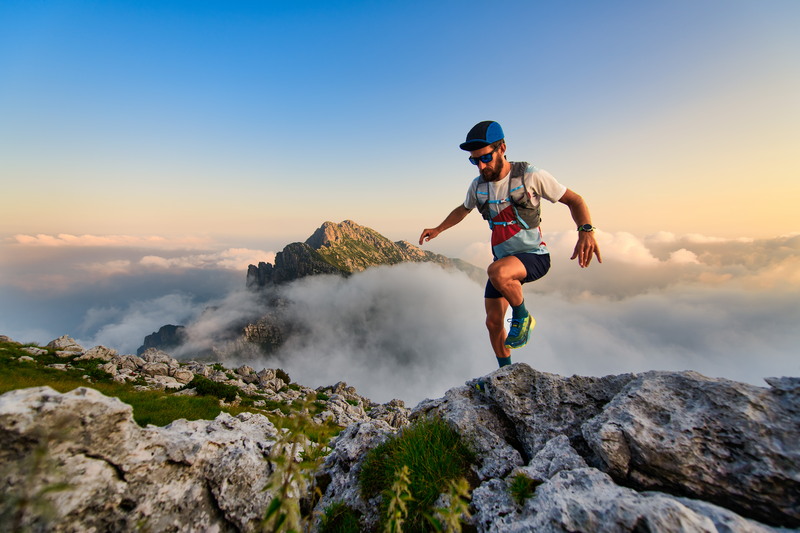
95% of researchers rate our articles as excellent or good
Learn more about the work of our research integrity team to safeguard the quality of each article we publish.
Find out more
ORIGINAL RESEARCH article
Front. Phys. , 04 May 2022
Sec. Interdisciplinary Physics
Volume 10 - 2022 | https://doi.org/10.3389/fphy.2022.887036
This article is part of the Research Topic Multiphase Flow Behavior in the Deep-Stratum and Deep-Water Wellbores View all 13 articles
The block deep condensate gas reservoir in the basin in the southeast of the South China Sea is a bottom water reservoir and is producing in the late effusion, which faces problems such as scaling, condensate oil–water two-phase flow, and low temperature at the subsea wellhead. The mud line for this kind of gas-well has characteristics including high condensate content in low temperature, high downhole temperature, and injection with a foam discharge agent and scale inhibitor. In this article, the influence of low temperature and scale inhibitor is considered for the first time, and a dynamic liquid-carrying experiment for the optimization and performance evaluation of foam discharge agents was carried out according to these characteristics. The experimental results show that the optimized foam discharge agent, ZHY-01, has good resistance to high temperature and condensate oil, and the optimal concentration of the foam discharge agent is recommended to be 0.25%. Under this concentration, the liquid-carrying capacity of the foam discharge agent decreases slightly by 10.17% at low temperature. The scale inhibitor MA/AA reduced the liquid-carrying capacity by 11.86%, and the scale inhibitor PESA reduced the liquid-carrying capacity by 10.17%. The research results in this article have certain reference significance for the chemical screening and evaluation of the foam drainage gas production process in deep-water condensate gas wells.
As an economical and effective means of drainage and production, foam drainage and gas recovery is widely used in major oil and gas fields [1–6]. At present, many scholars at home and abroad focus on the research on the foam discharge agent from the aspects of oil resistance and high temperature resistance for the foam drainage of condensate gas wells [7–9]. The high-content condensate-resistant foam discharge agent PQ-Y developed by Junwen Wu [10] improved the gas field production by 56%. Chaochao Qu [11] developed the oil-resistant foam discharge agent COT, which has been applied in 12 gas wells with good results. Guangfeng Liu [12] selected FDA1, a salt-resistant, oil-resistant, and temperature-resistant foam discharge agent suitable for the S75 well area, with an average daily gas production increase of 35.2%. In addition, the high-efficiency foam discharge agent LH developed by Shiqiang Hu [13], the foam discharge agent FHG-1 developed by Qianding Li [14], the foam discharge agent SJF-2 developed by Jifeng Song [15], and the foam discharge agent DC-1 developed by Yang Feng [16] have been proven by experiments to have excellent performance.
