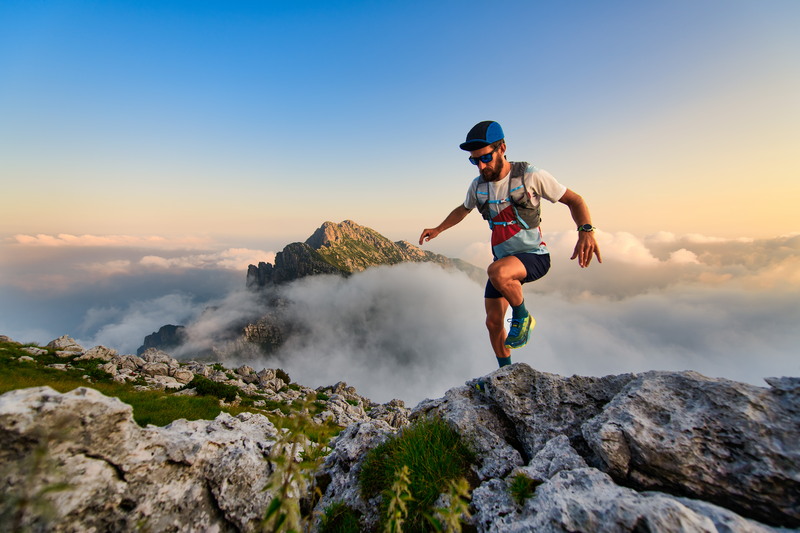
95% of researchers rate our articles as excellent or good
Learn more about the work of our research integrity team to safeguard the quality of each article we publish.
Find out more
ORIGINAL RESEARCH article
Front. Phys. , 14 March 2022
Sec. Optics and Photonics
Volume 10 - 2022 | https://doi.org/10.3389/fphy.2022.872992
This article is part of the Research Topic Plasmonic Metamaterials and Electromagnetic Devices View all 20 articles
This article proposes a dual-band slot IFA antenna using a combined technique of liquid metal (LM) filling and polydimethylsiloxane substrate. The antenna working at 2.4 and 5.8 GHz consists of three liquid metal layers—radiation patch, short circuit stub, and ground plane and can be bent to different radiuses for flexible, conformal, and wearable applications. The vacuum filling method enables realization of a monolithic-integrated substrate. The applicability of this antenna for a wearable wristband is validated through simulation.
The demand for compact, multiband, and flexible microwave components and antennas is increasing due to the prosperity of the Internet of Things (IoT) [1, 2]. Typical IoT systems are found in a lot of emerging and conventional scenarios, such as smart industry or wireless body area network (WBAN), where various sensors are required for industrial information collecting or human healthcare monitoring, among which conformal or flexible antennas are critical to transit the collected data. Such antennas for wearable applications (clothes, shoes, bracelets, and glasses) utilize flexible substrate, including paper, textiles or polymer composites, and conductive materials, such as electro-textiles and nanowire, instead of conventional rigid substrates or metal in cases they can be bent or twisted when worn on the human body [3–6]. Furthermore, in order to maximize the connectivity, the antenna for body communications usually operates at multiple bands for on- and off-body communications [7–9].
Eutectic liquid metal (LM) with low toxicity and high conductivity at room temperature is potential for creating antennas with flexibility and high conformity [10]. Particularly, the LM fluidity is critical for maintaining conductive continuity during deformation. When capsulated within soft materials, such as polydimethylsiloxane (PDMS), the LM-enabling technology enables creation of flexible antennas. The bendable microstrip patch and dipole antennas are constructed by injecting LM into microfluidic channels molded by PDMS [11, 12]. A flexible antenna based on liquid metal and additive printing technologies is given in [13], in which the microfluidic branch is printed in flexible NinjaFlex plastic. These antennas can be bent or curved to different radiuses, and at the same time the antenna radiation properties maintain stability during the deformation. Most of these LM channels or cavities are constructed along one-dimensional axis or on two-dimensional surfaces with only two layers, while the three-dimensional volume has not been fully exploited. Stretchable sensors using 3D-printed LM demonstrate stable conductivity of the liquid metal paste circuit interconnects among [14]. The combined technique of liquid metal filling and PDMS material as a substrate has great potential in flexible antenna applications. Based on the authors’ knowledge, there has not been much investigation into the LM antennas for wearable applications.
