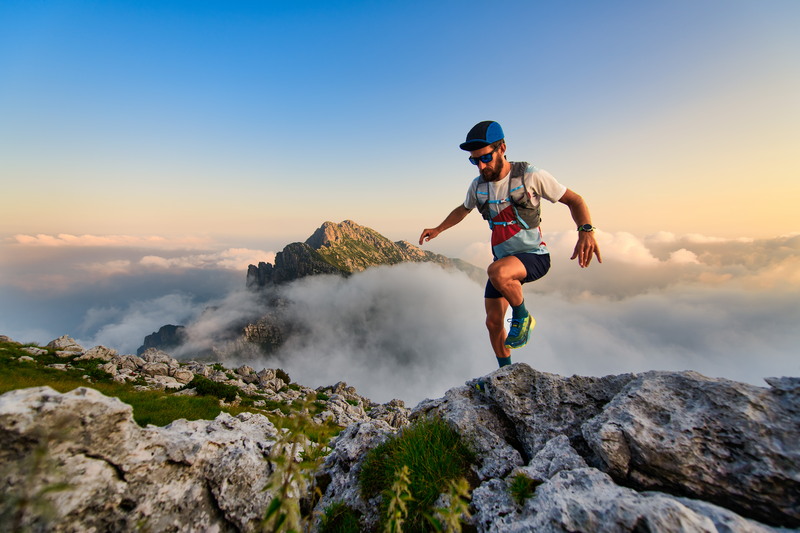
95% of researchers rate our articles as excellent or good
Learn more about the work of our research integrity team to safeguard the quality of each article we publish.
Find out more
ORIGINAL RESEARCH article
Front. Earth Sci. , 30 May 2023
Sec. Interdisciplinary Climate Studies
Volume 11 - 2023 | https://doi.org/10.3389/feart.2023.1196898
This article is part of the Research Topic Curbing Global Warming with Underground Mine Space for Energy Storage View all 6 articles
In order to cope with multi-dimensional mine disasters in deep mines, enhance the adaptability of the open tunnel-boring machine (TBM) to the actual mine working face environment, and improve the excavation speed of the open TBM, based on the excavation project of Gaojiapu Coal Mine in Zhengtong Coal Industry, Shaanxi Province, this paper comprehensively considers the difficulties encountered by the TBM in the excavation process and improves the open TBM system and its supporting equipment. The research shows that removing the redundant system and supporting equipment of the open TBM can effectively solve the difficulties of the TBM entering the mine, such as loading and unloading, and turning; optimizing the open TBM shield, shortening the main beam, and setting the support platform and jumbolter system on the main beam can deal with the problem that the TBM support is not timely and easy to jam. Opening circular holes and installing slag cleaning guide plates on the main beam of the open TBM can timely clean up the waste slag on the main beam and protect the main beam from deformation. Installing a slag cleaning bucket wheel machine between the main beam of the open TBM and the trailer can reduce the accumulation of waste slag on the road ahead. Compared with ordinary excavation construction technology, the monthly average footage level of the open TBM after technical improvement is 300.88 m, which is 3.8 times that of the rock roadway general excavation and 1.6 times that of the rock roadway comprehensive excavation.
With the decrease in the shallow coal seam, coal mining has begun to move to deep mining (Chun et al., 2023) and the mine environment will certainly become more complex. The environment of the deep roadway excavation face is very complex, has high ground pressure (Fan et al., 2019) (Liang et al., 2022) (Fan et al., 2020a), high ground temperature (Zhang et al., 2017), high gas (Fan et al., 2020b), high confined water (Guo et al., 2019), and soft rock, and other disasters are full of roadway. The traditional roadway excavation construction technology has not been well qualified for the excavation work under complex geological conditions in deep mines (Yuan and Zhang, 2023). The excavation construction technology of the mining industry needs to be reformed, and advanced intelligent equipment should be introduced to replace the old piece of equipment to improve the excavation speed and ensure production progress.
