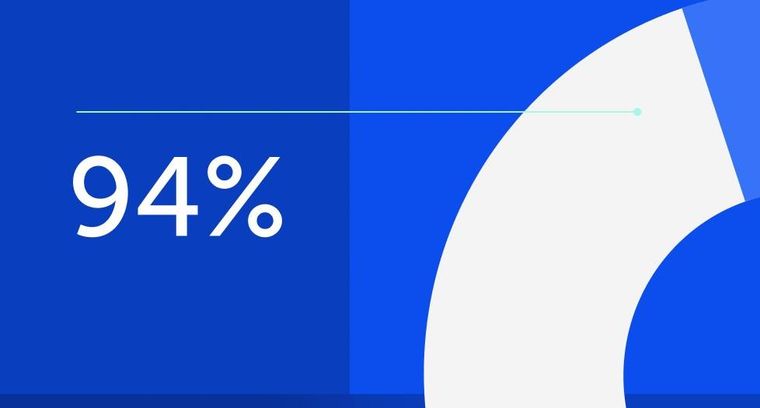
94% of researchers rate our articles as excellent or good
Learn more about the work of our research integrity team to safeguard the quality of each article we publish.
Find out more
ORIGINAL RESEARCH article
Front. Mech. Eng., 07 January 2025
Sec. Digital Manufacturing
Volume 10 - 2024 | https://doi.org/10.3389/fmech.2024.1437198
Introduction: The excessive uncertainty of in modern manufacturing systems is caused by machine failures, changes in material information, and other factors. In addition, the organizational production mode conflicts brought about by economic and technological development further exacerbate the perception of workshop interference in manufacturing systems.
Method: In order to further improve the adaptability of manufacturing systems, a control technique based on recursive control structure is proposed, which introduces an immune working mechanism to design the framework network of multi-agent manufacturing systems. Meanwhile, a negative selection algorithm is used to construct an antibody training system that considers perturbation problems.
Result: The results indicate that immune sensing nodes can effectively monitor manufacturing systems, reducing false alarm rates by over 4%. In the scheduling experiment, the completion time and equipment load improvement rate demonstrated by the research model were 3.29% and 12.38%, respectively. The production balance optimization rate exceeded 90%, far exceeding the results of traditional scheduling schemes, greatly improving the adaptive control capability of manufacturing system production.
Discussion: The regulatory approach proposed in this study can provide reference and assistance for improving the level of industrial production intelligence and establishing a sustainable economic system. However, the research results have not been applied to actual production processes, and the autonomy and coordination of intelligent manufacturing units in actual production processes still need to be further improved. In the future, research models and algorithms will be further explored in this area.
Manufacturing plays an important role in economic change, and its rise and fall is related to the comprehensive strength of a country. It is one of the important symbols to measure the international competitiveness of a country. Countries with strong manufacturing capacity are more likely to gain a leading position in the global market. At the same time, manufacturing products are a major part of international trade, and play an important role in promoting international trade and strengthening international cooperation. In recent years, with the rapid development of computer, information, and control technologies, the market requires enterprises to provide products to short delivery time, higher product quality, and after-sales service. Among enterprises, more and more competitive, enterprise manufacturing mode from mass production to small batch or even a single personalized production way, greatly promote manufacturing enterprise manufacturing mode innovation. In this case, the manufacturing process gradually appears high concurrency, mixing and difficult to predict features (Bi et al., 2021; Seitz et al., 2021; Dittrich and Fohlmeister, 2020). The operating environment of the manufacturing system often produces uncertain events such as machine tool failure and new emergency orders, which leads to the emergence of dynamic and non-linear manufacturing systems. Among them, discrete factories are the first manufacturing environment (Latsou et al., 2021; Vogel-Heuser et al., 2020) affected by various variable factors. Under the situation of economic development and consumption concept change, there are some problems of weak real-time scheduling and slow workshop layer disturbance response in the current mixed line production environment. In view of this problem, improving the existing organizational production mode is an important basis for realizing the new manufacturing mode (Yahouni et al., 2021). With the development of computer and network technology, the multi-agent manufacturing system (MAMS) based on the industrial Internet of Things, artificial intelligence, and cloud computing has been considered as an effective means to solve the current and manufacturing difficulties.
