hence, the gripper was equipped with a suction cup at the fingertips connected to a vacuum pump, and an electromagnet at the fingertip to grasp ferromagnetic objects, for example cutlery, which led to the creation of the Hybrid Compliant Gripper (HCG). It is possible to simultaneously grasp two objects in different positions with suction at each fingertip as shown in D’Avella et al. (2023). Although it works well for flat objects, for delicate (for instance, berries) or small curved objects (for instance, baby carrots), this approach is not feasible. We transformed the HCG by adding mini vacuum-powered soft grippers at the fingertips to grasp delicate or small curved objects. In contrast to the commercially available mini vacuum grippers like Peab (2023), or Rochu (2023), the custom-built version for HCG can open wider with over pressure and has a different chamber design. The largest object considered in the experiments in Section 3 is a shallot (Figure 7) with a diameter of around 30 mm. The mini gripper is designed for an open grasp span of 35 mm and a minimum closing of 8 mm. An even wider opening should be possible by adding a suitable high-pressure pump. Figure 5 shows the HCG with mini grippers at the fingertip and the molds to produce the mini grippers. The mini gripper is excellent for delicate objects due to low grasp force. By introducing a separate high-pressure line or valves to switch between vacuum and high-pressure, high grasping forces can also be generated. While the HCG with suction cups could grasp two objects simultaneously (D’Avella et al., 2023), the newly adapted version of HCG can grasp two objects with the mini grippers and a third object using the gripper fingers by accommodating it between the two mini grippers.
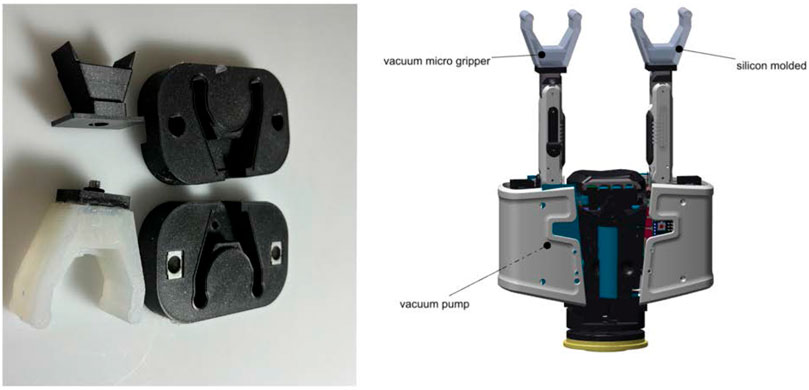
Figure 5. Hybrid Compliant Gripper. Left: Mold for mini vacuum grippper. Right: HCG with mini gripper mounted on the fingertips.
2.4 Two finger palm hand
Humans actively use their palm to provide enough support to grasp multiple objects simultaneously (Sun et al., 2022). Inspired by this, a Two-Finger Palm Hand (TPH) was developed (Figure 6). It has a 3D-printed palm and two 3-link fingers closing opposite to the palm. The two fingers, namely index and pinky, are connected by a flexible structure like a net, which provides additional grasping support by constraining the objects and replaces the missing middle and ring fingers. In contrast to the net like string structure in Wang et al. (2021), the net has connections between the single strings, that small objects cannot slide through the single strings. If the fingers build a bag with the net as shown in 13, missing connections would lead to a lot of lost objects. This is due to the fact that the strings are only preloaded by the weight of the object. The initial net was constructed using a single string between the fingers as shown in 6 right to mount nets similar to fish nets. This was then enhanced by a full printed TPE net, shown in 6 (left). The final version can be seen in the middle of 6, which includes a more dense net for multi-object grasping. The mounting interface to the robot arm is in the back of the palm, facilitating palm grasping, which is suitable for multi-object grasping. However, it is not ideal for single object grasps, as the fingers have to grasp the object with fully bent base joints when the last robot joint stays parallel to the object plane. However, since these fingers have a workspace five times higher than a human finger, single objects can be grasped with an adduction grip (Feix et al., 2016), keeping the object lateral between the fingers. This grip usually is not used by humans due to their kinematics. Furthermore, the adduction grip allows the TPH to generate minimal contact torque, as only one tendon in the finger generates the torque, compared to the palmar motion, where three tendons help together to generate the grasping force. The finger design of TPH is also inspired by CLASH hand (Friedl and Roa, 2020). The finger kinematic was optimized by a pybullet simulation using a similar approach as in Roa et al. (2014) to compare different kinematics to get the best inhand-manipulation ability.
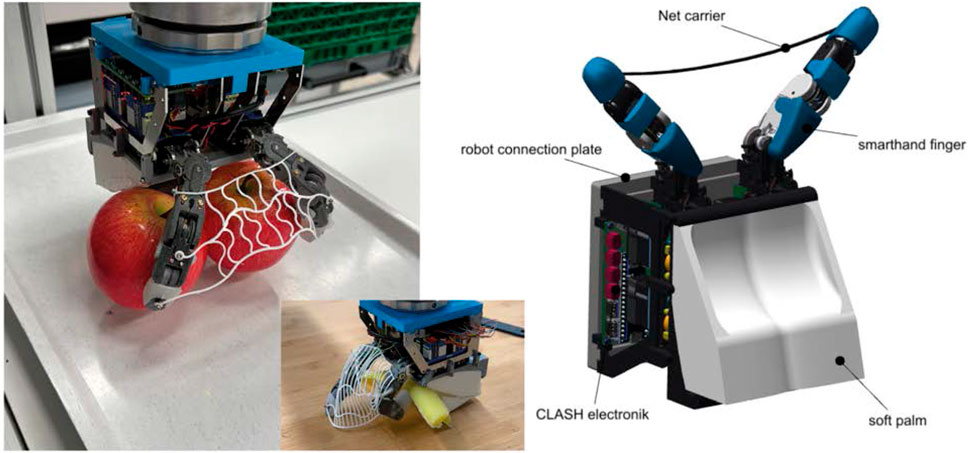
Figure 6. Two Finger Palm Hand (TPH). Left: Grasping two apples between fingers and palm. Middle:TPH with improved net grasping fish phantom. Right: Different components of TPH.
