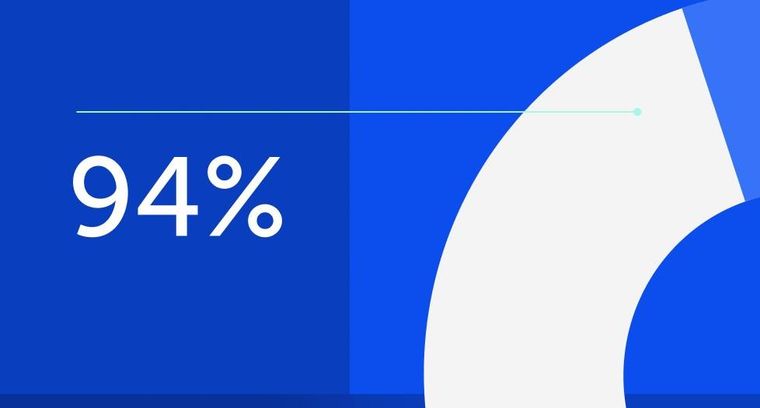
94% of researchers rate our articles as excellent or good
Learn more about the work of our research integrity team to safeguard the quality of each article we publish.
Find out more
ORIGINAL RESEARCH article
Front. Sustain. Food Syst., 09 November 2023
Sec. Sustainable Food Processing
Volume 7 - 2023 | https://doi.org/10.3389/fsufs.2023.1250646
This article is part of the Research TopicTechnological Advancements for Processing and Preservation of Fruits and VegetablesView all 15 articles
Over the past decades, increase in food shortages and food costs with the drought caused by population growth and climate change, it becomes more important to prevent food losses with the widespread use of cold storage. That’s why many countries provide incentives for the widespread use of cold stores. However, with cold storages becoming more widespread, keeping energy consumption under control becomes an important issue. Especially in most developing countries, the status and energy performance of installed cold stores are unknown. In this study, energy consumption data were examined by using data from cold stores from different countries. The relationships between some parameters (capacity, volume, etc.) affecting energy consumption were analyzed for 67 established cold stores. In order to measure the energy consumption data of the system under ideal operating conditions, experiments were carried out in the test room under laboratory conditions and comparisons were made according to the data obtained from the field. The data obtained showed that energy consumption in cold stores increased by up to 30%, depending on operating conditions. Therefore, it is very important that cold stores are inspected by the relevant institutions after they are established and during their operation.
In order to deliver the food to the consumer in the desired quality, the cold chain should not be interrupted in all processes involving cold logistics applications. Deficiencies in the cold chain pose a problem in terms of food safety. Storing the harvested products by maintaining the cold chain will prevent food waste. According to FAO’s State of Food and Agriculture Organization (2019) report, around 14 percent of the world’s food (valued at $400 billion per year) continues to be lost after it is harvested and before it reaches the shops; while UNEP’s Food Waste Index Report (2021) shows that a further 17 percent of our food ends up being wasted in retail and by consumers, particularly in households. According to FAO estimates, the food that is lost and wasted could feed 1.26 billion hungry people every year. Fruit and vegetables (40–50%) are among the wasted foodstuffs in the world. It is followed by fish (35%), cereals (30%), meat and dairy products (20%). Fruits and vegetables, plus roots and tubers, have the highest wastage rates of any food. In order to extend the storage period of food products, it is important to expand cold storage establishments and to increase incentives in this regard. In addition to the advantages of cold storage, the biggest obstacle we face in expanding its use is the installation, operation, and maintenance costs of cold storage. In particular, the energy consumption originating from the cooling units used in cold stores increases the operating costs considerably. Research has shown that cooling systems constitute 44.1% of the total electrical energy consumption of the factory (Carrasco et al., 2021). Energy savings can be up to 50% with improvements made in non-optimized conventional refrigeration plants. Efficient system design is the primary priority within the scope of efforts to save energy in cold stores. Since the highest energy consumption in the cooling system is on the compressor side, the studies here are focused on compressor efficiency. Variable operating conditions must be considered to reduce energy consumption from compressors. It is stated in the literature that up to 31% savings can be achieved with compressor staging (multiple compressor systems) and no-load operation strategies with correct capacity control (Carrasco et al., 2021). With appropriate capacity grading, annual system energy use can be reduced by 5–15%. In the researches conducted for the power consumption depending on the compression ratio, it is seen that by reducing the compression ratio (P0/P1) from 5 to 3, the power consumption in the compressor can be reduced by about 30% (Larsen and Thybo, 2004). In the study of Manske et al. (2000), efficiency comparison at part load was examined for different compressor types and it was seen that screw compressors had poor part load performance. On the evaporator side, it is necessary to use the most efficient motors possible for the application. VFD (Variable Frequency Drives) control of fans in cold stores is another