The current research status of foam discharge agents shows that many scholars have carried out sufficient experimental research on the foam discharge agent from the aspects of high salinity resistance, high temperature resistance, and oil resistance through the Rosssmile foam instrument, including foaming performance, foam stability, and liquid carrying rate of the foam discharge agent. However, the research on the influencing factors of the liquid carrying rate is not systematic, and the in-depth and optimal evaluation of the currently developed foam discharge agent and the common foam discharge agent on the market does not consider the influence of low temperature under deep-water conditions, and whether its performance is affected when it is co injected with other chemical inhibitors such as scale inhibitors in combination with the actual working conditions of the site.
A deep-water condensate gas reservoir in the Qiongdongnan Basin block in the South China Sea is an edge-bottom water gas reservoir. As the gas field enters the middle and late stages of development, the gas production decreases, and the fluid loading may often occur in the wellbore, affecting normal production. The highest formation temperature of the gas reservoir in this block is 138.7°C, the production wells are subsea wellhead production units [17, 18], the condensate oil content is 10%–50%, and has the characteristics of high temperature and high condensate oil. In addition, the temperature at the mud line of the production well in this block is 4°C. In the production process, due to the risk of scaling in the wellbore, the scale inhibitor is injected through a specific pipeline, and the foam discharge agent needs to be injected through the same pipeline. The low temperature environment at the mud line and the influence of the scale inhibitor on the foam discharge agent need to be fully considered. Therefore, in this study, four kinds of foam discharge agents with certain oil resistance and high temperature resistance were selected. Considering the influence of low temperature and scale inhibitors for the first time, a dynamic liquid-carrying experiment for the optimization and performance evaluation of foam discharge agents was carried out according to these characteristics. The research in this article expands the range of performance evaluation criteria for the foam discharge agents and provides a new perspective for the optimization of foam discharge agents.
Foam drainage gas recovery is a chemical drainage gas recovery method, which manifests as gas–liquid two-phase flow in the production process of gas wells. There are many studies on the gas–liquid two-phase flow [19–21]. The main principle is to inject a certain type of surfactant-based chemical into the bottom of the well that will produce foam when encountering water. When the foam discharge agent encounters water, it generates a large amount of low-density water-containing foam, and under the agitation of natural gas flow, the bottom-hole liquid is converted into a foamy fluid. On the one hand, the formation of foam reduces the density of the flowing medium and reduces the surface tension of water, thereby reducing the required minimum airflow velocity. On the other hand, the relative density of the foam mixed fluid decreases, the friction loss and gravity gradient in the wellbore are reduced, the pressure of the liquid column formed by the accumulated liquid is dispersed, the bottom-hole back pressure is reduced, the production pressure difference of the gas well increases, and the natural gas flow rate in the wellbore increases to achieve the purpose of drainage and gas extraction [22–24]. The performance of the foam drainage agent and quality of the foam directly determine the success of the entire foam drainage construction [25–27].
Foam discharge agents are mainly surfactants with special molecular structures, and their molecules contain hydrophilic and lipophilic groups, which are amphiphilic. Its drainage function is mainly achieved through the following effects [28].
1) Foaming effect: The foam discharge agent is a kind of surfactant, and only a small amount can make the vertical flow state of gas–water two-phase in oil pipe change evidently. The gas–water two-phase medium is highly foamed during the flow, and the density drops almost 10 times. If the gas-lift formation water previously required at least 5 m/s gas flow velocity, then only 0.5 m/s gas flow velocity is required to take the bottom-hole fluid out of the wellhead in the form of foam.
2) Dispersion effect: In the water-producing gas wells, large and small droplets are dispersed in the airflow, and the degree of agitation and impact of the airflow on the liquid phase determines the dispersing ability. The higher the degree of agitation, the smaller the droplets, and the easier it is to be carried to the wellhead by the airflow. According to the definition of surface tension, when the temperature, pressure, and composition are constant, if the surface area of the system is to increase, work must be carried out on the system; however, the dispersion effect of the airflow on the liquid phase is a process of overcoming surface tension to carry out work. The smaller the dispersion, the larger the specific surface, and the more work carried out. The foam discharge agent is an active agent that can greatly reduce the surface tension of formation water. After the formation water is added with the foam discharge agent and because the surface tension of the liquid phase (formation water) is greatly reduced, if the same dispersion degree is to be achieved, the work carried out will be greatly reduced when the surface tension is greatly reduced.
1) Laboratory reagents
Formation water sample, petroleum ether (instead of condensate), and foam discharge agents AES, BS12, ZHY-01, and ZHY-06.
