- 1Beijing Key Laboratory of Nonlinear Vibrations and Strength of Mechanical Structures, College of Mechanical Engineering, Beijing University of Technology, Beijing, China
- 2Engineering Research & Development Centre for Underground Technology of Jiangxi Province, School of Civil Engineering and Architecture, East China Jiaotong University, Nanchang, Jiangxi, China
- 3School of Civil Engineering, Central South University, Changsha, China
- 4State Key Laboratory of Green Building Materials, Beijing, China
- 5Hubei Key Laboratory of Theory and Application of Advanced Materials Mechanics, Wuhan University of Technology, Wuhan, China
- 6Guangdong Provincial Key Laboratory of Building Energy Efficiency and Application Technologies, Guangzhou University, Guangzhou, China
This study aims to carry out a high-temperature exposure assessment for graphene oxide (GO) reinforced cement in terms of weight loss, flexural strength, and compressive strength. Different additive amounts of GO in cement are experimentally studied to unfold its effect on enhancing the mechanical performance of prepared GO reinforced cement. Temperatures are chosen as room temperature, 200, 400, 600, and 800°C, corresponding to different reaction status of cement. It is found that as the temperature increases, the water evaporates from the GO reinforced cement. Evaporated quantity of water relies on the reaction status, and the relation between weight loss and temperature is provided. Benefiting from the bonding effects of GO, hydrated calcium silicate hydrate (C–S–H) is chemically produced and, thus, a reticular bridging system, which is greatly helpful to enhance the flexural strength, is formed. Unlike flexural strength, adding GO into cement statistically has little effect on the compressive strength, except when the temperature rises up to 800°C due to the occurrence of decarburization from dehydration.
Introduction
Reinforced cements are under rapid development regarding high strength, toughness, durability, crack resistance, and multifunction by adopting dual or multiple organic and inorganic composite materials, metal and non-metal materials, and fibrous and granular materials (Li et al., 2020). The development of nanomaterials provides great opportunities to improve the nanoscale microstructure of cement composites (Tyson et al., 2011; Parveen et al., 2015; Han et al., 2017). For example, to improve the durability and ductility of cement composites, graphene oxide (GO) could be added (Lu Z et al., 2020; Zhao et al., 2020). In addition, GO can increase the flexural and compressive strength of cement-based materials (Peng et al., 2019; Indukuri et al., 2020).
Fire incidents will result in the exposure of the building structure to high temperature, and the internal structure of concrete will be changed accordingly, and its compressive and flexural strength will be greatly reduced (Nadeem et al., 2014). High-temperature–resistant cement-based composites are promising aspects for practical application in improving the fire resistance of building structures. GO is an intermediate during the preparation of graphene from graphite oxide, and large amounts of active groups, such as hydroxyl, carboxyl, and epoxy groups, are residued (Poon et al., 2001a; Poon et al., 2001b). Due to hydrophilia, the distance between GO layers may increase, and thus, it is easy to disperse in the water solution or reaggregate with monomers to form an intercalation complex. These characteristics can be utilized to toughen some high polymers and inorganic non-metal materials (Lu et al., 2019). Scholars have found substantial enhancement on flexural strength and compressive strength of GO reinforced cement (GORC) as compared with the control group (Duan et al., 2018; Khan et al., 2019). Although the mechanism of how the addition of GO into cement improves the material properties of cement has been extensively studied, the literatures were mainly focused on its microstructure, mechanical properties, and durability, while the high-temperature exposure assessments of GORC are few and far between. The experiment shows that the stability of C-S-H structure is weakened under high temperature, including the stretching of silicon–oxygen bond, the decomposition of silicate chain, and the weakening of water molecule hydrolysis, but imbedding GO can effectively stabilize the C-S-H structure (Lu L et al., 2020). In addition, experiments show that this structure has high temperature resistance (Liang, 2014).