To this end, many scholars have conducted related research on the MAMS. To address issues such as dynamic task arrival, machine downtime, and abnormal task identification, D'Aniello et al. designed a multi-agent system in a cloud manufacturing system based on additive manufacturing technology to address these issues (D’Aniello et al., 2021). To allocate resources reasonably based on production needs and effectively avoid the impact of external interference on manufacturing systems, Nie et al. proposed an intelligent digital dual-workshop framework consisting of physical workshops, virtual workshops, and digital twin service systems. The results show that the intelligent digital dual workshop can effectively allocate resources and handle interference (Nie et al., 2022). To optimize the collaborative workflow of multi-agent systems in warehouses, Dusadeerungsikul et al. proposed a new network collaborative warehouse collaborative workflow protocol. The results show that this method can reduce total operating costs by 5.70% and total weighted completion time by 10.11% (Dusadeerungsikul et al., 2022). Johnson et al. proposed a multi-agent reinforcement learning (MARL) system based on a second-order temporal difference error dual-network algorithm to schedule dynamically arriving assembly tasks in robot assembly units. The system demonstrated better performance compared to rule-based heuristic methods (Johnson et al., 2022). To improve the flexibility and adaptability of product agents and their control strategies, Kovalenko et al. proposed a direct and active collaborative framework for product agents (Kovalenko et al., 2022).
Although the research on MAMS has achieved some research results, but in the face of large-scale complex manufacturing, the control decision response time is longer, and it is difficult for the current MAMS to achieve better control effect. To improve the regulation effect of intelligent manufacturing system, scholars have introduced biometric features into the field of manufacturing system research in recent years. For example, ElMaraghy et al. studied BMS from the perspective of Agent, and used biological characteristics to improve the production performance of manufacturing system for (ElMaraghy et al., 2021). However, most of these scholars carried out research from the perspective of biological genetic evolution, which are still in the conceptual discussion stage. They failed to apply the excellent regulatory mechanism of organisms (such as neuroendocrine regulation) to the manufacturing system, and could not be applied (Turner, 2021; Karbalaei et al., 2020) in the production process. With the development of information technology, computer technology and artificial intelligence, each intelligent manufacturing unit in the manufacturing system has a certain intelligence and information interaction ability. The manufacturing system will encounter a variety of disturbances in the process of operation, and the system is basically dynamic and nonlinear (Vanbecelaere et al., 2020; Wang et al., 2022). How to introduce the excellent characteristics of the biological system into the manufacturing system to evaluate the health status of the manufacturing system in real time, how to learn from the biological multi-layer immune response mechanism and use the corresponding artificial immune algorithm to quickly sense and process the perturbations in the system, and how to combine the biological immunity mechanism with reinforcement learning theory, apply it to production scheduling optimization, improve the system self-organization, adaptive ability and robustness, and then improve the operation efficiency of manufacturing system are important directions and difficulties in the field of manufacturing system research (Simon et al., 2023; Zeng et al., 2020). Based on this, the study combines biological immune theory and innovatively introduces artificial immune algorithms into intelligent manufacturing systems, constructing a control model for intelligent manufacturing systems based on recursive control structure.
Research introduces the negative selection algorithm (NSA) in artificial immune system theory to construct an intelligent manufacturing system regulation model based on recursive control structure, achieving rapid perception and processing of disturbances in manufacturing systems.
The current manufacturing industry is plagued by dynamic scheduling and workshop level disturbance perception problems in complex environments, especially the significant impact on flexible discrete job manufacturing workshops (Xu et al., 2024). In response to this issue, a new workshop level regulation model is designed by combining artificial immune system theory and multi-agent system theory. An intelligent agent is a program that can perceive the surrounding environment, operate autonomously, and act on a specific environment. The current cognitive and reactive intelligent agent structures are widely used mainstream structures. Aiming at flexible discrete job manufacturing workshops, this study combines the basic structure of cognitive intelligent agents, stores intelligent agent software programs on its own processor, and designs an intelligent agent structure for physical entity devices, as shown in Figure 1.
In Figure 1, the study divides the intelligent agent into adaptation layer, intelligent analysis layer, and communication development layer. For simplicity and ease of implementation, research is being conducted on modifying the device processor by adding an embedded industrial computer, which is connected to the device itself through customized hardware interfaces. Intelligent agents are encapsulated in a specific way and can be mapped to entities in the production and manufacturing workshop. Multiple intelligent agents form a loosely coupled organizational structure, laying the foundation for the development of workshop control systems. Starting from the system layer, the study represents the material flow and information flow resources in the manufacturing system as different intelligent agent structures, and then connects independent intelligent agents into an MAMS through intelligent agent protocols and network facilities, as shown in Figure 2.
