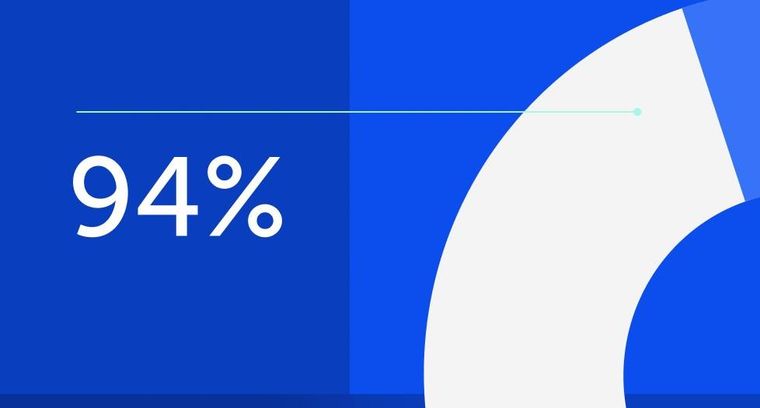
94% of researchers rate our articles as excellent or good
Learn more about the work of our research integrity team to safeguard the quality of each article we publish.
Find out more
METHODS article
Front. Energy Res., 03 August 2021
Sec. Electrochemical Energy Storage
Volume 9 - 2021 | https://doi.org/10.3389/fenrg.2021.702139
This article is part of the Research TopicBattery Technology and Management for Transportation ElectrificationView all 6 articles
With the increasing demand for electric vehicles, the high voltage safety of electric vehicles has attracted significant attention. More than 30% of electric vehicle accidents are caused by the battery system; hence, it is vital to investigate the fault diagnosis method of lithium-ion battery packs. The fault types of lithium-ion battery packs for electric vehicles are complex, and the treatment is cumbersome. This paper presents a fault diagnosis method for the electric vehicle power battery using the improved radial basis function (RBF) neural network. First, the fault information of lithium-ion battery packs was collected using battery test equipment, and the fault levels were then determined. Subsequently, the improved RBF neural networks were employed to identify the fault of the lithium-ion battery pack system using the experimental data. The diagnosis test results showed that the improved RBF neural networks could effectively identify the fault diagnosis information of the lithium-ion battery packs, and the diagnosis accuracy was about 100%.
With the increasing attractiveness of new energy vehicles, the safety of the electric vehicle battery is crucial. A total of 124 electric vehicle combustion accidents were reported in 2020, including 23% charging fire, 38% standing fire and 39% driving fire (Electric vehicle observer, 2020). These accidents are related to the car battery pack. Therefore, the correct diagnosis of the battery can effectively reduce the risks of battery thermal runaway and traffic accidents. To effective and accurate identification of failures for the battery, Schmid et al. (2021) developed a fault diagnosis method by using the fuzzy clustering algorithm. In this algorithm, the switches of reconfigurable battery system were used to isolate the fault of the electric vehicles. Tian et al. (2020) developed a sensor fault diagnosis algorithm using the equivalent models and particle filters. Then this diagnosis was employed to test the battery pack using the recursive least square algorithm. The results show that the algorithm proposed in this study can be used to identify the diagnosis of the battery pack. Schmid et al. (2020) developed a new data-driven method to identify the single cell voltages. The principal component analysis method was used first to estimate the fault information. Then a developed cross-cell monitoring algorithm was used to carry out the fault diagnosis. Jiang et al. (2021) proposed a new signal-based fault diagnosis model for lithium-ion batteries. Then this model was used to verify the data from the thermal runaway of electric vehicles. The results show that the method developed in their study can be used to diagnose the faults of the lithium-ion batteries. Development of the machine learning theory dramatically provides an effectively algorithm to diagnose and identify the fault information, like the neural network. The neural network method is a good algorithm to predict different data, since it can effectively study and train the different mathematical models. Therefore, it has been widely used to identify different engineering problems, especially for the vehicle engineering. Ardeshiri et al. (2020) summarized the main research methods for remaining service life and fault diagnosis using the machine learning algorithms. Li et al. (2020) used the Long Short-Term Memory (LSTM) neural network to diagnose the fault of the battery. Zhang et al. (2021) also used the LSTM neural network to diagnose the faults of the photovoltaic array problem. The results show that the method developed by Zhang et