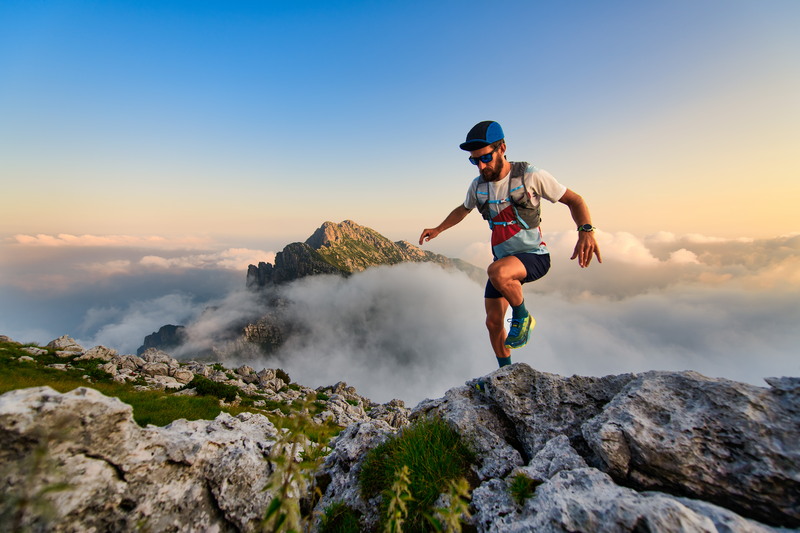
95% of researchers rate our articles as excellent or good
Learn more about the work of our research integrity team to safeguard the quality of each article we publish.
Find out more
BRIEF RESEARCH REPORT article
Front. Comput. Sci. , 03 May 2023
Sec. Mobile and Ubiquitous Computing
Volume 5 - 2023 | https://doi.org/10.3389/fcomp.2023.1012565
This article is part of the Research Topic Wearable Computing View all 7 articles
Wearable haptic assistive devices can provide tactile information to visually impaired people (VIP) to support independent living. However, electromechanical haptic feedback has a number of disadvantages, including hardware being relatively heavy, large, and producing excessive sound. Here, we present a design-driven investigation of the potential of shape memory alloy-based haptic feedback for VIP. We followed an iterative approach, focusing on hands-on material explorations, in which we identified challenges and subsequent solutions that designers of SMA-based wearable haptic assistive devices may be faced with when incorporating SMAs in their designs. We present several prototype iterations and an initial evaluation with VIP to offer insights into the potential of SMA-based wearable haptic devices for VIP.
Wearable haptic assistive devices for visually impaired people (VIP) can offer feedback during navigation (Ertan et al., 1998; Scheggi et al., 2014), provide information about facial expressions during a conversation (Buimer et al., 2018), or can provide means for digital interpersonal communication for people with combined visual and auditory impairments (Plaisier and Kappers, 2021). However, while wearable haptic assistive devices for VIP have shown promise to aid independent living (Sorgini et al., 2018; Hwang et al., 2020), they are not without their limitations. One particular limitation relates to the use of electromechanical haptic feedback systems. For one, vibration feedback can be produced with small vibration motors, but the haptic feedback from such systems, especially with extended use, does not feel particularly pleasant (Huisman et al., 2016; Schneider et al., 2016). Electromechanical haptic systems often require designs that are relatively heavy, large, and with sound production that limits their usability for VIP [e.g., Ion et al. (2015), though see Trase et al. (2020) and Li et al. (2021) for promising alternative approaches]. Shape memory alloy (SMA)-based haptic actuators (Kawate et al., 2018) offer opportunities to mitigate these issues. SMAs are thin, flexible, lightweight, and effective at producing haptic feedback that feels relatively natural (Cruz et al., 2018; Hamdan et al., 2019).
When mechanically deformed at room temperature, SMAs can recover their original shape when heat is applied above the transition temperature threshold (Bengisu and Ferrara, 2018). This characteristic of SMAs is called “shape memory effect” (SME) (Huang et al., 2010), which occurs due to martensite/austenite transformations in the crystallographic structure of the material (Jani et al., 2014; Bengisu and Ferrara, 2018). SMAs can be safely incorporated into wearable devices by carefully calibrating the transition temperature of the SMA during the process of ‘programming' the material, so that activation temperature ranges are skin-safe (Liu et al., 2022).
