- 1Paul M. Rady Department of Mechanical Engineering, University of Colorado Boulder, Boulder, CO, United States
- 2Artimus Robotics Inc., Boulder, CO, United States
This article introduces a model-based robust control framework for electrohydraulic soft robots. The methods presented herein exploit linear system control theory as it applies to a nonlinear soft robotic system. We employ dynamic mode decomposition with control (DMDc) to create appropriate linear models from real-world measurements. We build on the theory by developing linear models in various operational regions of the system to result in a collection of linear plants used in uncertainty analysis. To complement the uncertainty analyses, we utilize
1 Introduction
Soft robotic systems are under constant development and refinement as they offer advantages over conventional rigid robotic solutions. With their unrivaled potential to navigate unstructured environments, enable safe human-robot interactions, and interact with delicate items, soft robots could offer improvements in various real-world applications, including advancements in surgical devices, search and rescue efforts, and industrial automation (Kim et al., 2013; Rus and Tolley, 2015; Majidi, 2019; El-Atab et al., 2020). Several types of soft actuators have been developed in recent years as discussed in the survey, El-Atab et al. (2020), including those that rely on electrostatic actuation (Pelrine et al., 2000; Gu et al., 2017), those that use electrohydraulic actuation (Acome et al., 2018), those that respond to heat (Du et al., 2023), and those that are driven by pressure (Walker et al., 2020). A wide range of sensors have recently been innovated for use in soft systems as detailed in the review paper, Hegde et al. (2023), including resistive sensors (Bilodeau et al., 2015), capacitive sensors (Nguyen et al., 2019), optic sensors (Zhao et al., 2016), and magnetic sensors (Sundaram et al., 2023). While various soft technologies have emerged in recent years, the infrastructure and standardized framework surrounding model development and controller synthesis for these systems is deficient. The success of soft robotic systems implemented in the real-world depends on the realization of effective real-time controllers (Thuruthel et al., 2018).
Given the proliferation of these individual soft technologies, it has become increasingly difficult to determine a standardized process for developing models and control laws for the conglomerative soft systems. There is tremendous variability just within the slew of available sensors and actuators. In addition to the countless soft physical systems that could be conceived, the individual technologies are still undergoing iterative design processes, and are not yet ready to be mass produced (Lipson, 2014). This implies that there is potential for manufacturing inconsistencies from unit to unit. Additional physical unpredictabilities found in these systems could be due to the nature of their soft material properties. After accounting for the manufacturing variability, soft robotic systems can also possess highly nonlinear dynamics and nearly infinite degrees of freedom (Thuruthel et al., 2018). While rigid robots have the luxury of predictability and standardization, all of the aforementioned variables affect the overall dynamics and uncertainties associated with soft robots.
This paper presents a novel approach to model and control soft robotic systems in a structured, repeatable, and robust manner, accounting for their inherent uncertainties and complexities. This study demonstrates the first implementation of an
First, we rely on data-driven methods to alleviate the burden of deriving dynamical models via first principles for these complex systems. Modelling plays a substantial role in any controller synthesis process, and it is critical that the model obtained is reasonable and accurate to synthesize an appropriate controller. Given the current developmental state of soft robots, their potentially unpredictable mechanical behavior, and their innate nonlinearities, data driven modelling techiques are efficient tools for soft system identification. Further, empirical methods eliminate the need to rederive the complex dynamics from first principles with each system. Specifically, we discuss the data driven reduced order modelling system identification technique, dynamic mode decomposition with control (DMDc) (Proctor et al., 2016).
Our second simplification is to employ linearization as a means of modelling the nonlinear, possibly infinite dimensional systems. We desire the linear model to be an appropriate approximation of the robot’s dynamics. While it is important that the model represents the real-world system, we exploit a concept from linear system theory that the linearizing effects created by feedback control allow us to relax the accuracy of the models and allow for larger deviations from steady state (Skogestad and Postlethwaite, 2005). DMDc produces this desired linear model from empirical data.
Lastly, to complement the linear controller development, we employ robust control theory that enables us to analyze the system’s uncertainty and determine the success of the controller across the system’s operating range. The robustness analysis can be extended to determine if the system remains stable in the presence of inconsistencies due to manufacturing processes in addition to the neglected or unmodelled dynamics. To simplify the numerous potential sources of error from these systems, we “lump the uncertainty” into a single complex perturbation (Skogestad and Postlethwaite, 2005). We demonstrate the simplicity and efficacy of this generalized framework through the development of a controller for a nonlinear soft robotic system driven by HASEL actuators.
The system, depicted in Figure 1A, emulates the biceps and triceps configuration of the upper portion of the human arm using two antagonist stacks of contracting HASEL actuators. HASEL actuators are an optimal actuator technology for testing the presented modelling and controller synthesis framework due to their precision (Volchko et al., 2022), muscle-like performance (Rothemund et al., 2021), and fast dynamics (Kellaris et al., 2018; Mitchell et al., 2019). In this work, Peano-HASEL actuators were used due to their linear contraction on activation (Kellaris et al., 2018), which enables bioinspired robotic designs. While modelling and closed loop efforts have been made in the world of HASEL actuators (Schunk et al., 2018; Johnson et al., 2020; Rothemund et al., 2020; Volchko et al., 2022), none of them have demonstrated the application of robust control techniques.
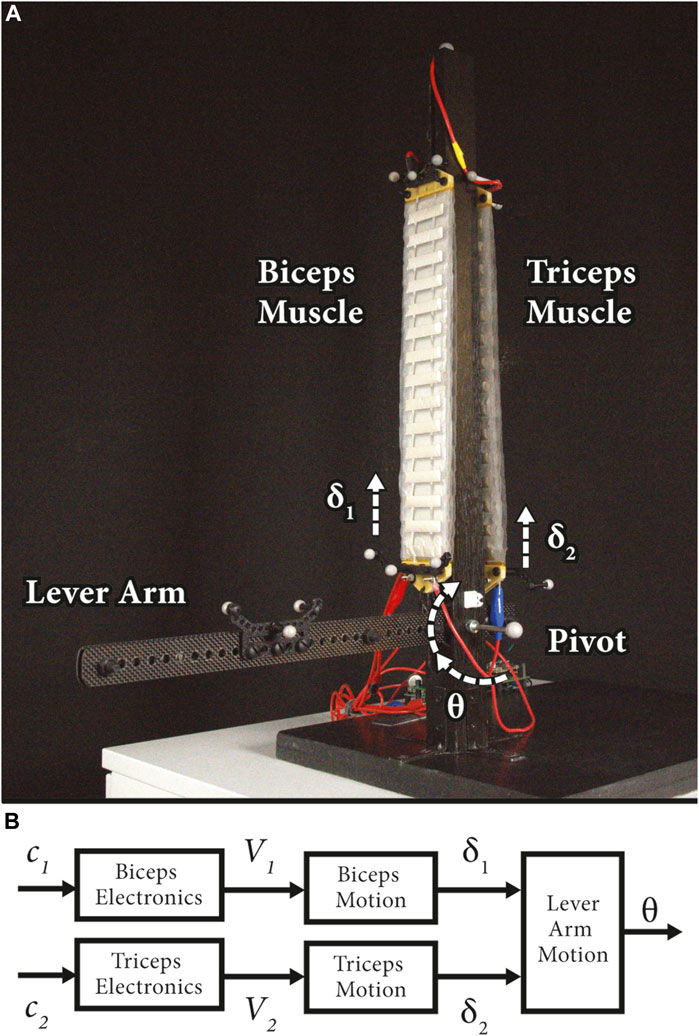
Figure 1. (A) The benchtop system emulates the upper portion of the human arm, where the antagonist muscles, biceps and triceps, work together to control the orientation,
The generalized linear system and robust control framework demonstrated in this paper could facilitate fast real-time control of soft robotic systems in real-world applications. In particular, we could apply this framework to electrohydraulic actuators used to control pumps or valves for fluid metering (Fuaad et al., 2023). In such systems, it would be important to adopt robust position control laws to help ensure accurate fluid flow and dosing. This framework could also be applied to bio-inspired swimming robots that rely on electrohydraulic actuation (Hess and Musgrave, 2023). These aquatic systems could benefit from robust control laws that increase their efficiency and maneuverability in hydrodynamic exploration of various underwater environments—aiding in CO2 monitoring and climate change predictions, for example,.
This paper is comprised of the following sections. Section 2 introduces the theory that is pivotal to the presented framework, including (2.1) an overview of linear system control theory, (2.2) multivariable robust control concepts, and (2.3) dynamic mode decomposition. Section 3 discusses the innerworkings of the HASEL actuator along with its advantages and relevance to this work. The subsequent Section 4 describes the experimental benchtop system, the methods applied, and the resultant performance. Two subsections describe the modelling and controller implementation of both the voltage dynamics (4.1) and the displacement dynamics (4.2). Finally, we conclude with discussion and future recommendations in Section 5.
