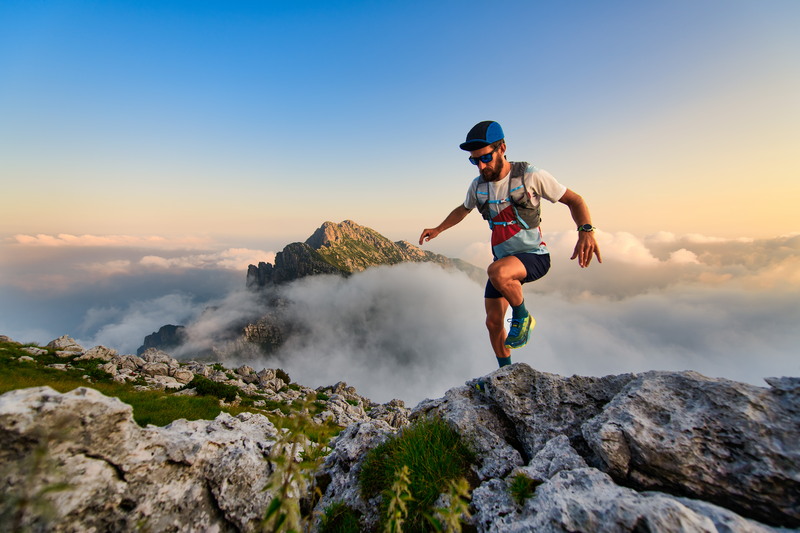
95% of researchers rate our articles as excellent or good
Learn more about the work of our research integrity team to safeguard the quality of each article we publish.
Find out more
ORIGINAL RESEARCH article
Front. Mech. Eng. , 21 February 2024
Sec. Tribology
Volume 10 - 2024 | https://doi.org/10.3389/fmech.2024.1365555
This article is part of the Research Topic Advancements in Thin Film Coating Technologies View all 4 articles
The tribomechanical characteristics of diamond-like carbon (DLC) coatings are notably superior to other hard coatings, making them highly desirable for industrial applications. This study focuses on the synthesis of nitrogen-doped DLC (N-DLC) films through chemical vapor deposition (CVD) methods, with an emphasis on varying the deposition temperature. Comprehensive characterization techniques such as atomic force microscopy (AFM), scanning electron microscopy (SEM), and nanoindentation were employed to investigate the morphological and mechanical attributes of these coatings. The thickness of the films, measured using a Dektak profilometer, demonstrated an increase from 1.9 to 2.8 µm as the deposition temperature rose. Nanoindentation testing revealed that the film deposited at 900°C exhibited the highest hardness (H) and modulus of elasticity (E), measuring 21.95 and 208.3 GPa, respectively. Conversely, the film deposited at 1,000°C showed the lowest values, with H and E at 14.23a and 141.9 GPa, respectively. The H/E ratio of the coatings initially rose from 0.096 to 0.106 as the deposition temperature increased from 800°C to 900°C. However, for deposition temperatures exceeding 900°C the H/E ratio began to decline.
The development of hard and highly wear-resistant materials is crucial for enhancing the longevity of mechanical components operating in demanding environments (Kalita et al., 2022; Ghadai et al., 2021a). To address this industrial requirement, coatings with superior hardness are often employed for their wear resistance capabilities (Vikram et al., 2020; Ghadai et al., 2021b). Carbon-based coatings, known for their exceptional performance in tribological applications, are increasingly adopted for mechanical parts such as bearings, gears, and various drivetrain components (Vikram et al., 2021). These coatings are primarily categorized into two types: diamond-like carbon (DLC) and ceramic coatings. Ceramic coatings, characterized by their high hardness and modulus, are extensively applied to steel components to provide protection against abrasive wear. Conversely, DLC coatings, typically amorphous and composed of a mixture of sp2 and sp3 hybridized carbon-carbon (C–C) and carbon-hydrogen (C–H) bonds (Kashyap and Ramkumar, 2022; Ghadai et al., 2023), are known for their low friction coefficients and enhanced wear resistance, especially when used in conjunction with steel counterfaces. The frictional heat generated during sliding contacts can cause the sp2 hybridized carbon in DLC to form a graphite-like tribolayer, which helps in reducing or stabilizing friction via a velocity accommodation mechanism. However, without meticulous deposition techniques, DLC coatings are prone to significant spalling and delamination, primarily due to the high internal compressive residual stress.