Several projects have explored SMA-based haptic actuator designs worn on the wrist (Knoop and Rossiter, 2015; Chernyshov et al., 2018), finger (Gupta et al., 2017), or on different body locations using adhesive patches (Hamdan et al., 2019). Researchers have explored ways in which SMA-based haptic wearables can produce different touch sensations, such as squeezing and stroking (Cao et al., 2018; Muthukumarana et al., 2020).
These examples showcase the potential of using SMAs for wearable haptic feedback applications following different approaches. For example, Chernyshov et al. (2018) shaped their ring-like SMA-based designs focusing on the tactile sensitivity of the glabrous skin of the hand. Hamdan et al. (2019) considered movements of the body and skin, and how adhesive patches with incorporated SMAs could best stretch the skin to provide haptic feedback. Most work on SMA-based haptic wearables uses off-the-shelve SMA wires (i.e., pre-shaped wires), rather than also consider the material properties of the SMAs themselves. Knowledge of the material properties of SMA and how these properties affect the SMA's performance as haptic actuators is important during the design process to make full use of the potential of SMAs. Here, we present an explorative, design-driven investigation of the potential of SMA-based haptic feedback for VIP.
Our work aligns with a research through design approach where “the designing act of creating prototypes is in itself a potential generator of knowledge” (Stappers, 2012, p. 87). With this approach we aim to gain knowledge on the process of designing with SMAs for wearable haptic applications for VIP (see Zimmerman et al., 2007). The iterative, active engagement with the materials, and iterative creation of prototypes served two purposes: one, to generate designerly knowledge about the materials in question (i.e., SMAs). Two, to enable people to interact with the prototypes and to have these interactions serve as prompts for discussions about the potential of SMA-based haptics for VIP.
Furthermore, our approach is inspired by material-driven design (Van Bezooyen, 2014; Karana et al., 2015) where hands-on explorations with the material in question (i.e., SMAs) formed the central activity in our work. We paid special attention to material experiences (Giaccardi and Karana, 2015; Karana et al., 2015), focusing not only on what the material in question is, but also what it does, how it expresses, and what it makes people do (Karana et al., 2015). These experiential aspects of a material should also be considered as part of larger socio-cultural assemblage in which acceptability of the material is important (Karana et al., 2015). For our purposes specifically, this meant involving VIP to discuss the potential of SMA-based haptic wearable devices.
Flexmet®SMA wires containing nickel, titanium (NiTi), and/or copper (NiTiCu) were used during the initial material explorations were.
They were used to create shape change by firstly forming the wire into a desired shape (e.g., spring), and then training the wire to memorize this shape by annealing the set-up in an oven at 550°C for 60 min. Using this technique, the straight Flexmet NiTi/NiTiCu or Flexinol NiTi wires of 0.5 mm diameter (austenite-finish-temperature of 90°C) were formed into spring shape with an outer diameter of 3.45 mm. In the later stages of exploration, additional four springs were made from the same Flexmet SMA wires with 10 windings.
Polylactic acid (PLA)-based 3D prints from an Ultimaker 2+ 3D printer were used for creating supporting structures that served as guides for the SMA wires and springs. The SMA springs that were created during the material exploration process were subjected to strain-controlled testing using a TA Instruments Q800 Dynamic Mechanical Analyser (DMA) (see Figure 1E).
Figure 1. Material explorations with SMA NiTi and NiTiCu wires. The top row shows (A) programming of the wire as springs, (B) flat springs, (C) and 3D-structures, (D) as well as failed shape recovery in the form of a spring and (E) DMA testing. The middle row shows several explorations with straight annealed SMA wires (F) of a longer length, (G) finger wearable, (H, I) in a tooth-structure, (J) and brad pin structure using Lycra, (K) or another SMA wire as bias force. The bottom row depicts (L) SMA springs in a brad pin supported structure, (M) a TPU ring structure, (N, O), and designs with effectors moved by springs.
The interactive prototype used a Seeeduino Lotus board with which each of four SMA springs could be individually controlled with a push button. A QSKJ DC-DC Adjustable Step-down Buck Converter XL4005 of 5A was used to make the interactive prototype run off of a lithium polymer battery. Four mosfet modules were incorporated (one for each spring) to control the voltage/current flow to each spring.
Students (two male, three female) from a design faculty were involved in an informal evaluation of the interactive wearable prototype to inform the iterative design process. Also, note that the insights gained during the design process by the designers themselves served as an important source of first-person knowledge, as is in line with research through design and material-driven design methods.
