- 1International Joint Research Lab for Eco-building Materials and Engineering of Henan, School of Civil Engineering and Communications, North China University of Water Resources and Electric Power, Zhengzhou, China
- 2Collaborative Innovation Center for Efficient Utilization of Water Resources, North China University of Water Resources and Electric Power, Zhengzhou, China
- 3Henan Fifth Construction Group, Zhengzhou, China
Producing concrete with large content of fly ash attracts increasing attention in low carbon building materials. In this paper, the fly-ash concrete (FAC) with a content of fly ash no less than 50% total weight of binders was developed. The adaptability of fly ash used for concrete was firstly examined by testing the water requirement of normal consistency and the setting time for cement fly-ash paste, and the strengths of cement fly-ash mortar at the curing age of 7 and 28 days. The factors of water-to-binder ratio from 0.3 to 0.5, the content of fly-ash from 40% to 80%, and the excitation measures with additional Ca(OH)2 and steam curing at initial were considered. After that, the FAC was designed by adding an excessive content of fly ash to reduce the water-to-binder ratio from 0.50 to 0.26, and the content of fly-ash varied from 52% to 60%. Results show that the cement fly-ash paste presented a reduction of water requirement and an elongation of setting time with the increased content of fly ash. This provides a foundation of maintaining the workability of fresh FAC with a decreased water-to-binder ratio by adding the excessive content of fly ash. The cement fly-ash mortar had a lower early strength due to the slow reaction of fly-ash with Ca(OH)2, which could be improved by steam curing at the initial 24 h due to the excitation of fly-ash activity. At curing age of 28 days, the FAC had the expected axial compressive strength and modulus of elasticity, but the tensile strength was lower than predicted. At the curing age of 56 days, all the basic mechanical properties of FAC reached the prediction. The resistances of FAC to chloride ion penetration and carbonization were realized at a very high level as specified in codes.
Introduction
Fly ash is a by-product of coal combustion in power stations, which presents as tiny grains with a certain pozzolanic activity. As one of the industrial solid wastes, fly ash has attracted much more attention on its comprehensive utilization to protect the environment (Wu and Lian, 1999; Choi et al., 2015; Amran et al., 2021). Based on its chemical composition, grain fineness, and pozzolanic activity, fly ash is classified into different types and is most widely used as a mineral admixture of cement and concrete (Wu and Lian, 1999; Li et al., 2013; GB/T1596-2017, 2017). Normally, fly ash admixed in concrete is no more than 40% of the total binder to improve the workability of fresh mix and get a better reliability of concrete, ensuring its strength (Liu et al., 2013a; Zhao et al., 2013; GB/T1596-2017, 2017; Zhao et al., 2018; Ding et al., 2020; Liu et al., 2021). Based on technique specifications (JGJ55-2011, 2011; JGJ/T281-2012, 2012; GB/T50164-2014, 2014), the limit content of fly ash is 35%-40% for the concrete with common Portland cement used for reinforced concrete structures when the water-to-binder ratio is no larger than 0.40 and should be reduced by 5% when the water-to-binder ratio is larger than 0.40. In order to control the early strength and reduce the loss of prestress caused by shrinkage and creep of concrete, the limit content of fly ash for the concrete used for prestressed concrete structures should be reduced by 10%-15% on the same condition to reinforce concrete structures. Because no mineral admixtures are admixed for the Portland cement, the limit content of fly ash can be increased by 5%–10% at the same above condition if the concrete is made with Portland cement.
The decreased strength of fly-ash concrete (FAC) especially at an early age is a drawback which confined the content of admixed fly ash. Normally, the FAC with content of fly ash larger than 30%–40% has an elongated setting time of fresh mix and presents a lower strength before the standard curing age of 28 days, although the strength continuously increased later (Malhotra and Paintert, 1989; Sun G. W. et al, 2019; Olivia et al., 2019). To solve this problem, excitation measures for the activity of fly ash have been studied. One is addition of other alkaline admixtures such as calcium hydrate, sodium silicate, and calcium carbonate, which makes the crystalline silicon and aluminum compounds of fly ash converse into active soluble compounds (Gunasekara et al., 2016; Hefni et al., 2018; Singh and Subramaniam, 2019; Promsawat et al., 2020). The second is the admixture of other high-activity admixtures such as silica fume, nano silica, and metakaolin. This accelerates the hydrations of both fly ash and cement, decreases the porosity and total pore volume, and improves the microstructure of the interface transition zone (Mei et al., 2018; Nežerka et al., 2019; Anjos et al., 2020). The third is the grounding of the fly ash into much more fineness. With the changes in particle morphology and distribution of irregular grains from broken spherical particles, fly ash behaves with higher pozzolanic activity and tiny-aggregate filling effect on the improvement of composite strength (Ma et al., 2021). The fourth is making of the fly-ash composites at a high-temperature environment; this accelerates the hydration of both cement and fly ash (Hefni et al., 2018; Mei et al., 2018; Singh and Subramaniam, 2019; Yang et al., 2021). However, some of the measures are debatable due to the lack of convenience of engineering application, high energy consumption, and/or low economic benefit.
