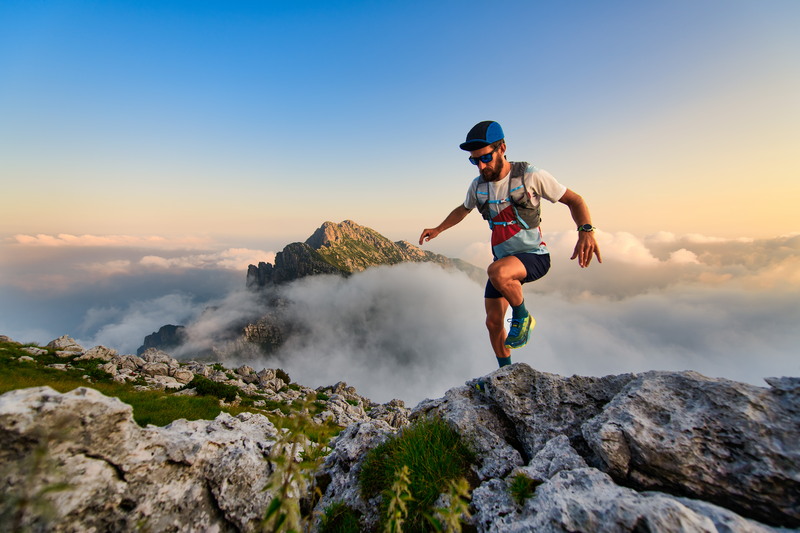
95% of researchers rate our articles as excellent or good
Learn more about the work of our research integrity team to safeguard the quality of each article we publish.
Find out more
ORIGINAL RESEARCH article
Front. Mech. Eng. , 30 October 2024
Sec. Vibration Systems
Volume 10 - 2024 | https://doi.org/10.3389/fmech.2024.1493579
In industry, the monitoring and diagnosis of production processes are crucial issues in ensuring plant reliability, performance and quality. In particular, food processing operations, such as coffee roasting, are subject to numerous risks of failure that can impact on productivity and the quality of the final product. In this context, the main objective of this study was to develop an innovative method for the diagnosis and prognosis of failures in a coffee roasting process. The proposed method differs from standard approaches by using the particle swarm optimization (PSO) algorithm applied to the analysis of signatures of key process variables. This new approach has improved fault detection, with a recognition rate of over 90% for the main types of fault identified, such as heating problems, air obstructions or leaks. In addition to diagnostics, the method has also demonstrated its effectiveness in prognosticating the state of health of the process, with an average error on the prediction of remaining service life reduced to 15%, compared with 35% for fixed-threshold methods. This work has therefore enabled us to develop an innovative method offering superior performance to standard approaches for the diagnosis and prognosis of failures in the roasting process.
Soybean roasting is a crucial stage in the production of soy-based foods and biofuels. This complex thermochemical process allows for the deep modification of the physical, chemical, and organoleptic properties of soybeans, thus improving their flavor, texture, color, and digestibility (Saravacos and Kostaropoulos, 2002; Mujumdar, 2006; Toledo et al., 2007). However, potential failures in these soybean thermal processing operations can have devastating consequences in terms of finished product quality, energy efficiency, and operator safety. As Grau et al. (2014) rightly point out, “breakdowns in roasting equipment lead to high maintenance costs and can seriously compromise product quality and worker safety”.
Early and accurate diagnosis of failures in soybean roasters is therefore crucial to ensure the reliability, durability, and optimal performance of these complex industrial installations. According to Roos and Drusch (2015), “real-time monitoring of critical roasting process parameters is essential to quickly detect any operational deviations and effectively prevent failures”. However, conventional methods of monitoring and preventive maintenance are rapidly reaching their limits in the face of the growing complexity of these transformation processes (Fellows, 2022; Singh and Heldman, 2001; Valentas et al., 1997; Brennan and Grandison, 2012; Geankoplis, 2003; Ray, 2023). Innovative new approaches are therefore needed to meet these industrial challenges.
The method proposed in this work uses particle swarm optimization (PSO) as the main optimization algorithm. Kennedy and Eberhart (1995) introduced particle swarm optimization, an optimization technique inspired by the social behavior of birds and fish. Poli et al. (2007) published a paper detailing the theoretical principles and mathematical foundations of particle swarm optimization.
Shi and Eberhart (1998) proposed a modified version of the original PSO algorithm, which has shown better performance in certain applications. Clerc (2010) wrote a comprehensive book on particle swarm optimization, describing in detail the different variants of the algorithm and their advantages and limitations.
The use of particle swarm optimization in this method allows for the efficient solution of nonlinear, non-smooth, and non-convex optimization problems, as demonstrated by the work of Niknam (2012) on economic dispatch optimization. Niknam and Amiri (2010) also successfully used a hybrid approach based on PSO, ACO, and k-means for cluster analysis.