This article proposes the design and implementation of a LM dual-band antenna for wrist-worn applications. The antenna, with dimensions of 30 × 12 × 4.5 mm3, operating at two WLAN frequency bands—2.4 and 5.8 GHz, comprises radiating cavities formed by LM filling within a PDMS substrate. In order to fabricate the proposed antenna, a layered-bonding method to fabricate the PDMS wristband structure and a vacuum compression method to inject LM into the microfluidic channels are implemented.
The structure of the LM antenna adopts the structure of inverted-F antenna (IFA) with three parts—the radiation patch of width W1 and length L1 on the top layer, a U-slot of width W2 and length L2 is etched on the radiation patch for generating the band at 5.8 GHz while the IFA resonates at 2.4 GHz, the ground plane of width W3 and length L3 on the bottom layer, and the rectangular short circuit of width SW and height H in between as shown in Figure 1. The distance from the short circuit to the left side of the grounding plane is optimized to be 2 mm for impedance matching. The two resonances can be roughly determined from the following equations (15),
Dimensions of the patch, the slot, and the short circuit are optimized to resonate the antenna at the aforementioned two bands and listed as follows: W1 = 8 mm, L1 = 15.5 mm, W2 = 3 mm, L2 = 7 mm, W3 = 10 mm, L3 = 30 mm, and H = 2.5 mm. The proposed antenna operates at dual-bands—2.4 GHz covering 100 MHz and 5.8 GHz covering 150 MHz with a well-matched reflection coefficient below −10dB. Different to conventional copper cladding on PCB technology, LM-based devices use post-filled LM to construct a conductive path. Based on our experimental experience, the whole cavity volume can be filled with LM through visual checking. But, still minor possibility of unfilled cavity corners might exit. Therefore, it is reasonable to briefly evaluate the sensitivity of the antenna resonances to the change of the aforementioned dimensions. Parametric simulations show that the resonance shifts less than 5% when L1 and L2 vary between 0.5 and 0.25 mm shown in Figure 2, respectively. This ensures that when corners of the microfluidic channels and cavities are occasionally hollow due to partially filled LM, the frequencies still locate within the desired bands and maintain the desired frequencies.
To achieve flexibility and mitigate the user discomfort of the antenna wristband, PDMS (Sylgard 184 kit, Dow Corning) with a dielectric constant of 2.68 and loss tangent of 0.0375 is chosen as the substrate material for its high elasticity and low surface tension. Meanwhile, PDMS is human skin-safe and widely used in various consumer and cosmetic products. PDMS is composed of two solvents—polymer and crosslinker with a mass ratio 10:1. PDMS can be cured by placing it in an oven at 80°C for 2 h and therefore is routinely used for preparing microfluidic channels. A layered bonding process technology is implemented to assemble the different PDMS layers. Due to the liquid nature of LM, channels are reserved within the PDMS substrate for latterly injecting LM into the channel.
The schematic view of the manufacturing process is presented in Figure 3. The fabrication process of the wearable antenna includes mainly molding the PDMS wristband and metalizing the wristband [16]. The three layers of wristband are made, respectively, which are made of PMMA material and processed using a high-precision computerized numerical control (CNC) machine. To ensure that LM is completely wrapped, the heights of the molds are not consistent. The prepared PDMS solution is poured into three molds, respectively, and then put them into a vacuum oven to cure at 80°C for 2 h. Since the PMMA material is easy to demold, the cured PDMS can be peeled out of the mold to obtain three substrate layers. These layers are bonded after cleansed using a plasma cleaning machine. A total of three holes with a diameter of 0.9 mm are drilled in the model, and then LM is pneumatically pushed into the cavity by the vacuum compression method [17]. In order to inject EGaIn into the PDMS wristband model, the wristband model is inverted and placed in the vacuum oven after putting the LM on top of the circular holes 1 and 2. After evacuating the air in the vacuum box and the microfluidic channel, EGaIn will all be pushed into the microfluidic channel once the vacuum box is opened.
