- 1Environmental Science and Sustainability Program, Harrisburg University of Science and Technology, Harrisburg, PA, United States
- 2Northeast Center to Advance Food Safety, University of Vermont Extension, Bennington, VT, United States
- 3Natural Resources Conservation Services, United States Department of Agriculture, Epping, NH, United States
- 4Civil and Environmental Engineering Department, University of New Hampshire, Durham, NH, United States
Coupled aquaponics is the integration of recirculating aquaculture systems (RAS) and hydroponic cropping systems (HCS) into one system with shared culture water. Water conservation, revenue diversification, location-independent food production, and a reduced reliance on synthetically derived fertilizer salts have been identified as potential benefits of coupled aquaponic production. Despite these potential benefits, it has been difficult for producers to achieve success at the commercial scale. This review discusses how traditional linear coupled aquaponic system designs are not suited for intensive production due to a lack of scalability and water flow rate optimization to meet the differing requirements for finfish, vegetables, and water treatment with practices commensurate with the individual RAS and HCS industries. An alternative design for intensive coupled aquaponics is presented that utilizes a parallel unit process approach for independent hydraulic retention time optimization of each system component. The production benefits and scaling opportunities for each of the primary components in an aquaponics system are discussed. A review of recently published coupled aquaponics literature demonstrates that a system utilizing a parallel unit process design can result in more intensive fish production and a greater nutrient supply for plant production, leading to the potential for greater economic and space use efficiency.
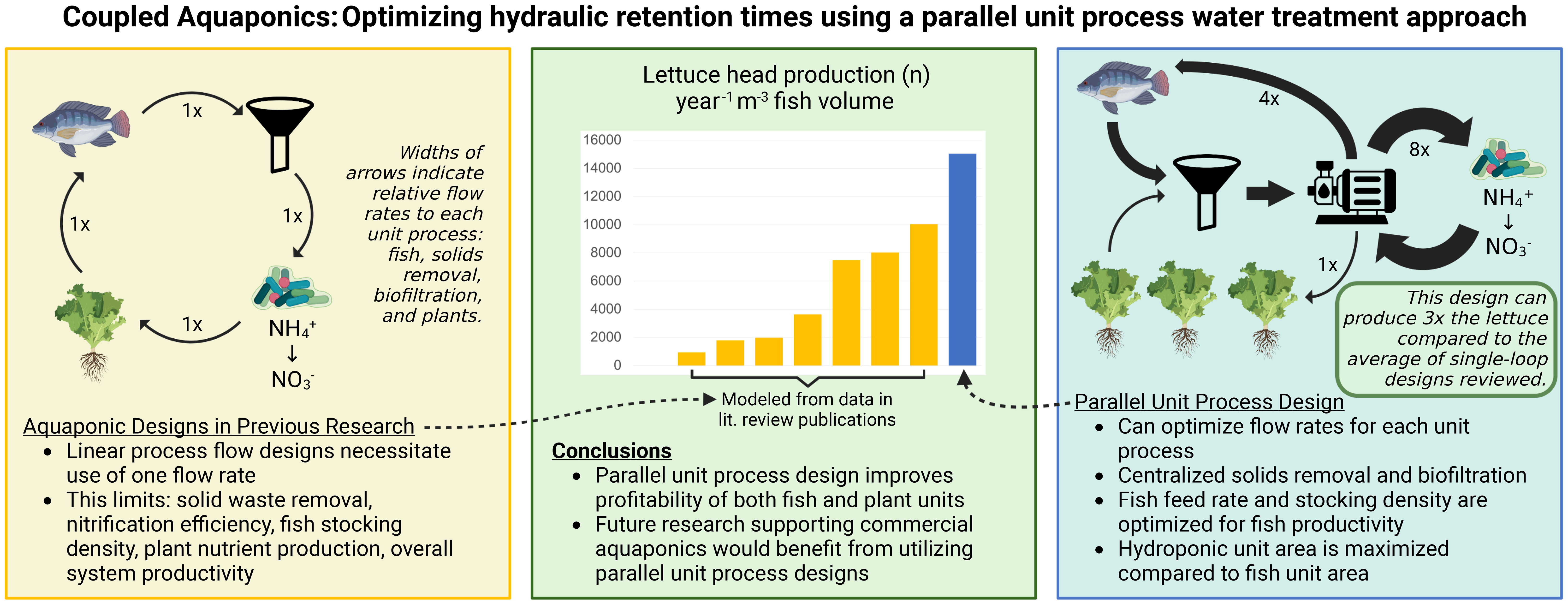
Graphical Abstract Created by Sean Fogarty, MS, with BioRender.com.
1 Introduction
Aquaponics is the integration of recirculating aquaculture systems (RAS) and hydroponic cropping systems (HCS) where dissolved nutrients in fish culture water are used to grow crops. Cited potential benefits of integrated production include increased revenue from the combination of fish and plant sales, minimized reliance on synthetically derived fertilizers, and both location-independent and season-independent protein and vegetable production in food deserts (Rakocy et al., 2006; Yep and Zheng, 2019). Aquaponic systems can be decoupled, where fish and plant production are independent and treated fish culture water is pumped from a RAS to a HCS without recirculation, or coupled, where fish and plant production units share water and water treatment systems (Goddek et al., 2016; Tetreault et al., 2021a). Since water does not flow back from the plant production systems to the RAS in decoupled systems, hydroponic crop culture water quality may be adjusted to meet plant needs and nutrients can be supplemented with synthetic solutions (Palm et al., 2018). While this separate optimization for fish and plant growth can achieve similar productivity to individual RAS and HCS, decoupled systems can require greater capital and maintenance costs, more physical space for separate water treatment units, and can be heavily supplemented—up to 49% of total nutrient mass—with synthetic fertilizers (Palm et al., 2018; Goddek et al., 2018).
The sharing of water treatment units in coupled systems requires water quality be maintained to balance both fish and plant health, which often results in diminished plant growth rates and fish stocking densities compared to decoupled systems (Goddek et al., 2019, pp. 163-201; Colt et al., 2021; Körner et al, 2021). The cited potential benefits of coupled production over decoupled include reduced capital costs, increased physical space for plants or fish, and the ability to grow plants without the addition of synthetic fertilizers and the environmental impacts associated with their use (Rakocy et al., 2006; Goddek et al., 2019, pp. 163-201; Yep and Zheng, 2019). Compared to the extensive research and economic success of RAS and HCS as standalone industries, commercial coupled aquaponics is relatively new and has struggled to find financial stability (Love et al., 2014; Goddek et al., 2015; Colt et al., 2021). In a recent grower survey, plant sales accounted for most of the generated revenue, fish production costs often exceeded fish related sales, and only 18-33% of aquaponic farms were profitable (Love et al., 2014; Love et al., 2015). Nutrient supply costs—primarily in the form of fish feed—can be identified as a barrier in commercial coupled aquaponic success. Fertilizer salts account for approximately 4% of total expenses for a typical commercial HCS (Souza et al., 2019; Turnšek et al., 2019). In contrast, the costs of nitrogen (N) and phosphorus (P) by mass are 7-14 times and 17-88 times more expensive, respectively, than synthetic salts when supplied solely by fish feed (Colt and Schuur, 2021). Therefore, a system that loses money from fish production and solely supplies plant nutrients with fish feed will struggle to become profitable. However, an integrated system with a profitable RAS can produce a naturally derived nutrient solution for vegetables that can further supplement income. A scalable design capable of intensive fish production could improve economic viability while maintaining the benefits of coupled production.
Many aquaponic growers develop their own system designs based on a linear process flow template derived from research conducted at the University of Virgin Islands (UVI) originally developed in the 1980s (Rakocy et al, 2006). As described in Rakocy et al. (2006), this UVI-based methodology utilizes a linear process flow to direct water from the fish production system in series with the plant system (Figure 1). Water and waste products flow from the fish rearing unit to a solid waste removal unit, then through biological filtration and hydroponic production units before returning the water to the fish rearing unit. While this linear flow effectively directs unused nutrients from the fish to the plants in small systems, the design lacks scalability to increase yield for greater economic viability due to limited control over water treatment processes to meet the specific requirements of crops and fish (Goddek et al., 2019, pp. 163-201).
