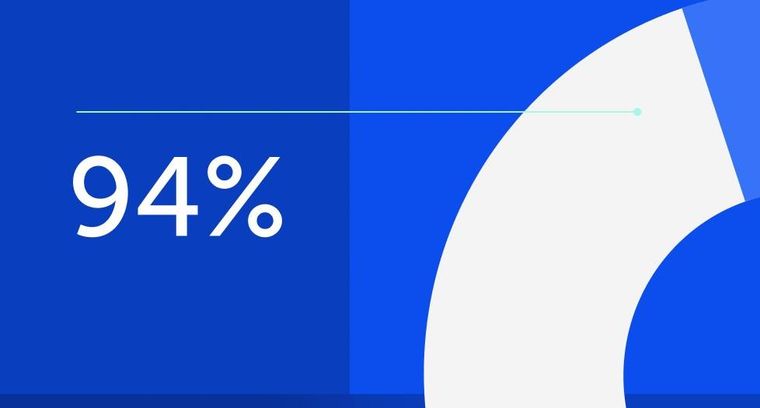
94% of researchers rate our articles as excellent or good
Learn more about the work of our research integrity team to safeguard the quality of each article we publish.
Find out more
REVIEW article
Front. Mech. Eng., 14 October 2020
Sec. Tribology
Volume 6 - 2020 | https://doi.org/10.3389/fmech.2020.571464
This article is part of the Research TopicFluids and Greases for Electrified VehiclesView all 6 articles
Electric and hybrid vehicles are gaining increasing attention in recent years. The distinguished difference between electric/hybrid vehicles from conventional ones is the intermittent on-and-off control of the internal combustion engine, whereas the electric vehicles operate on electrical motors. This difference creates new requirements in lubricants with performance characteristics that are otherwise uncritical: electrical properties (such as electrical conductivity and breakdown voltage) and thermal properties (thermal conductivity, specific heat, among others), in addition to fluidic performance that we have studied for decades. In this review, we discuss about lubricants for electric and hybrid vehicles in the following aspects. Starting with a brief historic review, we gathered information about current needs and challenges in electric and hybrid vehicles. We then compared the properties of lubricants, followed by the performance difference of those vehicles in terms of frictional performance, thermal management, and dielectric breakdown. Performance parameters are critically dependent on the properties of lubricants that are crucial for energy efficiency and reliability. This review can be used as a guidance for the future design of advanced lubricants for electric and hybrid vehicles.
Electric vehicle (EV) was first conceptualized in the early nineteenth century and commercial EVs came out in the late nineteenth century (He et al., 2020). The arrival of the Toyota Prius in 1997 was a milestone in the development of hybrid vehicles (HEVs) (Chau and Chan, 2007). The number of EVs/HEVs has continued to increase since (API, 2015; Becker, 2019). Reports have predicted continued increase in sales of electric cars globally (Andrew, 2019; Duncan, 2019). The historical timeline of main events leading to the research and development in EV/HEV is shown in Figure 1.
Depending upon the make, EVs can be of different types: battery, hybrid, plug-in hybrid, fuel cell battery, and solar electric vehicles (He et al., 2020). HEVs come in several designs: (1) classification based on electrical and mechanical power flows: series, parallel, series-parallel, or complex hybrids; (2) classification based on power levels and operation: full, micro, and mild hybrids (Chau and Chan, 2007). In the HEV, one unique feature is that it can shut off the IC engine when the vehicle has sufficient power to run from only the electric motors. This leads to more cooling of the IC engine and frequent starts and stops (Clarke, 2014).
The operating cost of an EV is estimated to be 2 cents/mile whereas for an ICE vehicle, it is about 12 cents/mile (Farfan-Cabrera, 2019). Also, an EV uses about 77% of grid energy compared with just 21.5% energy use from fuel for an ICEV (Farfan-Cabrera, 2019). Environmental protection, resource utilization, and customer satisfaction are the key drivers for innovation in EV/HEV lubrication. High fuel efficiency, low greenhouse and CO, NOx emissions, and high mileage are some key performance indicators of future design (Korcek et al., 2000). Plug-in hybrid vehicles (PHEVs) have demonstrated the advantages of sustainability over conventional ICE vehicles (Bradley and Frank, 2009).
The increasing subsidies for sustainable automotive technologies, across the globe, have provided impetus to the R&D of electric vehicles (EVs) and hybrid electric vehicles (HEVs). Nevertheless, state-of-the-art EV/HEV technology is still immature. Table 1 presents a comparative assessment of the conventional internal combustion engine (ICE) vehicles and the EV/HEV considering several key aspects.
Due to the aforementioned advantages, there has been a surge in research publications about EV/HEV (Figure 2A) and EV/HEV lubricants (Figure 2B).
Figure 2. The number of research publications and patents year wise for (A) EV/HEV and (B) EV/HEV lubricants. The x-axis shows the years. Data were collected through Google Scholar.
The outstanding challenges in EV technology include, for example, driving range before charging, time of charging, cost, and accessibility of charging (Van Rensselar, 2019). The major concerns in wider scale commercialization of EV/HEV are cost, vehicle efficiency, maintenance, component reliability, availability, and customer satisfaction. There is no standardized test for assessing noise in EV/HEVs (Andrew, 2019). In EV, the battery costs about 45.3% of the total cost. The current energy density of a battery to fossil fuel is 1:80. Hence, battery energy density and life are among the bottlenecks for EV technology (Van Rensselar, 2019). Other challenges lie in the area of development of advanced charging technology, supercapacitors, thermoelectric generators, regenerative braking, and photovoltaic cells, among others (Farfan-Cabrera, 2019).
In aspects of mechanical performance, the EV/HEV technology presents several tribological challenges. The failure of bearings that may account for almost 40% failures in motors in EV/HEV can be a major concern due to complex voltages in shafts and bearing currents. Premature bearing failures are accompanied by undesirable noise, vibration, and instability (He et al., 2020). A generalized solution to EV/HEV lubrication can be challenging because of a highly diverse bearing current range and design (He et al., 2020). Conventional solutions to friction and wear may also not be feasible in EV/HEV. For instance, the use of present-day friction modifiers like molybdenum dialkydithiocarbamates results in loss in effectiveness over miles accumulation (Korcek et al., 2000). Hence, new strategies and solutions are needed to improve tribology performance.
Lubricants play important roles in vehicles. Recent progress in lubrication has been reported in areas such as bio-lubricants, mineral oil-based lubricants, nanoparticle additives, and carbon nanotube–based lubricants, among others (Rensselar, 2010; Tang et al., 2013; Zin et al., 2016; Syahir et al., 2017; Dassenoy, 2019; Narita and Takekawa, 2019). The research efforts on lubricants have been of obtaining higher resistance to copper corrosion and compatibility with polymers employed in the electronic components of EV/HEV (Lin et al., 2011; Hunt et al., 2017). This involves the design of new standard test methods to measure properties in EVs (Hunt, 2017). Obtaining low viscosity and improvement of electric and thermal properties are other key areas of focus (Lou and Sabhapathy, 2004; Tazume, 2016). The most successful approaches have been the use of nanotechnology-based anti-wear and friction lubricants, vapor phase lubrication, ionic liquids, and low-viscosity oils (Farfan-Cabrera, 2019). Electric discharge, bearing currents, instability of lubricants, and common mode voltages are other topics of research interest (Willwerth and Roman, 2013; Xie et al., 2013; Romanenko et al., 2015, 2016; Gao et al., 2018a). Research on viscosity of EV lubricant is of high importance. Gupta et al. reported a 17% increase in engine efficiency in EV mode for a low-viscosity oil compared with factory transmission oil (Gupta, 2012). In EV, the importance of grease cannot be overlooked. In grease use, nanotechnology, synthetic base oils, and thickeners have demonstrated enhanced lubricity, higher service life, and low friction torque (Cann, 2007; Chen et al., 2019b). Lithium grease has shown to impart the advantages of high adherence, non-corrosiveness, and moisture resistance making them compatible with several applications (Cann, 2007). Aluminum and urea greases perform well too; however, their production is associated with hazardous processing and constraints on process balance (Andrew, 2019). There have been attempts to find green solutions to the lubrication problem. With low volatile organic compounds (VOCs), low compressibility, high dielectric strength, and good emulsifiability, bio-based lubricants have shown promise as alternatives to conventional oils. With chemical modifications (for high thermal stability and oxidative stability) and the use of suitable additives for load-bearing and friction properties, they can perform better than conventional lubricants (Syahir et al., 2017). Bio-inspired designs are also used to improve efficiency. Nakanishi et al. proposed a bio-inspired oil seal that mimicked articular cartilage and had a comparatively lower frictional torque compared with traditional oil seals (Nakanishi et al., 2016). The transmission fluid in HEV contains dispersants and needs to have insulating properties (low electrical conductivity) to avoid short-circuiting of motor parts. Tang et al. treated the dispersants in transmission fluid with phosphorus (P) and boron (B) to improve anti-wear and anti-friction properties. They reported that (B+P)/N ratios of 0.1 to about 0.8:1.0 were effective in achieving low electrical conductivities to the tune of 1,700 pS/m. A hybrid vehicle transmission fluid made of mineral oil type was formulated with optimal dispersant/detergent ratio that helped in attaining good anti-rust property and low electrical conductivity (Tang et al., 2013). Wheel bearings in EVs are important targets for improving efficiency. The high torque in the wheel bearings of an EV need to be well controlled. The grease used need to perform consistently at elevated temperature fluctuations. Commonly used test specifications for wheel bearing lubrication is provided in Table 2.
Table 2. Selected test specifications relevant to wheel bearing lubrication in electric vehicles (Andrew, 2019).
For enhancing the performance and efficiency of the vehicle, it is necessary that all the components involved in the power generation process should be optimized. Therefore, the study of the lubricants is of fundamental importance. In a conventional IC engine vehicle, the lubricants used are engine oil, transmission fluids, and grease. The engine oil provides hydrodynamic lubrication to the engine, wear protection in metal-to-metal contact, cooling for internal engine parts along with many other performance enhancement and protective functions (Passut, 2013). Be it automatic stepped transmission (AT), continuously variable transmission (CVT), or the dual-clutch transmission (DCT), the transmission fluid has the same broad purpose, that is, to create hydraulic pressure, dissipate heat, and protect the metal gears and other parts from wear (Beckman, 2019). The main role of grease in an automotive is to reduce frictional losses by lubricating bearings, i.e., most of the moving parts of the assembly (Rawat and Harsha, 2019). But along with the developments in automobile industries, the lubricants need to perform in harsh conditions and provide various performance and compatibility aspects (Soni and Singh Prajapati, 2017). Table 3 provides a summary of various lubricants used in IC engine vehicles (ICEVs), hybrid or plug-in hybrid vehicles (HEVs/PHEVs), and electric vehicles (EVs).
