- 1Luoyang Institute of Science and Technology, Luoyang, China
- 2School of Civil Engineering, Shaoxing University, Shaoxing, China
Waste slurry is a major component of construction waste, and its resource utilization can effectively reduce its environmental impact. The effect of polyacrylamide (PAM) content and moisture content on the strength characteristics of PAM modified cement stabilized construction waste slurry (PCMS) was studied using unconfined compressive strength (UCS) and triaxial tests. It can be concluded that, 1) The UCS of PCMS increases with the increase of curing age and significantly decreases with the increase of moisture content. As the content of PAM increases, it first increases and then decreases, with UCS reaching its maximum at a PAM content of 0.5%. 2) When the moisture content is 50%, PAM can increase the elastic modulus of PCMS. When the content of PAM is 0.5%, the elastic modulus reaches its maximum value. When the moisture content is 80% and 100%, the effect of PAM on the elastic modulus of PCMS is not significant. 3) The addition of PAM can improve the shear strength of PCMS. Under the same confining pressure, the shear strength of PCMS increases first and then decreases with the increase of PAM content, and the optimal content is 0.5%. 4) The variation pattern of PCMS cohesion is basically consistent with the shear strength. PAM improves the shear strength of PCMS by enhancing its cohesion. The addition of PAM has a relatively small impact on the internal friction angle of PCMS. These findings provide valuable insights for research into modification technology and the resource utilization of construction waste slurry.
1 Introduction
In recent years, with the advancement of urbanization, numerous construction projects have begun. However, the amount of engineering waste generated has also increased significantly. These engineering wastes not only cause serious waste of resources, but also pollute the environment, which is a difficult problem to be solved in future urban construction. Construction waste slurry is a serious engineering waste in construction, which is a suspended system composed of water, bentonite particles, cohesive soil particles, and additives (Sun et al., 2023; Sun et al., 2024). Slurry as an auxiliary material in engineering, plays an indispensable role in the construction process of foundation engineering. However, after multiple cycles of use, a large amount of waste slurry will inevitably be generated. Waste slurry on construction sites often occupies construction land, affecting the environment and progress of the construction site. Unreasonable discharge treatment can also lead to serious environmental pollution (Chen et al., 2022; Wang D. et al., 2023).
Although slurry plays a significant role in engineering construction, the disposal of excess mud and waste slurry has always been a major challenge for people. At present, the methods for treating waste slurry include direct discharge method, incineration method, chemical solidification method, mechanical treatment method, and chemical flocculation precipitation method (Ye et al., 2023; Jiang et al., 2021a; Jiang et al., 2021b; Jiang et al., 2019; Jiang et al., 2022). The direct discharge method and incineration method cannot recycle and reuse slurry and cause pollution to the environment. The mechanical processing method has limited processing scope and can only handle the separated soil. The chemical flocculation precipitation method has poor treatment effect on high-density slurry, and the solid phase of the slurry is not easy to coagulate and precipitate. The chemical solidification treatment method directly adds a solidification agent to the slurry, improving its properties and facilitating the resource utilization of waste slurry (Grohs, 2002; Li et al., 2019; He et al., 2020). In the initial research on curing agents, only ordinary Portland cement was generally added as the curing agent. However, adding cement alone as a curing agent poses issues such as carbon dioxide emissions and adverse effects on the strength and durability of the solidified material (Ma et al., 2019; Craeye et al., 2011; Lin and Zhang, 2016).
At present, there has been a continuous emergence of research on the modification of slurry by adding curing agents, and many research results have been achieved. Wang et al. (Wang Q. et al., 2023) used water glass solution and carbide slag as activators to study the solidification effect of fly ash on waste slurry. The research results indicate that when the ratio of carbide slag to water glass is 6:4, the strength of the cured product after 28 days can reach 2.2 MPa. Wang et al. (Wang et al., 2024) used kaolin, slag, and carbide slag to solidify waste slurry in engineering projects. This composite curing agent can achieve a 7-day strength of 3 MPa for cured specimens. Katsioti et al. (Katsioti et al., 2008) found that when cement: bentonite = 0.6:0.4, the best solidification effect of waste slurry was achieved, with a compressive strength of 350 kPa at 28 days. Xu H. et al., 2023) mixed slag and carbide slag to solidify the slurry soil and found that the compressive strength of the modified slurry soil after 7 days could reach 3.73 MPa when the mixed amount of binder was as high as 25%. However, they found that as the wet dry cycle progressed, the strength loss of modified slurry soil with a longer curing period was actually faster. Cao et al. (Cao et al., 2006) conducted indoor experiments by adding different proportions of lime, soil, and fly ash to slurry, and studied the engineering properties of solidified slurry under different mix ratios. The study found that under appropriate mix ratios, the strength of solidified slurry met the requirements of landfill, and the permeability was also greatly improved. Yang et al. (Yang et al., 2017) used lime as the main agent and cement and gypsum as auxiliary agents to improve Tianjin coastal soft soil. The experimental results showed that using unconfined compressive strength as the standard for determining the solidification effect, the optimal cement content only changed with different lime content. For example, in 12% lime solidified soil, a cement content of no more than 3% can best improve the strength of lime solidified soil. Gypsum cannot improve the strength of soil and can lead to poor water stability and cracking when exposed to water. Although inorganic curing agents have been effective in solidifying waste slurry, due to the high moisture content of waste slurry, direct addition of inorganic curing agents not only increases the proportion of cured materials, but also the strength of cured products is usually not high (Shao et al., 2018; Zhang et al., 2022).
Flocculation and dehydration of waste slurry is usually an economically reasonable approach. It is crucial to choose efficient flocculants in order to reduce the moisture content of waste slurry. Therefore, many researchers have made tremendous efforts to find suitable flocculants. Xiao et al. (Xiao et al., 2021) prepared three flocculants with different functional groups to coagulate wastewater containing heavy metal ions. The research results indicate that the magnetic carboxymethyl chitosan flocculant (MCAA) grafted with 2-acrylamide-2-methylpropane sulfonic acid copolymer has a good flocculation effect. Patra et al. (Patra et al., 2020) used branched starch as a flocculant to treat coal suspension and found that this flocculant has a good effect and helps with rapid settling. Flocculants can not only promote the settling of suspended particles and achieve solid-liquid separation, but also have the effect of solidification enhancement. Tong et al. (Tong et al., 2021) added ion curing agents to iron tailings and natural soil, and found that the compressive strength of the mixed material first increased and then stabilized with the increase of ion curing agent dosage.
