- 1The Engineering and Technical College of Chengdu University of Technology, Leshan, Sichuan, China
- 2College of Aviation Engineering, Civil Aviation Flight University of China, Guanghan, Sichuan, China
This paper provides a comprehensive review of current and prospective technologies for recycling carbon fiber reinforced polymer (CFRP), addressing the growing need for sustainable disposal and resource recovery driven by increasing CFRP applications. Four primary recycling methods are discussed: incineration, physical recycling, chemical recycling, and thermal recycling. Incineration, while offering energy recovery, is unsustainable due to limited material recovery and environmental pollution. Physical recycling, utilizing mechanical processes, is cost-effective but results in significant fiber degradation, restricting applications to low-value fillers. Chemical recycling, involving solvent or acid-based resin decomposition, can yield high-quality fibers but faces challenges regarding environmental impact, process efficiency, and economic viability. Thermal recycling, encompassing pyrolysis in various configurations (conventional, fluidized bed, and microwave), emerges as the most promising approach, offering reasonable recovery rates and acceptable fiber properties, albeit with concerns about energy consumption and potential fiber damage. The review critically evaluates each method based on recovery efficiency, recovered fiber quality, environmental impact, and economic feasibility. It highlights the need for future research focusing on developing greener chemical solvents and catalysts, optimizing thermal processes and exploring product valorization, and investigating novel recycling technologies such as supercritical fluids, bio-based methods, and electrochemical approaches. Furthermore, it emphasizes the importance of establishing comprehensive performance evaluation standards for recycled fibers, exploring surface modification techniques, and expanding application possibilities. Life cycle assessment, economic analysis, and strengthened collaborations among academia, industry, and government are also crucial for advancing CFRP recycling towards industrialization and promoting a circular economy within the composites sector.
Highlights
• Analyzes four CFRP recycling methods: incineration, physical, chemical, and thermal.
• Evaluates CFRP recycling: benefits, drawbacks, applications, and future prospects.
1 Introduction
CFRP, with its exceptional properties like light weight, high strength, corrosion resistance, fatigue resistance, excellent moldability, and design flexibility (Kojima and Furukawa, 1997; He et al., 2007; Liang quan, 2011; Gore and Kandasubramanian, 2018), is widely used in aerospace, new energy, automotive, rail transit, construction, and other fields (Jayalakshmi et al., 2019; Bintai et al., 2016; Xing, 2017; Das et al., 2019). Nevertheless, as with all materials, CFRP is subject to a finite lifespan. The long-term durability issues and eventual failure of CFRP inevitably result in a considerable amount of waste, which presents a significant challenge to the sustainability of the environment and natural resources.
Current waste management strategies for composite materials primarily depend on traditional methods such as incineration and landfilling, with landfilling being the main approach for most fiber-reinforced polymers (FRPs) (Naqvi et al., 2018; Krauklis et al., 2021; Deng et al., 2021). However, landfilling wastes substantial land resources and leads to soil and water contamination, while incineration contributes to greenhouse gas emissions (Li et al., 2016). Neither approach qualifies as recycling, as they fail to enable effective material recovery and reuse (Jang et al., 2020; Dong et al., 2015; Zhou et al., 2021). To underscore the urgency of this issue and the necessity of recycling, we examine global demand distribution, application areas, manufacturing processes, and waste generation patterns for carbon fiber and CFRP (Zhang et al., 2020) (Figure 1). As shown in Figure 1, wind energy (24.1%) and aerospace (23.2%) are the largest consumers of carbon fiber, where lightweight and high-strength materials are essential. However, these sectors also produce substantial waste. The aerospace industry alone accounts for 73.4% of total CFRP sales and generates a large volume of waste, primarily concentrated in Asia (26.8%), North America (22.9%), and Europe (22.9%). Recycling in these high-consumption regions could significantly reduce environmental impact and reliance on virgin materials, resulting in notable economic benefits. Geographical distribution also shapes recycling demand, with North America (40%) and Europe (25%) as primary markets and Asia (12%) following closely. Many countries now incentivize sustainable waste management, such as the UK’s landfill taxes and Europe’s landfill bans aimed at reducing municipal waste by 10% by 2030 (Shuaib and Mativenga, 2016; Bernatas et al., 2021). With increasingly stringent environmental regulations, the need for CFRP recycling and reuse grows more pressing, driven by high demand and substantial waste production. Recycling not only offers material cost savings but also promotes circular resource utilization, achieving both environmental protection and economic gains. Table 1 summarizes CFRP waste sources, types, and traditional treatment methods. CFRP recycling also faces manufacturing-related challenges. Prepreg (39.9%) and pultrusion/filament winding (26%) are dominant production methods, with prepreg recycling being particularly complex due to its intricate structure. Given its extensive use in aerospace and wind energy, overcoming prepreg recycling obstacles could reduce waste and offer significant economic gains. Regulations like the European End-of-Life Vehicle Directive, which mandates the recovery or reuse of 85% of vehicle components by weight (Petrakli et al., 2020), and strict European Commission regulations on construction, vehicles, and electronics (Correia et al., 2011; Gharde and Kandasubramanian, 2019) are further driving the composites industry to adopt innovative recycling strategies. China’s 2021 guidelines for establishing a green, low-carbon, and circular economy underscore the importance of CFRP recycling technology and reuse. These factors highlight the need for sustainable practices in the CFRP industry, with recycling as a key solution. As global demand for lightweight materials rises, CFRP production expands, while traditional recycling methods remain inefficient and costly. Therefore, developing an efficient, economical, and environmentally friendly recycling system is crucial. This will require increased investment in R&D for innovative recycling technologies, supportive government policies, and enhanced industry collaboration to create a robust CFRP recycling ecosystem. This comprehensive approach is essential not only for environmental protection but also for the long-term viability and sustainability of the CFRP industry. Compared to other fiber-reinforced composites, CFRP recycling poses greater challenges but also presents higher economic value. CFRP’s superior strength, stiffness, lightweight characteristics, and corrosion resistance make it valuable in demanding applications like aerospace and automotive. While GFRP and BFRP perform well, CFRP’s advantages in strength-to-weight and stiffness-to-weight ratios are significant. However, this performance also increases recycling complexity and potential rewards. CFRP’s high initial cost limits widespread adoption, and its unique properties make it susceptible to performance degradation during recycling, impacting the market demand and value of recovered materials. Efficient CFRP recycling not only reduces pollution but also conserves raw materials, lowers production costs, and supports sustainable resource utilization, critical for high-end manufacturing. Effective CFRP recycling requires careful separation and processing of fibers and matrix to preserve fiber performance. Chemical and thermal recycling surpass traditional mechanical methods in achieving high recovery efficiency and minimizing fiber degradation. Advances in recycling technology could enable recycled CFRP use not only in non-structural applications but potentially in high-performance sectors. For high-end manufacturing, CFRP recycling significantly cuts production costs and improves resource utilization, fostering sustainable development. Research into CFRP recycling technologies that enhance efficiency and reduce performance degradation is essential to maximize resource circularity and environmental protection. Process optimization, cost reduction, and performance improvements in recovered materials will expand CFRP applications and contribute to sustainable high-performance materials.
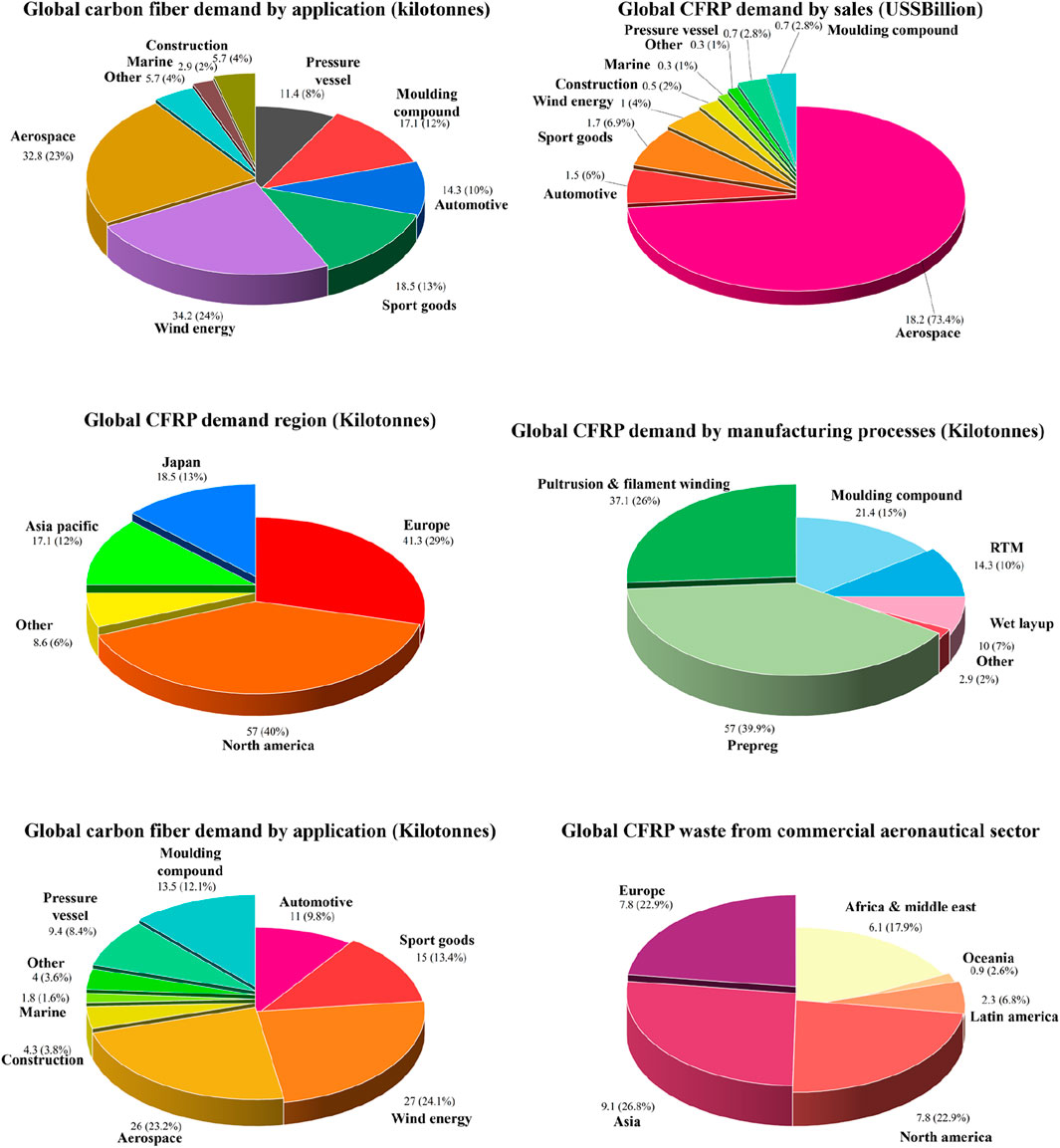
Figure 1. Global CFRP demand in 2018 by (A) application, (B) sales, (C) region and (D) manufacturing processes; global carbon fiber demand by application in 2020 (E), global CFRP waste from commercial aeronautical sector by region in 2050 (F). Redrawn and reproduced with permission from Elsevier (Zhang et al., 2020).