3 Grasping experiments
The Linear Scoop Gripper was design specially for soft objects like fish, so all grippers are tested also on grasping a soft fish-like object. The four end-effectors discussed in the previous section are evaluated for both single-object and multi-object grasping, as both capabilities are crucial. Different evaluation criteria and objects are considered in both cases. A benchmark was designed to compare the grippers in these criteria and the results are shown in the single grasp and multi grasp section. The different-shaped objects (Figure 7) used for evaluation are baby carrots (cylindrical), shallots (ellipsoidal), textile spheres representing cherry tomatoes, and wooden cuboids representing packaged goods. The carrots and shallots are realistic mock ups, 3D printed with thermoplastic polyurethane (TPU) material. Due to the different materials, the friction is also different for all the objects.
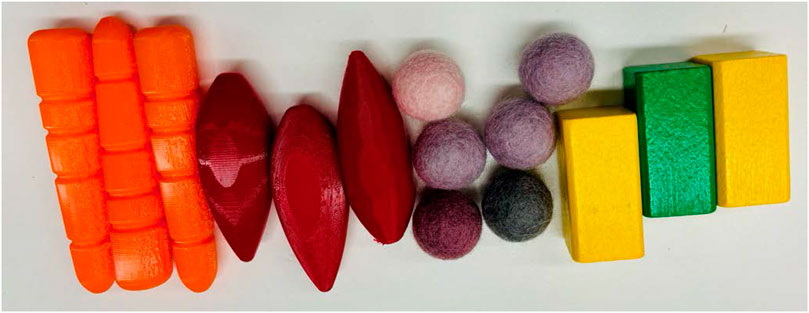
Figure 7. Objects used to evaluate single and multi-object grasping. From left to right: baby carrots, shallots, textile spheres representing cherry tomatoes, and wooden cuboids representing packaged goods.
3.1 Single object grasping
Table 2 top summarizes these main performance measurements for single object grasp. Humans grasp delicate objects such as strawberries in general using precision grasp in order to precisely control the grip force. Simultaneously grasping multiple objects brings the risk of damaging the objects. Moreover, single-object grasping is an essential skill for many scenarios and should not be compromised for multi-object grasping. Therefore, the capability of the four proposed end-effectors to grasp a single object was experimentally verified (Figure 8).
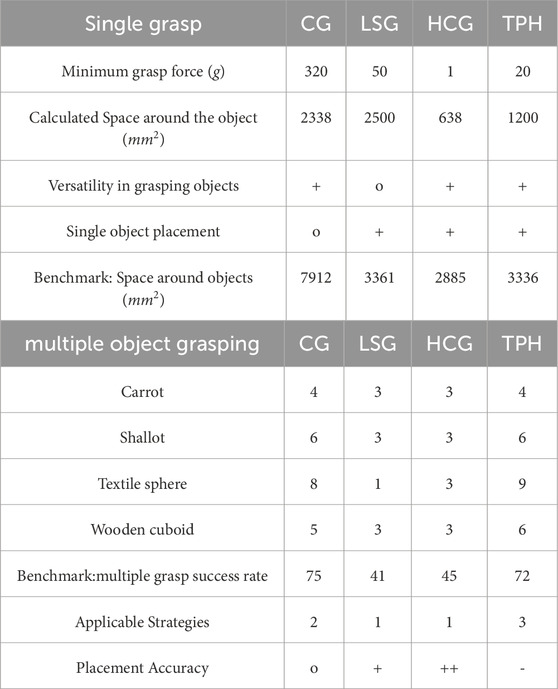
Table 2. Benchmark results for both single and multiple object grasping. (Explanation for rating symbols: = unsatisfactory; - = fair, o = satisfactory; + = well; ++ = excellent. For the placement the rating symbols mean: over 50 mm; - = 30–50 mm; o = 15–30 mm; + = 5–15 mm; 0–5 mm placement error), Note: 30 g minimum grasp force allow to grasp safe strawberries, 50 g is borderline. Note the needed space around the object, is the average for all four tested objects. The multiple grasp success rate is the average for all objects from two up to six objects.
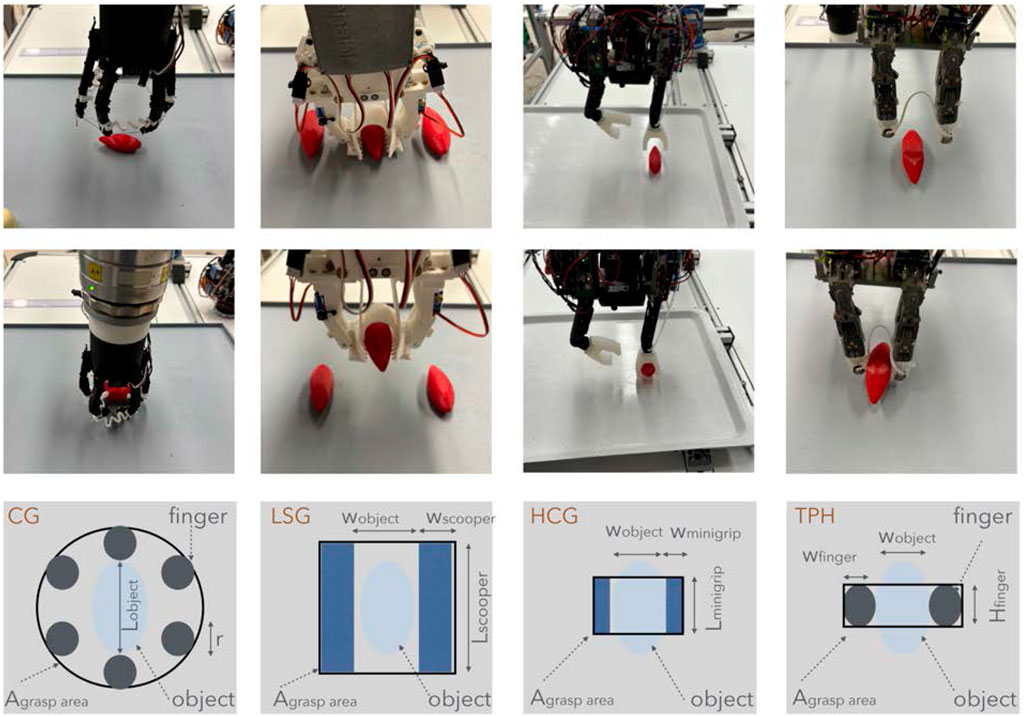
Figure 8. Grasping single items. From left to right: Constriction gripper, SoftEnable linear scoop gripper, HCG with suction fingertips, Two finger Palm Hand; Last row shows the space around each gripper to place it in clutter areas.