valuable source of power savings, providing system energy savings of up to 2% per year. Developments in fan design and engine efficiency in recent years offer significant advantages over old-style cooling systems and cold stores. Studies on the amount of power savings relative to cooling load due to the installation of variable speed drives in evaporator fans show that savings are greater at low cooling loads (NSW Office of Environment and Heritage, 2017). Another problem is that icing on the evaporator coils will reduce energy efficiency. Actively managing defrost frequency and duration can reduce annual system energy use by approximately 3% (U.S. Environmental Protection Agency, 2020). On the condenser side, if the system demand is not met, it will cause an increase in energy. The condenser that is not maintained will create a temperature increase. This will cause operation at high temperatures. Compressors will work more; energy loss will increase. For every 1°C increase in condensing temperature, the compressor uses between 2 and 4% more energy. Air cooled condenser is preferred for cooling systems with low cooling load. Water-cooled and evaporative condensers are suitable for systems with high cooling load and low condensing temperature. Choosing the right product will increase the system efficiency (Carbontrust, 2019). One of the most important problems experienced on the refrigerant side is leakage. The reduced fluid in the cooling system will overwork the compressor, cause energy loss and harm the environment. Apart from leakage, another important issue is charging the correct amount of fluid into the system. The relationship between performance loss (capacity and efficiency) is very difficult to predict, but results from experimental measurements taken by Kim and Braun (2010), can show that annual operating costs increase by 10% when the effective refrigerant charge is reduced to 85% of the correct amount. This annual operating cost loss increases non-linearly so that at 60% correct charging the operating cost loss is +45%. As another gain point, discharge temperatures in most cooling systems are quite high (in the range of 70°C to 100°C). Therefore, the heat obtained from it can be used to heat the domestic water to about 60°C. The amount of heat recovered will be between 10 and 15% of the total heat dissipated in the condenser (Reindl and Jekel, 2007; Kassai, 2019; González and Gordín, 2020). In addition to all these, it has been observed that phase change materials, which have been researched extensively in recent years, also create energy savings during their use in cold storage (Yilmaz et al., 2020; Ismail et al., 2022; Le et al., 2023).
The aim of this study is to draw attention to the issue by analyzing the reasons that increase energy consumption in cold storages. Because the function and importance of the cold chain is increasing day by day in terms of reducing product losses and increasing product quality. Reducing energy consumption by improving cold storages will increase the quality of the stored product and reduce operating costs. It is known that in developing countries, up to 30% of food and vegetables become unusable due to various incorrect and incomplete practices in stages such as harvest, processing, storage, transportation, distribution, and consumption, and this places a serious burden on the economy (Carbontrust, 2018). For this reason, it is important to control the improvements that need to be made to reduce energy consumption in cooling systems and to increase the regulations in this regard.
In this study, research was conducted on the energy consumption of different cold storages installed in various countries. It is not possible to obtain detailed data on the general situation of existing cold stores, especially in developing countries. Cold storage operators and project companies do not share this information for confidentiality reasons. In order to determine the current situation, data collection should be carried out more by researchers. For the study, the operators of cold storages established in different countries and companies that make experienced cooling system projects were interviewed and the data were collected and analyzed. The energy consumption of the systems was examined depending on many parameters such as problems arising during the operation of the warehouses, lack of maintenance, the climate of the region where it is installed, and the electricity prices in the country where it is installed. The data obtained from the field were examined and experiments were carried out in a laboratory test room to see the behavior of a system operated in ideal conditions, and these experiments were repeated by creating inappropriate operating conditions detected in the field. By comparing both cases, energy consumption differences are examined.