In Figure 2, when a new order task enters in the system, the task agent is activated by the order agent and sends processing information to each device agent through a distributed network. The device agent decides whether to accept the task according to its own processing ability. Finally, various production tasks are completed together through the autonomy and coordination of multiple agents. Based on the research results of biological immune system and combining with the structural characteristics of intelligent manufacturing unit, the regulatory model of intelligent manufacturing system based on immune mechanism is constructed, as shown in Figure 3.
The model consists of a perceptron (various immune organs), a decision maker (immune recognition, cell differentiation learning, memory), and an executor (the executor of antibodies). At the same time, the immune regulation unit can also communicate and communicate with other immune regulation units, forming a complete immune regulation system, which can achieve good immune regulation function. For the workshop production activities, the monitoring system based on the immune mechanism is composed of multiple machine tools, intelligent processing, intelligent detection, intelligent logistics (Automated Guided Vehicl, AGV), etc. The hardware entity of the agent is constructed by the embedded industrial control machine, and the corresponding immune monitoring mechanism is embedded to constitute the immune monitoring function of the intelligent manufacturing unit. The main functions regulated by the MAMS based on the immune mechanism include immune assessment, recognition, learning, and regulation.
After constructing an intelligent manufacturing system regulation model, the study analyzes its regulation mechanism. The control method of the intelligent manufacturing system proposed in the study is similar to the immune control structure of organisms, and also adopts a recursive control structure. It draws inspiration from the inherent immune response process and adaptive immune response process of organisms and adopts double-layer regulation. For the workshop layer disturbance perception problem in the intelligent manufacturing system, the research adopts the NSA algorithm, and the NSA realizes the judgment of the normal and abnormal state of the workshop layer by comparing the randomly generated mode with the “self mode, whose state space is represented by a set of feature vectors
In Equation 1,
The definition of our own sample
In Equation 3,
In Figure 4, it is difficult for FB-NSA to determine the mutual positional relationship between the diagnostic devices. Therefore, traditional RNSA algorithms cannot perform self/non-self recognition and can only calculate the distance from the test sample
In Equation 4,
The diagnostic layer is composed of multiple hypercubes adjacent to the self sample space, and the center position of each hypercube is used as the center position of the diagnostic device. In this way, the relative position relationship between the diagnostic device and the self space can form the FB-NSA diagnostic device. At this time, the diagnostic layer can be regarded as the outer boundary hypercube layer, and each outer boundary hypercube is an FB-NSA diagnostic device. After evenly dividing the state space
In Equation 6,
In Equation 7,
By constructing an intelligent manufacturing system model and explaining its regulatory mechanism, this study proposes a manufacturing system disturbance recognition model based on artificial immune algorithm, as shown in Figure 5.
In Figure 5, the manufacturing system first performs disturbance feature selection to determine the state space corresponding to a certain disturbance. Secondly, based on the FN-NSA algorithm, a disturbance diagnostic tool, namely, antibodies, is generated and mature antibodies are trained. Next, mature antibodies and disturbance samples extracted from the manufacturing system are detected, and antibodies with high matching degree are extracted for storage. Finally, when the manufacturing system encounters uncertain disturbances, the disturbance samples to be recognized are matched with the antibodies in the system. If the antibodies in the system can be activated, the corresponding disturbance is identified. To verify the effectiveness of immune algorithms in machine tool fault detection in manufacturing systems, the study uses real number encoding to represent antigen antibodies and describes the extracted feature values using
Among them,
The diagnostic device generated by the immune system is the antibody, and a single antibody targeting a certain disturbance can be represented as
The antibody set can be found in Equation 11.
The study defines the degree of antigen and antibody binding in immune algorithms as immune affinity. The affinity between antigen and antibody is denoted as
In Equation 12,
In response to the basic disturbance problem in discrete mechanical machining workshops with high levels of automation, research is conducted on the segmentation of state vectors. After segmentation, several independent state spaces will appear, and the manufacturing system will be monitored separately. Based on the device as the core, it uses Agent technology to construct control nodes with immune monitoring and scheduling functions. A recursive structure is adopted to construct an artificial immune monitoring structure for manufacturing systems, as shown in Figure 6.
