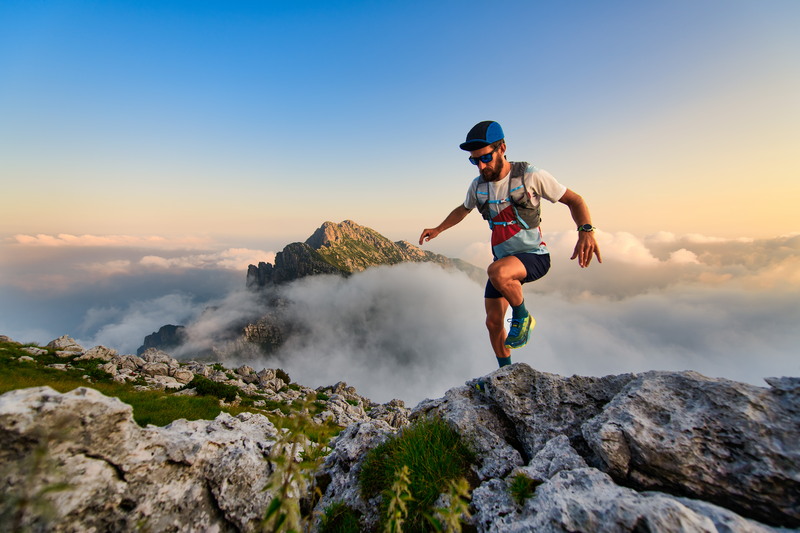
95% of researchers rate our articles as excellent or good
Learn more about the work of our research integrity team to safeguard the quality of each article we publish.
Find out more
REVIEW article
Front. Mech. Eng. , 12 July 2024
Sec. Solid and Structural Mechanics
Volume 10 - 2024 | https://doi.org/10.3389/fmech.2024.1284758
This article is part of the Research Topic Lightweight Mechanical and Aerospace Structures and Materials View all 5 articles
The penetration fuze, as the initiation control component of the penetration weapon, usually experiences an overload of tens of thousands or even hundreds of thousands of g during the penetration process. In order to prevent the fuze from being overloaded and causing the weapon to explode or misfire early, this article introduces the use of internal sealing reinforcement and external energy absorbing buffer materials to protect the internal circuit modules of the fuze. Several kinds of energy absorbing and buffering materials, including foam metal materials and composite sandwich structure materials, as well as metamaterials that have recently attracted the attention of industry and academia, are reviewed. The high overload impact energy absorption characteristics of materials and the mechanical properties of different material structures are emphatically introduced. In addition, this article also evaluates the applicability and limitations of existing buffer materials and methods, and proposes some potential improvement plans, such as the impact of parameters such as viscoelasticity, porosity, surface coating, printing process, heat treatment process on the energy absorption effect of materials, further improving the engineering practicality of buffer protection materials. A summary of the key technologies in the research of penetration fuze protective materials was made, and some mechanical testing methods were proposed, which can better characterize the impact resistance and resilience of materials. Finally, the future development direction of buffer materials for penetration fuzes was explored, which will help promote the research on the concept of buffer materials used on penetration missiles.
In tandem with the evolution of modern military technology, the potency of various strike equipment has grown significantly, prompting the continuous reinforcement of targeted defensive structures. In contemporary warfare, high-value targets such as command centers, hangars, fuel depots, and ammunition depots have largely shifted underground and have been fortified with multi-layered reinforced concrete protective layers, boasting strengths surpassing C35 and thicknesses exceeding 6 m. Conventional ammunition has become ineffective against such robust hard targets, rendering only high-energy penetrating ammunition capable of breaching these fortified underground structures (Ulbin et al., 2018a; Zhang, 2018; Li et al., 2021; Luo et al., 2021; Jiang et al., 2022).
During the penetration of hard targets by warhead components, the fuzes endure exceptionally high impact stresses, with impact acceleration amplitudes surpassing 100,000 gravity (g) and pulse durations ranging from hundreds of microseconds to milliseconds. This results in the impairment and malfunction of internal electronic components within the fuzes (Natticha et al., 2020; Yu et al., 2020; Amir et al., 2022). As penetrating projectiles serve as the principal armament for deep and forceful firepower strikes, the functional efficacy of accompanying fuzes significantly influences the overall combat effectiveness of the weapon system. Hence, buffering and protection of the fuzes and their electronic components under high g-force impacts bear paramount importance for the development of hard-target-penetrating munitions.
This paper aims to delve into the analysis of materials for safeguarding fuzes intended for penetrating hard targets. It meticulously investigates and synthesizes the current state of research on energy-absorbing buffering materials conducted. Building upon the theoretical foundations and research methodologies of previous researchers, this paper proposes a technological framework suitable for the study of protective materials for fuzes intended for penetration. It also explores the distinct characteristics and developmental trends of protective materials for such fuzes, providing a reference for research in the field of penetrating fuzes.
The first category of fuze protection primarily employs techniques such as spacers and encapsulation. Michailidis et al. (Michailidis et al., 2011) utilized raw sugarcane to prepare porous aluminum through dissolution and sintering methods, demonstrating that different deformation patterns are contingent on foam relative to density. Enhancement of energy absorption is achieved by reducing foam pore size and relative density, while pore uniformity and sintering temperature impact energy absorption. Lu et al. (2021) proposed a novel foam-filled aluminum core composite sandwich panel to enhance the impact resistance of conventional hollow-core sandwich panels. The tubular core material and foam aluminum filler dissipate a substantial portion of the impact energy. Results indicate that employing a foam aluminum filling, increasing the foam density, and augmenting the contact area between the foam aluminum and the panel bolster impact force and energy absorption. Foam aluminum filling also prevents a sharp increase in the impact force post-panel compaction. When designating flat steel plates and tubular core materials with analogous thicknesses, sandwich panels typically manifest improved energy absorption performance. Kyle et al. (2022) observed foam aluminum deformation during impact, characterized by the formation of multiple irregular collapse bands. These bands vary in size and shape, with propagation direction determined by pore distribution and solid composition. Collapse band width increases with augmented applied strain. Liu et al. (2013) experimentally studied impact behavior, deformation patterns, and energy absorption capacity during the axial fracture of foam aluminum. Two distinct foam aluminum components were prepared using a melt-transition foaming process. Test results revealed two dynamic impact steps: initial compression and progressive fracture. Peak load increase was attributed to micro-inertial effects within the displacement–load curve. Dual deformation modes exist due to wave propagation and reflection. Increasing foam density during impact leads to heightened specific energy absorption. Xiang et al. (2020) proposed a bio-inspired multi-layered graded foam-filled structure (MGFS) mimicking the bone microstructure and studied the influence of structural geometric dimensions on energy absorption characteristics through a combination of simulation and experimentation. Xiang et al. (2022) proposed a bionic multi-layer foam filling structure, simulating the microstructure characteristics of human bones, whale whiskers and other biological structures. The energy absorption characteristics of different combinations of structures were analyzed and the optimal model was obtained. Shen et al. (2011) studied the response of sandwich tubes under internal explosive loads, and analyzed the deformation mechanism of sandwich tubes by generating shock waves through TNT charging. Fan et al. (2013) studied the dynamic lateral crushing behavior of short hollow tubes and sandwich circular tubes. The test samples were dynamically tested at constant speeds of 1 m/s and 10 m/s, and the crushing and collapse processes of different specimens were studied. Ngoc and Lu (2019) provided a comprehensive overview of the latest progress in the development of biomimetic structures for energy absorption applications, introducing the contemporary challenges and future directions of biomimetic structures.
