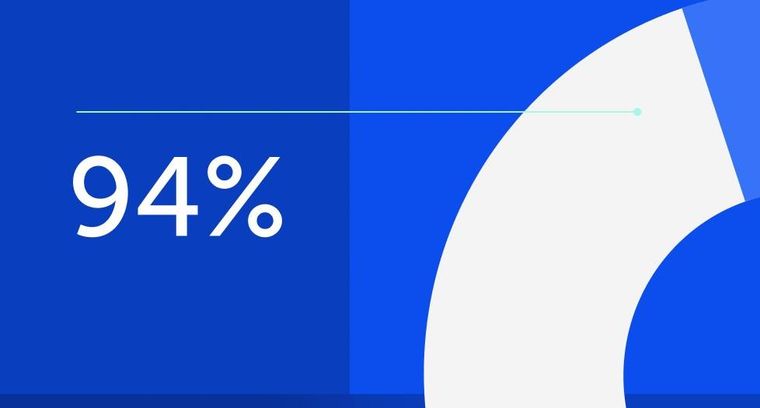
94% of researchers rate our articles as excellent or good
Learn more about the work of our research integrity team to safeguard the quality of each article we publish.
Find out more
ORIGINAL RESEARCH article
Front. Sustain. Food Syst., 23 February 2022
Sec. Agroecology and Ecosystem Services
Volume 6 - 2022 | https://doi.org/10.3389/fsufs.2022.848035
This article is part of the Research TopicOcean/Aquatic Food Systems: Interactions with Ecosystems, Fisheries, Aquaculture, and PeopleView all 11 articles
For over 50 years, government fishery agencies have recognized the need to transition excess fishing capacity in coastal waters to aquaculture. For the most part, investment strategies to move wild capture and harvest efforts into aquaculture have failed since the technology and capital expense for entry, such as large fish pens, was not conducive for acceptance. In contrast, low trophic level aquaculture of shellfish and seaweeds is suitable as an addition to the livelihoods of seasonal fishing communities and to those displaced by fishery closures, especially if vessels and gear can be designed around existing fishing infrastructures, thus allowing fishers to maintain engagement with their primary fishery, while augmenting income via aquaculture. In this study, an inexpensive, lightweight, and highly mobile gear for kelp seaweed farming was developed and tested over a 3-year period in southern Maine, USA. The system was different from existing kelp farming operations used in nearshore waters that use low-scope mooring lines, and heavy, deadweight anchors. Instead, a highly mobile, easy to deploy system using lightweight gear was designed for exposed conditions. The entire system fit into fish tote boxes and was loadable onto a standard pickup truck. The seaweed system had small but efficient horizontal drag embedment anchors connected to a chain catenary and pretensioned with simple subsurface flotation. The system was able to be deployed and removed in less than 4 h by a crew of three using a 10 m vessel and produced a harvest of 12.7 kg/m over an 8-month fall-winter growth period. The target group for this seaweed research and development effort were coastal fishing communities who move seasonally into non-fishing occupations in service industries, such as construction, retail, etc. An economic assessment suggests farmers would realize an 8% return on investment after3 years and $13.50/h greater income as compared to a non-farming off season job at minimum wage. This low-cost seaweed farming system for fall-winter operations fits well into a “livelihood” strategy for fishing families who must work multiple jobs in the offseason when their main fishery is unavailable.
In many global regions where small boat, community scale, coastal commercial fishing communities persist, aquaculture has been proposed as a livelihood alternative or supplement. While not operating at large, industrial scales, many commercial fishing interests possess much of the capital infrastructure (boats, gear, etc.), on-the-water knowledge and experiences needed to become part-time or seasonal ocean farmers. However, investments and initiatives to decrease coastal fishing efforts and replace it wholly with aquaculture have failed unless complete closure of a fishery was mandated and a large government investment made in aquaculture as an alternative livelihood. For example, gill net fishing in the Cedar Key region of Florida, USA was prohibited by federal law in 1994. A transition to calm aquaculture became a successful alternative for more than 350 gillnet fishers through a long term, expensive, federally funded job-retraining program (Stephenson, 2013). However, the complete collapse of a fishery need not occur for fishers to diversify in aquaculture. An owner-operated bioengineering approach to develop aquaculture in fishing communities can be pursued whereby approaches are developed with fishing communities to be complementary, supplemental incomes to fishing, not a total replacement to fishing.
The marine economy of coastal Maine, United States of America (USA) is one such case study where taking a preemptive, livelihoods-diversification approach to the adoption of aquaculture is yielding dividends. The Maine marine economy is almost entirely dependent on the nearshore landings of the American lobster (Homarus americanus). At the recent industry peak in 2016, lobster landings in the nearshore state fishery approached 60,000 tmt with an ex-vessel value of $533 million USD. The fishery is the keystone of the ocean-foods based economy in Maine; comprising 74% of total commercial landings across all fisheries by value, supporting 4,500 licensed commercial harvesters (ME DMR, 2021). Dependence on a single fishery in an ocean ecosystem warming faster than 90% of all other ocean regions (Pershing et al., 2015) represents considerable risk not only to the individual commercial fisher but the marine economy as a whole. A recent study by Le Bris et al. (2018) suggested that while the Maine lobster fishery may be more resilient than its collapsed southern New England counterpart (ASMFC, 2015) due to adaptive management strategies (e.g., escape slot sizes, minimum and maximum size limits, and conservation of egg-bearing females), the fishery still faces long-term climate driven vulnerability and likely declines. In fact, this reality may already be playing itself out. Since reaching peak landings in 2016 in both volume and value, both landings and value have since declined, dropping from 60,000 mt (2016) and $540 million to 43,545 mt and $405 million in 2020 (ME DMR, 2021).
Diversification from a fishery's landings could defray risks associated with single species dependence and mark a return to the legacy of diversified, multi-species harvesters in the Gulf of Maine region. However, Maine's commercial fisheries are effectively “locked” into a single species permitting approach, decreasing adaptability, and increasing risk and vulnerability for the many owner-operated harvesters. Maine's evolution to become a fisheries monoculture has occurred due to the confluence of: (1) The splitting of commercial fisheries licensing from only six licenses prior to 1977 (lobster, shellfish, marine worms, scallops, and a general category for other species) to now 23 license types across 16 fisheries, and (2) The collapse or decline of non-lobster fisheries, resulting in restricted access to commercial licenses. The rate of additional new lobster licenses over the past 25 years for example, is only 0.6/year (Stoll et al., 2016). With the changing climate placing uncertainty on species recovery (e.g., cod; Pershing et al., 2015) fishermen are “stuck” in their respective fisheries, unable to diversify by harvesting multiple species as in the past.