GFRP, despite its valuable properties and broad applications, also faces sustainability challenges due to durability issues and waste accumulation. Research by Xian et al. (2024a), Xian et al. (2024b) on the long-term performance of GFRP rebars and plates in various environments reveals declines in mechanical properties due to water absorption, temperature, stress, and hygrothermal conditions, predicting finite service life and eventual waste generation. Xian et al. (2024c) also notes the impact of manufacturing processes on GFRP rebar performance, where fiber twisting, interfacial debonding, and stress concentrations during bending reduce strength and increase failure risks, emphasizing the need for recycling. These studies affirm the inevitability of GFRP failure and waste generation, underscoring the importance of efficient recycling strategies. Recycling GFRP promotes circularity and environmental protection by reducing virgin material reliance, minimizing pollution, and recovering valuable fiber and resin resources, aligning with circular economy principles. However, efficient GFRP recycling requires careful consideration of the resin matrix type’s complexity and feasibility. Thermoset GFRPs, with their highly cross-linked structures (e.g., epoxy), are challenging to re-melt and reprocess, posing significant recycling obstacles. Existing methods, such as mechanical grinding, pyrolysis, and chemical recycling, suffer from low efficiency, high energy consumption, and secondary pollution. Research on advanced recycling technologies like selective resin dissolution, supercritical fluid technology, efficient glass fiber separation, large-scale reuse, and new recyclable/degradable thermoset resins is crucial. In contrast, thermoplastic GFRPs (e.g., polypropylene-based) offer easier recycling through melt reprocessing and injection molding, retaining material properties and providing economic and environmental benefits. Optimizing mechanical recycling and reuse processes for thermoplastic GFRPs, improving recycled product performance, expanding applications, and developing high-performance recyclable thermoplastic resin matrices are key to enhancing circularity. Developing efficient, economical, and environmentally friendly GFRP recycling technologies with tailored strategies for thermoset and thermoplastic GFRPs is essential for sustainable development in the composites industry.
The novelty of this study lies in its systematic comparison of CFRP recycling methods and forward-looking perspective on future directions. We analyze four primary CFRP recycling methods (mechanical, pyrolysis, chemical, and solvent recycling) alongside recent advancements. Beyond traditional reviews, we detail each method’s core principles, efficiency, cost-effectiveness, and environmental impact. This multi-faceted evaluation clarifies each method’s suitability for specific applications and identifies bottlenecks. Additionally, we examine the integrated operational pathways of these recycling methods, providing guidance for future technology selection and optimization. This comprehensive comparison offers a unique perspective on CFRP recycling, setting the stage for future innovation and practical applications. Achieving these advancements requires collaboration among academia, industry, and government to support technological R&D, policy development, and industry synergy, establishing a comprehensive recycling ecosystem for both CFRP and GFRP.
2 Classification of recycling methods
The recycling of carbon fiber reinforced polymers (CFRPs) is closely linked to their distinct physicochemical properties. CFRPs, typically produced through thermo-compression molding, consist of carbon fibers embedded in a resin matrix. This composite material combines excellent mechanical properties with significant anisotropy, low interlaminar strength, and notable differences in physicochemical properties between the fibers and the matrix. These characteristics pose challenges in processing, repair, and especially recycling. Epoxy resins, which make up approximately 80% of CFRP matrices, are favored for their heat, corrosion, and aging resistance, strong adhesion, and excellent mechanical properties. However, the irreversible cross-linking structure formed during curing renders epoxy resin insoluble and non-fusible, complicating CFRP recycling and reuse (Xuan-Jun et al., 2019; Wu et al., 2021; Mishnaevsky et al., 2017; Liu et al., 2022).
Currently, CFRP recycling methods are categorized into three main approaches: pyrolytic, mechanical, and chemical recycling (Figure 2). Table 2 outlines the process characteristics of these methods, comparing their working conditions, recovered fiber quality, and recycling benefits. The pyrolysis method degrades the resin matrix by heating it in various atmospheres to recover relatively pure carbon fibers. While simple and cost-effective, it is difficult to fully prevent oxidative damage to the fibers, even under inert conditions. Incomplete resin degradation and residual pyrolytic carbon on the fiber surface can also reduce the mechanical properties of recycled carbon fiber (rCF). The mechanical recycling method involves shredding and grinding CFRP waste into powder, followed by a separation process to isolate fiber powder from resin powder. Though easy to operate, this method significantly weakens the mechanical properties of the fibers. Moreover, the rCF produced is typically in the form of short fibers or powder, limiting its applications primarily to sheet or block molding compounds or as fillers in building materials. The chemical recovery method employs solvents or acids, along with catalysts, temperature, and pressure, to dissolve the resin matrix and recover purer carbon fibers. This approach better preserves the mechanical properties of the fibers, and some studies have even achieved resin matrix recycling. However, it has notable drawbacks: (1) environmental impact, as the process often generates chemical pollutants harmful to the environment; (2) low recycling efficiency, since the resin dissolves from the surface inward, prolonging the process; and (3) high economic cost, due to the need for corrosion-resistant vessels and pollutant treatment.
In conclusion, each CFRP recycling method has its advantages and limitations, requiring selection based on specific circumstances. Future research should focus on developing more efficient, environmentally friendly, and cost-effective recycling technologies to promote resource recycling and sustainable development.
2.1 Incineration recovery method
The incineration recycling method is mainly to incinerate CFRP directly and then recover the remaining carbon fiber. Incineration was a common means of disposal of waste carbon fiber reinforced polymer (CFRP) In the early days, incineration was a common method for disposing of CFRP waste (Palola et al., 2022). However, incinerating 1 ton of CFRP releases up to 2011 kg of CO₂ (Chen et al., 2023), contributing significantly to greenhouse gas emissions and negatively impacting air quality (Shen et al., 2023; Höhne et al., 2023; Termine et al., 2023; Yuyan et al., 2009; Deng et al., 2023). As environmental awareness has grown, the incineration of CFRP waste has increasingly been restricted. The carbon fiber production process is energy-intensive and costly (Limburg et al., 2019; Deng et al., 2021), and large amounts of carbon fiber waste are generated annually. Therefore, recycling carbon fiber waste offers both environmental and economic benefits. Recycling can reduce pollution, alleviate waste disposal burdens, decrease reliance on new resources, conserve energy, and support the development of a circular economy. It is important to note that incineration, while providing energy recovery, does not involve material recycling. Although some inorganic residues from incineration may be used in the cement industry, this process does not qualify as material recycling. Nevertheless, certain municipal solid waste incineration facilities with high thermal efficiencies are often classified as “recycling” installations. However, a clear distinction between “recycling” and “recovery” is made in the relevant European recycling directives. Currently, heat recovery technologies for CFRP waste are primarily limited to incineration and fluidized bed processes, with the latter showing promise for both incineration and pyrolysis applications. As a result, the prospects for using incineration for carbon fiber recovery are limited, and relevant studies remain scarce. Nanchang University of Aviation Yi can (Yi et al., 2013) and other use of incineration recycling method to recover carbon fiber, recycled carbon fiber combined with a new type of resin through the hand-lay-up molding to get the recycled composites, testing its tensile strength and other properties, found that only the raw material of about 35%–40%. It can be seen that this method is simple and low cost. But the recycling process will produce a large number of harmful substances, while the recycled carbon fiber is only 35%–40% of the raw material. The carbon fiber recovered by this method can only be used to produce a lower level of composite materials, and the strength and toughness of the composite materials produced are lower.
2.2 Physical recovery method
The main principle of the physical recycling method is through CFRP composites are first crushed into small pieces of 50–100 mm size and then ground by ball milling or fluidized bed reactor (Yang et al., 2015). The milled product consists of recyclates of different sizes, which can be classified into fibrous and powdery resin materials after sieving. The recycled fibrous product, which can be used as an additive or reinforcing component of low value-added composites (Ogi et al., 2007), is widely used in the field of infrastructure in materials such as concrete, synthetic panels, iron-making reductions, asphalt and so on (Verma et al., 2018; Meng et al., 2018). Figure 3 shows a schematic diagram of the physical recycling method. This method is only applicable to uncontaminated CFRP waste, and has the advantages of low cost, simple process and no pollutants, but the disadvantages are that the strength of the treated fibers will be severely reduced and the reuse value is low, and they can only be used as some fillers. Mechanical recovery currently faces limitations in fully separating reinforcing fibers from the polymer matrix, resulting in particles containing short fibers and residual matrix material (Rahimizadeh et al., 2020). While this process is cost-effective and has low carbon emissions, the degradation of fiber properties restricts its use in highly loaded structural applications (Rani et al., 2021). In the case of glass fiber reinforced plastic (GFRP) composites, the resin-rich fine powder obtained from recycling is often used as a filler in sheet molding compounds (SMC) or block molding compounds (BMC), replacing virgin fillers like calcium carbonate. Recycled materials can replace up to 10% of the virgin fillers without significantly affecting mechanical properties. The relatively low density of polymers compared to virgin fillers allows the use of recyclates to reduce the weight of the composition by about 5%. However, the low cost of virgin fillers makes this alternative economically uncompetitive (Pickering, 2006). SMC and BMC technologies are widely used in the automotive industry and comply with the 85% reuse criteria for end-of-life vehicles set by Directive 2000/53/EC (Fonte and Xydis, 2021). The automotive industry’s self-organized recycling system is expected to support recycling efforts, though this may limit the use of recycled materials in the wind power sector by other industries. For the wind power industry, recycling is a key goal, but mechanical recycling remains challenging due to the degradation of material properties. For example, recycled fiber-rich materials are of lower quality than virgin reinforcements, and their adhesion to the polymer matrix is poor. Larger particles can lead to stress concentrations, increasing the risk of failure (Pickering, 2006). Beauson et al. explored using recycled glass fiber composites from wind turbine blade load-bearing beams as reinforcing components, creating novel composites through a vacuum injection process. However, the resulting composites exhibited low breaking strength and deformation capacity, which was attributed to insufficient adhesion between the recycled material and the new matrix (Beauson et al., 2016). Furthermore, Palmer et al. emphasized that fine separation of recyclates and precise control during reformulation and production are essential for producing high-quality novel doughy molding compounds (DMCs). Examples of successful mechanical recycling applications include noise barriers made from debris materials by MILJØSKÆRM® (Miljoskarm). Studies have shown that replacing virgin reinforcement with recycled fibers in products can maintain reasonable mechanical properties, even with a high percentage of recycled fibers (Palmer et al., 2009). Additionally, mechanically recycled wind turbine blade waste has been used to enhance the mechanical properties of 3D-printed PLA materials (Rahimizadeh et al., 2019), improve UV resistance in wood coatings (Jensen and Skelton, 2018), and demonstrate superior mechanical properties in building materials and concrete applications (Ribeiro et al., 2015; García et al., 2014; Zhang et al., 2021; Asokan et al., 2010; Yazdanbakhsh et al., 2018). Although mechanical recycling has primarily focused on GFRP materials, some studies have also explored the recycling potential of CFRP. The high cost of carbon fiber and the degradation of recycled fiber properties present challenges for the application of mechanically recycled CFRP. Mamanpush et al. developed a composite panel combining recycled CFRP with thermoset and thermoplastic materials (Mamanpush et al., 2021), while Nassiri et al. found that adding chopped CFRP waste improved the durability of pervious concrete (Nassiri et al., 2021). Furthermore, adding GFRP and CFRP waste to pervious concrete pavements has been shown to improve flexural strength and enhance resource utilization of large quantities of composite waste, providing an effective solution to reduce landfill use (Singh et al., 2022).
