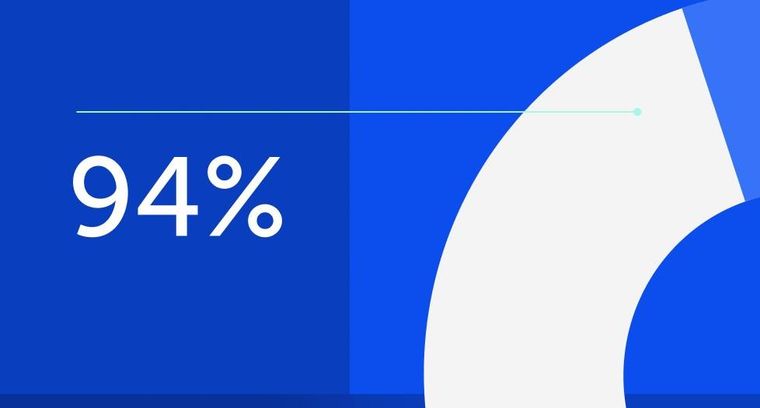
94% of researchers rate our articles as excellent or good
Learn more about the work of our research integrity team to safeguard the quality of each article we publish.
Find out more
ORIGINAL RESEARCH article
Front. For. Glob. Change, 27 April 2022
Sec. Forest Management
Volume 5 - 2022 | https://doi.org/10.3389/ffgc.2022.814049
This article is part of the Research TopicWorldwide Status of Wood Protection in ServiceView all 5 articles
For nearly 200 years wooden railway sleepers are impregnated with creosote. After initially using vacuum pressure processes for impregnation, empty-cell processes have been developed quickly and are used until today. Because of political developments and its alarming properties against human health and environment the use of creosote is already restricted to certain industrial and commercially used products and will probably be banned on the European market and elsewhere in the near future. Today, most of the sleepers in track are concrete sleepers, but wooden sleepers are still essential for particular applications such as tracks with narrow curve radii, mountain tracks with uneven underground conditions and low ballast bed thicknesses, for switches, for railway bridges and for shunting stations. Without a successor product, wooden sleepers have to be installed either again without adequate protection against wood destroying organisms or will possibly be replaced by sleepers made from alternative materials like concrete, steel or polymers. The Fürstenberg-System-Sleeper, which combines a mechanical pre-treatment (incising), a double impregnation of sleepers including an alternative oily wood preservative and a water-borne copper salt as well as a modernized quality control shall on the one hand serve as an alternative to creosoted sleepers and on the other hand ensure future use of wooden sleepers in track superstructure. Incising reduced the formation of checks regarding their length, width, and depth in sleepers made from European beech (Fagus sylvatica L.) until they are sufficiently seasoned for impregnation. A decrease of the seasoning speed was not observed. During seasoning, the average global moisture content (MC) as well as the local MC showed hardly any differences between incised and not incised sleepers. Additionally, incising showed no influence on the dimensional stability, which would have reduced the number of sleepers being culled based on excessive deformation. Furthermore, positive effects on preservative retention and penetration were observed, where incising doubled the penetration depth up to over 30 mm and increased the mean retention from 46.5 to 72.0 kg/m3. During double impregnation with the water-borne preservative first and the oily preservative afterward, it became evident, that a gross weight of at least 950 kg/m3 was needed for penetrating the peripheral area of the sleepers to achieve an additional homogenous envelope treatment during the second impregnation with an average retention of approximately 30 kg/m3.
The history of wooden railway sleepers as part of the track superstructure is as old as the railroad itself. During the beginning of the European railroad industry different sleeper types (single supports, long sleepers, and cross ties) made from different raw-materials (natural stone, wood, or iron) have been in direct competition. At the end of the 18th century the cross tie made from wood won the competition against the other sleeper-types and replaced those nearly completely (Schramm, 1952). The first installed sleepers in Europe were primarily made from Oak (Quercus spp.) with a high percentage of heartwood. Due to the increasing need of wooden sleepers and the low availability of sleepers made from Oak, the industry had to fall back on sleepers made from Scots pine (Pinus sylvestris L.) and Beech (Fagus sylvatica L.). Based on the low natural durability of both untreated wood species, the service life of the sleepers was between 6 and 8 years (Scots pine) and 2.5 and 5 years (Beech) and therefore not satisfactory (Mörath, 1956). At the end of the 18th century, the conservation of wooden sleepers by impregnation, had been started. To enhance the life span, creosote, a distillate of coal tar, has been used for more than 150 years (Pfabigan and Reitbauer, 2020). At the beginning, creosote has been inserted into the wooden structure using full cell processes.
