- 1CNOOC Research Institute Co., Ltd, Beijing, China
- 2CNPC Bohai Drilling Engineering Co, Ltd, Tianjin, China
- 3CNPC Engineering and Technology Research Institute of Southwest Oil and Gas Field Company, Guanghan, China
- 4School of New Energy and Materials, Southwest Petroleum University, Chengdu, China
As a porous brittle material, oil well cement in oil and gas well cementing is difficult to bear complex loads, which can easily lead to the failure of the mechanical integrity of cement sheath. In this paper, SiO2 coating-CF toughening material was obtained by SiO2 modified carbon fibers (CFs) surface. In addition, the mechanical properties and mechanism of SiO2 coated-CF cement stone were discussed. The obtained results showed that the mechanical properties of SiO2 coated-CF cement paste are significantly improved. After 14 days of curing, the compressive strength can reach 32.98 MPa and the tensile strength is increased by 162%. The CF after adding SiO2 surface film improves the adhesion between the interface and the fiber by forming chemical bonds at the bonding surface with the cement paste, so as to improve the CF reinforced cement paste.
1 Introduction
Portland cement is an inorganic gel material, which is widely used in the construction field and the cementing process of oil and gas reservoir development. Oil and gas well cementing consists in injecting cement slurry between formation and casing, which is of great significance for supporting casing and isolating underground fluid channeling. The development of oil and gas wells often relies on perforation, fracturing, and other means to enhance the productivity, which will make the cement stone under extremely high load. The hard and brittle characteristics of cement stone make it difficult to bear high load, which can easily lead to the failure of cement sheath interlayer sealing, and significantly affect the productivity, life, and safety of oil and gas wells (Zhang et al., 2020a). Several studies were conducted to improve the mechanical properties of oil well cement stone in order to have a certain elastic-plastic deformation and decrease the brittle failure ability, to avoid the local stress concentration of cement ring under impact load (Zhang et al., 2021). This allows to improve its ability to resist fractures, which is referred to as cement stone toughening. Several approaches exist for toughening cement stone, such as nano-materials (Jafariesfad et al., 2017; Xiao et al., 2019), latex (da Silva et al., 2017), fibers, and whiskers (Li et al., 2015). At present, the most effective toughening measure consists in adding fiber materials to cement (Zhang et al., 2020b) to prepare high performance fiber-cement composites.
Carbon fiber (CF) is a new type of fiber materials with low density, high specific strength, and high specific modulus. It is known as the “king of new materials” and it is widely used in various fields of national defense science and technology as well as national economy such as automobiles, aerospace, wind power generation, buildings, and bridges. It is also an ideal cement stone reinforcing material (Yang et al., 2022; Yu et al., 2022; Liu et al., 2023; Zhou et al., 2023). The CF reinforced cement and CF grid reinforced concrete have also been studied worldwide (Ibrahim et al., 2022). For instance, Lavagna (Lavagna et al., 2018) and Huang (Huang et al., 2019) applied carbon fiber to cement, which significantly improved the integrity and durability of cement. The emerging application markets include deep-sea oil platforms and high-speed railways (Lu et al., 2020). Although CF has very high performance due to its own production process, its surface is very smooth, the surface free energy is extremely low showing strong “chemical inertia” (Sun et al., 2017), and the surface wettability is poor, which results in poor interface bonding with cement hydration products. In addition, there are many defects in the interface, and the direct use will limit its performance. Therefore, the introduction of polar groups on the surface of CF to improve its wettability in the cement matrix or to form chemical bonds with the matrix, is the key to obtain high-performance fiber-cement-based composites.
CF reinforced cement-based composites are closely related to the matching of cement and fiber types, parameter optimization, and quality control in the forming process (Zhuravlev, 2000). In recent years, researchers tried to enhance the interfacial properties of composites by CF surface modification. Gas (liquid) phase oxidation was used to enhance the surface activity of CF and improve the surface roughness. CF was also reinforced by carbon deposition. Although these methods improve the performance of CF and its reinforced composites to a certain extent, most of them only improve one of their properties at the expense of decreasing other performances. Moreover, most of the modification methods are difficult to match the production line due to various defects. Studies have shown that coating SiO2 on the surface of CF will significantly increase the roughness of the CF surface (Fu et al., 2019). Nano-SiO2 particles can play an anchoring role. When the material is sheared and stretched, the nano-sphere can hinder the external force and prevent the slip of CF.