2.3 Chemical recovery method
The chemical recovery method uses chemical degradation or chemical dissolution to disrupt the crosslinked structure in the CFRP to form low molecular polymers or partially dissolve in reagents, thus removing the resin matrix around the fibers and achieving the separation of the fibers from the resin matrix (Yi-Feng, 2013). Compared to the thermal recovery method, the chemical recovery method only needs to complete the separation of resin and fiber at a relatively mild temperature, with less resin residue on the surface of the recovered fiber and less reduction in the mechanical properties of the fiber. Therefore, chemical recycling method is the most popular and studied method for CFRP recycling. Chemical recovery methods mainly include atmospheric pressure dissolution method, electrolytic chemical method, and supercritical fluid recovery method.
Atmospheric pressure dissolution method refers to the use of suitable strong acid and alkali solutions and catalysts to degrade the waste CFRP matrix into small molecules or monomers under heated conditions, so as to achieve the effective separation of the resin matrix and CF, and this method can even achieve the complete recycling of the two materials and then be used, Figure 4 shows the schematic diagram of atmospheric pressure dissolution method. Dissolution treatment at normal ambient pressure has the unique advantage of reducing damage to CF. Liu et al. utilized a mild chemical recovery method to recover CFRP at high Tg (>200 °C) using a ZnCl2/ethanol catalyst (Liu et al., 2017). The lower treatment temperature (<200 °C) caused negligible damage to CF and the recovered CFRP maintained high strength and modulus at loadings up to 15 wt% after addition of other new epoxy resins (Lo et al., 2018). Wang’s group developed an effective chemical recovery method for the selective cleavage of tertiary carbon-nitrogen bonds by using AlCl3/CH3COOH as a catalyst (Wang et al., 2015). By applying optimal recycling conditions (catalyst mass fraction of 15 wt%, 180°C, 6 h), up to 97% of the cured epoxy matrix was recycled and the recycled carbon fibers retained 98% of the tensile strength of virgin carbon fibers. Hou also investigated the recovery of CFRP from supercritical 1-propanol by adding 1 wt% of KOH additive to 1-propanol, and the final results showed higher recovery efficiency, but with a slight loss of mechanical properties of the carbon fibers (Yan et al., 2016). Ma and Nutt (2018) demonstrated that a mixture of acetic acid and hydrogen peroxide effectively degrades the GFRP matrix at 110°C under atmospheric pressure. However, this method has limitations, as it degrades the properties of the recovered glass fibers. In contrast Dang et al. (2005), Yuyan et al. (2006), achieved high-quality glass fibers by treating GFRP with nitric acid solution at lower temperatures, highlighting the superiority of nitric acid in low-temperature solvent cracking of GFRP. For CFRP recovery, various low-temperature solvent cracking methods have been explored. Among these, sulfuric acid and nitric acid solutions have been extensively studied and shown to yield significant results. Several studies (Feraboli et al., 2012; Liu et al., 2004; Lee et al., 2011) have demonstrated that sulfuric and nitric acids can effectively degrade the CFRP matrix and recover high-quality carbon fibers by controlling reaction conditions. Current research on low-temperature recycling focuses on developing environmentally friendly chemical solutions that minimize environmental impact while preserving fiber performance. For example, Zhao et al. (2022) proposed a low-temperature solvent cracking method using a mixture of ethanolamine and potassium hydroxide, successfully recovering carbon fibers with excellent performance under mild conditions. This approach offers a promising new direction for environmentally friendly chemical recovery technology. In addition to solvent cracking, oxidative degradation is another important chemical recycling route, utilizing oxidants to break down the polymer matrix and recover fibers. Xu et al. (2013) showed that hydrogen peroxide effectively degrades the CFRP matrix at low temperatures, with the recovered carbon fibers retaining more than 95% of their original tensile strength, demonstrating hydrogen peroxide’s potential for low-temperature CFRP recycling. Furthermore Das et al. (2018), developed an advanced oxidative degradation method that combines hydrogen peroxide with pure acetic acid. This method not only recovers carbon fibers from CFRP but also enables the multiple recycling of the polymer matrix and solvent, offering significant environmental and sustainability benefits. Above all, the atmospheric pressure dissolution method is simple to operate and although it can achieve the recovery of resin and carbon fibers, the whole reaction process is slow and the degradation mechanism is complicated. Moreover, the degradation solvent mainly uses very corrosive reagents such as strong acids, strong bases, strong oxidants and catalysts, which can easily cause environmental pollution. The core advantages of this technology are its low energy consumption and effective protection of fiber properties, making it a research hotspot in the field of composite recycling. But the reaction process is difficult to control. At present, the atmospheric pressure dissolution method is still in the experimental and small trial stage.
The electrochemical method uses the principle of electrocatalysis to achieve the degradation and recovery of CFRP in an electrolytic solution, Figure 5 shows the schematic diagram of the electrochemical recovery method. Chen (2017) optimized the current and sodium chloride parameters and added a catalyst, and greatly shortened the time of CFRP recovery, and also improved the amount of carbon fiber recovery and tensile strength. Zhu et al. (2019) proposed an electrically driven non-homogeneous catalytic decomposition method, in which CFRP was immersed in a sodium chloride electrolyte solution with potassium hydroxide catalyst fused in it, and the CFRP was used as the anode and the stainless steel bar was used as the cathode, with the CFRP being the anode and the stainless steel bar being the cathode. The reaction between CFRP and the solution was catalysed by applying an electric current to the electrolyte under test conditions at temperatures ranging from 40°C to 75°C. Approximately 100% removal of the resin matrix was achieved, and the mechanical properties of the carbon fibers were maintained at more than 90%. The advantages of the electrochemical method lie in the overall simplicity of the procedure, the low difficulty in recovering CFRP, the high recovery efficiency and the good strength of the recovered carbon fibers, but its disadvantages are also relatively significant, as the reaction process consumes a large amount of energy, which is mostly consumed by the electrolyte, resulting in a large amount of energy waste. Therefore, high energy consumption becomes the biggest limiting factor for the commercialization of the electrochemical method.
The supercritical fluid recovery method refers to the use of solvents such as water, methanol, or propanol as the fluid, under conditions exceeding its inherent critical temperature and pressure, so that the fluid is between liquid and gas and has the low viscosity, high mass transfer coefficient, and high diffusion coefficient of both gases and liquids, which can improve the reaction speed and efficiency of the degradation of the resin matrix as shown in Figure 6. Kim et al. (2019) used supercritical water to recover carbon fibers from commercial composites and achieved 99.5% degradation of the resin matrix by optimizing the recovery conditions. Supercritical water to recover carbon fibers from commercial composites, and the resin matrix degradation rate was up to 99.5% by optimizing the recycling conditions. Okajima et al. (2011) achieved the recovery of carbon fibers from CFRP as well as epoxy monomers in subcritical water at a temperature of 400°C and a pressure of 20 Mpa by using a concentration of potassium carbonate of 2.5% as a catalyst in the reaction, and the carbon fiber The mechanical properties were 85% of the original, and the recovery rate of epoxy monomer was 70.9%. Morales Ibarra et al. (2015) used supercritical water and subcritical benzyl alcohol to recover the resin matrix on the surface of CFRP, and the resin recovery rate reached 89.1% and 93.7%, respectively. Oliveux et al. (2012) observed a significant reduction in glass fiber tensile strength, up to 65%, when subcritical water hydrolysis was applied at 350°C. Kao et al. (2012) confirmed this result, attributing the strength loss to reactions between water and alkali metal oxides on the fiber surface, which led to microcrack formation. To address this issue and improve the quality of recovered fibers, researchers have investigated alternative supercritical solvents. Bai et al. (2010) showed that treating glass fiber reinforced composites with supercritical acetone retained up to 89% of the tensile strength, significantly higher than that achieved with near-critical water. This highlights the importance of solvent selection in preserving fiber properties during recycling. Catalysts are often used in both supercritical and subcritical solvent hydrolysis to enhance recovery efficiency, but their use complicates downstream processing by requiring the separation of catalysts from the recovered fibers and matrix. To simplify the process and improve environmental compatibility Das et al. (2018), proposed a catalyst-free subcritical recycling method using D-limonene, a relatively benign solvent, for polyester-based GFRP composites. Their results showed that subcritical D-limonene treatment enabled the recovery of fibers retaining approximately 85% of their original strength. For epoxy-based composites Morales Ibarra et al. (2015) treated CFRP with supercritical water and subcritical benzyl alcohol, achieving decomposition rates of 89.1% and 93.7%, respectively, demonstrating the effectiveness of both techniques in epoxy resin degradation. Kim et al. (2019) used catalyst-free supercritical water to remove epoxy resin from CFRP, achieving over 99% cleanliness. Okajima et al. (2017) employed subcritical acetone for CFRP recycling, successfully recovering intact, high-quality carbon fiber fabric while preserving the structural integrity of the original fibers. Their results indicated near-identical tensile strength between the recovered and virgin fibers, further demonstrating the efficacy of subcritical acetone in maintaining fiber properties. Different chemical recycling methods offer various advantages and disadvantages depending on material type, solvent choice, and process parameters. Low-temperature solvent lysis and oxidative degradation are energy-efficient and cost-effective, making them suitable for recovering both glass and carbon fibers. While supercritical and subcritical solvent hydrolysis require higher capital investment in equipment, they provide superior performance in matrix decomposition and fiber strength preservation. Future research should focus on developing energy-efficient, environmentally benign solvents for a broader range of composite materials and further optimizing recovered fiber properties to support circular economy principles and sustainable material utilization. In summary, the supercritical fluid recovery method is more efficient, with low contamination and high resin removal rate, but the test conditions are very harsh, requiring reactions at high temperature and pressure, and the overall safety factor is low, therefore, at this stage, the recovery method is still immature and stays only in the laboratory stage. All these factors have caused a certain degree of hindrance to the bulk recovery of CFRP. In summary, the chemical recovery method can better achieve the separation of resin matrix and carbon fiber, with less resin residue on the surface of the recovered fiber and less reduction of the mechanical properties of the fiber. However, the reasonably efficient and pollution-free chemical recycling method has not been explored yet, so the chemical recycling method is the most concerned and researched method for CFRP recycling. The advantages and disadvantages of chemical recovery methods are summarized in detail in Table 3.