To achieve economic benefits from effective utilization of fly ash, studies have been done to improve the applicability of FAC with large content of fly ash. With the replacement of 50% cement by fly ash containing 6.49% calcium oxide, the high-fluidity FAC was made by admixing the superplasticizer and air-entraining agent; the early strength was ensured by decreasing the water dosage and increasing the content of binders, and then the strength at the curing age of 28 days reached the target (Choi et al., 2015). In case of the replacement of 20%–80% cement by fly ash, the flowability of fly ash cement composites is improved at paste and concrete level (Thiyagarajan et al., 2018). The self-compacting FAC with strength around 30 MPa at the curing age of 28 days was made with the replacement of 50% cement by class-C fly ash of 14.1% calcium (Wardhono, 2021). The FAC was produced with the replacement of 50% cement by fly ash containing 14.6% calcium oxide; the compressive strength was 45 MPa at the curing age of 56 days (Solikin and Setiawan, 2017). The FACs were prepared with the replacement of 40%–70% cement by fly ash containing 8.75% calcium oxide. Due to critical controls of the dilution and the pozzolanic effects of fly ash on cement hydration, the compressive strength of FAC was lower at the early age with decreased heat release of hydration, while it developed faster beyond the curing age of 28 days; the FAC with 40% replacement of cement by fly ash showed comparable compressive strength to the control concrete at the curing age of 28 days, while those with 55% and 70% fly ash reduced by 30.9% and 52.7%, respectively (Sun J. et al, 2019). By lowering the water-to-binder ratio at 0.2 and properly combining raw materials, the FAC with adequate strength and workability was developed even when 80% of the cement was replaced by fly ash. In this case, the content of fly ash had no obvious effect on the cementing efficiency of fly ash. When the content of fly ash further increased, the cementing efficiency of fly ash decreased significantly. Meanwhile, adding a small amount of silica fume could improve the mechanical properties and the penetration performance of FAC (Yu et al., 2017). The concrete with 56% fly ash of binders was examined to have good long-term strength development accompanied with high resistance of chloride ion penetration (Sivasundaram et al., 1990). Due to the positive effects of fly ash on refinement of pores, filling macro pores and improving the microstructure of the interface transition zone, the concrete with large content of fly ash behaves with ideal resistances to chloride ion penetration and carbonation (Aruhan and Yan, 2011; Li et al., 2014; Amran et al., 2021).
Generally, the above studies provide a sound foundation for the understanding of the effect of fly ash on performance of FAC. In practice, considering the effective utilization of long-term strength of concrete and the control of early tensile stress due to the heat release of cement hydration, the large content of fly ash no less than 40% can be used for the large volume concrete structures, and the limit content of fly ash can be taken as 65% for the roller compacted concrete dam (JGJ55-2011, 2011; JGJ/T281-2012, 2012; GB/T50164-2014, 2014). However, lack of FAC with large content of fly ash over 50% is applied in reinforced concrete structures, and few studies have been done on the relationships of different basic mechanical properties which are needed in the structural design (Li et al., 2012; Liu et al., 2013b).
Aiming to provide sufficient proof for the application of FAC with large content of fly ash in reinforced concrete structures, an experimental study was carried out in this paper. To provide a foundation of FAC with the content of fly ash over 50%, tests for the activity of fly ash were firstly examined to verify the effects of fly-ash content on the workability and strength of cement fly-ash mortar and determine the efficiency of activity excitation by calcium hydroxide and steam curing. After that, the mixed proportion of FAC was designed by using the method of replacing cement with excessive fly ash to decrease the water-to-binder ratio (Li et al., 2012; Li et al., 2014). The workability of fresh mix, the mechanical properties at the curing age of 7–56 days, and the resistances to chloride ion penetration and carbonization of hardened FAC with content of fly ash from 52% to 60% were experimentally studied. Test results are discussed and evaluated with the comparisons to specifications of current codes.
Raw materials
Grade 42.5 common Portland cement and second-class fly ash produced by Henan Mengdian Cement Co. Ltd. (Zhengzhou, China) were used as binders. The physical and mechanical properties are presented in Tables 1, 2, which met the specifications of China codes (GB175-2007, 2007; GB/T1596-2017, 2017). The amounts of oxides in cement and fly ash were detected by the methods specified in the China code (GB/T176-2017, 2017); test results are presented in Table 3.
According to the specifications of China codes (GB/T14684-2011, 2011; GB/T14685-2011, 2011), the properties of fine and coarse aggregates were measured. The fine aggregate was manufactured sand with fineness modulus of 2.6, apparent density of 2,690 kg/m3, and mud content of 1.2%. The coarse aggregate was crushed limestone with apparent density of 2,800 kg/m3, closed-packing density of 1,745 kg/m3, crushed index in cylindrical tube of 4.8%, and mud content of 3.2%.
The water reducer was of high-performance polycarboxylic acid type with water reduction of 35%. The alkali activator for fly ash was Ca(OH)2. The mix water was tap water.
Tests for activity of fly ash
Properties of fresh cement fly-ash paste
Tests of the water requirement of normal consistency and the setting time for cement fly-ash paste were carried out according to the specification of the China code (GB/T1346-2011, 2011), the binder was 500 g in total, and the percent of fly ash changed from 40% to 80%. Concretely, the content of fly ash was 200, 250, 300, 350, and 400 g, respectively. Test results are presented in Figure 1. With the increasing content of fly ash, the water requirement of normal consistency reduced linearly, while the setting time was directly elongated. When the content of fly ash was 40%, the water requirement of normal consistency decreased by 7.7%, the initial setting time increased by 10.1%, and the final setting time increased by 4.1%. After that, with the content of fly ash increased by 10%, the water requirement of normal consistency decreased by about 1.5%, and the initial and final setting time increased by about 9.4% and 13.4%. This indicates that the flow friction of cement grains was decreased by the fly ash with a smooth surface of spherical particles, and the hydration process of cement was reduced by the dilution of fly ash with lesser cement. In fact, the hydration process of cement controls the setting time of binder paste; the reaction of fly ash with cement hydration product Ca(OH)2 is a little bit in the early age (Li et al., 2013; Li et al., 2021). This indicates that the replacement of cement by excessive content of fly ash is applicable to maintain the workability of fresh cement fly-ash mortar with content over 40% of fly ash.
