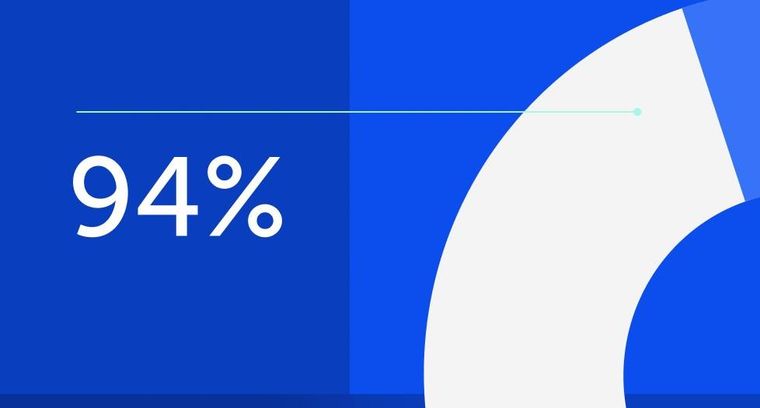
94% of researchers rate our articles as excellent or good
Learn more about the work of our research integrity team to safeguard the quality of each article we publish.
Find out more
ORIGINAL RESEARCH article
Front. Mater., 15 July 2022
Sec. Polymeric and Composite Materials
Volume 9 - 2022 | https://doi.org/10.3389/fmats.2022.944368
This article is part of the Research TopicFire Risk and Prevention Technologies of Polymeric and Composite MaterialsView all 5 articles
Phosphomolybdic acid (PMA) as a synergist was added into polyurethane (PU) rigid foam with ammonium polyphosphate (APP) to improve its flame retardancy and thermal stability. The combustion performance of PU was studied by limiting oxygen index (LOI), UL-94, and a cone calorimeter. The thermal degradation behavior of PU was determined by thermogravimetric analysis (TG) and thermogravimetric infrared spectroscopy (TG-IR). Experimental results showed that the introduction of PMA could further improve the flame retardant performance of PU/APP composites and significantly increase the amount of carbon residue at high temperatures. Adding 3wt% PMA to PU containing 12wt% APP could make the foam pass UL-94 V-0, increase the carbon residue at 800°C by 69.16% in the air atmosphere, and decrease the THR by 24.62% compared to those of PU/15APP. TG-IR results showed that the presence of PMA reduced the production of small-molecule gas-phase products. As for the mechanical properties of PU composites, the addition of PMA influences their density and compressive strength obviously. The results suggest that PMA and APP have good synergistic flame retardancy on PU and can reduce its fire risk.
Polyurethane (PU) rigid foam is a high-crosslinked polymer material with strong insulating properties. It is a three-dimensional polymer synthesized by polyols, isocyanates, and other additives (Tan et al., 2011; Członka et al., 2020). It has good mechanical properties, low conductivity, convenient preparation, good weather resistance, and other excellent properties. Polyurethane is widely used in various fields of heat preservation and insulation, mainly in building aviation and electrical (Hejna et al., 2017; Kirpluks et al., 2018; Bo et al., 2021). However, polyurethane itself is a highly flammable material and releases a lot of toxic gas when burned, which limits its widespread use (Xi et al., 20152015). Therefore, it is of great significance to study the flame retardant performance of polyurethane enhanced by flame retardants. The common method is to introduce additive flame retardants and reactive flame retardants into polyurethane to improve its flame retardancy (Jia et al., 2019; Li et al., 2020; Shen et al., 2021; Çalışkan et al., 2021).
Polyphosphate amine (APP) is a common additive halogen-free flame retardant with P and N flame retardant elements and is widely used to improve the flame retardant performance of polymers (Luo et al., 2021; Qin et al., 2021). There are also many literature reports on the use of APP in polyurethane to reduce its fire risk. (Zeng et al. 2021) used tetraethoxysilane and vinyltriethoxysilane as precursors to prepare modified APP and applied it to PU. When the addition amount of modified APP reached 20wt%, LOI increased from 19.8 to 30% and passed the UL-94 V-0. (Chen et al. 2017) modified APP with a synthetic modifier (M-APP), and the M-APP was added to polyurethane. The results showed that the dispersion of APP after modification was improved in the matrix, the peak heat release rate (PHRR) of PU/20% M-APP decreased by 51.18% compared with that of PU-APP and M-APP could also promote the formation of the carbon layer. (Xu et al. 2015) applied ZnO and montmorillonite (MMT) in polyurethane in combination with APP and dimethyl methyl phosphonate (DMMP). They found that ZnO and MMT could narrow the heat release which was 56% lower than the pure sample, and the LOI could get to 29.5%.