The prototype of the wearable antenna is fabricated as shown in Figure 4. The three PDMS layers are molded, respectively, and then bonded together by plasma treatment. Then, LM is pushed into the microfluidic channels through vacuum filling after assembling the three layers. The vacuum-filling method ensures that the least air bubbles are generated during this process so that the three-dimensional conductive path is well established. Superglue is attached between SMA connectors and the PDMS substrate to fix the connection in case the LM leaks and the frequency bands shift. Based on our knowledge, this is the first demonstration of multilayer PDMS-embedded liquid metal antenna for wearable applications. Compared to the liquid metal antenna printed on a planar surface with only two layers, although can be curved to different radiuses, this prototype antenna realizes a three-dimensional-layered LM structure that utilizes the vertical space of the flexible substrate. Although the antenna topology in this article is an inverted-F antenna commonly used for wireless communication, the proposed process technology can be extended to manufacturing of more complicated antenna structures, therefore exploiting the three-dimensional space and maximizing the design degree.
FIGURE 4. Photographs of the fabricated wearable antenna. (A) Flat wristband before and after filling LM and (B) curved wristband filled with LM.
To assess the radiation properties of the proposed flexible antenna, the prototype antenna in Figure 4 is built and measured. The experimental data are compared to the simulation results obtained from a full-wave simulator. The antenna impedance matching behavior over the frequency range of 1–7 GHz is shown in Figure 5. Due to the flexibility of the PDMS substrate and the fluidity of LM, this wearable antenna can be bent to curvatures of different radiuses.
The radiation patterns of the flexible antenna on a flat platform (in the x-y, x-z, and y-z planes) are simulated and measured as shown in Figure 6. The plots show the graphs of the Eφ and Eθ components, and it is seen that the patterns are nearly omnidirectional at several conditions of the two frequencies. The discrepancies between the simulated and measured radiation patterns are more prominent at higher frequencies possibly due to uneven filling of LM within cavities or unstable connection of LM to an SMA connector during rotation of measurements. The measured gain and efficiency of the flexible antenna are 1.55 dBi and 34.6% at 2.4 GHz, 1.66 dBi and 28.74% at 5.8 GHz, respectively. Compared to antenna structures copper plated on commercial substrates (Rogers or FR4 boards), this antenna has a low efficiency mainly due to the lossy PDMS substrates. Customizable PDMS made of different proportions of materials can be implemented to mitigate the negative effects brought by the PDMS substrates [16].
FIGURE 6. Measured and simulated radiation patterns of the wearable antenna for the x-z, y-z, and x-y planes at 2.4 GHz (left) and 5.8 GHz (right). Solid lines indicate the Eφ component and dashed lines for Eθ component. Red lines indicate the simulated patterns and black lines for measured patterns.
Since this flexible antenna can be bent to different radiuses, it could be used as a wearable antenna. Such as when worn on the human wrist, the antenna mainly works in areas close to the human body; the nonuniform human body will mutually affect the antenna performance due to its electrical complexity. Figure 7 shows a human wrist model consisting of skin, muscle, fat, and bone, exhibiting various electromagnetic properties over the bands of interest [18]. Our full-wave analysis indicates that when the wearable antenna is 5 mm away from the surface of the human body, the antenna operates with the same bands within free space. Meanwhile, the human body absorbs and dissipates part of the antenna electromagnetic radiation due to its lossy intrinsic, usually quantified by the specific absorption rate (SAR). SAR is usually limited to a standard of 2 W/kg per 10 g of human tissue [19]. Figure 5 shows the SAR values at the bands of 2.4 and 5.8 GHz. The local SAR peaks are 1.66 W/kg and 7.16 W/kg when the input power is on the scale of mW, which, however, is higher than the regulated SAR standards. For this particular scenario, the ground plane of the antenna is narrower than a typical IFA antenna, and the antenna structure has not been optimized for a reduced SAR. Enlarging the ground plane of the antenna and adapting the antenna topology are methods to reduce the SAR values to the regulated levels in our future research.
FIGURE 7. Average SAR values of the human wrist wearing the LM antenna. (A) Antenna worn on the human wrist, (B) average SAR values of the human wrist at 2.4 GHz, and (C) average SAR values of the human wrist at 5.8 GHz.
