- Chair of Materials Engineering, Faculty of Material Engineering and Physics, Cracow University of Technology, Cracow, Poland
Diatomaceous earth (diatomite) is a material that exhibits unique properties that can be used in many areas of the economy. The use of diatomite as a sorbent for absorbing oil substances has been known for many years. Diatomite, thanks to its structure, acts like a sponge, absorbing oil substances. Its micropores increase the surface area in contact with the pollutant, which speeds up the absorption process. Diatomite is used to clean up oil spills on land and water, secure industrial sites, treat wastewater, and manage pollution at ports and oil ports. Many scientific papers to date have focused on evaluating the potential of diatomite as a medium for petroleum substances. Still, there is little mention of the potential for using diatomite as a carrier for paraffinic PCMs. Paraffins are synthetic compounds obtained by distillation from a specific fraction of crude oil. This paper presents a study of the physicochemical properties of diatomite with a view to its subsequent use as a medium for absorbing paraffinic phase change materials. Thanks to its high porosity, high specific surface area, low density, and chemical inertness, this material is an ideal medium for paraffinic substances. In addition, its most important feature is the absence of desorption. A new type of environmentally friendly and cheap phase change materials may contribute to the increase in the use of this type of materials in construction. The benefits of using PCM materials are known.
1 Introduction
Diatomite, also known as diatomaceous earth, is a naturally occurring, soft, siliceous sedimentary rock consisting mainly of the fossilized remains of diatoms, which are single-celled algae. The main chemical constituent of diatomite is silica (SiO₂), along with smaller amounts of aluminum oxide (Al₂O₃), iron oxide (Fe₂O₃), calcium oxide (CaO), magnesium oxide (MgO) and organic matter (Wu et al., 2019; Liu et al., 2018; Zahajská et al., 2020; Reka et al., 2021a; Reka et al., 2021b). Its unique properties, including high porosity, low density, and high surface area, make it a valuable material in various industrial applications (Wu et al., 2019; Chu et al., 2008; Ferreira et al., 2024; Mejía et al., 2016).
Diatomite deposits are important both in Poland and around the world due to their unique properties and diverse applications. In Poland, diatomite deposits are in the Podkarpackie province, in the Przemyśl district of Jawornik Ruski. Diatomite mining in Poland has been used for various industrial applications, including filtration, insulation, and as a filler in building materials (Dobrosielska et al., 2021; Omar et al., 2022; Gondek et al., 2023; Nykiel et al., 2024). Mining methods often involve surface mining, which is effective for accessing the relatively shallow deposits found in the region (Dobrosielska et al., 2021; Łach et al., 2023; Marczyk et al., 2022).
Diatomite deposits are widespread around the world, with significant re-zerves in the United States, particularly in California, where the Monterey Formation is home to one of the largest commercial diatomite deposits (Moyle and Dolley, 2003). Other significant deposits are located in countries such as Turkey, Kazakhstan, and Algeria, and each exhibits unique geological characteristics that affect their re-inventory applications (Caner et al., 2015; Meradi et al., 2016). The global market for diatomite is driven by its applications in various industries, including agriculture, construction, and environmental management, due to its high porosity, lightweight, and chemical stability (Chu et al., 2008; Wang et al., 2014; Du et al., 2022).
Diatomite’s physical and chemical properties, such as its high specific surface area and porosity, make it an excellent material for use in filtration systems, as it can effectively remove impurities from liquids (Caner et al., 2015; Xiang et al., 2013). In addition, its thermal insulating properties have led to its use in construction materials, where it serves as a pozzolanic additive in cement and mortar formulations (Abrão et al., 2019). The versatility of diatomite is further enhanced by its ability to act as an adsorbent of pollutants, making it valuable in environmental applications such as wastewater treatment (Chu et al., 2008; Cuellar et al., 2018). Diatomite deposits in Poland and around the world are characterized by high silica content and uniquely physical properties that facilitate a wide range of industrial applications. Ongoing research and development in the use of diatomite continues to expand its applications, highlighting its importance as a natural resource.
The porous structure of diatomite contributes significantly to its functionality. Diatomite has a high void content, which increases its adsorption capacity, making it suitable for applications such as filter media, adsorbents, and catalyst carriers (Wu et al., 2019; Chu et al., 2008; Mao et al., 2013). Moreover, diatomite’s unique microstructure allows it to be used in various advanced applications, including as a phase change material (PCM) for thermal energy storage. Its high specific surface area facilitates the absorption of phase-change materials, which can be used in building materials to improve energy efficiency (Fořt et al., 2015; Zhang et al., 2012). Diatomite’s ability to enhance the performance of photocatalytic materials has also been investigated, where its porosity helps disperse active ingredients, thereby improving photocatalytic performance (Cui et al., 2021).
Diatomite is a versatile material characterized by its high silica content, porosity, and unique physical properties. Its applications span various fields, including construction, environmental engineering, and materials science, where it serves as a filler, adsorbent, and thermal energy storage medium. Diatomite has attracted attention as a promising energy storage medium, particularly in the context of thermal energy storage (TES) systems. Its unique properties, including its highly porous structure, low density, and excellent absorption capacity, make it an ideal candidate for supporting phase change materials (PCMs) (Qian et al., 2015a; Qian et al., 2015b; Benayache et al., 2018; Zhang et al., 2018; Zhang et al., 2021). Diatomite’s high porosity, which can reach 80%–90%, allows for significant encapsulation of PCMs, increasing their heat storage capabilities while reducing the risks associated with flammability and leakage (Guo et al., 2018; Costa et al., 2020; Lorwanishpaisarn et al., 2017; Li et al., 2014).
The integration of diatomite with various PCMs has been widely studied, revealing its effectiveness in stabilizing these materials during phase transitions. For example, the porous structure of diatomite not only accommodates PCMs, but also increases thermal conductivity, which is crucial for efficient energy transfer (Guo et al., 2018; Fu et al., 2015; Xu and Li, 2013; Sun et al., 2013). Studies indicate that composites formed from diatomite and fatty acids, or paraffin show better reliability and thermal stability, exhibiting minimal leakage during thermal cycling (Konuklu, 2020; Konuklu et al., 2015). The incorporation of diatomite into PCM formulations has been shown to yield stable composites that retain their structural integrity while effectively storing and releasing thermal energy (Zong et al., 2021; Qian et al., 2016).
Studies have shown that the interaction between diatomite and PCM can lead to increased thermal stability and improved heat transfer efficiency (Khezri and Fazli, 2018; Qian et al., 2017). For example, the addition of diatomite to polyethylene glycol (PEG) not only stabilizes the PCM but also increases its melting point and latent heat capacity, making it more effective in thermal energy storage applications (Qian et al., 2015b; Qian et al., 2016). Diatomite’s ability to effectively absorb and dissipate energy also helps reduce thermal fluctuations in building materials, thus contributing to energy efficiency in construction (Fořt et al., 2015).
Diatomite serves as a versatile and effective energy carrier, especially in the field of thermal energy storage. Its unique physical and chemical properties allow it to enhance the performance of phase-change materials, making it a valuable component in the development of sustainable energy solutions. Ongoing research on diatomite-based composites continues to reveal new opportunities for improving energy storage technology, highlighting its importance in the fields of materials science and energy management. In this article, the physical and chemical properties of diatomite were studied, and finished diatomite granules containing 60 wt.% paraffin were produced. The granules were divided into different fractions and their key thermal properties such as thermal conductivity and specific heat were studied. The study aimed to determine the performance of diatomite granules representing different particle sizes for their subsequent use in lightweight functional geopolymer foams for construction applications. In this study, the energy efficiency of diatomite granules from paraffin-ic-containing phase-change substances characterized by different particle size distributions was determined.
