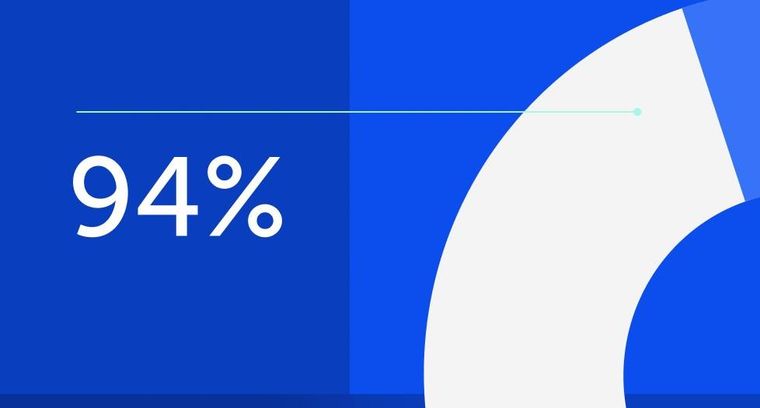
94% of researchers rate our articles as excellent or good
Learn more about the work of our research integrity team to safeguard the quality of each article we publish.
Find out more
ORIGINAL RESEARCH article
Front. Mater., 16 May 2022
Sec. Structural Materials
Volume 9 - 2022 | https://doi.org/10.3389/fmats.2022.871689
This article is part of the Research TopicApplication of Fiber and Composite Materials in Civil EngineeringView all 4 articles
The strengthening application of brick concrete recycled coarse aggregate (BCRCA) has become a “troublesome issue.” In this sense, an in-depth study on the strengthening method of BCRCA is needed. In order to improve the strengthening effect of BCRCA and perform the large-scale application of brick concrete waste, the strengthening method of BCRCA was investigated. Briefly, the performance of BCRCA was initially analyzed. Then, the pore characteristics of BCRCA were tested by CT scanning technology. The evaluation index of filling saturation was proposed. Finally, the BCRCA was strengthened by the negative pressure, and the influences of key parameters such as negative pressure, negative pressure time, negative pressure temperature, and stirring times on the strengthening effect were investigated. The test results showed that the best performance can be obtained by using the following parameters: negative pressure from −55 kPa to −80 kPa, the negative pressure time from 6 to 14 min, the negative pressure temperature from 40 to 80°C, and the stirring times from 1 to 4 times. Combined with the influence of negative pressure strengthening process parameters on filling saturation, it can be determined that a negative pressure of −75 kPa, a negative pressure time of 12 min, and a negative pressure temperature of 70°C with two times of stirring were the best negative pressure strengthening parameters. The unconfined compressive strength and indirect tensile strength reached 4.9 and 0.55 MPa, respectively, when the reinforced BCRCA was used for the cement-stabilized macadam. Therefore, the negative pressure strengthening process parameters determined in this study can achieve a good strengthening effect.
At present, the concrete materials made of recycled aggregate in proportion to replace natural aggregate have been widely used (Zaid et al., 2021; Ge et al., 2021; Meng et al., 2022; and Wei et al., 2022). The utilization of brick concrete recycled coarse aggregate (BCRCA) can reduce the production of natural aggregate and landfill disposals, and a variety of efforts have been made on it (Ding, 2016; Kisku et al., 2017). However, the BCRCA produced by the current technology usually presents defects such as lower apparent density, higher fracture index, and higher water absorption compared with natural coarse aggregate (Ferreira et al., 2011; Soares et al., 2014; and Gao et al., 2020). In addition, the application range of BCRCA is limited because of its poor physical and mechanical properties. Therefore, an effective strengthening method is needed to improve the performance of BCRCA and realize the large-scale utilization of BCRCA.