Aquaculture has been promoted as a potential diversification outlet for commercial fishers in the Gulf of Maine as it has in many global fisheries regions (S. Belle, personal communication). However, additional capital and operating investments to engage in new aquaculture operations are considered carefully by fishers. Clear information on returns to additional capital outlays (both human and monetary) are important to fishers as nearshore coastal fleets remain overcapitalized, and risks surrounding market development and increased volatility due to ocean climate change, among other risks are considered. A recent survey of fisherman on island communities in Maine indicated that outside of boats, there was very little overlap in capital equipment needed to engage in aquaculture, and that additional procurement of non-fisheries related capital equipment was an impediment to adoption of aquaculture (Love, 2016). This contradiction in the perception of aquaculture's diversification potential vs. reality is an important one. In order for commercial fishers to add ocean farming to their livelihoods a need exists to minimize the impact of four barriers to entry: (1) capital, (2) equipment, (3) knowledge, and (4) time.
Bivalve shellfish farming is a growing and lucrative sector of the coastal aquaculture industry worldwide. It has considerable market potential for expansion, especially in the northern temperate and peri-Arctic oceans for blue mussels (Mytilus edulis), American oysters (Crassostrea virginica), and sea scallops (Placopecten magellanicus). However, bivalve farming methods are capital, equipment, and knowledge intensive. Moreover, in the north, these species require significant time to harvest and consequently delay the generation of additional income (18–24 months for mussels; longer for scallops and oysters). Bivalve aquaculture as a result is unlikely to serve the purpose to provide a simple, low-cost gateway to starting ocean farming for coastal fishing communities as they exhibit all four barriers to entry.
For northern temperate oceans aquaculture of seaweeds, especially sugar kelp (Saccharina latissima), and other kelp species have fewer constraints. The farming of marine macrophytes is a global industry that continues to grow. In 2014, the sector was worth $6.4 billion USD (Cottier-Cook et al., 2016), growing to an estimated $13.1 billion USD in 2018 (FAO, 2020). Seaweeds are used in myriad products from human foods to toothpaste to exploratory research in biofuels and livestock feed. As with other seafood products, the USA imports the vast majority of seaweed from foreign producers (Piconi et al., 2020). This represents encouraging potential as domestic markets and value-added seaweed products are developing rapidly. The economic model for kelp aquaculture in Maine mirrors the existing way commercial fishing operates with the immediate dockside sales of raw product. Kelp is a fall-winter crop that comes to harvest size in less than 6 months; typically seeded in October–November and harvested in April–May. This eliminates the need for a multiyear husbandry commitment and is countercyclical to the traditional inshore summer lobster fishery. Kelp farming requires a skill set, knowledge base, social license, and equipment similar to those already possessed in abundance by established fishermen. These factors make seaweed aquaculture a logical option for fishers to adopt, as the model decreases all barriers to entry.
From 2015 to 2020, harvest of farmed sugar kelp in Maine increased more than 3,000% from 6.6 mt wet weight. While official Maine state datasets for 2021 are not yet available, the harvest will likely exceed 450 mt (Atlantic Sea Farms, personal communication). Demographic information on seaweed farm operators is not available. However, the largest value added kelp product producer in the state (Atlantic Sea Farms) works with 24 partner farmers, 21 of which are also commercial lobster fishers (Gershenson, 2020) indicating that the adoption of kelp farming by lobster fishers in Maine is already occurring. While farmed macroalgae is a multibillion-dollar enterprise world-wide, farmed seaweed from traditional production regions in China, South Korea, and Japan is traded at commodity scales yielding prices and markets in which kelp farms in the United States of America (USA) and the European Union (EU) cannot compete (FAO, 2017). Instead, emerging markets for kelp products in the USA and EU focus on high value niche food and health products (Grebe et al., 2019) This allows growers to operate smaller farms profitably, however even with domestic market price advantages, seaweed farming remains a largely a low-value, high-volume practice resulting in thin margins for producers. Given the part-time, supplemental nature of the current model of the Maine kelp farming sector, it is critical that every component of the farming process be cost-optimized for capital expenditure, efficiency of deployment, use, and harvest to ensure the greatest returns to the farmer. However, the current system design is cumbersome, immobile, and moorings are more or less permanent. These aspects make small scale adoption by fishers difficult. Moreover, Maine boasts >5,600 km of highly convoluted, rugged, and energetic coastline, and the areas close to shore are crowded with multiple user groups and stakeholders. As the industry grows the number of inshore, protected sites suitable for kelp growing will become limiting. However, there is ample opportunity to scale the sector by siting farms not offshore, but in nearshore exposed sites (Costa-Pierce and Chopin, 2021). It should also be noted that the same climate change driven environmental stressors impacting the American lobster also impact all macroalgae in the Gulf of Maine. Kelp forests are declining globally and the Gulf of Maine mirrors the trend (Filbee-Dexter et al., 2016; Filbee-Dexter and Wernberg, 2018; Witman and Lamb, 2018). While these changes are unlikely to be entirely overcome, challenges related to ocean warming are likely to be exacerbated closer to shore. Placing systems in higher energy conditions further from shore can help alleviate some of this risk through site selection. However, this requires sophisticated, well-engineered testing in the laboratory and field to ensure viability and survivability in these types of oceanic conditions. To overcome these constraints, inexpensive, lightweight, and highly mobile gear must be developed that can withstand high energy ocean conditions associated with exposed sites.
Currently the predominant gear-model employed by commercial seaweed farms in Maine is based on a model described by Flavin et al. (2013). This model is designed for calm waters and utilizes large, deadweight moorings with nearly vertical mooring lines. While suitable for protected waters, this model is costly to assemble and deploy, requiring large vessels capable of transporting 500–2,500 kg moorings to deploy the farm, and dictates the size of the farm be large from the outset to reach the economy of scale needed for profitability and permanence, since deadweight moorings are costly and difficult to move or reposition. Additionally, this system is suited only to the calmest of waters since the near-vertical moorings and the large surface flotation needed result in significant variations in tension as the water depth varies through tidal cycles. This results in a lack of tension in the system that can lead to slack moorings, drift of culture lines, and snap loads on the system in waves when the tide is low, and high tensions and difficult operations when the tide is high. Any of these factors can lead to failure of system components and potential loss of product. As farmers look to expand and scale up, innovations in farm designs for the many high energy sites available in nearshore oceans are needed to optimize the farming process to increase margins and to open areas to farming that previously would have been considered too exposed to operate in.
Innovations in engineering for seaweed farms have been occurring since the 1970s when the concept of biofuel production via offshore cultivation of Sargassum spp. was proposed (Bak et al., 2020), and more recently via the specter of co-location with offshore wind installations (Harkell, 2021), and furthermore via a reemergence of the biofuel concept (Harris et al., 2021). The design and testing of offshore and exposed seaweed cultivation platforms has been reviewed by Roesijadi et al. (2008), Langan and Buck (2017), and most recently by Bak et al. (2020). Commonplace among these assessments is complexity of design, high capital cost necessitating the need for scaling to achieve profitability, and the need to develop specialized mechanization and production flow processes specific to the husbandry platform. Examples of offshore cultivation rigs highlighting these issues are large ring structures deployed in the 2000s for cultivation of S. latissima within offshore wind structures (Buck and Buchholz, 2004, 2005) and tension leg platforms developed by the Korean Institute of Ocean Science and Technology for cultivation of Saccharina japonica (Chung et al., 2015). In both cases, the complexity of engineering and cost of operation proved insurmountable, and neither are currently employed commercially.
