- 1Biosystems and Agricultural Engineering, Michigan State University, East Lansing, MI, United States
- 2Extension, Michigan State University, East Lansing, MI, United States
- 3Computer Science and Engineering, Michigan State University, East Lansing, MI, United States
Due to the impact of climate change on agriculture and the emergence of water security issues, proper irrigation management has become increasingly important to overcome the challenges. The Internet of Things (IoT) technology is being utilized in agriculture for collecting field information and sharing it through websites in real time. This study discusses the efforts taken to develop an IoT-based sensor station, a user-friendly website, and a smartphone app for irrigation management. In addition, the demonstration of the IoT-based sensor station and its effectiveness are discussed. Before deploying the sensor station, soil moisture sensor calibration was conducted using a laboratory experiment. Overall, the calibrated soil moisture sensors met the statistical criteria for both sand [root mean squared error (RMSE) = 0.01 cm3/cm3, index of agreement (IA) = 0.97, and mean bias error (MBE) = 0.01] and loamy sand (RMSE = 0.023 cm3/cm3, IA = 0.98, and MBE = −0.02). This article focuses on case studies from corn, blueberry, and tomato fields in Michigan, USA. In the corn and blueberry fields, the evaluation of irrigation practices of farmer's using an IoT-based sensor technology was considered. In the tomato field, a demonstration of automation irrigation was conducted. Overirrigation was observed using the IoT-based sensor station in some fields that have sandy soil and use a drip irrigation system. In the blueberry demonstration field, the total yield per plant (p = 0.025) and 50-berry weights (p = 0.013) were found to be higher with the recommended irrigation management than the farmer's existing field. In the tomato demonstration field, there were no statistical differences in the number of marketable tomatoes (p = 0.382) and their weights (p = 0.756) between the farmer's existing method and the recommended irrigation strategy. However, 30% less water was applied to the recommended irrigation strategy plot. Thus, the result showed that the IoT-based sensor irrigation strategy can save up to 30% on irrigation while maintaining the same yields and quality of the product.
1 Introduction
Irrigation is a crucial practice followed in agriculture for centuries and plays a significant role in developing economies worldwide. Irrigation is the process of supplying water to the crops using an artificial means to provide moisture, which helps in the growth and produces higher yields in crops. It is particularly important in regions with low precipitation and limited water resources. Irrigation also significantly impacts local rural economies by affecting the production of crops, creating jobs, increasing carbon sequestration, and boosting economic growth. Climate change poses a threat to agriculture. Erratic and unpredictable precipitation patterns, rising global average temperatures, and water scarcity can compromise food security (Rosa, 2022). Crop health is affected by rainfall trends, such as wetter springs, and drier summers with temperature anomalies, such as cold or heat waves (Alam et al., 2021). These flooding and drought events, without precision irrigation, can decrease the yield and quality of the product. In addition to these precipitation changes, average global temperatures are expected to increase by around 2°C each year until the year 2100. Higher temperatures lead to alterations in evapotranspiration (ET) and weed growth, affect pollination, and decrease photosynthesis rate, source-sink relationship, and crop duration, all of which can affect plant health and productivity (Malhi et al., 2021). Precision irrigation management practices have the potential to increase water use efficiency while minimizing the effects of climate change on farms.
Irrigation scheduling is a well-established strategy to manage crop water needs throughout the growing season. This method involves monitoring the water requirements of crops and determining whether the existing soil moisture and any additional water from precipitation and irrigation can fulfill them. Irrigation scheduling also considers economic and environmental variables. Every day, farmers face the challenge of making decisions that balance the cost of applying water (labor and energy) against the goal of achieving a high yield, enhanced crop quality, and the efficient use of water resources. Several types of irrigation scheduling have been demonstrated in the past, including ET-, soil moisture-, and artificial intelligence (AI)-based irrigation scheduling (Aguilar et al., 2015; Goap et al., 2018; Yang et al., 2020; Alibabaei et al., 2021; Dong, 2023; Kelley et al., 2023). ET-based irrigation scheduling is a method of irrigating a crop using daily reference ET, particular crop coefficient (Kc) value, and the amount of precipitation. Kc is determined by crop types and crop growth stage. This method has been shown to save water by up to 61% compared to the conventional irrigation application method (Simić et al., 2023). Soil moisture sensor-based irrigation scheduling utilizes soil moisture sensors to estimate soil moisture content in the root zone to ensure optimal moisture levels for crops and avoid overirrigation. Typically, soil moisture sensors are installed at multiple depths in the root zone to understand the soil moisture levels at different depths comprehensively. The changes in soil moisture at different depths help to estimate the root growth. Many types of soil moisture sensors are available, including tensiometers, capacitance sensors, time domain reflectometry (TDR) sensors, and frequency domain reflectometry (FDR) sensors. A tensiometer is a soil water tension measuring tool comprised of a porous ceramic cup with a water-filled tube working on the capillary action principle, which measures the soil matric potential expressing soil water energy. Capacitance sensors measure soil dielectric constants that differ for different moisture regimes, which provide real-time data for precise irrigation management (Smajstrla and Harrison, 2023). TDR is an approach that works on the principles of sending an electromagnetic pulse to the soil, and the travel time of the pulse is directly related to the soil moisture content, and it provides continuous soil moisture data across different depths, which helps in understanding efficient irrigation management (He et al., 2021). In addition to these sensors, FDR is another technique based on electromagnetic wave reflections that send high-frequency waves to the soil for measuring dielectric properties, which determines the soil moisture for precision irrigation management (Choi et al., 2016). Previously, this soil moisture sensor-based irrigation scheduling helped to save water by up to 60% compared to conventional irrigation methods (Muñoz-Carpena et al., 2005; Grabow et al., 2013; Millán et al., 2019). A study conducted by Boltana et al. (2023) showed that the soil moisture sensor-based method saved 18% of irrigation water compared to the ET-based method in tomato fields (Boltana et al., 2023). Moreover, the sensor-based irrigation method increased water use efficiency in soybean and potato fields by 49% and 16%, respectively (Wood et al., 2020; Dong et al., 2023). The AI-based irrigation scheduling analyzes multiple input data, such as soil moisture, soil temperature, air temperature, relative humidity, plant canopy temperature, crop type, crop growth stage, and yield data, to develop AI logarithms. Machine learning, deep learning, and reinforcement learning techniques are typically used for developing algorithms. These algorithms provide predictive analytics about optimum irrigation volume, time and frequency of irrigation, and yield data. These data can be used for the long-term planning of water usage based on weather forecasts and provide predictive measures for proactive interventions. This AI-based irrigation scheduling has been shown to improve the efficiency of water use for irrigation by up to 50% (Mohammad et al., 2013; Zia et al., 2021) and save the usage of water by 59% (Jamroen et al., 2020) compared to the industry standard method.