al. can be used to identify photovoltaic array faults. Kara (2021) developed a fault diagnosis method combing Convolutional Neural Networks (CNN), LSTM, and PSO algorithms to accurately capture nonlinear characteristics for lithium-ion battery prediction problem. Although the prediction results for the LSTM neural network is good for diagnosing the fault of the battery and photovoltaic array problem, the structure of this method is very complex and it has a low prediction efficiency. Yao et al. (2020) used the wavelet-neural to identify the lithium-ion batteries of the electric vehicles. To improve the safety and reliability of the vehicles, four parameters were selected as the variables, influencing the performance of the electric vehicles. The results show that voltage difference value has great influence on the diagnosis of the electric vehicles. Niri et al. (2020) used the Wavelet-Markov Load Analysis method to predict the power state of the lithium ion batteries for electric vehicles. Meng et al. (2017) used the BP neural network to diagnose the lithium battery using nine parameters. Yao et al. (2021) used the Support Vector Machine (SVM) method to identify the Lithium-ion batteries. For the SVM algorithm, the kernel function parameter and penalty factor was optimized by using the grid search method. The results show that the SVM-based fault diagnosis algorithm can effectively identify the fault information of the batteries. The training speed of BP, wavelet, and SVM neural network is slow and easy to fall into local solution, therefore, these methods are always optimized using the optimization algorithm (Cheng et al., 2014; Gao et al., 2021; Shi et al., 2021).
With the increase of the electric vehicles, the lithium iron phosphate battery pack has attracted significant attention since it has high security and a significant market share. However, not too much researches have been published to test and diagnose the lithium iron phosphate battery pack. Therefore, the lithium battery type was selected as the research objective in this study. As can be seen from above, the neural network has become the main method to identify and diagnose the battery. In the neural network algorithms, the RBF neural network is a good algorithm since it can accurately approximate any nonlinear function with the fast convergence speed. Hence, this paper presented a fault diagnosis method for lithium-ion battery packs using improved RBF neural networks. The rest of the paper can be summarized as follows. To obtain the sample data, the test equipment of the lithium iron phosphate battery pack is shown in details in Data Preparing for Lithium-Ion Battery Packs, as well as the fault levels and treatment methods. In the Neural Networks, the neural networks used in this study are listed including the General Regression Neural Network (GRNN) and the Probabilistic Neural Network (PNN) algorithms. Following this, the results of the fault diagnosis using the different methods are shown and discussed in the Fault Diagnosis Results and Discussions. Finally, the conclusions and the future work are present in the Conclusions and Future Works.
The acquisition module of the electric vehicle plays a critical role in enhancing car safety because it can real-time display the data of the battery system, such as voltage, current, and temperature. It is widely known that the main failures of the electric vehicle are influenced by voltage, current, and temperature for batteries. Therefore, these three parameters were selected as the input data to establish the fault diagnosis model.
If errors occur inside the batteries, the Controller Area Network (CAN) bus of the battery management system immediately sends the fault data (voltage, current, and temperature) to the central control module. Subsequently, the main control module divides the fault information from the CAN bus into different fault levels according to the fault type and severity. Based on the vehicle safety requirements, the battery system fault information is always divided into four levels, as shown in the Table 1.