2) Experimental instruments
Dynamic liquid carrying tester (self-made in the laboratory), constant temperature treatment box, air compressor, float flowmeter, magnetic stirrer, electronic balance, stopwatch, measuring cylinder, and conventional glass instruments. A part of the experimental equipment diagram is shown in Figure 1.
3) Experimental method
FIGURE 1. Experimental drugs and related instruments. (A) Dynamic liquid-carrying string. (B) Air compressor. (C) Magnetic stirrer. (D) Foam discharge agent.
Based on the industry standards “SY/T6465-2000 Evaluation Method of Foaming Agent for Drainage and Gas Extraction” [29] and “SY/T5761-1995 Foaming Agent for Drainage and Gas Recovery CT5-2" [30], a self-made wellbore dynamic liquid carrying measurement device is used.
Combined with the production plan of the target block and formation water data, a formation water solution with a certain degree of salinity is prepared, taking into account the influence of condensate oil (adding petroleum ether) and formation high temperature (transferring the foam discharge agent into a constant temperature box for high-temperature treatment) and the low temperature at the mud line influence (adding the foam discharge agent into the refrigerator for low-temperature treatment). Liquid samples of different concentrations are prepared, and the foam dynamic liquid carrying measurement method is used to calculate the liquid-carrying gas–liquid ratio and liquid-carrying rate. The specific steps are as follows:
a. 1,000 ml of distilled water is measured with a measuring cylinder, transferred into the batching bucket, calibrated the volume scale of 1,000 ml, and then added the solute 27.8 g NaCl in turn while stirring. A certain mass of foaming agent is weighed and added, and a magnetic stirrer is used to make it fully mixed. A glass rod is used to lead it into the liquid-carrying column, and a certain amount of petroleum ether is added when considering the influence of the condensate oil.
b. Using an air compressor, the reading of the gas flowmeter is adjusted so that the flowmeter value is constant at 4 L/min, and the time is adjusted with a stopwatch.
c. The time period when the foam collection device begins to generate foam is 15 min. After 15 min, the collected foam and liquid are defoamed and the volume is read. Ventilation is continuously provided, and the air compressor is turned off at 1 h. The final collected foam and the liquid volume after the liquid is defoamed are read.
d. The abovementioned steps are repeated two–four times to calculate the average value of the three experimental data, and this average value is the final result.
e. All the instruments are turned off, the experiment is ended, and the instruments are cleaned. The liquid-carrying rate (liquid-carrying rate = liquid carried out/total volume of sample liquid × 100%) is calculated, which is the liquid-carrying capacity of the experimental sample.
According to the results of previous studies on foam discharge agents, the concentration range of the foam discharge agents is generally selected between 0.1–1% [31, 32]. In this article, under the conditions of 0.25 and 0.5% of foam discharge agent concentration, four kinds of foam discharge agents, AES, BS12, ZHY-01, and ZHY-06, were used to evaluate the liquid-carrying performance. The dynamic process of foam drainage and gas production is shown in Figure 2, and the experimental results are shown in Table 1 and Table 2.
The experimental results show that the liquid-carrying capacity of the four foam-discharging agents in 15 min is 710, 550, 600, and 500 ml, respectively. Under this condition, the liquid-carrying performance is the worst, and AES and ZHY-01 are initially recommended as the target block.
Because the formation temperature of the production well in the target block is as high as 138.7°C, the foam discharge agent is in a high-temperature condition when it is injected into the bottom of the well, and the high temperature may affect the liquid-carrying performance of the foam discharge agent to a certain extent. AES and ZHY-01, which have better performance, were subjected to comparative experiments after high-temperature aging. After the aging treatment (138.7°C) for 24 h of the two kinds of foam discharge agents in a constant temperature box, a dynamic liquid-carrying experiment was carried out. The experimental results are shown in Tables 3, 4.
TABLE 3. Comparison of liquid-carrying capacity of ZHY-01 aged at room temperature and high temperature at 0.5% concentration.
TABLE 4. Comparison of liquid-carrying capacity of AES at room temperature and high temperature at 0.5% concentration.
The experimental results show that at 0.5% concentration, the liquid-carrying capacity of AES decreases after aging, and the liquid-carrying gas–liquid ratio decreases by 12.68% at 15 min. It can be seen that AES is greatly affected by high temperature, but it still has better performance after aging. The liquid-carrying ability of the foam discharge agent ZHY-01 changed little after aging, indicating that the foam discharge agent ZHY-01 was less affected by temperature and was more resistant to high temperature than the foam discharge agent AES.