The above methods indicate that the mechanical properties of buffer materials can be effectively improved through gasket and sealing reinforcement technology. The main advantages of this method are low cost and high efficiency. However, with the continuous reinforcement of defense structures, the power of penetrating ammunition is also constantly increasing. The fuze shell installed inside the projectile body will also be squeezed and deformed due to the deformation of the projectile body. The deformation of the projectile body can cause deformation of the outer shell of the fuze, such as stretching and bending, which in turn leads to deformation of the sealing material. If there are bubbles or cracks in the sealing material, deformation will exacerbate its degree of damage. When the deformation amplitude generated by the sealing material is too large, it will inevitably cause deformation of the internal circuit board and components of the fuze, causing the fuze circuit to not work properly, thereby affecting the damage efficiency of the ammunition. Traditional fuze-protective materials are no longer sufficient to meet the buffering and protective requirements under high-overload and intense impact. Thus, fuze-protective materials must evolve towards a greater mechanical performance, ensuring the secure and stable operation of penetrating fuzes (Ulbin et al., 2018b; Wang et al., 2018; Talebi et al., 2019; Sun et al., 2020). In this context, composite buffering protective materials have become a viable option, surpassing the strength and toughness limitations of traditional foam metals. Consequently, under the backdrop of high-overload and intense impacts, research on composite buffering protective materials with higher yield and tensile strength holds significant theoretical and practical value within this domain.
In contrast to the first category of fuze-protective materials, the second category involves blending porous media with elastic substances to create foam metal composite protective materials. Foam metal, a significant subset of porous materials, has garnered extensive attention due to its lightweight nature and energy-absorbing capacity during deformation. Michał et al. studied aluminum–silicon carbide composite foam as a filler for thin-walled aluminum sections, as shown in Figure 1. To enhance energy absorption performance, the use of porous metal–ceramic composite structures as fillers was analyzed for improved crush efficiency metrics. Observations indicated smaller crush distances for foam-filled profiles, suggesting further potential for energy absorption. However, due to the unavailability of response states under high-speed impact, stringent requirements are imposed on protective materials for penetrating fuzes.
Figure 1. Aluminum–silicon carbide composite foam (Michał et al., 2022).
Ashutosh et al. fabricated aluminum composite foam-core sandwich structures with carbon fiber-reinforced cold-cured resin panels, as illustrated in Figure 2. Bending performance and energy absorption of these sandwich structures were analyzed through three-point bending tests. Findings indicated a significant increase in bending load-carrying capacity, bending stiffness, and energy absorption of sandwich structures with augmented foam core thickness. Strong interface bonding between the foam core and panels due to carbon fiber reinforcement enabled the sandwich structure to withstand a higher bending strength and stiffness. Compared to bare foam and sandwich structures containing only cold-cured acrylic resin, this material exhibited a greater energy absorption capacity.
Figure 2. Carbon fiber-reinforced cold-cured resin–aluminum composite foam-core sandwich (Ashutosh et al., 2020).
Taherishargh et al. developed a novel expanded perlite–aluminum composite foam, as depicted in Figure 3. This composite was formed through gravity infiltration of low-cost expanded perlite particles with molten A356 aluminum. Quasi-static uniaxial compression tests were conducted on this material. Under compression, the material displayed a stress–strain curve comprising elastic, plateau, and densification regions. Notably, this material exhibited high energy absorption efficiency, and a slight increase in composite foam density significantly improved its mechanical performance. Nonetheless, the mechanical strength of expanded perlite is limited and cannot directly enhance the mechanical properties of the composite foam.
Figure 3. Expanded perlite–aluminum composite foam (Taherishargh et al., 2014).
Cheng et al. investigated the compression performance and energy absorption characteristics of silicon rubber-filled porous aluminum foam (Figure 4). Stress–strain curves were generated for the foam aluminum and silica rubber composite material, and comparisons were made with foam aluminum and bulk silica rubber. The stress–strain curve exhibited two stress plateaus, contrasting with foam aluminum’s single plateau region and the absence of stress plateaus in bulk silica rubber. Experimental results revealed that, compared to foam aluminum, this composite material demonstrated a stronger energy absorption capacity and efficiency.
Figure 4. Silicon rubber-filled porous aluminum foam (Cheng and Han, 2003).
Furthermore, enhancing material mechanical properties can also be achieved through improved combinations, such as multi-layer composite structures. For instance, Bai et al. (2016) designed a sandwich structure material with functional gradient foam and carbon fiber composite materials for the upper, middle, and lower layers, using glass fiber composite material, polyurethane, and multi-walled carbon nanotube composite materials. They verified its electromagnetic wave absorption and shockwave-blocking abilities through optimization algorithms, making it suitable for novel armor plates capable of radar reconnaissance and reducing impact-induced harm to personnel. Changze et al. (2023) studied the damage characteristics of carbon fiber foam sandwich structures under different core thicknesses and impact energies. Ultrasonic scans were employed to measure depth and area of impact-damaged regions. Experimental results indicated a correlation between impact damage depth and area with impact energy, with changes in growth rates occurring with increased impact energy.
Baroutaji et al. proposed a sandwich tube composed of foam aluminum core and thin-walled circular pipes as an energy absorption device. The sandwich tube was laterally crushed under quasi-static loading conditions, as depicted in Figure 5. Factor analysis of the optimal design results was conducted to examine the impact of geometric parameters on sandwich tube responses. Additionally, multi-objective optimization design using an idealized approach determined that tubes with minimal inner layer diameter and maximum foam thickness were better suited for energy absorption components.
Figure 5. Sandwich tube under quasi-static loading (Baroutaji et al., 2015).
Zhang et al. explored the energy dissipation mechanism of pyramid lattice sandwich panels under underwater explosion conditions. Experimentally revealed deformation modes of the conical lattice sandwich panels under underwater explosions are illustrated in Figure 6. Analysis demonstrated the evident advantages of the conical lattice sandwich panel in resisting underwater explosions. The pulse transmitted to the experimental model was attenuated significantly to 54.97% of the incident pulse. This study provides better support for ship structural protection.
Figure 6. Equivalent stress–strain curve of the pyramid lattice cell (Zhang and Jin, 2022).
Houcine et al. investigated the energy absorption and damage characteristics of glass fiber-reinforced polymer (GFRP)-laminated and polyvinyl chloride (PVC) foam sandwich composite materials under repeated impacts, as shown in Figure 7. The study compared the energy absorption capacity and damage effects of GFRP-laminated and PVC foam sandwich composite panels used in naval equipment and aviation structures under repeated low-speed impacts and quasi-static indentation. A series of repeated impact tests were performed until complete energy absorption was achieved, followed by quasi-static compression tests. The damage mechanisms of these composite materials were analyzed. The experimental results demonstrated that compared to laminated composite materials, sandwich structures exhibited better resistance to repeated impact overload.
Figure 7. Foam core composite materials: (A) front view of laminated plate, (B) partial view of laminated plate, and (C) core section (Houcine et al., 2022).
The impact resistance capacity of sandwich composite materials crucially depends on the core. To further study the core’s impact on the energy absorption characteristics of sandwich structures, Neslihan et al. proposed a three-dimensional multi-layer stitched core sandwich composite material and conducted impact response tests. The research designed a 3D multi-layer stitched core integrated with glass/epoxy resin face layers, as shown in Figure 8. Dynamic impact test results indicated that peak force and energy absorption of sandwich composite materials increased with the number of core layers. Among the energy absorption mechanisms of sandwich composite materials, the core was more effective than the face. The number of core layers, core unit size, and stitching density were identified as the most critical parameters for impact failure in sandwich composite materials.
Figure 8. 3D multi-layer stitched core sandwich composite material (Neslihan and Gaye, 2022).
