- 1Department of Automotive and Marine Engineering Technology, Public Authority for Applied Education and Training, Kuwait City, Kuwait
- 2Department of Manufacturing Engineering Technology, The Public Authority for Applied Education and Training, Kuwait City, Kuwait
- 3Department of Civil Engineering, Engineering College, University of Anbar, Ramadi, Iraq
- 4Faculty of Health, Engineering and Sciences, The University Southern Queensland, QLD, Toowoomba, Australia
This study investigates the potential use of waste ceramic powder as a filler in concrete. Different percentages of waste ceramic powder were added to the concrete, and the compressive strength and water absorption properties were assessed. Failure mechanisms were analyzed using scanning electron microscopy (SEM). The findings revealed that incorporating 5% ceramic powder into concrete increased its compressive strength by approximately 12.5%. However, adding more than 5% ceramic powder led to a proportional decrease in strength. Additionally, water absorption increased when the ceramic content exceeded 5%. SEM analysis showed that higher ceramic content weakened the adhesion of the ceramic particles, and noticeable aggregation was observed.
1 Introduction
Disposal of waste materials is rapidly increasing (Brekailo et al., 2022), with most of the more than 200 million tons of waste materials produced in the United States going into landfill. In Australia, total waste management will reach more than ten million tons in the coming years in Adelaide alone. Therefore, new technology should be explored to utilize different waste material components as alternatives, substitutes, cores, and/or fillers. This would contribute to the reduction of materials being disposed of. Concrete materials are very consumable and can incorporate some additives from different resources (Table 1). Much research on this has been reported. Table 1 summarizes the studies on the use of various alternative fillers in concrete. In general, the materials explored in the literature seemed to be promising. Ceramic waste can be another potential additive in concrete; it can be divided into two categories—generated fired ceramic waste (brick, blocks, and roof tiles) and fired ceramic waste (wall, floor tiles, and sanitary ware) (Pacheco-Torgal and Jalali, 2010; Abou Rachied et al., 2023). The chemical composition of fired ceramic products is unremarkably different from the raw materials used to make the products. Crushing ceramic waste can generate coarse aggregates, fine aggregates, and ceramic powder, which can be used without additional processing. Much research has been done on using waste ceramic as aggregate in concrete (Kannan et al., 2017a; Kore Sudarshan and Vyas, 2019; Zegardło et al., 2016; Mir et al., 2022). However, waste ceramic in powder form has not been comprehensively explored as a potential filler in concrete. There is, though, a growing interest in using waste ceramics in buildings to incorporate ceramic powder in concrete rather than as aggregates (Li et al., 2020; Magbool, 2022; El-Dieb and Kanaan, 2018).
In recent years, there has been increasing interest in utilizing various waste materials as fillers in concrete to promote sustainable construction. Fly ash, for instance, has been extensively studied for its pozzolanic properties which enhance the strength and durability of concrete. However, with higher fly ash content, challenges such as increased brittleness and reduced water absorption have been reported, limiting its use in certain applications. Puthipad et al. (2017) and Golewski (2018) suggest that while fly ash can improve certain properties, its effect on the interfacial transition zone (ITZ) and water permeability can be detrimental to the overall performance of the concrete mixture. Similarly, recycled glass has been investigated as a filler, offering advantages such as improved sustainability and mechanical strength. However, concerns over alkali–silica reactions (ASR) can affect the long-term durability of concrete when using recycled glass as a filler. Saribiyik and Caglar (2016) and Mansour et al. (2023) have highlighted the limitations of recycled glass in concrete, particularly regarding crack initiation and the potential for internal reactions. In contrast, waste ceramic powder, as investigated in this study, shows promise as a sustainable filler due to its finer particle size, which allows for better dispersion within the concrete matrix. Compared to fly ash and recycled glass, ceramic powder appears to improve mechanical strength at lower inclusion rates without the adverse effects of ASR or significant brittleness. This study builds upon previous research by focusing on the powder form of ceramic waste, offering a unique contribution to the field of sustainable materials science.
Previous studies have extensively explored the use of ceramic waste in concrete, with a primary focus on using ceramic fragments as coarse or fine aggregates. These studies generally show mixed results, with higher ceramic aggregate content often leading to reduced mechanical strength due to issues such as poor interfacial bonding and increased porosity. However, the potential of ceramic waste in powder form as a filler remains underexplored. Unlike aggregates, ceramic powder offers a finer particle size, allowing for better dispersion within the concrete matrix and potentially leading to improved mechanical properties at lower inclusion rates. We here investigate the use of ceramic powder as a filler, focusing on its impact on the compressive strength and water absorption properties of concrete. This study represents a novel approach to utilizing waste ceramics by focusing on the powdered form which provides a more homogeneous mix and better particle–cement interaction. By optimizing the proportion of ceramic powder in the concrete mix, this study offers new insights into sustainable materials science and contributes to a circular economy by reducing the environmental burden of ceramic waste.
2 Sample preparation and experimental procedure
The material selected for this study is Portland cement supplied by Bunnings’s Warehouse in Toowoomba. The sand was also purchased from there. The ceramic powder was prepared at the lab and was ground using a ball mill to reduce the particle size and ensure a finer powder suitable for use as a filler. The ceramic powder had a particle size distribution ranging from 10 µm to 100 μm, with a median particle size (d50) of approximately 50 µm. The particle size distribution was measured using a laser particle size analyzer. The ceramic powder’s chemical composition comprised SiO2 at approximately 65% (±1%), around 3% CaO (±0.5%), 18% Al2O3 (±0.3%), 3% Fe2O3 (±0.4%), 3% MgO (±0.3%), and 3% K2O (±0.2%).
