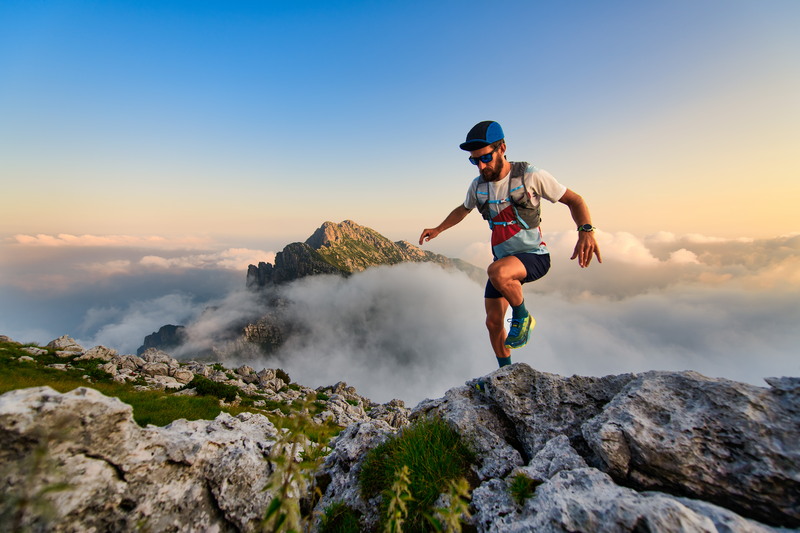
95% of researchers rate our articles as excellent or good
Learn more about the work of our research integrity team to safeguard the quality of each article we publish.
Find out more
ORIGINAL RESEARCH article
Front. Mater. , 23 February 2023
Sec. Structural Materials
Volume 10 - 2023 | https://doi.org/10.3389/fmats.2023.1148589
This article is part of the Research Topic Sustainable Fiber Reinforced Cementitious Composites for Construction and Building Materials View all 14 articles
A correction has been applied to this article in:
Corrigendum: Influence of ternary hybrid fibers on the mechanical properties of ultrahigh-strength concrete
Ultra-high performance concrete (UHPC), an advanced class of fiber-reinforced cementitious material with extraordinary mechanical properties, low permeability, shrinkage and creep, and high energy absorption capacity, has seen steady increase in use, with applications covering construction of new members and retrofit of existing ones. Fibers are added in the UHPC mix to bridge cracks, carry tensile stresses, and contribute greatly to member ductility and load capacity. Hybrid fibers comprising micro and macro types are beneficial where the first type resists microcracking and the second targets macrocracking. This study investigates the effects of blending three fiber types, namely, hooked-end steel (referred to as type 1, representing macro fibers class), straight-end steel (type 2, intermediate size fibers), and carbon (type 2, micro size fiber), on the mechanical properties of UHPC. Experimental tests were performed to characterize the following mechanical properties: flowability, compressive strength, tensile strength, flexural strength, modulus of elasticity, and dry shrinkage. The primary variable in the tests was the blending of different fiber types, using either a unary form of type 1, a binary form of type 1 and 3 or type 2 and 3, and a ternary mix of all three types, at 1.56% dosage by volume. The mix with ternary fibers yielded a compressive strength, tensile strength, flexural strength, and modulus of elasticity that is 14%–17%, 14%–16.8%, 43.66%–22.16%, and 12%–16%, larger than the same respective properties of the mix with unary fibers. In addition, ternary fibers increased the cohesiveness of the mix by 17% and 26% compared to unary fibers.
Ultra-high performance concrete (UHPC), also known as reactive powder concrete (RPC) and ultra-high performance fiber-reinforced concrete (UHPFRC) (Ter Maten, 2011; Qaidi et al., 2022a; Tayeh et al., 2022c), is an advanced class of fiber-reinforced cementitious material obtained through the removal of coarse aggregate, optimization of particle gradation, use of admixtures and microfibers (Ter Maten, 2011; Saeed et al., 2022; Zeybek et al., 2022). It consists of fine powders such as cement, quartz, fine sand, and mineral additives such as fly ash, silica fume, and ground granulated blast-furnace slag, used due to their pozzolanic properties and filling capacity (Shakor et al., 2019a; Puzatova et al., 2022; Vinod et al., 2022). With a low w/c ratio [typically less than 0.25 (Graybeal, 2014; Sanjuán and Andrade, 2021)], superplasticizers are also used to ensure good flow, consolidation, and workability of UHPC (Caluk et al., 2019; Tayeh et al., 2022a; Qaidi et al., 2022f). Discontinuous fiber reinforcement, typically made from steel with diameters of 0.5 mm, lengths of 12.5 mm, and dosage of 2%–4% by volume, are incorporated in UHPC mix to provide bond at the micro level and minimize micro-cracking (Harris and Roberts-Wollmann, 2005). The mechanical properties of UHPC include a compressive strength (fc′) of more than 150 MPa, and tensile strength exceeding 5 MPa with a strain-hardening response resembling metallic ductility. UHPC has low permeability, shrinkage, and creep; good durability, and high energy absorption capacity.
While the high initial cost prohibits its application in mass construction, UHPC has been used mainly in applications that maximize its attributes, including in members subjected to harsh environments, as a repair overlay for bridge decks and corroded steel girders ends; in construction of link slabs, hybrid members containing UHPC in highly stressed regions such as beam mid-spans and column plastic hinges; and as grout material for joints between adjacent precast girders or between a precast slab and steel girder (Grünewald, 2004; Qaidi et al., 2022f; He et al., 2022). Non-etheless, with the development of open-source mixes which help to reduce the unit price, establishment of design codes and guidelines, abundance of research studies and filed applications, and presence of educational programs introducing various design and construction aspects to professional engineers and contractors, UHPC is becoming increasingly used in the construction of full members such as beams (Standard, 2017; Qaidi S. M. et al., 2022; Tayeh et al., 2022d; Qaidi et al., 2022f), thin shells (Ter Maten, 2011; Shakor et al., 2019b), concrete sandwich panels (Qaidi et al., 2022c), marine structures, piers, and sewage treatment units (Tayeh et al., 2022b; Qaidi et al., 2022c; Qaidi et al., 2022d; Qaidi et al., 2022e; Faraj et al., 2022; He et al., 2022).
