- 1Vel Tech Rangarajan Dr. Sagunthala R&D Institute of Science and Technology, Chennai, Tamil Nadu, India
- 2Department of Biosciences, Saveetha School of Engineering, Saveetha Institute of Medical and Technical Sciences, Chennai, India
- 3Department of Mechanical Engineering, Gazi University Faculty of Engineering, Ankara, Türkiye
- 4Department of Machining, Assembly and Engineering Metrology, Faculty of Mechanical Engineering, VSB-Technical University of Ostrava, Ostrava, Czechia
- 5Department of Industrial Engineering, College of Engineering, King Saud University, Riyadh, Saudi Arabia
This study examined the use of geopolymer aggregate (GPA), produced from slag and an alkaline solution, as a substitute for coarse aggregate in conventional concrete. The research aimed to evaluate how different proportions of GPA (25%, 50%, 75%, and 100% replacement) affect the durability and mechanical properties of concrete. A series of tests were conducted, including slump, compressive strength, flexural strength, chloride resistance, sulfate resistance, sorptivity, and water absorption. The results demonstrated significant improvements in concrete properties with the inclusion of GPA. The compressive strength of GPA concrete ranged from 31 to 38 MPa, showing a 10%–15% increase over that of standard concrete. Flexural strength improved by 6% at 7 days and 7.5% at 28 days compared to control mixes. Water absorption was reduced by 42.58%, and sorptivity decreased by 47.9% compared to ordinary aggregate concrete. GPA concrete also excelled in acid resistance, with a weight loss of 28.6% and a lower reduction in strength compared to traditional acidic aggregates. In sulfate resistance tests, GPA concrete showed a 31% reduction in both weight and strength loss. These results highlight the advantages of using GPA as an alternative to conventional coarse aggregates. GPA not only enhances the mechanical and durability properties of concrete but also presents a more sustainable option, contributing to reduced environmental impacts associated with traditional aggregate materials.
1 Introduction
Industrialization and urbanization have brought numerous benefits, such as improved healthcare, economic growth, and technological advancements. These changes have also transformed the construction industry over the last two centuries, with the rapid adoption of innovative materials like prestressed and high-strength concrete (Saha and Rajasekaran, 2020; Rehman, 2019; Juma and Mustafaozakca, 2019). Concrete is the second most consumed material in the world after water, with an annual production of approximately 10 billion tons due to its cost-effectiveness, strength, durability, and versatility (Leelathawornsuk, 2018). However, this widespread use also presents significant challenges. The construction and demolition sector generates substantial waste, with the European Union producing around 374 million tons annually and India projecting an increase to 287 million tons per year by 2030. This waste requires extensive landfill space, leading to severe public health issues, high waste management costs, and environmental contamination (Gunasekera et al., 2018; Chindaprasirt, 2017; Gunasekera, 2008). Furthermore, concrete manufacturing significantly contributes to CO2 emissions, with cement production alone responsible for 8% of global emissions and the construction sector accounting for 39% of energy-related emissions (Dattatreya, 2019; Lakshman, 2019; Davidovits, 2018). Concrete production is responsible for around 10% of global CO2 emissions, significantly impacted by the environmental effects of aggregate procurement and transportation. With the global demand for construction aggregates expected to reach 53 billion metric tons by 2024, the scarcity of these materials has become a critical issue (Hajardijito, 2017). The International Energy Agency advocates for developing alternative materials to mitigate these environmental challenges (Harris, 2017; Karakurt, 2017; Lawson, 2017). Recycling waste materials, such as demolished concrete and industrial by-products, emerges as a promising solution, potentially reducing CO2 emissions by up to 30% and conserving natural resources. Innovations in concrete and mortar technologies, including the use of environmentally friendly materials like geopolymer concrete, align with sustainable development principles, aiming to reduce emissions, minimize waste, and enhance resource efficiency (Bishop, 2016). Research has investigated the viability of using waste materials as aggregate substitutes, with many countries adopting recycled aggregate (Hassan and arif, 2020). One method involves creating geopolymer aggregate (GPA) from slag and an alkaline solution, meeting the demand for new infrastructure (Moukanna et al., 2019). Ballast materials, typically comprising igneous or metamorphic rocks like granite or basalt, are known for their quality and specific properties. Basalts, particularly, show promise due to their favorable mechanical properties for concrete applications. Recycling GPA has shown promising results in partially replacing coarse aggregates in concrete, with replacement ratios reaching up to 20% (Muhd Izzat and Mohd, 2013). The cost of geopolymer concrete per cubic meter closely aligns with that of Portland cement concrete. However, when accounting for the potential environmental benefits associated with using GGBS and reducing the need for mining coarse aggregates in construction, geopolymer aggregate may offer both economic and environmental advantages (Gencel et al., 2021). Geopolymer aggregate have a lower elastic modulus compared to conventional ones like crushed stone or gravel, potentially leading to increased deformations under stress. Additionally, these materials may exhibit time-dependent deformation or creep under sustained loads, affecting the long-term performance of concrete structures. Comprehensive long-term studies are needed to understand the behavior of concrete structures using geopolymer materials, including monitoring deformation over time, assessing durability in various environmental conditions, and identifying potential degradation pathways. Despite these challenges, geopolymer materials offer environmental benefits such as reduced carbon emissions and enhanced chemical resistance compared to typical concrete, making them suitable for various construction applications. Ongoing innovation efforts aim to address these challenges, paving the way for long-term and sustainable construction solutions. Exploring the feasibility of incorporating higher proportions of geopolymer aggregate (GPA) into conventional concrete, and assessing its strength and durability, is a promising approach. The abundance and quality of GPA, along with positive findings in existing literature, support this proposition, despite limited research focusing on replacement ratios up to 100% and primarily examining strength and durability. Innovation in the construction sector is evident through the adoption of new materials like prestressed, high-strength, steel-reinforced, and fiber-reinforced concrete, enhancing construction processes. Additionally, there is a growing trend in researching alternate aggregate substitutes from waste resources, emphasizing sustainable construction practices. For instance, research has demonstrated that the use of pozzolans and nanoadditives in concrete can significantly reduce crack formation and propagation, enhancing the durability of the structures (Golewski, 2024a). Furthermore, the synergy between fly ash (FA) and nanosilica (Golewski, 2024b) has been shown to improve fracture behavior and structural integrity, making these materials highly relevant in the context of sustainable construction (Golewski, 2024c).
