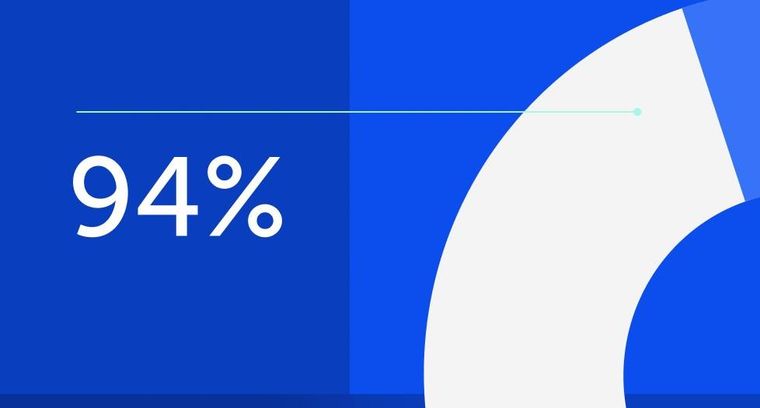
94% of researchers rate our articles as excellent or good
Learn more about the work of our research integrity team to safeguard the quality of each article we publish.
Find out more
REVIEW article
Front. Mater., 19 December 2022
Sec. Structural Materials
Volume 9 - 2022 | https://doi.org/10.3389/fmats.2022.1066796
This article is part of the Research TopicAdvanced Concretes and Their Structural Applications-Volume IIView all 15 articles
Steel is widely used as reinforcement for brittle structural materials such as concrete structure and unreinforced masonry structure (URM). However, the job wasted in steel reinforcement installation and the following corrosion hinder the development of construction industry. The emergence of strain-hardening cement composites (SHCC) provides an opportunity for steel-free construction. This paper provides a comprehensive review of the properties of SHCC and the corresponding practical exploration without reinforcement. The authors herein begin with a discussion on the superior properties of SHCC and its structural applications on the RC structure. Following this, the application of SHCC to retrofit URM is reviewed. Finally, we presents the advances of SHCC used in 3D concrete printing (3DCP) technology, and discuss the feasibility of SHCC structures without reinforcements in the future. When these explorations are coupled with appropriate theoretical models, true values for auto-construction without steel reinforcement will emerge.
Mechanical behavior of structures depends on the mechanical properties of structural materials. In the past, unreinforced masonry (URM) buildings were widely used around the world, while it processed poor strength and low ductility. With the emergency of steel and concrete, reinforced concrete (RC) structures became the most popular forms for civil engineering constructions. Meantime, steel reinforcements were also used in retrofitting URM. However, due to some inherent defects of concrete, such as brittleness, concrete is prone to cracking under tensile and bending loads, which may lead to serious steel corrosion in service life. Various damages in infrastructures, i.e., roads, bridges and water conservancy, are closely related to the brittleness of concrete and steel corrosion (Herrmann, 2013). Moreover, insufficient ductility of concrete is also one of the major causes to the structural damages under natural disasters. Take earthquake for example, the previous earthquake disaster statistics indicated that RC structures widely suffered concrete crushing and steel bar buckling under major earthquakes.
More importantly, due to population aging nowadays, labor shortage hinders the development of construction construction industry. The main challenges of civil engineering are the high demand for labor, the high cost of form-work, and the poor environmental sustainability. In recent years, 3D concrete printing (3DCP) technology was widely studied. However, the requirement for steel reinforcement, whose location is incompatible with the 3DCP process, is a significant obstacle to 3DCP.
A lot of work has gone into enhancing the characteristics of concrete in order to address the aforementioned issues. Numerous studies on fiber reinforced concrete (FRC) have shown that the mechanical properties of concrete are significantly enhanced by discontinuous short fibers used in cementitious matrix. In particular, strain-hardening cement composites (SHCC) process excellent tensile properties (Jun and Mechtcherine, 2010). In accordance with the principle of micro-mechanics in design, SHCC has a tensile capacity of more than 3% while maintaining a fiber volume fraction of no more than 2%. About two orders of magnitude more ductility (tensile strain capacity) exists in SHCC than in conventional cement. Multiple cracking with the widths smaller than 100 μm provide SHCC remarkably resistant to a variety of environmental exposure conditions (Li, 2012).
Considering the special features and excellent properties, it is not surprising that SHCC is gaining interest as a material for existing building retrofitting and innovative concrete manufacturing methods. This paper provides a comprehensive review of the structural application of SHCC without reinforcement, as shown in Figure 1. The authors herein begin with a discussion on the superior properties of SHCC and its structural applications on the RC structure. Particularly, a type of SHCC reinforced by polyethylene (PE) fibers is introduced, which processes similar deformability level with steel used in engineering. Following this, the application of SHCC to retrofit URM is reviewed. Finally, we presents the advances in 3DCP SHCC, and discuss the feasibility of SHCC structures without reinforcements in the future. Based on these discussions, more explorations in the SHCC materials and 3DCP technology would be identified in the future.