Fibers have a crucial role within UHPC, mainly acting as stitches, bridging cracks and transferring load across their faces, thus increasing the member’s ductility and load capacity (Emad et al., 2022; Faraj et al., 2022). Some of UHPC mechanical properties, particularly the post-cracking tensile stress-strain response, are dependent on fiber properties such as type, content, aspect ratio (length/diameter), combined stiffness (for fiber cocktail), and method of placement during casting (Ter Maten, 2011; Qaidi et al., 2021a; Almeshal et al., 2022). Multiple studies investigated key parameters related to the use of single-type fibers in UHPC. For example, Biolzi et al. (1997) studied the effects of three contents for steel fibers, namely: 2%, 4%, and 6% by volume, on UHPC’s compressive strength, direct tensile strength, and elastic modulus. Gao (2007) compared the dynamic load performance of plain and fiber-reinforced UHPC (Ali et al., 2022a; Ali et al., 2022b).
While single-type fibers are predominantly used, multiple studies have found that using a mixture of fiber lengths and types, results in better ductility and strength. Fiber cocktails enable better-cracking resistance where short fibers act to bridge microcracks while long ones restrain macrocracks. Different fiber types have been found to result in different attributes, namely, a) steel fibers to increase fracture energy and strength, b) Polypropylene (PP) fibers to increase fire resistance and reduce spalling and early shrinkage, and c) glass fibers to reduce internal stresses in fresh UPHC. The study by Rossi et al. (1987) was one of the first to propose the mix of multi-type fibers with the product dubbed multi-modal fiber-reinforced concrete. Few studies investigated the effects of blending multi-type fibers in UHPC. Raza et al. (2021) examined three types of single fiber-reinforced UHPC, namely: steel fiber (SF), glass fiber (GF), and carbon fiber (CF), and three blended fiber mixes, namely: SF-GF, GF-CF, and CFSF. A constant volume fraction of 2% was used for all fiber combinations. The study concluded that using a hybrid mix of 1% SF and 1% CF yielded the maximum overall mechanical performance among all combinations. Shaheen and Shrive (2006) compared CF- and SF-reinforced UHPC and found the former to result in significantly higher fracture toughness, and compressive and splitting tensile strength than the latter (Cao et al., 2018b; Khan et al., 2018; Ahmad et al., 2020).
Despite the limited studies, there is a need to examine further the effects of multi-type and blended fibers on the behavior of UHPC (Cao et al., 2018a; Khan et al., 2021; Khan et al., 2022). This study aims to examine whether higher mechanical and durability properties in UHPC can be obtained if a blend of multiple fiber types representing a range of micro and macro types with different dimensions, end conditions, and textures are used instead of single fiber type. Three types of fibers were used in the study: hooked-end steel fibers as macro class, straight-end steel fibers as intermediate class, and carbon fibers as micro reinforcement. Experimental tests were performed to characterize the common mechanical properties: flowability, compressive strength, tensile strength, flexural strength, modulus of elasticity, and dry shrinkage.
To understand the effects of blended micro and macro fiber bundles on the behavior of UHPC, five mixes were chosen and tested comprising diverse types of fibers (carbon fibers and straight steel fibers as microfiber and steel fiber with hooked-ends as macro fiber) (Figure 1) in its single and hybrid states with different volumetric percentages (Vf). The properties of the fibers used are presented in Table 1. They include a) hooked-end steel fibers (after this referred to as type 1) with a length (L) and diameter (D) of 50 and 0.75 mm, respectively, representing the macro reinforcement; b) straight-end steel fibers (after this referred to as type 2) with L and D of 15 and 0.2 mm, respectively, as an intermediate size micro reinforcement; and carbon fibers (after this referred to as type 3) with L and D of 8 and 0.007 mm, as a smaller size micro reinforcement. The volume fraction of steel fibers used in this study was 1.33% depending on the published earlier study (Ahmed and Abd, 2018; Al-Tayeb et al., 2022; Akeed et al., 2022c; Emad et al., 2022; Faraj et al., 2022), while the carbon fiber ratio chosen was based on a general review of the literature.
FIGURE 1. (A) Steel fibers with hooked ends, (B) steel fibers with straight ends, and (C) carbon fibers.
The UHPC was produced using exceptionally fine materials including ordinary Portland cement (type I), river silica sand, and silica fume, in addition to the use of a chemical additive superplasticizer (Gleinum 51) to reduce the w/c ratio to 20%. All the properties of the materials used are shown in Table 2, the sieve analysis of silica sand is shown in Table 3, and the details of the proportions of the mixture materials are shown in Table 4. Mixes 1 and 2 contain 1.33% of uni-type fibers, the former with type 1 and the latter with type 2, Table 4. Mix 3 contains a blend, of 1.33% of type 1% and 0.2% of type 3 fibers. Mix 4 features 1.33% of type 2 fibers and 0.2% of type 3, while mix 5 has a combination of 0.66% of type 1, 0.66% of type 2, and 0.2% of type 3 fibers. The effects of the hybrid fibers were characterized through material tests on several mechanical properties: compressive strength, tensile strength, flexural strength, and modulus of elasticity. Table 5 summarizes the various characterization tests performed on the mixes, showing the specimen configuration and dimensions for each test, along with the standard followed in each test.