Of those methods discussed, weather- and soil moisture-based irrigation scheduling are the most common methods, as they are relatively cheap, more practical, and easier to use. While the weather-based irrigation scheduling method uses reference ET and Kc to determine when and how much to irrigate, the soil moisture-based irrigation scheduling method utilizes actual in-field soil moisture data using sensors to estimate the current soil water available and determine the irrigation decision. Soil moisture sensors can also be used for monitoring the spatial variation of soil moisture within the fields, thus allowing precise irrigation management. Recently, soil moisture sensor adoption in agriculture in the United States is only 12% (as of 2020) (Kukal et al., 2020). To increase this adoption rate, systems should be more cost-effective and easier to use (Dong, 2023). Furthermore, farmers need to be more educated on how they work to increase the trust in using them. The cost, difficulty to use, and trust are the major challenges for adopting the technology by farmers. Therefore, affordable and easy-to-use technology is needed to increase the its adoption. In addition, the demonstration of the technology in agricultural fields to show the potential use in improving the efficiency of irrigation water use is needed. In this study, we propose to develop an affordable and easy-to-use sensor monitoring system for farmers to improve irrigation management. We implement a low-cost sensor monitoring system (LOCOMOS) to measure soil moisture at multiple depths and use the data to provide irrigation recommendations. This article focuses on case studies using LOCOMOS in corn, blueberry, and tomato fields.
2 Methodology
LOCOMOS, which was developed by Michigan State University Irrigation Lab, was used in this study. LOCOMOS is an IoT-based sensor monitoring system that measures in-field soil and environmental conditions. The collected data were sent to the IoT cloud web server, from which irrigation recommendations were provided.
2.1 An IoT-based sensor monitoring system
A LOCOMOS system can continuously measure soil moisture levels at multiple depths, leaf wetness duration, air temperature, relative humidity, and precipitation. The data were then sent to a LOCOMOS IoT website (https://www.locomos1.com) to display the recommended irrigation timing and amount, the location of the sensor system, the raw sensor data, and the switch to turn irrigation on and off. The dashboard on the LOCOMOS IoT website was updated every 15 min, allowing the user to observe and make timely farm management decisions. An SD card module was utilized for storing and backing up the sensor data locally. LOCOMOS is powered by a 12V 7A battery, a 12V solar panel, and a solar battery charging controller. Email and Text message alert systems were set up through the IoT website. For example, a user could receive an email and text message when the soil water available level is at 50% for growing corn. SoilWatch 10, the soil moisture sensors, manufactured by Pino-Tech (Stargard, Poland), were utilized for measuring soil moisture levels. SoilWatch 10 is a relatively cheaper sensor and has provided reliable soil moisture measurement. PHYTOS 31 Leaf Wetness Sensor, manufactured by METER Group (Pullmen, WA, USA), was utilized to record the duration of leaf wetness. An SHT30 temperature and humidity sensor, manufactured by Sensirion (Chicago, IL, USA), was utilized for measuring the air temperature and relative humidity. The accuracy tolerance for air temperature and relative humidity were ± 0.3°C and ± 3%, respectively. A rain gauge, manufactured by Davis Instruments (Hayward, CA, USA), was utilized for measuring the precipitation. The rain gauge measured every 0.02 cm increment. Hunter ICV valves with DC latching solenoids were connected to the microcontroller to turn the valve on and off. Figure 1 shows a block diagram of the LOCOMOS system.
The LOCOMOS smartphone application (LOCOMOS APP) is an easy-to-use app designed for farmers to manage irrigation for their crops. The LOCOMOS APP connects to the LOCOMOS IoT server to visualize the sensor data on the app. Each user will be verified using a digital ocean server (Figure 2). Figure 3 shows the pages of the LOCOMOS APP. To access the app, existing users can log in using their registered email ID and password. New users can sign up using their email ID and a unique invitation code, which is provided by the server. Once logged in, a list of sensor devices will be displayed. Each device contains its GPS coordinates and provides real-time available soil water (%) and maximum recommended irrigation amount. In addition, the LOCOMOS APP gathers ET and precipitation information from the Michigan State University Enviroweather Network. Users can either push the “Use My Location” button or select the closest weather station to their field to observe the ET and precipitation data. In addition, the map page allows users to visualize the precise locations of all deployed sensors on a map. This bird's-eye view offers a comprehensive overview of users' farmlands, making it easier to identify the location of each sensor.