SHCC is developed using fracture mechanics and micro-mechanics principles. The fiber, matrix and the interface between them might be tailored to gain the desired tensile strain-hardening properties, as shown in Figure 2A. First, particular types of fiber and the matrix’s compressive strength should be optimized. Following this, fiber-pullout test is designed to measure the fiber bridging strength (σ0) and the crack opening (δ), as illustrated in Figure 2B. The maximum complementary energy of fiber bridging (Jb’) could also be determined. Strength and energy criteria should be met simultaneously to achieve excellent tensile properties (Li VC and Leung, 1992). The tensile stress at first crack (σss) must be less than σ0, according to the strength criterion (Eq. 1). This could guarantee the steady state of cracking. Additionally, the crack tip toughness (Jtip) should be less than Jb’. It is the critical condition for multi-cracking feature of SHCC. Both of the aforementioned criteria must be met by adjusting the characteristics of the fiber, cementitious matrix, and their interface.
FIGURE 2. (A) Excellent tensile features of SHCC designed by micro-mechanics (Yu et al., 2018a). (B) Fiber bridging stress (σ) and the crack opening (δ) curve obtained from fiber-pullout test (Ding et al., 2022).
Due to the high modulus and ease of diffusion, PVA fiber has been the most often utilized material in the production of conventional SHCC. The chemical link between the fiber and the cementitious matrix is very powerful as a result of the hydrophilic quality of PVA fiber, which is not desirable and causes premature fiber rupture (Figure 3) before maximizing the fiber reinforcement capability (Yu et al., 2018b). And thus lowers the possibility for pseudo-strain-hardening behavior. As a result, various common treatments have been applied to weaken the strength of fiber/matrix interface and raise the tensile strain capacity of PVA-SHCC, including oil coating for PVA fiber and the supplement of an air-entraining agent. However, the normal-strength matrix can handle the PVA fiber’s comparatively modest tensile strength (i.e., 1,600 MPa). As a result, the compressive strength of PVA-SHCC is typically lower than 60 MPa. Additionally, the lower elastic modulus of PVA-SHCC is lower elastic modulus compared to regular concrete would result in greater deformation, particularly under compression stresses (Ding et al., 2020a).
FIGURE 3. Pullout lengths of PVA fibers (A,B) and typical shape of fibre fracture (C) (Mechtcherine et al., 2011).
Additionally, PE fibers with a higher molecular weight are employed to create SHCC. Due to its hydrophobic nature, PE fiber has lower chemical bonding strength but better tensile strength and elastic modulus as compared to the PVA fiber. PE fibers typically pull out rather than burst during the onset and spread of cracks (Figure 4) (Wang et al., 2020a). Based on these features of PE fiber, ultra-high ductile cementitious composites (UHDCC) was developed, which showed mean tensile strains of over 8%, with certain mixtures even exceeding 12% (Yu et al., 2017). It is demonstrated that the ultra-high fracture bridging capability is the reason for high ductility of PE-SHCC (Zhang et al., 2020; Zhang et al., 2021). As a result, PE-SHCC could exhibit excellent tensile behavior with the high fracture toughness matrix (Yu et al., 2018c). Other mechanical properties of PE-SHCC were also investigated, ranging from normal strength to high strength (Ding et al., 2018a; Wang et al., 2019).
FIGURE 4. PE fiber pulled out from high strength matrix in (A) quasi-static and (B) dynamic regimes (Curosu et al., 2016).
In order to increase the practical application of SHCC, a comprehensive examination of the tensile qualities of all-grade strength SHCC was carried out (Yu et al., 2021a). Through experimental research, the size effect (Yu et al., 2020a) and the rate-dependent tensile properties (Yu et al., 2018d) of SHCC were explored. Furthermore, a performance-based design concept for SHCC was given out based on the necessary mechanical and crack pattern qualities (Li et al., 2019).
Due to the exceptional mechanical properties of SHCC, it has already been applied into major places, including beam-column connection (Figure 5) and infill masonry in RC structures (Qudah and Maalej, 2014; Liao et al., 2022a). Test results have proven that SHCC can reduce the use of reinforcement and even eliminate it under certain conditions (Liao et al., 2022b). As a result, fewer steel reinforcements are needed for reinforced SHCC beams, which provides practical value in civil engineering (Ding et al., 2018b).
As illustrated in Figure 6, the mechanical properties of PE-SHCC were experimentally investigated at the various levels to confirm the viability of PE-SHCC structures without steel reinforcement (Yu et al., 2018e). The plain PE-SHCC beams exhibited mechanical properties that are comparable to those of RC beams with a steel reinforcement ratio of 0.5%–1.5%. The loading capacity of the plain PE-SHCC column was comparable to that of an RC column with a 0.8% steel ratio. Comparison between RC frame and PE-SHCC frame was conducted through shaking table tests (Yu et al., 2019). Under seismic action, PE-SHCC frame exhibited remarkable cracking control and complied with several seismic codes.
FIGURE 6. Muti-scale tests on the feasibility of PE-SHCC for construction without steel reinforcement.
URM structures have limited shear strength and ductility resulting in sudden calamitous failures in the process of earthquake. The failure modes of masonry wall mainly include two categories: in-plane cracking failure of walls and out-of-plane collapse of walls and roofing Figure 7. Depicts typical failure modes of URM structures.