The study of diatomite granules with the addition of paraffin represents an innovative approach to the development of materials with thermoregulatory properties. Diatomite, which is a natural silica material of sedimentary origin, is characterized by very high porosity and the ability to absorb various substances. The addition of paraffin, which is a popular phase change material (PCM), makes it possible to obtain a material with unique thermal energy storage properties.
The main innovation aspects of this study include:
1. The use of diatomite as a paraffin carrier: Diatomite, thanks to its structure with a large specific surface area, can effectively bind paraffin, which enables its safe and stable storage. This type of combination makes it possible to create a composite that is both durable and effective in heat accumulation.
2. The use of paraffin as a phase change material (PCM): Paraffin could absorb and release heat during the transition from solid to liquid and vice versa. Incorporating it into diatomite pellets makes it possible to use this effect to regulate the temperature in a variety of applications, from construction to energy storage systems.
3. Improving thermal efficiency: Diatomite-paraffin granules can be used as insulating elements in buildings or process systems, enabling a reduction in heat loss. In addition, by using PCMs, the flow of thermal energy can be better controlled, which can lead to the optimization of energy processes.
4. Environmental applications and sustainability: Combining the natural material diatomite with the eco-friendly functionality of paraffin allows for environmentally friendly solutions that can simultaneously contribute to energy savings and CO₂ emissions reductions.
5. Increased stability and durability of paraffin: By absorbing paraffin into the porous structure of diatomite, it is possible to increase the stability of paraffin during phase change cycles. This reduces paraffin leakage problems, increasing the life and safety of the material.
Potential applications:
1. Energy-saving construction: These granules can be used in building materials, such as concrete or plaster, to improve the thermoregulatory properties of walls and floors.
2. Energy storage: The ability to accumulate heat makes the material suitable for use in thermal energy storage systems, such as thermal batteries.
3. Thermal insulation: granules can be used in the insulation industry, where it is crucial to maintain a stable temperature while minimizing heat loss.
Research on paraffin-enhanced diatomite granules offers many innovative opportunities, especially in the areas of energy storage and temperature control, which could lead to new solutions in sustainability and energy savings.
2 Materials and methods
2.1 Base material: diatomite
Diatomite powder was used in the study, which came from a mine located in Jawornik Ruski in the Subcarpathian province (Specialized Mining Company Górtech Ltd, Cracow, Poland). It is the only active open pit mine in the country. The work used powdered diatomite, which was calcined for 4 h at different temperatures: 600°C, 650°C, 750°C, 800°C, 850°C, 900°C and 1,000°C. The calcination was carried out in a laboratory muffle furnace FCF 7 SHM (Alchem Group Ltd, Toruń, Poland). In the following part of the article, the physical and chemical properties of diatomite subjected to different temperatures of thermal treatment will be discussed. It was decided to choose the smallest available fraction of diatomite, i.e., powder, due to the highest sorption capacity of this material variant, based on previous research results of scientists from the Cracow University of Technology (Nykiel et al., 2024; Łach et al., 2023; Pławecka et al., 2023; Przybek, 2024). The temperature was chosen to be high enough to allow dehydration, dehydroxylation, and removal of organic matter while avoiding mineral decomposition and preventing the formation of liquid phases (sintering). Diatomite not subjected to calcination is characterized by a gray-brown color, while after calcination its color changes to orange. Figure 1 shows the diatomite after the calcination process used in this study. A total of 7 different variants of diatomite were selected for the study to compare the physicochemical properties of the material.
2.2 Paraffinic phase change material
The article is a continuation of the author’s previous research, so given the results obtained in the paper (Przybek, 2024), WARCHEM heavy paraffin was chosen for macroencapsulation of diatomite granules with paraffinic phase-change substances due to its sorption capacity exceeding 200 wt.% (WARCHEM Ltd., Zakręt, Poland). Figure 2 shows the characteristics of this substance.
2.3 Macroencapsulation of diatomite
The first step of macroencapsulation of diatomite with paraffin was to soak the diatomite with the substance. 60 wt.% paraffin was added to the diatomite powder and allowed to soak for about 4 h under laboratory conditions (at 23°C and 40%–60% humidity) until the components were fully combined. Diatomite powder calcined at 850°C was used for paraffin soaking due to its best absorbency of petroleum and paraffin substances. Absorbency tests have been described in other authors’ works (Łach et al., 2023; Przybek, 2024). Next, a GT-1 disc granulator from Atest (Atest Ltd, Kielce, Poland) was used to produce diatomite granules with paraffin. Parameters for the granulation process included the selection of a disc angle of 0°–60° and the selection of a disc speed of 0–50 rpm. Several preliminary granulation tests were carried out to select the correct test parameters, and granulation was finally carried out at a disc inclination of 30° and a rotational speed of 35 rpm. A solution of R-137 soda water glass with demineralized water in a 50/50 wt.% ratio was used as a binder. Several types of flours and starches (wheat starch, potato starch, corn starch, and coconut and rice flours) were also tested with water, in proportions of 50/50 wt.%, but the best durability of the granules was obtained when sodium water glass was added, so the article presents results only for granules in which the binder was a solution of R-137 with water. The final step was to separate the material into fractions. For this purpose, a vibrating shaker ANALYSETTE 3 PRO (MERAZET Joint Stock Company, Poznań, Poland) was used. This yielded 5 different diatomite fractions: <1.6 mm, 2.0–1.6 mm, 2.5–2.0 mm, 3.35–2.50 mm and >3.50 mm. Figure 3 shows the disc granulator used in the study with key functional elements highlighted.
2.4 Oxide analysis for diatomite
The X-ray fluorescence (XRF) method was used for oxide chemical composition analysis. Seven variants of calcined diatomite were analyzed at different temperatures using a SCHIMADZU EDX-7200 (SHIMADZU Europa GmbH, Duisburg, Germany). All measurements were carried out in an air atmosphere, using Mylar film and special holders dedicated to bulk materials.
2.5 Laser particle size analysis for diatomite
Using an Anton-Paar PSA 1190LD laser particle size analyzer (Anton-Paar, Graz, Austria), particle size characterization was performed for 7 variants of calcined diatomite. Five measurements of D10, D50, D90, and average particle size values were made for each material, and the average of the 5 measurements was calculated and the standard deviation was given. Kalliope Professional software (version 2.22.1) was used for the study.
2.6 Morphology analysis for diatomite
A scanning electron microscopy SEM method was used to study the morphology of all diatomite variants. A JEOL IT 200 scanning electron microscope (JEOL, Akishima, Tokyo, Japan) was used for these studies. Before testing, each material was attached to special holders using carbon disks and a special EM-Tec C33 carbon adhesive. Both fixtures, i.e., the carbon disks and the adhesive, were used to best attach the test material and lead to better conduction of the material. The final step was to coat the test materials with a conductive gold layer using a DII-29030SCTR Smart Coater vacuum sputtering machine (JEOL Ltd., Peabody, MA, USA). After comprehensive preparation of the samples, they were placed on metal tables and then in the holder, and observations of the morphology of the samples began.