Various percentages of ceramic powder were selected to investigate its effect on the compressive strength and water absorption mechanical properties of concrete. The chosen ceramic content levels—5%, 15%, 25%, 35%, and 45% by weight of cement—were based on a combination of insights from previous studies (Frías et al., 2021; de Castro Carvalho et al., 2024; Ergenç et al., 2020; Matias et al., 2014) and the need to examine a wide range of concentrations to understand the performance limits of ceramic powder as a filler. The decision to start with 5% ceramic powder content was guided by findings from existing research on similar materials, such as fly ash and ceramic aggregates, which demonstrated that low filler content often leads to improvements in mechanical properties (Vieira et al., 2020). Lower filler concentrations typically result in better integration within the cement matrix, enhancing bonding and reducing the likelihood of voids or cracks. Therefore, 5% was selected as a baseline to assess whether similar benefits could be achieved with ceramic powder, particularly given its finer particle size than aggregates.
Higher ceramic powder contents of 15%, 25%, 35%, and 45% were chosen to systematically explore the effect of increasing filler concentration. These increments were to monitor the transition from improved mechanical performance at lower content levels to the potential deterioration of properties as filler content increases. This approach is consistent with studies on other waste materials, such as recycled glass and plastic powder, which show that high filler content can reduce concrete strength due to poor dispersion and increased porosity (John et al., 2018). The increments of approximately 10% were chosen to provide meaningful differences between test samples without making the variation too granular, which might have obscured significant trends. These percentage levels strike a balance between capturing detailed data across a broad spectrum and maintaining practicality in material preparation and testing.
A weight scale was used to calculate the required amount of all the ingredients at an accuracy of ±0.1 mg. The prepared cement, water, and ceramics mixture was carefully poured into the cylinder mold (Figure 1). The samples were left for 7 days and then removed from the mold. There were three samples for each set of experiments and 7- and 14-days curing time. The samples dimensions were 150 mm × 300 mm according to standard ASTM C39. The samples were removed and water absorption was determined, as explained next.
2.1 Experimental procedure
An MTS 810 Universal Testing Machine A6 with a capacity of 100 kN, Servo Hydraulic, and Dynamic was used to perform compressive testing. The machine can perform tensile, compressive, flexural, and dynamic loading under static and dynamic conditions (Figure 2). Three samples were tested per set following ASTM C39, and the average was determined. The samples were placed between the two compressive plates in the experiments, as shown in the figure. The feeding rate was 2 mm/min. During the experiments, the samples were monitored using an imager to gain information, which may help in understanding the experimental data later.
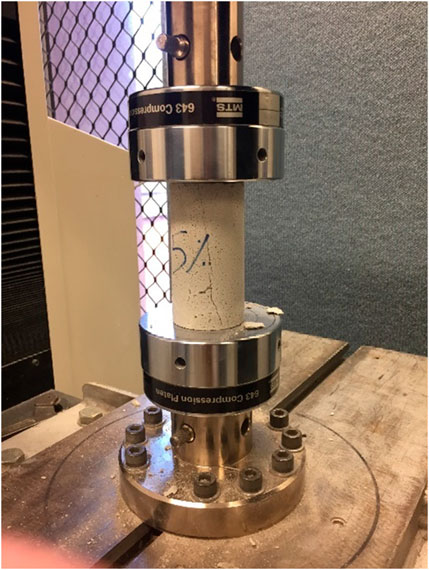
Figure 2. Photograph showing the sample under compressive loading conditions using the universal testing machine.
Each sample determined the water absorption, and the average of the three samples was determined. On the seventh day of the curing, the sample’s weight was measured, and again after 14 days. The weight reduction was determined by dividing the weight difference by the original weight times 100. Standard ASTM C642 was used to measure water absorption: a dry concrete specimen was weighed and then saturated by immersion in water for 24 h. After saturation, the specimen was removed, excess surface water removed, and it was reweighed. The difference in weight before and after saturation was used to calculate the water absorption as a percentage of the initial dry weight, providing valuable information about the porosity and permeability of the concrete—crucial for assessing its durability and performance.
3 Results after the seventh day of curing
3.1 After 7 days
The compressive testing data for the concrete without any addition of ceramic is given in Figure 3 as force vs. deformation. Three samples of the concrete were tested, as shown in the figure. Two samples have similar trends and peak values of force. One sample is out of the range, especially in deformation. This can be due to the presence of some peaks in the surface, which crashed when the testing began, and then the real test took place. However, the maximum force seems similar for the three samples, at approximately 13 kN. All three samples seem to be in brittle failure mode since the plastic deformation region drops dramatically after the peak, representing the crashed samples’ sequencing process after the test.