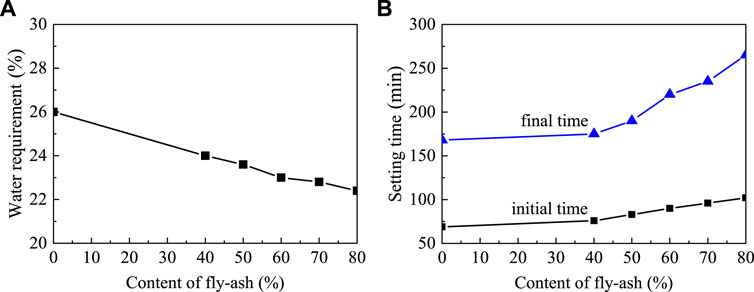
FIGURE 1. Test results of cement fly-ash paste: (A) water requirement of normal consistency; (B) setting time.
Strength of cement fly-ash mortar
The cement fly-ash mortar was designed referencing to the specifications for the determination of cement strength and the strength activity index of fly ash in China codes (GB/T1596-2017, 2017; GB/T17671-2020, 2020); the dosage of the binder was 450 kg/m3; the water-to-binder ratio was 0.3, 0.4, and 0.5, respectively, and the content of fly ash in weight of total binders changed from zero to 80%. Based on the test method of China codes (JGJ/T70-2009, 2009), the flowability of the test mortars was within 170–220, 180–220, and 210–280 mm with the change of the water-to-binder ratio. The compressive and flexural strengths were measured on a cement mortar testing machine with specimens of 40 mm × 40 mm × 160 mm at the curing age of 7 and 28 days. For each test, three specimens were made as a group. Test results are presented in Figure 2.
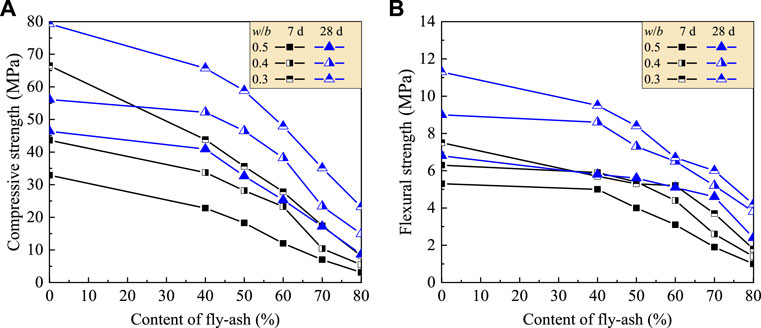
FIGURE 2. Changes in strength with content of fly ash: (A) compressive strength; (B) flexural strength.
The influence of fly ash on the strength of mortar was related to the water-to-binder ratio and the curing age in a complex relationship. At a lower water-to-binder ratio, the compressive strength and flexural strength decreased rapidly with the increasing content of fly ash, while the decrease at the early age of 7 days was larger than that at the age of 28 days. In the case of the cement fly-ash mortar with the content of fly ash at 40% and the water-to-binder ratio of 0.40, the compressive and flexural strengths decreased by 6.9% and 4.4% at the curing age of 28 days, although a relatively large decrease took place at the curing age of 7 days. Comparatively, the compressive strength decreased by 11.9% and 17.2%, and the flexural strength decreased by 14.7% and 15.9% at the curing age of 28 days when the water-to-binder ratio was 0.30 and 0.50, respectively. When the content of fly ash was over 40%, the compressive and flexural strengths tended to be decreased fast. With the content of fly ash changing from 50% to 60%, the compressive strength of mortar at the curing age of 28 days decreased by 25.8%–39.6%, 17.1%–31.9%, and 29.7%–45.4%, while the flexural strength decreased by 25.6%–40.7%, 18.9%–27.8%, and 17.6–25.0%, corresponding to the water-to-cement ratios of 0.3, 0.4, and 0.5. Therefore, in this test, the water-to-binder ratio of 0.40 was optimal, and the content of fly ash at 40% was almost the boundary to produce the mortar with less decrease in strength. To further improve the strength of cement fly-ash mortar with large content of fly ash over 40%, other measures should be adopted to excite the activity of fly ash in mortar.
Activity excitation of fly ash by calcium hydroxide and steam curing
A test for the pozzolanic activity of fly ash excited by calcium hydroxide Ca(OH)2 and steam curing was designed referencing to the specifications of China codes (GB/T1596-2017, 2017; GB/T17671-2020, 2020). The water-to-binder ratio was selected as 0.4 based on the above experiment, and the content of fly ash changed from zero to 80%. The content of Ca(OH)2 was 25.8% by weight of the binder based on the study reported (Gunasekara et al., 2016; Gunasekera et al., 2017); the compressive strength of the test mortar was measured on a testing machine with the specimens of 40 mm × 40 mm × 160 mm at the curing age of 7 and 28 days. Each test had three specimens as a group. For specimens by steam curing, they were steam cured at a temperature of 80°C and relative humidity of 95% for 24 h and then cured at standard curing room before testing (Mei et al., 2018; Yang et al., 2021). The comparisons of compressive strength of the test mortar with or without Ca(OH)2 excitation and those with Ca(OH) excitation at different curing conditions are presented in Figure 3.
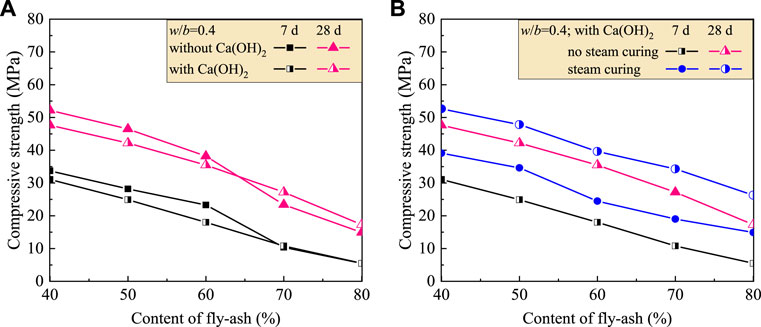
FIGURE 3. Comparisons for the changes of compressive strength of test mortars: (A) with and without Ca(OH)2 excitation; (B) cured in different conditions.