The HEV has an electric motor alongside the combustion engine. Its combustion engine is smaller in size compared with the ICE vehicles of corresponding sizes. As represented by Figure 3 (Kendall, 2008), the size of the ICE engine becomes smaller and that of the electric batteries grows as the vehicle approaches the EV. The DCT mechanism has the most efficient transmission technology in terms of mechanical efficiency. Therefore, most HEVs in the market have DCT modular transmission (Gahagan, 2017). In these types of vehicles, the e-motor is directly integrated with the DCT box and is cooled by transmission lubricant. Because the lubricating fluid is in contact with the electrical components, it is highly important that it has superior electric properties like electrical conductivity, dielectric constant, and dielectric strength (Narita and Takekawa, 2019).
Figure 3. (A) The illustration of electric drivetrains in comparison of the battery and IC engine sizes. (B) A representation of major components in EV, HEV, and ICEV where lubricants are applied (B sources: top—Tesla; middle—Volkswagen netcarshow; bottom—Subaru Forester showroom).
There is no combustion engine in the EV. The core jobs of lubricants remain the same. With the advancements of e-mobility technologies, those lubricants must play a major role in electrical compatibility, thermal management, and material adaptability. It is also expected in the near future that the EV transmissions and axles will accommodate an electric motor in the unit housing (Beyer et al., 2019). In this case, the presence of electric motor windings in the transmission would add up more copper in contact with the lubricants and therefore more copper corrosion problems will arise (Beyer et al., 2019). The large amount of heat produced at the motor windings will test the heat transfer ability of the lubricant as well as its thermal stability. To sustain these high temperatures, the need for use of new alloys and polymers (Davis, 2008) for manufacturing vehicle components is expected, which may give rise to new compatibility concerns (Beyer et al., 2019).
Several state-of-the-art EV/HEV lubrication systems have been reported recently. Gahagan reported that a DCT has advantages of higher energy efficiency and vehicle weight reduction over other transmission types viz. AT and CVT (Gahagan, 2017). This is so because a DCT does not have any torque converter loss and does not require components like high-pressure oil supplies. DCT-compatible lubricant was also developed in their work and its electrical conductivity and dielectric strength were characterized (Gahagan, 2017). In one energy efficiency simulation work of the EV driveline, Tehrani et al. found that using a single reduction for the gear was the optimal strategy. The simulation considered losses from the gearbox, electric motor, and power electronic device efficiencies and the gear ratio (Tehrani et al., 2016). Leach and Pearson reported that the HEV engine design and controls impacted the crankcase lubricants and that the lubricant temperature could be considerably lower compared with a conventional vehicle (Leach and Pearson, 2014).
Several energy-efficient systems for EV/HEV have been reported recently. Chau and Chan described some key energy-efficient systems that are gaining popularity for hybrid vehicles for high energy efficiency, for example, a recovery system for thermoelectric waste heat and generating electricity with it for HEV, electronically powered continuous variable transmission (E-CVT), and starter-generator in an integrated design that enables cold cranking and charging of batteries thus eliminating the need for flywheels and transmission belts (Chau and Chan, 2007).
The E-CVT system stands out with multiple benefits (Sasaki, 1998; Miller and Everett, 2005; Miller, 2006). Those include higher reliability due to mechanical simplicity; high transmission and engine efficiency due to absence of torque converters, shift gears, and clutch leading to overall size reduction; idle-stop features stops the engine completely when the vehicle is stopped whereas the electric launch feature provides all the torque to start a vehicle from stop; and regenerative braking during downhill motion of the vehicle and throttle acceleration at full capacity in which the engine is complemented by the motor to provide full power to the vehicle. For a diesel engine being optimized for hybrid vehicle applications, Yusaf reported that the brake-specific fuel consumption was the least (<300 g/kWh) at 1 kW charge load and speed of 1,900–2,700 rpm. Oxides of nitrogen (NOx) emissions were reported to be within acceptable limits (<180 ppm) with 2,500 rpm as the optimal speed for the least emission (Yusaf, 2009). Elgowainy et al. incorporated the economy of fuel and the use of electricity into a Powertrain System Analysis Toolkit simulation for PHEVs (Elgowainy et al., 2009). The focus was on understanding the use of energy and greenhouse emissions for PHEVs right from oil wells to the time of operation (wells-to-wheels or WTW). They reported that PHEVs had reduced fuel use than the HEVs. Also, the WTW was strongly impacted by the fuel type, economy of the fuel, and the type of generation of electricity. Lim and Kim designed an oil spray system for an electric vehicle for its in-wheel motors and used numerical simulation to optimize the shape of the hollow shaft for efficient delivery. The designed oil spray system showed improved performance than the existing ones (Lim and Kim, 2014). A fast approach to identify thermal behavior of incorporated electrical drives was used by Paar et al. The approach used simple yet effective strategy to predict machine losses which can be a useful aid in EV/HEV thermal management and design (Paar et al., 2015).
The main component of a lubricant is base oil (BO). Almost all the lubricants first started as BOs, and as the time passed by, different additives have been added to them to improve performance and/or save energy. It is believed that BOs and their viscosities are important factors for cooling performance, whereas additives play a critical role in the electrical conductivity of the EV. However, it is also observed that additives may have a little effect on cooling performance as well (Kwak et al., 2019).
Lubricants in EV need to have higher electrical insulation to prevent arcing as they are going to be directly in contact with the e-motor and/or other electrical components of the automobile. The operating conditions for EV are tough and may find high temperatures, more oxidation, and abrasion of particles. To sustain under these conditions, the lubricants should have stable dielectric properties throughout. Also, the lubricant comes in close contact with types of materials and that may lead to breakage, swelling, cracking, etc. of the components. Most of these components are made of copper due to its high electrical conductivity. Therefore, it is very much important that the lubricant should have excellent copper compatibility. There is a range of operating temperatures for the electric engine and other power electronics components where they are most efficient and durable. It is the lubricants' job to provide a first-rate heat evacuation for temperatures as high as 180°C (Bouvy et al., 2012). The higher torque in EV vehicles could cause wear issues that were unprecedented in the IC engine vehicles (Heap et al., 2011).
BO is manufactured from crude oil or chemically derived from synthetic materials. The American Petroleum Institute (API) categorizes BOs into five groups (API, 2015) based on their manufacturing techniques, sulfur content, saturate level, and viscosity index. Table 4 sums up all the five groups and their characteristics. The first three groups are refined from petroleum crude oil. Group IV BOs are totally synthetic (polyalphaolefin, PAO) oils. All the other BOs that do not fall in groups I through IV are included in group V. They mostly contain silicone, diester, polyolester, phosphate ester, alkylated benzene, etc. Basically, if it is a synthetic BO and it is not a PAO, it is a group V BO. The first three group BOs differ mainly in their manufacturing processes from the refined petroleum oil.
In general, the thermal stability of the BO groups improves with the increasing group number. In majority cases, the group V BOs are used for creating lubricant additives. Commercially, groups II and III BOs are used abundantly (Casserly et al., 2018). Saturated molecules remain stable for longer durations; therefore, the higher the number of saturates, the higher the molecular bond strength and better resistance to loss of viscosity. The petroleum BOs contain far fewer saturated molecules compared with the synthetic ones creating more durable lubricants. Also, the higher the viscosity index (VI), the more stable the viscosity is with changes in temperature. The viscosity index of groups IV and V is much higher than the crude oil BOs (Hope, 2018). It has been found out that the BOs with higher thermal conductivities, specific heat capacities, and densities provide better cooling. The cooling performance also depends on the molecular structure of the BO. The longer chains of molecules providing better cooling (Kwak et al., 2019).
Additives perform three roles in any lubricant: (1) enhance the desirable properties of the base oil, (2) suppress the undesirable ones, and (3) add new properties to the lubricant that improves its overall qualities (Sniderman, 2017). With the increasing demand for higher fuel efficiencies and cleaner fuel residues, the newer engines are more complex with many components and novel materials and alloys. The transmissions in hybrid and electric vehicles are more compact and require handling of higher speeds and greater torque. Along with these, the lubricants are required to lower viscosities and longer drain intervals (Guegan et al., 2019; Tsui, 2019).
To summarize the roles and requirements of lubricants in various vehicles, Table 5 lists the commonly used additives. Most of the additives perform a primary function, but apart from that, they also have secondary properties that enhance overall lubricant performance.
The requirement of tribological performance in EV/HEV is expected to be different from that in ICE vehicles. For EVs, a lubricant's thermal and electrical property, copper corrosion, and compatibility with elastomers/polymers of EV/HEV are among the most important concerns (Clarke, 2014; Van Rensselar, 2019). Proper lubrication at above 25,000 rpm speeds will be important for friction and wear protection of seals, bearings, and gears. The use of advanced materials in batteries and motors will make it necessary to formulate new lubricants that are compatible with those materials (Becker, 2019). This is so because lubricants would be in contact with motors and batteries. The incompatibility of the lubricants with the explosive electrolytes of the batteries and the motor parts could be dangerous and hazardous. The use of low-viscosity lubricants will also be necessitated by the aim to achieve higher heat transfer (Narita and Takekawa, 2019). Table 6 summarizes the key parameters required for EV and compares it with ICE vehicles. Each lubricant parameter in the second column of Table 6 is important to specific lubrication type(s) of Figure 3 (section Lubricants and Their Uses in Vehicles). The last column in Table 6 specifies all such lubrication types as pointed out in Figure 3.
Lubricants used in EVs and HEVs endure the current flow through the lubricated bearings while protecting the contacting surfaces. This current will occur on lubricated surfaces that electrically connected to the electric motor (Busse et al., 1997; Tischmacher et al., 2010; Di Piazza et al., 2011; Hadden et al., 2016). The lubricant with poor electric properties may cause ED (electric discharge) damage (Wang and Wang, 2008; Gunderson et al., 2011). To achieve such protection, it is essential to choose the lubricant with proper electric resistance and lubricant dielectric strength throughout the lubricant lifetime. The proper electric impedance and dielectric strength can be achieved with changing the BO (Sangoro et al., 2008; Somers et al., 2013) or using additives (Flores-Torres et al., 2018a,b,c; Gao et al., 2018a).
To avoid electric damages, having a low electric resistance is more important than having a high dielectric constant. The dielectric breakdown voltage of neat non-polar BOs such as PAO and mineral oil is in the range of 10 kV, orders of magnitude higher than the voltage applied across motor bearings (Wang and Wang, 2008; Tischmacher et al., 2010; Gunderson et al., 2011). However, dielectric breakdown voltage of oils drastically decreased when they contain impurities such as water or lubricant additives (Wang and Wang, 2008; Gunderson et al., 2011). The bearing electric wear test indicated that the ED damage could occur at the bearing voltage as low as 100 V (Tischmacher et al., 2010; Willwerth and Roman, 2013). The dielectric breakdown voltage of non-conductive grease can even decrease to a few volts when the tests were running for a long time (Jeschke and Hirsch, 2014; Jeschke et al., 2015). Thus, it is unrealistic to expect that high dielectric strength alone can prevent ED damage.