However, the current research only optimized and discussed the process of CF coated with SiO2 to improve fiber-cement based composites, and there was a lack of research on the influence of different modification methods on CF surface characteristics. In addition, the interface structure of modified carbon fiber and cement matrix and its strengthening mechanism remain unclear. Therefore, in this paper, nano SiO2 was prepared by sol-gel method, and CF was modified by chemical grafting and sol coating. The surface morphology and elemental composition of CF modified by different methods were analyzed by scanning electron microscopy (SEM) and energy dispersive spectroscopy (EDS). The surface functional groups of CF were characterized by Fourier transform infrared spectroscopy (FTIR). Finally, the mechanical properties of cement paste reinforced by SiO2 coated-CF were evaluated, and the interface structure between coating CF and cementite matrix was analyzed, and the strengthening mechanism was expounded, which provided a certain theoretical and experimental basis for the research of oil well cement reinforced by modified CF.
2 Experiment
2.1 Experimental materials
2.1.1 Cement and admixture
Class G high sulfate resistant oil well cement produced by Sichuan Jiahua Enterprise Co., Ltd., was used in this study. Its composition is presented in Table 1. The cement additive fluid loss agent (G33S), dispersant (SXY-II), and defoamer used in this paper are provided by Weihui Chemical Co., Ltd.
2.1.2 Reinforcement materials
Carbon fibers produced by Dalian Xingke Carbon Fiber Co., Ltd., are the main raw materials used in this study. The surface microstructure is shown in Figure 1. The short and long fibers have a length of 100 ± 2 μm, and 1,000 ± 2 μm, respectively. The properties of carbon fibers are presented in Table 2. Ethyl orthosilicate (AR), nitric acid (AR), ammonia (AR), concentrated hydrochloric acid (AR), silane coupling agent KH-550 (AR), silane coupling agent KH-560 (AR), toluene (AR), anhydrous ethanol (AR), and acetone (AR) were produced by Chengdu KeLong Chemical Reagent Factory.
2.2 Experimental methods
2.2.1 Surface pretreatment of CF
CF was oxidized by concentrated nitric acid at 60°C for 1 h in a fume hood. After treatment, the CF was washed with distilled water to neutral and dried at 100°C in vacuum. 3% concentration of KH550 ethanol solution was prepared, and an appropriate amount of CF acid treated was then immersed in the prepared solution. Afterwards, ultrasonic oscillator reaction was performed for 2–3 h, ethanol washing was applied 3 times, and vacuum filtration was conducted. Finally, drying at 75°C was performed, and the obtained solution was recorded as KH550-CF.
2.2.2 Preparation of SiO2
Since this study mainly consists of a comparative analysis of two kinds of CF coating methods, the preparation of SiO2 is divided into two types.
2.2.2.1 Preparation of nano-SiO2
The preparation process of nano-SiO2 is shown in Figure 2. It consists of adding 200 mL absolute ethanol, 4 mL deionized water, 12 mL 25% ammonia, then stirring at 40°C for 2 h in 250 mL three-neck flask, quickly adding 11.2 mL tetraethoxysilane (TEOS), stirring overnight at 40°C, filtering, washing three times with ethanol, and drying at 75°C. The surface modification was then carried out. The appropriate amount of dry nano-SiO2 was added to a 50 mL beaker, 30 mL toluene was added, and ultrasonic dispersion at 40°C was performed until a uniform suspension was obtained. Afterwards, the KH560 silane coupling agent was added, transferred to a water bath, and reacted at 80°C under stirring. After the reaction, suction filtration was performed under high temperature in the suction filtration process with anhydrous ethanol repeatedly washed 5 times. The obtained nano-SiO2 was then dispersed in toluene again, and ultrasonic dispersion was performed followed by filtration and washing 2–3 times. Finally, the obtained nano-SiO2 was placed in an oven and dried at 75°C for 6 h to obtain the modified KH560-SiO2 white powder.