Currently, the reinforcement approaches of BCRCA are mainly divided into physical shaping and chemical strengthening. The main purpose of physical shaping is to remove the cement mortar attached to the surface of recycled aggregate by the mechanical strengthening method and the heating grinding method (Hu and Sha, 2012; Xiao et al., 2017; Hu et al., 2019; Wang R. J. et al., 2020; Liu et al., 2021). The mechanical strengthening method is to use the friction between the recycled aggregate particles or between the particles and the external instruments under the action of an applied load to remove the mortar from the surface of the recycled aggregate. The heating and grinding methods take advantage of the principle that the thermal expansion coefficients of hardened cement mortar differ from those of the aggregate. The hardened cement mortar wrapped around the surface is dehydrated and becomes brittle by heating the recycled aggregate, followed by striking and grounding it to obtain high-quality recycled aggregate. However, the mortar encapsulated inside the recycled aggregate is not completely removed by the physical shaping methods. Therefore, it is not sufficient and effective to improve the performance of BCRCA using the method of stripping mortar (Bai et al., 2020; Wang X. F. et al., 2020). The purpose of chemical reinforcement is to strengthen the wrapped mortar and primary aggregate, including chemical slurry or solution soaking, carbonation treatment, osmotic crystallization modification, and nanotechnology modification (Ding et al., 2016; Wang et al., 2017; Huang et al., 2020; Liang et al., 2020). In the method of carbonation treatment, calcium hydroxide and calcium silicate in the mortar can react with CO2 to form CaCO3 and silica gel, which can fill the pores and strengthen the aggregate (Ying et al., 2017; Tam et al., 2016; Yang J. C., 2020; Li et al., 2021). With water as the carrier, the permeation crystallization material can quickly penetrate the micro-cracks of the recycled aggregate and the mortar layer adhering to its surface and performing a condensation reaction (Kumar et al., 2019). At the same time, the products of the polycondensation reaction can penetrate the internal voids of the aggregate and react with it to produce a mesh-type inorganic polymer, which can effectively fill the pores of the aggregate. Cement-based diatomaceous earth and SiO2 are representatives of the nanomaterials with advantages of small size, high adsorption, high permeability, large specific surface area, and various active atoms (Xu et al., 2019; Song et al., 2021). It can improve the performance of recycled aggregate and increase the strength of the mixture. However, the reagents for these methods are expensive, which increases the cost of intensification. In addition, CO2 needs to be collected and sequestered, which is tedious in the process of carbonization, and there is no suitable carbonization equipment at this stage. In addition to the aforementioned reinforcement methods, Hu et al. (2019) compared the strengthening effects of the secondary mixing process with those of the conventional mixing process. The compressive and tensile strengths of the recycled aggregate concrete prepared by the secondary mixing process under the same conditions all increased to some extent, and the interface transition zone was denser. Therefore, the secondary stirring can effectively improve the mechanical properties of recycled concrete. Most of the previous studies are primarily focusing on the reinforcement of recycled concrete under a single condition, while little attention is paid to the strengthening effect of recycled aggregate. Moreover, at the present stage, there are limited reinforced treatment methods with properties of significant efficiency, low cost, and simple control, which restrict further development of reinforced recycled aggregate.
This article proposes a novel strengthening method under negative pressure and with an evaluation index—filling saturation. Through the basic performance test of aggregate and the CT scanning technology, the process parameters of this method are comprehensively determined, which is of great significance to improve the engineering applications of recycled aggregate and solve the problems of resource utilization of construction waste. The research results of this project will provide the theoretical and application foundation for the studies of reinforcing materials, say recycled aggregate, which will significantly promote the BCRCA recycling technology.
At present, the application of recycled brick and concrete coarse aggregate (BCRCA) is mostly limited to theoretical feasibility and rarely used in practical engineering. To realize the large-scale application of reinforced BCRCA in engineering, it is believed that the reinforced material should be economical and readily available. In this article, cement slurry is selected as the reinforcement material. Cement not only plays the main role of reinforcing materials but also helps increase the strength of BCRCA in the later stage.
In this article, the P.O 42.5 cement is supplied by China Shanshui Cement Group Limited. The performance indicators of the P.O 42.5 cement are shown in Table 1. After comparison and verification, all the testing indicators meet the specification requirements.