An important criteria to compare these end-effectors is to consider the space required around the object to grasp it, which corresponds to the specific geometry of the end-effector. This information could be used in a finger position planner as shown in Sundaram et al. (2020). The needed area for the fingertips of the CG can be seen as a hexagon with the fingertips in the edge of it. A motor motion reduces the perimeter radius
where
For example, for a shallot with a length of
For the same shallot of
The needed space for the HCG is
Another important feature for the end effectors is that they can grasp delicate objects gently, as shown for instance for CLASH in Friedl and Roa (2020). The CG has no variable stiffness actuation nor other contact sensors are available, compared to the rest of the grippers. The only sensor which can be used is the current sensor inherited from the CLASH electronics, which is measured by the ZXCT102, a low offset high-side current monitor. The current consumption depends mainly from closing velocity and at a smaller fraction on the closing position. Figure 9 shows the current consumption in a typical setting. These values can then be used for setting a stop condition. With a force gauge calibrated for
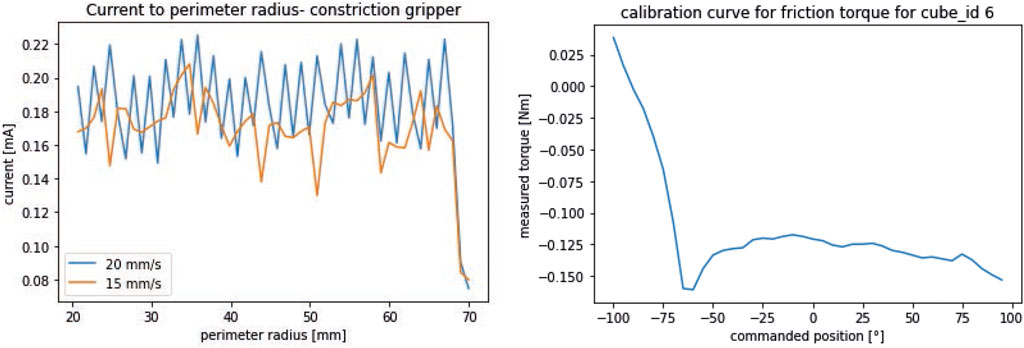
Figure 9. Performance measurements for grippers without direct grasp force measurement. Left: Current consumption of CG depending from the closing velocity for contact measurement; Right: friction torque of LSG. This measurements are needed to control the grasp force of the grippers.
For the Linear Scoop Gripper, the internal torque measurement can be used. The variable stiffness actuation has its own friction torque, which is increased by the finger mechanism and the return springs. Therefore, a measurement is needed to get a position-dependant offset for the stop conditions. The motors are moved over the full motion range and the torque and goal positions are stored. This pair can be then used in the stop conditions. For a closing speed of
The HCG can stop with an applied force of about
3.1.1 Grasping deformable objects
The grasping of deform-able objects like fish is tested on all four grippers, to get information about the multipurpose capability of the grippers and compare them to LSG, which is special designed for fish and meat grasping. For this test a fish-like silicone phantom has to be grasped from the top. The grasping benchmark for fish and meat described in 2.2 was simplified for this test. The object is placed at a fix position and the pose of the arm to the object is given by human. Also the strategy is given by some inertial first trials for each gripper. The grasping was performed for the fish 10 times and can show only a initial guess, how the gripper performance, for this task, due to the focus of the paper is multiple object grasping. The CG fail due to the opening of the finger is not enough to cage the phantom. Landing with some fingers on the object and closing works, but is very rough to the fish, and is not considered as successful due to marks on the fish. The failing of CG can be explained by its finger form which not allow sliding under the fish as HCG AND LSG can do. Also lifting the fish partly with one finger and then placing the next under the fish as the human or the TPH can do, is not possible with only one degree of freedom. The HCG needs to change the fingertips to grasp the fish, if the mini vacuum gripper are not optimizing for this new task by including nail like structures. With scoopers like on the LSG it is not a big problem due to the four degrees of freedom in each finger. More interesting for a multipurpose approach is, if by suction a tool can be taken, to allow to slide under the fish. This works well as long the fish gets not to heavy to push away the tool, while lifting it. For the TPH are more like human strategy is taken as show in Figure 10. One finger push the fish to palm, the slide on the table to get under the fish and lift it then up, the second can support the grasp.
