- 1School of Civil Engineering and Transportation, South China University of Technology, Guangzhou, China
- 2China Construction Third Bureau First Engineering Co., Ltd., Wuhan, Hubei, China
Steel fiber-reinforced concrete material has garnered significant attention in structure design due to its excellent resistance to fatigue damage. The application of the plain concrete microplane model is extended to steel fiber-reinforced concrete by modifying the stress-strain boundary conditions on the microplane and then extended to fatigue damage analysis by considering fatigue-related material stiffness, mainly concerned with tensile damage, mainly concerned with tensile damage. The normal positive strain on the micro-plane is regarded as the fatigue variable, and the fatigue history variable is the accumulation of the fatigue variable during the loading. The relationship between the fatigue history variable and the material stiffness fatigue degradation function is established. In the numerical implementation, the crack band model is combined to reduce the mesh sensitivity caused by strain localization. During the numerical simulation, the parameters of plain concrete, steel fiber-reinforced concrete, and the material fatigue degradation function can be calibrated sequentially, requiring only a few benchmark tests for accurate parameter calibration. The numerical results show that this model can be used for the fatigue damage analysis of plain concrete and steel fiber-reinforced concrete material. It is expected to be used for the refined analysis of concrete structures under complex loading conditions and structural forms in the future, providing convenience to engineering design, evaluation, and optimization.
1 Introduction
Concrete material has a wide range of applications in infrastructure, including bridges, roads, high-rise buildings, and the foundations of power machinery. However, concrete structures are often subjected to cyclic loads, such as traffic (Zhang et al., 2024) and wind, which can lead to material fatigue stiffness degradation (Riyar et al., 2023). This can gradually deteriorate the structural performance, potentially leading to structural failure. Fiber-reinforced concrete material has emerged as a promising solution to improve the durability and safety of concrete structures. Incorporating short fibers, including steel or polypropylene fibers, into fiber-reinforced concrete results in a composite material that exhibits enhanced resistance to cracking, improved toughness, and fatigue properties (Carlesso et al., 2019). It is imperative to investigate the fatigue characteristics of plain and fiber-reinforced concrete and their damage evolution patterns. This is crucial for precisely predicting and assessing the service life of concrete structures and developing adequate maintenance and reinforcement strategies.
As early as the late 19th century, engineers established the S-N curve (Aas-Jakobsen, 1970; Cornelissen, 1984; Miarka et al., 2022) based on experimental data to reflect the fatigue life of concrete at different stress levels. The S-N curve also applies to fiber-reinforced concrete, but it is necessary to consider the fiber type, volume fraction, and orientation effects on fatigue life. The S-N curve is a reasonable method for estimating the anticipated lifespan under disparate stress levels. However, it requires a substantial corpus of experimental data and may not accurately reflect the intricate stress conditions. With the advent of fracture mechanics, the Paris law (Paris and Erdogan, 1963) was introduced to describe the crack propagation rate in plain concrete under constant load. For fiber-reinforced concrete material, the parameters in the Paris law must be adjusted to reflect the hindering effect of fibers on crack propagation. The Paris law is suitable for single crack extension analysis under simple loading conditions, but its application is limited under complex or variable loading. Hillerborg et al. considered a virtual crack in front of a visible crack in concrete and cohesive stress between the interfaces of the virtual crack (Hillerborg et al., 1976). The cohesive zone model simulates the nonlinear fracture behavior of concrete by defining the relationship between the cohesive stress between the crack interfaces and the crack opening displacement and extends the model to fatigue loading by correcting the relationship between the cohesive stress and the crack opening displacement (Gylltoft, 1984). For fiber-reinforced concrete, the cohesive zone model needs to consider further the bridging effect of fibers, which can increase the cohesive stress at the crack surface and thus slow down the crack extension. The damage constitutive model (Marigo, 1985), on the other hand, describes the degradation of the mechanical properties of concrete under repetitive loading from a material microscopic point of view by introducing damage variables, which can be extended to fatigue loading by introducing fatigue history variables and adjusting the damage evolution conditions. This model considers the emergence and expansion of microcracks within concrete and their effect on the overall material properties. For fiber-reinforced concrete, the damage constitutive model needs to consider the effect of fibers on the damage evolution, including the reinforcing and toughening effects of fibers (Li et al., 2024).
In addition to the macro-mechanical modeling of concrete, researchers began to seek breakthroughs in micro-mechanical theories to study concrete constitutive relationships, such as the microplane damage model (Caner and Bažant, 2013a; Caner and Bazant, 2013b). The microplane, which represents a plane perpendicular to any direction at a material point, can describe the interactions between weak planes, cracks, and different defects on microstructures in all directions and can be used to model the inelastic behavior of quasi-brittle materials (e.g., concrete), and has been developed into its seventh version up to the present day. Subsequently, Caner et al. (2013) extended the normal concrete microplane model to fiber concrete by improving the stress-strain boundary conditions on the microplane to describe the pullout and fracture behavior of fibers in fiber-reinforced concrete. Kirane and Bažant (2015) incorporated the fatigue effect into the normal concrete microplane model by introducing a fatigue history variable to quantify the cyclic damage accumulation of the material. However, there is still a lack of microplane models applicable to fatigue damage studies of fiber-reinforced concrete. Although the performance of Engineered Cementitious Composites (ECC) (Lu et al., 2017; Huang et al., 2022; Zhu et al., 2022) and Ultra High-Performance Fiber Reinforced Concrete (UHPFRC) (Wille et al., 2014; Yoo et al., 2017; Nguyen et al., 2023) is higher than that of ordinary fiber-reinforced concrete. However, considering the cost and construction conditions, steel fiber-reinforced concrete specimen (SFRC) (Li et al., 2018; Chu et al., 2023) is still one of the most common FRCs used in engineering. Although compression also leads to fatigue-related material stiffness degradation, this paper will focus on the tensile fatigue damage of SFRC, considering the significant difference between concrete’s tensile and compressive properties.