This article introduces a dual-band flexible antenna for conformal or wearable applications. The combined technique of using liquid metal as the radiating patch and PDMS as the substrate enables creation of such flexible antenna structures. At the same time, a layered bonding processing technology and vacuum compression technology facilitate the monolithic integration. The radiation properties of the two bands at 2.4 and 5.8 GHz are evaluated. As a demonstration, the LM-embedded layered-PDMS antenna is implemented on a human wrist for validating its applicability. This article concludes that the LM–PDMS combined technique can be extended to more complex scenarios, such as flexible and conformal reconfigurable antenna arrays for sensing and communicating.
The original contributions presented in the study are included in the article/Supplementary Material, further inquiries can be directed to the corresponding author.
MW contributed to the conceptual design and simulation; ZL performed the simulation and wrote the first version of this manuscript; JD contributes to the conceptual design and implementation. All authors contributed to manuscript revision, and read and approved the submitted version.
This work was supported in part by the National Natural Science Foundation of China under Grant No. 61801521 and 61971450, in part by the Natural Science Foundation of Hunan Province under Grant No. 2018JJ2533.
The authors declare that the research was conducted in the absence of any commercial or financial relationships that could be construed as a potential conflict of interest.
All claims expressed in this article are solely those of the authors and do not necessarily represent those of their affiliated organizations, or those of the publisher, the editors, and the reviewers. Any product that may be evaluated in this article, or claim that may be made by its manufacturer, is not guaranteed or endorsed by the publisher.
1. Xu K-D, Luyen H, Behdad N. A Decoupling and Matching Network Design for Single- and Dual-Band Two-Element Antenna Arrays. IEEE Trans Microwave Theor Techn. (2020) 68(9):3986–99. doi:10.1109/tmtt.2020.2989120
2. Xu K-D, Xia S, Jiang Y, Guo Y-J, Liu Y, Wu R, et al. Compact Millimeter-Wave On-Chip Dual-Band Bandpass Filter in 0.15-μm GaAs Technology. IEEE J Electron Devices Soc (2022) 10:152–6. doi:10.1109/jeds.2022.3143999
3. Chen SJ, Kaufmann T, Ranasinghe DC, Fumeaux C. A Modular Textile Antenna Design Using Snap-On Buttons for Wearable Applications. IEEE Trans Antennas Propagat (2016) 64(3):894–903. doi:10.1109/tap.2016.2517673
4. Ullah M, Islam M, Alam T, Ashraf F. Paper-Based Flexible Antenna for Wearable Telemedicine Applications at 2.4 GHz ISM Band. Sensors (2018) 18(12):4214. doi:10.3390/s18124214
5. Kim S, Ren Y-J, Lee H, Rida A, Nikolaou S, Tentzeris MM. Monopole Antenna with Inkjet-Printed EBG Array on Paper Substrate for Wearable Applications. Antennas Wirel Propag Lett (2012) 11:663–6. doi:10.1109/lawp.2012.2203291
6. Kim BS, Shin K-Y, Pyo JB, Lee J, Son JG, Lee S-S, et al. Reversibly Stretchable, Optically Transparent Radio-Frequency Antennas Based on Wavy Ag Nanowire Networks. ACS Appl Mater Inter (2016) 8(4):2582–90. doi:10.1021/acsami.5b10317
7. Sanz-Izquierdo B, Miller JA, Batchelor JC, Sobhy MI. Dual-band Wearable Metallic Button Antennas and Transmission in Body Area Networks. IET Microw Antennas Propag (2010) 4(2):182–90. doi:10.1049/iet-map.2009.0010
8. Zhang XY, Wong H, Mo T, Cao YF. Dual-Band Dual-Mode Button Antenna for On-Body and Off-Body Communications. IEEE Trans Biomed Circuits Syst (2017) 11(4):933–41. doi:10.1109/tbcas.2017.2679048