The properties of the DLC films can be improved by incorporating various metals, semiconductors like Co, Fe, Ti, W, Al, Si, etc., and this kind of coating can find more suitable for the industrial application (Ghadai et al., 2019; Ghadai et al., 2018; Kumar et al., 2010). However, from the available literature it is observed that nitrogen (N2) can significantly enhance the adhesion between the substrate and film by decreasing the internal stress. The doping of nitrogen can also improve the tribomechanical characteristics of the coatings. Moreover, N2 doped coatings enhances the bond strength due to the possible creation of C–N, C–N–C, bonds (Kalita and Ghadai, 2022). The potential industrial application of the N-DLC film are the coating used in critical engine parts, mechanical face seals, magnetic hard discs, surgical tools, etc. (Prabhukumar et al., 2023). Zeng et al. (2017) reported the enhancement of the tribomechanical properties of N-DLC coating by incorporating N2 gas into the chamber. Ghadai et al. (2021c) synthesized nitrogen incorporated diamond-like carbon (N-DLC) films using atmospheric pressure chemical vapor deposition (APCVD) method by altering the N2 flow rates. The results showed an improvement in the tribomechanical properties of CVD deposited coating compared to other PVD deposited coatings. Chen et al. (2017) carried out research experiments for achieving low wear and low Friction under different humidity conditions by incorporating silicon (Si) and nitrogen (N2) in to the carbon coating by using RFCVD method. The film then characterised by nanoindentation, Raman Spectroscopy, XPS, and FTIR methods. The results showed that by the incorporating N2 and Si the friction coefficient and wear rate decreased. Lukaszkowicz et al. studied the characteristics of DLC coating synthesized by PACVD process on the hot work tool steel. It tribological and mechanical characteristics by methods like Raman Spectroscopy, HRTEM, SEM, Scratch test, Ball-on disc methods and the results showed that the mechanical properties of the coating synthesized using PACVD enhanced as compared to other synthesis methods (Lukaszkowicz and Paradecka, 2016). Khatir et al. (2015) observed the excellent biocompatibility and tribological properties of N-DLC coating. Lee et al. (2016) reported the hardness and young’s modulus of N-DLC film synthesized using unbalanced magnetron sputtering and found that both hardness and young’s modulus of the film increased with the increase of N2 flow rate. Das et al. (2020) deposited TiCN coatings using thermal CVD at high temperature by varying the N2 flow rate and observed that N2 flowrate has a significant effect over the tribomechanical properties of TICN coatings at high temperature.
Shu et al. (2024) contributed to this field by enhancing the performance of Ni–P molds used in precision glass molding. By depositing Ti/Ti-DLC layers using Filtered Cathodic Vacuum Arc (FCVA), they significantly improved the wear resistance and stability of these molds. Similarly, Ren et al. (2024) utilized FCVA for depositing hydrogen-free DLC on magnesium alloys, discovering that certain bias voltages yielded optimal anti-corrosion properties. The tribological behavior of DLC coatings was further explored by Milewski et al. (2024), who applied these coatings on steel in the lime industry using Plasma Enhanced Chemical Vapor Deposition (PECVD). Their study focused on evaluating the coatings’ performance under harsh conditions. Tian et al. (2024) also employed PECVD, but their work was directed towards enhancing DLC film properties on carbide substrates for cutting tools, varying enhancement modes and bias voltages.