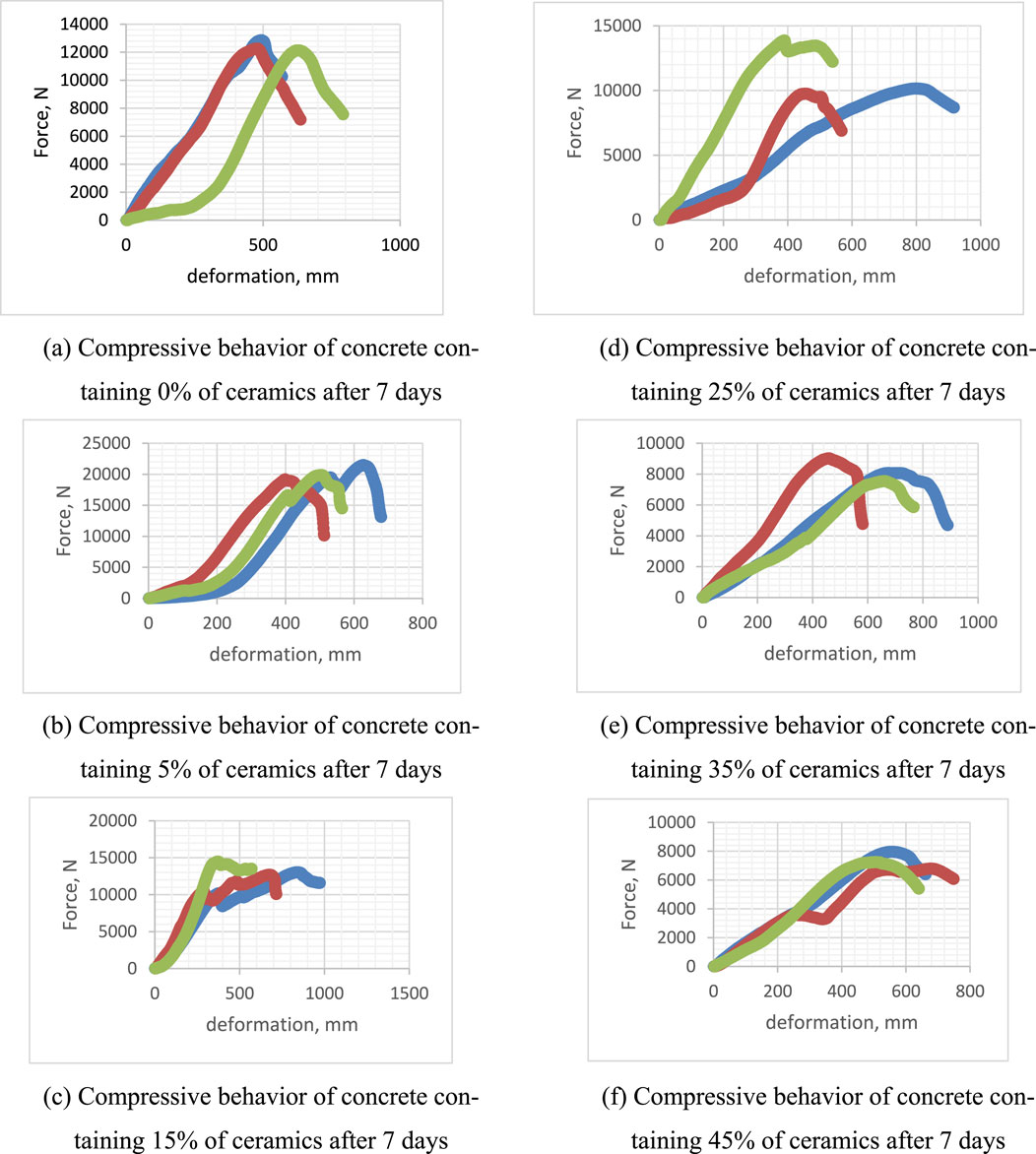
Figure 3. Compressive behavior of concrete containing different ceramics percent after 7 days: (A) 0%; (D) 25%; (B) 5%; (E) 35%; (C) 15%; (F) 45%.
The compressive behavior of concrete with 5% waste ceramic powder is given in Figure 3A. The curves of the three samples are in the same trend. There is high deformation with less stress at the initial stage. At approximately 200 mm deformation, the relation between force and deformation begins to be proportional, representing the deformation’s elastic region. The stress increases until the deformation reaches 400–600 mm, and then the force starts dropping, indicating the failure of the samples. Maximum force can be seen at approximately 21,000 N. In two samples, some yielding processes occur, which are at the force of approximately 16,000 N and 18,000 N. Compared to the previous section for the pure concrete without any addition of ceramic powder, there is an increase in the force required to fail the sample. This cannot be explained at this stage since the other data suggest that the addition of the ceramic reduces the strength of the concrete.
Force vs. deformation of the three samples is given in Figure 3B for the higher percentage of ceramic powder. The trends of two of the samples seem to be similar, but the third’s was different. The failure in the third sample did not last long after the peak force. More strain was achieved after the peak force for the other two samples. Maximum force can be found at approximately 14,000 N, much lower than the previous sections. This indicates that adding ceramic powder reduces the tensile properties of concrete. The reduction in the force is about 30% compared to the concrete without ceramic. The literature mentions many reasons for reducing concrete strength by adding ceramic as aggregate. The water absorption of the ceramic could deteriorate the bond between the ceramic and the concrete. The generation of voids inside the concrete creates initial cracks, reducing shear resistance. Ndambuki (Sheen et al., 2015) reported a similar effect of adding the ceramic to the concrete but in aggregate form. Aboubakr (Kore Sudarshan and Vyas, 2019) showed such a reduction in the strength of the concrete incorporated with waste ceramics.
At 25% of ceramic in the concrete, the trend and behavior of the concrete compression is similar to the previous one. However, the compressive loading resistance reduction becomes higher with a more significant amount of ceramic. At the high proportion of ceramic, there is an issue with aggregation, especially with powdered ceramic as reported in similar research in polymer composites—ceramic/epoxy composites tested by Ren et al. (2015). Figure 3C indicates that 12,000 N can be the maximum load that can be applied to concrete containing 25% ceramic powder. The figure displays a similar trend of compressive loading with a noticeable reduction in compressive load values. The maximum compressive load that can be used for concrete with 45% waste ceramic powder is 7,000 N.