To ensure that the fine particles overlap with each other and blend properly, the dry materials (cement, silica sand, and silica fume) were mixed for 3 min in a small rotary mixer. The superplasticizer was then diluted with the required water quantity and the final solution was added to the dry ingredients, where mixing was then continued for additional 2 min to obtain a homogeneous mixture. Finally, the fibers were distributed uniformly and gradually to prevent them from balling and agglomeration, while maintaining a uniform distribution over the mixture during the mixing period.
Before pouring the UHPC mix, the molds for material tests (i.e., cylinders, cubes, and prisms) were prepared by coating their inner surfaces with a thin layer of oil to facilitate specimen removal after the concrete hardens. The specimens were lightly tapped by a metal rod to reduce air voids and ensure good compaction. Figure 2 shows a representative sample of the freshly cast specimens in molds. The specimens were levelled using a trowel and then left to cure for 24 h. They were removed from the models and placed in a curing basin filled with water (Figure 3) until the required tests were performed at 7 and 28 days. A total of 90 specimens with different shapes (i.e., cubes, cylinders, and prisms) were prepared and tested for the 5 mixes in Table 4, at the ages of 7 and 28 days.
A flow test, following ASTM C-1437 (ASTM, 2007) standards, was conducted (Figure 4) to measure the workability of the five UHPC mixes used in the study. The flow is defined as the average increase in the base diameter, measured at least in four different diameters at approximately equidistant intervals, and is expressed as a percentage of the original base diameter.
Where:
Compression tests were conducted according to BS 1881 (BS, 1989) on cubes with a side length of 100 mm using a hydraulic testing machine with a capacity of 2,000 kN, at a loading rate of 0.25 ± 0.05 MPa per second, as shown in Figure 5.
Splitting tensile tests were performed according to ASTM C496 (Standard, 2017), on cylinders with diameters (D) and lengths (L) of 150 and 300 mm, respectively. Figure 6 shows a cylinder undergoing testing by a universal testing machine with a capacity of 2,000 kN. The splitting tensile strength was calculated using the following formula:
Where:
fsp: Splitting tensile strength (MPa).
P: Applied load in (N).
D: Cylinder diameter (mm).
L: Cylinder length (mm).
To characterize the UHPC modulus of rupture (fr), prisms with dimensions of 100 mm × 100 mm × 500 mm were prepared according to ASTM C78-22 specification (ASTM, 2010) and tested under two-point loading with a clear span of 450 mm, Figure 7. The following equation is used to determine fr:
Where:
P = maximum applied load in N, L = prism span (450 mm), b = prism width (100 mm), and h: prism depth (100 mm).
The modulus of elasticity (Ec) is a major parameter affecting the design and analysis of a UHPC member and is typically related to the square root of the compressive strength (fc′) in an empirical relation (Russell et al., 2013). Ec of the examined mixes was characterized experimentally by testing three 150 mm × 300 mm cylinders per mix, each instrumented with 2 strain gages placed within the middle third length of the cylinder in the axial direction (Figure 8). Averaging the two gage readings from all three cylinder tests, Ec for each mix was found using the following equation adopted from the ASTM C469/C479M-14 (ASTM, 2002) standards:
Where:
Prismatic 40 mm × 40 mm × 160 mm specimens were used to measure the length change of the concrete sample due to the effects of drying shrinkage, following specifications of ASTM C157/C157M-14 (Standard, 2014). For each mix, two specimens were tested under room temperature conditions, taking the average of the two as the mix drying shrinkage. A comparator length tool (Figure 9) was used to measure the change in length with time, while the following equation was utilized to determine the shrinkage at any age:
Where:
ΔLx = Length change at any age.
CRD = Difference between comparator reading and reference bar at any age.
G = Specimen length.
This section discusses the results of the various material tests conducted to characterize the effects of hybrid fibers on the mechanical performance of UHPC. The results are divided into six sections, each discussing the results of one of the material characterization tests addressed in Section 3.
The results of the flow table test are presented in Table 6 and Figure 10. The results show a decrease in the flow ability of the UHPC mix, as the fiber percentage increases from 1.33% to 1.53% (15% increase). Previous studies (Boulekbache et al., 2010; Sahoo et al., 2019; Akeed et al., 2022a) have shown that the reduction in flowability associated with the use of fiber reinforcements can be attributed to: 1) the large length and surface area of the fibers compared to the aggregates causing an increase in the cohesive forces between the two constituents; 2) fibers effects on altering the granular skeleton structure of the mix and hindering its flow; 3) fiber reinforcements tend to flow perpendicular to the paste; thus they generate resisting forces and moments to the flow velocity of the fresh mixture (Ahmed H. U. et al., 2022; Abd et al., 2022; Akeed et al., 2022b; Abd et al., 2023).
Figure 11 and Table 7 present the results of the compressive strength (fc′) of UHPC for the five different mixes with various fiber blends, at three ages, 7, 28, and 56 days. Comparing mixes 1 and 2, both with 1.33% single-type fibers but featuring type 1 for the former and type 2 for the latter, fc′ seems invariable for all ages (Ali et al., 2022a; El Ouni et al., 2022; Raza et al., 2022). Using a blend of two types of fibers as the case in mixes 3 and 4 seems to result in a negligible increase in fc’ at 7 and 56 days but a noticeable 11.5% increase at 28 days, on average, when compared to fc′ of mixes 1 and 2. On the other hand, the triple fiber type (mix 5) with fiber composition of 0.66% type 1, 0.66% type 2, and 0.2% type 3 results in a 5%–15% increase in fc’ compared to that of the single fiber type mixes (mixes 1 and 2), and 2%–6% compared to the double fiber type mixes (mixes 3 and 4). Incorporating hybrid fibers into the mix optimizes the benefits of each fiber type due to the different material properties for each type as well as different lengths. With microfibers bridging microcracks and macro ones targeting macrocracks, cracks with different sizes can be controlled, eventually improving compressive strength (Aisheh et al., 2022; Ahmed S. N. et al., 2022).