In terms of specific applications, Sawka et al. (2024) used 3D-printed models and Particle Image Velocimetry (PIV) to study the fluid flow in Extracorporeal Membrane Oxygenation (ECMO) cannulas. They found that bicaval 13 Fr DLCs caused the most hemolysis, providing valuable insights into medical device design. On the other hand, Yang et al. (2024) focused on improving rubber wear resistance by depositing N-DLC films, demonstrating superior tribological performance at certain nitrogen flow rates. Ghadai et al. synthesized N-DLC coating using thermal CVD techniques and observed that the mechanical and tribological properties of the DLC coating by the incorporation nitrogen (Ghadai et al., 2021c). Guo et al. developed multilayer DLC coatings [(Cr, N)-DLC/DLC] with different sp3 contents on YG8 (WC-Co) substrates by FCVA combined with DCVA technique. The results showed that the multilayer coatings possess excellent wear resistance and very good adhesion to YG8 Guo et al. (2015); Stojanovic and Glisovic, 2021).
Furthering the scope of DLC coatings, Song et al. (2024) compared coatings with methane and acetylene pre-gases on steel. They reported that DLC coatings with methane (DLC-CH4) showed superior corrosion resistance and a smoother surface. Similarly, Ramírez-Reyna et al. (2024) assessed various coatings including DLC, WC, and WCN on steel for bearings. Their findings suggested that the DLC/WC/WCN/W system offered the best wear resistance. In a different vein, Kim et al. (2024) optimized N-DLC coatings on glass for improved transmittance and electrical properties, altering the carbon bonding through pulsed-DC bias. This study exemplifies the versatility of DLC coatings beyond traditional mechanical applications.
Dai et al. (2024) took a unique approach by studying DLC films deposited at varying angles, revealing that certain angles led to optimal tribological performance and lower surface roughness. This finding opens new avenues for customizing DLC coatings for specific applications. Additionally, Guo et al. (2024) highlighted the importance of Coulomb interactions in the adsorption and structure of potassium salt molecules on DLC surfaces, a crucial aspect in chemical applications of DLC coatings. Wu et al. (2024), through extensive testing, demonstrated the enhanced loading capacity and wear resistance of 18CrNiMo7-6 gears with DLC coatings, reaffirming the material’s utility in heavy machinery. Ghadai et al. studied the effect of deposition temperature over the mechanical properties of thermal CVD deposited Al-DLC thin film coating. Their results showed that deposition temperature has a significant effect of the structural and mechanical properties of the coatings (Ghadai et al., 2023).
From the above literature it is observed that nitrogen doped DLC coatings have a wide industrial application in the field of protective coatings. By the incorporation nitrogen into DLC film the mechanical and tribological properties can significantly enhanced. Many authors have developed the coating by using various physical vapour deposition techniques particularly magnetron sputtering. Few papers were found where APCVD is used for the development of the coating. Also, in APCVD different process parameters can affect the properties of the coating. Among the process parameters deposition temperature can be considered as a vital one and the variation of deposition temperature for the development of N-DLC coating using APCVD are not extensively studied by the researchers. So present work aimed on the development and testing of N-DLC coating with the variation of deposition temperature.
In this study, nitrogen-doped diamond-like carbon (DLC) thin films were synthesized on Si (100) substrates using the Atmospheric Pressure Chemical Vapor Deposition (APCVD) process. The preparation of Si substrates involved a 2-min immersion in 2% hydrofluoric (HF) acid solution, followed by a 15-min ultrasonic cleaning in deionized water to eliminate the oxide layer. Subsequently, the substrates were removed from the solution and gently dried with clean, soft cloths. For the DLC film deposition on Si substrates, the nitrogen (N2) flow rate was set at 20 standard cubic centimeters per minute (sccm). The experiment produced five distinct samples by varying the deposition temperature between 800°C and 1,000°C, while keeping the acetylene (C2H2) flow rate and deposition time constant at 5 sccm and 120 min, respectively. The heating rate during the experiment was maintained at 5°C per minute, and the cooling rate at 3°C per minute. The base pressure for the process was kept at 5 × 10−6 Torr, and the process pressure at 500 mTorr. Morphological analysis of the DLC coatings was conducted using a Scanning Electron Microscopy (SEM) (JEOL, JSM 5510) with a magnification capability of up to ×100,000. A Dektak profilometer, equipped with a 2.5 μm radius stylus, was utilized to measure the film thickness. During this measurement, the profilometer’s stylus traversed each sample at four different points at a consistent speed, and the average step height was recorded for each pass. Nanoindentation tests were performed using a CSM instrument (model NHTX 55–0019) with a Berkovich indenter tip of 20 μm radius, applying a constant load of 10 mN.