2 Theory
This section aims to situate the experimental and applied work described in Section 4 within the broader framework outlined in this paper. By providing background information on the theory, readers can gain perspective on the scope of this methodology, understand its limitations and potential applications, and further develop this research for their own studies. The equations described in this section provide insight and context for the figures and plots presented in this work.
2.1 Linear system control theory
At first glance, it may seem unintuitive to apply linear system control theory to nonlinear soft robotic systems. However, it has been demonstrated that linear modelling and control techniques have been successful in enabling real-time control of other nonlinear dynamical systems working in real-world situations, such as helicopter flight control (Smerlas et al., 2001) and hydraulic actuator control (Niksefat and Sepehri, 2001). Implementing feedback control creates a local linearizing effect in which the linear model remains valid since the negative feedback loop keeps the system output near the desired state. This justifies the use of linear models in control design of nonlinear systems (Skogestad and Postlethwaite, 2005). Additionally, there is a global linearizing effect since the reference to output response is approximately linear for stable closed-loop systems (Skogestad and Postlethwaite, 2005). Many readily available and intuitive controller synthesis and analysis tools are designed for linear systems. Linear system theory provides us with a road map to create feasible control laws that can guarantee performance requirements, even in the presence of uncertainty. Further detail on the following overview of this theory can be found in (Chen, 1984; Skogestad and Postlethwaite, 2005).
Many physical dynamical systems can be described with the following set of equations:
where
with signals
While it is convenient to demonstrate performance metrics and analyze uncertainty in continuous time, it is necessary to collect data and implement digital controllers in discrete time. We denote the discrete-time LTI systems as:
where
where the identity matrix
as a function of frequency to synthesize a linear controller,
meet performance specifications. These design knobs are used to intuitively manipulate the shape of
where
The signal gains captured by these singular values correspond directly to the
The
describes the closed loop response from reference signals,
to describe the control output signal,
In order to formulate this optimization problem, the system must be restructured such that all the input signals,
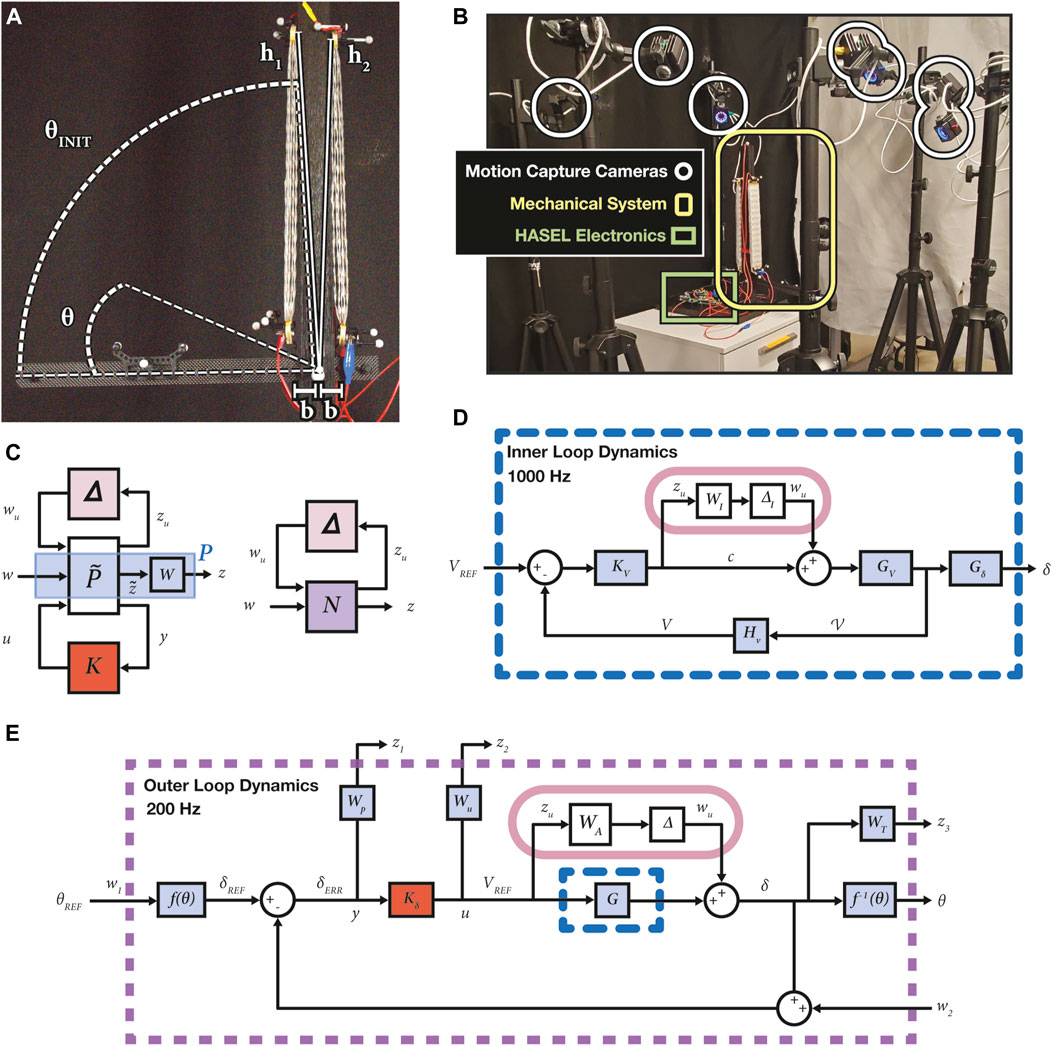
Figure 2. (A) The HASEL actuators were secured from the pivot at distances
Individual input signals
where
and
where real scalars
where
After adjusting the weighting functions, we can find the optimal
such that we can minimize its
where
2.2 Robust control theory
Robust control theory promotes the development of controllers that are effective in real world applications due to its ability to assess system properties such as stability and performance in the presence of system uncertainty. Within the robust control domain, we focus our work on robust stability. Robust stability signifies that all plants in a set of possible plants remain stable with the implementation of a selected controller. The uncertainty discussed in this section regards the variation from a set of possible plants to the nominal system model. Stability of a system is critical in real-world implementation and means that for a bounded input signal, the internal signals remain bounded. This translates to the system converging to equilibrium over time. Robust control theory has been applied to a multitude of fields including aerospace systems, chemical processes, power networks and fluidic systems (Dullerud and Paganini, 2013). However, it is not yet prevalent in the field of soft robotics.
Robust control techniques could be beneficial and complementary to the field of soft robotics, due to the uncertainty that can be attributed to various aspects of soft robots. For example, system uncertainties could include unmodelled or neglected dynamics. Given that soft robots can have nearly infinite dimensions (infinite degrees of freedom), it is important to account for the error arising from the missing dimensions as our model must be finite dimensional. In addition to a reduction in dimensionality, the controller synthesis techniques discussed require a linear model of the nonlinear plant, introducing further inaccuracies. This source of model uncertainty can also be accounted for by using robust control techniques.
In addition to the innately complex dynamics of soft robots that will be neglected in the models, there may also be uncertainties due to the operating conditions. Given the flexibility and compliance in these systems, there is room for deviations from expected dynamics with changes in external factors, such as temperature, humidity (Liu et al., 2019), and externally applied forces (Rothemund et al., 2020). There may also be inconsistencies in either the materials used in making the compliant actuators or the processes used to develop them.
Provided the many sources of uncertainty present in the field of soft robotics, it is important to use appropriate measures to represent such uncertainty and ensure the system remains stable for all possible plants. This work focuses its uncertainty analyses on unstructured (complex) uncertainty, rather than parametric (real) uncertainty. We use Bode plots to model the unstructured uncertainty in our models with a single frequency-dependent weighting function. Similarly, the previously discussed
We can lump the various sources of error in the model dynamics into a single complex perturbation which will simplify the analysis. The complex perturbation, denoted
is selected to set an upper bound on the multiplicative uncertainty,
where
is selected to set an upper bound on the additive uncertainty,
After selecting the weight,
2.3 Dynamic mode decomposition with control and the Koopman operator theory
In order to make use of the linear systems and robust control theory mentioned above, it is important to derive linear models of the soft system. Dynamic mode decomposition (DMD) can be used to develop linear models of complex nonlinear dynamical systems with no knowledge of the plant a priori (Tu et al., 2014). DMD is an empirical method that is used to linearly approximate the system’s underlying dynamics. DMDc is an extension of DMD as it disambiguates between the system’s intrinsic dynamics and its response to external forcing (Proctor et al., 2016). Soft robots can benefit from data-driven modelling approaches given that their dynamics are difficult to derive from first principles. Furthermore, this empirical system identification tool enables the physical soft systems to be reconfigured without rederiving mathematical models each time.