All mixes accrue an increase in fc′ with age, sharply during the first 7 days from casting and at a much slower rate afterwards. Aside from the similarity in trend with conventional concrete and natural hydration process, the presence of parts unique to UHPC, such as superplasticizers and silica fume, also contribute to compressive strength growth with time. For example, silica fume is known to react chemically with calcium hydroxide, thus increasing the strength and reducing the voids inside the concrete (Sahoo et al., 2019; Ahmed et al., 2021; Akeed et al., 2022d; Akeed et al., 2022e).
Although the tensile strength (ft) of UHPC is higher than that of conventional concrete, it is subpar to the compressive strength. Thus, tensile splitting tests were also performed to examine the effects of hybrid fiber types in improving the tensile strength of UHPC. Table 8 and Figure 12 present the ft values for the five different mixes at the ages of 7 and 28 days. ft of mix 2 was 50%–54% larger than that of mix 1, likely because of the larger tensile strength of the straight steel fibers (type 2) compared to the hooked-end ones (type 1). Both mix 1 and 2 contain single-type fibers. Mix 3 with 1.33% type 1 fibers and 0.2% type 3 (total fiver volume = 1.53%) had a 22%–36% larger ft than mix 1 with 1.33% type 1 fibers. Despite having 13% fewer fibers, mix 2 (with single-type 2 fibers) had ft 11%–26% larger than that mix 3. Comparing mix 4 and 2, both containing type 2 fibers but a small 0.2% of carbon fibers (type 3) is added to the former, mix 4 had 11% larger ft. Of the five proportions, mix 5 features the largest ft, 16.7 MPa at 7 days and 21 MPa at 28 days. This was a 100% increase over mix 1, 32%–35% over mix 2, 50%–67% over mix 3, and 19%–22% over mix 4. In all mixes, ft increased with age resonating with the trend observed for the tests on compressive strength.
Table 9 and Figure 13 present the results of the effect of using hybrid fibers on the flexural strength (fb) of UHPC, at the ages of 7 and 28 days. It can be seen that blending carbon fibers (type 3) with hooked-end steel fibers (type 1) as in mix 3 or straight-end steel fibers (type 2) as in mix 4 results in an increase in fb by about 12.67% and 10.78%, respectively, compared to mix 1 and 2 with single-type fibers. Using the three-type fiber blend resulted in the largest fb, 20.5 MPa at 28 days. This improvement is due to the increase in the bonding strength between the fibers and the concrete mixture, and thus an increase in the material’s ductility. Furthermore, due to the presence of fibers in the mix, higher energy input is required to extend the crack further, and the crack-tip region will be restrained, which can be attributed to the closing pressure on crack surfaces induced by the bridging fibers (Ter Maten, 2011).
Table 10 and Figure 14 present the results of the UHPC elastic modulus (E) for the five mixes, at two ages 7 and 28 days. The results show the hybrid fibres’ clear role in increasing the mix’s stiffness. When carbon fibers were used with hooked-end steel fibers (mix 3), E increased by about 7.18% compared to mix 1 (type 1 fibers only) and 5.7% compared to mix 2 (type 1 fibers only). Mix 5 (with a blend of all three fiber types) resulted in the highest E 49.63 MPa, at 28 days of age. E of concrete is directly affected by the compressive strength of concrete (Tomosawa et al., 1990) where fibers have an essential role in reducing the concrete cracking strains due to the crack bridging effects, and ultimately increasing the stiffness.
The results of the drying shrinkage test for the five mixes versus age in days are presented in Figure 15. The shrinkage was measured at five ages, namely, 3, 7, 28, 56, and 90 days. In line with other mechanical tests, Figure 15 confirms the advantages of hybrid fibers where mix 5 (with triple fiber type) yielded the smallest values for dry shrinkage.
The functions of the fibers in cement-based composites can be classified into two categories: shrinkage crack control and mechanical property enhancement. For shrinkage crack control, generally lesser amounts of low-modulus and low-strength fibers are added to restrain the early-age shrinkage and suppress shrinkage cracking. Short straight steel fibers can serve as bridging mechanisms during cracking. Therefore, the use of short steel fibers, especially those with a high aspect ratio, is beneficial in that case.
In conventional applications of fiber cementitious composites, the fibers’ function becomes visible after a major crack has formed in the composite (Shah, 1990). At this stage, there are one or few major cracks and the overall composite behaviour is characterized by strain softening after the peak load is reached. The incorporation of fibers significantly increases the total energy consumption and overall toughness of the composite. In such cases, and where fiber rupture does not govern, the gradual fiber debonding and pullout failures can consume a great amount of energy. On the other hand, with an increase in fiber volume fraction, microcracks formed in the matrix may be stabilized due to the interaction between the matrix and fibers through bonding, hence postponing the formation of the first major crack in the matrix. Thus, the apparent tensile strength of the matrix can be increased (Shah, 1990). Moreover, when a sufficient volume fraction of small-diameter steel, glass, or synthetic fibers is incorporated into the cement-based matrix, the fiber/matrix interaction can lead to strain hardening and multiple cracking behaviours, changing the failure mode from quasi-brittle to ductile.
As a result, the composite’s toughness and matrix tensile strength can be significantly improved. One of the mechanisms for slowing the growth of a transverse crack in unidirectional fiber composites can be attributed to the development of longitudinal cylindrical shear microcracks located at the boundary between the fiber and the bulk matrix, which allows the fibers to deboned while transferring the force across the faces of the main crack. In addition to enhancing the toughness and tensile strength, the addition of fibers can also improve the bending resistance of cement-based composites. However, adding fibers has only a minor influence on the compressive strength of cement-based composites. At a small fiber volume fraction, there is almost no effect. Hence, it is not worthwhile to incorporate fibers to enhance compressive strength. The enhancing order of fibers on the mechanical properties of cement-based composites is toughness, followed by flexural strength, tensile strength, and compressive strength (Shah, 1990).