Figure 1 show the 3-D and 2-D images of DLC thin film with respect to various deposition temperature. From the figure it is noticed that the roughness of the film increases with the increase of synthesis temperature. It is also observed that the roughness of the film deposited at 800°C is 46.7 nm and it decreased to 41.3 nm for the film deposited at 850°C. However further increase in temperature tends to increase the roughness of the film and the film deposited at 1,000°C becomes rougher as compared to all the samples. The increase in roughness may be due to the increase of randomness of gas particles within the chamber at high temperature (Das et al., 2023a). The film thickness of the coating increased from 1.9 to 2.8 µm with increase of deposition temperature (Mwema et al., 2018). The increase of coating thickness with increase of the deposition temperature may be due to the higher deposition rate of carbon at elevated temperature. The details of the film thickness and roughness of all five samples are presented in Table 1.
TABLE 1. Variation of film thick ness and roughness of the film with respect to various deposition temperature.
To support the AFM images Figure 2 shows the SEM images of DLC thin film coating with respect to various deposition temperature. The SEM images presented in Figure 2 have been taken at a magnification rage of ×1105. From the figure it is observed that the film is even enough and there are no unwanted pores throughout the substrate. Overall, it is noticed that the pattern of the surface is even, and the deposited film is equally developed throughout the surface. The film deposited at higher deposition temperature (particularly at 950 and 1,000°C) seems to be rougher as compared to other samples and similar results were also observed from AFM (Das et al., 2023a). It is also observed that at high temperature some agglomerated particles are form over the substrate. This agglomeration over the surface may be due to the irregularities in nucleation and growth of the coatings (Mwema et al., 2018).
Figure 3 shows the load–displacement curve of the DLC thin film synthesized at various deposition temperature with a maximum indentation load of 10 mN. The area under the load displacement curve shows the energy lost during plastic deformation. From the figure it has been observed that DLC thin film deposited at a deposition temperature of 900°C has lowest depth of indentation whereas the film deposited at 1,000°C has highest depth of indentation. The Hardness (H) and young’s modulus (E) of the films can be predicted from the load displacement curve. From the indentation depth in can be predicted that DLC film deposited at 900°C will have highest H and E whereas film deposited at 1,000°C will have lowest hardness. However, the H and E of the coatings have been calculated by examining the unloading part of the loading - unloading curve. The H and E can be evaluated by using Eqs. 1–3 (Das et al., 2023b).
Where Fmax and A are the maximum load applied over the work piece and contact area of the tip of the indenter over the substrate, respectively.
The stiffness (S) can be computed, by using Eq. 2 and it is presented below.
The elastic modulus of the film (Ew) can be calculated by the help of Equation 3
Where “S” defines the stiffness, and it can be calculated from the upper portion of the load-displacement curve and it gives the geometry independent eq. (
Figure 5 illustrates the changes in H/E and H3/E2 ratios of N-DLC thin films in relation to deposition temperatures ranging from 800°C to 1,000°C. These ratios are indicative of the films’ elastic-plastic characteristics (Charitidis and Logothetidis, 2005), as well as their wear properties. For instance, a typical diamond has H/E around 0.1, with hardness (H) and modulus of elasticity (E) values approximately 100 GPa and 1,000 GPa, respectively. The analysis of the figure reveals that the H/E ratio of the coatings initially rose from 0.096 to 0.106 as the deposition temperature increased from 800°C to 900°C. However, the H/E ratio began to decline for deposition temperatures exceeding 900°C. The H/E ratio reached a peak of 0.106 for films deposited at a C2H2 flow rate above 8 sccm. In a similar pattern, the H3/E2 ratio mirrored the H/E trend. Musil (Musil, 2012) has noted that films with H/E ratios greater than or equal to 0.1 are more resistant to cracking. A higher H3/E2 value indicates greater elasticity in the film, while a lower value suggests more pronounced plasticity. The observed variations in H/E and H3/E2 could be attributed to grain boundary sliding phenomena.