DMDc is closely related to the Koopman operator theory in that it uses a linear operator to describe highly complex, nonlinear system dynamics. Given that it is not tractable to work with infinite dimensionalities, as the Koopman operator entails, we can instead work with a finite dimensional approximation of it. Therefore, extensions of DMDc are relevant in the field of soft robotics since they offer a means of reducing high-dimensional dynamic systems to tractable low-order linear models. This is possible by extending the dictionary of observables in the state space to help account for nonlinearities that appear in the dynamics (Bruder et al., 2021). Related methods include eDMD, mrDMD, and SINDy, which could provide more accurate linear models of the nonlinear soft systems. eDMD works by increasing the dictionary of observables associated with the system (Li et al., 2017). While mrDMD combines DMD with wavelet theory and adjusts time resolutions and windowing to help account for varied temporal activity within the system dynamics (Kutz et al., 2016). Lastly, SINDy helps identify a sparse basis for the dynamical system (Brunton et al., 2016).
The following steps describe how to develop a model using DMDc (Proctor et al., 2016). First, the inputs and outputs of the system are selected to be recorded and stacked into the control snapshot vector,
as well as the state snapshot matrix shifted by
The matrices,
Similarly, the unknown dynamic and control input matrices are concatenated as well:
The linear dynamic equation expressed in Eq. 5 can be reformulated in the scope of the DMDc algorithm as
and rewritten in terms of the stacked matrices,
Then, we perform a pseudoinverse (
and thus, solve the expression:
Substituting the pseudoinverse of
and further calculate the approximate dynamic and input matrices,
with
for which
3 HASEL actuators
For this work, we used HASEL actuators to operate the demonstrative soft actuator platform (Figure 1A). These actuators are ideal to demonstrate controller operation as they can exhibit high-speed actuation (Kellaris et al., 2018; Johnson et al., 2020) and precise control (Volchko et al., 2022). In addition, they can be adapted to many robotic systems due to their versatile design space which can enable a wide range of morphologies and actuation modes such as contraction, expansion, bending, and twisting (Acome et al., 2018; Kellaris et al., 2018; Mitchell et al., 2019). HASEL actuators operate using an electrohydraulic mechanism; this mechanism uses principles of both electrostatic and hydraulic actuation, which enables efficient operation, controllable output, and high-speed response.
HASEL actuators are comprised of three main components: polymer film, a liquid dielectric, and conductive electrodes. The thin polymer film is formed into a shell which is filled with the liquid dielectric to create an enclosed pouch. Opposing electrodes are placed on either side of the actuator over a portion of the pouch. When a voltage (typically several kilovolts) is applied, electrostatic forces cause the electrodes to progressively “zip” together, displacing the fluid between the electrodes to a different region in the pouch, causing shape change of the structure. Due to the inextensible nature of the polymer film, this causes linear contraction in the actuator (Kellaris et al., 2018).
Additionally, HASEL actuators are operable outside of a laboratory and, more specifically, suitable for driving untethered soft robotic systems, due to their energy and power density, low-power consumption, and customizability. Although these devices require a high voltage stimulus, input currents are typically less than 1 mA, resulting in peak input power of only watts. These actuators have an inherent catch-state, due to their capacitive energy storage, wherein an actuated state can be held while consuming only milliwatts or less of power. HASELs have been shown to consume 100 times less power than a comparable servo motor while holding a position (Kellaris et al., 2021). Myriad examples of miniaturized DC-DC power supplies can be utilized to step-up battery level voltages to the necessary high voltage inputs, making these actuators an attractive solution for compact, battery-powered soft robotic systems (Mitchell et al., 2019; Mitchell et al., 2022; Wang et al., 2023).
4 Robust control implementation
The benchtop system (Figure 1A), similar to that described in (Volchko et al., 2022), was designed to imitate the upper portion of the human arm, where the artificial biceps and triceps muscles work together to control the orientation of the system’s end effector. We present an overview of the system signals that are necessary for the control scheme developed in this work in Figure 1B. Charge signals,
The dimensions of the system configuration are shown in Figure 2A, and the experimental setup is depicted in Figure 2B. The robotic arm consisted of a carbon fiber lever arm attached to a stationary wooden column using a low friction radial bearing. The wooden column was anchored to a wooden platform to secure the system. A stack of five contracting actuators (Part No. C-5020-15-01-C-CCBC-50-140) were electrically and mechanically connected in parallel to form the biceps muscle, and a separate stack of five identical actuators were used for the triceps muscle. All HASEL actuators were based on the Peano-HASEL design described in Kellaris et al. (2018) and provided by Artimus Robotics. Their parameters can be found in the Supplementary Table S1.
The electronics package to drive actuation was also provided by Artimus Robotics (Part No. PS2-10-030-02). This power supply consisted of two independently addressable high voltage amplifiers. A Teensy 4.0 microcontroller was used to generate control signals,
The controller design process is comprised of the following individual procedures: system identification, model validation, controller synthesis, and uncertainty analysis. This is followed by controller simulation, implementation, and validation. The electrical dynamics were assumed to be significantly faster than the physical dynamics (Rothemund et al., 2020), and thus a cascaded control approach was used, as shown in Figures 2D,E. Additionally, this control scheme made the signals easier to isolate in order to analyze and study them.
The following methods, technologies, and software were used to execute closed loop control of the system described above. ROS was used to communicate with the multi-channel high power supply and the motion capture system, while running the data collection and controller scripts on a Linux OS. Arduino timer interrupts and ROS timers regulated the data acquisition and control rates. ROS data was timestamped in real time with respect to all ROS topics. All scripts can be found within the linked repository.
All data collection for the inner loop (Figure 2D) was performed at 2000 Hz. The control loop for the voltage dynamics was on board the microcontroller and set to run at 1,000 Hz. However, the communication protocol used to communicate between the microcontroller and the Linux machine over USB was limited to 200 Hz. Communication rates greater than 200 Hz became inconsistent due to the low priority of USB bulk transfers, which the Teensy 4.0 serial communication is built on, and therefore, resulted in instability. Thus, the physical dynamics (Figure 2E) were analyzed with a data collection rate of 200 Hz, and the outer loop was closed at 200 Hz.
Finally, MATLAB (MathWorks R2023), its robust toolbox, and its Simulink environment were used for all of the post processing, data analysis and controller synthesis work.
4.1 Voltage control
The power supply provided by Artimus is fundamentally a current controlled system, where the duty cycle of the pulse-width modulation (PWM) signal controls the amount of current supplied to the actuators. However, a voltage-controlled system is desirable, since voltage is an easily measured parameter that provides a direct analog to the physical state of the actuator (as the actuator performance is proportional to the applied voltage squared (Kellaris et al., 2018)). Thus, our control approach began with synthesizing a voltage controller to regulate the output voltage at each channel by adjusting the duty cycle of the applied PWM signals.