A system in use since 2010 by Ocean Rainforest at a nearshore exposed site in the Faroe Islands called the Macroalgae Cultivation Rig (MACR) has been successful, and lessons can be gleaned from its simplicity (Bak et al., 2018). The MACR system consists of a 500 m long polysteel line (30 mm) suspended horizontally between two surface floats affixed to four mooring lines held in place with 1–15 t steel anchors each. From this backbone, 10 m vertical grow lines seeded with S. latissimia are attached, each with a surface buoy (Bak et al., 2018). The system has survived 4 m significant wave heights over multiple years indicating good survivability in exposed environments (Bak et al., 2018, 2020). However, with many vertical grow lines and a four-point mooring system, the cost of such a system would still likely be prohibitive for a small to medium scale, fishermen owner-operated farm operations. While this much simplified approach does reduce costs by comparison, it still requires purpose-built equipment and vessels to operate and harvest (Bak et al., 2018).
A rigorous design process is necessary to improve profitability and function of farming platforms intended for community scale applications in nearshore exposed environments for existing commercial fishers, as in Maine. In general, the design of offshore structures requires an engineered approach since risk can be substantial. This is especially true for industries such as oil/gas and wind where failures could be catastrophic. The same level of risk and return on investment does not necessarily exist for simpler, single owner operator kelp farming systems. Therefore, an ocean engineering approach is typically not applied. System optimization is needed so that exposed site gear is specified for the commercial fishery operator. Systems need to be designed to provide a solution to a problem, focused on the mechanical components in a precise, methodical, and mathematical fashion (Lindbeck, 1995; Haik, 2003). Because there is no pre-existing end user in traditional offshore seaweed farm system design, the engineering process is free to innovate and produce production systems that require acutely designed components from deployment through harvest and processing.
The criteria for design can be derived from the 30 commercial fishers who are also operating commercial scale kelp farms in the Gulf of Maine. Design criteria must consider the existing infrastructure in the form of fishing equipment and vessels that need to be repurposed to the greatest extent possible to assure profitability. Moreover, the dominant kelp farming model in Maine operates under the owner operated commercial fisheries model whereby harvesters bring product to port where it immediately changes hands to a processor or distributor. The existence of end users of the product (the kelp farming system) necessitates an innovative social-ecological industrial design approach.
In this applied research, a combined social-ecological industrial with ocean engineering design approach was used to establish a framework for developing a kelp farming platform for a specific target user group; namely, coastal owner operated fishing families who seek to employ seaweed farming in nearshore, exposed sites, as a product diversification tool for supplemental income. We have implemented a low-cost seaweed farming system for fall-winter operations that fits well into a livelihood strategy for rural coastal communities who must work multiple jobs in the offseason when their main fishery is unavailable due to seasonality, regulations, etc.
A design framework for seaweed farm engineering was developed to meet current industry needs and challenges. To assess industry priorities and desires for system function, our research team had informal conversations with several industry members currently farming S. latissima in the Gulf of Maine and leveraged the field research teams experience in operating a pre-existing experimental 200 m kelp farm of a different design over 3 years from 2015 to 2018. As part of this design process, our team sought to both satisfy engineering design goals (scalability, survivability, yield), blended with a system design meeting the needs of the growing inshore seaweed farming industry.
The project focused on an actual application to design, deploy, seed and harvest sugar kelp at a site with a State of Maine, Limited Purpose Aquaculture (LPA) license with the dimensions of 0.3 × 122 m (Conkling, 2021). The LPA is located in Saco Bay Maine (USA) with full exposure to the east (Figure 1). The site has a nominal mean sea level of 15.2 m with bottom substrate composed mostly of sand and a mean tidal range of 2.7 m. While the site is within 3 km of the shore, it is exposed to Nor'easter storm events (from the east) from the Gulf of Maine. One extreme event, called the Patriot's Day storm, occurred on 16 April 2007. Wave simulation hindcast modeling described in Xie et al. (2016) for this storm yielded significant wave heights at the site on the order of 4–5 m with a dominant period of 11 s. Return period analysis using long term datasets from the National Oceanic and Atmospheric Administration, National Data Buoy Center, Station 44007 buoy showed that the Patriot's Day event exceeded the 50-year storm condition. In addition to waves, typical currents at the site are associated with the M2 tides, though a strong, seasonal, surface component is influenced by the Saco River flow. To investigate oceanographic conditions, a NORTEK Acoustic Wave and Current Profiler (AWAC) was deployed near the site. Datasets showed a predominant, semi-diurnal tidal ellipse with a major axis oriented in an east-west direction with current magnitudes approaching 0.3 m/s. This orientation was critical for placement of anchors to be in line with the tides. The measured current magnitude was multiplied by 1.85 to estimate a 50-year return current speed of 0.56 m/s, using methods from the Norwegian Standard NS 9415 (DNV-RP-C25, 2010).
Figure 1. The field study was conducted at a 0.3 by 122 m LPA site in Saco Bay Maine (USA). While the site is only about 2.5 km from the shore, it is completely exposed to the east.
The initial design process focused on three criteria. Initially the farm must (1) fit within the lease site, (2) keep the gear as light as possible. Once the initial design components were specified, the farm was constructed, deployed, seeded, and assessed for biomass yield. With the known amount of biomass, the system was then evaluated for criterion (3) to be designed for the exposed, 50-year storm condition.
To fit within the lease site, the design incorporated a 122 m kelp grow line pre-tensioned with subsurface flotation at the corners with opposing anchor lines (Figure 2). The kelp line was situated in an east-west orientation aligned with the major axis of the tidal currents. It was important to define the orientation since this detail was required for the LPA application. The kelp line was held at 2.1 m below the surface with three support structures made with off the shelf rope, PVC pipe, and lobster floats at east, middle and west locations. Anchor lines extended to the seafloor at an angle of 32° to the horizontal to a depth of 15.2 m. At the seafloor, the system was designed to include a section of 15.2 m chain with one end attached to the anchor line (Figure 2B). In this design approach, 1/3 of the chain is pulled up into the water column by the subsurface flotation forming a spring-catenary that provides pretension to the system preventing snap loads. Two-thirds of the chain is situated on the seafloor and is connected to a drag embedment anchor. Drag embedment anchors are efficient when loaded horizontally with some having a holding power up to 50 times the weight. The intent was to eliminate the use of a 6672 Newton (N) concrete block typically used in the region as described in Flavin et al. (2013). The resulting anchor leg geometry has a scope of 3:1, achievable in part with the use of 15.2 meters of chain.
Figure 2. (A) The dimensions of the kelp aquaculture system deployed at the exposed site. (B) Mooring line detail only depicted for the western leg as the eastern mooring is identical.