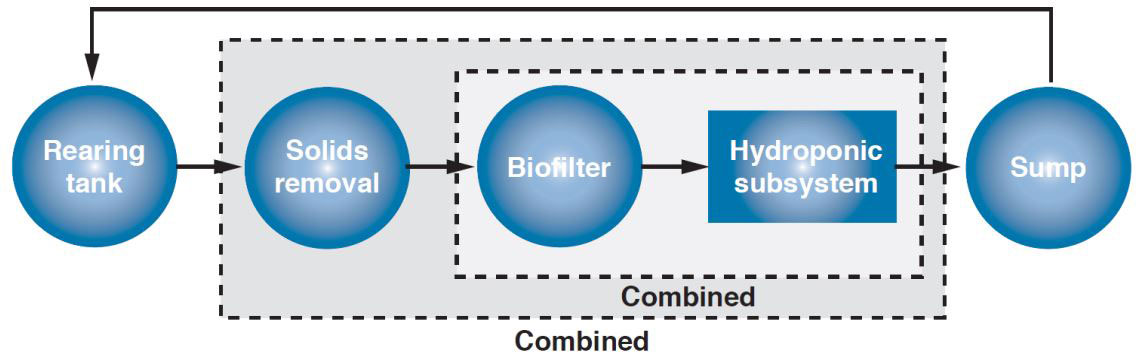
Figure 1 Primary components of common aquaponics design. Optimal layout as described by and retrieved from Rakocy et al. (2006) for a UVI-based aquaponic systems illustrating process flow where a linear stream of water gravity-flows at a constant rate from the rearing tank through all other units before draining into the sump for recirculation.
The concept of parallel plant and fish culture unit operation for water flow control, modeled after contemporary RAS designs, has been presented in recent literature when considering how to improve coupled aquaponics (Goddek et al., 2019, pp. 163-201; Palm et al., 2018). This parallel process allows hydraulic retention time (HRT) optimization for improved unit process performance and minimized pumping costs while still retaining the benefits of full integration at a larger scale. Despite this potential design improvement, much of the published coupled aquaponics research has still been conducted in systems with a linear flow and without metrics for direct comparison against individual RAS or HCS production (Baßmann et al., 2017; Knaus and Palm, 2017; Yang and Kim, 2020; Ani et al., 2022; Dusci et al., 2021) (Figure 2). Research on coupled aquaponics for commercial or intensive operations would benefit from adopting a parallel unit process design for more applicable results for farmers. This manuscript reviews recently published coupled aquaponics research and illustrates how a parallel unit process design provides the ability to maintain ideal HRTs in fish tanks, plant beds, and water treatment units. A mass balance of N using data from recently published work is used to demonstrate how a coupled system with appropriate water flow control can permit system scaling and greater fish stocking densities, fish feed rates, and nutrient production rates for plant use compared to linear flow systems.
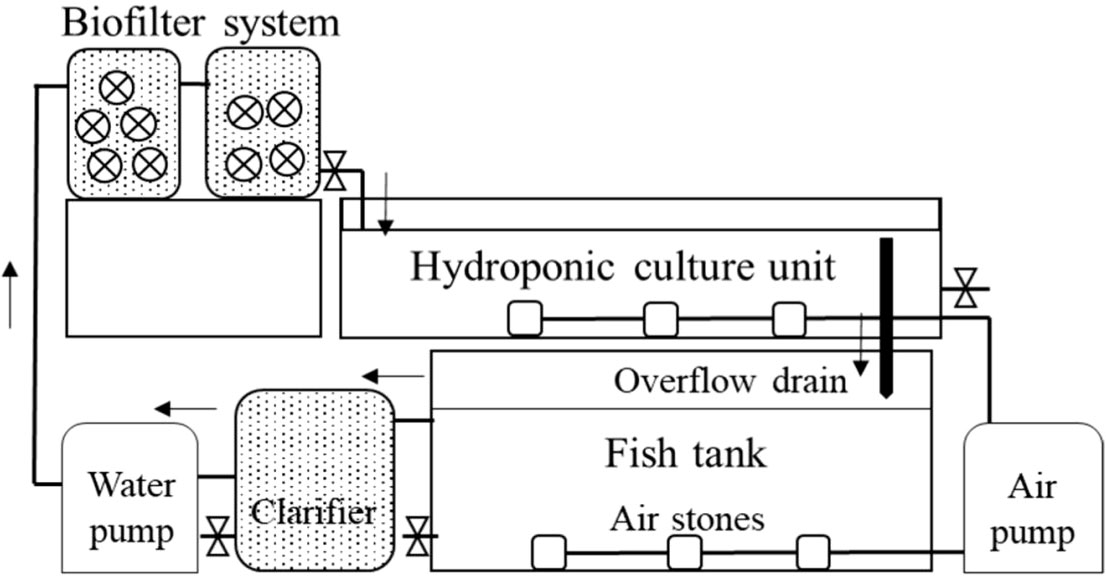
Figure 2 Detailed schematic of UVI-based research system. Flow schematic from Yang and Kim (2020) where research was conducted to determine the effect of 6-, 9-, and 17-hour hydroponic unit hydraulic retention times on water quality and fish and plant growth in small-scale systems. The system was comprised of a 0.37 m3 fish tank stocked at 20 kg/m3, 0.02 m3 clarifier, 0.04 m3 biofilter, and a 0.37 m3 deep water culture hydroponic unit.
2 HRT optimization in a parallel unit process design
Modern RAS utilize a unit process design where a complex system is divided into simpler functional units (primarily fish culture tanks, biofilters, and solids removal units) that can be individually maintained at specific HRTs for ideal operation (Losordo et al., 1999; Timmons et al., 2018). By using a parallel unit process approach, RAS are designed with each unit forming a separate loop with a single sump tank, which serves as a reservoir for treated water before being pumped individually back to each unit (Figure 3). Implementing the same unit process design for coupled aquaponics allows water flow rate to be optimized for nutrient loading, energy consumption, and physiological requirements to improve fish and crop production rates. The following subsections compare basic principles of aquaponic systems using a linear process flow and a RAS using a parallel unit process design. A parallel unit process design can more effectively meet the shared needs of fish and plants in coupled aquaponics compared to a linear flow. This manuscript is intended to illustrate and discuss the hydraulic optimization of different coupled aquaponic design methods and not to be used as a comprehensive guide for aquaponic or RAS design.
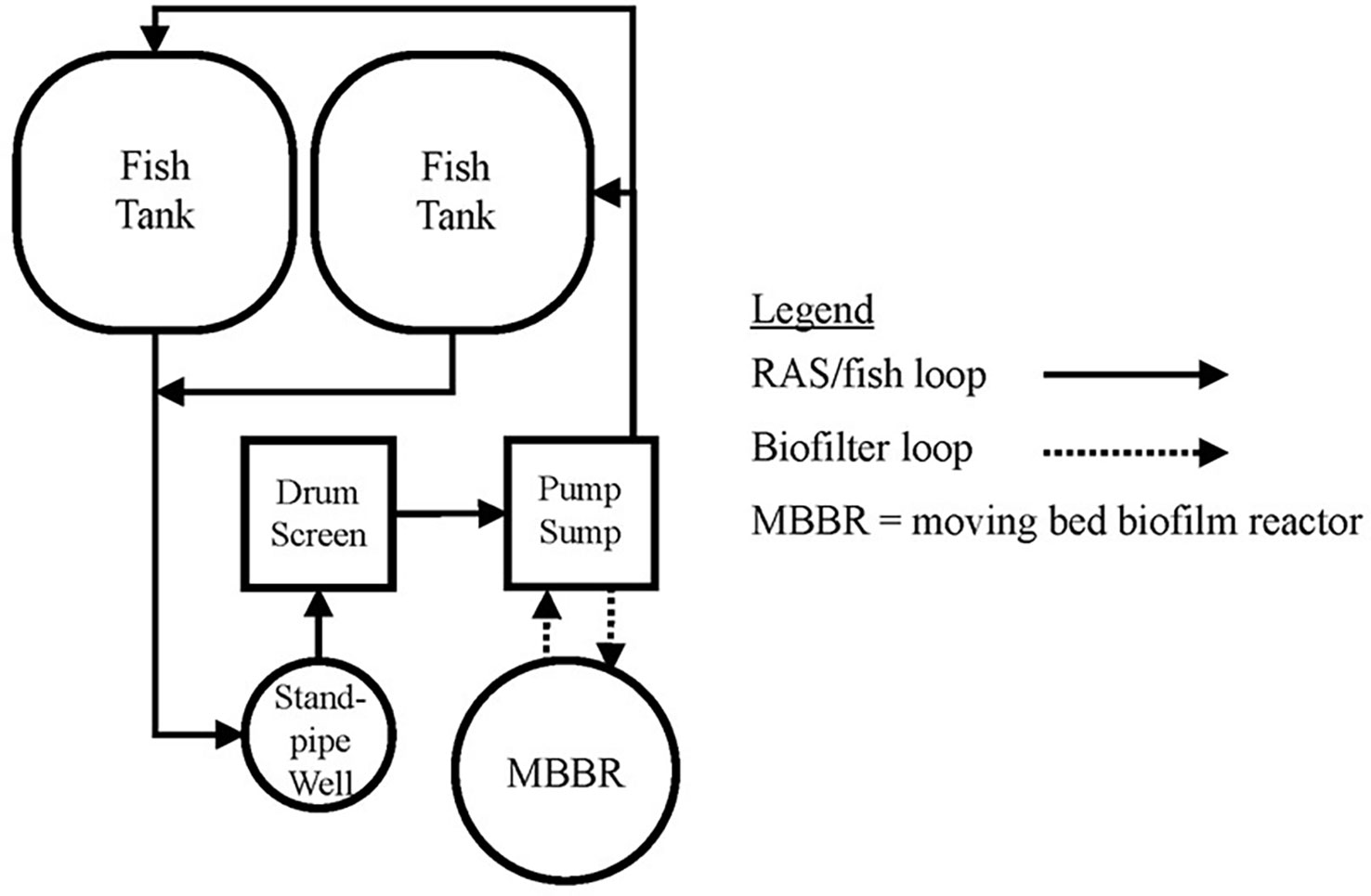
Figure 3 Typical RAS layout. This design utilizes a parallel unit process approach to allow independent operation of individual fish tanks and MBBR.