In this study, GORC with different additions of GO, 0.05, 0.08, 0.10, and 0.20 wt%, prepared in the laboratory is selected as samples to conduct the high-temperature exposure assessment. Pure cement specimens with no GO are also prepared as a control group. The temperatures are chosen as room temperature, 200, 400, 600, and 800°C, corresponding to different working conditions of the cement. The relation between weight loss as well as mechanical properties and temperature is explored.
Experiment
Raw Materials
The cement was PO 42.5 ordinary Portland cement, and GO produced by improved Hummer freeze-drying was purchased from Shenzhen Sixth Element Technology Co. Ltd., with physical parameters shown in Table 1. The water-reducing agent and dispersant PVP-K90 adopted market products from Shunjie Plastic Technology Ltd. The water was deionized.
Proportion of Mixture
GORC slurry specimens with different additions of GO, namely, 0.05, 0.08, 0.10, and 0.20 wt%, were prepared in the laboratory. A set of pure cement paste specimens was also prepared as a control group. A water-binder of 0.28 ratio was used, and the water-reducing agent was tentatively added to adjust the gelatinization situation of GORC in order to seek optimum operating condition. The usage of the dispersant agent increases with a fixed proportion of 4:1 related to the GO content, and the specific proportion of the mixture is listed in Table 2.
Experimental Process
First of all, specimens were prepared. Five specimens of each GO content were made, and a total of 25 specimens were made. The curing time was 28 days in an atomizing chamber with a temperature of 20°C and a relative humidity of 70%. The Sx-12-12 box-type resistance furnace produced by Hunan Coal Exploration Electric Furnace Factory was used to heat the specimens in a sealed manner at a specified temperature. The specimens with the same GO content were divided into five groups with one specimen in each group and heated at 200, 400, 600, and 800°C, respectively. One group was placed at room temperature. The heating rate was 5°C/min, and the temperature was constant for 10 min after reaching the target temperature. Then, the power was turned off, and the specimen was cooled to room temperature in the high-temperature furnace. After being taken out, it was weighed and recorded. Subsequently, the strength test was carried out. There was one specimen with the same temperature and GO content. The compressive and flexural strength tests were conducted according to the Cement Mortar Strength Test Method (GB/T17617-2007).
Results and Discussion
Specimen Characterization
The size of GORC specimens is 40 mm × 40 mm × 160 mm. Figure 1 shows the surface topographies of the five groups of GORC specimens after 28 days of the curing period under different high temperatures. From Figure 1A, it can be found that the surface crack of the specimen gradually grows as the temperature increases in terms of quantity and size. A transversal load is applied on the GORC block until the fracture occurs, and then the fracture surfaces are presented in Figure 1B. It is clearly shown that the fracture surface is nearly flat at room temperature and becomes more and more uneven under high-temperature working conditions, except the case of 800°C. This is because all the specimens spontaneously break at 800°C. At the working condition of room temperature and 200°C, all the samples reveal that there is little crack around the fracture surface, and no difference for the blank specimen GO-0 among other specimens was observed. Visible cracks can be observed when the temperature rises up to 400°C. Different from the sparse and dispersive cracks in the experimental groups, many cross-linked cracks grow in the surface of the GO-0 control group. As the temperature rises, more and more cracks grow, of which the width becomes larger and larger.