Above all, the out-of-plane collapse of walls caused by junction failure is the prime way of failure as shown in Figure 8 (Papanicolaou et al., 2007). Well constructed connection between walls can effectively avoid this type of failure. However, the falling of floor slab caused by collapse of walls is a severe failure mechanism resulting in a high mount of the fatalities. It is therefore vitally important to improve connection between walls and floor slab. This can save hundreds of thousands of buildings and lives.
Only when the walls and floor slab are well connected, the shear capacity of the walls can be mobilized through the development of shear cracks. Figure 9 shows four typical in-plane failure modes of masonry walls in plane, mainly including shear failure, sliding failure, overturning failure and corner crushing (Macabuag et al., 2012). The shear-compression ratio and the connection between mortar and bricks are the vital factors to determine the in-plane failure mode of masonry walls. Therefore, high shear strength and better interconnects between masonry walls are remarkably significant for masonry buildings to resist seismic load and other serious secondary disasters.
FIGURE 9. The various in-plane failure modes of masonry walls: (A) shear failure (B) sliding failure (C) overturning failure (D) corner crushing.
Engineers keep learning a lesson from the tragic disasters happened on URM buildings. After the Tangshan earthquake happened in 1976, a great mount of researches were carried out on retrofitting URM with reinforced mortar layer. Through a great quantity experimental study, the anti-seismic reinforcement of masonry with reinforced mortar layer has been adopted in JGJ 116-98, which is the industry standard technical code for seismic reinforcement of buildings in China. Figure 10 shows the practice of strengthening brick wall with double-sided steel reinforced mortar layer in practice.
FIGURE 10. Strengthening brick wall with double-sided reinforced mortar layer: (A) installing steel mesh and (B) mortar spraying.
However, this traditional strengthening method has many shortcomings. For example, the reinforced layer is made of steel reinforcement and mortar, which is much stiffer than the original masonry wall. Under extremely seismic impact, the composites system is incompatibility with the masonry substrate, and the material utilization rate of reinforcement is low. The reinforced mortar layer is generally in the range of 30–50 mm, too thick as used for indoor strengthening. Therefore, an increasing number of explorations were conducted on how to apply high-performance material to strengthening URM structures with higher efficiency, lower cost and better seismic enhancement.
As early as 1994, Victor Li found that the shear performance of SHCC is better than that of traditional concrete. Moreover, after the shear cracking, the stress of traditional concrete decrease sharply with the strain, while SHCC shows the unique characteristics of strain-hardening. It is considered that SHCC can be used in structures requiring both strength and ductility (Li, 2012). In recent years, the seismic performance of masonry structures strengthened with SHCC has been systematically studied, mainly including in-plane shear capacity, out-of-plane bending capacity, energy dissipation capacity, and structural integrity (Maalej et al., 2010; Mosallam and Banerjee, 2011).
Most studies on the in-plane shear capacity of masonry walls were carried out through diagonal compression tests (Brignola et al., 2008). It is found that the shear strength of masonry structure strengthened by SHCC was increased by 1.8–5.7 times, and its energy dissipation capacity was increased by at least 35 times (Dong et al., 2022a). The brittle failure of masonry structure can be significantly improved by multiple cracks in SHCC surface layer, as shown in Figure 11 (Dehghani et al., 2013). The strength and ductility of masonry walls were improved more significantly by double-sided strengthening than that single-sided strengthened. In addition, the masonry structure without any interface treatment does not suffer from interface stripping failure prior to structural failure. This demonstrated that SHCC and masonry can work well together, which is the key to making full use of SHCC materials. It is due to the comparatively low elastic modulus and thickness (20–30 mm) of the SHCC used in strengthening.
It is found that SHCC can greatly improve the out-of-plane strength and ductility of masonry structure through bending test, local-loading test, uniform-loading test and low-speed impact test (Singh and Munjal, 2020). This can effectively prevent masonry structure from collapse and destruction in earthquake and other sudden disasters. Moreover, parameter analysis was carried out in combination with ABAQUS simulation. Some better reinforcement details such as width to thickness ratio of SHCC surface layer is proposed.
Compared with the diagonal compression test, the stress state of the quasi-static test is closer to the engineering. The test results show that the strength, stiffness, ductility and energy dissipation capacity of masonry structure reinforced by SHCC can be improved by 56%–111% (Deng et al., 2020). In addition, SHCC can effectively restrain the cracking of masonry and improve its brittle failure (Lin et al., 2014; Choi et al., 2016). The in-plane shear strength of the reinforced masonry structure has been improved, while the bottom of the wall has become a relatively weak part. Therefore, the structure is prone to slip failure when the height to width ratio is small. If the connection between the wall and the beam or the floor is specially strengthened, the properties of the SHCC surface layer will be more fully utilized, thus further improving the seismic performance of the overall masonry structure (Esmaeeli et al., 2013; Dehghani et al., 2015). In addition, many scholars tried to spray SHCC surface layer for masonry strengthening, which further simplified the construction process without reducing the reinforcement quality (Kyriakides and Billington, 2014; Li et al., 2018).
