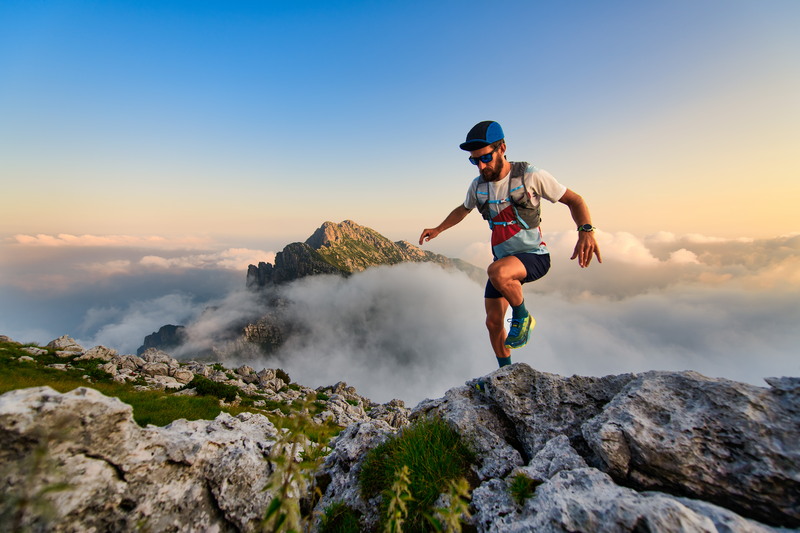
95% of researchers rate our articles as excellent or good
Learn more about the work of our research integrity team to safeguard the quality of each article we publish.
Find out more
REVIEW article
Front. Mech. Eng. , 20 October 2020
Sec. Tribology
Volume 6 - 2020 | https://doi.org/10.3389/fmech.2020.571786
This article is part of the Research Topic New Developments in Vehicle Thermal Management View all 6 articles
Global automotive industries have recently switched development trends from the traditional powertrain mechanical components into the digital transformation of the electrification components in advanced propulsion vehicles. This industrial impact on global development trend into automotive electrification designs has created an emerging technology for new propulsion systems such as hybrid electrical vehicles (HEV) or electrical vehicles (EV). Advanced propulsion systems rising from global guidelines are meant to improve vehicle fuel efficiency and minimize pollution emissions from transportation vehicles. In many HEV or EV advanced system designs, automotive lubricants such as drivetrain fluids or thermal coolants comes into contact with the integrated electric motor (e-motor) and thermal management devices. This leads to the addition of electrical and thermal properties, which must be taken into account on top of conventional lubricant properties. The introduction of electrification components has been targeted for energy efficiency and long-term durability. Automotive industries have asked for the implementation of specialized automotive lubricants or driveline fluids to allow for appropriate thermal cooling specifications, present bearing protection, ensure corrosion protection, and offer oxidation and sludge control. This review paper will provide with global insights on future automotive electrification growth trends with respect to innovative driveline lubricants and thermal cooling liquids used in Hybrid/EV vehicles. Coming research activities in innovative driveline fluids will be focused on minimizing friction loss and maximizing hybrid component durability. The major goal of this paper is to underline the future electrification development trends and the required lubricants for advanced Hybrid/EV vehicles. The major section of this paper will be focused on the most important progress of automotive lubrication in the areas of energy conversion effectiveness, driveline trustworthiness, cooling system design and thermal management control. In this review paper, new developments in thermal management fluids have been described to help promote the high-performance cooling system on electrical batteries, motors, and power electronics. In addition, global research activities using novel nanofluids for thermal cooling have the high potential for application to EV/Hybrid technologies. This paper has reviewed the state-of-art thermal management technology used for extending driving range and durability of EV/Hybrid vehicles. At the end of this paper, using high promising nanofluids for thermal cooling in fuel cell components will be illustrated to demonstrate this potential application in EV/Hybrid vehicles.
The elevated impact on the global environment due to greenhouse gas emissions has placed a demand on decreasing those said emissions. This led to significant new technical innovation for automotive industries to improve engine efficiency using the electrification components for replacement of traditional mechanical components. Innovation of Electrical Vehicles (EV) and Hybrid-Electrical Vehicles (HEV) has resulted in the advancement of propulsion system for improving their fuel economy and emissions benefits (Tung and Wong, 2018; Society for Tribologists Lubrication Engineers (STLE) 2020 Report, 2020). An HEV operates through a collection of an internal combustion engine and an electric motor. A differentiating advantage for the HEV is the capability to stop the IC engine when the power source from the electrical system goes over the requirements for propelling the vehicle (Tung, 2019a,b). This special feature will result in an overall lower operating temperature of the IC engine and increased frequency of the intermittent on-and-off control of the engine. However, sludge and varnish formation were vastly inferior for the hybrid vehicles. In addition, the smaller hybrid engine providing power over a relatively wide speed range will be running at a significantly higher temperature with a higher power density requirement. Therefore, driveline and lubrication technology are very crucial for HEV energy efficiency and durability performance requirements.
While hybrids can still use traditional driveline fluids for normal operation, however, OEM manufactures have requested to develop advanced driveline fluids for protection from wear and ensuring the proper functioning of the hybrid electrified drivetrain parts. Recently global OEMs (Tung and Wong, 2018; Tung, 2019a,b; Society for Tribologists Lubrication Engineers (STLE) 2020 Report, 2020) have highlighted three main considerations: (1) electrical conductivity of fluids and related safety concerns, (2) corrosion protection, and (3) thermal cooling and hardware material compatibility. The advanced drivetrain configuration developed by OEMs (Tung and Wong, 2018; Tung, 2019a,b; Society for Tribologists Lubrication Engineers (STLE) 2020 Report, 2020) have allowed the hybrid engine to operate over a much more expanded range of operating parameters. The power split unit, which doubles capability of the drivetrain configuration, consists of a planetary gear set, generator, electric motor and an oil pump. In contrast to conventional drivelines connection with internal combustion engines, advanced lubricants in hybrid electrified drivelines will subject to an additional load from electrostatic sparks and magnetic currents. The need of specific driveline fluid comes into play due to higher system voltages, a greater presence of copper materials, higher temperatures and speeds, and varying friction requirements. Thus, superior lubrication technology is of utmost importance in maintaining the high energy efficiency and system reliability of HEV and EV vehicle operations.
Performance characteristics of advanced driveline fluids specified for hybrids and EVs require appropriate electrical properties, warrant protection from corrosion and be able to work with insulating materials. In addition, all hybrids and EVs components require a better thermal transfer characteristic, high-speed bearing protection and oxidation and sludge control for engineering applications. The technical issues of driveline lubricants used in EV/Hybrid configuration need to be investigated. In addition, future demand for advanced transmission and driveline fluids will be not only minimizing friction loss but also maximizing component durability. Advanced driveline fluids are required to improve the drivetrain efficiency and be compatible with the other components such as pumps for energy efficiency, prevention of internal leakage, and extended clutch durability. In addition, EV or HEV drivetrain components include an electric motor (e-motor), a transmission, gear box, and/or a hydraulic unit. In various hybrid vehicles designs, the drivetrain fluid, also known as the electric transmission fluid (ETF), will be utilized to support the driving performance and endurance demands of electrification machineries. Therefore, the design of ETFs will need to accommodate a broad range of technical attributes, compared with the more conventional drivetrain components. This future design trend to match with hybrid configuration has created a substantial challenge for electric transmission fluid design for automotive and lubricant industries.
There are two considerations (OECD, 2019; Tung, 2019a,b), which it should be considered, when it comes to the electrical conductivity of fluids. A high electrical conductivity of the liquid leads to a higher chance of current leaking. Conversely, if it is too low then the accumulation of static charge will oxidize the lubricants due to electrical arcing. As a result, the protective features of the fluid will be greatly reduced.
Lubricants are not electrically conductive, but rather dissipative, though lubricant additives can affect the level of electrical conductivity. If specific lubricant additives can increase electrical conductivity, however, electrical conductivity can cause oil oxidation and deterioration. According to OEMs bench testing results (Tung and Wong, 2018; Tung, 2019a,b; Society for Tribologists Lubrication Engineers (STLE) 2020 Report, 2020), not only does the lubricant need to adapt to hybrid and electric vehicles but also with the testing methods. More advanced corrosion deposition tests need to be developed in response to the electrical components, volatile conductivity, and temperature changes of hybrid architectures. Furthermore, the OEM industry ought to implement a wire corrosion test (OECD, 2019; Tung, 2019a,b) because electrical components due to strayed voltages or energized circuits can promote corrosion that would normally not occur. In addition, more testing development programs such as the standard tests for dielectric breakdown voltage of insulating liquids and electrical conductivity of liquid hydrocarbons have been organized by the ASTM (OECD, 2019; Tung, 2019a,b).
Recently advanced driveline technological development is moving to apply the efficient dual clutch transmission for improving drivability. The EDCT (Electrical dual clutch transmission) (OECD, 2019; Tung, 2019b; United Nations Environment, 2019) composes of two motors rather than a twin clutch for smooth shifting. Due to the complications of the electrical components and wiring, a gearbox fluid must have copper corrosion protection and properly associated with insulation materials. Furthermore, an equilibrium must be reached between having a lubricant that has a low enough viscosity to preserve optimal energy efficiency, but not too low to still be able to have a protection of bearings and other mechanical parts.
The growth of many sophisticated automotive technologies is encumbered by the demand for thermal cooling of the electrical components. The traditional method for cooling has reached its threshold. The current cooling system is transferring heat from the engine to the coolant /water in the water jacket. Then the coolant will reach the radiator by heat transfer tubes, and the hot temperature coolant will be cooled. However, the thermal cooling of advanced driveline components needs to be enhanced by the other components such as electric motors and E-drive configuration. Electrification components including electric motors or regenerative brake components have been integrated in this advanced configuration with thermal management system for cooling applications. The electric motors and power electronics will be in contact with the coolants. Thermal coolants are required to cool the motors and power electronics by removing heat for better thermal management. In addition, automotive lubricants for electrified propulsion system needs to function as an effective coolant, provide corrosion protection to copper windings, composites, and rare earth magnetic materials while maintaining wear and oxidation protection.
New applications in thermal management (Tung, 2019a,b) are helping extend the driving range and lifetime of EV/Hybrid. In addition, the higher working temperatures of hybrid engine can generate extensive wear among the higher loading parts compared with the conventional driveline components. This will create a loss in fuel efficiency and ultimately seize the engine. To prevent this problem, there was a need for an advanced thermal cooling system.