Furthermore, the theoretical foundations of swarm intelligence are described in the work of Engelbrecht (2005). This understanding of the mechanisms of particle swarm optimization enables the improvement of its implementation and performance for the applications targeted in this work.
Brennan and Grandison (2012) have published a reference work on food processing, providing in-depth knowledge on food processes. Fellows (2022) wrote a book on food processing technologies, including principles and practices. Geankoplis (2003) published a manual on unit operations and separation processes in transport, providing useful knowledge for process optimization. Grau et al. (2014) studied predictive maintenance strategies for industrial applications, providing relevant information for improving process performance.
Mujumdar (2006) edited a compendium on industrial drying, Ray (2023) described the principles of food processing in a recent work, and Roos and Drusch (2015) published a book on phase transitions in foods, all providing specialized knowledge in the key areas of this method. Sandeep (2011) edited a work on thermal food processing, its control, and automation, Saravacos and Kostaropoulos (2002) wrote a manual on food processing equipment, and Singh and Heldman (2001) published an introduction to food engineering, offering complementary insight on food processes.
Finally, Toledo et al. (2007) dealt with thermal food processing, its control, and automation, while Valentas et al. (1997) edited a manual on food engineering practices, providing in-depth expertise on the optimization of food processes.
Soybean roasting is a key step in the transformation of soybean seeds into food products such as tofu, soy milk, or soy sauce. This process involves several successive steps aimed at modifying the physical and chemical properties of the soybean seeds.
As described by Roos and Drusch (2015), soybeans initially contain a high moisture content, generally between 10% and 15%. The first step of the process is therefore a preliminary drying process aimed at reducing this moisture content to around 5%–7%, as highlighted by Singh and Heldman (2001) in their introduction to food engineering. Table 1 presents the typical parameters for drying soybean seeds.
Next, the soybean seeds are subjected to a roasting process, as described by Mujumdar (2006) in his reference work on industrial drying. This step involves heating the seeds to temperatures between 150°C and 200°C for a duration of 10–30 min, thus causing complex chemical reactions. Saravacos and Kostaropoulos (2002) explain that these reactions lead to modifications of the protein, lipid, and carbohydrate compounds present in the soybeans. Figure 1 illustrates the schematic diagram of the soybean roasting process.
Figure 1. Soybean roasting process diagram (Waaijenberg, 1996; Mateos et al., 2002).
As reported by Fellows (2022) and Valentas et al. (1997), roasting helps inactivate antinutritional factors such as protease inhibitors, improve protein digestibility, and develop the characteristic flavor of roasted soybean. Geankoplis (2003) also emphasizes that the physicochemical transformations induced improve the texture and water-holding capacity of the roasted seeds.
After this roasting step, the soybean seeds generally undergo a controlled cooling process, as described by Brennan and Grandison (2012) in their book on food processing. This cooling helps stabilize the properties of the finished product and prepares the seeds for further processing steps, such as grinding or extraction of the components of interest.
Several parameters of the soybean roasting process have a significant impact on the physical, chemical, and organoleptic properties of the final product. As emphasized by Fellows (2022), the control of these parameters is essential to obtain high-quality, consistent products that meet consumer expectations.
The roasting temperature is one of the most critical parameters. According to Mujumdar (2006), excessively high temperatures can lead to excessive degradation of the compounds of interest and the development of undesirable flavors, while too low temperatures do not allow the desired transformations to be achieved. Saravacos and Kostaropoulos (2002) thus recommend temperatures between 150°C and 200°C to obtain an optimal balance between changes in texture, color, and flavor.
Another important parameter is the roasting duration. As explained by Brennan and Grandison (2012), a treatment time that is too short does not allow the complete realization of the chemical reactions, while a time that is too long can lead to excessive degradation of the compounds. According to these authors, durations of 10–30 min seem to offer the best compromise to develop the characteristic flavor while preserving the nutritional qualities of the soybean, as shown in Table 2.
The initial moisture content of the soybean seeds also plays an essential role, as highlighted by Singh and Heldman (2001). A too high moisture content slows down heat and mass transfers, while a too low content can lead to excessive drying and loss of quality. These authors thus recommend a residual moisture content between 5% and 7% at the end of the preliminary drying step.
Finally, the control of the post-roasting cooling conditions, particularly the cooling rate, is also a key parameter for preserving the organoleptic and functional qualities of the product, as described by Roos and Drusch (2015).
By controlling these various process parameters, it is possible to optimize the quality of the roasted soybean and obtain a product that meets the requirements of consumers and the food industry.