These efforts underscore a dedication to sustainable construction, striving to diminish environmental impacts and enhance material efficiency. This includes exploring the use of recycled aggregate in concrete production, already implemented in some regions. Research has shown that concrete composites containing fly ash, up to 30%, exhibit lower water absorption, which is crucial for long-term durability, particularly in structures exposed to water immersion (Golewski, 2023a). Moreover, studies have indicated that the grading of coarse aggregates can significantly affect the mechanical parameters and fracture toughness of concrete, making the careful selection and innovation of aggregates critical for future construction projects (Golewski, 2023b). Geopolymer aggregate, crafted from slag and an alkaline solution, provides an eco-friendly alternative to typical aggregates. Exploring the use of basalt as a concrete aggregate further contributes to these innovations, addressing the imperative to recycle construction waste while fulfilling infrastructure needs. The study examined the effects of GPA aggregates on mechanical and permeability properties, crucial for concrete durability. GPA was incrementally added to coarse aggregates at rates of 25%, 50%, 75%, and 100%. The addition of GPA improved compressive strength by 7%–15%, indicating potential for more durable concrete structures. Asymmetrical GPA showed better adhesion to cement paste, underscoring the importance of material quality. Flexural strength increased with GPA incorporation, suggesting improved load-bearing capacity. The GPA100 mix demonstrated enhanced moisture resistance and durability against sulfates and acids, potentially extending concrete service life in harsh environments. Overall, using GPA instead of coarse aggregate enhances concrete’s mechanical properties, longevity, and environmental resilience, promising high-performance, eco-friendly construction. The literature on sustainable construction materials has focused mainly on traditional aggregates, with limited research on alternative materials like geopolymer aggregate (GPA). This study addresses this gap by examining GPA’s impact on concrete’s mechanical and permeability properties. By using slag and an alkaline solution, GPA repurposes industrial waste and reduces environmental impact. These findings suggest that GPA can create more durable, eco-friendly concrete structures, offering a sustainable alternative to conventional aggregates.
2 Testing and methods
2.1 Materials
This research focuses on the application of three basic materials that are necessary for engineering and construction projects: ground granulated blast furnace slag (GGBS), river sand, and cement. Table 1 offers information on the chemical composition of each component of GGBS and cement separately. Tables 2, 3 provided an extensive overview of these materials’ physical characteristics. Moreover, the process of creating geopolymer aggregate (GPA) is essential to preserve natural resources. Raw material for GPA synthesis is GGBS, serving as foundational component for agglomeration. This agglomeration process is achieved by combining GGBS with an alkaline solution, which includes substances such as sodium silicate and sodium hydroxide. These dry components, encompassing GGBS and the alkaline solution, undergo thorough mixing using a mortar mixer to ensure an even distribution of the constituents throughout the mixture. The mechanism of preparation of GPA aggregates as shown in Figure 1.
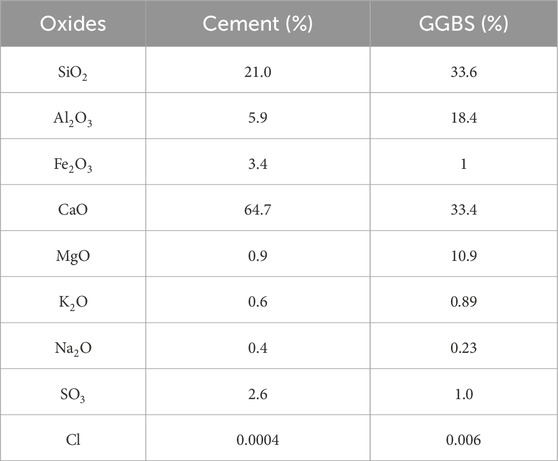
Table 1. Cement and GGBS chemical composition as provided by the manufacturer (Kumar and Kumar, 2023).
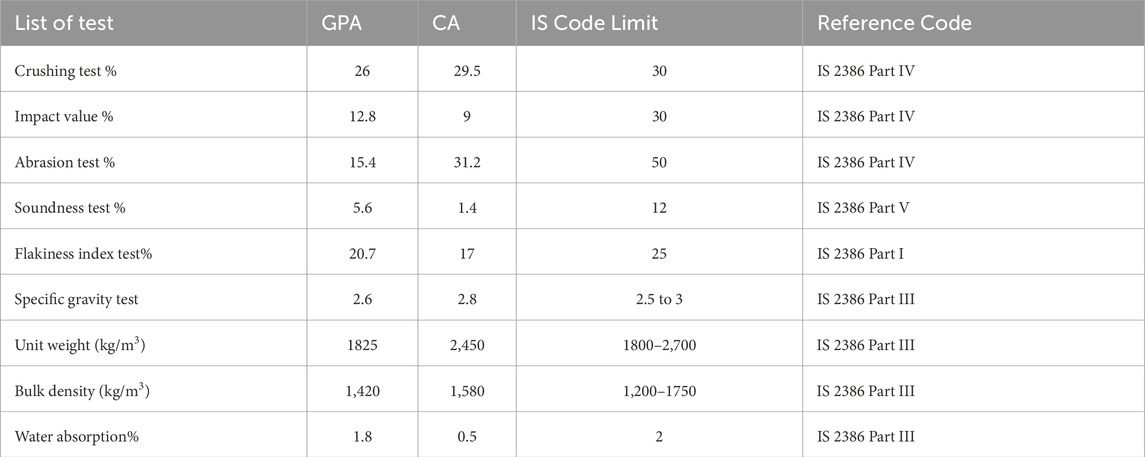
Table 3. Physical properties of geopolymer aggregate and natural aggregate (Kumar and Kumar, 2023).
Examining test findings entails contrasting geopolymer aggregates with natural aggregates (CA) that are often used in concrete, following the requirements for coarse aggregates specified in IS 2386 (PART III) - 1963. The detailed discussion highlights that geopolymer aggregates exhibit superior performance compared to natural aggregates, adhering to the IS 2386 (Part III) - 1963 standards. These standards specify that the crushing value should not exceed 26% and the impact value should not exceed 12.8%. Geopolymer aggregates typically show lower values for both tests, indicating better mechanical strength and toughness. This makes them a viable and sustainable alternative for concrete applications, providing comparable or superior durability and strength. Additionally, using geopolymer aggregates supports eco-friendly construction practices by recycling industrial byproducts.