Global research activities using novel nanofluids for thermal cooling have the high potential for cooling technologies (Tung, 2019a,b). This review paper will review the high-tech thermal management technology in EV/Hybrid vehicles using novel nanofluids for thermal cooling. Nanofluid, a novel grade of thermal cooling liquids created by the dispersion of solid particles between 20 and 60 nm in size in traditional water- or oil-based fluid (Tung, 2019a,b). The nano particles have larger surface area and help enhance the thermal cooling properties of the fluid. In addition, the suspended nanoparticles remarkably improve thermal cooling process and the nanofluid has significantly higher heat conductivity and heat transfer coefficient than the conventional coolant used in conventional automotive cooling system. Recent testing results (Tung, 2019a,b) have indicated that these new nanomaterials have high potential to promote high thermal conductivity nanofluid materials for thermal cooling applications in the future EV/Hybrid vehicles.
Energy is the prime mover for virtually all activities of existence, levels of prosperity and lifts billions of people out of poverty. On the other side of this medal, this is fueled by a relentless demand for natural resources. Today, energy is an integral catalyst inherent in every social, economic and environmental faction of human advancement. Energy serves as an invaluable aspect to economic prosperity. While energy services contribute to better living and environmental conditions, as well as aiding social development via public health and education. In addition, energy services are integral to meeting the most fundamental of human needs such food and shelter, as well as making possible the loftiest of human innovation and technology. While energy is a blessing in innumerable ways, there is always a potential downside to everything. Excessive use of energy and resources raises carbon tracks and pollution. However, poor execution of the energy supplies can harm the environments. The intricate interplay between energy usage and human growth is symbiotic, nuanced and multifaceted. We will endeavor to unravel this complex relationship in this article.
There have been many attempts, some more successful than others, to balance the demand for energy and the pernicious consequences that can result from designing machinery and instruments which are still able to fulfill society's wants while concurrently decreasing our reliance on fossil fuels. It is the mission of the designer to endeavor to span this gap between these two divergent polarities, which must find a way to coexist. A main component of achieving this objective is the achievement of reduction of wasteful systemic losses through wear and friction, which take a substantial toll on the performance of these machines. Identifying the components of a technology that has the most pronounced effect on the ecosystem is an alternate route to attempt to decrease or completely offset this impact.
The importance of tribology for the global society is as follows:
a. Economical losses due to wear, and also friction,
b. CO2 emissions due to friction (consumption of energy) and
c. Material footprint through the consumption of resources, which also include CO2 emissions.
The second aspect represent the consumption of resources for making consumer goods, housings or any machineries, which is so far not in the radar of politics and publics. OECD (2019) estimates, that the global raw material extraction will increase from 92.1 billion of metric tons (MT) in 2017 to 167 billion of MT until 2060 (United Nations Environment, 2019). It is clear that any material consumption generates CO2 and greenhouse gas emissions, including electric vehicles, internal combustion engines and lubricants.
In the last few years, a growing cognizance as to the malignant effects of chlorofluorocarbons (CFCs) as refrigerants to ozone layer and chlorinated hydrocarbons in metal working fluids, lead and Sulfur in fuels and more, has subsequently resulted in these toxic substances being banned. Therefore, scientists have had to invent or implement alternative materials and solutions to sustain the low friction, functionalities and reliability counted on from the components indicated. It is for this reason that the designer must grapple with the difficulties of both needing to diminish systematic losses, while many times concomitantly creating less detrimental options in place of the environmentally harmful lubricant practices currently in existence.
It is necessary to deal with the corrosion losses, robustness, reparability, and condition monitoring of the primary elements of a mechanical system, but in order to do so it is fundamental to possess a cogent grasp of the engineering and science buttressing their function. This is where the science of tribology comes into play (Jost, 1966). The environmental and economic benefits potential are enormous and global regarding tribology in the reduction of total worldwide carbon emissions by lower friction (Woydt et al., 2020) and longer use of resources or reduced wear. The huge significance of tribology as interdisciplinary science for national economics was demonstrated in 1977 by The American Society of Mechanical Engineers (economic savings of >2.8% of GDP) and in 1976 by the German Federal Ministry of Research and Development (economic savings of >2.0% of GDP), following an in-depth overview of the results of a comprehensive 2-years study conducted 2006 in China by the Chinese Tribology Institution (CTI), which encompassed six countries and demonstrated a conservative estimated savings of 41.4 billion of per year (Zhang and Xie, 2009), at prices of 2006, or equivalent to savings of 1.55% of Chinese GDP.
The prime catalysts of the technological progress of tribology are built in future upon the notions of sustainable or “green” tribology or “Zeronize” (Toyoda, 2007). The definitions and opinions are in flux in industry and science. They can broadly be described as the philosophy of the tribological facets of environmental equilibrium and biological results:
a. Durability and longevity of products reduce the material footprint, which always include CO2 emissions.
b. The reduction of friction saves energy sources and CO2.
The general assembly of United Nations has adopted in October 2015 17 sustainable development goals (SDG), which represent a globally accepted frame defining “sustainability” (United Nation General Assembly, 2015). This is imperative for environmental or energy sustainability while concurrently focusing on reducing the wide range of energy drains, while simultaneously addressing economic issues, since a significant amount of capital could be salvaged through improvements made to the mechanical components.
There was recently as assessment conducted on fundamental tribological study, which shed light on environmental issues including biodegradability and eco-toxicity, when it comes to the vanguard of production in the area of tribo-materials for maximum sustainability.
Tribological design is also of great importance regarding the primary IC engine components. In fact, 1.300 billion vehicles were registered for use globally, in 2018, with a further 95–100 million cars produced worldwide annually. If mechanical losses could be reduced with tribology, even 10% could mitigate fuel usage by 1.5% equaling about 340 l of petrol throughout the duration of a car's lifespan. With this in mind, it is glaringly evident that these seemingly insignificant reductions ($350 per vehicle), when translated to the huge quantity of running cars extant today, the fiscal savings and environmental advantages would amount to something great.
In addition, the dependability and longevity of mechanical parts will be aided by keeping increasingly extensive and even more accurate tribological data. It has been posited that experimenting of materials when put in situational proximity and environments is currently the most accurate means of procuring fundamental tribological data regarding management. The tribological approach to designing the systems cannot be overstated. It is believed, and backed up by current research and empirical evidence that the correct amalgamation of tribological know-how, electrical and mechanical engineering will facilitate the design tribologist to stretch the versatility of the tribology of renewable energy including wind and tidal turbines, illuminating the necessity of sturdiness and design to these massive engineering entities so that maximum potential of this environmentally-conscious energy source can be fulfilled by consistently and efficiently. Furthermore, chemical means of analysis must be accounted for as well when regarding the concept of sustainable tribology. A particular emphasis should be placed on developing, ameliorating and implementing green lubricants, adhesives and waxes.
Yet another sustainable consideration is waste management and plastic recycling, which has several advantages, such as the minimization of CO2 tracing, energy consumption reduction and oil conservation by converting plastic to fuels and lubes. The majority of plastic are comprised of crude oil, which represents 4% of the overall oil expenditure. Moreover, the entire quantity of waste which ends up being burned in landfills can be lessened tremendously by recycling. Most thermoplastics, like polyethylene and polypropylene, can be recycled and are recycled, but packaging for food have a complex structure and are multi-layer composed, which make recycling impossible. Alternatives are hard to find and nobody wants to miss the hygiene and expiry benefits for foods and pharmacies. For these is after usage the only strategy “plastics to fuel” or “plastics to lubes.” Other aspects for polymeric materials (“plastics,” and is not just a decorative nuisance on the wheels, is the generation of fine dust from brakes and tires. Long lasting brake pads and tires will limit these emissions fine dust/particulates but have a conflict with the spare part business.
Finally, if the field of tribology is going to fully enter the 21st century and realize its full power and potential, then the employment of natural resources must be undertaken in a realistic and economically savvy manner, if suitable raw materials are going to be developed via ecologically-conscious chemistry to produce cutting-edge adhesives, waxes, fuels and lubricants which is one of the most challenging aspects of this area which will be grappled with in the next decade.
The availability and affordability of resources may in general overrule the CO2-question. Petrochemical companies engage themselves more and more in wind and solar parks, re-refining, charging stations, hydrogen, methane, etc., because the overall target is not to prohibit fossil energy, but to provide CO2 or greenhouse gas neutral energy! They seem now to be ready to embrace the CO2 & sustainability issue as oil demand will peak by the early 2030s.
Each company and everyone in the public have their own view, perception and definition of sustainability, but is recommended to use the SDGs of the United Nation as orientation. Sustainable lubricants differ from the so-called “environmentally acceptable lubricants” (EAL) or “biolubes” (see EN16807). The most important schemes are:
a. European ecolabel as per EC/ 2018/1702,
b. Second issuance of U.S. Vessel General Permit and
c. Biolubricants as per EN16807.
EAL focus on human and environmental toxicology, when the fluids enter into the aquatic environment as well as some of the EAL schema require a content of renewables and respond to the SDG number 3.9 “reductions of hazardous chemicals and air, water and soil.” The accepted test methods, set limits and methodologies used differ for the “bio-no-tox” -properties, but all have common of a rapid ultimate biodegradation (full mineralization) or in other words, as short persistence in the environment, associated with low aquatic toxicities against the species of daphnia, algae and fish as well as of different levels of a renewable content. Esters, polyglycols and bio-olefins met these criteria.
Sustainable lubricants will consider:
d. the CO2 emissions during the whole lifecycle, even the resource is renewable;
e. the consumption of resources in respect of lifetime;
f. have extended drains.
The lifecycle analysis (LCA) of palm and soja oil is disadvantageous in respect to fossil resources (The Delegated Act on low/high ILUC Biofuels, 2019) and palm oil is no longer considered as a renewable resource.
With the increased focus on environmental friendliness, Original Equipment Manufacturers (OEMs) are invested in pushing for “the electrification of the powertrain” to reduce CO2 emissions. Hybrid vehicles have been taking monumental leaps in global interest for incorporating both gears (ATF fluids) and electric motors as the importance of emission reduction and is scrutinized on a magnifying glass by the EPA. Forecasted to 2040, the global light-duty vehicle (LDV) market expects a significantly strong growth in e-mobility from hybrid vehicle sales. However, hybrid vehicles are novel and upcoming and has a long journey to develop, especially in order to reduce costs and the keep the added values within the automotive manufacturers. Especially in the sustainability department since ICE vehicles are still dominant and hybrid vehicles yet have a dedicated transmission fluid. Figure 1 depicts the projected sales for different propulsion technologies in relation to the main applications.
Figure 1. Estimated technology penetration in urban and intercity bus and minibus stocks worldwide by scenario, 2015-2060 [International Energy Agency (IEA), 2017].
Hybrid cars are divided into three categories: mild hybrid, full hybrid, and plug-in hybrid and five architectures: parallel, series, power split, through the road, and complex. Each of these architectures have a transmission that is unique to the system which calls for unique corresponding fluids. With an integrated electric motor and transmission, the dedicated fluid will need to comply to electrical properties while maintaining thermal cooling and corrosion prevention properties. The lubricants must also be adopted to high-speed reduction gears. Electrical systems typically operate above 48 V compared to 12 V for standard engines. The fluid must balance between conducting and insulating electrical currents. High conduction risks current leakage would be vastly dangerous for anyone who contacts the charged parts. An effective insulating fluid could potentially trigger static electricity build-up and spark discharges, which can be damaging for the equipment and oxidizes the fluids. Therefore, thermal resistance and insulation is salient for a durable operation.