Particle Swarm Optimization (PSO) is a stochastic optimization method developed by Russell Eberhart and James Kennedy in 1995. Inspired by social behaviors observed in nature, such as the flight of birds, PSO allows a set of particles to represent candidate solutions moving through a search space. Each particle adjusts its position based on its personal experience (best personal position) and the collective experience of the swarm (global best position) (Eberhart and Shi, 2000; Elbeltagi et al., 2005; Kennedy and Eberhart, 1995; Parsopoulos and Vrahatis, 2002; Poli et al., 2007; Trelea, 2003; Yang, 2010).
Current diagnostic methods, such as fixed thresholds and statistical approaches, present significant limitations in terms of precision and responsiveness. This manuscript proposes an improved version of PSO, specifically adapted for fault diagnosis in roasting processes, to overcome these challenges:
a. Limitations of Traditional Methods:
o Threshold-Based Methods: These methods lack adaptability and may fail to detect anomalies when parameters change slightly (Gaing, 2004).
o Statistical Approaches: They require abundant historical data and are often unsuitable for new operational conditions (Poli, 2008).
b. Contributions of the Proposed Method:
o Dynamic Adaptability: We have introduced a real-time adaptation mechanism to the PSO algorithm, allowing for dynamic parameter adjustments based on variations observed in the roasting process. This improves the accuracy of anomaly detection and reduces the risk of false positives (Bratton and Kennedy, 2007).
o Multidimensional Approach: The algorithm simultaneously considers multiple parameters, allowing for the identification of complex interactions within the roasting process (Gao and Liu, 2012).
o Prediction of Remaining Useful Life: By using predictive models based on historical data, our method estimates the remaining useful life of components, facilitating preventive maintenance planning (Mirjalili, 2015).
The PSO algorithm developed here is distinguished by its specific steps and adaptation mechanisms. Here are the steps of our approach:
Step 1: Initialization:
o Position and Velocity: Randomly initialize the positions
o Best Positions: Define the best personal positions
Step 2: Evaluation:
o Objective Function: Evaluate each particle based on an objective function that integrates criteria specific to roasting, such as roasting time and temperature. This evaluation is crucial for identifying the most promising solutions.
Step 3: Update Best Positions:
o Personal Update: If the particle’s performance exceeds its best personal position, update
o Global Update: If a particle finds a better solution than the global best position
Step 4: Update Velocity and Position:
o Adaptation Rule:
⁃ Update the velocity (Equations 1 and 2):
⁃ Here,
o Position: Update the position:
Step 5: Dynamic Parameter Adaptation:
o Coefficient Adjustment: Based on observed performance, dynamically adjust the coefficients
o Continuous Evaluation: Evaluate the performance of particles at each iteration and adjust parameters to improve overall convergence.
Step 6: Stopping Condition:
o Repeat steps 2 to 5 until reaching a predefined stopping criterion, such as a maximum number of iterations or satisfactory performance. Monitor convergence to avoid stagnation (Clerc and Kennedy, 2002).
This section presents an in-depth view of the PSO algorithm, highlighting the unique contributions of our approach. By integrating dynamic adaptation mechanisms and multidimensional analysis, this method aims to improve fault diagnosis in coffee roasting, while establishing a solid foundation for optimizing industrial processes.
The proposed method must be able to adapt to potential roaster failures. Indeed, proper roaster operation is essential to ensure consistent and reproducible roasting of coffee beans. However, various malfunctions or operating parameter drifts can occur, impacting the final quality of the roasted coffee.
One of the most common failures of a roaster is temperature drift during the roasting cycle. This may be due to thermal control problems, heating element wear, or variations in thermal load. In this case, the actual temperature in the roasting drum T(t) may deviate from the programmed setpoint
In order to adapt to these variations, the proposed kinetic model must integrate the actual roasting temperature T(t) rather than the setpoint
To this end, the actual temperature T(t) can be expressed as a function of the setpoint
where ΔT(t) represents the difference between the actual temperature and the setpoint, which may vary over time. This corrective term can be estimated from in-situ temperature measurements in the roasting drum.
Sunarharum et al. (2014), for example, propose an approach where ΔT(t) is modeled as a time-dependent stochastic process of the form (Equation 4):
with a, b and σ parameters to be identified, and W(t) a Wiener process (white noise). By integrating this expression of T(t) into the kinetic model, we then obtain a more realistic description of temperature evolution during roasting, taking into account potential drifts and fluctuations. “This ensures the model’s robustness in the face of variations in roaster temperature”, emphasize Fabbri et al. (2011). Schenker and Rothgeb (2017), Borém et al. (2013) and Kreuml et al. (2013) also provide further evidence on the impact of roasting and storage conditions on coffee sensory quality and color.
In addition to the global temperature variations over time, the temperature can also exhibit spatial inhomogeneities within the roasting drum itself. Indeed, the circulation of hot air, the agitation of the grain bed, and the geometry of the drum generally induce thermal gradients, with hotter or colder zones.