No obvious excitation of Ca(OH)2 appeared on the strength of the cement fly-ash mortar. This indicates that the reaction of fly ash with Ca(OH)2 was a slow process although the concentration of Ca(OH)2 was increased by the addition (Wu and Lian, 1999; Li et al., 2014). When the content of fly ash was over 60%, less content of Ca(OH)2 was produced by the hydration of cement. The excitation effect of additional Ca(OH)2 began to present to make the cement fly-ash mortar reach about 16% higher compressive strength.
Because the solubility of Ca(OH)2 increases obviously with the rise in temperature (Hefni et al., 2018; Singh and Subramaniam, 2019), and the solubility of silica increased by about one-third when exposed to water vapor (Iler, 1979), the reaction of fly ash with Ca(OH)2 can be excited by steam curing at the start. This leads to a rapid reaction between silica and calcium hydroxide or calcium silicates and promotes the subsequent formation of hydrated calcium silicate. Finally, the reactions benefit the mechanical properties of the mortar after steam curing. When the content of fly ash was no larger than 60%, the compressive strength of the mortar increased by about 33% at the early age of 7 days and by about 12% at the age of 28 days. When the content of fly ash was larger than 60%, the compressive strength of the mortar increased by about 123% at the early age of 7 days and by about 39% at the age of 28 days. This indicates that the excitation effect of steam curing at the start contributed much more on the early strength of the mortar and tended obviously with the increasing content of fly ash especially higher than 60%.
Tests for FAC
Mix proportion
With reference to the specification of the China code (JGJ 55-2011, 2011), the mix proportion of FAC was designed by the method of absolute volume of concrete. The reference mix was designed with the basic content of fly ash corresponding to the water-to-binder ratio w/b of 0.30, 0.34, 0.42, and 0.50, respectively. The excessive weight of fly ash was selected as 10%, 20%, and 30% of the basic content, and all the binders were counted in the w/b (Li et al., 2012; Liu et al., 2013a). The results of the mix proportion of FAC are presented in Table 4. Four groups of FAC were produced for tests. The content of fly ash changed from 51.9% to 60.2%, and the w/b varied from 0.26 to 0.50.
Workability of fresh FAC
Tests for fresh FAC were carried out according to the specification of the China code (GB/T 50080-2002, 2002). Good workability presented with the slump of concrete in 50–95 mm and the water retention without separation of aggregates from paste. This coincides with the test results of the properties of fresh cement fly-ash paste and ensures the workability of FAC, with a lower water-to-binder ratio.
Mechanical properties of FAC
Tests for the basic mechanical properties of FAC were carried out in accordance with the China code (GB/T 50081-2002, 2002). The cubic specimens with a dimension of 100 mm were cast for the cubic compressive strength and splitting tensile strength; the prism specimens of 100 mm × 100 mm × 300 mm were cast for the axial compressive strength and the modulus of elasticity. For each test, three specimens were made as a group. The test results of compressive strength for specimens cured at standard curing room for 7, 28, and 56 days are presented in Table 5. On the test data, the strength ratio in each group of the FAC with excessive fly ash to the FAC with basic content of fly ash is computed and presented in Figure 4.
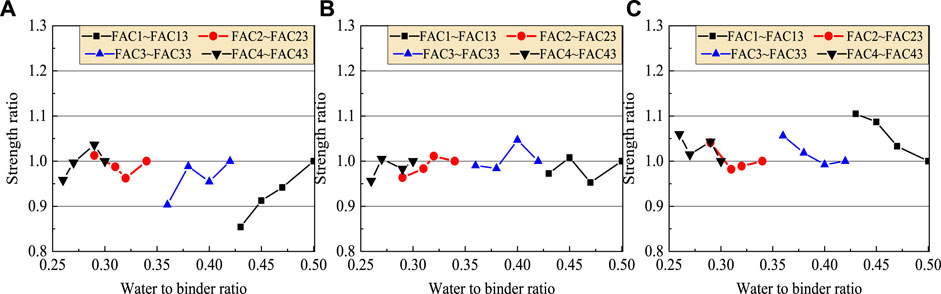
FIGURE 4. Changes of the strength ratio with the water-to-binder ratio at the curing age of (A) 7 days; (B) 28 days; and (C) 56 days.
The effect of excessive fly ash on the strength of FAC was obvious with the increasing water-to-binder ratio at the early curing age of 7 days. The compressive strength of the four groups of FAC reduced in maximum by 4.2%, 3.8%, 9.7%, and 14.6%, respectively. With the time going on, the negative effect of fly ash became weaker and weaker with the increased excessive fly ash. At the curing age of 28 days, the negative effect basically disappeared with the strength ratio in the same group changing from 0.953 to 1.046. At the curing age of 56 days, the positive effect was remarkable especially for the FAC with the w/b = 0.42 and 0.50 with the strength ratio ranging from 0.82 to 1.105. This reflects the long-term hydration process of fly ash which reacted with the hydration product Ca(OH)2 to form the calcium silicate hydrate gel (Wu and Lian, 1999; Li et al., 2014). With a higher water-to-binder ratio and less cement content of 125–140 kg/m3, the hydration of cement is slowed down by the lower temperature rise with the increasing content of fly ash. This needs a long-term development of strength with the hydration of cement (Li et al., 2014; Hefni et al., 2018; Anjos et al., 2020). Finally, a higher increment of strength is gained with sufficient hydration of fly ash (Ding et al., 2016; Zhao et al., 2017). Meanwhile, the compactness of FAC can be further increased by the filling of tiny grains of excessive fly ash (Li et al., 2014). Therefore, by using the excessive fly ash to reduce the water-to-binder ratio, the compressive strength of FAC can reach the target at the standard curing age of 28 days.