Microfibers are efficient in restraining microcracks and macro fibers in restraining macroscopic cracks. From the materials point of view, the fibers that are commonly used in fiber-reinforced cement-based composites are carbon, glass, polymeric (e.g., acrylic, aramid, nylon, polyester, polyethylene), natural (e.g., wood cellulose, sisal, coir), and steel (high tensile and stainless). Several types of fibers have different values of young’s modulus, tensile strength, surface textures, and elongation abilities. These properties affect the bond between the fibers and the matrix, the ability to bridge cracks, the improvement of matrix properties, and, by extension, how fiber-reinforced cement-based composites behave.
This study conducted tests on 90 small-scale specimens with different shapes and functions to characterize the effects of blended micro- and macro-size fibers on the mechanical properties of ultra-high performance concrete (UHPC). The fibers studied were hooked-end steel (referred to as type 1, representing macro class), straight-end steel (type 2, intermediate size), and carbon (type 2, micro size). Five mixes were cast and differing by the type and blend of fibers, namely, a) with type 1 unary fibers, b) with type 2 unary fibers, c) with type 1 and 3 binary fiber blend, d) with type 2 and 3 binary fiber blend, and e) with all three fibers. A fiber dosage of 1.56% by volume was used for blended fiber mixes. The characterization tests were performed on the following mechanical properties: flowability, compressive strength, tensile strength, flexural strength, modulus of elasticity, and dry shrinkage. Based on the results, the following conclusions were made:
1. Using ternary fiber cocktail instead of unary type 1 fibers resulted in a 20% decrease in the flowability of the UHPC mix.
2. The compressive strength (fc′), at ages of 7 and 28 days, does not seem to vary for mixes with unary fibers (type 1 or type 2). fc′ for the mixes with a blend of two types of fibers (type 1 and 3 or type 2 and 3) was slightly larger than that of the unary-fiber mixes at ages of 7 and 56 days, but 11.5% larger at 28 days. The ternary-fiber mix resulted in fc′ of 5%–15% and 2%–6% more than that of the unary-fiber and binary-fiber mixes, respectively.
3. The ternary fiber cocktail improved the UHPC tensile strength by 14% and 16.8%, compared to the mixes featuring unary and binary fibers. This is because of the multiple roles of different fiber classes in bridging various crack sizes.
4. The ternary fiber cocktail resulted in 22.16%–43.66% increase in flexural strength (an indicator of higher ductility) compared to the mixes featuring unary fibers.
5. The modulus of elasticity was increased by 12%–14% when ternary fiber cocktail was used in lieu of unary type 1 fibers.
6. The triple-fiber cocktail also resulted in smaller drying shrinkage than the other fiber blends. It is hypothesized that lesser amounts of low-modulus and low-strength fibers results in better restraint of the early-age shrinkage and shrinkage cracking.
The original contributions presented in the study are included in the article/Supplementary Material, further inquiries can be directed to the corresponding author.
Conception and design of the study: SA, RH, AJ, HN, SM, MB, and MS; acquisition of data: SA, RH, AJ, and HN; analysis and/or interpretation of data: SM, MB, and MS; drafting the manuscript: SA, RH, AJ, HN, SM, MB, and MS; revising the manuscript critically for important intellectual content: SA, RH, AJ, HN, SM, MB, and MS; and approval of the version of the manuscript to be published: SA, RH, AJ, HN, SM, MB, and MS.
This research was funded by the Ministry of Science and Higher Education of the Russian Federation within the framework of the state assignment No. 075-03-2022-010 dated 14 January 2022 and No. 075-01568-23-04 dated 28 March 2023 (Additional agreement 075-03-2022-010/10 dated 09 November 2022, Additional agreement 075-03-2023-004/4 dated 22 May 2023), FSEG-2022-0010.
The authors declare that the research was conducted in the absence of any commercial or financial relationships that could be construed as a potential conflict of interest.
All claims expressed in this article are solely those of the authors and do not necessarily represent those of their affiliated organizations, or those of the publisher, the editors and the reviewers. Any product that may be evaluated in this article, or claim that may be made by its manufacturer, is not guaranteed or endorsed by the publisher.