In this study, a method of diagnosing the battery system of electric vehicles was developed using the neural networks. A pure electric passenger car was employed to collect the fault information of a lithium iron phosphate battery pack. The main parameters of the battery pack were 352 V/ 100 Ah battery pack. Figure 1 shows the charging and discharging of the battery test equipment. The main experimental equipment consisted of the lithium iron phosphate battery pack, battery charge and discharge tester, CAN data analyzer, and laptop. Figure 2 shows the connection mode of the test equipment. The functions of each experimental equipment are as follows:
1) The battery charging and discharging tester was a TECHPOW intelligent charging and discharging tester, which could analyze energy feedback during battery charging and discharging and simulate different vehicle conditions for evaluating the power battery performance. The direct-current voltage of this tester ranged from 0 to 1500 V, and its current ranged from 0 to 400 A.
2) The tested battery pack was a 352 V / 100 Ah battery pack divided into two boxes and used in series.
3) A CAN data analyzer was used to collect the data from the internal sensor of the battery.
4) A stabilized voltage of 12 V was used to power the battery management system.
5) A laptop was used to collect and show the experimental data.
Six parameters of the battery were selected as the input data, the fault levels were set as the output data for the neural network. For discussing the voltage fault of battery pack, the voltage of battery pack and single battery should be discussed respectively. Due to the individual differences in the production and application of batteries, the total voltage of battery pack may be in a reasonable range, while the voltage of a single battery is abnormal. Therefore, the system should monitor the voltage of battery pack and single battery at the same time. The data collection method can be summarized as follows:
1) Single-voltage (L1 and L2).
The range of the charging voltage for lithium iron phosphate single-voltage is from 2.0 to 3.65 V. The charging voltage was set from 2.4 to 3.25 V. For the upper-limit voltage, the voltage for fault diagnosis was 3.7 V when the actual battery voltage collected using the sensor was 3.3 V. The fault level for this condition is denoted No. I. For the lower-limit voltage, the fault diagnosis voltage was 2.05 V, as the actual battery voltage collected using the sensor was 2.45 V. The fault level for this condition is denoted No. II. Because the voltage for Level IV was very high, the fault value was randomly selected to some extent.
2) Battery voltage (L3 and L4).
The battery pack voltage of lithium iron phosphate battery packs ranges from 275 to 401.5 V. Considering the safety during the experiments, a 315–361.5 V battery pack voltage was adopted. For the upper-limit voltage of the battery pack, the fault diagnosis voltage was 410 V when the actual voltage of the battery pack recorded by the sensor was 450 V. The fault level for this condition is denoted No. I. For the lower limit, the fault diagnosis voltage was 203 V when the actual voltage of the battery pack collected using the sensor was 243 V. The fault level for this condition is denoted No. III. The fault value was also selected randomly, as the voltage range for fault level III was broad.
3) Discharge current of battery pack (L5).
The test battery is a battery pack with consideration to both power and energy, so a discharge rate of up to 10 C (time less than 10 s) will not pose potential safety hazards. Values detected by the current sensor are measured values. Due to the wide range of current value in Grade IV faults, the fault value is randomly selected according to the range.
4) Temperature of battery pack (L6).
The tests were performed under the temperature of 298.15 K and the pressure of 101.325 kPa condition. The electric heating system inside the battery pack is utilized to works, so that the temperature sensor inside the battery pack detects the temperature value reaching the fault levels. Because the temperature value range of Grade IV faults is large, the fault value is randomly selected according to the range.
Based on the design requirements of the electric vehicle and the performance of the lithium iron phosphate battery pack, the parameter ranges for all faults levels were determined, as shown in the Table 2. The maximum and minimum single-voltage values, L1 and L2, were used to control the charging and discharging processes, respectively. The charging and discharging processes were stopped when the voltage reached the maximum and minimum values. The maximum voltage of battery pack L3 was utilized to control battery pack charging, and the minimum voltage of battery pack L4 was used to regulate battery pack discharging. The discharge current of the battery pack was used to control the discharging current of the battery pack. The battery pack temperature was used to control the temperature value of the battery pack during charging and discharging. Fifty sample data were randomly selected at every time in the experiment. Figures 3–6 show the test data obtained using the above experimental equipment for different fault levels.