2.7 Thermal analysis for diatomite/paraffin granules
Using a Lambda HFM 446 plate apparatus (Netzsch, Selb, Germany), thermal conductivity and specific heat were measured for all 5 variants of diatomite/paraffin granules. The device described here operates under EN 12664 (EN 12664, 2001) and other equivalent standards: ASTM C1784 (ASTM C1784, 2020), ASTM C518 (ASTM C518, 2021), and ISO 8301 (ISO 8301, 1991). The accuracy of a single measurement is ±1%–2%, and temperature regulation and control have been verified by an advanced Peltier system. The thermal conductivity coefficient and specific heat were determined using a measuring machine that employs the cold and hot plate method. The lambda coefficient was tested over a temperature range of 0°C–20°C, while the specific heat was tested over 4 temperature ranges: 17.5°C–22.5°C, 22.5°C–27.5°C, 27.5°C–32.5°C and 32.5°C–37.5°C. Typically, building materials can operate at slightly elevated temperatures, so energy efficiency was tested in different temperature ranges.
3 Results
3.1 Oxide analysis for diatomite
Table 1 shows the results of oxide composition measurements for different variants of calcined diatomite. The table below shows only the most important oxides detected in the chemical composition, whose weight share is greater than 0.1 wt.%. The oxide compositions of all analyzed diatomite materials are similar. Each of the calcined diatomites contains the most SiO2 and Al2O3, with about 79–80 wt.% silicon dioxide and 14–16 wt.% diglinium trioxide. It is noticeable, however, that the highest amount of silica was identified for the diatomite calcined at 850°C. Other oxides detected in the chemical composition of diatomite include Fe2O3, K2O, SO3, TiO2, and CaO.
3.2 Laser particle size analysis for diatomite
Table 2 shows the particle size distribution for calcined powder at different temperatures. The tests were carried out using ultrasound to eliminate the risk of agglomeration of the material in water, the dispersing agent. It can be noted that the lowest average particle size at the same time with very low measurement error was obtained for diatomite powder calcined at 850°C. Calcination at temperatures mainly 600°C, 750°C, and 800°C affected the increase in powder particle diameter. This phenomenon is most likely due to the agglomeration of the smallest diatomite particles, caused by partial sintering of the low-melting phases present in the material. The observed increase in the diameter of diatomite particles after calcination at these temperatures can be explained by the permanent bonding that was formed during thermal processing and the presence of a liquid phase. The lowest particle size affects the sorption capacity of the material to absorb paraffins. The lower the average particle size, the better the material absorbs the test substance.
3.3 Morphology analysis for diatomite
Figure 4 shows the results of testing the morphology of calcined diatomite powder at different temperatures. All variants of diatomite, which are described in this article, were studied. All the photos taken illustrate mainly diatomite carapaces and different forms of diatomite occurrence. The SEM morphology photos illustrate mainly diatoms that have been mechanically degraded or are disk-shaped. Cylindrical diatoms can also be seen in some images. The morphological images show the varied shapes and sizes of diatoms and the markedly high porosity of their structure. Such porosity is crucial to the diatoms’ ability to absorb substances, in this case paraffins. The microstructure of the diatomite plays an important role in its sorption capacity. SEM images were taken at high magnification, 1,000 and 2000×, to show the shape of the diatoms.
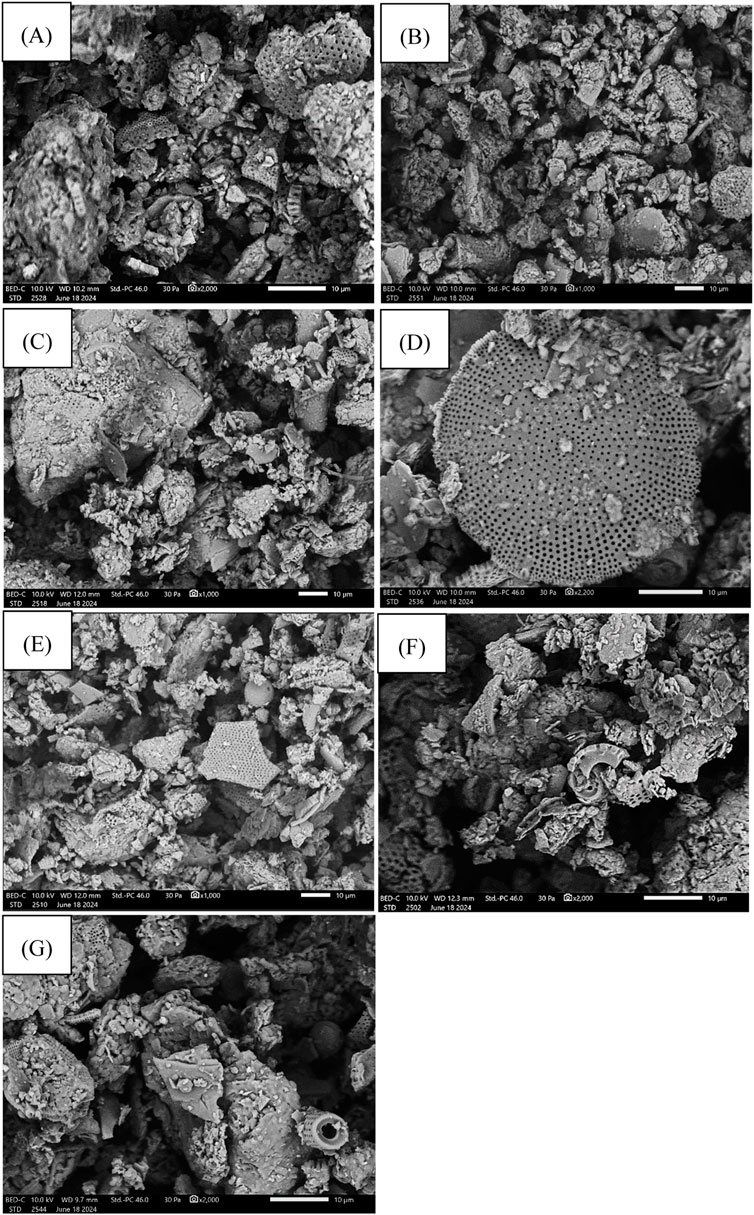
Figure 4. Morphology of diatomite: (A) diatomite powder after 600°C calcination, (B) diatomite powder after 650°C calcination, (C) diatomite powder after 750°C calcination, (D) diatomite powder after 800°C calcination, (E) diatomite powder after 850°C calcination, (F) diatomite powder after 900°C calcination, (G) diatomite powder after 1,000°C calcination.
3.4 Thermal analysis for diatomite/paraffin granules
Table 3 shows the thermal parameters of the produced diatomite/paraffin granules. The abbreviation D/P - denoting diatomite/paraffin - has been introduced. Information on the fraction size of the produced granules was also added in each caption. The tests were conducted using a Lambda HFM 446 plate apparatus with a special frame for bulk materials. The test area was 15 × 15 cm. For all fractions of diatomite, the thermal conductivity coefficient and specific heat were tested in 4 temperature ranges to check the energy efficiency of the finished material. The lowest value of the thermal conductivity coefficient was recorded for D/P 2.0–1.6 mm. However, all the thermal conductivity results are very low, settling at 0.07–0.10 W/m × K. As for the specific heat, on the other hand, all measured values for each type of granule are very high, oscillating within 1.5 kJ/kg × K. The highest specific heat was recorded for the largest granules at the test temperature of 27.5°C–32.5°C.
3.5 Durability test for diatomite/paraffin granules
In each test series, samples were taken for which brittleness and strength properties were determined. Brittleness was determined using a comparative method in the range from high (0) to low (10). The strength properties of the granules were determined using a gravity drop resistance test in the fresh state and after heating in a laboratory furnace at a temperature of 60°C for 24 h. The gravity drop resistance test consisted of dropping 10 granules from a height of 1.0 m onto a ceramic plate and assessing their condition after the experiment. The granules were considered resistant when, after repeating the drop cycle three times, at least 80% were undamaged. This value meets the requirements due to the processes of loading, unloading, and transport from the manufacturer to the recipient of the granulate. The results of the study are shown in Table 4. The highest durability was characteristic of granules in which the binder was sodium water glass R-137.