Zhang et al. mixed porous material particles with elastic polymers to form thin film materials, making activated carbon rubber fuze protective materials. By changing the microstructure and the content of elastic polymers, their protective performance was improved. The Marshall hammer test system was used to verify the protective film gasket. From the overall trend, as the EPDM rubber content increased, the recoverable performance of the composite film in multiple loading tests improved, as shown in Figure 9A. It can be seen that adding EPDM rubber to porous activated carbon films can significantly improve the elasticity of composite carbon films. From local details, when the content of EPDM rubber is less than 10%, the coefficient of recovery of the sample increases rapidly with the increase of EPDM rubber content; When the content of EPDM rubber is greater than 10%, the recovery coefficient of the sample increases slowly, as shown in Figure 9B. Therefore, when adding EPDM rubber, attention should be paid to the proportion of rubber. Adding excessive rubber will not bring an equal amount of performance improvement, but will instead affect its internal structure and compressibility. Through previous research accumulation, the structure of high-performance buffer materials can be determined as a combination of superelasticity and high porosity.
Figure 9. Test results of activated carbon rubber fuze protective material. (A) The relationship between the recovery coefficient corresponding to different stresses and the proportion of rubber mass (B) Acceleration changes after adding cushioning materials (Zhang et al., 2022a).
The above composite cushioning and protective materials all have strong mechanical properties and energy absorption characteristics, which can improve the material’s impact resistance. In addition, the above research also compares and analyzes the impact energy absorption effects under different structures by changing the geometric parameters of porous materials, providing a reference basis for the design of porous structures. However, there are still some influencing factors that need to be studied, such as the influence of parameters such as porosity, surface coating, printing process, and heat treatment process on the energy absorption effect of the material, in order to further improve the engineering practicality of composite buffer protection materials.
The third category of cushioning protective materials involves incorporating new materials or metamaterials as additives to metallic materials to further enhance the mechanical properties of foam metals. Graphene, one of the strongest materials with excellent toughness, when combined with metal forms graphene–metal composite alloys that significantly elevate alloy yield and tensile strength. Aerogels exhibit ultra-high toughness, National Aeronautics and Space Administration (NASA) scientists have experimented with flexible aerogels made of polymers as insulation materials for spacecraft during atmospheric entry. Aerogels can be employed for blast-resistant suits and armored vehicles in the military domain and for protecting electronic mechanical components in space exploration, unaffected by large temperature differentials. Compared to traditional impact-resistant materials, nano-carbon materials possess advantages such as being lightweight, having a high energy dissipation specific capacity, and exceptional thermal stability under extreme environmental conditions. Metamaterials refer to composite materials with artificially designed structures that exhibit extraordinary physical properties not present in natural materials. For instance, local resonance-type metamaterials, when the frequency of external impact loads aligns with the internal resonance frequency of the metamaterial, the internal microstructure of the local resonance-type metamaterial resonates, absorbing impact energy and mitigating impact loads. Honeycomb structure mechanical metamaterials possess advantages such as being lightweight, having a high specific stiffness, negative Poisson’s ratio, adjustable structural parameters, and stable mechanical properties.
Gao et al. proposed a novel negative-stiffness-based mechanical metamaterial, as shown in Figure 10, which possesses buffering, energy absorption, and state recovery characteristics in two loading directions. The unit of this metamaterial consists of intersecting curved beams, support frameworks, and support beams. By inducing the sudden change in curved beam stability, buffering, energy absorption, and initial state recovery are achieved. Static compression and tension experiments were conducted on three designed negative-stiffness structures, revealing leap behavior and energy absorption effects in both loading directions. Therefore, this structure can be used for bidirectional cushioning and energy absorption, exhibiting good state recovery and impact resistance through repeated experiments. The structure undergoes initial deformation at an acceleration of 20 m/s2, elastic imbalance at 120 m/s2, and compaction at 280 m/s2, with corresponding acceleration attenuation rates of 20%, 50.6%, and 1.6%.
Figure 10. Negative-stiffness bidirectional cushioning and energy absorption metamaterial (Gao et al., 2021).
Ma et al. introduced a series of innovative metamaterials with planar and cylindrical patterns for elastic energy dissipation and shock absorption, as shown in Figure 11. These metamaterials feature planar unit cells with two axes of reflection symmetry primarily composed of two V-shaped regions, four identical right-angled triangle regions, and narrow regions. The three-dimensional and cylindrical units were obtained through rotation and convolution methods. The designed multi-layer metamaterial exhibited substantial energy dissipation induced by leap-induced hysteresis force-displacement behavior, with its performance influenced by geometric parameters and layers. Finally, the designed metamaterial effectively suppresses acceleration responses through leap behavior induced by elastic instability. Experimental and numerical research was conducted on the impact response processes and corresponding deformation mechanics. This metamaterial holds significant potential in impact and vibration engineering. Research has shown that the dynamic buffering performance of cylindrical metamaterials slightly increases with the increase of impact height, leading to a slight increase in peak acceleration. The penetration behavior exhibited by the peak acceleration in the second stage can suppress the acceleration response of the impactor, and the experimental dissipated energy under quasi-static load is 0.692J.
Figure 11. Planar and cylindrical metamaterials (Ma et al., 2022).
Zhao et al. designed and manufactured a series of mechanically metamaterials dominated by tensile mechanical performance (Figure 12). These metamaterials can absorb large amounts of energy while maintaining low density. The design strategy relies on network structures in periodic grid topologies, using microstructures with multiple beams as building blocks to connect grid nodes. Mechanical properties can be adjusted by altering the topology parameters. Furthermore, metamaterials manufactured using 4D printing technology exhibit intelligent properties, transitioning from one mode to another under external stimuli. These materials excel in compression resistance, energy absorption, shock absorption, and shape memory effects, finding applications in engineering fields such as bone tissue scaffolding, aerospace, and automotive engineering. However, these materials exhibit slow self-healing speeds and are not suitable for environments with short intervals of continuous impact overloads. The research results indicate that the relative compressive stiffness increases with the increase of truss diameter. In addition, the ratio of cell height to length can effectively affect the value of relative stiffness. The higher the ratio, the greater the relative stiffness. Poisson’s ratio is very sensitive to changes in truss diameter, length, height ratio, and other parameters. As the diameter of the truss increases, the Poisson’s ratio gradually decreases. In addition, the Poisson’s ratio gradually increases with the increase of length to height ratio.
Figure 12. 4D-printed metamaterial with excellent energy absorption capacity (Zhao et al., 2022).
Chen et al. introduced and fabricated a reusable continuous carbon fiber-reinforced polymer composite with a negative stiffness mechanical metamaterial, as illustrated in Figure 13. The combination of compression tests and numerical simulations verified the quasi-static mechanical performance of this structure. The repetitive nature of this metamaterial was then demonstrated through cyclic compression tests. Quasi-static test results revealed that this metamaterial exhibited excellent reusability and energy absorption capabilities. Furthermore, the cushioning performance of this metamaterial was studied through flat impact tests. The metamaterial structure displayed robust impact resistance without undergoing any plastic deformation. In terms of energy absorption, the maximum specific energy absorption and average compression force of the 0°stacked sequence structure used in this study are 690.2 J/kg and 149.9 N, respectively. When the bending beam of the structure adopts a superposition sequence of ±45°and 90°, the maximum specific energy absorption of the structure is 189.1 J/kg and 47.2 J/kg, respectively, which is equivalent to 27.4% and 6.8% of the bending beam with a superposition sequence of 0°. Similarly, the average compression force of the ±45°and 90°stacked sequence structures decreased to 41.1 N and 10.2 N, respectively, compared to the 0°stacked sequence structure, which showed a relative decrease of 72.6% and 93.2%. This study holds guiding significance for designing the impact resistance performance of penetration fuzes in high-overload environments.
Figure 13. Continuous carbon fiber-reinforced polymer composite with a negative stiffness mechanical metamaterial (Chen et al., 2022).