In the following study, Section 2 presents the basic framework of the microplane damage model for plain concrete, including the three processes of projecting macrostrain to micro-strain, establishing the stress-strain relationship on the microplane, and homogenizing microstress to macro-stress. Section 3 describes how to extend the microplane model from plain concrete to steel fiber-reinforced concrete and how to consider fatigue effects in the microplane damage model. Section 4 summarises the numerical algorithm for the microplane model, parameter calibration, and validation of the concrete microplane damage model. Section 5 compares the fatigue damage analysis of plain and steel fiber-reinforced concrete with experimental results. Section 6 summarises the further research focus. Finally, Section 7 summarises the main conclusions of the paper.
2 Microplane damage model for plain concrete
2.1 A framework for microplane theory
The concrete microplane damage model (Caner and Bažant, 2013a; Caner and Bazant, 2013b) consists of three parts: physical mapping of “macro to micro physical variables,” establishment of constitutive relationship at the micro scale, and homogenization of “micro to macro physical variables,” as shown in Figure 1.
2.2 Macroscale to microscale strain decomposition
The microplane model portrays the mechanical behavior of concrete materials at the microscopic level in terms of stresses and strains in vector form, so it is necessary to transform the stresses or strains at the macroscopic level into the stresses or strains at the microscopic level. According to the treatment of the relationship between the macroscopic stress tensor or macroscopic strain tensor and the stress or strain vector on the microplane, they are usually categorized into static and kinematic constraints. They can be understood as the projection of the macroscopic stress tensor on the microplane to obtain the corresponding stress vector and the projection of the macroscopic strain tensor on the microplane to obtain the corresponding strain vector, respectively. Due to the strain-softening behavior of quasi-brittle materials such as concrete, the kinematic constraints shown in Figure 2 are used in the concrete microplane damage model to ensure the stability of the model when analyzing strain softening.
As shown in Figure 2, the strain vector
where
where
2.3 Stress-strain relationships on microplane
2.3.1 Elastic response and stiffness degradation
Unlike the traditional tensor-type constitutive model, the microplane model defines constitutive relations on a general plane (microplane) in any direction at a material point. If the strain component on the microplane has been obtained from kinematic constraints, the general expression for the stress on the microplane is given by Equation 3.
where
When the stress on the microplane develops in the elastic range, the normal strain is not decomposed into its volume component
where
In addition, when the material is in the elastic stage, the modulus of elasticity is gradually degraded due to the progression of damage. The evolution of the microplane normal elastic modulus needs to be considered in the damage variables. Here the current value of the microplane normal elastic modulus damage is calculated by retrieving the largest magnitude of positive and negative normal strains
and in the case of
In Equation 5, the fatigue degradation function
It is worth noting that Equation 5 is used in order to ensure that the unloading moves towards the origin along the initial elastic slope after intersection, rather than continuing along the original unloading path after intersection.
2.3.2 Stress-strain boundaries on microplanes
As shown in Figure 2, the strain on the microplane is divided into normal strain and tangential strain, and normal strain can be divided into tensile strain and compressive strain. For normal tensile strain, the tensile normal stress-strain boundary is introduced to characterize the inelastic response on the microplane. For normal compression strain, the key innovation of M7 that significantly improves it is that when the microplane is under pressure, it no longer separately determines whether the volume stress and deviator stress exceed the boundary, but calculates the two boundary values separately and then sums them up, i.e.,
2.3.2.1 Normal tensile stress-strain boundary
Figure 3A shows that the normal tensile stress-strain boundary controls the tensile fracture behavior, calculated by Equation 8.
where
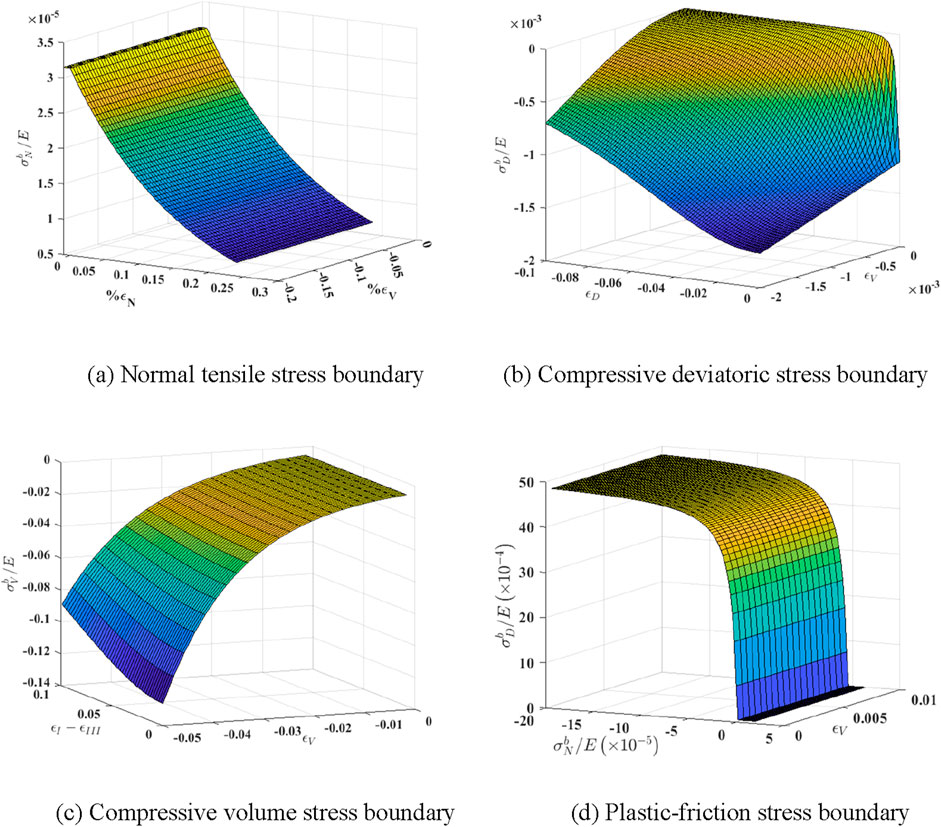
Figure 3. Stress-strain boundaries on the microplane. (A) Normal tensile stress boundary. (B) Compressive deviatoric stress boundary. (C) Compressive volume stress boundary. (D) Plastic-friction stress boundary.