2.4 Heat recovery method
Thermal treatment is a method of high temperature degradation of waste composites using the high temperature resistance of carbon fibers to decompose the thermosetting resin into hydrocarbons, gases such as methane and low molecular weight carbon-containing materials, to obtain degradation products as oils, gases, and solid products (fibers, final fillers, and coke, etc.). Currently, thermal recovery method is the most commonly used method for CFRP waste recovery and has become commercially available (Verma et al., 2018). Thermal recovery methods mainly include high temperature pyrolysis, fluidized bed pyrolysis, and microwave pyrolysis.
High-temperature pyrolysis (Zhang et al., 2020), shown in Figure 7, refers to a thermal decomposition process carried out in an oxygen-free inert gas atmosphere, where the CFRP is heated up to between 400°C and 1,000°C to recover long carbon fibers with high modulus (Machado et al., 2018). The recovered carbon fibers have a tensile strength of w 50%–85% of virgin carbon fibers. During pyrolysis, the decomposed resin matrix is separated from the CFRP to produce gas, oil, tar and coke, and the pyrolyzed carbon fibers also require oxidation reaction in oxygen to remove the coke residue on the surface of the carbon fibers and to obtain clean fibers for reuse (Overcash et al., 2018; Gastelu et al., 2018). Typically, polyester resins require lower temperatures for complete conversion, while epoxy resins require higher temperatures for decomposition. The selection criteria for the processing temperature is determined by the degree of conversion of the resin, which leads to a significant loss of mechanical properties of the carbon fiber. Giorgini et al. studied the pyrolysis of fiber-reinforced polyester composite waste in their 70 kg pilot plant and found that pyrolysis at 500°C–600 °C produced 20 wt% of oil, 40 wt% of gases, and 40 wt% of solid residue. Then further oxidation at 500°C for 50 min or at 600°C for 20 min was sufficient to obtain clean fibers (Giorgini et al., 2016). Kim used a new super-heated steam method (temperature 550°C) to recover high-quality carbon fibers with no carbon residue on the surface of the fibers, and the recovered fibers had better mechanical properties (Kim et al., 2017). Guo et al. (2019) pyrolyzed CFRERC to produce 2D rCF-reinforced carbon composites, observing minimal damage to the rCF and properties comparable to vCF, with flexural strengths of 90.3 MPa (rCF) and 95.5 MPa (vCF). Residual pyrolytic carbon did not significantly affect mechanical performance. In another study Guo et al. (2021), used pyrolysis on CFRERC to produce high-value-added rCF composites, finding minimal oxidation or damage to the rCF, which retained similar interfacial bonding (12.6 MPa vs. 13.0 MPa) and flexural strengths (106.4 MPa vs. 111.5 MPa) compared to vCF. Additionally Guo et al. (2022), examined the effects of oxidation conditions on rCF properties derived from CFRERC. Pyrolysis at 600°C for 30 min, followed by oxidation at 450°C for 15–20 min, yielded optimal results, with over 90.2% tensile strength retention, over 84.4% tensile modulus retention, over 70% conductivity, and over 95.2% recovery. Ren et al. (2023) achieved a high rCF tensile strength of 3,229.3 MPa (96.2% of vCF) with similar surface morphology. Wei et al. (Wei and Hadigheh, 2023) combined low-temperature pyrolysis with solvent pretreatment for CFRERC, reducing energy consumption and improving rCF mechanical properties, achieving 90.5% strength retention, 10.2% higher than pyrolysis alone. Lopez-Urionabarrenechea et al. (2021) recovered rCF from CFRERC while generating hydrogen gas through a two-stage thermal process, retaining 80% tensile modulus, 50% interlaminar shear strength, and 70% flexural strength of vCF, while achieving over 66% hydrogen yield. Nahil and Williams (2011) recovered rCF from carbon fiber reinforced benzoxazine resin composites at 500°C, retaining 90% of vCF mechanical properties. In a similar approach Lopez-Urionabarrenechea et al. (2020) used pyrolysis to recover clean, mechanically sound rCF and valuable gas fractions from benzoxazine resin-based waste composites. Yousef et al. (2024) recovered carbon fiber from unsaturated polyester-based wind turbine blade waste, demonstrating that pyrolysis at 500°C effectively decomposed polyester into oil and gas products, with a 78 wt% solid residue containing carbon fiber. A life cycle assessment showed the environmental benefits of oxidative pyrolysis. Wei and Hadigheh (2024) analyzed the pyrolysis kinetics of CFRC to optimize parameters for clean, undamaged rCF. A nitrogen flow rate of 20 mL/min, a heating rate of 15 C/min, and a temperature of 425°C resulted in higher conversion rates. Isothermal oxidation at 550°C for 45 min produced clean rCF, retaining 87.6% tensile modulus and 80.3% tensile strength of vCF.
In summary, it can be seen that the mechanical properties of the recovered fibers are retained better and the size is controllable, the disadvantages are the generation of harmful gases and residues on the recovered surface. Currently, the high temperature pyrolysis process is considered to be the most feasible and sustainable CFRP recycling process to achieve process and resource efficiency.
Secondly, fluidized bed pyrolysis is a process in which waste CFRPs fragments, crushed to less than 25 mm, are placed in the charging hopper of a fluidized bed reactor (with air acting as the fluidizing gas), and under certain conditions of temperature and pressure (450°C–550°C, 10–25 kPa), the matrix resin undergoes oxidative decomposition, and the fibers are separated from the matrix and transported to the fiber tanks under the action of the air flow, as shown in Figure 8. The main work health hazards of this process are the presence of contaminant gases, organic solvents and high energy use, depending on the recovery conditions. The reaction temperature is chosen to ensure decomposition of the thermoset matrix without significant fiber degradation. Following rapid heating, fibers are released through abrasion and thermal decomposition degradation of the matrix, which is then separated and collected. The gases released from the matrix are combusted to oxidize the by-products. The recovered fibers are 5–10 mm in length and retain 10%–75% of the original carbon fiber tensile strength (Pickering et al., 2015). The process is suitable for EOL composite parts as rivets, bolts and other fittings can be collected in the bed and the carbon fibers of the composite can be recovered. Overall, the reuse of fluidized bed recycled fibers is competitive as they have a relatively low environmental impact (Meng et al., 2017). Fluidized bed recycling has been developed at the University of Nottingham since 2000 and is now operating on a pilot scale (Melendi-Espina et al., 2016). Wong et al. (2010) used a fluidized bed process to convert rCF into nonwoven veils for electromagnetic interference (EMI) shielding materials. The performance of the resulting composites was comparable to those made from virgin carbon fiber (vCF). Shielding effectiveness increased with veil density, while fiber length had little impact on shielding efficiency, provided the fiber distribution was uniform. Jiang et al. (2008) studied the surface properties of carbon fibers recovered through high-temperature fluidized bed processing. Their results showed that surface hydroxyl groups were oxidized during recovery due to exposure to the thermos-oxidative atmosphere, but the oxidative decomposition of the epoxy matrix did not adversely affect the interfacial bonding properties of the rCF. Yip et al. (2002) recovered rCF with average lengths up to 10 mm from fluidized bed degradation of CFRERC. The recovered fibers retained 75% of the tensile strength of vCF, maintained their Young’s modulus, and exhibited similar surface conditions. Song et al. (2017) fabricated rCF-reinforced polyvinylidene fluoride (PVDF) composites using carbon fibers recovered via a fluidized bed process. They found that the rCF had higher chemical activity and surface roughness, resulting in stronger interfacial bonding with PVDF compared to vCF.
Microwave pyrolysis refers to the decomposition of resin matrix in composites by microwave radiation heating under inert gas atmosphere. Compared with the traditional pyrolysis method, microwave pyrolysis makes use of its unique heat and mass transfer law, heating uniformity and temperature controllability, so that the resin can be heated internally by the microwave energy absorbed by the CF, realising uniform heating and rapid decomposition of the resin, reducing the overall processing time and saving energy, and achieving the complete recycling of CF, as shown in Figure 9. This method was initially proposed by Lester (Binner et al., 2014) at the University of Nottingham, United Kingdom in 2004 for the recovery of glass fibers, and its main principle is to use microwaves to gasify the resin into gas or grease under the protection of inert gas. Ren et al. (2022) proposed a new method for rapid recovery of carbon fibers by microwave pyrolysis and oxidation processes. The resin matrix was rapidly pyrolyzed by directly heating CFRP with microwave radiation, and then the residual carbon and organic matter on the surface of the carbon fibers were removed by oxidation to obtain recycled carbon fibers (RCFs).
The recovery rate of the recycled carbon fibers was measured and their mechanical properties were evaluated by tensile strength and tensile modulus tests. The results showed that after microwave pyrolysis at 500°C for 15 min and oxidation at 550°C for 30 min, the maximum tensile strength of the RCFs was 3,042.90 MPa (about 99.42% of that of the virgin carbon fibers), and the tensile modulus was 239.39 GPa, with a recovery rate of about 96.5%. The microstructure and chemical composition of RCF were characterized by scanning electron microscopy, X-ray diffraction, Raman spectroscopy, Fourier transform infrared (FTIR) spectroscopy and X-ray photoelectron spectroscopy, and the compositions of pyrolysis by-products were detected by gas chromatography-mass spectrometry (GC-MS). These results indicate that the method is suitable for the effective recovery of high quality carbon fibers from CFRP. Hao et al. (2021), in their study of carbon fiber recovery from prepregs by microwave pyrolysis, successfully recovered carbon fibers from cured carbon fiber/epoxy resin (CF/EP) prepregs by microwave pyrolysis at 450, 550, and 650°C. The tensile properties, surface morphology and elements/functional groups on the surface of the recovered carbon fibers were also investigated, and the results showed that the distribution of elements and functional groups on the surface of the recovered carbon fibers was similar to that of the original carbon fibers. Li et al., (2021) used microwave pyrolysis to remove resin from discarded bicycle frames and recover carbon fiber, which was then incorporated into carbon fiber reinforced concrete composites. Their study found that composites containing 1 wt% rCF exhibited optimal impact resistance compared to those made with vCF or without coupling agents. Lester et al. (2004) also employed microwave pyrolysis to recover rCF from CFRERC and compared its properties to vCF using single-fiber tensile tests. The rCF retained 72.4% of the tensile strength and 89.7% of the tensile modulus of vCF. Chen et al. (2022) successfully recovered carbon fiber from CFRC used in vehicles via microwave pyrolysis. Under controlled microwave conditions (300–1,000 W for 30 min), the resin was nearly completely pyrolyzed without damaging the carbon fiber structure. Thermoplastic composites made from this rCF showed superior thermal properties compared to those reinforced with vCF. However, the effects of microwave pyrolysis on fiber properties can vary. Jensen and Skelton (2018) compared two-step pyrolysis with microwave-assisted pyrolysis for carbon fiber recovery. Two-step pyrolysis resulted in less surface and structural damage, with rCF retaining over 95% of the tensile strength of vCF. In contrast, microwave pyrolysis caused significant surface defects, reducing tensile strength to 60% and altering the graphite structure. Despite this, microwave pyrolysis offered a 70% faster recovery rate and produced rCF with superior surface activity. Obunai et al. (2015) investigated the influence of atmospheric conditions (air, nitrogen, and argon) during microwave pyrolysis of CFRERC. Microwave heating under an argon atmosphere proved most effective, yielding rCF with strength comparable to that of virgin carbon fiber. Deng et al. (2019) compared microwave and conventional pyrolysis for CFRERC, finding that microwave pyrolysis reduced reaction time by 56.7%, increased the recovery rate by 15%, and produced cleaner carbon fibers with greater efficiency and lower energy consumption.