Polyacrylamide (PAM) is a water-soluble polymer, white powder, insoluble in most organic solvents, and is a relatively new type of curing agent. It is often used in combination with other traditional inorganic curing agents in soft soil solidification technology or soft soil foundation treatment methods. At present, there are also studies on its incorporation into cement. PAM is mainly used as an additive to play a flocculation role and also has a good reinforcement effect. Qin et al. (Qin et al., 2023) utilized industrial solid waste such as construction waste powder and slag powder, and introduced PAM as a flocculant to solidify waste slurry with different moisture contents. The superiority of this curing agent combination in solidifying waste slurry was verified through a combination of macroscopic and microscopic experiments. Zhang et al. (Fengjun et al., 2020) prepared a new type of flocculant by combining three flocculants to solidify waste slurry. The results showed that the best flocculation effect was achieved when the ratio of polyacrylamide, joint branch powder, and flocculation settling promoter was 1:0.75:0.5. Xu et al. (Xu S. et al., 2023) studied the flocculation and dehydration of kaolin slurry treated with single and double polymer flocculants. The research results indicate that non-ionic PAM has the best flocculation effect. This is attributed to the strongest adsorption and bridging ability of PAM. Deng et al. (Deng et al., 2022) found through a series of indoor experiments that adding PAM to cement soil can improve the plastic deformation ability of solidified soil. An appropriate content of PAM can significantly increase the ultimate strain of solidified soil at shear failure. The permeability of cement soil decreases with the increase of cement content and curing age, but adding a certain amount of PAM to cement soil can effectively improve its permeability. Chang et al. (Chang and Chang, 2010) pointed out that adding a certain amount of cement to hydraulic fill sand can significantly improve its liquefaction resistance, but the cement hydraulic fill sand is easily dispersed when soaked in water. Adding PAM can enhance the aggregation force between cement hydraulic fill sand particles. Under the condition of constant cement addition, the unconfined compressive strength of solidified soil initially increases with the increase of PAM content. After reaching its peak, the unconfined compressive strength gradually decreases with the increase of PAM content, and PAM has the most optimal addition amount. Kim et al. (Kim, 2016) jointly used aluminum chloride and PAM to treat wastewater. Research has shown that this composite flocculant has better performance and faster settling speed. According to these researches, the use of polyacrylamide can improve the mechanical properties of high water content (≥50%) slurry, and the appropriate dosage of polyacrylamide is less than 1%.
In summary, PAM can improve the deformation ability of cementitious soil, enhance the polymerization force between cement and slurry, and thus enhance the strength of cementitious soil. Therefore, PAM was added to improve the strength of cement modified slurry. But the strength characteristics of polyacrylamide modified waste slurry (PCMS) under axial and triaxial loads under different moisture contents and curing ages need further investigation. So the strength characteristics of PAM modified cement stabilized construction waste slurry (PCMS) were studied through unconfined compressive strength (UCS) tests and triaxial tests, providing reference for the resource utilization of slurry.
2 Materials and methods
2.1 Materials
2.1.1 Slurry
The slurry used in the experiment comes from a construction site in Shaoxing City, China, and the slurry is dark brown in color, as shown in Figure 1. After drying, as shown in Figure 2, it appears light brown. The main physical and mechanical indicators include specific gravity, liquid plastic limit, plasticity index, water moisture, and organic matter content, as shown in Table 1. The drying temperature is 105°C and the drying time is 24 h. After drying, the slurry was subjected to XRF testing, and the compound composition was obtained as shown in Table 1.
It can be seen that the mud is mainly composed of sheet-like particles, with the main elemental components being Si, Al, Ca, and O. The main compounds are SiO2, Al2O3, CaO, Fe2O3, and K2O.
2.1.2 Cement
The cement used in the experiment is M32.5, sourced from Shaoxing Zhaoshan Building Materials Co., Ltd. China, as shown in Figure 3. M32.5 cement has the characteristics of high later strength, moderate setting time, low hydration, good workability, low water bleeding, and high water retention rate.
2.1.3 Polyacrylamide
Polyacrylamide (PAM) is a water-soluble polymer material with the chemical formula (C3H5NO)n. The PAM used in this study is produced by Xinlida Water Treatment Company in Zhengzhou City, China, and appears as white particles, as shown in Figure 4. Molecular weight of PAM is 1800 × 104, pH value is five to eight, solid content is 8.5% and insoluble substances is 26.5%.
2.2 Sample production and curing
According to Chinese code GBT 50123–2019 (GB/T 50123, 2019), both the unconfined compression strength (UCS) and triaxial samples in this test are cylindrical, with a diameter of D = 39.1 mm and a height of H = 80 mm. The specific steps for sample production are as follows:
(1) Prepare the raw materials for the sample. Before the experiment, put the air dried slurry into an oven for further drying, and sieve the impurities in the slurry soil through a 2 mm aperture standard sieve to obtain fine powder soil.
(2) Assemble the test mold. First, tighten the clamp sleeve of the mold with a screwdriver, then evenly apply Vaseline inside the mold barrel, seal one end of the mold with a plastic film and tighten it with a rubber band. Finally, use the rubber band to fix the two end bearing plates with the mold and assemble it into a vibrator. The assembled mold is shown in Figure 5A.
(3) Prepare the mixture. According to the predetermined experimental plan, weigh the corresponding masses of slurry soil, water, cement, PAM, and put each material into a mixing pot. First, manually mix until it is initially uniform, and then place it on a mixer for secondary mixing. The mechanical mixing time is about 5 min. As shown in Figure 5B, obtain the experimental mixture.
(4) Injecting and compacting. Pour the mixed material evenly into the compactor in three parts, and vibrate for about 40 s each time to make it compact. After the compaction is completed, let it stand for about 4–6 h.
(5) Sample trimming and curing. After the sample is left to stand, remove the two end bearing samples, scrape the two ends flat, as shown in Figure 5C, and fix the filter paper with rubber rings at both ends of the mold cylinder, as shown in Figure 5D. Then immerse the sample in water for curing to simulate an environment of air isolation and saturated curing, as shown in Figure 5E. Finally, place it in a standard curing room with a temperature of 20°C ± 2°C and a humidity of 95%.
(6) Sample demolding. After curing the sample to the testing age, remove the mold cylinder and shape the sample, as shown in Figure 5F.
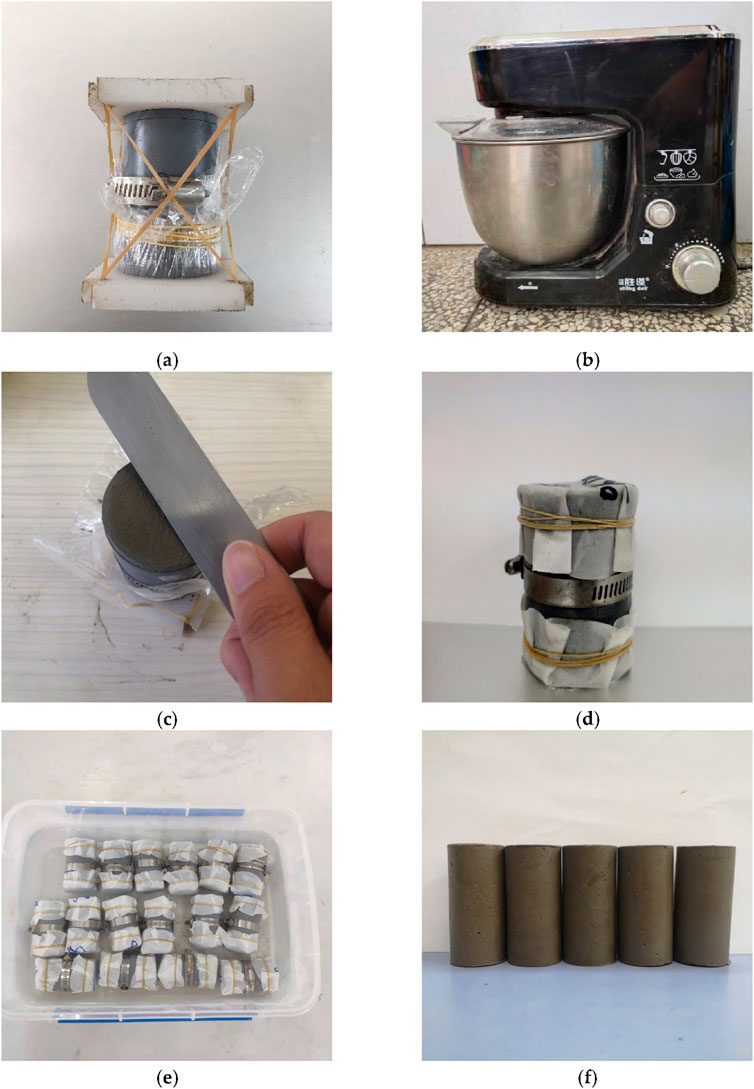
Figure 5. Sample preparation procedures: (A) Assembled mold; (B) Mixer; (C) Sample trimming; (D) Sample binding; (E) Sample curing; (F) Samples.