Experimental studies were conducted on whole masonry buildings strengthened with SHCC material. As illustrated in Figure 12, the seismic performance of the masonry building before and after retrofitting were comparably observed by shaking table test. It is found that SHCC layer can significantly improves damage pattern, deformability and overall stiffness of structure, delays the degradation of structure stiffness. Meanwhile, the masonry building strengthened by SHCC outperformed the similar one strengthened with steel-grid-reinforced mortar layer (Deng et al., 2019).
As plotted in Figure 13, an earthquake damaged Chuan-dou timber-framed masonry building was retrofitted by using UHDC (Dong et al., 2022b). Shaking table tests were carried out on the original and the retrofitted masonry building. Experimental results demonstrated that the seismic behavior and ductility of Chuan-dou timber-framed masonry building were improved obviously. The structural integrity of the strengthened building for earthquake resistance was also much better than that of the unreinforced building. The features of SHCC, such as high ductility, high toughness and ease of constructions, promote wide use in structural retrofitting (Zhu et al., 2021).
FIGURE 13. Chuan-dou timber-framed masonry building: (A) Earthquake damaged building, (B) Process of spraying UHDC layer and (C) Shaking table test of the strengthened masonry building.
Compared with the reinforced mortar, SHCC with the characteristics of multi-cracking and strain-hardening has its special advantage in strengthening masonry building. Meanwhile, the proper stiffness and good bond with the block make it work well with the original structure. Moreover, the SHCC material is easy to construction by either spraying or artificial plastering. Furthermore, by increasing the connection between walls and floors/roofing, SHCC layer can improve the integrity of masonry buildings and consequently avoid collapse of buildings under earthquake action. In addition, the original architectural features of ancient buildings can be preserved by single-sided strengthening. Table 1 compares the characteristics of several different reinforcement materials.
Powder-based 3D printing technique (Yu et al., 2020b) and extrusion-based nozzle-printing technique (Buswell et al., 2018) are the two primary varieties of 3DCP. Extrusion-based concrete printing is currently the most widely utilized technique owing to its simplicity of use, speed of construction, and suitability with the creation of light weight structures (Wang et al., 2020b). As shown in Figure 14, the extrusion-based 3DCP process is popular and has a multi—stage process (Yu et al., 2021b). This method doesn’t need a framework or particles and might be utilized for printing with the proper cementitious material. For continuous construction, the fresh combinations must first be easily pumped from the mixer to the printing nozzle, i.e., pumpability. After that, the mixtures must have the ability to be continually extruded through the printing nozzle, i.e., extrudability. The extruded filaments must also be able to support the weight of upper layers, maintain their original shape without deforming, and firmly stack up layer after layer without showing any visible distortion, i.e., buildability (Ma et al., 2018; Panda et al., 2018).
Specific qualities of concrete materials, both in fresh and hardened state, are needed by 3DCP (Ma et al., 2018; Lu et al., 2019). Fresh property, such as pumpability, extrudability, and buildability, becomes more important (Wangler et al., 2019). Sometimes these properties are conflicting in nature, and achieving their coordination is an important challenge.
The mechanical behavior of 3DCP-SHCC as well as the fresh behavior were widely analyzed. The ideal open time range for continuous printing was established by various flowability studies, as depicted in Figure 15. Pumpability and buildability were tested using a 1.5 m high 3DP-SHCC twisted column with 150 printed layers that were each 10 mm thick (Li et al., 2020). It was discovered that fibers and nanoparticles will improve the rheological characteristics for form retention (Chu et al., 2021). The results demonstrate that SHCC exhibit respectable work-ability in 3D printing (Ye et al., 2021a).
The mechanical behavior of 3DCP-FRC with various types of fibers, including basalt, steel, and polypropylene, have all been studied on various scales. No strain hardening tendency has been observed, with the exception of mortars explicitly created as SHCC (Chu et al., 2021).
The in-plane properties of extruded SHCC tend to be better that of the cast SHCC, as seen in Figure 16 (Soltan and Li, 2018). The robotically printed specimens showed the typical numerous micro-cracking and strain-hardening characteristic (Ogura et al., 2018). The fiber alignment parallel to the printing direction was greatly improved by the reduced nozzle size and larger fiber volume percentage. As a result, the printed specimens surpassed the mold-cast specimens mechanically (Arunothayan et al., 2021). Due to the strong compressive and flexural strengths and deflection-hardening behavior of SHCC, it is possible to make thinner 3D-printed structures with a significant reduction in or elimination of conventional steel bars (Arunothayan et al., 2020). Additionally, the printed PE-SHCC has superior deformability and energy dissipation than mold-cast specimens in some loading directions (Ye et al., 2021b).
Model cast concrete is regarded as isotropic. However, the multi-layer structure might introduce anisotropy in terms of durability and strength. The issue is more complicated for SHCC. The fiber orientation in the manufactured filament itself is not random. As a result, it is reasonable to anticipate that ductility and strength will vary in different directions. Some primary explorations on 3D-SHCC anisotropy have been carried out. Differences in the mechanical properties of interlayer separation and compression have been identified (Ding et al., 2020b).
Moreover, some advantages were also found in this hierarchical structures (Ye et al., 2021c). Inspired by natural nacre, a type of novel 3DCP-PE-SHCC member was developed. It exhibited better mechanical behavior than model cast members, especially in ductility and toughness as shown in Figure 17. It was demonstrated that the interface between layers could release the stress concentration and induce the crack-deflection, which is similar to nacre toughing motifs. The results further verified the significant potential of the 3DCP-SHCC structures without reinforcements.