In summary, the thermal recycling process is simple and is the only waste CFRP recycling technology that has achieved pre-commercial application. However, the resin matrix is mainly recycled in the form of gas or liquid, with low overall recycling efficiency and high energy consumption, and most of the fibers in the whole pyrolysis process are severely damaged and the fiber size is too low, which is not conducive to the recycling of high-value CFs. Therefore, under the current economic cycle system, it is necessary to further develop new thermal recovery processes to achieve maximum recovery of carbon fibers and resins from waste CFRP. Finally we have also summarized the advantages and disadvantages of the pyrolysis method in detail in Table 4.
3 Summary and outlook
At present, CFRP recycling technology is still in the process of continuous research and improvement and has also achieved carbon fiber recycling of various CFRP wastes, which is of great significance to the sustainable development of carbon fiber. First of all, due to the incineration method in the recycling process will produce a lot of harmful substances, at the same time, the recycled carbon fiber is only 35%–40% of the raw material, the strength of the fiber after physical recycling method will be seriously reduced and the value of reuse is also low, it can only be used as some fillers. It can be seen that the disadvantages of the two recycling methods are so great that it is unlikely that there will be room for progress in the future development of these two methods. Secondly, the chemical recovery method of atmospheric pressure dissolution method, electrolytic chemical method, supercritical fluid recovery method has its own advantages and disadvantages, but after a comprehensive analysis and analysis of the current situation, due to the atmospheric pressure dissolution method and electrolytic chemical method to recover the CFRP are harmful to the environment after the production of substances and electrolytic chemical method of energy consumption is huge and contrary to the advocate of energy in the future development of the two methods of further use of the chances are not great. However, with the development of production technology and production process, supercritical fluid recovery method is expected to be commercialized in the future due to the excellent performance of the recovered carbon fiber, high recovery efficiency and low pollution. Third, thermal recovery methods mainly include high temperature pyrolysis, fluidized bed pyrolysis and microwave pyrolysis. Each of these methods has its own characteristics. The mechanical properties of fibers recovered by high-temperature pyrolysis are better preserved and the size is controllable, but the disadvantages are the generation of harmful gases and residues on the recovered surface. Currently, high temperature pyrolysis is considered to be the most viable and sustainable CFRP recycling process for achieving process and resource efficiency. The main drawbacks of fluidized bed pyrolysis are the generation of pollutant gases, the presence of organic solvents and the high energy use, although commercialization of fluidized bed pyrolysis is very much in the future according to current industrial methods. Microwave pyrolysis is an emerging technology developed in the last few years, with the advantage of excellent performance in recovering carbon fibers and relatively simple experimental equipment, but with the disadvantage of generating toxic gases that pollute the environment. Despite the shortcomings of the current recycling methods, with the development of science and technology and social progress, recycling technology is bound to flourish. Combined with the development of the current recycling technology, the future development of research work mainly includes the following points: 1) Green and Efficient Chemical Recovery Processes: Future chemical recovery research needs to break through the limitations of traditional processes and develop more environmentally friendly and efficient solvent systems and recyclable catalysts. For example, explore the use of low-toxicity, bio-based or deep eutectic solvents (DES) for the selective dissolution of different resin matrices (e.g., epoxy resins, benzoxazine resins), so as to efficiently separate resins from carbon fibers. Meanwhile, the effects of process parameters, such as temperature, pressure, and solvent concentration, on the recovery efficiency and fiber properties should be systematically investigated, and databases and prediction models of optimal process parameters should be constructed in order to achieve a stable and high-quality recovery process. This kind of research will bring both environmental protection and economic benefits to the chemical recovery method, which is in line with the needs of sustainable development; 2) Optimization and Multiple Integration of Heat Recovery Processes: Heat recovery technologies such as microwave pyrolysis and fluid bed pyrolysis have high recovery potentials, but energy consumption and fiber damage are still pressing issues. Future research can reduce energy consumption and improve the quality of recovered fibers by optimizing the reactor design and improving the heat transfer performance of fluidized bed media. In addition, attempts can be made to combine the pyrolysis process with chemical recycling and physical recycling methods to form an efficient multistage composite process. For example, low-temperature chemical pretreatment is carried out first to remove part of the resin, and then complete recovery of carbon fibers is achieved through pyrolysis, which enhances the resource utilization rate and reduces the energy consumption of the process. At the same time, pathways for high value-added utilization of pyrolysis products (e.g., oil, gas, coke, etc.) should be explored, e.g., converting pyrolysis oil into chemical products or biofuels through refining, in order to improve the overall economic benefits of recycling; 3) Exploration of new cutting-edge recycling technologies: In addition to traditional chemical and thermal recycling methods, supercritical fluid recycling technology, bio-enzyme-based biorecycling technology and low-energy electrochemical recycling technology can be further studied in the future. Supercritical fluid technology, with its high diffusivity and low viscosity, can achieve efficient resin decomposition at low temperatures while maintaining fiber properties to the maximum extent possible; bio-enzyme catalytic technology, with its advantages of low pollution and low energy consumption, can be explored for application in CFRP recycling in the future, especially for low-pollution and sustainable recycling systems; electrochemical recycling can reduce energy consumption while further enhancing fiber purity through selective electrolysis of degraded resins; and electrochemical recycling can reduce energy consumption while further enhancing fiber purity. Electrochemical recycling can further improve fiber purity while reducing energy consumption through selective electrolytic degradation of resin. The successful application of these emerging technologies will open up even more possibilities for CFRP recycling; 4) Quality Evaluation and Application Expansion of Recycled Fibers: In order to make recycled carbon fibers widely used in high value-added fields, it is necessary to establish a systematic performance evaluation standard, including mechanical properties, surface chemical composition and microstructure of fibers. At the same time, surface modification technologies (such as nano-coating, plasma surface treatment, etc.) should be studied to improve the interfacial bonding properties between recycled fibers and the matrix, so as to expand their applications in the fields of composites, cementitious materials, adsorbent materials, etc., and they can even be used in aerospace, automotive and other industries with high requirements for performance, so as to realize value-added utilization of recycled fibers; 5) Intelligent and data-driven process optimization: The future CFRP recycling process can be intelligently and data-driven optimized through artificial intelligence (AI) and big data technologies. By building data models, changes in process parameters can be monitored in real time and intelligently adjusted to optimize the recycling effect and improve process stability. Additionally, variables such as temperature, pressure, solvent concentration, etc. can be monitored in real time in combination with sensors and IoT technology to achieve precise process control, thereby significantly improving production efficiency and ensuring the quality of recovered fibers; 6) Comprehensive Life Cycle Assessment (LCA) and Economic Analysis: In order to ensure the sustainability of the CFRP recycling process, it is necessary to systematically carry out the Life Cycle Assessment (LCA) and economic analysis of different recycling technologies to quantify the carbon footprint, energy consumption and cost of each method, and to identify recycling pathways with the highest environmental and economic benefits. Based on the LCA results, data support can be provided for policy formulation to encourage the development of green recycling processes and to promote the process of carbon neutrality in the recycling process. Such evaluation will provide scientific basis for enterprises and policymakers to promote the development of the industry in the direction of green and low carbon; 7) Industry chain synergy and policy support: Achieving the industrialization of CFRP recycling technology requires the collaboration of all parties, especially the synergy between academia, industry and government. The government can promote the application of green recycling technology by formulating standardized recycling specifications, providing tax incentives, etc., and encouraging enterprises to give priority to environmentally friendly recycling technology in production; while the industry should strengthen cooperation with academic institutions, promote the transformation of technological achievements, and form an efficient recycling industry chain. Meanwhile, the establishment of a sound industry standard and policy framework will help the scale promotion of CFRP recycling technology. These directions cover the optimization and innovation of chemical recycling, thermal recycling and new recycling technologies, as well as key aspects such as performance characterization, application expansion and life cycle evaluation of recycled carbon fibers. In the future, the in-depth development of these research directions will not only promote the comprehensive improvement of CFRP recycling technology in terms of efficiency, economy and environmental protection, but also help to realize the sustainable recycling of carbon fiber materials, promote the green transformation and sustainable development of the composite materials industry, and ultimately provide strong support for achieving the strategic goal of carbon neutrality.
Author contributions
MY: Conceptualization, Data curation, Formal Analysis, Investigation, Methodology, Resources, Software, Supervision, Validation, Visualization, Writing–original draft, Writing–review and editing. ZL: Writing–review and editing, Data curation, Methodology, Supervision, Conceptualization, Investigation. ZT: Writing–review and editing, Methodology, Supervision, Conceptualization, Formal analysis, Investigation.
Funding
The author(s) declare that no financial support was received for the research, authorship, and/or publication of this article.
Conflict of interest
The authors declare that the research was conducted in the absence of any commercial or financial relationships that could be construed as a potential conflict of interest.
Publisher’s note
All claims expressed in this article are solely those of the authors and do not necessarily represent those of their affiliated organizations, or those of the publisher, the editors and the reviewers. Any product that may be evaluated in this article, or claim that may be made by its manufacturer, is not guaranteed or endorsed by the publisher.