2.3.2.2 Compressive deviatoric stress-strain boundary
Figure 3B shows that the compression deviatoric stress-strain boundary is used to model the damage evolution under compression conditions, calculated by Equation 9.
where
2.3.2.3 Compressive volume stress-strain boundary
As shown in Figure 3C, the compressive volumetric stress-strain boundary is used to model pore collapse and expansion rupture of the material, calculated by Equation 10.
where
2.3.2.4 Plastic-friction stress-strain boundary (shear boundary)
As shown in Figure 3D, the plastic-friction boundary is used to model the shear behavior of the material, calculated by Equation 11.
where
2.3.3 Yielding and plastic flow criteria on microplane
The yield condition and plastic flow criterion on the microplane are defined as follows: when the stress on the microplane lies within the stress-strain boundary, the stress-strain on the microplane is in the elastic phase. At this time, the stress is given by
The shear stress on the microplane is given by Equation 13.
Where the incremental, cumulative form of the formula for calculating the shear stress in the elastic phase on the microplane is given by Equations 14–16.
2.4 Homogenization from microscale to macroscale
After defining the stress-strain relationship on the microplane, the principle of virtual work is applied to establish the equation between the microplane stress vector and the macroscopic stress tensor, from which the macroscopic stress tensor
where
The integral is approximated by the optimal Gaussian integral formula for the sphere, denoting the weighted sum of microplane in the direction
3 Microplane model extend to steel fiber-reinforced concrete and fatigue damage
3.1 Extend to fiber-reinforced concrete
The simplest way to extend the plain concrete microplane model to make it applicable to SFRC containing materials such as steel fibers is to adjust the stress-strain boundary conditions on the microplane (Caner et al., 2013). First, fibers usually increase the tensile capacity of the concrete material (Jiang et al., 2023; Lakavath et al., 2024), so the effect of steel fiber reinforcement needs to be introduced on the normal tensile stress-strain boundary. The contribution of fiber reinforcement is given by a simplified form of the Kholmyansky equation (Kholmyansky, 2002), as Equation 20.
This contribution is obtained by the gradual activation of the bridging of the fibers during the development of the crack, as shown in Figure 4. Assuming parallel coupling of the fibers and the matrix, the normal stress on the microplane is Equation 21.
where
In addition, the tensile capacity that steel fiber-reinforced concrete can withstand changes (increases or decreases) before cracks develop. Therefore, the normal tensile stress-strain boundary Equation 8 of the plain concrete matrix needs to be adjusted to Equation 23.
Secondly, the addition of steel fibers changes the compressive capacity of the concrete material, especially the shear expansion deformation, so the compressive deviatoric stress-strain boundary condition Equation 9 needs to be adjusted to Equation 24.
Finally, steel fibers change the mechanical behavior of concrete in triaxial compression, so the plastic-friction boundary Equation 11 needs to be adjusted to Equation 25.
where
The microplane model of steel fiber-reinforced concrete is based on the microplane model of plain concrete. Therefore to calibrate its parameters, it is necessary to calibrate the parameters of plain concrete first. Then from the uniaxial tensile data of SFRC,
3.2 Extend to fatigue damage
In the concrete microplane damage model, taking the stretch shown in Equation 5 as an example, the damage behavior of concrete under several cycles can be described by assuming that the elastic modulus
where
3.2.1 Fatigue history variable
The fatigue damage variable is denoted as
The fatigue damage behavior of concrete under compressive loading can be used as a fatigue variable for compressive fatigue damage by using the normal negative strain,
3.2.2 Fatigue damage estimation
Next, the stiffness degradation of the material is related to the fatigue damage history variables. A model is obtained that is suitable for both fatigue damage analyses without affecting the calibration of the parameters of the original microplane model. The material stiffness degradation on the microplane is represented by the damage parameter
Then, introduce
where
Usually taking
Similarly,
4 Numerical implementation, parameter calibration and model validation
4.1 Numerical implementation
In the numerical implementation, it is necessary to incorporate the crack band model to reduce the mesh size sensitivity of the computed results (Bažant and Oh, 1983; Červenka et al., 2005). In ABAQUS commercial finite element software, VUMAT subroutine is written for numerical implementation. If the stress tried exceeds the stress-strain boundary, it is necessary to keep the strain and limit the stress to the stress-strain boundary. In the finite element method program, if the strain increment
Step 1. First, the strain and strain increment on the microplane are calculated by Equation 33 according to Equation 1,
Step 2. Calculate the volumetric strain and its increment at the end of the previous and current steps, based on the given strain and its increment by Equation 34.
Then, calculate
and
Step 3. Calculate the
Step 4. Calculate the normal tensile boundary
Step 5. Holding the strain constant and allowing the stress to drop vertically to the normal tensile stress-strain boundary by Equation 37.
Meanwhile, update the history maxima
Step 6. Calculate an approximation of the current volumetric stress by Equation 38.
Retrieve the originally stored microplane shear stresses
Step 7. Calculate the shear response upon return to the stress-strain boundary by Equations 12–16.