2.3 Test plan
Compressive strength and shear strength are the two most basic strength indicators of geotechnical materials, so this study adopts unconfined compressive strength test and triaxial test to study the strength performance of PCMS. The influence of different PAM content and moisture content on the strength characteristics of modified mud was studied using unconfined compressive strength tests and triaxial tests. The specific test plan is shown in Table 2. Moisture content refers to the ratio of the mass of water to the mass of dry slurry.
To ensure the authenticity and reliability of the measured test data, the UCS test is repeated in groups of five specimens. Using triaxial tests to obtain the mechanical properties of PCMS under different stress conditions. The study primarily considers the influence of confining pressures of 50 kPa, 100 kPa, 150 kPa, and 200 kPa. In both the UCS and triaxial tests, the shear rate of the sample is set to 1 mm/min, and the test is halted when the axial strain reaches 15%.
3 Results and analysis
3.1 Unconfined compressive performance
3.1.1 Unconfined compressive stress-strain curve
Conduct UCS tests on PCMS and obtain 24 sets of unconfined stress-strain curves. As shown in Figure 6.
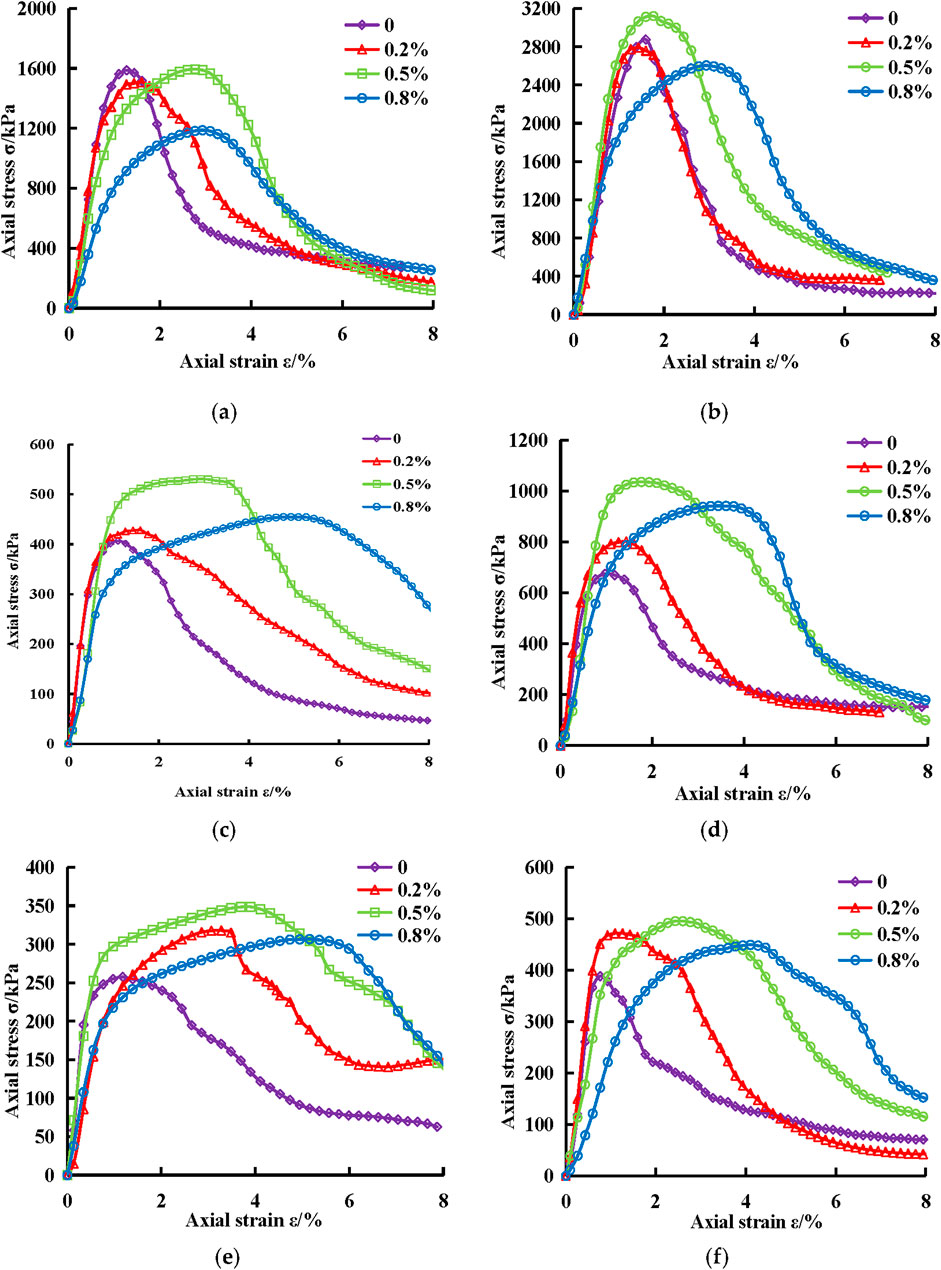
Figure 6. Unconfined compressive stress-strain curves of PCMS: (A) 50% moisture content and 7d curing age; (B) 50% moisture content and 28d curing age. (C) 80% moisture content and 7d curing age; (D) 80% moisture content and 28d curing age. (E) 100% moisture content and 7d curing age; (F) 100% moisture content and 28d curing age.
From Figure 6, it can be seen that: The stress-strain curves of PCMS all have similar curve patterns and are all softening type curves. With the increase of PAM content, the peak stress of PCMS first increases and then decreases, and the peak strain continues to increase. When the moisture content is 50% and 80%, regardless of whether it is at the curing age of 7 days or 28 days, the slope of the stress-strain curve in the elastic stage is the highest when the content of PAM is 0.5%, which means that the rate of stress increasing with strain is the highest. When PAM content is 0.5%, the stress growth rate of PCMS is the fastest. When the moisture content is 100%, at the curing age of 7 days, the slope of the stress-strain curve in the elastic stage is the highest when the content of PAM is 0.5%. At the curing age of 28 days, the slope of the stress-strain curve in the elastic stage is the highest when the content of PAM is 0.2%. This indicates that as curing age increases and PAM content rises, the effect on the stress growth rate becomes less significant. This is because, with longer curing, the hydration products in the PCMS continue to increase, making PAM’s modifying effect on PCMS less pronounced.
3.1.2 Unconfined compressive strength analysis
In order to facilitate the analysis of the modification effect of PAM on the compressive performance of PCMS, the UCS of each proportion of PCMS varies with the content of PAM, as shown in Figure 7.