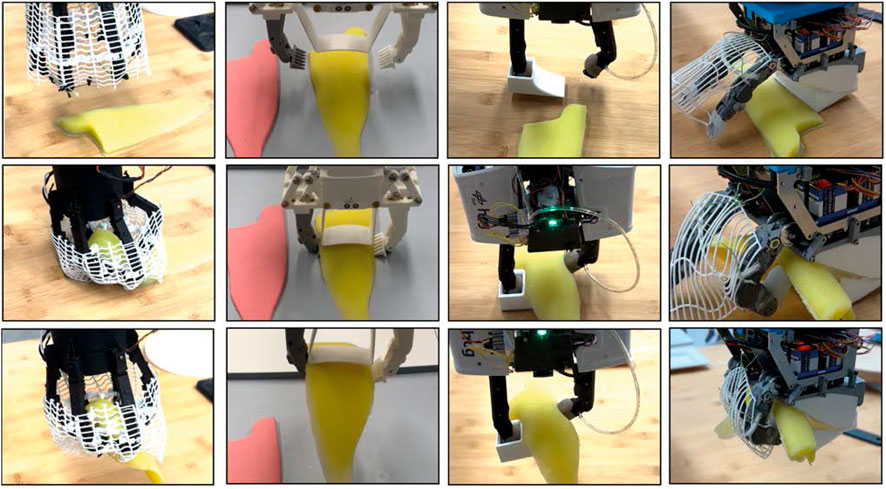
Figure 10. Grasping fish phantom: Left: LSG; Middle; HCG with suctioned slope tool; TPH with human lift strategy.
Out of the experiment two successful fish grasping strategies can be observed, Fingertip with a flat low friction design like scoopers can slide under the fish to grasp it. The needed force to bring the deformable object on the scoopers, can be taken out of the Equation 4 of the inclined plane.
A low angle
3.2 Benchmark for single and multi object grasping
The setup for the benchmark consists (see Figure 11) of a grasp plate with adaptable clutter, this clutter can be changed by six obstacle objects. Furthermore it consists of a release plate to measure the placement. On the release plate is a human readable scale on paper which gives the accuracy of the placement. For simpler and fast evaluation a mobile phone with a face camera or a USB camera can be mounted under the transparent release plate to take pictures of the placement. The position for the grasp and release is one time taught for each gripper and then the grippers has to grasp each object 10 times with obstacles near as possible to the grasp object and release them on the plate. Afterward the obstacles are putting one slot out to and the test is repeated. If the test runs successful for over 100 percent in the grasp phase, the maximum clutter density is found for the gripper. The position of the obstacles has to be report in the benchmark sheet, beginning with clockwise at 12, for this the plate should be mounted on the table, that the two mounting holes are parallel to the y-axis of the robot world frame. The mounting hole should be count from the middle and then report in the benchmark documentation sheet. The average of the six position is than taken to calculate the minimum space around the center of the object to grasp it. This is clear a approximation and could be improved by more complicated model than a circle. The Equation 5 to calculate the minimum grasp area is:
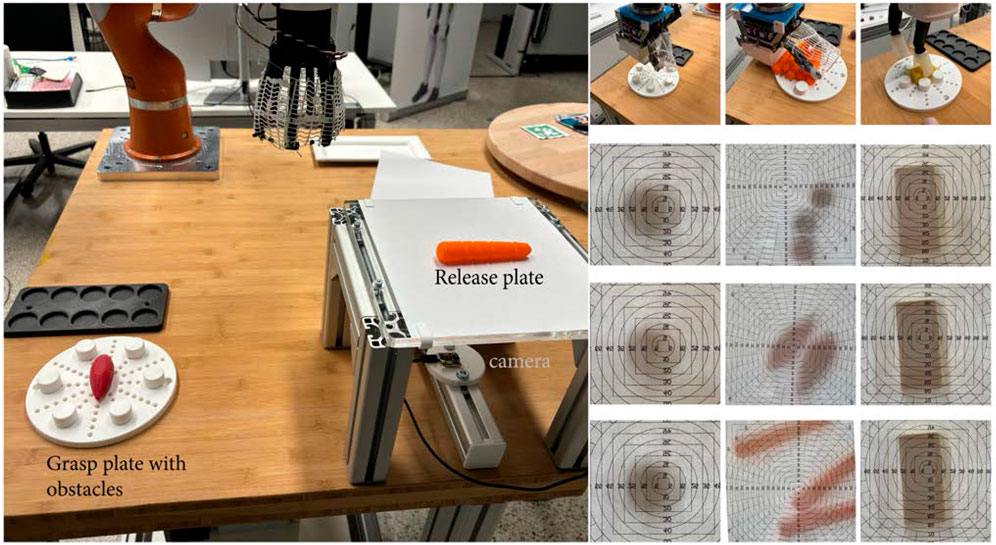
Figure 11. Benchmark setup to test single and multi object grasp; right: grasp trials and placing for different grippers. TPH is able to grasp a high number of objects, but the placing should be improved by better opening motion.
The plate has two different slots systems, the first aligns with the mounting holes and has a minimum distance for the first hole of
The results of the benchmark are shown in Table 2 and also in detail be include as addition materials.