3.6 Macro photos for diatomite/paraffin granules
Figure 5 shows macrophotographs of the produced diatomite/paraffin granules. The photos were taken to illustrate the appearance and form of the finished material for thermal energy storage and which, at a later stage, will be used in lightweight functional geopolymer foams for, among other things, thermal insulation, and energy storage.
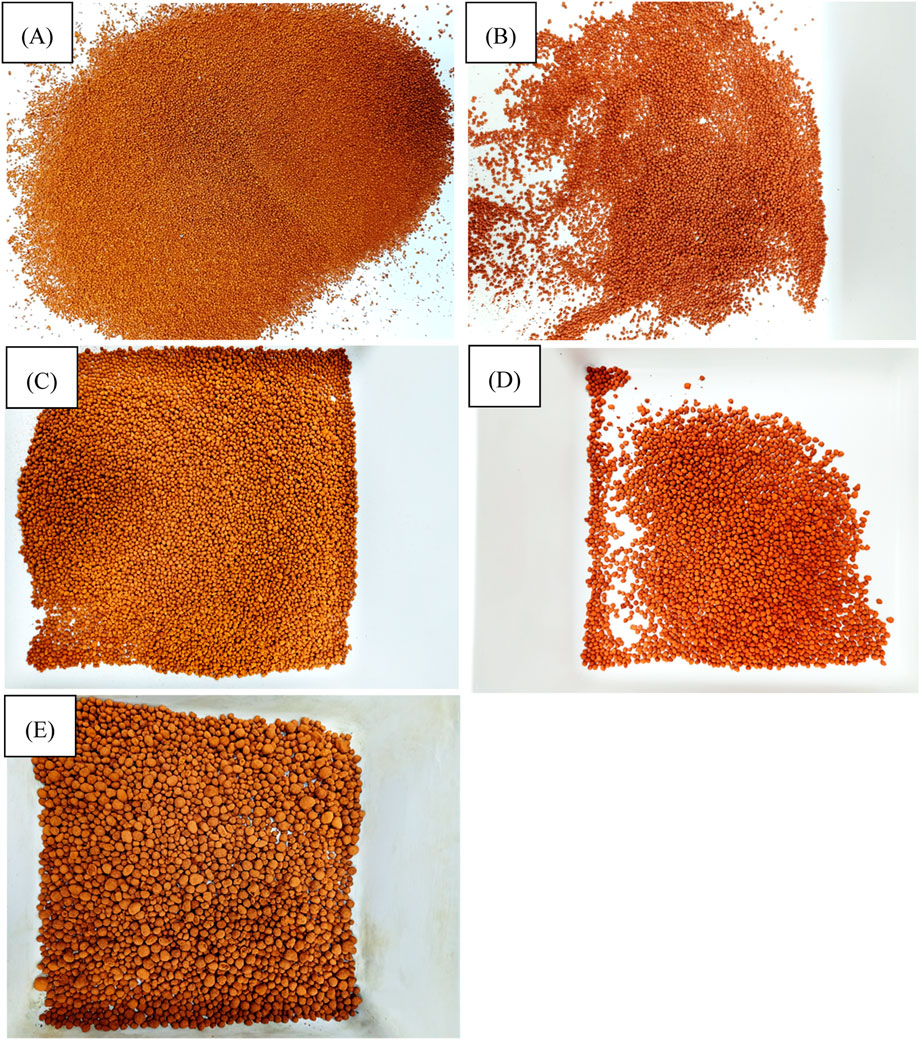
Figure 5. Macro photos od diatomite/paraffin granules: (A) D/P < 1.6 mm, (B) D/P 2.0–1.6 mm, (C) D/P 2.5–2.0 mm, (D) D/P 3.35.-2.0 mm, (E) D/P > 3.35 mm.
3.7 Micro photos for diatomite/paraffin granules
Figure 6 shows micrographs of the produced diatomite/paraffin granules. The photographs were taken to illustrate the appearance and size of the pores. The photographs were taken at 2,000× or 3,000× magnification. The white color in the micrographs indicates paraffin. Pores of various sizes ranging from 200–800 nm were identified.
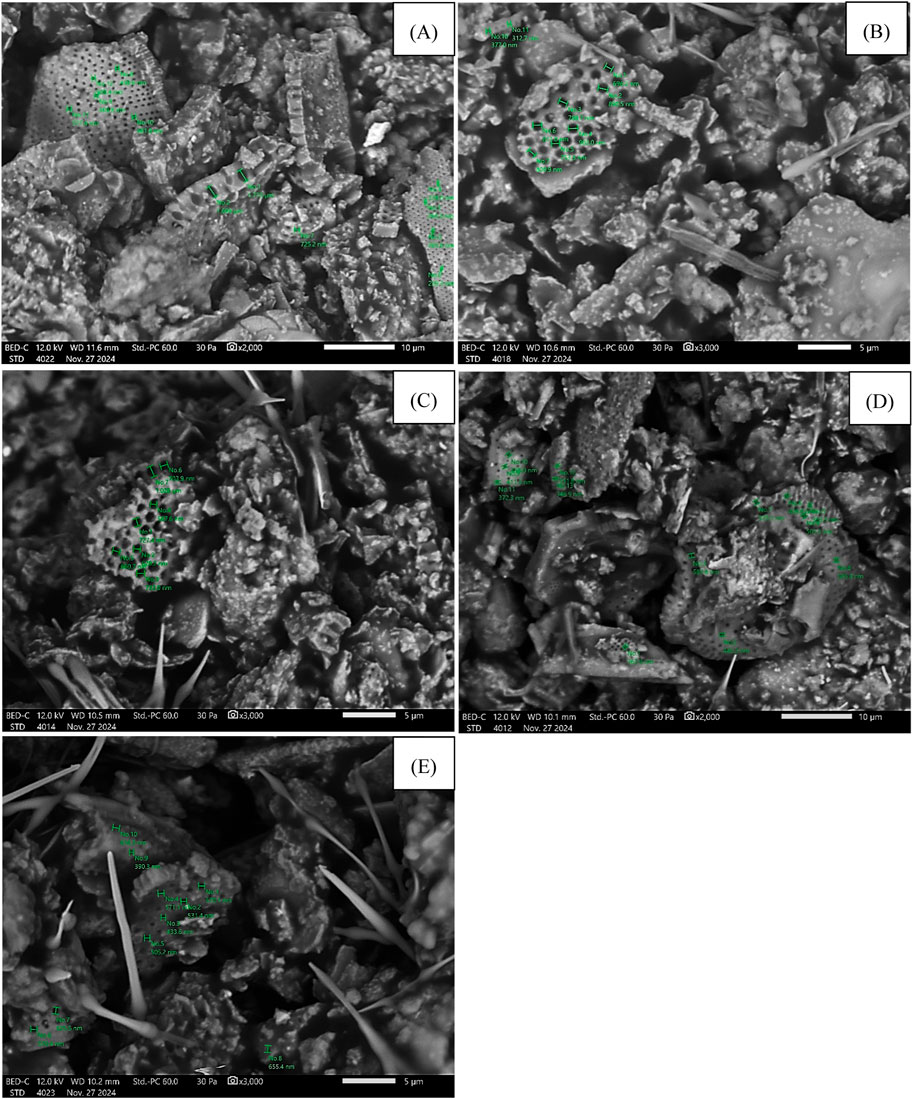
Figure 6. Micro photos od diatomite/paraffin granules: (A) D/P < 1.6 mm, (B) D/P 2.0–1.6 mm, (C) D/P 2.5–2.0 mm, (D) D/P 3.35.-2.0 mm, (E) D/P > 3.35 mm.