Certain BOs have low electric conductivity. Using ionic liquid as a neat lubricant would provide low conductivity, low coefficient of friction, and high wear resistance (Sangoro et al., 2008; Somers et al., 2013). However, it may cause the tribo-corrosive effect when the bearing current is high.
The conductivity of a lubricant can also be modified by adding additives into the BO. Common additives that affect lubricant conductivity are summarized in Table 7. Some substances with polar molecules such as phospholipid and calcium salicylates can reduce the conductivity of the lubricant (Flores-Torres et al., 2018a,b,c; Gao et al., 2018a). Ionic liquid as a lubricant additive can effectively increase the wear resistance and lower the conductivity of the lubricant (Flores-Torres et al., 2018a,b,c). However, its high cost prevents wide adoption.
Furthermore, it is important to test the electric damages experimentally. Even though there are practical solutions to control the electric conductivity, the knowledge of how those additives function was still lacking. In some cases, adding additives can increase the electric damages, causing more wear on the bearing surface (Xie et al., 2013). Only experiment can determine if an additive is effective in controlling the electric damage.
Tests on the lubricant electric damage can be performed on the motor or in laboratory-controlled conditions. The lubricant property can be measured in a controlled environment with a modified tribometer (Jablonka et al., 2013; Chen and Liang, 2019). To test the performance of a lubricant in real life conditions, motor bearings powered with inverter can be tested in simulated rigs. The bearing current and wear can be directly measured (Noguchi et al., 2010; Hobelsberger and Posedel, 2013; Chatterton et al., 2016; Suzumura, 2016) with a simulated setup. In those experiments, a voltage that simulates the voltage from an inverter was applied though the bearing to simulate the working conditions inside EV/HEV. The experiment can also be performed on the actual motors inside an EV/HEV. By using the inductive measurement on the electric motors, the so-called hardware in the loop (HiL) setup provides more accurate measurement and can integrate into EV/HEV systems (Jeschke and Hirsch, 2014; Jeschke et al., 2015; Xie et al., 2016).
A highly fluctuating charged environment requires specially tailored lubricants to avoid component damage and premature failure caused by improper lubrication. Some failure mechanisms explored are degradation, microbubble formation, and electrowetting. In terms of degradation, the BO and thickeners undergo chemical oxidation to form carboxyl compounds (Yu and Yang, 2011). Lubricity is lost on account of the formation of highly viscous and acidic degradation products and agglomeration of additives (Romanenko et al., 2016). Heat generation causes faster BO evaporation. Luo et al. first discovered the phenomenon of microbubble formation in charged lubricant (Luo et al., 2006). Local overheating under charged conditions causes the microbubble formation around the lubricated contact (Xie et al., 2008a,b). When these microbubbles move outward from the contact, they have a tendency to coalesce. Not only the lubricant having microbubbles is susceptible to electrical breakdown but also to destabilization (Xie et al., 2008b). AC frequency and electrode insulation also affect the microbubble formation. A model for microbubble formation has been reported recently (Xie et al., 2009a). Microbubble formation can sometimes lead to large bubble size. Local pressure gradient and viscous drag may move these large bubbles away from the surface. Dielectrophoretic forces which are the forces experienced by the microbubble as a result of an external electric field may also cause these bubbles to move away from the point of generation. In terms of electrowetting, the electric field induces interfacial stress on a non-polar lubricant confined between two metallic surfaces (McHale et al., 2019). This leads to the spread and breakdown of the lubricant when the electrostatic stress is too high (Mugele and Baret, 2005). Due to differing dielectric properties, a two-phase dispersion of lubricant may also destabilize (He et al., 2020).
There has been fundamental research to understand and tune lubrication under the electric field. Phenomena of interest are electrostatic interaction, charge distribution, the formation of transfer film/structural change, and chemical–physical property changes (Xie et al., 2009b; Drummond, 2012). It has been found that lubrication is aided by weak electrostatic interactions (Kolodziejczyk et al., 2007; Fan and Wang, 2014). Static charges and the transient polarized charges on surfaces, which may be induced and strengthened by the externally applied field, enhance electrostatic interactions (Goto, 1995; Yang et al., 2017; Jiang et al., 2018). At low potentials, wear is adhesive type dominated whereas it is abrasive type dominated when the potential is high. DC has been observed to enhance friction while the friction is reduced by AC. This is due to vibration induced by the electrostatic force which is fluctuating. Structural change/oxidative transfer film formation in a certain material combinations, e.g., graphite–graphite and graphite–copper, has been found responsible for increased wear and reduced friction under the application of the external electric field (Lavielle, 1994; Csapo et al., 1996). Chemical reactions and physical absorption occur at material interfaces under the influence of an external electric field leading to a change in surface friction and lubrication behavior (Sweeney et al., 2012; Romanenko et al., 2016). Carrier (electron-hole) charge distribution through the formation of localized quantum dots and electron-hole recombination affect interfacial mobility and surface friction properties (He et al., 2020).
The BO's molecular structure determines the thermal capacity and thermal conductivity of a lubricant (Pettersson, 2007). The molecular structure of the BO determines how many “quantum states” it can have, e.g., how many ways it can freely rotate or vibrate. The higher the number of the rotational and vibrational quantum state, the higher the thermal capacity (Callen, 1998). When there are high numbers of vibrational and rotational states, it takes higher energy input to raise the averaged kinetic energy, e.g., the temperature. The thermal conductivity of BO was correlated to the molecular diffusivity in the fluid (Gedde, 1995). The easier the molecules of a lubricant pass through each other, the higher the lubricant thermal conductivity. This also means that there is a relationship between the lubricant viscosity and lubricant thermal properties because both the molecular quantum state density and the diffusivity closely correlated to the lubricant viscosity. This correlation can restrict the selection of the lubricant when both the tribological working condition and thermal management are considered. When tribological working conditions take a higher priority, it is difficult to change the BO thermal properties. Thus, it is desirable to change the lubricant thermal property with some additives.
Adding nanoparticle to the lubricant can significantly increase the thermal conductivity and thermal capacity of a lubricant (Shaikh et al., 2007; Jin et al., 2014). Essentially, adding those dispersed nanoparticles increased the carriers of thermal energies. Adding 0.8 vol.% of silica nanoparticles can double the thermal conductivity of a lubricant (Shaikh et al., 2007). The PAO containing 0.5 vol.% of carbon nanotube has more than 50% of thermal conductivity compared with the neat PAO. However, the nanoparticle also lowers the specific heat of the lubricant (Barbés et al., 2013). This additive can be used to optimize the thermal property of lubricant to fit any specific powertrain cooling design. Moreover, the nanoparticle additive improves the tribological performance of lubricants (Dai et al., 2016; Chen et al., 2019a). The experimental evidence that this method works in EV/HEV lubricant was still lacking, but there are potentials.
The most common experimental method for measuring the thermal conductivity of a lubricant was called the transient hot-wire method (Nagasaka and Nagashima, 1981; Håkansson et al., 1988). This method is illustrated in Figure 4A. The transient hot-wire experimental setup was simple to perform and has high accuracy. This method used a Pt or Ni wire which was sealed inside a cylindrical pressure vessel filled with lubricant. The wire was heated up for a short amount of time electrically, and its temperature was monitored simultaneously by its electric resistance. The thermal conductivity and the thermal capacity of the lubricant can be calculated from the temperature change of the wire. Essentially, this measurement setup can be modeled as an axisymmetric thermal transportation problem (Håkansson et al., 1988). It has an additional advantage when used to characterize lubricants, as the lubricant thermal properties are highly correlated with its pressure, and the pressurized transient hot-wire method is relatively easy to achieve.
Figure 4. Measurement of lubricant thermal properties with (A) transient hot-wire method and (B) laser flash method. The yellow color indicates lubricant, and the red is the heat source.
For small quantity lubricant measurement, a laser flash method can be used for measuring the thermal diffusivity (Tada et al., 1978; Vozár and Hohenauer, 2004; Shaikh et al., 2007). This measurement system is illustrated in Figure 4B. This system used a laser to heat up the lubricant and optically measure the temperature change (Vozár and Hohenauer, 2004). Instead of an axisymmetric rod, this method models the system as an infinite sized slab. The laser heats up an infinitely thin layer of lubricant, and the temperature change thus can be fitted with a function of thermal diffusivity and thermal capacity (Vozár and Hohenauer, 2004). This method has an advantage when used for small batch experiments as it only requires a tiny amount of lubricant.
In summary, testing a lubricant's thermal property requires a controlled heat source and an accurate temperature monitoring system. The system accuracy and precision depended on a simple and easy-to-model measurement setup. Both transient hot-wire method and laser flash method used the thermal transportation equations with reduced dimensions. The laser flash method has an advantage to testing small-quantity lubricant.
Lubricants play important roles in various components in vehicles. The overall performance of vehicles, in particular, is influenced by lubricants. To evaluate such effects, while no report has been found in such scope of comparison, we analyzed the frictional performance of the transmission fluid of vehicles with our own understanding. It is understood that EVs have an electric motor that has a higher acceleration rate than mechanical ones. Such a lubricant endures high shear rate in EVs than otherwise. It is assumed that vehicles considered were fully lubricated. The frictional behavior of two scenarios by EV and ICE, respectively, are thus estimated and plotted in Figure 5. Here, we use ICE as reference and EV for comparison. We used the widely accepted Stribeck curve as the performance parameter. Figure 5A is the estimated coefficient of friction (CoF) against time. The blue color is ICE and red is for EV. Figure 5B is the plotted Stribeck curve with the Sommerfeld number (Sommerfeld number is ηV/P, where η = fluid viscosity, V = speed, P = load). It should be noted that it is the best assumed scenario for EV: assume the hydrodynamic lubrication regime was achieved and the friction coefficient was as low as that in the ICE vehicle. The figures have been obtained based on data from several published reports regarding the behavior of Stribeck curve for lubricants. The following boundary conditions are used: initially (time = 0), the lubricants have a finite CoF. The CoF falls gradually to a minimum value with the progression of time. After a certain time interval in the hydrodynamic lubrication regime, the CoF rises from its minimum value and tends to be higher. Each letter denotes a point. The smaller letters refer to the EV lubricants whereas the capital letters refer to the ICE vehicle lubricants. BDL, ML, and HDL refer to boundary lubrication, mixed lubrication, and hydrodynamic lubrication regimes, respectively, in the case of ICE vehicle lubricants. Similarly, bdl, ml, and hdl refer to boundary lubrication, mixed lubrication, and hydrodynamic lubrication regimes, respectively, in the case of EV lubricants. The parameter λ, where λ = t/r, t = film thickness and r = surface roughness, determines the lubrication regimes.