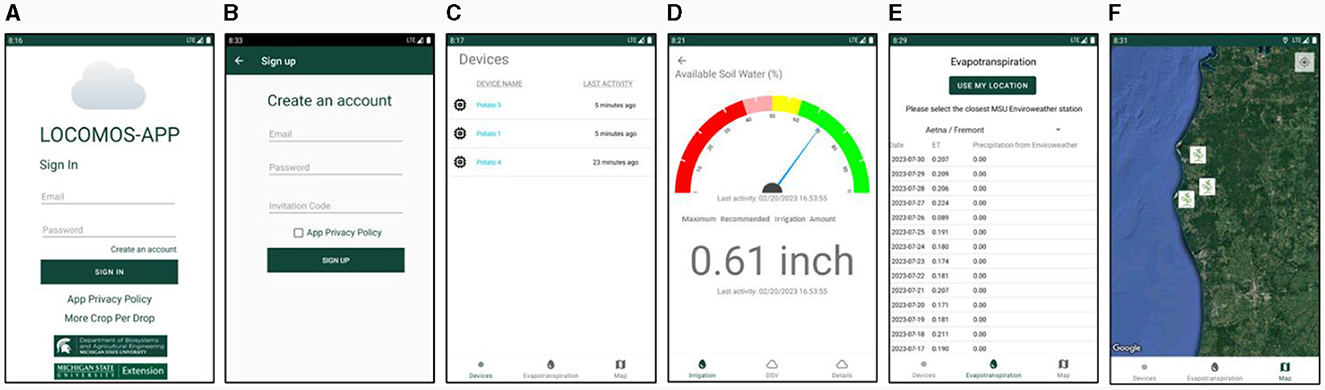
Figure 3. LOCOMOS-APP pages; (A) LOCOMOS login page, (B) Account setup, (C) Device list, (D) Available soil water and maximum recommended irrigation amount, (E) Weather information from MSU Enviroweather, and (F) LOCOMOS devices on the map.
2.2 Soil moisture sensor calibration
The calibration of soil moisture sensors to specific soil types was critical as the accuracy could be varied. A laboratory experiment was conducted to calibrate the SoilWatch 10 soil moisture sensors and evaluate their performances in two soil types. The soil types, including sand and loamy sand, were used in this laboratory experiment. Two 144-L size polypropylene containers (80 × 41 × 35 cm) were used. The volumetric water content (VWC) analysis was performed six times using a 61-cm3 size soil ring during this laboratory experiment. Detailed information on the procedure of the sensor calibration can be found in Smajstrla et al.'s study (Smajstrla and Harrison, 2023).
2.3 Soil moisture sensor-based irrigation recommendation model
The soil moisture sensor-based irrigation recommendation was estimated using the field capacity of soil and current soil moisture content using soil moisture sensors. The irrigation recommendation was calculated by finding the difference between the field capacity of the soil and the current soil moisture content. This recommendation was the maximum amount of irrigation that could be applied without water being lost through deep percolation beyond the root zone. The equation of soil moisture sensor-based irrigation recommendation is shown in Equation (1). An assumption was made that the volumetric soil water content for its representative soil layer is uniform and has the same moisture level.
where IR is the maximum irrigation recommendation (cm), FCLayeri is the field capacity of the layer i soil depth (cm/cm), DLayeri is the representative layer i soil depth (cm), and θvLayeri is the volumetric soil water content of the layer i soil depth (cm3/cm3).
2.4 Statistical analysis
The performance of the soil moisture sensors was evaluated using root mean squared error (RMSE), index of agreement (IA), and mean bias error (MBE). RMSE measures the difference between sensor values and soil sample values and is defined in Equation (2). The index of agreement was proposed by Willmott (1981), as defined in Equation (3). MBE is defined in Equation (4).
where N is the sample size, M is the measured (soil sampling) value, P is the predicted (sensor measurement) value, and is the average measured value. The units for RMSE and MBE are VWC (cm3/cm3), and IA is dimensionless. A range of IA lies between 0 and 1, and a value of 0 indicates no agreement between the measured and predicted values. A value of 1 indicates a perfect fit between the observed and predicted values. The higher value of IA indicates better agreement between observed and predicted values. Hignett and Evett (2008) revealed that the sensor measurement accuracy for most agricultural applications needs to be <0.02 cm3/cm3. Varble and Chávez (2011) and Dong et al. (2020) reported that the criteria for MBE and RMSE were ±0.02 cm3/cm3 and <0.035 cm3/cm3, respectively. Therefore, this study evaluated the sensor performance using the following criteria: MBE ± 0.02 cm3/cm3 and RMSE < 0.035 cm3/cm3.
