- 1Faculty of Built Environment, Research Centre Terra, Tampere University, Tampere, Finland
- 2Materials Science and Environmental Engineering, Faculty of Engineering and Natural Sciences, Tampere University, Tampere, Finland
The primary contributors to greenhouse gas (GHG) emissions in railway transport include the energy consumed during transportation, the materials used for infrastructure construction, and maintenance. Track structures commonly employ materials with a substantial carbon footprint, such as concrete and steel. This article explores the feasibility of using materials with a smaller carbon footprint for track structures. Recycled plastics that are currently incinerated might serve as a viable alternative. The key research question revolves around whether GHG emissions resulting from track construction and maintenance can be reduced by utilizing recycled plastics. Among various track components, sleepers were chosen as a potential application for recycled plastic due to their substantial material usage and consequent impact on overall emissions. The study also investigated the necessary material properties for plastic sleepers and assessed whether recycled plastic could meet those requirements. The study investigated recycled plastic fractions, including waste materials recycled by incineration, acrylonitrile butadiene styrene (ABS) from waste electrical and electronic equipment (WEEE), and a byproduct of liquid packaging cardboard repulping (LPB repulping reject). These materials offer a reduced carbon footprint because they have already completed one life cycle and can still be recycled as material. To assess their mechanical properties, laboratory tests were conducted on injection-molded test rods made from recycled plastic components. These rods underwent tensile and bending tests using a universal testing device. Additionally, the softening temperatures of the materials were measured through Vicat and HDT tests. Finally, based on the amount of waste material flows, the emission reduction potential obtained using recycled plastic was evaluated. Recycled ABS is significantly more suitable for use in track structures due to its superior mechanical durability compared to LPB repulping reject. Additionally, recycling ABS as a sleeper material significantly reduces overall GHG emissions compared to incineration.
1 Introduction
Evaluating the carbon footprint of railway system requires selecting appropriate indicators for calculation. These indicators can include primary energy, carbon dioxide CO2 (global warming potential), particulate matter (PM10) and nitrogen oxide (NOX) (Tuchschmid et al., 2011). In this study, we focus on solely on CO2 emissions. The distribution of emissions across train traffic, construction, and maintenance depends heavily on the line’s traffic volume. On busy high-speed lines, energy consumption for moving trains can account for over 70% of total emissions (Lin et al., 2019). Conversely, on low-volume lines, construction materials play a more significant role. The type of energy production also significantly impacts overall emissions. Regarding construction materials, concrete and steel have high specific emissions. Consequently, bridges, tunnels, and rails contribute significantly to emissions (Lin et al., 2019). However, the most promising application for recycled plastic is estimated to be railway sleepers, although encouraging studies have also explored the use of recycled plastic as part of the track’s substructure materials (Arulrajah et al., 2020; Imteaz et al., 2021).
In addition to energy usage, the carbon footprint of materials used in track construction includes factors such as virgin raw materials, manufacturing equipment, and production process emissions. Additionally, emissions occur during transportation and handling. The recyclability of materials—how they are used after their initial life cycle—significantly impacts total emissions. For instance, railway sleepers can be reused as material, incinerated for energy, or, in the worst case, disposed of in a landfill or similar trivial manner. Among traditional sleeper materials, wood can be easily incinerated for energy. Concrete sleepers are typically crushed, and the resulting crushed concrete can be used for service roads and, to some extent, in manufacturing new concrete sleepers. Rebar used in sleepers and steel sleepers are readily recyclable materials.
Regarding emissions, manufacturing sleepers plays a significant role. Rempelos et al. (2020) estimate that the largest carbon footprint from manufacturing is associated with steel sleepers, followed by concrete sleepers, hardwood sleepers, and finally, softwood sleepers (Figure 1). The unit of measurement is tCO2e per stkm (CO2 equivalent emissions normalized over a kilometer of single railway track). Overall, the emissions from railway sleepers are relatively small when considering the entire system. For instance, Lin et al. (2019) estimate the total annual emissions of the Beijing-Shanghai High-Speed Line to be 3,000 kilotonnes (kt) of CO2. Dividing this by the line’s length (1,318 km) results in annual emissions of 2,278 tCO2e per km. Assuming a sleeper life of 30 years, concrete sleepers contribute annual emissions only 4 tCO2e per km (or 8 tCO2e per km for a double track). Thus, sleeper manufacturing emissions constitute only a small portion of the total emissions for a busy track line.
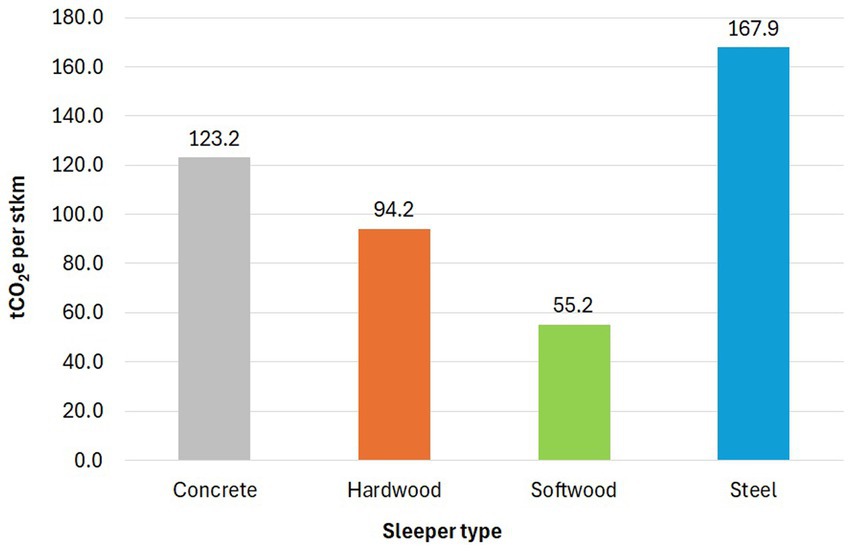
Figure 1. CO2 impact from the construction (materials, labour and plant, transport) of a stkm for each sleeper type (in tonnes of CO2e emissions per stkm). Reprinted from (Rempelos et al., 2020) and The Lancet with permission from Elsevier.
Emissions during the life cycle are significantly affected by the lifespan of the sleeper, which varies between 10 and 60 years (Ueda et al., 1999; Milford and Allwood, 2010; Manalo et al., 2010; Bolin and Smith, 2013; Ferdous and Manalo, 2014; Ferdous et al., 2015). On low-traffic lines, the need to renew sleepers arises primarily due to age or decay. However, on busy lines, sleepers may require replacement multiple times during the review period due to mechanical damage. Rempelos et al. (2020) used a 60-year review period for their calculations. The emissions over the entire life cycle were practically double compared to manufacturing concrete sleepers for a normally operated line (10 EMGTPA), assuming that concrete sleepers need replacement once during the review period. Regarding wooden sleepers, their total emissions were relatively higher because they are replaced 3–4 times during the review period and are typically disposed of in landfills. Nevertheless, wooden sleepers have the lowest emissions overall for 10 EMGTPA line. On busy track lines (60 EMGTPA), the emission effects balance out between concrete and wooden sleepers, as wooden sleepers must be replaced multiple times. Steel sleepers, assuming high traffic volume, exhibit even higher emissions compared to other types. The study assumed that on busy track line concrete sleepers would be renewed twice, hardwood sleepers three times, softwood sleepers six times, and steel sleepers three times during the review period. Carbonation of concrete and incineration with heat recovery for wooden sleepers contribute to reduced total emissions. In these comparisons, concrete sleepers exhibit the lowest direct emissions. However, when considering sleeper disposal, softwood sleepers ultimately result in the lowest total emissions (Figure 2) (Rempelos et al., 2020).
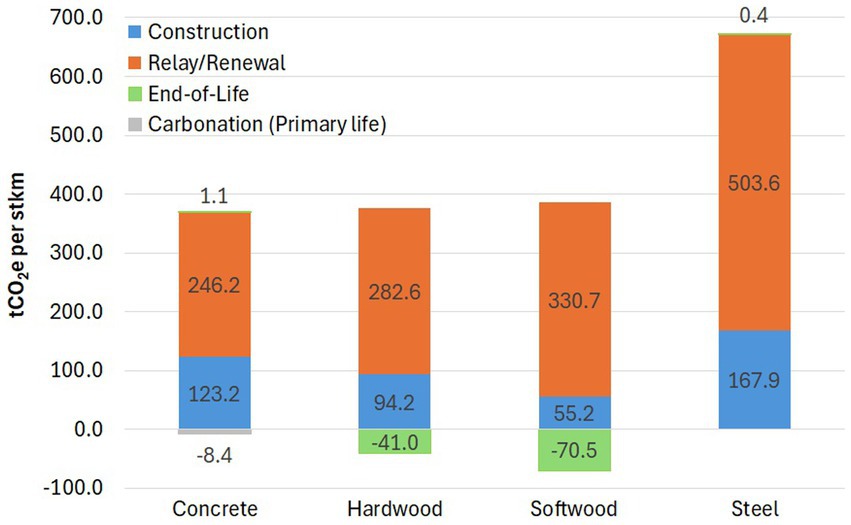
Figure 2. Carbon footprint for each sleeper type broken down by LCA phase for a 60-year appraisal period including wood incineration. Reprinted from (Rempelos et al., 2020) and The Lancet with permission from Elsevier.