3.8 Safety assessment of diatomite/paraffin granules
Diatomite-paraffin granulate is a material considered safe under normal conditions of use. Diatomite does not meet the criteria for classification as a hazardous substance according to Regulation (EC) No. 1272/2008 (CLP). Diatomite has a hygienic certificate number B-BK-60211-0114/20. Diatomite is non-flammable and insoluble in water. The pH range is 5.7–8.3, which makes it neutral or slightly alkaline. It does not exhibit explosive or self-igniting properties. Diatomite does not desorb the absorbed substance, so paraffin leakage is impossible. Diatomite is a rich source of silica, which in the acidic environment of the stomach is transformed into orthosilicic acid. This compound is considered the best source of silicon because it is easily absorbed by humans. For this reason, diatomite is used as a dietary supplement to replenish the level of silicon in the body. Thanks to its natural composition, diatomaceous earth is safe for humans and animals, and contains no toxic chemicals, which makes it an ideal choice for those looking for ecological solutions.
4 Discussion
In the present study, the physicochemical properties of 7 different diatomite powders calcined at different temperatures were investigated: 600°C, 650°C, 750°C, 800°C, 850°C, 900°C and 1,000°C. The study showed that the highest amount of silica was identified for diatomite calcined at 850°C. Performing laser measurement of particle size also showed that the lowest average particle size at the same time with very low measurement error was obtained for diatomite powder calcined at 850°C. Both the presence of a large amount of silica and a very low average particle size have a positive effect on the sorption capacity of diatomite to absorb paraffins. The present study only confirmed the tests described in another paper by the authors Przybek (2024), where diatomite powder calcined at 850°C showed the highest absorption capacity. Another study by scientists from the Cracow University of Technology, i.e., conducting specific surface area measurements, also showed that the best results were obtained for the described calcined diatomite powder (Łach et al., 2023).
Calcination of diatomite significantly affects its sorption capacity, mainly by altering its physical and chemical properties. Calcination, a thermal treatment process, typically increases the silica content and modifies the surface properties of diatomite, which are crucial to its effectiveness as an adsorbent. One of the main effects of calcination is an increase in reactive silica (SiO₂) content. Other researchers Costafreda et al. (2023) have noted that calcined diatomite (CDT) exhibits a higher SiO₂ content compared to non-calcined diatomite (NDT), which is crucial for improving its pozzolanic properties. This increase in reactive silica is attributed to thermal processes occurring during calcination, which can maintain or even increase SiO₂ levels depending on the temperature used (Costafreda et al., 2023). In addition, calcination-induced structural changes lead to the formation of micro- and mesopores, which increase the surface area and porosity of the material, thereby improving its adsorption capacity (Figarska-Warchoł et al., 2020). Modification of diatomite by calcination also affects its interaction with various impurities. For example, studies have shown that calcined diatomite exhibits better adsorption capacity for heavy metals and organic contaminants compared to its raw counterpart. Researchers Yang et al. (2013) showed that the adsorption of zinc (Zn (II)) ions was significantly increased when the diatomite was treated with sodium hydroxide before calcination, which created surface defects that increased its negative charge and adsorption capacity. Similarly, Zhao et al. (2020), found that alkali-activated diatomite showed better adsorption capacity for alkaline fuchsin, with the capacity increasing as the activation temperature increased. However, it should be noted that excessively high calcination temperatures can adversely affect the sorption capacity of diatomite. Others Guo et al. (2024) have pointed out that calcination at high temperatures can lead to structural degradation, which reduces the adsorption properties of the material. This suggests that although moderate calcination can increase sorption capacity, there is a threshold beyond which the benefits may be negated. Moreover, specific calcination conditions, such as temperature and duration, play a key role in determining the ultimate properties of diatomite. Researchers Nurgain et al. (2020) have investigated the effects of different calcination temperatures and acid pretreatment on diatomite, revealing that optimal conditions can provide sorbents with adapted physical and chemical properties suitable for specific applications. This adaptability is crucial for developing effective adsorbents for various contaminants in wastewater treatment. Calcination of diatomite is a key process that increases its sorption capacity by increasing its reactive silica content, improving its surface area, and adjusting its structural properties. However, careful control of calcination parameters is necessary to avoid detrimental effects on its adsorption capacity. Ongoing research to optimize these conditions will continue to expand the applications of diatomite in environmental remediation and other fields.
The second part of the study focused on the energy efficiency of granules produced from diatomite powder with the addition of 60 wt.% WARCHEM heavy liquid paraffin. Five different diatomite fractions were produced: <1.6 mm, 2.0–1.6 mm, 2.5–2.0 mm, 3.35–2.50 mm, and >3.50 mm. A 50/50 wt.% solution of R-137 soda glass with demineralized water was used as a binder. Attempts were made to use more environmentally friendly and natural binders such as flour or starch, but despite baking the granules in a laboratory oven at 75°C for 24 h, the durability of these granules was too low and they only coated the manufactured diatomite-paraffin granules without increasing the strength of the finished material. Given this, the paper describes only granules with high durability, which can be successfully used as a thermal energy storage medium. The tests carried out showed that the lowest value of thermal conductivity was recorded for D/P 2.0–1.6 mm. However, all the thermal conductivity results are very low, oscillating between 0.07–0.10 W/m × K. As for the specific heat, on the other hand, all measured values for each granule type are very high and oscillate above 1.5 kJ/kg×K. The highest specific heat was recorded for the largest granules at the test temperature of 27.5°C–32.5°C.
The thermal conductivity and specific heat of diatomite-paraffin granules have been the subject of various studies, highlighting the unique properties of diatomite as a thermal insulator and its effectiveness when combined with paraffin in composite materials. Diatomite, with its high porosity and low density, exhibits low thermal conductivity, which is advantageous in thermal insulation applications. For example, Han et al. (2020), reported a thermal conductivity of 0.068 ± 0.001 W/m × K for diatomite ceramics at 473 K, which decreased with increasing porosity, indicating that higher porosity correlates with lower thermal conductivity. Similarly, the thermal conductivity of diatomite consolidated with starch was 0.0984 W/m × K, demonstrating the insulating properties of diatomite in composite molds (Alvarado et al., 2023). When diatomite is used as a support matrix for phase change materials (PCMs) such as paraffin, it significantly affects the thermal properties of the resulting composites. For example, Jia et al. (2020), synthesized composites of palmitic acid and diatomite and noted that thermal conductivity was increased due to the porous structure of the diatomite, which facilitated better heat transfer in the composite. In addition, the incorporation of diatomite into paraffin-based PCMs has been shown to improve thermal stability and reduce the overcooling effect, as evidenced by the work of (Zhang et al., 2017), who found that the enthalpies of melting and crystallization of their diatomite/paraffin composites were 108.2 J/g and 98.5 J/g, respectively. This indicates that diatomite not only serves as a structural support but also improves the thermal properties of paraffin-based materials. The specific heat capacity of diatomite-paraffin composites is also an important factor affecting their thermal properties. The interaction between diatomite and paraffin can lead to changes in specific heat, which is crucial for thermal energy storage applications. For example, the thermal properties of PCM/diatomite composites were analyzed by differential scanning calorimetry (DSC), revealing that the latent heat capacities of these composites were about 50% of those of pure PCM (Jeong et al., 2012). This suggests that while diatomite increases the thermal stability and conductivity of paraffin, it can also affect the specific heat capacity, which is essential for effective thermal energy storage. Integration of diatomite with paraffin results in composites that exhibit favorable thermal properties, including low thermal conductivity and increased specific heat capacity. These features make diatomite-paraffin granules suitable for applications in thermal insulation and energy storage systems.