References
Asokan, P., Osmani, M., and Price, A. D. F. (2010). Improvement of the mechanical properties of glass fibre reinforced plastic waste powder filled concrete. Constr. Build. Mater. 24 (4), 448–460. doi:10.1016/j.conbuildmat.2009.10.017
Bai, Y., Wang, Z., and Feng, L. (2010). Chemical recycling of carbon fibers reinforced epoxy resin composites in oxygen in supercritical water. Mater. Des. 31 (2), 999–1002. doi:10.1016/j.matdes.2009.07.057
Beauson, J., Madsen, B., Toncelli, C., Brøndsted, P., and Ilsted Bech, J. (2016). Recycling of shredded composites from wind turbine blades in new thermoset polymer composites. Compos. Part A Appl. Sci. Manuf. 90, 390–399. doi:10.1016/j.compositesa.2016.07.009
Bernatas, R., Dagréou, S., Despax-Ferreres, A., and Barasinski, A. (2021). Recycling of fiber reinforced composites with a focus on thermoplastic composites. Clean. Eng. Technol. 5, 100272. doi:10.1016/j.clet.2021.100272
Binner, E., Mediero-Munoyerro, M., Huddle, T., Kingman, S., Dodds, C., Dimitrakis, G., et al. (2014). Factors affecting the microwave coking of coals and the implications on microwave cavity design. Fuel Process. Technol. 125, 8–17. doi:10.1016/j.fuproc.2014.03.006
Bintai, L., Xing, L., and Bao, J. (2016). Progress of aerospace resin matrix composites R&D in the key laboratory of advanced composites for national defence science and technology. J. Aerosp. Mater. 36 (3), 92–100. doi:10.11868/j.issn.1005-5053.2016.3.01
Butenegro, J. A., Bahrami, M., Martínez, M. Á., and Abenojar, J. (2023). Reuse of carbon fibers and a mechanically recycled CFRP as rod-like fillers for new composites: optimization and process development. Processes 11 (2), 366. doi:10.3390/pr11020366
Chen, C. H., Chiang, C. L., Wang, J. X., and Shen, M. Y. (2022). A circular economy study on the characterization and thermal properties of thermoplastic composite created using regenerated carbon fiber recycled from waste thermoset CFRP bicycle part as reinforcement. Compos. Sci. Technol. 230, 109761. doi:10.1016/j.compscitech.2022.109761
Chen, P. (2017). Research on electrochemical recycling method of carbon fiber reinforced composites. Shenzhen: Shenzhen University.
Chen, P. Y., Feng, R., Xu, Y., and Zhu, J. H. (2023). Recycling and reutilization of waste carbon fiber reinforced plastics: current status and prospects. Polymers 15, 3508. doi:10.3390/polym15173508
Correia, J. R., Almeida, N. M., and Figueira, J. R. (2011). Recycling of FRP composites: reusing fine GFRP waste in concrete mixtures. J. Clean. Prod. 19 (15), 1745–1753. doi:10.1016/j.jclepro.2011.05.018
Dang, W., Kubouchi, M., Sembokuya, H., and Tsuda, K. (2005). Chemical recycling of glass fiber reinforced epoxy resin cured with amine using nitric acid. Polymer 46 (6), 1905–1912. doi:10.1016/j.polymer.2004.12.035
Das, M., Chacko, R., and Varughese, S. (2018). An efficient method of recycling of CFRP waste using peracetic acid. ACS Sustain. Chem. and Eng. 6 (2), 1564–1571. doi:10.1021/acssuschemeng.7b01456
Das, T. K., Ghosh, P., and Das, N. C. (2019). Preparation, development, outcomes, and application versatility of carbon fiber-based polymer composites: a review. Adv. Compos. Hybrid Mater. 2, 214–233. doi:10.1007/s42114-018-0072-z
Deng, J., Xu, L., Zhang, L., Peng, J., Guo, S., Liu, J., et al. (2019). Recycling of carbon fibers from CFRP waste by microwave thermolysis. Processes 7 (4), 207. doi:10.3390/pr7040207
Deng, Z., Fan, J., Huang, Z., and Yang, X. (2023). Efficient recycling of carbon fiber from carbon fiber reinforced composite and reuse as high performance electromagnetic shielding materials with superior mechanical strength. Polym. Test. 125, 108110. doi:10.1016/j.polymertesting.2023.108110
Deng, Z., Yue, J., and Huang, Z. (2021). Solvothermal degradation and reuse of carbon fiber reinforced boron phenolic resin composites. Compos. Part B Eng. 221, 109011. doi:10.1016/j.compositesb.2021.109011
Dong, P. A. V., Azzaro-Pantel, C., Boix, M., Jacquemin, L., and Domenech, S. (2015). Modelling of environmental impacts and economic benefits of fibre reinforced polymers composite recycling pathways. Comput. Aided Chem. Eng. 37, 2009–2014. doi:10.1016/b978-0-444-63576-1.50029-7
Feraboli, P., Kawakami, H., Wade, B., Gasco, F., DeOto, L., and Masini, A. (2012). Recyclability and reutilization of carbon fiber fabric/epoxy composites. J. Compos. Mater. 46 (12), 1459–1473. doi:10.1177/0021998311420604
Fonte, R., and Xydis, G. (2021). Wind turbine blade recycling: an evaluation of the European market potential for recycled composite materials. J. Environ. Manag. 287, 112269. doi:10.1016/j.jenvman.2021.112269
García, D., Vegas, I., and Cacho, I. (2014). Mechanical recycling of GFRP waste as short-fiber reinforcements in microconcrete. Constr. Build. Mater. 64, 293–300. doi:10.1016/j.conbuildmat.2014.02.068
Gastelu, N., Lopez-Urionabarrenechea, A., Solar, J., Acha, E., Caballero, B. M., López, F. A., et al. (2018). Thermo-catalytic treatment of vapors in the recycling process of carbon fiber-poly (Benzoxazine) composite waste by pyrolysis. Catalysts 8 (11), 523. doi:10.3390/catal8110523
Gharde, S., and Kandasubramanian, B. (2019). Mechanothermal and chemical recycling methodologies for the fibre reinforced plastic (FRP). Environ. Technol. and Innovation 14, 100311. doi:10.1016/j.eti.2019.01.005
Giorgini, L., Leonardi, C., Mazzocchetti, L., Zattini, G., Cavazzoni, M., Montanari, I., et al. (2016). Pyrolysis of fiberglass/polyester composites: recovery and characterization of obtained products. FME Trans. 44 (4), 405–414. doi:10.5937/fmet1604405g
Gore, P. M., and Kandasubramanian, B. (2018). Functionalized aramid fibers and composites for protective applications: a review. Industrial Eng. Chem. Res. 57 (49), 16537–16563. doi:10.1021/acs.iecr.8b04903
Guo, L. R., Xu, L., Ren, Y. Y., Shen, Z. G., Fu, R. Z., Xiao, H., et al. (2022). Research on a two-step pyrolysis-oxidation process of carbon fiber-reinforced epoxy resin-based composites and analysis of product properties. J. Environ. Chem. Eng. 10, 107510. doi:10.1016/j.jece.2022.107510
Guo, W., Bai, S., and Ye, Y. (2021). A new strategy of reusing abandoned carbon fiber reinforced plastic: microstructures and properties of C/C composites based on recycled carbon fiber. J. Reinf. Plastics Compos. 40 (7-8), 294–306. doi:10.1177/0731684420959443
Guo, W., Bai, S., Ye, Y., and Zhu, L. (2019). Rapid preparation of 2D C/C composite by moulding method based on recycled carbon fiber. Appl. Compos. Mater. 26, 1163–1175. doi:10.1007/s10443-019-09771-9
Hao, S., He, L., Liu, J., Liu, Y., Rudd, C., and Liu, X. (2021). Recovery of carbon fibre from waste prepreg via microwave pyrolysis. Polymers 13 (8), 1231. doi:10.3390/polym13081231
He, F., and Sun, W. (2007). High-tech Fibers Appl. 32 (6), 9. doi:10.3969/j.issn.1007-9815.2007.06.002
Höhne, C. C., Brantsch, P., Reichert, T., and Hanich-Spahn, R. (2023). Chemical recycling of carbon fibre reinforced polyurethane for aviation applications. J. Phys. Conf. Ser. IOP Publ. 2526 (1), 012050. doi:10.1088/1742-6596/2526/1/012050
Howarth, J., Mareddy, S. S. R., and Mativenga, P. T. (2014). Energy intensity and environmental analysis of mechanical recycling of carbon fibre composite. J. Clean. Prod. 81, 46–50. doi:10.1016/j.jclepro.2014.06.023
Jang, Y. C., Lee, G., Kwon, Y., Lim, J. h., and Jeong, J. H. (2020). Recycling and management practices of plastic packaging waste towards a circular economy in South Korea. Resour. Conservation Recycl. 158, 104798. doi:10.1016/j.resconrec.2020.104798
Jayalakshmi, C. G., Inamdar, A., Anand, A., and Kandasubramanian, B. (2019). Polymer matrix composites as broadband radar absorbing structures for stealth aircrafts. J. Appl. Polym. Sci. 136 (14), 47241. doi:10.1002/app.47241
Jensen, J. P., and Skelton, K. (2018). Wind turbine blade recycling: experiences, challenges and possibilities in a circular economy. Renew. Sustain. Energy Rev. 97, 165–176. doi:10.1016/j.rser.2018.08.041
Jiang, G., Pickering, S. J., Walker, G. S., Wong, K., and Rudd, C. (2008). Surface characterisation of carbon fibre recycled using fluidised bed. Appl. Surf. Sci. 254 (9), 2588–2593. doi:10.1016/j.apsusc.2007.09.105
Kao, C. C., Ghita, O. R., Hallam, K. R., Heard, P., and Evans, K. (2012). Mechanical studies of single glass fibres recycled from hydrolysis process using sub-critical water. Compos. Part A Appl. Sci. Manuf. 43 (3), 398–406. doi:10.1016/j.compositesa.2011.11.011
Kim, K. W., Lee, H. M., An, J. H., Chung, D. C., An, K. H., and Kim, B. J. (2017). Recycling and characterization of carbon fibers from carbon fiber reinforced epoxy matrix composites by a novel super-heated-steam method. J. Environ. Manag. 203, 872–879. doi:10.1016/j.jenvman.2017.05.015
Kim, Y. N., Kim, Y. O., Kim, S. Y., Park, M., Yang, B., Kim, J., et al. (2019). Application of supercritical water for green recycling of epoxy-based carbon fiber reinforced plastic. Compos. Sci. Technol. 173, 66–72. doi:10.1016/j.compscitech.2019.01.026