Lithium greases have been ubiquitously used as lubricants for ICE vehicles due to their many beneficial properties including long life, high dropping point, corrosion protection, and moisture resistance (Andrew, 2019). These greases can commonly be used in EV for lubricating door locks and hinges, but have here dry solid bonded films as a strong competitor. However, with the inclusion of an electric motor, dedicated lubricants need to fulfill different requirements for properties such as noise, efficiency (low friction), dielectric properties, and compatibility with the electrical components (Andrew, 2019). Vehicle noise derives heavily from the engine of ICE vehicles at low speed, whereas tires and wind dominate at high speeds. Excessive traffic noise can cause hearing damage and even cardiovascular diseases (Toubeau, 2019). Electric motors are steadier and produces less noise than ICE but nonetheless, require an appropriate grease to mitigate this issue. Noises generated from air flow around the car body and tires also remain for EVs. Figure 2 displays the difference in noise between ICE vehicles and EV.
Figure 2. Noise difference between ICE vehicles and EV (Salleh et al., 2013).
Efficiency is another area of focus and correlates directly to the torque properties of EV. Reducing friction in the electric powertrain increases the usable torque through the development of low viscosity lubricants will push EVs to dominance in the auto industry (Andrew, 2019). Through various tests, friction was successfully reduced by lowering viscosity from ν100∘C= 5.5 centistokes to ν100°C= 4.5 centistokes fluids with strong hope for further lower numbers in the future. However, the formulated grease must refrain from altering tensile strength and crack resistance, which requires many trial tests to balance the properties (Andrew, 2019).
In addition, we have discussed another important application of driveline lubricants or greases to be used for thermal cooling and lubrication besides the tribological performance characteristics. With the incorporation of electric motors in the transmissions of hybrid and electric vehicles, major considerations have been emphasized on the capability of the driveline fluids with specific thermal properties to remove heat for thermal cooling purpose. Even the temperatures of the driveline fluids in these electrified transmissions components are expected to be controlled under a temperature range of 160–170°C. The capability to remove heat from the electric motor directly impacts the electrical motor durability, thermal efficiency, and the driving range of hybrid vehicles.
Other than for performance purposes, the developing lubricant needs to be well-matched with the electrical components including electric modules, polymeric insulations, sensors, and circuits1. The electric motor generates heat and inductive currents that must be insulated from the electric modules. Myriad cooling concepts and thermal management requirements will need to be considered when developing a compatible lubricant. The most popular lubricants today include mineral-based oils with different additives and synthetic-based oils (PAO, esters and PAGs) due to their improved lubricity and thermal and oxidative stability (Farfan-Cabrera, 2019). Table 1 displays the performance grades of these lubricants.
Table 1. Lubricant performances (Benedicto et al., 2017).
Other than EV, the growth of hybrid electric vehicles also requires dedicated lubricants and functionalized coolants. When a combustion engine with an electric motor, there are concerns regarding heat and aging stability (Andrew, 2019). Strong insulation properties will need to be create a viable lubricant.
Various lubricant tests are performed to ensure specifications are met. Oil viscosity is developed according to load, speed, and operating temperature of the application (Andrew, 2019). While viscosity should be reduced to minimize friction loss, too low of a viscosity hinders durability and causes the lubricant to leak out of the bearings. This brings to play oxidation properties and dropping point when undergoing extreme temperatures. Oxidation, enhanced by spark discharges, deteriorates the oil and increases the chances of sludge buildup, which hinders thermal control from the motor. Additives are added to modify these properties, but some may be counterintuitive and shorten the life span of the grease. Lastly, the lubricant must maintain electrical properties such as volume resistivity, dissipation factor, and dielectric strength to avoid electrical losses in the system (Andrew, 2019). Overall, the lubricant must be formulated to balance all these requirements. Table 2 depicts specific properties that must be tested today.
Fretting (micro-movements) in tribosystems will also become more important. ASTM offers other basic lab test methods as shown in Table 3 for specific properties related to electric fields, which have yet to be reviewed and assessed for lubricants used in electric vehicles. There is also an additional need for further test methods.
Recent research for the development of these oils and greases incorporates nano technology (carbon nanotubes and nanoparticles) to strengthen the product (Farfan-Cabrera, 2019), but these oils and greases must have a functional competition with “additive chemistries.” Recently, spherical alumina nanoparticles have been tested to aid friction reduction as well (Farfan-Cabrera, 2019). Also, the addition of synthetic oils and titanium complex thickeners have been viable in reducing friction torque and increasing the lifespan of greases (Farfan-Cabrera, 2019). Specifically, sulfur and phosphorus gear oil additives are commonly used to lower wear. Other than incorporating additives and polymers, laser surface texturing has been implemented to coat the gear teeth (Farfan-Cabrera, 2019). Coatings on gears made by thermos-chemical treatment, like double glow plasma alloying with tungsten-molybdenum and plasma nitriding or thin film coatings, like tungsten doped diamond-like carbon (DLC) and tungsten doped diamond-like carbon (DLC) deposited on chromium nitiride (CrNx), molybdenum nitride (MoNx) have been applied as well, all of which have shown improvements in reducing friction and wear (Farfan-Cabrera, 2019). As for corrosion protection, boron compounds have been promising in enhancing corrosion preventive and severe pressure properties as well as oxidation and cooling (Farfan-Cabrera, 2019). Figure 3 illustrates a myriad of tribo-components to monitor.
Figure 3. Tribo-components of EV (Farfan-Cabrera, 2019).
With growing concerns over the environment and sustainability, biodegradability and reduced toxicity are a trending development. Bio-lubricants can be formulated based on animal fats, vegetable oils, esters, polyglycols and even low viscosity PAOs as well as are effective alternatives to mineral oils due to their physicochemical properties (Farfan-Cabrera, 2019). The polarities in the molecular backbones of most bio-lubricants have been shown to display enhanced lubrication compared to other typical oils. However, it lacks thermal and oxidative stability limiting it at extreme temperatures (Farfan-Cabrera, 2019). Figure 4 shows the past and projected biolubricant market revenue in the U.S.
Figure 4. U.S. biolubricant market revenue from 2014-2024 (Millions of US-$) (Jackson, 1970).
This issue can be alleviated through adding of electrically conductive nanoparticles or advanced polymers such as rubber, polypropylene, and methyl pentene, which all showed promising results in high speed applications (Farfan-Cabrera, 2019). Additives such as antioxidants and pour point depressants and chemical modifications such as transesterification and epoxidation have also contributed to alleviate those issues (Farfan-Cabrera, 2019). Currently, the most efficacious grease additives include 3% MoS2 and graphite and future prospects for bio-lubricants include resources, like microalgae and non-edible oil seed crops, specifically for grease soaps, hydroxy-fatty acids from Jatropha carcass, Calophyllum inophyllum, Pongamia pinnata, Hevea brasiliensis (rubber seed), Ricinus communis L. (castor oil), and Simmondsia chinensis (Spaltmann et al., 2010). Figure 5 highlights the commonly used additives market volume.
Figure 5. U.S lubricant additive market volume (Farfan-Cabrera, 2019).
As EV are becoming mainstream, dedicated EV lubricants follow evidently. However, these lubricants are still in development stages, which brings uncertainty for the future. With the stable growth in lithium greases, dedicated lubricants will be challenged as well. Lithium for greases competes with lithium inevitably needed for batteries. Lithium hydroxy stearate is therefore not mandatory the preferred choice for soaps in greases.
However, the growing optimism and strong push for environmental friendliness make the development of EV lubricants more of a reality than mere pipe dream. The question now is when will these lubricants be developed and how grandeur will EV prosper.
Major technology Issues will be summarized as follows:
1) Material compatibility
2) It must have appropriate thermal transfer characteristics, offer high-speed bearing protection and
3) deliver oxidation and sludge control.
4) Thermal cooling requirements and durability requirements
5) Electrification requirements
6) It must have appropriate electrical properties, be protected from corrosion, and compatibility with
7) insulating materials.
8) Base stock requirements (synthetic base stock) and low viscosity grade.
1. Emulsification and corrosion
Depending on drive cycle, the engine lubricants operating in hybrid vehicles may only run for very short periods of time (imagine a hybrid vehicle with a 38-mile, in an all-electric range, which is driven by a person with a 40-mile daily commute. The engine only runs for a couple minutes per day. Fuel dilution and water will collect and form acids. It may also lead to high wear rate and more prevalent in HEVs.
2. Buidup of moisture in engine oil during cold weather combined with short driving cycles.
3. New contaminants from cooled and/or dedicated EGR
Electrification may lead to the simplification of the ICE, moving away from turbocharging and even GDI. It uses a simple PFI engine operating with an Atkinson cycle, and uses cooled EGR. Both could potentially increase/accelerate oil degradation and lead to deposit issues and potentially high wear (Benedicto et al., 2017; Farfan-Cabrera, 2019)1.
Future demand for advanced transmission and driveline fluids will be not only minimizing friction loss but also maximizing component durability. Performance characteristics of these driveline fluids are required to protect the function of transmission efficiency and the other components such as pump efficiency, internal leakage, and clutch durability.
Besides tribological performance benefits using advanced driveline lubricant in EV/hybrid applications, automotive industries claimed that EVs might require new gear oil additives and performance tests for measuring wear protection under EVs' high-load/lower-temperature operating conditions. A new class of driveline lubricants (Farfan-Cabrera, 2019; Tung, 2019a,b)1 needs to be developed to improve gear efficiency and performance, lower operating temperatures and extend the driving range and driveline durability. Moving to a lower viscosity reduces churning and pumping losses, increasing efficiency. Gearbox churning losses are typically reduced with lower viscosity lubricants. However, in some cases churning losses increase as viscosity is lowered. Especially at high speed operation, churning losses seem to more pronounced for design engineers. In addition, the most common option for gear box application is to use high-performance synthetic gear oils; these oils have potential to reduce friction and wear further using new additive technology. This new class of synthetic oils can be used for developing E-drives with minimal friction and better driveline durability.
Concerning fuel economy benefits, automotive driveline lubricants of EV/hybrid are not specifically designed for only fuel economy purpose. In many HEV or EV advanced system designs, automotive lubricants such as drivetrain fluids or thermal coolants comes into contact with the integrated electric motor (e-motor) and thermal management devices. This leads to the addition of electrical and thermal properties, which must be taken into account on top of conventional lubricant properties. The introduction of electrification components has been targeted for energy efficiency and long-term durability. Automotive industries have asked for the implementation of specialized automotive lubricants or driveline fluids to allow for appropriate thermal cooling specifications, present bearing protection, ensure corrosion protection, and offer oxidation and sludge control. As mentioned in our paper, the tribological performance (friction coefficient, wear rate, surface roughness parameters) of driveline fluids in the hybrid-electrical vehicles will depend on the hybrids' configuration (for examples, P1, P2, P3, P4, P5, etc.). Different hybrid configurations can influence on their tribological performance under the different operating conditions and testing parameters.