In a similar study (Quik et al., 2020), researchers examined a slightly different selection of sleepers. Alongside traditional concrete sleepers, the review included sleepers made of virgin polyethylene (PE) plastic, recycled plastic, and polyurethane-glass fiber (PU-glass). The basic unit of measurement differed; in this study, the Functional Unit (FU) was 100 meters of track length, resulting in emissions an order of magnitude smaller than those in Rempelos et al.'s (2020) study (Figure 3). Notably, this study incorporated emissions from rail fastenings into the overall sleeper emissions. Consequently, wooden sleepers did not exhibit significantly lower emissions compared to standard concrete sleepers made with Portland cement. Instead, plastic and composite sleepers showed higher emissions during their initial life cycle. The full benefit of using recycled plastic is not realized until subsequent life cycles (Quick et al., 2020).
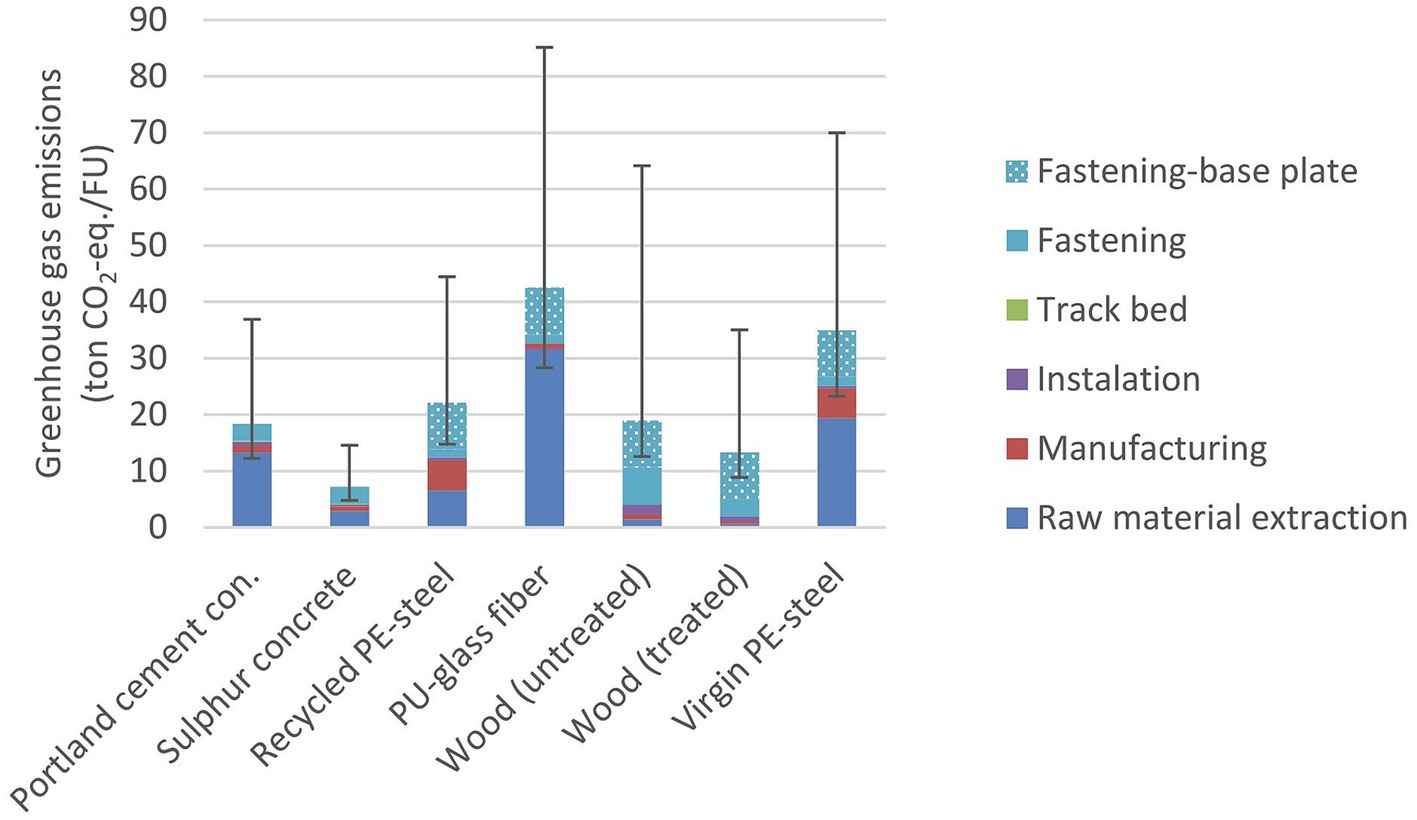
Figure 3. GHG emissions associated with different parts of a railway sleeper and fastening system per FU. Whiskers give the upper and lower bound of GHG emissions associated with the sleepers with a longer or shorter service life and the effect of using a new steel base-plate with every wooden sleeper replacement. Reproduced from the National Institute for Public Health and the Environment, RIVM 2020 (Quik et al., 2020).
Quick et al. (2020) extended calculations to the second service life. The study assumed that sleepers would either be reused by recycling as material or disposed of through incineration, utilizing the released heat as energy. Based on these calculations, sleepers made of plastic demonstrated the greatest potential for saving GHG emissions (Figure 4). When considering emissions during the first service life of the sleeper and the potentially avoidable emissions during the second life, recycled plastic sleepers emerged as the material with the lowest GHG emissions (Figure 5).
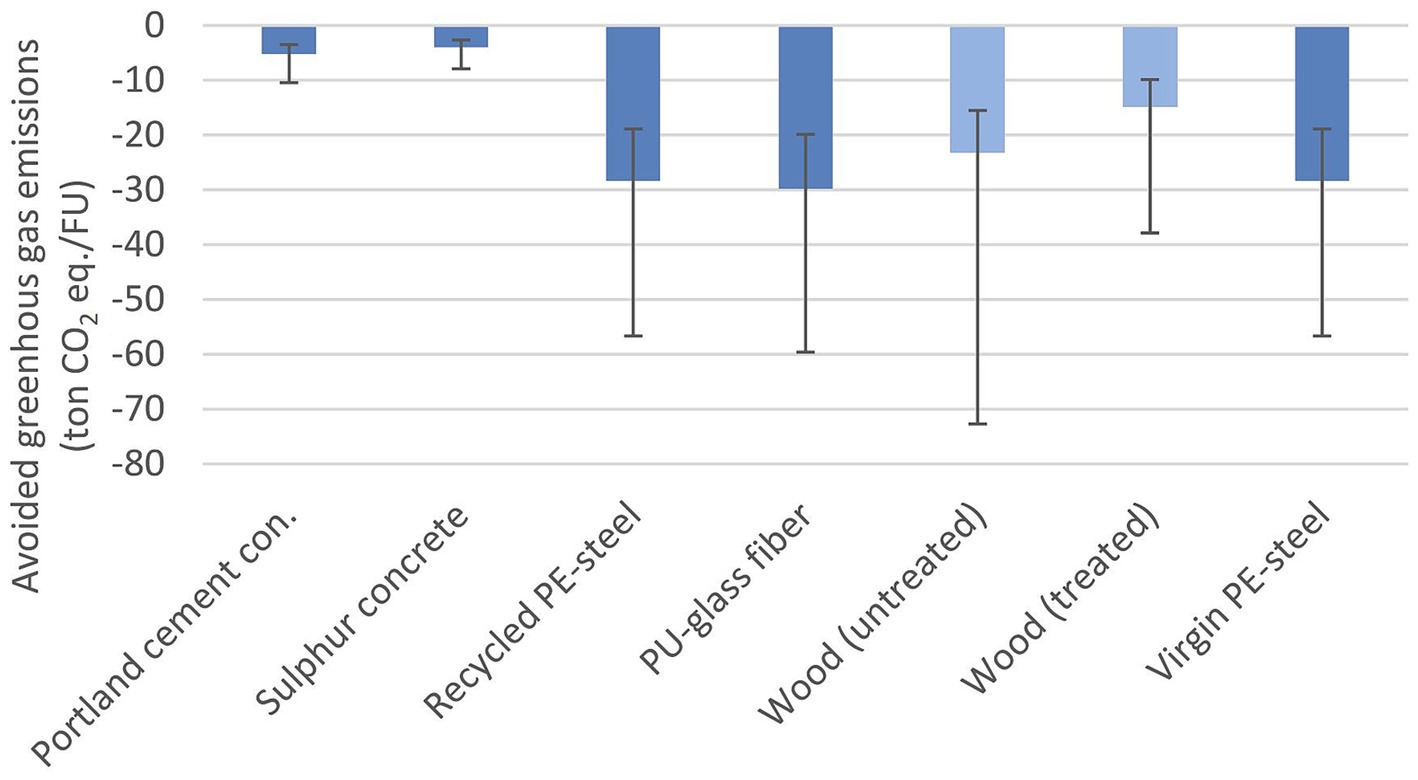
Figure 4. Potentially avoided GHG emissions in the next life cycle due to the reuse, recycling (dark blue) or energy recovery (light blue) from different railway sleepers. Whiskers indicate the upper and lower bound related to the uncertainty in service life. Reproduced from the National Institute for Public Health and the Environment, RIVM 2020 (Quik et al., 2020).