3.2 After 14 days
The compressive results of the concrete samples after 14 days of curing are presented in Figure 4. Compared to Figure 3 for similar samples cured for 7 days, curing after 14 days increased the brittleness of the samples since there was not much deformation after the peak of the force. The energy under the curve was thus less after 14 days of curing than after 7 days. However, in terms of force, 14-day curing increases compressive force to approximately 15 kN; after 7 days curing, the force was only approximately 12 kN. This is the normal behavior of the majority of concrete: longer curing duration for high strength.
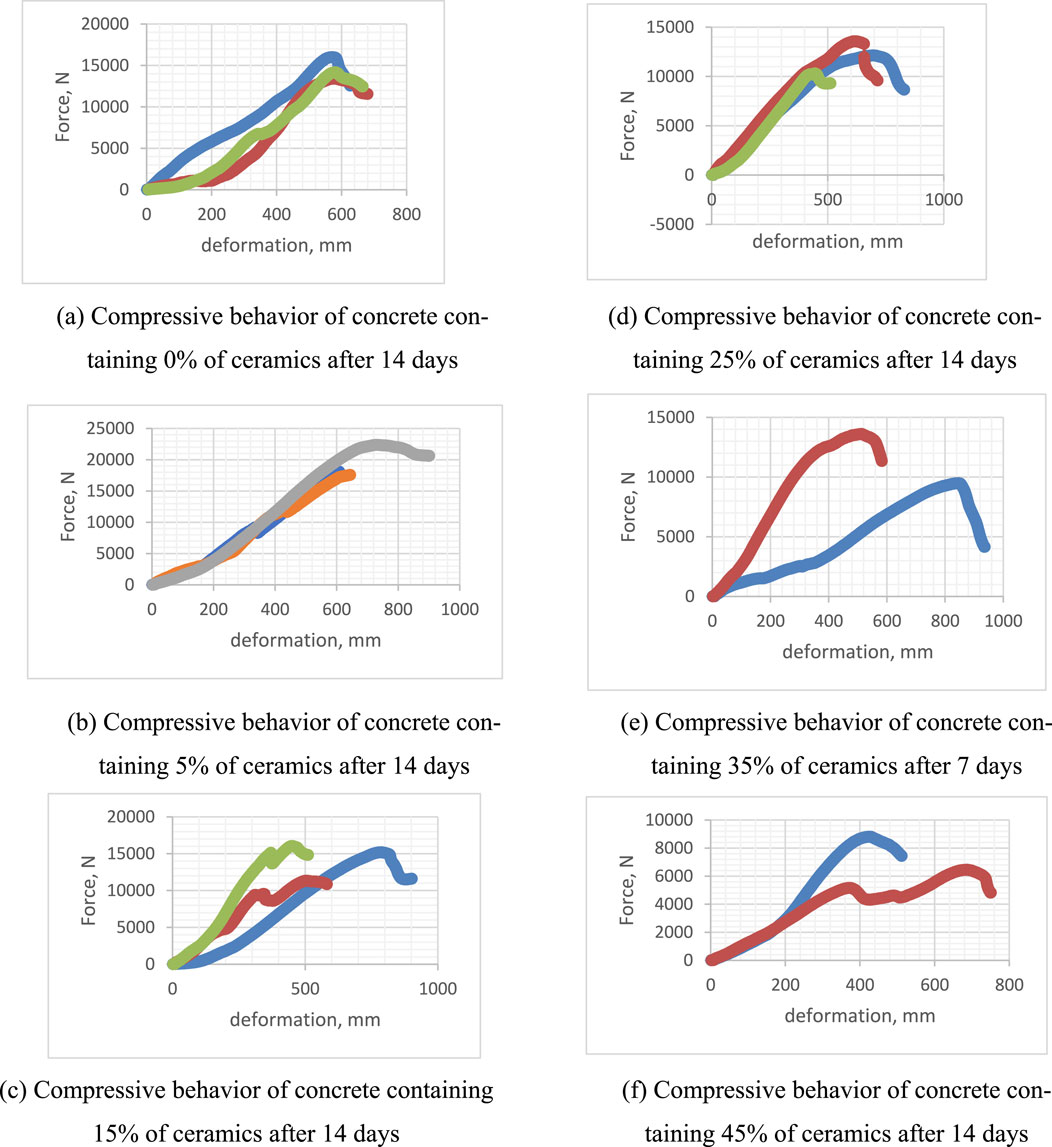
Figure 4. Compressive behavior of concrete containing different percentage concentrations after 14 days: (A) 0%; (D) 25%; (B) 5%; (E) 35%; (C) 15%; (F) 45%.
The force vs. deformation of the concrete with different contents of ceramic powder is given in Figures 4A–F. For the first low content of 5% ceramic, Figure 4 shows strain variation in the behavior of the concrete since two samples failed at approximately 19,000 N while one carried up to 23,000 N. Compared to the same content cured for 7 days, the average force was approximately 20,000 N. This indicates that the third sample in the fourteenth curing day is accurate, giving a high strength up to the maximum force of 23,000 N. The compressive behavior of the 15% ceramic in concrete exhibits a similar trend to 5% concrete. Significant differences exist in the trend of the three samples since they failed in different manners. The maximum force was approximately 16,000 N, greater than the one cured for 7 days only (14,000 N). The other concrete with a high proportion of ceramic showed similar trends and findings since there was an increase in the force compared to 7 days of curing.