From Figure 7, it can be seen that: (1) When the moisture content is 50%, whether at the curing age of 7 days or 28 days, only when the content of PAM is 0.5%, the UCS of PCMS can be improved. The remaining PAM content has a negative effect on the UCS of PCMS. When the moisture content is 80%, the UCS of PCMS at 7d and 28d curing ages increases first and then decreases with the increase of PAM content. When the content is 0.5%, the optimal values are 531 kPa and 1,036 kPa, respectively, with an increase of 31% and 53%. The moisture content is 100%, and its variation pattern is consistent with that at 80% moisture content. When the PAM content is 0.5%, the optimal strength values are reached at 7 days and 28 days curing age, which are 349 kPa and 495 kPa, respectively, with an increase of 35% and 28%. When the moisture content is 50%, the moisture content is low, the PAM introduces closed bubbles into PCMS, thereby reducing the strength of PCMS. When the moisture content is greater than 50%, PAM makes the hydration products of the cement matrix more dense, thereby increasing the strength of PCMS. Therefore, when the moisture content of PCMS is high, the strengthening effect of PAM on PCMS is greater than the weakening effect. (2) When the moisture content and PAM content of PCMS are constant, the UCS of PCMS increases with curing age. When the moisture content is 50%, the UCS of PCMS with a curing age of 28 days increased by 81%, 85%, 96%, and 119% at PAM’s content of 0%–0.8% compared to the UCS at 7 days curing age, respectively. When the moisture content is 80%, the UCS of PCMS with a curing age of 28 days increased by 66%, 87%, 95%, and 107% at PAM’s content of 0%–0.8% compared to the UCS at 7 days curing age, respectively. When the moisture content is 100%, the UCS of PCMS with a curing age of 28 days increased by 51%, 48%, 42%, and 46% at PAM’s content of 0%–0.8% compared to the UCS at 7 days curing age, respectively. From this, it can be seen that when the moisture content is 50%, PCMS is most affected by the curing age, and the effect of curing age is most significant when the content of PAM is 0.8%. (3) When the curing age of PCMS and the content of PAM are constant, the UCS of PCMS decreases significantly with the increase of moisture content.
3.1.3 Elastic modulus
Select the linear elastic stage on the stress-strain curve of UCS test, and fit the data of the linear elastic stage with a straight line. The slope of the straight line is the elastic modulus. The elastic modulus of each mix proportion of PCMS is shown in Figure 8.
From Figure 8, it can be seen that: (1)When the moisture content is 50%, PAM cannot increase the elastic modulus of PCMS at the curing age of 7 days. At 28 days curing age, the elastic modulus of PCMS increases with the increase of PAM content, reaching the optimal value of 304 MPa at a content of 0.5%, with an increase of 18.2%. When the moisture content is 50%, PAM can effectively improve the elastic modulus of PCMS at 28 days of curing age. (2)When the moisture content is 80%, at the curing age of 7 days, only when the content of PAM is 0.2%, the elastic modulus of PCMS can be improved, but the increase is not significant. At 28 days curing age, the addition of 0.5% PAM can significantly improve the elastic modulus of PCMS. When the moisture content is 80%, PAM can still improve the elastic modulus of PCMS. (3) At a moisture content of 100% and a 7-day curing age, PAM cannot increase the elastic modulus of PCMS. At 28 days of curing age, the addition of 0.2% PAM can increase the elastic modulus of PCMS.
When the moisture content is 50% and 100%, at the curing age of 7 days, PAM cannot increase the elastic modulus of CMS. This is because PAM introduces closed bubbles into PCMS, thereby reducing the elastic modulus of PCMS. At the age of 28 days, when the PAM content is 0.2%, the elastic modulus of CMS can be increased because the particles in the PCMS also have a strong adsorption effect on PAM molecules. When these PAM molecules adsorb on the surface of the particles, they will greatly improve the surface characteristics of these microparticles. Forming a water film on the surface of the cement particles ensures sufficient hydration of the cement. This allows for more complete contact between water and cement, leading to a more compact structure. Consequently, this increases the stiffness and improves the elastic modulus of the cement.
3.2 Triaxial shear performance
3.2.1 Triaxial shear stress-strain curve
Part of the triaxial test stress-strain curves of the PCMS sample are shown in Figure 9. They are first classified into three categories based on different moisture contents, and then classified according to different PAM content.
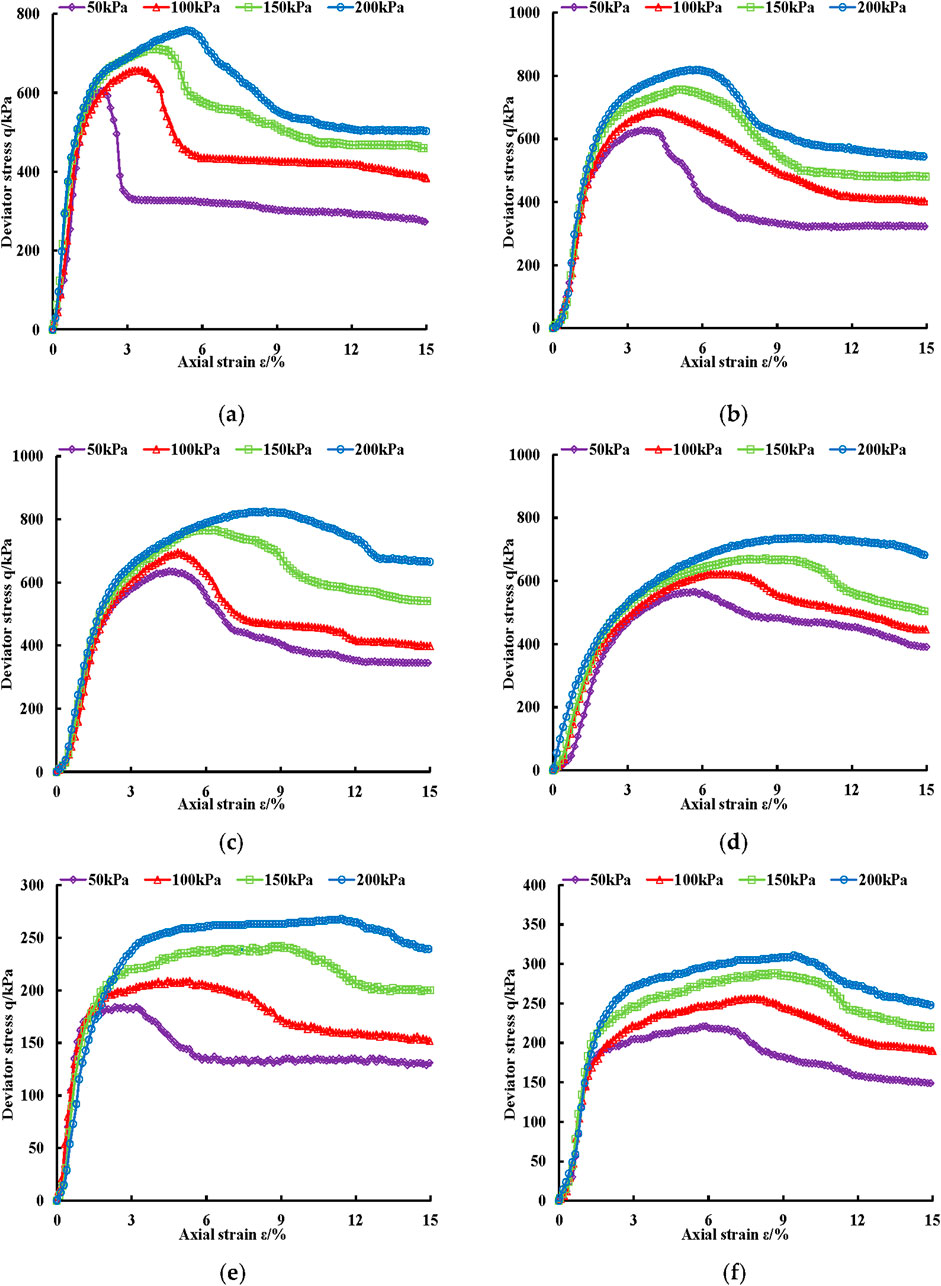
Figure 9. Deviatoric stress-strain curve of PCMS: (A) 50% moisture content and 7d curing age with 0% PAM content; (B) 50% moisture content and 7d curing age with 0.2% PAM content. (C) 50% moisture content and 7d curing age with 0.5% PAM content. (D) 50% moisture content and 7d curing age with 0.8% PAM content. (E) 80% moisture content and 7d curing age with 0% PAM content; (F) 80% moisture content and 7d curing age with 0.2% PAM content.