The BCRCA used in this study is provided by Shandong Pulvxiang Environmental Protection Technology Co., Ltd. The material yard is located at the demolition site in Jinan, Shandong. The site is shown in Figure 1.
It can be seen from Table 2 that the crushing value, water absorption, and the flat and elongated particle of BCRCA were relatively high, while the apparent density was relatively low. Therefore, BCRCA has the characteristics of low strength and high porosity.
The negative pressure strengthening equipment for BCRCA was independently developed based on previously reported studies (Liu 2018; Zhao et al., 2019; Liu 2020; Yang Z. Y., 2020). The test equipment is composed of three parts: test tank, pump, and air pressure display meter, which are connected by a high-strength hose with good sealing. This test equipment is shown in Figure 2. Among them, the test tank is made of acrylic, rubber, and stainless steel materials, which can bear more than 50 kg of weight and ±5 MPa of pressure. The air pump is a high-pressure electric air pump produced by Guangdong Berson with a maximum negative pressure state of 1 MPa approximately.
The negative pressure strengthening test is divided into the immersion control group and the negative pressure strengthening test group. The negative pressure strengthening test is divided into the following 5 parts: 1) A number of BCRCA and natural stones with particle sizes of 10–20 mm were selected. It was ensured that the quality difference range of different aggregate is less than 5% and that there is no specific difference in shape. 2) According to the bonding status of the cement slurry and recycled material, the water-to-cement ratio was initially estimated to be from 0.5 to 2.5 and the approximate water-to-cement ratio range was obtained as 1.4–2.2. The five water-to-cement ratios for this test were determined based on engineering experience: 1.4, 1.6, 1.8, 2.0, and 2.2. 3) The cement and water were poured into the cement slurry mixer separately to prepare the cement slurry. Then, the cement slurry was added into the negative pressure strengthening equipment to cover one-third of the aggregate. Meanwhile, the quantity of the cement slurry was recorded to ensure that the amount of the cement slurry added to the two experimental aggregate materials was equal. 4) The air pump was turned on at different temperatures after a period of time of performing the negative pressure, and the number of stirrings was increased. It was allowed to stand for 20–30 min until the cement slurry does not fall off. The ranges of negative pressure, negative pressure temperature, stirring time, and stirring times are 0–100 kPa, 0–80°C, 0–15 min, and 1–4 times, respectively. 5) At the end of the test, the aggregate was left outdoors for 24 h to obtain the reinforced BCRCA. The test results were characterized by crushing value, water absorption, and apparent density tests. The experimental results are shown in Figure 3.
First, the pore characteristics of BCRCA can be observed by the microscopic analysis method of CT scanning, as shown in Figure 4. Then, according to the depth of the cement slurry immersed in the pores of different sections, the evaluation index of filling saturation is proposed. Finally, the optimal strengthen technology parameters can be determined by the crushing value, water absorption, and apparent density. In this experiment, the decrease in crushing value, water absorption, and increase in apparent density is all due to the fact that in the process of filling the pores of BCRCA, the cement slurry will clog the pores of aggregate and increase the internal stress conduction. Therefore, it is proposed that the filling saturation index can reflect the filling degree of the slurry.
FIGURE 4. Scanning graph of the pore characteristics of recycled coarse aggregate at 100 times magnification. (A) Close pore, (B) open pore, and (C) connect pore
Filling saturation refers to the ratio of the depth of the cement slurry entering the pores to the depth of the pores. Filling saturation reflects the filling degree of the cement slurry. In this experiment, one aggregate was selected for CT scanning. As can be seen from Figure 5, the aggregate contains an opening pore with a length of 87 um. After negative pressure strengthening, a CT scan was performed on the same part of the aggregate. The 87 um open pore of the aggregate was filled with approximately 36 um of cement slurry. Therefore, when the pore length is 87 um and the filling depth is 36 um, the filling saturation is calculated to be 41.4%.