In recent years, it has been reported that the flame retardant and thermal stability of polymer can be improved by adding a flame retardant coefficient. Also, polyoxometalate has been applied in many fields as an environmentally efficient catalyst and coefficient (Ye and Li, 2016; Yimin et al., 2020). Phosphomolybdic acid (H3PO4·12MoO3 for short PMA) is a polyoxometalate formed by oxygen condensation of molybdenum oxide and phosphoric acid (Yimin et al., 2020). Since it contains flame retardant elements P and Mo, some scholars began to study its flame retardancy. (Chen et al. 2013; Chen et al. 2016) added a polyoxometalate-based ionic liquid (PIL) into conventional polypropylene/intumescent flame retardant (PP/IFR) composites. The PP composite with 14.5wt% IFR and 0.5wt% PIL could pass the UL-94 V-0, while that for a single IFR needed more than 25wt%. (Yimin et al. 2020) made phosphomolybdic acid reacting with three different metal ions (Ni, Na, and Zn) to form phosphomolybdate and used it in PP, which were used to improve the flame retardant efficiency of PP/IFR. To reach the UL-94 V-0, the addition amount of IFR alone needed 25wt%, but if 0.5wt% sodium phosphomolybdate or zinc phosphomolybdate was added, IFR only needed 14.5wt%. (Jiao et al. 2021) synthesized a green flame retardant for epoxy resin (EP) by chemical modification of phosphomolybdate with imidazole. When the amount of flame retardant was 8wt%, the polymer could pass the UL-94 V-0, and PHRR and total smoke release volume (TSR) decreased by 37.78 and 31.03%, respectively compared to those of pure epoxy.
Many literatures have reported the use of APP and PMA in polymers to improve their flame retardancy and thermal stability, but there are few reports on the use of PMA and APP in polyurethane. In this paper, APP and PMA were compounded and added to polyurethane. The flame retardant performance and the possible synergistic effect of APP and PMA on polyurethane were studied. Flame retardant property and thermal degradation behavior of flame retarded polyurethane were determined by limiting oxygen index (LOI) test, cone calorimeter, thermogravimetric analysis (TGA) and thermogravimetric infrared analyzer (TG-IR), and the possible synergistic effect of APP and PMA on polyurethane was discussed.
Polyether polyol (LY-4110) was provided by Shandong Bluestar Dongda Co., LTD. PAPI(PM-200) was supplied by China Wanhua Chemical Group Co., LTD. Silicone foam stabilizer (AK-8805) was obtained from Maitu High-tech Materials Co., LTD. TEA was purchased from Jining Huakai Resin Co., LTD. Triethylene diamine (A33,33%) could get from Xuzhou Yihuiyang New Material Co., LTD. Dibutyltin dilaurate (LC) was provided by Shanghai Aladdin Biochemical Technology Co., LTD. Deionized water was made in the laboratory; Ammonium polyphosphate (APP 231) was purchased from Pulsefuru (Qingyuan) Phosphorus Chemical Co., LTD. Phosphomolybdic acid hydrate [H3P(Mo3O10)4·10H2O] was obtained from Shanghai MacLin Biochemical Technology Co., LTD.
A one-step free foaming method was used to prepare PU and flame retardant PU. The main formulas are shown in Table 1. First, the white material, APP, or PMA were put into a 500 ml plastic beaker and stirred evenly with a high-speed mixer for about 2 min. Second, added PAPI into the plastic cup and quickly agitated with an electric stirrer for 30 s. Third, after mixing, the mixture was quickly poured into a mold. About 1 min later, foaming was completed to obtain rigid polyurethane foam. Then, the foam was put in a thermostat at 80°C for 8 h to fully react. Finally, cut the rigid polyurethane foam according to different test requirements.
A conical calorimeter (Suzhou Yangyi Volchi Testing Technology Co., LTD.) was used to study the thermal properties of the samples according to the ISO560-2002 standard. The sample size was 100 mm × 100 mm × 25 mm and thermal radiation power was 35 kW/m2.
The oxygen index (LOI) test was carried out using the hc-2 oxygen index instrument (Jiangning analytical instrument co. LTD.). The sample size was 100 mm × 10 mm × 10 mm.
A vertical combustion grade test (Jiangning analytical instrument co. LTD.) was performed on a polyurethane sample whose size was 127 mm × 13 mm × 10 mm according to ASTM D3801-2010.