Step 8. The stress
4.2 Parameter calibration
In the microplane model (M7), the shape of the response curve is determined by five free parameters and twenty-one fixed parameters. Tables 1, 2 provide a concise explanation of the meaning and default value of each parameter. The fixed parameters, as detailed in Table 1, are calibrated using the uniaxial compressive strength
To optimize the fitting of a large amount of experimental data, it is not necessary to change all five free parameters simultaneously in the actual microplane model (Caner and Bažant, 2013a; Caner and Bazant, 2013b). The elastic modulus
4.3 Validation of representative examples
4.3.1 Plain concrete specimen
First, the uniaxial compression test of Chern et al. (1993) was fitted to the elastic modulus
Next, a triaxial compression experiment of concrete under hydrostatic pressure was fitted. Plain concrete material parameters (Chern et al., 1993): elastic modulus
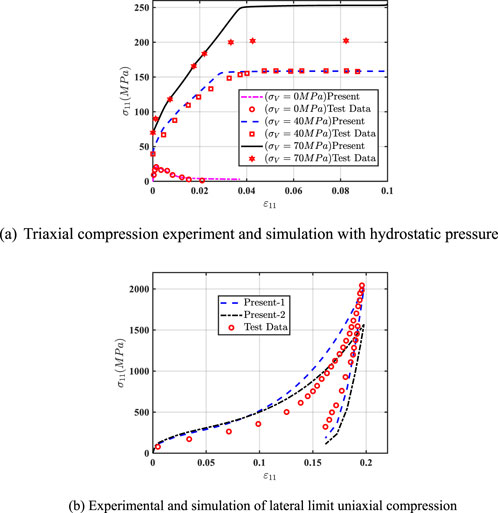
Figure 7. Experimental and simulation of compression. (A) Triaxial compression experiment and simulation with hydrostatic pressure. (B) Experimental and simulation of lateral limit uniaxial compression.
Then, the mechanical behavior of plain concrete under side-limited uniaxial compression was fitted. The plain concrete material parameters (Caner and Bazant, 2013a): elastic modulus
4.3.2 Steel fiber-reinforced concrete specimen
In this section, the mechanical response of steel fiber-reinforced concrete is analyzed. The parameter calibration was performed for fiber reinforced, as shown in Table 3 (Caner et al., 2013). The experimental and simulation results of FRC containing carbon steel fibers (fiber volume admixture
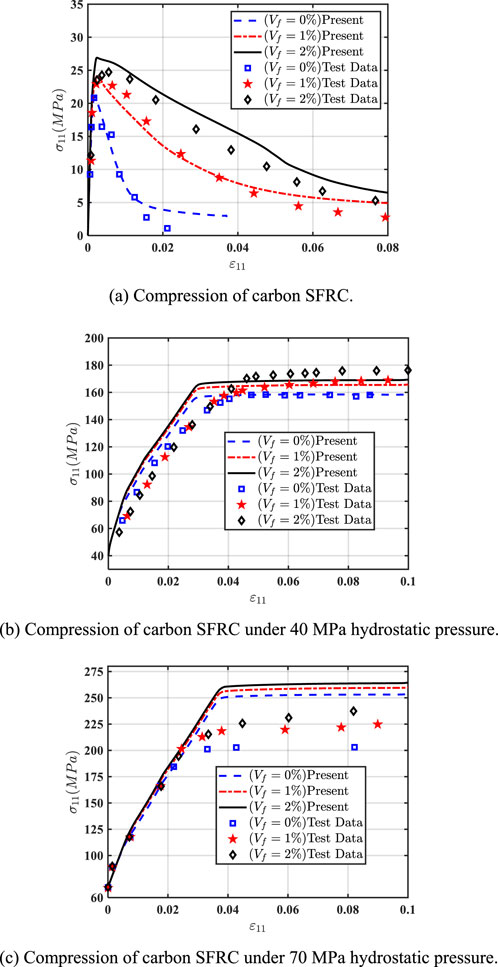
Figure 8. Experiment and simulation of carbon SFRC. (A) Compression of carbon SFRC. (B) Compression of carbon SFRC under 40 MPa hydrostatic pressure. (C) Compression of carbon SFRC under 70 MPa hydrostatic pressure.
5 Fatigue damage analysis
5.1 Plain concrete material
In this section, we consider a notched plain concrete beam of depth
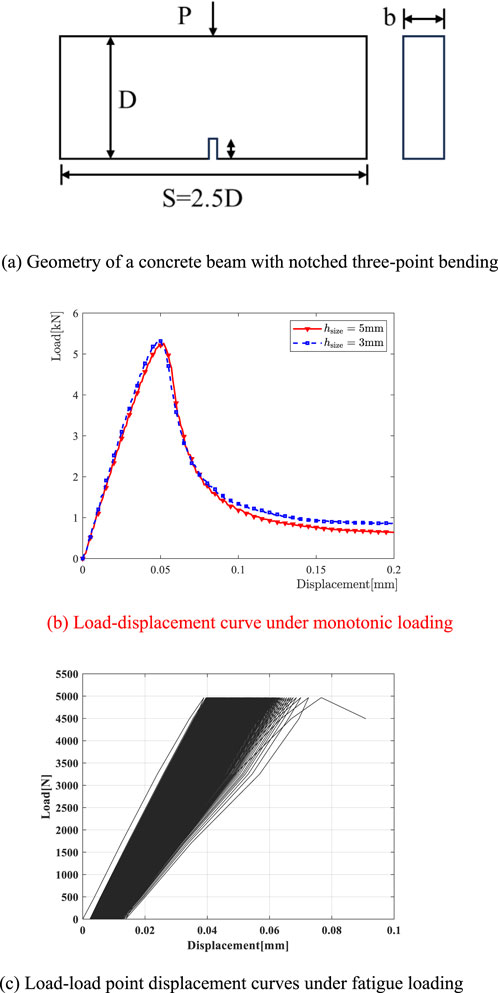
Figure 9. Simulated load-displacement curve under monotonic and fatigue loading. (A) Geometry of a concrete beam with notched three-point bending. (B) Load-displacement curve under monotonic loading. (C) Load-load point displacement curves under fatigue loading.