Additionally, in order to comply with the IS regulation, the water absorption value for coarse aggregates must not exceed 2 and the flakiness value cannot exceed 25%. When compared to natural aggregate, artificial geopolymer coarse aggregate has abrasion value is less than natural aggregate. Based on equivalent mass, abrasion resistance of both aggregates is assessed in accordance with IS 2366 (PART IV) - 1963. Los Angeles abrasion machine’s geopolymer coarse aggregate has higher volume because of its lower density, which makes it take up more space. The discussion centers on IS 2366 (Part IV) - 1963 standards for evaluating abrasion resistance in aggregates, including geopolymer coarse aggregates. These standards guide the Los Angeles abrasion test, crucial for assessing durability in concrete applications. Geopolymer aggregates, with their lower density and higher volume per equivalent mass, often exhibit superior abrasion resistance compared to natural aggregates. This makes them promising for sustainable construction practices, leveraging industrial by-products effectively in concrete mixes. If compare between geopolymer and natural aggregate, it is recommended an equal volume of both materials be utilized for abrasion testing. This method would provide a more accurate and significant assessment of their abrasion resistance characteristics.
There are several steps involved in the production of geopolymer aggregates. After being formed, geopolymer stones are crushed. Following this stage of crushing, the material that is left behind is sieved in order to get size distribution, which is essential to getting necessary aggregate properties. This sieving operation helps in classifying geopolymer stones into required appropriate sizes of aggregate. Comprehensive comparison between geopolymer aggregates and conventional natural aggregates (NA) properties were studied. The distinctions in characteristics between the natural and geopolymer aggregates are carefully analysed and compared. Figure 2, provides graphical representation of grading curve for both natural aggregate and geopolymer coarse aggregate. Taken together, these irregular shapes make it difficult to properly compact the material, reduce packing density, increase water demand, and encourage stress concentrations in the concrete mixture, all of which lead to a weaker concrete product.
2.2 Mix proportions
Five different mixtures were prepared in this study, and their compositions are detailed in Table 4. When reviewing existing literature, it is observed that in concrete mixtures, substitution of ballast aggregate with regular aggregate was typically limited to maximum of 40% (Habert et al., 2020; Sainz-Aja et al., 2019; Kazmi et al., 2021; Dasari et al., 2020; Sainz-Aja et al., 2020a; Sainz-Aja J. A. et al., 2020b). However, in studies involving various recycled aggregates, particularly those based on basalt, this substitution rate varied widely, ranging from 25% to 100% (Sainz-Aja et al., 2020c). Consequently, this research utilized waste basalt-based ballast aggregate of high-quality, replacing the coarse aggregate with Geo polymer Aggregate (GPA) at rates of 25%, 50%, 75%, and 100%. These replacement percentages are denoted as GPA25, GPA50, GPA75 and GPA100mix respectively. The selection of the most suitable aggregate mixture was determined to be a combination of crushed stone aggregate by 60% and natural sand by 40%.
Once the aggregate ratio was established, the target concrete compressive strength was set to M25 grade. To validate the design, slump tests as shown in Figure 3 were conducted according to IS 1199 (1959). The values were calculated by volume basis. GPA concrete manufacturing process as shown in Figures 4A–D.
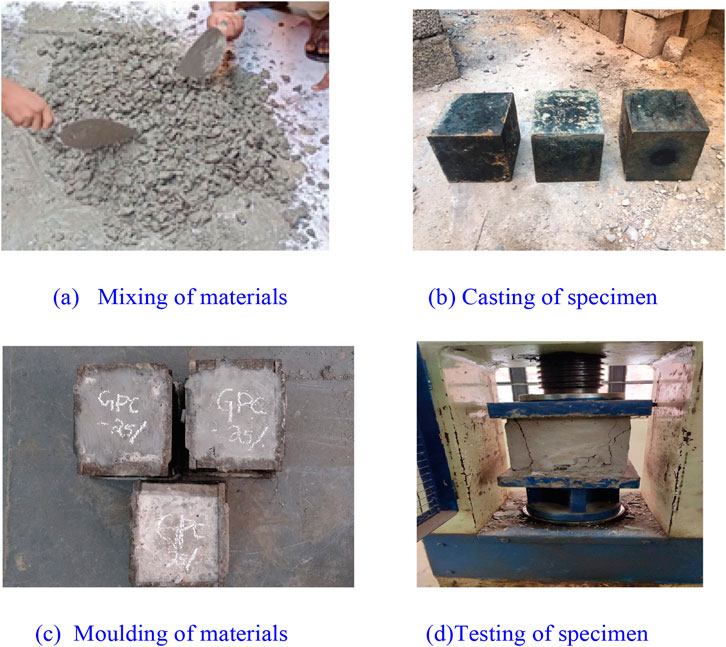
Figure 4. (A) Mixing of materials, (B) Casting of specimen, (C) Moulding of materials, (D) Testing of specimen: GPA concrete manufacturing process.
2.3 Material testing
2.3.1 Test on mechanical property
At specified intervals of 7 and 28 days, assessment of compressive and flexural strength for various mixtures was carried out following guidelines outlined in IS 516 (1959) (Kazmi et al., 2021). To determine compressive strength of each mix, three cubic specimens, each measuring 150 mm × 150 mm × 150 mm are employed. In flexural test, three prism specimen each with dimensions of 100 mm × 100 mm × 500 mm are used. Utilizing average values obtained from these specimens, compressive and flexural strengths are subsequently computed as shown in Figures 5A, B.
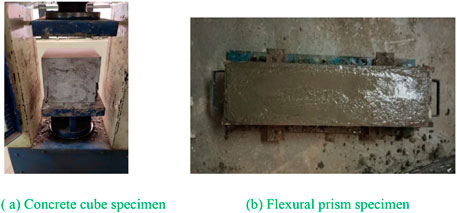
Figure 5. Material testing on mechanical property of specimen. (A) Concrete cube specimen, (B) Flexural prism specimen.
2.3.2 Sorptivity test
To evaluate capillary action within the concrete pore structure, the sorptivity test was conducted in accordance with ASTM C 1585–04 standards. This test assesses the concrete’s ability to draw fluids into its structure. Initially, a coefficient variation of 6% was established as an acceptable range for absorption measurements. The testing process involved concrete slices of 100 mm diameter and 50 mm thickness in dimensions which is shown in Figure 6. To ensure precision, specimen’s sides were wax coated and sealed using plastic sheets before initial mass measurement. During test, specimens were immersed in a tray containing water to depth ranging from 2 to 5 mm. Upon taking measures to eliminate any excess surface water and ensuring proper drainage, specimen mass was measured at specified intervals. Hence, sorptivity value is determined by calculating slope of line that offered most accurate fit for cumulative absorption value plotted against square root of time.