According to GB/T8813-2008, at the temperature of 25 ± 2°C, the compression property of PU was characterized by Instron 1185. The sample size was 50 mm × 50 mm × 50 mm.
The thermal stability of the samples was performed on a thermogravimetric analyzer (TGA) in an air or nitrogen atmosphere with a heating rate of 20°C/min and a temperature ranges from room temperature to 800°C.
Apparent density was tested according to ASTM D1622. The size of the foam samples for the measurement was 30 mm × 30 mm × 30 mm, the average value was taken three times.
SEM (Hitachi SU8010) was used to study the morphology of the sample after the oxygen index test. The sample was pretreated with gold spraying and aluminum alloy.
TG-IR was combined with TGA 8000 thermogravimetric analyzer and Frontier infrared spectrometer. Under a nitrogen atmosphere, the heating rate was 20°C/min, temperature range was room temperature to 800°C.
TGA thermogravimetric analysis was used to study the thermal decomposition properties of polyurethane and its composites. The TGA and DTG curves in the air atmosphere with a heat rise rate of 20°C/min are shown in Figure 1, typical thermal parameters are shown in Table 2. The PU with APP can present that the thermal decomposition procedure increases from two stages to three stages in Figure 1B. An obvious thermal degradation peak appears after 650°C, mainly because APP has a thermal decomposition behavior at about 650°C (Zhou et al., 2013). Table 2 presents that the value of T5% of PU composites doesn’t change much with introducing APP, but the T50% value increases by 23.8%. The amount of carbon residue at 800°C increases 82.92% after the addition of 15wt% APP. Because APP which is a gas source and acid source can promote the thermal oxidation decomposition process of polyurethane to form more carbon layers (Ni et al., 2009).
It is obvious that for the initial decomposition temperature, there is little change when a small amount of PMA has been introduced into the composite as Table 2 shows. However, when the 5wt% PMA is added to polyurethane, T5% decreases to 239.81°C. When the addition amount of PMA is 3wt%, the amount of carbon residue at 800°C increased by 69.16% compared with the carbon residue of PU/15APP, and increased by 209.43% compared with that of PU. For TG curves, the PU/12APP/3PMA has a larger weight loss at the first and second stages compared with PU/15APP. PMA and APP can participate in the thermal decomposition process of polyurethane, and they play a good synergic effect to promote the formation of carbon, thus improving the thermal stability of the system.
Figure 2 shows the TG diagram in the nitrogen atmosphere. According to Table 3, PU begins to decompose at about 238°C, and the carbon residue of 800°C is only 10.51%. After adding 15wt% APP to the matrix, the initial decomposition temperature rises. The carbon residue at 800°C reaches 30.13% and increases by 187% compared with that of PU. And it is higher than many research results (Chen et al., 2017; Yan et al., 2021; Zeng et al., 2021). The addition of ammonium polyphosphate improves the stability of the carbon layer, mainly because APP accelerates the polymer to form more carbon layers. When APP and PMA are used in combination, the values of T5% begin to decrease with the comparison that of PU/15APP, and T5% of PU/10APP/5PMA is 230.34°C. The char residue of PU/12APP/3PMA is 34.16% at 800°C. Compared with the char yield of PU/15APP, PU/12APP/3PMA demonstrates an enhanced thermal degradation behavior related to char yield which increases by 13%. Thus, it can be evaluated that the combination of APP and PMA exerts a synergetic effect as flame retardants against PU, this inference is mainly attributed to their high char yield.
The flame retardancy of PU can be evaluated by LOI and vertical combustion tests. Table 4 presents the data provided by the experiments on LOI and UL-94. The LOI of PU is only 19.4%, and PU/15APP increases to 24.1%. However, the LOI value decreases with the addition of PMA. Mainly because APP plays a major role in flame retardant polyurethane, when APP is burned, a dense carbon layer is formed to cover the surface of the material and prevent oxygen from further entering the matrix for combustion. The increase of PMA content leads to the decrease of APP content, so the LOI value declines. The test results of UL-94 can also be seen in Table 4. PU cannot pass the test UL-94. For PU/15APP, it can pass the UL-94 V-1. When 0.5wt% PMA is added to polyurethane, the polymer can reach UL-94 V-0.
