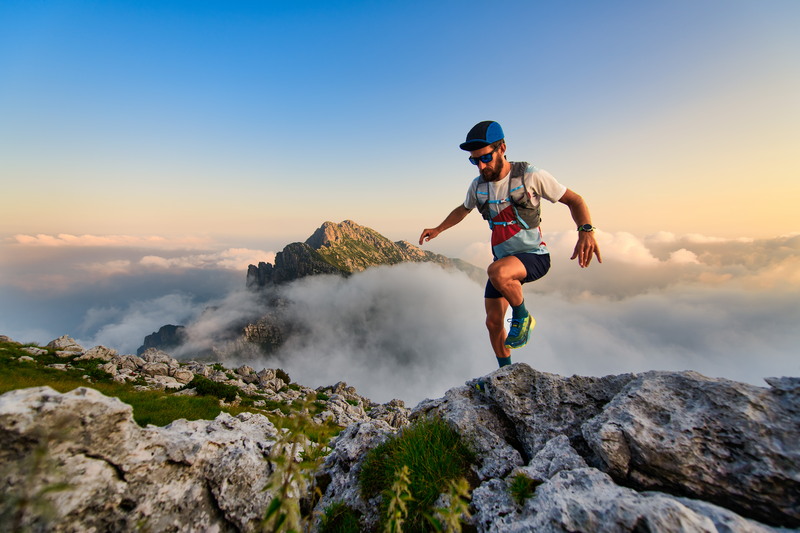
95% of researchers rate our articles as excellent or good
Learn more about the work of our research integrity team to safeguard the quality of each article we publish.
Find out more
EDITORIAL article
Front. Robot. AI , 08 April 2024
Sec. Soft Robotics
Volume 11 - 2024 | https://doi.org/10.3389/frobt.2024.1399217
This article is part of the Research Topic Design, Modeling and Control of Kinematically Redundant Robots View all 5 articles
Editorial on the Research Topic
Design, modeling and control of kinematically redundant robots
Redundant robots, which were originally inspired by biological redundant structures, have more joints and movable axes than the minimum required to reach a specific position and orientation in their workspace (Spong et al., 2020). Redundancy improves flexibility and dexterity, thereby improving obstacle avoidance and fault tolerance, and leads to improved environmental adaptability and system robustness. However, redundant mechanical structures not only increase the difficulty of mechanical design, but also increase the number of actuators and sensors, and pose challenges in control and path planning. Recent research has deeply integrated machine learning methods with the design, modeling, and control of redundant robots to reduce modeling difficulty, improve control efficiency, and enhance system reliability (Jin et al., 2018; Wang et al., 2021; Li, 2023). This Research Topic assembles some representative works, including the discussion of existing challenges in redundant soft robot modeling (Sadati et al.), and latest breakthrough in using continuum robots to improve dexterity (Grassmann et al.; Yang et al.), and solving the control and planning problems with learning techniques (Yang et al.; Ma et al.).
Sadati et al. reviewed and compared the techniques of Reduced-Order Modeling (ROM) and Model Order Reduction (MOR) that improve the control efficiency of Soft Robots. Controlling soft robots is difficult because their shapes are complex and their configuration spaces are high-dimensional (Whitesides, 2018). Geometrically exact modeling approaches, like Cosserat rod and Finite Element Methods (FEM), are computationally expensive for real-time control (Till et al., 2019). ROM and MOR can address these challenges by creating lower-dimensional models of the soft robot. ROM uses simplifying assumptions to create a lower-dimensional model, while MOR reduces the state-space dimension of a high-fidelity FEM-based model. The work provides an in-depth survey of ROM and MOR techniques for the continuum and soft robotics and can provide aid in selecting proper models for specific tasks.
Grassmann et al. presented a fully actuated segment (FAS) design for tendon-driven continuum robots to verify the hypothesis that utilizing all degrees of freedom significantly improves motion capabilities, follow-the-leader (FTL) deployment, and position and orientation capabilities. Being different from rigid surgical robots or other tendon-driven flexible robots, the actuated twist of the proposed system is implemented by reconsidering spacer disks and leveraging the design of a concentric tube continuum robot. It translated the robot backbone and used floating spacer disks to implement variable segment lengths (Li et al., 2019; Anderson et al., 2024; Rosen et al., 2017). By simply rotating the backbone, it achieves variable tendon routing, therefore, it exploits four DOF for one segment; bending in two planes, translation, and rotation.
Yang et al. also studied continuum robots. This work utilized the flexibility and adaptability of the continuum manipulator to navigate complex spaces and conform to the shape of the cracks for precise repair. Furthermore, by integrating the continuum arm with an unmanned aerial vehicle (UAV), the system can detect and repair structural damage for building safety and cost-effectiveness. The detection and repair of structural damages were automatized by artificial intelligence. A convolutional neural network is trained to represent the structural feature of the crack with a centerline. Furthermore, a multi-layer perceptron neural network (MLPNN) estimates the length of the bending tubes for guiding the continuous deposit of the putty material to fill the microscopic crack.