Figure 6 shows the variation of residual stress (σ) of N-DLC coatings with respect to the deposition temperature. The σ of the coatings has been computed by using the Stoney equation given in Eq. 4
From the results, it is observed that σ of the DLC films is compressive in nature and the σ increases from 1.98 to 3.06 GPa with the increase of the deposition temperature from 800°C to 900°C. However, σ of the DLC film decreased while the deposition temperature increased above 900°C. Due to the increase of the deposition temperature above 900°C the soft graphite-like sp2 increases in the DLC films which tends reduces the σ (Kumar et al., 2010).
The present work reports the effects of deposition temperature over the morphological and tribomechanical properties of CVD deposited N-DLC coatings. From the results it is observed that the variation of deposition temperature can significantly affect the properties of the coatings. AFM results showed that the surface roughness of the film increases with the increase in temperature from 850°C to 1,000°C. The hardness and young’s modulus of the coating initially increased with the increase of deposition temperature from 800 to 900°C. However, the H and E of the film decreased with further increase of deposition temperature above 900°C. The residual stress of the DLC films is compressive in nature and the σ increases from 1.98 to 3.06 GPa with the increase of the deposition temperature from 800 to 900°C. However, σ of the DLC film decreased while the deposition temperature increased above 900°C.
The original contributions presented in the study are included in the article/supplementary material, further inquiries can be directed to the corresponding author.
GS: Conceptualization, Formal Analysis, Investigation, Methodology, Writing–original draft. MV: Conceptualization, Formal Analysis, Investigation, Methodology, Writing–original draft. KL Conceptualization, Methodology, Resources, Writing–original draft. LC: Conceptualization, Resources, Writing–review and editing. ME: Conceptualization, Methodology, Resources, Writing–original draft.
The author(s) declare that no financial support was received for the research, authorship, and/or publication of this article.
Author ME was employed by Bond Marine Consultancy.
The remaining authors declare that the research was conducted in the absence of any commercial or financial relationships that could be construed as a potential conflict of interest.
All claims expressed in this article are solely those of the authors and do not necessarily represent those of their affiliated organizations, or those of the publisher, the editors and the reviewers. Any product that may be evaluated in this article, or claim that may be made by its manufacturer, is not guaranteed or endorsed by the publisher.