In addition, four VIP participated in an evaluation session with an improved version of the interactive prototype. The participants consisted of two males and two females with different levels of vision. Two had 0% vision, one had 1% vision, and the another 50% vision in one eye and 25% in the other eye.
The material exploration phase took place over a number of weeks. During this time, the designers engaged with the materials to help develop understanding of the possibilities of incorporating SMA in wearable haptic applications. The general procedure was inspired by the steps formulated by Karana et al. (2015). As a first step to understanding the material we started by tinkering with the materials in an iterative fashion. During this iterative process small prototypes were tested and discussed with the research team to inform the next iterative cycle of material exploration. We conducted strain- controlled tests on two NiTi SMA springs to quantify the relation between wire load and displacement. The samples were looped into small plastic rings to secure them into the DMA machine. The samples were stretched to 100 and 200% elongation The samples were then activated with heat and the load produced between 50°C and 90°C were measured.
We took the knowledge gained from this explorative first step and applied those to the design of an interactive prototype that embodied our vision of how a SMA-based haptic wearable for VIP could function. The further exploration of this vision was represented in the iterations of the interactive prototype that was used in a session with VIP. In this session, the prototype was attached to the arm of the VIP with the help of medical tape. The haptic sensations were produced on the dorsal and ventral sides of the lower arm. In the first part of the session, each spring was individually activated starting with the spring closest to the elbow followed by the other springs in a clock-wise direction. After every sensation, the participants were asked to explain what they perceived. In the second part of the session, two different types of feedback were provided. First, a squeezing type feedback produced by activating both wires running across the arm simultaneously. Second, a stroking sensation where first the wire closest to the hand was activated followed by the wire closest to the elbow. Participants were asked to identify and compare each sensation. The session ended with an interview and discussion of the participants' experiences and their suggestions for possible applications of the interactive prototype. Participants' responses were noted down by the designers.
Note, Internal review board approval, according to the university's regulations, was not mandatory at the time of running the study.
We started by tinkering with SMA materials in different formats (see Figure 1 for an overview), to explore the materials' properties and capabilities, to guide the material selection process, and to inspire the design of the interactive prototype.
As a first step different actuator designs using SMAs were explored. NiTiCu (nickel, titanium, copper) wires of diameter 0.5 mm and NiTi (nickel, titanium) wires of diameter 0.08 mm were tested. Both wires had an austenite finish temperature of 65°C. The wires were trained as springs, flat springs, and a 3D structure which requires the wires to be fixed in the desired shape using nuts and bolts and then annealed at 500°C for 45 min in a ceramic oven (see Figures 1A–C). After taking them out of the oven, the wires are cooled in water which also removes oxide layers from the wires.
After training the wires, shape recovery was tested by using both joule heating and hot water as the stimuli. The transition temperature for the wires were between 30°C and 60°C. The power to heat up the 0.5 mm diameter wires sufficiently was 2A with 2V output. This is the power needed to reach to austenite finish temperature of the wire in order to have the complete phase transformation (i.e., the complete shape recovery of the spring). It was found that the wires trained to be a 3D shape had the poorest shape recovery due to the difficulty of properly fixing the wire into a 3D shape. In general, it was found to be important to keep the wires tightly secured during training in order for them to recover their shape and be able to exert appropriate forces; a requirement to produce haptic feedback. If not securely affixed during the training process, wires would recover to a distorted shape when heated after deformation (see Figure 1D). The NiTi wires were more difficult to control and fixed in place compared to NiTiCu wires. This is not only because they are considerably thinner (0.08 mm compared to 0.5 mm) but also because the wires containing copper are more flexible and thus easier to bend into a desired shape. Note, that the rigidity of NiTi wires may actually be preferred for spring-shaped SMAs to create springs that can resists stronger load forces. Compared to regular springs, flat springs showed poorer shape recovery because they tended to deflect along the vertical axis.
Mechanical testing of the relationship between load and displacement showed how the thicker SMA wire produced considerably higher forces when heated to return to its trained shape. The stress-temperature-time graphs for 100% strain for both samples can be found in Figure 2. There was only a minimal difference in the wires' performance at 100 vs. 200% elongation, thus only the results for 100% elongation are shown here. There is a considerable difference, however, between the force produced by both springs: spring 1 produced 0.31 N while spring 2 produced 4.61 N. As can observed from the graphs in Figure 2 we can conclude that by adapting the diameter of the spring, the force can be fine tuned. In this case, by changing the diameter from 0.2 mm to 0.5 mm the force increased by factor of 14.87. The stronger forces produced by spring 2 meant it would be more suitable for producing noticeable haptic sensations, thus, further explorations used the same diameter of SMA wire as spring 2.