Component specification also considered operational capabilities for the gear to be as light as possible as defined by design criterion #2. Since many fishing vessels have limited deck equipment like “A-frame” structures and high-capacity winches, the intent was to size the gear to be under 445 N so that two people could handle the components. The first step was to specify the weight of the chain in the catenary to offset the flotation at the corner of the kelp line. This was done by submerging two lobster buoys, for a total 222 N of flotation at each corner. To maintain the geometry, the anchor legs each incorporated a 16 mm, long-link, galvanized steel chain weighing 222 N/4.5 m. This chain has a working load limit of approximately 31 kN. The geometry with the catenary shape was verified using mooring system design techniques described in Faltinsen (1990). With 222 N of buoyancy and the specified geometry at the corners, pretension values of 356 and 418 N were calculated for the horizontal kelp and anchor lines, respectively. The anchor and kelp line components were specified with 25 mm of three-strand nylon rope having an estimated breaking strength when spliced of approximately 108 kN. The drag embedment anchors were also specified, each having a weight of 0.49 kN and an estimated holding capacity of 24.5 kN. The system was deployed and seeded on 30 October 2018 with kelp harvested on 22 May 2019. With the estimated biomass yield, the 122 m kelp farm system components were evaluated for the 50-year storm condition (criterion #3).
“Brood stock” was collected from wild sporophytes showing development of ripe sorus tissue, identified as possessing differentiated sorus tissue laterally along the central axis of the distal frond. Ripe sorus tissue was targeted as being thickened and distinct from somatic tissues having a dark color, non-translucent opacity and raised tissue margin. Sori was harvested by cutting the blade distally from the meristematic tissues, leaving behind the hold fast, stipe and meristem to allow regrowth of the thallus. Collected tissue was stored in coolers with ice packs for transport to the nursery facility.
Sorus tissue was immediately prepped for spore release in the nursery by first removing all somatic tissue and trimming sori into approximately 3 × 5 cm portions with a clean razor blade. Visually obvious epiphytes and tissue imperfections were also trimmed and or scraped from the tissue in the same fashion. Sori were then rinsed thoroughly with 0.25 μm filtered seawater (FSW) and bathed for 30 s in a 10% betadine solution diluted with FSW. Following the betadine rinse, sori were rinsed again with FSW and conditioned for spore release by placing between paper towels dampened with FSW and incubating in dark conditions at 8°C for 24 h. Spore release was then induced by placing prepared tissues in 10°C FWS and monitored for release with light microscopy. Spore densities were quantified with a haemocytometer. Sporing was considered complete when zoospore densities were adequate to achieve 10,000 spores/ml concentration in inoculation tube water.
The spores were allowed to settle on PVC pipe spools of 5.1 cm diameter wrapped with 165 m of #9 nylon tufting twine (1.07 mm diameter) by placing them in 4 L settlement tubes and inoculated with FSW containing ~10–20,000 spores/ml. Settlement spools were incubated at 12°C for 24 h, after which spools were transferred to 75 L culture tanks. Culture tanks were maintained at 12°C with a 12:12 light-dark photoperiod. Nutrients were provided via Guillard′s (F/2) nutrient media. Water changes were conducted weekly to maintain cleanliness and adequate nutrient levels. Spools were inspected daily for gametophyte and sporophyte development and maintained in culture tanks until sporophytes were 2–5 mm in length. The seed spools that were eventually deployed on the farm were settled on 10-September-2018, introduced to the nursery on 11-September-2018 and then deployed to the experimental farm site on 30-October-2018.
Farm monitoring was targeted at twice monthly during deployment. Due to the exposed nature of the site, this was often not possible due to weather, air temperature, or adverse sea conditions. Sampling intensity was increased during the spring (March–May) as more weather days became available and as kelp growth accelerated.
During site visits, the farm system was inspected for position and integrity to the greatest extent allowable by the weather conditions. Soft connections, and surface floatation connection points were inspected for wear and chaffing.
Biomass monitoring was conducted by collecting all kelp individuals from a 10 cm section of farm (linearly along the culture rope). Since sampling was destructive, and given the small nature of the farm, 10 cm was chosen as a biomass that was acceptable to remove from the farm at frequent intervals without appreciable impacting the final yield of the farm, and thereby the engineered structure's performance and behavior. During each sampling event, three replicate 10 cm samples were targeted: one each from the east, middle, and west portions of the farm. Samples were stored in individual plastic bags and kept cool and moist until processing.
Samples were processed for total wet weight. Each individual sporophyte was also processed for total wet weight, blade weight and stipe weight. Individual length and width measurements were also taken for all sporophytes sampled: Total length, blade length, as well as blade width along basal, medial and apical portions of the blade. Presence absence of sorus tissue was noted within each sample.
A basic capital expenses to gross income and initial rate of return assessment was conducted. The assessment was limited to capital expenses required for purchasing farm components for a single 122 m longline. Assumptions were made that farmers were existing commercial fishers in which case infrastructure of on water operations were already in ownership (i.e., boats, trailers, trucks, etc.) and that expenses for the farm would be only the new capital outlay needed. Seed costs and farm-gate crop values were estimated from current market values in the region and the extensive personal experience of the research team.
The components that were specified for the farm system was pre-measured, cut and stored in standard black fish totes to be transported in a standard pickup truck (Figure 3A). The lightweight gear fit easily on a 10 m, landing craft style research vessel (Figure 3B). Note that in Figure 3B only one anchor assembly is shown. The system was deployed and seeded on 30 October 2018.
Figure 3. (A) The components of the farm fit into fish totes loaded in a standard pickup truck. (B) The gear was loaded on a 10 m landing craft research vessel. Note that only one of the two anchor assemblies are shown. (C) In February, the kelp was growing on the intact system. (D) Growth continued and in April, biomass was estimated at 5.37 kg/m and (E) harvested at 12.67 kg/m on 22-May-2019.
The kelp farm was monitored throughout the winter season of 2019. In early February 2019, a site survey indicated that the 122 m farm had maintained its position at the exposed site with kelp starting to grow to lengths of 10–30 cm (Figure 3C). Inclement weather continued, but the next site survey on 20 March 2019 showed an even distribution of kelp growing on the line. By April 2019 the biomass was estimated at 5.7 kg/m (Figure 3D) and at 12.7 kg/m at harvest in May (Figure 3E).
Total wet weight biomass at time of harvest was extrapolated from the measured biomass sub-samplings at time of harvest determined to be 1546.1 kg wet weight total over a 122 m grow line. Peak biomass was 12.67 kg/m (±0.4 kg) at harvest (5/22/2019, day 107). A logistic growth curve for biomass (N) as a function of time (t) was calculated using:
The growth curve was fitted between the initial (N0 = 0.1 kg/m) and the final (K = 12.7 kg/m) yield values with a rate (r) obtained from the dataset using the techniques described in Masters and Ela (2007) (Figure 4). Finding where the slope of dN/dt is equal to zero identifies the maximum growth rate, which occurred on 10 April with a value of 0.2 kg/m/d.