2.3.3 Acid resistance test
Following a 28-day curing period from the first casting, Geopolymer Aggregate Concrete (GPC) was subjected to an acid resistance assessment using 100 mm cubes. The initial weights of these specimens were meticulously documented before immersing them separately in two solutions such as 3% hydrochloric acid (Hcl) and 3% sulfuric acid (H2SO4), each for duration of 30 days as shown in Figure 7. It's worth noting that the concentration of these acid solutions remained constant throughout the entire test. At the conclusion of the 30-day immersion period, specimens were carefully removed from acid solutions. Surface of each cube underwent thorough cleaning, and their weights were re-measured. Following this, the cubes were subjected to compression testing using equipment with a 1,000 kN capacity, applying a consistent loading rate of 140 kg/cm2/min. This assessment encompassed the calculation of both weight loss and the reduction in compressive strength observed in GPA cubes after exposure to the acid solutions.
2.3.4 Sulphate resistance test
The evaluation of sulphate resistance was carried out meticulously, following ASTM C 642 the standards. To assess durability resistance of geopolymer concrete to sulphate exposure, both mass change and residual compressive strength were calculated. For these sulphate resistance tests, concrete specimens took the sizeof 150 mm × 150 mm × 150 mm cubes and 100 mm × 200 mm cylinders. All mixtures of geopolymer aggregate concrete specimens were immersed in depth of 30 mm in two distinct solutions: a 3% sodium sulphate solution and a 3% sodium chloride solution. Furthermore, a magnesium sulphate solution was introduced to the geopolymer concrete specimens on the third day following casting. Subsequently, complete submersion in these solutions occurred on the 14th and 28th days, with a volume four times that of the specimens to ensure sufficient exposure. The solutions were refilled weekly to maintain the desired concentration and consistency, with regular mixing to prevent any deposits from forming at base. Effects of these solutions on specimens were periodically assessed through visual examinations, weight change measurements and strength tests. During compression testing process, surfaces of cubes were cleaned, weighed and subjected to strength testing.
3 Results and discussion
3.1 Test for compressive strength
Results of compressive strength test for specimens are graphically represented in Figure 8. As proportion of GPA increased, there was corresponding rise in compressive strength of mixtures. Specifically, at 7-day testing, compressive strength displayed increments of 5% for GPA25, 6.6% for GPA50, 10.5% for GPA75, and 15.5% for GPA100 when compared to control mixture. The + compressive strength at 28 days exhibited improvements in range of 6.5%, 7.3%, 9.5% and 15.1% respectively, for same GPA mixtures. These findings demonstrate that inclusion of GPA had positive impact on compressive strength of concrete. This enhancement could be attributed to two critical factors. First, high-quality nature of GPA, supported by Ray et al. (2021), played a significant role. Second, irregular particle shape of GPA contributed to increased adhesion between paste and GPA, as mentioned in Mo et al. (2020). Importantly, existing literature also underscores favorable influence of GPA or basalt on compressive strength. For instance, employed GPA as a substitute for coarse aggregate with increasing percentages leading to higher compressive strength. Concrete incorporating recycled ballast met compressive strength criteria for slab track construction. Strength of concrete made with limestone and gravel aggregate made with basalt aggregate, showing boost in strength with basalt (Sainz-Aja J. A. et al., 2020). Experiments with varying percentages of basalt replacing coarse aggregate consistently found that use of basalt improved compressive strength (Sainz-Aja et al., 2020c). In another study, substituted crushed stone with 100% basalt in high-strength self-compacting concrete yielded the highest compressive strength exceeding the control mixture (Ray et al., 2021). Mechanical properties and enhanced compressive strength of concrete manufactured from waste basalt as well as natural basalt were similar (Mo et al., 2020). In summary, utilization of GPA100 mix increased compressive strength, compared to lesser extent than reported in existing literature. Difference can be attributed to substantially higher replacement ratio of GPA employed in our study compared to previous studies.
3.2 Flexural strength test
Figure 9 illustrates outcomes of flexural strength tests conducted on mixtures. Control mixture and GPA100 mix demonstrated lowest and highest flexural strengths, at both 7 and 28 days. Remarkably, flexural strength of GPA100mix improved by 6.5% and 7.5% at 7 and 28 days, respectively, in comparison with control mixture. This underscore positive effect of incorporating geopolymer aggregate on mixtures flexural strength. This enhancement can be attributed to uneven and elongated shape of GPA, as discussed in Bishop (2016). In a similar, replacement of 20% of coarse aggregate with GPA resulting in notable increases of 17.5% and 19.2% in flexural strengths at 7 and 28 days (Mohammed and Najim, 2020). Experiments were carried out in over-burnt brick ballast in place of coarse aggregate, and it is discovered that 20% of GPA100mix utilisation resulted in a notable 30% increase in 28-day flexural strength when compared to control mixture (Dong et al., 2021). It was also highlighted that concrete with basalt aggregate showed greater levels of strength than concrete with gravel aggregate. These test results clearly show that the addition of GPA to our study improved the combinations’ flexural strength (International Energy Agency IEA, 2024).
3.3 Test on water absorption
First, cast concrete cubes in standard molds measuring 150 mm × 150 mm × 150 mm and cure them under controlled conditions for 28 days to ensure proper hydration and strength development as shown in Figure 10. Once cured, remove the cubes and dry their surfaces with an absorbent cloth to remove any residual moisture. Weigh each cube using a precise scale to obtain the dry weight. Next, immerse the dried cubes in a water bath or container fully filled with water, ensuring that the cubes are completely submerged. Allow them to remain in the water for 24 h to achieve saturation. After this period, carefully remove the cubes from the water and wipe their surfaces with an absorbent cloth to remove excess water, being careful not to remove water absorbed into the pores of the concrete. The investigation encompassed a methodical assessment of water absorption in concrete squares with predetermined dimensions, thereby guaranteeing a regulated and dependable experimental configuration. The purpose of the study was to determine whether ground-granulated blast furnace slag (GGBS) could be used in place of geopolymer aggregate (GPA) in concrete compositions. This change was made to allow for a direct comparison between the two mixes by investigating the influence of water absorption. Figure 11 shows a significant decrease in water absorption when GGBS was used, with a reduction of 42.58% compared to samples containing GPA100 mix. This finding was supported by precise quantitative data, such as the 0.75% average water absorption detected in GPA concrete samples. The observed decrease in water absorption shows that the presence of GGBS may potentially lead to advances in the strength and durability of concrete, therefore implying that overall performance of concrete could be improved. As a result, the findings highlight the importance of GGBS in building materials, not only for its ability to reduce water absorption, but also for its potential to promote ecologically sustainable construction practices.
