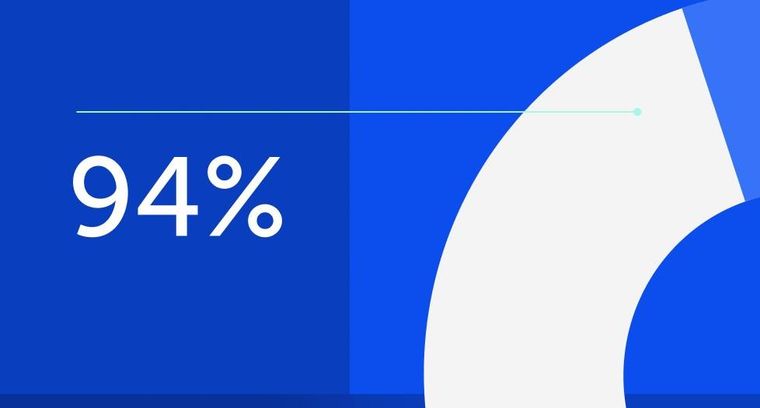
94% of researchers rate our articles as excellent or good
Learn more about the work of our research integrity team to safeguard the quality of each article we publish.
Find out more
PERSPECTIVE article
Front. Nucl. Eng., 22 July 2024
Sec. Nuclear Reactor Design
Volume 3 - 2024 | https://doi.org/10.3389/fnuen.2024.1308045
This article is part of the Research TopicWomen in Nuclear Engineering ResearchView all 15 articles
NASA and the Department of Defense are planning for a mission to Mars in the 2030s–2040s using nuclear thermal propulsion (NTP). NTP uses a nuclear reactor to heat flowing hydrogen and create thrust. A serious concern for crewed and uncrewed missions to Mars is the loss of reactor control. The reactor startup and initial rocket impulse are initiated in cislunar or near-earth orbital regions; therefore, radio communications between ground control and the NTP engine should occur in real time. However, radio communications can take more than 20 min, depending on planet positions, to reach Mars orbiters from ground control. To address this delay, local autonomous controls are implemented onboard the NTP engine to ensure acceptable operation. However, autonomous controls have not been demonstrated or implemented in research or power reactor contexts because of safety and reliability concerns. To enable autonomous controls development, demonstration, and validation, Oak Ridge National Laboratory has created a nonnuclear hardware-in-the-loop test bed. Sensors throughout the test bed relay system status and hardware response to the user control algorithm, including measurements of temperature, flow, pressure of a loop, control drum position, and drum speed. This paper discusses the development of this facility and user accessibility.
NASA and the US Department of Defense (DOD) aim to launch a mission to Mars in the next 2 decades using nuclear thermal propulsion (NTP). NTP uses a variation of chemical rocket engines to create thrust by ejecting burning gases in the opposite direction of the planned trajectory. Chemical rockets use a chemical reaction, creating a phase change that requires a great deal of working mass. However, nuclear rockets provide heat to create a phase change. Nuclear rockets are more appealing than chemical rockets because of their improved efficiency, their reduced size, and the independence of the heat source from the working mass. The specific impulse (Eq. 1) of the rocket engine is defined by
where
NASA characterizes NTP as a “game changing technology for deep space exploration” (Hall, 2018). NASA and the former Atomic Energy Commission began investigating nuclear reactors as a heat source for rocket propulsion through the Nuclear Engine for Rocket Vehicle Application (NERVA) program in 1961 (Hall, 2018). Over 2 decades (i.e., 1965–1973) under the Space Nuclear Propulsion Office, the NERVA program “established a technology base for nuclear rocket engine systems to be utilized in the design and development of propulsion systems for space mission applications” (Robbins, 1991). The reactor development origins came from the United States Air Force Project ROVER (1955–1973), executed at Los Alamos Scientific Laboratory (LASL), and focused on the development of nuclear-powered intercontinental ballistic missiles. Three ROVER reactors (i.e., Kiwi, Phoebus, and Pewee) were built and tested at LASL to characterize highly enriched uranium fuels and the nuclear material performance of graphite, beryllium, and boron. Projects ROVER and NERVA were cancelled in 1973: reactors were only ground tested. However, reactors were tested across 48 ground demonstrations in under 5 years (Finseth, 1991).