3.3 Multi-object grasping
To evaluate the multi-object grasping capability of each gripper, different strategies (top-down grasp, group and grasp, environmentally constrained grasp) were implemented to maximize the number of objects grasped simultaneously. HCG can grasp three objects robustly (Figure 12, third from left) with a top-down grasp strategy. Each vacuum mini gripper on the fingertip can grasp one object and another object can be grasped between the two fingers. But for achieving this, the three objects to be grasped must be placed in a parallel way. Hence, a suitable multi-object grasp planner needs to be developed to search for these object configurations. Due to high opening span of HCG, objects up to
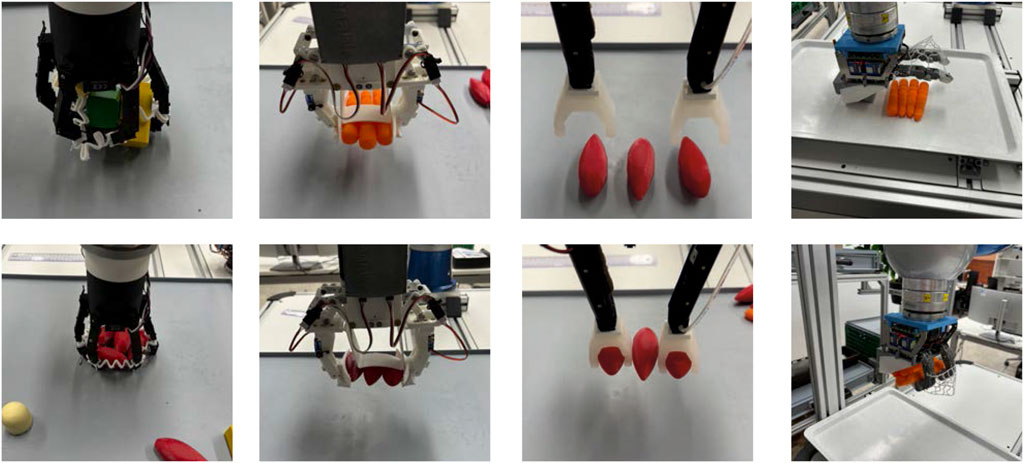
Figure 12. Multi-object grasping performed by different end-effectors. First (from left, top and bottom): CG grasping 5 wooden cuboids, CG grasping 6 shallots. Second (from left, top and bottom): LSG grasping 3 carrots, LSG grasping 3 shallots. Third (from left, top and bottom): HCG in pre-grasp approach to grasp 3 shallots, HCG after grasping 3 shallots. Fourth (from left, top and bottom): TPH in pre-grasp approach to grasp 4 carrots, TPH after grasping 4 carrots.
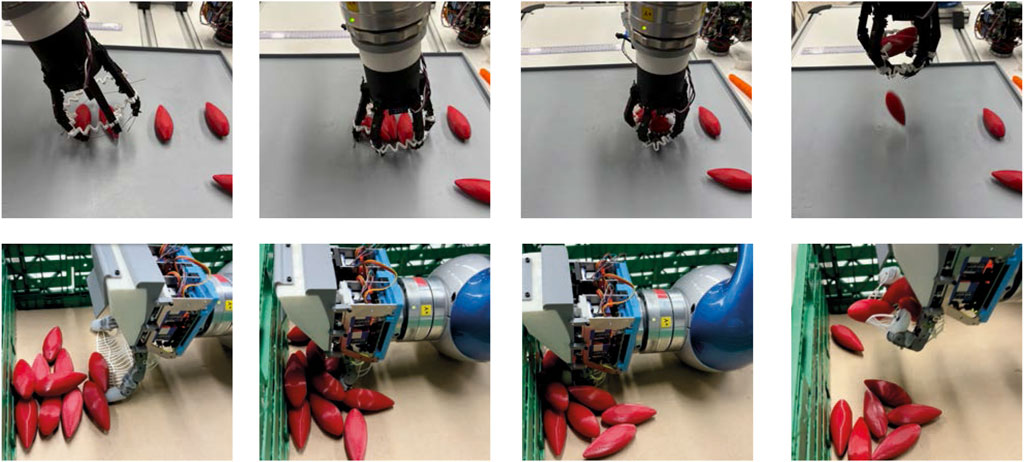
Figure 13. Mulit-object grasping strategies executed by CG and TPH. Top: CG collects objects in a linear motion for a group and grasp strategy. Bottom: TPH groups objects against the bin’s wall for a environmental constrained grasp strategy.
In addition to grasping, the ability of the end-effectors to place the grasped objects precisely is also important for packing or delivering the objects. HCG is the most suited hardware to achieve this due to known object position in the fingers. Precise placement can be achieved by first placing the object between the fingers, followed by the objects in the mini vacuum grippers. LSG is also also robust as all the objects stay parallel within the gripper upon closure. Placement can be achieved by either opening one or both the scrappers, or by opening the fingers. The placement of objects grasped by CG and TPH is relatively inaccurate as they can stay in any orientation within the hand after grasping. For specific shapes, for instance, cylindrical objects like carrot can be placed accurately by TPH. This is due to the inherent shape of TPH that is suitable for constraining specific shapes between the finger and the palm. But if to many carrots are taken, the placement can get even worse, than at the CG as shown in 3.2. For each end-effector, the maximum number of objects that can be grasped, the number of grasp strategies applicable, and the placement accuracy are summarized in Table 2.
4 Discussion
All the four end-effectors presented and experimented in the previous sections were successful in grasping single objects, multiple objects, and placing them. If the results are compared with the requirements, the CG had problems to fullfill two of them due to no direct force measurment and only one degree of freedom. LSG and HCG can both fulfil the requirements, the design of LSG is simpler and has some advantages in maximum number of objects, which can be grasped simultaneously. HCG is better suited for grasping simultaneously two delicate objects and placing them. TPH cannot fullfil the simultaneously multi grasp placement error with the simple release, which was programmed, but has similar good simultaneously multi grasping performance as CG paired with very low contact forces and better single grasp performance. However, each end-effector is better suited for different conditions, depending on which task is more critical. The different single and multi-object grasping experiments discussed in the previous section provide valuable insights into the design aspects that need to be considered for the end-effectors for different use cases.
For grasping single object, the end-effectors need varying space around the object for grasp interaction (Table 2). A two-finger end-effector is the most suited one if the objects need to be grasped from clutter. With suitable sensorization, gentle grasping can be achieved as well. For the placing the grippers are all quite accurate, the benchmark could be improve to get more comparable results with 3D printed placement pattern, to compensate human placement errors, which can be seen in 3.2 for example grasping the wooden blocks by the HCG. The vertical position is changing mostly by human placement. Furthermore a second camera looking on the grasp plan, helps to analyze grasp failures better and documents the obstacle positions.