3.3 Influence of ceramic powder content in concert and curing duration on strength
To gain an overview of the influence of waste ceramic on concrete strength, the average compressive strength of the materials is plotted in a bar chart with an error bar for the different durations of curing (Figure 5). In general, adding ceramic reduced the strength of the concrete, especially after 15% ceramic. At 5% ceramic, there was a 25% increase in the strength of the concrete. At 15% and above, there was a decrease in strength. Regarding the effect of curing duration, 28 days of curing increased concrete strength for all percentages of waste ceramics. For 14 days of curing, the influence of curing at this period is not that remarkable since the data are scattered.
For a high content of ceramic in concrete, the deterioration in strength could be due to many factors, such as the interfacial adhesion of the ceramic powder with the concrete, the void generation in the concrete due to the ceramic’s very high porosity, and the aggregation of the powder in clusters. Recent work by Öztürk (Frías et al., 2021) has suggested that the hydration of cement is the main reason for the reduction in strength due to the low amount of C3S, which is supported by Puertas et al. (2010). In these studies, the ceramic was used in aggregate form, and the concrete’s strength reduction was evident at all proportions of content. In the current study, the strength improved by 5%. Subaşı et al. (2017) found a 20% reduction in concrete strength with 15% aggregate ceramic. In our study, the reduction in the same percentage of ceramic but in powdered form is almost zero. In other words, using ceramic in powdered form is much better than use in aggregate form. This could principally be because a large amount of aggregate ceramic can dehydrate concrete at the first stage of the curing worse than with ceramic. Powdered ceramic (microscale) is very small, and the absorption and release of water can be faster than aggregate on a centimeter scale. Aboubakr (de Castro Carvalho et al., 2024) also suggested this, with results in high agreement with ours. Kannan et al. (2017b) suggested that the high porosity of concrete with a high proportion of waste ceramic powder is the main reason for a reduction in concrete strength. Recycled concrete aggregates (RCA) have been investigated as a potential reinforcement material in concrete by Nor et al. (2023), who found that 50% of prepared concrete incorporating RCA resulted in a compressive strength of approximately 36 MPa. The lower compressive strength observed in this case can be attributed to the high porosity of RCA and its poor interfacial adhesion with the aggregate, water, and cement. Zhang et al. (2020) assessed the compressive strength of fiber-reinforced concrete with recycled aggregate derived from waste clay bricks. Due to the waste clay aggregate’s inherent weakness and relatively large size, the maximum compressive strength achieved was approximately 65 MPa. Comparing these earlier findings with our current results, it becomes evident that ceramic powder presents a more promising alternative to RCA or waste clay. This is highlighted by a significantly higher compressive strength of approximately 200 MPa when utilizing 25% ceramic powder in the concrete mixture.
3.4 Water absorption
Figure 6 shows water absorption in the prepared concrete after 28 days where adding ceramic to concrete increases its water absorption. This will significantly affect the formation and setting of the concrete during the curing process. The ceramic absorbed the water, not leaving enough water for the cement to react, which resulted in a fragile structure. At the low percentage of ceramic, the increase in the absorption rate was much less compared to the high percentage of the waste ceramic, which may be the main reason for the low strength of the concrete at the high rate of ceramic.
3.5 SEM observation
The fractured surface of the samples after the tests is graphed in Figures 7–9 for the 0%, 25%, and 45% ceramic content. At 0% ceramic, the fractured surface seems normal. There are some detachments for the aggregate, and there is some debris on the surface, representing the concrete’s brittleness. At 25% ceramic, there is an apparent aggregation of the ceramic powder, which forms clusters. This generated a layer around the concrete’s aggregate (Figure 8). This weakened the structure of the concrete and resulted in reduced strength. This is very clear for the high percentage of ceramic as seen in Figure 9, where the aggregation of the ceramic powder is apparent and large, resulting in detachments of the ordinary aggregate in the concrete and the generation of microcracks in the structure. The sample with 0% ceramic content exhibited a porosity of approximately 5%, while the sample with 45% ceramic powder showed a significantly higher porosity of around 15%. These results align with the observed reduction in compressive strength at higher ceramic powder content, suggesting that increased porosity weakens the concrete matrix by creating more voids and reducing interfacial bonding.
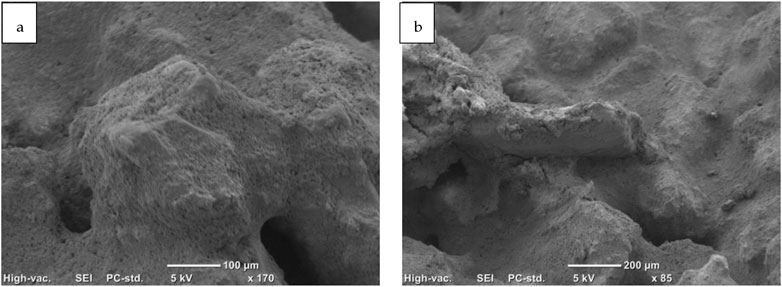
Figure 7. (A) Micrographs (×100 µm) of concrete containing 0% ceramics after 28 days. (B) Micrographs (×200 µm) of concrete containing 0% ceramics after 28 days.
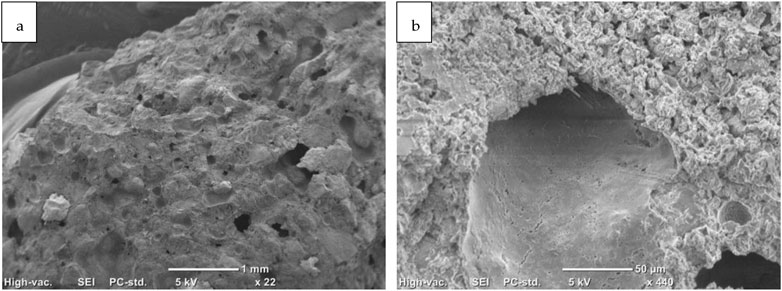
Figure 8. (A) Micrographs (×1 mm) of concrete containing 25% ceramics after 28 days. (B) Micrographs (×50 µm) of concrete containing 25% ceramics after 28 days.