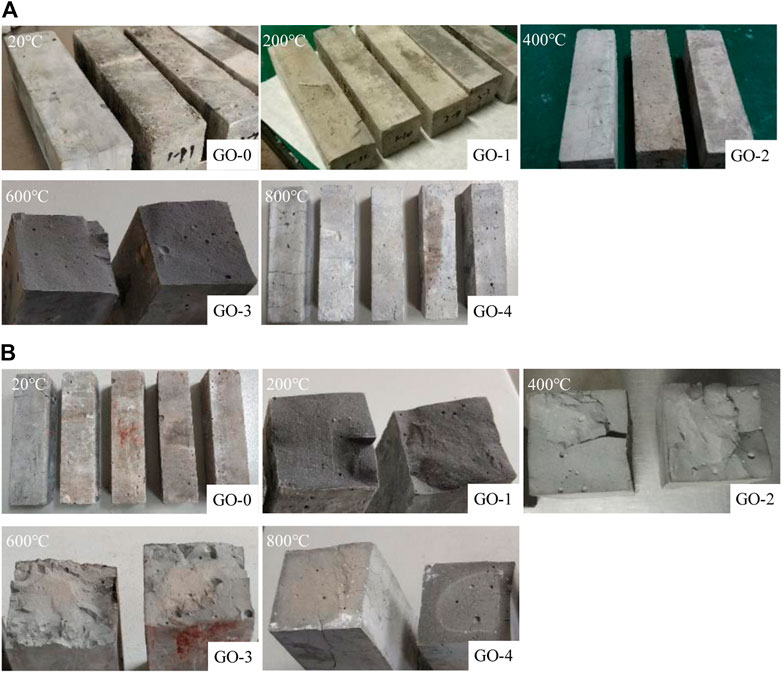
FIGURE 1. Surface topographies of GORC after 28-day curing period exposure to different high temperatures (A) and their fractured counterparts (B). Note: the specimens are observed to spontaneously break at 800°C.
Due to the addition of GO, the cracks of experimental group GORC specimens are much fewer. One reason is that GO possesses good bonding effect, and hydrated calcium silicate hydrate (C-S-H) is chemically produced so that GORC can alleviate the crack growth when there is thermal stress inside. Another possible reason is that GO could timely transfer the heat from the inside to the surface of the specimen, thus reducing the thermal stress gradient. The color also changes as the temperature increases. At room temperature, the color of the samples is cyan and as the temperature rises up to 200°C, the color is almost unchanged. As it continues to rise to higher than 400°C, due to decomposition of Ca(OH)2, the color changes slightly lighter. When the temperature reaches 800°C, the color of specimens turns gray–white due to the decomposition of CaCO3.
The onset of burst is observed at 400°C. The main reason is that much water is chemically generated in the samples only when the temperature reaches up 400°C and then evaporates out. The high vapor pressure breaks through the barrier and forms many channels and finally yields a burst of the samples. This is consistent with the relatively larger weight loss as discussed in detail in the following section. When the temperature continues to increase, only a small fraction of water vapor is generated. Besides, the aforementioned formed channels timely release the vapor pressure. This double effect prevents the burst from occurring again even though the temperature continues to heat up (Qin et al., 2013).
Weight Loss
Figure 2 plots the weight loss–temperature curves for GORC specimens. The control group is set as the reference coordinate, of which weight loss is returned to zero. The weight loss is obtained by subtracting the specimen’s weight at room temperature from its counterpart weight at high temperature and then divided by the weight at room temperature. During the first temperature-rise period, there is only 2.85–5.12% weight loss, in which the weight loss significantly decreases as the addition of GO increases. The second temperature-rise period is most critical, during which 12.19–14.63% weight loss with low fluctuation is reached, that is, more than half of the total weight loss, which is a reasonable explanation of the onset of burst phenomenon as described above. At this stage, the addition has a much smaller effect on the weight loss as than that of the first temperature-rise period. The high temperature provides sufficient energy to prompt a large amount of evaporation of free water, capillary water, gel water, and crystal water escape from the inside of the specimen (Zhang et al., 2016).
As the temperature continues to increase, the change of weight loss becomes small. At the third temperature-rise period, the maximum weight loss is only 3.15%; this corresponds to the decomposition of Ca(OH)2 and the continuous loss of crystal water and bound water, of which the active energy is much higher (Guo et al., 2017). At the last stage, the maximum loss is 6.25%. At this stage, the weight loss is mainly caused by the decomposition of calcium silicate hydrate (C-S-H) and CaCO3 (Ji-Shu, 2017). It is noteworthy that there is a significant difference among the samples with different GO content in the weight loss at 600°C. Among all the results, the maximum weight loss always occurs at the GO-0 samples, and thus we can draw that the addition of GO can alleviate weight loss. A reasonable explanation is that GO can regulate hydration products and improve structures and defects (Lv et al., 2014), and thus reduce evaporation of water.