Negative pressure intensification equipment was used to conduct the performance intensification test of the BCRCA, determining the effects of five factors: water-to-cement ratio, negative pressure, negative pressure time, negative pressure temperature, and stirring times. The influence range of the five factors can be determined by controlling the variables. The initially proposed process parameters such as negative pressure, time, temperature, and stirring times were taken as the median values of each influencing factor, which were −50 kPa, 7.5 min, 45°C, and 3 times, respectively. The experiments were conducted in accordance with the method of sequential control variables and were able to obtain a range of parameters for each factor.
It can be seen from Figure 6 that when the water-to-cement ratio was 1.8, the crushing value reached the lowest value of 28.8%. In the range of the water-to-cement ratio from 1.5 to 1.8, the declining tendency of the crushing value leveled off. When the water-to-cement ratio was in the range of 2.2, the crushing value fluctuated around 29%. The changing trend of the water absorption rate was similar to the variation of the crushing value. The lowest point appeared in the interval of 1.8. At this time, the water absorption rate was 8.3%. In the interval of 2.2, the water absorption rate rebounded. The apparent density reached 2,648 kg/m3 when the water-to-cement ratio was 1.8. When the water-to-cement ratio was 1.8, the water absorption and crushing value were in the best state and decreased slightly in the subsequent interval. After the careful and comprehensive comparative analysis, the performance index was better than that of unreinforced BCRCA with the water-to-cement ratio of 1.8. Therefore, the optimal water-to-cement ratio for the subsequent experiments is 1.8.
It can be seen from Figure 7 that with the increase in negative pressure, the change of the crushing value generally showed a decreasing trend. When the negative pressure varied in the range from −50 kPa to −70 kPa, the crushing value dropped from 30.8 to 28.3%. The overall change in the water absorption rate showed a decreasing trend. Moreover, when the negative pressure changed in the interval of −30 kPa∼−70 kPa, the decreasing trend was the most obvious. At this time, the water absorption rate decreased from 9.1 to 7.7%, with a total decrease of 15.4%. The overall change in the apparent density showed an increasing trend. The rising trend was the most obvious when the negative pressure varied in the interval of −50 kPa to −70 kPa. At this time, the apparent density rose from 2,557 kg/m3 to 2,715 kg/m3, with a total increase of 6.2%. To ensure the accuracy of the test and expand the test range, the final test range of negative pressure should be locked between −55 kPa and −80 kPa. Under the action of negative pressure in this range, the crushing value, water absorption rate, and apparent density of BCRCA changed more significantly.
It can be seen from Figure 8 that with the increase in negative pressure time, the crushing value and water absorption showed a decreasing trend, while the apparent density showed an increasing trend. Within the variation of negative pressure time, the apparent density reached 2,581 kg/m3 at 11 min and the crushing value and water absorption presented the best effects at 12 min. When the pressure was stabilized within 6–14 min, the impact of the strengthening effect was more obvious with a significantly improved performance. Therefore, the range of the negative pressure time is from 6 min to 14 min.
It can be seen from Figure 9 that the crushing value, water absorption, and apparent density all improved significantly when the temperature was increased. When the temperature was 60°C, the water absorption rate dropped to 9.3%. When the temperature increased to 70°C, the crushing value and apparent density achieved the best strengthening effects, which were 29.9% and 2,576 kg/m3, respectively. Therefore, the range of the negative pressure temperature is considered to be from 40 to 80°C.
It can be seen from Table 3 that with the increase in stirring times, the crushing value and water absorption rate showed a trend of decreasing first and then increasing with the peak appearing at the second stirring. Compared with a single stirring, the crushing stone value and water absorption decreased by 4.5 and 7.0%, respectively. The apparent density increased with the increase in stirring times. The change in apparent density slowed down after the third stirring. Therefore, the performance with two times of stirring is the best.
The best state of a single parameter was selected from Figures 7–9 and Table 3 as the initial process parameters for CT scanning (negative pressure −70kPa, negative pressure temperature 70°C, negative pressure time 11 min, stirring twice). For example, when the negative pressure changes, the negative pressure temperature is set to 70°C, and the negative pressure time is set to 11 min with two times of stirring. The optimal negative pressure is determined at the maximum filling saturation. The negative pressure was used as a fixed parameter for the subsequent experiments. The negative pressure temperature, negative pressure time, and stirring times were changed in turn to determine the optimal process parameters. In total, 20 cross sections of the samples from the experimental group and the control group were selected, and the average filling saturation of each group was recorded. The data are shown in Figure 10 and Table 4.