A full cell process essentially consists of a combination of vacuum and pressure. Inside a closed autoclave, the wood is exposed to a vacuum phase. Afterwards, under maintaining the vacuum, the autoclave is flooded with the preservative and an excessive liquid pressure is applied. For creating a dry surface, an additional post vacuum phase can be implemented at the end of the process (Leiße, 1992; Figure 1). Using full cell processes resulted in high consumptions of creosote (approximately 277 kg/m3 for Beech and Pine sleepers and 78 kg/m3 for sleepers made from Oak, Schramm, 1952) and therefore exceeded significantly the requested amount, necessary for protecting the wood against wood destroying organisms (Broese van Groenou, 1983). In 1902, the impregnation process developed by Rüping was the first empty cell process, which was able to control the inserted amount of creosote to a certain extent (Broese van Groenou, 1983). At the beginning of a Rüping process, the wood is exposed to a preliminary air pressure, which compresses the present air inside the porous wooden structure. The creosote is then fed into the treatment cylinder against the existing air pressure. Afterward, an excessive liquid pressure is applied, whose duration and intensity are depending on the wood species and its dimension. While decompressing to atmospheric pressure, the compressed and trapped air inside the porous wooden structure causes a removal of excessive wood preservative, leaving only coated empty cell walls. To support the exiting air, an additional post vacuum phase is applied (Figure 1). Based on a variation of intensity and duration of air and liquid pressure the retention of creosote can be controlled and reduced to less than 100 kg/m3. Shortly after the invention of the Rüping process, another empty cell process was developed and patented by Lowry (1906). Unlike the Rüping process, the atmospheric pressure is used as air pressure. The hot creosote is fed into the cylinder right after starting the process and an excessive liquid pressure is directly applied. Afterwards, also a post vacuum phase is applied to support the compressed air exiting the porous wooden structure and removing excessive wood preservative (Figure 1). Ongoing research to optimize the impregnation quality led to the introduction of the improved Rüping process by the German Railways (Deutsche Bahn) in 1966. The sleepers were pre-conditioned in hot creosote. This was carried out directly after the air pressure phase/filling of the impregnation cylinder with creosote. With the pressure remaining unchanged, the sleepers were heated together with the creosote at more than 100°C for 1–2 h (Broese van Groenou, 1983). Investigations by Schulz (1987) regarding the temperature profile inside the impregnation vessel and inside the wood during the impregnation of Beech sleepers with creosote led to a further improvement of the impregnation process. Due to its simple feasibility the Rüping process is still used today (DIN 68811, 2007) as the standard operating procedure for the impregnation of railway sleepers with creosote. According to DIN 68811 (2007), sleepers made from Oak and Pine need to be impregnated using the single, improved Rüping process. Beech, on the other hand, is impregnated using the improved double Rüping process (Figure 1).
Figure 1. (1) Diagram of a full cell process with an optional post vacuum with (A) pre-vacuum, (B) flooding the autoclave under maintenance of the vacuum, (C) released vacuum and increased liquid pressure, (D) maintenance of liquid pressure, (E) released liquid pressure and removing of the preservative, and (F) optional final vacuum; (2) Diagram of a Rüping process with (A) air pressure, (B) flooding the autoclave under maintenance of the air pressure, (C) increase of the liquid pressure, (D) maintenance of the liquid pressure, (E) released liquid pressure and removing of the preservative, and (F) required post vacuum; (3) Diagram of a Lowry process with (A) flooding the autoclave with preservative, (B) increase of the liquid pressure, (C) maintenance of the liquid pressure, (D) released liquid pressure and removing of the preservative, and (E) required post vacuum; (4) Diagram of an improved double Rüping process with (A) air pressure, (B) flooding the autoclave under maintenance of the air pressure and pre-heating of at least 150 min, (C) increase of the liquid pressure, (D) maintenance of the liquid pressure, (E) released liquid pressure and removing of the preservative, (F) atmospheric pressure of at least 30 min, (G) second air pressure, (H) applied liquid pressure, (I) second liquid pressure (twice as long as first liquid pressure), (J) released liquid pressure and removing of the preservative, and (K) required post-vacuum.