Individual sporophyte weight followed similar trends to overall biomass however with sporophyte measurements beginning on 3.25, the data represent the linear portion of the growth curve thereby allowing for linear regression as opposed to logistic regression. Sporophyte growth rate by wet weight over the growing season was 0.9 g/day starting at a minimum of 26.5 g (± 16 g) when first measured on 3/25 and ending at a maximum average weight of 83.3 g (± 50 g) (Figure 5).
Figure 5. Mean individual sporophyte wet weight over time during linear growth phase. Linear regression shown. Error bars represent standard error.
Each component of the structure withstood the growing season without failure. However, to verify structural survivability for the 50-year storm condition (criterion #3), a set of numerical modeling simulations were conducted using the previously described biomass yield characteristics. Simulations were conducted using a dynamic finite element numerical modeling approach that incorporates macroalgae hydrodynamics as drag areas per unit length derived from Fredriksson et al. (2020). This modeling approach solves the equations of motion of each element at each time step as summarized in NOAA's Basis-of-Design Technical Guidance for Offshore Aquaculture Installations in the Gulf of Mexico (Fredriksson and Beck-Stimpert, 2019). Wave and current loading on elements (including biomass elements) is incorporated into the model using a Morison equation formulation (Morison et al., 1950) modified to include relative motion between the structural element and the surrounding fluid. For elements intersecting the free surface, buoyancy, drag, and added mass forces are multiplied by the fraction of the element's volume that is submerged.
Input to the model included an irregular sea-state time series with a significant wave height of 4.5 m and a dominant period of 11 s. The 50-year estimated current speed was taken to be uniform with depth and applied in the same direction as the waves. In the design simulations, load cases were configured with the waves and current at 0°, 45°, and 90° orientations to the farm with 0° being aligned with the grow line. The kelp was modeled as a series of 1 m aggregates knowing the yield (12.5 kg/m), mass density (1,054 kg/m3), and length (1.3 m) obtained from field datasets. With this information, aggregate weight and buoyancy was calculated and drag area values per unit length applied. Inputs to the model are included in Table 1.
For each load case, the maximum expected tensions, and forces in a 1-h storm were calculated assuming an extreme value distribution of the maximum loads. The capacities of the mooring components were divided by the maximum expected tensions and forces to compute a factor of safety for each component (Table 2).
The American Bureau of Shipping (ABS) recommends a safety factor of 1.82 on synthetic ropes and 1.67 for chain (ABS, 2012). The American Petroleum Institute recommends a safety factor of 1.67 on chain moorings and recommends that additional chain diameter be incorporated to allow for material lost to corrosion (API, 2005). The U.S. Navy Geotechnical Handbook (Naval Facilities Engineering Service Center, 2012) recommends a safety factor of 1.5 for drag embedment anchors. Thus, the specified structural components meet these standard requirements.
An economic analysis was conducted in constant dollars over a 3-year period considering the small-scale operations of the Maine working waterfront as an opportunity to supplement fishing activities during the offseason. In this context, the offseason represents October to May opposite the lobster fishing months. The analysis included the capital costs for the equipment specified for survivability at the exposed site (Table 3). It was assumed that the equipment would have a minimum design life of approximately 3 years with only minor additions of $200 at the beginning of years 1 and 2. The dataset included yearly seed and permit costs of $300 and $100, respectively. The capital and yearly expenditures were applied in the procedure at the beginning of the budget year (Table 4). Labor, fuel, and revenues were applied at the end of the budget (Table 4) as if for tax purposes. Tax and depreciation was not included in the analysis because proceeds would most likely be lower than the requirement for filing.
Labor was first modeled assuming minimum wage at $12.75/h for a total of 40 h/year ($510) (ME DOL, 2022). The time requirement was estimated from the following offseason schedule:
• October: 8 h for system preparation
• November: 8 h for deployment
• December–April: 2 h each month for system monitoring
• May: 8 h for harvest
• June: 6 h for equipment storage.
Yearly fuel costs were estimated assuming a 10 m lobster vessel burning diesel at 1 gallon/h for 40 h at a price of $3.50/gallon ($140/year). Revenues were based on the values provided in Table 4 from a total yield of 1546.1 kg wet weight total over a 122 m grow line measured from the Saco Bay site. The yield value was adjusted by 10% due to blade and holdfast trimming (1394.4 kg). Revenues were based on a price of $1.65/wet kg resulting in $2301 per year. This pricing is based on the author's professional experiences in the kelp industry in Maine. Over the past 10 years, farm-gate prices have varied from $1.10–$2.20 USD/wet kg. $1.65/wet kg represents the median of this spread and was verified by current sellers. It should be noted that this price is representative and that no kelp grown on the experimental farm was sold, to avoid competition with the commercial kelp farming community.
An internal rate of return analysis (i) was then performed using the gross income cash flow column in Table 4. This was calculated by setting the Net Present Worth (NPW),
to a value of zero and solving the series iteratively for internal rate of return (i). In Equation (2), cn are the cash flow values, n is the year from 0 to 3 and N is the total number of years. At minimum wage, the offseason lobster fisher would return approximately 8.6% of their investment, though profits would be minimal. The analysis was also done for a 0% rate of return by increasing the labor rate, which occurred at $4.75 above the minimum wage. Therefore, the lobster fisher could pay themselves $17.50/h and break even. Note that this analysis assumes that the infrastructure (vessel, truck, trailer, etc.) is paid for during the fishing season and is appropriate for handling the lightweight gear designed for the exposed kelp farming operations.
Scale is one of the most controversial aspects of aquaculture today. In the nearshore oceans of much of the western hemisphere which are common property resource areas, scaling issues play a central role in the political and regulatory obstacles to advancing aquaculture (Knapp and Rubino, 2016; Stead, 2018). In the Western hemisphere, a barrier to the growth of aquaculture and in this case, seaweed aquaculture, is the high competition for nearshore ocean space which is crowded with existing users (Goldburg et al., 2001). Areas are less crowded in more exposed regions with higher energy, or seasonally when winter creates harsh conditions.
Size of individual farms is also a critical component of scale. Siting conflicts increase proportionally with the size of the space occupied. Globally, in emerging seaweed farming economies a disconnect exists between the rhetoric and the reality that successful commercial farms are all relatively small and focused on producing seaweed for human consumption. The disconnect often centers on development of industrial scale seaweed farms aimed at producing large amounts of product on a single site, often for feed, fuel, or sale of carbon credits (Costa-Pierce and Chopin, 2021). The State of Maine is one of the only jurisdictions in the world to simplify scaling by allowing easy entry into small scale ocean aquaculture of low trophic level aquaculture species (seaweeds, shellfish) in a “limited purpose aquaculture permit” (LPA) (Conkling, 2021) which has alleviated barriers to entry for small scale seaweed farming. Thus, for expansion of new owner operated fishing interests, two aquaculture developmental models are available for them: (1) “scaling out,” or (2) “scaling up.” Scaling up of ocean space for aquaculture remains regulated though an ocean-leasing structure tiered by size. This tired system has size limitations the upper bounds beyond which social license to operate become limiting. By contrast, the LPA license allows for scaling out; allowing for geographic expansion, while constraining the overall footprint of any one farm. This tool has allowed for a rapid scaling out of sea seaweed farming sector in Maine.