The following performance characteristics are crucial for future requirements for hybrid transmission and driveline lubricants:
• Energy efficiency improvements
• Higher speeds transmission applications (beyond six speed)
• Use of low viscosity fluids for fuel economy benefits
• Electrification compatibility (Hybrid, battery compatibility, plug-in, etc.)
• Use of light-weight materials (such as use of aluminum or composites materials)
• Start stop technology with integrated e-motor & duel clutch
• Advanced torque converter and clutch design for advanced driveline components
• Synchronizer designs and fuel-efficient bearings
• Low friction and wear-resistant coatings for enhancing tribological performance.
• Material compatibility for driveline durability requirements
• Thermal cooling requirements.
In our next section, the authors will review the current thermal management technology and their future challenges of electrical and thermal cooling characteristics in EV/Hybrid vehicles.
Fluids specifically designed for hybrids and EVs should include appropriate electrical properties to guarantee protection from corrosion and be well-suited with insulating materials (Farfan-Cabrera, 2019; Tung, 2019a,b)1. There are two additional considerations on electrical conductivity and thermal conductivity of fluids. If the electrical conductivity of the liquids exceeds a certain value, current leaking can occur. But, if it is too low, degradation of the oil can occur as a result of lubricant oxidation, a direct outcome of electrical arcing in oil and leads to the decrease in the protective ability of the fluid. Lubricants are not conductive, but rather dissipative, though additives can affect the level of electrical conductivity. Conductivity might increase, however, as oxidation causes an oil to deteriorate. Additive suppliers suggested lubricants susceptible to oxidation are potentially problematic. They also need to have appropriate thermal transfer characteristics, offer high-speed bearing protection and provide oxidation and sludge control.
Desired lubricant additive properties in HEV/EV (Tung, 2019a,b) have been grouped into the following table as shown in Table 4. All additive properties need to test their performance characteristics are compared with the other Fluids. The symbol “X” indicates the characteristics needed for the conventional driveline lubricants in manual or automatic transmission. The red region indicates new performance tests. which have been added in for the newly developed driveline fluids for modern HEV and EV with or without clutches (Tung, 2019a,b). This table has indicated that these newly developed tests such as electrical conductivity, thermal conductivity, extreme speed and bearing protection capability are crucial performance characteristics to meet hybrid or EV vehicles performance requirements.
Table 4. Desired lubricant additive properties in HEV/EV compared with the other Fluids (Tung, 2019a,b).
The heat generation rates in engine power controllers, computer chips and optical devices/systems are on the rise as a result of future development trends that favor higher speeds and smaller features for increased performance for engine components, microelectronic devices, and brighter beams for optical devices (Choi, 1995; Hu and Dong, 1998; Xuan and Li, 2000, 2003; Xuan and Roetzel, 2000; Choi and Eastman, 2001; Choi et al., 2001; Xie et al., 2003). Thermal cooling becomes one of the main focuses of the advanced industries such as microelectronics, transportation, manufacturing, and metrology. Electric hybrid and fuel cell vehicles use power electronics to control electric motor. Power electronics require their own cooling loop including: heat exchanger, pump, and radiator. Power densities exceeding 100 W/cm2 while needing to maintained below 125°C, may eventually exceed 250 W/cm2. Conventional cooling methods to promote heat rejection rates apply increased surface areas such as fins and micro-channels for heat dissipation. However, current thermal cooling designs have already reached its threshold. At present, advanced thermal cooling fluids such as nanofluids or nanographene (Eastman et al., 1999; Lee et al., 1999; Keblinski et al., 2002; Das et al., 2003; Xue et al., 2003; Yu and Choi, 2003) have been developed to achieve ultra-high-performance cooling (Eastman et al., 1999; Lee et al., 1999; Keblinski et al., 2002; Das et al., 2003; Xue et al., 2003; Yu and Choi, 2003). This review paper will describe the nanofluid applications with a high capability to enhance the fluid's thermal properties of hybrid vehicle and fuel cell thermal management in the next few sections.
For hybrid or electrical vehicles, the cooling requirements are more stringent than the IC engines, especially in the case of fast charging and heavy consumption. Lithium-ion batteries and EV motor system need to maintain the correct temperature range by cooling means. If they exceed this right range, batteries will face a “runaway,” not deliver the same power but more importantly, they degrade quickly. Power electronics are also very susceptible to heat, especially during recharging. Heat sinks are used to draw away the heat. The solutions for batteries are as follows:
a. Cooling circuits for batteries and fast charging cables or
b. Immersion of battery cells in a dielectric fluid.
Fast charging with powers above 270 kilowatts requires cooled cables. Assuming 4–5% of charging losses for a 100-kWh battery means, that during fast charging in 15 min 16–20 kW of power heats up the battery. In consequence, in 95-kWh battery 22 liters (5.8 US gal) of coolant circulate around the 40 meters (131.2 ft) of cooling pipes (see Figure 6)3.
Figure 6. Animation of the cooling circuit of the PORSCHE Taycan (courtesy: Porsche SE, Germany)2.
Dielectric fluids are electrically insulating. In consequence, they can come into direct contact with battery packs. The immersion of the batteries in the dielectric fluid cools by direct heat transfer at the “heat” source with no reliance on a secondary indirect cooling system. Silicone oils (polydimethyl siloxane) or PDMS), synthetic esters, fluorinated liquids or hydrocarbons are in use as insulating fluids. The technical constraints in electrified powertrains of vehicles require fluids with long lasting dielectric properties. Water contents deteriorate the insulating properties against arcing and shall remain below 50 ppm. Esters and secondary esters (estolides) offer high breakdown voltages associated with bio-no-tox-properties.
The projected growth of electric vehicles (EV) hybrid electric (HEV) in the automotive industries has made evolutional changes in propulsion system electrification components. Powertrain and driveline components will be enhanced by electric motors and E-drive configuration. Electrification components including electric motors or regenerative brake components will be integrated in this advanced configuration with thermal management system for cooling applications. The electric motors and power electronics will be in contact with the lubricant. Lubricants or coolants are required to cool the motors and power electronics by removing heat for thermal management. In addition, automotive lubricants for electrified propulsion system must function as an effective coolant, reduce corrosion of copper windings, composites, and rare earth magnetic materials while upholding wear and oxidation protection and energy efficiency.
The future development of thermal management technologies is encumbered by the urgent demand for thermal protection and cooling of the electrical components. The traditional method for thermal cooling can no longer be progressed. New requirements have been enforced for high performance cooling on electrical vehicles batteries, motors, and power electronics. New developments in thermal management of EV/Hybrid vehicles are helping extend the driving range and lifetime requirement. Global research activities using advanced coolants have the scientific merits and high potential application in thermal cooling technologies. In order to meet these thermal management requirements, automakers are using combinations of cooling fluids and advanced thermal cooling devices throughout the EV/Hybrid vehicle propulsion system to improve overall energy efficiency and coolant compatibility with electrification components. In the next few sections, the authors will review the state-of-art thermal management technology used for meeting thermal cooling and extended driving range requirements of EV/Hybrid vehicles.
Power electronics including power generation and operational equipment are the most critical components for higher efficiency and cooling needs. Increased system capabilities lead to higher densities and more waste heat! Selecting off the shelf thermal solutions is no longer a viable option for power electronics; Increasing thermal performance with minimal impact to system packaging and volume will become future trends that minimize operating cost and maintenance. Power electronics including power generation and operational equipment are the most critical components for higher efficiency and cooling needs. Increased system capabilities lead to higher densities and more waste heat. Selecting off the shelf thermal solutions is no longer a viable option for power electronics. Increasing thermal performance with minimal impact to system packaging and volume will become future trends that minimize operating cost and maintenance.
Recent development on thermal cooling methods (You et al., 2003; Wrenick et al., 2006; Tung, 2019a,b) can be classified into the following methods as shown in Figures 7 and 8:
1) Forced fluid convection: Using air can cool up to 10 W/cm2; this can be increased by using liquid such as water or glycol. Example: Aluminum heat sink and fan or pin finned heat exchanger with 50/50 water and glycol.
2) Jet-impingement cooling: A coolant fluid impinged perpendicular to the heat source at a high speed. This forms a thin boundary layer and allows heat to be removed more effectively.
3) Spray cooling: This can be an open or closed looped process that sprays de-ionized water or fluorinates onto the heat source and removes heat through the fluid's latent heat of vaporization.
4) Heat pipes: Heat pipes are closed cylindrical vessels filled with a working fluid and lined with a capillary structure. The heat causes the fluid to vaporize and the pressure difference created forces the vapor into the condenser section from which the fluid is returned by the capillary structure.
5) Thermosyphons: This is a system similar to a heat pipe; however, a thermosyphon relies on gravity to return the condensate not the capillary action. This allows heat to be removed from a small source and cooled over a larger.
Figure 7. Cooling methods for EV/Hybrid Components: (A) Forced fluid convection; (B) Spray cooling; and (C) Thermosyphons (You et al., 2003; Wrenick et al., 2006; Tung, 2019b).
Figure 8. Typical range of heat capacities (Left) and of thermal conductivity (Right) of different base oil types (Wrenick et al., 2006).
The next progression in thermal management is active pumped single phase (liquid cooling). This technology offers higher power capability compared with air cooling. Liquid cooled systems typically use glycol/water cooling fluids for cold freezing and corrosion protection. The current indirect liquid cooling method using a water/glycol mixture will not be sufficient to remove the heat at fast charging rates. Therefore, direct immersion cooling of the batteries using dielectric fluids like esters will be the advanced technology of choice in future generation EVs. In addition, selecting the proper pump, heat exchanger and cold plate design is important to achieving the desired EVF/HEV applications (You et al., 2003; Wrenick et al., 2006; Tung, 2019a,b).
Concerning the highest-powered systems, pumped two phase provides the highest level of heat dissipation with the least amount of energy consumption. Dielectric fluid is pumped to the cold plate where it boils as it absorbs the heat from the components. The two-phase fluid flows to a remotely located condenser, where the vapor is condensed and pumped back around the loop. The pumping power required for two-phase cooling relative to single-phase cooling is reduced by 85% which improves system-level efficiency (You et al., 2003; Wrenick et al., 2006; Tung, 2019a,b).