Today’s use of creosote as a wood preservative is restricted to certain industrial and commercially used products based on its alarming properties against human and environment (REACH, 2006). Current political developments in Europe show that the use of creosote for impregnation of wooden products, is accepted less and less. This also includes railway sleepers. A complete ban of creosote on European level will certainly come, but the final date has not been determined, yet. The requirements towards an adequate substitute product are high, since creosote has excellent properties like its toxicity against wood-destroying organisms, its water repellence and low corrosiveness to metal fasteners. Alternatives regarding creosote as wood preservative are available like for example pentachlorophenol or copper naphthenate, which are both used in the United States of America for the preservation of wood in heavy duty applications. In case of Europe, pentachlorophenol hasn’t been used for decades and copper naphthenate is not permitted by now in the European Union, but is under review for registration. At the moment, further alternative oily preservatives are used in the EU. All contain copper hydroxide as the primary active ingredient and also organic acid co-solvents (Brient et al., 2020).
Despite the fact, that today the majority of sleepers in track are concrete sleepers, wooden sleepers are still essential for particular applications such as tracks with narrow curve radii, mountain tracks with uneven underground conditions and low ballast bed thicknesses, for switches, for railway bridges and for shunting stations, based on their excellent properties (light weight, good elastic behavior, and simple handling in tight spaces; Pfabigan and Reitbauer, 2020).
A possible ban of creosote would have major consequences for the railway industries, based on the fact, that without a successor product, wooden sleepers have to be installed either again without adequate protection against wood destroying organisms or will more likely be simply replaced by sleepers made from alternative materials like concrete, steel or polymers.
In order to maintain wooden sleepers as a component of the track superstructure an alternative product to the creosoted wooden sleeper is urgently sought.
The System-Sleeper, as alternative for creosote treated sleepers, uses the principles of the wooden sleeper used for centuries and combines them to a system based on three innovative aspects: (1) mechanical pre-treatment by incising, which had never been applied for railway sleepers in Europe before (2) in case of Beech sleepers a double impregnation using first a water-borne preservative and afterwards an alternative wood preservative based on natural oils for an additional envelope treatment and (3) a modernized concept of quality control, which ensures the traceability of each sleeper during its production process, recording moisture content (MC) before impregnation, the used impregnation process and the average preservative retention of the batch.
Incising is a mechanical pre-treatment of wood, where incisions are pressed into the surfaces by knives running in an axial direction. Incising pattern, incision depth and width depend on the wood species and the dimension of the processed product. While in case of railway sleepers, large knives are usually used at wide spacing (Morrell and Winandy, 1987), the knife size as well as the distance between the individual incisions decreases with smaller product dimension. Incising is used to improve the penetration of wood preservatives, to increase the drying speed and to minimize checking of the wood (Franciosi, 1956; Morris et al., 1994). A reduction in check formation can improve the product quality and thus extend the service life. The number of sleepers that cannot be used by the customer due to check formation (checks due to drying) developing before impregnation shall be reduced by the use of incising. Large checks that develop in service in the track bed can also be reduced. Loss of strength, weakening of the holding force of fasteners, but also entry ports for wood-destroying organisms are thus reduced (Evans, 2016). Despite the positive effects on the check formation during seasoning (especially Beech sleepers) found by Harkom (1932) and Franciosi (1956), incising as a mechanical pre-treatment did not prevail in Europe as standard procedure. Incising can also influence the penetration of wood preservatives by increasing the transverse surfaces of the treated product. The penetration of fluids in axial direction is much more effective than in radial and tangential direction. Thus, there is an improvement in penetration in the area of the incision (Morris et al., 1994; Morrell et al., 1998). This results in a better penetration and distribution of the preservatives, especially in refractory wood species. With regard to the penetration of alternative oily wood preservatives for the impregnation of railway sleepers, the influence of incising has not been further investigated by now in European wood species.