From Figure 9, it can be seen that: (1)When the confining pressure is between 50 kPa and 200 kPa, the shear strength and peak strain of PCMS increase with the increase of confining pressure under different moisture content conditions. The stress-strain curves of PCMS are all softening type, and the smaller the confining pressure, the more obvious the softening trend of PCMS. (2)Under high moisture content (80% and 100%) and high confining pressure (200 kPa), the stress-strain curve of PCMS exhibits a weak softening curve. With the addition of PAM, the softening trend of the stress-strain curve of PCMS first increases and then decreases. (3)With the increase of curing age, the softening trend of the stress-strain curve of PCMS at 50% moisture content increases, all of which become strong softening curves. When the moisture content is high, the form of the stress-strain curve of PCMS does not change significantly, and it still remains a weak softening curve under high confining pressure.
3.2.2 Triaxial shear strength analysis
The shear strength of the PCMS corresponds to the maximum deviatoric stress in the deviatoric stress-strain curve. The relationship curve between the content of PAM and the shear strength of PCMS is shown in Figure 10.
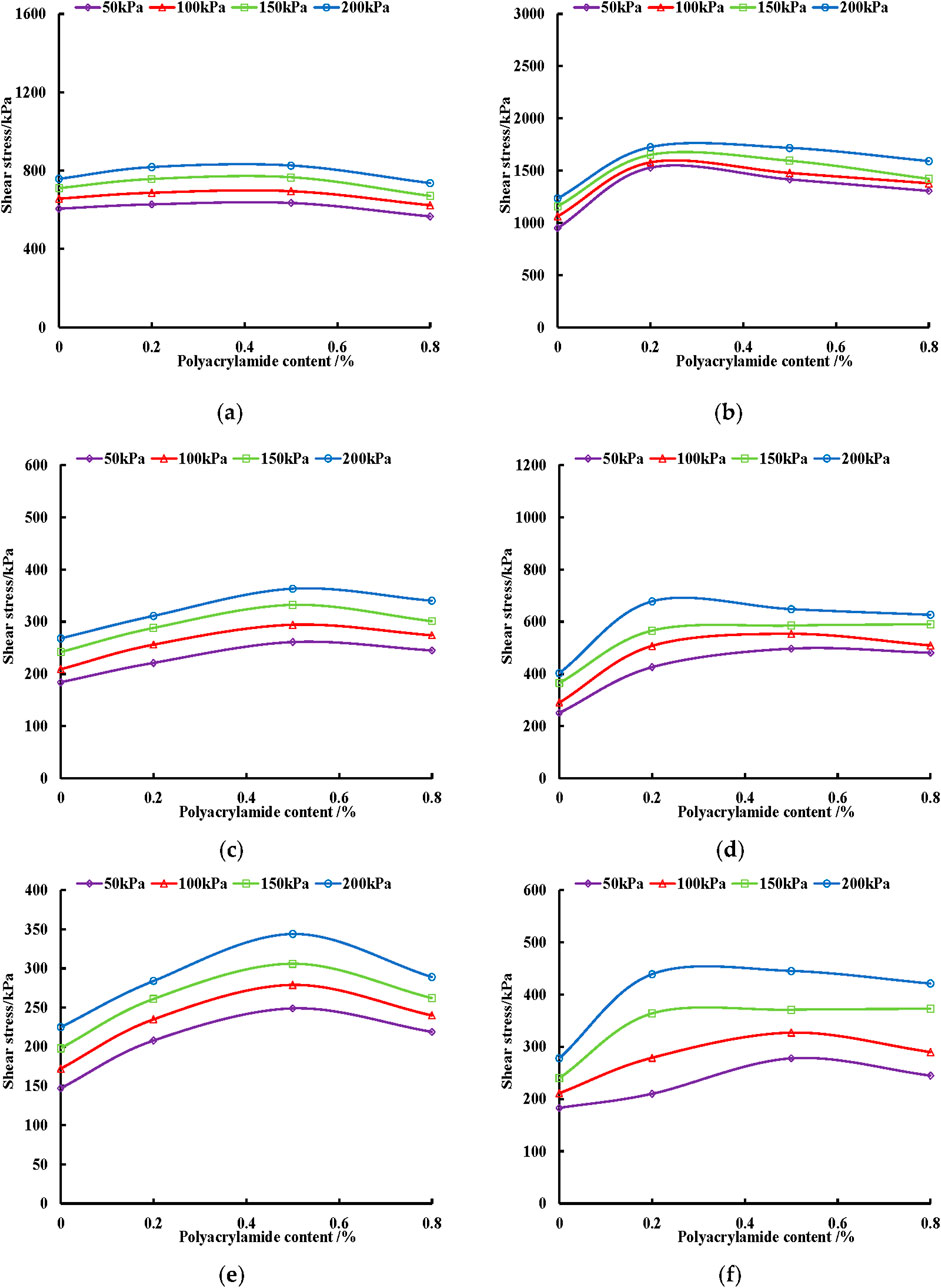
Figure 10. Relationship between the content of PAM and PCMS Shear strength: (A) 50% moisture content and 7d curing age; (B) 50% moisture content and 28d curing age. (C) 80% moisture content and 7d curing age; (D) 80% moisture content and 28d curing age. (E) 100% moisture content and 7d curing age; (F) 100% moisture content and 28d curing age.
According to Figure 10, the addition of PAM can improve the shear strength of PCMS. Under the same confining pressure, the shear strength of PCMS increases first and then decreases with the increase of PAM content.
When the moisture content is 50% and the curing age is 7 days, the effect of PAM on the shear strength of PCMS is relatively small. Under confining pressures of 50 kPa, 100 kPa, 150 kPa, and 200 kPa, the corresponding shear strength of PCMS is 606 kPa, 657 kPa, 711 kPa, and 758 kPa, respectively. The shear strength of PCMS with 0.2% and 0.5% PAM content increased by 4%–8% and 5%–9% compared with PCMS without PAM (CMS), respectively. When the confining pressure is between 50 kPa and 200 kPa, with a negative increase at 0.8% content of PAM. When the curing age is 28 days, the modification effect of PAM on shear strength increases, and the best modification effect is achieved at a 0.2% content. Under confining pressures of 50 kPa, 100 kPa, 150 kPa, and 200 kPa, the corresponding shear strength of PCMS is 950 kPa, 1,063 kPa, 1,158 kPa, and 1,234 kPa, respectively. The shear strength of PCMS with 0.2%, 0.5%, and 0.8% PAM content increased by 38%–61%, 38%–49%, and 23%–37% compared with CMS, respectively.