In Figure 6, using Agent technology and a distributed structure, a monitoring unit based on immune mechanism is constructed. The immune monitoring structure in the system adopts a recursive control form, which not only completes the acquisition and processing of its own state information, but also feeds back relevant information to the main control unit and accepts coordinated control from the main control unit. The health status of the immune monitoring unit is also influenced by the monitoring status factors of each unit. The study defines the main controller of this monitoring unit as an immune perception node. Each immune perception node in the manufacturing system monitors the real-time operation status of the system (status information of each machine tool), and verifies whether the system has deviations (i.e., whether it is affected by uncertain disturbance factors) by comparing it with normal operation status information. Once a deviation is detected by the corresponding immune perception node, the immune perception node will perform an immune response operation, transmit perception information to the decision maker, and generate corresponding scheduling strategies (antibodies) based on different disturbance types, indicating possible operations to be performed and interference recovery. Drawing inspiration from the hierarchical defense mechanism of the biological immune system and the interaction between levels, a two-layer immune adaptive regulation model for fault diagnosis is proposed, as shown in Figure 7.
In Figure 7, the first layer is the inherent immune regulation layer, which mainly realizes rapid response and processing of known uncertain factors. The second layer is the adaptive immune regulation layer, which realizes intelligent detection and self-learning of unknown disturbances. The adaptive immune regulation layer utilizes the FB-NSA algorithm to regenerate diagnostic devices in local regions without retraining all diagnostic devices. This enables the immune system to adjust diagnostic devices in real-time according to certain rules and changes in its own space during operation, enabling the immune system designed and manufactured by the research to have continuous learning capabilities. Assuming there are 4 samples, their relationship can be found in Equation 13.
Assuming that
In Equation 14,
The study acquired error data from different measurement components post-operation via experimental simulation and divided the resulting dataset into two subsets—A and B—based on the size of the error data. In the two datasets, 80% was designated as the test set, 10% as the validation set, and 10% as the training set. In the experiment, genetic algorithms (GAs) and simulated annealing (SA) were introduced as experimental comparisons. The performance of the algorithms was compared and analyzed based on precision and area under the curve (AUC) values as evaluation indications. Figure 8 depicts the precision comparison under different methods.
In Figure 8, the experimental results of the proposed algorithm on the two datasets were similar. After 100 iterations, they remained stable with an accuracy of 0.7. As the amount of iterations increased, the change in stability became smaller and more stable. GA had a precision of 0.5 in both datasets, but had better iteration times in dataset 1. The precision of dataset 1 was about 0.5, which was 0.1 higher than that of dataset 2, but its convergence speed was slightly reduced. The proposed algorithm improved convergence speed, operational efficiency, and the precision of error prediction. The comparison of AUC values under different methods is denoted in Figure 9.
Figure 9 illustrates the results of the training and testing of dataset 1. The proposed algorithm achieved an AUC value of 0.849, which was 0.076 higher than the AUC value of GA. SA exhibited the lowest AUC value, which was 0.740. In the training and testing of dataset 2, the AUC values of the proposed algorithm, GA, and SA were 0.824, 0.764, and 0.736, respectively. It can be observed that the AUC value of the proposed algorithm is the highest in both datasets, indicating that the proposed algorithm has the best performance.
To verify the effectiveness and application effect of the research model, the experimental verification platform of MAMS based on immune mechanism was built. According to its functions, the platform was divided into four levels, namely, human-computer interaction layer (human-machine interface), physical platform layer (hardware device layer), immune regulation layer (control software and database), and communication layer (communication protocol). The hardware equipment in the system could be used for the actual production of the workshop, including: 2 CNC lathes, 2 CNC milling machines, 2 engraving machines, 2 AGVs, 2 six-DOF manipulator with ground rail and 1 automatic three-dimensional warehouse AS/RS. Among them, 6 CNC machine tools were allocated on both sides of the system, and each processing equipment had 4 workpiece buffer areas. The system was developed by using C # programming language, and it was composed of human-computer interaction interface, software system and physical unit (processing equipment, AGV and three-dimensional warehouse). The software platform mainly included user management, data information management, immune monitoring, immune evaluation, immune learning and immune decision. Human-computer interface could observe the running status of AGV, working process of processing equipment, immune monitoring related form, etc.,. The experimental platform provided processing tests for three types of workpieces: plate parts, flange parts, and shaft parts. The process type, labor cost, and other parameter information of each machine tool are shown in Table 1.