Because the tunnel boring machine (TBM) has the advantages of high work efficiency (Wu et al., 2021a), strong applicability (Wei et al., 2019), strong safety and reliability (Wen et al., 2022), and good roadway forming, it is widely used in railways, subways, and other industries. The traditional excavation construction technology is very slow in the complex geological roadway, which causes tension in the follow-up work of the mine and seriously affects the economic benefits of the enterprise. In recent years, there have been more and more research studies on the TBM. He et al. (2013) proposed that the adaptability of the TBM to roadway should be improved according to the surrounding rock conditions and TBM models after comparing different roadway excavation construction technologies. Tan et al. (2022) proposed 11 evaluation indexes for TBM tunneling adaptability combined with the actual conditions of the tunnel and optimized the evaluation indexes. Zhang et al. (2022) used the Bi-GRU-ATT model to study the prediction of TBM tunnel parameters, and the research shows that the model can help the TBM to make intelligent decision analysis. Wu et al. (2021b) proposed a method of mutual feedback perception between TBM equipment and the surrounding rock by using the deep neural network (DNN) combined with tunnel surrounding rock parameters. Mao et al. (2015) developed a new type of TBM automatic positioning control system, which can solve the problems of low accuracy, complex operation, and time consumption of the previous TBM control system. Du et al. (2022) not only simplified the installation of TBM disc props but also developed a manipulator to assist in replacing props, which reduced the labor intensity of TBM maintenance personnel and improved the safety factors of underground work. He et al. (2022) developed a new TBM slag removal robot for cleaning the waste slag at the bottom of the tunnel, which can effectively remove the waste slag at the bottom of the open TBM.
So far, research studies on the TBM mainly focus on the adaptability evaluation of the excavation face, tunnel model prediction, and other operations. There are few studies on the improvement of the TBM system and its supporting equipment (Sun et al., 2018). Therefore, based on the working environment of the Gaojiapu Coal Mine in the Zhengtong Coal Industry of Shaanxi Province, this paper will study the technical improvement of the open TBM system and supporting equipment so that the open TBM can better adapt to the environment of the Gaojiapu Coal Mine excavation face and improve the efficiency of excavation work. In addition, the open TBM construction causes less disturbance to the surrounding rock and can form a neat roadway section, which is conducive to the future use of underground mine empty areas to build oil and gas storage (Qiu et al., 2023) (Zhang et al., 2023) (Qiu et al., 2022) (Fan et al., 2016) (Wang et al., 2023) (Chen et al., 2020) (Zhao et al., 2023) (Fan et al., 2020c). Finally, by comparing the excavation workload generated by different excavation construction techniques in the Gaojiapu Coal Mine, the advantages of using the improved open TBM are objectively evaluated. It provides a new solution for mines with poor geological conditions and low excavation–construction efficiency such as Gaojiapu, and also accumulates valuable experience for the application of the TBM in deep mine multi-coupling disaster mines.
The Gaojiapu Coal Mine of the Zhengtong Coal Industry in Shaanxi Province is located in the northwest of the Binchang mining area, and the detailed location distribution is shown in Figure 1. The area of the Gaojiapu Coal Mine is 219 km2, the buried depth of the mine is 1,000–1,100 m, the coal reserves are 974 million tons, and the service life is expected to be 62.5 years. The roadway developed in the Gaojiapu Coal Mine comprises mainly four rock roadways in the east and west areas, respectively. The total amount of roadway development is 31,800 m, and 4,870 m have been completed. The remaining work tasks are very heavy. Due to the influence of mine geological conditions, roadway excavation construction technology, and mine disasters, the excavation progress of the Gaojiapu Mine is very slow, and subsequent production work of the mine is seriously affected. According to the current mine production situation, if the construction technology of ordinary comprehensive excavation and blasting excavation is adopted, the Gaojiapu Mine will have a one-sided production situation of up to 1 year, when the working faces of the fourth and fifth plates are connected. Coal production will be reduced by about 1.5 million tons. Therefore, improving the speed of roadway excavation has become a key factor to solve the problem of tight production connection in the Gaojiapu Mine. The TBM has the advantages of fast excavation speed, high safety factor, and good roadway forming capability (Xie et al., 2023; Liu et al., 2023; Yang et al., 2023; Wang et al., 2020; Wang et al., 2022), which can solve the current technical problems in the Gaojiapu Mine. After full investigation and technical demonstration, combined with the actual working conditions of the roadway excavation face, the open TBM was finally selected as the new piece of roadway excavation equipment to solve the problems of slow roadway excavation speed and tight mine production connection in the Gaojiapu Coal Mine.
The Gaojiapu Coal Mine has the characteristics of complex geological conditions and multiple coupling of disasters. The following problems need to be considered when using the open TBM in this mine.
(1) The roadway space is limited, and the open TBM has problems such as difficult entry, difficult loading and unloading, and difficult turning.