2.2.2.2 Preparation of SiO2 sol
The preparation process of SiO2 sol is shown in Figure 3. The analytically pure TEOS and distilled water were used as raw materials, anhydrous ethanol was used as solvent, and 25% HCl was used as catalyst for hydrolysis reaction. The sol was prepared according to the ratio of TEOS:anhydrous ethanol:deionized water of 1:4:1.5. TEOS and ethanol were first added to a three-necked flask and evenly stirred, water was then added, and finally hydrochloric acid was added to adjust the pH value to 2.5.
2.2.3 Preparation of SiO2 coating on carbon fiber surface
2.2.3.1 Grafting method
5 g KH560-SiO2 was first dispersed in 30 mL toluene and ultrasonically dispersed for 60 min 2 g KH550-CF was then added. After heating for 12 h, the reaction was cooled to room temperature, washed with ethanol for 6 times, and then dried at 75°C to obtain carbon fibers grafted with nano-SiO2.
2.2.3.2 Sol coating method
After the sol was prepared, anhydrous ethanol was used as diluent to dilute it with silicon atom having a w (Si) of 1%, and the sol was evenly mixed by ultrasonication. The sol with w (Si) of 1% was put into a beaker, and the weight of KH550-CF was 1.5 g was added. The sol was placed in an ultrasonic cleaner for 10 min, and then dried in a blast drying oven at 65°C for 12 h.
2.2.4 Preparation of cement samples
The cement slurry was prepared according to API RP 10B “Recommended Practice For Testing Well Cements” (Ibrahim et al., 2022), and the water cement ratio was 0.44. Uncoated and coated CFs were added into the cement slurry to prepare cement stone. The slurry formula is presented in Table 3. In addition, the experiment set up a blank group of pure cement stone. The prepared slurry was poured into the mold of size 50.8 × 50.8 × 50.8 mm, which was maintained in a constant temperature water bath of 60°C for 14 days.
2.2.5 Chemical structure and microstructure analysis
2.2.5.1 FT-IR analysis
The changes of functional groups of CF before and after coating were tested using the NICOLET 6700 Fourier infrared (IR) spectrometer. The CF samples before and after coating were mixed with potassium bromide at a ratio of 1:100 and evenly ground in an agate mortar. After being pressed into thin slices, the scanning range was 4,000–400 cm-1.
2.2.5.2 XRD analysis
The crystal structure of SiO2 was analyzed using the DX-2700B X-ray diffractometer. The sample was continuously scanned with a step of 0.04°/s and 2θ varying between 5° and 80°.
2.2.5.3 Scanning electron microscopy micro-morphology
The ZEISS EV0 MA15 scanning electron microscope was used to observe the micro-morphology of the surface and the interface of the samples. A small amount of untreated CF samples, two types of SiO2-CF samples, and fresh cement cross-section samples were placed on the conductive adhesive and sprayed with gold. A working voltage of 5 kV and a current of 10 μA were considered. EDS surface scanning was used to obtain the information of element type, content, and distribution in the selected area.
2.2.5.4 Mechanical properties of cement paste
The cement paste was prepared and cured at 60°C water bath for 14 days according to the GB/T19139 2012 “oil well cement test method.” The compressive strength and splitting tensile strength of cement stone were measured using an electronic hydraulic testing machine.
3 Results and discussion
3.1 Experimental results
3.1.1 XRD
The SiO2 thin film was analyzed by XRD to determine its composition and crystal form. Due to the irregular arrangement of internal atoms, the X-ray diffraction pattern of amorphous was very different from that of crystal, and the typical feature was the existence of ‘steamed bread peak’. It can be seen from Figure 4 that two obvious steamed bread peaks appeared at 2θ in the range of 5°–30°. A PDF card comparison analysis was performed on the diffraction pattern using the MDI Jade software. It was deduced that the steamed bread peak corresponding to 2θ of 21.98° was SiO2, which indicated that the composition of the coating was SiO2, the SiO2 film obtained under this condition did not complete the crystallization process, and the film was still amorphous. The amorphous alloy was in metastable state and had high energy and chemical activity.