FIGURE 17. Mechanical behavior of nacre-inspired 3DCP-SHCC beams: (A–F) normal design beams and (G) nacre-inspired beam.
This review paper discusses the superior properties of the SHCC and its applications in a variety of types of structures. The high ductility and toughness of SHCC make it possible to release the concrete from the steel reinforcements. As a result, a serious of structural applications of SHCC have been developed, as shown in Figure 18.
For the URM structures, brittleness and poor shear performance should be reinforced to meet current structural requirements. Compared with steel reinforced method, SHCC layer has been proved to be a better method. For the concrete structures, the feasibility of using SHCC without steel reinforcement has been verified at material, structural member and structure levels.
In the future, 3DCP would become a reasonable technology to solve the labor shortage problem of construction industry. In this context, 3DCP-SHCC structures have been widely investigated. The printed SHCC exhibits a serious of features, such as high ductility, high toughness, and anisotropic properties. Additionally, a nacre-inspired 3DCP-SHCC with enhanced mechanical properties is developed. This is further demonstrating the potential of the 3DCP-SHCC structures without reinforcements.
There remain a number of areas of needed research in 3DCP-SHCC structures without reinforcement. These include for example the interface between layers, the full-scale structural behaviors, and response to seismic action. Moreover, the workability and shrinkage of 3DCP-SHCC should be noticed in the future, which provide necessary conditions for engineering applications. When these explorations are coupled with theoretical models, true values for 3DCP-SHCC without reinforcement will emerge.
FJ: Conceptualization, Writing—original draft. XL: Investigation. LT: Investigation, Supervision. YT: Investigation. JY: Conceptualization, Funding acquisition, Supervision.
The authors declare that the research was conducted in the absence of any commercial or financial relationships that could be construed as a potential conflict of interest.
All claims expressed in this article are solely those of the authors and do not necessarily represent those of their affiliated organizations, or those of the publisher, the editors and the reviewers. Any product that may be evaluated in this article, or claim that may be made by its manufacturer, is not guaranteed or endorsed by the publisher.
Arunothayan, A. R., Nematollahi, B., Ranade, R., Bong, S. H., and Sanjayan, J. (2020). Development of 3D-printable ultra-high performance fiber-reinforced concrete for digital construction. Constr. Build. Mater. 257, 119546. doi:10.1016/j.conbuildmat.2020.119546
Arunothayan, A. R., Nematollahi, B., Ranade, R., Bong, S. H., Sanjayan, J. G., and Khayat, K. H. (2021). Fiber orientation effects on ultra-high performance concrete formed by 3D printing. Cem. Concr. Res. 143, 106384. doi:10.1016/j.cemconres.2021.106384
Brignola, A., Frumento, S., Lagomarsino, S., and Podestà, S. (2008). Identification of shear parameters of masonry panels through the in-situ diagonal compression test. Int. J. Archit. Herit. 3 (1), 52–73. doi:10.1080/15583050802138634
Buswell, R. A., Leal de Silva, W. R., Jones, S. Z., and Dirrenberger, J. (2018). 3D printing using concrete extrusion: A roadmap for research. Cem. Concr. Res. 112, 37–49. doi:10.1016/j.cemconres.2018.05.006
Choi, H.-K., Bae, B.-I., and Choi, C.-S. (2016). Lateral resistance of unreinforced masonry walls strengthened with engineered cementitious composite. Int. J. Civ. Eng. 14 (6), 411–424. doi:10.1007/s40999-016-0026-1
Chu, S. H., Li, L. G., and Kwan, A. K. H. (2021). Development of extrudable high strength fiber reinforced concrete incorporating nano calcium carbonate. Addit. Manuf. 37, 101617. doi:10.1016/j.addma.2020.101617
Curosu, I., Mechtcherine, V., and Millon, O. (2016). Effect of fiber properties and matrix composition on the tensile behavior of strain-hardening cement-based composites (SHCCs) subject to impact loading. Cem. Concr. Res. 82, 23–35. doi:10.1016/j.cemconres.2015.12.008
Dehghani, A., Fischer, G., and Nateghi Alahi, F. (2013). Strengthening masonry infill panels using engineered cementitious composites. Mat. Struct. 48 (1-2), 185–204. doi:10.1617/s11527-013-0176-4
Dehghani, A., Nateghi-Alahi, F., and Fischer, G. (2015). Engineered cementitious composites for strengthening masonry infilled reinforced concrete frames. Eng. Struct. 105, 197–208. doi:10.1016/j.engstruct.2015.10.013