It can be seen from Table 4 and Figure 10 that with the increase of negative pressure temperature, the filling saturation showed a trend of increasing and then decreasing. The maximum value appeared when the negative pressure temperature was 68°C. The increase in the filling saturation was 66.5% compared to the negative pressure control group, and the change was 54.6% compared to that at the negative pressure temperature of 56°C. The change range gradually decreased after 70°C. Therefore, 70°C should be set as the optimum negative pressure temperature.
With the extension of negative pressure time, the filling saturation gradually increased. When the negative pressure time was in the range from 10 to 12 min, the filling saturation changed significantly and the maximum value appeared at 12 min. The increase in the filling saturation was 50.2% in comparison with that of the negative pressure control group. The increase in the filling saturation was 23.3% compared with the value at a negative pressure time of 10 min. The change range showed a downward trend after 12 min. Therefore, 12 min should be set as the optimal negative pressure time.
Compared with the negative pressure control group, the increase in the filling saturation was 107.4% at the negative pressure of −75 kPa, and the change in the filling saturation was 3.5% compared with that at the negative pressure of −70 kPa. There was a downward trend observed at −75 kPa. According to the changing laws of crushing value, water absorption, and apparent density in Figure 7, the value of −75 kPa can be set as the optimal negative pressure. At the same time, compared with the negative pressure control group, the filling saturation during the second stirring increased by 28.8% and the filling saturation did not change after the second stirring. Therefore, it can be determined that two times of stirring should be used in the negative pressure strengthening process.
In the negative pressure strengthening method, combined with the effects of parameters on crushing value, water absorption, and apparent density, the four types of technological parameters can be determined. It can be concluded that BCRCA presents the best negative pressure reinforcement effect with the following processing parameters: negative pressure of −75 kPa, negative pressure time of 12 min, negative pressure temperature of 70°C, and two times of stirring.
Four grades of aggregate were used for the grading design with the ratio of G1 (20–30 mm):G2 (10–20 mm):G3 (5–10 mm):G4 (0–5 mm) being 17:23:23:37. The grading curve is shown in Figure 11.
The specimens with 8, 9, 10, 11, and 12% of moisture contents were selected for the compacting experiments, and the curves of moisture content–dry density were plotted to determine the optimum moisture content and the maximum dry density. The results of the compaction test are shown in Figure 12.
According to Figure 13 and Figure 14, the representative value of the 7 days’ unconfined compressive strength was 2.3 MPa, and the indirect tensile strength of unreinforced aggregate was 0.28 MPa. After 90 days, the hydration of the cement gradually slowed down and the strength change of the concrete became stabilized with the unconfined compressive strength and indirect tensile strength reaching 3.5 MPa and 0.41 MP, respectively. After strengthening the performance of BCRCA, the representative values of unconfined compressive strength and indirect tensile strength after 7 days were 3.2 and 0.36 MPa, respectively, which were 39.1 and 28.6% higher than those without the strengthening. Moreover, the representative values of unconfined compressive strength and indirect tensile strength after 90 days were 4.9 and 0.55 MPa, respectively, which were 40.0 and 34.1% higher than those without the strengthening. All the experimental results had a 95% guarantee rate. As a result, the strengthening technology parameters under negative pressure can effectively improve the mechanical properties of the mixture.
In this study, the performance of BCRCA was reinforced by the negative pressure and its parameters were investigated by the BCRCA performance and the filling saturation. The unconfined compressive strength and indirect tensile strength of BCRCA before and after strengthening were evaluated, respectively. The main conclusions are as follows.
1. When the water-to-cement ratio is 1.8, the range of the negative pressure strengthening process parameters is determined as follows: the negative pressure is from −55 kPa to −80 kPa. The negative pressure time ranges from 6 min to 14 min. The negative pressure temperature is in range of 40°C–80°C. The stirring times are 1–4 times.