According to the China code (JGJ 55-2011, 2011), the cubic compressive strength of FAC at the curing age of 28 days reached 24.3–41.2 MPa, which corresponds to the strength grades of C15 to C30. The cubic compressive strength of FAC at the curing age of 56 days reached 33.4–56.8 MPa, which corresponds to the strength grades of C20 to C45. Therefore, if the structure is not subject to early loads except weight itself, the strength of FAC can be controlled at a longer curing age such as 56 days to obtain the economic benefit of fly-ash utilization.
To explore the effect of curing relative humidity (RH) on the strength of FAC, three FACs FAC1, FAC22, and FAC4 were cured at curing RH of 40%, 60%, and 95%. The test results of cubic compressive strength at 7 and 28 days are presented in Table 6. Due to sufficient supply of water for the hydration at the early age of 7 days, the FACs cured at lower RH got higher strength than those cured at RH of 95%; however, the increment was below 10.9% and tended to decrease with the decreasing water-to-binder ratio. With the curing time going on, the curing RH needed to be increased not less than 60% due to the needs of humidity condition for hydration to get the higher strength of FAC. Therefore, it is better to adjust the curing RH in stages, combined with the water-to-binder ratio of FAC.
As specified in the China code (GB 50010-2010, 2010), the cubic compressive strength is used for the express of strength grade, axial compressive strength, splitting tensile strength, and modulus of elasticity used for structural design which should be converted from the cubic compressive strength. Therefore, the above three FACs were also tested for the basic mechanical properties. The curing age of specimens was 7, 28, and 56 days, respectively, before testing. The results are presented in Table 7. This indicates a fast development of the basic mechanical properties of FAC before the curing age of 28 days, after which the increases become slow (Sivasundaram et al., 1990; Ding et al., 2016; Zhao et al., 2017). For the conversion, test data presented in Tables 5, 7 should successively multiply the coefficients of 0.95, 0.95, and 0.85 corresponding to standard specimens with sectional dimensions of 150 mm (GB/T 50081-2002, 2002).
Based on the relationship of the conventional concrete, a direct proportion exists between axial compressive strength and cubic compressive strength; the tensile strength (ft) and the modulus of elasticity (Ec) of FACs at the curing age of 28 days in this study can be calculated with following formulas. The ratio of the test to calculated results is presented in Figure 5A).
where fcu is the cubic compressive strength of concrete (MPa).
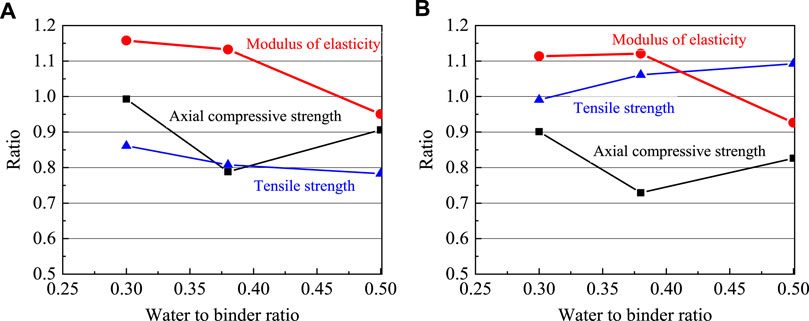
FIGURE 5. Ratios of test to computed results for the mechanical properties at the curing age of (A) 28 days and (B) 56 days.
The ratio of axial compressive strength to cubic compressive strength varies from 0.788 to 0.992, which is higher than the coefficient of 0.76 for conventional concrete at the curing age of 28 days. Meanwhile, the ratio of tensile strength varies from 0.783 to 0.861, and the ratio of the modulus of elasticity varies from 0.951 to 1.158. Therefore, FAC has a higher axial compressive strength, a lower tensile strength, and an almost equal modulus of elasticity compared to conventional concrete with the same strength grade. This is different from the fact that the FAC with content of fly ash no larger than 40% has equal tensile strength to conventional concrete (Liu et al., 2013b).
Making the above analyses on the FACs at the curing age of 56 days, the ratios are presented in Figure 5B. The ratio of axial compressive strength to cubic compressive strength varies from 0.729 to 0.901, the ratio of tensile strength varies from 0.991 to 1.093, and the ratio of modulus of elasticity varies from 0.926 to 1.121. This shows a higher adaptability of the above relationships for the FAC at the curing age of 56 days. The changes in ratios reflect the changes in FAC microstructure with the increasing curing age. The FAC behaves better in compression due to the tiny aggregate effect of fly ash on the microstructure of FAC with refined pores and dense texture, while the splitting tensile strength of FAC mainly relies on the calcium silicate hydrate gel that came from the hydration of cement and the continuous hydration of fly ash. This depends much more on the hydration process with the increasing curing age (Sivasundaram et al., 1990; Ding et al., 2016).
Resistance to chloride-ion penetration of FAC
The electric flux test was carried out for the chloride ion penetration of FAC in accordance with the China code (GB 50082-2009, 2009), which is similar to the test method specified in ASTM C1202-19 (2019). The samples of ϕ100 mm × 50 mm were cut from the specimen of ϕ100 mm × 200 mm. The specimens were cured at standard curing room for 56 days before testing. Each test had three specimens as a group. The measured total electric flux (Q100) was converted to be the value (Qs) of a standard sample with diameter of 95 mm. Three FACs identified in Table 4 as FAC1, FAC22, and FAC4 were tested, and the test results of Qs are 821 C, 516 C, and 413 C, successively. This indicates that the resistance of the test FAC to chloride penetration was basically positive to the water-to-binder ratio and the strength of FAC.