2.5 LOCOMOS field demonstration—Irrigation practice evaluation
Once the sensors were calibrated and evaluated, LOCOMOS was deployed in irrigated fields in Michigan farmlands to evaluate the existing farmer's irrigation practices. Irrigated corn and blueberry fields were evaluated. The demonstration irrigated corn field was located in Manchester, Michigan, USA. A commercial corn was cultivated in this field and was irrigated with 20–28 cm of water and 224 kg/ha of nitrogen was applied. The commercial corn fields were irrigated using a center pivot irrigation system. The second demonstration field was located in West Olive, Michigan, USA. The field size was approximately 20 acres, and blueberries were cultivated in it. These blueberry fields were irrigated using a surface double-drip line system. Soil samples were collected to test the soil texture. The physical properties of the soils at different depths are shown in Table 1. The soils in these fields were mostly sandy soil, such as loamy sand and sandy loam, which were the common soil types in irrigated fields in Michigan. Figure 4 shows installed LOCOMOS in the irrigated corn and blueberry fields in Michigan, USA. Corn roots typically grow up to 90 cm in this demonstration field. Thus, the soil moisture sensors were installed at 15, 60, and 90 cm in the irrigated corn field. In the irrigated blueberry field, the sensors were installed at 15, 30, 45, and 60 cm. All data loggers were programmed to record soil moisture measurements every 30 min. The soil samples were collected three times during this monitoring period. These samples were analyzed for texture and volumetric water content. The VWC from the soil samples was utilized for testing the accuracy of the sensors.
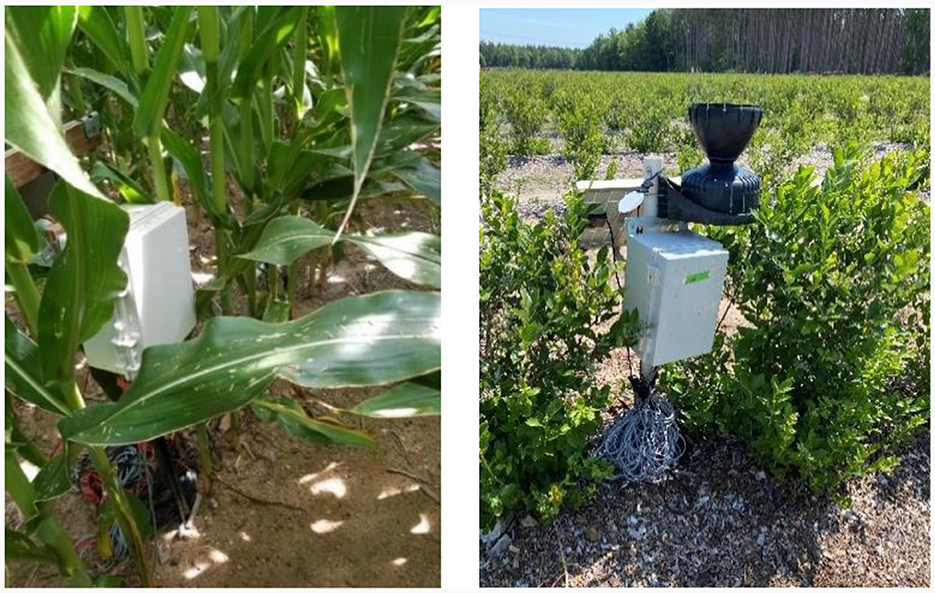
Figure 4. LOCOMOS stations installed in an irrigated corn field in Manchester, MI, USA (left) and an irrigated blueberry field in West Olive, MI, USA (right).
2.6 LOCOMOS field demonstration—automation irrigation
Automation irrigation using LOCOMOS was demonstrated in a tomato field in Hart, Michigan, USA. The 9V DC solenoid valves with Hunter's ICV valves were utilized to control irrigation. Fresh tomatoes were cultivated in this field, and plastic mulch was used to maintain the soil moisture and keep the weeds out. Figure 5 shows the experimental setup for this tomato field. This tomato field is irrigated with a surface single drip line system. Two irrigation strategies, namely, the farmer's existing irrigation management and automation irrigation trigger, were evaluated. The farmer's existing irrigation management included 1 h of irrigation per day in June and twice in 1 h of irrigation per day in July and August. The automation irrigation trigger method was based on the soil moisture sensor data and used Equation (1). Four replications with randomized plot designs were utilized for the comparison. The team has collected the number of marketable tomatoes and their weights to compare the effectiveness of the treatments. Eight plants per replication were considered. Statistic software R v4.3.1 was utilized for running a one-way ANOVA.
3 Results and discussion
3.1 Soil moisture sensor calibration
The calibration of the SoilWatch 10 soil moisture sensor was conducted for sand and loamy sand. Soil temperature during this laboratory experiment was kept constant at 22 ± 1°C. The soil moisture sensors were powered at 3.3 V, and analog raw counts were used for the calibration. Figure 6 shows the comparison of measured VWC and raw count. Based on the curve fitting, Equation (5) was developed. The calibration of SoilWatch 10 was based on a wide range of VWC from 0.04 to 0.4 cm3/cm3. The calibration of the sensor provided confidence in using it for field demonstration.
where VWC is the volumetric water content (cm3/cm3) and RC is the analog raw counts that outputs from the sensor.
3.2 The performance evaluation of the soil moisture sensor
The performance of the soil moisture sensor in the sand and loamy sand was evaluated. Figures 7, 8 show the comparison of sensors with measured VWC using a gravimetric method for sand and loamy sand, respectively. Table 2 shows the result of the statistical analysis. The MBE values for the soil moisture sensor showed that this sensor overestimated VWC by an average of 0.01 cm3/cm3 in the sand and underestimated it by an average of 0.02 cm3/cm3 in the loamy sand. The performance of the soil moisture sensor for sand and loamy sand satisfied both MBE and RMSE criteria. The MBE values of the calibrated SoilWatch 10 were similar to Campbell Scientific's CS 616 TDR sensors. The MBE of CS 616 for sand and loamy sand were 0.01 and 0.03 cm3/cm3, respectively (Dong et al., 2020). The calibrated SoilWatch 10 provided reliable performance in measuring moisture content in sand and loamy sand. This confirmed the satisfaction of the calibration process.