In order to collect data from facilities operating cold store, nearly 300 investors and refrigeration companies were interviewed. However, only 67 companies allowed data collection. Obtaining this data from companies has not been easy due to confidentiality reasons. For this reason, this data collection study took approximately 2 years. The data collected for the study are shown in Table 1. These data were collected through verbal interviews, and in case of visible differences in energy consumption, more detailed information about the maintenance and operating status was sought.
The data of the research was obtained from 16 different countries. Some of these countries are located in the temperate climate zone, and some are in the hot climate zone. Different climate impacts were taken into account when conducting research. All of the products stored in the facilities where the research was conducted are vegetables and fruits. Meat and processed meat products, poultry products, milk and dairy products, and pharmaceutical storage facilities are excluded from this study. The storage temperature of the products is in two different types: cold (0/+4°C) and frozen storage (−18°C). Warehouse volumes vary between 170 m3 and 18,000 m3. The cooling capacities of the refrigeration system vary between approximately 10 hp. and 1,000 hp. R404a is generally used as a refrigerant, and in a few facilities, Ammonia, 449A and 407C gases are also used. Approximately 40% of these facilities are new facilities, while other facilities are 1 to 10 years old. Detailed information about the warehouses is shown in Table 2.
Facilities generally vary between 1 and 23 cold rooms, and if there is more than one room, the rooms are connected to the central cooling system. Cold rooms open to a common corridor, and in most applications, the corridors are also cooled in a controlled manner. Most facilities have a front-loading area, and goods are loaded into these front rooms by trucks. Figure 1 shows a schematic view of an example facility. The number of evaporators is placed as one or more depending on the size of the rooms. Figure 2 shows images from the cold stores where the research was conducted. These photographs were used to give an idea about the structure of the cold stores used in the study.
In the second part of the study, in order to verify all this information obtained from the field; energy consumption data from a cold room operating in ideal condition was compared with the data of a cold room that was not operated properly. Energy consumption measurements were made in an empty test room with a volume of 25 m3 in the laboratory environment. The test room polyurethane panel thickness is 10 cm, fully insulated and established in accordance with (ISO 5149-2:2014) standards. The test room is maintained regularly and all measuring instruments in the room are calibrated. The defrost system is controlled electronically and ice formation on the evaporator surface is not allowed. Entes® Network Analyzer, Televis® remote monitoring system was used for measurement and recording of test data. In Table 3, the characteristics of the measuring instruments used in the experiment are given.
The refrigeration system cooling capacity 39.3 kW for 0°C evaporation temperature / 40°C condensation temperature conditions, 16.7 kW for-18°C evaporation temperature / 40°C condensation temperature conditions. The refrigeration system was tested for 24-h performance and energy consumption first in cold room conditions (0°C) and then in freezing room conditions (−18°C). During the tests, the outdoor temperature was measured to be approximately 23°C. The refrigeration system operating differential value is set to 2°C. Ice on the evaporator surface is melted by using heating element which is a widely used defrost method in the market. The defrost system was activated every 4 h, causing short-term temperature increases in the room.
Ideal operating conditions were examined in the first configuration and in the second configuration, inappropriate operating conditions were examined to verify the data obtained from the field. During these tests, defrost cycle periods were changed to allow icing on the evaporator surface, and proper air flow was prevented by placing an obstacle in front of the evaporator. The same measurements were made for both configurations and the energy consumption of the refrigeration system depending on the operating times was compared.
Experimental results are used to calculate the percentages of running time and energy saving by using Eqs 1, 2, respectively (ASHRAE Handbook – Refrigeration, 2022). By measuring the compressor on–off time, the running time per cycle is calculated as follows:
The compressor power consumption is calculated by integrating the measured power for a duration t. For a 24 h energy consumption is calculated by Eq. (3).