The Flexural Strength
Figure 3 demonstrates the residual flexural strength of GORC specimens exposed to different temperatures. Observed from the change of flexural strength of kinds of GORC specimens at room temperature, a significantly enhancing effect of GO on the cement can be drawn. The flexural strength of the specimens reinforced by GO has different degrees of improvement, among which the flexural strength seems to increase at the early stage and then decrease. The maximum flexural strength increment occurs at the GO-2 specimen involving 0.08 wt% GO, with an amplitude of ∼126% as compared with the control specimen. The enhancing reason is that GO possesses a large amount of oxygen functional groups, of which strong electrostatic attraction can closely bind together to chemically form cement hydration products (C-S-H) (Xu et al., 2017). Uniformly dispersive GO solution in cement spontaneously formed spatially crosslinked bridge structure to take full advantage of the ultrahigh toughness of GO (Tombros et al., 2011; Peng et al., 2018). Nevertheless, as the GO content increases, such as GO-3 and GO-4, the amount of the PVP dispersant agent concomitantly increases, yielding too much gas during the dispersion process and thus too many voids which decreases the flexural strength. That is to say, the improvement in the flexural strength of cement depends on the balance of the addition of GO and concomitantly required a PVP dispersant agent.
As the temperature increases, the residual flexural strength generally decreases. This is because the cement-based material has undergone a process from dehydration to decarburization during the heating process. A significantly large decrease in the residual flexural strength of GORC specimens occurs at the second temperature-rise period, rather than the first period. This conclusion coincides with the abovementioned discussion of weight loss. In the first temperature-rise period, only free water evaporates from the inside of the GORC, and a decrease of 7% flexural strength is found. In the second temperature-rise period, high temperature produces high atmospheric pressure and removes the barrier that prevents them, mainly free water, capillary water, gel water, and crystal water, from escaping from the inside of specimens. Different from the other periods, a larger increase of flexural strength is observed in the third temperature-rise period. CaO and CaCO3 are produced from dehydrated Ca(OH)2 at a temperature of 580°C, which can repair the crack of the specimens, and thus enhances the flexural strength of GORC.
The Compressive Strength
The variation of residual compressive strength of GORC specimens as the temperature increases is demonstrated in Figure 4. As compared with the flexural strength of GORC specimens, the compressive strength is an order of magnitude larger, 10–20 times. According to the standard value, the GORC specimens have found to be well-cured. As observed from Figure 4, there is no clear rule for the compressive strength of GORC to follow when adding GO in the cement, which is quite different from the flexural strength. The data demonstrated in the figure exhibit a large discreteness when different additive amounts of GO are used. The addition of GO into cement statistically has little effect on the compressive strength. Also the compressive strength is also insensitive to the temperature except when it rises up to 800°C. Several possible reasons may explain this phenomenon.
First, although GO possesses superior compressive and tensile properties, its flake-like structure is bound to only enhance the flexural strength of GORC, but not compressive strength, because of its compressive instability. Second, cement has high compressive strength but low tensile strength as demonstrated by the experimental data; thus, when introducing GO, a significantly increasing flexural strength of GORC can be found, but not the compressive strength. Therefore, we should avoid the adverse condition of cement in tension and GO in compression. Besides, the randomly distributed pore and water have considerable influence on the GORC specimens, causing discrete results. When the temperature is lower than 600°C, water evaporates and some new pores generate, which is also a reason to cause the major fluctuations of compressive strength. Nevertheless, when the temperature rises from 600 to 800°C, GORC specimens undergo a process from dehydration to decarburization. A thermal decomposition of calcium silicate hydrate (C-S-H) and CaCO3 occurs and thus reduces the compressive strength.