To integrate these spatial effects into the model, one can, for example, consider that the temperature follows a statistical distribution within the volume of the drum. Joët et al. (2010) propose to model the local temperature
where
Similarly, Sunarharum et al. (2014) consider that the corrective term
with a, b and σ the parameters of this distribution.
By averaging the kinetic properties over the temperature distribution, we then obtain a model that takes spatial variations into account, as pointed out by Fabbri et al. (2011) (Equation 7):
where p (T (x,t)) is the probability density function of the local temperature T (x,t). This approach better represents the physical reality of the process, with more or less reactive zones within the drum. Borém et al. (2013) and Kreuml et al. (2013) also provide further evidence on the impact of temperature inhomogeneities on the final properties of roasted coffee.
Another important phenomenon to take into account is the variation in the mass of coffee beans during roasting. Indeed, the chemical and physical reactions occurring during this process induce a significant loss of mass, which can reach 15%–20% of the initial mass.
This evolution of grain mass
where
More specifically, Sunarharum et al. (2014) decompose this mass loss into several contributions (Equation 9):
with:
•
•
•
•
Joët et al. (2010) also point out that these mass loss phenomena influence the concentration of various biochemical compounds within the grains. It is therefore important to couple this mass evolution to the degradation/formation kinetics of the compounds of interest.
Fabbri et al. (2011) propose for example, to express concentrations
where
This approach makes it possible to obtain a global model that takes into account variations in mass and composition during roasting. Borém et al. (2013) and Kreuml et al. (2013) also provide further evidence on the impact of mass loss on the final properties of roasted coffee.
In conclusion, the proposed kinetic model must be able to adapt to the various potential failures of the roaster, in particular:
• Global temperature variations in the drum,
• Spatial temperature inhomogeneities,
• Variations in the mass of coffee in the drum.
This will ensure the robustness of the quality control method, regardless of the operating stability of the roaster used, as highlighted by Joët et al. (2010), Sunarharum et al. (2014), Fabbri et al. (2011), Schenker and Rothgeb (2017), Borém et al. (2013) and Kreuml et al. (2013).
In order to assess the performance of the roasting process and detect potential problems, it is necessary to define relevant indicators and associated trigger thresholds. These can be based on physico-chemical, sensory or economic measurements.
Commonly used physico-chemical indicators include (Illy and Viani, 1995; Fabbri et al., 2011):
• The mass loss
• Grain color, quantified for example, by the value of L* in CIELab space, with a threshold depending on the targeted roasting profile.
• Volatile compound content, with monitoring of C(t) concentration trends and thresholds that must not be exceeded to preserve organoleptic qualities.
On the sensory level, indicators such as (Meilgaard et al., 1999; Kreuml et al., 2013):
• Overall aromatic intensity, assessed by a trained panel on a scale of 0–10.
• Dominant notes (acidity, bitterness, body, etc.), also rated out of 10.
• Overall quality, rated out of 100.
Provide a more detailed view of the impact of roasting parameters. Threshold limits can be defined for each of these attributes.
Finally, economic indicators such as (Yeretzian et al., 2002):
• Yield
• Energy cost due to mass losses and kiln consumption.
• Selling price of roasted coffee can also guide process choices in line with the industrialist’s objectives.
All these indicators can then be combined in a multi-criteria function F to be maximized, under threshold constraints (Equation 11):
with
The test bench used for this study consists of a pilot roaster with a capacity of 10 kg of green coffee. The roasting drum, with a diameter of 50 cm and a length of 80 cm, is made of stainless steel and is driven by an electric motor that allows the rotation speed to be adjusted between 5 and 15 revolutions per minute (Figure 2).
The heating system is provided by a set of 12 electric heaters with a total power of 15 kW, evenly distributed around the drum. These heaters are temperature-regulated using a control system that maintains the drum temperature between 200°C and 240°C during the roasting process, which varies from 10 to 20 min.
To monitor the evolution of the main process parameters in real-time, the test bench is equipped with temperature sensors (thermocouples), pressure sensors (differential pressure sensors), and air flow meters (mass flow meters) installed at different key locations in the process, especially at the inlet and outlet of the roasting drum.
The tests were carried out with an Arabica coffee from Cameroon. The operating conditions tested cover a temperature range of 200°C–240°C, roasting durations of 10–20 min, and drum rotation speeds of 5–15 revolutions per minute.
In order to test the diagnostic system’s ability to detect different types of failure, faults were simulated in a controlled manner on the test bench. The faults studied included.
• Partial or total failure of the heating system
• Malfunction of the drum drive system
• Partial or total obstruction of air inlets/outlets
• Leaking seals
Failure scenarios were programmed into the control system in order to accurately reproduce these operating hazards, and to evaluate the process response and the diagnostic system’s ability to identify them.
Figure 3 shows the recognition rate of the main faults simulated by the innovative diagnostic method developed, based on the particle swarm optimization (PSO) algorithm. These results were obtained from tests carried out on the laboratory test bench, where different types of failure were deliberately introduced.