Next, the fatigue simulation of a three-point bending beam was performed. Cyclic loading was applied up to
5.2 Steel fiber-reinforced concrete material
Then, the fatigue damage behavior of steel fiber-reinforced concrete is analyzed. A three-point bending beam (Qing et al., 2023) with notched specimen size
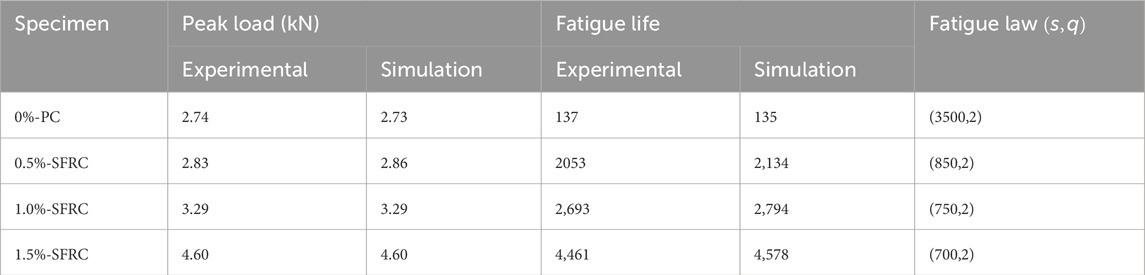
Table 5. Experiments and simulations of monotonic and fatigue loading of steel fiber reinforced concrete.
Next, fatigue analysis of fiber-reinforced concrete three-point bending beams was performed. The maximum applied cyclic load was 85% of the monotonically loaded peak load. The fatigue damage law parameters were adjusted until the life prediction was close enough. The strains of SFRC three-point bending beam with 0.5% volume steel fiber admixture for the one cycle before fatigue loading failure are shown in Figure 10A, and the strains for the remaining three groups are similar. The fatigue damage metric used is Equation 31, and the calibrated fatigue damage law parameters are shown in Table 5 for various fiber-reinforced concretes. The corresponding material fatigue damage law is shown in Figure 10B. The fatigue resistance of concrete is gradually improved with the increase of steel fiber mixing, and the fatigue resistance improvement is gradually slowed down when the steel fiber admixture is more than 1%. Therefore, the present model can be well used to analyze the mechanical response of fiber-reinforced concrete under monotonic and fatigue loading.
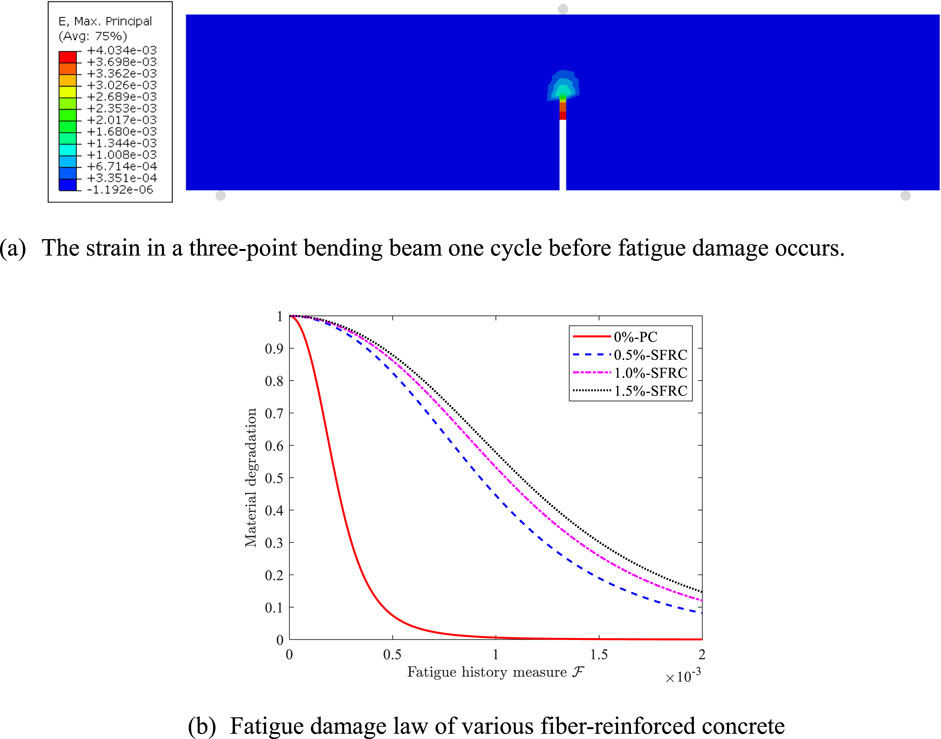
Figure 10. The strain in a three-point bending beam and fatigue damage law. (A) The strain in a three-point bending beam one cycle before fatigue damage occurs. (B) Fatigue damage law of various fiber-reinforced concrete.