SNAP-10A, also known as Systems for Nuclear Auxiliary Power, was the first nuclear-powered satellite. It launched in 1965 and operated for 43 days, after which the reactor stopped functioning because of electrical component failure (Truscello, 1983). This was the first and only demonstration of a US nuclear fission reactor in space. However, many small reactor systems have been deployed in space by the former Soviet Union and China. The design of the SNAP-10 nuclear satellite was much less complex than that of nuclear rockets: the assembly included the reactor, an energy converter used to generate electricity, and a radiator to dissipate excess heat (Corliss, 1966). The overall size of the payload was greatly decreased and did not require a working mass for propulsion.
In February 1983, a resurgence in NTP research resulted in the SP-100 project. A new approach to fuel, the pebble bed concept, promised a specific impulse of 1,000 s. However, NASA deemed the SP-100 design an insufficient technology improvement over NERVA (Truscello, 1983). A summary of program dates, starts, temperatures, flow rates, and specific impulses is provided in Table 1.
Like other DOD and US Department of Energy initiatives, NTP has been a catalyst for the development of nuclear fuels, advanced instrumentation and controls (I&Cs), high-temperature materials, and other technologies. Many terrestrial nuclear concepts, such as microreactors and advanced generation IV reactors, benefit from the innovations in materials and technology. NASA, in partnership with the national laboratory complex and industry partners, restarted the NTP program in 2016 with the goal of achieving a mission to Mars in the 2030s. Figure 1 displays a side-by-side view of the original conceptual NERVA NTP engine design (Figure 1A) and the most recent NTP engine conceptual design illustration created by NASA (Figure 1B). Some discrepancies between the two images are: Figure 1A does not include the hydrogen tank but instead only illustrates the turbo-machinery, piping, reactor, and nozzle. It is difficult to visualize the nozzle on the left side of Figure 1B because this image includes the trans hab and hydrogen tank, but the image points out a key features including the nozzle and reactor core. Both of these images are good for general discussion but limited for in-depth technical discussion. Figure 1B is also a good illustration of the size of engine.
Figure 1. Illustrations of (A) NERVA and (B) the current NTP conceptual design (Borowski et al., 2013; Hall, 2018).
A full ground demonstration, as previously executed in ROVER/NERVA days is the preferred method for comprehensive testing. However, limitations in funding prohibit a full ground demonstration today. Therefore, Oak Ridge National Laboratory (ORNL) is supporting NASA and the NTP community in advancing I&C technology maturation through development of this test bed infrastructure. I&C test beds enable validation and verification of autonomous control algorithm with hardware-in-the-loop demonstrations; such facilities also provide exhaustive test candidate instrumentation.
Most NTP reactor designs use liquid hydrogen as both the rocket propellant and reactor coolant. Reactor power controls are implemented using drums with graphite or beryllium on one side and boron poison on the other side. However, hydrogen flow also affects the reactivity. Therefore, control schemes for a nuclear rocket comprise two principal mechanisms: the rotation of the drums and the hydrogen flow. A serious concern for crewed and uncrewed missions to Mars is loss of reactor control. The reactor startup and initial rocket impulse are initiated in cislunar or near-earth orbital regions; therefore, radio communications between ground control and the NTP engine can occur in real time. However, currently for the Rovers on Mars’s surface (mars.nasa.gov, 2020), radio communications can take more than 20 min, depending on planet positions, to reach Mars orbiters from ground control. This is not a complete loss in communication but instead a lag in signal reception. While this may not be an issue for science missions streaming data, reactors can require fine-tune controls with fast instrumentation sample rates and near-real time processing. To mitigate this issue, local (or autonomous) controls will be needed onboard the NTP engine to ensure sustainable operation. Autonomous controls are well understood and widely used in manufacturing, chemical processing, and other large-scale process industries (Antsaklis et al., 1991). However, autonomous control schemes have not been demonstrated or implemented in research or power reactor contexts because they carry heavy implications for safety and reliability. To enable autonomous controls development, demonstration, and validation, ORNL created a nonnuclear hardware-in-the-loop test bed. Sensors throughout the test bed relay system status and hardware response to the autonomous control algorithm, including measurements of temperature, flow, pressure of a loop, control drum position, and drum speed. To reduce qualification timelines, space rated systems are employed where possible.