Conclusion
In summary, the flexural and compressive strength of GORC with different additive amounts are experimentally investigated under different temperatures. At room temperature, the involved GO has a decreasing effect on weight loss. The maximum weight loss occurs at the second temperature-rise period, during which more than half of the total weight loss is found with low fluctuation, implying that GO has a slight effect on water retention as the temperature increases. This conclusion is consistent with the onset of burst phenomenon. For flexural strength, the addition of GO has a significantly enhancing effect on the cement at room temperature, nearly an amplitude of ∼126%. This is due to the oxygen functional groups having strong electrostatic attraction that can be closely combined to promote the production of C-S-H, thus spontaneously forming spatially crosslinked bridge structure. Nevertheless, the amount of the PVP dispersant agent concomitantly increases when increasing the GO content and yields too many voids. Finally, the flexural strength decreases. Therefore, we should seek the balance of the addition of GO and concomitantly require a PVP dispersant agent to pursue the optimum properties of GORC. As the temperature increases, the residual flexural strength generally decreases. This is because the cement-based material has undergone a process from dehydration to decarburization during the heating process. Differently, a larger increase of flexural strength is observed in the third temperature-rise period because CaO produced from dehydrated Ca(OH)2 can repair the crack of the specimens. The compressive strength is an order of magnitude larger than flexural strength. However, there is no clear rule for the compressive strength of GORC to follow. A large discreteness is observed. The addition of GO into cement has only statistically little effect on the compressive strength, which is also insensitive to the temperature, except when it rises up to 800°C since GORC specimens undergo a process from dehydration to decarburization. A thermal decomposition of calcium silicate hydrate (C-S-H) and CaCO3 occurs and, thus, reduces the compressive strength.
Data Availability Statement
The original contributions presented in the study are included in the article/Supplementary Material; further inquiries can be directed to the corresponding author.
Author Contributions
JY: methodology, data analysis, validation, writing—review and editing, project administration, and funding acquisition; JW: investigation, methodology, and draft writing; HC: investigation, methodology, and draft writing; PX: validation and resources.
Funding
This study was supported by grants from the National Natural Science Foundation of China (Grant No. 11972379 and and 12072112), the National Natural Science Foundation Excellent Youth Cultivation Project (Grant No. 20202ZDB01001), the Opening Projects of State Key Laboratory of Green Building Materials, Beijing, Hubei Key Laboratory of Theory and Application of Advanced Materials Mechanics, Wuhan and Guangdong Provincial Key Laboratory of Building Energy Efficiency and Application Technologies, Guangzhou, Central South University (Grant Nos. 212190102, 502045006 and 502390001), the Key R&D Program of Hunan Province (No. 2020SK2060), and Hunan Science Fund for Distinguished Young Scholars (No. 2021JJ10061).
Conflict of Interest
The authors declare that the research was conducted in the absence of any commercial or financial relationships that could be construed as a potential conflict of interest.
The reviewer NW declared a shared affiliation with one of the authors, JY, to the handling editor at the time of review.
Publisher’s Note
All claims expressed in this article are solely those of the authors and do not necessarily represent those of their affiliated organizations, or those of the publisher, the editors, and the reviewers. Any product that may be evaluated in this article, or claim that may be made by its manufacturer, is not guaranteed or endorsed by the publisher.