For multi-object grasping, a high contact area to support and stabilize the objects is crucial. This can be done by many fingers as in CG, or by the soft palm in LSG, or with a combination of net and palm as in TPH. So an ideal solution would be a multi-fingered hand, with at-least two highly actuated fingers to enable gentle single object grasping and more than two under-actuated fingers to support the multi-object grasping with more contact area. Adding nets between the fingers can improve the capability to grasp very small objects. Finger kinematics can also be optimized to achieve maximum contact area. A fixed coupling between distal and middle joint allows for a contact only at the tip of the finger. Contact on all phalanges can be achieved by adding one more actuator or a return spring in the distal joint of an under-actuated finger. Furthermore, introducing a stiffness joint brake mechanism similar to the one shown in Friedl et al. (2018) for a variable stiffness finger in TPH can provide a better grasp against the palm, by giving more contact area, between fingers and palm. Considering net between the fingers and improved soft palm surfaces can be transferred to all human like multi-finger hands. For grasping many delicate objects and reducing arm motions, an integrated storage in the gripper could be a solution to reduce transport time and costs. To test this, TPH got a counter part to the palm, to generate a storage. This storage is printed by TPE and as a volume of approximate
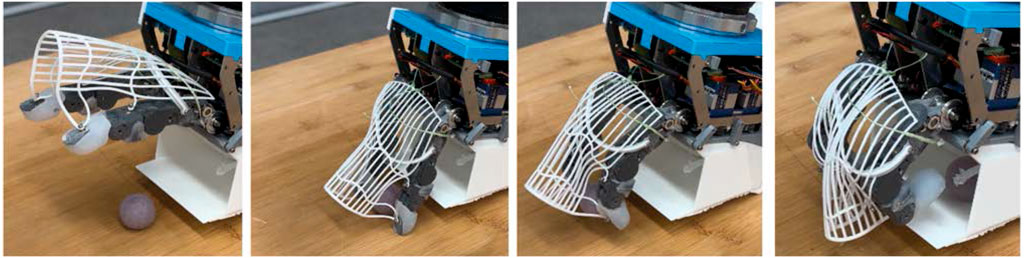
Figure 14. Storage grasp of delicate object. From left to right. The gripper is positioned to grasp the object; Grasping object by adduction grasp; inhand manipulation of object by fingers to place it inside storage; object in storage.
If precise object placement objects is crucial, HCG with the mini vacuum grippers is better suited, but then without a storage. By increasing the number of fingers to more than two, even more objects can be grasped simultaneously. The drawback in this case would be increased system complexity, size, and cost.
5 Conclusion
This paper presented four robotic end-effectors for the simultaneous grasping of multiple objects. Furthermore, single-object grasping performance, an essential skill that should not be compromised, was also analyzed. A benchmark is introduced to test the single grasp and placing performance, and furthermore the simultaneous multi grasp performance. The benchmark can help to compare better different designs and improve the results of new developments relative to grippers with force sensing. The simplest solution, the Constriction Gripper, has six fingers with three degrees of freedom each and is actuated by one servo, which pulls in a round rope that runs through the fingertips and thus bends the fingers. This gripper performs well for multi-object grasping, as the fingers can wrap around many objects, and the net between the fingers holds the objects inside the gripper. It is not a suitable solution for single-object grasping in cluttered environments and delicate object grasping due to the large grasp space around the object and no accurate force sensing. Also, the gripper is not precise for placing the objects. To improve single-object grasping, an extra motor to actuate two opposing fingers coupled with moving out fingertips can be developed. These fingers could gently grasp objects with a flexible antagonistic spring like CLASH. The Linear Scoop Gripper can grasp up to three small objects and place them precisely. Single-object grasping is also much better than CG, but it still needs a lot of space around the object. An improvement could be an actuated counter palm to better use the small side of the scoopers. However, the scoopers and soft palm can be transferred to other two-finger grippers to significantly improve the performance of multiple object grasping. Furthermore, these two features are ideal for grasping flat or deformable objects. The Two Finger Palm Hand, designed with two high workspace fingers, has good behavior for single-object grasping and can also grasp several objects by using its palm or net. However, multi-object grasping behavior is not predictable. TPH can grasp three or even six objects, depending on the pull strategy and the contact interaction between the objects. A new palm design could improve the grasp against the palm, and the finger kinematics could be adapted to the task. For instance, a finger with only a longer distal phalanges instead of a fixed coupling between the distal and middle phalanges is better suited. A more exciting option for multi-object grasping is to have more fingers like DLR Awiwi hand Grebenstein et al. (2011) and perhaps some net between the fingers. The concept of nets between fingers can be transformed on all multi-finger hands to improve multiple object grasping. The simplest solution is a glove for a human-like hand with “webs” between each finger. The Hybrid Compliant Gripper HCG with mini-vacuum grippers at the fingertips shows good single-object grasp performance and can also take up to three objects simultaneously. It can also place them precisely, which looks like a very promising solution for delicate and small objects. A new finger kinematic improvement could help grasp objects placed in different rotations and allow new in-hand manipulation. The mini grippers could also be improved to generate higher forces to grasp heavier objects. As a next step, a multi-object grasp planner could be integrated to evaluate realistic bin-picking use cases, for instance, grasping multiple delicate fruits and packaging them. Furthermore analyse of the object stiffness based on haptic contact as shown in Mohammadi et al. (2024) would be an interesting aspect while grasping flexible and delicate objects to get information of the state of the object and the fitting strategy. HCG and TPH should have compareable sensor information, but should allow higher closing velocities due to the variable stiffness actuation.
Data availability statement
The original contributions presented in the study are included in the article/supplementary material, further inquiries can be directed to the corresponding author.
Author contributions
WF: Conceptualization, Methodology, Software, Validation, Writing–original draft.
Funding
The author(s) declare that financial support was received for the research, authorship, and/or publication of this article. The development of CG and HCG is supported by the European Union’s Horizon Europe framework under grant agreement No. 101070136, project IntelliMan. The development of LSG is supported by the European Union’s Horizon Europe framework under grant agreement No. 101070600, project SoftEnable. The development of TPH is supported by the Bavarian government, project SmartHand.