4.1.1 System identification and model validation
To perform system identification on the inner most loop, visualized in Figure 2D, we chose to represent the system with inputs of duty cycles of the PWM signals that were sent to the power supply unit,
To collect data for system identification, the closed loop system was sent a voltage reference profile around incremental voltage biases that ranged from 500 V to 5500 V. We selected multiple voltage biases due to the aforementioned variability in voltage responses depending on the operating point. The reference voltage profiles then varied from the initial biases by
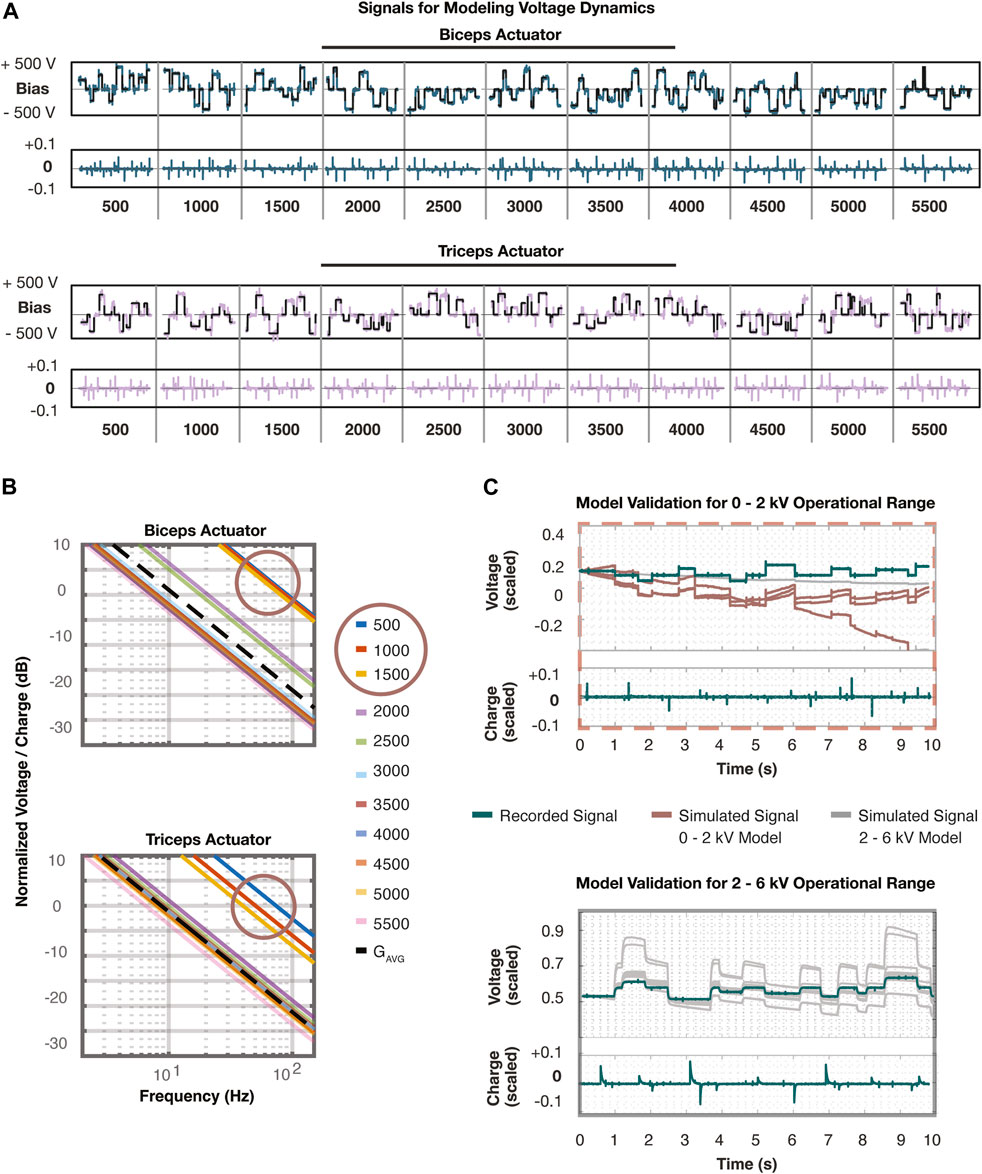
Figure 3. (A) These plots represent all data collected to identify linear models of the voltage dynamics. A reference voltage was sent to the initially implemented voltage controller to remain within small regions of the operational voltage range. A linear model was identified at every 500 V step from 500 to 5500 V for both the biceps and triceps muscles. The charge input was recorded and the voltage that followed was recorded. The vertical lines distinguish the segments of data corresponding to each voltage bias listed at the bottom. Each segment corresponds to 10 s of data collection. (B) The 22 transfer functions are plotted that were discovered using DMDc on each segment of data in (A). Additionally, an estimate (black dashed line) of the average of these transfer functions is depicted. The two distinct regions of dynamics are apparent in this figure, where the linear models formed around the voltage biases 500–1500 V (circled) have a much higher magnitude on the Bode plot than the others. This demonstrated the need to break the system into two distinct regions and proceed by developing and analyzing one controller for each region. (C) The top plot demonstrates the validation of the voltage dynamics in the 0–2 kV range where the input and output data (teal) was recorded and compared against the simulated response of all linear models. The dark red lines denote the models within this range, while the grey lines represent the models in the 2–6 kV range. It is apparent these models demonstrate little response to the recorded input and appear as a nearly flat line. The bottom plot demonstrates the validation of the voltage dynamics in the 2–6 kV range where the input and output data (teal) was recorded and compared against the simulated response of all linear models. However, the linear models from the 0–2 kV range quickly deviated from the initial state and therefore were not plotted alongside.
Before developing the linear models, all signals were normalized with respect to their maximum values prior to performing DMDc to help the interpretability of the Bode plots. The voltage signal was normalized with respect to the estimated maximum voltage of the power supply at 6000 V and the charge signal was normalized with respect to the maximum 12-bit resolution PWM signal duty cycle of 4096. Applying the DMDc algorithm following Eqs 27-38 to each segment of normalized data resulted in 22 distinct models of the voltage dynamics in the form Eq. 5. These 22 models represent the collection of possible plants,