Figure 2. Results of strain-controlled testing and correlation with the amount of load measured with TA Instruments Q800 DMA of two SMA springs. (A) Spring 1: NiTi SMA springs with an austenite finishing temperature of 90°C a wire diameter of 0.20 mm, spring diameter of 1.37 mm with ten coils. (B) Spring 2: NiTi SMA spring with an austenite finishing temperature of 90°C a wire diameter of 0.50 mm, spring diameter of 3.45 mm with five coils.
As a next step, the SMA wires were integrated with several 3D-printed structures to enable different types of motion (see Figure 1 middle row). Both straight annealed wires and spring-shaped wires were used. The explorations of specific wire-structure combinations were primarily driven by what kind of sensation the design could potentially produce on the skin in a wearable form factor. These were motions over the skin surface in one, or multiple directions, poking, pinching, and squeezing sensations.
Early explorations with longer, continuous lengths of SMA wires were largely unsuccessful. The main challenge with working with these lengths of wire is that without fixing each contact point to the supporting structure, the wire has too much play to move around, resulting in minimal actuation of the supporting structure (Figure 1F). In addition, designs with longer lengths of wire accumulate more heat making it more difficult to actuate the wire repeatedly. In the next iteration, wire length was reduced and the SMA wire was secured to lycra fabric that could worn around the finger (see Figure 1G). In this way, heating the wire would result in a squeezing sensation on the finger. While the design did result in such a squeeze, the force produced by the wire was considered too minimal to be reliably noticeable.
Next, sliding mechanisms using different materials to produce bias forces (i.e., Lycra, silicone rubber, a second SMA wire) were explored. These mechanisms could potentially produce a wider range of sensations on the skin, depending on the orientation of the actuator relative to the skin surface (Figures 1H–K). The “toothed design” (Figures 1H, I) produced only minimal displacement, despite different tooth shapes. The design with separate PLA components connected using brad pins (Figures 1J, K) produced noticeable displacement, and, using a second SMA wire, could generate repetitive motions.
After explorations with straight annealed wires, SMA wires of 0.5 mm diameter and with an austenite finishing temperature of 65°C, were trained into spring-shapes (Figures 1L–O). One actuator design using brad pins (Figure 1L) could create sliding as well as pinching sensations on the skin. SMA springs were also tested in a 3D-printed thermoplastic polyurethane (TPU) ring-type structure (see Figure 1M). The ring was flexible enough to be bend substantially by the SMA spring and was strong enough to act as a bias force. The design resulted in a pinching sensation on the skin. However, due to the size of the springs, the actuator was large and less suitable for wearable applications.
A final design that was explored was a design with a single effector connected to multiple spring-shaped SMA wires (Figures 1N, O). The idea behind this design was that the effector contacts the skin and can be moved over the surface of the skin in two dimensions by activating one or more SMA springs. A Lycra sheet was placed between the skin and the wires to prevent the wires touching the skin. This design was able to successfully move the effector, with the other springs serving as a bias force to bring the effector back to the center. It was important to fix one end of each spring securely to the Lycra sheet to ensure the wires could complete a full range of motion. The mechanism also had the ability to create a large range of motion depending on the sequence of activation of the wires. This large range of motion combined with the potential to produce different types of sensations made this ‘effector design' a good candidate for further development into a wearable interactive prototype.
A first step to making the effector-based design into a wearable form factor was to isolate the SMA wires from the skin. Kinesiology tape was suggested (Hamdan et al., 2019) as a suitable heat barrier (Figure 3A). However, after testing different spring shapes that produced the most prominent motion, it was found that kinesiology tape alone was not sufficient to isolate against higher temperatures (i.e., above 90°C) necessary to fully actuate some SMA wires. We therefore added a layer of silicone rubber over the kinesiology tape as an additional heat barrier. A polyvinyl chloride (PVC) ring was added to the prototype to add structural integrity and to have a surface to securely fasten the SMA wires to (Figures 3B, C). After testing with different wires it was found that Flexinol NiTi wires with a diameter of 0.50 mm produced the most prominent motion. These wires were trained into spring shapes with an outer diameter of 3.45 mm and a spring length of 70 mm (total wire length was 240 mm for each spring). The springs had approximately 10 windings and austenite finishing temperature of 90°C.