3.3 Demonstration in an irrigated corn field
Figure 9 shows the collected soil moisture sensor data, precipitation, and irrigation. Appropriate irrigation should maintain the soil moisture level in the root zone at an optimal level and ensure the water does not flow below the root zone to save freshwater and energy, reducing nutrient leaching and maximizing return on investment. The corn roots in this demonstration field grew up to 90 cm; thus, the goal of irrigation management was to moisten only the top 90 cm of soil. During the growing season, five events affected increasing soil moisture levels at a depth of 90 cm, which means that the water has reached and passed through the 90 cm depth. In events #1, #3, and #5, soil moisture at a depth of 90 cm increased due to continuous and heavy rainfalls. In events #2 and #3, the soil moisture level at 90 cm depth was increased due to the combination of rainfall and irrigation. The corn farmer in Michigan typically applied irrigation each time between 2.50–3.20 cm. When heavy rainfall is forecasted, the farmer could reduce the irrigation application volume to capture the rainfall within the root zone and minimize the potential leaching of water and nutrients below the root zone. In addition, the installation of the SoilWatch 10 soil moisture sensors within the root zone and right below the root zone helps to evaluate whether the farmer is applying irrigation adequately or excessively. These sensor data are helpful in making better-informed decisions on when and how much to irrigate.
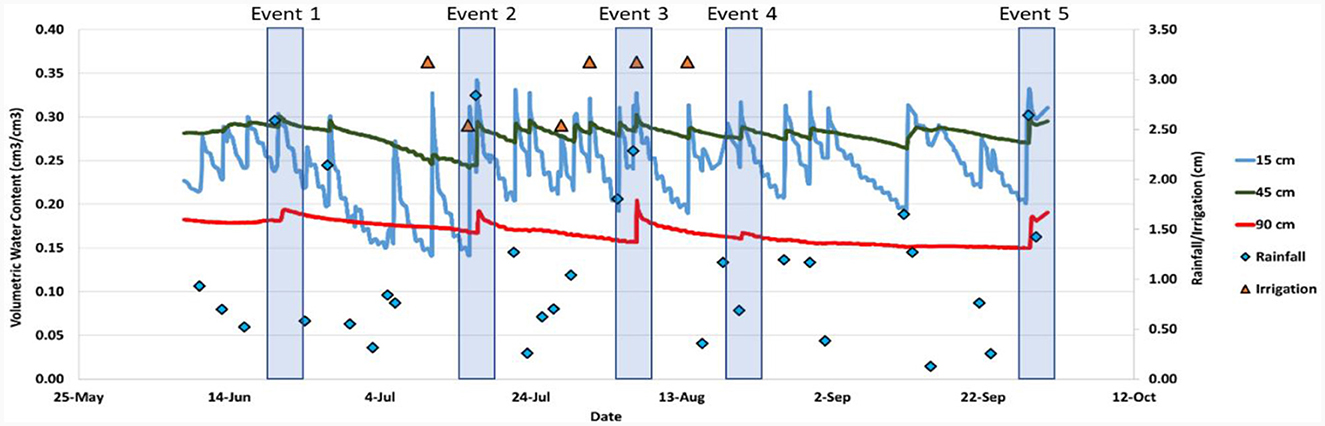
Figure 9. The volumetric water content at 15, 45, and 90 cm soil depths at an irrigated corn demonstration field.
3.4 Demonstration in an irrigated blueberry field
In the irrigated blueberry field, soil moisture sensors were installed at 15, 30, 45, and 60 cm depths. The flow rate of the drip emitter was 41 cm/h and was applied for 60 min during each application. During this monitoring period, there were no rainfalls. Figure 10 shows the soil moisture changes from the farmer's irrigation management practice. Proper irrigation for blueberries on this farm should ensure that water does not flow below the root zone, which is the top 45 cm of soil depth. Figure 10 indicates that the farmer's existing irrigation management practice provided an adequate amount of water to the blueberry root system. However, the overirrigation events were observed because of the spike in the soil moisture sensor at both 45 and 60 cm depths. Thus, it was recommended to reduce the irrigation time from 60 min to 40 min. The farmer tested his part of the field to demonstrate the reduced and recommended irrigation management practice. Figure 11 shows the soil moisture monitoring at the reduced and recommended irrigation plots. The reduced irrigation increased the soil moisture levels of the depth up to 30 cm, which is the effective water uptake root zone for blueberries grown in sandy soil. Thus, the reduced and recommended amount was adequate; however, when the blueberry was at the significant growth stage (at first blue fruit) and higher ET, more frequent (three times a day) irrigation was suggested, if needed. The soil type in this blueberry field is loamy sand. A smaller amount and more frequent application might be needed for the fields that have sandy soil. For finer texture soils, irrigating once a day with large volume application might be adequate as they have a large water holding capacity.