4.1.2 Controller synthesis
Following the validation of the models, we used loop shaping methods to develop a controller for closed loop voltage control following the process outlined in Åström and Murray (2021). The Bode plots labelled “Loop Shaping” in Figures 4A,B depict the transfer function of the nominal plant,
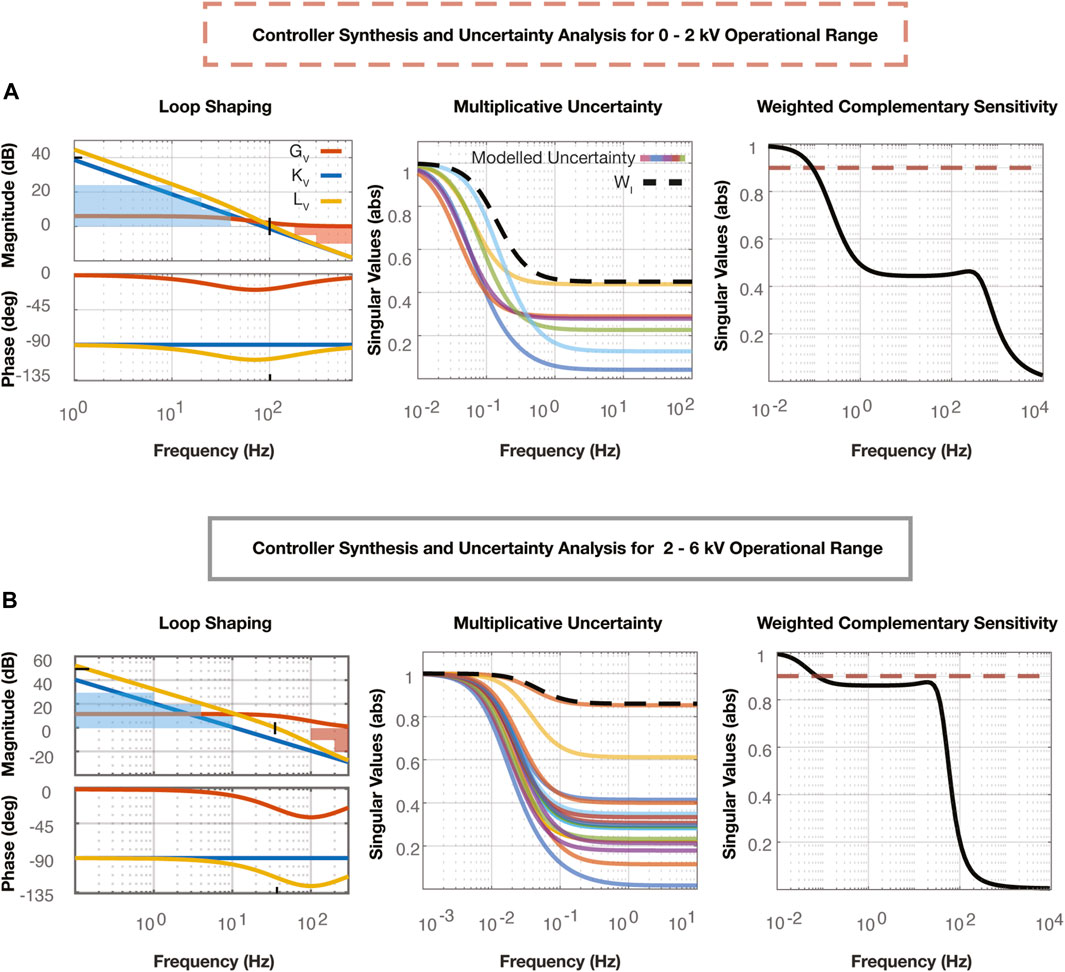
Figure 4. (A) The Loop Shaping plot represents the open loop shaping process used to synthesize the voltage controller in the 0–2 kV range. All three transfer functions are plotted, including the nominal plant,
The resultant lag controller,
The resultant lag controller,
4.1.3 Uncertainty analysis
Uncertainty analysis methods integrating the lag controller were used to determine if these controllers would suffice for all possible plants,
4.1.4 Controller simulation, implementation, and validation
Before implementing the voltage controller on the physical system, a simulation was created in the Simulink environment, with additional measures to ensure that a discrete-time controller maintained similar performance to the continuous-time controller. The resulting closed loop simulations can be found in Figures 5A,B. The new lag compensators were discretized at 1,000 Hz using a zero-order hold and implemented into the system as
and
We implemented the gain scheduling approach based on the scheduling variable, voltage. If the recorded voltage signal was less than 2,000 V,
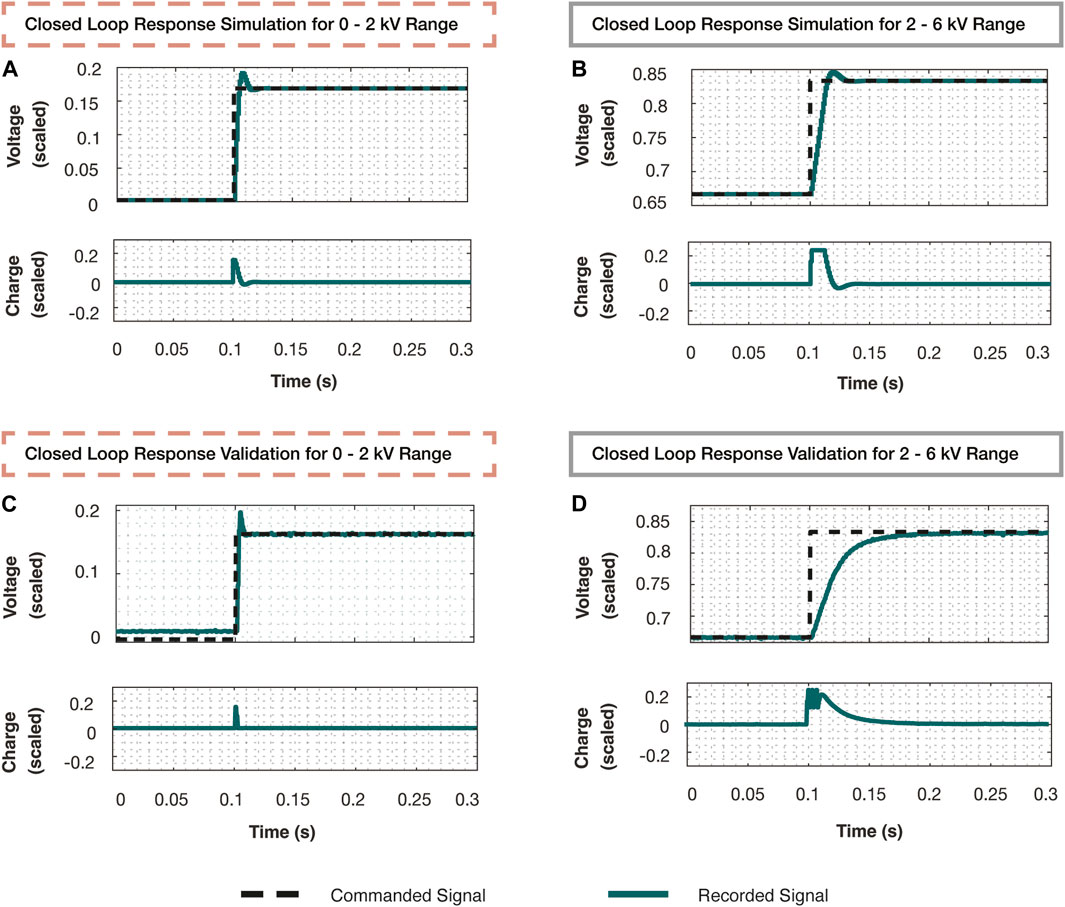
Figure 5. (A) The step response of the simulated closed loop system from 0 to 1 kV using the controller,
4.2 Position control
After the inner loop voltage controller was implemented, we synthesized the outer loop displacement controller. The first block,
and
with
All variables are depicted in the system setup in Figure 2A and describe the system’s initial orientation,
4.2.1 System identification and model validation
To begin identifying the dynamics of the MIMO plant,
Next, we commanded both muscles with random step inputs lasting 0.2–1.2 s and ranging in magnitudes of
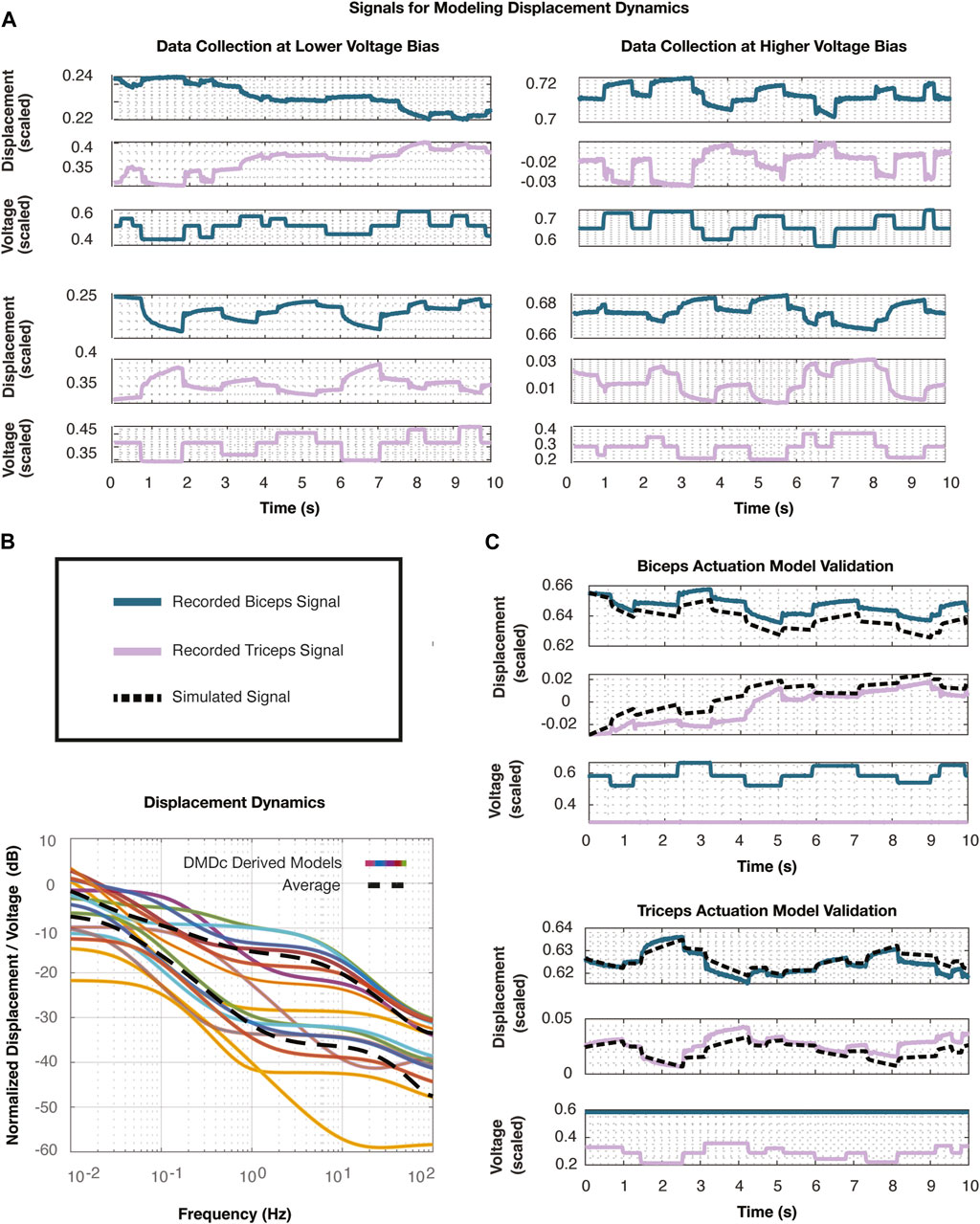
Figure 6. (A) These plots depict the signals collected to identify linear models of the actuator displacement dynamics. The system actuators were offset by a voltage bias, and two of these eight scenarios are plotted, for which the system is actuated by the biceps (top) and the triceps (bottom). (B) The singular value plots show all eight linear models developed using DMDc, each corresponding to a voltage bias that was set for data collection. The dashed line represents an approximate average of all of these transfer functions and was selected as the nominal plant for the controller synthesis and uncertainty analysis procedures. (C) Simulated step responses demonstrate voltage input to displacement output and validate the nominal models discovered with DMDc with respect to both biceps (top) and triceps (bottom) actuation.