Figure 3. Development of the interactive wearable prototype. (A) Testing of kinesiology tape as a heat barrier. (B) A first design of the prototype. (C) The first design being worn on the forearm. (D) Improved prototype. (E) Schematic detailing the prototype's components.
The PLA effector featured a design with a chamfered edge which produced the most noticeable sensations and smoothest motion. Based on the feedback provided by student participants a number of changes were made to the interactive prototype. The biggest of these changes was to focus on motion along the arm only, and to have a third spring be able to provide a squeezing sensation on the arm. Further refinements to the chamfered edge of the effector were made and the overall shape of the prototype was elongated to allow for easier motion along the arm. This improved version of the prototype was used in the session with VIP (Figures 3D, E, 4).
In the session with VIP the interactive wearable prototype was used to produce stroking sensations along the arm (up and down) and squeezing sensations. The motion along the arm was perceived as a such by all participants and participants were able to tell the direction of motion in most cases (in one instance P3 experienced the sensation as non-directional pressure). P1 described the stroking motion as a “wheel running along the arm”, P2 described how it felt like an “animal walking along the arm”, and both P3 and P4 described the sensation “like a finger running along the arm”. The squeezing sensation was described by all participants as gentle, or gradual pressure. For shorter activation durations it was harder to perceive this sensation for all participants. The experience of both motion and squeezing sensations differed between dorsal and ventral sides of the lower arm for all participants. In general, sensations on the ventral side felt more subtle to all participants and for P3 it was very difficult to feel anything at all on the ventral side. This is consistent with the fact that the hairy skin on the dorsal side is more sensitive to stroking sensations (see Knight et al., 2014), such as the ones produced by the prototype. All participants found the sensations produced by the interactive wearable prototype to be pleasant. Three out of four participants mentioned that they found the motion along the arm to feel the most pleasant and considered it as a viable type of feedback for several wearable haptic applications for VIP.
Participants reflected on the potential of SMA-based haptics for wearable applications. Their main interest for application of SMA-based haptic feedback was in navigation, obstacle avoidance, and guidance toward specific objects. Participants considered several aspects of the interactive prototype in light of these applications: they expressed being positively surprised that one prototype could produce a variety of sensations, especially in comparison to other haptic devices that they were familiar with and that used more conventional actuator types, such as vibrotactile actuators. P1 remarked that an ideal device would incorporate all of these different types of feedback (including vibration) in order to provide a variety of information to users. However, for critical moments, such as warnings while walking through traffic, the intensity of the SMA-based haptic sensations would have to be increased so as to not go unnoticed. In this same scenario, the fact that the device did not produce any sound when delivering haptic feedback was considered a benefit. This way, information would remain personal (i.e., would not be available to others) and VIP would be able to focus more on environmental sounds.
The placement of the prototype on the body was also topic of discussion. P2 considered how well the sensation would be felt on different body locations and considered the shoulder or the arm, close to the wrist, ideal locations for wearing such a device. P1 remarked that, as long as the type of feedback had real value for them, they were ambivalent about where to wear the device. Similarly, P1 participant remarked that the body location should match with the specific application. For complex navigation scenarios placement of SMA-based actuators on different body locations was also considered. For example, actuators could be placed on both arms to enable avoidance of obstacles to the left and right of a person. A different placement that was considered by P3 and P4 was centrally on the body, in the form of a belt or necklace. This way, the effector could help people orient toward the left or right.
In this article we have detailed a research through material-driven design approach to the design of SMA-based haptic wearables for VIP. We have highlighted specific challenges that arise when working with SMA materials in the design of wearable haptic devices. These challenges pertain to the functioning of the materials, the use of supporting structures, and considerations for wearability. In addition, the prototypes developed in this process served as prompts for VIP, to share their insights regarding the sensations produced by the prototypes as well as the potential application possibilities.
We argue that the design-driven approach used here could be of benefit to the future design of SMA-based haptic wearables in general. The approach allowed for rapid prototype iterations which could be tried and improved upon quickly. This helped us to understand the possibilities and limitations of the material within the context of wearable haptic devices. The material exploration process highlighted the importance of understanding the properties of SMA materials. The wire's diameter, length, configuration, and material composition (e.g., alloys with copper) all need to be considered and decisions need to be made based on the specific design one is working on. For example, NiTi wires, while harder to train from our experience, are more suitable for creating SMA springs due to the fact that they are stiffer. As another example, the total length of a SMA wire in a wearable design needs to be carefully considered as longer wires accumulated more heat, potentially up to temperature levels that are uncomfortable for wearable applications, even when using heat barrier materials.