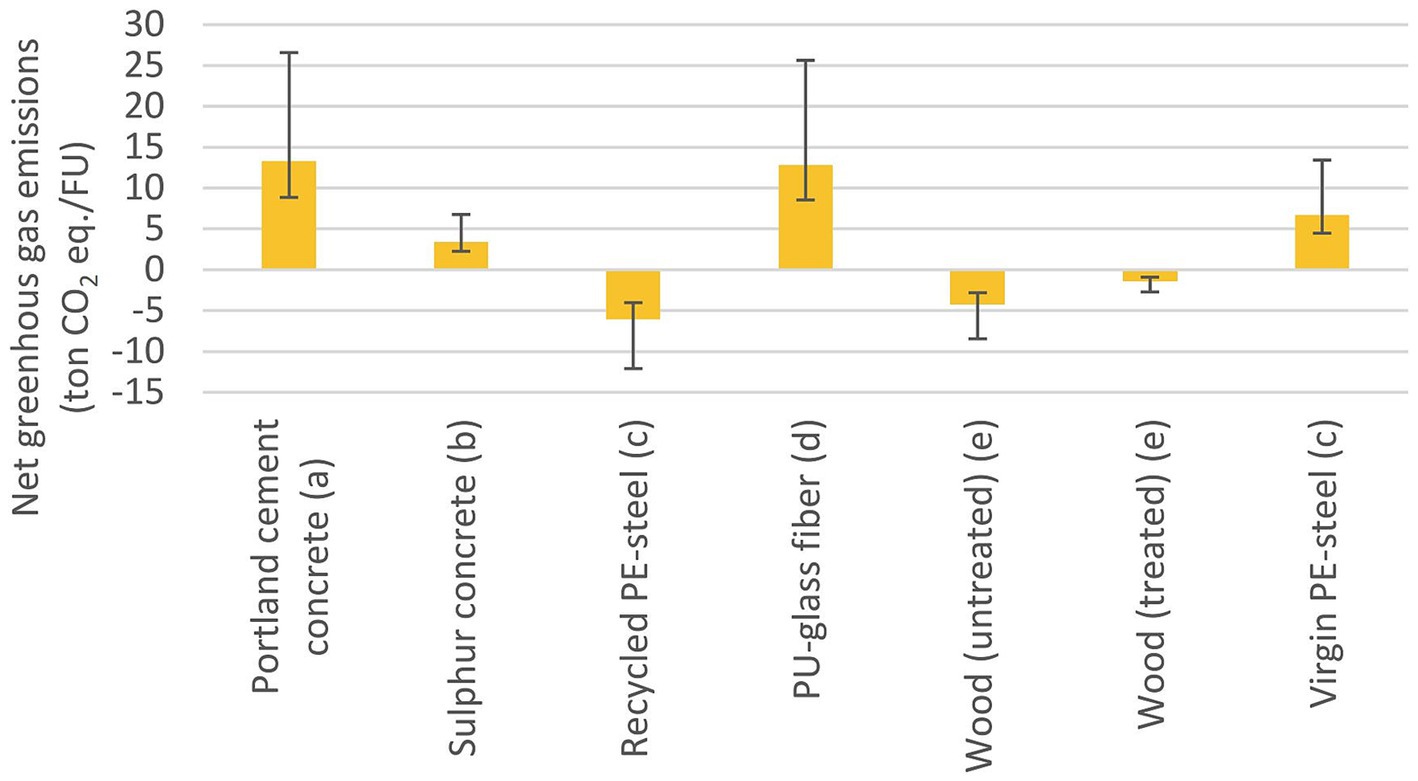
Figure 5. Net GHG emission from production in the first life cycle and avoided GHG emissions in the next life cycle. End of Life scenario consisting of (a) cement concrete and steel recycling; (b) Sulphur concrete and steel recycling; (c) PE and steel recycling; (d) PU-glass fiber sleeper reuse; (e) wood incineration; all scenario’s include steel recycling and incineration of polymer based materials from the fastening systems. Whiskers indicate the upper and lower bound related to the uncertainty in service. Reproduced from the National Institute for Public Health and the Environment, RIVM 2020 (Quik et al., 2020).
Many recent research has explored sleepers made from recycled plastics or composites (Zhang et al., 2023; Esmaeili et al., 2023; Salih et al., 2021; Ju et al., 2020; Silva et al., 2017; Kaewunruen et al., 2017). Often, the focus has been on sleeper durability rather than the carbon footprint. While environmental effects of recycled plastics have received less attention, there are studies examining virgin plastic or composite sleepers from this perspective as well (Rempelos, 2023; Sañudo Ortega et al., 2022; Kaewunruen and Liao, 2021; Dolci et al., 2020). Notably, several railway sleepers made from recycled materials are already available in the market, including TieTek, Sicut, IntegriCo, Tufflex, KLP, Evertrack, Atlas Trading International and Agico (Louie, 2013; Sicut, 2024; Integrico, 2024; Tufflex, 2024; Siahkouhi et al., 2021; Evertrack, 2024; Atlas Trading International, 2024; Agico, 2024).
This research aims to address two primary questions: First, it investigates the feasibility of utilizing currently incinerated recycled plastic fractions as sleeper materials, focusing on their mechanical durability. Second, it examines the potential for reducing GHG emissions using recycled plastics as material and quantifies the extent of potential GHG emissions reductions in Finland. The contribution of the study is to provide the track owner with information on the potential reduction in emissions achievable using recycled plastics.
2 Materials and methods
This article is based on a recent master’s thesis (Halme, 2022). The research aimed to utilize recycled plastics obtained from the waste stream, specifically for use as sleeper materials, with the goal of reducing GHG emissions. To achieve this, the properties of recycled plastics were investigated both at a general level and in terms of the specific requirements for railway sleepers made of plastic. The central idea was to replace concrete—known for its high carbon footprint as a sleeper material—with recycled plastic. The third criterion for selecting the replacement sleeper material was the availability of recycled material. It is essential to have sufficient recycled plastic material to economically produce an adequate number of sleepers and achieve emission reductions. The perspective considered recycled material flows within Finland.
2.1 Studied recycled plastic materials
2.1.1 Liquid packaging board (LPB) repulping reject
One of the most significant industries that use plastic is the packaging sector, which accounts for about 40% of the total plastic consumption. The fastest growing product in the packaging sector is liquid packaging board (LPB) (PLAST, 2024). LPB plays a crucial role in storing and transporting liquid food. LPB waste typically faces two options: incineration or recycling. In recycling facilities, the cellulose fibers within LPB are separated from plastic and aluminum through a repulping process (Khan et al., 2021).
LPB consists of a multilayer structure containing different materials. The plastics found in LPB primarily consist of polyethylene (PE), polypropylene (PP), ethylene vinyl alcohol (EVOH), and polyethylene terephthalate (PET). However, the reject material resulting from repulping—comprising plastic and aluminum—poses difficulties for recycling. Currently, this reject material is incinerated (Khan et al., 2021). Due to the difficult recyclability, plastic waste must be utilized by incineration, the efficiency of which is significantly lower compared to mechanical recycling (PLASTin, 2024).
Considering the challenges of recyclability, an intriguing question arises: Can the LPB repulping reject material be mechanically recycled into railway sleepers? Given that it is currently incinerated, repurposing it as sleeper material and potentially reusing it after its service life as sleepers could significantly reduce the overall carbon footprint.
2.1.2 Waste electronic and electrical equipment plastic
Another rapidly growing sector that extensively uses plastic, as covered in the PLASTin project, is electrical and electronic equipment (EEE). Plastic consumption in EEE accounts for approximately 6% of the total plastic usage. Due to rapid technological advancements, the use of plastic in electrical and electronic products has seen significant growth (PLASTin, 2024). Waste electronic and electrical equipment (WEEE) typically contains a heterogeneous mix of materials due to the various components used in these devices. Historically, separating the metal and plastic fractions within WEEE has been challenging, leading to common WEEE plastic recycling methods involving incineration. Additionally, plastic waste has often been exported from Finland, sometimes even ending up in landfills abroad. However, advancements in material separation techniques now make it easier and more efficient to separate different plastics and utilize them.
In the past, there was limited demand for recycled plastics within Finland, resulting in most recovered plastic being exported to regions like the Far East (Ignatius et al., 2009). However, this scenario could change if plastic separated from WEEE were used in manufacturing railway sleepers. One of the most commonly used plastics in electrical and electronic equipment is Acrylonitrile Butadiene Styrene (ABS). Given its widespread use, investigating the separation of ABS from WEEE and its recycling into sleepers is worthwhile. As the demand for electrical and electronic products continues to surge, the availability of raw materials for applications like railway sleepers is constantly increasing. Furthermore, redirecting WEEE from incineration to material reuse could significantly reduce GHG emissions.
2.2 Test specimens
For the mechanical tests, test rods were produced, and their properties were tested with a universal testing device after production. The process for preparing LPB material began from scratch, starting with the processing of the repulping reject (see Figure 6). In contrast, ABS was directly obtained as recycled granules ready for injection molding.
The LPB reject material arrived from Germany and contained many different types of waste including layers of liquid packaging cartons, aluminum and plastic. Additionally, the waste included plastic caps and some cellulose fibers. A few pieces of glass and metal springs were also found among the waste. To prevent damage to the processing equipment, glass and metals (except for the aluminum layer structure of the liquid packaging cardboard) were manually removed from the waste.