Kojima, A., and Furukawa, S. (1997). Recycling of resin matrix composite materials VII: future perspective of FRP recycling. Adv. Compos. Mater. 6 (3), 215–225. doi:10.1163/156855197x00085
Krauklis, A. E., Karl, C. W., Gagani, A. I., and Jørgensen, J. K. (2021). Composite material recycling technology—state-of-the-art and sustainable development for the 2020s. J. Compos. Sci. 5 (1), 28. doi:10.3390/jcs5010028
Lee, S. H., Choi, H. O., Kim, J. S., Lee, C. K., Kim, Y. K., and Ju, C. S. (2011). Circulating flow reactor for recycling of carbon fiber from carbon fiber reinforced epoxy composite. Korean J. Chem. Eng. 28, 449–454. doi:10.1007/s11814-010-0394-1
Lester, E., Kingman, S., Wong, K. H., Rudd, C., Pickering, S., and Hilal, N. (2004). Microwave heating as a means for carbon fibre recovery from polymer composites: a technical feasibility study. Mater. Res. Bull. 39 (10), 1549–1556. doi:10.1016/j.materresbull.2004.04.031
Li, X., Bai, R., and McKechnie, J. (2016). Environmental and financial performance of mechanical recycling of carbon fibre reinforced polymers and comparison with conventional disposal routes. J. Clean. Prod. 127, 451–460. doi:10.1016/j.jclepro.2016.03.139
Li, Y. F., Li, J. Y., Ramanathan, G. K., Chang, S. M., Shen, M. Y., Tsai, Y. K., et al. (2021). An experimental study on mechanical behaviors of carbon fiber and microwave-assisted pyrolysis recycled carbon fiber-reinforced concrete. Sustainability 13 (12), 6829. doi:10.3390/su13126829
Limburg, M., Stockschläder, J., and Quicker, P. (2019). Thermal treatment of carbon fibre reinforced polymers (Part 1: recycling). Waste Manag. and Res. 37 (1_Suppl. l), 73–82. doi:10.1177/0734242x18820251
Liu, T., Zhang, M., Guo, X., Liu, C., Xin, J., Zhang, J. W., et al. (2017). Mild chemical recycling of aerospace fiber/epoxy composite wastes and utilization of the decomposed resin. Polym. Degrad. Stab. 139, 20–27. doi:10.1016/j.polymdegradstab.2017.03.017
Liu, W., Huang, H., Liu, Y., Cheng, H., and Liu, Z. (2021). Life cycle assessment and energy intensity of CFRP recycling using supercritical N-butanol. J. Material Cycles Waste Manag. 23, 1303–1319. doi:10.1007/s10163-021-01206-7
Liu, Y., Meng, L., Huang, Y., and Du, J. (2004). Recycling of carbon/epoxy composites. J. Appl. Polym. Sci. 94 (5), 1912–1916. doi:10.1002/app.20990
Liu, X., Shimei, X., and Wang, Y. (2022). A new upcycling method for thermosetting resins and their Composites. Mater. Prog. China. doi:10.7502/j.issn.1674-3962.202108043
Lo, J. N., Nutt, S. R., and Williams, T. J. (2018). Recycling benzoxazine–epoxy composites via catalytic oxidation. ACS Sustain. Chem. Eng. 6 (6), 7227–7231. doi:10.1021/acssuschemeng.8b01790
Lopez-Urionabarrenechea, A., Gastelu, N., Acha, E., Caballero, B., Orue, A., Jiménez-Suárez, A., et al. (2020). Reclamation of carbon fibers and added-value gases in a pyrolysis-based composites recycling process. J. Clean. Prod. 273, 123173. doi:10.1016/j.jclepro.2020.123173
Lopez-Urionabarrenechea, A., Gastelu, N., Jiménez-Suárez, A., Prolongo, S. G., Serras-Malillos, A., Acha, E., et al. (2021). Secondary raw materials from residual carbon fiber-reinforced composites by an upgraded pyrolysis process. Polymers 13 (19), 3408. doi:10.3390/polym13193408
Ma, Y., and Nutt, S. (2018). Chemical treatment for recycling of amine/epoxy composites at atmospheric pressure. Polym. Degrad. Stab. 153, 307–317. doi:10.1016/j.polymdegradstab.2018.05.011
Machado, J. J. M., Gamarra, P. M. R., Marques, E. A. S., and da Silva, L. F. (2018). Numerical study of the behaviour of composite mixed adhesive joints under impact strength for the automotive industry. Compos. Struct. 185, 373–380. doi:10.1016/j.compstruct.2017.11.045
Mamanpush, S. H., Li, H., Tabatabaei, A. T., and Englund, K. (2021). Heterogeneous thermoset/thermoplastic recycled carbon fiber composite materials for second-generation composites. Waste Biomass Valorization 12, 4653–4662. doi:10.1007/s12649-021-01341-0
Melendi-Espina, S., Morris, C. A., Turner, T. J., and Pickering, S. (2016). Recycling of carbon fiber composites in Proceedings of carbon 2016 (US: Penn state university), 1–8.
Meng, F., McKechnie, J., Turner, T. A., and Pickering, S. (2017). Energy and environmental assessment and reuse of fluidised bed recycled carbon fibres. Compos. Part A Appl. Sci. Manuf. 100, 206–214. doi:10.1016/j.compositesa.2017.05.008
Meng, F., Olivetti, E. A., Zhao, Y., Chang, J. C., Pickering, S. J., and McKechnie, J. (2018). Comparing life cycle energy and global warming potential of carbon fiber composite recycling technologies and waste management options. ACS Sustain. Chem. and Eng. 6 (8), 9854–9865. doi:10.1021/acssuschemeng.8b01026
Mishnaevsky, L., Branner, K., Petersen, H. N., Beauson, J., McGugan, M., and Sørensen, B. (2017). Materials for wind turbine blades: an overview. Materials 10 (11), 1285. doi:10.3390/ma10111285
Morales Ibarra, R., Sasaki, M., Goto, M., Quitain, A. T., García Montes, S. M., and Aguilar-Garib, J. A. (2015). Carbon fiber recovery using water and benzyl alcohol in subcritical and supercritical conditions for chemical recycling of thermoset composite materials. J. Material Cycles Waste Manag. 17, 369–379. doi:10.1007/s10163-014-0252-z
Nahil, M. A., and Williams, P. T. (2011). Recycling of carbon fibre reinforced polymeric waste for the production of activated carbon fibres. J. Anal. Appl. pyrolysis 91 (1), 67–75. doi:10.1016/j.jaap.2011.01.005
Naqvi, S. R., Prabhakara, H. M., Bramer, E. A., Dierkes, W., Akkerman, R., and Brem, G. (2018). A critical review on recycling of end-of-life carbon fibre/glass fibre reinforced composites waste using pyrolysis towards a circular economy. Resour. Conservation Recycl. 136, 118–129. doi:10.1016/j.resconrec.2018.04.013
Nassiri, S., AlShareedah, O., Rodin, I. I. I. H., and Englund, K. (2021). Mechanical and durability characteristics of pervious concrete reinforced with mechanically recycled carbon fiber composite materials. Mater. Struct. 54 (3), 107. doi:10.1617/s11527-021-01708-8
Obunai, K., Fukuta, T., and Ozaki, K. (2015). Carbon fiber extraction from waste CFRP by microwave irradiation. Compos. Part A Appl. Sci. Manuf. 78, 160–165. doi:10.1016/j.compositesa.2015.08.012
Ogi, K., Nishikawa, T., Okano, Y., and Taketa, I. (2007). Mechanical properties of ABS resin reinforced with recycled CFRP. Adv. Compos. Mater. 16 (2), 181–194. doi:10.1163/156855107780918982
Okajima, I., Hiramatsu, M., and Sako, T. (2011). Recycling of carbon fiber reinforced plastics using subcritical water. Adv. Mater. Res. 222, 243–246. doi:10.4028/www.scientific.net/amr.222.243
Okajima, I., Watanabe, K., Haramiishi, S., Nakamura, M., Shimamura, Y., and Sako, T. (2017). Recycling of carbon fiber reinforced plastic containing amine-cured epoxy resin using supercritical and subcritical fluids. J. Supercrit. Fluids 119, 44–51. doi:10.1016/j.supflu.2016.08.015
Oliveux, G., Bailleul, J. L., and La Salle, E. L. G. (2012). Chemical recycling of glass fibre reinforced composites using subcritical water. Compos. Part A Appl. Sci. Manuf. 43 (11), 1809–1818. doi:10.1016/j.compositesa.2012.06.008
Overcash, M., Twomey, J., Asmatulu, E., Vozzola, E., and Griffing, E. (2018). Thermoset composite recycling–Driving forces, development, and evolution of new opportunities. J. Compos. Mater. 52 (8), 1033–1043. doi:10.1177/0021998317720000
Palmer, J., Ghita, O. R., Savage, L., and Evans, K. (2009). Successful closed-loop recycling of thermoset composites. Compos. Part A Appl. Sci. Manuf. 40 (4), 490–498. doi:10.1016/j.compositesa.2009.02.002
Palola, S., Laurikainen, P., García-Arrieta, S., Goikuria Astorkia, E., and Sarlin, E. (2022). Towards sustainable composite manufacturing with recycled carbon fiber reinforced thermoplastic composites. Polymers 14 (6), 1098. doi:10.3390/polym14061098
Petrakli, F., Gkika, A., Bonou, A., Karayannis, P., Koumoulos, E. P., Semitekolos, D., et al. (2020). End-of-Life recycling options of (nano) enhanced CFRP composite prototypes waste—a life cycle perspective. Polymers 12 (9), 2129. doi:10.3390/polym12092129
Pickering, S., Turner, T., Meng, F., Morris, C., Heil, J., Wong, K., et al. (2015). Developments in the fluidized bed process for fiber recovery from thermoset composites in Proceedings of 2nd annual composites and advanced materials expo (Dallas, Texas USA).
Pickering, S. J. (2006). Recycling technologies for thermoset composite materials—current status. Compos. Part A Appl. Sci. Manuf. 37 (8), 1206–1215. doi:10.1016/j.compositesa.2005.05.030
Pickering, S. J., Yip, H., Kennerley, J. R., Kelly, R., and Rudd, C. D. (2000). The recycling of carbon fibre composites using a fluidised bed process/FRC 2000–Composites for the Millennium. United Kingdom: Woodhead Publishing, 565–572.