Charitidis, C. A., and Logothetidis, S. (2005). Effects of normal load on nanotribological properties of sputtered carbon nitride films. Diam. Relat. Mater 14, 98–108. doi:10.1016/j.diamond.2004.07.022
Chen, T., Wu, X., Ge, Z., Ruan, J., Lv, B., and Zhang, J. (2017). Achieving low friction and wear under various humidity conditions by co-doping nitrogen and silicon into diamond-like carbon films. Thin Solid Films 638, 375–382. doi:10.1016/j.tsf.2017.07.072
Dai, W., Shi, Y., Wang, Q., and Wang, J. (2024). Smooth diamond-like carbon films prepared by cathodic vacuum arc deposition with large glancing angles. Diam. Relat. Mater. 141, 110672. doi:10.1016/j.diamond.2023.110672
Das, S., Guha, S., Das, P. P., and Ghadai, R. K. (2020). Analysis of morphological, microstructural, electrochemical and nano mechanical characteristics of TiCN coatings prepared under N2 gas flow rate by chemical vapour deposition (CVD) process at higher temperature. Ceram. Int. 46, 10292–10298. doi:10.1016/j.ceramint.2020.01.023
Das, S., Guha, S., and Ghadai, R. K. (2023b). Influence of post-heat treatment over structural network and mechanical properties of carbon (C)-incorporated CVD TiCN thin-film coating. Carbon Lett. 33, 1073–1094. doi:10.1007/s42823-023-00499-y
Das, S., Protim Das, P. P., Ghadai, R. K., and Guha, S. (2023a). Improvising CODAS method functionalized with grey numbers to improve the performance of PVD titanium carbon nitride (TiCN) thin film coating: a novel approach. Phys. Scr 98, 125928. doi:10.1088/1402-4896/ad081f
Ghadai, R. K., Das, S., Kalita, K., Shivakoti, I., Mondal, S. C., and Swain, B. P. (2021c). Effect of nitrogen (N2) flow rate over the tribological, structural and mechanical properties diamond-like carbon (DLC) thin film. Mater Chem. Phys. 260, 124082. doi:10.1016/j.matchemphys.2020.124082
Ghadai, R. K., Das, S., Kalita, K., Swain, B. P., and Davim, J. P. (2021a). Structural and mechanical analysis of APCVD deposited diamond-like carbon thin films. Silicon 13, 4453–4462. doi:10.1007/s12633-020-00760-3
Ghadai, R. K., Das, S., Kumar, D., Mondal, S. C., and Swain, B. P. (2018). Correlation between structural and mechanical properties of silicon doped DLC thin films. Diam. Relat. Mater 82, 25–32. doi:10.1016/j.diamond.2017.12.012
Ghadai, R. K., and Kalita, K. (2020). Accurate estimation of DLC thin film hardness using genetic programming. Int. J. Mater Res. 111, 453–462. doi:10.3139/146.111911
Ghadai, R. K., Kalita, K., Mondal, S. C., and Swain, B. P. (2019). Genetically optimized diamond-like carbon thin film coatings. Mater Manuf. Process. 34, 1476–1487. doi:10.1080/10426914.2019.1594273
Ghadai, R. K., Shanmugasundar, G., Cepova, L., Das, S., Kumar Mahto, P., and Kalita, K. (2023). A temperature-based synthesis and characterization study of aluminum-incorporated diamond-like carbon thin films. Front. Mech. Eng. 9, 1325040. doi:10.3389/fmech.2023.1325040
Ghadai, R. K., Singh, K., Sharma, A., Roy, M. K., and Swain, B. P. (2021b). “Mechanical and Tribological properties of metal incorporated DLC thin film,” in Nanostructured materials and their applications, 229–263. doi:10.1007/978-981-15-8307-0_12
Guo, C. Q., Pei, Z. L., Fan, D., Gong, J., and Sun, C. (2015). Microstructure and tribomechanical properties of (Cr, N)-DLC/DLC multilayer films deposited by a combination of filtered and direct cathodic vacuum arcs. Diam. Relat. Mater. 60, 66–74. doi:10.1016/j.diamond.2015.10.019
Guo, S., Zhao, Z., Sun, T., Cao, Y., Luo, Y., and Xiao, S. (2024). Adsorption of fatty acid potassium salts on diamond-like carbon: effects of alkyl chain lengths and adsorptive conditions. Appl. Surf. Sci. 643, 158717. doi:10.1016/j.apsusc.2023.158717