The projected growth of electric vehicles (EV) hybrid electric (HEV) in the automotive industries has made evolutional changes in propulsion system electrification components. Powertrain and driveline components will be enhanced by electric motors and E-drive configuration. Electrification components including electric motors or regenerative brake components will be integrated in this advanced configuration with thermal management system for cooling applications. The electric motors and power electronics will be in contact with the lubricant. Lubricants or coolants are required to cool the motors and power electronics by removing heat for thermal management. In addition, automotive lubricants for electrified propulsion system must function as an effective coolant, reduce corrosion of copper windings, needs composites and rare earth magnetic materials while upholding wear and oxidation protection and energy efficiency.
Table 5 is a comparison among these cooling methods for their performance characteristics such as heat density, thermal resistance, maintenance, complexity, temperature uniform, compactness, energy efficiency, expandability, and cost. Thermal management methods using active pumped single phase (liquid cooling) and two-phase cooling have the most advantages applied to hybrid or EV vehicles (Tung, 2019a,b). This table showed three different performance level (High, Medium, and Low) to represent their performance characteristics.
Table 5. A comparison among these cooling methods for their performance characteristics (Wrenick et al., 2006; Tung, 2019a,b).
Water offers the highest heat capacity, either by weight of volume, and also the highest thermal conductivity of fluids followed by glycols for anhydrous fluids. In consequence, water-glycol mixtures, as proven from engine coolant circuits, represent the state-of-the-art for cooling batteries.
The developments in thermal management of EV/Hybrid vehicles seek to increase the heat capacity of fluids by dispersing nanosized particles into the fluid. Global research activities using nanofluids have the scientific reach and high potential payoff to usher in a revolution in cooling technologies.
Nanofluid is a novel grade of thermal cooling fluids created by dispersing solid particles between 20 and 60 nm in size in traditional water- or oil-based fluid (Lee et al., 1999, 2009; You et al., 2003; Yu and Choi, 2003; Wrenick et al., 2006; Gullac and Akalin, 2010; Ganapathy Pandian, 2014; Khare et al., 2018)4 The nano particles have larger surface area and help enhance the thermal cooling properties of the fluid. In addition, the suspended nanoparticles remarkably improve thermal cooling process and the nanofluid has significantly higher heat conductivity and heat transfer coefficient than the conventional coolant used in conventional automotive cooling system. Recent testing results (Lee et al., 1999, 2009; You et al., 2003; Yu and Choi, 2003; Wrenick et al., 2006; Gullac and Akalin, 2010; Ganapathy Pandian, 2014; Khare et al., 2018)3,4 have indicated that these new nanomaterials have high potential to promote high thermal conductivity nanofluid materials for thermal cooling applications in the future EV/Hybrid vehicles. Challenging remains their stable dispersion in the fluid over an extended range of working temperature and to limit the sedimentation, because of the mismatch in density between the particles and the carrying fluid.
To apply nanofluids in automotive applications, a wider range of nanoparticles can be mixed with both water and oil-based fluids using conventional coolants such as ethylene glycol-based coolants. Specific dispersants have been invented to achieve the lasting stability (Choi, 1995; Hu and Dong, 1998; Eastman et al., 1999; Lee et al., 1999, 2009; Xuan and Li, 2000, 2003; Xuan and Roetzel, 2000; Choi and Eastman, 2001; Choi et al., 2001; Keblinski et al., 2002; Das et al., 2003; Xie et al., 2003; Xue et al., 2003; You et al., 2003; Yu and Choi, 2003; Gullac and Akalin, 2010; White et al., 2010, 2011a,b; Ganapathy Pandian, 2014; Khare et al., 2018). Recent experimental outcomes displayed that the thermal conductivity and convective heat transfer coefficient of the developed nanoparticles have been improved. Moreover, the impacts of heat transfer have been measured as the volume fraction of the suspended nanoparticles. As the volume fraction of nanoparticles increased, the heat transfer properties increased as well. In addition, the wear properties and load capacity of the oil-based nanofluids has room for upgrade. The improvement in tribological properties suggest the potential to lower the heat generation, reduce the component of wear, and improve the G-ratio using the nanofluid as the coolant for MQL (minimum quantity lubrication) grinding process (Tung et al., 2008).
The heat generation rates in computer chips, car engines, and optical devices are ever rising due to the needs for higher speeds and miniature attributes for microelectronic devices, higher performance capabilities for engines, and more luminous beams for optical devices. Thermal cooling becomes one of the main focuses of the sophisticated industries such as microelectronics, transportation, manufacturing, and metrology. Established cooling methods to improve heat rejection rates apply increased surface areas such as fins and micro-channels for heat dissipation. However, current thermal cooling designs have already reached its upper limit. Nanofluids are being developed to achieve ultra-high-performance cooling. with the capability to enhance the fluid's thermal properties are of great interest (You et al., 2003; Tung et al., 2008; Lee et al., 2009; Gullac and Akalin, 2010; White et al., 2010, 2011a,b; Ganapathy Pandian, 2014; Khare et al., 2018; Chen et al., 2019).
An extensive study of the thermal properties of nanofluid used in automotive thermal cooling applications was conducted to illustrate their thermal and tribological characteristics of nanofluids in this review paper. Because of the boosts in thermal conductivity, the convective heat transfer of nanofluid has been improved by the dispersion effect of the nanoparticles. The augmentations in thermal conductivity by those developed nanofluids has been quantified in this review paper. Nanofluids with better thermal and tribological properties have been replaced the traditional coolants in advanced thermal management. The enhanced thermal conductivity using nanofluids or nano lubricants has greatly improved energy efficiency and tribological performance to protect our driveline components such as gears or pumps (Tung et al., 2008; White et al., 2010, 2011a,b; Tung and Shaw, 2012; Chen et al., 2019). Furthermore, nanofluids can easily flow through the microchannel of EV/Hybrid and fuel cell system without plugging due to its nano-size particles mixed with the advanced coolants illustrated in this review paper. Future thermal management devices can be built using more compact and lighter weight materials. Using those novel nano lubricants or nanofluids, automotive engineers can provide EV/Hybrid thermal management systems with more energy-efficient, fast-cooling system, and higher heat dissipation processes.
In Table 6, the effects of heat and cold on EV subsystem were listed to demonstrate the importance of control thermal management for EV subsystems (Tung et al., 2008; Chen et al., 2019). For examples, many EV/hybrid components, including the battery, electronics and motor, require active thermal management for the thermal efficiency and safety justification as shown in Table 6 (Tung and Shaw, 2012; Tung, 2015; Chen et al., 2019). In Table 6, the effects of heat and cold on EV subsystem were listed to demonstrate the importance of thermal management for controlling the thermal cooling and battery safety of the EV subsystems (Tung and Shaw, 2012; Tung, 2015; Chen et al., 2019).
Table 6. Effects of heat and cold on EVs subsystems (Tung, 2015; Chen et al., 2019; Van Rensselar, 2019).
Fuel cell membrane needs to be maintained at lower temperatures than IC engines. The temperature range between the coolant and environment is smaller. In order to dissipate the same amount of heat energy, the radiator must be larger. To offset this increase in radiator size, thermal properties of the coolant must be improved. Recently Tung and his associates (Tung, 2019a,b) have investigated the coolant flow and temperature distribution to control thermal management in fuel cell system as shown in the following Figures 9, 10. Temperature distribution in fuel cell membrane and its bi-polar plates must be controlled in a precise range of 80–84°C. If the temperature limit is beyond the upper limit of 85°C, fuel cell membrane will dry out and fail in function. Therefore, thermal management issues become crucial for fuel cell performance and durability. Global R&D activities have been focused on thermal management using novel coolants (Tung, 2019a,b). However, the requirements for the coolant in the fuel cell system need to be specified by the automotive industries and Tier 1 suppliers. It should match with the future EV/Hybrid vehicle requirements. For examples, the fuel cell coolants must be electrically non-conductive for not only safety, but also stack efficiency. To protect membrane and bipolar plates, coolants must have Increased thermal and heat transfer properties for fast speed cooling. In addition, coolants must have high density and specific heat to greatly lessen the volume flow of coolant throughout the system to provide abundant cooling.
The next section will introduce the current fuel cell coolant requirements for future refinement.
• Electrically non-conductive for both safety and stack efficiency
• Increased thermal and heat transfer characteristics
• High density and specific heat to greatly lessen the flow of the coolant throughout the system to provide essential cooling
• An uncompromising viscosity for pumping at −40°C while not so thin as to leak through small cracks at 80°C.
• Vapor pressure must be under 2 bar at 80°C
• Material compatibility with gaskets and additional resources in the fuel cell system
• Able to take in hydrogen gas in solution without degradation
• Able to accept strong voltage fields and voltage difference exceeding 450 V DC
• No corrosion, erosion, and plugging of micro channels (0.30 mm)
• Stable coolant for the anticipated 10-years life
• No flammability and toxicity.
Nanofluid is a novel class of heat transfer and anti-wear liquids produced by dispersing solid particles smaller than 30–40 nm in size in traditional water- or oil-based fluid. The name nanofluid was coined by Choi (1995), Choi and Eastman (2001), and Choi et al. (2001). Dr. Choi and his associates have discovered that the nanoparticles have larger surface area and help augment the heat transfer and wear properties of the fluid if these nanoparticles can mix with dispersants to prevent from agglomerating after a long-term application (Choi, 1995; Choi and Eastman, 2001; Choi et al., 2001; Xie et al., 2003).
Nanoparticles for nanofluids can be metal or oxides, while metal nanoparticles are superior in enhancing the heat transfer properties when compared to oxide nanoparticles. An example of the TEM micrographs of copper nano particle dispersed in water-based coolant is shown in Figure 11A. The increase of fluid thermal conductivity at different volume percentage of suspended Cu, CuO, and Al2O3 nanoparticles is shown in Figure 11B. A mere addition of 0.3 volume percent of copper nanoparticles boosted the thermal conductivity of water-based coolant up by 40%. A small amount of thioglycolic acid can be mixed with the copper nanofluids, marked as Cu Acid, to further enhance conductivity. More recently, nanofluids containing carbon nanotubes (CNT) and SiC were produced (Choi, 1995; Choi and Eastman, 2001; Choi et al., 2001; Xie et al., 2003). Tests show that these new nanomaterials have the capability to become the high thermal conductivity nanofluid materials of the future.
Figure 11. Nanofluids, (A) transmission electron microscope (TEM) micrograph of copper nanoparticles produced by direct evaporation and (B) enhancement of thermal conductivity of nanofluid, k, over the thermal conductivity ko of water, the base fluid (Choi, 1995; Choi et al., 2001; Courtesy of Dr. Choi, Choi and Eastman, 2001).
Two methods to produce nanofluids for heat transfer applications have been developed (Choi, 1995; Choi and Eastman, 2001; Choi et al., 2001). The one-step method produces the metal nanofluids by directly condensing the evaporated metal vapor to the fluid to produce the metallic nano particles. The two-step method, as shown in Figure 12, starts with the formation of nanoparticles by inert gas condensation and followed by their dispersion in a base fluid. This method is simpler, less expensive to produce oxide and non-metallic nanofluids. A wider range of nanoparticle materials can be produced for both water- and oil-based fluids. No dispersants are needed for the nanofluid developed using both methods to achieve the long-term stability.