Figure 5. A qualitative comparison of the frictional performance of EV and ICE. (A) is the COF against time and (B) the standard Stribeck curve plotted against Sommerfeld number. BDL, ML, and HDL refer to boundary lubrication, mixed lubrication, and hydrodynamic lubrication regimes, respectively. Small letters in the legend are provided for EV and capital letters for ICE. Each letter denotes a point. The parameter λ, where λ = t/r, t = film thickness and r = surface roughness, determines the lubrication regimes. Sommerfeld number is ηV/P, where η = fluid viscosity, V = speed, P = load.
In an EV, the tribological environment around the bearings, for the same lubricant, is different than those in an ICE vehicle. The EV lubricant will be of lighter and low-viscosity oils (as listed in Table 6). This is because the high load-bearing function of the lubricant (as in an ICE vehicle) would be replaced by mainly torque transferring function (Van Rensselar, 2019). The bearing lubricant in an EV would be exposed to high speeds, high temperatures, and highly fluctuating electric and magnetic fields.
In an EV, the electric motor imparts a high starting torque (Van Rensselar, 2019). This results in a faster attainment of a high entrainment speed by the EV lubricant compared with an ICE lubricant where the speed increase is gradual. Thus, in an EV, in the time scale (Figure 5A), the boundary lubrication layer (bdl) and the mixed lubrication (ml) regimes appear faster than those in ICE (BDL and ML correspondingly). Also, the elongation period (rs) proceeds for a longer time before a steep rise (st). The “rs” part of the curve represents the zone where the lubricant does not undergo any degradation and the CoF is more or less the same. In EV, a lighter viscosity oil with a heat transfer coefficient will lead to higher cooling rates. Thus, at lower speeds where the thermal loading would be less, the lubricant would be able to mitigate the heat because of its higher cooling tendency. Only at high speeds, which happens after a longer time, the effects of thermal and electrical degradation will kick in. At high speeds, the high thermal loading combined with the effects of high fluctuating electric fields on the oil will lead to the onset of lubricant degradation (point “s”). In ICE, on the contrary, such a lubricant degradation happens quite fast due to a heavy mechanical load in addition to thermal loading and a high-viscosity oil with lower heat transfer coefficient. As such, point “C” appears before “s” in Figure 5A. The rs portion is dotted to show that the COF in this region can fluctuate higher or lower than that of an ICE vehicle. Thus, lubricant designers need to thoroughly consider several key aspects in EV lubricant design: viscosity, thermal and electrical environment, friction loss, lubrication regime, contact load, and bearing type, among potential others.
Accordingly, there are several aspects of the Stribeck curve (Figure 5B) that come into light for a lubricant used in an EV (curve pqrst) transmission when compared with use in an ICE vehicle transmission (curve ABCD).
1) EV transmission would preferably use a lubricant with low viscosity (Van Rensselar, 2019). At the start (time = 0), due to the low viscosity of lubricant, there would be more metal–metal contact compared with ICE transmission (which uses a higher viscosity oil) (Allen and Drauglis, 1969). Due to a higher metal–metal contact, the initial COF would be higher in case of EV (Zhang, 2006). This would result in a similar or somewhat higher initial CoF at the start (point p) compared with that in an ICE (point A), i.e., p either overlaps with A or it is somewhat higher than A.
2) The Sommerfeld number is given as ηV/P, where η = fluid viscosity, V = speed, P = load. Increase in fluid speed (V) leads to an increase in the Sommerfeld number (left to right on the x-axis in Figure 5B). Lubrication regime transition parameter “λ” is defined as the ratio of film thickness to the surface roughness (λ = t/r, t = film thickness, r = surface roughness; for BDL, λ < 1.2; for ML: 1.2 < λ <3; for HDL: λ > 3) (Chong and Cruz, 2014). Because the lubricant in EV would be of a lower viscosity than that in ICE vehicle, the initial film thickness (t) would be lower in EV than in ICE (i.e., tEV < tICE). This is because the fluid thickness is directly proportional to fluid viscosity (Guangteng and Spikes, 1996). Hence, this would imply that λEV < λICE. Thus, to reach a value of 1.2 (which is the value for regime transition from bdl to ml), a higher corresponding increase in Sommerfeld number (and therefore speed, V) would be necessitated for an EV lubricant compared with an ICE lubricant. In other words, speed increment (ΔV) required would be more in EV lubricant to reach to the mixed layer (“ml”) lubrication regime transition (i.e., ΔVEV > ΔVICE). This would then result in a longer boundary layer regime (bdl) compared with that in an ICE (BDL).
3) The mixed lubrication regime is indicated by region ML for ICE lubricant and ml for the EV lubricant. Slopes of the curves qr (for the EV lubricant) and BC (for the ICE lubricant) are of interest. For the same reasons as in point 2 earlier, the speed increment (ΔV) required would be more in EV lubricant to reach to the hydrodynamic layer (“hdl”) lubrication regime transition (i.e., ΔVEV > ΔVICE). This would lead to a gentler slope of qr compared with BC. In addition, the EV lubricant would have high thermal load as a result of large currents and fluctuating electric and magnetic fields. Under such conditions, recent reports have shown that for a higher lubricant temperature, the rate of decline of CoF is slower, as indicated by a gentler slope of qr compared with that of BC (Lu et al., 2006; Nikolic et al., 2018).
4) In the hydrodynamic lubrication regime, a consistently high film thickness at very high speeds in EV prohibits metal–metal contact for the EV lubricant. This delays the rise of CoF because of thermal and electrical degradation of lubricant. Hence, the rs part of the EV curve is more elongated than that of ICE (point C). After point s, a further rise in speed would lead to a steeper rise in CoF (st) compared with CD in the ICE lubricant. This is so because at high speeds, (a) there is a high heat generation which would lead to some thermal degradation of the lubricant lowering the film thickness, and (b) there is electric field–induced film deformation (e.g., electrowetting, micro-bubbling, interface chemical reactions, and electric discharge). Both of these result in increased metal–metal contact and hence a steeper CoF rise (Lu et al., 2006; Vladescu et al., 2018).
In the previous section, we discussed about lubricants and their impacts on vehicle performance in terms of friction. It was seen that thermal management is important for EV/HEVs. Optimized performance in electric motors requires a thermally controlled working condition. To maintain a thermally controlled working condition, the thermal path between the source of energy loss and the thermal sink needs to have a high thermal conductivity (Yang et al., 2016b). One of the most important thermal paths in EV/HAV was lubricated contacts. In addition to that, the lubricant can be circulated to provide additional cooling for electric motors (Stockton, 1983; Hasebe et al., 1994). Failed thermal management increases the resistance of copper wires in electric motor, decreasing motor efficiency. The high temperature in the electric motor can also be demagnetizing the permanent magnets and lowering the life expectancy of the electric motor (Yang et al., 2016b).
Two lubricant thermal properties can impact the thermal management of the EV/HEV. The thermal conductivity and thermal capacity of lubricants influence the cooling efficiency of the electric motors in EV/HEV.
The relationship between the thermal property of a lubricant and the electric motor's efficiency loss varies in vehicles. Here, we propose a simplified model to characterize the effect of a lubricant's thermal property using the dimensional analysis method.
The major contribution of electric energy loss is from the resistance of the coil (Yang et al., 2016b):
where ηloss is the efficiency loss caused by coil resistivity, rloss is the efficiency loss caused by coil resistivity at room temperature, ΔT is the temperature increase from room temperature, and α is the temperature coefficient of copper which has a value of 0.0393% K−1 (Callen, 1998).
The thermal energy that causes this change can be dissipated partly by the flow of lubricant, which can be inferred based on the dimensional analysis principles:
where Fcooling is a factor that characterizes how fast the thermal energy can transfer into the lubricant, ṁ it the flow rate of the lubricant, and Cp is the specific heat of the lubricant. Because the Fcooling is smaller than 1 and dimensionless, this factor can be approximated to
where K is the thermal conductivity of lubricant and Ks is a quantity related to vehicle design and has the same dimension as the thermal conductivity. By combining Equations (1), (2), and (3), ΔT can be eliminated. The equation of efficiency loss related to the lubricant thermal energy is
Using Equation (4), the relationship between the thermal property and EV/HEV efficiency can be plotted and is shown in Figure 6. This curve has two distinguished regions. When the thermal conductivity and thermal capacity are low, as in the area toward 0.0 on axis, the motor cannot be cooled efficiently, and the loss of efficiency was highly correlated to the lubricant thermal properties. When the thermal conductivity and thermal capacity are high enough, as the x-axis moves toward higher, there is little correlation between the lubricant thermal property and motor efficiency. This indicated that there is a lower limit requirement for both the lubricant thermal conductivity and thermal capacity of lubricant. This limit should be used for consideration in design of lubricants for EVs.
Similar to ICE, the powertrain of EV and HEV demands different and unique physical properties for lubricating oils (Yang et al., 2016a; Becker, 2019). One of the most important requirements for EV/HEV lubricant is its low impedance. Both EV and HEV vehicles are powered by batteries that output a single DC voltage. The speed control is achieved by a pulse-width-modulation process. Essentially, a semiconductor device called inverter rapidly switches the voltage input to the motor (Walther and Holub, 2014; Hadden et al., 2016; Reed et al., 2017). The pulse modulated input cannot be fully consumed by the electric motors. This causes additional current leak from the rotor of the motor to the ground. This stray current runs across the bearings supporting the rotor and into the surrounding environment. In addition to that, tribo-pairs inside those bearings can act as a capacitor when the lubricant impedance was high. The voltage between those tribo-pairs will increase until it reaches the breakdown voltage of lubricant film, causing a large current surge. Without proper mitigation, it can cause both electric interference and mechanical damage to electric vehicles.
The amplitude of the aforementioned current surge is closely related to the electrical properties of lubricant, the electric impedance of the lubricant, and the dielectric strength. The electric impedance of a lubricant determines the electric conductivity across the lubricated tribo-pairs. The dielectric strength of the lubricant determines the breakdown voltage across the lubricated tribo-pairs. The tribo-pairs lubricated with high impedance lubricant will cause a build-up of electric charge which led to dielectric breakdown and component damage (He et al., 2020). The peak bearing current was several times higher when lubricated with non-conductive grease (Walther and Holub, 2014).
