- 1Escola de Química, Universidade Federal do Rio de Janeiro (UFRJ), Rio de Janeiro, Brazil
- 2Instituto de Química, Universidade Federal do Rio de Janeiro (UFRJ), Rio de Janeiro, Brazil
- 3INCT Energia e Ambiente, Bahia, Brazil
The production of solketal fuel additive was studied from the reaction of glycerol and acetone in the presence of pressurized CO2 as switchable catalyst. A design of experiments (DoE) was used to study the significance of temperature, initial pressure of CO2, glycerol/acetone molar ratio, and reaction time. The response variable was the glycerol conversion that was analyzed by GC-MS. Temperature, reaction time and initial pressure of CO2 were statistically significant whereas the molar ratio of glycerol/acetone was not. The maximum conversion at the optimal conditions (118°C, 42 bar and 5 h) was 61%. Reactions with glycerol doped with common contaminants present in the glycerin of biodiesel production was also carried out. Water has a drastic effect on the conversion, as well as the concomitant addition of water and NaCl. Reactions with a glycerin of biodiesel production, using NaOH or Ba(OH)2 as catalyst of transesterification, gave 6 and 20% conversion, respectively.
Introduction
The utilization of biofuels is expanding because of the environmental impact caused by the massive use of fossil fuels and emissions of carbon dioxide in the atmosphere. Biodiesel is one of the main biofuels used worldwide (Andrade et al., 2005). It is mainly produced by the transesterification of oils and fats, which produce glycerol as byproduct. The widespread consumption of biodiesel has reduced the price of glycerol, which is produced in ~10 wt% in the transesterification of vegetable oils to afford the biodiesel. Glycerol is used in a variety of applications such as surfactants, emulsifiers, solvents, humectants, lubricants, and cosmetics. Nevertheless, these applications cannot drain the large amounts of glycerol being produced today (Pinto and Mota, 2014; Pinto et al., 2017).
The chemical transformation of glycerol into more valuable products has been extensively studied. Etherification of glycerol with different alcohols has been reported to yield potential oxygenated fuel additives (Klepáčová et al., 2003; Mota et al., 2009; Pinto et al., 2016). The acid-catalyzed reaction of glycerol with isobutene generates tert-butyl-glyceryl ethers, which can be used as bioadditives (Klepacova et al., 2005). Propene can be produced from the selective hydrogenolysis of glycerol over supported metal catalysts (Mota et al., 2016). Glycerol carbonate can be produced through the carbonation of glycerol with CO2 over metal oxide catalysts (Guerra et al., 2015). Oxidative dehydration of glycerol to acrylic acid has been studied over vanadium-impregnated zeolite Beta (Pestana et al., 2013). Acetylation of glycerol with acetic acid or acetic anhydride yield the acetins, which are also potential fuel additives (Gonçalves et al., 2008; Dodson et al., 2014a,b).
The acetalization/ketalization of glycerol has been studied under different conditions and catalysts (da Silva et al., 2009 and Oliveira et al., 2016). Solketal, the product of the acid-catalyzed reaction of glycerol with acetone, has proven to be a good additive for gasoline, improving the octane number and reducing gum formation (Mota et al., 2010; Silva et al., 2010). Nevertheless, the use of crude glycerol, with impurities coming from the biodiesel production process, significantly affects the activity of the catalysts (da Silva and Mota, 2011), requiring purification steps, which may impact the final costs.
The most common catalysts used in the acetalization of glycerol are acid heterogeneous catalysts. Solid acids deactivate when impure glycerin is used (da Silva and Mota, 2011). Besides that, heterogeneous catalysts present many disadvantages: final disposal problems when life cycle is over, difficult to study, due to its complex structure, most of them are highly expensive and some of them are oil derivatives. Thus, CO2 appears to be the most suitable choice in a green chemistry context, as it is low cost (can be captured from the atmosphere), it is easily recovered from the reaction medium and can be reused.
There is a continuous interest in CO2 utilization owing to the environmental impacts that its emission causes in the atmosphere. The dry reforming of methane has been widely investigated, as it converts two greenhouse gases (Valderrama et al., 2013). Hydrocarbons can be produced from CO2 by combining the reverse water gas shift and Fischer-Tropsch synthesis (Dimitriou et al., 2015). CO2 is also a raw material for the production of carbonates, like methyl carbonate, ethylene carbonate and glycerol carbonate. High pressure CO2-H2O has been used in the valorization of lignocellulosic and starch-based biomass to produce chemicals and other value-added products (Relvas et al., 2015). CO2 has been used as a catalyst for the reaction of amines and NO2 to produce nitrosamine (Sun et al., 2011).