The RBF neural network is a three-layer typical feedforward neural network developed by Powell in 1985. It is an effective algorithm to predict different data in different fields. With the rapid development of machine learning techniques, the improved RBF algorithm can improve the data prediction accuracy, like the GRNN and the PNN algorithms. In this study, these two algorithms were employed to diagnose the fault information for the lithium-ion battery packs.
The GRNN is an improved model of the RBF method developed by Specht (1991). It can obtain better solutions than the RBF neural network especially in the non-linearity mathematical problem using the less samples. The structure of the GRNN model can be found in the Figure 7 with four layers. The Gaussian function is used to obtain the output value from the hidden layer (Zhang, 2019):
where i = 1, 2, ..., m. x is the input value and xi is the center of the ith neural. δ is the extended speed.
FIGURE 7. The structure of the GRNN neural network (Specht, 1991; Ghritlahre and Prasad, 2018).
The PNN method used the density function estimation and Bayesian theory to approximate the output data (Song, 2020). It also includes an input, a pattern, a summation and an output layer, like the structure of the GRNN neural network in the Figure 7. The input and output in the pattern layer of the PNN algorithm can be expressed as (Ni, 2014):
where i = 1, 2, ..., n. d is the dimension of sample space. σ is the smoothing factor.
For verifying the accuracy of the neural networks, the last five samples for each fault levels were selected as the test samples, and the first 45 samples were used as the training data in the Figures 3–6 .
The parameters of the neural networks have great influence on the output results. To obtain the best results, the selection of the parameters becomes very important. For the GRNN and PNN algorithms, the spread value is one of the most important parameters need to be determined. The results are too rough if the spread value is very big, and the results are not smooth enough if the spread value is very small (Wen et al., 2014). Therefore, different spread values have been selected and discussed for GRNN and PNN algorithms using the first 20 samples for each fault level. To compare the calculation accuracy for the improved RBFNN, a traditional RBF neural network is also employed in this study to diagnose the fault of the battery. The results can be found from the Tables 3–5. As can be seen from the Tables 3–5. The number of errors for the traditional RBF neural network is more than the other two algorithms. It can be conclusion that the GRNN and PNN algorithms are suitable for battery diagnosis problem. The diagnosis accuracy has been changed with the change of the spread value. The diagnosis accuracy is the best when the spread value is equal to 20 for GRNN and PNN algorithms. In addition, the PNN algorithm is superior to the GRNN algorithm for the identification of the fault information of the battery.
The selection of the sample size also influences the output results of the neural networks. Therefore, different sample size has been used to diagnose the fault information of the lithium iron phosphate battery pack with the spread value of 20, as shown in the Tables 6, 7 As can be seen from the table, with the increase of the sample size, the diagnosis accuracy is increased. When the sample size is 45, the GRNN and PNN algorithms can both identify fault information of the battery. The diagnosis accuracy is about 100%. It can be inferred that the GRNN and PNN algorithms can be used to identify the fault information of the lithium iron phosphate battery pack with high accuracy. The PNN algorithm can obtain the better results using the less samples than the GRNN algorithm.
This paper presented a fault diagnosis method for the electric vehicle power battery using the improved RBF neural networks. Six parameters of the lithium iron phosphate battery pack were selected as the variables, and the fault levels were selected as the target. The CAN bus was used to collect all the experimental data. Then the GRNN and the PNN algorithms were employed to identify the fault information of the battery. At the same time, the parameter and the sample size were also discussed and compared. The results show that the parameter and the sample size influence the output results of the neural networks, and the GRNN and PNN algorithms can be used to identify the fault information of the battery. To protect the battery effectively and precisely, further studies will introduce the state of health (SOH) parameter, and the new fault diagnosis method will be employed to verify the accuracy and feasibility.
The original contributions presented in the study are included in the article/Supplementary Material, further inquiries can be directed to the corresponding author.
JW is responsible for the full-paper design and experimental data analysis, SZ is responsible for the compilation of the algorithm, and XH is responsible for obtaining the experimental data.