The dielectric breakdown of the lubricant can cause a large bearing current. This bearing current can cause electronic magnetic interference to the adjacent components (Akagi and Tamura, 2006; Di Piazza et al., 2011). It can also cause destructive damage to bearings and transmission. War is induced by electric discharge (ED) or tribo-corrosion process (Akagi and Tamura, 2006; Mukherjee et al., 2009; Walther and Holub, 2014; Chatterton et al., 2016; Kwak et al., 2019; He et al., 2020). The occurrence of an ED incidence often has a peak current around a few amperes (Tischmacher et al., 2010; Chatterton et al., 2016; He et al., 2020). The current caused an intense localized heat that melts and removes a tiny portion of bearing surfaces (He et al., 2020). The ED damage can cause different types of wear that depended on the bearing type and lubricant properties. The electric “micro craters” and “frosting” indicated damage caused by many EDs (Chatterton et al., 2016). They were characterized by microscopic “craters” that closely packed together. In previous reports, the loosely packed micro craters were also termed “pitting” (Chatterton et al., 2016). However, this may be confusing because “pitting” can be interpreted as some other phenomenon that happened in corrosion. Sometimes, the micro craters were referred to as ED damages that are less frequent but deeper into the bearing surface. When the lubricant has low dielectric strength and impedance, the tribo-corrosion effect may cause the “fluting” damage. It was characterized by elongated micro craters on the surface. In Figure 7, the relationship between dielectric strength, electric impedance, and electric bearing damage is shown.
Because of the unique failure modes, the traditional anti-wear additives such as ZDDP and MoDTC in ICE may not be suitable for EV/hybrid transmission systems (Spikes, 2008, 2015; Becker, 2019). Such tribo-film forming additives could lead to the increment of electric resistance (Flores-Torres et al., 2018a; Gao et al., 2018a,b). However, some novel lubricant anti-wear additives may provide both anti-wear properties and low conductivity, for example, ionic liquid additives or carbon-based nanoparticles (Somers et al., 2013; Naddaf and Heris, 2018).
In addition to direct damage of the contacting surfaces, the charge that builds up between the two components can cause other types of lubricant failures as well. The lubricant film could collapse under a high electric charge, causing lubricating starvation (Xie et al., 2017). The thermal dielectric breakdown directly led to lubricant degradation (Didenko and Pridemore, 2012; Liu, 2014; Romanenko et al., 2015, 2016). The ED current can break down and oxidize the lubricant in the bearings, further lowering its dielectric strength (Romanenko et al., 2015).
Finally, the lubricant electric conductivity is not always the higher the better. In powertrain, the lubricant is needed as insulator. A lubricant with too low conductivity can also cause current leakage (Flores-Torres et al., 2018a; Gao et al., 2018b).
Achieving a high energy efficiency is one of the prime goals for future EV/HEV. Energy efficiency is inextricably connected to thermal efficiency and design. Herein, the fundamental issues, material, and system design aspects of EV/HEV lubrication are presented that focus on attaining high energy and thermal efficiencies. Future research needs more fundamental research on lubricant behavior under applied electric field and dynamic EV/HEV conditions. Furthermore, the effects of lubricants on the wear and corrosion of EV/HEV components need to be well established. High temperature and electrical stability for a low-viscosity lubricant in EV/HEV are of considerable interest.
Understanding the effect of electric and magnetic field environments on the lubrication systems in electric vehicles is of utmost scientific and industrial importance. Research should focus on minimizing the electric field and grounding, diminishing electrical breakdown, enhancing bearing insulation performance, and improving the conduction of the lubricated interface (He et al., 2020). Optimal choice and control of the lubricant electrical conductivity are necessary. High electrical conductivity can lead to current leakage whereas a low conductivity (less than 4 × 10−12 S/cm) may lead to static charge build-up and electrical arcing which degrades a lubricant (Gahagan, 2017; Whitby, 2018). Detection, classification, and quantification of electric environments surrounding the lubrication need to be complemented with low-cost robust alternatives and a general model for prediction of bearing current. The development of new materials that may be self-lubricating and self-healing with tailored surfaces for desired electrical response are good directions for future research. The designed lubricant should be able to protect EV components during frequent starts/stops. The effects of emulsion formation in a fluid resulting from water condensation could be of research interest. All these fundamental issues need tackling in future research endeavors which need a collective participation of industry and academia.
There are several aspects to consider for a thermal and energy-efficient design of EV/HEV lubricants. The use of low-viscosity fluids will lead to reduced film thickness. A reduction in film thickness will result in a higher operating temperature leading to reduced fatigue life of bearings (Peskoe-Yang, 2020). In lubricant design, the use of organic molecules with a longer chain and less branching will enhance heat transfer on account of intermolecular collisions (Narita and Takekawa, 2019). It has been found that even low amounts of phosphorus or sulfur may be extremely detrimental to components. Hence, antiwear and antioxidant additives like dialkyldithiophosphates may not be used in future formulations (Korcek et al., 2000). With the use of grease being dominant, an understanding of the fundamental grease lubrication mechanism and theoretical tools for their performance prediction in future EV/HEV is going to be of prime importance. New grease formulations capable of withstanding high-temperature fluctuations and high shear will be required. The use of eco-friendly and bio-degradable greases will go up. The new and varied design of EV/HEV will require reformulating the greases, coolants, and gear oils. The requirement of grease will be especially high in EV with properties like the life of grease, resistance to water, load-bearing capacity, corrosion resistance, and performance at low temperatures being of prime importance (Peskoe-Yang, 2020). For greases, it is desired to obtain reduced torque characteristics through a better combination of thickeners, BOs, and additives. Grease formulations should also not alter the electrical and mechanical properties (hardness, crack resistance, and tensile strength) of components in EV/HEV. Also, due to varied EV components and design, it is highly desirable to obtain application-specific tailor-made greases rather than developing generic ones (Gonçalves et al., 2017). Polyurea-based greases can provide a seal-for-life function. Hence, they would be in high demand in future EVs while the lithium-based greases would encounter a lot of uncertainties (Andrew, 2019).
The system design for EV/HEV should provide conditions that complement the lubricant material to perform at optimal performance for achieving high thermal and energy efficiencies. About 57% energy of an EV is used to overcome friction (Farfan-Cabrera, 2019). There is a great opportunity for reducing energy losses in electronics, battery use, air conditioning, air drag, and cabin ventilation of an EV/HEV. As the EV devices will be more oriented toward torque transfer, the role of lubricants will be more toward the reduction of NVH (noise, vibration, and harshness). High-speed rotor dynamics, control, and high-speed air compressor lubrication will emerge as popular research topics (Van Rensselar, 2019). The future EVs would benefit from spray cooling. The runoff from spray cooling could be used for attendant bearing lubrication. The hydrodynamic load on the journal bearings in EV should be lower than that in ICE vehicles. Thus, the load bearing function of lubricants in ICE vehicles would need to be shifted to torque transfer function in EV (Van Rensselar, 2019). Controlling excessive oil aeration should also be considered in the overall design process. To reduce bearing fatigue, the lighter lubricants and the lubrication system components would need a 10-fold higher life than what the present mechanical systems are designed for (Van Rensselar, 2019). Transmission fluid needs to have a high heat transfer coefficient to keep the motor cool. Advanced coatings would be required to offset surface adhesion (creeping) and the effect of thin films resulting from using low-viscosity lubricants. Extended lubricant drain periods lead to problems of wear and component durability due to lubricant degradation. Hence, the future EV designs should focus on the installation of smart oil monitoring systems that can monitor several parameters and using state-of-the-art high-quality sensors (Korcek et al., 2000). Advanced cooling designs like the direct pin-fin-based liquid cooling, used by Wang et al., for improving component reliability would be necessary (Wang et al., 2014).
In the present article, we reviewed the state-of-the-art and challenges of lubricants used for electric and hybrid vehicles. From about 150 articles, a comprehensive review of lubricants was done in terms of composition and fluidic/electrical/physical properties against the various conditions they are used in vehicles. Based on the information and data collected, we analyzed the frictional performance of those vehicles against application conditions. The frictional performance, thermal management, and dielectric breakdown were examined. Performance parameters were found critically dependent on the properties of lubricants that are crucial for energy efficiency and reliability. This review pointed three aspects that have not been discussed previously.
• A Stribeck curve for electric vehicles presents significant challenges than otherwise. The high acceleration rate poses challenges in generating lubricant films quickly and maintaining stability at elevated temperature and electrical field.
• Optimized electric properties of a lubricant can prevent the bearing electrical damage often seen in electric vehicles. The properties are electrical impedance and dielectric strength. The relationship between bearing damage and lubricant electric properties were identified.
• The thermal efficiency of an electrical motor depends on the thermal properties of a lubricant: thermal conductivity, heat capacity, and flow rate. Optimization of energy efficiency can be achieved though evaluation of those properties for high efficiency.
Through this review, it is apparent that achieving high lubrication performance and component reliability while not sacrificing on vehicle energy efficiency is a challenging task. This review can be used as a guidance for the future design of advanced lubricants for electric and hybrid vehicles.
YC, SJ, and AR conducted literature search, analyzed information, and wrote the paper. WZ provide inputs and reviewed the paper. HL designed the structure and content and wrote the paper. All authors contributed to the article and approved the submitted version.
WZ is employed by the company Tesla.
The remaining authors declare that the research was conducted in the absence of any commercial or financial relationships that could be construed as a potential conflict of interest.
Part of this work was sponsored by the TAMU President's Excellence Fund X-Grants.
Akagi, H., and Tamura, S. (2006). A passive EMI filter for eliminating both bearing current and ground leakage current from an inverter-driven motor. IEEE Trans. Power Electron. 21, 1459–1469. doi: 10.1109/TPEL.2006.880239
Allen, C. M., and Drauglis, E. (1969). Boundary layer lubrication: monolayer or multilayer. Wear 14, 363–384. doi: 10.1016/0043-1648(69)90017-9
Andrew, J. M. (2019). The future of lubricating greases in the electric vehicle era. Tribol. Lubr. Technol. 75, 38–44.
API (2015). API Base Oil Interchangeability Guidelines for Passenger Car Motor Oils and Diesel Engine Oils (Washington, DC), E1–E28.
Atkins, M. J., and Koch, C. R. (2003). A Well-to-Wheel Comparison of Several Powertrain Technologies. SAE Technical Paper Report No.: 0148-7191. doi: 10.4271/2003-01-0081
Barbés, B., Páramo, R., Blanco, E., Pastoriza-Gallego, M. J., Pineiro, M. M., Legido, J. L., et al. (2013). Thermal conductivity and specific heat capacity measurements of Al2 O3 nanofluids. J. Thermal Anal. Calorim. 111, 1615–1625. doi: 10.1007/s10973-012-2534-9
Barnes, A. M., Bartle, K. D., and Thibon, V. R. A. (2001). A review of zinc dialkyldithiophosphates (ZDDPS): characterisation and role in the lubricating oil. Tribol. Int. 34, 389–395. doi: 10.1016/S0301-679X(01)00028-7
Beckman, M. (2019). The Fluid Transmission. Park Ridge: Society of Tribologists and Lubrication Engineers.