Figure 12. Two-step production method of nanofluid (Choi, 1995; Choi et al., 2001; Courtesy of Dr. Choi, Choi and Eastman, 2001).
Another type of nanoparticle, crystal titanium borate, has been experimented for anti-wear and friction reduction in nanofluid (Hu and Dong, 1998). Experimental results show that the wear resistance and load capacity of the oil-based nanofluid were enhanced and the coefficient of friction was reduced. The improvement in tribological properties suggest the potential to decrease the wheel wear, lower the heat generation, and improve the G-ratio, which is the ratio of the volume of material removed to the volume of wheel wear, using the nanofluid as the coolant for MQL grinding.
Extensive study of the thermal properties of nanofluid has been conducted (Choi, 1995; Hu and Dong, 1998; Eastman et al., 1999; Lee et al., 1999; Xuan and Li, 2000, 2003; Xuan and Roetzel, 2000; Choi and Eastman, 2001; Choi et al., 2001; Keblinski et al., 2002; Das et al., 2003; Xie et al., 2003; Xue et al., 2003; You et al., 2003; Yu and Choi, 2003; Wrenick et al., 2006; Ganapathy Pandian, 2014; Khare et al., 2018)3,4. In addition to the enhancement in the thermal conductivity, the convective heat transfer of nanofluid is boosted by the random movement and dispersion effect of the nanoparticles (Xuan and Li, 2000, 2003) measured the Nusselt number, which indicates the convective heat transfer performance, increased by 40% for the nanofluid with two volume percent Cu nanoparticles. The enhancement in thermal conductivity of the Cu nanofluid has been quantified by Eastman et al. (Xue et al., 2003), Lee et al. (Eastman et al., 1999), Das et al. (Das et al., 2003). Keblinski et al. (Keblinski et al., 2002) studied the methods of heat flow in suspension nanoparticles. The function of interfacial layers, which exists between the nano-sized particles and the fluid, in the enhanced thermal conductivity of nanofluids was investigated by Yu and Choi (Yu and Choi, 2003), Lee and Choi et al. (Lee et al., 1999). For CNT nanofluid, 20% thermal conductivity improvement is observed at 1.0 vol.-% of CNT in decane (Choi et al., 2001; Ganapathy Pandian, 2014; Khare et al., 2018). This is a continuing evolving research area. Nanofluids with better thermal and tribological properties are poise to challenge the traditional metalworking fluids.
The upgraded thermal conductivity means an improved energy efficacy, enhanced performance, and reduced costs of operation. Some fluids provide superior resistance to wear and load capacity, which minimalizes the necessity for upkeep and repair. With such a minute particle size, nanofluids can flow unhindered even in the smallest channels. As a result, miniaturized systems do not need a large supply of liquid and the reduction of thermal systems is possible. Smaller machineries in vehicles translate to an improved efficiency, resulting in money savings for consumers, and reduced gas emissions, which results in a cleaner environment. Potential applications of nanofluids include the fuel cell and engine cooling system, transmission grease, and coolant/lubricant for forming/stamping and machining operations.
Recent heat transfer studies of nanofluids (Tung et al., 2008; Lee et al., 2009; White et al., 2010, 2011a,b) have revealed that the thermal properties of a liquid can be influenced by nanoparticles that are suspended within the liquid and can also alter the surface roughness by accumulating on the heater surface. Combined boiling studies of nanofluids have shown a mixed result—either enhancing or diminishing heat transfer. However, how much the suspended particles affect increased surface roughness and restrain of bubble transport is yet to be attributed due to the fact that the base fluids were used on a clean boiling surface as a comparison. These studies have overcome the aforementioned issue by observing the boiling performance of tests with water and water-based nanofluids with suspended 40 nm ZnO nanoparticles and an exposed surface. The results show that the water tests displayed a dramatic increase in performance, up to a 62% improvement after 4 cycles. This improvement connects well with a surface roughness model for boiling, which uses atomic force microscopy-measured surface data to enumerate the layering of nanoparticles in disrupting nanofluid boiling tests. The results also showed that the ZnO nanofluid tests initially presented a 24% augmentation on a clean surface, but decreased steadily as nanoparticle layering occurs, showing a development that is contrary to the results of the water test. This was attributed to the limit of bubble formation and motion by the suspended nanoparticles. These studies show that the surface roughness as a result of the accumulation of the nanoparticles can have a pro and a con of significantly enhancing the boiling for the base fluid and marginally reducing the function for the nanofluid, respectively.
Recently Steve White and Simon Tung have published several papers (White et al., 2010, 2011a,b) on nanofluids application for thermal cooling. White and Tung reported the potential applications using nanofluids for heat transfer applications in thermal cooling devices such as EV or hybrid vehicles (White et al., 2010, 2011a,b). As shown in Table 7 is a list of thermal conductivity measurement for various metallic solids, non-metallic solids, and heat transfer fluids (White et al., 2010, 2011a,b).
Table 7. Thermal conductivity measurement for metallic solids, nonmetallic solids, and heat transfer fluids (White et al., 2010, 2011a,b).
Thermal management is becoming the most crucial issue to EV/hybrid engineers. Both heating and cooling are involved (You et al., 2003; Tung et al., 2008; Lee et al., 2009; Gullac and Akalin, 2010; White et al., 2010, 2011a,b; Ganapathy Pandian, 2014; Khare et al., 2018). An example is warming at startup to get a reasonable battery output; at the other end, if you exceed a certain temperature, you can permanently hurt the battery. In addition, EV/hybrid must control thermal management for cooling of most components such as electric motors, battery, and power electronics. The EV motor is efficient, but it still generates heat. If overheating of EV motor or battery system, it can permanently damage the battery and motor, requiring replacement of the motor. Making the motor more efficient by using better lubricants would reduce this risk. For the coolant used in EV/hybrid, pumping losses have become a huge issue and the automotive industry are moving to a new direction using the lower viscosity fluids. In addition, power electronics heat up quickly. It will generate thermal running-up and damage all power electronics and battery system. Nanofluids or nano lubricants (such as nanographene) will be ideal to apply for thermal cooling of EV/hybrid components. Based on Tung and his colleagues estimated in their recent publications (White et al., 2010, 2011b), using nanofluids or nanographene in EV/hybrid or fuel cell applications have improved almost 35–40% of thermal cooling efficiency compared with the traditional coolants such as polyethylene glycol or the other synthetic polyether coolants.
In addition, White and their co-authors (White et al., 2010, 2011a,b) have discovered that significant improvement of the electrical conductivity of propylene glycol-based ZnO nanofluids will create promising application of these for fuel cell membrane cell and hybrid vehicle electrification components. Electrical conductivity is a central quality for potential functions of nanofluids in technology that are still quite novel. Traditional depictions such as the Maxwell model do not take into account the important effects of surface charges on electrical conductivity, especially at high nanoparticle volume fractions. In these studies, tests were done on electrical characterizations of propylene glycol-based ZnO nanofluids. The nanofluids used has a volume fraction up to 7%, which lead to an improvement in electrical conductivity of ~100 times over that of the base fluid. Furthermore, these large increases in electrical conductivity are accompanied by a rise in volume fraction and a reduction in particle size, but the increase hits a plateau at high volume fractions. The aforementioned developments are in line with previously established models for colloidal suspensions in salt-free media. Specifically, the plateauing of electrical conductivity at elevated volume fractions, which the authors believe were a result of counter-ion condensation, shows a noticeable difference from the “linear fit” models that were used before to attribute the electrical conductivity of nanofluids.
Simon Tung, and Albert Shih have investigated the wet, dry and minimum quantity lubrication (MQL) grinding of cast iron (Tung et al., 2008). Water based Al2O3 and diamond nanofluids are used in MQL grinding procedures and the outcomes are contrasted with the results of pure water. During the progression of MQL grinding using nanofluids, a dense and hard slurry layer is created on the wheel surface and assists the grinding performance. Experimental outcomes show that G-ratio can be enhanced with highly concentrated nanofluids. Compared to pure water, the application of nanofluids can lessen grinding forces, enhance the surface roughness, and inhibit workpieces from burning. In comparison to dry grinding, MQL grinding can greatly minimize grinding temperature and energy partition. More research activities on nanofluid became an emerging technology on thermal cooling used for EV/Hybrid components or manufacturing applications. Besides thermal cooling benefits using nanofluids, nanoparticles blended with lubricants have been studied to generate promising applications on friction and wear reduction in automotive and manufacturing components (White et al., 2010).
Table 8 is a recent list of advanced nanofluids properties published in literatures (Hu and Dong, 1998; Eastman et al., 1999; Lee et al., 1999, 2009; Xuan and Li, 2000, 2003; Xuan and Roetzel, 2000; Choi et al., 2001; Keblinski et al., 2002; Das et al., 2003; Xie et al., 2003; Xue et al., 2003; You et al., 2003; Yu and Choi, 2003; Wrenick et al., 2006; Tung et al., 2008; Gullac and Akalin, 2010; White et al., 2010, 2011a,b; Ganapathy Pandian, 2014; Khare et al., 2018; Chen et al., 2019)3,4. In this table different metallic or non-metallic particles have been blended with different types of base fluids with different volume fractions. Average particle size is varied between 10 and 80 nm. The reported thermal conductivity can be increased from 15 to 150%. Several nanofluids such as multiwall carbon nanotube (Choi and Eastman, 2001) mixed with synthetic oil or CuO nanoparticles (Eastman et al., 1999) mixed with water showed significant increase of thermal conductivity compared with the other nanofluids (Lee et al., 1999; Keblinski et al., 2002; Das et al., 2003; Yu and Choi, 2003). The factors affecting suspension are particle size, and dispersant for blending the nanoparticles. Chen et al. (2019) have reported their findings on nanofluids about dispersion effect on nanofluid stability.
Table 8. Testing results of advanced nanofluids properties published in literatures (Hu and Dong, 1998; Eastman et al., 1999; Lee et al., 1999, 2009; Xuan and Li, 2000, 2003; Xuan and Roetzel, 2000; Choi et al., 2001; Keblinski et al., 2002; Das et al., 2003; Xie et al., 2003; Xue et al., 2003; You et al., 2003; Yu and Choi, 2003; Wrenick et al., 2006; Li et al., 2008; Tung et al., 2008; Buongiorno et al., 2009; Gullac and Akalin, 2010; White et al., 2010, 2011a,b; Ganapathy Pandian, 2014; Zhou et al., 2015; Dai et al., 2016; Harmandeep et al., 2018; Khare et al., 2018, Chen et al., 2019)3,4.