The inclusion of Ground Granulated Blast Furnace Slag (GGBS) in concrete significantly reduces water absorption, enhancing the material’s strength and durability by minimizing porosity (Siddique, 2014). Studies have shown that GGBS improves concrete’s resistance to harmful substances, freeze-thaw cycles, and alkali-silica reactions, leading to longer-lasting structures (Thomas et al., 2012). Additionally, GGBS promotes ecological sustainability by reducing the need for Portland cement and lowering the carbon footprint of concrete production (Gao, 2015). These benefits highlight GGBS as a valuable component in modern concrete, aligning with both performance and environmental goals in construction. The integration of GGBS into concrete formulas increases the potential for environmentally responsible construction practices, which aligns with the construction industry’s growing emphasis on sustainability.
3.4 Sorptivity
As indicated in Figure 12A, the experimental configuration requires the plotting of absorption values against the square roots of time. This graphic illustrates the temporal evolution of absorption for different concrete compositions. As depicted in Figure 12A, this configuration facilitates a direct juxtaposition of conventional concrete (represented by the blue line) and geopolymer aggregate (GPA) concrete (represented by the red line), thereby enabling an evaluation of their distinct absorption characteristics. A quantitative analysis is performed by calculating sorptivity values for each concrete type (obtained from the slope of the absorption curve). This enables a thorough comparison of the absorption characteristics. The influence of GPA100mix in addition on sorptivity is additionally clarified in Figure 12B, which illustrates a significant decline in comparison to the control sample, with the minimum recorded value of 0.1062 indicating a reduction of approximately 47.9%. The aforementioned numerical observation highlights the importance of GPA in mitigating water absorption and implies possible enhancements to the functionality of concrete, specifically with regard to increased resistance to water, longevity, and durability. Therefore, the significance of GPA in preventing water absorption and its adverse impacts on concrete structures is highlighted by these results. The inclusion of GPA in concrete significantly reduces water absorption, enhancing the material’s resistance to water, durability, and longevity (Chindaprasirt et al., 2007). Studies have shown that GPA improves concrete by refining its pore structure, increasing compressive strength, and reducing thermal cracking (Neville, 1996). GPA also contributes to environmental sustainability by reducing the carbon footprint of concrete production (Sata et al., 2007). These benefits highlight GPA’s multifaceted importance in modern concrete technology, improving both the performance and sustainability of concrete structures.
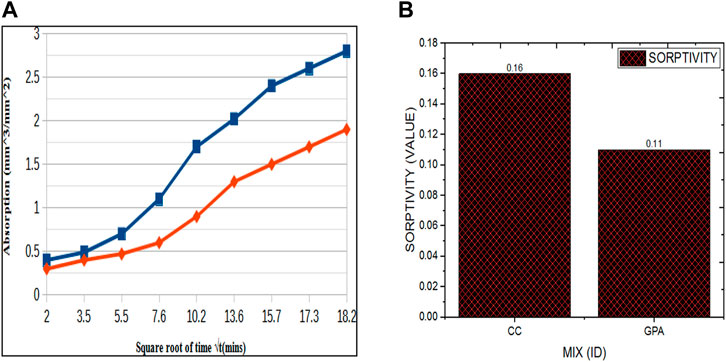
Figure 12. (A) Absorption Vs. Square root of time, (B) Sorptivity of conventional vs. GPA100 mix concrete.
3.5 Acid resistance test
The test findings provide a thorough description of trial arrangement and results regarding acid resistance of concrete built with geopolymer aggregate (GPA). The findings demonstrate reduction in weight and compressive strength of GPA concrete specimens following 30 days of immersion in solutions containing 3% H2SO4 and HCl.
These findings offer important insights into material’s behavior in acidic conditions. Figure 13 clearly depicts changes in weight and strength decreases of GPA concrete specimens, making it easier to compare and evaluate experimental data. Additionally, visual representation of data is enhanced by distinctions in strength and weight reductions for both acidic solutions, which are depicted in Figure 13. The work emphasizes that including GPA into concrete significantly improves its resistance to acid, resulting in lower percentage losses in both strength and weight when compared to control specimens. This study means that GPA concrete performs similarly, if not better, than conventional concrete and GGBS-based aggregate concrete, both of which have previously been tested in corrosive environments. Nonetheless, it is worth noting that, while GPA concrete is more resistant to acids, its reduced structural compactness reduces its efficiency as a barrier against H2SO4 and HCl. As a result, weight and compressive strength deficiencies become more noticeable after the 30-day exposure period. Overall, the findings of this study highlight the endurance and viability of GPA concrete as an alternative material in acidic environments. Furthermore, they underline the importance of using structural attributes when assessing operational effectiveness. Despite these deficiencies, GPA concrete demonstrates notable endurance and viability as an alternative material in such conditions, due to its improved resistance to acid attacks compared to traditional Portland cement concrete (Ahmad et al., 2011). This improved resistance is attributed to GPA’s lower calcium hydroxide content and the formation of more stable compounds (Ganjian et al., 2009). The study also emphasizes the importance of evaluating structural attributes, such as porosity and microstructure, to assess the long-term operational effectiveness of construction materials (Al-Khaiat and Ayesh, 2002). These findings are supported by various studies highlighting the benefits of using supplementary cementitious materials like GPA in enhancing the durability and sustainability of concrete.
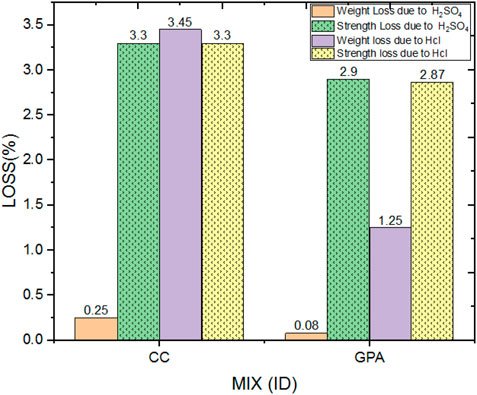
Figure 13. Weight and compressive strength loss of GPA100 mix on exposure to H2SO4 and Hcl solution.