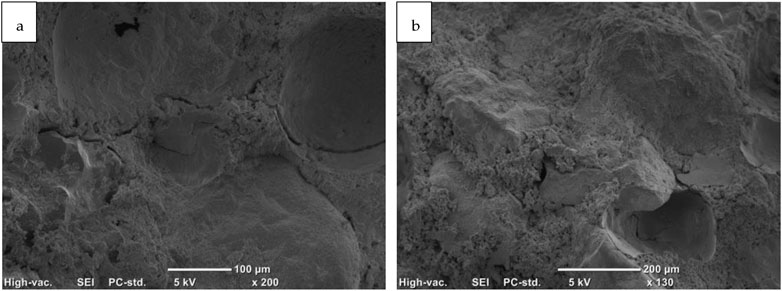
Figure 9. (A) Micrographs (×100 µm) of concrete containing 45% ceramics after 28 days. (B) Micrographs (×200 µm) of concrete containing 45% ceramics after 28 days.
This study was conducted to better understand the influence of waste ceramic content on concrete materials. The results presented the fractured surfaces for concrete samples with different ceramic contents: 0%, 25%, and 45%. The aim was to observe how the addition of ceramic waste affected concrete’s microstructure and mechanical properties. Figure 5 shows that as the ceramic waste content increased, the concrete’s strength decreased. This suggests that the incorporation of ceramics diminished the overall performance of concrete. The SEM micrographs of the concrete samples show specific changes depending on the ceramic content. As this increased, the micrographs reveal the deterioration of the concrete’s structure. At high ceramic content (45%), there are visible aggregations of ceramic particles, acting as additional voids within the concrete matrix. These voids weaken the concrete’s structure, reducing resistance to external loading forces. At 25% ceramic content, the micrographs show a relatively better concrete structure compared to the 45% content. However, there are still signs of detachment of ceramic particles, indicating poor interfacial adhesion between the ceramic particles and the cement matrix. This poor adhesion could contribute to weaknesses in the concrete’s overall mechanical properties.
4 Conclusion
The results of this experimental study lead to the following conclusions.
• The investigation into the influence of ceramic powder content in concrete and of curing duration on its strength has provided valuable insights. Adding ceramic powder to concrete demonstrates a complex relationship with its strength. A significant increase in strength is observed at 5% ceramic content, but exceeding a 15% threshold results in a notable decline. This decline may be attributed to poor interfacial adhesion, void generation, and the aggregation of ceramic particles in the concrete. The difference in results between ceramic in aggregate and powdered forms suggests the latter’s superiority, possibly due to faster water absorption and release at the microscale.
• Comparisons with studies involving other reinforcement materials, such as recycled concrete aggregates (RCA) and waste clay, suggest that ceramic powder is a more promising alternative, yielding higher compressive strength, particularly at 25% ceramic content. Water absorption experiments have revealed that increased ceramic content leads to higher water absorption in the concrete, impacting its setting and formation during curing.
• Scanning electron microscope (SEM) observations provided visual evidence of the structural changes in the concrete at different ceramic content levels. At 45% ceramic content, noticeable aggregations of ceramic particles weaken the concrete’s structure, while at 25%, the detachment of ceramic particles indicates suboptimal interfacial adhesion.
• These findings underscore the importance of carefully balancing ceramic powder content in concrete mixtures to achieve optimal strength. Utilizing ceramic powder at appropriate proportions and considering the impact on water absorption and microstructural integrity can enhance performance, making it a viable option for reinforcement in concrete applications. Further research could explore optimization of the ceramic-to-concrete ratio and additional factors influencing interfacial adhesion and microstructure to maximize the benefits of ceramic incorporation in concrete construction.
Data availability statement
The original contributions presented in the study are included in the article/supplementary material; further inquiries can be directed to the corresponding author.
Author contributions
JA: writing–review and editing. AA: investigation and writing–review and editing. TA: formal analysis, validation, and writing–review and editing. JK: methodology and writing–original draft. BY: writing–original draft.
Funding
The author(s) declare that no financial support was received for the research, authorship, and/or publication of this article.
Conflict of interest
The authors declare that the research was conducted in the absence of any commercial or financial relationships that could be construed as a potential conflict of interest.
The author(s) declared that they were an editorial board member of Frontiers, at the time of submission. This had no impact on the peer review process and the final decision.
Publisher’s note
All claims expressed in this article are solely those of the authors and do not necessarily represent those of their affiliated organizations, or those of the publisher, the editors, and the reviewers. Any product that may be evaluated in this article, or claim that may be made by its manufacturer, is not guaranteed or endorsed by the publisher.