2. The effect of negative pressure on filling saturation is greater with a 107.4% increase compared to the control group. The effect of temperature and time under negative pressure on filling saturation is similar. The experiments values are improved by 50.4 and 66.5%, respectively. The effect of the number of stirring on the filling saturation is limited. The value after enhancement is only 28.8%, and no longer increases after three times of stirring.
3. The variations of the BCRCA crushing value, water absorption, apparent density, and filling saturation analysis are analyzed by the strengthening process parameters under negative pressure. The negative pressure of −75 kPa, negative pressure time of 12 min, negative pressure temperature of 70°C, and stirring times of 2 times are verified to be the optimal negative pressure strengthening parameters.
4. The unconfined compressive strength and indirect tensile strength reach 4.9 and 0.55 MPa, respectively, which increase by 40.0 and 34.1% compared with the unreinforced BCRCA. Therefore, the strengthening procedure parameters under the negative pressure determined in this study can achieve a good strengthening effect.
The raw data supporting the conclusions of this article will be made available by the authors, without undue reservation.
HL and ZZ: conceptualization and writing original manuscript preparation. HL, ZZ, and ZY: methodology. ZY, RW, MX, and ZZ: investigation. HL, ZY, and MX: data curation. ZZ, RW, and MX: writing review and editing. HL, ZY, and MX: visualization. ZZ and RW: supervision, project administration, and funding acquisition. All authors contributed to the article and approved the submitted version.
This research was supported by the National Key R&D Program of China (No. 2018YFB1600100), the Science and Technology Plan of Shandong Transportation Department (Nos. 2018B02-01, 2020B93, and 2019B63), the Natural Science Foundation of Shandong Provincial (No. ZR2020QE274), the Key Technology Research and Development Program of Shandong (Soft Science Project) (No. 2020RKB01602), and Doctor Graduate Scientific Research Ability Improvement Project of Beijing University of Civil Engineering and Architecture (No. DG2021012).
ZY was employed by the company Shandong Hi-speed Company Limited.
The remaining authors declare that the research was conducted in the absence of any commercial or financial relationships that could be construed as a potential conflict of interest.
All claims expressed in this article are solely those of the authors and do not necessarily represent those of their affiliated organizations, or those of the publisher, the editors, and the reviewers. Any product that may be evaluated in this article, or claim that may be made by its manufacturer, is not guaranteed or endorsed by the publisher.
Bai, G., Zhu, C., Liu, C., and Liu, B. (2020). An Evaluation of the Recycled Aggregate Characteristics and the Recycled Aggregate concrete Mechanical Properties. Construction Building Mater. 240, 117978. doi:10.1016/j.conbuildmat.2019.117978
Ding, H. B. (2016). Research on Performance Enhancement of Waste Concrete Aggregate Based on Wrap Slurry Technology. China J. Highw. Transp. 29, 36–42.
Ding, T., Xiao, J., and Tam, V. W. Y. (2016). A Closed-Loop Life Cycle Assessment of Recycled Aggregate concrete Utilization in China. Waste Management 56, 367–375. doi:10.1016/j.wasman.2016.05.031
Ferreira, L., de Brito, J., and Barra, M. (2011). Influence of the Pre-saturation of Recycled Coarse concrete Aggregates on concrete Properties. Mag. Concrete Res. 63, 617–627. doi:10.1680/macr.2011.63.8.617
Gao, D., Zhang, L., Zhao, J., and You, P. (2020). Durability of Steel Fibre-Reinforced Recycled Coarse Aggregate concrete. Construction Building Mater. 232, 117119. doi:10.1016/j.conbuildmat.2019.117119
Ge, P., Huang, W., Zhang, J., Quan, W., and Guo, Y. (2021). Mix Proportion Design Method of Recycled brick Aggregate concrete Based on Aggregate Skeleton Theory. Construction Building Mater. 304, 124584. doi:10.1016/j.conbuildmat.2021.124584
Hu, L. Q., and Sha, A. M. (2012). Performance Test of Cement Stabilized Crushed Clay Brick for Road Base. Mater. China J. Highw. Transp. 25, 73–79+86.