References
Duan, Z., Zhang, L., Lin, Z., Fan, D., Saafi, M., Castro Gomes, J., et al. (2018). Experimental Test and Analytical Modeling of Mechanical Properties of Graphene-Oxide Cement Composites. J. Compos. Mater. 52 (22), 3027–3037. doi:10.1177/0021998318760153
Guo, R., He, K., Ma, Q., and Yan, F. (2017). Compressive Properties and Microstructure of Modified Lightweight Aggregate Concrete after Exposure to Elevated Temperatures. J. Building Mater. 20 (3), 333–339. doi:10.3969/j.issn.1007-9629.2017.03.003
Han, B., Zhang, L., Zeng, S., Dong, S., Yu, X., Yang, R., et al. (2017). Nano-core Effect in Nano-Engineered Cementitious Composites. Compos. A Appl. Sci. Manuf. 95, 100–109. doi:10.1016/j.compositesa.2017.01.008
Indukuri, C. S. R., Nerella, R., and Madduru, S. R. C. (2020). Workability, Microstructure, Strength Properties and Durability Properties of Graphene Oxide Reinforced Cement Paste. Aust. J. Civil Eng. 18 (1), 1–9. doi:10.1080/14488353.2020.1721952
Ji-Shu, C. (2017). High Temperature Resistance Performance of Portland Cement. Bull. Chin. Ceram. Soc. 36 (4), 1452–1456.
Khan, A. A., Mirza, E. H., Mohamed, B. A., El-Sharawy, M. A., Hasil Al-Asmari, M., Abdullah Al-Khureif, A., et al. (2019). Static and Dynamic Mechanical Properties of Graphene Oxide-Based Bone Cementing Agents. J. Compos. Mater. 53 (16), 2297–2304. doi:10.1177/0021998319826347
Li, J. Q., Wu, Z. M., Shi, C. J., Yuan, Q., and Zhang, Z. (2020). Durability of Ultra-high Performance concrete - A Review. Constr. Build. Mater. 255, 13. doi:10.1016/j.conbuildmat.2020.119296
Liang, H. (2014). Mid-infrared Response of Reduced Graphene Oxide and its High-Temperature Coefficient of Resistance. Aip Adv. 4 (10), 013106. doi:10.1063/1.4898786
Lu, Z., Chen, B., Leung, C. Y., Li, Z., and Sun, G. (2019). Aggregation Size Effect of Graphene Oxide on its Reinforcing Efficiency to Cement-Based Materials. Cem. Concr. Compos. 100, 85–91. doi:10.1016/j.cemconcomp.2019.04.005
Lu L, L., Zhang, Y., and Yin, B. (2020). Structure Evolution of the Interface between Graphene Oxide-Reinforced Calcium Silicate Hydrate Gel Particles Exposed to High Temperature. Comput. Mater. Sci. 173, 109440. doi:10.1016/j.commatsci.2019.109440
Lu Z, Z., Yu, J., Yao, J., and Hou, D. (2020). Experimental and Molecular Modeling of Polyethylene Fiber/cement Interface Strengthened by Graphene Oxide. Cem. Concr. Compos. 112, 103676. doi:10.1016/j.cemconcomp.2020.103676
Lv, S-H., Liu, J-J., Qiu, C-C., Ma, Y. J., and Zhou, Q. F. (2014). Microstructure and Mechanism of Reinforced and Toughened Cement Composites by Nanographene Oxide. J. Funct. Mater. 45 (4), 04084–04089.