Beyer, M., Brown, G., Gahagan, M., Higuchi, T., Hunt, G., Huston, M., et al. (2019). Lubricant concepts for electrified vehicle transmissions and axles. 14, 428–437. doi: 10.2474/trol.14.428
Bouvy, C., Baltzer, S., Jeck, P., Gißing, J., Lichius, T., and Eckstein, L. (2012). “Holistic vehicle simulation using modelica-an application on thermal management and operation strategy for electrified vehicles,” in Proceedings of the 9th International MODELICA Conference; September 3-5; 2012 (Munich: Linköping University Electronic Press).
Bradley, T. H., and Frank, A. A. (2009). Design, demonstrations and sustainability impact assessments for plug-in hybrid electric vehicles. Renew. Sustain. Energy Rev. 13, 115–128. doi: 10.1016/j.rser.2007.05.003
Busse, D., Erdman, J., Kerkman, R., Schlegel, D., and Skibinski, G. (1997). Characteristics of shaft voltage and bearing currents. IEEE Ind. Appl. Mag. 3, 21–32. doi: 10.1109/2943.628116
Callen, H. B. (1998). Thermodynamics and an Introduction to Thermostatistics. Hoboken, NJ: American Association of Physics Teachers.
Cann, P. (2007). Grease lubrication of rolling element bearings—role of the grease thickener. Lubr. Sci. 19, 183–196. doi: 10.1002/ls.39
Casserly, E., Langlais, T., Springer, S. P., Kumar, A., and Mallory, B. J. L. M. (2018). The effect of base oils on thickening and physical properties of lubricating greases. Euro. Lubric. Ind. Magazine 144, 32–37. Available online at: http://www.lube-media.com/wp-content/uploads/Lube-Tech-115-The-Effect-of-Base-Oils-on-Thickening-and-Physical-Properties-of-Lubricating-Greases.pdf
Chatterton, S., Pennacchi, P., and Vania, A. (2016). Electrical pitting of tilting-pad thrust bearings: modelling and experimental evidence. Tribol. Int. 103, 475–486. doi: 10.1016/j.triboint.2016.08.003
Chau, K. T., and Chan, C. C. (2007). Emerging energy-efficient technologies for hybrid electric vehicles. Proc. IEEE. 95, 821–835. doi: 10.1109/JPROC.2006.890114
Chen, Y., and Liang, H. (2019). Tribological evaluation of electrical resistance of lubricated contacts. J. Tribol. 142:114502. doi: 10.1115/1.4045578
Chen, Y., Renner, P., and Liang, H. (2019a). Dispersion of nanoparticles in lubricating oil: a critical review. Lubricants 7:7. doi: 10.3390/lubricants7010007
Chen, Y., Wang, X., Clearfield, A., and Liang, H. (2019b). Anti-galling effects of α-zirconium phosphate nanoparticles as grease additives. J. Tribol. 141:031801. doi: 10.1115/1.4041538
Chong, W., and Cruz, M. (2014). Elastoplastic contact of rough surfaces: a line contact model for boundary regime of lubrication. Meccanica 49, 1177–1191. doi: 10.1007/s11012-013-9861-1
Clarke, D. (2014). Understanding Lubricant Requirements of Hybrid-Electric Vehicles. SAE International.
Covitch, M. J. (2003). “Olefin copolymer viscosity modifiers,” in Chemical Industries (New York, NY: Marcel Dekker), 293–328.
Csapo, E., Zaidi, H., and Paulmier, D. (1996). Friction behaviour of a graphite-graphite dynamic electric contact in the presence of argon. Wear 192, 151–156. doi: 10.1016/0043-1648(95)06788-4
Dai, W., Kheireddin, B., Gao, H., and Liang, H. (2016). Roles of nanoparticles in oil lubrication. Tribol. Int. 102, 88–98. doi: 10.1016/j.triboint.2016.05.020
Dassenoy, F. (2019). Nanoparticles as additives for the development of high performance and environmentally friendly engine lubricants. Tribol. Online. 14, 237–253. doi: 10.2474/trol.14.237
Davis, J. (2008). “Lightweight materials for cars and trucks,” in Office of Energy Efficiency & Renewable Energy, ed P. Gary (Brussels: WWF European Policy Office).
Di Piazza, M. C., Ragusa, A., and Vitale, G. (2011). Power-loss evaluation in CM active EMI filters for bearing current suppression. IEEE Trans. Ind. Electron. 58, 5142–5153. doi: 10.1109/TIE.2011.2119456
Didenko, T., and Pridemore, W. D. (2012). Electrical fluting failure of a Tri-lobe roller bearing. J. Fail. Anal. Prev. 12, 575–580. doi: 10.1007/s11668-012-9598-5
Drummond, C. (2012). Electric-field-induced friction reduction and control. Phys. Rev. Lett. 109:154302. doi: 10.1103/PhysRevLett.109.154302
Egede, P. (2017a). “Case studies on the comparison of (lightweight) electric vehicles with conventional and reference electric vehicles,” in Environmental Assessment of Lightweight Electric Vehicles, eds C. Herrmann and S. Kara (Cham: Springer International Publishing), 93–119. doi: 10.1007/978-3-319-40277-2_5
Egede, P. (2017b). “Electric vehicles, lightweight design and environmental impacts,” in Environmental Assessment of Lightweight Electric Vehicles, 9–40. doi: 10.1007/978-3-319-40277-2_2
Elgowainy, A., Burnham, A., Wang, M., Molburg, J., and Rousseau, A. (2009). Well-To-Wheels Energy Use and Greenhouse Gas Emissions of Plug-in Hybrid Electric Vehicles. SAE Technical Report. doi: 10.2172/951259
Fan, X., and Wang, L. (2014). Tribological properties of conductive lubricating greases. Friction 2, 343–353. doi: 10.1007/s40544-014-0062-2
Farfan-Cabrera, L. I. (2019). Tribology of electric vehicles: a review of critical components, current state and future improvement trends. Tribol. Int. 138, 473–486. doi: 10.1016/j.triboint.2019.06.029
Feng, W., and Figliozzi, M. A. (2012). Conventional vs electric commercial vehicle fleets: a case study of economic and technological factors affecting the competitiveness of electric commercial vehicles in the USA. Proc. Soc. Behav. Sci. 39, 702–711. doi: 10.1016/j.sbspro.2012.03.141
Flores-Torres, S., Holt, D. G., and Carey, J. T. (2018). Lubricating Oil Compositions for Electric Vehicle Powertrains. Washington, DC: U.S. Patent and Trademark Office.
Flores-Torres, S., Holt, D. G. L., and Carey, J. T. (2018a). Method for Controlling Electrical Conductivity of Lubricating Oils in Electric Vehicle Powertrains. U.S. Patent 0,100,118A1. Annandale, NJ: ExxonMobil Research and Engineering Co.
Flores-Torres, S., Holt, D. G. L., and Carey, J. T. (2018b). Method for Preventing or Minimizing Electrostatic Discharge and Dielectric Breakdown in Electric Vehicle Powertrains. U.S. Patent No. 0,100,120A1. Annandale, NJ: ExxonMobil Research and Engineering Co.
Flores-Torres, S., Holt, D. G. L., and Carey, J. T. (2018c). Lubricating Oil Compositions for Electric Vehicle Powertrains. U.S. Patent No. 0,100,117A1. Annandale, MJ: ExxonMobil Research and Engineering Co.
Gahagan, M. P. (2017). Lubricant Technology for Hybrid Electric Automatic Transmissions. SAE Technical Paper report. doi: 10.4271/2017-01-2358
Gao, Z., Salvi, L., and Flores-Torres, S. (2018a). High Conductivity Lubricating Oils for Electric and Hybrid Vehicles. U.S. Patent No. 0,100,115A1. ExxonMobil Research and Engineering Co.
Gao, Z., Salvi, L., and Flores-Torres, S. (2018b). High Conductivity Lubricating Oils for Electric and Hybrid Vehicles. Washington, DC: U.S. Patent and Trademark Office.
Gonçalves, D., Vieira, A., Carneiro, A., Campos, A., and Seabra, J. (2017). Film thickness and friction relationship in grease lubricated rough contacts. Lubricants 5:34. doi: 10.3390/lubricants5030034
Goto, K. (1995). The influence of surface induced voltage on the wear mode of stainless steel. Wear 185, 75–81. doi: 10.1016/0043-1648(95)06600-4
Guangteng, G., and Spikes, H. A. (1996). Boundary film formation by lubricant base fluids. Tribol. Trans. 39, 448–454. doi: 10.1080/10402009608983551
Guegan, J., Southby, M., and Spikes, H. J. T. L. (2019). Friction modifier additives, synergies and antagonisms. Tribol. Lett. 67:83. doi: 10.1007/s11249-019-1198-z
Gunderson, S., Fultz, G., Snyder, C., Wright, J., Gschwender, L., and Heidger, S. (2011). The effect of water content on the dielectric strength of polyalphaolefin (PAO) coolants. IEEE Trans. Dielectr. Electr. Insul. 18, 295–302. doi: 10.1109/TDEI.2011.5704521
Gupta, A. (2012). Characterization of Engine and Transmission Lubricants for Electric, Hybrid, and Plug-in Hybrid Vehicles. The Ohio State University.
Håkansson, B., Andersson, P., and Bäckström, G. (1988). Improved hot-wire procedure for thermophysical measurements under pressure. Rev. Sci. Instrum. 59, 2269–2275. doi: 10.1063/1.1139946
Hadden, T., Jiang, J. W., Bilgin, B., Yang, Y., Sathyan, A., Dadkhah, H., et al. (2016). “A review of shaft voltages and bearing currents in EV and HEV motors,” in IECON 2016 – 42nd Annual Conference of the IEEE Industrial Electronics Society.
Hamblin, P., Kristen, U., and Chasan, D. J. L. S. (1990). Ashless antioxidants, copper deactivators and corrosion inhibitors: their use in lubricating oils. Lubr. Sci. 2, 287–318. doi: 10.1002/ls.3010020403
Hasebe, M., Miyaishi, Y., Wakuta, S., Minezawa, Y., Hara, T., and Tsuzuki, S. (1994). Oil Circulating System for Electric Vehicle. Washington, DC: U.S. Patent and Trademark Office.
He, F., Xie, G., and Luo, J. (2020). Electrical bearing failures in electric vehicles. Friction 8, 4–28. doi: 10.1007/s40544-019-0356-5
Heap, A. H., Sah, J.-J. F., and Kaminsky, L. A. (2011). Engine Control System for Torque Management in a Hybrid Powertrain System. Washington, DC: U.S. Patent and Trademark Office.
Hobelsberger, M., and Posedel, Z. (2013). Method for Monitoring the Shaft Current and/or the Insulation of the Shaft of Electric Machines and Device for Performing the Method. Washington, DC: U.S. Patent and Trademark Office.