Abd, S. M., Mhaimeed, I. S., Tayeh, B. A., Najm, H. M., and Qaidi, S. (2022). Flamingo technique as an innovative method to improve the shear capacity of reinforced concrete beam. Case Stud. Constr. Mater. 17, e01618. doi:10.1016/j.cscm.2022.e01618
Abd, S. M., Mhaimeed, I. S., Tayeh, B. A., Najm, H. M., and Qaidi, S. (2023). Investigation of the use of textile carbon yarns as sustainable shear reinforcement in concrete beams. Case Stud. Constr. Mater. 18, e01765. doi:10.1016/j.cscm.2022.e01765
Ahmad, W., Farooq, S. H., Usman, M., Khan, M., Ahmad, A., Aslam, F., et al. (2020). Effect of coconut fiber length and content on properties of high strength concrete. Materials 13, 1075. doi:10.3390/ma13051075
Ahmed, B. K., and Abd, S. M. (2018). Eliminating the shrinkage of high strength concrete by using super absorbent polymer (SAP). Diyala J. Eng. Sci. 11, 8–13. doi:10.24237/djes.2018.11402
Ahmed, H. U., Mohammed, A. A., Rafiq, S., Mohammed, A. S., Mosavi, A., Sor, N. H., et al. (2021). Compressive strength of sustainable geopolymer concrete composites: A state-of-the-art review. Sustainability 13, 13502. doi:10.3390/su132413502
Ahmed, H. U., Mohammed, A. S., Faraj, R. H., Qaidi, S. M. A., and Mohammed, A. A. (2022a). Compressive strength of geopolymer concrete modified with nano-silica: Experimental and modeling investigations. Case Stud. Constr. Mater. 16, e01036. doi:10.1016/j.cscm.2022.e01036
Ahmed, S. N., Hamah Sor, N., Ahmed, M. A., and Qaidi, S. M. A. (2022b). Thermal conductivity and hardened behavior of eco-friendly concrete incorporating waste polypropylene as fine aggregate. Mater. Today Proc. 57, 818–823. doi:10.1016/j.matpr.2022.02.417
Aisheh, Y. I. A., Atrushi, D. S., Akeed, M. H., Qaidi, S., and Tayeh, B. A. (2022). Influence of steel fibers and microsilica on the mechanical properties of ultra-high-performance geopolymer concrete (UHP-GPC). Case Stud. Constr. Mater. 17, e01245. doi:10.1016/j.cscm.2022.e01245
Akeed, M. H., Qaidi, S., Ahmed, H. U., Emad, W., Faraj, R. H., Mohammed, A. S., et al. (2022a). Ultra-high-performance fiber-reinforced concrete. Part III: Fresh and hardened properties. Case Stud. Constr. Mater. 17, e01265. doi:10.1016/j.cscm.2022.e01265
Akeed, M. H., Qaidi, S., Ahmed, H. U., Faraj, R. H., Mohammed, A. S., Emad, W., et al. (2022c). Ultra-high-performance fiber-reinforced concrete. Part IV: Durability properties, cost assessment, applications, and challenges. Case Stud. Constr. Mater. 17, e01271. doi:10.1016/j.cscm.2022.e01271
Akeed, M. H., Qaidi, S., Ahmed, H. U., Faraj, R. H., Majeed, S. S., Mohammed, A. S., et al. (2022b). Ultra-high-performance fiber-reinforced concrete. Part V: Mixture design, preparation, mixing, casting, and curing. Case Stud. Constr. Mater. 17, e01363. doi:10.1016/j.cscm.2022.e01363
Akeed, M. H., Qaidi, S., Ahmed, H. U., Faraj, R. H., Mohammed, A. S., Emad, W., et al. (2022d). Ultra-high-performance fiber-reinforced concrete. Part I: Developments, principles, raw materials. Case Stud. Constr. Mater. 17, e01290. doi:10.1016/j.cscm.2022.e01290
Akeed, M. H., Qaidi, S., Ahmed, H. U., Faraj, R. H., Mohammed, A. S., Emad, W., et al. (2022e). Ultra-high-performance fiber-reinforced concrete. Part II: Hydration and microstructure. Case Stud. Constr. Mater. 17, e01289. doi:10.1016/j.cscm.2022.e01289
Al-Tayeb, M. M., Aisheh, Y. I. A., Qaidi, S. M. A., and Tayeh, B. A. (2022). Experimental and simulation study on the impact resistance of concrete to replace high amounts of fine aggregate with plastic waste. Case Stud. Constr. Mater. 17, e01324. doi:10.1016/j.cscm.2022.e01324
Ali, B., Azab, M., Ahmed, H., Kurda, R., El Ouni, M. H., and Elhag, A. B. (2022a). Investigation of physical, strength, and ductility characteristics of concrete reinforced with banana (Musaceae) stem fiber. J. Build. Eng. 61, 105024. doi:10.1016/j.jobe.2022.105024
Ali, B., Farooq, M. A., El Ouni, M. H., Azab, M., and Elhag, A. B. (2022b). The combined effect of coir and superplasticizer on the fresh, mechanical, and long-term durability properties of recycled aggregate concrete. J. Build. Eng. 59, 105009. doi:10.1016/j.jobe.2022.105009
Almeshal, I., Al-Tayeb, M. M., Qaidi, S. M. A., Abu Bakar, B. H., and Tayeh, B. A. (2022). Mechanical properties of eco-friendly cements-based glass powder in aggressive medium. Mater. Today Proc. 58, 1582–1587. doi:10.1016/j.matpr.2022.03.613
Astm, C. (2010). “Standard test method for flexural strength of concrete (using simple beam with third-point loading),” in American society for testing and materials), 19428–12959.()
Astm, C. (2002). Standard test method for static modulus of elasticity and Poisson’s ratio of concrete in compression. Annu. book ASTM Stand. 4, 469.
Biolzi, L., Guerrini, G. L., and Rosati, G. (1997). Overall structural behavior of high strength concrete specimens. Constr. Build. Mater. 11, 57–63. doi:10.1016/s0950-0618(96)00026-8
Boulekbache, B., Hamrat, M., Chemrouk, M., and Amziane, S. (2010). Flowability of fibre-reinforced concrete and its effect on the mechanical properties of the material. Constr. Build. Mater. 24, 1664–1671. doi:10.1016/j.conbuildmat.2010.02.025
Caluk, N., Mantawy, I., and Azizinamini, A. (2019). Durable bridge columns using stay-in-place UHPC shells for accelerated bridge construction. Infrastructures 4, 25. doi:10.3390/infrastructures4020025
Cao, M., Li, L., and Khan, M. (2018a). Effect of hybrid fibers, calcium carbonate whisker and coarse sand on mechanical properties of cement-based composites. Mater. Construcción 68, e156. doi:10.3989/mc.2018.01717
Cao, M., Xie, C., Li, L., and Khan, M. (2018b). The relationship between reinforcing index and flexural parameters of new hybrid fiber reinforced slab. Comput. Concr. Int. J. 22, 481–492.