5 Conclusion
The solution presented has a significant impact on the energy efficiency of buildings, which brings some benefits in both economic and environmental terms. One of the key aspects of energy efficiency is preventing buildings from overheating in summer and minimizing heat loss in winter. With the right technologies such as diatomite-paraffine granules used in building components, it is possible to maintain a stable temperature inside the building. Appropriately selected building materials prevent unnecessary heating of rooms in summer, which reduces the need for air conditioning. In turn, in winter, the same technologies allow heat to be retained inside the building, leading to less energy loss for heating. The thermal stability of buildings, i.e., the ability to maintain the right temperature over a long period without large fluctuations, is crucial for the comfort of the occupants. At the same time, it reduces the need for additional energy sources for cooling and heating, leading to financial savings and lower energy consumption, and consequently a reduction in greenhouse gas emissions. The use of diatomite-paraffin granules in construction contributes to energy efficiency, provides thermal comfort, and helps to achieve sustainability goals.
The research results presented in this article lead us to draw some important conclusions that summarize the work:
I. Calcination of diatomite has a positive effect on its sorption capacity by increasing its reactive silica content. However, the thermal treatment must be carried out at a suitable temperature and for a certain duration of the process. The best results can be obtained for a temperature of 850°C for 4 h.
II. The best sorption capacity of diatomite can be obtained for the material with the lowest average particle size, which was characterized by diatomite powder calcined at 850°C.
III. Natural binder only encapsulates diatomite-paraffin granules and, despite its environmental benefits, is not a viable candidate. The best granule durability was achieved using a 50/50 wt.% solution of R-137 soda glass with demineralized water.
IV. It is possible to produce diatomite-paraffin granules containing 60 wt.% paraffin with a thermal conductivity coefficient of 0.07–0.10 W/m × K and an energy efficiency of 1.5 kJ/kg×K or higher.
Further work by the researchers will focus on producing granules with another paraffin substance, i.e., FLEXOL paraffin oil. It is also planned to produce granules with 80 wt.% paraffin. Once the new granules have been produced, further thermal tests will be carried out, which will include the studies presented in this article and other complementary ones, such as TMA. The authors’ future work will also present tests of finished lightweight functional geopolymer foams for insulation applications and capable of heat storage.
Diatomite-paraffin granules have significant environmental and energy-saving benefits, making them an extremely attractive solution for sustainable development. These granules, thanks to the thermoregulatory properties of paraffin, help to efficiently store and release thermal energy. This allows more efficient use of heat in buildings and other systems, leading to a reduced need for additional energy sources. As a result, less energy is wasted, which translates into lower consumption of fossil fuels and reduced carbon emissions. Incorporating these granules into building materials such as plaster, walls, and concrete makes buildings more energy efficient. The granules can accumulate heat during the day and release it at night, reducing the need for heating and air conditioning. In this way, they contribute to passive temperature control systems that minimize the need for energy-consuming appliances. With their ability to store heat and improve energy efficiency, diatomite-paraffin granules can significantly reduce greenhouse gas emissions. Lower energy consumption from traditional sources means lower CO₂ emissions, which has a direct impact on the fight against climate change. Diatomite is a natural and environmentally friendly material, and paraffin, being a phase-change material, is safe to use and has a long service life. The combination of these materials makes it possible to create products that are environmentally friendly and easy to dispose of, further enhancing their eco-friendly properties. The use of diatomite-paraffin granules promotes sustainability, as it enables better use of natural resources through efficient heat management. In the long term, such solutions reduce the need to exploit energy resources and contribute to savings on both a household and industrial scale. Diatomite-paraffin granules play a key role in the pursuit of environmental and energy efficiency. Their ability to accumulate and regulate heat contributes to reducing energy consumption, reducing greenhouse gas emissions, and supporting sustainable development, making them a valuable solution for combating climate change and improving energy efficiency.
Data availability statement
The original contributions presented in the study are included in the article/supplementary material, further inquiries can be directed to the corresponding authors.
Author contributions
AP: Conceptualization, Data curation, Formal Analysis, Investigation, Methodology, Resources, Validation, Writing–original draft, Writing–review and editing. MŁ: Conceptualization, Formal Analysis, Funding acquisition, Methodology, Supervision, Validation, Visualization, Writing–review and editing. MH-K: Investigation, Resources, Writing–review and editing. KM: Validation, Visualization, Writing–review and editing. JM: Supervision, Writing–review and editing.
Funding
The author(s) declare that financial support was received for the research, authorship, and/or publication of this article. This work was funded by the Ministry of Science and Higher Education: PN/01/0067/2022 (Research of functional lightweight porous structures based on alkali-activated aluminosilicates).
Conflict of interest
The authors declare that the research was conducted in the absence of any commercial or financial relationships that could be construed as a potential conflict of interest.
Generative AI statement
The author(s) declare that no Generative AI was used in the creation of this manuscript.
Publisher’s note
All claims expressed in this article are solely those of the authors and do not necessarily represent those of their affiliated organizations, or those of the publisher, the editors and the reviewers. Any product that may be evaluated in this article, or claim that may be made by its manufacturer, is not guaranteed or endorsed by the publisher.
References
Abrão, P. C. R. A., Cardoso, F. A., and John, V. M. (2019). Evaluation of portland pozzolan blended cements containing diatomaceous earth. Cerâmica 65 (1), 75–86. doi:10.1590/0366-6913201965s12596
Alvarado, C., Alvarado-Quintana, H., and Jara, R. S. (2023). Ceramic thermal insulator based on diatomite obtained by starch consolidation casting. Materials 16 (11), 4028. doi:10.3390/ma16114028
ASTM C1784 (2020). Standard test method for using a heat flow meter apparatus for measuring thermal storage properties of phase change materials and products. Int. Am. Soc. Test. Mater. West Conshohocken, PA, USA.
ASTM C518 (2021). Standard test method for steady-state thermal transmission properties by means of the heat flow meter apparatus. Int. Am. Soc. Test. Mater. West Conshohocken, PA, USA.
Benayache, S., Alleg, S., Mebrek, A., and Suñol, J. J. (2018). Thermal and microstructural properties of paraffin/diatomite composite. Vacuum 157, 136–144. doi:10.1016/j.vacuum.2018.08.044
Caner, N., Sarı, A., and Tüzen, M. (2015). Adsorption characteristics of mercury(II) ions from aqueous solution onto chitosan-coated diatomite. Industrial and Eng. Chem. Res. 54 (30), 7524–7533. doi:10.1021/acs.iecr.5b01293
Chu, H., Cao, D., Jin, W., and Dong, B. (2008). Characteristics of bio-diatomite dynamic membrane process for municipal wastewater treatment. J. Membr. Sci. 325 (1), 271–276. doi:10.1016/j.memsci.2008.07.040
Costa, J. A. C., Martinelli, A. E., do Nascimento, R. B., and Mendes, A. M. (2020). Microstructural design and thermal characterization of composite diatomite-vermiculite paraffin-based form-stable PCM for cementitious mortars. Constr. Build. Mater. 232, 117167. doi:10.1016/j.conbuildmat.2019.117167
Costafreda, J. L., Martín, D. A., Astudillo, B., Presa, L., Parra, J. L., and Sanjuán, M. Á. (2023). Diatomites from the iberian peninsula as pozzolans. Materials 16 (10), 3883. doi:10.3390/ma16103883
Cuellar, Z. Y. M., Rivero, Y. I. N. S., and Rodríguez, G. P. (2018). Water treatment using porous ceramics based on recycled diatomite and kaolin. Contemp. Eng. Sci. 11 (75), 3729–3738. doi:10.12988/ces.2018.88366
Cui, T., Ma, J. F., Wang, Q. S., Zhou, Q., and Tang, D. B. (2021). Hydrothermal fabrication of BiVO4/diatomite composite photocatalysts and their photocatalytic performance. Key Eng. Mater. 904, 350–357. doi:10.4028/www.scientific.net/kem.904.350
Dobrosielska, M., Dobrucka, R., Brząkalski, D., Gloc, M., Rębiś, J., Głowacka, J., et al. (2021). Methodological aspects of obtaining and characterizing composites based on biogenic diatomaceous silica and epoxy resins. Materials 14, 4607. doi:10.3390/ma14164607
Du, T., Song, P., and Liu, L. (2022). Experimental study on activated diatomite modified asphalt pavement in deep loess area. Processes 10 (6), 1227. doi:10.3390/pr10061227
EN 12664 (2001) “Thermal performance of building materials and products. Determination of thermal resistance by means of guarded hot plate and heat flow meter methods,” in Dry and moist products of medium and low thermal resistance. Brussels, Belgium: European Committee for Standardisation.