We normalized all of the signals with respect to their maximum values to drive the intuition behind the following controller synthesis and uncertainty analysis procedures. The voltage was again scaled with respect to the rail voltage of 6,000 V and the displacement was normalized with respect to its maximum recorded displacement of 8 mm. Similar to the system identification approach of the voltage dynamics, we developed linear models following the DMDc algorithm in Eqs 27-38 from the various base voltages for the actuator displacement dynamics combining the biceps and triceps actuation profiles at each corresponding bias. Thus, we used eight distinct voltage biases to create eight distinct linear models where the state and input of the system were selected to be
The resultant linear models are depicted in the singular value plot in Figure 6B. The transfer functions were averaged to result in the averaged linear model of the system (dashed line). We selected the DMDc model that most closely followed this average transfer function as the nominal plant in the following controller synthesis steps. The selected nominal model,
We simulated the nominal plant using 20 s of validation data that was collected at the same voltage biases. This simulated data is compared with the empirical data in Figure 6C. The system was validated against both biceps and triceps input data, giving us confidence to proceed with the control design using the nominal plant,
4.2.2 Controller synthesis
After selecting a nominal plant,
were specified to maintain a closed loop bandwidth of 0.8 and 0.6 Hz and provide nearly 0% steady state error in the biceps muscle. These weightings were adjusted following the approach outlined in Eqs 18, 19. We allowed for greater steady state error in the triceps muscle, to ensure that there was room for error in the measurements used in the geometric functions 39–41. We limited the control effort by selecting weighting functions,
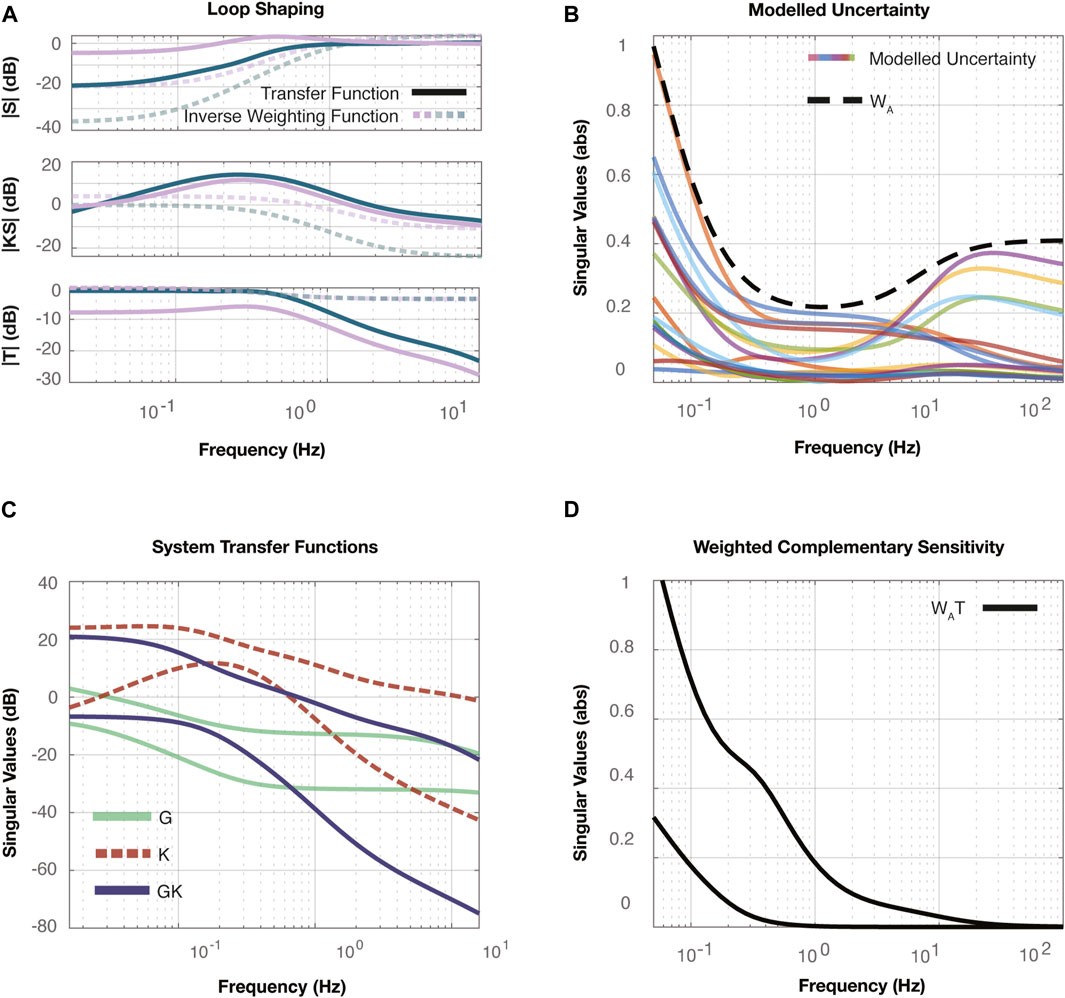
Figure 7. (A) The mixed synthesis results are shown with the three singular value plots. The top plot compares the resultant system’s sensitivity,
These specifications resulted in the
4.2.3 Uncertainty analysis
An uncertainty analysis was performed for the actuator displacement dynamics. However, due to the large uncertainties induced when attempting to use a multiplicative model for uncertainty, we resorted to a less restrictive uncertainty analysis, employing additive model uncertainty. The additive uncertainty structure can be found in Figure 2E. We calculated the uncertainty using
4.2.4 Controller simulation, implementation, and validation
Prior to implementing the
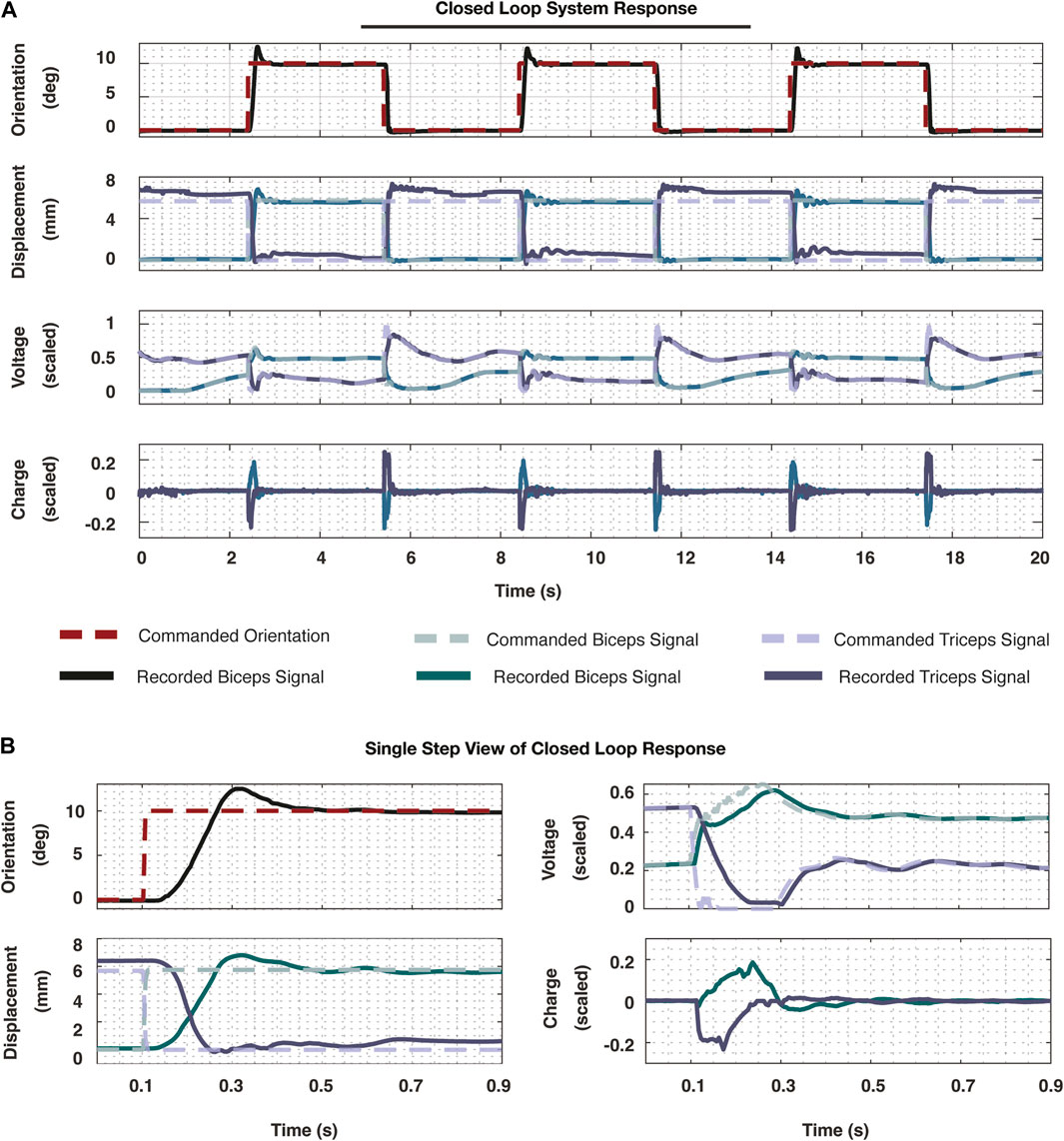
Figure 8. (A) The resultant signals are plotted from implementing the entire cascade controller developed in this work. The system was prescribed three step commands. The top plot demonstrates the reference orientation signal (dashed) and the recorded orientation (solid). These signals were recorded at 200 Hz. The following plot demonstrates the reference displacement signals that were commanded (dashed) and the recorded displacements (solid) of the two actuators. The subsequent plot further demonstrates the commanded voltage signal (dashed) and the measured voltage signal (solid). Finally, at the core of the system, the charge signals were plotted for each of the muscles. While the charge and voltage signals are scaled, the true measurements for displacement and orientation are plotted to highlight the scale of this work. (B) To truly visualize the response of the system, a single rising side of one step response is plotted, including all the signals represented in (A). This demonstrates the speed of which the system was able to achieve steady state along with the other performance metrics noted in this work.