2.1 Fish culture tank design influences fish health and productivity
In RAS, round tanks with low HRTs and a vertical water inlet manifold spanning the entire tank depth provide a self-cleaning property by creating a circular water flow where waste is drawn to a center drain for rapid removal (Timmons et al., 1998; Losordo et al., 1999). The time required to fully pump and evacuate one equivalent tank water volume is described as the nominal HRT. The actual HRT of a tank may be influenced by a combination of flow rate, water inlet and outlet design, tank shape, and the tank diameter:depth ratio, and are typically greater than the nominal HRT. Precise inlet and outlet flow rate control is required to maintain water quality and the ideal HRT across fish life stages (Timmons et al., 1998; Davidson and Summerfelt, 2004). Water velocity is typically maintained from 0.5 – 2.0 fish body lengths second-1 to exercise fish and swirl waste to the center drain (Davison, 1997; Timmons et al., 2018, pp. 93-133). A recent survey of commercial RAS in Norway found that typical fish tank HRTs in systems built after 2010 were less than 60 minutes (Summerfelt et al., 2016). Systems with high culture tank HRTs can suffer from reduced dissolved oxygen (DO) concentrations, organic carbon (OC) accumulation from suspended solid waste, and toxic total ammoniacal nitrogen (TAN) accumulation (Timmons et al., 2018). Yang and Kim (2020) conducted a study to identify the ideal single hydraulic loading rate for all units in a linear system. The highest flow rate resulted in an estimated fish tank HRT of 2.78 hours. The authors acknowledged that such high fish tank HRTs may result in poor water quality in high density culture fish systems but were limited in fish tank control due to the 6 h HRT chosen to meet plant needs in the hydroponic unit, which resulted in a flow rate of 2-3 L min-1 (Yang and Kim, 2020). While this system design successfully grew a variety of crops and maintained adequate fish health at a small scale, direct adoption in commercial-scale operations would not be suitable for intensive fish growth or nutrient production for plant use due to inadequate water quality management.
2.2 Effective solid waste removal improves fish health
The effective removal of RAS solid waste, which primarily consists of fish feces, uneaten feed, and sloughed scales, is required to maintain optimal water quality parameters and the requisite high water recirculation rates (Guerdat et al., 2013). Solid waste accumulation can negatively affect DO concentration, TAN concentration, and downstream biofiltration, while also increasing potential pathogen proliferation (Masser et al., 1999; Guerdat et al., 2013; Timmons et al., 2018). Commercial RAS commonly use granular filters for physical removal of solids > 20 microns, or rotating drum microscreens—often fitted with filter screens ranging in mesh sizes of 40-80 microns—for mechanical removal (Timmons et al., 2018, pp. 139-188). To work effectively, granular filters must be sized to maintain an HRT that does not limit other units, while screen filters are controlled by a float switch which triggers a high-pressure spray and does not rely on or affect the flow rate of water from the culture tank (Timmons et al., 2018, pp. 139-188). Thus, effective use of microscreen drum filters can remove one of the major impediments to process optimization.
Ineffective solids removal has been identified as a primary limiting factor for optimizing fish production in RAS and coupled aquaponic systems (Thorarinsdottir, 2015; Raviv et al., 2019). Many commercial operations and research-based systems use clarifiers and other gravimetric solids separation methods (Figure 4) (Baßmann et al., 2017; Knaus and Palm, 2017; Yang and Kim, 2020; Ani et al., 2022). Optimally designed gravity-based clarification systems can remove solids > 100 microns, with effectiveness depending on clarifier HRT providing sufficient time for particles to settle (Timmons et al., 2018, pp. 139-188). However, extending clarifier HRT will then reduce the flow rate and self-cleaning properties of preceding culture tanks or will require excessively large clarifying units to achieve the optimal tank flow rates and required HRTs for optimal solids removal efficiency.
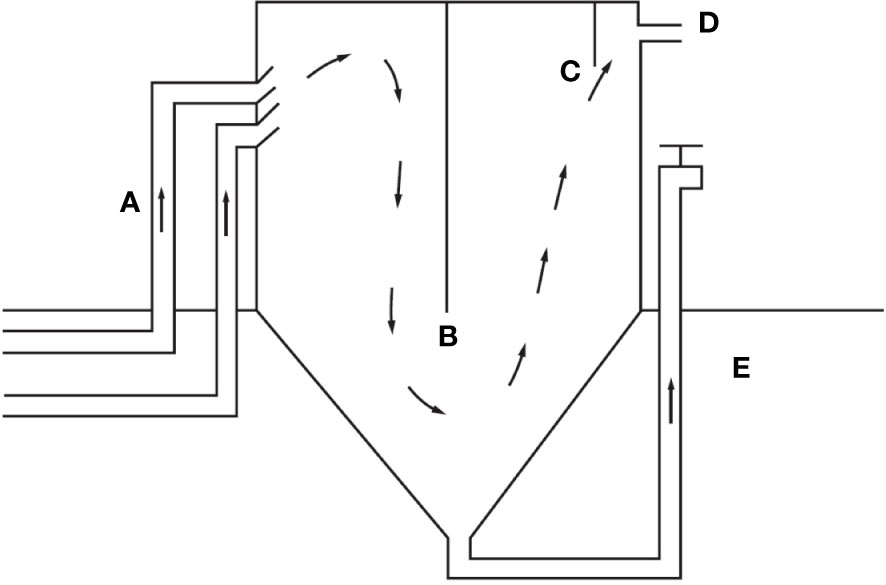
Figure 4 The clarifier design recommended by and retrieved from Rakocy et al. (2006). Commonly used in UVI-based aquaponic systems where (A) is the culture tank drain lines, (B) is the center baffle, (C) is the discharge baffle, (D) is the filtered water line, and (E) is the sludge discharge drain. Water flow in preceding and following units and solids separation rate are dependent on clarifier HRT.
The commercial scale system at UVI achieved stocking densities commensurate with commercial RAS but required two 3.8 m3 clarifiers with a combined area of 5.26 m2 and a 20-minute HRT to remove solids from four 7.8 m3 fish culture tanks with a combined area of 29.2 m2 (Timmons et al., 2018, pp. 663-710). While increasing clarifier diameter and utilizing baffles to lengthen the traveling path and settling period of solids allowed greater fish stocking densities, flow control was restricted in preceding and following units and the clarifiers consumed physical space that could otherwise be used for plant and/or fish production. Additionally, intensive clarifier maintenance is required to prevent the resuspension of solids and accumulation of organic carbon. Long periods between solids purging can also result in resuspension through denitrification, which produces nitrogen bubbles that get caught in the microbial biomass and cause masses of sediment to float to the surface and re-enter the flow stream. Nitrous oxide (N2O) is an intermediary of the denitrification process and a potent greenhouse gas with radiative forcing 265 times greater than carbon dioxide (IPCC, 2013). These emissions represent both nutrient loss for plant utilization and environmental consequences. Due to the compromises associated with intensive fish production and gravimetric solids removal, lower fish stocking densities and feed rates than in commercial RAS are commonly used in these UVI-based coupled aquaponic systems to prevent solids accumulation and maintain safe water quality (Baßmann et al., 2017; Knaus and Palm, 2017; Yang and Kim, 2020; Ani et al., 2022).