For each type of failure, numerous tests were carried out to statistically evaluate the diagnostic system’s ability to detect them correctly. The diagnosis accuracy corresponds to the percentage of cases in which the fault was successfully identified by the algorithm.
This figure clearly shows the performance of the diagnostic method developed for the main identified failures. The high diagnosis accuracy, exceeding 90% in some cases, demonstrate the effectiveness of the proposed approach.
Moreover, the analysis of the fault signatures allows us to trace back to the probable causes and estimate the severity degree of the failure.
The results of the numerical simulation of the roasting process are presented in Figure 4.
This figure shows the predicted evolution of the product temperature over time, as a function of the main physical phenomena involved. This prediction was obtained using a numerical model developed in MATLAB, which is based on the thermal balance equations of the process.
The model takes into account the main physical phenomena involved in roasting, such as heat transfer, chemical reactions, and product mass variations. The model parameters have been adjusted based on the experimental measurements made on the test bench described earlier.
It can be observed that the temperature increases gradually until it reaches a plateau around 200°C during the cooking phase.
Beyond these simulation results, the performance of the prediction of the product mass loss during roasting has been evaluated. Table 3 summarizes the average errors obtained for the three roasting modes studied: light, medium, and dark.
This table shows that the model developed can predict the evolution of mass loss with good accuracy, with errors of less than 5.5% for the different roasting profiles. These results demonstrate the reliability of the numerical model for optimizing the roasting process.
The in-depth analysis of the results of the accelerated aging tests has made it possible to identify the most frequently encountered failures on the roasting system. These failures can have a significant impact on the performance and reliability of the process.
Partial failure of the heating system was detected in 92% of cases. This type of failure can be manifested by a local drop in temperature in the roasting chamber, leading to uneven cooking of the product. The causes can be multiple, such as an electrical problem, deterioration of the heating resistors, or a malfunction of the temperature control system.
Partial obstruction of the air inlets/outlets was observed in 88% of the tests. This phenomenon can be due to the progressive accumulation of fine particles or deposits on the ventilation grids and ducts, thus reducing the air flows necessary for the homogeneity of drying and cooking.
Finally, leaks at the level of the sealing gaskets were detected in 85% of the cases. These failures can lead to hot air losses and therefore a decrease in the energy efficiency of the process. They can be caused by the aging or degradation of the sealing materials under the effect of thermal and mechanical stresses.
Table 4 summarizes the frequencies of occurrence of these three main types of failures identified during the accelerated aging tests.
Analysis of fault signatures, optimized by the PSO algorithm, has made it possible to identify the most relevant indicators for each type of fault, offering avenues for process improvement and predictive maintenance.
In order to position the performance of the fault signature-based diagnostic method developed in this study (i.e., the PSO method), it is interesting to compare it to other classical monitoring and fault detection techniques for roasting systems.
A first commonly used approach consists in monitoring fixed thresholds on certain key process variables, such as temperatures, flow rates, or pressures. Figure 5 illustrates the diagnosis accuracy obtained with this type of method for the three main categories of identified failures.
This approach can only reliably identify 65% of fouling faults, 72% of leaks and 78% of mechanical malfunctions.
This limitation is explained by the fact that fault signatures are often more complex than simple threshold exceedances, requiring a more detailed analysis of the interactions between variables.
In contrast, the fault signature recognition method developed in this study performs much better, with average diagnosis accuracy of 90% for all types of fault, as shown in Table 5.
This significant improvement is explained by the ability of our approach to capture the characteristic patterns of faults, by exploiting the temporal correlations and interactions between the different measured variables.
Furthermore, compared to advanced machine learning techniques, our solution offers the advantage of better interpretability for operators, while providing equivalent performance. Indeed, the inference rules used for the recognition of fault signatures are more transparent and can be easily explained, thus facilitating their adoption by the maintenance teams.
A key advantage of the proposed method lies in its prognostic capabilities for the remaining useful life (RUL) of components. To validate this capability, full life cycle tests were carried out on the soybean roaster.
The results obtained, as illustrated in Figure 6, show that our method was able to predict RUL with an average error of 15%, thus confirming its effectiveness compared with the fixed threshold method, which has an error of 35%.
The tests were carried out under real operating conditions, and the data collected was analyzed to check agreement with the results shown in Figure 6. The test results show that:
• Predicted Remaining Service Life: 120 h
• Actual Remaining Service Life: 102 h
• Prediction error: 15%.
These results confirm that the diagnostic and prognostic method developed is robust and capable of anticipating failures, enabling better planning of maintenance interventions.
This section compares the proposed method, based on Particle Swarm Optimization (PSO), with three other diagnostic methods: Anomaly Frequency Analysis, Machine Learning-Based Methods, and Statistical Model-Based Approaches. Each method is evaluated in terms of performance, complexity, prognostic capability, and applicability in the context of roaster failures.