The major mechanisms of the nano lubricants/nanofluids can be explained by the physical absorption of the nanoparticles on the interface to form the dispersant-stabilizing nanofluids (Tung and Shaw, 2012; Tung, 2015; Chen et al., 2019). In general, those dispersants are amphiphilic molecules which have both lipophobic and lipophilic functional groups. An organic layer, which can sterically stabilize the nanoparticles, can be created due to the absorption by the lipophobic portion on the surface of the nanoparticle (Chen et al., 2019). In certain situations, the addition of specific dispersants decreased the efficacy of nanoparticles (Tung and Shaw, 2012; Tung, 2015; Chen et al., 2019). The stable time was less than only a few weeks. If the nanoparticles mixed with silane surface modification could reach a long-time stability (Tung and Shaw, 2012; Tung, 2015; Chen et al., 2019). Furthermore, the dispersion agents used in their studies have changed the formulation of a lubricating oil. Recently, an investigation was done on the synergetic friction modification between ionic liquid and nanoparticle additives (Tung and Shaw, 2012; Tung, 2015). It was observed that the adding of ionic liquid would significantly improve the dispersion capability of nano-lubricants. It was an unequivocal proof that the surface modification methods were highly effective to form a stable nanoparticle dispersion.
The effect of material, particle size, and surface modification on dispersion was also studied (Tung and Shaw, 2012; Chen et al., 2019). Surface modification methods were crucial to disperse nanoparticles into a lubricating oil. Theoretical analysis in Chen and Liang paper (Chen et al., 2019) had indicated that steric stabilization can play an important role in lubricating oils. Steric stabilization was an effective method by combining oil with a dispersant to create a surface layer of organics. To achieve a firm suspension, it was essential for the surface of nanoparticles to have elongated alkyl chains with ample grafting density and thickness-to-size ratio (Tung and Shaw, 2012). For nanoparticles with sizes under 50 nm, the usage surfactants can alter their interfaces of nanoparticles and the adsorbed layers to reach a desirable suspension of nanofluids. For the oxide particles that were larger than 10 nm, surface salinization proved to be a much better option due to its higher grafting density and versatility. The higher volume fraction of nanoparticles in base coolants could create a higher thermal conductivity of nanofluids as opposed to the base coolant such as polyethylene glycol as shown in Table 8 (Hu and Dong, 1998; Eastman et al., 1999; Lee et al., 1999, 2009; Xuan and Li, 2000, 2003; Xuan and Roetzel, 2000; Choi et al., 2001; Keblinski et al., 2002; Das et al., 2003; Xie et al., 2003; Xue et al., 2003; You et al., 2003; Yu and Choi, 2003; Wrenick et al., 2006; Tung et al., 2008; Gullac and Akalin, 2010; White et al., 2010, 2011a,b; Ganapathy Pandian, 2014; Khare et al., 2018; Chen et al., 2019)3,4.
In addition, Professor Diana Berman at the University of North Texas (Berman et al., 2018) developed a lab-scale experimental research program for investigation the effects of nanographene on frictional energy dissipation and losses at interfaces. She and her colleagues investigated the origins of macroscale behavior of nanomaterials. They controlled the shearing of 2D materials to minimize friction between surfaces. They developed innovative approaches to manipulate the structures of these 2D materials for improving their nanographene performance. A novel way to achieve superlubricity was discovered in their research program (Berman et al., 2018). The coefficient of friction could be <0.01, but it was too low to measure using the conventional instruments. Referring to Berman's work how nanographene lubricants compares to other types of hard coatings like DLC, nanographene particles can attach to a steel surface with relatively weak van der Waals forces. Nanographene particles could allow the graphene layers to adapt to external stresses and accommodate those stresses to minimize friction. In addition, graphene's electron mobility could enable the attached surface layers to prevent from corrosion and other environmental effects. Those novel lubricants could be replenished easily and protect surface coatings from wear or scuffing (Tung, 2015; Berman et al., 2018). In an industrial application, an injector system could continuously replenish the graphene in ethanol suspension at the contact site. In contrast with the micron-scale deposited coatings common with disulfides and DLCs, these nanographene coatings were on the order of 1–2 nm thick. Graphene thin coatings could have a high surface area, and they usually could coat on the substrate conformally. Automotive industry is looking for more engineering application using nanographene for protection of battery materials and thermal management devices in a variety of thermal cooling environments (Tung, 2015; Berman et al., 2018).
The projected growth of electric vehicles (EV) hybrid electric (HEV) in the automotive industries has made evolutional changes in propulsion system electrification components. Powertrain and driveline components have been enhanced by electric motors and E-drive configurations. Electrification components including electric motors or regenerative brake components will be integrated in this advanced configuration with thermal management system for cooling applications. The electric motors and power electronics will be in contact with the driveline lubricant or coolants. Lubricants or coolants are required to cool the motors, power electronics, and batteries by removing heat for better thermal management. In addition, automotive lubricants for electrified propulsion system must function as an effective coolant, reduce corrosion of copper windings, composites, and rare earth magnetic materials while upholding wear and oxidation protection and energy efficiency.
As electrified powertrains are becoming mainstream, dedicated EV lubricants with new test methods follow evidently. However, these advanced lubricants and testing methods are still in development stages, which brings challenges for the future. With the stable growth in lithium greases, dedicated lubricants will be challenged as well. Lithium for greases competes with the other types of grease inevitably needed for batteries. Lithium hydroxy stearate is therefore not mandatory the preferred choice for soaps in greases. However, growing optimism and the strong push for environmental friendliness lubricants makes the development of electrified powertrain lubricants more of a reality than mere pipe dream. The question now is when will these driveline lubricants be developed and how electrification components will be dominated in EV/hybrid future development trends.
New developments in thermal management are helping extend the driving range and lifetime of EV/Hybrid. Global research activities using novel nanofluids or nanographene for thermal cooling have the high potential for cooling technologies. This review paper has described the advanced thermal management technology in EV/Hybrid vehicles. This paper also demonstrated a high promising application using nanofluids or nanographene for thermal cooling in EV/Hybrid and fuel cell components.
The major goal of this review paper is to underline the future electrification development trends for advanced Hybrid/EV vehicles. The major sections of this review paper covered the most important progress of automotive lubrication in the areas of energy conversion effectiveness, driveline consistency, cooling system design and thermal management requisites.
Thermal management has become a key technology for the successful development of electric vehicles and other new energy vehicles, and still faces many technical challenges. For examples, power lithium batteries, fuel cell components, and dynamic response of electric drive systems and integrated thermal management technology, electric vehicle heat pump air conditioning technology, and so on. These not only bring new challenges to automotive engineers or scientists, but also bring new research opportunities to the global academic community. It is imperative to design new electrification components and advanced propulsion vehicles with high energy efficiency and reliable thermal management solutions.
All authors listed have made a substantial, direct and intellectual contribution to the work, and approved it for publication.
RS is employed by Koehler Instrument Company.
The remaining authors declare that the research was conducted in the absence of any commercial or financial relationships that could be construed as a potential conflict of interest.
1. ^N.N., Electric Cars—New Technology Calls for New Lubrication. FUCHS Petrolub AG, Germany, company brochure. Available online at: https://www.fuchs.com/dk/en/products/download-center/articles/electric-cars-new-technology-calls-for-new-lubrication/
2. ^Available online at: https://newsroom.porsche.com/en_AU/products/taycan/battery-18557.html
3. ^Available online at: https://www.audi-technology-portal.de/en/mobility-for-the-future/audi-future-lab-tron-experience_en/audi-e-tron-charging-and-thermal-management
4. ^Available online at: https://newsroom.porsche.com/en_AU/products/taycan/battery-18557.html
5. ^Lubricant Additives Market Share | Industry Report, 2024. (n.d.). Retreived From: https://www.grandviewresearch.com/industry-analysis/lubricant-additives-market (accessed June 10, 2020).
Eastman, J. A., Choi, S. U. S., Li, S., Soyez, G., Thompson, L. J., and DiMelfi, R. J. (1999). Novel thermal properties of nanostructured materials. Mater. Sci. Forum 312, 629–634. doi: 10.4028/www.scientific.net/MSF.312-314.629
Ganapathy Pandian, S. (2014). Tribological Characteristics of Stabilized Zirconia Nanolubricants. SAE Technical Paper. doi: 10.4271/2014-01-2790
Gullac, B., and Akalin, O. (2010). Frictional characteristics of IF-WS2 nanoparticles in simulated engine conditions. Tribol. Trans. 53, 939–947. doi: 10.1080/10402004.2010.511761
Hu, Z. S., and Dong, J. X. (1998). Study on antiwear and reducing friction additive of nanometer titanium borate. WEAR 216, 87–91. doi: 10.1016/S0043-1648(97)00249-4
Keblinski, P., Phillpot, S. R., Choi, S. U. S., and Eastman, J. A. (2002). Mechanisms of heat flow in suspensions of nano-sized particles (nanofluids). Int. J. Heat Mass Transfer 45, 855–863. doi: 10.1016/S0017-9310(01)00175-2
Khare, H. S., Lahouij, I., Jackson, A., Feng, G., Chen, Z., Cooper, G. C., et al. (2018). Nanoscale generation of robust solid films from liquid-dispersed nanoparticles via in situ atomic force microscopy: growth kinetics and nanomechanical properties. ACS Appl. Mater. Interfaces 10, 40335–40347. doi: 10.1021/acsami.8b16680
Lee, K., Hwang, Y., Cheong, S., Choi, Y., Kwon, L., Lee, J., et al. (2009). Understanding the role of nanoparticles in nano-oil lubrication. Tribol. Lett. 35, 127–131. doi: 10.1007/s11249-009-9441-7
Lee, S., Choi, S. U. S., Li, S., and Eastman, J. A. (1999). Measuring thermal conductivity of fluids containing oxide nanoparticles. ASME J. Heat Transfer 121, 280–289. doi: 10.1115/1.2825978
Tung, S. C. (2019a). “The impact of advanced propulsion system on thermal management and lubrication requirements,” in China International Lubricants Conference and Technology Exhibition (INTEX) Keynote Speaker (Guangzhou).
Tung, S. C. (2019b). “Overview of energy innovation technology and future development trends responding to improving energy efficiency requirements and green environmental opportunities,” in Invited Speaker, SAE China International Congress (China: SAE).