Deng, M., Dong, Z., Wang, X., Zhang, Y., and Zhou, T. (2019). Shaking table tests of a half-scale 2-storey URM building retrofitted with a high ductility fibre reinforced concrete overlay system. Eng. Struct. 197, 109424. doi:10.1016/j.engstruct.2019.109424
Deng, M., Zhang, W., and Li, N. (2020). In-plane cyclic loading tests of concrete hollow block masonry walls retrofitted with high ductile fiber-reinforced concrete. Constr. Build. Mater. 238, 117758. doi:10.1016/j.conbuildmat.2019.117758
Ding, T., Xiao, J., Zou, S., and Zhou, X. (2020). Anisotropic behavior in bending of 3D printed concrete reinforced with fibers. Compos. Struct. 254, 112808. doi:10.1016/j.compstruct.2020.112808
Ding, Y., Yu, J.-t., Yu, K.-Q., and Xu, S.-l. (2018). Basic mechanical properties of ultra-high ductility cementitious composites: From 40 MPa to 120 MPa. Compos. Struct. 185, 634–645. doi:10.1016/j.compstruct.2017.11.034
Ding, Y., Yu, K.-Q., Yu, J.-t., and Xu, S.-l. (2018). Structural behaviors of ultra-high performance engineered cementitious composites (UHP-ECC) beams subjected to bending-experimental study. Constr. Build. Mater. 177, 102–115. doi:10.1016/j.conbuildmat.2018.05.122
Ding, Y., Yu, K., and Li, M. (2022). A review on high-strength engineered cementitious composites (HS-ECC): Design, mechanical property and structural application. Structures 35, 903–921. doi:10.1016/j.istruc.2021.10.036
Ding, Y., Yu, K., and Mao, W. (2020). Compressive performance of all-grade engineered cementitious composites: Experiment and theoretical model. Constr. Build. Mater. 244, 118357. doi:10.1016/j.conbuildmat.2020.118357
Dong, F., Li, Z., Yu, J., Jiang, F., and Wang, H. (2022). Shaking-table test on a two-story timber-framed masonry structure retrofitted with ultra-high ductile concrete. J. Struct. Eng. (N. Y. N. Y). 148 (1). doi:10.1061/(asce)st.1943-541x.0003164
Dong, F., Wang, H., Jiang, F., Xing, Q., and Yu, J. (2022). In-plane shear behavior of masonry panels strengthened with ultra-high ductile concrete (UHDC). Eng. Struct. 252, 113609. doi:10.1016/j.engstruct.2021.113609
Esmaeeli, E., Manning, E., and Barros, J. A. O. (2013). Strain hardening fibre reinforced cement composites for the flexural strengthening of masonry elements of ancient structures. Constr. Build. Mater. 38, 1010–1021. doi:10.1016/j.conbuildmat.2012.09.065
Herrmann, A. W. (2013). ASCE. 2013 report card for America’s infrastructure. http://www.infrastructurereportcard.org/road-infrastructure.
Jun, P., and Mechtcherine, V. (2010). Behaviour of Strain-hardening Cement-based Composites (SHCC) under monotonic and cyclic tensile loading. Cem. Concr. Compos. 32 (10), 801–809. doi:10.1016/j.cemconcomp.2010.07.019
Kyriakides, M. A., and Billington, S. L. (2014). Cyclic response of nonductile reinforced concrete frames with unreinforced masonry infills retrofitted with engineered cementitious composites. J. Struct. Eng. (N. Y. N. Y). 140 (2). doi:10.1061/(asce)st.1943-541x.0000833
Li, L., Cai, Z., Yu, K., Zhang, Y. X., and Ding, Y. (2019). Performance-based design of all-grade strain hardening cementitious composites with compressive strengths from 40 MPa to 120 MPa. Cem. Concr. Compos. 97, 202–217. doi:10.1016/j.cemconcomp.2019.01.001
Li Vc, L. C., and Leung, C. K. Y. (1992). Steady-state and multiple cracking of short random fiber composites. J. Eng. Mech. 118 (11), 2246–2264. doi:10.1061/(asce)0733-9399(1992)118:11(2246)
Li, V. C., Bos, F. P., Yu, K., McGee, W., Ng, T. Y., Figueiredo, S. C., et al. (2020). On the emergence of 3D printable engineered, strain hardening cementitious composites (ECC/SHCC). Cem. Concr. Res. 132, 106038. doi:10.1016/j.cemconres.2020.106038
Li, V. C. (2012). Tailoring ecc for special attributes: A review. Int. J. Concr. Struct. Mat. 6 (3), 135–144. doi:10.1007/s40069-012-0018-8
Li, Y., Zhu, J., and Wang, Z. (2018). Investigation on mechanical properties of masonry infill wall strengthened with ECC. KSCE J. Civ. Eng. 23 (1), 295–306. doi:10.1007/s12205-018-5424-2
Liao, Q., Su, Y., Yu, J., and Yu, K. (2022a). Compression-shear performance and failure criteria of seawater sea-sand engineered cementitious composites with polyethylene fibers. Constr. Build. Mater. 345, 128386.
Liao, Q., Su, Y., Yu, J., and Yu, K. (2022b). Torsional behavior of BFRP bars reinforced engineered cementitious composites beams without stirrup. Eng. Struct. 268, 114748.