Hu, X. H., Xiao, J., Yang, H. P., Wu, C. F., and Zhang, J. S. (2019). Research on Chemical Strengthening Experimental of Recycled Coarse Aggregate. J. China Foreign Highw. 01, 256–260.
Huang, Q., Zhu, X. H., Xiong, G. Q., Wang, C. Q., Liu, D. S., and Zhao, L. (2020). Recycling of Crushed Waste clay brick as Aggregates in Cement Mortars: An Approach from Macro- and Micro-scale Investigation. Constr. Build. Mater. 274, 122068. doi:10.1016/j.conbuildmat.2020.122068
JTG E30, (2005). Test Methods of Cement and concrete for Highway Engineering. Beijing: Ministry of Transport of the People’s Republic of China.
JTG E42, (2005). Test Methods of Aggregate for Highway Engineering. Beijing: Ministry of Transport of the People’s Republic of China.
Kisku, N., Joshi, H., Ansari, M., Panda, S. K., Nayak, S., and Dutta, S. C. (2017). A Critical Review and Assessment for Usage of Recycled Aggregate as Sustainable Construction Material. Construction Building Mater. 131, 721–740. doi:10.1016/j.conbuildmat.2016.11.029
Li, L. K., Liu, Q., Ma, Z. C., and Peng, B. (2021). Research Progress on Properties of Recycled Concrete Aggregates by Carbon Dioxide Mineral Carbonation Curing. Therm. Power Generation 50, 94–103.
Liang, C. F., Du, X. M., Qiu, J. Y., and Gao, Y. Q. (2020). Research Progress on Modification Methods of Recycled Concrete Aggregate. China Concrete Cement Prod. 12, 87–91.
Liu, G. Q. (2018).Research on Technical of Industrial Waste gypsum Impedance Semi-rigid Base Cracking. Jinan: Shandong Jiaotong University. Master thesis.
Liu, H. Z. (2020).Research on the Effect of Strengthening Materials and Methods on the Properties of Recycled brick-concrete Coarse Aggregate. Jinan: Shandong Jiaotong University. Master thesis.
Liu, S., Shen, P., Xuan, D., Li, L., Sojobi, A., Zhan, B., et al. (2021). A Comparison of Liquid-Solid and Gas-Solid Accelerated Carbonation for Enhancement of Recycled concrete Aggregate. Cement and Concrete Composites 118, 103988. doi:10.1016/j.cemconcomp.2021.103988
Meng, T., Wei, H., Dai, D., Liao, J., and Ahmed, S. (2022). Effect of brick Aggregate on Failure Process of Mixed Recycled Aggregate concrete via X-CT. Construction Building Mater. 327, 126934. doi:10.1016/j.conbuildmat.2022.126934
Santha Kumar, G., Saini, P. K., Karade, S. R., and Minocha, A. K. (2019). Chemico-thermal Treatment for Quality Enhancement of Recycled concrete fine Aggregates. J. Mater. Cycles Waste Manag. 21, 1197–1210. doi:10.1007/s10163-019-00874-w
Soares, D., de Brito, J., Ferreira, J., and Pacheco, J. (2014). Use of Coarse Recycled Aggregates from Precast concrete Rejects: Mechanical and Durability Performance. Construction Building Mater. 71, 263–272. doi:10.1016/j.conbuildmat.2014.08.034
Song, X.-b., Li, C.-z., Chen, D.-d., and Gu, X.-l. (2021). Interfacial Mechanical Properties of Recycled Aggregate concrete Reinforced by Nano-Materials. Construction Building Mater. 270, 121446. doi:10.1016/j.conbuildmat.2020.121446
Tam, V. W. Y., Butera, A., and Le, K. N. (2016). Carbon-conditioned Recycled Aggregate in concrete Production. J. Clean. Prod. 133, 672–680. doi:10.1016/j.jclepro.2016.06.007
Wang, R., Yu, N., and Li, Y. (2020). Methods for Improving the Microstructure of Recycled concrete Aggregate: A Review. Construction Building Mater. 242, 118164. doi:10.1016/j.conbuildmat.2020.118164
Wang, X., Yang, X., Ren, J., Han, N., and Xing, F. (2021). A Novel Treatment Method for Recycled Aggregate and the Mechanical Properties of Recycled Aggregate concrete. J. Mater. Res. Technology 10, 1389–1401. doi:10.1016/j.jmrt.2020.12.095
Wang, Z. X., Yao, H., Li, Q. Y., and Guo, Y. X. (2017). Effect of Enhanced Processing Mode Properties of Recycled Coarse Aggregate on the Carbonation Resistance of Recycled Concrete. Concrete 09, 57–60.