The process of training wires into different shapes, rather than only using pre-formed wires, offered additional flexibility in the creation of various designs. At the same time, the challenges of training wires were also highlighted. For example, training wires into 3D shapes proved challenging due to the difficulties of fixing the wires during the training process. This would be an interesting avenue for future explorations with SMA-based actuators to pick up on. It is not unthinkable that with properly trained wires, additional support structures become unnecessary for providing appropriate haptic feedback. The use of supporting structures did offer opportunities to design different types of haptic actuators with relatively similarly trained SMA wires (e.g., springs). Nevertheless, several challenges emerged while designing with supporting structures. For one, affixing the SMA wires was found to be vitally important but not always easy to do, especially with longer lengths of wire. Moreover, most of the designs using supporting structures produced relatively subtle haptic sensations. There may be application scenarios where such sensations could be used, but for VIP applications the produced feedback was considered to be too minimal. In the end, designs where the SMA wires in the form of springs could freely move an effector over the skin proved to be the most viable. Iterative development of such a design eventually led us to create the interactive wearable prototype.
The interactive wearable prototype served as a valuable tool to gain feedback from participants on SMA-based haptic wearables. Overall, feedback was noticeable by participants, despite the fact that directional information was still hard to discern. Considering that the VIP participants mentioned navigation and object avoidance as interesting use cases, this would be a potential challenge to overcome for future developments based on the current prototype design. Still, the fact that the prototype did offer such (imperfect) directional information triggered discussions around SMA-based haptics as being appropriate for navigation purposes. This was mainly due to the fact that multiple types of feedback could be created in a single device, which would allow for richer information to be presented while navigating. An additional consideration here would be the placement of the device on the body. While glabrous skin, such as on the palm, is more sensitive to tactile feedback (see Chernyshov et al., 2018), the hand offers little space to produce the type of motion that was appreciated by our VIP participants.
To make the interactive prototype suitable for testing in such a navigation scenario, however, participants remarked that the feedback intensity would need to be improved. An interesting suggestion made by a VIP participant was to combine the SMA-based feedback with more traditional forms of haptic feedback, such as vibrotactile feedback. The proposed design of a necklace that provides navigation information could be an interesting concept to explore. Vibrotactile feedback could notify a VIP about new navigation instructions. The user can then feel the directional SMA-based feedback on their body and they could use their hand to touch the necklace to verify the feedback. These kinds of applications should ideally be explored further in collaboration with VIP to ensure that the type of feedback matches the use case that is most valuable to them. The iterative process outlined in this article could offer some initial guidance on where to start with such a SMA-focussed design process.
In addition, two other interesting directions for future research can be considered here. First, we are planning to conduct studies in which we benchmark SMA-based haptics against electromechanical haptic systems. This benchmarking should focus first on perceptual properties of the produced feedback which should highlight where SMA-based haptics for wearable applications offer advantages over traditional haptics, and where the may fall short. Second, it is important to consider the potential differences between designing with SMA-based haptics and traditional haptics. The unique properties of SMAs to be shaped, trained, and combined with different supporting structures makes for a design process that differs from other haptic design approaches. Shedding further light on this process could aid designers in successfully applying SMAs in their wearable haptic designs for VIP.
The raw data supporting the conclusions of this article will be made available by the authors, without undue reservation.
Ethical review and approval was not required for the study on human participants in accordance with the local legislation and institutional requirements. The patients/participants provided their written informed consent to participate in this study.
PS was the driving force behind the material explorations, material tests, and session with visually impaired people. SG and GH were involved in iterative testing of the design explorations and in making decisions during the iterative process and collaboratively wrote the paper. All authors contributed to the article and approved the submitted version.
The authors declare that the research was conducted in the absence of any commercial or financial relationships that could be construed as a potential conflict of interest.
All claims expressed in this article are solely those of the authors and do not necessarily represent those of their affiliated organizations, or those of the publisher, the editors and the reviewers. Any product that may be evaluated in this article, or claim that may be made by its manufacturer, is not guaranteed or endorsed by the publisher.