Creosote as a wood preservative combines high toxicity with hydrophobicity of the surface, which provides additional moisture protection of the sleepers. The double impregnation of Beech sleepers is intended to achieve exactly this effect. Beech is not durable, and therefore assigned to durability class 5 (DC5, EN 350, 2016). Therefore, deep penetration of the entire sleeper volume is necessary to ensure sufficiently high protection against wood-destroying organisms. A complete penetration shall be achieved using a water-borne wood preservative. For hydrophobation and to additionally increase the efficacy of the peripheral area against wood-destroying organisms, an alternative wood preservative based on natural oils is applied to the sleeper in a second impregnation step.
The System- Sleeper includes incising, a type of mechanical pre-treatment that has been used for years outside Europe for railway sleepers made of different types of wood. In order to re-investigate and clarify the positive effect of incising on Beech sleepers, the Fürstenberg-THP GmbH was cooperating with the Department of Wood Biology and Wood Products at the University of Goettingen evaluating the following aspects:
• Drying speed until requested degree of seasoning is reached.
• Moisture distribution within the sleepers until fiber saturation is reached.
• Formation of checks during seasoning.
• Dimensional stability during seasoning.
• Penetration depth and retention of an alternative oily wood preservative.
In the case of a double impregnation with a water-borne preservative first and subsequently with an alternative preservative based on natural oils, it is not only the time of the first impregnation that is decisive. According to the customer’s standard or specification, this is mainly regulated by the fiber saturation, where the wood is considered ready for impregnation. Since the second impregnation is intended to achieve additional hydrophobic properties as well as an increased efficacy against wood destroying organisms, it was important to determine the optimum time for the impregnation with the oily preservative in order to achieve the required retention and distribution of the protective agent in the fringe area of the sleepers.
Ten freshly cut Beech (F. sylvatica L.) sleepers (2,600 mm × 260 mm × 160 mm) with an average gross weight (=raw density) of 932 kg/m3 were divided into two specimen collectives to investigate the influence of incising on drying and check formation. Collective 1 was mechanically pre-treated and received incisions with a length and depth of 20 mm and a width of 3 mm, while collective 2 remained untreated. Monthly, the global MC of the sleepers was gravimetrically determined. Therefore, the sleepers were weighed to the nearest 0.1 kg. From the current weight, the raw density (analogous to the so-called “gross weight” according to DIN 68811, 2007) of the sleepers was calculated. Based on an average normal raw density of Beech of 710 kg/m3 (corresponding to an average dry density of 634 kg/m3) according to EN 350 (2016), the current global wood MC of the sleepers was calculated according to Eq. 1.
MCSleeper = Global moisture content of the sleeper (%)
ρf = Raw density wet (kg/m3)
ρ0 = Oven-dry density of Beech (kg/m3) = 634 kg/m3
VSleeper = Sleeper volume = 0.10816 m3
Additionally, the local MC of the sleepers was continuously determined and recorded at nine previously defined positions using data loggers (Materialfox, Scanntronik, Zorneding) according to the electrical resistance principle. To avoid measuring the MC in the possibly existing red heartwood, usually located in the center of the sleeper cross section or on the bottom of the sleeper, the depth of the holes and the distance to the sleeper side were varied, ensuring the measurement of only sapwood. Figure 2 shows the distances of the measuring points to the end grain, to the outer side of the sleeper and the installation depth. Stainless steel screws acted as electrodes for measuring the local MC. Previously drilled holes in the head of the screw served as a plug input for connecting the data logger. After the screws were driven into the holes for a few millimeters, the holes were sealed with silicone and the data logger cables were connected to the screws using banana plugs. The connection was additionally sealed watertight using heat-shrink tubes.
The MC was calculated using resistance characteristics for Beech according to Brischke and Lampen (2014).