2.3 Biofiltration is essential to fish health and productivity
After solids removal, culture water still contains dissolved ammonia (NH3/NH4+) that is lethal to fish in low concentrations (Tomasso, 1994). Nitrate (NO3-) is the predominant form of nitrogen utilized for most crop plants in commercial and research HCS (Resh, 2013, pp. 31-31, 52-53). For these reasons, NH4+ must be converted into NO3- through nitrification (Brune et al., 2004). To achieve this, microbial biofilters are colonized with and support the growth of the two primary species of autotrophic nitrifying bacteria, Nitrosomonas and Nitrobacter, responsible for the two-step process where NH4+ is converted into nitrite (NO2-) and then into NO3- (Ebeling et al., 2006). A moving bed biofilm reactor (MBBR) with media designed to maximize surface area for biofilm production are often used in RAS and coupled aquaponics (Odegaard et al., 1994). Appropriate biofilter sizing is crucial for fish health and maximizing nitrification. Calculating biofilter volume is a multi-step process described in detail throughout RAS literature that is based on estimates of daily NH4+ production rates from feed regimens and NH4+ conversion rates of specific media (Guerdat et al., 2010; Timmons et al., 2018, pp. 277-314). Rusten et al. (2006) found that after appropriate MBBR sizing, an HRT of 2-5 minutes was effective for nitrification at commercial scale. Maintaining ideal MBBR retention times is not possible in a linear process flow system unless the preceding fish tanks and solids removal system and the following hydroponic units all use the same water flow rates.
Effective solids removal prior to biofiltration is required to achieve maximum nitrification as increased particulate OC promotes the growth of heterotrophic bacteria that outcompete desired autotrophic bacteria and reduces nitrification efficiency (Figure 5) (Chen et al., 2006; Guerdat et al., 2011). Even if a linear process flow system with gravimetric solids removal was operated to achieve ideal biofilter HRT, overall production could still be limited. If the clarifier was sized for appropriate solids removal, crop production area would be reduced as gravimetric solids removal devices occupy valuable space and are not ideal for commercial-scale production. Nitrification efficiency would be reduced if the clarifier was undersized with poor solids removal. A linear process flow is not suitable for commercial production intending to profit from fish and plant sales because it cannot simultaneously meet the differing hydraulic requirements for fish, plant, and water quality management under intensive growing conditions. Maximizing system productivity requires independently managed unit processes that can each adjust water flow rate for HRT optimization to facilitate efficient function at any scale.
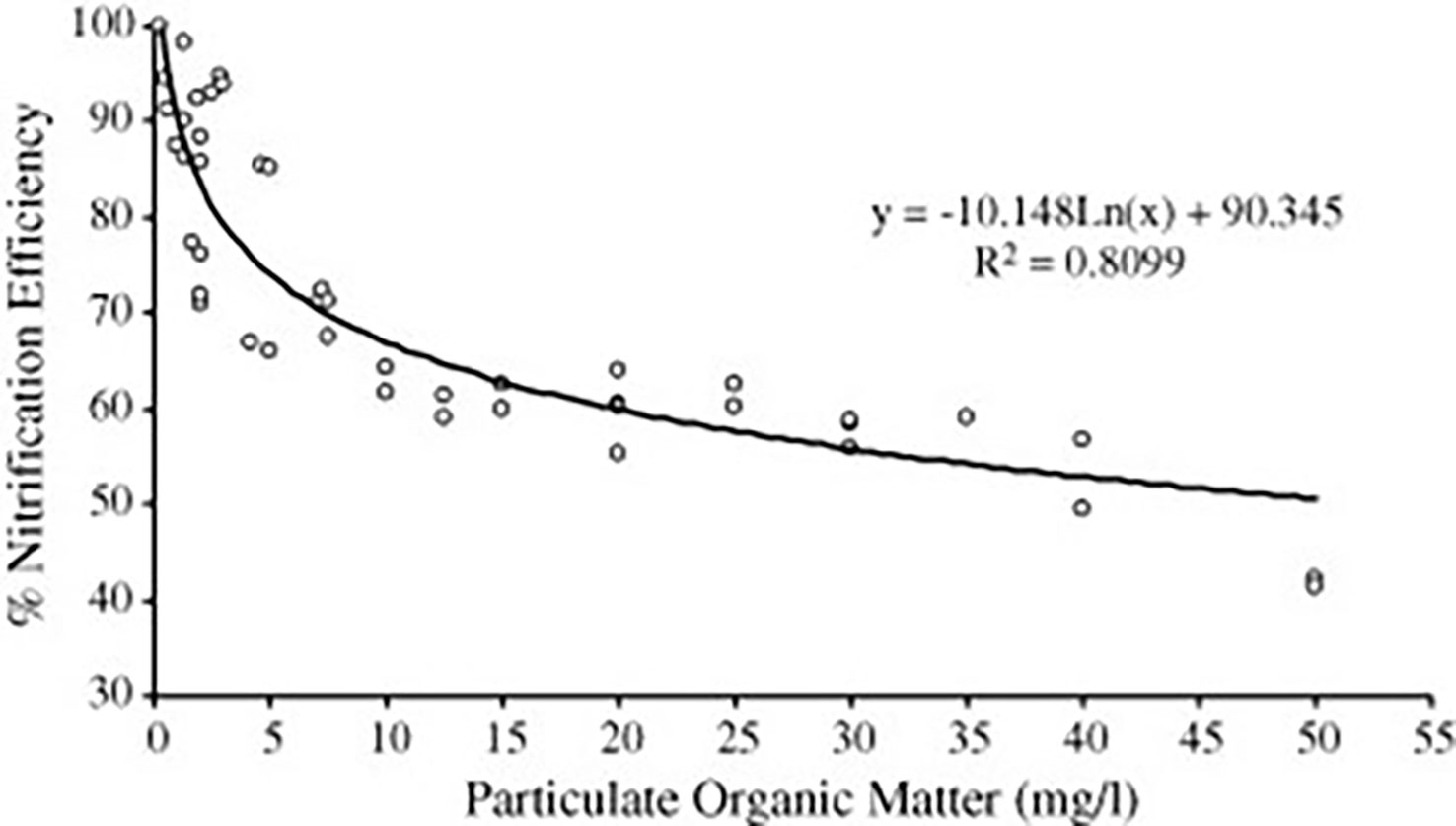
Figure 5 The effect of organic matter on biofilter performance. Figure retrieved from Chen et al. (2006) demonstrating the effect of particulate matter concentration on RAS biofilter nitrification efficiency and the importance of effective solids removal prior to biofiltration.
3 Parallel unit aquaponics design
Research studying coupled aquaponics without focus on meeting RAS production standards provides limited opportunity for advancement as a viable commercial industry. Several publications have begun expressing the importance of transitioning towards a parallel unit process design for commercial coupled aquaponics. Goddek et al. (2019) presented the parallel unit design utilized at the 1,000 m3 coupled facility at University of Rostock (UR) (Germany) as a model for commercial production (Figure 6). Fogarty (2021) provided a similar flow schematic for the University of New Hampshire Kingman Farm Research Aquaponic Greenhouses (KFRAG) located in Madbury, New Hampshire, USA (Figure 7).