The cone calorimeter test is an effective method to evaluate the combustion performance of polymers. Table 5, Table 6 summarize the data collected during the experiment. The cone-volume thermal curves of the polyurethane system with APP and PMA are shown in Figure 3, including HRR, THR, and TSR. Table 5 presents that the TTI of all samples is very short. It may be related to the porous structure of the polyurethane material itself. As for Figure 3A, after APP is added to PU, a sharp peak first appears in flame retardant polyurethane, then the curve gradually slows down. A small peak appears near 150 s, which may be caused by the combustion of intermediate products or unstable carbon layers. HRR curve of PU reaches the peak value of 378.31kW/m2 at the beginning of combustion and then attenuates. The PHRR value of PU/15APP is 290.61 kW/m2, decreasing by 23.26% compared with that of PU. Figure 3B and Figure 3C represent the change curves of THR and TSR. THR curve of PU/15APP decreases first and then levels off compared with that of PU. The TSR value of PU/15APP decreases by 25.20% as shown in Table 5. This is mainly because APP which is a flame retardant can improve the flame retardant performance of polymers.
When PMA is added to PU/15APP composite, the HRR curves have little change before they reach the first peak, but the time to reach the second peak is delayed. According to the data in Table 5, for the PU with APP and PMA, HRR values increase first and then decrease compared with that of PU without PAM. The main reason for the increase is that APP plays a major role in flame retarding polyurethane. When the content of the APP decreases, the flame retarding effect weakens. The reason for the decrease is that PMA plays a synergistic effect with APP. When PMA content is 3wt%, the PHRR value is 286.78 kW/m2, and the TSR value is 346.63 m2/m2. As can be seen from Figure 3B, the THR value is relatively low when the PMA addition amount is 0.5wt% and 1wt%. However, when the PMA addition amount is 3wt%, before 180 s, the THR value is higher than PU/15APP, but after that, it is significantly lower than PU/15APP. PU/10APP/5PMA shows the same phenomena. Table 5 shows that the THR value first decreases, then increases, and last decreases. THR value of PU/10APP/5PMA decreases by 25% compared with THR of PU/15APP. These results indicate that the PMA which is a synergist can directly cooperate with APP to improve the fire safety of polyurethane.
SEM is used to further observe the morphology of carbon residue of polyurethane composite after the oxygen index test. Figure 4 shows the results obtained from studies of SEM. The morphology of carbon residue is more wrinkled, non-uniform, and irregular on the surface of PU. After APP is introduced to the matrix, the morphology of carbon residue is significantly different. It can be seen that a large bubble structure appears on the polymer surface, forming an expandable carbon layer, which can isolate oxygen and heat insulation. When PMA replaced part of APP in PU, the bubbles are significantly increased and more prominent, and the cracks and pores are reduced, forming a dense and continuous carbon layer. This compact carbon layer causes a large surface area, which plays an important role in thermal stability.
FIGURE 4. SEM micrographs of: (A) PU; (B) PU/15APP; (C) PU/14.5APP/0.5PMA; (D) PU/14APP/1PMA; (E) PU/12APP/3PMA; (F) PU/10APP/5PMA.
The foam density and compress strength of PU are two important physical properties of the foam, which have a great influence on the thermal stability and other properties of polyurethane. Figure 5 shows the density and compress strength of polyurethane composites. There is a certain correlation between the density of polyurethane and the compress strength. Higher density leads to smaller plastic deformation between the inner layer and the combustion layer (Chen, 2016). Figure 5 presents that the density and corresponding compress strength increased after APP is introduced to PU. The physical properties of the material, such as compress strength, are affected by material’s bubble structure. Adding an appropriate amount of APP can make the foam holes of polyurethane smaller and denser, thus increasing the density of polyurethane foam and enhancing its compression performance. The addition of PMA destroys the cellular structure of the composite and makes the flame retardant agglomerate in polyurethane. With the increase of PMA content, the structural damage is more obvious and the influence on the mechanical properties of polyurethane is greater. It can be seen that the addition of PMA affects the mechanical properties of polyurethane.
Thermogravimetric infrared spectroscopy (TG-IR) can be used to quantitatively analyze the gas products during sample pyrolysis (Lin, 2016). Taking PU/12APP/3PMA as an example, Figure 6 is the infrared 3D spectrum of polyurethane and flame retardant polyurethane. The figure shows that the type and intensity of gas release of polyurethane with flame retardant added are less and weaker than PU. The absorption peaks of degradation are mainly distributed in the wave number periods of 3,700–3,800 cm−1, 3,300–3,400 cm−1, 2,200–2,400 cm−1, 1700–1800 cm−1, 1500–1600 cm−1 and 1100–1300 cm−1 (Liu et al., 2020).
FIGURE 6. 3D TG-FTIR spectra of gas products in degradation process for (A) PU; (B) PU/15APP and (C) PU/12APP/3PMA.