Nadeem, A., Memon, S. A., and Lo, T. Y. (2014). The Performance of Fly Ash and Metakaolin concrete at Elevated Temperatures. Constr. Build. Mater. 62, 67–76. doi:10.1016/j.conbuildmat.2014.02.073
Parveen, S., Rana, S., Fangueiro, R., and Paiva, M. C. (2015). Microstructure and Mechanical Properties of Carbon Nanotube Reinforced Cementitious Composites Developed Using a Novel Dispersion Technique. Cem. Concr. Res. 73, 215–227. doi:10.1016/j.cemconres.2015.03.006
Peng, H., Ge, Y., Yang, Z., Liu, Y., and Lv, Y. (2018). Mechanical Properties and Microstructure of Graphene Oxide Reinforced Cement-Based Composites. Fuhe Cailiao Xuebao/Acta Mater. Compos. Sin. 35 (8), 2132–2139. doi:10.13801/j.cnki.fhclxb.20170919.001
Peng, H., Ge, Y., Cai, C. S., Zhang, Y., and Liu, Z. (2019). Mechanical Properties and Microstructure of Graphene Oxide Cement-Based Composites. Constr. Build. Mater. 194, 102–109. doi:10.1016/j.conbuildmat.2018.10.234
Poon, C.-S., Azhar, S., Anson, M., and Wong, Y.-L. (2001a). Comparison of the Strength and Durability Performance of normal- and High-Strength Pozzolanic Concretes at Elevated Temperatures. Cem. Concr. Res. 31 (9), 1291–1300. doi:10.1016/s0008-8846(01)00580-4
Poon, C.-S., Azhar, S., Anson, M., and Wong, Y.-L. (2001b). Strength and Durability Recovery of Fire-Damaged concrete after post-fire-curing. Cem. Concr. Res. 31 (9), 1307–1318. doi:10.1016/s0008-8846(01)00582-8
Qin, J. J., Yao, W., and Zuo, J. Q. (2013). Temperature Sensitive Properties of Hybrid Carbon Nanotube/Carbon Fiber Cement-Based Materials. Kem 539, 89–93. doi:10.4028/www.scientific.net/kem.539.89
Tombros, N., Veligura, A., Junesch, J., Jasper van den Berg, J., Zomer, P. J., Wojtaszek, M., et al. (2011). Large Yield Production of High Mobility Freely Suspended Graphene Electronic Devices on a Polydimethylglutarimide Based Organic Polymer. J. Appl. Phys. 109 (9), 093702–093705. doi:10.1063/1.3579997
Tyson, B. M., Abu Al-Rub, R. K., Yazdanbakhsh, A., and Grasley, Z. (2011). Carbon Nanotubes and Carbon Nanofibers for Enhancing the Mechanical Properties of Nanocomposite Cementitious Materials. J. Mater. Civ. Eng. 23 (7), 1028–1035. doi:10.1061/(asce)mt.1943-5533.0000266
Xu, Y., Zeng, J., Chen, W., Mao, J., Shen, J., and Hu, D. (2017). A State-Of-The-Art Review on Graphene Oxide Reinforced Cement Based Composites. Cailiao Daobao/Materials Rev. 31 (12), 150–155. doi:10.11896/j.issn.1005-023X.2017.023.022
Zhang, H., Yuan, Z., and Jia, Y. (2016). Experimental Study on Mechanical Properties of Metakaolin-Fly Ash-Based Geopolymer Concrete after Exposure to Elevated Temperatures. J. Disaster Prev. Mitigation Eng. 36 (3), 373–379.
Keywords: graphene oxide reinforced cement, high temperature, weight loss, flexural strength, compressive strength
Citation: Yan J, Wang J, Chen H and Xiang P (2022) High Temperature Exposure Assessment of Graphene Oxide Reinforced Cement. Front. Mater. 9:786260. doi: 10.3389/fmats.2022.786260
Received: 30 September 2021; Accepted: 05 January 2022;
Published: 09 March 2022.
Edited by:
John L. Provis, The University of Sheffield, United KingdomReviewed by:
C. Li, Soochow University, TaiwanNing Wang, East China Jiaotong University, China
Aldo Fernando Sosa Gallardo, The University of Manchester, United Kingdom
Copyright © 2022 Yan, Wang, Chen and Xiang. This is an open-access article distributed under the terms of the Creative Commons Attribution License (CC BY). The use, distribution or reproduction in other forums is permitted, provided the original author(s) and the copyright owner(s) are credited and that the original publication in this journal is cited, in accordance with accepted academic practice. No use, distribution or reproduction is permitted which does not comply with these terms.
*Correspondence: Ping Xiang, cHhpYW5nMi1jQG15LmNpdHl1LmVkdS5oaw==, OTA5ODU5ODk0QHFxLmNvbQ==