Holmberg, K., Andersson, P., and Erdemir, A. (2012). Global energy consumption due to friction in passenger cars. Tribol. Int. 47, 221–234. doi: 10.1016/j.triboint.2011.11.022
Holmberg, K., and Erdemir, A. (2019). The impact of tribology on energy use and CO2 emission globally and in combustion engine and electric cars. Tribol. Int. 135, 389–396. doi: 10.1016/j.triboint.2019.03.024
Hope, K. J. L. (2018). PAO contributions to energy efficiency in 0W-20 passenger car engine oils. Lubricants 6:73. doi: 10.3390/lubricants6030073
Horne, W. V. (1949). Polymethacrylates as viscosity index improvers and pour point depressants. Ind. Eng. Chem. 41, 952–959. doi: 10.1021/ie50473a017
Hunt, G. (2017). New perspectives on the temperature dependence of lubricant additives on copper corrosion. SAE Int. J. Fueis Lubr. 10, 521–527. doi: 10.4271/2017-01-0891
Hunt, G. J., Gahagan, M. P., and Peplow, M. A. (2017). Wire resistance method for measuring the corrosion of copper by lubricating fluids. Lubric. Sci. 29, 279–290. doi: 10.1002/ls.1368
Jablonka, K., Glovnea, R., Bongaerts, J., and Morales-Espejel, G. (2013). The effect of the polarity of the lubricant upon capacitance measurements of EHD contacts. Tribol. Int. 61, 95–101. doi: 10.1016/j.triboint.2012.11.016
Jeschke, S., and Hirsch, H. (2014). “Investigations on the EMI of an electric vehicle traction system in dynamic operation,” in 2014 International Symposium on Electromagnetic Compatibility (IEEE: Gothenburg).
Jeschke, S., Tsiapenko, S., and Hirsch, H. (2015). “Investigations on the shaft currents of an electric vehicle traction system in dynamic operation,” in 2015 IEEE International Symposium on Electromagnetic Compatibility (EMC) (IEEE: Dresden).
Jiang, Z., Fang, J., Chen, Y., Wu, J., Liu, P., Gu, K., et al. (2018). A review of lubricating mechanisms from the perspective of tribo-electrophysics and tribo-electrochemistry. Sci. China Technol. Sci. 61, 1–11. doi: 10.1007/s11431-017-9291-3
Jin, H., Andritsch, T., Tsekmes, I. A., Kochetov, R., Morshuis, P. H., and Smit, J. J. (2014). Properties of mineral oil based silica nanofluids. IEEE Trans. Dielectr. Electr. Insul. 21, 1100–1108. doi: 10.1109/TDEI.2014.6832254
Kolodziejczyk, L., Rojas, T., Martinez-Martinez, D., Fernandez, A., and Sanchez Lopez, J. (2007). Surface-modified Pd nanoparticles as a superior additive for lubrication. J. Nanoparticle Res. 9, 639–645. doi: 10.1007/s11051-006-9124-3
Korcek, S., Sorab, J., and Johnson, J. R. K. (2000). Automotive lubricants for the next millennium. Ind. Lubr. Tribol. 52, 209–220. doi: 10.1108/00368790010373175
Kwak, Y., Cleveland, C., Adhvaryu, A., Fang, X., Hurley, S., and Adachi, T. (2019). Understanding Base Oils and Lubricants for Electric Drivetrain Applications. Richmond, VA: SAE Technical Paper. Report No.: 0148-7191. doi: 10.4271/2019-01-2337
Lavielle, L. (1994). Electric field effect on the friction of a polyethylene-terpolymer film on a steel substrate. Wear 176, 89–93. doi: 10.1016/0043-1648(94)90201-1
Leach, B., and Pearson, R. (2014). Eengine Lubrication and Cooling During Hybrid Vehicle Operation. SAE Technical Paper Report. doi: 10.4271/2014-01-2784
Lévay, P. Z., Drossinos, Y., and Thiel, C. (2017). The effect of fiscal incentives on market penetration of electric vehicles: a pairwise comparison of total cost of ownership. Energy Policy. 105, 524–533. doi: 10.1016/j.enpol.2017.02.054
Lim, D. H., and Kim, S. C. (2014). Thermal performance of oil spray cooling system for in-wheel motor in electric vehicles. Appl. Thermal Eng. 63, 577–587. doi: 10.1016/j.applthermaleng.2013.11.057
Lin, X.-Z., Zhu, M.-H., Mo, J.-L., Chen, G.-X., Jin, X.-S., and Zhou, Z.-R. (2011). Tribological and electric-arc behaviors of carbon/copper pair during sliding friction process with electric current applied. Trans. Nonferrous Met. Soc. China 21, 292–299. doi: 10.1016/S1003-6326(11)60712-7
Liu, W. (2014). The prevalent motor bearing premature failures due to the high frequency electric current passage. Eng. Fail. Anal. 45, 118–127. doi: 10.1016/j.engfailanal.2014.06.021
Lou, Z., and Sabhapathy, P. (2004). Hybrid Electrical Vehicle Powertrain Thermal Control. Google Patents.
Lu, X., Khonsari, M. M., and Gelinck, E. R. M. (2006). The stribeck curve: experimental results and theoretical prediction. J. Tribol. 128, 789–794. doi: 10.1115/1.2345406
Luo, J., He, Y., Zhong, M., and Jin, Z. (2006). Gas bubble phenomenon in nanoscale liquid film under external electric field. Appl. Phys. Lett. 89:013104. doi: 10.1063/1.2213979
Ma, H., Balthasar, F., Tait, N., Riera-Palou, X., and Harrison, A. (2012). A new comparison between the life cycle greenhouse gas emissions of battery electric vehicles and internal combustion vehicles. Energy Policy. 44, 160–173. doi: 10.1016/j.enpol.2012.01.034
Marom, R., Amalraj, S. F., Leifer, N., Jacob, D., and Aurbach, D. (2011). A review of advanced and practical lithium battery materials. J. Mater. Chem. 21, 9938–9954. doi: 10.1039/c0jm04225k
McHale, G., Orme, B., Wells, G., and Ledesma-Aguilar, R. (2019). Apparent contact angles on lubricant impregnated surfaces/SLIPS: from superhydrophobicity to electrowetting. Langmuir 35, 4197–4204. doi: 10.1021/acs.langmuir.8b04136
Miller, J. (2006). Hybrid electric vehicle propulsion system architectures of the e-CVT type. Power Electron. IEEE Trans. 21, 756–767. doi: 10.1109/TPEL.2006.872372
Miller, J. M., and Everett, M. (2005). An Assessment of Ultra-Capacitors as the Power Cache in Toyota THS-II, GM-Allision AHS-2 and Ford FHS Hybrid Propulsion Systems, Vol. 1. 481–490.
Mugele, F., and Baret, J.-C. (2005). TOPICAL REVIEW: electrowetting: from basics to applications. J. Phys. Condensed Matter 17, R705–R774. doi: 10.1088/0953-8984/17/28/R01
Mukherjee, R., Patra, A., and Banerjee, S. (2009). Impact of a frequency modulated pulsewidth modulation (PWM) switching converter on the input power system quality. IEEE Trans. Power Electron. 25, 1450–1459. doi: 10.1109/TPEL.2009.2037421
Naddaf, A., and Heris, S. Z. (2018). Experimental study on thermal conductivity and electrical conductivity of diesel oil-based nanofluids of graphene nanoplatelets and carbon nanotubes. Int. Commun. Heat Mass Transfer. 95, 116–122. doi: 10.1016/j.icheatmasstransfer.2018.05.004
Nagasaka, Y., and Nagashima, A. (1981). Simultaneous measurement of the thermal conductivity and the thermal diffusivity of liquids by the transient hot-wire method. Rev. Sci. Instrum. 52, 229–232. doi: 10.1063/1.1136577
Nakanishi, Y., Honda, T., Kasamura, K., Nakashima, Y., Nakano, K., Kondo, K., et al. (2016). “Bio-inspired shaft seal in coolant pump for electric vehicles,” in 2016 IEEE International Conference on Renewable Energy Research and Applications (ICRERA).
Narita, K., and Takekawa, D. (2019). Lubricants Technology Applied to Transmissions in Hybrid Electric Vehicles and Electric Vehicles. Chiba: SAE Technical Paper Report No.: 0148-7191. doi: 10.4271/2019-01-2338
Nikolic, N., Dorić, J, Antonic, Z., and Mitar, J. (2018). Influence of Load and Oil Viscosity on Stribeck Curve Shape for Long Journal Bearing.
Noguchi, S., Kakinuma, S.-N., and Kanada, T. (2010). Measurement of direct current voltage causing electrical pitting. J. Adv. Mech. Des. Syst. Manufact. 4, 1084–1094. doi: 10.1299/jamdsm.4.1084
Paar, C., Muetze, A., and Kolbe, H. (2015). Influence of machine integration on the thermal behavior of a PM drive for hybrid electric traction. IEEE Trans. Ind. Appl. 51, 3914–3922. doi: 10.1109/TIA.2015.2427280
Passut, C. A. (2013). “Engine lubricants,” in Encyclopedia of Tribology, eds Q. J. Wang and Y.-W. Chung (Boston, MA: Springer), 977–981.
Peskoe-Yang, L. (2020). Electric vehicles make grease's future uncertain. Tribol. Lubr. Technol. 76, 24–25.
Pettersson, A. (2007). High-performance base fluids for environmentally adapted lubricants. Tribol. Int. 40, 638–645. doi: 10.1016/j.triboint.2005.11.016
Propfe, B., Redelbach, M., Santini, D. J., and Friedrich, H. (2012). Cost analysis of plug-in hybrid electric vehicles including maintenance & repair costs and resale values. World Elect. Vehicle J. 5, 886–895. doi: 10.3390/wevj5040886
Rawat, S. S., and Harsha, A. (2019). Current and Future Trends in Grease Lubrication. Automotive Tribology: Springer.
Reed, J. K., Ludois, D. C., Mason, W. P., and Wolf, D. (2017). Rotary Capacitor for Shunting High Frequency Bearing Currents and Reducing EMI in Electric Machinery. U.S. Patent No. 9,653,970B2. Madison, WI: C-Motive Technologies Inc.
Rensselar, J. (2010). Biobased lubricants: gearing up for a green world. Tribol. Lubr. Technol. 66, 32–34.
Romanenko, A., Muetze, A., and Ahola, J. (2016). Effects of electrostatic discharges on bearing grease dielectric strength and composition. IEEE Trans. Ind. Appl. 52, 4835–4842. doi: 10.1109/TIA.2016.2596239
Romanenko, A., Mütze, A., and Ahola, J. (2015). “Effects of electrostatic discharges on bearing grease electric properties,” in 2015 IEEE International Electric Machines & Drives Conference (IEMDC) (San Diego, CA: IEEE). doi: 10.1109/IEMDC.2015.7409068
Rossi, A. (1980). Pour Point Depressant Additive for Fuels and Lubricants. Washington, DC: U.S. Patent and Trademark Office.