3.1.2 FT-IR
Figure 5 shows the FT-IR absorption spectra of untreated CF and sol-coated SiO2-CF samples. By comparing the peak shape and peak position of the two spectral lines, it can be deduced that the types and quantities of functional groups on the CF surface significantly changed, which also indicated that the SiO2 film successfully adhered to the CF surface. For the untreated CF, the absorption peaks at 1,404 cm-1 and 1,625 cm-1 were caused by-COO- and C = O stretching vibration, and the absorption peak at 3133 cm-1 may be related to the C-H stretching vibration of methyl (-CH3) or methylene (-CH2-). For the SiO2-CF sample, the broad peak near 3374 cm-1 corresponded to the O-H symmetric stretching vibration, H-O-H bending vibration at 1,635 cm-1, Si-O-Si antisymmetric stretching, Si-O-C symmetric stretching at 1,137 cm-1 and 1,120 cm-1. The strong and wide peak around 719 cm-1 was related to the Si-O-Si symmetric stretching or O-H bending vibration. The peak near 2,146 cm-1 was caused by the presence of SiO2 in the film.
The infrared test results showed that the SiO2 film was successfully attached to the surface of CF and significantly changed its original surface chemical structure (functional group).
Figure 6 shows the FTIR absorption spectrum of SiO2-CF. The absorption peaks near 3,448 cm-1 and 1,641 cm-1 in the spectral line are the absorption peaks of water on the CF surface and in the surrounding air. By comparing the a and c curves, it can be deduced that after grafting nano-SiO2, new absorption peaks appear at 1,110 cm-1 and 804 cm-1. In addition, 804 cm-1 is the antisymmetric stretching vibration absorption peak of the Si-O-Si bond of SiO2. Moreover, a weak vibration absorption peak of -C-O-Si- appears at 1,110 cm-1. By comparing the a and b curves, it can be deduced that the asymmetric stretching vibration absorption peak (2,700–3000 cm-1) of -CH3 and -CH2- on the surface of CF after grafting is significantly larger, which is due to the grafted nano-SiO2 particles. The surface has also a large amount of -CH3 and -CH2-, and the increase of their number leads to a significant increase of the absorption peak. Grafting SiO2 on the surface of CF is equivalent to bringing in a large number of Si-O-Si bonds, and the absorption is further enhanced. That is, the absorption peak of CF near 1,110 cm-1 becomes significantly larger, and the symmetric stretching vibration absorption peak of Si-O-Si bond appears at 804 cm-1. The vibration absorption peak of -C-O-Si- (1,193 cm-1) appears in line A, which does not appear in line B. The changes of these peaks and the emergence of new peaks indicate that nano-SiO2 particles are successfully grafted on the CF surface.
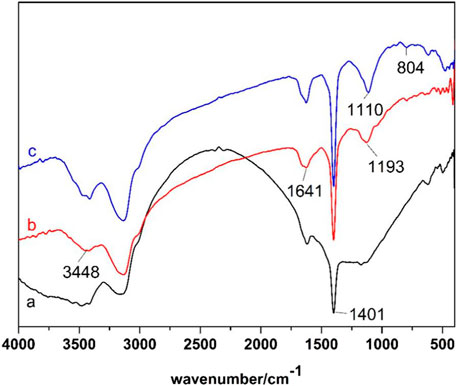
FIGURE 6. Infrared absorption spectrum of CF obtained using the grafting method (A): grafted silica CF; (B) KH560 treated CF; (C) unmodified CF).
3.1.3 Scanning electron microscopy morphology observation
In order to more intuitively and clearly obtain the microstructure of the SiO2 film on the CF surface, the adhesion effect of the film was determined. In the experiment, SEM was used to analyze the surface microstructure of the CF samples before and after modification. Among them, Figure 7 shows the microstructure of unmodified carbon fiber, Figure 8 shows the microstructure of carbon fiber after graft modification of SiO2, and Figure 9 shows the microstructure of carbon fiber after modification of SiO2 coating.
Figure 7 The uncoated CF surface has no impurity adhesion and has grooves parallel to the fiber, which facilitates the adhesion of the coating on the CF surface. Figures 8, 9 show the micro-morphology of CF after coating using the grafting and sol coating methods, respectively. It can be seen from Figure 8 that the surface of CF is covered with a large number of granular materials that are nano-SiO2. In addition, the surface parallel to the fiber axis is significantly reduced and the depth is shallow. This shows that nano SiO2 is successfully grafted onto the CF surface. It can be observed from Figure 9 that a thick and dense film is successfully attached to the CF surface. Compared with the CF without the film, the SiO2 film prepared using the sol coating method can be well attached to the CF surface, and the integrity of the film is better. After the SiO2 film is prepared on the CF surface, the longitudinal stripes on it are significantly reduced, which leads to a decrease of the surface roughness and the specific surface area. Although these two methods will reduce the CF surface parallel to the axial groove, the CF surface, namely, the SiO2 particles, are convex. It can provide an anchor point for the mechanical interlocking of fiber and matrix, and therefore it is beneficial for the mechanical interlocking of fiber and matrix.