Bengisu, M., and Ferrara, M. (2018). Materials That Move: Smart Materials, Intelligent Design. Cham: Springer. doi: 10.1007/978-3-319-76889-2
Buimer, H. P., Bittner, M., Kostelijk, T., Van Der Geest, T. M., Nemri, A., Van Wezel, R. J., et al. (2018). Conveying facial expressions to blind and visually impaired persons through a wearable vibrotactile device. PLoS ONE 13, e0194737. doi: 10.1371/journal.pone.0194737
Cao, F., Saraiji, M. Y., and Minamizawa, K. (2018). “Skin+ programmable skin as a visuo-tactile interface,” in ACM SIGGRAPH 2018 Poster 1–2. doi: 10.1145/3230744.3230772
Chernyshov, G., Tag, B., Caremel, C., Cao, F., Liu, G., and Kunze, K. (2018). “Shape memory alloy wire actuators for soft, wearable haptic devices,” in Proceedings of the 2018 ACM International Symposium on Wearable Computers 112–119. doi: 10.1145/3267242.3267257
Cruz, M., Kyung, K.-U., Shea, H., Böse, H., and Graz, I. (2018). Applications of smart materials to haptics. IEEE Trans. Haptics 11, 2–4. doi: 10.1109/TOH.2018.2809058
Ertan, S., Lee, C., Willets, A., Tan, H., and Pentland, A. (1998). “A wearable haptic navigation guidance system,” in Digest of Papers. Second International Symposium on Wearable Computers (Cat. No. 98EX215) (IEEE) 164–165.
Giaccardi, E., and Karana, E. (2015). “Foundations of materials experience: An approach for hci,” in Proceedings of the 33rd Annual ACM Conference on Human Factors in Computing Systems 2447–2456. doi: 10.1145/2702123.2702337
Gupta, A., Irudayaraj, A. A. R., and Balakrishnan, R. (2017). “Hapticclench: Investigating squeeze sensations using memory alloys,” in Proceedings of the 30th Annual ACM Symposium on User Interface Software and Technology, pages 109–117. doi: 10.1145/3126594.3126598
Hamdan, N. A.-,h., Wagner, A., Voelker, S., Steimle, J., and Borchers, J. (2019). “Springlets: Expressive, flexible and silent on-skin tactile interfaces,” in Proceedings of the 2019 CHI Conference on Human Factors in Computing Systems 1–14. doi: 10.1145/3290605.3300718
Huang, W., Ding, Z., Wang, C., Wei, J., Zhao, Y., and Purnawali, H. (2010). Shape memory materials. Mater. Today 13, 54–61. doi: 10.1016/S1369-7021(10)70128-0
Huisman, G., Darriba Frederiks, A., Van Erp, J. B., and Heylen, D. K. (2016). “Simulating affective touch: Using a vibrotactile array to generate pleasant stroking sensations,” in International Conference on Human Haptic Sensing and Touch Enabled Computer Applications (Cham: Springer) 240–250. doi: 10.1007/978-3-319-42324-1_24
Hwang, J., Kim, K. H., Hwang, J. G., Jun, S., Yu, J., and Lee, C. (2020). Technological opportunity analysis: Assistive technology for blind and visually impaired people. Sustainability 12, 8689. doi: 10.3390/su12208689
Ion, A., Wang, E. J., and Baudisch, P. (2015). “Skin drag displays: Dragging a physical tactor across the user's skin produces a stronger tactile stimulus than vibrotactile,” in Proceedings of the 33rd Annual ACM Conference on Human Factors in Computing Systems 2501–2504. doi: 10.1145/2702123.2702459
Jani, J. M., Leary, M., Subic, A., and Gibson, M. A. (2014). A review of shape memory alloy research, applications and opportunities. Mater. Design 56, 1078–1113. doi: 10.1016/j.matdes.2013.11.084
Karana, E., Barati, B., Rognoli, V., Zeeuw Van Der Laan, A., et al. (2015). Material driven design (mdd): A method to design for material experiences. Int. J. Des. 9, 35–54. doi: 10.1016/j.matdes.2015.07.042
Kawate, S. S., Chethan, K., Keni, L. G., Pai, A., and Padmaraj, N. (2018). Innovations and recent trends in shape memory alloy: A review. Int. J. Eng. Technol. 7, 2172–2177. doi: 10.14419/ijet.v7i4.11445
Knight, F. L. C., Longo, M. R., and Bremner, A. J. (2014). Categorical perception of tactile distance. Cognition 131, 254–262. doi: 10.1016/j.cognition.2014.01.005