As a result of the research, the desired data could be obtained from 67 cold storages. These data were examined in detail and the parameters affecting energy consumption were evaluated and those with the highest impact were selected and investigated. The first of these is the climatic characteristics of the cities where data are collected. The climates where cold storages are located are divided into two different groups, hot and temperate, according to annual average meteorological data. The average summer temperature in hot climates is approximately 45°C, and in temperate climates the average summer temperature is 30°C. In order to compare energy consumption based on climate data, 25 cold storages of similar ages and characteristics operating under the same conditions were selected. 12 of these cold storages were established in the temperate climate region, and 13 of them were established in the hot climate region. All cold stores operate under cold storage conditions (range 0–4°C). The data are compared in Figure 3 by plotting the changes in the energy consumption of the refrigeration system depending on the volume of the cold store. Accordingly, while the difference in daily energy consumption of the refrigeration system is around 9% in small volumes, this difference increases to around 15% as the volume increases. The most important reason for this is that the refrigeration system works approximately 12–14 h a day in temperate climate regions and approximately 18–20 h a day in hot climate regions. It was observed that this period increased depending on the operating conditions.
It is seen from the results that; sustainable cooling strategies need to be implemented in hot and humid climates. At this point, solar-powered cooling systems come to the fore and represent the best alternative in solving both energy consumption and environmental pollution problems. Additionally, there is a direct relationship between the availability of solar radiation and the peak of cooling demand, making solar energy a focus of great interest. In fact, solar driven adsorption cooling systems appear to be a good solution for hot climate regions. Research shows that; adsorption cooling systems can be operated with a lower heat source temperature range, are environmentally friendly as there is no ozone depletion potential or global warming potential, are more robust, less complex, and have no crystallization issues compared to absorption cooling systems (Wang and Oliveira, 2006; Wang et al., 2009; Rahman et al., 2021). Therefore, solar driven adsorption cooling systems represents the best choice to meet international guidelines in solving both energy and environmental impacts in cold storage applications (Mostafa et al., 2022).
Another issue that should be taken into consideration in hot climate regions is that the increase in condenser temperature depending on the environmental temperature will reduce the cooling capacity of the cycle due to the decrease in the liquid content in the evaporator. In other words, the high pressure and temperature of the air-cooled condenser will significantly reduce the performance of the cooling system. In this case, performance can be increased with some improvements on the condenser side. Some of those; the air-side modifications include adding spray water above condenser, wet pad before condenser, and water vapor nozzle in the condenser air flow. Studies on adding spray water above condenser, one of these solutions, have shown that it is an important tool for increasing cooling capacity and also reducing power consumption, especially in hot climates (Vrachopoulos et al., 2007; Alhamdo et al., 2015).
Another important parameter that causes an increase in energy consumption is operational conditions. Systems operated under incorrect operational conditions have been frequently encountered in the field. Problems arising from reasons such as lack of training of the operating personnel, economic reasons, and lack of quality control have a significant impact on energy consumption and product loss in cold storages. The most common operational fault is incorrect product stacking. Figure 4 shows photographs of incorrectly stacked warehouse examples. As seen in the photo, the air flow was disrupted by covering the front of the evaporator with cases, and some cases were placed in areas of the room with no air flow. There should be no obstacles that would disrupt the air flow in front of the evaporator while stacking. The placement of the crates must be done very carefully so that all the products inside the crates can cool homogeneously. Otherwise, some of the products cool down while others do not cool down enough.
Apart from stacking, there are other parameters that affect operational conditions. In order for cold storage to be carried out correctly, the necessary conditions must be defined correctly. These conditions are temperature and relative humidity values in the cold room specified in the standards depending on the product, condensation temperature, the amount of product in the cold store must be suitable for the capacity of the cold store, correct project design of processes and correct product selection, etc.
In addition to energy consumption in systems working under incorrect operating conditions, deterioration will occur because the products are not stored at the correct temperatures, which will trigger the formation of bacteria in the products and cause bad odors. For example, research has shown that; Increasing the temperature in the apple warehouse by 1°C causes a 13% loss in storage life. In interviews with operators working in facilities that are not properly operated, it has been confirmed that product losses remain above average values. However, since verifiable data could not be obtained, this subject was not included in the scope of the study.
In the research, an increase of 30 to 50 percent in energy consumption was measured in 11 facilities due to faulty operating conditions. Cold stores working under incorrect operating conditions were examined separately and comparisons were made in terms of energy consumption with cold stores operating ideal conditions in similar volumes. In Figure 5, cold stores under ideal and faulty operating conditions are compared in terms of volume-dependent energy consumption. As seen in Figure 5, with the increase in volume of the cold storage, the increase in energy consumption reaches 50% due to faulty operating conditions.