The test rod manufacturing process included six steps: compression, milling, extrusion, granulation, drying and injection molding. After coarse separation of the waste, the material was compacted by compression at 200°C for about 4 min (Figure 7a). The compacted waste sheets were ground with a Rapid Granular grinder (Figure 7b). Extrusion was performed with a Brabender twin-screw extruder (Figure 7c) with a temperature of 200°C and a speed of 110 1/min. As the end product of the extrusion, two ribbon-like products were obtained, which were immediately cooled after the extruder in a water bath. After cooling, the ribbon-like products were chopped into small granules with a Brabender granulator (Figure 7d). In some of the granules made from the rejects of LPB repulping, the core was formed by unmelted PET plastic (Figure 7e), because PET has a melting point of about 260°C and did not melt during extrusion. The granules were dried with a drying device (Figure 7f) at 70°C for approximately 2 h to remove moisture. After drying, test rods were injection molded from the granulates with a FANUC Roboshot α-30c injection molding machine (Figure 7g). At the beginning of injection molding, the optimal parameters were searched for the materials, so that the material melts appropriately and flows well into the mold. In addition to this, the portion size was adjusted so that there is no empty space in the mold or it does not overflow too much. The other most significant parameters were kept the same in the injection molding of LPB repulping reject and ABS, except that the cylinder temperature was increased for the processing of LPB repulping reject from 210°C to 230°C for ABS and the back pressure time from 10 s to 13 s. The finished test rods are shown in Figure 7h and the injection molding parameters are summarized in Table 1.
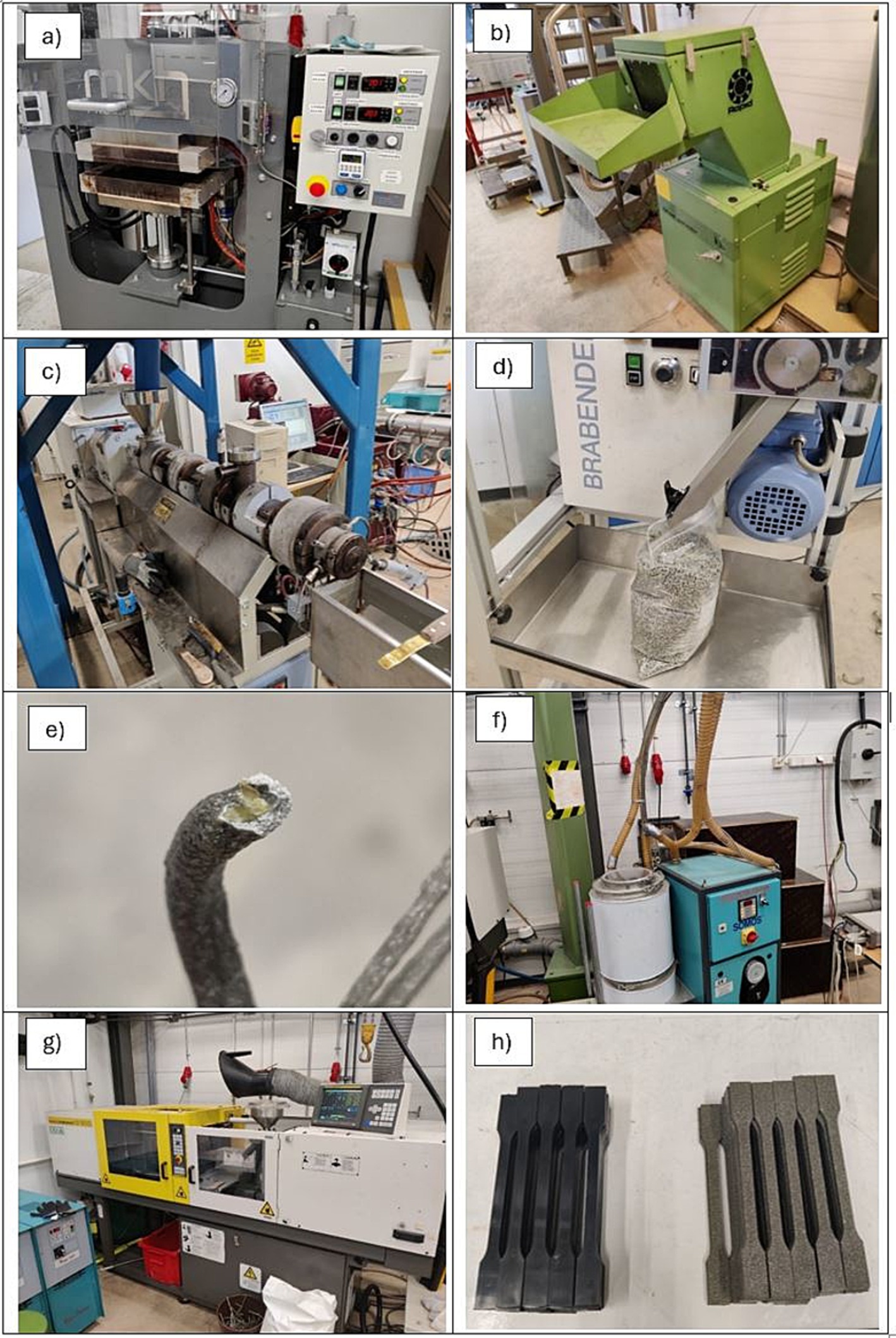
Figure 7. Test specimen manufacturing process: (a) compression, (b) milling, (c) extrusion, (d) granulating, (e) example of poorly melted material, (f) drying, (g) injection molding and (h) test ready specimens: ABS on the left-hand side and LPB on the right-hand side.
2.3 Mechanical testing
2.3.1 Desired properties of plastic sleeper
Determining the desired properties for recycled plastic material used in railway sleepers is a challenging task. The sleeper must have adequate strength to resist loadings coming from the trains and the environment. The ISO standards ISO 12856-1:2022 (2022) and ISO 12856-1:2014 (2014) outline various test methods for assessing material properties for plastic railway sleepers in railway applications. For plastics, tensile properties play a crucial role and are evaluated according to ISO 527-1:2019 (2019). The desired value depends on track line demands: for fast passenger traffic line the material properties must be considerably higher than for lower speed operated freight traffic lines. The purpose of the tensile tests was to determine how well the selected materials could meet these strength requirements.
The primary function of sleepers is to transfer loads from the rails to the underlying structural layers. Additionally, sleepers maintain gauge and track geometry (Zakeri and Sadeghi, 2007). To fulfill these requirements, flexural properties are essential, and these are evaluated following the standard ISO 178:2019 (2019) plastics—determination of flexural properties. The purpose of the tests was to determine if recycled materials are stiff enough to maintain gauge and avoid excess ballast deformations.
Given that railway structures are exposed to extreme temperature fluctuations, the material properties of sleepers must remain reliable even under such conditions. Tests like Vicat and HDT help determine the operating temperature at which plastic materials soften to a point where they are no longer usable. With the help of Vicat and HDT tests it is possible to define if materials are heat resistant enough to be used in temperatures taking place in Finland.
Among these, there are many other properties that may affect the usability of recycled plastic in railway sleeper applications, such as UV resistance. Damage from UV radiation can cause materials to fade, discolor, or become brittle over time. UV resistance was selected to be out of scope.
2.3.2 Tensile strength test procedure
Tensile tests were conducted using an Instron 5967 universal testing device (Figure 8a) in accordance with ISO 527-1:2019 (2019) plastics—determination of tensile properties. For each material, five parallel samples were tested. An extensometer was employed to precisely measure strain. The numerical output of the tensile test includes changes in the distance between the testing device jaws, the change in the distance between the extensometer tongs and the measured force in relation to time. When the tensile strength test was started, the test rod was stretched lengthwise between the jaws. The measuring device started stretching the sample at a speed of 5 mm/min. At this stage, an extensometer was attached to the sample to measure the exact elongation of the specimen and with the help of which the elastic modulus was determined. Stretching continued automatically until reaching the set limit value of 5% elongation, at which point the extensometer was removed. Further stretching occurred at a higher speed of 50 mm/min until the specimen broke.