Yang et al. designed a cross symmetric hyperbolic beam mechanical metamaterial (BCBS), as shown in Figure 14. Compared to traditional curved beam structures, its axial and circumferential symmetry can achieve synergistic buffering protection for the forward impact received by the fuze in the bore and the lateral impact received during penetration. This design is based on the concept of bistability and combines negative stiffness sandwich structure and hyperbolic beam structure for microstructure design. Compared to traditional negative Poisson’s ratio materials that can only absorb energy through irreversible collapse or plastic deformation, negative stiffness structures with bistability can achieve high energy absorption while switching between multiple steady states. By introducing negative stiffness microstructures, the energy absorption of the steady-state buffer layer is increased, ensuring a certain degree of recoverability while absorbing a large amount of energy, which can meet the requirements of fuze buffering protection in short interval multiple strong impact environments. In addition, multiple continuous dynamic impact tests were conducted on BCBS metamaterials, and dynamic numerical simulations were conducted based on the projectile impact 5-layer target plate condition. As shown in Figure 14A, the overall system applies an initial velocity, simulates the initial target collision conditions, applies the acceleration received by the projectile on the upper constraint surface, and transmits it to the lower rigid surface through the BCBS structure buffer, simulating the energy transfer process between the projectile, buffer, and fuze during the impact process. The consistency and calculation time comparison between the equivalent simulation calculation method and dynamic penetration simulation are shown in Figure 14B. Under the same operating conditions, 89.5 h of time are saved. Figure 14C shows the magnitude of the acceleration at the fuze during five consecutive impacts with the addition of BCBS. After adding buffering, the peak acceleration significantly decreased and the oscillation frequency was also suppressed. Figure 14D shows that BCBS has a better energy absorption effect. As the number of impacts increases, the peak attenuation ability of BCBS acceleration decreases from 54.7% for the first time to 34.8% for the fifth time. In multi-layer penetration, the peak overload reaches nearly 146,000 g without buffering, and after BCBS buffering, the peak value can be reduced by 75,000 g, effectively reducing interlayer oscillation signals.
Figure 14. Dynamic simulation of multiple impact process for BCBS configuration. (A) Constraints and load settings for finite element simulation; (B) Comparison of calculation time between equivalent simulation and penetration dynamics simulation; (C) Dynamic acceleration signals under different buffering conditions (D) Maximum acceleration and energy absorption ratios under different buffering conditions (Yang et al., 2024).
Xiang et al. (2021) used SLM technology to print 8 Miura-ori metamaterials with different gradients, and studied the effects of different geometric parameters, gradient spacing, and stacking order on the mechanical properties of stainless steel materials. Research has found that compared to uniform metamaterials, The graded Miura ori stainless steel metamaterials can effectively reduce the reduction in compressive load after peak force and improve energy absorption capacity. Models with larger gradient intervals have higher average load displacement forces and lower peak crushing forces. Sun et al. (2019) designed a hierarchical honeycomb structure, replacing each trilateral vertex of a regular hexagonal lattice with a smaller hexagonal shape. Specific structural layering parameters were proposed, and the effects of structural hierarchy, wall thickness, and core layer height on the honeycomb back plate and core layer were explored. The optimal structural parameters for explosion resistance were obtained.
Overall, honeycomb structured metamaterials have a higher negative Poisson’s ratio effect, and the plastic collapse of the metastructure can quickly achieve kinetic energy conversion, which can cope with the impact estimation environment of long pulse width and high overload. Due to its precise structure, higher requirements are placed on machining accuracy. For products with a large batch demand such as fuzes, it is also necessary to pay attention to their machining efficiency. In addition, viscoelasticity is also an important indicator of energy absorbing materials, and there are few reports in the current research process. A large number of theoretical and experimental studies have shown that although honeycomb structured metamaterials have good energy absorption characteristics, due to irreversible plastic deformation during the first impact process, they become compacted and dense, resulting in a rapid decrease in their energy absorption characteristics during subsequent impact processes. At the same time, the compression characteristics of honeycomb structured metamaterials make the buffer structure mainly composed of porous media form a compressed space after a single penetration of the target, making it difficult or less likely for the data storage chip inside the fuze to survive in multi-layer hard target penetration experiments. Therefore, honeycomb structured metamaterials are usually only suitable for single impact processes, and their buffering and energy absorption performance in multiple impacts cannot meet the protection requirements during multi-layer penetration processes.
The protection research of the internal circuit module of the fuze mainly focuses on two aspects: internal sealing reinforcement and external vibration isolation and buffering.
(1) Internal reinforcement and sealing
The internal reinforcement potting technology mainly utilizes potting materials with strong impact resistance and high bonding ability to potting the circuit components inside the fuze as a whole, On the one hand, it can provide structural support for components and achieve the purpose of firmly connecting them in situ on the circuit board. On the other hand, it can utilize the energy absorption characteristics of the potting material itself to dissipate the mechanical energy transmitted to electronic devices, improving the high impact resistance and shear strength of the test structure from within the fuze. At present, materials based on epoxy resin, organosilicon polymers, and polyurethane are the most researched sealing materials in the chemical industry. The high g-value ballistic flight recorder FDR developed by the Swiss Weapon Systems and Ammunition Testing Center was successfully measured with a peak acceleration of 90000 g and a pulse width of 200us (Rothacher and Giger, 1999). In order to avoid damage, the circuit and battery parts were sealed with epoxy resin and protected with a steel shell. Li et al. analyzed the performance characteristics of several sealing materials such as silicone rubber, polyurethane, and epoxy resin, and used epoxy resin to reinforce electronic products, as shown in Figure 15. Simulation and physical experiments were conducted, and the results showed that the impact resistance of electronic products sealed with epoxy resin was significantly enhanced. This technology has certain practicality.
Figure 15. Physical image of electronic products sealed with epoxy resin (Li et al., 2020).
Of course, overall sealing and reinforcement of the internal components of the fuze can also have adverse effects, mainly reflected in the following two aspects:Firstly, the sealing material will bring additional mass, which increases the overall quality of the fuze system; Secondly, the thermal conductivity of the encapsulation material is poor, which affects the heat dissipation of some circuit units. During continuous operation, the reliability of the system may be reduced due to heat accumulation. Therefore, improving material heat dissipation, molecular density, and optimizing material electrical, mechanical, and thermal properties are important directions for the development and research of encapsulation materials at present.
(2) External vibration isolation and buffering
In addition to the internal sealing reinforcement method introduced above, external vibration isolation and buffering are also commonly used buffering protection measures for fuzes. Its protection principle is to isolate the fuze from the warhead by using appropriate buffering materials to avoid direct stress on the fuze. On the one hand, due to the different wave impedances of stress waves transmitted in different media, the difference in wave impedances of different materials can be effectively used to suppress the transmission of stress waves from the projectile to the fuze; On the other hand, buffer materials, due to their own elastic-plastic deformation ability and damping effect, can absorb the impact load acting on the fuze during the penetration process, thereby reducing the stress on the internal components of the fuze during the penetration process, achieving the purpose of buffer protection. For penetration fuzes, they withstand strong impacts of thousands or even tens of thousands of grams of overload during operation, and the design space left for the fuze inside the projectile is extremely limited. The thickness of the material is greatly limited, so suitable buffer materials are not common. At present, in practical engineering applications, there are two kinds of buffer materials commonly used in fuzes, namely, foam metal materials with porous structure and polymer materials with relatively stable performance.