While the LPA licensing tool, unique to Maine, has alleviated some of the siting conflicts with regards to farm footprint, it does not alleviate conflicts related to siting of farms close to shore. Generally, stakeholders increase in both number and diversity with increasing proximity to shore. Maine boasts 5,600 km of highly rugose shoreline with many protected bays, inlets, fjards, and islands. While the waters around these features are attractive for seaweed aquaculture due to quiescent waters and proximity to shore, they are impacted by many potential conflicts including but not limited to commercial fishing, recreational boating, riparian landowner viewsheds, conservation areas (seagrass beds, nesting seabirds, etc.), shipping, and other aquaculture farms (bivalves). However, there is major opportunity for expansion of seaweed aquaculture just outside these areas; not “offshore” but “near-shore, exposed” sites that remain close to shore, but offer more energetic oceanographic conditions with which the aforementioned conflict agents often do not overlap. The coast of Maine is ~360 km straight line distance from New Hampshire to Canadian borders. If this straight light were drawn along the outer edges of every inshore island and bay, state waters would still extend another 4 km from shore. This means there is at least 1,700 km2 of available space that is within 4 km from shore in exposed oceanographic conditions.
These areas are attractive for scaling out seaweed aquaculture especially as a supplemental livelihood to existing commercial fishers and these individuals have the local ecological knowledge needed to operate in these more challenging oceanographic sites. In this dynamic and rapidly changing sector, the primary challenges to expansion can change quickly. As recently as 2019 for example, Grebe et al. (2019) posit market access as a primary blockade to increasing kelp production. However, as of 2021 seaweed markets for domestic value added food and nutraceutical products are expanding rapidly as companies continue to pursue innovative new products and expand markets (Atlantic Sea Farms, personal communication). If this trend continues, it is assumed that perspective farmers will first assess the ability of the market to bear increased production prior to engaging in farming. Beyond this assessment, the limitation to entering farming then becomes farm system design that is suitable to operate safely and predictably in these nearshore exposed sites. As discussed previously, engineering approaches to farm system design are not often employed that small scales, and yet this is exactly what is needed for a scaled-out systems approach to sector growth to be successful.
The system designed and tested in this study demonstrates the value of user-focused design process. Design criteria were delineated based on knowledge of the intended user; existing small scale fishers who would farm as a livelihood augmentation, not a livelihood alternative. This type of social-ecological focused design process has identified as a priority to helping the sector minimize environmental impacts and stakeholder conflicts as well as amplifying social benefits (sustainability and resiliency in coastal communities and economies) (Grebe et al., 2019). Maximizing overlap of existing equipment, namely vessels, was prioritized as was minimization of capital outlay needed to acquire and assemble the system as well as minimize or eliminate the need for specialized parts or equipment. The resulting system not only satisfies the factors of safety in design to survive and produce in high energy ocean environments, but is comprised of components easily sourced from an outlet already familiar to commercial fishers; the marine supply store. Moreover, all system components were sized in order to be easily deployable and serviceable from a prototypical Gulf of Maine lobster boat. All components could be assembled and or fabricated on shore and packed efficiently for transport and ease of deployment (Figure 3).
In terms of crop yield the system produced 1546.1 kg wet weight total over a 122 m grow line. peak biomass was 12.67 kg/m (± 0.4 kg), in line with biomass production on kelp farms grown in protected portions of the same Saco Bay region (Grebe et al., 2021). Assuming a 10% biomass loss due to trimming at harvest, at a price point of $1.65/kg wet weight, this would yield the farmer a gross revenue of $2,301. From a standard return on investment analysis over 3 years, at this crop yield and farm gate price, our analysis shows a farmer can see an 8% return on investment over 3 years. However, a more nuanced perspective should be taken when assessing the economics of livelihood augmentation in small scale, seasonal commercial fishers that accounts for the opportunity costs and benefits of engaging in ocean farming as demonstrated by Mazumdar (1989). If one assumes that a seasonal harvester would typically take non-fisheries facing jobs during the off season, the revenue gained vs. labor invested from seaweed farming should be compared against revenues should that individual have worked those hours in a more traditional off-season vocation. In our case, if we assume the farmer would otherwise have worked a job benchmarked to minimum wage (12.75/h), the income would have been $510 over the 40 h worked. Once the initial investment is recovered, an annual return of $1,050/season that already includes wages represents a $13.50 increase in wages/h when compared to the same individual working 40 h at another job at 12.75/h; a significant incentive to farm seaweeds to enhance fishing family livelihoods.
Seaweed farming could have widespread impacts on coastal communities from a socio-economic perspective given the technology is relatively simple and requires a very small initial capital investment. Our seaweed system was intentionally designed to limit barriers to deployment and operability to traditional fishing interests as it could be adopted easily by those with a knowledge of working on the ocean.
Small scale seaweed systems meet the demands of rural fishing communities and regional food markets. Small-scale farmers acquire knowledge and ability to scale up if favorable business models develop and would allow these new entrants to integrate into larger, national, and global markets, creating new value chains and trade. Scaling up inherently increases social, regulatory, and operational complexities and risky, whereas scaling-out allows for multiple adopters and development of cooperatives and regional hubs to consolidate and process products.
The farm system tested is very small, constrained by what is allowable with a single LPA from the state of Maine. However, even at this scale however, the financial analysis suggests a farmer can break even after 3 years utilizing a system that allows migration of farms to more energetic ocean environments using cost efficient, readily available components. Individuals can hold multiple LPAs in Maine or may pursue larger standard leases upon which this same farming system could be employed. Important next steps will be to assess the scalability of this farm design to understand how costs and labor demands scale with increasing farm size (i.e., length). If, for example, the most expensive components of the farm could be held relatively constant (moorings) while increasing the length of the culture line and minimally increasing labor demands then profitability of this farm design becomes increasingly attractive.
Facilitating industry growth at a community scale will require both scaling up of farms, but also scaling out with many small scale farms operating in more exposed nearshore sites. This study highlights the need for engineered approaches to seaweed farm design at scales previously considered too small to be required. This approach should be explored broadly, and beyond Maine not only with kelp farming but for other community scale, low trophic level aquaculture sectors that may benefit from exploring the opportunity for farming nearshore exposed ocean areas.
The raw data supporting the conclusions of this article will be made available by the authors, without undue reservation.
AS-G: conceptualization, resources, methodology, investigation, formal analysis, writing lead-original draft, writing—review, and editing. DF: conceptualization, methodology, investigation, formal analysis, supervision, project administration, funding acquisition, writing-original draft, writing—review, and editing. TD: conceptualization, methodology, software, investigation, formal analysis, writing—original draft, writing—review, and editing. ZM-H: resources, writing-original draft, writing—review, and editing. BC-P: conceptualization, resources, project administration, writing—original draft, writing—review, editing, and funding acquisition. KJ: resources. All authors contributed to the article and approved the submitted version.