The study in this paper was sponsored by the Natural Science Foundation of the Jiangsu Higher Education Institutions of China (19KJB580006) and Natural Science Foundation of Jiangsu Province (BK20201052).
Author XH was employed by the company Shanghai Automotive Industry Corp. Group.
The remaining authors declare that the research was conducted in the absence of any commercial or financial relationships that could be construed as a potential conflict of interest.
All claims expressed in this article are solely those of the authors and do not necessarily represent those of their affiliated organizations, or those of the publisher, the editors and the reviewers. Any product that may be evaluated in this article, or claim that may be made by its manufacturer, is not guaranteed or endorsed by the publisher.
Ardeshiri, R. R., Balagopal, B., Alsabbagh, A., Ma, C., and Chow, M. Y. (2020). “Machine Learning Approaches in Battery Management Systems: State of the Art: Remaining Useful Life and Fault Detection,” in 2020 2nd IEEE International Conference on Industrial Electronics for Sustainable Energy Systems (IESES) (IEEE). doi:10.1109/ieses45645.2020.9210642
Cheng, S. F., Cheng, X. H., and Yang, L. (2014). Application of Wavelet Neural Network with Improved Particle Swarm Optimization Algorithm in Power Transformer Fault Diagnosis. Power Syst. Prot. Control. 42 (19), 37–42.
Electric vehicle observer (2020). Analysis of Electric Vehicle Fire Accidents in 2020. Available at: https://m.d1ev.com/kol/138145 (Accessed 02 18, 2020).
Gao, C., Yu, Z., and Zhou, Q. (2021). Application of GA-ACO Optimized BP Neural Network in Fault Diagnosis of Planetary Gearbox. J. Mech. Transm. 45 (3), 153–160. doi:10.16578/j.issn.1004.2539.2021.03.025
Ghritlahre, H. K., and Prasad, R. K. (2018). Investigation of thermal Performance of Unidirectional Flow Porous Bed Solar Air Heater Using MLP, GRNN, and RBF Models of ANN Technique. Therm. Sci. Eng. Prog. 6, 226–235. doi:10.1016/j.tsep.2018.04.006
Jiang, J., Cong, X., Li, S., Zhang, C., Zhang, W., and Jiang, Y. (2021). A Hybrid Signal-Based Fault Diagnosis Method for Lithium-Ion Batteries in Electric Vehicles. IEEE Access 9, 19175–19186. doi:10.1109/ACCESS.2021.3052866
Kara, A. (2021). A Data-Driven Approach Based on Deep Neural Networks for Lithium-Ion Battery Prognostics. Neural Comput. Appl., 1–14. doi:10.1007/s00521-021-05976-x
Li, D., Zhang, Z. S., Liu, P., Wang, Z., and Zhang, L. (2020). Battery Fault Diagnosis for Electric Vehicles Based on Voltage Abnormality by Combining the Long Short-Term Memory Neural Network and the Equivalent Circuit Model. IEEE Trans. Power Electron. 36, 1303–1315. doi:10.1109/TPEL.2020.3008194
Meng, Q. B., Zhao, H. W., and Sun, R. C. (2017). Research on Fault Diagnosis of Battery Pack Based on BP Neural Network Algorithm. Automation and instrumentation. 11, 45–47. doi:10.14016/j.cnki.1001-9227.2017.11.045
Ni, S. J. (2014). Research of Young Female Body Shape Recognition Based on Longitudinal Section Curve Form. Hangzhou: Zhejiang Sci-Tech University Press.
Niri, M. F., Dinh, T. Q., Yu, T. F., Marco, J., and Bui, T. M. N. (2020). State of Power Prediction for Lithium-Ion Batteries in Electric Vehicles via Wavelet-Markov Load Analysis. IEEE Trans. Intell. Transport. Syst. 99, 1–16. doi:10.1109/tits.2020.3028024
Schmid, M., Gebauer, E., Hanzl, C., and Endisch, C. (2021). Active Model-Based Fault Diagnosis in Reconfigurable Battery Systems. IEEE Trans. Power Electron. 36 (3), 2584–2597. doi:10.1109/TPEL.2020.3012964
Schmid, M., Kneidinger, H. G., and Endisch, C. (2020). Data-Driven Fault Diagnosis in Battery Systems through Cross-Cell Monitoring. IEEE Sensors J. 99, 1.