It is known that a compressible gas dissolved in an organic solvent can be converted in a new liquid compound with different properties (Herrero et al., 2017). For this reason, it is acceptable to think that CO2 dissolved in alcohols, at high pressures, can be converted in carbonic acids in a reversible way. Thus, acid-catalyzed reactions can be potentially carried out in these medium, with the concept of switchable catalysts. Upon pressurizing the reactants with CO2, an acidic medium is formed through the formation of carbonic acids. After reaction and pressure release, the carbonic acid is decomposed yielding only the products and non-converted reactants.
There are many studies reporting the use of heterogeneous acid catalysts for the production of solketal. Nevertheless, many of them are quite expensive or produced from fossil sources. In addition, they are highly affected if crude glycerin of biodiesel production is used as feedstock, because the main impurities present in the glycerol phase deactivate the acid catalysts (da Silva and Mota, 2011). Therefore, the use of CO2 as a switchable catalyst may be an option, due to its easily recovery from the reaction medium for reuse and the possibility of neutralizing any hydroxide base present in the glycerol. In this contribution, we wish to report the use of CO2 as switchable catalyst in the reaction of glycerol with acetone to produce solketal (Scheme 1).
Materials and Methods
Experimental Procedure
Pure Glycerol Experimental Tests
Glycerol 99.5% Vetec® and acetone 99.9% Vetec® were introduced in a 100 mL Parr® reactor that was mechanically stirred at 500 rpm to ensure a good mixing of reactants. The system was then pressurized with CO2 and heated to the desired temperature. At the end, the pressure was released and the products were analyzed by GC-MS to obtain the glycerol conversion. Blank reactions of glycerol with acetone under N2 pressure were also carried out for comparison purpose.
Doped Glycerol Experimental Tests
Glycerol Vetec®, acetone Vetec®, and contaminants (Methanol Vetec®, water and NaCl Vetec®) were introduced in a 100 mL Parr® reactor that was mechanically stirred at 500 rpm to ensure a good mixing of reactants. The system was then pressurized with CO2 and heated to the desired temperature. At the end, the pressure was released and the products were analyzed by GC-MS to obtain the glycerol conversion. Experiments with doped and crude glycerin were carried out at the optimum condition found in the previous analysis. The content of the contaminants refers to the amount of glycerol in the system.
Biodiesel Production
Soybean oil transesterification was performed to obtain crude glycerin. Soybean oil was added to a stirred reactor and heated to 60°C. A methanol/NaOH solution was then added to the reactor (a mixture of 1 g of NaOH Vetec® and 35 mL of methanol, for each 100 mL of oil used). After 40 min of vigorous stirring (1,500 rpm), the reaction was then stopped and settled to decant to separate the two phases. The excess of methanol was removed from the glycerin phase under reduced pressure in a rotary evaporator and used in the solketal production.
It was also obtained crude glycerin from the transesterification of soybean oil with methanol catalyzed by Ba(OH)2 Vetec®. Ba(OH)2 was heated to 100°C (10°C/min). The pre-heated solid was then added to a glass reactor containing soybean oil and Methanol, considering 1:6 molar ratio and 2% m/m of catalyst. The mixture was heated to 60°C. After 90 min of vigorous stirring (1,500 rpm), the reaction was then stopped and settled to decant to separate the two phases. The excess of methanol was removed from the glycerin phase under reduced pressure in a rotary evaporator and used in the solketal production.
Product Analysis
Glycerol conversion and solketal production was obtained with the aid of an Agilent 6850 gas chromatograph coupled to an Agilent 5973 mass quadrupole spectrometer, operating in electron impact ionization (70 eV) and using a column of methyl-phenyl-silicone (30 m × 250 μm × 0.25 μm.). Analyses were carried out with the temperature increasing from 30 to 120°C (with a slope of 10°C/min). The results were computed considering the average of two injections.