Knoop, E., and Rossiter, J. (2015). “The tickler: a compliant wearable tactile display for stroking and tickling,” in Proceedings of the 33rd Annual ACM Conference Extended Abstracts on Human Factors in Computing Systems 1133–1138. doi: 10.1145/2702613.2732749
Li, J., Godaba, H., and Zhu, J. (2021). Paper-based origami transducer capable of both sensing and actuation. Extreme Mech. Lett. 49, 101507. doi: 10.1016/j.eml.2021.101507
Liu, Q., Ghodrat, S., and Jansen, K. M. (2022). Modelling and mechanical design of a flexible tube-guided SMA actuator. Mater. Design 216, 110571. doi: 10.1016/j.matdes.2022.110571
Muthukumarana, S., Elvitigala, D. S., Forero Cortes, J. P., Matthies, D. J., and Nanayakkara, S. (2020). “Touch me gently: recreating the perception of touch using a shape-memory alloy matrix,” in Proceedings of the 2020 CHI Conference on Human Factors in Computing Systems 1–12. doi: 10.1145/3313831.3376491
Plaisier, M., and Kappers, A. (2021). “Social haptic communication mimicked with vibrotactile patterns-an evaluation by users with deafblindness,” in The 23rd International ACM SIGACCESS Conference on Computers and Accessibility 1–3. doi: 10.1145/3441852.3476528
Scheggi, S., Talarico, A., and Prattichizzo, D. (2014). “A remote guidance system for blind and visually impaired people via vibrotactile haptic feedback,” in 22nd Mediterranean Conference on Control and Automation (IEEE) 20–23. doi: 10.1109/MED.2014.6961320
Schneider, O. S., Seifi, H., Kashani, S., Chun, M., and MacLean, K. E. (2016). “Hapturk: crowdsourcing affective ratings of vibrotactile icons,” in Proceedings of the 2016 CHI Conference on Human Factors in Computing Systems 3248–3260. doi: 10.1145/2858036.2858279
Sorgini, F., Caliò, R., Carrozza, M. C., and Oddo, C. M. (2018). Haptic-assistive technologies for audition and vision sensory disabilities. Disabil. Rehabilit. 13, 394–421. doi: 10.1080/17483107.2017.1385100
Stappers, P. J. (2012). “Doing design as a part of doing research,” in Design Research Now (Birkhäuser) 81–91. doi: 10.1007/978-3-7643-8472-2_6
Trase, I., Xu, Z., Chen, Z., Tan, H., and Zhang, J. X. (2020). Thin-film bidirectional transducers for haptic wearables. Sensors Actuat. A. 303, 111655. doi: 10.1016/j.sna.2019.111655
Van Bezooyen, A. (2014). “Materials driven design,” in Materials Experience (Elsevier) 277–286. doi: 10.1016/B978-0-08-099359-1.00019-9
Keywords: shape memory alloy, haptics, wearables, visually impaired people, assistive device, research through design, material-driven design
Citation: Ghodrat S, Sandhir P and Huisman G (2023) Exploring shape memory alloys in haptic wearables for visually impaired people. Front. Comput. Sci. 5:1012565. doi: 10.3389/fcomp.2023.1012565
Received: 05 August 2022; Accepted: 13 April 2023;
Published: 03 May 2023.
Edited by:
Daniel Roggen, University of Sussex, United KingdomReviewed by:
David Swapp, University College London, United KingdomCopyright © 2023 Ghodrat, Sandhir and Huisman. This is an open-access article distributed under the terms of the Creative Commons Attribution License (CC BY). The use, distribution or reproduction in other forums is permitted, provided the original author(s) and the copyright owner(s) are credited and that the original publication in this journal is cited, in accordance with accepted academic practice. No use, distribution or reproduction is permitted which does not comply with these terms.
*Correspondence: Sepideh Ghodrat, Uy5HaG9kcmF0QHR1ZGVsZnQubmw=
Disclaimer: All claims expressed in this article are solely those of the authors and do not necessarily represent those of their affiliated organizations, or those of the publisher, the editors and the reviewers. Any product that may be evaluated in this article or claim that may be made by its manufacturer is not guaranteed or endorsed by the publisher.
Research integrity at Frontiers
Learn more about the work of our research integrity team to safeguard the quality of each article we publish.