Figure 5. Variation of daily power consumption depending on volume for ideal and faulty operating conditions.
It has been shown that in some warehouses where energy consumption data is higher than other systems of similar capacity, the defrost cycle is not implemented correctly and the necessary air circulation between the evaporator fins is not provided due to frost. Figure 6 shows snow-covered evaporator images from some facilities.
It has been determined that in warehouses where the defrost process is not applied correctly, up to 30 percent more energy is consumed than the energy consumption expected under ideal conditions. Figure 7 clearly shows this difference in energy consumption compared to cold stores with approximately the same volume operating in ideal conditions.
Figure 7. Volume-dependent variation of the effect of snow formation on the evaporator surface on daily power consumption.
Another striking point is that when an evaluation is made between the countries where data are collected, there are country-by-country differences in hourly electricity consumption prices. This affects energy expenditures depending on the installation of the same capacity cold storage in different countries. In this study, an analysis was made on this subject. Among the countries from which data were obtained, 15 countries were selected and the electricity costs in these countries were calculated by considering a cold store with a capacity of 5,000 tons. In Figure 8, the difference in energy costs when a cold storage with the same capacity is operated in different countries is analyzed. When the graph is examined, if we consider the country with the lowest electricity prices (Algeria) and the world average, it is seen that cold store operating costs increased approximately 5.5 times depending on the country. This shows that, in addition to operating conditions, the country where the cold storage is installed is an important parameter in terms of energy costs depending on electricity prices.
In countries where electricity prices are high, applying some methods used to reduce energy consumption provides savings. The role of the cold thermal energy storage (CTES) system, one of these methods, has become even more important in the last decade (Rismanchi et al., 2012). In general, CTES systems are designed to store cold energy in thermal reservoirs for use when needed. The most common media for cold storage are eutectic salt phase change materials (PCM), ice, chilled water or paraffin, depending on the application and temperature ranges (Al-Rabghi and Akyurt, 2004; Bahnfleth and Song, 2005). This method has the benefit of reducing energy usage by shifting electricity consumption to off-peak hours when the electricity price is generally cheaper.
In order to verify all these data, the energy consumption of the cold store operating ideal conditions (config. 1) and the cold store with faulty operating conditions (config. 2) were examined in the test room established. Ideal operating conditions were examined in the first configuration, and as seen from the graphics, the test chamber reached 0°C in approximately 20 min (Figure 9A) and-18°C in approximately 1 h (Figure 9B). As a result of the energy consumption measurements made with the network analyzer during the experiments, it was recorded that the total energy consumption of the freezing room was 69 kWh, and the cold room was 26 kWh. This consumption data includes compressors, condenser fans, solenoid valve on the device and electrical components. Evaporator fans, defrost resistors, remote control panel and evaporator solenoids are not included. Using the results obtained from the measurements for both configurations; running time, energy saving and 24 h energy consumption was calculated with Eqs 1–3. The results of the calculations are shown in Table 4. According to the calculations, in the 2nd configuration, the operating time of the compressor increased from 3.2 h to 4.1 h, and the energy saving is 32.2% when the system operates under ideal conditions. Similar studies in the literature report that energy savings in non-optimized conventional facilities can reach up to 50% (Industrial Refrigeration Guide, 2017). It is clear that this value will increase as operating conditions worsen. For this reason, the importance of correct operation of the system as well as the design stages should be emphasized.
Figure 9. Time dependent variation of 399 room temperature and total power consumption for Cold room (A), and Freezing room (B).
The first waves of the global climate crisis began to spread to Anatolia. The farmer is aware of the change in air, soil, and yield. Agricultural reports contain dramatic results, reminding decision makers, researchers, and citizens of our responsibilities. In the latest report of the Intergovernmental Panel on Climate Change (IPCC), it is predicted that temperature increases will be around 2.5–3 degrees for 2050 and will reach 6 degrees by the end of this century. Today, while the observed effects of a 1 degree increase in temperature are so great, the economic, social, and environmental risks posed by a 6 degree increase show that climate change is one of the biggest risks faced by human history. While all this is happening, most of the agricultural products produced are wasted because they cannot be stored correctly. Therefore, cold storage emerges as a much more important player. Incentives for the expansion of cold storage are increasing day by day. However, here too, as a major handicap, the energy increases consumed by cold stores that are not operated properly.