According to the China code for durability assessment of concrete (JGJ/T 193-2009, 2009), the grade of resistance to chloride penetration of test FACs belongs to Q-IV with the Qs of 1,000–500 C. Therefore, the test FACs are good at resisting the penetration of chloride ion. In view that the cubic compressive strength of test FACs was only 15.2–30.8 MPa, the high-level resistance to chloride ion penetration came mainly from the admixing of large content of fly ash. The pores of concrete are filled with tiny particles of fly ash and refined by the reaction of fly ash with the hydration product Ca(OH)2; a denser microstructure forms to block the osmotic path of chloride ion (Wu and Lian, 1999; Li et al., 2014). This lets chloride ion penetration in FAC to be at a very low level.
Carbonization of FAC
The fast carbonization test was carried out for the carbonization of FAC in accordance with the China code (GB 50082-2009, 2009). The cubic specimens with the dimension of 150 mm were cured at standard curing room for 56 days before testing in the carbonization chamber. The chamber was operated with the concentration of CO2 at (20
The FACs used for the carbonization test were the same as those used for the chloride ion penetration test. The carbonized depth was 7.3, 3.2, and 0.4 mm for the three FACs identified as FAC1, FAC22, and FAC4, successively. This indicates that the carbonized depth decreased obviously with the decreasing water-to-binder ratio, due to the dense microstructure of FAC which blocks the diffusion of CO2 (Wu and Lian, 1999; Zhao et al., 2013). According to the specification of the China code for the durability assessment of concrete (JGJ/T 193-2009, 2009), the resistance of test FACs to carbonization belonged to T-IV with 10–0.1 mm of the carbonized depth. This is a very high level of the resistance of concrete to carbonization.
Conclusion
1) The water requirement of normal consistency decreased, and the setting time elongated with the increase in fly-ash content in cement fly-ash paste. This provides a good flowability of building mortar and FAC with large content of fly ash.
2) The optimal content of fly ash for mortar was related to the water-to-binder ratio. In the case of the mortar with a water-to-binder ratio of 0.40 and the content of fly ash at 40%, the compressive and flexural strengths decreased by 6.9% and 4.4% at the curing age of 28 days. When the content of fly ash was over 40%, the decrease in the compressive and flexural strengths tended to be fast. The decrease in the water-to-binder ratio benefited to the contribution of pozzolanic activity of fly ash to the strength of mortar.
3) There was no excitation of Ca(OH)2 on the early strength of the mortar with large content of fly ash, except for the less increase in the strength of the ones with fly ash over 60% at the curing age of 28 days. Steam curing for 24 h at the start presented the strengthening effect on the compressive strength of the mortar at the curing age of 7 and 28 days.
4) The mix proportion of FAC with large content of fly ash over 50% can be reasonably designed by the absolute volume method with excessive fly ash. With the increase in the water-to-binder ratio, it seems reasonable to adjust the curing RH from low to high with the increased curing age to ensure the hydration of cement and fly ash at a proper wet environment.
5) A higher decrease in cubic compressive strength of FAC took place at the curing age of 7 days. The cubic compressive strength of FAC maintained closely with the increase in fly ash content at the curing age of 28 days and tended to increase with the increase in fly-ash content at the curing age of 56 days. The strength grade of FAC at the curing age of 56 days can be raised to one to three grades over that at the curing age of 28 days. The relationships of axial compressive strength, tensile strength, and modulus of elasticity with cubic compressive strength of FAC at the curing age of 56 days are similar to those of conventional concrete at the curing age of 28 days. Therefore, it is more reasonable to evaluate the strength of FAC at the curing age of 56 days.
6) FAC with large content of fly ash from 51.9% to 57.6% presented super resistances to chloride ion penetration and carbonization. The resistances increased with the decrease in the water-to-binder ratio and reached a very high level of current specifications.
Data availability statement
The original contributions presented in the study are included in the article/supplementary material; further inquiries can be directed to the corresponding authors.
Author contributions
CL, BS, and FL contributed to the methodology, writing of the review, and funding acquisition; HG, SZ, and MD were involved in the tests, data interpretation, and writing of the original draft.
Funding
This research was funded by the Henan Provincial Special Project of Key Sci-Tech Research and Development Promotion, China (grant number 202102310272); Attracting Foreign Talents Fund of Henan, China (grant number YWZ 2018-6-HS2); and Innovative Sci-Tech Team of Eco-building Material and Structural Engineering of Henan Province, China (grant number YKRZ-6-066).
Conflict of Interest
Author BS was employed by the company Henan Fifth Construction Group.
The remaining authors declare that the research was conducted in the absence of any commercial or financial relationships that could be construed as a potential conflict of interest.
Publisher’s Note
All claims expressed in this article are solely those of the authors and do not necessarily represent those of their affiliated organizations, or those of the publisher, the editors and the reviewers. Any product that may be evaluated in this article, or claim that may be made by its manufacturer, is not guaranteed or endorsed by the publisher.
Acknowledgments
Thanks are given to the supervision of Dr. David W. Law at RMIT University, Australia.
References
Amran, M., Debbarma, S., and Ozbakkaloglu, T. (2021). Fly Ash-Based Eco-Friendly Geopolymer concrete: a Critical Review of the Long-Term Durability Properties. Construction Building Mater. 270, 121857. doi:10.1016/j.conbuildmat.2020.121857
Anjos, M. A. S., Camões, A., Campos, P., Azeredo, G. A., and Ferreira, R. L. S. (2020). Effect of High Volume Fly Ash and Metakaolin with and without Hydrated Lime on the Properties of Self-Compacting concrete. J. Building Eng. 27, 100985. doi:10.1016/j.jobe.2019.100985
Aruhan, , and Yan, P. Y. (2011). Carbonation Characteristics of concrete with Different Fly-Ash Contents. J. Chin. Ceram. Soci. 39 (1), 7–12. doi:10.14062/j.issn.0454-5648.2011.01.022
ASTM C1202-19 (2019). Standard Test Method for Electrical Indication of Concrete’s Ability to Resist Chloride Ion Penetration. West Conshohocken, PA, USA: ASTM International.