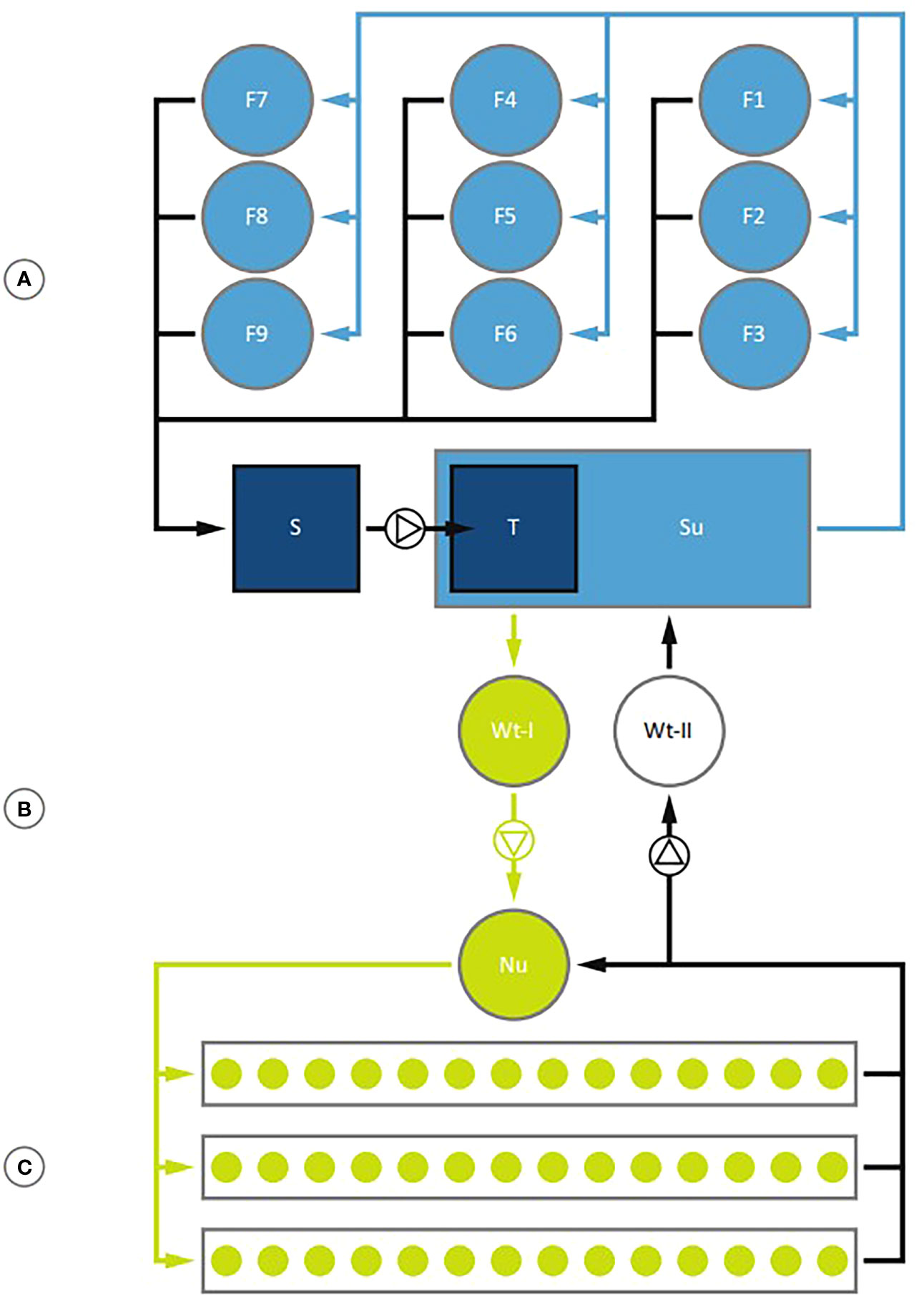
Figure 6 Schematic of the coupled aquaponics system at UR. Figure retrieved from Goddek et al. (2019) and demonstrating the water flow direction and potential HRT control to individual fish tanks, hydroponic beds, and water treatment units. The independent aquaculture (A), water transfer system (B), and hydroponic (C) units are shown. Sub-units include individual fish tanks (F1-F9), a sedimenter (S), trickling filter (T), sump (Su), water transfer tank from aquaculture unit (Wt-I), nutrient tank for independent hydroponic operation (Nu), and water transfer tank to transfer water back to aquaculture unit (Wt-II). The needed biofilter pump, aquaculture recirculation pump, aquaculture unit to hydroponic unit pump, and an additional pump to transfer nutrients from the hydroponic units back to Wt-II are not shown.
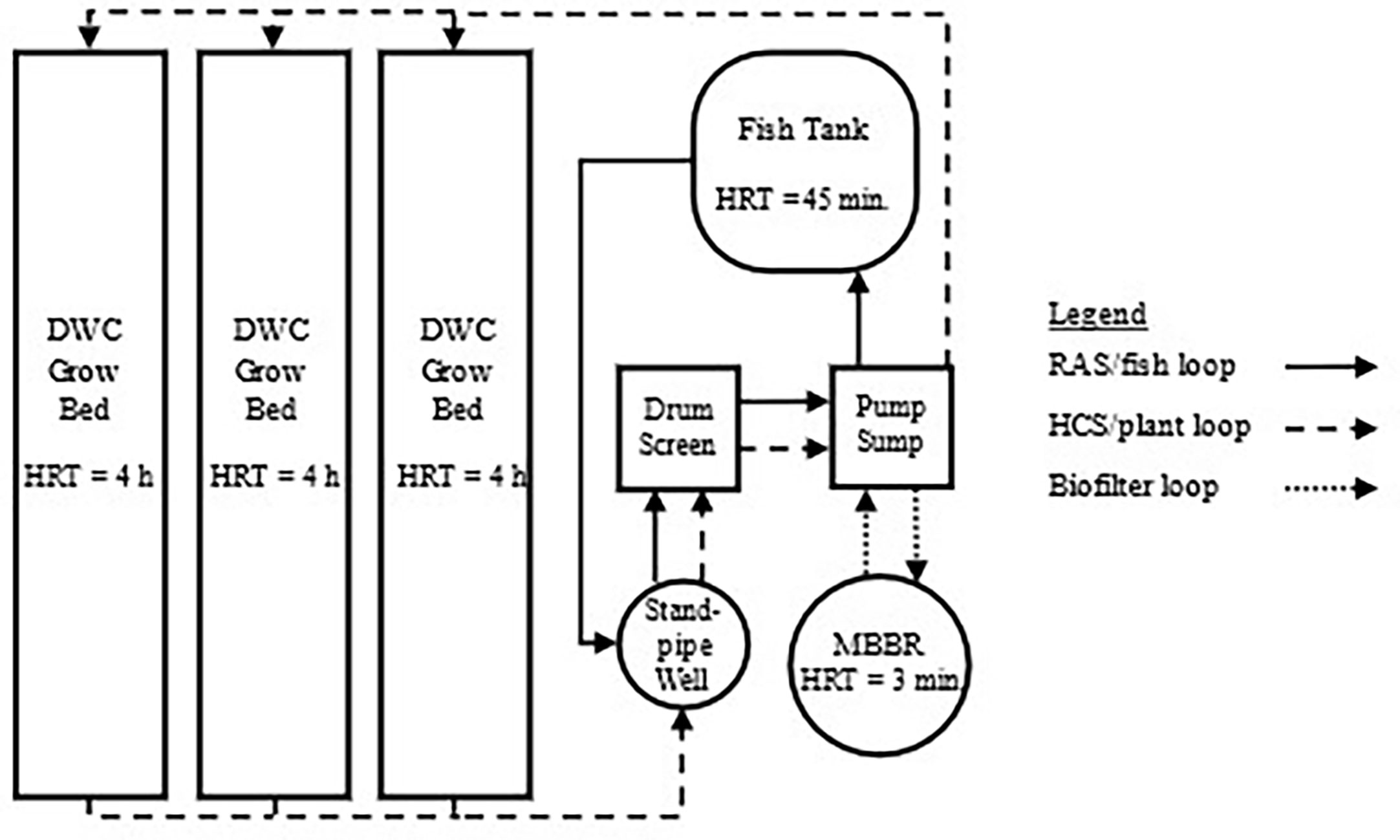
Figure 7 Basic components of the KFRAG system design. Flow schematic adapted from Fogarty (2021) of experimental aquaponic system located in Madbury, NH, USA demonstrating a parallel unit process coupled aquaponic design. The branching loops from the sump separate the aquaculture and hydroponic process flows until all wastewater is drained into the standpipe well. Solids are removed by a 54-micron drum screen microfilter before water flows to the sump, which supports the MBBR on an independent side loop. Fish culture tank flow rate is operated independently of all other units in the isolated fish loop, shown in solid arrows. Additional tanks could be added without limiting control by creating more loops branching from the sump with wastewater draining into the standpipe well prior to solids removal. Flow rate and HRT can be optimized for each tank and controlled for the needs of fish at different sizes. Similarly, additional hydroponic loops, in dashed arrows, could be added and operated at differing flow rates to meet the needs of diverse crops and growing methods.
The number of pumps and water transfer tanks are the primary differences between the two systems. The UR system required four pumps, a sump, and two additional water transfer tanks. One of the additional pump and water tank sets from the UR system allowed switching between coupled and decoupled production if nutrient supplementation was desired. The UNH KFRAG system utilized a single water pump and sump for all mixing. While this did not allow decoupling on demand, the simplification may result in lower capital and operating costs, fewer potential equipment failures, and a greater percent of the total system area dedicated to growing space. Regardless of these differences, both systems permitted independent water flow rate control to multiple fish culture tanks, hydroponic beds, and water treatment units that could be scaled to meet specific requirements for optimal production. Modular, scalable designs are fundamental to commercialization and maximizing economic sustainability and may even facilitate production of fish at multiple growth stages and multiple crops within a single coupled aquaponic system.
Fogarty (2021) reported the water flow rates, unit HRTs, and operating conditions for the UNH KFRAG system. The system consisted of a 3 m3 fish tank filled with 2,500 L of water, a rotary drum screen filter fitted with 54-micron screens, a 1.3 m3 MBBR, a 0.2 m3 pump sump, a 0.3 m3 standpipe well, and three 3.6 m3 deep water culture (DWC) hydroponic grow beds for a total volume of 15 m3. Tilapia were fed 1,300 g of 40% protein content feed per day. Bi-weekly sampling and population adjustments were used to ensure that 1,300 g of feed per day would provide nutrition for optimal fish growth (Delong et al., 2009). After reaching a 36 kg m-3 stocking density, the fish population was managed to maintain the desired feed rate and stocking density until harvest. The three hydroponic DWC grow beds each had a growing area of 11.9 m2 with lettuce (Lactuca sativa) planted at a density of 24.2 plants m-2.