Experimental Design
In order to first identify the important factors affecting the reaction, a factorial design 24 with three central points was used. The factors studied were temperature, reaction time, initial CO2 pressure and glycerol/acetone molar ratio, whose levels were, respectively, 80–110°C, 2–4 h, 20–45 bar, and 1:2–1:5. By applying the analysis of variance (ANOVA), the statistically significant factors were identified and a search for a region where the conversion is maximum was done by using the steepest ascent method. After that, a central composite design was performed and the optimum factor levels were found where the conversion reached a maximum value.
Results and Discussion
Optimization of the Reaction Conditions
Because pressure and temperature would act in opposite directions in the experiments of solketal production with CO2 was switchable catalyst, we decided to carry out a design of experiments (DoE) to assess which parameter would be the most important. Increasing temperature would accelerate the reaction, although it would decrease the solubility of CO2 in the medium. On the other hand, higher pressures would favor the dissolution of CO2, although not having a great impact in the reaction rate. An analysis of variance (ANOVA) showed that the molar ratio was the only factor non-statistically significant (Supplementary Material). Thus, a 1:2 glycerol/acetone molar ratio was chosen to run the next experiments to search a region where the glycerol conversion was maximum. This region was 100–130°C, 30.5–55.5 bar, and 3.2–5.2 h, for temperature, pressure and time, respectively. After that, a central composite design was performed and the optimum factor levels were found, where the conversion reached a maximum value. The results are shown in Table 1.
Upon the analysis of the ANOVA data (Supplementary Material), one can conclude that only the quadratic terms of pressure and temperature and the linear term of time are statistically relevant, considering 5% of significant level. The quadratic term of time and the interaction term between pressure and temperature were marginally significant (0.05 < p-level ≤ 0.1). The most important factor was the quadratic initial pressure, followed by the quadratic temperature and linear time.
The mathematical model, in terms of the original variables, is given by Equation (1), considering all terms, as the coefficient of determination (R2) obtained was 0.94; the residuals are normal and the variance is homogeneous. The parameter standard deviations were at least one order of magnitude lower than the respective parameter values, as it needs to be.
The surface and contour plots are shown in Figure 1.
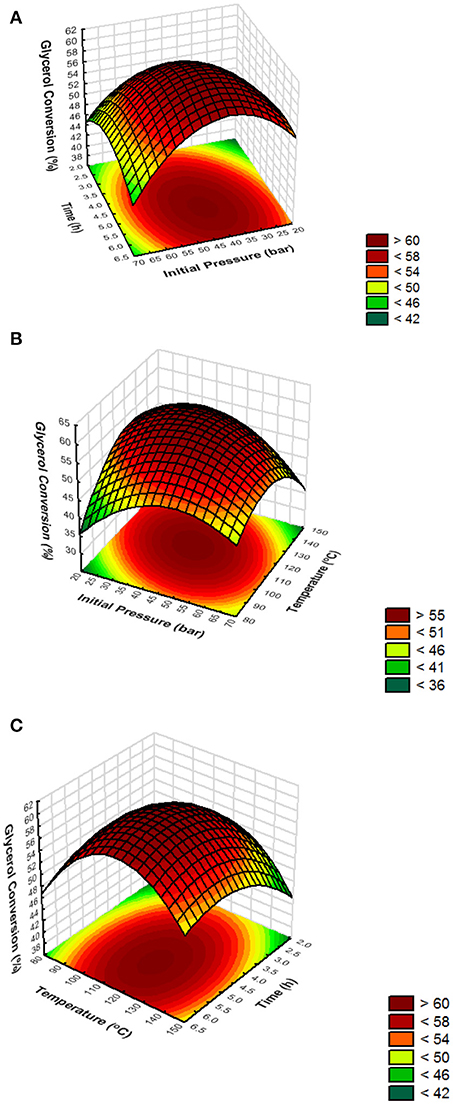
Figure 1. Response Surface of time against initial pressure (A); temperature against initial pressure (B) and temperature against time (C).
By analyzing the three curves, it is possible to see that the glycerol conversion reaches a maximum of 60.2%, at 42.2 bar, 5.0 h and 118°C of initial pressure, time and temperature, respectively. Experimental tests at these optimal conditions were carried out with two replicates and the glycerol conversion was 60.6% ± 1.2, consistent with the predicted value. This result is lower than the values found with heterogeneous catalysts, such as Amberlyst-15, zeolite Beta and Montmorillonite (da Silva et al., 2009). The explanation is associated with the strength of the acid catalyst. Whereas Amberlyst-15 and zeolite Beta present strength similar to concentrated solutions of H2SO4 (Mota et al., 2016), carbonic acid derivatives are significantly weaker.