Ma et al. studied the dynamics and control of maintaining a squirrel’s head facing the landing spot, while its other body segments tumble in the air. The work developed a simplified 2D multibody dynamics model with body segment collision constraints of a squirrel and further applied two very different control methods to reproduce the observed squirrel behavior. The first control method is classical: it plans a reference motion trajectory, represents the squirrel motion behavior, and applies a PD feedback controller to track the planned reference trajectory. The second control method utilized reinforcement learning (RL) techniques (Kaelbling et al., 1996): it trains a deep neuron-network-based control policy based on the observations. Comparatively, the RL method performs better in terms of closer to expected behavior and robustness against sensor errors, however, shows more variant joint motions with respect to noisy input data near the landing time. Meanwhile, the RL method do not need to plan a reference trajectory, and thus the method would suit more to the natural environment and lead to more natural outcomes.
The works covered in the Research Topic provide valuable insights and resources for researchers and engineers working on redundant robots, help them to deeply understand the challenges of redundant robot control, select proper modeling methods, and improve applications in surgery and construction.
YL: Writing–original draft, Writing–review and editing. IV: Writing–original draft, Writing–review and editing. SS: Writing–original draft, Writing–review and editing. EF: Writing–original draft, Writing–review and editing.
The author(s) declare that no financial support was received for the research, authorship, and/or publication of this article.
The authors declare that the research was conducted in the absence of any commercial or financial relationships that could be construed as a potential conflict of interest.
The author(s) declared that they were an editorial board member of Frontiers, at the time of submission. This had no impact on the peer review process and the final decision.
All claims expressed in this article are solely those of the authors and do not necessarily represent those of their affiliated organizations, or those of the publisher, the editors and the reviewers. Any product that may be evaluated in this article, or claim that may be made by its manufacturer, is not guaranteed or endorsed by the publisher.
Anderson, P. L., Hendrick, R. J., Rox, M. F., and Webster III, R. J. (2024). Exceeding traditional curvature limits of concentric tube robots through redundancy resolution. Int. J. Robotics Res. 43, 53–68. doi:10.1177/02783649231202548
Jin, L., Li, S., Luo, X., Li, Y., and Qin, B. (2018). Neural dynamics for cooperative control of redundant robot manipulators. IEEE Trans. Industrial Inf. 14, 3812–3821. doi:10.1109/tii.2018.2789438
Kaelbling, L. P., Littman, M. L., and Moore, A. W. (1996). Reinforcement learning: a survey. J. Artif. Intell. Res. 4, 237–285. doi:10.1613/jair.301
Li, Y. (2023). Deep causal learning for robotic intelligence. Front. Neurorobotics 17, 1128591. doi:10.3389/fnbot.2023.1128591
Li, Y., Hannaford, B., and Rosen, J. (2019). The raven open surgical robotic platforms: a review and prospect. Acta Polytech. Hung. 16, 9–27.
Rosen, J., Sekhar, L. N., Glozman, D., Miyasaka, M., Dosher, J., Dellon, B., et al. (2017). “Roboscope: a flexible and bendable surgical robot for single portal minimally invasive surgery,” in 2017 IEEE International Conference on Robotics and Automation (ICRA) (IEEE), Singapore, Singapore, May 29 - June 3, 2017, 2364–2370.
Spong, M. W., Hutchinson, S., and Vidyasagar, M. (2020). Robot modeling and control. New Jersey, United States: John Wiley & Sons.
Till, J., Aloi, V., and Rucker, C. (2019). Real-time dynamics of soft and continuum robots based on cosserat rod models. Int. J. Robotics Res. 38, 723–746. doi:10.1177/0278364919842269
Wang, X., Li, Y., and Kwok, K.-W. (2021). A survey for machine learning-based control of continuum robots. Front. Robotics AI 8, 730330. doi:10.3389/frobt.2021.730330
Keywords: redundant robot, modeling, design, control, robotics
Citation: Lee Y, Virgala I, Sadati SMH and Falotico E (2024) Editorial: Design, modeling and control of kinematically redundant robots. Front. Robot. AI 11:1399217. doi: 10.3389/frobt.2024.1399217
Received: 11 March 2024; Accepted: 25 March 2024;
Published: 08 April 2024.
Edited and reviewed by:
Kostas J. Kyriakopoulos, National Technical University of Athens, GreeceCopyright © 2024 Lee, Virgala, Sadati and Falotico. This is an open-access article distributed under the terms of the Creative Commons Attribution License (CC BY). The use, distribution or reproduction in other forums is permitted, provided the original author(s) and the copyright owner(s) are credited and that the original publication in this journal is cited, in accordance with accepted academic practice. No use, distribution or reproduction is permitted which does not comply with these terms.
*Correspondence: Yangming Lee, eWFuZ21pbmcubGVlQHJpdC5lZHU=
Disclaimer: All claims expressed in this article are solely those of the authors and do not necessarily represent those of their affiliated organizations, or those of the publisher, the editors and the reviewers. Any product that may be evaluated in this article or claim that may be made by its manufacturer is not guaranteed or endorsed by the publisher.
Research integrity at Frontiers
Learn more about the work of our research integrity team to safeguard the quality of each article we publish.