The isolated fish and plant loops are indicated in Figure 7 using solid and dashed arrows, respectively. Treated water from the shared sump was pumped to the DWC beds, fish tank, and MBBR separately for desired flow rates to be achieved and adjusted, as needed, at each inlet manifold. Hydroponic and fish wastewater were combined in a standpipe well prior to solids removal and biofiltration. The standpipe well prevented water from travelling between fish and plant units without prior treatment and allowed independent operation of fish culture tanks and hydroponic beds while requiring only one water pump. The flow rate and HRT for the fish tanks, DWC grow beds, and MBBR are shown in Table 1, and are commensurate with the standards for RAS production cited above.
4 Discussion regarding feed rate and nitrogen production
As noted above, nutrients from fish feed are significantly more expensive than synthetic fertilizers, making it difficult for coupled aquaponic production to be profitable when fish are not a viable revenue source (Colt and Schuur, 2021). Profitable fish production in RAS is generally achieved through intensification of the process to make efficient use of the inputs. While tilapia has historically been a common RAS and aquaponic fish, feed practices and stocking densities can vary between industries (Rakocy et al., 2006; Delong et al., 2009; Goddek et al., 2019, pp. 163-201; Yang and Kim, 2020). Intensive RAS tilapia feed rates are based on fish age, with fry receiving up to 30% of the system biomass weight in feed per day before tapering gradually to approximately 1.5% of the system biomass in feed per day as fish reach harvest mass (Riche & Garling, 2003; Delong et al., 2009). Tilapia are commonly harvested at 680 g when feed conversion ratio (FCR) increases and the return on weight gain to cost of feed is diminished (Delong et al., 2009). Conversely, many coupled aquaponic systems have lower stocking densities and either feed a daily rate between 2% and 5% of the initial fish biomass without adjustment to account for growth or feed several times a day until visible satiation to provide consistent nutrient inputs without waste accumulation (Baßmann et al., 2017; Knaus and Palm, 2017; Yang and Kim, 2020; Ani et al., 2022; Dusci et al., 2021). Restrictive feed rates and lower stocking densities in coupled aquaponics will reduce the fish production rate and the rate of dissolved nutrient output available for crop growth, which further supports the need to adopt a parallel unit process design for intensive fish production when nutrient supplementation is not desired or possible (Yep and Zheng, 2019).
Excluding carbon, N is often the most required nutrient by mass for effective plant growth (Marschner, 2011). Because of its importance by mass to plant growth and the cost disparity between sourcing N from fish feed and conventional fertilizer salts, the potential of greater N production from intensive fish rearing is vital when considering coupled aquaponic management. TAN production (solubilization and excretion of N in feed) from the fish unit can be utilized to calculate the potential plant productivity of such a system. The differences in estimated daily TAN production rates in eight systems from recently published coupled aquaponics research demonstrate the effect of feed rate and stocking density on nutrient production (Table 2). Daily TAN production was calculated using the following equation retrieved from Timmons et al. (2018, pp. 52-93) and data taken from the methods used in each manuscript:
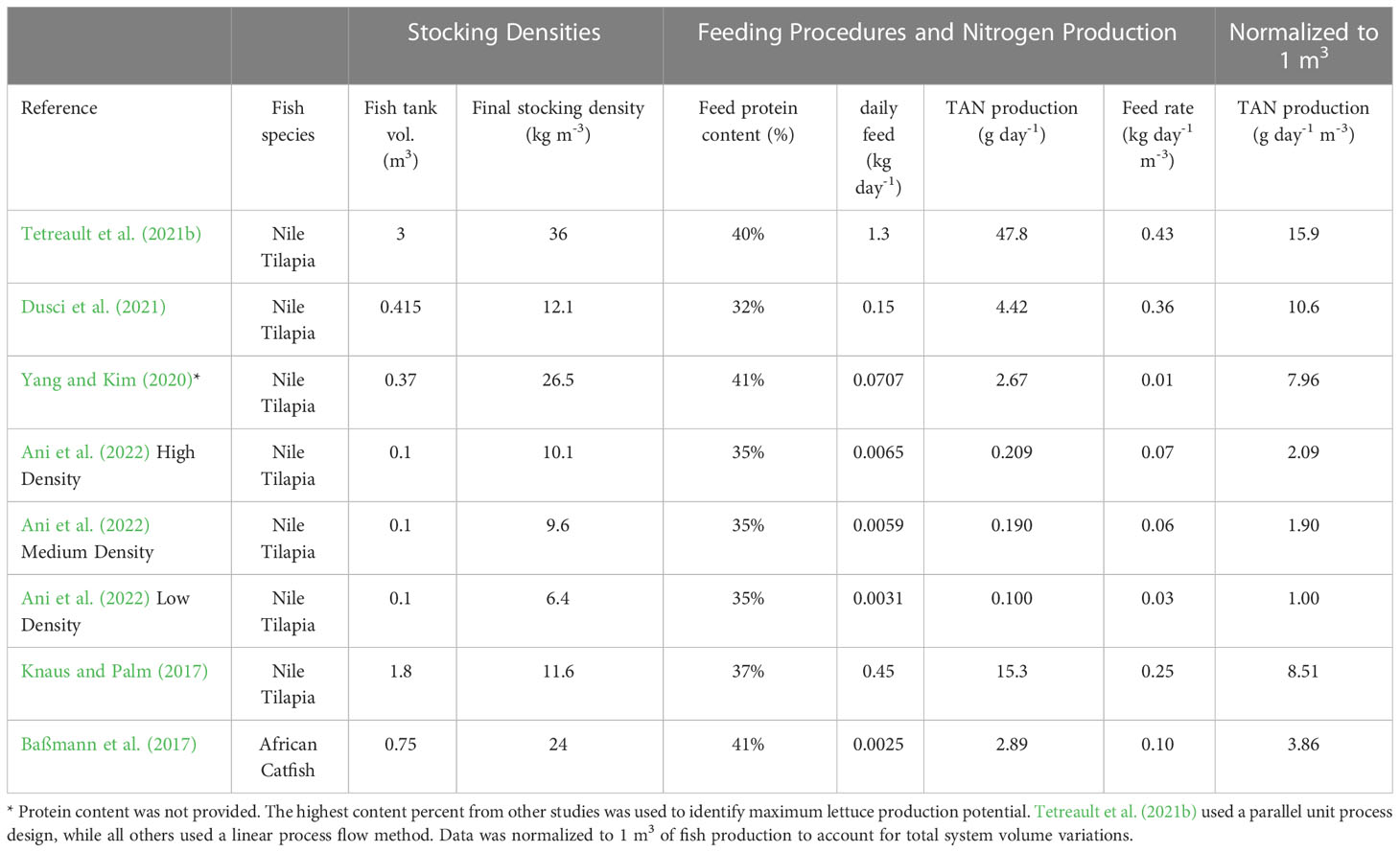
Table 2 The estimated daily total ammoniacal nitrogen (TAN) production of eight experimental coupled aquaponic systems using data provided in methods sections from six recent manuscripts accepted in peer reviewed journals.
where PTAN is daily TAN production (g day-1), FR is daily feed rate (kg day-1), PC is the protein content of feed (%), and 0.092 is the average percent of the feed mass excreted as ammonia. The production of TAN was normalized to 1 m3 of fish at each reported stocking density and feed rate to accurately compare nutrient production. Tetreault et al. (2021a) used the KFRAG greenhouses described above while all other systems used a variation of a linear flow method. The data from these research systems confirm that increased fish stocking density and feed rate results in greater specific daily N production.
Lettuce or other leafy greens are the most commonly grown aquaponic crops and can be used as a model crop to demonstrate the effect of maximizing nutrient production by the fish and biofilter units (Love et al., 2014). Timmons et al. (2018, pp. 663-710) presented an average N assimilation rate of 0.0184 g day-1 plant-1 for a common three-phased lettuce growing method to calculate the ideal feed rate to plant ratio. The weekly and yearly number of plants that could be supported by a 1 m3 fish tank operated at the stocking densities and feed rates used in each research system from Table 2 are shown in Table 3. Based on the data provided by each manuscript, the greater specific N output achieved using the parallel unit process design, fish stocking density, and daily feed rate from Tetreault et al. (2021b) would result in the most heads of lettuce grown per year. More intensive fish production uses less space and supports a greater hydroponic growing area, resulting in more efficient space utilization and greater profitability of both the RAS and HCS components in coupled aquaponic systems.