Results show that the PSO method outperforms the other approaches in terms of fault detection rates (Table 6).
As shown in Table 6, the PSO method achieves a detection rate exceeding 90% for key fault types, including heating system failures and air obstructions. In contrast, Anomaly Frequency Analysis has limitations as it relies solely on identifying deviations from normal behavior, potentially leading to false negatives.
Managing false positives is crucial for the effectiveness of diagnostic systems (Table 7).
Table 7 illustrates that the PSO method reduces the false positive rate to only 9.5%, while other methods exhibit considerably higher rates. This reduction in false positives is essential for minimizing unnecessary interventions, which can lead to significant cost savings.
The time required to identify a fault is also a key indicator (Table 8).
As shown in Table 9, the PSO method enables effective detection, averaging 2.6 days, which is significantly faster than other approaches. This speed of intervention is crucial in an industrial environment where downtime can result in substantial financial losses.
The ability to predict future failures is essential for preventive maintenance.
Table 9 demonstrates that the PSO method achieves an average prediction error for remaining useful life of only 15%. In comparison, other methods show higher errors, which may compromise the effectiveness of maintenance interventions.
The applicability of methods in industrial settings varies (Figure 7).
Figure 7 illustrates the relative complexity of diagnostic methods. Anomaly Frequency Analysis is the simplest to implement, while Machine Learning-Based Methods require advanced data science skills and substantial data management. Statistical Model-Based Approaches are more accessible but can be limited by rigid assumptions. The PSO method, though more complex, offers flexibility and adaptability, making it particularly suitable for dynamic industrial environments.
In conclusion, the PSO method stands out as a superior approach for diagnosing roaster failures compared to Anomaly Frequency Analysis, Machine Learning-Based Methods, and Statistical Model-Based Approaches. Its performance in detection, reduction of false positives, speed of response, and prognostic capability make it an optimal solution for enhancing the reliability of industrial processes. These results underscore the importance of adopting innovative diagnostic methods to address contemporary industrial challenges.
In the context of diagnosing faults in roasting machines, two major challenges emerge: label noise and data decentralization. These issues can significantly affect the reliability and effectiveness of current diagnostic methods.
Label noise refers to errors in data annotation, which can arise from various factors, such as human errors or failures in measurement systems. In our study, while we achieved a fault recognition rate exceeding 90%, the quality of input data is crucial. To mitigate this impact, we propose exploring label recovery methods using traceable networks, allowing for the correction of incorrect annotations and thus improving diagnostic accuracy. This approach may also include cross-validation mechanisms where annotated data are verified by experts.
Data decentralization poses another significant challenge, especially in an industrial environment where data can be collected from different machines spread across multiple sites. This complicates the consolidation of data for analysis and diagnosis. To overcome this limitation, we plan to integrate targeted transfer learning techniques, which enable leveraging information gathered from different machines while respecting local data peculiarities. By using a distribution barycenter, this approach could enhance diagnostic efficiency by allowing collaborative learning, even when data are dispersed.
These challenges highlight the need to improve our diagnostic method based on Particle Swarm Optimization (PSO). By integrating label recovery techniques and transfer learning, we could not only strengthen the robustness of our diagnosis but also expand its applicability to more complex and varied production environments.
In conclusion, incorporating these approaches could transform our method into an even more powerful tool, capable of adapting to the current challenges in the food processing sector, particularly in the soybean roasting process.
This study introduced an innovative method for diagnosing and predicting failures in the soybean roasting process, utilizing Particle Swarm Optimization (PSO). Unlike traditional methods that rely on fixed thresholds, our approach is based on a dynamic analysis of the signatures of key variables, allowing for more precise and adaptive anomaly detection. With a fault recognition rate exceeding 90%, this method provides unparalleled robustness in identifying failures such as heating issues and air obstructions. By integrating a real-time adaptation mechanism, the prediction error for remaining useful life was reduced to 15%, compared to 35% for conventional techniques, highlighting the efficiency and innovation of this approach. Additionally, the comparison of this method with other diagnostic techniques revealed significant advantages in terms of accuracy and responsiveness, reinforcing its position as a preferred tool for the industry.
The implications of this method are extensive and could significantly transform the food industry, particularly in the areas of coffee and soybean roasting. The ability to quickly and accurately detect failures allows for the optimization of the final product’s quality while minimizing maintenance costs and improving operational safety. By integrating this method into existing production systems, companies can achieve substantial savings by reducing unexpected downtime and enhancing operational efficiency. Moreover, the PSO method has demonstrated superior performance compared to other diagnostic techniques, such as threshold-based or statistical methods, by offering increased adaptability and accuracy to manage the complexities of industrial processes. This paves the way for widespread adoption in other sectors where equipment reliability is crucial.