The only control functions in an NTP engine are the reactor reactivity and the hydrogen flow. This hardware-in-the-loop test bed is designed to operate as a tightly coupled system symbolic of the nuclear rocket engine. This means, the test bed allow users to study the reactor and flow loop as a singular engine instead of two isolated systems—which is different from other available test beds. However, the test bed is modular, scalable, and rapidly reconfigurable, making it adaptable for various design criteria test cases. The support infrastructure is built of 80/20 materials for simple assembly, disassembly, and reconfiguration. The NASA NTP program invested in the development of this test bed starting in 2017. The instrumentation and actuator locations and parts were heavily influenced by the ROVER/NERVA and SNAP-10A literature. Also, the ORNL team worked closely with BWXT and AeroJet Rocketdyne to select components comparable to industry designs. As seen in Figure 2, six hollow control drums with associated motors are positioned uniformly and axially around the periphery of the mock reactor section of the test bed. Assorted materials fill the inside of the control drums to adjust the weight. This enables variable torque measurements with distinctive control responses. Motor encoders, torque meters, and resolvers monitor the performance of drum position and speed. As discussed, control drums are typically composed of two materials, one absorbing the neutrons to control reactivity. Because this is a nonnuclear test bed, the neutronics are modeled and represented physically in the system through either light generation and photon transport or conduction and heat transport, according to the user’s preference. As the neutronics model steps through startup and steady-state operation, the furnace emits a correlating heat intensity. Moreover, the power of each of these mechanisms is monitored for systematic diagnostics. To sense the mock reactor neutrons, a thermocouple monitor the heat generated. The temperature measurement is symbolic to radiation detection using gas filled detectors.
Refined rotation of the control drums is only one portion of the test bed. To realize the flow portion of the engine, the mock reactor is coupled with a two-phase flow loop. The loop enables users to test pressure, flow, and temperature sensors. Because of facility limitations, flowing cryogenic liquid hydrogen (
A heat exchanger on the loop is driven by a reactor kinetics model and provides a temperature change in the loop that is representative of the hydrogen phase change. Thermocouples, resistive thermometers (i.e., resistance temperature detectors), and infrared cameras are used to monitor the temperature and feed data back into the software for analysis and implementation in the control loop. The entire loop is a scaled-down version of the anticipated loop hardware and functionality of the engine; however, the scaled-down version can provide invaluable data for modeling and simulation (M&S) of dynamic systems or digital twins.
Many modern systems aim for autonomous functions, forcing real-time data analysis deeper into system control algorithms and modeling schemes, such as digital twins and dynamic system modeling (DSM). Therefore, M&S and real-time data analysis require more computational power and edge computing. Because the test bed was developed to operate in real time and demonstrate advanced autonomous controls while maintaining scalability, the data acquisition hardware should function in the same manner. The NVIDIA Jetson graphics card enables interfacing the hardware-in-the-loop instrumentation with traditional industrial programmable logic controllers (PLCs). Because edge devices are already implemented in autonomous vehicle technology with large data streams, deployment of edge computing resources in nuclear applications is not far-fetched. A PC, high-performance computing, or cloud computing system communicates with the NVIDIA Jetson, leveraging GitLab to upload and download code. Users develop autonomous control algorithms locally at their facility and upload them to GitLab, then ORNL downloads the version-controlled code and executes it on the hardware-in-the-loop test bed. This method of development was selected to reduce design to demonstration time as well as system costs. This platform is very flexible and can host various programming languages such as C++, Python, etc.
To investigate specific behaviors of I&Cs as they encounter normal and off-normal operating conditions, ORNL developed a DSM that includes reactor neutronics (i.e., a point kinetics model) (Williams et al., 2023). The model was developed in Modelica (Rader et al., 2019; Rader and Smith, 2020) for nominal operating conditions with an operational set-point of outlet temperature and pressure at the nozzle, which can be changed to control the input for the simulation. The model is parameterized to allow for testing the off-nominal operation of individual components. For example, the turbomachinery can be tested at off-nominal efficiencies to simulate performance degradation or malfunctions. Moreover, drum malfunctions, such as the drums sticking, causing reactivity changes inside the point kinetics model can also be simulated. The Functional Mock-Up (FMU) standard is used to package the simulation with the numerical solvers in a convenient black box surrogate model and is run as a real-time simulation in the hardware loop to provide calculated responses based on the first principles model.
Building a digital twin of the system can serve many purposes, including adding redundancy using digital sensors and acting as a living model. Additionally, the digital twin can actively learn and adapt to real-time information during collection. The mock reactor system design allows the user to navigate easily between the physical reality and the digital twin; the digital twin can provide surrogate models as replacements for gaps in the hardware. Through exhaustive testing and demonstration, this approach uses digital twin models as redundant instrumentation and reducing payloads to build the confidence for licensing and approvals.
NTP is one mechanism that will enable crewed missions to Mars; however, gaps in the technology must be addressed. Specifically, autonomous control of the engine in the case of communication delay or loss will be critical for ensuring the safe and reliable operation of the reactor and flowing hydrogen loop. ORNL developed a hardware-in-the-loop system to serve as a nonnuclear autonomous control test bed to address technology gaps for NTP. This test bed, coupled with Modelica modeling, provides engine developers with the ability to elevate the technology readiness levels of instrumentation and autonomous controls. This approach represents one of the only means of performing autonomous controls and instrumentation testing in the absence of a complete ground demonstration of the engine.