Kalita, K., and Ghadai, R. K. (2022). Optimization of plasma enhanced chemical vapor deposition process parameters for hardness improvement of diamond-like carbon coatings. Sci. Iran. 29, 1795–1805. doi:10.24200/SCI.2022.56869.4952
Kalita, K., Ghadai, R. K., and Chakraborty, S. (2022). Parametric optimization of CVD process for DLC Thin film coatings: a comparative analysis. Sādhanā 47, 57. doi:10.1007/s12046-022-01842-1
Kashyap, V., and Ramkumar, P. (2022). DLC coating over pre-oxidized and textured Ti6Al4V for superior adhesion and tribo-performance of hip implant. Surf. Coat. Technol. 440, 128492. doi:10.1016/j.surfcoat.2022.128492
Khatir, S., Hirose, A., and Xiao, C. (2015). Characterization of physical and biomedical properties of nitrogenated diamond-like carbon films coated on polytetrafluoroethylene substrates. Diam. Relat. Mater 58, 205–213. doi:10.1016/j.diamond.2015.08.003
Kim, J.-I., Lee, W.-Y., Tanaka, K., Tokoroyama, T., Murashima, M., and Umehara, N. (2024). Nitrogen-containing diamond-like carbon deposited on glass substrate via filtered cathodic vacuum arc with high-frequency pulsed DC substrate bias. Surfaces Interfaces 44, 103695. doi:10.1016/j.surfin.2023.103695
Kumar, S., Dwivedi, N., Rauthan, C. M. S., and Panwar, O. S. (2010). Properties of nitrogen diluted hydrogenated amorphous carbon (n-type a-C:H) films and their realization in n-type a-C:H/p-type crystalline silicon heterojunction diodes. Vacuum 84, 882–889. doi:10.1016/j.vacuum.2009.12.003
Lee, J., Choi, B. H., Yun, J. H., and Park, Y. S. (2016). Characteristics of nitrogen doped diamond-like carbon films prepared by unbalanced magnetron sputtering for electronic devices. J. Nanosci. Nanotechnol. 16, 4893–4896. doi:10.1166/jnn.2016.12225
Lukaszkowicz, K., and Paradecka, A. (2016). Characteristics of diamond-like carbon (DLC) film deposited by PACVD process. Mater. Engineering-Materiálovéinžinierstvo (MEMI) 23, 132–137.
Milewski, K., Piotrowska, K., and Madej, M. (2024). Assessment of the properties of diamond-like carbon coatings (dlc) used in the lime industry. Metalurgija 63, 81–84.
Musil, J. (2012). Hard nanocomposite coatings: thermal stability, oxidation resistance and toughness. Surf. Coat. Technol. 207, 50–65. doi:10.1016/j.surfcoat.2012.05.073
Mwema, F. M., Oladijo, O. P., Sathiaraj, T. S., and Akinlabi, E. T. (2018). Atomic force microscopy analysis of surface topography of pure thin aluminum films. Materials Research Express 5 (4), 046416. doi:10.1088/2053-1591/aabe1b
Oliver, W. C., and Pharr, G. M. (1992). An improved technique for determining hardness and elastic modulus using load and displacement sensing indentation experiments. J. Mater Res. 7, 1564–1583. doi:10.1557/jmr.1992.1564
Prabhukumar, S., Chohan, J. S., and Kalita, K. (2023). “MEREC-MABAC based-parametric optimization of chemical vapour deposition process for diamond-like carbon coatings,” in International conference on intelligent computing and optimization. doi:10.1007/978-3-031-50158-6_41
Ramírez-Reyna, O., Pérez-Alvarez, J., Flores-Martínez, M., Rodríguez-Castro, G. A., and Rodil, S. E. (2024). Evaluation of mechanical properties and tribological behavior of DLC/WC/WCN/W multilayer coatings deposited by HiPIMS. Mater. Lett. 357, 135737. doi:10.1016/j.matlet.2023.135737
Ren, L., Liu, X., Cao, H., Tang, Y., Qi, F., Zhao, N., et al. (2024). Mechanical and corrosion properties of hydrogen-free DLC coatings prepared on degradable as-extruded WE43 alloy using FCVA technology. Surf. Coatings Technol. 476, 130293. doi:10.1016/j.surfcoat.2023.130293