Lin, Y.-W., Wotherspoon, L., Scott, A., and Ingham, J. M. (2014). In-plane strengthening of clay brick unreinforced masonry wallettes using ECC shotcrete. Eng. Struct. 66, 57–65. doi:10.1016/j.engstruct.2014.01.043
Lu, B., Weng, Y., Li, M., Qian, Y., Leong, K. F., Tan, M. J., et al. (2019). A systematical review of 3D printable cementitious materials. Constr. Build. Mater. 207, 477–490. doi:10.1016/j.conbuildmat.2019.02.144
Ma, G., Li, Z., and Wang, L. (2018). Printable properties of cementitious material containing copper tailings for extrusion based 3D printing. Constr. Build. Mater. 162, 613–627. doi:10.1016/j.conbuildmat.2017.12.051
Maalej, M., Lin, V. W. J., Nguyen, M. P., and Quek, S. T. (2010). Engineered cementitious composites for effective strengthening of unreinforced masonry walls. Eng. Struct. 32 (8), 2432–2439. doi:10.1016/j.engstruct.2010.04.017
Macabuag, J., Guragain, R., and Bhattacharya, S. (2012). Seismic retrofitting of non-engineered masonry in rural Nepal. Proc. Institution Civ. Eng. - Struct. Build. 165 (6), 273–286. doi:10.1680/stbu.10.00015
Mechtcherine, V., Millon, O., Butler, M., and Thoma, K. (2011). Mechanical behaviour of strain hardening cement-based composites under impact loading. Cem. Concr. Compos. 33 (1), 1–11. doi:10.1016/j.cemconcomp.2010.09.018
Mosallam, A., and Banerjee, S. (2011). Enhancement in in-plane shear capacity of unreinforced masonry (URM) walls strengthened with fiber reinforced polymer composites. Compos. Part B Eng. 42 (6), 1657–1670. doi:10.1016/j.compositesb.2011.03.015
Ogura, H., Nerella, V. N., and Mechtcherine, V. (2018). Developing and testing of strain-hardening cement-based composites (SHCC) in the context of 3D-printing. Mater. (Basel) 11 (8), 1375. doi:10.3390/ma11081375
Panda, B., Unluer, C., and Tan, M. J. (2018). Investigation of the rheology and strength of geopolymer mixtures for extrusion-based 3D printing. Cem. Concr. Compos. 94, 307–314. doi:10.1016/j.cemconcomp.2018.10.002
Papanicolaou, C. G., Triantafillou, T. C., Papathanasiou, M., and Karlos, K. (2007). Textile reinforced mortar (TRM) versus FRP as strengthening material of URM walls: Out-of-plane cyclic loading. Mat. Struct. 41 (1), 143–157. doi:10.1617/s11527-007-9226-0
Qudah, S., and Maalej, M. (2014). Application of Engineered Cementitious Composites (ECC) in interior beam–column connections for enhanced seismic resistance. Eng. Struct. 69, 235–245. doi:10.1016/j.engstruct.2014.03.026
Singh, S. B., and Munjal, P. (2020). Out-of-Plane response of ECC strengthened masonry wallets with openings. KSCE J. Civ. Eng. 24 (7), 2078–2087. doi:10.1007/s12205-020-1346-x
Soltan, D. G., and Li, V. C. (2018). A self-reinforced cementitious composite for building-scale 3D printing. Cem. Concr. Compos. 90, 1–13. doi:10.1016/j.cemconcomp.2018.03.017
Wang, L., Jiang, H., Li, Z., and Ma, G. (2020). Mechanical behaviors of 3D printed lightweight concrete structure with hollow section. Arch. Civ. Mech. Eng. 20 (1), 16. doi:10.1007/s43452-020-00017-1
Wang, Y., Liu, F., Yu, J., Dong, F., and Ye, J. (2020). Effect of polyethylene fiber content on physical and mechanical properties of engineered cementitious composites. Constr. Build. Mater. 251, 118917. doi:10.1016/j.conbuildmat.2020.118917
Wang, Y., Wei, L., Yu, J., and Yu, K. (2019). Mechanical properties of high ductile magnesium oxychloride cement-based composites after water soaking. Cem. Concr. Compos. 97, 248–258. doi:10.1016/j.cemconcomp.2018.12.028
Wangler, T., Roussel, N., Bos, F. P., Salet, T. A. M., and Flatt, R. J. (2019). Digital concrete: A review. Cem. Concr. Res. 123, 105780. doi:10.1016/j.cemconres.2019.105780
Xu, S., Hou, L.-J., and Zhang, X.-F. (2012). Shear behavior of reinforced ultrahigh toughness cementitious composite beams without transverse reinforcement. J. Mat. Civ. Eng. 24 (10), 1283–1294. doi:10.1061/(asce)mt.1943-5533.0000505
Ye, J., Cui, C., Yu, J., Yu, K., and Dong, F. (2021). Effect of polyethylene fiber content on workability and mechanical-anisotropic properties of 3D printed ultra-high ductile concrete. Constr. Build. Mater. 281, 122586. doi:10.1016/j.conbuildmat.2021.122586
Ye, J., Cui, C., Yu, J., Yu, K., and Xiao, J. (2021). Fresh and anisotropic-mechanical properties of 3D printable ultra-high ductile concrete with crumb rubber. Compos. Part B Eng. 211, 108639. doi:10.1016/j.compositesb.2021.108639
Ye, J., Yu, K., Yu, J., Zhang, Q., and Li, L. (2021). Designing ductile, tough, nacre-inspired concrete member in metric scale. Cem. Concr. Compos. 118, 103987. doi:10.1016/j.cemconcomp.2021.103987