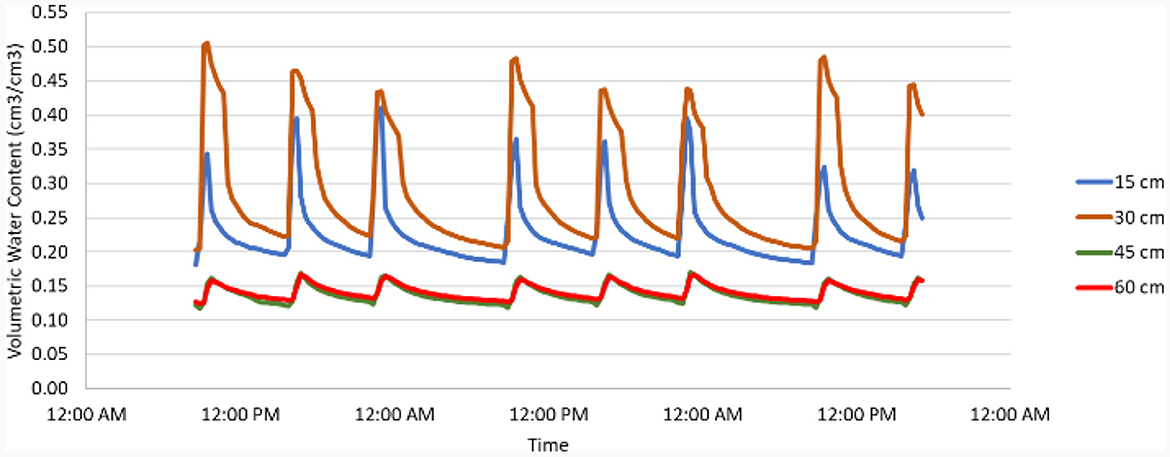
Figure 10. Soil moisture monitoring at the existing blueberry farmer's irrigation practice at the blue fruit stage.
The total yield/plant and 50-berry weights were collected from this demonstration field for both the farmer's existing irrigation method and the reduced/recommended irrigation management. The yield per plant for the farmer's irrigation method and the recommended irrigation management were 552 and 722 g, respectively. There were statistical differences between the treatments (p = 0.025). 50-berry weights for the farmer's irrigation method and the recommended irrigation management were 87.7 and 93.7 g, respectively. There were statistical differences between the treatments (p = 0.013). A potential cause of higher yield in the recommended irrigation management could be due to proper irrigation application that reduced nutrient leaching below the root zone in the sandy soil. An IoT-based irrigation management can help save water while maintaining the same blueberry quality and yields as the farmer's typical irrigation management.
3.5 Irrigation automation in a tomato field
Figure 12 shows the number of tomatoes that are marketable and their total weight from each treatment. The figure shows that there were no statistical differences among the treatments in the numbers of marketable tomatoes from the 2022 growing season (p = 0.382) and their weights (p = 0.756). Thus, the production and quality of tomatoes were similar from all treatments, but the amount of applied irrigation was different. The sensor-based irrigation strategy applied a 30% lower amount than the farmer's irrigation scheduling method, which indicates that the farmer could improve their irrigation water use efficiency using the sensor technology. An IoT-based automation irrigation management using a soil moisture sensor's recommendation can help to save water by 30% while maintaining the same marketable yields and quality of tomatoes as the farmer's typical irrigation management. In addition to conserving water, saving energy by pumping less water reduces farm energy costs. Moreover, low energy usage contributes to reducing greenhouse gas emissions from agriculture. The primary benefit of an automatic irrigation system is that it can save farmers' time and labor costs in operating the irrigation system.
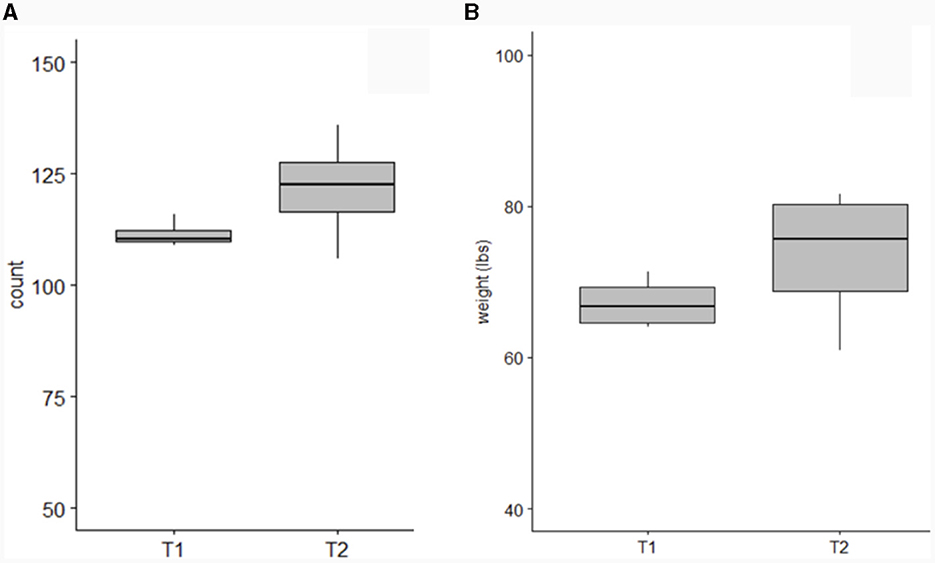
Figure 12. The total number of marketable tomatoes (A) and the total weight of marketable tomatoes from each replication (B). T1 is the farmer's typical irrigation management. T2 is an IoT soil moisture sensor-based irrigation recommendation.