The injection concentration of the foam discharge agent is an important parameter in the foam discharge process. When the concentration is too low, the amount of foam is insufficient and the drainage effect is poor. When the injection concentration is too high, it is not conducive to reduce the economic cost of foam discharge, and it is not easy to defoam, so the injection concentration of the foam discharge agent should be kept appropriate. For the two selected foam unloading agents ZHY-01 and AES, the dynamic liquid-carrying experiments were carried out under the conditions of 0.1%, 0.15%, 0.2%, 0.25%, 0.3%, 0.35%, 0.4%, 0.45%, and 0.5% of the foam discharge agent. It should be noted that because the foam discharge agent AES is greatly affected by high temperature and mainly plays a role in mixing with the fluid at the bottom of the well, in order to better fit the actual production, the foam discharge agent AES after high-temperature aging is used for different concentrations. However, ZHY-01 was little affected by high temperature, so the experiment was carried out at room temperature.
Through the experiments, it was found that when the concentration of the foam discharge agent was as low as 0.1% and 0.15%, the foaming ability in the later period of liquid-carrying became weak, the amount of foam produced was reduced, and the liquid in the wellbore could not be completely removed, indicating that the liquid-carrying ability in the later period of liquid-carrying was insufficient. When the concentration of the foam discharge agent reaches 0.25% or more, it can be found that the liquid-carrying capacity is still sufficient in the later stage of liquid-carrying, and the liquid in the wellbore is basically carried up. The final liquid-carrying process is shown in Figure 3, and the results of the liquid-carrying experiments of the foam discharge agent ZHY-01 and AES under different concentrations are shown in Figure 4, Figure 5, Table 5 and Table 6.
FIGURE 3. Schematic diagram of the AES liquid carrying process at (A) 0.1% concentration. (B) 0.25% concentration. (C) 0.5% concentration.
It can be inferred from the liquid-carrying results of the two foam discharge agents at different concentrations that when the concentration of the foam discharge agent is 0.25%, the liquid-carrying rate does not increase significantly. Considering that the foam discharge agent AES is a light yellow paste, the viscosity is much higher than that of the foam discharge agent ZHY-01, and the dilution process and injection process are limited. Therefore, considering the overall consideration, it is recommended to use the foam discharge agent ZHY-01 as the target block foam discharge agent, with a concentration of 0.25%.
Considering the coproduction of production well water and condensate oil in the target block, condensate oil, as a natural defoamer, has a weakening effect on the liquid-carrying ability of the foam discharge agent. The condensate content of the production wells in the target block is between 10% and 50%. Therefore, the volume proportion of the condensate is selected as 10%, 20%, 30%, 40%, and 50%. When the optimal concentration of the foam discharge agent was 0.25%, the oil resistance and liquid-carrying evaluation experiment of the selected foam discharge agent ZHY-01 was carried out. Figure 6 shows the dynamic bubble discharge and liquid-carrying process at the condensate content of 10%, 20%, 30%, 40%, and 50%, and the experimental results are shown in Table 7.
FIGURE 6. Dynamic bubble drainage and liquid-carrying process under the condensate content of 10%, 20%, 30%, 40%, and 50%.
The results of the liquid-carrying evaluation experiment show that ZHY-01 has good oil resistance and sufficient liquid-carrying capacity under the condition of 50% oil content. As shown in Figure 6, from left to right, the condensate content increases. When the condensate content is 10%, 20%, and 30%, it can be seen that the generated foam is uniform and fine, and the foaming ability is relatively good. When the oil separation content is 40% and 50%, it can be seen that the foam becomes larger and sparser with the naked eye, and the foaming ability decreases.
The development well in the target block is a production operation in a deep-water environment, and the ambient temperature at the mud line is relatively low. Considering that high temperature will affect the relevant properties of some foam discharge agents, the foam discharge agent may also be affected by the low ambient temperature during the injection or flowback process. Therefore, in addition to the conventional performance evaluation experiments of the foam discharge agent at high temperature, it is still necessary to analyze the performance of the foam discharge agent at low temperature. After placing the foam discharge agent ZHY-01 in a refrigerator (0°C) for 24 h, at its optimal concentration of 0.25%, the liquid-carrying experiment was carried out to evaluate the low-temperature performance of the foam discharge agent. The experimental results are shown in Table 8. The experimental results show that low temperature slightly reduces the liquid-carrying capacity of the foam discharge agent, and the liquid-carrying rate decreases by 10.17%, but the liquid-carrying capacity meets the demand.