The Gaojiapu Coal Mine has the characteristics of large coal seam depth, small roadway section, and limited roadway space. In addition, the size of the auxiliary shaft cage in the Gaojiapu Coal Mine is 5.8 m long, 2.5 m wide, and 3.8 m high. The maximum lifting load of the cage is only 37 t. The size of the flat car in the roadway of the mine is 4.5 m long and 1.8 m wide, and the maximum bearing capacity is only 40 t. Because the existing open TBM systems and their supporting equipment have the disadvantages of large size, weight, and turning radius, and high difficulty in loading and unloading in the mine, it is not suitable for direct use in the Gaojiapu Coal Mine. If it is put into the Gaojiapu Coal Mine without technical improvement, there will be problems such as difficult entry, difficult loading and unloading, and difficult turning. Therefore, in order to solve the aforementioned problems, it is necessary to simplify the existing open TBM system and supporting equipment in the market so that the open TBM can better adapt to the working environment of the Gaojiapu Coal Mine.
(2) The lithology changes greatly, the roadway formation is poor, and the open TBM has problems such as untimely support and easy jamming.
The stratum structure of the Gaojiapu Coal Mine is complex and changeable. The open TBM excavation inevitably passes through soft strata such as sandstone, sandy mudstone, and coal seam. When the open TBM passes through the soft strata, due to the soft rock strata of the roof and floor of the roadway and the excessive deformation of the surrounding rock, it is prone to collapse accidents such as roof fall and spalling, which leads to open TBM jamming (Ding et al., 2022a; Fan et al., 2021; Chen et al., 2014; Ding et al., 2022b; Liu et al., 2019; Ma et al., 2022). In order to solve the problem of TBM jamming, the existing open TBM generally installs a shield device to reduce the TBM jamming problem through the protective effect of the shield. However, some of the existing shields cannot freely expand and contract, and other expansion ranges are limited, which cannot play a supporting role in time and effectively when the weak surrounding rock is broken. In addition, the existing support technology of the open TBM needs to be supported manually, which has the disadvantages of slow support speed and high risk (Song et al., 2023) (Chen et al., 2022). If the open TBM is not supported in time, it will seriously threaten the safety of staff and equipment. Therefore, the open TBM used in the Gaojiapu Coal Mine needs to have the functions of timely support and preventing equipment jamming.
(3) The excavation distance of the roadway is long, the amount of waste slag is large, and the open TBM has the problem of untimely slag removal.
The roadway of the Gaojiapu Coal Mine was designed to have four main roadways in the east and west areas, respectively. The length of roadway development in the east area was 30,000 m, the length of roadway development in the west area was 31,800 m, and the length of the unexplored roadway in the east and west areas was 56,930 m. In summary, the Gaojiapu Coal Mine has the characteristics of long roadway distance, large excavation workload, and large amount of waste slag. However, the open TBM is comprehensive equipment that integrates multiple technologies and can quickly complete rock breaking, support, slag removal, and other operations. The amount of roadway development in the Gaojiapu Coal Mine is large, and the open TBM will produce a large amount of waste slag and congest the road during the construction process, resulting in the difficulty of the open TBM advancement. In addition, the Gaojiapu Mine has soft strata and the open TBM in the construction process will inevitably encounter roof fall, spalling, and other emergencies, making the waste slag directly fall on the main beam of the open TBM or through the finger shield gap to the main beam. As a result, the accumulation of waste slag in the inner cavity of the main beam affects the normal operation of the belt conveyor. In severe cases, it will squeeze the main beam to produce deformation and damage the main beam structure. Therefore, the open TBM used in the Gaojiapu Coal Mine must have the function of rapid slag removal; otherwise, a large amount of waste accumulation will inevitably affect the normal operation of the TBM.
Usually the TBM consists of systems for excavation, support, slag discharge, ventilation, dust removal, anti-impact, explosion-proof, and other systems (Zhang et al., 2021) and is equipped with a cutterhead, main drive, shield, gripper, trailer, and other supporting equipment (Wang et al., 2014). Due to the complexity of the open TBM system and supporting equipment, it is easy to cause the disadvantages of large size, weight, and turning radius, which is not suitable for the Gaojiapu Coal Mine with a small roadway section and limited roadway space. Therefore, the Shaanxi Zhengtong Coal Industry is based on the existing open TBM; combined with the actual working environment of the Gaojiapu Mine, the existing open TBM is improved to better adapt to the actual working environment of the Gaojiapu Mine.