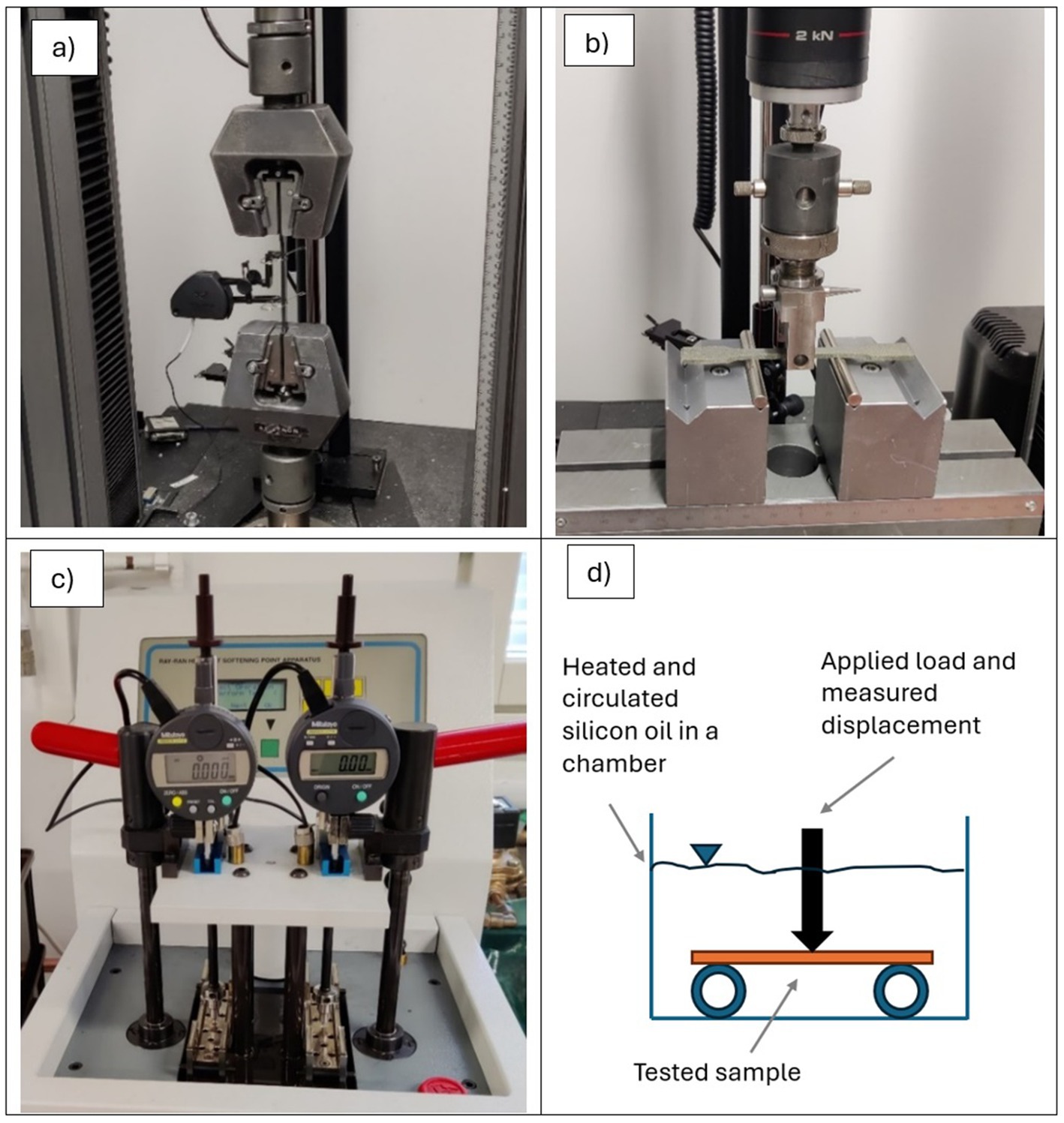
Figure 8. Test arrangement of mechanical tests: (a) universal testing machine in tensile test, (b) universal testing machine in bending test, (c) Vicat and HDT testing machine and (d) principle of HDT test procedure (ISO 75-1:2020, 2020).
2.3.3 Bending strength test procedure
The bending test followed standard ISO 178:2019 (2019) plastics—determination of flexural properties. Five parallel samples of both materials were tested. In the universal testing device, the jaws used for the tensile test were replaced with three-point bending heads (Figure 8b). Supports were positioned 64 mm apart. A constant-speed load head targeted at the center of the sample. Bending was continued until the force required for bending no longer increased. The data collected from the bending test includes the downward movement of the bending head from the origin and the force over time.
2.3.4 Vicat softening temperature (VST) test procedure
The Vicat softening temperature (VST) was determined according to the standard ISO 306:2022 (2022) plastics—thermoplastic materials—determination of Vicat softening temperature 497 (VST). The test was conducted using a RAY-RAN/HDV2 measuring device (Figure 8c). The VST test employed the Vicat softening point A50 method, where a force of 10 N was applied to the sample while its temperature increased by 50°C per hour. Injection-molded test rods, similar to those used in the tensile and bending tests, served as samples. The test rod thickness was 4 mm, and the samples were immersed in silicone oil. A load head with a 1 mm2 tip area was pressed against the sample surface using a kilogram weight. Testing began when the sample in silicone oil reached room temperature, and the temperature was then raised by 50°C per hour. Heating continued until the loading head had sunk into the sample by 1 mm. The temperature at which the sample softened sufficiently for the load head to sink 1 mm into the sample is called the Vicat softening temperature (VST).
2.3.5 Heat deflection temperature (HDT) test procedure
Heat deflection temperature (HDT) was determined according to the standard ISO 75-1:2020 (2020) plastics—determination of temperature of deflection under load. The same RAY-RAN/HDV2 measuring device used for VST testing was employed for HDT determination. The HDT test provides an estimate of the maximum operating temperature of the material. During the test, the test rod underwent bending stress similar to that in a three-point bending test, while the sample temperature increased steadily. Figure 8d illustrates the typical structure of an HDT measuring device and its components.
The HDT test was started by placing the specimen on the supports of the measuring device, after which the sample was immersed in silicone oil. A loading head was placed in the middle of the sample, whose weight was selected such that the required bending stress 1.8 MPa could be generated. The temperature was increased by 120°C per hour until the required constant deflection value was reached. The temperature at that moment was recorded as the HDT temperature.
3 Results and analysis
3.1 Tensile and bending tests
All samples injection-molded from ABS material formed nearly identical stress–strain curve, except for the first sample, which broke even before 5% strain. In the manufacturing process, the unmelted material can act as a reinforcement in the structure of the sample, improving the strength properties of the specimen, or lead to premature specimen failure, as observed in the first sample. The impact of unmelted material diminishes as the object size increases. Full-size sleepers are less affected than small test rods, where even minor impurities alter behavior significantly. The other ABS samples broke only after removing the extensometer during continued stretching (Figure 9). The typical stress–strain curve for ABS plastic shows a clear yield point, where stress tends to decrease with increased strain.
The samples injection-molded from the LPB repulping reject material exhibited nearly identical stress–strain curves. Unlike ABS plastic tests, the yield point is not visible in LPB samples stress–strain curve (see Figure 9). Elastic modulus, yield strengths and elongations obtained from the graphs for ABS plastic are presented with the standard deviations in Table 2. With the help of the nominal elongation, it is possible to find out the behavior after a 5% elongation to see how high the tension rises. The value of the tensile strength of the sample was determined from the graph as the ratio of the maximum stress to the corresponding strain. However, with ABS plastic, the maximum strain practically occurs at around 2% elongation. The stress of the LPB samples clearly increases after 5% elongation, all the way to failure. Because of this, especially in the case of LPB samples, it is important to determine the tensile strength value from the nominal elongation values. The breaking strengths, elongations and tensile strengths obtained from the data are presented with the standard deviations in Table 2. Additionally, the results of the bending tests are provided in Table 3.
The strength values of recycled ABS obtained in mechanical tests were slightly higher than the reference values for tensile properties of virgin ABS specified in standard ISO 527-2:2012 (2012). The reference value for tensile elastic modulus in the standard is 1,779 MPa, which is approximately 24% lower than the elastic modulus 2,367 MPa measured for recycled ABS in the test. The yield strength reference value in the standard is 36.4 MPa, about 7.6% lower than the value 39.4 MPa measured in the tensile test for recycled ABS. The standard specifies 2.6% yield elongation, which is 0.6% higher than the value measured in the tensile test. Based on the results, it can be concluded that the tensile strength of recycled ABS can be even slightly higher than the strength of virgin ABS, even though the recycled material contains impurities. However, there are several different ABS plastic grades, the properties of which differ slightly from each other. The greater strength in recycled ABS plastic can be due, for example, to the fact that other material fractions among the WEEE, have not been completely separated from the ABS. These fractions containing other materials remaining in the recycled waste may act as reinforcements in the material, increasing the strength.
The standard ISO 178:2019 (2019) specifies a laboratory-tested reference value for the elastic modulus of virgin ABS, which is 2,470 MPa. The reference value given in the standard is about 6.3% higher than the value 2,315 MPa obtained from measurements. Despite this small difference, the values are very close to each other. In addition, the sliding of a very slippery ABS test specimen in the test apparatus during the measurement may also have influenced the result. The use of recycled ABS may reduce the strength properties on average approximately 6% after each recycling (Bibb et al., 2021). This is very well in line with the results achieved in this study.
The tensile properties of LPB repulping reject have previously been tested by Mäki-Tulokas (2021) and Jönkkäri et al. (2023). In her thesis, the average tensile elastic modulus of samples with different compositions was found to be 827.8 MPa, which is in the same range as the result tested in this work. The small difference in the measured results can probably be explained by variations in the aluminum content of the waste, the amount of residual fibers and the proportions of other material components. In particular, the cellulose content of repulping rejects has been found to vary by up to 50% between waste batches (Mäki-Tulokas, 2021). Cellulose content significantly affects the mechanical properties of the samples, weakening in the material structure.
3.2 VST and HDT
The results obtained from VST and HDT measurements are summarized in Table 4. ABS plastic has a clearly better ability to resist deformation caused by high temperatures. The measured VST value of 103°C for recycled ABS was 7% lower compared to that determined by Krache and Debbah (2011) in their tests with virgin ABS. Conversely, the HDT was 8% higher than what Krache and Debbah (2011) determined. The VST value of 95°C for LPB repulping reject is well within the range of VST values for LDPE (94.6°C) and HDPE (124.5°C) found in the literature (Sikora et al., 2019; Mizera et al., 2022). The measured HDT value of 43.1°C for LPB repulping reject is practically identical to that determined by Sikora et al. (2019) in their tests for LDPE. Based on this observation, LPB repulping reject most likely consists of LDPE.