3.2 Mechanical property
The compressive strength and tensile strength of cement stone samples with blank group (CF-0), unmodified CF (CF-0.4), and SiO2 surface film CF (SiO2-CF) were tested. The experimental results are shown in Figures 10A,B. It can be seen from Figure 10A that under the curing condition of 60°C, the compressive strength of the CF-0 cement stone sample at 14 days is only 26.13 Mpa, that of the unmodified CF cement stone is increased to 32.98 Mpa, and it can be increased by 26%. The compressive strength of the cement stone sample with SiO2 surface film is further improved. The compressive strength of the SiO2-CF cement stone sample at 14 days is increased to 38.64 Mpa, and it can be increased by 48%.
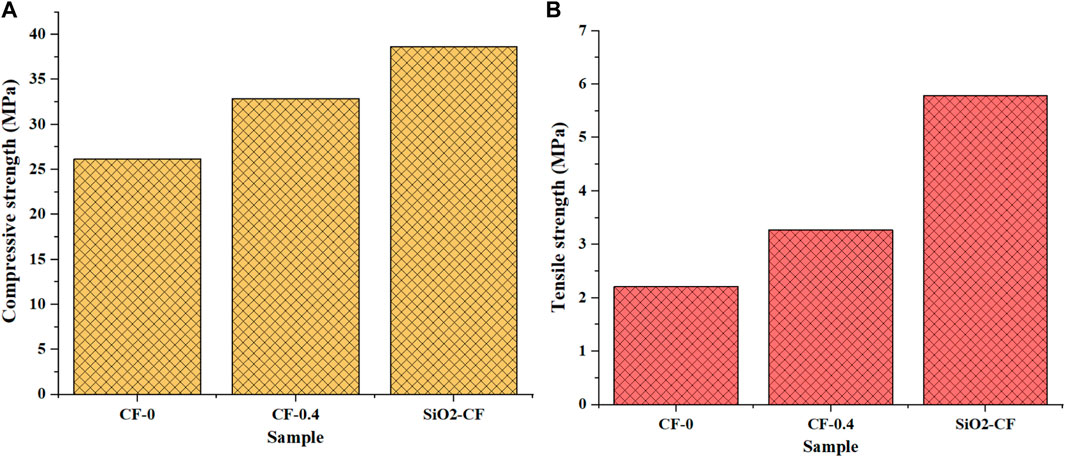
FIGURE 10. Tensile strength of cement stone specimens. (A) Compressive strength; (B) Tensile strength.
The tensile strength changes of the CF-0, CF-0.4, and SiO2-CF cement stone samples are shown in Figure 10B. It can be seen that the change rule of the tensile strength is similar to that of the compressive strength. The 14 days tensile strength of the cement stone sample with SiO2 surface film can reach 5.78 Mpa, and it is increased by 162%. Thus, adding SiO2 surface film can achieve the purpose of reinforcing and toughening the cement stone.
3.3 CF-cement paste interface structure
The surface morphology of the CF and SiO2 films in cement stone is shown in Figure 11. It can be seen from Figure 11A that CF is embedded in the cement stone matrix, and part of the SiO2 film on the surface completely falls off, revealing a smooth surface. However, the SiO2 film on the side near the cement stone does not fall off, and the root is tightly bonded in a fluffy state, which indicates that SiO2 on the CF surface reacts with calcium hydroxide to form hydrated calcium silicate. In Figure 11B, it can be observed that CF is completely wrapped by cement matrix and the interface is in good contact. Since the surface of carbon fiber is coated with active silicon dioxide, in an alkaline environment, active silicon dioxide can react with calcium hydroxide in volcanic ash. In Figure 11B, it can be obviously observed that carbon fiber becomes fluffy and big, which may be caused by the production of more hydration products such as C-S-H. When the cement stone is subjected to an external load, CF becomes the main carrier of the load. When the CF reinforced cement stone is broken under external force, if the plane of the crack development is perpendicular to the carbon fiber, the CF is pulled out of the cement stone and peeled off, as shown in Figure 11C. In the stripping process, energy will be consumed, which enhances the mechanical properties of the cement paste. By comparing the a and b diagrams, it can be deduced that the surface morphology of CF has significantly changed and the surface roughness has increased.