Influence of Impurities
We have shown (da Silva and Mota, 2011) that glycerol containing common contaminants of biodiesel production, such as methanol coming from incomplete distillation, NaCl formed upon the neutralization of the base catalyst and water may significantly affect the conversion of the acid-catalyzed ketalization to yield solketal, due to neutralization or weakening of the acid strength. On the other hand, excessive purification of the glycerol would increase the costs. Since the formed carbonic acid may be less affected by the presence of these impurities, we decided to test glycerol doped with given amounts of water, methanol and NaCl to check the influence on the conversion to solketal.
Figure 2 shows the results at the optimized reaction conditions of 42 bar, 5 h and 118°C for different composition of glycerol doped with the most common impurities found the glycerol of biodiesel production. The addition of methanol slightly decreases the conversion, especially with 5% of this compound. This is probably because this alcohol may react with acetone to form ketals too. Water has a more pronounced effect on the conversion. Addition of 15 wt% of water drops the conversion to 32%. The results can be explained by the fact that ketalization is a reversible reaction and water is formed as product. Thus, when water is present in the medium, the equilibrium may be shifted and lower conversions are observed. Another possible explanation is that water may interact with the formed carbonic acid through hydrogen bonds, which ultimately leads to the stabilization of the species and decrease of the catalytic activity. On the other hand, the addition of 5% of NaCl did not affect the conversion, whereas 10% of salt increases the glycerol conversion to 70%. Probably, the dissociated salt can be partially converted in HCl, and this acid can also show some catalytic activity, increasing the overall conversion.
The simultaneous addition of methanol and water leads to a conversion of 41%, which stress the predominant effect of water on the conversion, since the value is almost the same when water was added to glycerol. The simultaneous addition of water and NaCl have a great impact on the conversion, which decreases to around 30%. Besides the effect of the water on the equilibrium of the reaction, the significant decrease in the conversion indicates a more complex behavior of the system. A possible explanation is the solvation of the NaCl by glycerol and water molecules, which would decrease its reactivity. Nevertheless, the present data cannot clearly explain the results found when water and NaCl are added to the medium to simulate the behavior of the glycerin from biodiesel production. It is worthy to mention that the same trend was observed with the use of Amberlyst-15 and zeolite Beta as catalyst (da Silva and Mota, 2011). Even with the use of pressurized CO2, the impurities, mainly water and NaCl, greatly affect the conversion, indicating that some purification of the glycerin of biodiesel production is necessary.
We also tested the crude glycerin obtained from biodiesel production, using NaOH or Ba(OH)2 as catalysts. The idea was to pressurize the system with CO2 to form the respective carbonate. The excess CO2 would catalyze the reaction of glycerol with acetone upon the formation of carbonic acid. The conversion was 6% for the glycerin containing NaOH and 20% for the glycerin containing Ba(OH)2 (Table 2). In both experiments, there was formation of the respective carbonates. Since barium carbonate is less soluble in the reaction medium than sodium carbonate and it precipitated during the reaction. These results indicate that the presence of dissolved salts affects the reaction, probably because of the role of the glycerol molecule in solvation the ions. Hence, the higher conversion observed for the glycerin containing Ba(OH)2 may be explained by the precipitation of BaCO3.
Although the absolute conversion was still low (20%), the experiment indicated that crude glycerin of biodiesel production could be transformed in a valuable fuel additive without any further purification.
Conclusions
The reaction of glycerol with acetone was carried out with pressurized CO2 as switchable catalyst. A DoE showed that temperature, reaction time and initial pressure of CO2 are significant factors and have positive influence in the reaction. The maximum conversion of 61% was obtained at 118°C, 42 bar and 5 h reaction time, as predicted in the DoE. This value was lower than the conversions observed in the literature with the use of other heterogeneous catalysts, such as Amberlyst-15 and zeolite Beta, and ascribed to the weaker acid strength of the formed carbonic acid.
Experiments with glycerol doped with methanol, NaCl and water, which are found in the glycerin of biodiesel production, showed that water and water plus NaCl have a major effect in the conversion. Reactions with the glycerin from biodiesel production, containing NaOH or Ba(OH)2, without any purification or treatment gave conversion up to 20%. The results were interpreted in terms of formation of the respective carbonate that remains, at least partly, dissolved in the medium.