Monthly, the development of the 10 largest checks was evaluated on the surface of the remaining “free” sleeper section, until a raw density of ≤800 kg/m3 was reached. The length, width and depth of the checks in millimeters were measured using a folding ruler and a feeler gauge. For later comparison of check development during seasoning, a classification system was defined, dividing check length, width and depth into five categories (Table 1).
In order to investigate the influence of incising on the penetration depth and retention of an alternative oily preservative, test specimens of 40 (ax.) mm × 40 mm × 80 mm were made from defect free Beech and afterwards sealed from five sides in two steps (SIKA Unitherm Top W & SIKA PU sealing compound). The unsealed radial surface (40 mm × 40 mm) was left untreated in the first collective (collective 1), while in collective 2 a single incision [20 mm × 20 mm × 3 mm (L × D × W)] was pressed in centrally. After following impregnation with a water-borne, chromium free, copper-based wood preservative in a vacuum/pressure process (60 min −850 mbar, 120 min 8 bar), the collectives 1 and 2 were each divided into groups of 10 test specimens and dried to different target gross weights (1,100; 1,000; 950; 900; 850; and 800 kg/m3).
After reaching the target gross weights, the test specimens were impregnated with the alternative oily wood preservative, which is based on a natural hydrophobic carrier substance in combination with copper hydroxide and an organic co-biocide. For impregnation, a Rüping process (air pressure 20 min 3 bar, oil pressure 100 min 8 bar, post-vacuum -800 mbar approx. 720 min) was used. Finally, the retention in kg/m3, as well as the penetration of the oily preservative was determined on split test specimens. Therefore, the specimens have been split completely in the direction of the incision and the penetration depth of the alternative oily wood preservative has been measured.
Whether freshly cut Beech sleepers show distortions during seasoning is not directly evident in the beginning of the examination. A direct comparison of incised and standard sleepers can therefore lead to misleading interpretations due to non-appearance of deformations. Therefore, only incised sleepers were included in this examination. For evaluating the possible effect of incising on the dimensional stability during seasoning, 700 freshly sawn Beech sleepers (2,600 mm × 260 mm × 160 mm) were mechanically pre-treated by incising the narrow as well as the broad sides of each sleeper. Afterward, the sleepers were stacked and stored outside according to DIN 68811 (2007). After reaching the requested gross weight of 800 kg/m3, the sleepers were examined visually for occurring deformation. Sleepers with deformation were sorted out for further evaluation using the parameter given by the technical delivery conditions for track and cross ties from the Austrian Federal Railways (ÖBB; ÖBB Infra, 2017; Table 2).
Table 2. Accepted tolerances given by the Austrian Federal Railways regarding the deformation of Beech sleepers.
The dimension of the occurring spring, bow and twist were measured using a straightedge and a folding ruler. To measure bow and spring, the straightedge was placed in centered position on the upper and narrow sides of the sleeper and the rise was measured using the folding ruler. The twist was measured by placing the straightedge diagonally on the upper side of sleepers and calculating the difference of both rises from the diagonals.
To investigate the influence of the gross weight of impregnated Beech sleepers using a double impregnation, 36 Beech sleepers with an average gross weight of 786 kg/m3 were first impregnated with a water-borne wood preservative in a vacuum/pressure process (180 min −950 mbar, 480 min 9 bar). After impregnation, the sleepers were divided into six groups of similar average gross weight (kg/m3) and were stacked in accordance with DIN 68811 (2007) for seasoning outdoors. Six different target gross weights were defined as starting points for a 2nd impregnation of the sleepers with the alternative oily preservative. The sleeper collectives were then weighed weekly in bundles of six to monitor the average gross weight. When a bundle reached the previously defined gross weight, the respective collective was prepared for impregnation. For this purpose, all sleepers were first weighed individually in order to determine the subsequent retention of the oily preservative. Impregnation of the sleepers was carried out using a Rüping process (air pressure 20 min 3 bar, oil pressure 100 min 8 bar, and post-vacuum −800 mbar approx. 720 min). After impregnation and weighing, the sleepers were cut at a distance of 30, 80, and 130 cm from the end of the sleeper and the penetration of the alternative oily preservative was visually evaluated.