Foam metal material refers to special metal material containing foam pores, which is a new engineering material emerging in recent decades. Due to its low relative density (only about 40% of aluminum alloy) and excellent energy absorption characteristics, it is widely used in military protection, aerospace, automobile transportation and other fields. At present, known foam metal materials include foam copper, open cell foam aluminum, closed cell foam aluminum, foam nickel, foam magnesium, etc. Among them, foam aluminum materials are widely used in engineering due to its relatively low price and excellent energy absorption and buffering performance. The current research results show that the energy absorption performance of foam aluminum mainly comes from compression deformation, which is related to many factors such as porosity, strain rate, pore size, pore structure type, and uneven pore structure distribution.
Because foam aluminum has good energy absorption and buffering characteristics, many researchers apply it to the buffering protection of missile borne equipment. Xu et al. (2010) of Xi’an Institute of Mechanical and Electrical Technology, proposed to use foam aluminum as the buffer pad of the hypersonic penetration fuze, established a hypersonic penetration model of 1800 m/s, and used LS-DNYA finite element software for simulation analysis. The results show that the 6 mm foam aluminum pad can effectively attenuate the impact amplitude, reduce the impact on the fuze components to be tested to below the extreme value, and play a better role in resisting high overload impact. Gao Hua of the Army University of Engineering and others conducted research on the dynamic mechanical properties of foam aluminum under multiple impacts, and used the Hopkinson bar device to carry out multiple loading tests on foam aluminum under medium and low strain rates, as shown in Figure 16. The results show that with the increase of impact times, the cellular structure in foam aluminum gradually collapses and compacts, and the elastic limit stress increases, while the elastic limit strain increases, so the attenuation of stress waves decreases.
Figure 16. Physical Profile of foam Aluminum under Multiple Loading. (A) Before impact. (B) After the first impact. (C) After the second impact. (D) After the third impact. (E) After the fourth impact. (F) After the fifth impact. (Gao et al., 2018).
Ding et al. conducted compression tests and Machert hammer tests on four types of fuze protective rubbers (nitrile rubber, fluororubber, silicone rubber, and natural rubber), The experimental results are shown in Figure 17. After experimental comparison and analysis, it was found that the protective effect of fluororubber is the worst regardless of its thickness, while the other rubbers exhibit different protective performance under different penetration overloads or thicknesses. When using a 2 mm thick gasket, regardless of the size of the overload, natural rubber has the best comprehensive protective performance. This is because natural rubber has the best comprehensive performance, with high elasticity, strength, and impact toughness; When using a 4 mm gasket, silicone rubber should be used for protection when the overload does not exceed 60,000 g. When the overload exceeds 60,000 g, nitrile rubber should be used because nitrile rubber has the highest impact strength; When using a 6 mm gasket, silicone rubber should be used for protection when the overload does not exceed 50,000 g. When the overload exceeds 50,000 g, nitrile rubber should be used. When the penetration overload does not exceed 50,000 g, the optimal choice should be 4 mm silicone rubber; On the contrary, 2 mm nitrile rubber should be used.
Figure 17. Test results of four types of protective rubber gaskets for fuze. (A) 13 tooth impact 2 mm thick gasket, (B) 13 tooth impact 6 mm thick gasket, (C) 17 tooth impact 2 mm thick gasket, (D) 17 tooth impact 6 mm thick gasket (Ding et al., 2023).
Drawing upon research on cushioning protection materials, the categorization of cushioning protection materials can be outlined as follows:
Figure 18 illustrates that cushioning protection materials can be broadly classified into two categories: the first category employs foam structures for plastic deformation energy absorption in padding, and the second category pertains to encapsulation materials for safeguarding lightweight electronic devices. Foam metal primarily constitutes the materials for padding, where foam metal materials exhibit a stable yield region, enabling them to steadily absorb considerable energy over a prolonged stress plateau—making them well-suited as cushioning energy-absorbing materials (Selivanov et al., 2021). However, foam metal has a relatively low overload capacity, when the peak overload exceeds 50,000 g, the material experiences fractures, failing to achieve optimal protective effects. Furthermore, metal materials are only suitable for single-impact events, their cushioning energy-absorbing effects in multi-impact scenarios cannot fulfill the protection requirements for multi-layer penetration processes (Zhang et al., 2022b). Hence, the development of foam metal composites is essential to create high-strength, high-stiffness, and high-elasticity protective materials. By compounding foam metal with elastic polymer materials, it is possible to fabricate penetration fuze protection materials that possess both the mechanical performance of metal materials and the high damping and elasticity of elastic polymer materials (Zhou et al., 2021). Additionally, with the widespread application of new materials/super materials in fields such as aerospace, machinery, chemical engineering, biology, and medicine, this category of materials showcases excellent mechanical performance. These materials hold significant application prospects within the realm of fuzes (Mohammad and Bidhendi, 2022). In summary, the research characteristics of cushioning protection materials can be outlined as follows:
Firstly, most materials predominantly focus on energy absorption effects. However, for penetration fuzes, they endure multiple strong impact loading processes. Materials not only need to exhibit effective energy absorption during impact but also must self-recover after overload release in order to function as cushioning protection during subsequent impact events. Secondly, the majority of materials undergo quasi-static compression tests. While these tests provide the most direct and fundamental study of foam material energy absorption characteristics, they do not systematically investigate the characteristic curves and deformation modes of materials under high-dynamic impact with high overload. Thirdly, full consideration must be given to the scenario where fuzes penetrate multiple layers of target plates in a continuous manner. Moreover, the impacting velocity can sometimes reach several Mach, and the time interval between consecutive impacts of the fuze on the target is only a few milliseconds. This imposes higher requirements on the self-recovery efficiency of the materials. In summary, for penetration fuzes, the ideal protective material should possess both high energy absorption characteristics and rapid recoverability.
The overall technical roadmap for penetration fuze protection material research is illustrated in Figure 19. This system comprises five components: material preparation, mechanical performance analysis, dynamic impact testing, field tests, and signal acquisition systems.
From this perspective, the research on penetration fuze protection materials involves the following key techniques:
1) Material model design and fabrication
Material models for penetration fuze protection are designed that cater to high-overload scenarios (Li and Patricia, 2022; Hu et al., 2021; Li and Wang, 2021). Simulation analyses are conducted on material model elasticity, plasticity, porosity, and damage, solving nonlinear relationships between material stress and strain. The elastic deformation range, yield limit, impact of pore volume in porous media on the buffering effects, and material deformation behavior are simulated under mechanical loads (from initial elastic deformation to nonlinear fracture stages). Material elastic strain tensors and crack zone damage models are established, laying a solid foundation for material impact dynamics analysis (Adam et al., 2022; Liu et al., 2022).
2) Analysis of mechanical transmission laws
Finite element models for penetration fuze protection materials are constructed, achieving full parameterized control of the model (Wei et al., 2022). The dynamic response of materials under high-overload impact are systematically investigated. The deformation patterns under various impact velocities are studied, exploring the dynamic response of different density and thickness laminated structures, and the effective ranges for impact functions suitable for penetration fuzes and geometric functions of laminated structures are determined—establishing the ultimate thickness of the lamination for both compression/tension and bending resistance (Adam et al., 2022). Based on material strength and stiffness theories, the orthogonal anisotropic-equivalent mechanical parameters are derived, dynamic impact processes are numerically simulated, propagation patterns of internal stress waves observed, dynamic responses measured, and optimization recommendations for local reinforcement positions are provided to improve processing techniques.
3) High-g dynamic response testing
For dynamic energy absorption tests of penetration fuze protection materials, an in-house high-overload, wide-pulse, large-weight single-impact test device is employed, as depicted in Figure 20. This apparatus generates impact overloads >50,000 g, with an impact pulse width ≥231 μs Dynamic impact tests are performed on various samples, analyzing the material deformation and energy absorption characteristics for penetration fuze protection. Simultaneously, materials of different energy absorption characteristics and fill densities are tested, systematically researching sample the deformation modes and dynamic interactions.
Figure 20. Single-impact testing apparatus (Man et al., 2014).