References
Abou Rachied, T., Dbouk, F., Hamad, B., and Assaad, J. J. (2023). Structural behavior of beams cast using normal and high strength concrete containing blends of ceramic waste powder and blast furnace slag. Clean. Mater. 7, 100179. doi:10.1016/j.clema.2023.100179
Brekailo, F., Pereira, E., Pereira, E., Farias, M. M., and Medeiros-Junior, R. A. (2022). Red ceramic and concrete waste as replacement of portland cement: microstructure aspect of eco-mortar in external sulfate attack. Clean. Mater. 3, 100034. doi:10.1016/j.clema.2021.100034
de Castro Carvalho, I., de Oliveira, G. T., Kirchheim, A. P., da Costa, H. N., and Cabral, A. E. B. (2024). Utilization of red ceramic waste in the production of binary eco-friendly alkali-activated binder: fresh and hardened state investigation. Case Stud. Constr. Mater. 21, e03681. doi:10.1016/j.cscm.2024.e03681
El-Dieb, A. S., and Kanaan, D. M. (2018). Ceramic waste powder an alternative cement replacement–Characterization and evaluation. Sustain. Mater. Technol. 17, e00063. doi:10.1016/j.susmat.2018.e00063
Ergenç, D., Sierra-Fernandez, A., del Mar Barbero-Barrera, M., Gomez-Villalba, L. S., and Fort, R. (2020). Assessment on the performances of air lime-ceramic mortars with nano-Ca (OH) 2 and nano-SiO2 additions. Constr. Build. Mater. 232, 117163. doi:10.1016/j.conbuildmat.2019.117163
Farahani, J. N., Shafigh, P., Alsubari, B., Shahnazar, S., and Mahmud, H. B. (2017). Engineering properties of lightweight aggregate concrete containing binary and ternary blended cement. J. Clean. Prod. 149, 976–988. doi:10.1016/j.jclepro.2017.02.077
Frías, M., Martínez-Ramírez, S., de la Villa, R. V., Fernández-Carrasco, L., and García, R. (2021). Reactivity in cement pastes bearing fine fraction concrete and glass from construction and demolition waste: microstructural analysis of viability. Cem. Concr. Res. 148, 106531. doi:10.1016/j.cemconres.2021.106531
Gesoglu, M., Güneyisi, E., Hansu, O., Etli, S., and Alhassan, M. (2017). Mechanical and fracture characteristics of self-compacting concretes containing different percentage of plastic waste powder. Constr. Build. Mater. 140, 562–569. doi:10.1016/j.conbuildmat.2017.02.139
Gilabert, F., Van Tittelboom, K., Tsangouri, E., Van Hemelrijck, D., De Belie, N., and Van Paepegem, W. (2017). Determination of strength and debonding energy of a glass-concrete interface for encapsulation-based self-healing concrete. Cem. Concr. Compos. 79, 76–93. doi:10.1016/j.cemconcomp.2017.01.011
Golewski, G. L. (2018). Evaluation of morphology and size of cracks of the Interfacial Transition Zone (ITZ) in concrete containing fly ash (FA). J. Hazard. Mater. 357, 298–304. doi:10.1016/j.jhazmat.2018.06.016
John, V. M., Damineli, B. L., Quattrone, M., and Pileggi, R. G. (2018). Fillers in cementitious materials—experience, recent advances and future potential. Cem. Concr. Res. 114, 65–78. doi:10.1016/j.cemconres.2017.09.013
Kannan, D. M., Aboubakr, S. H., El-Dieb, A. S., and Reda Taha, M. M. (2017a). High-performance concrete incorporating ceramic waste powder as large partial replacement of Portland cement. Constr. Build. Mater. 144, 35–41. doi:10.1016/j.conbuildmat.2017.03.115
Kannan, D. M., Aboubakr, S. H., El-Dieb, A. S., and Reda Taha, M. M. (2017b). High performance concrete incorporating ceramic waste powder as large partial replacement of Portland cement. Constr. Build. Mater. 144 (Suppl. C), 35–41. doi:10.1016/j.conbuildmat.2017.03.115
Kisku, N., Joshi, H., Ansari, M., Panda, S. K., Nayak, S., and Dutta, S. C. (2017). A critical review and assessment for usage of recycled aggregate as sustainable construction material. Constr. Build. Mater. 131, 721–740. doi:10.1016/j.conbuildmat.2016.11.029
Kore Sudarshan, D., and Vyas, A. K. (2019). Impact of fire on mechanical properties of concrete containing marble waste. J. King Saud Univ. - Eng. Sci. 31, 42–51. doi:10.1016/j.jksues.2017.03.007
Kumar, R. (2017). Influence of recycled coarse aggregate derived from construction and demolition waste (CDW) on abrasion resistance of pavement concrete. Constr. Build. Mater. 142, 248–255. doi:10.1016/j.conbuildmat.2017.03.077
Li, L., Liu, W., You, Q., Chen, M., and Zeng, Q. (2020). Waste ceramic powder as a pozzolanic supplementary filler of cement for developing sustainable building materials. J. Clean. Prod. 259, 120853. doi:10.1016/j.jclepro.2020.120853
Ma, C., and Chen, B. (2017). Experimental study on the preparation and properties of a novel foamed concrete based on magnesium phosphate cement. Constr. Build. Mater. 137, 160–168. doi:10.1016/j.conbuildmat.2017.01.092
Maalouf, C., Ingrao, C., Scrucca, F., Moussa, T., Bourdot, A., Tricase, C., et al. (2018). An energy and carbon footprint assessment upon the usage of hemp-lime concrete and recycled-PET façades for office facilities in France and Italy. J. Clean. Prod. 170, 1640–1653. doi:10.1016/j.jclepro.2016.10.111