Ferreira, R. L. S., Pinto, L., Nóbrega, A. F., and Carneiro, A. M. P. (2024). Diatomaceous earth: a review of its characteristics and effects on the properties of mortars. Constr. Build. Mater. 421, 135711. doi:10.1016/j.conbuildmat.2024.135711
Figarska-Warchoł, B., Rembiś, M., and Stańczak, G. (2020). The impact of calcination on changes in the physical and mechanical properties of the diatomites of the leszczawka member (the outer carpathians, Poland). Geol. Geophys. Environ. 45 (4), 269. doi:10.7494/geol.2019.45.4.269
Fořt, J., Trník, A., Pavlíková, M., and Pavlík, Z. (2015) Diatomite/palm wax composite as a phase change material for latent heat storage. Adv. Mater. Res. 1126, 33–38. doi:10.4028/www.scientific.net/amr.1126.33
Fu, X., Liu, Z., Xiao, Y., Wang, J., and Lei, J. (2015). Preparation and properties of lauric acid/diatomite composites as novel form-stable phase change materials for thermal energy storage. Energy Build. 104, 244–249. doi:10.1016/j.enbuild.2015.06.059
Gondek, K., Micek, P., Baran, A., Bajda, T., Kowal, J., Lis, M., et al. (2023). Modified natural diatomite with various additives and its environmental potential. Materials 16 (12), 4494. doi:10.3390/ma16124494
Guo, X., Huang, Y., and Cao, J. (2018). Performance of a thermal energy storage composite by incorporating diatomite stabilized paraffin as phase change material. Energy Build. 158, 1257–1265. doi:10.1016/j.enbuild.2017.11.032
Guo, Z., Ren, Z., Gao, H., Guan, J., Li, P., Zheng, R., et al. (2024). Controllable preparation of zeolite-p/calcined diatomite with mgcl2. Korean J. Chem. Eng. 41 (6), 1851–1859. doi:10.1007/s11814-024-00013-8
Han, L., Li, F., Zhang, H., Pei, Y., Dong, L. H., Liang, F., et al. (2020). Freeze-drying preparation of porous diatomite ceramics with high porosity and low thermal conductivity. Adv. Appl. Ceram. 119 (4), 195–203. doi:10.1080/17436753.2020.1732622
ISO 8301 (1991). Thermal insulation—determination of steady-state thermal resistance and related properties—heat flow meter apparatus. London, UK: International Standards Organization.
Jeong, S., Lee, J. H., and Kim, S. (2012). Preparation of shape stabilized pcms by vacuum impregnating method of diatomite. Adv. Mater. Res. 630, 71–74. doi:10.4028/www.scientific.net/amr.630.71
Jia, W., Wang, C., Wang, T., Cai, Z., and Chen, K. (2020). Preparation and performances of palmitic acid/diatomite form-stable composite phase change materials. Int. J. Energy Res. 44 (6), 4298–4308. doi:10.1002/er.5197
Khezri, K., and Fazli, Y. (2018). A study on the kinetics and thermal properties of polystyrene/diatomite nanocomposites prepared via in situ atrp. J. Thermoplast. Compos. Mater. 33 (2), 180–197. doi:10.1177/0892705718805128
Konuklu, Y. (2020). Preparation and characterization of form-stable phase change material/end-of-life tires composites for thermal energy storage. Turkish J. Chem. 44 (2), 421–434. doi:10.3906/kim-1911-23
Konuklu, Y., Ersoy, O., and Gökçe, Ö. (2015). Easy and industrially applicable impregnation process for preparation of diatomite-based phase change material nanocomposites for thermal energy storage. Appl. Therm. Eng. 91, 759–766. doi:10.1016/j.applthermaleng.2015.08.040
Łach, M., Pławecka, K., Marczyk, J., Ziejewska, C., Hebdowska-Krupa, M., Nykiel, M., et al. (2023). Use of diatomite from Polish fields in sustainable development as a sorbent for petroleum substances. J. Clean. Prod. 389, 136100. doi:10.1016/j.jclepro.2023.136100
Li, X., Sanjayan, J. G., and Wilson, J. L. (2014). Fabrication and stability of form-stable diatomite/paraffin phase change material composites. Energy Build. 76, 284–294. doi:10.1016/j.enbuild.2014.02.082
Liu, H., Zhang, M., Jiao, Y., and Fu, L. (2018). Preparation parameter analysis and optimization of sustainable asphalt binder modified by waste rubber and diatomite. Adv. Mater. Sci. Eng. 1, 1–14. doi:10.1155/2018/3063620
Lorwanishpaisarn, N., Kasemsiri, P., Posi, P., and Chindaprasirt, P. (2017). Characterization of paraffin/ultrasonic-treated diatomite for use as phase change material in thermal energy storage of buildings. J. Therm. Analysis Calorim. 128, 1293–1303. doi:10.1007/s10973-016-6024-3
Mao, J., Zheng, S. L., Zhang, Y. Z., Bi, Y., and Liu, Y. (2013). Preparation and characterization of diatomite loaded composite phase change materials. Appl. Mech. Mater. 320, 314–319. doi:10.4028/www.scientific.net/amm.320.314
Marczyk, J., Pławecka, K., Hebdowska-Krupa, M., Nykiel, M., and Łach, M. (2022). Research on diatomite from Polish deposits and the possibilities of its use. J. Achiev. Mater. Manuf. Eng. 115 (1), 5–15. doi:10.5604/01.3001.0016.2337
Mejía, J. M., de Gutiérrez, R. M., and Montes, C. (2016). Rice husk ash and spent diatomaceous earth as a source of silica to fabricate a geopolymeric binary binder. J. Clean. Prod. 118, 133–139. doi:10.1016/j.jclepro.2016.01.057
Meradi, H., Atoui, L., Bahloul, L., Labiod, K., and Ismail, F. (2016). Characterization of diatomite from Sig region (West Algeria) for industrial application. Manag. Environ. Qual. 27 (3), 281–288. doi:10.1108/MEQ-04-2015-0057
Moyle, P. R., and Dolley, T. P. (2003). Chapter D: with or without salt-a comparison of marine and continental-lacustrine diatomite deposits. USGS Numbered Ser., 2209. doi:10.3133/b2209D
Nurgain, А., Нажипкызы, М., Zhaparova, A., Issanbekova, A. T., Alfè, M., and Musina, A. S. (2020). Acid modification of diatomite-based sorbents. Eurasian Chemico-Technological J. 22 (3), 157. doi:10.18321/ectj975
Nykiel, M., Korniejenko, K., Setlak, K., Melnychuk, M., Polivoda, N., Kozub, B., et al. (2024). The influence of diatomite addition on the properties of geopolymers based on fly ash and metakaolin. Materials 17, 2399. doi:10.3390/ma17102399
Omar, B., Fatiha, A., Marwa, B., Kharchi, F., Maissan, B., and Farid, B. (2022). Potential use of algerian natural diatomite as pozzolanic and insulator material in cement mortar. Ecol. Environ. Conservation 28 (2), 1005–1012. doi:10.53550/eec.2022.v28i02.065