3.3 Available volume of recycled plastic
An essential factor in evaluating the amount of emission reduction is the volume of available recycled plastic. When considering how much LPB repulping reject could potentially be available as material for railway sleepers, we need to know the amount of recycling streams and the LPB share of the recycling stream. LPB is a part of municipal waste. In 2020, a total of 3.3 million tons of municipal waste was generated in Finland (Official Statistics of Finland (OSF), 2021). The municipal waste recycling rate between 2015 and 2019 has been around 42%, and the target for 2020 was 50%. The calculation assumes that 50% of municipal waste would be recycled. On average, about 0.9% of the composition of municipal waste is LPB (Nikkari, 2013). In LPB recycling, the cellulose fibers are separated in the repulping process, which leaves about 25% of the material mainly consisting of aluminum and plastics as rejects. This 25% share of the LPB recycling amount would therefore be possible to recycle as sleeper material (Khan et al., 2021). However, repulping is not a completely lossless process, for example the yield of the separation process carried out in the laboratory was around 55–85% (Khan et al., 2021). For this reason, an 80% yield is used in the calculations when aluminum and plastic are separated from cellulose fibers. Based on these assumptions, LPB recycling could potentially yield approximately 3,000 tons of repulping rejects per year as material for railway sleepers. Finally, one can think about how many sleepers could be produced with this amount of material. The dimensions of a typical plastic sleeper can be found in the ISO 12856-1:2014 (2014) standard, which indicates that typical plastic sleeper size is 0.15 m thick, 0.25 m wide and 2.6 m long. Thus, the volume of one sleeper is about 0.0975 m3. In the LPB repulping reject, most of the material is polyethylene, the density of which is about 960 kg/m3. With this information, it can be calculated that the weight of one sleeper would be approximately 93.6 kg. If all repulping rejects recycled annually were used as material for railway sleepers, approximately 31,730 sleepers would be produced from it. With a typical sleeper spacing of Finnish continuous rail track, i.e., 1,640 sleepers per kilometer, that amount would be enough to cover the sleepers of the 19.3 km long single-track section (RATO 11, 2024; Sañudo Ortega et al., 2021).
When analyzing the recycling flow of ABS, we must start from the recovery amounts of WEEE. In Finland, in 2019, 63,030 tons of WEEE were collected from households and 10,266 tons from non-households totaling approximately 73,296 tons. The reuse and recycling target for WEEE is 80% for heating and cooling devices and other large devices, 70% for monitors, and 55% for small devices and small telecommunications devices (Pirkanmaan ELY-keskus, 2021). Thus, the average of the reuse and recycling targets is 68%. This average of the target values can be considered as a potential portion that could be recycled as material for the manufacture of railway sleepers, approximately 49,841 tons per year. WEEE also contains many other materials than plastic, the share of which is only about 20%. In addition to that, ABS accounts for about 33% of the plastic contained in WEEE (Hulsman et al., 2007). When recycling WEEE, ABS must be separated from other plastics. The yield of the ABS separation process was estimated to be 80%, as was also the case with the separation of plastics form LPB. When all of these are taken into account, approximately 2,631 tons of recycled ABS can potentially be obtained annually as a raw material for railway sleepers. When the density of ABS is 1,070 kg/m3, the weight of the sleeper is approximately 104.3 kg. With the amount of recycled ABS during 1 year, a total of 25,225 sleepers can be produced. Following the usual sleeper distribution, this amount would cover 15.3 km of a single-track line.
4 Discussion
4.1 Material suitability
There are no limit values for the tensile test for recycled plastic material intended for use in railway sleepers. The tensile test was only introduced in the 2022 update of ISO 12856-1:2022 (2022), which does not specify precise limits that the tested material must meet. The standard only states that the mechanical properties of the material used for sleepers should be tested by means of a tensile test. However, analysis of the measurement results reveals that recycled ABS plastic exhibits an elastic modulus in tension almost three times higher than that of LPB repulping reject. Based on this observation, using recycled ABS would provide the sleeper with significantly greater tensile stiffness compared to LPB repulping reject.
For flexural properties required in plastic sleepers, ISO 12856-1:2014 (2014) specifies requirements for three different types of plastic sleeper material. Among these, material type B best corresponds to the wooden sleeper railway commonly used in Finland. Material type B allows a maximum axle weight of 22.5 tons and a speed limit of 160 km/h. The standard mandates a minimum flexural modulus of 2,500 MPa for material type B. However, neither of the materials tested in this work meets the requirements for the flexural modulus of material type B. Recycled ABS comes significantly closer to meeting these requirements, and its virgin reference value is very close to the minimum requirements.
For the lower requirement level, material type C, the standard specifies a minimum flexural modulus of 1,170 MPa. Recycled ABS comfortably satisfies the requirement for material type C. Considering the flexural modulus, recycled ABS could be suitable for freight traffic lines. To slightly enhance the flexural modulus, reinforcing fibers could be added to the sleeper’s structure, easily meeting the level required for material type B.
In standard ISO 306:2022 (2022), reference temperatures have been tested in the laboratory for several different ABS plastic grades. The average VST of these ABS grades was 107.5°C, which is only 4.2% higher than the tested recycled ABS. On this basis, it can be concluded that recycling does not significantly reduce the maximum operating temperature of ABS. In standard ISO 75-2:2013 (2013), reference value of 79.3°C for the HDT is specified for ABS plastic, which is 3.1% higher than the HDT measured in the work. This indicates that mechanical recycling does not significantly reduce the maximum temperature of ABS plastic under deflection.
RATO 11 (2024) specifies the maximum temperature for rails, 55°C, to be considered when designing Finnish railways. In winter, the heat load due to the heating of the turnouts can be higher than this and the temperature near the heaters can reach up to more than 100°C. However, in cold weather, the temperature drops significantly on the way from the heaters to the sleeper. Sleepers must withstand track environment temperatures without significant property changes. Based on the VST obtained from the measurements, the materials do not soften significantly at the maximum temperature typical of the track environment, but turnout heating must be considered avoiding.
The HDT test results can be concluded that only recycled ABS can withstand the maximum temperature of 55°C typical for a track environment as specified in the track specifications without softening too much for bending. In contrast, the HDT value of the LPB repulping reject is too low for the high temperatures encountered in the track environment.
4.2 Carbon footprint
The first approach to evaluate effects on the carbon footprint is based on literature presented by Quik et al. (2020). The benefits of recycled plastics in reducing GHG emissions depend on the number of lifecycles the material can sustain. Calculations are based on the scenario depicted Figure 5, where the GHG emissions of a concrete sleeper amount to approximately 13 tCO2e/FU, while steel reinforced sleeper made of recycled polyethylene plastic emits around-6 tCO2e/FU. This results in a difference of 19 tCO2e/FU. The emissions are scaled for a 100 m section (FU) of track with a 50-year lifetime, with 167 sleepers (Quik et al., 2020). A previously presented calculation suggests that the annual LPB recycling rate would allow the construction of about 19.3 km of track. When we apply the emissions difference between recycled reinforced plastic and concrete sleepers to this length of track, the impact on GHG emissions amounts to approximately 3,610 tCO2e per year. To put this in perspective, the CO2 emissions from heating a typical electrically heated detached house are approximately 3 tCO2e per year (Lindgren, 2019). Therefore, if concrete sleepers were replaced by recycled plastic sleepers reinforced with steel bars, using the available waste stream in Finland, CO2 emissions could be reduced by an amount equivalent of the annual heating-related emissions of 1,200 electrically heated detached houses.
In the study by Quik et al. (2020), the recycled plastic sleeper used in the comparison included 26% steel reinforcement by volume. If the CO2 emissions from the steel reinforcement could be eliminated by using only recycled plastic, like fiber class from wind turbine blade as reinforcement, the reduction in emissions would be even more significant.
The other approach to evaluate the effects on carbon footprint is based on difference between waste plastic incineration and mechanical recycling. When polyethylene is recycled by incineration, as is currently the case for LPB repulping rejects, the resulting CO2 emissions are approximately 5.1 kg CO2e per kg. In contrast, the CO2 emissions from incinerating ABS from WEEE are 7.8 kg CO2e per kg. When LPB waste containing PE is mechanically recycled, e.g., for example to a railway sleeper, its CO2 emissions would be approximately 1.45 kg CO2e per kg. When ABS is mechanically recycled instead of incineration, its CO2 emissions are around 2.75 kg CO2e per kg. Notably, mechanical recycling of LPB results in about 47% lower CO2 emissions compared to mechanical recycling of ABS recovered from WEEE (Schwarz et al., 2021). However, mechanical recycling has a relatively small carbon footprint compared to incineration of materials. Mechanical recycling alone would reduce annual CO2 emissions by 11,000 tCO2e with LPB repulping reject and by 13,300 tCO2e with ABS. The potential of reducing the GHG emissions by mechanical recycling of waste plastic could be three times higher than in the calculations based on Quik et al. (2020). Although, this calculation does not consider the emissions of sleeper production, steel reinforcement, transportation and installation.