Acknowledgments
The author would like to thank Ashok M. Sundaram and Maximo Roa for different hardware discussion, Aurel Schräter for the development of the LSG mechanism, Rene Rittgart and Herbert Eichberg for the development of the LSG electronics, Ana Elvira H. Martin for helping with the LSG software integration, and the DLR workshop colleagues for their immense support during the construction process. The design of the constriction gripper and the molds for the mini grippers will be publish open source druing the EU project Intelliman. Furthermore the first version of the Linear Scoop Gripper will be publish open source during the EU project Softenable, and a adapt version of the Two-finger Palm Hand with LEAP fingers Shaw et al. (2023), due to the kinematic is similar, will be published open source.
Conflict of interest
The author declares that the research was conducted in the absence of any commercial or financial relationships that could be construed as a potential conflict of interest.
Publisher’s note
All claims expressed in this article are solely those of the authors and do not necessarily represent those of their affiliated organizations, or those of the publisher, the editors and the reviewers. Any product that may be evaluated in this article, or claim that may be made by its manufacturer, is not guaranteed or endorsed by the publisher.
Supplementary material
The Supplementary Material for this article can be found online at: https://www.frontiersin.org/articles/10.3389/frobt.2024.1351932/full#supplementary-material
References
Agboh, W. C., Ichnowski, J., Goldberg, K., and Dogar, M. R. (2022). Multi-object grasping in the plane
Babin, V., and Gosselin, C. (2018). Picking, grasping, or scooping small objects lying on flat surfaces: a design approach. Int. J. Robotics Res. 37, 1484–1499. doi:10.1177/0278364918802346
Bo, V., Franco, L., Turco, E., Pozzi, M., Malvezzi, M., Prattichizzo, D., et al. (2024). “Design and control of soft-rigid grippers for food handling,” in ICRA2024 workshop on cooking robotics: perception and motion planning.
Catalano, M., Grioli, G., Farnioli, E., Serio, A., Piazza, C., and Bicchi, A. (2014). Adaptive synergies for the design and control of the Pisa/IIT softhand. Int. J. Robotic Res. 33, 768–782. doi:10.1177/0278364913518998
Chen, T., Shenoy, A., Kolinko, A., Shah, S., and Sun, Y. (2021). Multi-object grasping – estimating the number of objects in a robotic grasp, 4995, 5001. doi:10.1109/iros51168.2021.9636777
[Dataset] Rochu (2023). Soft beak - soft robotics gripper. Available at: https://www.softroboticgripper.com/soft-beak.
D’Avella, S., Sundaram, A. M., Friedl, W., Tripicchio, P., and Roa, M. A. (2023). Multimodal grasp planner for hybrid grippers in cluttered scenes. IEEE Robotics Automation Lett. 8, 2030–2037. doi:10.1109/LRA.2023.3247221
Durner, M., Boerdijk, W., Sundermeyer, M., Friedl, W., Márton, Z., and Triebel, R. (2021). “Unknown object segmentation from stereo images,” in 2021 IEEE/RSJ international conference on intelligent robots and systems (IROS), 4823–4830. doi:10.1109/IROS51168.2021.9636281
Feix, T., Romero, J., Schmiedmayer, H.-B., Dollar, A. M., and Kragic, D. (2016). The grasp taxonomy of human grasp types. IEEE Trans. Human-Machine Syst. 46, 66–77. doi:10.1109/THMS.2015.2470657
Friedl, W., Höppner, H., Schmidt, F., Roa, M. A., and Grebenstein, M. (2018). “Clash: compliant low cost antagonistic servo hands,” in 2018 IEEE/RSJ international conference on intelligent robots and systems (IROS), 6469–6476. doi:10.1109/IROS.2018.8593903
Friedl, W., and Roa, M. A. (2020). Clash a compliant sensorized hand for handling delicate objects. Front. Robotics AI 6, 138. doi:10.3389/frobt.2019.00138
Friedl, W., and Roa Garzon, M. A. (2019). “Clash wrist - a hardware to increase the capability of clash fruit gripper to use environment constraints exploration,” in 2019 IEEE/RSJ international conference on intelligent robots and systems, IROS 2019.
Friedl, W. A., and Roa, M. A. (2021). Experimental evaluation of tactile sensors for compliant robotic hands. Front. Robotics AI 8, 704416. doi:10.3389/frobt.2021.704416
Gafer, A., Heymans, D., Prattichizzo, D., and Salvietti, G. (2020). “The quad-spatula gripper: a novel soft-rigid gripper for food handling,” in 2020 3rd IEEE international conference on soft robotics (RoboSoft), 39–45. doi:10.1109/RoboSoft48309.2020.9115968
Grebenstein, M., Albu-Schäffer, A., Bahls, T., Chalon, M., Eiberger, O., Friedl, W., et al. (2011). “The dlr hand arm system,” in 2011 IEEE international conference on robotics and automation, 3175–3182. doi:10.1109/ICRA.2011.5980371
Gyeongji, Y.-J., and Kahye, S. K. D.-Y. (2023). Grasping through dynamic weaving with entangled closed loops. Nat. Commun. 14, 8935–8941. doi:10.1038/s41467-023-40358-y
Harada, K., and Kaneko, M. (1998). Kinematics and internal force in grasping multiple objects. Proc. 1998 IEEE/RSJ Int. Conf. Intelligent Robots Syst. Innovations Theory, Pract. Appl. (Cat. No.98CH36190) 1, 298–303. doi:10.1109/IROS.1998.724635
He, T., Aslam, S., Tong, Z., and Seo, J. (2021). Scooping manipulation via motion control with a two-fingered gripper and its application to bin picking. IEEE Robotics Automation Lett. 6, 6394–6401. doi:10.1109/LRA.2021.3093896
Höfer, T., Shamsafar, F., Benbarka, N., and Zell, A. (2021). “Object detection and autoencoder-based 6d pose estimation for highly cluttered bin picking,” in 2021 IEEE international conference on image processing (ICIP), 704–708. doi:10.1109/ICIP42928.2021.9506304
Ichnowski, J., Avigal, Y., Satish, V., and Goldberg, K. (2020). Deep learning can accelerate grasp-optimized motion planning. Sci. Robotics 5, eabd7710. doi:10.1126/scirobotics.abd7710
Jain, S., Dontu, S., Teoh, J. E. M., and Alvarado, P. V. Y. (2023). A multimodal, reconfigurable workspace soft gripper for advanced grasping tasks. Soft Robot. 10, 527–544. PMID: 36346280. doi:10.1089/soro.2021.0225
Mahler, J., and Goldberg, K. (2017). “Learning deep policies for robot bin picking by simulating robust grasping sequences,” in Conference on robot learning.