Data Availability
All datasets generated for this study are included in the manuscript and/or the Supplementary Files.
Author Contributions
BP, JN, VC, and CM contributed to the conception and design of the study. JN was the researcher who carried out the laboratory work. JN and BP organized the database. JN and VC performed the statistical analysis. JN wrote the first draft of the manuscript. BP, JN, VC, and CM wrote sections of the manuscript. All authors contributed to manuscript revision, read and approved the submitted version.
Funding
Authors thank CNPq, Capes, and Faperj for financial support.
Conflict of Interest Statement
The authors declare that the research was conducted in the absence of any commercial or financial relationships that could be construed as a potential conflict of interest.
Supplementary Material
The Supplementary Material for this article can be found online at: https://www.frontiersin.org/articles/10.3389/fenrg.2019.00058/full#supplementary-material
References
Andrade, J. B., Pinto, A. C., Guarieiro, L. L. N., Rezende, M. J. C., Ribeiro, N. M., Torres, E. A., et al. (2005). Biodiesel: an overview. J. Braz. Chem. Soc. 16, 1313–1330. doi: 10.1590/S0103-50532005000800003
da Silva, C. X. A., Gonçalves, V. L. C., and Mota, C. J. A. (2009). Water-tolerant zeolite catalyst for the acetalisation of glycerol. Green Chem. 11:38. doi: 10.1039/B813564A
da Silva, C. X. A., and Mota, C. J. A. (2011). The influence of impurities on the acid-catalyzed reaction of glycerol with acetone. Biomass Bioenergy 35, 3547–3551. doi: 10.1016/j.biombioe.2011.05.004
Dimitriou, I., García-Gutiérrez, P., Elder, R. H., Cuellar-Franca, R., Azapagic, A., and Allen, R. W. K. (2015). Carbon dioxide utilisation for production of transport fuels: process and economic analysis. Energy Environ. Sci. 8, 1775–1789. doi: 10.1039/C4EE04117H
Dodson, J. R., Avelar, T., Nascimento, J. A. C., and Mota, C. J. A. (2014a). Glycerol acetals with antioxidant properties. Pure Appl. Chem. 86, 905–912. doi: 10.1515/pac-2013-1106
Dodson, J. R., Leite, T. C. L., Pontes, N., Pinto, B. P., and Mota, C. J. A. (2014b). Green acetylation of solketal and glycerol formal by heterogeneous acid catalysts to form a biodiesel fuel additive. ChemSusChem. 7, 2728–2734. doi: 10.1002/cssc.201402070
Gonçalves, V. L. C., Pinto, B. P., Silva, J. F. C., and Mota, C. J. A. (2008). Acetylation of glycerol catalyzed by different solid acids. Catal. Today 133–135, 673–677. doi: 10.1016/j.cattod.2007.12.037
Guerra, A. C. O., Mota, C. J. A., Turci, C. C., Sousa-Aguiar, E. F., Miranda, J. L., Ozório, L. P., et al. (2015). Metal-impregnated zeolite Y as efficient catalyst for the direct carbonation of glycerol with CO2. Appl. Catal. 504, 187–191. doi: 10.1016/j.apcata.2014.12.010
Herrero, M., Mendiola, J. A., and Ibánez, E. (2017). Gas expanded liquids and switchable solvents. Curr. Opin. Green. Sustain. Chem. 5, 24–30. doi: 10.1016/j.cogsc.2017.03.008
Klepáčová, A., Mravec, D., Hájeková, E., and Bajus, M. (2003). Etherification of glycerol. Pet. Coal. 45, 54–57. Available online at: http://www.vurup.sk/wp-content/uploads/dlm_uploads/2017/07/pc_1_2_03_klepacova_54_57.pdf
Klepacova, A., Mravec, D., Hajekova, E., and Bajus, M. (2005). Catalytic etherification of glycerol with alcohols. Appl. Catal. A 294, 141–147. doi: 10.1016/j.apcata.2005.06.027
Mota, C. J. A., da Silva, C. R. B., Gonçalves, V. L. C., and Lachter, E. R. (2009). Etherification of glycerol with benzyl alcohol catalyzed by solid acids. J. Braz. Chem. Soc. 20, 201–204. doi: 10.1590/S0103-50532009000200002