Rahimizadeh, A., Kalman, J., Fayazbakhsh, K., and Lessard, L. (2019). Recycling of fiberglass wind turbine blades into reinforced filaments for use in Additive Manufacturing. Compos. Part B Eng. 175, 107101. doi:10.1016/j.compositesb.2019.107101
Rahimizadeh, A., Tahir, M., Fayazbakhsh, K., and Lessard, L. (2020). Tensile properties and interfacial shear strength of recycled fibers from wind turbine waste. Compos. Part A Appl. Sci. Manuf. 131, 105786. doi:10.1016/j.compositesa.2020.105786
Rani, M., Choudhary, P., Krishnan, V., and Zafar, S. (2021). A review on recycling and reuse methods for carbon fiber/glass fiber composites waste from wind turbine blades. Compos. part B Eng. 215, 108768. doi:10.1016/j.compositesb.2021.108768
Ren, Y., Xu, L., Shang, X., Shen, Z., Fu, R., Li, W., et al. (2022). Evaluation of mechanical properties and pyrolysis products of carbon fibers recycled by microwave pyrolysis. Acs Omega 7 (16), 13529–13537. doi:10.1021/acsomega.1c06652
Ren, Y., Xu, L., Sun, Y., Li, X., Shen, Z., Li, H., et al. (2023). Study on oxidation behavior during process of recycling carbon fibers from CFRP by pyrolysis. J. Environ. Manag. 347, 119103. doi:10.1016/j.jenvman.2023.119103
Ribeiro, M. C. S., Meira-Castro, A. C., Silva, F. G., Santos, J., Meixedo, J., Fiúza, A., et al. (2015). Re-use assessment of thermoset composite wastes as aggregate and filler replacement for concrete-polymer composite materials: a case study regarding GFRP pultrusion wastes. Resour. Conservation Recycl. 104, 417–426. doi:10.1016/j.resconrec.2013.10.001
Shen, M. Y., Guo, Z. H., and Feng, W. T. (2023). A study on the characteristics and thermal properties of modified regenerated carbon fiber reinforced thermoplastic composite recycled from waste wind turbine blade spar. Compos. Part B Eng. 264, 110878. doi:10.1016/j.compositesb.2023.110878
Shuaib, N. A., and Mativenga, P. T. (2016). Energy demand in mechanical recycling of glass fibre reinforced thermoset plastic composites. J. Clean. Prod. 120, 198–206. doi:10.1016/j.jclepro.2016.01.070
Singh, A., Charak, A., Biligiri, K. P., and Pandurangan, V. (2022). Glass and carbon fiber reinforced polymer composite wastes in pervious concrete: material characterization and lifecycle assessment. Resour. Conservation Recycl. 182, 106304. doi:10.1016/j.resconrec.2022.106304
Song, C., Wang, F., Liu, Y., Wang, X., and Yang, B. (2017). Recycling carbon fiber from composite waste and its reinforcing effect on polyvinylidene fluoride composite: mechanical, morphology, and interface properties. Polym. Compos. 38 (11), 2544–2552. doi:10.1002/pc.23845
Stieven Montagna, L., Ferreira de Melo Morgado, G., Lemes, A. P., Roberto Passador, F., and Cerqueira Rezende, M. (2023). Recycling of carbon fiber-reinforced thermoplastic and thermoset composites: a review. J. Thermoplast. Compos. Mater. 36 (8), 3455–3480. doi:10.1177/08927057221108912
Termine, S., Naxaki, V., Semitekolos, D., Trompeta, A. F., Rovere, M., Tagliaferro, A., et al. (2023). Investigation of carbon fibres reclamation by pyrolysis process for their reuse potential. Polymers 15 (3), 768. doi:10.3390/polym15030768
Verma, S., Balasubramaniam, B., and Gupta, R. K. (2018). Recycling, reclamation and re-manufacturing of carbon fibres. Curr. Opin. green Sustain. Chem. 13, 86–90. doi:10.1016/j.cogsc.2018.05.011
Wang, B., Ma, S., Yan, S., and Zhu, J. (2019). Readily recyclable carbon fiber reinforced composites based on degradable thermosets: a review. Green Chem. 21 (21), 5781–5796. doi:10.1039/c9gc01760g
Wang, Y., Cui, X., Ge, H., Yang, Y., Wang, Y., Zhang, C., et al. (2015). Chemical recycling of carbon fiber reinforced epoxy resin composites via selective cleavage of the carbon–nitrogen bond. ACS Sustain. Chem. and Eng. 3 (12), 3332–3337. doi:10.1021/acssuschemeng.5b00949
Wei, Y., and Hadigheh, S. A. (2023). Development of an innovative hybrid thermo-chemical recycling method for CFRP waste recovery. Compos. Part B Eng. 260, 110786. doi:10.1016/j.compositesb.2023.110786
Wei, Y., and Hadigheh, S. A. (2024). Enhancing carbon fibre recovery through optimised thermal recycling: kinetic analysis and operational parameter investigation. Mater. Today Sustain. 25, 100661. doi:10.1016/j.mtsust.2023.100661
Wong, K. H., Pickering, S. J., and Rudd, C. D. (2010). Recycled carbon fibre reinforced polymer composite for electromagnetic interference shielding. Compos. Part A Appl. Sci. Manuf. 41 (6), 693–702. doi:10.1016/j.compositesa.2010.01.012
Wu, J., Gao, X., Wu, Y., Wang, Y., Nguyen, T. T., and Guo, M. (2022). Recycling carbon fiber from carbon fiber-reinforced polymer and its reuse in photocatalysis: a review. Polymers 15 (1), 170. doi:10.3390/polym15010170
Wu, Q., Wan, Q., Yang, X., Wang, F., and Zhu, J. (2021). Effects of chain length of polyether amine on interfacial adhesion of carbon fiber/epoxy composite in the absence or presence of polydopamine bridging platform. Appl. Surf. Sci. 547, 149162. doi:10.1016/j.apsusc.2021.149162
Xian, G., Bai, Y., Zhou, P., Wang, J., Li, C., Dong, S., et al. (2024a). Long-term properties evolution and life prediction of glass fiber reinforced thermoplastic bending bars exposed in concrete alkaline environment. J. Build. Eng. 91, 109641. doi:10.1016/j.jobe.2024.109641
Xian, G., Zhou, P., Li, C., Dong, S., Du, H., Tian, J., et al. (2024b). Mechanical properties evaluation of glass fiber reinforced thermoplastic composite plate under combined bending loading and water immersion. Constr. Build. Mater. 440, 137470. doi:10.1016/j.conbuildmat.2024.137470
Xian, G., Zhou, P., Bai, Y., Wang, J., Li, C., Dong, S., et al. (2024c). Design, preparation and mechanical properties of novel glass fiber reinforced polypropylene bending bars. Constr. Build. Mater. 429, 136455. doi:10.1016/j.conbuildmat.2024.136455
Xing, L. (2017). Structure-function integrated composite material technology. Beijing: Aviation Industry Press.
Xu, P., Li, J., and Ding, J. (2013). Chemical recycling of carbon fibre/epoxy composites in a mixed solution of peroxide hydrogen and N, N-dimethylformamide. Compos. Sci. Technol. 82, 54–59. doi:10.1016/j.compscitech.2013.04.002
Xuan-Jun, Z., Jian-Chao, W., and Jia-Jun, S. (2019). Research status of thermal damage in LASER processing of carbon Fiber Composites. Appl. Laser 39 (6), 1041–1044. doi:10.14128/j.cnki.al.20193906.1041
Yan, H., Lu, C., Jing, D., Chang, C. b., Liu, N. x., and Hou, X. l. (2016). Recycling of carbon fibers in epoxy resin composites using supercritical 1-propanol. New Carbon Mater. 31 (1), 46–54. doi:10.1016/s1872-5805(16)60004-5
Yang, J., Liu, J., Liu, W., Wang, J., and Tang, T. (2015). Recycling of carbon fibre reinforced epoxy resin composites under various oxygen concentrations in nitrogen–oxygen atmosphere. J. Anal. Appl. Pyrolysis 112, 253–261. doi:10.1016/j.jaap.2015.01.017
Yazdanbakhsh, A., Bank, L. C., Rieder, K. A., Tian, Y., and Chen, C. (2018). Concrete with discrete slender elements from mechanically recycled wind turbine blades. Resour. Conservation Recycl. 128, 11–21. doi:10.1016/j.resconrec.2017.08.005
Yi, K., Zhipeng, L., Jianglin, Q., Wang, Q., Zhu, W., and Zhu, H. (2013). Experimental study on carbon fiber recovery by incineration. Jiangxi Chem. Ind. (2), 84. doi:10.14127/j.cnki.jiangxihuagong.2013.02.084
Yi-Feng, L. (2013). Development of recycling and reuse technology for carbon fiber composite waste. Text. Her. (12), 36–39. doi:10.3969/j.issn.1003-3025.2013.12.010
Yip, H. L. H., Pickering, S. J., and Rudd, C. D. (2002). Characterisation of carbon fibres recycled from scrap composites using fluidised bed process. Plastics, rubber Compos. 31 (6), 278–282. doi:10.1179/146580102225003047
Yousef, S., Eimontas, J., Stasiulaitiene, I., Zakarauskas, K., and Striūgas, N. (2024). Recovery of energy and carbon fibre from wind turbine blades waste (carbon fibre/unsaturated polyester resin) using pyrolysis process and its life-cycle assessment. Environ. Res. 245, 118016. doi:10.1016/j.envres.2023.118016
Yuyan, L., Guohua, S., and Linghui, M. (2009). Recycling of carbon fibre reinforced composites using water in subcritical conditions. Mater. Sci. Eng. A 520 (1-2), 179–183. doi:10.1016/j.msea.2009.05.030
Yuyan, L., Linghui, M., Yudong, H., and Lixun, L. (2006). Method of recovering the fibrous fraction of glass/epoxy composites. J. Reinf. plastics Compos. 25 (14), 1525–1533. doi:10.1177/0731684406066748
Zhang, J., Chevali, V. S., Wang, H., and Wang, C. H. (2020). Current status of carbon fibre and carbon fibre composites recycling. Compos. Part B Eng. 193, 108053. doi:10.1016/j.compositesb.2020.108053
Zhang, Y., Pontikes, Y., Lessard, L., and Willem van Vuure, A. (2021). Recycling and valorization of glass fibre thermoset composite waste by cold incorporation into a sustainable inorganic polymer matrix. Compos. Part B Eng. 223, 109120. doi:10.1016/j.compositesb.2021.109120
Zhao, Q., An, L., Li, C., Zhang, L., and Jiang, J. (2022). Environment-friendly recycling of CFRP composites via gentle solvent system at atmospheric pressure. Compos. Sci. Technol. 224, 109461. doi:10.1016/j.compscitech.2022.109461
Zhou, A., Zhang, W., Wei, H., Liu, T., Zou, D., and Guo, H. (2021). A novel approach for recycling engineering sediment waste as sustainable supplementary cementitious materials. Resour. Conservation Recycl. 167, 105435. doi:10.1016/j.resconrec.2021.105435
Keywords: carbon fiber reinforced composites, recycling technology classification, advantages and disadvantages analysis, current situation analysis, future prospects
Citation: Yuan M, Li Z and Teng Z (2024) Progress and prospects of recycling technology for carbon fiber reinforced polymer. Front. Mater. 11:1484544. doi: 10.3389/fmats.2024.1484544
Received: 22 August 2024; Accepted: 05 December 2024;
Published: 19 December 2024.
Edited by:
Eugene Caldona, North Dakota State University, United StatesReviewed by:
Chenggao Li, Harbin Institute of Technology, ChinaAnas Karuth, Bridgestone, United States
Copyright © 2024 Yuan, Li and Teng. This is an open-access article distributed under the terms of the Creative Commons Attribution License (CC BY). The use, distribution or reproduction in other forums is permitted, provided the original author(s) and the copyright owner(s) are credited and that the original publication in this journal is cited, in accordance with accepted academic practice. No use, distribution or reproduction is permitted which does not comply with these terms.
*Correspondence: Min Yuan, eW14dWVzaHVAcXEuY29t