In order to solve the problems of difficult entry, difficult loading and unloading, and difficult turning of the open TBM, first, the open TBM system and supporting equipment were simplified, and then, the redundant rear-supporting trailer was removed. Only four trailers were retained, and each trailer was connected by the universal joint. The first trailer was equipped with automatic jumbolters to anchor the monorail suspension equipment, and the idle position could be used to stack materials; the second trailer was equipped with a cooler and dust collector; the third trailer was equipped with a dust collector, a fan, and a wind storage tube, and a position reserved for the auxiliary gripper. On both sides of the fourth trailer, jumbolters were installed as the bottom angle support rigs, which are responsible for 1–2 bolts below the waist line. Second, according to the actual situation of the mine, the connection bridge and sprayed concrete system in the supporting equipment were canceled (practice found that it was not necessary). Third, an automatic correction device was added to the first wheel of each trailer (Figure 2). The automatic correction device can adjust the wheel direction of the trailer through the oil cylinder, thereby assisting the TBM to successfully complete the turning work. Finally, 15 suspension vehicles were equipped on the open TBM, and some supporting systems and equipment were suspended on the right monorail through the suspension vehicle. The size of each pulley was determined according to the size of the cage. The assembly method of the pulley was relatively simple. It only needed to be hoisted to the monorail crane beam and then connected with the ball hinge, without the need for a cumbersome assembly and splicing. Each pulley was equipped with independent pipelines and cables, which could be quickly installed and evacuated by connecting pipelines and cables. This not only removes unnecessary devices in the open TBM system and the supporting equipment but also reduces the assembly difficulty of the TBM system and supporting equipment. It also greatly reduces the workload of the assembly chamber layout and saved the preparation time before the TBM work. Figures 3, 4 show the schematic diagrams of the open TBM system and supporting equipment before and after simplification. The total length of the unsimplified open TBM is 167 m, and the total length of the simplified open TBM is only 75 m.
In order to solve the problems of untimely support and jamming of the open TBM shield when the surrounding rock is broken, first, the length of the shield connected to the cutterhead was shortened (Figure 5), and then, the top part of the shield was replaced with a finger shield capable of secondary expansion (Figure 6). The finger shield can use the oil cylinder to expand up and down, to achieve the purpose of timely support, reducing TBM jamming and ensuring roof safety. Second, the main beam of the open TBM was shortened to 14 m, and a movable support platform was arranged on the upper part of the main beam (Figure 7), which is not only conducive to the support work of the open TBM but also reduces the turning radius of the TBM. The specific methods are as follows: a large support platform was set on the upper part of the main beam in front of the gripper. The large support platform was welded by multiple steel plates and steel frame structures, and the steel frame structure was bolted to both sides of the main beam 1 and fixed with the large support platform. A multi-level partition support platform was arranged on the upper part of the main beam behind the gripper. By setting up a large support platform and a multi-level partition support platform, it is convenient for workers to complete the support work on the support platform. A propulsion cylinder was arranged under the large support platform to push the support platform for displacement, and the maximum distance of the platform forward was 1.2 m. When the TBM is excavating, by promoting the support platform, the jumbolters on the platform were supported, and the two could work together to improve the support efficiency. Third, eight jumbolter systems were set up on the support platform of the open TBM main beam (Figure 8), and the encoder was arranged at the bottom of the jumbolter. In this way, it can not only support the top, shoulder, and two sides of the roadway synchronously and quickly to significantly improve the support efficiency of open TBM but also accurately control the jumbolter to support the bolt and anchor cable at the designated position of the roadway surrounding rock to effectively improve the safety factors of underground work. Finally, in order to save manpower and improve the safety factors of underground work, the jumbolter was installed at the bottom of the fourth trailer to support the bolt and anchor cable at the bottom of the roadway to increase the support strength of the roadway and improve its safety.