The moisture monitoring of Beech sleepers in standard dimensions with and without incising showed that the incising pattern used in this test setup had no significant influence on the drying rate. The required degree of seasoning for impregnation was not reached faster for sleepers with incising. The average global MCsleeper showed hardly any differences between mechanically pre-treated and untreated sleepers. Coincidently, the electrically measured local wood MC did not differ significantly between the collectives. In the first half of the drying period, the electrically determined mean wood MC of both sleeper collectives was clearly below the gravimetrically determined mean global MC of the sleepers. In the second half of the drying period, the electrically determined wood MC exceeded the mean global MC by several percent points. A clear wood MC gradient between the individual measurement points, even though placed at different measuring depths and distances from the end grain, did not occur for either of the two sleeper collectives (Figures 3, 4).
Figure 3. Electrically determined mean local moisture content (MC) at measuring points S1 to S9, mean gravimetrically determined global MC, and mean raw density of sleepers without incising during seasoning.
Figure 4. Electrically determined mean local moisture content (MC) at measuring points S1 to S9, mean gravimetrically determined global MC, and mean raw density of sleepers with incising during seasoning.
Incising positively affected the formation of checks in Beech sleepers. Already during the first evaluation at the beginning of the test, sleepers without incising showed comparatively longer checks. While there was an increase in the check length in sleepers without incising during seasoning, sleepers with incising showed hardly any changes in check length. The same applied to check widths and check depths. Sleepers without incising showed more, wider, and deeper checks during the whole evaluation period. Sleepers with incising also showed an increase in check width and check depth. However, this was significantly smaller compared to non-incised sleepers (Figure 5).
Figure 5. Check length, width and depth (mm) in Beech sleepers with and without incising at the start and after 32 weeks of seasoning.
The positive effect of incising on the check performance of sleepers is exemplarily shown in Figure 6. While the sleeper without incising (S) showed already clearly recognizable checks on the surface at the beginning of seasoning, larger checks on the sleeper with incising (I) were only visible at the end grain. During 32 weeks, the sleepers reached the required degree of seasoning for later impregnation and the checks in the non-perforated sleeper top side had increased significantly in length, width and depth. The sleeper with incising pattern showed an enlargement of the checks only at the end grain.
Figure 6. Examples of positively influenced check performance due to incising of Beech sleepers [n = 5 for both incised (I) and not incised sleepers (S)] between 13.02.2018 (left) and 07.11.2018 (right).
After the evaluation of the 700 incised Beech sleepers, 95% of the sleepers were sound and showed visually no bow, spring or twisting, or the deformation did not exceed the specified tolerances. 5% of the sleepers were deformed to an extent, that they were selected for more detailed investigations (n = 40). A more detailed evaluation of the deformation showed that 2% of the sleepers exceeded the limit value with regard to deformation by twisting and 2% by bow. Only 1% of the sleepers showed an excessive curvature of the narrow side (spring; Figure 7).
Figure 7. Distribution of the different deformation types of the evaluated Beech sleepers (n = 700).
Incising had a positive effect on the penetration depth and solution uptake of the alternative oily preservative for test specimens on laboratory scale. Differently selected gross weights, however, had no influence on penetration and solution uptake. The specimen collectives without incising all showed a penetration depth between 10 and 15 mm. The different gross weights (moisture contents) did not influence the penetration depth (Figure 8). The specimen collectives with incising showed a penetration of the wood preservative twice as deep across all gross weights. Again, the penetration depth was not influenced by the different gross weights (Figure 9).
Figure 8. Penetration depth of an alternative oily preservative in mm in specimens without incising.
While the mean retention at all gross weights for specimens without incision was 46.5 kg/m3, it was 72.0 kg/m3 for specimens with incision (Figures 10, 11).
Figure 10. Solution uptake of an alternative oily preservative in kg/m3 for specimen without incising.