Mota, C. J. A., da Silva, C. X. A., Rosenbach, N. Jr., Costa, J., and da Silva, F. (2010). Glycerin derivatives as fuel additives: the addition of glycerol/acetone ketal (solketal) in gasolines. Energy Fuels 24, 2733–2736. doi: 10.1021/ef9015735
Mota, C. J. A., Gonçalves, V. L. C., Mellizo, J. E., Rocco, A. M., Fadigas, J. C., and Gambetta, R. (2016). Green propene through the selective hydrogenolysis of glycerol oversupported iron-molybdenum catalyst: the original history. J. Mol. Catal. A Chem. 422, 158–164. doi: 10.1016/j.molcata.2015.11.014
Oliveira, P. A., Souza, R. O. M. A., and Mota, C. J. A. (2016). Atmospheric pressure continuous production of solketal from the acid-catalyzed reaction of glycerol with acetone. J. Braz. Chem. Soc. 27, 1832–1837. doi: 10.5935/0103-5053.20160066
Pestana, C. F. M., Guerra, A. C. O., Ferreira, G. B., Turci, C. C., and Mota, C. J. A. (2013). Oxidative dehydration of glycerol to acrylic acid over vanadium-impregnated zeolite Beta. J. Braz. Chem. Soc. 24, 100–105. doi: 10.1590/S0103-50532013000100014
Pinto, B. P., de Lima, A. L., and Mota, C. J. A. (2017). Glycerol: A Versatile Renewable Feedstock for the Chemical Industry. Rio de Janeiro: Advances in Biorefineries: Biomass and Waste Supply Chain Exploitation.
Pinto, B. P., and Mota, C. J. A. (2014). “Developments in glycerol byproduct-based biorrefineries,” in Advances in Biorefineries. Biomass and Waste Supply Chain Exploitation 1, eds B. P. Pinto, C. J. A. Mota, L. A. Pfaltzgraff, J. H. Clark, T. R. Brown, M. M. Wright, et al. (Cambridge: Woodhead Publishing; Elsevier, 364–385.
Pinto, B. P., Nascimento, J. A. C., Lyra, J. T., and Mota, C. J. A. (2016). Ethers of glycerol and ethanol as bioadditives for biodiesel. Fuel 168, 76–80. doi: 10.1016/j.fuel.2015.11.052
Relvas, F. M., Morais, A. R. C., and Bogel-Lukasik, R. (2015). Selective hydrolysis of wheat straw hemicellulose using high-pressure CO2 as catalyst. RSC Adv. 5:73935. doi: 10.1039/C5RA14632A
Silva, P. H. R., Gonçalves, V. L. C., and Mota, C. J. A. (2010). Glycerol acetals as anti-freezing additives for biodiesel. Bioresour. Technol. 101, 6225–6229. doi: 10.1016/j.biortech.2010.02.101
Sun, Z., Liu, Y. D., and Zhong, R. Z. (2011). Carbon dioxide in the nitrosation of amine: catalyst or inhibitor? J. Phys. Chem. A 115, 7753–7764. doi: 10.1021/jp202002m
Keywords: acetalization, glycerol, solketal, CO2, switchable catalyst, design of experiments
Citation: Nascimento JAC, Pinto BP, Calado VMA and Mota CJA (2019) Synthesis of Solketal Fuel Additive From Acetone and Glycerol Using CO2 as Switchable Catalyst. Front. Energy Res. 7:58. doi: 10.3389/fenrg.2019.00058
Received: 26 February 2019; Accepted: 03 June 2019;
Published: 25 June 2019.
Edited by:
Greeshma Gadikota, University of Wisconsin-Madison, United StatesReviewed by:
Hui Zhou, ETH Zürich, SwitzerlandDeepika Malhotra, Pacific Northwest National Laboratory (DOE), United States
Copyright © 2019 Nascimento, Pinto, Calado and Mota. This is an open-access article distributed under the terms of the Creative Commons Attribution License (CC BY). The use, distribution or reproduction in other forums is permitted, provided the original author(s) and the copyright owner(s) are credited and that the original publication in this journal is cited, in accordance with accepted academic practice. No use, distribution or reproduction is permitted which does not comply with these terms.
*Correspondence: Bianca P. Pinto, cGludG8uYmlhbmNhQGdtYWlsLmNvbQ==