There were a total of 6 CNC machine tools in Table 1, and the parameter information in the table provided data support for the objective optimization mathematical model. It submitted orders in the cloud system according to Table 2. To ensure comparability in each experiment, the size parameters of the same order were consistent across different instances.
The experimental system subsystem contained two devices of the same type, and the remaining processing time of the work piece to be processed by the two devices would form a two-dimensional state space. Research collected the machine load values within the subsystem under normal scheduling conditions, normalized them, and input them into the antibody training program, as shown in Figure 9. As shown in Figure 9A, the input numerical samples were used to obtain their own space, and antibody training was performed using the FB-NSA algorithm. The final results are shown in Figures 10B, C.
Figure 10. Schematic diagram of antibody generation for subsystem load anomaly diagnosis. (A) Sample. (B) My own space. (C) Antibody generation.
According to the method of generating pre position information, it completed the generation of antibody position information and obtained the final set of antibody information. The antibody set was imported into the testing program to test the antibody performance. When the false alarm rate was less than 3%, the antibody was qualified and imported into the immune perception node of the subsystem. The abnormal information would be fed back to the server-side immune perception node for artificial immune adaptive regulation.
At runtime, the study conducted targeted scenario testing and recorded the actual operation situation in two stages, before and after, to test the antibody performance. The actual antibody performance is shown in Figure 11A. Then, a scheduling experiment was conducted on the case design of the study, and the experimental results are shown in Figure 11B.
Figure 11. Experimental operation results. (A) Antibody operation results. (B) Scheduling experiment results.
From Figure 11A, in the first stage, there were 8 false negatives and 2 false positives in the immune state space, with a false negative rate of 18.2% and a false positive rate of 5.2%. According to the actual situation, the immune perception node updated the antibodies online based on the adaptive immune processing mechanism designed by the research, with a total refresh rate of 21.2%. In the second stage of actual testing, the false positive rate was reset to zero, and the false negative rate decreased to 4.5%, significantly improving the system monitoring performance. At the same time, the actual operating results indicated that the multi-layer immune response mechanism designed by the research could effectively provide health warning for disturbance of underlying equipment and avoid accidents when there were no or few people in the factory. From Figure 11B, the scheduling results of traditional contract networks for scheduling experiments included completion time, total cost, and total equipment load of 425, 106.38, and 1,607, respectively. The scheduling results using the research model for scheduling experiments were 411, 102.67, and 1,408 for completion time, total cost, and total equipment load, respectively. The three scheduling indicators of completion time, total cost, and total equipment load all improved by nearly 3.29%, 3.49%, and 12.38%, respectively. The comparison results of production balance rate and smoothness index are shown in Figure 12.
From Figure 12, the production pace of the original production line was too high and the processes were unbalanced. The production balance rate was as low as 38.65%, and the smoothness index was as high as 43.8. The study optimized the production line using FB-NSA and artificial immune algorithm, and the production balance rate increased to 92.2%, while the smoothness index decreased to 4.33. Due to the poor stability and convergence of traditional methods, the application of artificial immune algorithms improved stability and convergence. The production balance rate was 92.57%, and the smoothing index was 4.12. According to the research model search for the optimal individual combination, actual adjustments were made to the workshop processes, resulting in a production balance rate of 91.11%, a smoothness index of 4.77, and a reduced production time for one workpiece from 201 s before improvement to 164 s.