When the moisture content is 80% and the curing age is 7 days, the corresponding shear strength of PCMS under confining pressures of 50 kPa, 100 kPa, 150 kPa, and 200 kPa is 184 kPa, 209 kPa, 242 kPa and 268 kPa, respectively. The shear strength of PCMS with 0.2%, 0.5%, and 0.8% PAM content increased by 16%–22%, 35%–42%, and 24%–33% compared with CMS, respectively. The maximum increase was observed at 0.5% content of PAM. When the curing age is 28 days, the corresponding shear strength of PCMS under confining pressures of 50 kPa, 100 kPa, 150 kPa and 200 kPa is 251 kPa, 290 kPa, 365 kPa, and 403 kPa, respectively. The shear strength of PCMS with 0.2%, 0.5%, and 0.8% PAM content increased by 55%–70%, 60%–98%, and 55%–92% compared with CMS, respectively. The best improvement effect was achieved with 0.5% PAM content.
When the moisture content is 100% and the curing age is 7 days, the corresponding shear strength of PCMS under confining pressures of 50 kPa, 100 kPa, 150 kPa, and 200 kPa is 147 kPa, 172 kPa, 198 kPa, and 225 kPa, respectively. The shear strength of PCMS with 0.2%, 0.5%, and 0.8% PAM content increased by 26%–41%, 53%–69% and 28%–49% compared with CMS, respectively. The maximum increase was observed at 0.5% content. When the curing age is 28 days, the corresponding shear strength of PCMS under confining pressures of 50 kPa, 100 kPa, 150 kPa, and 200 kPa is 183 kPa, 211 kPa, 240 kPa, and 278 kPa, respectively. The shear strength of PCMS with 0.2%, 0.5%, and 0.8% PAM content increased by 15%–58%, 52%–60% and 34%–55% compared with CMS, respectively. The best improvement effect was achieved with 0.5% PAM content.
The porosity of PCMS increase with the increase of moisture content. According to references [(He and Lu, 2023; He et al., 2023; Chen et al., 2021a; Chen et al., 2021b)], the strength change of PCMS is mainly due to the increase of its porosity.
In summary, the addition of PAM can improve the shear performance of PCMS, and the improvement rate of PAM on the shear strength of PCMS increases with the increase of curing age. The optimal PAM content of PCMS for shear strength at 50% moisture content is 0.2%, and the optimal PAM content of PCMS for shear strength at 80% and 100% is 0.5%. It can be seen that moisture content has a certain influence on the optimal content of PAM.
3.2.3 Analysis of shear strength indicators
In order to further investigate the modification effect of PAM on the shear strength of CMS, the strength envelope diagram of PCMS was drawn based on the Mohr Coulomb theory. According to Figure 9, the peak value of deviatoric stress is taken as the failure point. When there is no peak value, the difference in principal stress at 15% axial strain is taken as the failure point. Using normal stress σ as the x-axis and shear stress τ as the y-axis, draw a failure stress diagram on the τ - σ stress plane with (σ1+σ2)/2 as the center and (σ1-σ2)/2 as the radius, and plot the envelope of the Mohr stress circle under different confining pressures. Some strength envelope diagrams were as shown in Figure 11.
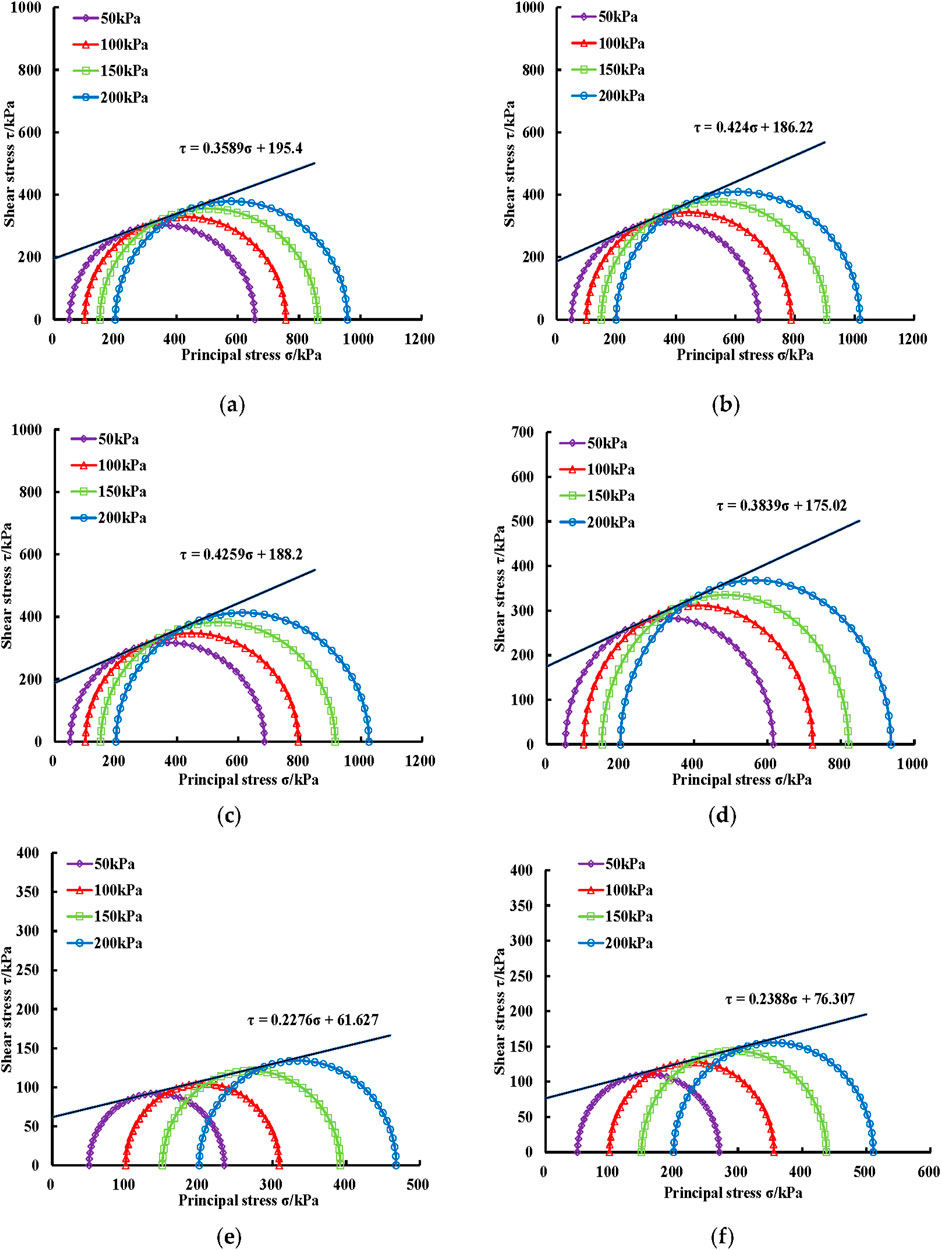
Figure 11. Shear strength envelope of PCMS: (A) 50% moisture content and 7d curing age with 0% PAM content; (B) 50% moisture content and 7d curing age with 0.2% PAM content. (C) 50% moisture content and 7d curing age with 0.5% PAM content. (D) 50% moisture content and 7d curing age with 0.8% PAM content. (E) 80% moisture content and 7d curing age with 0% PAM content; (F) 80% moisture content and 7d curing age with 0.2% PAM content.