The original contributions presented in the study are included in the article/Supplementary Material, further inquiries can be directed to the corresponding author.
NE: Conceptualization, Methodology, Project administration, Supervision, Writing–original draft.
The author(s) declare that financial support was received for the research, authorship, and/or publication of this article. This research is funded by NASA’s Space Technology Mission Directorate under the Space Nuclear Propulsion Program.
The author would like to acknowledge NASA Marshall Space Flight Center, Aerojet Rocketdyne, and BWXT for their contributions to the design of the test bed, as well as the ORNL research staff and technicians who were instrumental in the fabrication of the system, including Brandon Wilson, Craig Gray, and Nick Termini. The data acquisition and controls hardware was developed by Charles Taylor at Louisiana State University, and the dynamic modeling software was developed by ORNL researcher Wesley Williams.
This manuscript has been authored by UT-Battelle, LLC under contract DE-AC05-00OR22725 with the US Department of Energy (DOE). The US government retains and the publisher, by accepting the article for publication, acknowledges that the US government retains a nonexclusive, paid-up, irrevocable, worldwide license to publish or reproduce the published form of this manuscript, or allow others to do so, for US government purposes. DOE will provide public access to these results of federally sponsored research in accordance with the DOE Public Access Plan (http://energy.gov/downloads/doe-public-access-plan).
The author declares that the research was conducted in the absence of any commercial or financial relationships that could be construed as a potential conflict of interest.
All claims expressed in this article are solely those of the authors and do not necessarily represent those of their affiliated organizations, or those of the publisher, the editors and the reviewers. Any product that may be evaluated in this article, or claim that may be made by its manufacturer, is not guaranteed or endorsed by the publisher.
Antsaklis, P., Passino, K., and Wang, S. (1991). An introduction to autonomous control systems. IEEE Control Syst. Mag. 11, 5–13. doi:10.1109/37.88585
Borowski, S. K., McCurdy, D., and Packard, T. (2013). “Nuclear thermal propulsion (NTP): a proven, growth technology for ‘fast transit’ human missions to mars,” in AIAA SPACE 2013 Conference and Exposition 5354.
Finseth, J. L. (1991). Rover nuclear rocket engine program: overview of rover engine tests. Final Report. Tech. Rep. Sverdrup Technol Inc.
Rader, J. D., Smith, M. B., Greenwood, M. S., and Harrison, T. (2019). Nuclear thermal propulsion dynamic modeling with modelica
Robbins, W. (1991). “An historical perspective of the nerva nuclear rocket engine technology program,” in Conference on Advanced SEI Technologies, USA, 06 September 1991.
Truscello, V. C. (1983). SNAP nuclear space reactors. Tech. rep., U. S. Space Nucl. React. Power Program.
Keywords: nuclear thermal propulsion, autonomous controls, demonstration test bed, Modelica modeling, verification and validation
Citation: Ezell NDB (2024) Demonstrating autonomous controls on hardware test beds is a necessity for successful missions to Mars and beyond. Front. Nucl. Eng. 3:1308045. doi: 10.3389/fnuen.2024.1308045
Received: 05 October 2023; Accepted: 20 June 2024;
Published: 22 July 2024.
Edited by:
Tonya Vitova, Karlsruhe Institute of Technology (KIT), GermanyReviewed by:
Christiane Heinicke, University of Bremen, GermanyCopyright © 2024 Ezell. This is an open-access article distributed under the terms of the Creative Commons Attribution License (CC BY). The use, distribution or reproduction in other forums is permitted, provided the original author(s) and the copyright owner(s) are credited and that the original publication in this journal is cited, in accordance with accepted academic practice. No use, distribution or reproduction is permitted which does not comply with these terms.
*Correspondence: N. Dianne Bull Ezell, YnVsbG5kQG9ybmwuZ292
†ORCID: N. Dianne Bull Ezell, orcid.org/0000-0001-9334-5822
Disclaimer: All claims expressed in this article are solely those of the authors and do not necessarily represent those of their affiliated organizations, or those of the publisher, the editors and the reviewers. Any product that may be evaluated in this article or claim that may be made by its manufacturer is not guaranteed or endorsed by the publisher.
Research integrity at Frontiers
Learn more about the work of our research integrity team to safeguard the quality of each article we publish.