At present, with the rapid development of Internet+ and artificial intelligence technology, the market competition is becoming more and more fierce. The production workshop or modern manufacturing system has been in the process of dynamic change, often encountering changes in the internal and external environment such as emergency orders and machine failures. To improve the dynamic response capability of intelligent manufacturing systems, this study fused the biological immune mechanism ideas, and used FB-NSA algorithm and artificial immune algorithm to construct a recursive control structure-based intelligent manufacturing system regulation model. The actual antibody generation experiment results showed that in the first stage, there were 8 false negatives and 2 false positives in the immune state space, with a false negative rate of 18.2% and a false positive rate of 5.2%. According to the actual situation, the immune perception node updated the antibodies online based on the adaptive immune processing mechanism designed by the research, with a total update rate of 21.2%. In the second stage of actual testing, the false negative rate was reset to zero, and the false positive rate decreased to 4.5%, significantly improving the system monitoring performance. The actual operation results showed that the multi-layer immune response mechanism designed by the research could effectively provide health warning for disturbance of underlying equipment and avoid accidents when there were no or few people in the factory. The scheduling experiment results showed that the completion time, total cost, and total equipment load of the traditional contract network scheduling experiment were 425, 106.38, and 1,607, respectively. The scheduling results using the research model for scheduling experiments were 411, 102.67, and 1,408 for completion time, total cost, and total equipment load, respectively. The three scheduling indicators of completion time, total cost, and total equipment load all improved by nearly 3.29%, 3.49%, and 12.38%, respectively. The scheduling experiment results showed that the proposed model could improve workshop completion time, total cost, and total equipment load, and was practical and feasible. In addition, the study optimized the production line using FB-NSA and artificial immune algorithms, resulting in an increase in production balance rate to 92.2% and a decrease in smoothness index to 4.33. On the basis of learning from the immune mechanism of biological system, the paper constructed the regulation model of MAMS, and the biological immune response mechanism was used to regulate the MAMS to improve the dynamic response ability of the system. With reference to the biological immune mechanism, the immune agent learning model based on reinforcement learning was constructed to learn the perturbation factors of the manufacturing system uncertainty, which was a single-step decision problem of serialization. In the future research work, according to the characteristics of the MAMS and the immune learning and memory mechanism of the biological system, it can further explore the learning model and learning algorithm, and the immune learning mechanism of the biological system can be better applied to the monitoring model of the MAMS to improve the coordination ability of the system. At the same time, because the research results are not applied in the actual production process, the autonomy and coordination of the intelligent manufacturing units in the actual production process still need to be further improved. In the future, the research model and algorithm will be further explored in this aspect.
The original contributions presented in the study are included in the article/supplementary material, further inquiries can be directed to the corresponding author.
BT: Conceptualization, Data curation, Formal Analysis, Investigation, Methodology, Project administration, Software, Writing–original draft, Writing–review and editing.
The author(s) declare that no financial support was received for the research, authorship, and/or publication of this article.
The authors declare that the research was conducted in the absence of any commercial or financial relationships that could be construed as a potential conflict of interest.
All claims expressed in this article are solely those of the authors and do not necessarily represent those of their affiliated organizations, or those of the publisher, the editors and the reviewers. Any product that may be evaluated in this article, or claim that may be made by its manufacturer, is not guaranteed or endorsed by the publisher.
Bi, M., Kovalenko, I., Tilbury, D. M., and Barton, K. (2021). Dynamic resource allocation using multi-agent control for manufacturing systems. IFAC-PapersOnLine 54 (20), 488–494. doi:10.1016/j.ifacol.2021.11.220
D’Aniello, G., De Falco, M., and Mastrandrea, N. (2021). Designing a multi-agent system architecture for managing distributed operations within cloud manufacturing. Evol. Intell. 14 (4), 2051–2058. doi:10.1007/s12065-020-00390-z
Dittrich, M. A., and Fohlmeister, S. (2020). Cooperative multi-agent system for production control using reinforcement learning. CIRP Ann. 69 (1), 389–392. doi:10.1016/j.cirp.2020.04.005