9. Xu KD, Li D, Liu Y, Liu QH. Printed Quasi-Yagi Antennas Using Double Dipoles and Stub-Loaded Technique for Multi-Band and Broadband Applications. IEEE Access (2018) 6:31695–702. doi:10.1109/access.2018.2838328
10. Khan MR, Eaker CB, Bowden EF, Dickey MD. Giant and Switchable Surface Activity of Liquid Metal via Surface Oxidation. Proc Natl Acad Sci USA (2014) 111(39):14047–51. doi:10.1073/pnas.1412227111
11. Hayes GJ, Ju-Hee So JH, Qusba A, Dickey MD, Lazzi G. Flexible Liquid Metal Alloy (EGaIn) Microstrip Patch Antenna. IEEE Trans Antennas Propagat (2012) 60(5):2151–6. doi:10.1109/tap.2012.2189698
12. Morishita AM, Kitamura CKY, Ohta AT, Shiroma WA. A Liquid-Metal Monopole Array with Tunable Frequency, Gain, and Beam Steering. Antennas Wirel Propag Lett (2013) 12:1388–91. doi:10.1109/lawp.2013.2286544
13. Cosker M, Lizzi L, Ferrero F, Staraj R, Ribero J-M. Realization of 3-D Flexible Antennas Using Liquid Metal and Additive Printing Technologies. Antennas Wirel Propag Lett (2017) 16:971–4. doi:10.1109/lawp.2016.2615568
14. Votzke C, Daalkhaijav U, Menguc Y, Johnston ML. 3D-Printed Liquid Metal Interconnects for Stretchable Electronics. IEEE Sensors J (2019) 19(10):3832–40. doi:10.1109/jsen.2019.2894405
15. Salonen P, Keskilammi M, Kivikoski M. “Dual-band and Wide-Band PIFA with U- and Meanderline-Shaped Slots.” in Proceedings of the IEEE Antennas and Propagation Society International Symposium 2001 Digest Held in conjunction with: USNC/URSI National Radio Science Meeting (Cat No01CH37229); 8-13 July 2001; Boston, MA, USA (2001).
16. Trajkovikj J, Zurcher J-F, Skrivervik AK. PDMS, A Robust Casing for Flexible W-BAN Antennas [EurAAP Corner]. IEEE Antennas Propag Mag (2013) 55(5):287–97. doi:10.1109/map.2013.6735538
17. Bharambe V, Parekh DP, Ladd C, Moussa K, Dickey MD, Adams JJ. Liquid-Metal-Filled 3-D Antenna Array Structure with an Integrated Feeding Network. Antennas Wirel Propag Lett (2018) 17(5):739–42. doi:10.1109/lawp.2018.2813309
18. Jun SY, Elibiary A, Sanz-Izquierdo B, Winchester L, Bird D, McCleland A. 3-D Printing of Conformal Antennas for Diversity Wrist Worn Applications. IEEE Trans Compon., Packag Manufact Technol (2018) 8(12):2227–35. doi:10.1109/tcpmt.2018.2874424
Keywords: liquid metal, flexible antennas, microfluidic channel, PDMS, wearable application
Citation: Wang M, Liu Z and Dong J (2022) Liquid Metal-Embedded Layered-PDMS Antenna for Flexible and Conformal Applications. Front. Phys. 10:872992. doi: 10.3389/fphy.2022.872992
Received: 10 February 2022; Accepted: 21 February 2022;
Published: 14 March 2022.
Edited by:
Zhewang Ma, Saitama University, JapanReviewed by:
Lei Xing, Nanjing University of Aeronautics and Astronautics, ChinaCopyright © 2022 Wang, Liu and Dong. This is an open-access article distributed under the terms of the Creative Commons Attribution License (CC BY). The use, distribution or reproduction in other forums is permitted, provided the original author(s) and the copyright owner(s) are credited and that the original publication in this journal is cited, in accordance with accepted academic practice. No use, distribution or reproduction is permitted which does not comply with these terms.
*Correspondence: Jian Dong, ZG9uZ2ppYW5AY3N1LmVkdS5jbg==
Disclaimer: All claims expressed in this article are solely those of the authors and do not necessarily represent those of their affiliated organizations, or those of the publisher, the editors and the reviewers. Any product that may be evaluated in this article or claim that may be made by its manufacturer is not guaranteed or endorsed by the publisher.
Research integrity at Frontiers
Learn more about the work of our research integrity team to safeguard the quality of each article we publish.