Based on the above shear strength envelope diagram, the shear strength indicators of PCMS with different moisture content and PAM content, such as cohesion c and internal friction angle φ, are obtained. The variation of the shear strength index of PCMS with the content of PAM was obtained under different moisture contents and different curing age, as shown in Figures 12, 13, respectively.
From Figures 12, 13, it can be seen that: When the moisture content is 50%, the addition of PAM cannot increase the c of PCMS at 7 days of curing age, but it has a certain improvement in the φ of PCMS. The maximum improvement is achieved at a 0.5% PAM content, which is 17% higher than CMS. At 28 days of curing age, the c of PCMS increases first and then decreases with the increase of PAM content. The optimal content is 0.2%, which is 88% higher than CMS. This is consistent with the shear strength of PCMS at a 50% moisture content. But the φ only increased by 4% when the PAM content was 0.5%.
When the moisture content is 80%, PAM can improve the c of CMS at both 7d and 28d curing ages, and it first increases and then decreases with the increase of PAM content. The maximum value is reached at 0.5% PAM content, which is 41% and 137% higher than the c of CMS at 7d and 28d curing age, respectively. It can be seen that the improvement of c at 28d curing age is significant and still consistent with the change law of PCMS shear strength. At the curing age of 7 days, the variation pattern of φ and c is consistent, reaching its maximum at 0.5% PAM content and increasing by 16%. At 28 days of curing age, the φ only increased by 31% with a 0.2% PAM content.
When the moisture content is 100%, at the 7d curing age, the c of PCMS increases first and then decreases with the increase of PAM content, reaching its maximum value at 0.5% PAM content, which is 74% higher than CMS. At this point, the φ is also at its maximum, increasing by 16%, while the φ decreases under other doping levels. At 28d curing age, the c of PCMS was improved at a PAM content of 0.5% and 0.8%, with the maximum increase at a 0.5% content, which was 29%. The φ was improved with the addition of PAM, and the maximum increase was observed at a 0.2% PAM content, with an increase of 87%.
4 Conclusion
By conducting unconfined compressive strength tests and triaxial shear tests on PCMS, the effects of factors such as moisture content, curing age, and PAM content on the unconfined compressive and shear properties of PCMS were studied. The following conclusions can be drawn:
(1) Under axial stress, the stress-strain curves of PCMS are all softening curves. The UCS of PCMS increases with the increase of curing age and significantly decreases with the increase of moisture content. As the content of PAM increases, it first increases and then decreases, with UCS reaching its maximum at a PAM content of 0.5%.
(2) When the moisture content is 50%, PAM can increase the elastic modulus of PCMS. When the content of PAM is 0.5%, the maximum elastic modulus is achieved at 304 MPa. When the moisture content is 80% and 100%, the effect of PAM on the elastic modulus of PCMS is not significant, and the range of elastic modulus variation is 22–105 MPa.
(3) The stress-strain curves of PCMS under triaxial stress are all softening type curves. The addition of PAM can improve the shear strength of PCMS. Under the same confining pressure, the shear strength of PCMS increases first and then decreases with the increase of PAM content.
(4) The variation pattern of PCMS cohesion is basically consistent with the shear strength. The maximum cohesion is achieved at 50% moisture content and 0.5% PAM content, with a maximum cohesion of 476.1 kPa. The variation range of internal friction angle with moisture content and PAM content is 10.9°–30.5°. The improvement of shear performance of PCMS by PAM is mainly achieved by enhancing the cohesion of PCMS, and the addition of PAM has a relatively small impact on the friction between particles inside PCMS.
Data availability statement
The raw data supporting the conclusions of this article will be made available by the authors, without undue reservation.
Author contributions
FG: Writing–original draft, Writing–review and editing, Conceptualization. JH: Investigation, Writing–review and editing.
Funding
The author(s) declare that no financial support was received for the research, authorship, and/or publication of this article.
Conflict of interest
The authors declare that the research was conducted in the absence of any commercial or financial relationships that could be construed as a potential conflict of interest.
Publisher’s note
All claims expressed in this article are solely those of the authors and do not necessarily represent those of their affiliated organizations, or those of the publisher, the editors and the reviewers. Any product that may be evaluated in this article, or claim that may be made by its manufacturer, is not guaranteed or endorsed by the publisher.
References
Cao, Y., Yan, S., and Zhao, L. (2006). Engineering properties and microstructure feature of solidified sludge. Roc. Soil Mech. 27 (5), 740–744. doi:10.16285/j.rsm.2006.05.011
Chang, T.-H., and Chang, H.-W. (2010). Improvement of liquefaction resistance of reclaimed sand in water-an experimental study. J. Geoengin. 5 (2), 39–49.
Chen, H., Huang, X., He, R., Zhou, Z., Fu, C., and Wang, J. (2021b). Mechanical properties of polypropylene fiber cement mortar under different loading speeds. Sustainability 13, 3697. doi:10.3390/su13073697
Chen, H., Zhou, X., Li, Q., He, R., and Huang, X. (2021a). Dynamic compressive strength tests of corroded SFRC exposed to drying–wetting cycles with a 37 mm diameter SHPB. Materials 14, 2267. doi:10.3390/ma14092267
Chen, X., Wu, J., Ning, Y., and Zhang, W. (2022). Experimental study on the effect of wastewater and waste slurry of mixing plant on mechanical properties and microstructure of concrete. J. Build. Eng. 52, 104307. doi:10.1016/j.jobe.2022.104307
Craeye, B., Geirnaert, M., and De Schutter, G. (2011). Super absorbing polymers as an internal curing agent for mitigation of early-age cracking of high-performance concrete bridge decks. Constr. Build. Mater. 25 (1), 1–13. doi:10.1016/j.conbuildmat.2010.06.063
Deng, Y., Jiang, Y., Wu, J., Sun, H., and Geng, X. (2022). Desert silty sand modified by anionic PAM and ordinary portland cement: microfabric reinforcement and durability. Transp. Geotech. 37, 100846. doi:10.1016/j.trgeo.2022.100846
Fengjun, Z., Cui, K., Xianyang, S., Xuan, L., Jin, L., and Qianbao, C. (2020). Study on preparation and properties of novel ternary flocculant for rapid separation of underground continuous wall waste mud. Pigm. Resin Technol. 49 (6), 421–429. doi:10.1108/prt-08-2019-0073
GB/T 50123-2019; Chinese code. Standard for Geotechnical Testing Method National Standards of the People’s Republic of China: Beijing, China, 2019.
Grohs, H. (2002). Cost-efficient regeneration of bore slurry for driving of the weser tunnel. Aufbereitungstechnik 43 (11), 30–37.