In observing a single step response in Figure 8B from this
5 Discussion and future directions
This paper outlines a novel framework for synthesizing robust control laws for soft robotic systems and demonstrates its implementation. We presented the first multivariable
Specific to the electrohydraulic actuators used in this work, we employed a cascade control architecture, allowing us to close the inner voltage control loop at a higher rate than the outer position control loop. Therefore, we developed the voltage control laws first. We determined simplified linear models of the voltage dynamics across the entire operating range using a data driven approach known as DMDc. The various models allowed us to address the variability within the nonlinear system’s full range of motion. Specifically, we identified two voltage regimes with distinct behaviors and correspondingly designed two separate lag controllers using loop shaping methods. We performed the uncertainty analyses for each regime by lumping the plant variability within a single complex perturbation. We implemented feedback control for each muscle using a gain scheduling procedure which resulted in closed loop rise times of 0.0013 and 0.0416 s, settling times of 0.008 and 0.163 s, and a stable response across the entire operational range.
To begin synthesizing a position controller, we identified a set of linear dynamic models to represent the motion of the mechanical system at different operating points. We selected a nominal model for each family of plants and employed
The success of this framework relies on properly selecting a linear model or set of linear models to represent the system. The linear models must appropriately estimate the complex dynamics of each unique system. More accurate models lend themselves to more appropriately designed controllers and more accurate uncertainty models. While the DMDc-derived models demonstrated substantial agreement to the system’s true response, the models did not capture the higher-frequency dynamics that were present. Extensions of DMD could better estimate physical system dynamics from empirical data. Some extensions include extended DMD (eDMD), multiresolution DMD (mrDMD) and Sparse Identification of Nonlinear Dynamics (SINDy) (Brunton et al., 2016; Kutz et al., 2016; Li et al., 2017). We suggest incorporating these methods when DMDc-derived models are not valid approximations of the physical plant.
Additionally, it would be advantageous to demonstrate this control methodology applied outside of a motion capture environment by utilizing integrated sensory feedback. A key advantage of HASEL actuators is their ability to simultaneously act as sensors and actuators (Acome et al., 2018; Ly et al., 2021). As deformable capacitors, HASEL actuators change capacitance as they actuate, and this capacitance change can be mapped to a change in the actuator displacement. Integrating capacitive self-sensing with the robust control methods elucidated in this work will broaden applications for electrohydraulic soft-actuated systems that operate outside of a laboratory environment. The developed framework can be implemented on untethered electrostatic systems powered by HASELs or DEAs, like those presented in Mitchell et al. (2019), Mitchell et al. (2022), Wang et al. (2023), Li et al. (2021) and Zhang et al. (2018).
These robust methods can extend past modelling a single system and can be used to determine the uncertainty across a range of actuators and capture the change in dynamics for a variety of actuator shapes, sizes, or materials. These robust methods could also be used to analyze the presence of extrinsic factors, such as loading or significant temperature changes. Using the methodology outlined in this article, we could work to understand stability regimes for a range of soft actuators or their varying environmental settings.
While we address robust stability and closed loop nominal performance individually, future work could focus on developing controllers that combine these two aspects to achieve robust performance of soft systems.
The framework outlined in this paper provides a methodology for applying linear control theory and robust stability measures to nonlinear soft robotic systems. Importantly, this method requires no knowledge of the system a priori. Implementing the measures of robustness outlined in this controller synthesis framework enables real-time, stable control of high-speed soft robotic systems, regardless of their means of sensing and actuation, inherent nonlinearities, or other uncertainties prevalent in the field of soft robotics. In order to unleash soft robots into the real world, we need to develop a generalized control framework that is just as adaptable and compliant as the physical systems.
Data availability statement
The datasets generated and analyzed for this study can be found in the Robust Control of Electrohydraulic Soft Robots github repository at https://github.com/avolchko/Robust_Control_of_Electrohydraulic_Soft_Robots.git.
Author contributions
AV: Conceptualization, Data curation, Formal Analysis, Investigation, Methodology, Software, Supervision, Writing–original draft, Writing–review and editing. SM: Formal Analysis, Investigation, Methodology, Software, Supervision, Writing–original draft, Writing–review and editing, Conceptualization, Funding acquisition, Validation. TS: Writing–review and editing, Software. ZT: Writing–review and editing, Writing–original draft. JH: Supervision, Writing–review and editing.
Funding
The author(s) declare that financial support was received for the research, authorship, and/or publication of this article. This material is based upon work supported by U.S. Army Small Business Technology Transfer Program Office and Army Research Office Under Contract No. W911NF22C0024.
Conflict of interest
SM is listed as an inventor on a U.S. patent application US10995779B2 and US20210003149A1 which cover fundamentals and basic designs of HASEL actuators. SM is a co-founder of Artimus Robotics, a start-up company commercializing HASEL actuators.
The remaining authors declare that the research was conducted in the absence of any commercial or financial relationships that could be construed as a potential conflict of interest.
Publisher’s note
All claims expressed in this article are solely those of the authors and do not necessarily represent those of their affiliated organizations, or those of the publisher, the editors and the reviewers. Any product that may be evaluated in this article, or claim that may be made by its manufacturer, is not guaranteed or endorsed by the publisher.
Supplementary material
The Supplementary Material for this article can be found online at: https://www.frontiersin.org/articles/10.3389/frobt.2024.1333837/full#supplementary-material
References
Acome, E., Mitchell, S. K., Morrissey, T. G., Emmett, M. B., Benjamin, C., King, M., et al. (2018). Hydraulically amplified self-healing electrostatic actuators with muscle-like performance. Science 359, 61–65. doi:10.1126/science.aao6139
Åström, K. J., and Murray, R. M. (2021). Feedback systems: an introduction for scientists and engineers. Princeton, NJ: Princeton University Press.
Bilodeau, R. A., White, E. L., and Kramer, R. K. (2015). “Monolithic fabrication of sensors and actuators in a soft robotic gripper,” in 2015 IEEE/RSJ international conference on intelligent robots and systems (IROS) (IEEE), 2324–2329.
Bruder, D., Fu, X., Gillespie, R. B., Remy, C. D., and Vasudevan, R. (2021). Data-driven control of soft robots using koopman operator theory. IEEE Trans. Robotics 37, 948–961. doi:10.1109/TRO.2020.3038693
Brunton, S. L., Proctor, J. L., and Kutz, J. N. (2016). Discovering governing equations from data by sparse identification of nonlinear dynamical systems. Proc. Natl. Acad. Sci. 113, 3932–3937. doi:10.1073/pnas.1517384113
Chen, C.-T. (2014). Linear system theory and design. in The Oxford Series in Electrical and Computer Engineering Series. Oxford University Press.
Du, H., Li, G., Sun, J., Zhang, Y., Bai, Y., Qian, C., et al. (2023). A review of shape memory alloy artificial muscles in bionic applications. Smart Mater. Struct. 32, 103001. doi:10.1088/1361-665X/acf1e8
Dullerud, G. E., and Paganini, F. (2013). A course in robust control theory: a convex approach, vol. 36. Springer Science & Business Media.