Choi, Y., Park, M., Choi, B., and Oh, S. A. (2015). Study on the Evaluation of Field Application of High-Fluidity concrete Containing High Volume Fly Ash. Adv. Mater. Sci. Eng., 507018. doi:10.1155/2015/507018
Ding, X., Li, C., Xu, Y., Li, F., and Zhao, S. (2016). Experimental Study on Long-Term Compressive Strength of concrete with Manufactured Sand. Construction Building Mater. 108, 67–73. doi:10.1016/j.conbuildmat.2016.01.028
Ding, X., Zhao, M., Li, J., Shang, P., and Li, C. (2020). Mix Proportion Design of Self-Compacting SFRC with Manufactured Sand Based on the Steel Fiber Aggregate Skeleton Packing Test. Materials 13, 2833. doi:10.3390/ma13122833
GB 50082-2009 (2009). Standard for Test Methods of Long-Term Performance and Durability of Ordinary Concrete. Beijing, China: China Building Industry Press.
GB 50010-2010 (2010). Code for Design of Concrete Structures Beijing, China: China Building Industry Press.
GB/T 1346-2011 (2011). Test Methods for Water Requirement of Normal Consistency, Setting Time and Soundness of the Portland Cement. Beijing, China: China Standard Press.
GB/T 14685-2011 (2011). Pebble and Crushed Stone for Construction. Beijing, China: China Standard Press.
GB/T 176-2017 (2017). in Cement - Test Methods -Part 1: Analysis by Wet Chemistry, NEQ) (Beijing, China: China Standard Press).Methods for Chemical Analysis of Cement (ISO29581-1:2009
GB/T 17671-2020 (2020). Methods of Testing Cements: Determination of Strength (ISO679:2009 Cement Test Methods- Determination of Strength, MOD). Beijing, China: China Standard Press.
GB/T 50080-2002 (2002). Standard for Test Methods on Performance of Ordinary Fresh Concrete. Beijing, China: China Building Industry Press.
GB/T 50081-2002 (2002). Standard for Test Methods on Mechanical Properties of Ordinary Concrete. Beijing, China: China Building Industry Press.
GB/T 50164-2014 (2014). Technique Code for Application of Fly Ash Concrete. Beijing, China: China Standard Press.
Gunasekara, C., Law, D. W., and Setunge, S. (2016). Long Term Permeation Properties of Different Fly Ash Geopolymer Concretes. Construction Building Mater. 124, 352–362. doi:10.1016/j.conbuildmat.2016.07.121
Gunasekera, C., Setunge, S., and Law, D. W. (2017). Correlations between Mechanical Properties of Low-Calcium Fly Ash Geopolymer Concretes. J. Mater. Civ. Eng. 29 (9), 04017111. doi:10.1061/(asce)mt.1943-5533.0001916
Hefni, Y., Zaher, Y. A. E., and Wahab, M. A. (2018). Influence of Activation of Fly Ash on the Mechanical Properties of concrete. Construction Building Mater. 172, 728–734. doi:10.1016/j.conbuildmat.2018.04.021
Iler, R. K. (1979). The Chemistry of Silica: Solubility, Polymerization, Colloid and Surface Properties, and Biochemistry. New York: John Wiley & Sons.
JGJ 55-2011 (2011). Specification for Mix Proportion Design of Ordinary Concrete. Beijing, China: China Building Industry Press.
JGJ/T 193-2009 (2009). Standard for Inspection and Assessment of Concrete Durability. Beijing, China: China Building Industry Press.
JGJ/T 281-2012 (2012). Technique Specification for Application of High Strength Concrete. Beijing, China: China Building Industry Press.
JGJ/T 70-2009 (2009). Standard for Test Method of Performance on Building Mortar. Beijing, China: China Building Industry Press.
Li, C. Y., Jiang, L., Liu, Y., and Xu, Z. M. (2013). Experimental Study on Activity of Fly Ash Replacing Cement in concrete. Amm 438-439, 46–49. doi:10.4028/www.scientific.net/amm.438-439.46
Li, C., Zhang, X., Zhang, B., Tan, Y., and Li, F. (2021). Reuse of Sintered Sludge from Municipal Sewage Treatment Plants for the Production of Lightweight Aggregate Building Mortar. Crystals 11, 999. doi:10.3390/cryst11080999
Li, F. L., Liu, C. ., Pan, L. Y., and Li, C. Y. (2014). Manufactured Sand Concrete. Beijing, China: China Waterpower Press.
Li, F. L., Zeng, Y., and Li, C. Y. (2012). Review of Mix Proportion Design Methods for Fly Ash concrete with Machine-Made Sand. Adv. Mater. Res. 418-420, 441–444.