Funding for this research was received from the United States Department of Energy Macroalgae Research Inspiring Novel Energy Resources (MARINER) program award #DEAR0000917, from the National Science Foundation Established Program to Stimulate Competitive Research (EPSCoR) award #IIA-1355457 to Maine EPSCoR at the University of Maine subaward to the University of New England (UNE), and by the UNE School of Marine and Environmental Programs.
BC-P is employed by Ecological Aquaculture Foundation LLC. TD is employed by Kelson Marine Co. KJ is employed by Atlantic Sea Farms - Ocean's Approved.
The remaining authors declare that the research was conducted in the absence of any commercial or financial relationships that could be construed as a potential conflict of interest.
All claims expressed in this article are solely those of the authors and do not necessarily represent those of their affiliated organizations, or those of the publisher, the editors and the reviewers. Any product that may be evaluated in this article, or claim that may be made by its manufacturer, is not guaranteed or endorsed by the publisher.
The authors thank Tollef Olsen for assistance with the project in the field and in the lab. The authors appreciate Tim Arienti and Addie Waters for assistance with vessel operation and project coordination. The authors also thank Dan Chadbourne for assisting in permitting, liaising with the local marine community, and vessel support.
ABS (2012). Guidance Notes on the Application of Synthetic Ropes for Offshore Mooring. Drive Spring, TX: American Bureau of Shipping (ABS).
API (2005). API RP 2SK: Recommended Practice for Design and Analysis of Stationkeeping Systems for Floating Structures, 3rd Edn. (with Addendum in 2008). Washington, DC: American Petroleum Institute (API).
ASMFC (2015). American Lobster Benchmark Stock Assessment and Peer Review Reports. Arlington, VA: Atlantic States Marine Fisheries Commission (ASMFC).
Bak, U. G., Gregersen, Ó., and Infante, J. (2020). Technical challenges for offshore cultivation of kelp species: Lessons learned and future directions. Bot. Mar. 63, 341–353. doi: 10.1515/bot-2019-0005
Bak, U. G., Mols-Mortensen, A., and Gregersen, O. (2018). Production method and cost of commercial-scale offshore cultivation of kelp in the Faroe Islands using multiple partial harvesting. Alg. Res. 33, 36–47. doi: 10.1016/j.algal.2018.05.001
Buck, B. H., and Buchholz, C. M. (2004). The offshore-ring: a new system design for the open ocean aquaculture of macroalgae. J. App. Phycol. 16, 355–368. doi: 10.1023/B:JAPH.0000047947.96231.ea
Buck, B. H., and Buchholz, C. M. (2005). Response of offshore cultivated Laminaria saccharina to hydrodynamic forcing in the North Sea. Aquaculture 250, 674–691. doi: 10.1016/j.aquaculture.2005.04.062
Chung, H., Kim, N. G., Choi, K. J., and Woo, H. C. (2015). “Novel ocean system for high density mass production of seaweed biomass in Korea,” in World Congress on Advances in Structural Engineering and Mechanics (ASEM15) (Incheon).
Conkling, M. (2021). Has the LPA System Been Successful? Small-Scale Aquaculture Recruitment in Maine Through the Limited-Purpose Aquaculture (“LPA”) Licensing System. Biddeford, ME: Graduate Program in Ocean Foods Systems, University of New England.
Costa-Pierce, B. A., and Chopin, T. (2021). The hype, fantasies and realities of aquaculture development globally and its new geographies. World Aquacult. 52, 23–35.
Cottier-Cook, E. J., Nagabhatla, N., Badis, Y., Campbell, M. L., Chopin, T., Dai, W., et al. (2016). Safeguarding the Future of the Global Seaweed Aquaculture Industry. United Nations University and Scottish Association for Marine Science Policy Brief. Available online at: http://voices.nationalgeographic. com/files/2016/08/Final-unu-seaweed-aquaculturepolicy-for-printing.pdf (accessed December 3, 2021).
DNV-RP-C25 (2010). Environmental Conditions and Environmental Loads. DET NORSKE VERITAS. Available online at: http://www.dnv.com (accessed December 30, 2021).
Faltinsen, O. M. (1990). Wave loads on offshore structures. Ann. Rev. Fluid Mech. 22, 35–56. doi: 10.1146/annurev.fl.22.010190.000343
FAO (2017). Committee on Fisheries: Sub-Committee on Aquaculture. Thematic Background Study No. 4: Genetic Resources for Farmed Seaweeds. Ninth Session, 24–27th October 2017. Rome: FAO. Available online at: http://www.fao.org/cofi/46056-0e272e19f4b0051d1e1c3b679e5ca8ada.pdf (accessed December 27, 2021).
Filbee-Dexter, K., Feehan, C., and Scheibling, R. (2016). Large-scale degradation of a kelp ecosystem in an ocean warming hotspot. Mar. Ecol. Prog. Ser. 563, 141–152. doi: 10.3354/meps11554
Filbee-Dexter, K., and Wernberg, T. (2018). Rise of Turfs: a new battlefront for globally declining kelp forests. Bioscience 68, 64–76. doi: 10.1093/biosci/bix147
Flavin, K., Flavin, N., and Flahive, B. (2013). Kelp Farming Manual: A Guide to the Processes, Techniques, and Equipment for Farming Kelp in New England Waters. Saco, ME: Ocean Approved LLC. Available online at: https://maineaqua.org/wp-content/uploads/2020/06/OceanApproved_KelpManualLowRez.pdf (accessed November 8 2021).
Fredriksson, D. W., and Beck-Stimpert, J. (2019). Basis-of-Design Technical Guidance for Offshore Aquaculture Installations in the Gulf of Mexico. U.S. Dept. of Commerce, NOAA. NOAA Technical Memorandum. p. 29.
Fredriksson, D. W., Dewhurst, T., Drach, A., Beaver, W., St. Gelais, A. T., Johndrow, K. L., et al. (2020). Hydrodynamic characteristics of a full-scale kelp model for aquaculture applications. Aquacult. Eng. 90, 102086. doi: 10.1016/j.aquaeng.2020.102086
Gershenson, G. (2020). “I'm not a quitter”: lobstermen turn to kelp farming in the face of climate crisis. The Guardian. Available online at: https://www.theguardian.com/environment/2020/may/19/im-not-a-quitter-lobstermen-turn-to-kelp-farming-in-the-face-of-global-crises (accessed October 10 2021).
Goldburg, R. J., Elliott, M. S., Naylor, R. L., and Pew Oceans Commission. (2001). Marine Aquaculture in the United States: Environmental Impacts and Policy Options. Arlington, VA: PEWOC.
Grebe, G. S., Byron, C. J., Brady, D. C., Geisser, A. H., and Brennan, K. D. (2021). The nitrogen bioextraction potential of nearshore Saccharina latissima cultivation and harvest in the Western Gulf of Maine. J. App. Phycol. 33, 1741–1757. doi: 10.1007/s10811-021-02367-6
Grebe, G. S., Byron, C. J., Gelais, A. S., Kotowicz, D. M., and Olsond, T. K. (2019). An ecosystem approach to kelp aquaculture in the Americas and Europe. Aquacult. Rep. 15, 100215. doi: 10.1016/j.aqrep.2019.100215
Harkell, L. (2021). UK fishing industry takes fright over offshore wind energy boom. Undercurrent News. Available online at: https://www.undercurrentnews.com/2021/11/23/uk-fishing-industry-takes-fright-over-offshore-wind-energy-boom/ (accessed November 24 2021).