3.6 Sulphate resistance test
Results on the deterioration of weight and compressive strength of geopolymer aggregate (GPA) concrete specimens after 30 days of immersion in a 3% sodium sulfate solution. Visual representations of the variations in weight and strength decreases, respectively, are presented in Figure 8. A significant observation is presented concerning the progression of strength in GPA100 mix concrete as opposed to conventional concrete (CC). In contrast to the modest 6% increase in strength observed in GPA100 mix concrete, conventional concrete demonstrates a substantial 63% increase in strength during the course of 28 days.
This implies that the ultimate strength of GPA concrete is achieved at a quicker rate compared to conventional concrete. In addition, the text presents data regarding the decrease in weight and compressive strength that were noted in GPA concrete specimens subsequent to a 30-day immersion in a 3% sodium chloride solution. The fluctuations in weight and strength reductions are visually represented in Figure 14. Notwithstanding slight fluctuations in weight spanning from 0.4% to 1.35% throughout the duration of exposure, conventional concrete specimens undergo a substantial decline in strength of approximately 12.2%. GPA concrete specimens, on the other hand, exhibit virtually no discernible strength decline. The results of this study emphasize the exceptional longevity and robustness of GPA concrete, specifically when exposed to corrosive chemical surroundings, thereby establishing its viability as a dependable building material. The study demonstrates that GPA concrete maintains its strength and shows virtually no decline in performance even in corrosive chemical environments (Berndt, 2009). This durability is attributed to GPA’s ability to form a denser, less permeable matrix and stable chemical compounds resistant to acids (Bentz et al., 2012). Comparative studies support these findings, showing that SCMs like GPA enhance concrete durability (Chi and Huang, 2013). The implications for construction are significant, with GPA concrete offering a reliable, sustainable option for structures exposed to harsh conditions, reducing maintenance costs and environmental impact (Hossain, 2006).
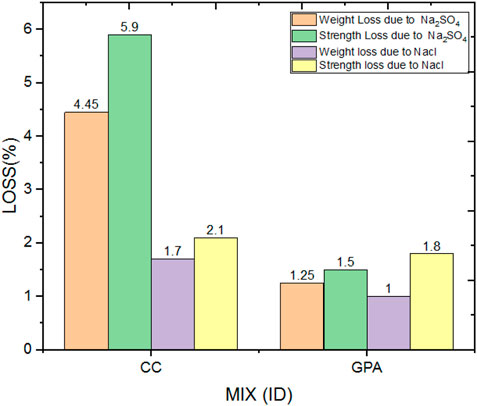
Figure 14. Weight loss and strength loss of GPA100 mix on exposure to sodium sulphate and sodium chloride solution.
4 Conclusion
•The incorporation of GPA in concrete mixtures led to significant improvements in compressive strength. Specifically, the GPA25, GPA50, GPA75, and GPA100 mixes demonstrated strength increases of approximately 7%, 8%, 10%, and 15%, respectively, compared to the control mixture. At 7 and 28 days, the GPA100 mix showed 7.5% and 6% higher compressive strength than the control, indicating a robust improvement in early and later age strength.
•The GPA100 mix exhibited remarkable enhancements in durability, with a 42.58% reduction in water absorption and a 47.9% decrease in sorptivity compared to traditional aggregate concrete. These results suggest that GPA concrete has a much lower susceptibility for water ingress, contributing to its long-term durability and service life.
•The GPA100 mix demonstrated substantial resistance to aggressive environmental conditions. In acid and sulfate resistance tests, GPA100 showed significantly lower weight loss and strength degradation compared to conventional aggregate concrete. This resistance to chemical attack suggests that GPA concrete is more suitable for use in environments exposed to acidic or sulfate-rich conditions.
•Utilizing GPA as a substitute for conventional coarse aggregate promotes sustainability by reducing reliance on natural resources and minimizing the environmental footprint of concrete production. This makes GPA concrete an environmentally friendly option that aligns with sustainable construction practices.
The findings underscore the practical applicability of using GPA in various concrete structures, especially where enhanced durability, mechanical properties, and environmental resistance are critical. GPA concrete can be particularly beneficial in infrastructure projects exposed to harsh environmental conditions, such as marine environments, industrial floors, and wastewater treatment plants. Additionally, exploring the economic viability and scalability of GPA production could facilitate its broader adoption in the construction industry.
Data availability statement
The original contributions presented in the study are included in the article/supplementary material, further inquiries can be directed to the corresponding author.
Author contributions
TU: Conceptualization, Data curation, Formal Analysis, Funding acquisition, Investigation, Methodology, Project administration, Resources, Software, Supervision, Validation, Visualization, Writing–original draft, Writing–review and editing. MV: Conceptualization, Data curation, Formal Analysis, Funding acquisition, Investigation, Methodology, Project administration, Resources, Software, Supervision, Validation, Visualization, Writing–original draft, Writing–review and editing. SS: Conceptualization, Data curation, Formal Analysis, Funding acquisition, Investigation, Methodology, Project administration, Resources, Software, Supervision, Validation, Visualization, Writing–original draft, Writing–review and editing. RC: Conceptualization, Data curation, Formal Analysis, Funding acquisition, Investigation, Methodology, Project administration, Resources, Software, Supervision, Validation, Visualization, Writing–original draft, Writing–review and editing. EA: Conceptualization, Data curation, Formal Analysis, Funding acquisition, Investigation, Methodology, Project administration, Resources, Software, Supervision, Validation, Visualization, Writing–original draft, Writing–review and editing.
Funding
The author(s) declare that financial support was received for the research, authorship, and/or publication of this article. The authors extend their appreciation to King Saud University for funding this work through Researchers Supporting Project number (RSP 2024R164), King Saud University, Riyadh, Saudi Arabia. This article was co-funded by the European Union under the REFRESH—Research Excellence for Region Sustainability and High-tech Industries project number CZ.10.03.01/00/22_003/0000048 via the Operational Program Just Transition and has been done in connection with project Students Grant Competition SP2024/087 ‘Specific Research of Sustainable Manufacturing Technologies’ financed by the Ministry of Education, Youth and Sports and Faculty of Mechanical Engineering VŠB-TUO.