Figure 7 is the infrared spectrum corresponding to the maximum weight loss of polyurethane and flame retardant polyurethane in a nitrogen atmosphere. It can be seen from Figure 7 the O-H bond of the free water molecule is at 3730 cm−1 (Liu et al., 2015), 3,650 cm−1 is the stretching vibration of the O-H bond, C-H stretching vibration compound generated at 2,930 cm−1, 2,360 cm−1 is the characteristic peak of CO2 generated by cracking, and 2,310 cm−1 is the NCO absorption peak. The absorption peaks of phenyl compounds are 1524 cm−1, 1510 cm−1, and 672 cm−1 (Ravey and Pearce, 1997). −C =O bond appears at 1850 cm−1 (He et al., 2016). 1110 cm−1 corresponds to the C-O group of ethers. The absorption peak of NH3 is at 948 cm−1, and the flexural vibration of P-O-P is near 832 cm−1 (Yang et al., 2020).
FIGURE 7. FTIR spectra of pyrolysis products at maximum decomposition rate for PU; PU/15APP and PU/12APP/3PMA.
After APP is added to polyurethane, not only new absorption peaks are generated, but also the existing absorption peaks are significantly changed. The absorption characteristic peak of the O-H bond at 3,730 cm−1 enhances, which is mainly attributed to water molecules. The increased content of water molecules can take away the heat generated by combustion. The absorption peaks of the benzene ring at 1524 cm−1 and 1510 cm−1 are weakened, while the absorption peaks of C-O at 1110 cm−1 and −C =O bond at 850 cm−1 promote. The absorption peak of NH3 at 948 cm−1 is generated by APP decomposition, and the P-O-P flexural vibration near 832 cm−1 is also newly generated.
When the PU contains APP and PMA, the absorption peak value of the O-H bond produced by the water molecule at 3,730 cm−1 increases, while the peak of the C-H bond at 2,930 cm−1 decreases compared with the peak of PU without PMA. The addition of PMA also weakens the absorption peak of the −C=O bond at 1850cm−1.
In order to understand the influence of flame retardant on the escaping gas more clearly, the main absorption peaks of gas are compared, such as CO2 absorption peak at 2360cm−1, C-H compound absorption peak at 2930cm−1, benzene ring absorption peak at 672cm−1, and absorption peak of C-O group produces by ether bond at 1110 cm−1. Figure 8A shows the change in the C-H absorption peak. The release time of the C-H compound reaches the peak earlier after APP is added to PU, and the release amount decreases after PMA is added to PU composite. The changes in the CO2 peak at 2360cm−1 are summarized in Figure 8B. After the addition of flame retardants, the CO2 output is higher than PU, mainly because APP reacts with polyurethane to generate CO2 (Grassie and Perdomo Mendoza, 1985). However, after adding PMA, the CO2 yield is still lower than PU/15APP. Figure 8C shows the change of benzene ring absorption peak at 672cm−1. After 15wt% APP is added into the matrix, the time for benzene ring peak is earlier than the time for PU. After PMA is added to flame retardant polyurethane, the peak decreased. Figure 8D shows the results obtained from studies of the change of absorption peak of the C-O bond at 1110 cm−1. After APP is added to PU, the time of C-O appears earlier and the release amount decreases, and the release amount further decreases with the addition of PMA.
FIGURE 8. Intensity of decomposition products for PU; PU/15APP and PU/12APP/3PMA versus time: (A) C-H compounds spectra; (B) CO2spectra; (C) benzene ring spectra; (D) C-O spectra.
PMA and APP are combined with flame retardant polyurethane, and they can play a good synergistic flame retardant effect. Figure 9 shows that the possible flame retardancy mechanism of PMA in APP/PU composite. The addition of a small amount of PMA makes the flame retardant polyurethane pass the UL-94 V-0, and the heat released during the combustion process is reduced. According to the analysis results, the presence of PMA restrains the thermal decomposition process of polyurethane materials, which reduces the production of decomposition products, such as CO2, C-H, -C-O, and the benzene ring, and the reduction of combustible small molecule products further weakens the combustion reaction and reduces the heat release amount of the system. At the same time, PMA and APP jointly promote the generation of the cross-linking system, forming more protective carbon layers. The increase of carbon layers can play a better shielding role, limiting the transfer of oxygen heat and combustible gas. In addition, the infrared spectrum shows that after joining PMA, more water is released during the thermal decomposition of the system. On the one hand, the water molecules can take away the heat from the burning of polyurethane and dilute the concentration of combustible gas. On the other hand, the result shows that more -OH combined with -H to form water, rather than with carbon atom to form alcohol, ether, and other flammable small molecule compounds. In conclusion, for polyurethane foam insulation material, PMA is a high-quality flame retardant synergist of APP, which can further improve the flame retardant performance of PU.