Considering that there is a certain scaling risk in the production wells in the study block in the middle and later stages of production, the physical antiscaling method is limited by the structure of the wellbore and the difficulty in the operation of the technological antiscaling method, combined with the developmental characteristics of deep-water gas wells; it is recommended to adopt the chemical antiscaling method with low cost, good effect, and wide application range to prevent and control wellbore fouling and flow obstacles, guaranteeing the normal production of deep-water gas wells. The predicted scaling risk in the study block is recommended to use antiscalants to inject the pipeline for chemical scale prevention, and the risk of liquid loading in the case well is formulated. In the case of long-term foam drainage and gas production plan, the foam drainage agent can be injected into the bottom hole through the scale inhibitor pipeline. When the scale inhibitor and the foam discharge agent are mixed and injected, it is necessary to fully consider whether the scale inhibitor has an influence on the performance of the foam discharge agent. Therefore, it is necessary to carry out the compound experiment of scale inhibitors and foam discharge agents. For the concentration of the 0.25% foam discharge agent ZHY-01, the compatibility test was carried out with two excellent scale inhibitors, MA/AA and PESA (60 mg/L), selected from the research block. The results are shown in Figure 7. The compatibility test results show that ZHY-01 has good compatibility with the scale inhibitor PESA and scale inhibitor MA/AA. After compounding with PESA, the solution becomes colorless and transparent. After compounding with MA/AA, the solution becomes colorless and transparent. The solution turned slightly white, and the whole solution was transparent, and no obvious precipitate was formed. On this basis, the liquid-carrying experiment, after compounding, was carried out, and the experimental results are shown in Table 9.
TABLE 9. Evaluation results of the liquid-carrying performance of ZHY-01 combined with the scale inhibitors MA/AA and PESA.
The test results show that both the antiscalants reduce the liquid-carrying performance of the foam discharge agent. The addition of the scale inhibitor MA/AA reduces the liquid-carrying rate by 11.86%, and the scale inhibitor PESA reduces the liquid-carrying rate by 10.17%. In comparison, the scale inhibitor MA/AA has a great influence on the liquid-carrying performance of the foam discharge agent ZHY-01.
1) Considering the characteristics of high formation temperature and high yield of the condensate oil in the study block, the high-temperature performance evaluation, optimal concentration screening, and anti-condensate oil performance comparison of the four existing foam discharge agents with good performance were carried out. In the end, ZHY-01 was selected as the foam discharge agent for the gas well at a risk of liquid loading in this block, and the optimal concentration was 0.25%.
2) In addition to the conventional performance evaluation of the foam discharge agent, such as high temperature resistance and anticondensation oil, this study takes into account the low production temperature of the subsea wellhead of the production well; considering the low production temperature of the subsea wellhead of the production well, a comparative experiment was carried out for the first time on the performance evaluation of the anti-low temperature of the foam discharge agent. The experimental results show that low temperature makes the liquid-carrying ability of the foam discharge agent ZHY-01 decrease slightly, and the decrease rate is 10.17%.
3) Considering the characteristics of coinjection of the foam discharge agent and scale inhibitor in the later stage of production, the actual comparative experiment of the dynamic liquid-carrying evaluation after the combination of the foam discharge agent with the scale inhibitor MA/AA and scale inhibitor PESA was carried out for the first time. The experimental results show that both the antiscalants reduce the liquid-carrying performance of the foam discharge agent. The addition of the scale inhibitor MA/AA reduces the liquid-carrying capacity by 11.86%, and the scale inhibitor PESA reduces the liquid-carrying capacity by 10.17%.
4) The research in this article expands the range of performance evaluation criteria of the foam discharge agents, provides a new viewpoint for the optimal study of the foam discharge agents, and provides effective theoretical support for the foam-draining liquid–gas recovery process of production wells in the deep-water condensate gas reservoirs.
The original contributions presented in the study are included in the article/Supplementary Material, further inquiries can be directed to the corresponding author.