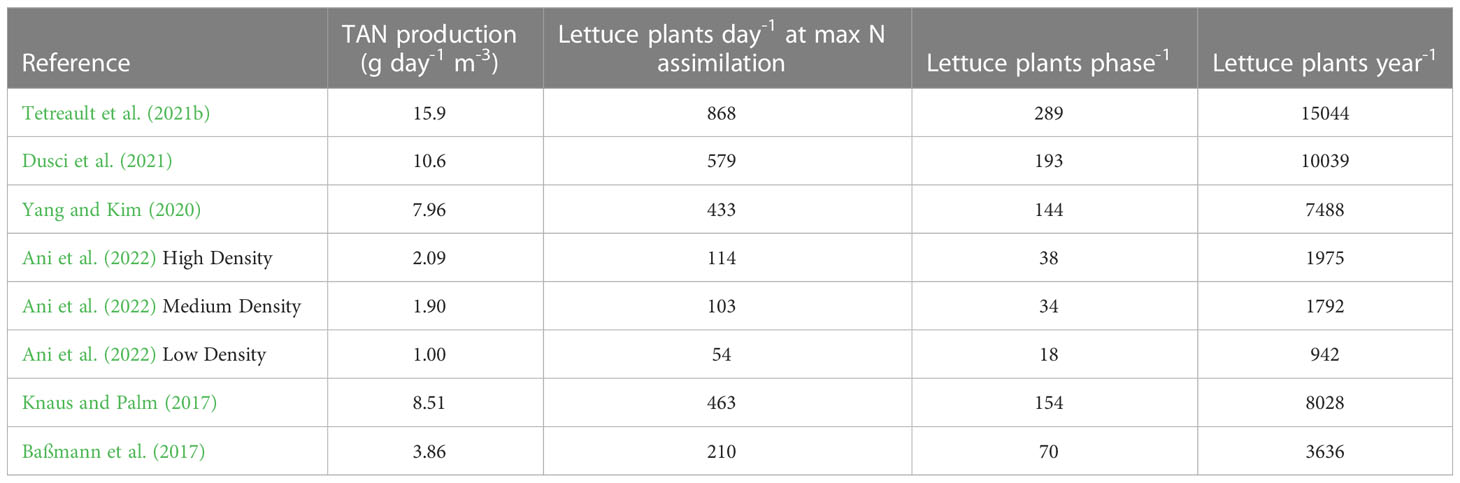
Table 3 The estimated lettuce production of eight coupled aquaponics systems normalized to 1 m3 of fish production using a common three-phased growing method described in (Timmons et al., 2018, pp. 663-710).
5 Conclusion
The review of the literature and research shows that intensive coupled aquaponics may be improved with a scalable parallel unit process design adapted from RAS, as demonstrated at both UR and KFRAG. This type of design facilitates increased fish stocking densities, fish feed rates, and water treatment performance while minimizing capital and operating costs to improve fish profitability and nutrient output quantity and quality for hydroponic crops. Aquaponic research studies employing system designs not optimized for commercial-scale and intensive fish production will have limited scalability and application for commercial utilization. While research intended for commercial applications of coupled aquaponics would benefit from maximizing fish production, it is also important for pilot-scale studies to provide proof-of-concept data before expanding research. With the variety of purposes for aquaponic production, multiple system designs and research approaches are valuable and required. However, the current research outlined in this review supports the need for a system design capable of intensive fish production, such as that used at UR and KFRAG, to begin the development of a commercially viable coupled aquaponics industry.
The lack of a scalable system design to maximize fish production is limiting the potential development of the commercial coupled aquaponics industry to increase lean protein availability and fresh produce access in food deserts. The predominantly cited design references for aquaponic system construction developed at UVI inherently lack scalability and demonstrate intrinsic inefficiencies as compared to a parallel unit process approach based on contemporary RAS. Comparison of energy and resource use efficiency between linear and parallel aquaponic systems could further address potential differences in sustainability as well as production optimization. Implementation of parallel unit processes for water treatment and crop production may allow increased fish and plant production rates. Continued research at the pilot and commercial scale of this design approach is required to identify specific water quality and operating parameters to balance fish and crop health, confirm consistency in production over time, develop treatment processes for solid waste, and to develop cost analyses to determine profitability with a variety of system scales, fish and crop types, and energy demands.
Data availability statement
The raw data supporting the conclusions of this article will be made available by the authors, without undue reservation.
Author contributions
JT: conceptualization, investigation, data curation, writing – original draft, writing – review & editing, and project administration. RF: conceptualization, validation, writing – review & editing, and visualization. SF: conceptualization, writing – original draft, visualization, and writing – review & editing. TG: conceptualization, writing – review & editing, and project administration. All authors contributed to the article and approved the submitted version.
Conflict of interest
The authors declare that the research was conducted in the absence of any commercial or financial relationships that could be construed as a potential conflict of interest.
Publisher’s note
All claims expressed in this article are solely those of the authors and do not necessarily represent those of their affiliated organizations, or those of the publisher, the editors and the reviewers. Any product that may be evaluated in this article, or claim that may be made by its manufacturer, is not guaranteed or endorsed by the publisher.
References
Ani J., Manyala J., Masese F., Fitzsimmons K. (2022). Effect of stocking density on growth performance of monosex Nile tilapia (Oreochromis niloticus) in the aquaponic system integrated with lettuce (Lactuca sativa). Aquac. Fish. 7 (3), 328–335. doi: 10.1016/j.aaf.2021.03.002
Baßmann B., Brenner M., Palm H. W. (2017). Stress and welfare of African catfish (Clarias gariepinus burchell 1822) in a coupled aquaponic system. Water 9 (7), 504. doi: 10.3390/w9070504
Brune D., Kirk K., Eversole A. (2004). Autotrophic intensification of pond aquaculture: shrimp production in a partitioned aquaculture system (Roanoke, Virginia: Proceedings of the Fifth International Conference on Recirculating Aquaculture), 201–210.
Chen S., Ling J., Blancheton J.-P. (2006). Nitrification kinetics of biofilm as affected by water quality factors. Aquac. Eng. 34 (3), 179–197. doi: 10.1016/j.aquaeng.2005.09.004
Colt J., Schuur A. (2021). Comparison of nutrient costs from fish feeds and inorganic fertilizers for aquaponic systems. Aquac. Eng. 95, 102205. doi: 10.1016/j.aquaeng.2021.102205
Colt J., Schuur A., Weaver D., Semmens K. (2021). Engineering design of aquaponics systems. Rev. Fish. Sci. Aquac. doi: 10.1080/23308249.2021.1886240
Davidson J., Summerfelt S. (2004). Solids flushing, mixing, and water velocity profiles within large (10 and 150 m3) circular ‘Cornell-type’ dual-drain tanks. Aquac. Eng. 32 (1), 245–271. doi: 10.1016/j.aquaeng.2004.03.009
Davison W. (1997). The effects of exercise training on teleost fish, a review of recent literature. Comp. Biochem. Physiol. Part A: Physiol. 117 (1), 67–75. doi: 10.1016/S0300-9629(96)00284-8
DeLong D., Losordo T., Rakocy J. (2009). Tank culture of tilapia (USDA Southern Regional Aquaculture Center, SRAC Publication No. 282). Available at: https://wkrec.ca.uky.edu/files/tilapiatankculture.pdf.
Dusci J., Hager J., Coyle S., Tidwell J. (2021). Evaluation of freshwater prawn, Macrobrachium rosenbergii, for biological solids control in raft aquaponic systems and the protective effectiveness of root guards. J. World Aquac. Soc. 53 (1), 290–308. doi: 10.1111/jwas.12856
Ebeling J., Timmons M., Bisogni J. (2006). Engineering analysis of the stoichiometry of photoautotrophic, autotrophic, and heterotrophic removal of ammonia–nitrogen in aquaculture systems. Aquac. Eng. 257 (1-4), 346–358. doi: 10.1016/j.aquaculture.2006.03.019
Fogarty S. Z. (2021). “Foodborne pathogens and water quality in commercial-scale aquaponic systems with rapid micro screen solids removal”. Master's Theses and Capstones. 1507. Available at: https://scholars.unh.edu/thesis/1507.
Goddek S., Delaide B., Mankasingh U., Ragnarsdottir K., Jijakli H., Thorarinsdottir R. (2015). Challenges of sustainable and commercial aquaponics. Sustainability 7 (4), 4199–4224. doi: 10.3390/su7044199
Goddek S., Delaide B. P. L., Joyce A., Wuertz S., Jijakli M. H., Gross A., et al (2018). Nutrient mineralization and organic matter reduction performance of RAS based sludge in sequential UASB-EGSB reactors. Aquac. Eng. 83, 10–19. doi: 10.1016/j.aquaeng.2018.07.003
Goddek S., Espinal C., Delaide B., Jijakli M., Schmautz Z., Wuertz S., et al. (2016). Navigating towards decoupled aquaponic systems: A system dynamics design approach. Water 8 (7), 303. doi: 10.3390/w8070303
Goddek S., Joyce A., Kotzen B., Burnell G. (2019). Aquaponics food production systems: Combined aquaculture and hydroponic production technologies for the future (Berlin/Heidelberg, Germany: Springer Open), 163–201.