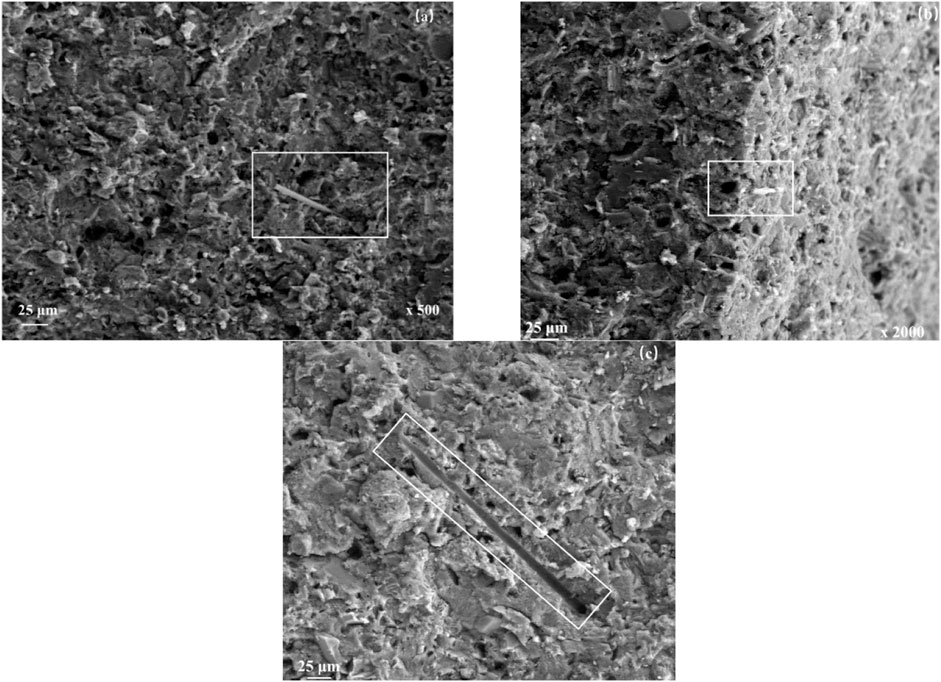
FIGURE 11. Cement paste-CF composite interface (A): The coated fiber is partially detached; (B) The interface between the modified fiber and the cement matrix is closely bonded; (C) The modified fibers are completely stripped.).
In order to further prove this inference, EDS scanning of granular materials on the CF surface was conducted (Figure 12). Note that microanalysis of the elements at the interface can be performed. The scan results are presented in Table 4.
The main elements include carbon (C), oxygen (O), silicon (Si), calcium (Ca), and gold (Au). C comes from CF, and Au is mainly caused by surface spray gold, and therefore it is not analyzed in this study. The granular material on the CF surface contains more O, Si, and Ca elements. This may be due to the fact that the coating SiO2 layer on the surface of CF participates in the hydration reaction and generates amorphous hydrated calcium silicate. Thus, the formation of chemical bonds at the interface allows to refine it and to improve the fiber adhesion, which leads to cement paste enhancement.
4 Conclusion
In this paper, Nano-SiO2 and SiO2 surface modified CF were prepared to study the influence of the modified CF on the mechanical properties of oil well cement paste. The main findings of this study can be summarized as follows.
(1) Through phase analysis and microstructure observation, it can be deduced that after the SiO2 film was prepared on the CF surface, its roughness decreased and there were SiO2 particle attachments on it. The SiO2 particle attachments provide anchor points for the mechanical interlocking of fibers and substrates.
(2) The evaluation results showed that the mechanical properties of the cement stone samples with SiO2 surface film are significantly improved, the compressive strength and tensile strength can be increased by 48% and 162%, respectively.