In a cold climate country like Finland, the need for heating in winter is significant. Therefore, all the energy recovered from the incineration of recycled plastic is essential for heating. When this source of energy is mechanically recycled for railway sleepers, the required energy for heating must be produced by other means. The average GHG emissions in Finnish heat production are 145 kg CO2/MWh, which is much less than using only heating oil (263 kg CO2/MWh), whose energy content is similar to waste plastic. GHG emissions from heat production are decreasing continuously as renewable energy sources are increasingly adopted (Motiva, 2024).
4.3 Other aspects
The use of recycled plastic also allows other benefits, such as greater design flexibility for sleeper shapes. The KLP sleeper serves as a good example of how sleeper design can be used to enhance lateral resistance in tracks (Ferdous et al., 2015). Additionally, plastic sleepers are lightweight and easy to handle. The weight reduction can decrease the lateral resistance of track and lead to track buckling, which needs to be considered when replacing concrete sleepers with plastic sleepers on continuously welded rail. Liu et al. (2021) measured lateral resistance for rectangular composite sleeper only 4.85 kN compared to that of more complicated shape concrete sleeper 13.61 kN. Based on similar research at Tampere University, the shape of the sleeper has significant effect on lateral resistance as well as the weight of the sleeper.
Other challenges include uncertainty about the long-term durability, for example the UV resistance, of recycled plastic and the potential production of microplastics due to mechanical abrasion from plastic sleepers. Further research is needed to address these issues.
5 Conclusion
This research explored the potential of using two types of recycled plastics, which are currently incinerated, as materials for railway sleepers. From these waste plastics, ABS and LPB repulping reject, ABS emerges as a significantly more promising alternative for sleeper material. Recycled ABS material is approximately three times stronger and stiffer than LPB repulping reject. Based on mechanical testing, the strength properties of recycled plastics are relatively similar to those of virgin ABS and LDPE. Sleepers made from recycled ABS are moderately suitable for all types of tracks, with a particular advantage for freight traffic lines. On the other hand, sleepers made from recycled LPB repulping reject are prone to excessive softening in summer temperatures and cannot be used as railway sleeper material in their current form. While it is possible to increase the softening point with additives, this was outside the scope of this research.
Using recycled plastic in sleepers can lead to a reduction in GHG emissions from railway operations, especially when considering emissions avoided throughout the material’s past and future life cycle. For instance, if all the LPB repulping rejects recycled in Finland during the year were used to manufacture sleepers instead of concrete, a reduction of 3,610 tCO2e could be achieved, even if the sleepers required substantial reinforcement with steel bars. Furthermore, if all recycled ABS and LPB plastics were mechanically recycled and used as material instead of incineration, an annual emission reduction of 24,200 tCO2e would be realized. A significant reduction in GHG emissions is possible even when considering the substitute energy source for incineration heat recovery.
Plastic railway sleepers offer several advantages, such as easy formability, low cost, lightweight, mechanical strength, and resistance to environmental conditions. However, the lightweight nature of the sleepers may increase the risk of track buckling, and their long-term resistance to UV radiation has not been tested in this study. Future studies will include mechanical testing on full-scale sleepers and attempts to estimate their long-term behavior.
Data availability statement
The original contributions presented in the study are included in the article/supplementary material, further inquiries can be directed to the corresponding author.
Author contributions
HL: Writing – review & editing, Writing – original draft, Visualization, Validation, Supervision, Resources, Project administration, Methodology, Investigation, Funding acquisition, Formal analysis, Data curation, Conceptualization. RH: Writing – original draft, Methodology, Investigation, Formal analysis, Data curation. IJ: Writing – review & editing, Validation, Supervision, Methodology, Data curation, Conceptualization.
Funding
The author(s) declare that financial support was received for the research, authorship, and/or publication of this article. This project was supported by the Finnish Transport Infrastructure Agency (FTIA).
Acknowledgments
Authors wishes to gratefully acknowledge the Finnish Transport Infrastructure Agency (FTIA) for financial support and their long-term vision regarding R&D activities related to the railway system. The authors are also very grateful to Tampere University, specifically the Faculty of Built Environment and the Faculty of Engineering and Natural Sciences, for their support and facilities. The author(s) declare that Generative AI was used in the creation of this manuscript. Generative AI was used for the creation of this manuscript. Authors used Microsoft Copilot for proofreading.
Conflict of interest
The authors declare that the research was conducted in the absence of any commercial or financial relationships that could be construed as a potential conflict of interest.
Publisher’s note
All claims expressed in this article are solely those of the authors and do not necessarily represent those of their affiliated organizations, or those of the publisher, the editors and the reviewers. Any product that may be evaluated in this article, or claim that may be made by its manufacturer, is not guaranteed or endorsed by the publisher.
References
Agico (2024). Agico Group, China. Available at: https://www.rail-fastener.com/recycled-plastic-railway-sleepers.html (Accessed July 4, 2024).
Arulrajah, A., Naeini, M., Mohammadinia, A., Horpibulsuk, S., and Leong, M. (2020). Recovered plastic and demolition waste blends as railway capping materials. Transp. Geotech. 22:100320. doi: 10.1016/J.TRGEO.2020.100320
Atlas Trading International (2024). Available at: http://www.atlastradinginternational.com/ (Accessed July 4, 2024).
Bibb, M., Nowicki, M., McDonald, K., and Zander, N. (2021). “Strength and quality of recycled acrylonitrile butadiene styrene (ABS)”. Proceedings of the ASME 2021 International Mechanical Engineering Congress and Exposition. Volume 3: Advanced Materials: Design, Processing, Characterization, and Applications. Virtual, Online. November 1–5: V003T03A007. ASME. doi: 10.1115/IMECE2021-70583
Bolin, C. A., and Smith, S. T. (2013). Life cycle assessment of creosote-treated wooden railroad crossties in the US with comparisons to concrete and plastic composite railroad crossties. J. Transp. Technol. 3, 149–161. doi: 10.4236/JTTS.2013.32015
Dolci, G., Rigamonti, L., and Grosso, M. (2020). Potential for improving the environmental performance of railway sleepers with an outer shell made of recycled materials. Transp. Res. Interdiscip. Perspect. 6:100160. doi: 10.1016/J.TRIP.2020.100160
Esmaeili, M. H., Norouzi, H., and Niazi, F. (2023). Evaluation of mechanical and performance characteristics of a new composite railway sleeper made from recycled plastics, mineral fillers and industrial wastes. Compos. Part B 254:110581. doi: 10.1016/J.COMPOSITESB.2023.110581
Evertrack (2024). Evertrak LLC. Available at: https://evertrak.com/ (Accessed July 4, 2024).
Ferdous, W., and Manalo, A. (2014). Failures of mainline railway sleepers and suggested remedies – review of current practice. Eng. Fail. Anal. 44, 17–35. doi: 10.1016/j.engfailanal.2014.04.020
Ferdous, W., Manalo, A., van Erp, G., Aravinthan, T., Kaewunruen, S., and Remennikov, A. (2015). Composite railway sleepers – recent developments, challenges and future prospects. Compos. Struct. 134, 158–168. doi: 10.1016/j.compstruct.2015.08.058
Halme, R. (2022). Kierrätysmuovien hiilijalanjälki ja käyttömahdollisuudet ratarakenteissa. Tampereen yliopisto. (Master's thesis, in Finnish). Available at: https://urn.fi/URN:NBN:fi:tuni-202210187677 (Accessed July 4, 2024).
Hulsman, J., Magalini, F., and Kuehr, R. (2007). Review of directive 2002/96 on waste electrical and electronic equipment (WEEE), United Nations University, 2007, 378 p.
Ignatius, S.-M., Myllymaa, T., and Dahlbo, H. (2009). Sähkö-ja elektroniikkaromun käsittely Suomessa. Suomen ympäristökeskus Suomen Ympäristökeskuksen raportteja. Available at: http://hdl.handle.net/10138/39678 (Accessed July 4, 2024).
Imteaz, M., Mohammadinia, A., and Arulrajah, A. (2021). Environmental suitability, carbon footprint and cost savings of recycled plastic for railway applications. Int. J. Sustain. Eng. 14, 725–734. doi: 10.1080/19397038.2021.1929551
Integrico (2024). IntegriCo Composites. Available at: www.integrico.com (accessed July 4, 2024)
ISO 12856-1:2014 (2014). Plastics — Plastic railway sleepers for railway applications (railroad ties). Part 1: Material characteristics. Withdrawn (Edition 1, 2014).