In this study, data were collected from cold stores established in developing countries. When these data are analyzed, it is seen that the increase in energy consumption caused by improperly operated warehouses reaches almost 32%. This value can be reduced by controlling it with correct operating methods and increasing regulations. Apart from this, in order to reduce the increase in energy consumption due to uncontrollable ambient temperature and country policies, new technologies must be integrated during the cold storage installation phase and these disadvantages must be eliminated with correct project design. Increasing the data collected from existing cold stores is very important in terms of drawing attention to this issue. For this reason, future studies and research in different countries will make the subject more clear. In addition, the measurable determination of product losses as well as energy loss in improperly operated cold stores, should be the subject of future studies.
The original contributions presented in the study are included in the article/supplementary material, further inquiries can be directed to the corresponding author.
All authors listed have made a substantial, direct, and intellectual contribution to the work and approved it for publication.
The authors declare that the research was conducted in the absence of any commercial or financial relationships that could be construed as a potential conflict of interest.
All claims expressed in this article are solely those of the authors and do not necessarily represent those of their affiliated organizations, or those of the publisher, the editors and the reviewers. Any product that may be evaluated in this article, or claim that may be made by its manufacturer, is not guaranteed or endorsed by the publisher.
Alhamdo, M. H., Theeb, M. A., and Abdulhameed, J. J. (2015). Using evaporative cooling methods for improving performance of an air-cooled condenser. Univ. J. Mech. Eng. 3, 94–106. doi: 10.13189/ujme.2015.030304
Al-Rabghi, O. M., and Akyurt, M. M. (2004). A survey of energy efficient strategies for effective air conditioning. Energy Convers. Manag. 45, 1643–1654. doi: 10.1016/j.enconman.2003.10.004
ASHRAE Handbook Refrigeration (2022). American Society of Heating, Atlanta, USA: Refrigerating and Air-Conditioning Engineers,Inc.
Bahnfleth, W. P., and Song, J. (2005). Constant flow rate charging characteristics of a full-scale stratified chilled water storage tank with double-ring slotted pipe diffusers. Appl. Therm. Eng. 25, 3067–3082. doi: 10.1016/j.applthermaleng.2005.03.013
Carbontrust (2018). Manufacturing sector guide. Available at: https://www.carbontrust.com/resources/manufacturing-sector-guide (Accessed June 20, 2023).
Carbontrust (2019). Refrigeration Guide. Available at: https://www.carbontrust.com/resources/refrigeration-guide (Accessed June 20, 2023).
Carrasco, J. C., Guillamón, M. P., and Vicente, F. S. (2021). Improve the energy efficiency of the cooling system by slide regulating the capacity of refrigerator compressors. Appl. Sci. 11, 1–13. doi: 10.3390/app11052019
Food and Agriculture Organization (2019). The state of food and agriculture 2019. Moving forward on food loss and waste reduction. Rome: Food and Agriculture Organization of the United Nations.
González, J. I., and Gordín, R. G. (2020). Comments on a heat recovery unit in refrigeration industry. Therm. Sci. Eng. 3, 31–38. doi: 10.24294/tse.v3i1.1497
Ismail, K. A., Lino, F. A., Machado, P. L. O., Teggar, M., Arıcı, M., Alves, T. A., et al. (2022). New potential applications of phase change materials: a review. J. Ener. Stor. 53:105202. doi: 10.1016/j.est.2022.105202
ISO 5149-2:2014 Refrigerating systems and heat pumps. Safety and environmental requirements. Design, construction, testing, marking and documentation. International Organization for Standardization.
Kassai, M. (2019). Recovering heat from condenser unit produced refrigerant system in food processing facility. Periodica Polytechnica Mech. Eng. 63, 220–229. doi: 10.3311/PPme.14044
Kim, W., and Braun, J. E., (2010). Impacts of refrigerant charge on air conditioner and heat pump performance. International refrigeration and air conditioning conference. Paper 1122. USA: Purdue e-Pubs, Purdue University. Available at: http://docs.lib.purdue.edu/iracc/1122
Larsen, L.S., and Thybo, C. (2004). Potential energy savings in refrigeration systems using optimal set-points, proceedings of the 2004 IEEE international Conference on Control Applications. Taipei, Taiwan. 1, 701–704.