Sawka, D. M., Su, Y., Monteagudo, J., and Zenit, R. (2024). Fluid flow analysis of neonatal dual-lumen cannulas for venovenous extracorporeal Membrane oxygenation. J. biomechanical Eng. 146, 021008. doi:10.1115/1.4064212
Shu, C., Yin, S., and Huang, S. (2024). Preparation and performance of Ti/Ti-DLC composite coatings for precision glass molding. Ceram. Int. 50, 5210–5223. doi:10.1016/j.ceramint.2023.11.267
Song, J., Tian, H., Li, J., Zhang, P., and Sun, A. (2024). Effect of methane and acetylene pre-gases on the corrosion resistance of DLC coatings. Vacuum 221, 112899. doi:10.1016/j.vacuum.2023.112899
Stojanovic, B., and Glisovic, J. (2021). “Application of ceramic matrix composite in automotive industry,” in Encyclopedia of materials: composites (Elsevier), 275–292. doi:10.1016/B978-0-12-819724-0.00018-5
Tian, H., Jie, S., Zhang, P., Li, J., and An, S. (2024). Effects of deposited particle energy on the structure and properties of diamond-like carbon films. Diam. Relat. Mater. 141, 110671. doi:10.1016/j.diamond.2023.110671
Vikram, K., Kalita, K., and Ghadai, R. K. (2020). Multi-attribute optimization of diamond-like carbon thin films. AIP Conf. Proc. 2273. doi:10.1063/5.0024626
Vikram, K., Ragavendran, U., Kalita, K., Kumar Ghadai, R. K., and Gao, X. Z. (2021). Hybrid metamodel-NSGA-III-EDAS based optimal design of thin film coatings. Comput. Mater Contin. 66, 1771–1784. doi:10.32604/cmc.2020.013946
Wu, J., Wei, P., Liu, G., Chen, D., Zhang, X., Chen, T., et al. (2024). A comprehensive evaluation of DLC coating on gear bending fatigue, contact fatigue, and scuffing performance. Wear 536-537, 205177. doi:10.1016/j.wear.2023.205177
Yang, T., Xie, M., Wang, W., Wang, C., Qi, X., Deng, Q., et al. (2024). Low friction and wear of Nitrogen-doped diamond-like carbon films deposited on NBR with different flows of N2 by DC-MS. Vacuum 220, 112774. doi:10.1016/j.vacuum.2023.112774
Keywords: nitrogen-doped diamond-like carbon, tribomechanical properties, chemical vapor deposition, nanoindentation, deposition temperature
Citation: Shanmugasundar G, Vanitha M, Logesh K, Cepova L and Elangovan M (2024) Effect of deposition temperature on the tribo-mechanical properties of nitrogen doped DLC thin film. Front. Mech. Eng 10:1365555. doi: 10.3389/fmech.2024.1365555
Received: 04 January 2024; Accepted: 08 February 2024;
Published: 21 February 2024.
Edited by:
Lokeswar Patnaik, National Institute of Advanced Manufacturing Technology (Formerly NIFFT), IndiaReviewed by:
Prosun Mandal, National Institute of Technology, Silchar, IndiaCopyright © 2024 Shanmugasundar, Vanitha, Logesh, Cepova and Elangovan. This is an open-access article distributed under the terms of the Creative Commons Attribution License (CC BY). The use, distribution or reproduction in other forums is permitted, provided the original author(s) and the copyright owner(s) are credited and that the original publication in this journal is cited, in accordance with accepted academic practice. No use, distribution or reproduction is permitted which does not comply with these terms.
*Correspondence: Muniyandy Elangovan, bXVuaXlhbmR5LmVAZ21haWwuY29t
†ORCID: G. Shanmugasundar, orcid.org/0000-0002-5608-7737; M. Vanitha, orcid.org/0000-0001-7539-126X
Disclaimer: All claims expressed in this article are solely those of the authors and do not necessarily represent those of their affiliated organizations, or those of the publisher, the editors and the reviewers. Any product that may be evaluated in this article or claim that may be made by its manufacturer is not guaranteed or endorsed by the publisher.
Research integrity at Frontiers
Learn more about the work of our research integrity team to safeguard the quality of each article we publish.