In order to solve the problem of untimely cleaning of waste slag by the open TBM, first, a slag cleaning bucket wheel machine with a speed of 1r/min was set between the open TBM main beam and the first trailer (Figure 9), which is used to clean up the waste slag on the track in front of the trailer and transport it to the belt conveyor. The slag cleaning bucket wheel machine could be lifted by a lifting cylinder up to 300 mm. Second, the slag-skimming device was installed on the second wheel of the four trailers of the TBM to further clean up the falling rocks on the road. Third, multiple circular holes were added to the main beam of the open TBM (Figure 10). The belt conveyor was directly below the circular holes to facilitate the timely cleaning of the waste slag. Each circular hole was equipped with a corresponding cover, which can be sealed when not in use to maintain the internal ventilation of the main beam. This not only facilitates the cleaning and maintenance of the internal equipment of the main beam but also reduces the weight of the main beam and saves the manpower and material resources consumed in the assembly. It can also stack materials on the circular holes after the upper cover of the main beam to improve the space utilization rate. The specific practices are as follows: Figure 10 shows that the main beam was designed as a split structure, and the main beam 1 was connected to the main beam 2 by bolts. In order to solve the problem of waste slag accumulation on the main beam, four circular holes 1–4 were arranged on the main beam 1, in which the circular holes 3 and 4 were located directly below the circular holes 1 and 2, respectively, and the main beam 1 was penetrated. There were six circular holes 5–10 on the main beam 2, in which the circular holes 8–10 were located directly behind the circular holes 5–7, and the main beam 2 was penetrated. All circular holes had corresponding covers, which were connected with circular holes by hinges. Figure 11 shows that circular holes 1 and 2 are used to collect automatically dropped waste slag or manually clean the waste slag to the hole, and then let the waste slag pass through the main beam and fall on the belt from circular holes 3 and 4. In addition, the lower circular holes 3 and 4 can also be used to repair the equipment in the main beam and clean up the waste slag falling into the main beam. Side circular holes 5–10 are also used to repair the piece of equipment in the main beam and clean up the waste. Finally, a slag-cleaning guide plate device was set up on the upper part of the main beam of the open TBM, which can automatically collect the falling waste slag from the finger shield gap.
Table 1 is the statistical table of the footage level after different excavation–construction techniques are adopted in the Gaojiapu Coal Mine from January to August 2021. Table 1 shows that the total amount of the footage level of different tunneling construction technologies is in the order of the open TBM > rock roadway comprehensive excavation > rock roadway general excavation. According to the calculation of actual working months, it is found that the monthly average footage level of rock roadway general excavation and rock roadway comprehensive excavation is 79.17 m and 187.71 m, respectively. However, after the construction of the improved open TBM, the monthly average footage level is as high as 300.88 m. In addition, after further detailed calculation, it is found that the average daily footage levels of rock roadway general excavation and rock roadway comprehensive excavation are 2.62 m and 6.24 m, respectively, while the average daily footage level is 9.91 m after the improved open TBM construction. Compared with rock roadway general excavation and rock roadway comprehensive excavation, the monthly average footage level of the open TBM is nearly four times (3.8 times) and nearly two times (1.6 times) the construction speed of rock roadway general excavation and rock roadway comprehensive excavation, respectively. This shows that the improved open TBM in the Gaojiapu Coal Mine can adapt well to the environment of the roadway excavation face, significantly improve the excavation speed, and effectively alleviate the tension of production connection in the Gaojiapu Coal Mine. It also shows that improving the open TBM according to the working conditions of the mining site is conducive to improving the adaptability of the open TBM to the environment of the roadway excavation face.
(1) By removing the redundant rear-supporting trailer and installing the automatic correction device on the wheels of the remaining trailer, the problems of difficult entry, difficult loading and unloading, and difficult turning of the open TBM can be solved.
(2) By improving the open TBM shield, shortening the main beam and arranging the mobile support platform on the main beam, and then setting the anchor jumbolter system on the support platform, the problems of untimely support and easy jamming of the open TBM can be solved.
(3) By opening circular holes on the main beam of the open TBM, installing a slag-cleaning guide plate, and adding a slag-cleaning bucket wheel machine between the main beam and the trailer, the problem of untimely slag cleaning of the open TBM can be solved.
(4) Compared with the ordinary excavation construction technology, the improved open TBM can well adapt to the environment of the excavation face and significantly improve the tunneling speed, which can alleviate the tension of the mine production connection.
The original contributions presented in the study are included in the article/Supplementary Material; further inquiries can be directed to the corresponding author.
YL: conceptualization, supervision, and writing—original draft. DR: methodology, writing—review and editing, and data curation. CZ: validation, resources, investigation, and formal analysis. ZD and HQ: validation and formal analysis. CL: review and editing. All authors contributed to the article and approved the submitted version.
This work was supported and financed by the Natural Science Fund (Nos. 52074209 and 51904225) and the Natural Science Foundation of Shaanxi Province (No. 2021JLM-06), all of which are greatly appreciated. Construction of Shaanxi Qinchuangyuan’s “Scientist + Engineer” Team (2023KXJ-057).