Harris, K., Tan, E. C., Thomas, V. M., Johnston, J., D'Souza, S., Jones, C. W., et al. (2021). Combined Techno-Economic Analysis and Life Cycle Assessment of an Integrated Direct Air Capture System with Advanced Algal Biofuel Production (No. NREL/PR-5100-81411). Golden, CO: National Renewable Energy Laboratory.
Knapp, G., and Rubino, M. C. (2016). The political economics of marine aquaculture in the United States. Rev. Fish. Sci. Aquacult. 24, 213–229. doi: 10.1080/23308249.2015.1121202
Langan, R., and Buck, B. H. (2017). Aquaculture Perspective of Multi-use Sites in the Open Ocean: The Untapped Potential for Marine Resources in the Anthropocene. Cham: Springer Nature.
Le Bris, A., Mills, K. E., Wahle, R. A., Chen, Y., Alexander, M. A., Allyn, A. J., et al. (2018). Climate vulnerability and resilience in the most valuable North American fishery. Proc. Nat. Acad. Sci. U.S.A. 115, 1831–1836. doi: 10.1073/pnas.1711122115
Love, E. (2016). Shellfish and Seaweed Aquaculture as a Mechanism for Economic Diversification in Maine Island and Coastal Communities. Portland, ME: University of Southern Maine, Muskie School of Public Service, Casco Bay Estuary Partnership.
Masters, G. M., and Ela, W. (2007). Introduction to Environmental Engineering and Science, 3rd Edn. Hoboken, NJ: Prentice Hall. p. 720.
Mazumdar, D. (1989). Microeconomic Issues of Labor Markets in Developing Countries. Washington, DC: World Bank. Available online at: https://hvtc.edu.vn/Portals/0/files/6363406327898546810-8213-1183-2.pdf
ME DMR (2021). Historical Lobster Landings Chart. Maine Department of Marine Resources (ME DMR). Available online at: https://www.maine.gov/dmr/commercial-fishing/landings/documents/lobster.table.pdf (accessed November 10, 2021).
ME DOL (2022). Per State Law, Maine's Minimum Wage to Increase to $12.75 Per Hour in 2022. Maine Department of Labor (ME DOL). Available online at: https://www.maine.gov/labor/news_events/article.shtml?id=5636664 (accessed January 19, 2022).
Morison, J. R., Johnson, J. W., and Schaaf, S. A. (1950). The force exerted by surface waves on piles. J. Pet. Technol. 2, 149–154. doi: 10.2118/950149-G
Naval Facilities Engineering Service Center (2012). “Naval Facilities Engineering Command,” in Handbook for Marine Geotechnical Engineering. Technical, SP-2209-OCN, eds D. Thompson and D. J. Beasley (Port Hueneme, CA: Naval Facilities Engineering Service Center).
Pershing, A. J., Alexander, M. A., Hernandez, C. M., Kerr, L. A., Le Bris, A., Mills, K. E., et al. (2015). Slow adaptation in the face of rapid warming leads to collapse of the Gulf of Maine cod fishery. Science 350, 809–812. doi: 10.1126/science.aac9819
Piconi, P., Veidenheimer, R., and Chase, B. (2020). Edible Seaweed Market Analysis. Available online at: https://www.islandinstitute.org/edible-seaweed-market-analysis/ (accessed January 19, 2022).
Roesijadi, G., Copping, A. E., Huesemann, M. H., Forster, J., and Benemann, J. R. (2008). Techno-Economic Feasibility Analysis of Offshore Seaweed Farming for Bioenergy and Biobased Products. Battelle Pacific Northwest Division Report Number PNWD-3931, 1e115. Seattle: Batelle.
Stead, S. M. (2018). Rethinking marine resource governance for the United Nations sustainable development goals. Curr. Op. Env. Sus. 34, 54–61. doi: 10.1016/j.cosust.2018.12.001
Stephenson, F. (2013). Saving Cedar Key: A Historic Fishing Village is Now Florida's Clam Capital. Available online at: https://explore.research.ufl.edu/saving-cedar-key.html (accessed November 15, 2021).
Stoll, J. S., Beitl, C. M., and Wilson, J. A. (2016). How access to Maine's fisheries has changed over a quarter century: the cumulative effects of licensing on resilience. Glob. Environ. Change 37, 79–91. doi: 10.1016/j.gloenvcha.2016.01.005
Witman, J. D., and Lamb, R. W. (2018). Persistent differences between coastal and offshore kelp forest communities in a warming Gulf of Maine. PLoS ONE 13, e0189388. doi: 10.1371/journal.pone.0189388
Keywords: aquaculture engineering, kelp, seaweed, aquaculture, ocean-food-systems, fisheries diversification
Citation: St-Gelais AT, Fredriksson DW, Dewhurst T, Miller-Hope ZS, Costa-Pierce BA and Johndrow K (2022) Engineering A Low-Cost Kelp Aquaculture System for Community-Scale Seaweed Farming at Nearshore Exposed Sites via User-Focused Design Process. Front. Sustain. Food Syst. 6:848035. doi: 10.3389/fsufs.2022.848035
Received: 03 January 2022; Accepted: 21 January 2022;
Published: 23 February 2022.
Edited by:
Sudhakar Srivastava, Banaras Hindu University, IndiaReviewed by:
Mark Flaherty, University of Victoria, CanadaCopyright © 2022 St-Gelais, Fredriksson, Dewhurst, Miller-Hope, Costa-Pierce and Johndrow. This is an open-access article distributed under the terms of the Creative Commons Attribution License (CC BY). The use, distribution or reproduction in other forums is permitted, provided the original author(s) and the copyright owner(s) are credited and that the original publication in this journal is cited, in accordance with accepted academic practice. No use, distribution or reproduction is permitted which does not comply with these terms.
*Correspondence: Adam T. St-Gelais, YWRhbS5zdEBtYWluZS5lZHU=
†Present address: Adam T. St-Gelais, Aquaculture Research Institute, University of Maine, Orono, ME, United States
Barry Antonio Costa-Pierce, Ecological Aquaculture Foundation LLC, Biddeford, ME, United States
Kathryn Johndrow, Atlantic Sea Farms – Ocean's Approved, Biddeford, ME, United States
Disclaimer: All claims expressed in this article are solely those of the authors and do not necessarily represent those of their affiliated organizations, or those of the publisher, the editors and the reviewers. Any product that may be evaluated in this article or claim that may be made by its manufacturer is not guaranteed or endorsed by the publisher.
Research integrity at Frontiers
Learn more about the work of our research integrity team to safeguard the quality of each article we publish.