LG: conceptualization, methodology, supervision, writing-original draft, and writing—review and editing. HC: data curation, resources, investigation, experimental data analysis, and writing—review and editing. YL: investigation, methodology, experimental operation, experimental data sorting, and writing—review and editing. XS: investigation, methodology, experimental operation, and writing—review and editing.
Author LG was employed by Sinopec Shengli Petroleum Engineering Company Limited Tarim branch. Author HC was employed by Drilling Technology Research Institute of Sinopec Shengli Oilfield Service Corporation.
The remaining authors declare that the research was conducted in the absence of any commercial or financial relationships that could be construed as a potential conflict of interest.
All claims expressed in this article are solely those of the authors and do not necessarily represent those of their affiliated organizations, or those of the publisher, the editors, and the reviewers. Any product that may be evaluated in this article, or claim that may be made by its manufacturer, is not guaranteed or endorsed by the publisher.
1. Jia H, Zhu J, Cao G, Lu Y, Lu B, Zhu H. A Model Ranking Approach for Liquid Loading Onset predictions[C] (2021). SPE209578.
2. Jelinek W, Schramm LL. Improved Production from Mature Gas wells by Introducing Surfactants intowells[J]. Doha: International Petroleum Technology conference (2005).
3. Price BP, Gothard B. Foam Assisted Lift-Importance of Selection and application[C] (2007). SPE106465.
4. Campbell S, Ramachandran S, Bartrip K. Corrosion Inhibition/foamer Combination Treatment to Enhance Gas production[C] (2001). SPE67325.
5. Liu Q, Jiang J, Shi Q, Feng M Analysis of the Application Effect of Liquid Drainage and Gas Recovery Methods at home and Abroad[J]. Nat Gas Exploration Develop (2006) 2006(03):51-4–65+73.
6. Yu Y. Research on Gas Recovery Technology of Gas Well Drainage in Offshore Oil and Gas fields[D]. Daqing, China: Daqing Petroleum Institute (2009).
7. Uddin MFM, Tayyab I, Koondhar NH, Ahmed QI, Soomro AA. Production Optimization of Foam Assisted Lift (FAL) wells and Evaluation of Good and Bad Practices to Ensure Maximum production[C] (2015). SPE181121.
8. Nimwegen DV, Portela LM, Henkes RAWM. The Effect of Surfactants on Vertical Air/water Flow for Prevention of Liquid Loading[C] (2015). SPE164095.
9. Solesa M, Sevic S. Production Optimization Challenges of Gas wells with Liquid Loading Problem Using Foam Discharge Agents (Russian)[J]. Der Anaesthesist (2006) 52(6):516–21.
10. Wu J, Zhang R, Wang H, Cen X, Jia W, Xiao Z, et al. Development and Field Application of High-Content Condensate-Resistant Foam-Removing Agent[J]. Oilfield Chem (2019) 36(03):508–12+534.
11. Qu C, Liu Z, Yin H, Lu G, Li Z, Feng Y, et al. A New Type of Anti-condensation Oil Bubble Discharge Agent for Drainage and Gas Production[J]. Chin J Pet (2020) 41(07):865–74.
12. Liu G, Gao Y, Zhang J, Chen S, Li X, et al. Development of Salt-Resistant, Oil-Resistant and Temperature-Resistant Foam-Removing Agent in S75 Well Area of Sulige Gas Field[J]. Spec oil gas reservoirs (2015) 22(02):133-6–157-8.
13. Hu S, Liu J, Li Y, Ye C, Du X, et al. Study on the Foam Performance of a New Type of High-Efficiency Foaming Agent LH[J]. Nat Gas Industry (2007) 2007(01):102–4+159.
14. Li Q, Song J, Xue D, Li H, et al. Research on an Oil-Resistant and Methanol-Resistant Gas Well Foam Removal Agent [J]. Oilfield Chem (2013) 30(01):29–32.
15. Song J. Research on the Selection of Foaming Agents and Optimization of Filling System in Block Su 20 of Sulige Gas Field [D]. Xi'an, China: Xi'an Petroleum University (2013).
16. Feng Y, Li Q, Guan C, Dong J, Guo L, et al. Performance Evaluation of Amine Oxide Type Foaming Agent for Gas wells in Northern Shaanxi [J]. Chem Technol Develop (2020) 49(10):12–4.