Saji, V. S. (2010). A Review on Recent Patents in Corrosion Inhibitors. (Ulsan). doi: 10.2174/1877610801002010006
Sangoro, J., Iacob, C., Serghei, A., Naumov, S., Galvosas, P., Kärger, J., et al. (2008). Electrical conductivity and translational diffusion in the 1-butyl-3-methylimidazolium tetrafluoroborate ionic liquid. J. Chem. Phys. 128:214509. doi: 10.1063/1.2921796
Sasaki, S. (1998). “Toyota's newly developed hybrid powertrain,” in Proceedings of the 10th International Symposium on Power Semiconductor Devices and ICs ISPSD'98 (IEEE Cat No98CH36212). doi: 10.1109/ISPSD.1998.702540
Shaikh, S., Lafdi, K., and Ponnappan, R. (2007). Thermal conductivity improvement in carbon nanoparticle doped PAO oil: an experimental study. J. Appl. Phys. 101:064302. doi: 10.1063/1.2710337
Sniderman, D. (2017). The chemistry and function of lubricant additives. Tribol. Lubric. Technol. 73, 18–29. Available online at: https://www.stle.org/images/pdf/STLE_ORG/BOK/LS/Additives/The%20Chemistry%20and%20Function%20of%20Lubricant%20Additives.pdf
Somers, A. E., Howlett, P. C., MacFarlane, D. R., and Forsyth, M. (2013). A review of ionic liquid lubricants. Lubricants 1, 3–21. doi: 10.3390/lubricants1010003
Soni, A., and Singh Prajapati, R. (2017). Tribological aspects of Internal combustion engine. IRJET 9, 451–454.
Spikes, H. (2008). Low-and zero-sulphated ash, phosphorus and sulphur anti-wear additives for engine oils. Lubr. Sci. 20, 103–136. doi: 10.1002/ls.57
Stockton, T. R. (1983). Transmission Lubrication and Motor Cooling System. Washington, DC: U.S. Patent and Trademark Office.
Suzumura, J. (2016). Prevention of electrical pitting on rolling bearings by electrically conductive grease. Q Rep. RTRI. 57, 42–47. doi: 10.2219/rtriqr.57.1_42
Sweeney, J., Hausen, F., Hayes, R., Webber, G. B., Endres, F., Rutland, M. W., et al. (2012). Control of nanoscale friction on gold in an ionic liquid by a potential-dependent ionic lubricant layer. Phys. Rev. Lett. 109:155502. doi: 10.1103/PhysRevLett.109.155502
Syahir, A. Z., Zulkifli, N. W. M., Masjuki, H. H., Kalam, M. A., Alabdulkarem, A., Gulzar, M., et al. (2017). A review on bio-based lubricants and their applications. J. Clean. Prod. 168, 997–1016. doi: 10.1016/j.jclepro.2017.09.106
Tada, Y., Harada, M., Tanigaki, M., and Eguchi, W. (1978). Laser flash method for measuring thermal conductivity of liquids—application to low thermal conductivity liquids. Rev. Sci. Instrum. 49, 1305–1314. doi: 10.1063/1.1135573
Tang, H.-Z., and Jao, T.-C. (2013). “Dispersant additives,” in Encyclopedia of Tribology, eds. Q. J. Wang and Y.-W. Chung (Boston, MA: Springer), 771–781.
Tang, T. H.-Z., Devlin, M., Mathur, N., Henly, T., and Saathoff, L. (2013). Lubricants for (Hybrid) electric transmissions. SAE Int. J. Fuels Lubr. 6, 289–294. doi: 10.4271/2013-01-0298
Tazume, K. (2016). Oil Circulation System for Electric Motor in a Hybrid Electric Vehicle. Washington, DC: U.S. Patent and Trademark Office.
Tehrani, G. M., Kelkka, J., Sopanen, J., Mikkola, A., and Kerkkänen, K. (2016). Electric vehicle energy consumption simulation by modeling the efficiency of driveline components. SAE Int. J. Commer. Veh. 9, 31–39. doi: 10.4271/2016-01-9016
Tischmacher, H., Gattermann, S., Kriese, M., and Wittek, E. (2010). “Bearing wear caused by converter-induced bearing currents,” in IECON 2010 - 36th Annual Conference on IEEE Industrial Electronics Society (Glendale, CA). doi: 10.1109/IECON.2010.5675212
Vladescu, S.-C., Marx, N., Fernández, L., Barceló F, and Spikes, H. (2018). Hydrodynamic friction of viscosity-modified oils in a journal bearing machine. Tribol. Lett. 66:127. doi: 10.1007/s11249-018-1080-4
Vozár, L., and Hohenauer, W. (2004). Flash method of measuring the thermal diffusivity. A review. High Temp. High Press. 36, 253–264. doi: 10.1068/htjr119
Walther, H. C., and Holub, R. A. (2014). “Lubrication of electric motors as defined by IEEE standard 841-2009, shortcomings and potential improvement opportunities,” in 2014 IEEE Petroleum and Chemical Industry Technical Conference (PCIC) (IEEE: San Francisco, CA).
Wang, X., and Wang, Z. (2008). “Particle effect on breakdown voltage of mineral and ester based transformer oils,” in 2008 Annual Report Conference on Electrical Insulation and Dielectric Phenomena (Quebec, QC: IEEE). doi: 10.1109/CEIDP.2008.4772859
Wang, Y., Jones, S., Dai, A., and Liu, G. (2014). Reliability enhancement by integrated liquid cooling in power IGBT modules for hybrid and electric vehicles. Microelectron. Reliabil. 54, 1911–1915. doi: 10.1016/j.microrel.2014.07.037
Willwerth, A., and Roman, M. (2013). “Electrical bearing damage — a lurking problem in inverter-driven traction motors,” in 2013 IEEE Transportation Electrification Conference and Expo (ITEC) (Michigan, IN). doi: 10.1109/ITEC.2013.6573484
Xie, G., Cui, Z., Si, L., and Guo, D. (2017). Destabilization of lubrication oil micropool under charged conditions. Ind. Lubr. Tribol. 69, 59–64. doi: 10.1108/ILT-11-2015-0184
Xie, G., Luo, J., Guo, D., Liu, S., and Li, G. (2013). Damages on the lubricated surfaces in bearings under the influence of weak electrical currents. Sci. China Technol. Sci. 56, 2979–2987. doi: 10.1007/s11431-013-5399-7
Xie, G., Luo, J., Liu, S., Guo, D., Li, G., and Zhang, C. (2009a). Effect of liquid properties on the growth and motion characteristics of micro-bubbles induced by electric fields in confined liquid films. J. Phys. D Appl. Phys. 42:115502. doi: 10.1088/0022-3727/42/11/115502
Xie, G., Luo, J., Liu, S., Guo, D., and Zhang, C. (2009b). “Freezing” of nanoconfined fluids under an electric field. Langmuir 26, 1445–1448. doi: 10.1021/la903419v
Xie, G., Luo, J., Liu, S., Zhang, C., and Lu, X. (2008a). Micro-bubble phenomenon in nanoscale water-based lubricating film induced by external electric field. Tribol. Lett. 29, 169–176. doi: 10.1007/s11249-007-9288-8
Xie, G., Luo, J., Liu, S., Zhang, C., Lu, X., and Guo, D. (2008b). Effect of external electric field on liquid film confined within nanogap. J. Appl. Phys. 103:094306. doi: 10.1063/1.2917373
Xie, K., Liu, L.-C., Li, X.-P., and Zhang, H.-L. (2016). Non-contact resistance and capacitance on-line measurement of lubrication oil film in rolling element bearing employing an electric field coupling method. Measurement 91, 606–612. doi: 10.1016/j.measurement.2016.05.080
Yang, H., Liu, K., Wang, Y., Liu, H., Man, J., and Sun, B. (2017). Electronic controlling on nanotribological properties of a textured surface by laser processing. J. Spectrosc. 2017:7920652. doi: 10.1155/2017/7920652
Yang, Y., Ali, K. A., Roeleveld, J., and Emadi, A. (2016a). State-of-the-art electrified powertrains - hybrid, plug-in, and electric vehicles. Int. J. Powertrains 5, 1–29. doi: 10.1504/IJPT.2016.075181
Yang, Y., Bilgin, B., Kasprzak, M., Nalakath, S., Sadek, H., Preindl, M., et al. (2016b). Thermal management of electric machines. IET Electr. Syst. Transp. 7, 104–116. doi: 10.1049/iet-est.2015.0050
Yu, Z.-Q., and Yang, Z.-G. (2011). Fatigue failure analysis of a grease-lubricated roller bearing from an electric motor. J. Fail. Anal. Prev. 11, 158–166. doi: 10.1007/s11668-010-9422-z
Yusaf, T. F. (2009). Diesel engine optimization for electric hybrid vehicles. J. Energy Resourc. Technol. 131:012203. doi: 10.1115/1.3068347
Zhang, Y. (2006). Boundary lubrication—an important lubrication in the following time. J. Mol. Liquids 128, 56–59. doi: 10.1016/j.molliq.2005.12.002
Keywords: electric vehicles, hybrid vehicles, lubricants, energy efficiency, electrical properties of lubricants, thermal properties of lubricants
Citation: Chen Y, Jha S, Raut A, Zhang W and Liang H (2020) Performance Characteristics of Lubricants in Electric and Hybrid Vehicles: A Review of Current and Future Needs. Front. Mech. Eng. 6:571464. doi: 10.3389/fmech.2020.571464
Received: 10 June 2020; Accepted: 02 September 2020;
Published: 14 October 2020.
Edited by:
Valentin L. Popov, Technical University of Berlin, GermanyReviewed by:
Mitjan Kalin, University of Ljubljana, SloveniaCopyright © 2020 Chen, Jha, Raut, Zhang and Liang. This is an open-access article distributed under the terms of the Creative Commons Attribution License (CC BY). The use, distribution or reproduction in other forums is permitted, provided the original author(s) and the copyright owner(s) are credited and that the original publication in this journal is cited, in accordance with accepted academic practice. No use, distribution or reproduction is permitted which does not comply with these terms.
*Correspondence: Hong Liang, hliang@tamu.edu
†These authors have contributed equally to this work
Disclaimer: All claims expressed in this article are solely those of the authors and do not necessarily represent those of their affiliated organizations, or those of the publisher, the editors and the reviewers. Any product that may be evaluated in this article or claim that may be made by its manufacturer is not guaranteed or endorsed by the publisher.
Research integrity at Frontiers
Learn more about the work of our research integrity team to safeguard the quality of each article we publish.