El Ouni, M. H., Shah, S. H. A., Ali, A., Muhammad, S., Mahmood, M. S., Ali, B., et al. (2022). Mechanical performance, water and chloride permeability of hybrid steel-polypropylene fiber-reinforced recycled aggregate concrete. Case Stud. Constr. Mater. 16, e00831. doi:10.1016/j.cscm.2021.e00831
Emad, W., Mohammed, A. S., Bras, A., Asteris, P. G., Kurda, R., Muhammed, Z., et al. (2022). Metamodel techniques to estimate the compressive strength of UHPFRC using various mix proportions and a high range of curing temperatures. Constr. Build. Mater. 349, 128737. doi:10.1016/j.conbuildmat.2022.128737
Faraj, R. H., Ahmed, H. U., Rafiq, S., Sor, N. H., Ibrahim, D. F., and Qaidi, S. M. A. (2022). Performance of self-compacting mortars modified with nanoparticles: A systematic review and modeling. Clean. Mater. 4, 100086. doi:10.1016/j.clema.2022.100086
Gao, X. (2007). Mix design and impact response of fibre reinforced and plain reactive powder concrete. RMIT University.
Graybeal, B. (2014). Design and construction of field-cast UHPC connections. Washington, DC: United States. Federal Highway Administration.
Harris, D. K., and Roberts-Wollmann, C. L. (2005). Characterization of the punching shear capacity of thin ultra-high performance concrete slabs. Charlottesville, VA: Virginia Center for Transportation Innovation and Research.
He, X., Yuhua, Z., Qaidi, S., Isleem, H. F., Zaid, O., Althoey, F., et al. (2022). Mine tailings-based geopolymers: A comprehensive review. Ceram. Int. 48, 24192–24212. doi:10.1016/j.ceramint.2022.05.345
Khan, M., Cao, M., Chu, S., and Ali, M. (2022). Properties of hybrid steel-basalt fiber reinforced concrete exposed to different surrounding conditions. Constr. Build. Mater. 322, 126340. doi:10.1016/j.conbuildmat.2022.126340
Khan, M., Cao, M., Hussain, A., and Chu, S. H. (2021). Effect of silica-fume content on performance of CaCO3 whisker and basalt fiber at matrix interface in cement-based composites. Constr. Build. Mater. 300, 124046. doi:10.1016/j.conbuildmat.2021.124046
Khan, U. A., Jahanzaib, H. M., Khan, M., and Ali, M. (2018). “Improving the tensile energy absorption of high strength natural fiber reinforced concrete with fly-ash for bridge girders,” in Key engineering materials (Switzerland: Trans Tech Publ), 335–342.
Puzatova, A., Shakor, P., Laghi, V., and Dmitrieva, M. (2022). Large-scale 3D printing for construction application by means of robotic arm and gantry 3D printer: A review. Buildings 12, 2023. doi:10.3390/buildings12112023
Qaidi, S. M. A., Dinkha, Y. Z., Haido, J. H., Ali, M. H., and Tayeh, B. A. (2021a). Engineering properties of sustainable green concrete incorporating eco-friendly aggregate of crumb rubber: A review. J. Clean. Prod. 324, 129251. doi:10.1016/j.jclepro.2021.129251
Qaidi, S. M. A., Tayeh, B. A., Zeyad, A. M., De Azevedo, A. R. G., Ahmed, H. U., and Emad, W. (2022a). Recycling of mine tailings for the geopolymers production: A systematic review. Case Stud. Constr. Mater. 16, e00933. doi:10.1016/j.cscm.2022.e00933
Qaidi, S. M., Atrushi, D. S., Mohammed, A. S., Ahmed, H. U., Faraj, R. H., Emad, W., et al. (2022b). Ultra-high-performance geopolymer concrete: A review. Constr. Build. Mater. 346, 128495. doi:10.1016/j.conbuildmat.2022.128495
Qaidi, S., Yahia, A., Tayeh, B. A., Unis, H., Faraj, R., and Mohammed, A. (2022c). 3D printed geopolymer composites: A review. Mater. Today Sustain. 20, 100240. doi:10.1016/j.mtsust.2022.100240
Qaidi, S. M. A., Sulaiman Atrushi, D., Mohammed, A. S., Unis Ahmed, H., Faraj, R. H., Emad, W., et al. (2022d). Ultra-high-performance geopolymer concrete: A review. Constr. Build. Mater. 346, 128495. doi:10.1016/j.conbuildmat.2022.128495
Qaidi, S. M. A., Tayeh, B. A., Ahmed, H. U., and Emad, W. (2022e). A review of the sustainable utilisation of red mud and fly ash for the production of geopolymer composites. Constr. Build. Mater. 350, 128892. doi:10.1016/j.conbuildmat.2022.128892
Qaidi, S. M. A., Tayeh, B. A., Isleem, H. F., De Azevedo, A. R. G., Ahmed, H. U., and Emad, W. (2022f). Sustainable utilization of red mud waste (bauxite residue) and slag for the production of geopolymer composites: A review. Case Stud. Constr. Mater. 16, e00994. doi:10.1016/j.cscm.2022.e00994
Raza, S. S., Ali, B., Noman, M., Fahad, M., and Elhadi, K. M. (2022). Mechanical properties, flexural behavior, and chloride permeability of high-performance steel fiber-reinforced concrete (SFRC) modified with rice husk ash and micro-silica. Constr. Build. Mater. 359, 129520. doi:10.1016/j.conbuildmat.2022.129520
Raza, S. S., Qureshi, L. A., Ali, B., Raza, A., and Khan, M. M. (2021). Effect of different fibers (steel fibers, glass fibers, and carbon fibers) on mechanical properties of reactive powder concrete. Struct. Concr. 22, 334–346. doi:10.1002/suco.201900439
Rossi, P., Acker, P., and Malier, Y. (1987). Effect of steel fibres at two different stages: The material and the structure. Mater. Struct. 20, 436–439. doi:10.1007/bf02472494
Russell, H. G., Graybeal, B. A., and Russell, H. G. (2013). Ultra-high performance concrete: A state-of-the-art report for the bridge community". United states. McLean, Virginia: Federal Highway Administration. Office of Infrastructure.