Author YL was employed by the company Shandong Energy Group Xibei Mining Co., Ltd. Authors DR and CZ were employed by the company Shaanxi Zhengtong Coal Industry Co., Ltd.
The remaining authors declare that the research was conducted in the absence of any commercial or financial relationships that could be construed as a potential conflict of interest.
All claims expressed in this article are solely those of the authors and do not necessarily represent those of their affiliated organizations, or those of the publisher, the editors, and the reviewers. Any product that may be evaluated in this article, or claim that may be made by its manufacturer, is not guaranteed or endorsed by the publisher.
Chen, L., Sheng, G., and Chen, G. (2014). Investigation of impact dynamics of roof bolting with passive friction control. Int. J. Rock Mech. Min. Sci. 70, 559–568. doi:10.1016/j.ijrmms.2014.06.003
Chen, J., Lu, D., Liu, W., Fan, J., Jiang, D., Yi, L., et al. (2020). Stability study and optimization design of small-spacing two-well (SSTW) salt caverns for natural gas storages. J. Energy Storage. 27, 101131. doi:10.1016/j.est.2019.101131
Chen, Q., Li, Z., Niu, T., Zhang, H., Zhou, Y., and Yu, J. (2022). Optimization of tunnel lining cross-section by tunnel boring mahine method in plateau railway with complex geology. Tunn. Constr. 42, 334–344.
Chun, C., Lei, G., He, T., Zuo, J., Yu, X., Zheng, J., et al. (2023). Crack development characteristics and fracture modes of primary coal-rock mass induced by the unloading of confining pressure in deep coal mining. J. China Coal Soc. 1–16. doi:10.13225/j.cnki.jccs.2022.1545
Ding, Z., Li, X., Huang, X., Wang, M., Tang, Q., and Jia, J. (2022). Feature extraction, recognition, and classification of acoustic emission waveform signal of coal rock sample under uniaxial compression. Int. J. Rock Mech. Min. Sci. 160, 105262. doi:10.1016/j.ijrmms.2022.105262
Ding, Z., Jia, J., Tang, Q., and Li, X. (2022). Mechanical properties and energy damage evolution characteristics of coal under cyclic loading and unloading. Rock Mech. Rock Eng. 55, 4765–4781. doi:10.1007/s00603-022-02884-x
Du, L., Yuan, J., Bao, S., Guan, R., and Wan, W. (2022). Robotic replacement for disc cutters in tunnel boring machines. Autom. Constr. 140, 104369. doi:10.1016/j.autcon.2022.104369
Fan, J., Chen, J., Jiang, D., Ren, S., and Wu, J. (2016). Fatigue properties of rock salt subjected to interval cyclic pressure. Int. J. Fatigue. 90, 109–115. doi:10.1016/j.ijfatigue.2016.04.021
Fan, J., Jiang, D., Liu, W., Wu, F., Chen, J., and Daemen, J. (2019). Discontinuous fatigue of salt rock with low-stress intervals. Int. J. Rock Mech. Min. Sci. 115, 77–86. doi:10.1016/j.ijrmms.2019.01.013
Fan, J., Liu, W., Jiang, D., Chen, J., Tiedeu, W., and Daemen, J. (2020). Time interval effect in triaxial discontinuous cyclic compression tests and simulations for the residual stress in rock salt. Rock Mech. Rock Eng. 53, 4061–4076. doi:10.1007/s00603-020-02150-y
Fan, J., Liu, P., Li, J., and Jiang, D. (2020). A coupled methane/air flow model for coal gas drainage: Model development and finite-difference solution. Process Saf. Environ. Prot. 141, 288–304. doi:10.1016/j.psep.2020.05.015