For tests evaluating material recoverability, an in-house high-speed multi-layer target penetration simulation test system is employed, as shown in Figure 21. This system performs continuous impacts >8 times, with impact overloads >10,000 g, impact pulse widths >210 μs, and impact time intervals ≤3 ms. Continuous multi-dynamic impacts are performed on various test samples, analyzing the material recoverability. Different impact overloads, impact time intervals, and consecutive impact numbers are tested to assess the material’s multiple-absorption cushioning capabilities against shockwaves. Finally, samples with superior protective performance are used in conjunction with penetration projectiles for live firing field tests to verify the stable operation of internal electronic devices during the penetration process and their reliable triggering of warheads.
4) Signal acquisition and storage
Figure 21. High-speed multi-layer target penetration simulation test system (Li, 2022).
With the advancement of electronic technology, penetration fuze initiators commonly include internally loaded circuit boards and high-g acceleration sensors to measure acceleration signal changes during penetration. This signal is then identified, assessed, and used to determine the spatial position of the penetration fuze at a given moment. This information guides whether the preset detonation control strategy is met. Onboard memory (Figure 22) is utilized to store and retrieve test data. The axial acceleration curve produced during penetration is analyzed to verify the buffer energy absorption characteristics of the fuze protection material (Wei et al., 2022).
1) Lower density
In considering the lightweight and cost factors of penetration fuze buffer protection materials, when certain conditions such as impact force, contact area, stress–strain, and yield limits are met, materials with a lower density are prioritized (Lin et al., 2023).
2) Higher strength and recoverability
The strength of penetration fuze buffer protection materials determines the reliability of the fuze during high-speed penetration into hard targets. As military technologies develop worldwide, defensive structures become more robust, leading to increased impact overload on the fuzes. This places higher demands on material strength and stiffness. Moreover, complex defensive structures, reinforced with high-strength steel and layers of protection, will subject penetration fuzes to multiple consecutive impacts. Hence, better recoverability of materials is required to achieve precise hits on specific targets (Chen et al., 2023).
3) Improved electromagnetic shielding and thermal insulation
During the penetration of multi-layer hard targets, sensor signals are often interfered with by noise, leading to signal overlap issues that hinder target recognition. Therefore, penetration fuze protection materials need to exhibit excellent noise reduction, electromagnetic shielding, and thermal insulation properties. This helps prevent the introduction of external interference signals, allowing for the approximation that the acceleration measured by the accelerometer corresponds to the rigid body acceleration generated by the impact contact force (Lu et al., 2023).
4) Enhanced filtering performance
In the process of high-speed penetration of targets, fuzes experience significant stress, which propagates through the fuze’s internal media in the form of stress waves. When stress generated by collision reaches the fuze’s circuit board and chip internals, it can cause various failure modes, such as detachment of component pins, fractures of internal chip wires, and discharging of energy storage components (capacitors, batteries), leading to the overall failure of the fuze. The mechanism behind the improved impact resistance of fuze electronic components in penetration fuze protection materials primarily involves stress wave reflection and attenuation, i.e., mechanical filtering. The stress wave transmitted to the fuze’s circuit components undergoes attenuation through the buffering isolation structure, reducing damage to the internal structure of the fuze. Simultaneously, the buffering material can absorb the kinetic energy generated by the fuze’s overall oscillations (Wang et al., 2022).
5) Ease of processing, installation, and high forming precision
Given that fuzes are disposable products produced in large quantities, especially in times of conflict, the buffer protection materials for fuzes must be rapidly processable and easy to install. They should also maintain their shape and possess a high degree of integration with the fuze systems (Simoes et al., 2022).
This review gives an extensive overview of the latest research on energy absorbing buffer materials, which can be divided into three categories: foam metal materials, composite sandwich structural materials and metamaterials. These methods can cope with high overload impact environments and have different advantages. If the cost factor is taken into consideration, foam metal alloy can be selected; if the reserved space in the buffer zone is enough, composite sandwich structure can be selected; if the processing equipment technology level is high, metamaterial can be selected. In addition, an important aspect of the design process of energy absorbing materials is the mechanical impact characterization of the material. Mechanical testing should be targeted and realistic, and should simulate the real penetration environment as much as possible. Finally, more attention should be paid to the influence of process parameters on energy absorption efficiency, and the relationship between factors such as porosity, strain rate, pore size, pore structure type, pore structure distribution, and energy absorption efficiency should be determined. We hope that this review can promote research in specific fields of penetration fuzes and provide reference for relevant researchers.
AZ: Writing–original draft. PL: Writing–review and editing, HZ: Writing–review and editing.
The author(s) declare that financial support was received for the research, authorship, and/or publication of this article. This study has received support from the National Natural Science Foundation of China, with the Project No. 61403201.
The authors declare that the research was conducted in the absence of any commercial or financial relationships that could be construed as a potential conflict of interest.
All claims expressed in this article are solely those of the authors and do not necessarily represent those of their affiliated organizations, or those of the publisher, the editors and the reviewers. Any product that may be evaluated in this article, or claim that may be made by its manufacturer, is not guaranteed or endorsed by the publisher.
The Supplementary Material for this article can be found online at: https://www.frontiersin.org/articles/10.3389/fmech.2024.1284758/full#supplementary-material
Adam, E. G., Jeffrey, P. B., and Gregory, C. B. (2022a). An arbitrary Lagrange-Eulerian investigation of HRAM shallow jet pre-spurt formation and time sensitivities to impact plate dynamics. Int. J. Impact Eng. 167, 264–275. doi:10.1016/j.ijimpeng.2022.104275
Adam, G., Jeffrey, B., and Gregory, B. (2022b). An arbitrary Lagrange-Eulerian investigation of HRAM shallow jet pre-spurt formation and time sensitivities to impact plate dynamics. Int. J. Impact Eng. 167, 267–275. doi:10.1016/j.ijimpeng.2022.104275
Amir, R., Esmaeili, G., Meisoll, N. M., and Mohammadi, R. (2022). On the droplet impact dynamics of nonionic surfactant solutions on non-wettable coatings. J. Colloid Interface Sci. 623, 1039–1047. doi:10.1016/j.jcis.2022.05.097