Dusadeerungsikul, P. O., He, X., Sreeram, M., and Nof, S. Y. (2022). Multi-agent system optimisation in factories of the future: cyber collaborative warehouse study. Int. J. Prod. Res. 60 (20), 6072–6086. doi:10.1080/00207543.2021.1979680
ElMaraghy, H., Monostori, L., Schuh, G., and ElMaraghy, W. (2021). Evolution and future of manufacturing systems. CIRP Ann. 70 (2), 635–658. doi:10.1016/j.cirp.2021.05.008
González, F. A., and Dasgupta, D. (2003). Anomaly detection using real-valued negative selection. Genet. Program. Evolvable Mach. 4 (4), 383–403. doi:10.1023/a:1026195112518
Johnson, D., Chen, G., and Lu, Y. (2022). Multi-agent reinforcement learning for real-time dynamic production scheduling in a robot assembly cell. IEEE Robotics Automation Lett. 7 (3), 7684–7691. doi:10.1109/lra.2022.3184795
Karbalaei, M., Rezaee, S. A., and Farsiani, H. (2020). Pichia pastoris: a highly successful expression system for optimal synthesis of heterologous proteins. J. Cell. Physiology 235 (9), 5867–5881. doi:10.1002/jcp.29583
Kovalenko, I., Balta, E. C., Tilbury, D. M., and Barton, K. (2022). Cooperative product agents to improve manufacturing system flexibility: a model-based decision framework. IEEE Trans. Automation Sci. Eng. 20 (1), 440–457. doi:10.1109/tase.2022.3156384
Latsou, C., Farsi, M., Erkoyuncu, J. A., and Morris, G. (2021). Digital twin integration in multi-agent cyber physical manufacturing systems. IFAC-PapersOnLine 54 (1), 811–816. doi:10.1016/j.ifacol.2021.08.096
Nie, Q., Tang, D., Zhu, H., and Sun, H. (2022). A multi-agent and internet of things framework of digital twin for optimized manufacturing control. Int. J. Comput. Integr. Manuf. 35 (10-11), 1205–1226. doi:10.1080/0951192x.2021.2004619
Seitz, M., Gehlhoff, F., Cruz Salazar, L. A., Fay, A., and Vogel-Heuser, B. (2021). Automation platform independent multi-agent system for robust networks of production resources in industry 4.0. J. Intelligent Manuf. 32 (7), 2023–2041. doi:10.1007/s10845-021-01759-2
Simon, K., Vicent, M., Addah, K., Bamutura, D., Atwiine, B., Nanjebe, D., et al. (2023). Comparison of deep learning techniques in detection of sickle cell disease. AIA 1 (4), 228–235. doi:10.47852/bonviewaia3202853
Turner, E. C. (2021). Possible poriferan body fossils in early Neoproterozoic microbial reefs. Nature 596 (7870), 87–91. doi:10.1038/s41586-021-03773-z
Vanbecelaere, S., Van den Berghe, K., Cornillie, F., Sasanguie, D., Reynvoet, B., and Depaepe, F. (2020). The effectiveness of adaptive versus non-adaptive learning with digital educational games. J. Comput. Assisted Learn. 36 (4), 502–513. doi:10.1111/jcal.12416
Vogel-Heuser, B., Seitz, M., Cruz Salazar, L. A., Gehlhoff, F., Dogan, A., and Fay, A. (2020). Multi-agent systems to enable Industry 4.0. Comput. Sci. Eng. 68 (6), 445–458. doi:10.1515/auto-2020-0004
Wang, G. G., Gao, D., and Pedrycz, W. (2022). Solving multiobjective fuzzy job-shop scheduling problem by a hybrid adaptive differential evolution algorithm. IEEE Trans. Industrial Inf. 18 (12), 8519–8528. doi:10.1109/tii.2022.3165636
Xu, T., Wang, H., Feng, L., and Zhu, Y. (2024). Risk factors assessment of smart supply chain in intelligent manufacturing services using DEMATEL method with linguistic q-ROF information. J. Operations Intell. 2 (1), 129–152. doi:10.31181/jopi21202417
Yahouni, Z., Ladj, A., Belkadi, F., Meski, O., and Ritou, M. (2021). A smart reporting framework as an application of multi-agent system in machining industry. Int. J. Comput. Integr. Manuf. 34 (5), 470–486. doi:10.1080/0951192x.2021.1901312
Keywords: manufacturing systems, recursive structure, intelligent agents, immune mechanism, negative selection algorithm
Citation: Teng B (2025) An intelligent manufacturing system based on a recursive control structure. Front. Mech. Eng. 10:1437198. doi: 10.3389/fmech.2024.1437198
Received: 23 May 2024; Accepted: 11 December 2024;
Published: 07 January 2025.
Edited by:
Vamsi Krishna Balla, Central Glass and Ceramic Research Institute (CSIR), IndiaReviewed by:
Shohin Aheleroff, SUEZ Smart Solutions, New ZealandCopyright © 2025 Teng. This is an open-access article distributed under the terms of the Creative Commons Attribution License (CC BY). The use, distribution or reproduction in other forums is permitted, provided the original author(s) and the copyright owner(s) are credited and that the original publication in this journal is cited, in accordance with accepted academic practice. No use, distribution or reproduction is permitted which does not comply with these terms.
*Correspondence: Bingyan Teng, dGJ5ODgwMzA5QDEyNi5jb20=
Disclaimer: All claims expressed in this article are solely those of the authors and do not necessarily represent those of their affiliated organizations, or those of the publisher, the editors and the reviewers. Any product that may be evaluated in this article or claim that may be made by its manufacturer is not guaranteed or endorsed by the publisher.
Research integrity at Frontiers
Learn more about the work of our research integrity team to safeguard the quality of each article we publish.