Saeed, A., Najm, H. M., Hassan, A., Sabri, M. M. S., Qaidi, S., Mashaan, N. S., et al. (2022). Properties and applications of geopolymer composites: A review study of mechanical and microstructural properties. Materials 15, 8250. doi:10.3390/ma15228250
Sahoo, K. K., Sarkar, P., and Davis, R. (2019). Mechanical properties of silica fume concrete designed as per construction practice. Proc. Institution Civ. Engineers-Construction Mater. 172, 20–28. doi:10.1680/jcoma.16.00085
Sanjuán, M. Á., and Andrade, C. (2021). Reactive powder concrete: Durability and applications. Appl. Sci. 11, 5629. doi:10.3390/app11125629
Shah, S. P. (1990). Toughening of cement-based materials with fiber reinforcement, MRS Online Proceedings Library (OPL. 211.
Shaheen, E., and Shrive, N. G. (2006). Optimization of mechanical properties and durability of reactive powder concrete. ACI Mater. J. 103, 444.
Shakor, P., Nejadi, S., Paul, G., and Malek, S. (2019a). Review of emerging additive manufacturing technologies in 3D printing of cementitious materials in the construction industry. Front. Built Environ. 4, 85. doi:10.3389/fbuil.2018.00085
Shakor, P., Nejadi, S., Paul, G., Sanjayan, J., and Nazari, A. (2019b). Mechanical properties of cement-based materials and effect of elevated temperature on three-dimensional (3-D) printed mortar specimens in inkjet 3-D printing. ACI Mater. J. 116, 55–67.
Standard, A. (2014). C157,“Standard test method for length change of hardened hydraulic-cement mortar and concrete”. West Conshohocken, PA, United States: Annual Book of ASTM Standards. 4.
Standard, A. (2017). C496/C496M-17 Standard test method for splitting tensile strength of cylindrical concrete specimens. West Conshohocken PA: ASTM International.
Tayeh, B. A., Akeed, M. H., Qaidi, S., and Bakar, B. H. A. (2022a). Influence of microsilica and polypropylene fibers on the fresh and mechanical properties of ultra-high performance geopolymer concrete (UHP-GPC). Case Stud. Constr. Mater. 17, e01367. doi:10.1016/j.cscm.2022.e01367
Tayeh, B. A., Akeed, M. H., Qaidi, S., and Bakar, B. H. A. (2022b). Influence of sand grain size distribution and supplementary cementitious materials on the compressive strength of ultrahigh-performance concrete. Case Stud. Constr. Mater. 17, e01495. doi:10.1016/j.cscm.2022.e01495
Tayeh, B. A., Akeed, M. H., Qaidi, S., and Bakar, B. H. A. (2022c). Influence of the proportion of materials on the rheology and mechanical strength of ultrahigh-performance concrete. Case Stud. Constr. Mater. 17, e01433. doi:10.1016/j.cscm.2022.e01433
Tayeh, B. A., Akeed, M. H., Qaidi, S., and Bakar, B. H. A. (2022d). Ultra-high-performance concrete: Impacts of steel fibre shape and content on flowability, compressive strength and modulus of rupture. Case Stud. Constr. Mater. 17, e01615. doi:10.1016/j.cscm.2022.e01615
Tomosawa, F., Noguchi, T., and Onoyama, K. (1990). “Investigation of fundamental mechanical properties of high-strength concrete,” in Summaries of technical papers of annual meeting of Architectural Institute of Japan), 497–498.()
Vinod, S., Shakor, P., Sartipi, F., and Karakouzian, M. (2022). Object detection using ESP32 cameras for quality control of steel components in manufacturing structures. Arabian J. Sci. Eng., 1–18. doi:10.1007/s13369-022-07562-2
Keywords: UHPC, fiber-reinforced concrete, reactive powder concrete, fibers, fiber reinforced polymer
Citation: Abed S, Hadi R, Jawdhari A, Mohammed Najm H, Mahmood S, Bilema M and Muayad Sabri Sabri M (2023) Influence of ternary hybrid fibers on the mechanical properties of ultrahigh-strength concrete. Front. Mater. 10:1148589. doi: 10.3389/fmats.2023.1148589
Received: 20 January 2023; Accepted: 07 February 2023;
Published: 23 February 2023.
Edited by:
Pshtiwan Shakor, Institute of Construction Materials, AustraliaReviewed by:
Babar Ali, COMSATS University Islamabad, PakistanCopyright © 2023 Abed, Hadi, Jawdhari, Mohammed Najm, Mahmood, Bilema and Muayad Sabri Sabri. This is an open-access article distributed under the terms of the Creative Commons Attribution License (CC BY). The use, distribution or reproduction in other forums is permitted, provided the original author(s) and the copyright owner(s) are credited and that the original publication in this journal is cited, in accordance with accepted academic practice. No use, distribution or reproduction is permitted which does not comply with these terms.
*Correspondence: Shaker Mahmood, c2hha2VyNzMwQHlhaG9vLmNvbQ==
Disclaimer: All claims expressed in this article are solely those of the authors and do not necessarily represent those of their affiliated organizations, or those of the publisher, the editors and the reviewers. Any product that may be evaluated in this article or claim that may be made by its manufacturer is not guaranteed or endorsed by the publisher.
Research integrity at Frontiers
Learn more about the work of our research integrity team to safeguard the quality of each article we publish.