In this study, different contents of PMA were introduced into PU foam with APP to explore their influence on the combustion and thermal properties of polyurethane insulation materials. Combustion performance test results showed that PU/14.5APP/0.5PMA can achieve a UL-94 V-0 rating. When PMA replaced part of APP in PU, the PHRR first increased and then decreased. The THR of PU/12APP/3PMA was 24.62% lower than that of PU/15APP. SEM results revealed that flame retardant PU containing PMA had a more prominent expansive carbon layer. Thermogravimetric analysis results in different atmospheres showed that the presence of PMA significantly improved the thermal stability of polyurethane composites at high temperatures. Compared with PU, the amount of carbon residue in PU/12APP/3PMA at 800°C increased by 209.43% in the air atmosphere. TG-IR was used to further explore the flame retardant synergistic mechanism of PMA. The results showed that the presence of PMA reduced the production of decomposition products, such as CO2, C-H, -C-O, and benzene, and also made the system release more water molecules. According to various test results, PMA is a good synergistic agent for APP flame retardant PU, which can further improve its flame retardant performance and thermal stability.
The raw data supporting the conclusions of this article will be made available by the authors, without undue reservation.
ZX performed the data analyses and wrote the manuscript; ZIX contributed to the test of the samples; RT performed the experiment; LM contributed to the tables and figures of the manuscript; JZ contributed to the conception of the study; JX provided the experimental conditions; and TY contributed to the fund support.
This work was financially supported by the Natural Science Foundation Youth Program of Anhui Province under Grant number 1808085QE150, Natural Science Research Project of Anhui Province under Grant number KJ 2020A0450, and Natural Science Research Foundation for Introduction of Talent and Doctor under Grant number 2019QDZ59.
The authors declare that the research was conducted in the absence of any commercial or financial relationships that could be construed as a potential conflict of interest.
All claims expressed in this article are solely those of the authors and do not necessarily represent those of their affiliated organizations, or those of the publisher, the editors, and the reviewers. Any product that may be evaluated in this article, or claim that may be made by its manufacturer, is not guaranteed or endorsed by the publisher.
Bo, G., Xu, X., Tian, X., Wu, J., He, X., Xu, L., et al. (2021). Enhancing the Flame Retardancy for castor Oil-Based Rigid Polyurethane Foams via Silica Aerogel. J. Non-Crystalline Solids 562, 120783. doi:10.1016/j.jnoncrysol.2021.120783
Çalışkan, E., Çanak, T. Ç., Karahasanoğlu, M., and Serhatlı, I. E. (2021). Synthesis and Characterization of Phosphorus-Based Flame Retardant Containing Rigid Polyurethane Foam. J. Therm. Anal. Calorim. 147, 4119–4129. doi:10.1007/s10973-021-10837-9
Chen, S., Li, J., Zhu, Y., Guo, Z., and Su, S. (2013). Increasing the Efficiency of Intumescent Flame Retardant Polypropylene Catalyzed by Polyoxometalate Based Ionic Liquid. J. Mat. Chem. A 1 (48), 15242–15246. doi:10.1039/c3ta13538a
Chen, S., Wang, C., and Li, J. (2016). Effect of Alkyl Groups in Organic Part of Polyoxo-Metalates Based Ionic Liquids on Properties of Flame Retardant Polypropylene. Thermochim. Acta 631, 51–58. doi:10.1016/j.tca.2016.03.020
Chen, Y. J. (2016). Study on the Structure and Flame Retardant Properties of Environment-Friendly Halogen-free Rigid Polyurethane Foam. master’s thesis. China: South China University of Technology.