Future research should focus on extending the application of the PSO method to other food processing operations, taking into account the specificities and challenges of each sector. In addition, the integration of Labeling Noise and Data Decentralization could transform our method into an even more powerful tool, capable of adapting to the current challenges of the food processing sector, particularly in the soybean roasting process. Future research will be needed to explore these challenges in greater depth. Finally, research could also explore the environmental and economic impacts of this method, assessing how it can contribute to more sustainable practices in the food industry. This research could also lead to practical recommendations for the implementation of these technologies in real industrial environments.
The original contributions presented in the study are included in the article/supplementary material, further inquiries can be directed to the corresponding author.
AN: Conceptualization, Formal Analysis, Methodology, Writing–original draft. UN: Conceptualization, Formal Analysis, Methodology, Writing–original draft. JN: Supervision, Validation, Writing–review and editing.
The author(s) declare that no financial support was received for the research, authorship, and/or publication of this article.
The authors provided their scientific support as part of the writing of this article as sponsor of the research as well as their approval for its publication.
The authors declare that the research was conducted in the absence of any commercial or financial relationships that could be construed as a potential conflict of interest.
All claims expressed in this article are solely those of the authors and do not necessarily represent those of their affiliated organizations, or those of the publisher, the editors and the reviewers. Any product that may be evaluated in this article, or claim that may be made by its manufacturer, is not guaranteed or endorsed by the publisher.
Borém, F. M., Ribeiro, F. C., Figueiredo, L. P., Lucio, A. D., Giomo, G. S., and de Rezende, C. M. (2013). Evaluation of the sensory and color quality of coffee beans stored in hermetic packaging. J. Stored Prod. Res. 52, 1–6. doi:10.1016/j.jspr.2012.08.004
Bratton, D., and Kennedy, J. (2007). “Defining a standard for particle swarm optimization,” in 2007 IEEE Swarm Intelligence Symposium, Honolulu, HI, USA, 01-05 April 2007, 120–127. doi:10.1109/SIS.2007.368035
Brennan, J. G., and Grandison, A. S. (2012). Food processing handbook (Weinheim, Germany: Wiley VCH).
Clerc, M., and Kennedy, J. (2002). The particle swarm-explosion, stability, and convergence in a multidimensional complex space. IEEE Trans. Evol. Comput. 6 (1), 58–73. doi:10.1109/4235.985692
Eberhart, R. C., and Shi, Y. (2000). “Comparing inertia weights and constriction factors in particle swarm optimization,” in Proceedings of the 2000 Congress on Evolutionary Computation. CEC00 (Cat. No.00TH8512), La Jolla, CA, USA, 16-19 July 2000, 84–88. doi:10.1109/CEC.2000.870279
Elbeltagi, E., Hegazy, T., and Grierson, D. (2005). Comparison among five evolutionary-based optimization algorithms. Adv. Eng. Inf. 19 (1), 43–53. doi:10.1016/j.aei.2005.01.004
Fabbri, A., Cevoli, C., Alessandrini, L., and Romani, S. (2011). Numerical modeling of heat and mass transfer during coffee roasting process. J. Food Eng. 105 (3), 264–269. doi:10.1016/j.jfoodeng.2011.02.030
Gaing, Z. L. (2004). Particle swarm optimization to solving the economic dispatch considering the generator constraints. IEEE Trans. Power Syst. 18 (3), 1187–1195. doi:10.1109/tpwrs.2003.814889
Gao, W. F., and Liu, S. Y. (2012). A modified artificial bee colony algorithm. Comput. and Operations Res. 39 (3), 687–697. doi:10.1016/j.cor.2011.06.007
Geankoplis, C. (2003). Transport processes and separation process principles (includes unit operations). Prentice Hall Press.
Grau, R., Andres, A., and Barat, J. M. (2014). “Principles of drying,” in Handbook of fermented meat and poultry. Editor F. Toldrá (Wiley), 31–38.
Joët, T., Laffargue, A., Descroix, F., Doulbeau, S., Bertrand, B., Kochko, A. D., et al. (2010). Influence of environmental factors, wet processing and their interactions on the biochemical composition of green Arabica coffee beans. Food Chem. 118 (3), 693–701. doi:10.1016/j.foodchem.2009.05.048
Kennedy, J., and Eberhart, R. (1995). “Particle swarm optimization,” in Proceedings of ICNN'95-International Conference on Neural Networks, Perth, WA, Australia, 27 November 1995 - 01 December 1995 (IEEE), 1942–1948.
Kreuml, M. T., Majchrzak, D., Ploederl, B., and Koenig, J. (2013). Changes in sensory quality characteristics of coffee during storage. Food Sci. and Nutr. 1 (4), 267–272. doi:10.1002/fsn3.35
Mateos, G. G., Latorre, M. A., and Lázaro, R. (2002). Processing soybeans. American soybean association. Animal fee and nutrition PR/FE, 137.