Guerdat T., Losordo T., Classen J., Osborne A., Delong D. (2010). An evaluation of commercially available biological filters for recirculating aquaculture systems. Aquac. Eng. 42 (1), 38–49. doi: 10.1016/j.aquaeng.2009.10.002
Guerdat T., Losordo T., Classen J., Osborne A., DeLong D. (2011). Evaluating the effects of organic carbon on biological filtration performance in a large scale recirculating aquaculture system. Aquac. Eng. 44 (1), 10–18. doi: 10.1016/j.aquaeng.2010.10.002
Guerdat T., Losordo T., DeLong D., Jones R. (2013). An evaluation of solid waste capture from recirculating aquaculture systems using a geotextile bag system with a flocculant-aid. Aquac. Eng. 54, 1–8. doi: 10.1016/j.aquaeng.2012.10.001
IPCC (2013). Climate change 2013: The physical science basis. contribution of working group I to the fifth assessment report of the intergovernmental panel on climate change. Eds. Stocker T. F., Qin D., Plattner G.-K., Tignor M., Allen S. K., Boschung J., Nauels A., Xia Y., Bex V., Midgley P. M. (Cambridge University Press). Available at: https://www.ipcc.ch/site/assets/uploads/2018/03/WG1AR5_SummaryVolume_FINAL.pdf.
Knaus U., Palm H. (2017). Effects of the fish species choice on vegetables in aquaponics under spring-summer conditions in northern Germany (Mecklenburg Western pomerania). Aquaculture 473, 62–73. doi: 10.1016/j.aquaculture.2017.01.020
Körner O, Bisbis M., Baganz G., Baganz D., Staaks G., Monsees M., et al. (2021). Environmental impact assessment of local decoupled multi-loop aquaponics in an urban context. J. Clean Prod. 313, 127735. doi: 10.1016/j.jclepro.2021.127735
Losordo T., Masser M., Rakocy J. (1999). Recirculating aquaculture tank production systems – a review of component options (USDA Southern Regional Aquaculture Center, SRAC Publication No. 453). Available at: https://www.webpages.uidaho.edu/fish422and424/Aquaculture%20422/422LabFiles/Lab%201%20Systems/Losordo%20et%20al%201999%20Recirculating%20component%20options.pdf.
Love D., Fry J., Genello L., Hill E., Frederick J., Li X., et al. (2014). An international survey of aquaponics practitioners. PloS One 9 (7), e102662. doi: 10.1371/journal.pone.0102662
Love D., Fry J., Li X., Hill E., Genello L., Semmens K., et al. (2015). Commercial aquaponics production and profitability: Findings from an international survey. Aquaculture 435, 67–74. doi: 10.1016/j.aquaculture.2014.09.023
Marschner H. (2011). Mineral nutrition of higher plants. 3rd ed (Cambridge, MA, USA: Academic Press).
Masser M., Rakocy J., Losordo T. (1999). Recirculating aquaculture tank production systems – management of recirculating systems (USDA Southern Regional Aquaculture Center, SRAC Publication No. 452). Available at: https://appliedecology.cals.ncsu.edu/wp-content/uploads/452.pdf.
Odegaard H., Rusten B., Westrum T. (1994). A new moving bed biofilm reactor - applications and result. Water Sci. Technol. 29 (10-11), 157–165. doi: 10.2166/wst.1994.0757
Palm H. W., Knaus U., Appelbaum S., Goddek S., Strauch S., Vermeulen T., et al. (2018). Towards commercial aquaponics: A review of systems, designs, scales and nomenclature. Aquacult Int. 26, 813–842. doi: 10.1007/s10499-018-0249-z
Rakocy J. E., Masser M. P., Losordo T. M. (2006). Recirculating aquaculture tank production systems: Aquaponics–integrating fish and plant culture (USDA Southern Regional Aquaculture Center, SRAC Publication No. 454). Available at: https://wkrec.ca.uky.edu/files/454fs.pdf.
Raviv M., Lieth H., Bar-Tal A., Silber A. (2019). “Growing plants in soilless culture: Operational conclusions,” in Soilless culture – theory and practice. Eds. Raviv M., Lieth J. H., Bar-Tal A. (London: Academic Press), 637–669.
Resh H. M. (2013). Hydroponic food production: A definitive guidebook for the advanced home gardener and the commercial hydroponic grower. 7th ed (CRC Press).
Riche M., Garling D. (2003). Feeding tilapia in intensive recirculating systems (USDA North Central Regional Aquaculture Center, NCRAC Publication No. 114). Available at: https://www.ncrac.org/files/biblio/ncrac114.pdf.
Rusten B., Eikebrokk B., Ulgenes Y., Lygren E. (2006). Design and operations of the kaldnes moving bed biofilm reactors. Aquac. Eng. 34 (3), 322–331. doi: 10.1016/j.aquaeng.2005.04.002
Souza S., Gimenes R., Binotto E. (2019). Economic viability for deploying hydroponic system in emerging countries: A differentiated risk adjustment protocol. Land Use Policy. 83, 357–369. doi: 10.1016/j.landusepol.2019.02.020
Summerfelt S., Mathisen F., Buran Holan A., Fyhn Terjesen B. (2016). Survey of large circular and octagonal tanks operated at Norwegian commercial smolt and post-smolt sites. Aquac. Eng. 74, 105–110. doi: 10.1016/j.aquaeng.2016.07.004
Tetreault J., Fogle R., Guerdat T. (2021a). Towards a capture and reuse model for aquaculture effluent as a hydroponic nutrient solution using aerobic microbial reactors. Horticulturae 7 (10), 334. doi: 10.3390/horticulturae7100334
Tetreault J., Fogle R., Guerdat T. (2021b). Anaerobic mineralization of recirculating aquaculture drum screen effluent for use as a naturally-derived nutrient solution in hydroponic cropping systems. Conservation 1 (3), 151–167. doi: 10.3390/conservation1030013
Thorarinsdottir R. (Ed.) (2015). Aquaponics guideline (Reykjavik, Iceland: Haskolaprent). Available at: http://aquaponics.is/europonics/wpcontent/uploads/2015/09/Guidelines_Aquaponics.pdf.
Timmons M. B., Guerdat T. C., Vinci B. J. (2018). Recirculating aquaculture. 4th ed (Ithaca Publishing Company LLC), 52–93. 93-133, 241-273, 663-707.
Timmons M., Summerfelt S., Vinci B. (1998). Review of circular tank technology and management. Aquac. Eng. 18 (1), 51–69. doi: 10.1016/S0144-8609(98)00023-5
Tomasso J. (1994). Toxicity of nitrogenous wastes to aquaculture animals. Rev. Fish. Sci. 2 (4), 291–314. doi: 10.1080/10641269409388560
Turnšek M., Morgenstern R., Schröter I., Mergenthaler M., Hüttel S., Leyer M. (2019). Commercial Aquaponics: A Long Road Ahead. In Goddek S., Joyce A., Kotzen B., Burnell G. M. (eds) Aquaponics Food Production Systems Switzerland: Springer Nature, pp. 453–485. doi: 10.1007/978-3-030-15943-6_18
Yang T., Kim H.-J. (2020). Effects of hydraulic loading rate on spatial and temporal water quality characteristics and crop growth and yield in aquaponic systems. Horticulturae 6 (1), 9. doi: 10.3390/horticulturae6010009
Keywords: aquaponic system design, nutrient bioeconomy, controlled environment agriculture (CEA), nitrogen management, recirculating aquaculture systems (RAS)
Citation: Tetreault J, Fogle RL, Fogarty S and Guerdat T (2023) Coupled aquaponics: Optimizing hydraulic retention times using a parallel unit process water treatment approach. Front. Hortic. 2:1140998. doi: 10.3389/fhort.2023.1140998
Received: 09 January 2023; Accepted: 22 February 2023;
Published: 09 March 2023.
Edited by:
Safina Naz, Bahauddin Zakariya University, PakistanReviewed by:
Juan Gabriel Correa Reyes, Autonomous University of Baja California, MexicoGeorgios K. Ntinas, Hellenic Agricultural Organization – ELGO, Greece
Copyright © 2023 Tetreault, Fogle, Fogarty and Guerdat. This is an open-access article distributed under the terms of the Creative Commons Attribution License (CC BY). The use, distribution or reproduction in other forums is permitted, provided the original author(s) and the copyright owner(s) are credited and that the original publication in this journal is cited, in accordance with accepted academic practice. No use, distribution or reproduction is permitted which does not comply with these terms.
*Correspondence: Joseph Tetreault, anRldHJlYXVsdEBoYXJyaXNidXJndS5lZHU=