Chen, Y., Li, L., Wang, W., and Qian, L. (2017). Preparation and Characterization of Surface-Modified Ammonium Polyphosphate and its Effect on the Flame Retardancy of Rigid Polyurethane Foam. J. Appl. Polym. Sci. 134 (40), 45369. doi:10.1002/app.45369
Członka, S., Strąkowska, A., Strzelec, K., Kairytė, A., and Kremensas, A. (2020). Melamine, Silica, and Ionic Liquid as a Novel Flame Retardant for Rigid Polyurethane Foams with Enhanced Flame Retardancy and Mechanical Properties. Polym. Test. 87, 106511. doi:10.1016/j.polymertesting.2020.106511
Grassie, N., and Perdomo Mendoza, G. A. (1985). Thermal Degradation of Polyether-Urethanes: 5. Polyether-Urethanes Prepared from Methylene Bis(4-Phenylisocyanate) and High Molecular Weight Poly(ethylene Glycols) and the Effect of Ammonium Polyphosphate. Polym. Degrad. Stab. 11 (4), 359–379. doi:10.1016/0141-3910(85)90039-4
He, J. J., Jiang, L., Sun, J., and Lo, S. M. (2016). Thermal Degradation Study of Pure Rigid Polyurethane in Oxidative and Non-oxidative Atmospheres. J. Anal. Appl. pyrolysis 120, 269–283. doi:10.1016/j.jaap.2016.05.015
Hejna, A., Kirpluks, M., Kosmela, P., Cabulis, U., Haponiuk, J., and Piszczyk, Ł. (2017). The Influence of Crude Glycerol and castor Oil-Based Polyol on the Structure and Performance of Rigid Polyurethane-Polyisocyanurate Foams. Industrial Crops Prod. 95, 113–125. doi:10.1016/j.indcrop.2016.10.023
Jia, D., Hu, J., He, J., and Yang, R. (2019). Properties of a Novel Inherently Flame‐retardant Rigid Polyurethane Foam Composite Bearing Imide and Oxazolidinone. J. Appl. Polym. Sci. 136 (3), 47943. doi:10.1002/app.47943
Jiao, E., Wu, K., Qu, Z., Liu, Y., Lu, M., Nan, B., et al. (2021). Preparation and Curing Kinetics of Intrinsic Flame Retardant Epoxy Resin System Based on Polyoxometalates. J. Therm. Anal. Calorim. 146 (3), 1063–1076. doi:10.1007/s10973-020-10075-5
Kirpluks, M., Kalnbunde, D., Benes, H., and Cabulis, U. (2018). Natural Oil Based Highly Functional Polyols as Feedstock for Rigid Polyurethane Foam Thermal Insulation. Industrial Crops Prod. 122, 627–636. doi:10.1016/j.indcrop.2018.06.040
Li, X., Yu, Z., and Zhang, L. (2020). Synthesis of a Green Reactive Flame‐retardant Polyether Polyol and its Application. J. Appl. Polym. Sci. 138, 50154. doi:10.1002/app.50154
Lin, S.-Y. (2016). An Overview of Advanced Hyphenated Techniques for Simultaneous Analysis and Characterization of Polymeric Materials. Crit. Rev. Solid State Mater. Sci. 41 (6), 482–530. doi:10.1080/10408436.2016.1186598
Liu, X. Y., Zhang, B., Zhang, H., Du, X. Y., and Tang, G. (2020). Research of Flame Retardant Mechanism for RPUF/EG Composites Based on TG-FTIR and XPS [J]. Spectrosc. Spectr. Analysis 40 (5), 8. doi:10.3964/j.issn.1000-0593(2020)05-1626-08
Liu, X., Zhou, Y., Hao, J., and Du, J. (2015). Smoke and Toxicity Suppression by Zinc Salts in Flame-Retardant Polyurethane-Polyisocyanurate Foams Filled with Phosphonate and Chlorinated Phosphate. J. Appl. Polym. Sci. 132 (16), 41846. doi:10.1002/app.41846
Luo, Q., Wang, M., Zhang, H., Ouyang, Y., Lin, H., Shu, Y., et al. (2021). Preparation and Properties of Bio-Based Flame Retardant L-APP/Poly(L-lactic Acid) Composites. J. Renew. Mater. 9, 2067–2076. doi:10.32604/jrm.2021.016255
Ni, J., Song, L., Hu, Y., Zhang, P., and Xing, W. (2009). Preparation and Characterization of Microencapsulated Ammonium Polyphosphate with Polyurethane Shell Byin Situpolymerization and its Flame Retardance in Polyurethane. Polym. Adv. Technol. 20 (12), 999–1005. doi:10.1002/pat.1354
Qin, P., Yi, D., Xing, J., Zhou, M., and Hao, J. (2021). Study on Flame Retardancy of Ammonium Polyphosphate/montmorillonite Nanocompound Coated Cellulose Paper and its Application as Surface Flame Retarded Treatment for Polypropylene. J. Therm. Anal. Calorim. 146, 2015–2025. doi:10.1007/s10973-020-10427-1