Ashutosh, P., Dilip, M., and Rajeev, K. (2020). Flexural deformation behavior of carbon fiber reinforced aluminium hybrid foam sandwich structure. Compos. Part B Eng. 183, 107–729. doi:10.1016/j.compositesb.2019.107729
Bai, Z. H., He, C., and Zhu, F.(2016).Analysis of electromagnetic and impact properties of composite sandwich panels,44(9):137–143. doi:10.3969/j.issn.1000-565X.2016.09.020
Baroutaji, A., Gilchrist, M. D., Smyth, D., and Olabi, A. (2015). Analysis and optimization of sandwich tubes energy absorbers under lateral loading. Int. J. Impact Eng. 103, 74–88. doi:10.1016/j.ijimpeng.2015.01.005
Changze, S., Hamda, A., Vaibhav, A., Saleh, M. N., Cantwell, W. J., and Guan, Z. (2023). Improving the structural integrity of foam-core sandwich composites using continuous carbon fiber stitching. Compos. Struct. 324, 117509. doi:10.1016/j.compstruct.2023.117509
Chen, S., Tan, X. J., Hu, J. Q., Wang, B., Wang, L., Zou, Y., et al. (2022). Continuous carbon fiber reinforced composite negative stiffness mechanical metamaterial for recoverable energy absorption. Compos. Struct. 288, 115411–411. doi:10.1016/j.compstruct.2022.115411
Chen, Y., Lin, J., Gaber, A. M., Zuo, J., Li, J., Wang, Q., et al. (2023). “Several birds with one stone” strategy of pH/thermoresponsive flame-retardant/photothermal bactericidal oil-absorbing material for recovering complex spilled oil. J. Mater. Sci. Technol. 128, 82–97. doi:10.1016/j.jmst.2022.05.002
Cheng, H. F., and Han, F. S. (2003). Compressive behavior and energy absorbing characteristic of open cell aluminum foam filled with silicate rubber. Scr. Mater. 49, 583–586. doi:10.1016/S1359-6462(03)00332-4
Ding, L. B., Zhang, A., Peng, J. W., and Li, C. (2023). The protective performance of rubber pads for penetration fuze. Front. Mater. 10. doi:10.3389/fmats.2023.1284738
Fan, Z. H., Shen, J. H., Lu, G. X., and Ruan, D. (2013). Dynamic lateral crushing of empty and sandwich tubes. Int. J. Impact Eng. 53, 3–16. doi:10.1016/j.ijimpeng.2012.09.006
Gao, H., Xiong, C., and Ying, J. H. (2018). Experimental and ConstitutiVe model on properties of AIuminum foams dynamic CompressiVe mechanical under repeated impacts. AcTA ARMAMENTARII 39 (12), 2410–2419. doi:10.3969/j.issn.1000-1093.2018.12.015
Gao, R. J., Guo, S., Tian, X. Y., and Liu, S. (2021). A negative-stiffness based 1D metamaterial for bidirectional buffering and energy absorption with state recoverable characteristic. Thin-Walled Struct. 169, 108319–319. doi:10.1016/j.tws.2021.108319
Houcine, Z., Bennaceur, O., and Said, B. (2022). Energy absorption and damage characterization of GFRP laminated and PVC-foam sandwich composites under repeated impacts with reduced energies and quasi-static indentation. Case Stud. Constr. Mater. 58, 38–44. doi:10.1016/j.cscm.2021.e00844
Hu, M. B., Zhou, J. D., Li, Y., Zhuo, X., and Jing, D. (2021). Effects of the surface wettability of nanoparticles on the impact dynamics of droplets. Chem. Eng. Sci. 246, 116977–77. doi:10.1016/j.ces.2021.116977
Jiang, W. F., Yin, G. F., Xie, L. F., and Yin, M. (2022). Multifunctional 3D lattice metamaterials for vibration mitigation and energy absorption. Int. J. Mech. Sci. 233, 107678–78. doi:10.1016/j.ijmecsci.2022.107678
Kyle, O., Masakazu, S., and Kazuo, Y. (2022). Measurement and analysis of impact dynamics suitable for modelling pneumatic transport of metallic powder flow through a directed energy deposition nozzle. Adv. Powder Technol. 33, 500–515. doi:10.1016/j.apt.2022.103515
Li, J., and Patricia, W. (2022). Droplet impact and Leidenfrost dynamics on a heated post. Int. J. Heat Mass Transf. 201, 123581–581. doi:10.1016/j.ijheatmasstransfer.2022.123581
Li, F. Y., Ma, S. J., and Zhang, H. (2022). Simulation research on dynamic action process of continuous high impact experimental equipment. Nanjing Univ. Sci. Technol. 43 (1), 255–259. doi:10.11809/bqzbgcxb2022.01.040
Li, J., and Wang, Y. X. (2021). Numerical study on surface-heterogeneity-induced anisotropic impact dynamics of droplet. Colloid Interface Sci. Commun. 44, 74–95. doi:10.1016/j.colcom.2021.100495
Li, J. J., Tian, C. Y., Hong, W. J., Duan, S., Zhang, Y., Wu, W., et al. (2021). Shock responses of nanoporous gold subjected to dynamic loadings: energy absorption. Int. J. Mech. Sci. 192, 106191–106271. doi:10.1016/j.ijmecsci.2020.106191
Li, Z. R., Chen, H., et al. (2020). Application of epoxy resin encapsulating technology in protection of high overload products. Electron. Process Technol. 41 (4), 222–225. doi:10.14176/j.issn.1001-3474.2020.04.011
Lin, K. X., Tan, Y. K., Chen, H. G., Tao, X., Ouyang, Y., and Du, Y. (2023). Phononic characteristics to determine absorbing shock-wave energy for low-dimensional materials. Carbon 203, 410–415. doi:10.1016/j.carbon.2022.12.006
Liu, H., Cao, Z. K., Luo, H. J., Shi, J., and Yao, G. (2013). Performance of closed-cell aluminum foams subjected to impact loading. Mater. Sci. Eng. 570, 27–31. doi:10.1016/j.msea.2012.11.094
Liu, L. H., Zhang, Y. C., and Cai, G. B. (2022). Peichun Amy Tsai,High-speed dynamics and temperature variation during drop impact on a heated surface. Int. J. Heat Mass Transf. 189, 7–13. doi:10.1016/j.ijheatmasstransfer.2022.122710
Lu, J. Y., Wang, Y. H., Zhai, X. M., Zhi, X., and Zhou, H. (2021). Impact behavior of a cladding sandwich panel with aluminum foam-filled tubular cores. Thin-Walled Struct. 169, 108459–108545. doi:10.1016/j.tws.2021.108459
Lu, X., Chen, Y. B., Yang, Y. J., Wu, T., Xia, H., et al. (2023). Incorporation of FexOy nanoparticles into 3D interlinked porous carbon nanofiber networks to synergistically enhance the electrical insulation, electromagnetic wave absorbing/shielding performance and thermal conductivity. Chem. Eng. J. 469, 143952. doi:10.1016/j.cej.2023.143952
Luo, H. T., Li, Y. X., Wu, X., Liu, G., et al. (2021). Design and experimental research on buffer protection of high-g penetrator for deep space exploration. Acta Astronaut. 189, 63–78. doi:10.1016/j.actaastro.2021.08.020
Ma, H. Y., Wang, K., Zhao, H. F., Shi, W., Xue, J., Zhou, Y., et al. (2022). Energy dissipation and shock isolation using novel metamaterials. Int. J. Mech. Sci. 228, 107464–464. doi:10.1016/j.ijmecsci.2022.107464
Man, X. F., Ma, S. J., and Zhang, H. (2014). Study of physical simulation experiment of penetration fuze layer-count burst point control. Acta Armamentarii 35 (10), 1556–1561. doi:10.3969/j.issn.1000-1093.2014.10.006
Michailidis, N., Stergioudi, F., and Tsouknidas, A. (2011). Deformation and energy absorption properties of powder-metallurgy produced Al foams. Mater. Sci. Eng. 528, 7222–7227. doi:10.1016/j.msea.2011.05.031
Michał, R., Jakub, G., and Katarzyna, G. (2022). Crashworthiness analysis of thin-walled aluminum columns filled with aluminum-silicon carbide composite foam. Compos. Struct. 299, 116–102. doi:10.1016/j.compstruct.2022.116102
Mohammad, R. T., and Bidhendi, K. B. (2022). High-velocity transverse impact of monolayer graphene oxide by a molecular dynamics study. Comput. Mater. Sci. 216, 111881–881. doi:10.1016/j.commatsci.2022.111881
Natticha, S., Natthaphat, S. A., and Sirinart, K. (2020). The effects of iron overload on mitochondrial function, mitochondrial dynamics, and ferroptosis in cardiomyocytes. Archives Biochem. Biophysics 680, 235–241. doi:10.1016/j.abb.2019.108241
Neslihan, H., and Gaye, K. (2022). Experimental investigation on impact response of sandwich composites integrated with a novel 3D multi-layer stitched core. Compos. Struct. 296, 58–68. doi:10.1016/j.compstruct.2022.115888
Ngoc, S. H., and Lu, G. X. (2019). A review of recent research on bio-inspired structures and materials for energy absorption applications. Compos. Part B Eng. doi:10.1016/j.compositesb.2019.107496
Rothacher, T., and Giger, B. (1999). High g ballistic flight data recoder. 18th Int. Symposium Ballist.