Wei, D., Zhu, P., Yan, X., Liu, H., Chen, C., and Wang, Z. (2022). Potential Evaluation of Waste Recycled Aggregate concrete for Structural concrete Aggregate from Freeze-Thaw Environment. Construction Building Mater. 321, 126291. doi:10.1016/j.conbuildmat.2021.126291
Xiao, J., Wu, C. F., Zhen, Z. H., Tan, X. G., and Dong, W. J. (2017). Research on Performances of Cement Stabilized Brick and Concrete Recycled Aggregate Base. China J. Highw. Transp. 30, 25–32.
Xu, K. D., Wang, J. N., Li, Z. X., Ma, X. W., Niu, J. M., Yang, H., et al. (2019). Strengthening Mechanism of Nano SiC Modified Water Glass on Recycled Aggregate. China Concrete Cement Prod. 07, 91–95.
Yang, J. C. (2020). Effect of Recycled Aggregate of Waste Clay Bricks on the Properties of Grouting. Mater. Concrete. 04, 138–140.
Yang, Z. Y. (2020).Study on Negative Pressure Strengthening Technology and Process Parameters of Recycled Aggregate of brick and concrete. Jinan: Shandong Jiaotong University. Master thesis.
Ying, J. W., Meng, Q. J., and Xiao, J. Z. (2017). Effect of CO2 Modified Recycled Aggregate on Compressive Strength of Concrete. J. Building Mater. 20, 277–282.
Zaid, O., Zamir Hashmi, S. R., Aslam, F., and Alabduljabbar, H. (2021). Experimental Study on Mechanical Performance of Recycled Fine Aggregate Concrete Reinforced with Discarded Carbon Fibers. Front. Mater. 8, 481. doi:10.3389/fmats.2021.771423
Keywords: brick concrete recycled coarse aggregate, negative pressure strengthening, process parameters, micro-analysis, improve performance of aggregate
Citation: Liu H, Zhao Z, Yang Z, Wang R and Xu M (2022) Laboratory Investigation on Key Technological Parameters of Brick Concrete Recycled Coarse Aggregate Strengthened by Negative Pressure. Front. Mater. 9:871689. doi: 10.3389/fmats.2022.871689
Received: 08 February 2022; Accepted: 31 March 2022;
Published: 16 May 2022.
Edited by:
Xijun Shi, Texas State University, United StatesReviewed by:
Ping Duan, China University of Geosciences Wuhan, ChinaCopyright © 2022 Liu, Zhao, Yang, Wang and Xu. This is an open-access article distributed under the terms of the Creative Commons Attribution License (CC BY). The use, distribution or reproduction in other forums is permitted, provided the original author(s) and the copyright owner(s) are credited and that the original publication in this journal is cited, in accordance with accepted academic practice. No use, distribution or reproduction is permitted which does not comply with these terms.
*Correspondence: Meng Xu, MzAzODk3OTgzQHFxLmNvbQ==
Disclaimer: All claims expressed in this article are solely those of the authors and do not necessarily represent those of their affiliated organizations, or those of the publisher, the editors and the reviewers. Any product that may be evaluated in this article or claim that may be made by its manufacturer is not guaranteed or endorsed by the publisher.
Research integrity at Frontiers
Learn more about the work of our research integrity team to safeguard the quality of each article we publish.