5.3 Plain and steel fiber-reinforced concrete beam
Fatigue damage modeling ultimately aims to fine-tune the analysis of the whole process of fatigue damage in concrete structures. This section simulates the fatigue damage of reinforced concrete beams using the proposed model as an illustrative study. The cross-section height of the concrete beam is
First, a numerical simulation of the four-point bending of reinforced concrete beams (
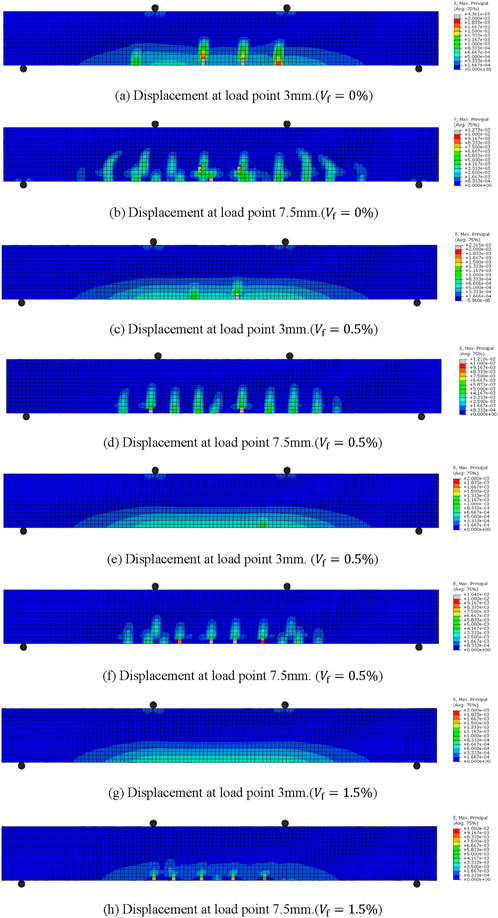
Figure 13. Strain in reinforced concrete beams under monotonic loading. (A) Displacement at load point 3 mm (
Next, fatigue damage simulations of reinforced concrete structures (
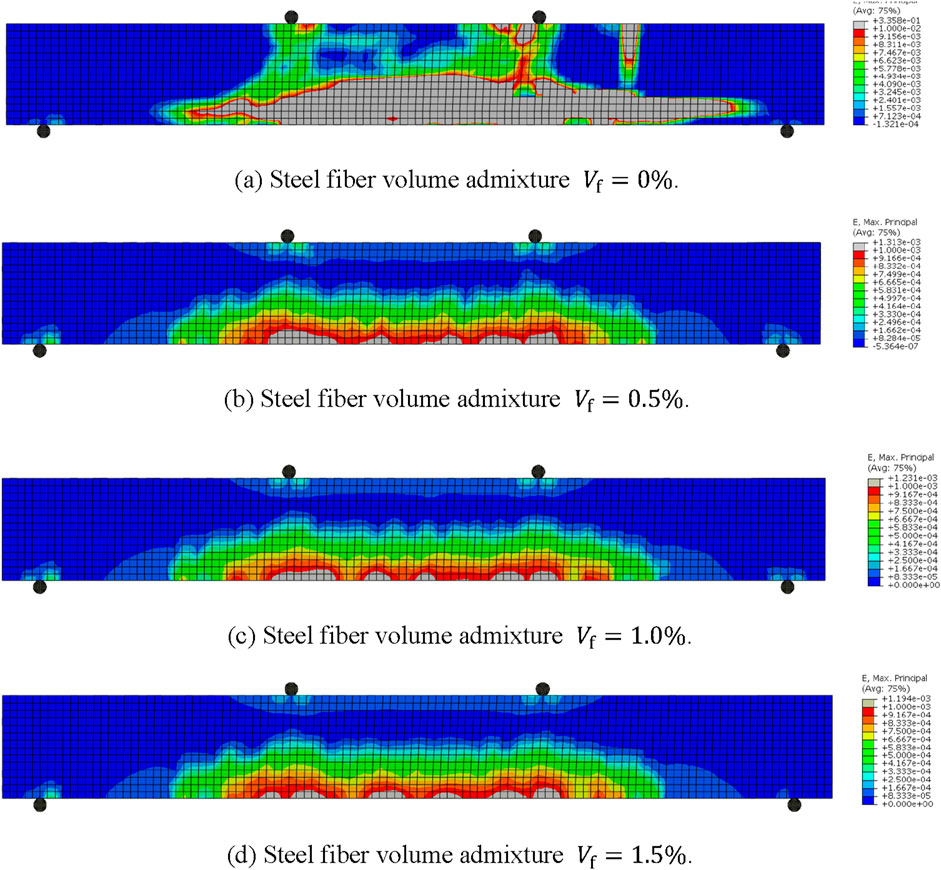
Figure 14. Reinforced concrete beam strains after fatigue loading. (A) Steel fiber volume admixture
It is worth noting that for the fatigue of reinforced concrete structures, to capture the various mechanical behaviors in the tests, the slip between the concrete and the reinforcement also needs to be considered, and the degradation of the fatigue properties of materials such as reinforcement and fibers needs to be considered. However, this is not the focus of this study and will be illustrated in future studies. This model is expected to be used for the whole-process analysis of fatigue damage of plain concrete and steel fiber-reinforced concrete structures under complex loading conditions and structural forms, which will facilitate engineering design, evaluation, and optimization.
6 Further study
Despite the success in expanding the application of microplanar modeling of plain concrete, many issues need to be solved. In subsequent research, the following issues will be focused on:
(1) simplifying the extremely cumbersome parameters in M7 and developing user-friendly software tools or plug-ins.
(2) Consider the fatigue-related material stiffness under compression conditions and extend the model to compression fatigue analysis.
(3) Optimize the fiber toughening mechanism and expand the model to fatigue damage analysis of concrete materials such as ECC and UHPFRC.
7 Conclusion
This study successfully extends the microplane model for assessing fatigue damage in steel fiber-reinforced concrete (SFRC). The model combines material stiffness degradation, critical for analyzing fatigue damage, with fatigue history variables accumulated during cyclic loading. A more detailed prediction of the fatigue life and behavior of plain and steel fiber-reinforced concrete materials is possible. The following conclusions were obtained:
(1) The extended microplane model is suitable for mechanical response analysis of steel fiber-reinforced concrete materials. It provides an effective tool for predicting fatigue damage of concrete structures under cyclic loading by introducing fatigue history variables and establishing their relationship with material stiffness degradation.
(2) It is shown that steel fiber incorporation can substantially improve concrete’s mechanical properties and fatigue resistance. The extended model can capture the reinforcing effect of fibers, which is consistent with the experiments.