Yu, J., Yao, J., Lin, X., Li, H., Lam, J. Y., Leung, C. K., et al. (2018). Tensile performance of sustainable Strain-Hardening Cementitious Composites with hybrid PVA and recycled PET fibers. Cem. Concr. Res. 107, 110–123. doi:10.1016/j.cemconres.2018.02.013
Yu, J., Ye, J., Zhao, B., Xu, S., Wang, B., and Yu, K. (2019). Dynamic response of concrete frames including plain ductile cementitious composites. J. Struct. Eng. (N. Y. N. Y). 145 (6). doi:10.1061/(asce)st.1943-541x.0002292
Yu, K.-Q., Yu, J.-T., Dai, J.-G., Lu, Z.-D., and Shah, S. P. (2018). Development of ultra-high performance engineered cementitious composites using polyethylene (PE) fibers. Constr. Build. Mater. 158, 217–227. doi:10.1016/j.conbuildmat.2017.10.040
Yu, K., Ding, Y., and Zhang, Y. X. (2020). Size effects on tensile properties and compressive strength of engineered cementitious composites. Cem. Concr. Compos. 113, 103691. doi:10.1016/j.cemconcomp.2020.103691
Yu, K., Li, L., Yu, J., Wang, Y., Ye, J., and Xu, Q. (2018). Direct tensile properties of engineered cementitious composites: A review. Constr. Build. Mater. 165, 346–362. doi:10.1016/j.conbuildmat.2017.12.124
Yu, K., Li, L., Yu, J., Xiao, J., Ye, J., and Wang, Y. (2018). Feasibility of using ultra-high ductility cementitious composites for concrete structures without steel rebar. Eng. Struct. 170, 11–20. doi:10.1016/j.engstruct.2018.05.037
Yu, K., McGee, W., Ng, T. Y., Zhu, H., and Li, V. C. (2021). 3D-printable engineered cementitious composites (3DP-ECC): Fresh and hardened properties. Cem. Concr. Res. 143, 106388. doi:10.1016/j.cemconres.2021.106388
Yu, K. Q., Dai, J.-G., Lu, Z.-D., and Poon, C.-S. (2018). Rate-dependent tensile properties of ultra-high performance engineered cementitious composites (UHP-ECC). Cem. Concr. Compos. 93, 218–234. doi:10.1016/j.cemconcomp.2018.07.016
Yu, K., Wang, Y., Yu, J., and Xu, S. (2017). A strain-hardening cementitious composites with the tensile capacity up to 8%. Constr. Build. Mater. 137, 410–419. doi:10.1016/j.conbuildmat.2017.01.060
Yu, K., Zhu, H., Hou, M., and Li, V. C. (2021). Self-healing of PE-fiber reinforced lightweight high-strength engineered cementitious composite. Cem. Concr. Compos. 123, 104209. doi:10.1016/j.cemconcomp.2021.104209
Yu, S., Du, H., and Sanjayan, J. (2020). Aggregate-bed 3D concrete printing with cement paste binder. Cem. Concr. Res. 136, 106169. doi:10.1016/j.cemconres.2020.106169
Zhang, Z., Liu, S., Yang, F., Weng, Y., and Qian, S. (2021). Sustainable high strength, high ductility engineered cementitious composites (ECC) with substitution of cement by rice husk ash. J. Clean. Prod. 317, 128379. doi:10.1016/j.jclepro.2021.128379
Zhang, Z., Yang, F., Liu, J.-C., and Wang, S. (2020). Eco-friendly high strength, high ductility engineered cementitious composites (ECC) with substitution of fly ash by rice husk ash. Cem. Concr. Res. 137, 106200. doi:10.1016/j.cemconres.2020.106200
Keywords: strain-hardening cementitious composites, strengthening masonry building, 3D concrete print, without reinforcement, automatic construction
Citation: Jiang F, Long X, Tian L, Tan Y and Yu J (2022) Tensile strain-hardening cementitious composites and its practical exploration without reinforcement: A review. Front. Mater. 9:1066796. doi: 10.3389/fmats.2022.1066796
Received: 11 October 2022; Accepted: 06 December 2022;
Published: 19 December 2022.
Edited by:
Zhigang Zhang, Chongqing University, ChinaReviewed by:
Lili Kan, University of Shanghai for Science and Technology, ChinaCopyright © 2022 Jiang, Long, Tian, Tan and Yu. This is an open-access article distributed under the terms of the Creative Commons Attribution License (CC BY). The use, distribution or reproduction in other forums is permitted, provided the original author(s) and the copyright owner(s) are credited and that the original publication in this journal is cited, in accordance with accepted academic practice. No use, distribution or reproduction is permitted which does not comply with these terms.
*Correspondence: Likang Tian, NjE2MDAwMzYzQHFxLmNvbQ==
Disclaimer: All claims expressed in this article are solely those of the authors and do not necessarily represent those of their affiliated organizations, or those of the publisher, the editors and the reviewers. Any product that may be evaluated in this article or claim that may be made by its manufacturer is not guaranteed or endorsed by the publisher.
Research integrity at Frontiers
Learn more about the work of our research integrity team to safeguard the quality of each article we publish.