Fan, J., Xie, H., Chen, J., Jiang, D., Li, C., Tiedeu, W., et al. (2020). Preliminary feasibility analysis of a hybrid pumped-hydro energy storage system using abandoned coal mine goafs. Appl. Energy. 258, 114007. doi:10.1016/j.apenergy.2019.114007
Fan, C., Xu, H., Wang, G., Wang, J., Liu, Z., and Cheng, Q. (2021). Determination of roof horizontal long drilling hole layout layer by dynamic porosity evolution law of coal and rock. Powder Technol. 394, 970–985. doi:10.1016/j.powtec.2021.09.002
Guo, J., Ma, L., and Zhang, D. (2019). Management and utilization of high-pressure floor-confined water in deep coal mines. Mine Water Environ. 38, 780–797. doi:10.1007/s10230-019-00639-9
He, F., Lu, Y., Dai, E., Tian, Y., Wu, F., Pan, S., et al. (2013). Application of TBM in coal mine adaptability type selection analysis and new technology development. Coal Sci. Techno., 1–13. doi:10.13199/j.cnki.cst.2022-1404
He, F., Zhuo, X., Sun, Y., Yuan, X., and Jiang, L. (2022). Design and experiment of muck removal robot for tunneling boring machine. Adv. Eng. Sci. 54, 12–19. doi:10.15961/j.jsuese.202101044
Liang, Z., Qian, X., Zhang, Y., and Liao, Z. (2022). Numerical simulation of dynamic fracture properties of rocks under different static stress conditions. J. Cent. South Univ. 29, 624–644. doi:10.1007/s11771-022-4903-2
Liu, Q., Wang, W., and Ma, H. (2019). Parallelized combined finite discrete element (FDEM) procedure using multi-GPU with CUDA. Int. J. Numer. Anal. Meth. Geomech. 44, 208–238. doi:10.1002/nag.3011
Liu, B., Wang, J., Wang, R., Wang, Y., and Zhao, G. (2023). Intelligent decision-making method of TBM operating parameters based on multiple constraints and objective optimization. J. Rock Mech. Geotech. Eng. doi:10.1016/j.jrmge.2023.02.014
Ma, H., Wang, W., Liu, Q., Tian, Y., Jiang, Y., Liu, H., et al. (2022). Extremely large deformation of tunnel induced by rock mass fracture using GPGPU parallel FDEM. Int. J. Numer. Anal. Meth. Geomech. 46, 1782–1807. doi:10.1002/nag.3368
Mao, S., Shen, X., and Lu, M. (2015). Virtual laser target board for alignment control and machine guidance in tunnel-boring operations. J. Intell. Robot. Syst. 79, 385–400. doi:10.1007/s10846-014-0113-y
Qiu, H., Zhang, F., Liu, L., Huan, C., Hou, D., and Kang, W. (2022). Experimental study on acoustic emission characteristics of cemented rock-tailings backfill. Constr. Build. Mat. 315, 125278. doi:10.1016/j.conbuildmat.2021.125278
Qiu, H., Liang, C., Tu, B., Liu, L., Zhang, F., and Lv, W. (2023). Study on mechanical properties of cemented backfill with different mineral admixtures. Constr. Build. Mat. 367, 130251. doi:10.1016/j.conbuildmat.2022.130251
Song, X., Hou, T., Xie, Z., Cui, G., Ding, Z., Huang, X., et al. (2023). Preventing method of jamming of TBM tunneling machine in deep composite stratum roadway. Coal Technol. 42, 44–48. doi:10.13301/j.cnki.ct.2023.03.008
Sun, H., Guo, W., Liu, J., Song, L., and Liu, X. (2018). Layout design for disc cutters based on analysis of TBM cutter-head structure. J. Cent. South Univ. 25, 812–830. doi:10.1007/s11771-018-3786-8
Tan, Z., Li, Z., Zhou, Z., Lai, H., Jiao, Y., Li, F., et al. (2022). Research on an evaluation method for the adaptability of TBM tunnelling. App. Sci. 12, 4590. doi:10.3390/app12094590
Wang, D., Song, Z., and Xiao, B. (2014). Static analysis of double spherical parts for TBM boots system. Manuf. Autom. 36, 68–70.