ISO 12856-1:2022 (2022). Railway applications — Polymeric composite sleepers, bearers and transoms. Part 1: Material characteristics, published (Edition 2, 2022)
ISO 178:2019 (2019). Plastics — Det2.3.2. ermination of flexural properties. Published (Edition 6, 2019)
ISO 306:2022 (2022). Plastics — Thermoplastic materials — Determination of Vicat softening temperature (VST). Published (Edition 6, 2022)
ISO 527-1:2019 (2019) Plastics — Determination of tensile properties. Part 1: General principles. Published (Edition 3, 2019)
ISO 527-2:2012 (2012) Plastics — Determination of tensile properties. Part 2: Test conditions for moulding and extrusion plastics. Published (Edition 2, 2012)
ISO 75-1:2020 (2020) Plastics — Determination of temperature of deflection under load. Part 1: General test method. Published (Edition 4, 2020)
ISO 75-2:2013 (2013). Plastics — Determination of temperature of deflection under load. Part 2: Plastics and ebonite. Published (Edition 3, 2013)
Jönkkäri, I., Mäki-Tulokas, S., Niini, A., Saarimäki, E., and Sarlin, E. (2023). Processing and characterizing repulping reject of liquid package board. J. Appl. Polym. Sci. 140. doi: 10.1002/app.53942
Ju, S., Yoon, J., Sung, D., and Pyo, S. (2020). Mechanical properties of coal ash particle-reinforced recycled plastic-based composites for sustainable railway sleepers. Polymers 12, 1–15. doi: 10.3390/polym12102287
Kaewunruen, S., and Liao, P. (2021). Sustainability and recyclability of composite materials for railway turnout systems. J. Clean. Prod. 285:124890. doi: 10.1016/J.JCLEPRO.2020.124890
Kaewunruen, S., You, R., and Ishida, M. (2017). Composites for Timber-Replacement Bearers in Railway Switches and Crossings. Infrastructures 2, 13. doi: 10.3390/infrastructures2040013
Khan, M. M. H., Laitinen, V., Havukainen, J., and Horttanainen, M. (2021). Carbon footprint of different recovery options for the repulping reject from liquid packaging board waste treatment process. Waste Manag. 136, 93–103. doi: 10.1016/J.WASMAN.2021.10.003
Krache, R., and Debbah, I. (2011). Some mechanical and thermal properties of PC/ABS blends. Mater. Sci. Appl. 2, 404–410. doi: 10.4236/msa.2011.25052
Lin, J., Li, H., Huang, W., Xu, W., and Cheng, S. (2019). A carbon footprint of high-speed railways in China: a case study of the Beijing-Shanghai line. J. Ind. Ecol. 23, 869–878. doi: 10.1111/jiec.12824
Lindgren, S., (2019). Pientalon lämmityksen hiilijalanjälki, Satakunnan ammattikorkeakoulu, 2019. Available at: https://tulevaisuudenrakentaminen.samk.fi/2019/05/31/pientalon-lammityksen-hiilijalanjalki/ (accessed July 4, 2024)
Liu, J., Chen, R., Liu, Z., Liu, G., Wang, P., and Wei, X. (2021). Comparative analysis of resistance characteristics of composite sleeper and concrete sleeper in ballast bed. Constr. Build. Mater. 300:124017. doi: 10.1016/j.conbuildmat.2021.124017
Louie, M. L. (2013). Sustainable solutions for railroad trackwork. In Urban public transportation systems 2013 (pp. 338–346). doi: 10.1061/9780784413210.030
Mäki-Tulokas, S. (2021). Recycling of plastics from liquid carton packaging, Tampere University, 76 p. Available at: https://urn.fi/URN:NBN:fi:tuni-202111188532 (Accessed July 4, 2024).
Manalo, A., Aravinthan, T., Karunasena, W., and Ticoalu, A. (2010). A review of alternative materials for replacing existing timber sleepers. Compos. Struct. 92, 603–611. doi: 10.1016/j.compstruct.2009.08.046
Milford, R. L., and Allwood, J. M. (2010). Assessing the CO2 impact of current and future rail track in the UK. Transp. Res. Part D: Transp. Environ. 15, 61–72. doi: 10.1016/j.trd.2009.09.003
Mizera, A., Manas, M., and Stoklasek, P. (2022). Effect of temperature ageing on injection molded high-density polyethylene parts modified by accelerated electrons. Materials 15:742. doi: 10.3390/ma15030742
Motiva (2024). CO2-päästökertoimet. Available at: https://www.motiva.fi/ratkaisut/energiankaytto_suomessa/co2-paastokertoimet (accessed September 3, 2024)
Nikkari, E. (2013). Kaatopaikkakaasun muodostumisen mallinnus – yhdyskuntajätteen koostumuksen ja käytetyn hajoamisvakion vaihtelujen vaikutukset, Lappeenrannan Teknillinen Yliopisto. Available at: https://urn.fi/URN:NBN:fi-fe201306134005 (Accessed July 4, 2024).
Official Statistics of Finland (OSF). (2021). Waste statistics (e-publication). ISSN=2323–5314. Municipal waste 2020. Helsinki: Statistics Finland. Available at: http://www.stat.fi/til/jate/2020/13/jate_2020_13_2021-12-09_tie_001_en.html (Accessed July 4, 2024).
Plastin. (2024). ALL-IN for Plastic Recycling (PLASTin) -project. Available at: https://clicinnovation.fi/project/plastin/
Pirkanmaan ELY-keskus. (2021). Sähkö-ja elektroniikkalaitetilastot. Available at: https://www.ymparisto.fi/fi-fi/kartat_ja_tilastot/jatetilastot/tuottajavastuun_tilastot/sahko_ja_elektroniikkalaitetilastot (accessed July 4, 2024)
Quik, J. T. K., Dekker, E., and Montforts, M. H. M. M. (2020). Safety and sustainability analysis of railway sleeper alternatives application of a novel method for material loops. National Institute for Public Health and the Environment, RIVM. doi: 10.21945/RIVM-2020-0181
Rempelos, G. (2023). A whole life carbon model for railway track system interventions doctoral dissertation, University of Southampton.
Rempelos, G., Preston, J., and Blainey, S. (2020). A carbon footprint analysis of railway sleepers in the United Kingdom. Transp. Res. Part D: Transp. Environ. 81:102285. doi: 10.1016/J.TRD.2020.102285
Salih, C., Manalo, A., Ferdous, W., Abousnina, R., Yu, P., Heyer, T., et al. (2021). Novel bending test method for polymer railway sleeper materials. Polymers 13:1359. doi: 10.3390/polym13091359
Sañudo Ortega, R., Goswami, R. R., Ricci, S., and Miranda, M. (2022). Efficient reuse of railway track waste materials. Sustainability (Switzerland) 14:11721. doi: 10.3390/su141811721
Sañudo Ortega, R., Pombo, J., Ricci, S., and Miranda, M. (2021). The importance of sleepers spacing in railways. Constr. Build. Mater. 300:124326. doi: 10.1016/J.CONBUILDMAT.2021.124326
Schwarz, A. E., Ligthart, T. N., Godoi Bizarro, D., de Wild, P., Vreugdenhil, B., and van Harmelen, T. (2021). Plastic recycling in a circular economy; determining environmental performance through an LCA matrix model approach. Waste Manag. 121, 331–342. doi: 10.1016/J.WASMAN.2020.12.020
Siahkouhi, M., Li, X., Markine, V., and Jing, G. (2021). An experimental and numerical study on the mechanical behavior of Kunststof Lankhorst product (KLP) sleepers. Sci. Iran. 28, 2568–2581. doi: 10.24200/sci.2021.57165.5096
Sicut (2024). Sicut North America. Available at: https://sicut.co.uk/ (accessed July 4, 2024)
Sikora, J. W., Gajdoš, I., and Puszka, A. (2019). Polyethylene-matrix composites with halloysite nanotubes with enhanced physical/thermal properties. Polymers 11:787. doi: 10.3390/polym11050787
Silva, É. A., Pokropski, D., You, R., and Kaewunruen, S. (2017). Comparison of structural design methods for railway composites and plastic sleepers and bearers. Aust. J. Struct. Eng. 18, 160–177. doi: 10.1080/13287982.2017.1382045
Tuchschmid, M., Knörr, W., Schacht, A., and Schmied, M. (2011.). Carbon footprint and environmental impact of railway infrastructure content. Available at: https://uic.org/IMG/pdf/uic_rail_infrastructure_111104.pdf (accessed July 4, 2024)
Tufflex (2024). Tufflex Plastic Products Pty. Ltd. Available at: http://tufflex.co.za/ (accessed July 4, 2024)
Ueda, H., Takai, H., Tsujimura, T., and Emoto, M. (1999). Fundamental investigation of LCA of cross tie. Q. Rep. RTRI (Railway Tech. Res. Inst. (Japan)) 40, 210–213. doi: 10.2219/RTRIQR.40.210
Zakeri, J. A., and Sadeghi, J. (2007). Field investigation on load distribution and deflections of railway track sleepers. J. Mech. Sci. Technol. 21, 1948–1956. doi: 10.1007/BF03177452
Keywords: carbon footprint, recycled plastic, sleeper, emission reduction, ABS, LPB repulping reject, railway
Citation: Luomala H, Halme R and Jönkkäri I (2024) Reducing the carbon footprint of railway sleepers using recycled plastics. Front. Sustain. 5:1460159. doi: 10.3389/frsus.2024.1460159
Edited by:
Sakdirat Kaewunruen, University of Birmingham, United KingdomReviewed by:
Asela Kulatunga, University of Exeter, United KingdomKaruppiah Koppiahraj, Saveetha University, India
Copyright © 2024 Luomala, Halme and Jönkkäri. This is an open-access article distributed under the terms of the Creative Commons Attribution License (CC BY). The use, distribution or reproduction in other forums is permitted, provided the original author(s) and the copyright owner(s) are credited and that the original publication in this journal is cited, in accordance with accepted academic practice. No use, distribution or reproduction is permitted which does not comply with these terms.
*Correspondence: Heikki Luomala, aGVpa2tpLmx1b21hbGFAdHVuaS5maQ==