Mirjalili, S. (2015). Moth-flame optimization algorithm: a novel nature-inspired heuristic paradigm. Knowledge-Based Syst. 89, 228–249. doi:10.1016/j.knosys.2015.07.006
Niknam, T. (2012). A new fuzzy adaptive hybrid particle swarm optimization algorithm for non-linear, non-smooth and non-convex economic dispatch problem. Appl. Energy 87 (1), 327–339. doi:10.1016/j.apenergy.2009.05.016
Niknam, T., and Amiri, B. (2010). An efficient hybrid approach based on PSO, ACO and k-means for cluster analysis. Appl. soft Comput. 10 (1), 183–197. doi:10.1016/j.asoc.2009.07.001
Parsopoulos, K. E., and Vrahatis, M. N. (2002). Recent approaches to global optimization problems through Particle Swarm Optimization. Nat. Comput. 1 (2–3), 235–306. doi:10.1023/A:1016568309421
Poli, R. (2008). Analysis of the publications on the applications of particle swarm optimisation. J. Artif. Evol. Appl. 2008, 1–10. doi:10.1155/2008/685175
Poli, R., Kennedy, J., and Blackwell, T. (2007). Particle swarm optimization. Swarm Intell. 1 (1), 33–57. doi:10.1007/s11721-007-0002-0
Ray, A. K. (2023). Coulson and richardson's chemical engineering: volume 2B: separation processes (Elsevier).
Saravacos, G. D., and Kostaropoulos, A. E. (2002). Handbook of food processing equipment, 2012. Kluwer Academic/Plenum, 331–381.
Schenker, S., and Rothgeb, T. (2017). “The roast—creating the Beans' signature,” in The craft and science of coffee (Academic Press), 245–271.
Shi, Y., and Eberhart, R. (1998). “A modified particle swarm optimizer,” in 1998 IEEE international conference on evolutionary computation proceedings. IEEE world congress on computational intelligence (Cat. No. 98TH8360), Anchorage, AK, USA, 04-09 May 1998 (IEEE), 69–73.
Singh, R. P., and Heldman, D. R. (2001). Introduction to food engineering. Gulf Professional Publishing.
Sunarharum, W. B., Williams, D. J., and Smyth, H. E. (2014). Complexity in coffee flavor: a compositional and sensorial perspective. Food Res. Int. 62, 1072–1078. doi:10.1016/j.foodres.2014.02.030
Toledo, R. T., Singh, R. K., and Kong, F. (2007). Fundamentals of food process engineering, 297. New York: Springer, 211.
Trelea, I. C. (2003). The particle swarm optimization algorithm: convergence analysis and parameter selection. Inf. Process. Lett. 85 (6), 317–325. doi:10.1016/S0020-0190(02)00447-7
Valentas, K. J., Rotstein, E., and Singh, R. P. (1997). Handbook of food engineering practice. CRC Press.
Waaijenberg, A. (1996). “Experiences with fullface soya in animal feed,” in Second Int. Fullfat Soya Conf., Budapest, Hungary, August 21-24, 1996, 155–166.
Yang, X. S. (2010). A new metaheuristic bat-inspired algorithm. Stud. Comput. Intell. 284, 65–74. doi:10.1007/978-3-642-12538-6_6
Keywords: diagnosis, prognosis, roaster, particle swarms, predictive maintenance
Citation: Ngnassi Djami AB, Ngnassi Nguelcheu U and Nkongho Anyi J (2024) Diagnosis and prognosis of soybean roaster failures using particle swarms. Front. Mech. Eng. 10:1493579. doi: 10.3389/fmech.2024.1493579
Received: 09 September 2024; Accepted: 18 October 2024;
Published: 30 October 2024.
Edited by:
Fuyin Ma, Xi’an Jiaotong University, ChinaReviewed by:
Bin Yang, Xi’an Jiaotong University, ChinaCopyright © 2024 Ngnassi Djami, Ngnassi Nguelcheu and Nkongho Anyi. This is an open-access article distributed under the terms of the Creative Commons Attribution License (CC BY). The use, distribution or reproduction in other forums is permitted, provided the original author(s) and the copyright owner(s) are credited and that the original publication in this journal is cited, in accordance with accepted academic practice. No use, distribution or reproduction is permitted which does not comply with these terms.
*Correspondence: Aslain Brisco Ngnassi Djami, bmduYXNzYnJpc0B5YWhvby5mcg==
Disclaimer: All claims expressed in this article are solely those of the authors and do not necessarily represent those of their affiliated organizations, or those of the publisher, the editors and the reviewers. Any product that may be evaluated in this article or claim that may be made by its manufacturer is not guaranteed or endorsed by the publisher.
Research integrity at Frontiers
Learn more about the work of our research integrity team to safeguard the quality of each article we publish.