(3) The model’s parameters can be calibrated against benchmark experimental data. The model can be implemented numerically in ABAQUS commercial finite element software in conjunction with a crack band model for engineering analysis.
(4) The model can predict the fatigue life and mechanical behavior of plain and steel fiber-reinforced concrete materials, which helps in engineering design and optimization. Next, it is expected to be used for fatigue analysis of concrete structures under complex loading conditions and structural forms by considering the slip of reinforcement with concrete and the degradation of the fatigue performance of reinforcement.
Data availability statement
The original contributions presented in the study are included in the article/supplementary material, further inquiries can be directed to the corresponding author.
Author contributions
CQ: Methodology, Supervision, Writing–original draft, Writing–review and editing. XD: Funding acquisition, Resources, Writing–original draft. BW: Data curation, Investigation, Writing–original draft. LC: Validation, Visualization, Writing–original draft. SW: Formal Analysis, Project administration, Writing–original draft. QX: Conceptualization, Software, Writing–review and editing, Writing–original draft.
Funding
The author(s) declare that financial support was received for the research, authorship, and/or publication of this article. The research described in this paper was financially supported by the China Construction Third Bureau First Engineering Co., Ltd. (Grant No. CSCEC3B1C-2022-13).
Conflict of interest
Authors CQ, XD, BW, LC, and SW were employed by China Construction Third Bureau First Engineering Co., Ltd.
The remaining author declares that the research was conducted in the absence of any commercial or financial relationships that could be construed as a potential conflict of interest.
The authors declare that this study received funding from China Construction Third Bureau First Engineering Co., Ltd. The funder had the following involvement in the study: study design, data collection, funding acquisition, preparation of the paper, and decision to submit it for publication.
Generative AI statement
The author(s) declare that no Generative AI was used in the creation of this manuscript.
Publisher’s note
All claims expressed in this article are solely those of the authors and do not necessarily represent those of their affiliated organizations, or those of the publisher, the editors and the reviewers. Any product that may be evaluated in this article, or claim that may be made by its manufacturer, is not guaranteed or endorsed by the publisher.
References
Aguilar, M., Baktheer, A., and Chudoba, R. (2022). “Numerical investigation of load sequence effect and energy dissipation in concrete due to compressive fatigue loading using the new microplane fatigue model MS1,” in Presentations and videos to 16th International Conference on Computational Plasticity (COMPLAS 2021). IS17-Multiscale Modelling of Concrete and Concrete Structures. doi:10.23967/complas.2021.053
Baktheer, A., Aguilar, M., and Chudoba, R. (2021). Microplane fatigue model MS1 for plain concrete under compression with damage evolution driven by cumulative inelastic shear strain. Int. J. Plasticity 143, 102950. doi:10.1016/j.ijplas.2021.102950
Bažant, Z. P., and Oh, B. H. (1983). Crack band theory for fracture of concrete. Mat. Constr. 16, 155–177. doi:10.1007/BF02486267
Bazant, Z. P., and Schell, W. F. (1993). Fatigue fracture of high-strength concrete and size effect. Mater. J. 90, 472–478. doi:10.14359/3880
Bažant, Z. P., Xiang, Y., and Prat, P. C. (1996). Microplane model for concrete. I: stress-strain boundaries and finite strain. J. Eng. Mech. 122, 245–254. doi:10.1061/(ASCE)0733-9399(1996)122:3(245)
Caner, F. C., and Bažant, Z. P. (2013a). Microplane model M7 for plain concrete. I: formulation. J. Eng. Mech. 139, 1714–1723. doi:10.1061/(ASCE)EM.1943-7889.0000570
Caner, F. C., and Bazant, Z. P. (2013b). Microplane model M7 for plain concrete. II: calibration and verification. J. Eng. Mech. 139, 1724–1735. doi:10.1061/(ASCE)EM.1943-7889.0000571
Caner, F. C., Bažant, Z. P., and Wendner, R. (2013). Microplane model M7f for fiber reinforced concrete. Eng. Fract. Mech. 105, 41–57. doi:10.1016/j.engfracmech.2013.03.029
Carlesso, D. M., de la Fuente, A., and Cavalaro, S. H. P. (2019). Fatigue of cracked high performance fiber reinforced concrete subjected to bending. Constr. Build. Mater. 220, 444–455. doi:10.1016/j.conbuildmat.2019.06.038
Červenka, J., Bažant, Z. P., and Wierer, M. (2005). Equivalent localization element for crack band approach to mesh-sensitivity in microplane model. Int. J. Numer. Methods Eng. 62, 700–726. doi:10.1002/nme.1216
Chern, J., Yang, H., and Chen, H. (1993). Behavior of steel fiber reinforced concrete in multiaxial loading. Mater. J. 89. doi:10.14359/1242
Chu, S. H., Unluer, C., Yoo, D. Y., Sneed, L., and Kwan, A. K. H. (2023). Bond of steel reinforcing bars in self-prestressed hybrid steel fiber reinforced concrete. Eng. Struct. 291, 116390. doi:10.1016/j.engstruct.2023.116390
Cornelissen, H. A. W. (1984). Fatigue failure of concrete in tension. HERON 29 (4), 1–68. Available at: https://www.semanticscholar.org/paper/Fatigue-Failure-of-Concrete-in-Tension-Cornelissen/660b8ce20194711cb9477f0f6fc30503c637af43 (Accessed June 25, 2023).