Liu, C. J., Jia, C. Y., and Li, C. Y. (2013a). Evaluation of Relations Among Basic Mechanical Properties of Fly-Ash Concrete with Machine-Made Sand. Amm 438-439, 15–19. doi:10.4028/www.scientific.net/amm.438-439.15
Liu, C. J., Xu, Y. Y., and Zhang, X. Y. (2013b). Study on Durability of concrete with Machine-Made Sand Part I: Time-dependent Chloride Penetration. Amm 438-439, 3–9. doi:10.4028/www.scientific.net/amm.438-439.3
Liu, S., Zhu, M., Ding, X., Ren, Z., Zhao, S., Zhao, M., et al. (2021). High-Durability Concrete with Supplementary Cementitious Admixtures Used in Corrosive Environments. Crystals 11 (2), 196. doi:10.3390/cryst11020196
Ma, J., Wang, D., Zhao, S., Duan, P., and Yang, S. (2021). Influence of Particle Morphology of Ground Fly Ash on the Fluidity and Strength of Cement Paste. Materials 14 (2), 283. doi:10.3390/ma14020283
Malhotra, V. M., and Painter, K. E. (1989). Early-age Strength Properties, and Freezing and Thawing Resistance of concrete Incorporating High Volumes of ASTM Class F Fly Ash. Int. J. Cement Composites Lightweight Concrete 11 (1), 37–46. doi:10.1016/0262-5075(89)90034-1
Mei, J., Ma, B., Tan, H., Li, H., Liu, X., Jiang, W., et al. (2018). Influence of Steam Curing and Nano Silica on Hydration and Microstructure Characteristics of High Volume Fly Ash Cement System. Construction Building Mater. 171, 83–95. doi:10.1016/j.conbuildmat.2018.03.056
Nežerka, V., Bílý, P., Hrbek, V., and Fládr, J. (2019). Impact of Silica Fume, Fly Ash, and Metakaolin on the Thickness and Strength of the ITZ in concrete. Cem. Concr. Compos. 103, 252–262. doi:10.1016/j.cemconcomp.2019.05.012
Olivia, M., Wibisono, G., and Saputra, E. (2019). Early Strength of Various Fly Ash Based concrete in Peat Environment. MATEC Web Conf. 276, 01022. doi:10.1051/matecconf/201927601022
Promsawat, P., Chatveera, B., Sua-iam, G., and Makul, N. (2020). Properties of Self-Compacting concrete Prepared with Ternary Portland Cement-High Volume Fly Ash-Calcium Carbonate Blends. Case Stud. Construction Mater. 13, e00426. doi:10.1016/j.cscm.2020.e00426
Singh, G. V. P. B., and Subramaniam, K. V. L. (2019). Influence of Processing Temperature on the Reaction Product and Strength Gain in Alkali-Activated Fly Ash. Cement and Concrete Composites 95, 10–18. doi:10.1016/j.cemconcomp.2018.10.010
Sivasundaram, V., Carette, G. G., and Malhotra, V. M. (1990). Long-term Strength Development of High-Volume Fly Ash concrete. Cement and Concrete Composites 12 (4), 263–270. doi:10.1016/0958-9465(90)90005-i
Solikin, M., and Setiawan, B. (2017). The Effects of Design Strength, Fly Ash Content and Curing Method on Compressive Strength of High Volume Fly Ash concrete: a Design of Experimental. MATEC Web Conf. 103, 01003. doi:10.1051/matecconf/201710301003
Sun, G. W., Tang, Q. Q., Zhang, L. J., and Wang, C. H. (2019a). Early Activation Effect and Mechanism of High Volume Fly Ash. J. Harbin Eng. Univ. 40 (3), 540–547. doi:10.11990/jheu.201711102
Sun, J., Shen, X., Tan, G., and Tanner, J. E. (2019b). Compressive Strength and Hydration Characteristics of High-Volume Fly Ash concrete Prepared from Fly Ash. J. Therm. Anal. Calorim. 136, 565–580. doi:10.1007/s10973-018-7578-z
Thiyagarajan, H., Mapa, M., and Kushwaha, R. (2018). Investigation on the Rheological Behavior of Fly Ash Cement Composites at Paste and concrete Level. J. Inst. Eng. India Ser. A. 99 (2), 295–301. doi:10.1007/s40030-018-0284-9
Wardhono, A. (2021). Flowability and Strength Properties of High Volume of Fly Ash Material on Self-Compacting concrete. J. Phys. Conf. Ser. 1747, 012033. doi:10.1088/1742-6596/1747/1/012033
Yang, J., Hu, H., He, X., Su, Y., Wang, Y., Tan, H., et al. (2021). Effect of Steam Curing on Compressive Strength and Microstructure of High Volume Ultrafine Fly Ash Cement Mortar. Construction Building Mater. 266, 120894. doi:10.1016/j.conbuildmat.2020.120894
Yu, J., Lu, C., Leung, C. K. Y., and Li, G. (2017). Mechanical Properties of green Structural concrete with Ultrahigh-Volume Fly Ash. Construction Building Mater. 147, 510–518. doi:10.1016/j.conbuildmat.2017.04.188
Zhao, M., Zhao, M., Chen, M., Li, J., and Law, D. (2018). An Experimental Study on Strength and Toughness of Steel Fiber Reinforced Expanded-Shale Lightweight concrete. Construction Building Mater. 183, 493–501. doi:10.1016/j.conbuildmat.2018.06.178
Zhao, S. B., Li, Y. T., and Xu, Y. Y. (2013). Study on Durability of concrete with Machine-Made Sand Part II: Long-Term Carbonization. Amm 438-439, 10–14. doi:10.4028/www.scientific.net/amm.438-439.10
Keywords: concrete with large content of fly-ash, activity of fly-ash, mechanical property, strength development, chloride ion penetration, carbonization
Citation: Li C, Geng H, Zhou S, Dai M, Sun B and Li F (2022) Experimental Study on Preparation and Performance of Concrete With Large Content of Fly Ash. Front. Mater. 8:764820. doi: 10.3389/fmats.2021.764820
Received: 26 August 2021; Accepted: 26 November 2021;
Published: 06 January 2022.
Edited by:
Xijun Shi, Texas State University, United StatesReviewed by:
Ionut Ovidiu Toma, Gheorghe Asachi Technical University of Iași, RomaniaJiaqing Wang, Nanjing Forestry University, China
Copyright © 2022 Li, Geng, Zhou, Dai, Sun and Li. This is an open-access article distributed under the terms of the Creative Commons Attribution License (CC BY). The use, distribution or reproduction in other forums is permitted, provided the original author(s) and the copyright owner(s) are credited and that the original publication in this journal is cited, in accordance with accepted academic practice. No use, distribution or reproduction is permitted which does not comply with these terms.
*Correspondence: Changyong Li, lichang@ncwu.edu.cn; Fenglan Li, lifl64@ncwu.edu.cn