Le, T. L., Duong, X. Q., Nguyen, D. T., Nguyen, P. Q. P., Rajamohan, S., Vo, A. V., et al. (2023). Application of phase change materials in improving the performance of refrigeration systems. Sust. Ener. Technol. Assess. 56:103097. doi: 10.1016/j.seta.2023.103097
Manske, K. A., Reindl, D. T., and Klein, S. A. (2000). Load sharing strategies in multiple compressor refrigeration systems. International refrigeration and air conditioning conference. Paper 523. Available at: http://docs.lib.purdue.edu/iracc/523
Mostafa, A., Hassanain, M., and Elgendy, E. (2022). Transient simulation and design parameters optimization of a cold store utilizes solar assisted adsorption refrigeration system. Case Stud. Therm. Eng. 37:102273. doi: 10.1016/j.csite.2022.102273
Rahman, A., Abas, N., Dilshad, S., and Saleem, M. S. (2021). A case study of thermal analysis of a solar assisted absorption air-conditioning system using R-410A for domestic applications. Case Stud. Therm. Eng. 26:101008. doi: 10.1016/j.csite.2021.101008
Reindl, D. T., and Jekel, T. B. (2007). Heat recovery in industrial refrigeration. ASHRAE J. 49, 22–28.
Rismanchi, B., Saidur, R., Boroumand Jazi, G., and Ahmed, S. (2012). Energy, exergy and environmental analysis of cold thermal energy storage (CTES) systems. Renew. Sust. Energ. Rev. 16, 5741–5746. doi: 10.1016/j.rser.2012.06.002
U.S. Environmental Protection Agency (2020). Energy efficiency opportunities in industrial refrigeration. USA: University of Delaware Industrial Assessment Center.
United Nations Environment Programme (2021). Food waste index report 2021. Nairobi: United Nations Environment Programme.
Vrachopoulos, M. G., Filios, A. E., Kotsiovelos, G. T., and Kravvaritis, E. D. (2007). Incorporated evaporative condenser. Appl. Therm. Eng. 27, 823–828. doi: 10.1016/j.applthermaleng.2006.09.021
Wang, R. Z., and Oliveira, R. G. (2006). Adsorption refrigeration—an efficient way to make good use of waste heat and solar energy. Prog. Energy Combust. Sci. 32, 424–458. doi: 10.1016/j.pecs.2006.01.002
Wang, L. W., Wang, R. Z., and Oliveira, R. G. (2009). A review on adsorption working pairs for refrigeration. Renew. Sust. Energ. Rev. 13, 518–534. doi: 10.1016/j.rser.2007.12.002
Keywords: food storage, cold chain, energy management, refrigeration, sustainability
Citation: Karacan MA, Yilmaz IC and Yilmaz D (2023) Key implications on food storage in cold chain by energy management perspectives. Front. Sustain. Food Syst. 7:1250646. doi: 10.3389/fsufs.2023.1250646
Received: 30 June 2023; Accepted: 27 October 2023;
Published: 09 November 2023.
Edited by:
Pankaj B. Pathare, Sultan Qaboos University, OmanReviewed by:
Rasaq Lamidi, University of Birmingham, United KingdomCopyright © 2023 Karacan, Yilmaz and Yilmaz. This is an open-access article distributed under the terms of the Creative Commons Attribution License (CC BY). The use, distribution or reproduction in other forums is permitted, provided the original author(s) and the copyright owner(s) are credited and that the original publication in this journal is cited, in accordance with accepted academic practice. No use, distribution or reproduction is permitted which does not comply with these terms.
*Correspondence: Deniz Yilmaz, ZGVuaXp5aWxtYXpAYXJlbC5lZHUudHI=
Disclaimer: All claims expressed in this article are solely those of the authors and do not necessarily represent those of their affiliated organizations, or those of the publisher, the editors and the reviewers. Any product that may be evaluated in this article or claim that may be made by its manufacturer is not guaranteed or endorsed by the publisher.
Research integrity at Frontiers
Learn more about the work of our research integrity team to safeguard the quality of each article we publish.