Magbool, H. M. (2022). Utilisation of ceramic waste aggregate and its effect on Eco-friendly concrete: a review. J. Build. Eng. 47, 103815. doi:10.1016/j.jobe.2021.103815
Malaiškienė, J., Vaičienė, M., and Žurauskienė, R. (2011). Effectiveness of technogenic waste usage in products of building ceramics and expanded clay concrete. Constr. Build. Mater. 25 (10), 3869–3877. doi:10.1016/j.conbuildmat.2011.04.008
Mansour, M. A., Ismail, M. H. B., Imran Latif, Q. B. a., Alshalif, A. F., Milad, A., and Bargi, W. A. A. (2023). A systematic review of the concrete durability incorporating recycled glass. Sustainability 15 (4), 3568. doi:10.3390/su15043568
Matias, G., Faria, P., and Torres, I. (2014). Lime mortars with ceramic wastes: characterization of components and their influence on the mechanical behaviour. Constr. Build. Mater. 73, 523–534. doi:10.1016/j.conbuildmat.2014.09.108
Mir, N., Khan, S. A., Kul, A., Sahin, O., Lachemi, M., Sahmaran, M., et al. (2022). Life cycle assessment of binary recycled ceramic tile and recycled brick waste-based geopolymers. Clean. Mater. 5, 100116. doi:10.1016/j.clema.2022.100116
Nor, N. M., Setiawan, A. F., Fauzi, N. E. H. M., Zaini, M. N., Saliah, S. N. M., Nujid, M. M., et al. (2023). The behaviour of one-hollow interlocking concrete block made from recycled concrete aggregate under flexural loading. Procedia Struct. Integr. 47, 732–743. doi:10.1016/j.prostr.2023.07.046
Pacheco-Torgal, F., and Jalali, S. (2010). Reusing ceramic wastes in concrete. Constr. Build. Mater. 24 (5), 832–838. doi:10.1016/j.conbuildmat.2009.10.023
Pakravan, H. R., Latifi, M., and Jamshidi, M. (2017). Hybrid short fiber reinforcement system in concrete: a review. Constr. Build. Mater. 142, 280–294. doi:10.1016/j.conbuildmat.2017.03.059
Puertas, F., García-Díaz, I., Palacios, M., Gazulla, M. F., Gómez, M. P., and Orduña, M. (2010). Clinkers and cements obtained from raw mix containing ceramic waste as a raw material. Characterization, hydration and leaching studies. Cem. Concr. Compos. 32 (3), 175–186. doi:10.1016/j.cemconcomp.2009.11.011
Puthipad, N., Ouchi, M., Rath, S., and Attachaiyawuth, A. (2017). Enhanced entrainment of fine air bubbles in self-compacting concrete with high volume of fly ash using defoaming agent for improved entrained air stability and higher aggregate content. Constr. Build. Mater. 144, 1–12. doi:10.1016/j.conbuildmat.2017.03.049
Ren, Z. H., Jin, P., Cao, X. M., Zheng, Y. G., and Zhang, J. S. (2015). Mechanical properties and slurry erosion resistance of SiC ceramic foam/epoxy co-continuous phase composite. Compos. Sci. Technol. 107, 129–136. doi:10.1016/j.compscitech.2014.12.012
Saribiyik, A., and Caglar, N. (2016). Flexural strengthening of RC Beams with low-strength concrete using GFRP and CFRP. Struct. Eng. Mech. 58 (5), 825–845. doi:10.12989/sem.2016.58.5.825
Saribiyik, M., Piskin, A., and Saribiyik, A. (2013). The effects of waste glass powder usage on polymer concrete properties. Constr. Build. Mater. 47, 840–844. doi:10.1016/j.conbuildmat.2013.05.023
Sheen, Y.-N., Le, D.-H., and Sun, T.-H. (2015). Innovative usages of stainless steel slags in developing self-compacting concrete. Constr. Build. Mater. 101 (Part 1), 268–276. doi:10.1016/j.conbuildmat.2015.10.079
Subaşı, S., Öztürk, H., and Emiroğlu, M. (2017). Utilizing of waste ceramic powders as filler material in self-consolidating concrete. Constr. Build. Mater. 149 (Suppl. C), 567–574. doi:10.1016/j.conbuildmat.2017.05.180
Vieira, G. L., Schiavon, J. Z., Borges, P. M., da Silva, S. R., and de Oliveira Andrade, J. J. (2020). Influence of recycled aggregate replacement and fly ash content in performance of pervious concrete mixtures. J. Clean. Prod. 271, 122665. doi:10.1016/j.jclepro.2020.122665
Zegardło, B., Szeląg, M., and Ogrodnik, P. (2016). Ultra-high strength concrete made with recycled aggregate from sanitary ceramic wastes – the method of production and the interfacial transition zone. Constr. Build. Mater. 122, 736–742. doi:10.1016/j.conbuildmat.2016.06.112
Keywords: waste ceramic, powder, concrete, flexure, compressive
Citation: Alotaibi JG, Alajmi AE, Alsaeed T, Khalaf JA and Yousif BF (2024) On the incorporation of waste ceramic powder into concrete. Front. Mech. Eng. 10:1469727. doi: 10.3389/fmech.2024.1469727
Received: 24 July 2024; Accepted: 23 September 2024;
Published: 16 October 2024.
Edited by:
Vinod Ayyappan, King Mongkut’s University of Technology North Bangkok, ThailandCopyright © 2024 Alotaibi, Alajmi, Alsaeed, Khalaf and Yousif. This is an open-access article distributed under the terms of the Creative Commons Attribution License (CC BY). The use, distribution or reproduction in other forums is permitted, provided the original author(s) and the copyright owner(s) are credited and that the original publication in this journal is cited, in accordance with accepted academic practice. No use, distribution or reproduction is permitted which does not comply with these terms.
*Correspondence: Belal F. Yousif, QmVsYWwuWW91c2lmQHVuaXNxLmVkdS5hdQ==