Ravey, M., and Pearce, E. M. (1997). Flexible Polyurethane Foam. I.Thermal Decomposition of a Polyether-Based, Water-Blown Commercial Type of Flexible Polyurethane Foam. J. Appl. Polym. Sci. 63, 47–74. doi:10.1002/(SICI)1097-4628(19970103)63:1<47::AID-APP7>3.0.CO;2-S
Shen, M.-Y., Kuan, C.-F., Kuan, H.-C., Ke, C.-Y., and Chiang, C.-L. (2021). Flame Retardance and Char Analysis of an Eco-Friendly Polyurethane Hyperbranched Hybrid Using the Sol-Gel Method. Sustainability 13, 486. doi:10.3390/su13020486
Tan, S., Abraham, T., Ference, D., and Macosko, C. W. (2011). Rigid Polyurethane Foams from a Soybean Oil-Based Polyol. Polymer 52, 2840–2846. doi:10.1016/j.polymer.2011.04.040
Xi, W., Qian, L., Chen, Y., Wang, J., and Liu, X. (2015). Addition Flame-Retardant Behaviors of Expandable Graphite and [bis(2-Hydroxyethyl)amino]-Methyl-Phosphonic Acid Dimethyl Ester in Rigid Polyurethane Foams. Polym. Degrad. Stab. 122, 36–43. doi:10.1016/j.polymdegradstab.2015.10.013
Xu, W., Wang, G., and Zheng, X. (2015). Research on Highly Flame-Retardant Rigid PU Foams by Combination of Nanostructured Additives and Phosphorus Flame Retardants. Polym. Degrad. Stab. 111, 142–150. doi:10.1016/j.polymdegradstab.2014.11.008
Yan, J., Xu, P. F., Zhang, P. K., and Fan, H. J. (2021). Surface-modified Ammonium Polyphosphate for Flame-Retardant and Reinforced Polyurethane Composites. Colloids Surfaces A Physicochem. Eng. Aspects 626, 127092. doi:10.1016/j.colsurfa.2021.127092
Yang, L., Ye, Z. B., Ai, L. H., Zeng, L. J., and Liu, P. (2020). Synergistic Flame Retardant Effect of Ammonium Polyphosphate and Aluminum Hydroxide on Polyurethane. Synthetic Mater. Aging Appl. 49 (5), 5. doi:10.1007/s11595-022-2562-7
Ye, T., and Li, J. (2016). Effect of Anion of Polyoxometalate Based Organic-Inorganic Hybrid Material on Intumescent Flame Retardant Polypropylene. Polym. Adv. Technol. 27, 1211–1219. doi:10.1002/pat.3786
Yimin, L., Chengle, W., and Juan, L. (2020). Improvement of Metal Caions in Polyoxometalate on Flame Retardant Efficiency of Polypropylene. J. Inorg. Mater. 35 (9), 1029–1033. doi:10.15541/jim20190529
Zeng, F., Zhao, Y., Meng, Y., Su, J., and Han, J. (2021). Study on Sol-Gel-Modified Ammonium Polyphosphate and its Application in the Flame-Retardant Polyurethane Composites. J. Sol-Gel Sci. Technol. 98 (3), 615–626. doi:10.1007/s10971-021-05526-w
Keywords: polyurethane, ammonium polyphosphate, phosphomolybdic acid, flame retardancy, residual carbon
Citation: Xu Z, Xu Z, Tao R, Mao L, Zhan J, Xiao J and Yu T (2022) Combustion and Thermal Properties of Flame Retardant Polyurethane Foam With Ammonium Polyphosphate Synergized by Phosphomolybdic Acid. Front. Mater. 9:944368. doi: 10.3389/fmats.2022.944368
Received: 15 May 2022; Accepted: 27 May 2022;
Published: 15 July 2022.
Edited by:
Wei Wu, City University of Hong Kong, Hong Kong SAR, ChinaReviewed by:
Yongqian Shi, Fuzhou University, ChinaCopyright © 2022 Xu, Xu, Tao, Mao, Zhan, Xiao and Yu. This is an open-access article distributed under the terms of the Creative Commons Attribution License (CC BY). The use, distribution or reproduction in other forums is permitted, provided the original author(s) and the copyright owner(s) are credited and that the original publication in this journal is cited, in accordance with accepted academic practice. No use, distribution or reproduction is permitted which does not comply with these terms.
*Correspondence: Jing Zhan, emhhbmppbmdAdXN0Yy5lZHUuY24=
Disclaimer: All claims expressed in this article are solely those of the authors and do not necessarily represent those of their affiliated organizations, or those of the publisher, the editors and the reviewers. Any product that may be evaluated in this article or claim that may be made by its manufacturer is not guaranteed or endorsed by the publisher.
Research integrity at Frontiers
Learn more about the work of our research integrity team to safeguard the quality of each article we publish.