Wang, W., Liu, Q., Ma, H., Lu, H., and Wang, Z. (2020). Numerical analysis of material modeling rock reinforcement in 2D FDEM and parameter study. Comput. Geotech. 126, 103767. doi:10.1016/j.compgeo.2020.103767
Wang, W., Ding, Z., Ma, H., Sun, W., and Ren, J. (2022). Simulation analysis on bolting and grouting reinforcement of fractured rock using GPU parallel FDEM. Geomech. Geophys. Geo-energ. Geo-resour. 175, 175. doi:10.1007/s40948-022-00488-x
Wang, M., Guo, P., Dong, W., and Yang, F. (2023). Research on borehole repair model and working parameters optimization of self-propelled rotary excavator. Front. Earth Sci. 11. doi:10.3389/feart.2023.1137946
Wei, L., Khan, M., Mehmood, O., Dou, Q., Bateman, C., Magee, D., et al. (2019). Web-based visualisation for look-ahead ground imaging in tunnel boring machines. Autom. Constr. 105, 102830. doi:10.1016/j.autcon.2019.04.025
Wen, H., Wang, J., Guo, X., Li, H., Li, S., and Li, X. (2022). A new transient electromagnetic prospecting method in TBM tunnel environment. J. Appl. Geophy. 196, 104492. doi:10.1016/j.jappgeo.2021.104492
Wu, F., Gao, Q., Li, Z., Qiu, H., Jin, C., Huang, L., et al. (2021). Development and application of cutterhead vibration monitoring system for TBM tunnelling. Int. J. Rock Mech. Min. Sci. 146, 104887. doi:10.1016/j.ijrmms.2021.104887
Wu, Z., Wei, R., Chu, Z., and Liu, Q. (2021). Real-time rock mass condition prediction with TBM tunneling big data using a novel rock–machine mutual feedback perception method. J. Rock Mech. Geotech. Eng. 13, 1311–1325. doi:10.1016/j.jrmge.2021.07.012
Xie, W., Zhang, X., Liu, X., Xu, C., Li, X., Song, D., et al. (2023). Real-time perception of rock–machine interaction information in TBM tunnelling using muck image analysis. Tunn. Undergr. Sp. Tech. 136, 105096. doi:10.1016/j.tust.2023.105096
Yang, T., Liu, S., Zhao, H., and Li, X. (2023). Study on the restraint control of an isolation pile on an existing high-speed railway during the close passing of a shield machine. Front. Earth Sci. 11. doi:10.3389/feart.2023.1142864
Yuan, L., and Zhang, P. (2023). Research progress and thinking on integrated tunneling and detection technology of rock roadway with TBM. Coal Geol. Explor. 51, 21–32.
Zhang, Y., Wan, Z., Gu, B., Zhou, C., and Chen, J. (2017). Unsteady temperature field of surrounding rock mass in high geothermal roadway during mechanical ventilation. J. Cent. South Univ. 24, 374–381. doi:10.1007/s11771-017-3439-3
Zhang, H., Hu, Z., Chen, J., Zhu, C., Zhao, Y., Zheng, X., et al. (2021). TBM techniques for intelligent excavating large-section rock roadway in the deep high-temperature coal mines: Application of TBM in Xinkuang No. 1. J. China Coal Soc. 46, 2174–2185. doi:10.13225/j.cnki.jccs.jj21.0579
Zhang, Q., Yang, B., Zhu, Y., Guo, C., Jiao, C., and Cai, A. (2022). Prediction method of TBM tunneling parameters based on Bi-GRU-ATT model. Adv. Civ. Eng. 2022, 1–16. doi:10.1155/2022/3743472
Zhang, W., Li, Y., Dong, Z., and Yang, Q. (2023). Construction applicability of mechanical methods for connecting aisle in the bohai mudstone stratum with high water pressure. Front. Earth Sci. 10. doi:10.3389/feart.2022.1085327
Keywords: open TBM, supporting equipment, complex geology, roadway excavation, goaf
Citation: Liu Y, Ren D, Zhou C, Qiu H, Ding Z and Liang C (2023) Study on the improvement of the open TBM system and supporting equipment based on the Gaojiapu Coal Mine. Front. Earth Sci. 11:1196898. doi: 10.3389/feart.2023.1196898
Received: 30 March 2023; Accepted: 15 May 2023;
Published: 30 May 2023.
Edited by:
Jinyang Fan, Chongqing University, ChinaReviewed by:
Weiqin Wang, Xi’an University of Architecture and Technology, ChinaCopyright © 2023 Liu, Ren, Zhou, Qiu, Ding and Liang. This is an open-access article distributed under the terms of the Creative Commons Attribution License (CC BY). The use, distribution or reproduction in other forums is permitted, provided the original author(s) and the copyright owner(s) are credited and that the original publication in this journal is cited, in accordance with accepted academic practice. No use, distribution or reproduction is permitted which does not comply with these terms.
*Correspondence: Ziwei Ding, endkaW5nQHh1c3QuZWR1LmNu
Disclaimer: All claims expressed in this article are solely those of the authors and do not necessarily represent those of their affiliated organizations, or those of the publisher, the editors and the reviewers. Any product that may be evaluated in this article or claim that may be made by its manufacturer is not guaranteed or endorsed by the publisher.
Research integrity at Frontiers
Learn more about the work of our research integrity team to safeguard the quality of each article we publish.