Tung, S. C., Shen, B., and Shih, A. (2008). Application of nanofluids in minimum quantity lubrication grinding. STLE Tribol. Trans. 51, 730–737. doi: 10.1080/10402000802071277
White, S. B., Shih, A. J., and Pipe, K. P. (2010). Effects of Nanoparticles in Nanofluid and Base Fluid Pool Boiling heat transfer from a Horizontal surface under atmospheric pressure. J. Appl. Phys. 107:114302. doi: 10.1063/1.3342584
White, S., Shih, A., and Tung, S. (2011a). Boiling surface enhancement by electrophoretic deposition of particles from a nanofluid. Int. J. Heat Mass Transfer 54, 4370–4375. doi: 10.1016/j.ijheatmasstransfer.2011.05.008
White, S. B., Shih, A. J., Pipe, K. P., and Tung, S. (2011b). Investigation of the electrical conductivity of propylene glycol-based ZnO nanofluids. Nanoscale Res. Lett. 6:2012. doi: 10.1186/1556-276X-6-346
Chen, Y., Renner, P., and Liang, H. (2019). Dispersion of nanoparticles in lubricating oil: a critical review. Lubricants 7, 5–11. doi: 10.3390/lubricants7010007
Wrenick, S., Sutor, P., Pangilinan, H., and Schwartz, E. E. (2006). “Heat transfer properties of engine oils,” in Proceeding World Tribology Conference (Washington, DC). doi: 10.1115/WTC2005-64316
Xie, H. Q., Lee, H., Youn, W., and Choi, M. (2003). Nanofluids containing multiwalled carbon nanotubes and their enhanced thermal conductivities. J. Appl. Phys. 94, 4967–4971. doi: 10.1063/1.1613374
Xuan, Y. M., and Li, Q. (2000). Heat transfer enhancement of nanofluids. Int. J. Heat Fluid Flow. 21, 58–64. doi: 10.1016/S0142-727X(99)00067-3
Xuan, Y. M., and Li, Q. (2003). Investigation on convective heat transfer and flow features of nanofluids. ASME J. Heat Transfer. 125, 151–155, Friction and wear. doi: 10.1115/1.1532008
Xuan, Y. M., and Roetzel, W. (2000). Conceptions for heat transfer correlation of nanofluids. Int. J. Heat Mass Transfer 43, 3701–3707. doi: 10.1016/S0017-9310(99)00369-5
Xue, L., Keblinski, P., Phillpot, S. R., Choi, S. U. S., and Eastman, J. A. (2003). Two regimes of thermal resistance at a liquid-solid interface. J. Chem. Phys. 118, 337–339. doi: 10.1063/1.1525806
You, S. M., Kim, J. H., and Kim, K. H. (2003). Effect of nanoparticles on critical heat flux of water in pool boiling heat transfer. Appl. Phys. Lett. 83, 3374–3376. doi: 10.1063/1.1619206
Yu, W., and Choi, S. U. S. (2003). The role of interfacial layers in the enhanced thermal conductivity of nanofluids: a renovated maxwell model. J. Nanoparticle Res. 5, 167–171. doi: 10.1023/A:1024438603801
Choi, S. U. S., Zhang, Z. G., Yu, W., Lockwood, F. E., and Grulke, E. A. (2001). Anamalous thermal conductivity enhancement in nanotube suspensions. Appl. Phys. Lett. 79, 2252–2254. doi: 10.1063/1.1408272
Das, S. K., Putra, N., Thiesen, R., and Roetzel, W. (2003). Temperature dependence of thermal conductivity enhancement for nanofluids. ASME J. Heat Transfer 125, 567–574. doi: 10.1115/1.1571080
Andrew, J. M. (2019). The future of lubricating greases in the electric vehicle era. Tribol. Lubric. Technol. 38:44
Benedicto, E., Carou, D., and Rubio, E. M. (2017). Technical, economic and environmental review of the lubrication/cooling systems used in machining processes. Proc. Eng. 184, 99–116. doi: 10.1016/j.proeng.2017.04.075
Berman, D., Erdemir, A., and Sumant, A. V. (2018). Approaches for achieving superlubricity in two-dimensional materials. ACS Nano 12, 2122–2137. doi: 10.1021/acsnano.7b09046
Buongiorno, J., Venerus, D. C., Prabhat, N., McKrell, T., Townsend, J., Christianson, R., et al. (2009). A benchmark study on the thermal conductivity of nanofluids. J. Appl. Phys. 106:14. doi: 10.1063/1.3245330
Choi, S. U. S. (1995). “Enhancing thermal conductivity of fluids with nanoparticles,” in Developments and Applications of Non-Newtonian Flows, ASME FED 231/MD 66, 99–103.
Choi, S. U. S., and Eastman, J. A. (2001). Enhanced Heat Transfer Using Nanofluids for Thermal Cooling. US Patent Number 6:275.
Dai, W., Kheireddin, B., Gao, H., and Liang, H. (2016). Roles of nanoparticles in oil lubrication. Tribol. Int. 102, 88–98. doi: 10.1016/j.triboint.2016.05.020
Farfan-Cabrera, L. I. (2019). Tribology of electric vehicles: a review of critical components, current state and future improvement trends. Tribol. Int. 138, 473–486. doi: 10.1016/j.triboint.2019.06.029
Harmandeep, S., Lahouij, I., Jackson, A., Feng, G., Chen, Z., and Cooper, G. D. (2018). Nanoscale Generation of Robust Solid Films from Hydrogenated Amorphous Carbon Coatings. Carbon. 93, 851–860.
International Energy Agency (IEA) (2017). Energy Technology Perspectives. Available online at: https://www.buildup.eu/en/node/53488
Jackson, T. A. (1970). Biolubricants Market Size to Reach $2.92 Billion By 2024. Retrieved from: http://cmfemarketresearchindustryreports.blogspot.com/2018/01/the-global-biolubricants-market-analysis.html
Jost, H. P. (1966). Lubrication (Tribology). Education and Re-Search Report. London: Department Education and Science, Her Majesty's Stationary Office.
Li, X. F., Zhou, D. S., Wang, X. J., Wang, N., Gao, J. W., and Li, H. (2008). Thermal conductivity enhancement dependent pH and chemical surfactant for Cu-H2O nanofluids. Thermochim Acta 469, 98–103. doi: 10.1016/J.TCA.2008.01.008
Masuda, H., Ebata, A., Teramae, K., and Hishinuma, N. (1993). Alteration of thermal conductivity and viscosity of liquid by dispersing ultra-fine particles (dispersions of c-Al2O3, SiO2, and TiO2 ultrafine particles). Netsu. Bussei. 7, 227–233. doi: 10.2963/jjtp.7.227
OECD (2019). Global Material Resources Outlook to 2060: Economic Drivers and Environmental Consequences. Paris: OECD Publishing. Available online at: https://doi.org/10.1787/9789264307452-en doi: 10.1787/9789264307452-en
Salleh, L., Raja, R. I., and Md Zain, M. Z. (2013). Evaluation of annoyance and suitability of a back-up warning sound for electric vehicles. Int. J. Automot. Mech. Eng. 8, 1267–1277. doi: 10.15282/ijame.8.2013.16.0104
Society for Tribologists Lubrication Engineers (STLE) 2020 Report (2020). Emerging Issues and Trends in Tribology and Lubrication Engineering. Published by Society of Tribologists and Lubrication Engineers. Available online at: www.stle.org
Spaltmann, D., von Gablenz, A., and Woydt, M. (2010). CO2-neutral fuels and lubricants based on second generation oils such as jatropha. J. ASTM Int. 7, 1–12. doi: 10.1520/JAI102549
The Delegated Act on low/high ILUC Biofuels (2019). European Commission Delegation Regulation (EU) 2019/807. Available online at: https://eur-lex.europa.eu/eli/reg_del/2019/807/oj
Toubeau, C. (2019). Reduction of Vehicle Noise Emissions - Technological Potential and Impacts. Available online at: https://www.transportenvironment.org/publications/reduction-vehicle-noise-emissions-technological-potential-and-impacts-0
Toyoda, S. (2007). All Toyota tribological innovation to realize “Zeronize “and “Maximize” society. Tribol. Online 2, 19–22. doi: 10.2474/trol.2.19
Tung, S. C. (2015). “Overview and future trends of nano-graphene film and carbon-based material technology,” in Innovation Technology Consulting Inc., Presentation at STLE 2015 Annual Meeting (Dallas, TX).
Tung, S. C., and Shaw, U. (2012). Nanographene Layers and Particles and Lubricants Incorporating the Same. US Patent No. 8227386.
Tung, S. C., and Wong, V. W. (2018). Engine lubricants overview and future development trends. America Society of Materials (ASM). Handbook Tribol. 18, 150–161. doi: 10.31399/asm.hb.v18.a0006413
United Nation General Assembly (2015). Resolution 70/1 “Transforming Our World: The 2030 Agenda for Sustainable Development” adopted by the General Assembly. Available online at: https://www.un.org/en/development/desa/population/migration/generalassembly/docs/globalcompact/A_RES_70_1_E.pdf
United Nations Environment (2019). Global Resource outlook. A Report of the International Resource Panel. Available online at: https://unstats.un.org/sdgs/report/2019/Overview,/
Van Rensselar, J. (2019). “EVs are at the beginning of an evolving technology,” in Tribology & Lubrication Technology (Park Ridge, IL: Society of Tribologists and Lubrication Engineers).
Woydt, M., Wincierz, C., Luther, R., Rienäcker, A., Wetzel, F. J., and Hosenfeldt, T. (2020). Tribology in Germany: Interdisciplinary Technology for the Reduction of CO2-Emissions and the Conservation of Resources, 2019, German Society for Tribology (www.gft-ev.de). Available online at: https://www.gft-ev.de/wp-content/uploads/GfT-Study-Tribology-in-Germany.pdf
Zhang, S.-W., and Xie, Y.-B., (eds.). (2009). Tribology Science Industrial Application Status and Development Strategy. 2008. The Investigation on Position and Function of Tribology in Industrial Energy Conservation, Consumption and Emission Reduction (Report of 2-year Chinese Investigation). Beijing: Higher Education Press.
Keywords: EV/hybrid components, driveline lubrication, thermal management, lubricant thermal performance testing, nanofluids, fuel cell applications
Citation: Tung SC, Woydt M and Shah R (2020) Global Insights on Future Trends of Hybrid/EV Driveline Lubrication and Thermal Management. Front. Mech. Eng. 6:571786. doi: 10.3389/fmech.2020.571786
Received: 11 June 2020; Accepted: 13 August 2020;
Published: 20 October 2020.
Edited by:
Alessandro Ruggiero, University of Salerno, ItalyReviewed by:
Mohamed Kamal Ahmed Ali, Minia University, EgyptCopyright © 2020 Tung, Woydt and Shah. This is an open-access article distributed under the terms of the Creative Commons Attribution License (CC BY). The use, distribution or reproduction in other forums is permitted, provided the original author(s) and the copyright owner(s) are credited and that the original publication in this journal is cited, in accordance with accepted academic practice. No use, distribution or reproduction is permitted which does not comply with these terms.
*Correspondence: Simon C. Tung, c3R1bmc1NEB5YWhvby5jb20=
Disclaimer: All claims expressed in this article are solely those of the authors and do not necessarily represent those of their affiliated organizations, or those of the publisher, the editors and the reviewers. Any product that may be evaluated in this article or claim that may be made by its manufacturer is not guaranteed or endorsed by the publisher.
Research integrity at Frontiers
Learn more about the work of our research integrity team to safeguard the quality of each article we publish.