4 Conclusion
Based on the field demonstration, the IoT-based sensor technology has proven to improve irrigation water use efficiency by evaluating the farmer's existing irrigation practices and providing recommendations if needed. Providing real-time in-field soil moisture sensor data is helpful in making day-to-day irrigation management decisions, especially under unpredictable precipitation patterns. Minimizing overirrigation can reduce the risk of nutrients leaching below the root zone, ultimately protecting groundwater quality. In future studies, more on-farm demonstrations are needed to increase technology adoption. In addition, a continuation of extension outreach activities to promote making irrigation management decisions based on scientific data is needed. Besides irrigation management, this IoT sensor technology can be utilized to help other management practices such as nutrient, pesticide, insecticide, frost protection, and plant health monitoring (heat and water stress). Therefore, continued efforts to explore the application of IoT-based sensor technology in agriculture to combat the effect of climate change are needed.
LOCOMOS utilizes cellular networks to communicate; however, cellular reception may be poor in some rural areas. Other communication network systems, such as radio, NB-IoT, and Sigfox, should be explored to overcome the signal issues. Moreover, the effectiveness of IoT-based technology should also be evaluated in other crop types. The usability of the LOCOMOS technology, including the installation technique, software interface, data accessibility, and alert systems, needs to be improved to make the technology easy to adopt for farmers. Additionally, other potential applications of the LOCOMOS platform, such as wind speed for spray drift reduction, soil moisture sensors for irrigation management, leaf surface temperature measurement for plant heat stress, and carbon dioxide measurement for greenhouse gas emission, should be considered in the future. Concerns about agricultural water use have been and will continue to grow due to the effect of climate change on agriculture. Because water is a limited resource, technologies that improve irrigation water use efficiency will play a significant role in increasing agricultural water sustainability.
Data availability statement
The datasets presented in this article are not readily available because the data will be made available strictly for academic purposes upon justification. Requests to access the datasets should be directed to YD (corresponding author).
Author contributions
YD: Conceptualization, Data curation, Funding acquisition, Investigation, Methodology, Resources, Supervision, Visualization, Writing – original draft, Writing – review & editing. BW: Conceptualization, Methodology, Writing – original draft, Writing – review & editing. ZC: Conceptualization, Methodology, Writing – original draft, Writing – review & editing. GL: Methodology, Writing – original draft, Writing – review & editing.
Funding
The author(s) declare financial support was received for the research, authorship, and/or publication of this article. The author would like to thank Michigan Department of Agriculture and Rural Development and Michigan Translational Research and Commercialization (MTRAC) AgBio Innovation Hub, Michigan State University AABI ProjectGREEEN, Michigan Blueberry Commission, and USDA Natural Resources Conservation Services (NRCS) for supporting the funding for the project. Author appreciate utilizing the information collected from the USDA Natural Resources Conservation Service Project (Grant No. NR213A750013G015) to support this paper.
Acknowledgments
The author appreciates Lyndon Kelley, Steve Miller, Brenden Kelley, Hunter Hansen, Catherine Christenson, and Allison Smith for their support in conducting experiments.
Conflict of interest
The authors declare that the research was conducted in the absence of any commercial or financial relationships that could be construed as a potential conflict of interest.
Publisher's note
All claims expressed in this article are solely those of the authors and do not necessarily represent those of their affiliated organizations, or those of the publisher, the editors and the reviewers. Any product that may be evaluated in this article, or claim that may be made by its manufacturer, is not guaranteed or endorsed by the publisher.
References
Aguilar, J., Rogers, D., and Kisekka, I. (2015). Irrigation scheduling based on soil moisture sensors and evapotranspiration. Kansas Agricult. Exp. Station Res. Rep. 1, 5. doi: 10.4148/2378-5977.1087
Alam, M. S., Han, B., and Pichtel, J. (2021). Irrigation suitability of white river in Indiana, midwestern USA. Environ Geochem Health 43, 2. doi: 10.1007/s10653-021-00905-2
Alibabaei, K., Gaspar, P. D., and Lima, T. M. (2021). Crop yield estimation using deep learning based on climate big data and irrigation scheduling. Energies (Basel) 14, 3004. doi: 10.3390/en14113004
Boltana, S. M., Bekele, D. W., Ukumo, T. Y., and Lohani, T. K. (2023). Evaluation of irrigation scheduling to maximize tomato production using comparative assessment of soil moisture and evapotranspiration in restricted irrigated regions. Cogent. Food Agric. 9, 2214428. doi: 10.1080/23311932.2023.2214428
Choi, E.-Y., Kim, H.-Y., Choi, K.-Y., and Lee, Y.-B. (2016). Comparisons in volumes of irrigation and drainage, plant growth and fruit yield under fdr sensor-, integrated solar radiation-, and timer-automated irrigation systems for production of tomato in a coir substrate hydroponic system. Prot. Horticult. Plant Fact. 25, 63–70. doi: 10.12791/KSBEC.2016.25.1.63
Dong, Y. (2023). “Irrigation scheduling methods: overview and recent advances,” in Irrigation and Drainage - Recent Advances. Intechopen. doi: 10.5772/intechopen.107386
Dong, Y., Check, J., Willbur, J., and Chilvers, M. (2023). Improving Irrigation and Disease Management in Irrigated Potato Fields Using IoT-Based Sensor Technology (Omaha, Nebraska: American Society of Agricultural and Biological Engineers).