Pławecka, K., Bąk, A., Hebdowska-Krupa, M., and Łach, M. (2023). The use of calcined diatomite as an additive to geopolymeric materials. Mater. Proc. 13, 28. doi:10.3390/materproc2023013028
Przybek, A. (2024). Assessment of physico-chemical behavior and sorptivity—diatomaceous earth as support for paraffinic phase-change materials. Materials 17, 4691. doi:10.3390/ma17194691
Qian, T., Li, J., and Deng, Y. (2016). Pore structure modified diatomite-supported peg composites for thermal energy storage. Sci. Rep. 6 (1), 32392. doi:10.1038/srep32392
Qian, T., Li, J., Feng, W., and Nian, H. (2017). Enhanced thermal conductivity of form-stable phase change composite with single-walled carbon nanotubes for thermal energy storage. Sci. Rep. 7 (1), 44710. doi:10.1038/srep44710
Qian, T., Li, J., Min, X., Deng, Y., Guan, W., and Lei, N. (2015b). Diatomite: a promising natural candidate as carrier material for low, middle and high temperature phase change material. Energy Convers. Manag. 98, 34–45. doi:10.1016/j.enconman.2015.03.071
Qian, T., Li, J., Min, X., Guan, W., Deng, Y., and Lei, N. (2015a). Enhanced thermal conductivity of peg/diatomite shape-stabilized phase change materials with ag nanoparticles for thermal energy storage. J. Mater. Chem. A 3 (16), 8526–8536. doi:10.1039/c5ta00309a
Reka, A. A., Pavlovski, B., Boev, B., Bogoevski, S., Boškovski, B., Lazarova, M., et al. (2021b). Diatomite—evaluation of physico-mechanical, chemical, mineralogical and thermal properties. Geol. Maced. 35 (1), 5–14. doi:10.46763/GEOL21351368005ar
Reka, A. A., Pavlovski, B., Fazlija, E., Berisha, A., Pacarizi, M., Daghmehchi, M., et al. (2021a). Diatomaceous Earth: characterization, thermal modification, and application. Open Chem. 19 (1), 451–461. doi:10.1515/chem-2020-0049
Sun, Z., Zhang, Y., Zheng, S., Park, Y., and Frost, R. L. (2013). Preparation and thermal energy storage properties of paraffin/calcined diatomite composites as form-stable phase change materials. Thermochim. Acta 558, 16–21. doi:10.1016/j.tca.2013.02.005
Wang, W. H., Li, L. Y., Zhang, X. Q., Qiu, J. Q., Wang, J., and Zhang, Y. S. (2014). Enhanced coagulation for slightly polluted seawater using ferric sulfate and modified diatomite. Adv. Mater. Res. 955-959, 102–107. doi:10.4028/www.scientific.net/AMR.955-959.102
Wu, G., Ma, S., Bai, Y., and Zhang, H. (2019). The surface modification of diatomite, thermal, and mechanical properties of poly(vinyl chloride)/diatomite composites. J. Vinyl and Addit. Technol. 25 (s2), E39–E47. doi:10.1002/vnl.21664
Xiang, Y., Wang, N., Song, J., Cai, D., and Wu, Z. (2013). Micro-nanopores fabricated by high-energy electron beam irradiation: suitable structure for controlling pesticide loss. J. Agric. Food Chem. 61 (22), 5215–5219. doi:10.1021/jf401274y
Xu, B., and Li, Z. (2013). Paraffin/diatomite composite phase change material incorporated cement-based composite for thermal energy storage. Appl. Energy 105, 229–237. doi:10.1016/j.apenergy.2013.01.005
Yang, Z. Z., Lu, Y., and Li, Y. Y. (2013). The adsorption of zinc(ii) from aqueous solution on modified diatomite. Appl. Mech. Mater. 438-439, 211–214. doi:10.4028/www.scientific.net/amm.438-439.211
Zahajská, P., Opfergelt, S., Fritz, S. C., Stadmark, J., and Conley, D. J. (2020). What is diatomite? Quat. Res. 96, 48–52. doi:10.1017/qua.2020.14
Zhang, P., Cui, Y., Zhang, K., Wu, S., Chen, D., and Gao, Y. (2021). Enhanced thermal storage capacity of paraffin/diatomite composite using oleophobic modification. J. Clean. Prod. 279, 123211. doi:10.1016/j.jclepro.2020.123211
Zhang, X., Li, X., Yuan, Z., Hai, C., Shen, Y., Ren, X., et al. (2017). Calcium chloride hexahydrate/diatomite/paraffin as composite shape-stabilized phase-change material for thermal energy storage. Energy &Amp; Fuels 32 (1), 916–921. doi:10.1021/acs.energyfuels.7b02866
Zhang, X., Li, X., Zhou, Y., Hai, C., Shen, Y., Ren, X., et al. (2018). Calcium chloride hexahydrate/diatomite/paraffin as composite shape-stabilized phase-change material for thermal energy storage. Energy fuels. 32 (1), 916–921. doi:10.1021/acs.energyfuels.7b02866
Zhang, Y., Huang, B., Zhang, J. Y., and Li, D. X. (2012). Preparation and performance study of fatty acid diatomite composite phase change materials and light weight phase change gypsum wall materials. Appl. Mech. Mater. 193-194, 307–313. doi:10.4028/www.scientific.net/amm.193-194.307
Zhao, Y., Geng, J., Cai, J., Cai, Y., and Cao, C. (2020). Adsorption performance of basic fuchsin on alkali-activated diatomite. Adsorpt. Sci. and Technol. 38 (5-6), 151–167. doi:10.1177/0263617420922084
Keywords: diatomite, phase change materials, macroencapsulation, advanced building materials, properties of material, improvement of thermal comfort
Citation: Przybek A, Łach M, Hebdowska-Krupa M, Miernik K and Mikuła J (2024) Research of the physical and chemical properties of diatomite as a carrier of phase change materials for use in advanced building materials. Front. Mater. 11:1507779. doi: 10.3389/fmats.2024.1507779
Received: 08 October 2024; Accepted: 09 December 2024;
Published: 24 December 2024.
Edited by:
Siqi Ding, Hong Kong Polytechnic University, Hong Kong SAR, ChinaReviewed by:
Linyang Wei, Northeastern University, ChinaHossein Kabir, University of Illinois at Urbana-Champaign, United States
Copyright © 2024 Przybek, Łach, Hebdowska-Krupa, Miernik and Mikuła. This is an open-access article distributed under the terms of the Creative Commons Attribution License (CC BY). The use, distribution or reproduction in other forums is permitted, provided the original author(s) and the copyright owner(s) are credited and that the original publication in this journal is cited, in accordance with accepted academic practice. No use, distribution or reproduction is permitted which does not comply with these terms.
*Correspondence: Agnieszka Przybek, YWduaWVzemthLnByenliZWtAcGsuZWR1LnBs; Michał Łach, bWljaGFsLmxhY2hAcGsuZWR1LnBs