Selivanov, V. V., Silnikov, M. V., Markov, V. A., Popov, Y., and Pusev, V. (2021). Using highly porous aluminum alloys and honeycomb structures in spacecraft landing gear. Acta Astronaut. 180, 105–109. doi:10.1016/j.actaastro.2020.12.014
Shen, J. S., Lu, G. X., Zhao, L. M., and Zhang, Q. M. (2011). Short sandwich tubes subjected to internal explosive loading. Eng. Struct. 55, 56–65. doi:10.1016/j.engstruct.2011.12.005
Simoes, M., Harris, J. A., Ghouse, S., Hooper, P., and McShane, G. (2022). Process parameter sensitivity of the energy absorbing properties of additively manufactured metallic cellular materials. Mater. Des. 224, 111398. doi:10.1016/j.matdes.2022.111398
Sun, G. Y., Zhang, J. T., Shiqiang Li, S. Q., Fang, J., Wang, E., and Li, Q. (2019). Dynamic response of sandwich panel with hierarchical honeycomb cores subject to blast loading. Thin-Walled Struct. 142, 499–515. doi:10.1016/j.tws.2019.04.029
Sun, X., Liu, X., Wang, J., Jiang, X., Liu, R., et al. (2020). Nanobundles structural Co-HKUST on the foamed nickel with a high supercapacitor performance. Appl. Sci. 2, 414–510. doi:10.1007/s42452-020-2205-6
Taherishargh, M., Belova, I. V., Murch, G. E., and Fiedler, T. (2014). Low-density expanded perlite–aluminium syntactic foam. Mater. Sci. Eng. 604, 127–134. doi:10.1016/j.msea.2014.03.003
Talebi, S., Sadighi, M., and Aghdam, M. M. (2019). Numerical and experimental analysis of the closed-cell aluminium foam under low velocity impact using computerized tomography technique. Acta Mech. Sin. 35, 144–155. doi:10.1007/s10409-018-0795-7
Ulbin, M., Vesenjak, M., Borovinšek, M., Duarte, I., Higa, Y., Shimojima, K., et al. (2018a). Detailed analysis of closed-cell aluminum alloy foam internal structure changes during compressive deformation. Adv. Eng. Mater. 20, 158–164. doi:10.1002/adem.201800164
Ulbin, M., Vesenjak, M., Borovinšek, M., Duarte, I., Higa, Y., Shimojima, K., et al. (2018b). Detailed analysis of closed-cell aluminum alloy foam internal structure changes during compressive deformation. Adv. Eng. Mater. 20, 164–180. doi:10.1002/adem.201800164
Wang, J., Wang, N., Liu, X., Ding, J., Xia, X., Chen, X., et al. (2018). Compressive deformation behavior of closed-cell micro-pore magnesium composite foam. Materials 11, 731–741. doi:10.3390/ma11050731
Wang, X. Y., Liang, Y., Wei, S. C., Wang, Y., Yuan, Y., Li, L., et al. (2022). Preparation and absorbing property analysis of ZnO-doped magnetic graphene composite material. J. Magnetism Magnetic Mater. 556, 169450. doi:10.1016/j.jmmm.2022.169450
Wei, X. J., Zhang, J. W., and He, X. H. (2022). Dynamic properties of impact hammer operator and their influence on dynamics of lightweight structures. J. Sound Vib. 529, 19–32. doi:10.1016/j.jsv.2022.116932
Xiang, X. M., Fu, Z. S., Zhang, S. L., Lu, G., Liang, Y., et al. (2021). The mechanical characteristics of graded Miura-ori metamaterials. Mater. Des. 211, 110173. doi:10.1016/j.matdes.2021.110173
Xiang, X. M., Shao, D. H., Pang, T., Ngo, T. T., and Zhang, S. (2022). Energy absorption of multilayer aluminum foam-filled structures under lateral compression loading. Mech. Adv. Mater. Struct. 31, 659–675. doi:10.1080/15376494.2022.2118405
Xiang, X. M., Zou, S. M., Ngoc, S. H., Lu, G., and Kong, I. (2020). Energy absorption of bio-inspired multi-layered graded foam-filled structures under axial crushing. Compos. Part B Eng. 198, 108216. doi:10.1016/j.compositesb.2020.108216
Xu, C. P., Huang, H. D., et al. (2010). The foamed aluminium gasket in hypersonic penetrating fuze. J. Detection&Control 32 (6), 63–67. doi:10.3969/j.issn.1008-1194.2010.06.016
Yang, B. Q., Dai, K. R., Yu, D., Zhang, A., Cheng, J., et al. (2024). Lightweight recoverable mechanical metamaterials for efficient buffering of continuous multi extreme impacts. Sustain. Mater. Technol. 39, e00839. doi:10.1016/j.susmat.2024.e00839
Yu, D., Dai, K., Zhang, J., Yang, B., Zhang, H., and Ma, S. (2020). Failure mechanism of multilayer ceramic capacitors under transient high impact. Appl. Sci. 10, 8435–35. doi:10.3390/app10238435
Zhang, H. (2018). Development 0f AmmuIlition for the demand and PrOmotiOn of fuze technology. J. Ordnance Equip. Eng. 39, 1–5. doi:10.11809/bqzbgcxb2018.03.001
Zhang, J. M., Zhang, H., and Dai, K. R. (2022b). Preparation of elastic porous composite material and its energy-absorption characteristics. ACTA ARMAMENTARII 43, 159–168. doi:10.3969/j.issn.1000-1093.2022.01.017
Zhang, J. M., Zhang, H., et al. (2022a). Preparation of elastic porous composite material and its energy-absorption characteristics. ACTA ARMAMENTARII. doi:10.3969/j.issn.1000-1093.2022.01.017
Zhang, Z. H., and Jin, X. (2022). Study on the energy dissipation mechanism of the pyramidal lattice sandwich panel subjected to underwater explosion. Mar. Struct. 110, 103243–104113. doi:10.1016/j.marstruc.2022.103243
Zhao, W., Yue, C. B., Liu, L. W., Leng, J., and Liu, Y. (2022). Mechanical behavior analyses of 4D printed metamaterials structures with excellent energy absorption ability. Compos. Struct. 116, 116360–116366. doi:10.1016/j.compstruct.2022.116360
Keywords: high overload, buffering, penetration, fuze, hard targets, energy absorption, protection, weaponry
Citation: Zhang A, Liu P and Zhang H (2024) Advancements in research on high-overload impact-buffering protective materials. Front. Mech. Eng 10:1284758. doi: 10.3389/fmech.2024.1284758
Received: 29 August 2023; Accepted: 20 June 2024;
Published: 12 July 2024.
Edited by:
Zhangxian Yuan, Worcester Polytechnic Institute, United StatesReviewed by:
Ngoc San Ha, RMIT University, AustraliaCopyright © 2024 Zhang, Liu and Zhang. This is an open-access article distributed under the terms of the Creative Commons Attribution License (CC BY). The use, distribution or reproduction in other forums is permitted, provided the original author(s) and the copyright owner(s) are credited and that the original publication in this journal is cited, in accordance with accepted academic practice. No use, distribution or reproduction is permitted which does not comply with these terms.
*Correspondence: Peng Liu, bmp1c3RjYUBuanVzdC5lZHUuY24=
Disclaimer: All claims expressed in this article are solely those of the authors and do not necessarily represent those of their affiliated organizations, or those of the publisher, the editors and the reviewers. Any product that may be evaluated in this article or claim that may be made by its manufacturer is not guaranteed or endorsed by the publisher.
Research integrity at Frontiers
Learn more about the work of our research integrity team to safeguard the quality of each article we publish.