(3) After adding SiO2 surface film, CF improved the adhesion between the interface and the fiber by forming chemical bonds at the bonding surface with the cement stone, so as to improve the CF toughening cement stone.
Data availability statement
The original contributions presented in the study are included in the article/Supplementary Material, further inquiries can be directed to the corresponding author.
Author contributions
YG: Conceptualization, investigation, writing-original draft, data curation QR: Validation, resources, writing—review and editing, supervision. ZY: Validation, formal analysis, investigation, data curation DH: Formal analysis, project administration ZW: Formal analysis, project administration CZ: Resources, funding acquisition JC: Validation, resources, writing—review and editing, supervision. XC: Methodology, conceptualization.
Funding
The authors appreciate the support of the Sichuan Science and Technology Program (2021YFQ0045 and 2021YFSY0056) and the Cnooc’s preliminary project: Feasibility study of Wenchang 9-7 oilfield (2021PFS-05).
Acknowledgments
The authors would also like to thank the Advanced Cementing Materials Research Center of SWPU for their kind assistance with the experiments. This study was financially supported by 111 Project, No. D18016.
Conflict of interest
The authors YG, ZW, are from CNOOC Research Institute Co., Ltd., Beijing. The authors QR, ZY, are from CNPC Bohai Drilling Engineering Co. Ltd. The authors DH are from CNPC Engineering and Technology Research Institute of Southwest Oil and Gas Field Company. Authors CZ, JC, and XC are from School of New Energy and Materials, Southwest Petroleum University, Chengdu; This research is under the overall responsibility of the CNOOC Research Institute Co., Ltd. with the assistance of school of New Energy and Materials, Southwest Petroleum University.
The remaining authors declare that the research was conducted in the absence of any commercial or financial relationships that could be construed as a potential conflict of interest.
Publisher’s note
All claims expressed in this article are solely those of the authors and do not necessarily represent those of their affiliated organizations, or those of the publisher, the editors and the reviewers. Any product that may be evaluated in this article, or claim that may be made by its manufacturer, is not guaranteed or endorsed by the publisher.
References
da Silva, E. J., Marques, M. L., Velasco, F. G., Fornari Junior, C., Luzardo, F. M., and Tashima, M. M. (2017). A new treatment for coconut fibers to improve the properties of cement-based composites – combined effect of natural latex/pozzolanic materials. Technol 12, 44–51. doi:10.1016/j.susmat.2017.04.003
Fu, J., Zhang, M., Jin, L., Liu, L., Li, N., Shang, L., et al. (2019). Enhancing interfacial properties of carbon fibers reinforced epoxy composites via Layer-by-Layer self assembly GO/SiO2 multilayers films on carbon fibers surface. Appl. Surf. Sci. 470, 543–554. doi:10.1016/j.apsusc.2018.11.168
Huang, S., Cheng, X., Guo, X., Shi, Y., and Wang, W. (2019). Ethanol plasma-induced polymerization of carbon fiber surface for improving mechanical properties of carbon fiber-reinforced lightweight oil well cement. Appl. Surf. Sci. 497, 143765. doi:10.1016/j.apsusc.2019.143765
Ibrahim, A. M., Abd, S. M., Hussein, O. H., Tayeh, B. A., and Najm, . M. (2022). Influence of adding short carbon fibers on the flexural behavior of textile-reinforced concrete one-way slab. Case Stud. Constr. Mater 17, e01601. doi:10.1016/j.cscm.2022.e01601
Jafariesfad, N., Geiker, M. R., Gong, Y., Skalle, P., Zhang, Z., and He, J. (2017). Cement sheath modification using nanomaterials for long-term zonal isolation of oil wells: Review. J. Pet. Sci. Eng. 156, 662–672. doi:10.1016/j.petrol.2017.06.047
Lavagna, L., Musso, S., Ferro, G., and Pavese, M. (2018). Cement-based composites containing functionalized carbon fibers. Cem. Concr. Compos 88, 165–171. doi:10.1016/j.cemconcomp.2018.02.007