El-Atab, N., Mishra, R. B., Al-Modaf, F., Joharji, L., Alsharif, A. A., Alamoudi, H., et al. (2020). Soft actuators for soft robotic applications: a review. Adv. Intell. Syst. 2, 2000128. doi:10.1002/aisy.202000128
Fuaad, M. R. A., Hasan, M. N., Muthalif, A. G. A., and Ali, M. S. M. (2023). Electrostatic-hydraulic coupled soft actuator for micropump application. Smart Mater. Struct. 33, 015033. doi:10.1088/1361-665X/ad1428
Gu, G.-Y., Zhu, J., Zhu, L.-M., and Zhu, X. (2017). A survey on dielectric elastomer actuators for soft robots. Bioinspiration Biomimetics 12, 011003. doi:10.1088/1748-3190/12/1/011003
Hegde, C., Su, J., Tan, J. M. R., He, K., Chen, X., and Magdassi, S. (2023). Sensing in soft robotics. ACS Nano 17, 15277–15307. doi:10.1021/acsnano.3c04089
Hess, I., and Musgrave, P. (2023). “Nebula: a flexible, solid-state swimming robot enabled by hasel actuators,” in ASME 2023 conference on smart materials, adaptive structures and intelligent systems of smart materials, adaptive structures and intelligent systems), V001T06A004. doi:10.1115/SMASIS2023-110945
Johnson, B. K., Sundaram, V., Naris, M., Acome, E., Ly, K., Correll, N., et al. (2020). Identification and control of a nonlinear soft actuator and sensor system. IEEE Robotics Automation Lett. 5, 3783–3790. doi:10.1109/LRA.2020.2982056
Kellaris, N., Gopaluni Venkata, V., Smith, G. M., Mitchell, S. K., and Keplinger, C. (2018). Peano-HASEL actuators: muscle-mimetic, electrohydraulic transducers that linearly contract on activation. Sci. Robotics 3, eaar3276. doi:10.1126/scirobotics.aar3276
Kellaris, N., Rothemund, P., Zeng, Y., Mitchell, S. K., Smith, G. M., Jayaram, K., et al. (2021). Spider-inspired electrohydraulic actuators for fast, soft-actuated joints. Adv. Sci. 8, 2100916. doi:10.1002/advs.202100916
Kim, S., Laschi, C., and Trimmer, B. (2013). Soft robotics: a bioinspired evolution in robotics. Trends Biotechnol. 31, 287–294. doi:10.1016/j.tibtech.2013.03.002
Kutz, J. N., Fu, X., and Brunton, S. L. (2016). Multiresolution dynamic mode decomposition. SIAM J. Appl. Dyn. Syst. 15, 713–735. doi:10.1137/15m1023543
Landau, I. D., and Rolland, F. (1994). “An approach for closed loop system identification,” in Proceedings of 1994 33rd IEEE conference on decision and control (IEEE), 4, 4164–4169.
Li, G., Chen, X., Zhou, F., Liang, Y., Xiao, Y., Cao, X., et al. (2021). Self-powered soft robot in the mariana trench. Nature 591, 66–71. doi:10.1038/s41586-020-03153-z
Li, Q., Dietrich, F., Bollt, E. M., and Kevrekidis, I. G. (2017). Extended dynamic mode decomposition with dictionary learning: a data-driven adaptive spectral decomposition of the Koopman operator. Chaos Interdiscip. J. Nonlinear Sci. 27, 103111. doi:10.1063/1.4993854
Lipson, H. (2014). Challenges and opportunities for design, simulation, and fabrication of soft robots. Soft Robot. 1, 21–27. doi:10.1089/soro.2013.0007
Liu, X., Zhang, J., and Chen, H. (2019). Ambient humidity altering electromechanical actuation of dielectric elastomers. Appl. Phys. Lett. 115, 184101. doi:10.1063/1.5126654
Ly, K., Kellaris, N., McMorris, D., Johnson, B. K., Acome, E., Sundaram, V., et al. (2021). Miniaturized circuitry for capacitive self-sensing and closed-loop control of soft electrostatic transducers. Soft Robot. 8, 673–686. doi:10.1089/soro.2020.0048
Majidi, C. (2019). Soft-matter engineering for soft robotics. Adv. Mater. Technol. 4, 1800477. doi:10.1002/admt.201800477
Mitchell, S. K., Martin, T., and Keplinger, C. (2022). A pocket-sized ten-channel high voltage power supply for soft electrostatic actuators. Adv. Mater. Technol. 7, 2101469. doi:10.1002/admt.202101469
Mitchell, S. K., Wang, X., Acome, E., Martin, T., Ly, K., Kellaris, N., et al. (2019). An easy-to-implement toolkit to create versatile and high-performance HASEL actuators for untethered soft robots. Adv. Sci. 6, 1900178. doi:10.1002/advs.201900178
Nguyen, N. T., Sarwar, M. S., Preston, C., Le Goff, A., Plesse, C., Vidal, F., et al. (2019). Transparent stretchable capacitive touch sensor grid using ionic liquid electrodes. Extreme Mech. Lett. 33, 100574. doi:10.1016/j.eml.2019.100574
Niksefat, N., and Sepehri, N. (2001). “Designing robust force control of hydraulic actuators despite system and environmental uncertainties,” in IEEE control systems magazine.
Pelrine, R., Kornbluh, R., Pei, Q., and Joseph, J. (2000). High-speed electrically actuated elastomers with strain greater than 100%. Science 287, 836–839. doi:10.1126/science.287.5454.836
Proctor, J. L., Brunton, S. L., and Kutz, J. N. (2016). Dynamic mode decomposition with control. SIAM J. Appl. Dyn. Syst. 15, 142–161. doi:10.1137/15m1013857
Rothemund, P., Kellaris, N., Mitchell, S. K., Acome, E., and Keplinger, C. (2021). HASEL artificial muscles for a new generation of lifelike robots—recent progress and future opportunities. Adv. Mater. 33, 2003375. doi:10.1002/adma.202003375
Rothemund, P., Kirkman, S., and Keplinger, C. (2020). Dynamics of electrohydraulic soft actuators. Proc. Natl. Acad. Sci. 117, 16207–16213. doi:10.1073/pnas.2006596117
Rus, D., and Tolley, M. T. (2015). Design, fabrication and control of soft robots. Nature 521, 467–475. doi:10.1038/nature14543
Schunk, C., Pearson, L., Acome, E., Morrissey, T. G., Correll, N., Keplinger, C., et al. (2018). “System identification and closed-loop control of a hydraulically amplified self-healing electrostatic (HASEL) actuator,” in 2018 IEEE/RSJ international conference on intelligent robots and systems (IROS), 6417–6423. doi:10.1109/IROS.2018.8593797
Skogestad, S., and Postlethwaite, I. (2005). Multivariable feedback control: analysis and design. Wiley.
Smerlas, A., Walker, D., Postlethwaite, I., Strange, M., Howitt, J., and Gubbels, A. (2001). Evaluating H∞ controllers on the NRC Bell 205 fly-by-wire helicopter. Control Eng. Pract. 9, 1–10. doi:10.1016/s0967-0661(00)00088-5
Sundaram, V., Ly, K., Johnson, B. K., Naris, M., Anderson, M. P., Humbert, J. S., et al. (2023). Embedded magnetic sensing for feedback control of soft HASEL actuators. IEEE Trans. Robotics 39, 808–822. doi:10.1109/TRO.2022.3200164
Thuruthel, T. G., Ansari, Y., Falotico, E., and Laschi, C. (2018). Control strategies for soft robotic manipulators: a survey. Soft Robot. 5, 149–163. doi:10.1089/soro.2017.0007
Tu, J. H., Rowley, C. W., Luchtenburg, D. M., Brunton, S. L., and Kutz, J. N. (2014). On dynamic mode decomposition: theory and applications. J. Comput. Dyn. 1, 391–421. doi:10.3934/jcd.2014.1.391
Volchko, A., Mitchell, S. K., Morrissey, T. G., and Humbert, J. S. (2022). “Model-based data-driven system identification and controller synthesis framework for precise control of SISO and MISO HASEL-powered robotic systems,” in 2022 IEEE 5th international conference on soft robotics (RoboSoft), 209–216. doi:10.1109/RoboSoft54090.2022.9762220
Walker, J., Zidek, T., Harbel, C., Yoon, S., Strickland, F. S., Kumar, S., et al. (2020). Soft robotics: a review of recent developments of pneumatic soft actuators. Actuators 9, 3. doi:10.3390/act9010003
Wang, T., Joo, H.-J., Song, S., Hu, W., Keplinger, C., and Sitti, M. (2023). A versatile jellyfish-like robotic platform for effective underwater propulsion and manipulation. Sci. Adv. 9, eadg0292. doi:10.1126/sciadv.adg0292
Zhang, H., Zhou, Y., Dai, M., and Zhang, Z. (2018). A novel flying robot system driven by dielectric elastomer balloon actuators. J. Intelligent Material Syst. Struct. 29, 2522–2527. doi:10.1177/1045389X18770879
Keywords: robust control, soft robotics, linear system theory, H infinity synthesis, uncertainty analysis, HASEL actuators
Citation: Volchko A, Mitchell SK, Scripps TG, Turin Z and Humbert JS (2024) Robust control of electrohydraulic soft robots. Front. Robot. AI 11:1333837. doi: 10.3389/frobt.2024.1333837
Received: 06 November 2023; Accepted: 17 June 2024;
Published: 02 August 2024.
Edited by:
Concepción A. Monje, Universidad Carlos III de Madrid, SpainReviewed by:
Jakub Bernat, Poznań University of Technology, PolandManmatha Mahato, Korea Advanced Institute of Science and Technology (KAIST), Republic of Korea
Copyright © 2024 Volchko, Mitchell, Scripps, Turin and Humbert. This is an open-access article distributed under the terms of the Creative Commons Attribution License (CC BY). The use, distribution or reproduction in other forums is permitted, provided the original author(s) and the copyright owner(s) are credited and that the original publication in this journal is cited, in accordance with accepted academic practice. No use, distribution or reproduction is permitted which does not comply with these terms.
*Correspondence: Angella Volchko, QW5nZWxsYS5Wb2xjaGtvQENvbG9yYWRvLmVkdQ==