Gylltoft, K. (1984). A fracture mechanics model for fatigue in concrete. Mat. Constr. 17, 55–58. doi:10.1007/BF02474057
Hillerborg, A., Modéer, M., and Petersson, P.-E. (1976). Analysis of crack formation and crack growth in concrete by means of fracture mechanics and finite elements. Cem. Concr. Res. 6, 773–781. doi:10.1016/0008-8846(76)90007-7
Huang, B.-T., Zhu, J.-X., Weng, K.-F., Li, V. C., and Dai, J.-G. (2022). Ultra-high-strength engineered/strain-hardening cementitious composites (ECC/SHCC): material design and effect of fiber hybridization. Cem. Concr. Compos. 129, 104464. doi:10.1016/j.cemconcomp.2022.104464
Jiang, J., Luo, Q., Wang, F., Sun, G., and Liu, Z. (2023). Uniaxial tensile constitutive model of fiber reinforced concrete considering bridging effect and its numerical algorithm. J. Sustain. Cement-Based Mater. 12, 207–217. doi:10.1080/21650373.2022.2034549
Kholmyansky, M. M. (2002). Mechanical resistance of steel fiber reinforced concrete to axial load. J. Mater. Civ. Eng. 14, 311–319. doi:10.1061/(ASCE)0899-1561(2002)14:4(311)
Kirane, K., and Bažant, Z. P. (2015). Microplane damage model for fatigue of quasibrittle materials: sub-critical crack growth, lifetime and residual strength. Int. J. Fatigue 70, 93–105. doi:10.1016/j.ijfatigue.2014.08.012
Lakavath, C., Prakash, S. S., and Allena, S. (2024). Tensile characteristics of ultra-high-performance fibre-reinforced concrete with and without longitudinal steel rebars. Mag. Concr. Res. 76, 738–754. doi:10.1680/jmacr.23.00181
Li, B., Chen, Z., Wang, S., and Xu, L. (2024). A review on the damage behavior and constitutive model of fiber reinforced concrete at ambient temperature. Constr. Build. Mater. 412, 134919. doi:10.1016/j.conbuildmat.2024.134919
Li, B., Chi, Y., Xu, L., Li, C., and Shi, Y. (2018). Cyclic tensile behavior of SFRC: experimental research and analytical model. Constr. Build. Mater. 190, 1236–1250. doi:10.1016/j.conbuildmat.2018.09.140
Lu, C., Leung, C. K. Y., and Li, V. C. (2017). Numerical model on the stress field and multiple cracking behavior of Engineered Cementitious Composites (ECC). Constr. Build. Mater. 133, 118–127. doi:10.1016/j.conbuildmat.2016.12.033
Marigo, J. J. (1985). Modelling of brittle and fatigue damage for elastic material by growth of microvoids. Eng. Fract. Mech. 21, 861–874. doi:10.1016/0013-7944(85)90093-1
Miarka, P., Seitl, S., Bílek, V., and Cifuentes, H. (2022). Assessment of fatigue resistance of concrete: S-N curves to the Paris’ law curves. Constr. Build. Mater. 341, 127811. doi:10.1016/j.conbuildmat.2022.127811
Nguyen, D.-L., Le, H.-V., Vu, T.-B.-N., Nguyen, V.-T., and Tran, N.-T. (2023). Evaluating fracture characteristics of ultra-high-performance fiber-reinforced concrete in flexure and tension with size impact. Constr. Build. Mater. 382, 131224. doi:10.1016/j.conbuildmat.2023.131224
Paris, P., and Erdogan, F. (1963). A critical analysis of crack propagation laws. J. Basic Eng. 85, 528–533. doi:10.1115/1.3656900
Qing, L., Wang, Y., Li, M., and Mu, R. (2023). Fatigue life and fracture behaviors of aligned steel fiber reinforced cementitious composites (ASFRC). Int. J. Fatigue 172, 107643. doi:10.1016/j.ijfatigue.2023.107643
Riyar, R. L., Mansi, M., and Bhowmik, S. (2023). Fatigue behaviour of plain and reinforced concrete: a systematic review. Theor. Appl. Fract. Mech. 125, 103867. doi:10.1016/j.tafmec.2023.103867
Wille, K., El-Tawil, S., and Naaman, A. E. (2014). Properties of strain hardening ultra high performance fiber reinforced concrete (UHP-FRC) under direct tensile loading. Cem. Concr. Compos. 48, 53–66. doi:10.1016/j.cemconcomp.2013.12.015
Yoo, D.-Y., Kim, S., Park, G.-J., Park, J.-J., and Kim, S.-W. (2017). Effects of fiber shape, aspect ratio, and volume fraction on flexural behavior of ultra-high-performance fiber-reinforced cement composites. Compos. Struct. 174, 375–388. doi:10.1016/j.compstruct.2017.04.069
Zhang, H., Chen, S., Zhang, W., and Liu, X. (2024). Service life evaluation of curved intercity rail bridges based on fatigue failure. Infrastructures 9, 139. doi:10.3390/infrastructures9090139
Keywords: material stiffness degradation, fatigue damage, plain concrete, steel fiber-reinforced concrete, microplane model
Citation: Qin C, Dong X, Wu B, Cai L, Wang S and Xia Q (2024) Fatigue damage analysis of plain and steel fiber-reinforced concrete material based on a stiffness degradation microplane model. Front. Mater. 11:1505295. doi: 10.3389/fmats.2024.1505295
Received: 02 October 2024; Accepted: 04 November 2024;
Published: 12 December 2024.
Edited by:
Ping Xiang, Central South University, ChinaReviewed by:
Amir Ali Shahmansouri, Washington State University, United StatesHan Zhao, City University of Hong Kong, Hong Kong SAR, China
Yao JingRu, Shandong Jianzhu University, China
Copyright © 2024 Qin, Dong, Wu, Cai, Wang and Xia. This is an open-access article distributed under the terms of the Creative Commons Attribution License (CC BY). The use, distribution or reproduction in other forums is permitted, provided the original author(s) and the copyright owner(s) are credited and that the original publication in this journal is cited, in accordance with accepted academic practice. No use, distribution or reproduction is permitted which does not comply with these terms.
*Correspondence: Qing Xia, YXppbGlhb25Ab3V0bG9vay5jb20=