Li, M., Liu, M., Yang, Y., Li, Z., and Guo, X. (2015). Mechanical properties of oil well cement stone reinforced with hybrid fiber of calcium carbonate whisker and carbon fiber. Pet. Explor. Dev. 42, 104–111. doi:10.1016/s1876-3804(15)60012-x
Liu, X., Wang, G., Yu, J., Liu, R., Lyu, K., Zuo, J., et al. (2023). Stress-sensitivity of carbon nanotube-grafted-carbon fiber incorporated cement-based composites. J. Build. Eng. 64, 105589. doi:10.1016/j.jobe.2022.105589
Lu, J., Li, W., Kang, H., Feng, L., Xu, J., and Liu, R. (2020). Microstructure and properties of polyacrylonitrile based carbon fibers. Polym. Test. 81, 106267. doi:10.1016/j.polymertesting.2019.106267
Sun, J., Zhao, F., Yao, Y., Jin, Z., Liu, X., and Huang, Y. (2017). High efficient and continuous surface modification of carbon fibers with improved tensile strength and interfacial adhesion. Appl. Surf. Sci. 412, 424–435. doi:10.1016/j.apsusc.2017.03.279
Xiao, H., Zhang, F., Liu, R., Zhang, R., Liu, Z., and Liu, H. (2019). Effects of pozzolanic and non-pozzolanic nanomaterials on cement-based materials. Constr. Build. Mater 213, 1–9. doi:10.1016/j.conbuildmat.2019.04.057
Yang, Z., Yang, J., Shuai, B., Niu, Y., Yong, Z., Wu, K., et al. (2022). Superflexible yet robust functionalized carbon nanotube fiber reinforced sulphoaluminate cement-based grouting materials with excellent mechanical, electrical and thermal properties. Constr. Build. Mater. 328, 126999. doi:10.1016/j.conbuildmat.2022.126999
Yu, H., Lei, Y., Pei, C., Wei, L., Zhu, J. H., and Xing, F. (2022). Enhancing the mechanical and functional performance of carbon fiber reinforced cement mortar by the inclusion of a cost-effective graphene nanofluid additive. Cem. Concr. Compos. 134, 104777. doi:10.1016/j.cemconcomp.2022.104777
Zhang, C., Cai, J., Cheng, X., Zhang, X., Guo, X., and Li, Y. (2020). Interface and crack propagation of cement-based composites with sulfonated asphalt and plasma-treated rock asphalt. Constr. Build. Mater. 242, 118161. doi:10.1016/j.conbuildmat.2020.118161
Zhang, W., Zhang, Y., and Liu, B. (2021). Hybrid effect of basalt fiber and carbon fiber on the mechanical properties and microstructure of oil well cement. Constr. Build. Mater. 286, 122696. doi:10.1016/j.conbuildmat.2021.122696
Zhang, Y., He, M., Xu, M., Song, J., Xu, P., and Wang, X. (2020). Effect of modified sepiolite and carbon fiber composite on performance of oil-well cement and mechanism analysis. Constr. Build. Mater. 239, 117837. doi:10.1016/j.conbuildmat.2019.117837
Zhou, F., Pan, G., and Zhang, L. (2023). Enhancing the shrinkage resistance and impermeability of cement-based materials using carbon fiber modified by in situ-grown nano-SiO2 and carbon nanotubes. J. Build. Eng. 63, 105542. doi:10.1016/j.jobe.2022.105542
Keywords: oil well cement stone, interface, carbon fibers, SiO2 film, strength
Citation: Geng Y, Ren Q, Yang Z, He D, Wu Z, Cai J, Zhang C and Cheng X (2023) Preparation of SiO2 coated carbon fibers and its interfacial properties with cement paste matrix. Front. Mater. 10:1128054. doi: 10.3389/fmats.2023.1128054
Received: 20 December 2022; Accepted: 20 February 2023;
Published: 01 March 2023.
Edited by:
Haibo Li, Ningxia University, ChinaReviewed by:
Salim Barbhuiya, University of East London, United KingdomSun Dawei, Beijing University of Technology, China
Copyright © 2023 Geng, Ren, Yang, He, Wu, Cai, Zhang and Cheng. This is an open-access article distributed under the terms of the Creative Commons Attribution License (CC BY). The use, distribution or reproduction in other forums is permitted, provided the original author(s) and the copyright owner(s) are credited and that the original publication in this journal is cited, in accordance with accepted academic practice. No use, distribution or reproduction is permitted which does not comply with these terms.
*Correspondence: Xiaowei Cheng, chengxw@swpu.edu.cn