He, R., and Lu, N. (2023). Unveiling the dielectric property change of concrete during hardening process by ground penetrating radar with the antenna frequency of 1.6 GHz and 2.6 GHz. Cem. Concr. Comp. 144, 105279. doi:10.1016/j.cemconcomp.2023.105279
He, R., Nantung, T., Olek, J., and Lu, N. (2023). Field study of the dielectric constant of concrete: a parameter less sensitive to environmental variations than electrical resistivity. J. Build. Eng. 74, 106938. doi:10.1016/j.jobe.2023.106938
He, X., Zheng, Z., Ma, M., Su, Y., Yang, J., Tan, H., et al. (2020). New treatment technology: the use of wet-milling concrete slurry waste to substitute cement. J. Clean. Prod. 242, 118347. doi:10.1016/j.jclepro.2019.118347
Jiang, P., Chen, Y., Zhou, L., Mao, T., Wang, W., Yuan, J., et al. (2021b). The time effect and micromechanism of the unconfined compressive strength of cement modified slurries. Adv. Mater. Sci. Eng. 2021, 5597275. doi:10.1155/2021/5597275
Jiang, P., Mao, T., Li, N., Jia, L., Zhang, F., and Wang, W. (2019). Characterization of short-term strength properties of fiber/cement-modified slurry. Adv. Civ. Eng. 2019, 3789403. doi:10.1155/2019/3789403
Jiang, P., Zhou, L., Mao, T., Yuan, J., Wang, W., and Li, N. (2022). Damage model and time effect of cement-modified waste slurry. J. Jilin Uni. Eng. Tech. Edi 52 (12), 2874–2881. doi:10.13229/j.cnki.jdxbgxb20210430
Jiang, P., Zhou, L., Wang, Y., Qian, B., Wang, W., Li, N., et al. (2021a). Freeze–thaw damage model of polypropylene fiber reinforced cement stabilized waste construction slurry under uniaxial action. Minerals 11, 743. doi:10.3390/min11070743
Katsioti, M., Katsiotis, N., Rouni, G., Bakirtzis, D., and Loizidou, M. (2008). The effect of bentonite/cement mortar for the stabilization/solidification of sewage sludge containing heavy metals. Cem. Concr. Compos. 30 (10), 1013–1019. doi:10.1016/j.cemconcomp.2008.03.001
Kim, S.-C. (2016). Application of response surface method as an experimental design to optimize coagulation–flocculation process for pre-treating paper wastewater. J. Ind. Eng. Chem. 38, 93–102. doi:10.1016/j.jiec.2016.04.010
Li, N., Zhu, Q., Wang, W., Song, F., An, D., and Yan, H. (2019). Compression characteristics and microscopic mechanism of coastal soil modified with cement and fly ash. Materials. 12, 3182. doi:10.3390/ma12193182
Lin, B., and Zhang, Z. (2016). Carbon emissions in China׳ s cement industry: a sector and policy analysis. Ren. Sust.e Ener. Rev. 58, 1387–1394. doi:10.1016/j.rser.2015.12.348
Ma, X., Liu, J., and Shi, C. (2019). A review on the use of LWA as an internal curing agent of high performance cement-based materials. Constr. Build. Mater. 218, 385–393. doi:10.1016/j.conbuildmat.2019.05.126
Patra, A. S., Patra, P., Chowdhury, S., Mukherjee, A., and Pal, S. (2020). Cationically functionalized amylopectin as an efficient flocculant for treatment of coal suspension. Colloids Surf. A 586, 124229. doi:10.1016/j.colsurfa.2019.124229
Qin, X., Zhou, Z., He, B., Xu, B., Yu, S., Qin, G., et al. (2023). Characteristics of waste mud treated by construction waste-slag based flocculation-solidification combined method. Constr. Build. Mater. 370, 130699. doi:10.1016/j.conbuildmat.2023.130699
Shao, Z.-B., Zhang, M.-X., Li, Y., Han, Y., Ren, L., and Deng, C. (2018). A novel multi-functional polymeric curing agent: synthesis, characterization, and its epoxy resin with simultaneous excellent flame retardance and transparency. Chem. Eng. J. 345, 471–482. doi:10.1016/j.cej.2018.03.142
Sun, X., Chen, Z., Sun, Z., Wu, S., Guo, K., Dong, Z., et al. (2023). High-efficiency utilization of waste shield slurry: a geopolymeric flocculation-filtration-solidification method. Constr. Build. Mater. 387, 131569. doi:10.1016/j.conbuildmat.2023.131569
Sun, X., Zhang, H., Han, Z., Huang, S., Wu, S., Tian, Z., et al. (2024). Mechanism of geopolymeric solidification in shield-tunnelling slurry from diverse sources: the role of bentonite adsorption in influencing the reaction process. Constr. Build. Mater. 431, 136627. doi:10.1016/j.conbuildmat.2024.136627
Tong, J., Niu, X., Wang, Y., and Lu, Y. (2021). Strength characteristics of iron tailings blended soil as a road base material. Appl. Sci. 11 (16), 7587. doi:10.3390/app11167587
Wang, D., Min, F., Lyu, H., Chen, J., Wang, B., and Zhang, J. (2023a). Recycling waste sand from slurry shield tunneling: a sustainable filter aid for waste slurry dehydration. J. Clean. Prod. 383, 135387. doi:10.1016/j.jclepro.2022.135387
Wang, Q., Zhang, R., Guo, J., Cai, G., and Li, Y. (2024). Study on mechanical properties and microstructure of metakaolin-slag-calcium carbide residue synergistic solidifying waste engineering mud. Constr. Build. Mater. 438, 137135. doi:10.1016/j.conbuildmat.2024.137135
Wang, Q., Zhang, R., Xu, H., Li, M., and Fang, Z. (2023b). Study on mechanical properties and microstructure of fly-ash-based geopolymer for solidifying waste mud. Constr. Build. Mater. 409, 134176. doi:10.1016/j.conbuildmat.2023.134176
Xiao, X., Yu, Y., Sun, Y., Zheng, X., and Chen, A. (2021). Heavy metal removal from aqueous solutions by chitosan-based magnetic composite flocculants. J. Environ. Sci. 108, 22–32. doi:10.1016/j.jes.2021.02.014
Xu, H., Wang, Q., Zhou, W., Li, M., and Cai, G. (2023a). Study on compressive strength and microstructure of slag–calcium carbide residue solidified mud under wetting–drying cycles. Arab. J. Sci. Eng. 48 (4), 5087–5096. doi:10.1007/s13369-022-07302-6
Xu, S., Shi, J., Deng, J., Sun, H., Wu, J., and Ye, Z. (2023b). Flocculation and dewatering of the kaolin slurry treated by single-and dual-polymer flocculants. Chemosphere 328, 138445. doi:10.1016/j.chemosphere.2023.138445
Yang, A., Zhong, X., Liang, C., and Li, Y. (2017). Experiment study of solidification performance and long-term mechanical properties of dredger filled mud. Roc. Soil Mech. 38 (9), 2589–2596. doi:10.16285/j.rsm.2017.09.016
Ye, J., Jiang, P., Chen, L., Zhou, X., Rao, F., and Tang, X. (2023). Strength and deformation characteristics of fiber and cement-modified waste slurry. Polymers 15, 3435. doi:10.3390/polym15163435
Keywords: construction waste slurry, polyacrylamide, moisture content, unconfined compressive strength, shear strength
Citation: Guo F and Hu J (2024) Strength characteristics of cement stabilized construction waste slurry modified by polyacrylamide with different moisture contents. Front. Mater. 11:1475277. doi: 10.3389/fmats.2024.1475277
Received: 03 August 2024; Accepted: 12 September 2024;
Published: 25 September 2024.
Edited by:
Linglin Li, Hefei University of Technology, ChinaReviewed by:
Jue Li, Chongqing Jiaotong University, ChinaChuanqing Fu, Zhejiang University of Technology, China
Copyright © 2024 Guo and Hu. This is an open-access article distributed under the terms of the Creative Commons Attribution License (CC BY). The use, distribution or reproduction in other forums is permitted, provided the original author(s) and the copyright owner(s) are credited and that the original publication in this journal is cited, in accordance with accepted academic practice. No use, distribution or reproduction is permitted which does not comply with these terms.
*Correspondence: Feng Guo, MTQ3OTA3MDU0QHFxLmNvbQ==