Dong, Y., Miller, S., and Kelley, L. (2020). Performance evaluation of soil moisture sensors in coarse-and fine-textured michigan agricultural soils. Agriculture (Switzerland) 10, 598. doi: 10.3390/agriculture10120598
Goap, A., Sharma, D., Shukla, A. K., and Rama Krishna, C. (2018). An IoT based smart irrigation management system using machine learning and open source technologies. Comput. Electron. Agric. 155, 40. doi: 10.1016/j.compag.2018.09.040
Grabow, G. L., Ghali, I. E., Huffman, R. L., Miller, G. L., Bowman, D., and Vasanth, A. (2013). Water application efficiency and adequacy of ET-basedand soil moisture–based irrigation controllers for turfgrass irrigation. J. Irrigat. Drain. Eng. 139, 113–123. doi: 10.1061/(ASCE)IR.1943-4774.0000528
He, H., Aogu, K., Li, M., Xu, J., Sheng, W., Jones, S. B., et al. (2021). “A review of time domain reflectometry (TDR) applications in Porous media,” in Advances in Agronomy. (Cambridge: Academic Press Inc), 83–155.
Hignett, C., and Evett, S. (2008). “Direct and surrogate measures of soil water content,” in Field Estimation of Soil Water Content (Vienna: International Atomic Energy Agency (IAEA): IAEA), 1–21.
Jamroen, C., Komkum, P., Fongkerd, C., and Krongpha, W. (2020). An intelligent irrigation scheduling system using low-cost wireless sensor network toward sustainable and precision agriculture. IEEE Access 8, 172756–172769. doi: 10.1109/ACCESS.2020.3025590
Kelley, B., Chilvers, M., Kelley, L., Miller, S., and Dong, Y. (2023). “Implementation of a Sensor Monitoring System to Improve Irrigation Management through On-Farm Demonstration,” in Proceedings of the 2023 ASABE Annual International Meeting. (Omaha, Nebraska: American Society of Agricultural and Biological Engineers), 2300137.
Kukal, M. S., Irmak, S., and Sharma, K. (2020). Development and application of a performance and operational feasibility guide to facilitate adoption of soil moisture sensors. Sustainability (Switzerland) 12, 321. doi: 10.3390/su12010321
Malhi, G. S., Kaur, M., and Kaushik, P. (2021). Impact of climate change on agriculture and its mitigation strategies: a review. Sustainability (Switzerland) 13, 1318. doi: 10.3390/su13031318
Millán, S., Casadesús, J., Campillo, C., Moñino, M. J., and Prieto, M. H. (2019). Using soil moisture sensors for automated irrigation scheduling in a plum crop. Water (Switzerland) 11, 2061. doi: 10.3390/w11102061
Mohammad, F. S., Al-Ghobari, H. M., and ElMarazky, M. S. A. (2013). Adoption of an intelligent irrigation scheduling technique and its effect on water use efficiency for tomato crops in arid regions. Aust J. Crop Sci. 7, 13985083.
Muñoz-Carpena, R., Dukes, M. D., Li, Y. C., and Klassen, W. (2005). Field comparison of tensiometer and granular matrix sensor automatic drip irrigation on tomato. Hort Technol. 15, 584–590. doi: 10.21273/HORTTECH.15.3.0584
Rosa, L. (2022). Adapting agriculture to climate change via sustainable irrigation: biophysical potentials and feedbacks. Environm. Res. Lett. 17, 063008. doi: 10.1088/1748-9326/ac7408
Simić, D., Pejić, B., Bekavac, G., Mačkić, K., Vojnov, B., Bajić, I., et al. (2023). Effect of different ET-based irrigation scheduling on grain yield and water use efficiency of drip irrigated maize. Agriculture (Switzerland) 13, 1994. doi: 10.3390/agriculture13101994
Smajstrla, A. G., and Harrison, D. S. (2023). Tensiometers for Soil Moisture Measurement and Irrigation Scheduling. University of Florida Extension CIR487.
Varble, J. L., and Chávez, J. L. (2011). Performance evaluation and calibration of soil water content and potential sensors for agricultural soils in Eastern Colorado. Agric. Water Manag. 101, 7. doi: 10.1016/j.agwat.2011.09.007
Willmott, C. J. (1981). On the validation of models. Phys Geogr 2, 2213. doi: 10.1080/02723646.1981.10642213
Wood, C. W., Krutz, L. J., Henry, W. B., Irby, T., Orlowski, J. M., Bryant, C. J., et al. (2020). Developing sensor-based irrigation scheduling that maximizes soybean grain yield, irrigation water use efficiency, and returns above irrigation costs. Crop Forage Turfgrass Manage. 6, 20029. doi: 10.1002/cft2.20029
Yang, Y., Hu, J., Porter, D., Marek, T., Heflin, K., Kong, H., et al. (2020). Deep reinforcement learning-based irrigation scheduling. Trans ASABE 63, 13633. doi: 10.13031/trans.13633
Keywords: irrigation, Internet of Things (IoT), soil moisture sensors, smart agriculture, automation
Citation: Dong Y, Werling B, Cao Z and Li G (2024) Implementation of an in-field IoT system for precision irrigation management. Front. Water 6:1353597. doi: 10.3389/frwa.2024.1353597
Received: 11 December 2023; Accepted: 26 January 2024;
Published: 15 February 2024.
Edited by:
Abdelazim Negm, Zagazig University, EgyptReviewed by:
Tamer A. Elbana, National Research Centre, EgyptKaveh Ostad-Ali-Askari, Stanford University, United States
Copyright © 2024 Dong, Werling, Cao and Li. This is an open-access article distributed under the terms of the Creative Commons Attribution License (CC BY). The use, distribution or reproduction in other forums is permitted, provided the original author(s) and the copyright owner(s) are credited and that the original publication in this journal is cited, in accordance with accepted academic practice. No use, distribution or reproduction is permitted which does not comply with these terms.
*Correspondence: Younsuk Dong, ZG9uZ3lvdW5AbXN1LmVkdQ==