Conflict of interest
The authors declare that the research was conducted in the absence of any commercial or financial relationships that could be construed as a potential conflict of interest.
Publisher’s note
All claims expressed in this article are solely those of the authors and do not necessarily represent those of their affiliated organizations, or those of the publisher, the editors and the reviewers. Any product that may be evaluated in this article, or claim that may be made by its manufacturer, is not guaranteed or endorsed by the publisher.
References
Ahmad, S., Siddique, R., and Awais, M. (2011). Durability of concrete in acidic environments: a review. Constr. Build. Mater. 25 (2), 957–965. Available at: https://publisher.uthm.edu.my/ojs/index.php/IJSCET/article/view/653
Al-Khaiat, H., and Ayesh, A. (2002). Performance of concrete containing various supplementary cementitious materials exposed to acidic environments. Constr. Build. Mater. 16 (8), 659–664.
Bentz, D. P., Ferraris, C. F., Jones, S. Z., Hansen, A. S., and Guynn, J. M. (2012). Influence of particle size distributions on yield stress and viscosity of cement-fly ash pastes. Cem. Concr. Res. 42 (2), 404–409. doi:10.1016/j.cemconres.2011.11.006
Berndt, M. L. (2009). Properties of sustainable concrete containing fly ash, slag, and recycled concrete aggregate. Constr. Build. Mater. 23 (7), 2606–2613. doi:10.1016/j.conbuildmat.2009.02.011
Bishop (2016). Flexural strength ofconcrete beams with corroding reinforcement. ACI Struct. J. 10 (7), 156–162. doi:10.14359/606
Chi, M., and Huang, R. (2013). Effect of phosphate addition on the properties of fly ash-based geopolymer. Cem. Concr. Compos. 34 (9), 1023–1030. doi:10.1016/j.conbuildmat.2020.121486
Chindaprasirt (2017). Correlation ratio on phase and microstructure of reaction products of metakaolin-rice husk ash geopolymer. Constr. Build. Mater. 226 (25), pp406–417. doi:10.1016/j.conbuildmat.2019.07.146
Chindaprasirt, P., Chotithanorm, C., Cao, H. T., and Sirivivatnanon, V. (2007). Influence of fly ash fineness on strength, drying shrinkage and sulfate resistance of blended cement mortar. Cem. Concr. Res. 37 (7), 1037–1044. doi:10.1016/j.cemconres.2003.11.021
Dasari, N., Jogi, S., Daripalli, V. B., and Suryawanshi, P. (2020). Comparative analysis of concrete strength against recyclable ballast and granite scrap as partial replacement of coarse aggregate. Int. J. Prog. Res. Sci. Eng. 1, 36–41.
Dattatreya (2019). High-alkali cements for 21st century concretes. Concr. Technol. Past, Present Future 144 (19), 383–398. Published by International Concrete Abstract portal.
Davidovits (2018). Geopolymer inorganic polymeric new materials. Int. J. Alkalinity Phys. Sci. 5 (37), 1633–1656. doi:10.14359/4523
Dong, Q., Wang, G., Chen, X., Tan, J., and Gu, X. (2021). Recycling of steel slag aggregate in Portland cement concrete: an overview. J. Clean. Prod. 282, 124447. doi:10.1016/j.jclepro.2020.124447
Ganjian, E., Khorami, M., and Maghsoudi, A. A. (2009). Effect of pozzolans on the properties of concrete subjected to acidic attack. Cem. Concr. Compos. 31 (6), 383–391.
Gao, X., Oti, J. E., Kinuthia, J. M., Adeleke, B. O., and Billong, N. (2015). Durability of concrete containing GGBS against freeze-thaw cycles. J. Mater. Civ. Eng. 27 (7), 04014221.
Gencel, O., Karadag, O., Oren, O. H., and Bilir, T. (2021). Steel slag and its applications in cement and concrete technology: a review. Constr. Build. Mater. 283, 122783. doi:10.1016/j.conbuildmat.2021.122783
Golewski, G. L. (2023a). Assessing of water absorption on concrete composites containing fly ash up to 30% in regards to structures completely immersed in water. Case Stud. Constr. Mater. 19, e02337. doi:10.1016/j.cscm.2023.e02337
Golewski, G. L. (2023b). Examination of water absorption of low volume fly ash concrete (LVFAC) under water immersion conditions. Mater. Res. Express 10 (8), 085505. doi:10.1088/2053-1591/acedef
Golewski, G. L. (2024a). Investigating the effect of using three pozzolans (including the nanoadditive) in combination on the formation and development of cracks in concretes using non-contact measurement method. Adv. Nano Res. 16 (3), 217. doi:10.12989/anr.2024.16.3.217
Golewski, G. L. (2024b). Enhancement fracture behavior of sustainable cementitious composites using synergy between fly ash (FA) and nanosilica (NS) in the assessment based on digital image processing procedure. Theor. Appl. Fract. Mech. 131, 104442. doi:10.1016/j.tafmec.2024.104442
Golewski, G. L. (2024c). Determination of fracture mechanic parameters of concretes based on cement matrix enhanced by fly ash and nano-silica. Materials 17 (17), 4230. doi:10.3390/ma17174230
Gunasekera (2008). “Sustainability acid resistant eco-friendly concrete from geo-polymerization of blast furnace slag” Structural Engineering Research Centre. 19 (21). 357–367.
Gunasekera, C., Law, D. W., and Setunge, S. (2018). Effect of geopolymer aggregate on strength and microstructure of concrete. ACI Mater. J. 115 (6), 899–908. doi:10.14359/51706846
Habert, G., Miller, S. A., John, V. M., Provis, J. L., Favier, A., Horvath, A., et al. (2020). Environmental impacts and decarboniza-tion strategies in the cement and concrete Industries. Nat. Rev. Earth Environ. 1, 559–573. doi:10.1038/s43017-020-0093-3
Hajardijito (2017). High strength concrete manufacture and properties. Int. Conf. Sustain. Eng. Tech. 47 (2), 441–448.
Harris (2017). Utilization of natural zeolite inaerated concrete production. Cem. Concr. Compos. Int. J. Concr. Struct. Mater. 32 (1), 1–8.
Hassan, A., and Arif, M. (2020). Stability of glassy concrete under elevated temperatures. Eur. J. Environ. Civ. Eng. 8 (6), 3157–3168.
Hossain, K. M. A. (2006). Blended cement using volcanic ash and pumice. Cem. Concr. Res. 36 (6), 1123–1129.