MarelFish (2020). Salmon showhow 2020: get a grip on smarter processing. Available at: https://www.youtube.com/watch?v=5wmHSMDXPVs
Mohammadi, V., Shahbad, R., Hosseini, M., Gholampour, M. H., Shiry Ghidary, S., Najafi, F., et al. (2024). Development of a two-finger haptic robotic hand with novel stiffness detection and impedance control. Sensors 24, 2585. doi:10.3390/s24082585
Mucchiani, C., and Yim, M. (2020). “A novel underactuated end-effector for planar sequential grasping of multiple objects,” in 2020 IEEE international conference on robotics and automation (ICRA), 8935–8941. doi:10.1109/ICRA40945.2020.9197380
Nguyen, V. P., and Chow, W. T. (2023). Wiring-claw gripper for soft-stable picking up multiple objects. IEEE Robotics Automation Lett. 8, 3972–3979. doi:10.1109/LRA.2023.3273512
Ocado (2023). Robotic-arm-grocery. Available at: https://www.ocadogroup.com/media/press-releases/ocado-showcases-robotic-arm-grocery-picking.
Peab (2023). Sanfte greifer. Available at: https://www.piab.com/de-de/saugnapfe-und-soft-gripper/sanfte-greifer/.
qbrobotics (2023). Soft claw. Available at: https://qbrobotics.com/product/qb-softclaw/.
Qiu, Z., Paul, H., Wang, Z., Hirai, S., and Kawamura, S. (2023). An evaluation system of robotic end-effectors for food handling. Foods 12, 4062. doi:10.3390/foods12224062
Roa, M., Chen, Z., Staal, I., Muirhead, J., Maier, A., Pleintinger, B., et al. (2014). Towards a functional evaluation of manipulation performance in dexterous robotic hand design. 6800, 6807. doi:10.1109/icra.2014.6907863
Sakamoto, T., Wan, W., Nishi, T., and Harada, K. (2021). “Efficient picking by considering simultaneous two-object grasping,” in 2021 IEEE/RSJ international conference on intelligent robots and systems (IROS), 8295–8300. doi:10.1109/IROS51168.2021.9636727
Shaw, K., Agarwal, A., and Pathak, D. (2023). Leap hand: low-cost, efficient, and anthropomorphic hand for robot learning
SmartHand, D. (2023). Bayerisches verbundforschungsprogramm bayvfp des freistaates bayern förderlinie digitalisierung. Available at: https://www.dlr.de/rm/en/desktopdefault.aspx/tabid-18656/.
SoftEnable, E. U. (2022). Towards soft fixture-based manipulation primitives enabling safe robotic manipulation in hazardous healthcare and food handling applications. Available at: https://cordis.europa.eu/project/id/101070600.
Sun, Y., Amatova, E., and Chen, T. (2022). Multi-object grasping – types and taxonomy, 3, 777, 783. doi:10.1109/icra46639.2022.9812388
Sundaram, A. M., Friedl, W., and Roa, M. A. (2020). Environment-aware grasp strategy planning in clutter for a variable stiffness hand. IEEE/RSJ International Conference on Intelligent Robots and Systems IROS, 9377–9384. doi:10.1109/IROS45743.2020.9340689
UniversalRobots (2023). Actinav autonomous bin picking. Available at: https://www.universal-robots.com/about-universal-robots/news-centre/universal-robots-launches-actinav-autonomous-bin-picking/.
Wang, Z., Furuta, H., Hirai, S., and Kawamura, S. (2021). A scooping-binding robotic gripper for handling various food products. Front. Robotics AI 8. doi:10.3389/frobt.2021.640805
Wang, Z., Hirai, S., and Kawamura, S. (2022). Challenges and opportunities in robotic food handling: a review. Front. Robotics AI 8, 789107. doi:10.3389/frobt.2021.789107
Keywords: robotic hand, hand design, multi-object grasping, robotic grasping, variable impedance
Citation: Friedl W (2024) Evaluation of different robotic grippers for simultaneous multi-object grasping. Front. Robot. AI 11:1351932. doi: 10.3389/frobt.2024.1351932
Received: 07 December 2023; Accepted: 01 October 2024;
Published: 07 November 2024.
Edited by:
Hamidreza Kasaei, University of Groningen, NetherlandsReviewed by:
Maria Pozzi, University of Siena, ItalyVahid Mohammadi, University of Nebraska Omaha, United States
Copyright © 2024 Friedl. This is an open-access article distributed under the terms of the Creative Commons Attribution License (CC BY). The use, distribution or reproduction in other forums is permitted, provided the original author(s) and the copyright owner(s) are credited and that the original publication in this journal is cited, in accordance with accepted academic practice. No use, distribution or reproduction is permitted which does not comply with these terms.
*Correspondence: Werner Friedl, d2VybmVyLmZyaWVkbEBkbHIuZGU=