17. Wang Z, Zhang J, Meng W, Sun B, Sun J, Wang J, et al. Formation, Deposition Characteristics and Control Methods of Gas Hydrate in Deep Water Gas Wells[J]. Chin J Pet (2021) 42(06):776–90.
18. Fu W, Wang Z, Chen L, Sun B. Experimental Investigation of Methane Hydrate Formation in the Carboxmethylcellulose (CMC) Aqueous Solution. SPE J (2020) 25:1042–56. doi:10.2118/199367-pa
19. Fu W, Yu J, Xiao Y, Wang C, Huang B, Sun B. A Pressure Drop Prediction Model for Hydrate Slurry Based on Energy Dissipation under Turbulent Flow Condition. Fuel (2022) 311:122188. doi:10.1016/j.fuel.2021.122188
20. Fu W, Yu J, Xu Y, Wang C, Huang B, Sun B. A Pressure Drop Prediction Model for Hydrate Slurry Based on Energy Dissipation under Laminar Flow condition[C] (2022). SPE209586.
21. Fu W, Wang Z, Zhang J, Cao Y, Sun B. Investigation of Rheological Properties of Methane Hydrate Slurry with Carboxmethylcellulose. J Pet Sci Eng (2020) 184:106504. doi:10.1016/j.petrol.2019.106504
22. Zhu J, Zhu H, Wang Z, Zhang J, Cuamatzi-Melendez R, Farfan JAM, et al. Surfactant Effect on Air/water Flow in a Multistage Electrical Submersible Pump (ESP). Exp Therm Fluid Sci (2018) 98:95–111. doi:10.1016/j.expthermflusci.2018.05.013
23. Zhao Q, Zhu J, Cao G, Zhu H, Zhang H-Q. Transient Modeling of Plunger Lift for Gas Well Deliquification. SPE J (2021) 26(05):2928–47. doi:10.2118/205386-pa
24. Wang X. Optimization of Foam Drainage Technology for Low-Pressure Gas wells in Daniudi Gas field[D]. Xi'an, China: Xi'an Shiyou University (2014).
25. Kanda M, Schechter RS. Mechanism of Foam Formation in Porous Media[J]. AmericanInst Mining Metallurgical Pet Eng Dallas (1976).
26. Sun W, Littleton HE, Bates CE. Formation Mechanism of Gas Cavity Defects in Lost Foam Iron Castings. Int J Cast Met Res (2003) 16(6):549–53. doi:10.1080/13640461.2003.11819634
27. Xiao C. Evaluation of Foam Discharge Agent for Foam Complex Flooding[J]. Adv Fine Petrochemicals (2008).
28. Qin M. Research and Application of Foam Drainage Gas Recovery technology[D]. Daqing, China: Northeast Petroleum University (2011).
31. Zhang S. Performance Evaluation Method of Foaming Agent and its Application in Sulige Gas field[D]. Xi'an, China: Xi'an Petroleum University (2018).
Keywords: deepwater condensate gas well, foam drainage gas recovery, high temperature resistant, low temperature resistant, oil resistant, foam discharge agent and scale inhibitor
Citation: Ge L, Cui H, Li Y and Sui X (2022) Optimization and Performance Evaluation of Foam Discharge Agent for Deep Aquatic Condensate Gas Well. Front. Phys. 10:887036. doi: 10.3389/fphy.2022.887036
Received: 01 March 2022; Accepted: 04 April 2022;
Published: 04 May 2022.
Edited by:
Weiqi Fu, China University of Mining and Technology, ChinaReviewed by:
Haiwen Zhu, University of Tulsa, United StatesCopyright © 2022 Ge, Cui, Li and Sui. This is an open-access article distributed under the terms of the Creative Commons Attribution License (CC BY). The use, distribution or reproduction in other forums is permitted, provided the original author(s) and the copyright owner(s) are credited and that the original publication in this journal is cited, in accordance with accepted academic practice. No use, distribution or reproduction is permitted which does not comply with these terms.
*Correspondence: Yingchao Li, MzgwMDEzMTYyQHFxLmNvbQ==
Disclaimer: All claims expressed in this article are solely those of the authors and do not necessarily represent those of their affiliated organizations, or those of the publisher, the editors and the reviewers. Any product that may be evaluated in this article or claim that may be made by its manufacturer is not guaranteed or endorsed by the publisher.
Research integrity at Frontiers
Learn more about the work of our research integrity team to safeguard the quality of each article we publish.