International Energy Agency (IEA) (2024). United States—policies and legislation. Available at: http://www.ieahev.org/by-country/united-states-policy-and-legislation/. (Accessed on December 27, 2022).
Juma, M., and Mustafaozakca, (2019). Fire-resistant geo-polymer produced by granulated blast furnace slag. ROC Mater. J. 26 (12), 205–210.
Karakurt (2017). Microstructure properties of waste tire rubber composites. J. material cycle waste Manag. 26 (5), 422–433.
Kazmi, S. M. S., Munir, M. J., and Wu, Y. F. (2021). Application of waste tire rubber and recycled aggregates in concrete products: a new compression casting approach. Resour. Conserv. Recycl. 167, 105353. doi:10.1016/j.resconrec.2020.105353
Kumar, T. U., and Kumar, M. V. (2023). Microstructure characteristics of geopolymer aggregate concrete on the effect of liquid/slag ratio. J. Build. Pathology Rehabilitation 8 (2), 104. doi:10.1007/s41024-023-00348-5
Lakshman (2019). The role of inorganic polymer technology in the development of green concrete. Cem. Concr. Res. 37 (17), 1590–1597.
Lawson (2017). Non-destructive evaluation of concrete using ultrasonic pulse velocity. Nucl. Appl. Cent. Nac. 22 (8), 125–161.
Leelathawornsuk (2018). Workability and strength of coarse high calcium geo-polymer. Cem. Concr. Compos. 22 (12), 224–229.
Mo, K. H., Thomas, B. S., Yap, S. P., Abutaha, F., and Tan, C. G. (2020). Viability of agricultural wastes as substitute of natural aggregate in concrete: a review on the durability-related properties. J. Clean. Prod. 275, 123062. doi:10.1016/j.jclepro.2020.123062
Mohammed, S. I., and Najim, K. B. (2020). Mechanical strength, flexural behavior and fracture energy of recycled concrete aggregate self-compacting concrete. Structures 23, 34–43. doi:10.1016/j.istruc.2019.09.010
Moukanna, S., Nazari, A., Bagheri, A., Loutou, M., Sanjayan, J., and Hakkou, R. (2019). Alkaline fused phosphate mine tailings for geopolymer mortar synthesis: thermal stability, mechanical and microstructural properties. J. Non-Crystalline solids 511 (4), 76–85. doi:10.1016/j.jnoncrysol.2018.12.031
Muhd Izzat, A., and Mohd, A. (2013). Sulfuric acid attack on ordinary Portland cement and geopolymer material. Tech. Univ. Cluj Napoca, Fac. Civ. Eng. 3 (6), 343–350.
Ray, S., Haque, M., Soumic, S. A., Mita, A. F., Rahman, M. M., and Tanmoy, B. B. (2021). Use of ceramic wastes as aggregates in concrete production: a review. J. Build. Eng. 43, 102567. doi:10.1016/j.jobe.2021.102567
Rehman, A., Abbas, N., Saba, T., Rahman, S. I. U., Mehmood, Z., and Kolivand, H. (2019). Classification of acute lymphoblastic leukemia using deep learning. ACI Material J. 81 (11), 1310–1317. doi:10.1002/jemt.23139
Saha, S., and Rajasekaran, C. (2020). Enhancement of the properties of fly ash based geopolymer paste incorporating ground granulated blast furnace slag. Asian J. Civ. Eng. 146 (6), 615–620. doi:10.1016/j.conbuildmat.2017.04.139
Sainz-Aja, J., Carrascal, I., Polanco, J. A., Thomas, C., Sosa, I., Casado, J., et al. (2019). Self-compacting recycled aggregate concrete using out-of-Service railway superstructure wastes. J. Clean. Prod. 230, 945–955. doi:10.1016/j.jclepro.2019.04.386
Sainz-Aja, J., Pombo, J., Tholken, D., Carrascal, I., Polanco, J., Ferreño, D., et al. (2020c). Dynamic calibration of slab track models for railway applications using full-scale testing. Comput. Struct. 228, 106180. doi:10.1016/j.compstruc.2019.106180
Sainz-Aja, J., Thomas, C., Carrascal, I., Polanco, J. A., and de Brito, J. (2020a). Fast fatigue method for self-compacting recycled aggregate concrete characterization. J. Clean. Prod. 277, 123263. doi:10.1016/j.jclepro.2020.123263
Sainz-Aja, J. A., Carrascal, I. A., Polanco, J. A., Sosa, I., Thomas, C., Casado, J., et al. (2020b). Determination of the optimum amount of superplasticizer additive for self-compacting concrete. Appl. Sci. 10, 3096. doi:10.3390/app10093096
Sata, V., Jaturapitakkul, C., and Kiattikomol, K. (2007). Influence of pozzolan from various by-product materials on mechanical properties of high-strength concrete. Constr. Build. Mater. 21 (7), 1589–1598. doi:10.1016/j.conbuildmat.2005.09.011
Siddique, R. (2014). Utilization of industrial by-products in concrete. Procedia Eng. 95, 335–347. doi:10.1016/j.proeng.2014.12.192
Keywords: alkaline solution, geopolymer aggregate, durability, compressive strength, flexural strength, sorptivity
Citation: Udhaya Kumar T, Vinod Kumar M, Salunkhe S, Cep R and Abouel Nasr E (2024) Impact of geopolymer aggregate on the mechanical properties and durability characteristics of concrete. Front. Built Environ. 10:1445954. doi: 10.3389/fbuil.2024.1445954
Received: 08 June 2024; Accepted: 29 October 2024;
Published: 13 November 2024.
Edited by:
Abdullah Mohsen Zeyad, Jazan University, Saudi ArabiaReviewed by:
Kinga Korniejenko, Cracow University of Technology, PolandGrzegorz Golewski, Lublin University of Technology, Poland
Copyright © 2024 Udhaya Kumar, Vinod Kumar, Salunkhe, Cep and Abouel Nasr. This is an open-access article distributed under the terms of the Creative Commons Attribution License (CC BY). The use, distribution or reproduction in other forums is permitted, provided the original author(s) and the copyright owner(s) are credited and that the original publication in this journal is cited, in accordance with accepted academic practice. No use, distribution or reproduction is permitted which does not comply with these terms.
*Correspondence: Sachin Salunkhe, c2FjaGluc2FsdW5raGVAZ2F6aS5lZHUudHI=