Shi, J. P., Huang, H. M., Xue, S. M., and Li, B. J. (2021). Research on Seismic Signal Classification and Recognition Based on PSO-SVM. Comput. Digital Eng. 380 (6), 1037–1046.
Song, H. W. (2020). Research on Fault Detection of Photovoltaic Array Based on Probabilistic Neural Network. Zibo: Shandong University of Technology Press. doi:10.1109/cac51589.2020.9327582
Specht, D. F. (1991). A General Regression Neural Network. IEEE Trans. Neural Netw. 2 (6), 568–576. doi:10.1109/72.97934
Sun, L. C. (2014). Study on Horizontal Displacement Prediction of Retaining Structure of Deep Foundation Pit Based on Generalized Regression Neural Network. Beijing: China University of Geosciences (Beijing) Press.
Tian, J., Wang, Y., and Chen, Z. (2020). Sensor Fault Diagnosis for Lithium-Ion Battery Packs Based on Thermal and Electrical Models. Int. J. Electr. Power Energ. Syst. 121, 106087. doi:10.1016/j.ijepes.2020.106087
Wen, X., Li, X., and Zhang, X. W. (2014). The Application of Matlab Neural Network. Beijing: National Defense Industry Press. doi:10.1109/icmc.2014.7231590
Yao, L., Fang, Z., Xiao, Y., Hou, J., and Fu, Z. (2021). An Intelligent Fault Diagnosis Method for Lithium Battery Systems Based on Grid Search Support Vector Machine. Energy 214, 118866. doi:10.1016/j.energy.2020.118866
Yao, L., Xiao, Y., Gong, X., Hou, J., and Chen, X. (2020). A Novel Intelligent Method for Fault Diagnosis of Electric Vehicle Battery System Based on Wavelet Neural Network. J. Power Sourc. 453 (453), 227870. doi:10.1016/j.jpowsour.2020.227870
Zhang, D. T. (2019). Design of Photovoltaic Power Prediction System Based on GA-WNN and GRNN Combined Algorithm. Shenyang: Shenyang Institute of Engineering Press.
Keywords: fault diagnosis, lithium-ion battery packs, RBF, neural network, battery safety
Citation: Wang J, Zhang S and Hu X (2021) A Fault Diagnosis Method for Lithium-Ion Battery Packs Using Improved RBF Neural Network. Front. Energy Res. 9:702139. doi: 10.3389/fenrg.2021.702139
Received: 29 April 2021; Accepted: 21 July 2021;
Published: 03 August 2021.
Edited by:
Xiaogang Wu, Harbin University of Science and Technology, ChinaReviewed by:
Haijun Ruan, Imperial College London, United KingdomCopyright © 2021 Wang, Zhang and Hu. This is an open-access article distributed under the terms of the Creative Commons Attribution License (CC BY). The use, distribution or reproduction in other forums is permitted, provided the original author(s) and the copyright owner(s) are credited and that the original publication in this journal is cited, in accordance with accepted academic practice. No use, distribution or reproduction is permitted which does not comply with these terms.
*Correspondence: Shenglong Zhang, c3Vja2Vyc2FuZHM4OEAxNjMuY29t
Disclaimer: All claims expressed in this article are solely those of the authors and do not necessarily represent those of their affiliated organizations, or those of the publisher, the editors and the reviewers. Any product that may be evaluated in this article or claim that may be made by its manufacturer is not guaranteed or endorsed by the publisher.
Research integrity at Frontiers
Learn more about the work of our research integrity team to safeguard the quality of each article we publish.