With decreasing gross weight, i.e., re-drying of the previously water-borne impregnated sleepers, the retention of the alternative oily preservative increased. While an average gross weight of 1,123 kg/m3 still resulted in a negative average uptake of the alternative oily preservative (−1.7 kg/m3), the retention subsequently increased to approx. 20 kg/m3. From an average gross weight of 950 kg/m3 an increase in the average retention up to 30 kg/m3 was occurring, but remained comparable at further decreasing gross weights (Figure 12).
Figure 12. Average retention in kg/m3 of the alternative oily preservative after 2nd impregnation at different gross weights.
Figure 13 shows exemplarily the influence of the decreasing gross weight on the retention as well as the penetration of the oily preservative. While at a gross density of 1,114 kg/m3 the penetration of the oily preservative was still inhomogeneous and insufficient, it improved to a closed homogeneous envelope treatment at a gross weight of 965 kg/m3.
Figure 13. Penetration of the alternative oily preservative in sleepers at different gross weights (1,114; 979; and 965 kg/m3) at 300, 800, and 1,300 mm.
Hullberg (2000) concedes that incising has a positive influence on the drying time. However, Suttie (2002) reported that incising has no influence on the drying speed. Studies by Franciosi (1956) also showed no influence of incising on the drying speed of railway sleepers made of Beech. One possible explanation is the high permeability of Beech. During drying, evaporation on the wood surface as well as the internal moisture movement play a role. The drying of permeable wood species is primarily dominated by mass flow. In this phase, the permeability of the wood structure is primarily decisive. Diffusion as a transport mechanism only becomes relevant below fiber saturation (Keey et al., 2000). Due to the high permeability of Beech, a possible positive effect of incising would thus be masked during the drying of the Beech sleepers. Whether a positive effect can be achieved by a modification of the incising pattern has to be evaluated in further investigations. Furthermore, resistance-based measurements MCs above 25% become increasingly inaccurate (Du et al., 1991). This may explain to some extent the differences between the electrically determined local MC and the gravimetrically determined global MC.
A check is the separation of the fiber bond in the longitudinal direction of the wood. Different factors can be decisive for this effect such as growth stresses, moisture gradients and ansitropical shrinkage (Fang et al., 2008; Niemz and Sonderegger, 2017). Large cross-sections are particularly susceptible to checking, since a fast drying quickly results in large differences in MC between inner and outer wood sections. If the resulting stresses exceed the strength of the wood, checks will form. The emerging tensions are thereby relieved again (Neuhaus, 2009). With regard to the exact mechanisms behind the reduction of check formation by means of incising, different approaches are discussed in the literature. While Hill (1923) and Edscorn and Davis (1989) suggested a stress relaxation for the reduction of check formation, Meierhofer (1986) proposed stress compensating effects, which lead to the development of many small checks instead of a few large checks. In contrast, Burnes (1923) considered a concentration of stresses through the incisions as a possibility for reducing large checks.
Warping of Beech sleepers during seasoning is very common. Every year, about 3% of the sleepers purchased and stored for drying must be written off as waste due to excessive deformation (Werner, 2008). According to Schulz (1971) the deformation of Beech sleepers is caused either by the growth of the tree (spring) or by tension and shrinkage (bow). Existing tensions will be released during logging or during cutting, especially if the cut is made directly through the middle of the trunk in radial direction. Longitudinal shrinkage is minimal compared to radial and tangential shrinking. For Beech, the longitudinal shrinkage is 0.3%, while the radial and tangential shrinkage is 5.8 and 11.8%, respectively (Schulz, 1971).
Beimgraben (2002) suggested growth stresses being responsible for the warping of Beech. Growth stresses will be released after trees or logs are cut in sections and afterwards cause checks or warping of the timber products (Becker and Beimgraben, 2001). Additionally, Bleile (2006) investigated the presence of reaction wood in Beech as probable cause for growth tensions in logs and distortions in sawn timber. It became evident, that the formation of tension wood leads to growth stresses in round woods as well as to distortions of sawn wood. Further examinations showed, that on average, only comparatively small changes in the location of the strongest reaction wood sections in radial direction of the trunk can be observed. Despite different types of wood modification, which are actually based on chemical or physical changes of the wooden structure itself (Scheiding et al., 2016), incising as mechanical pre-treatment is not actively changing the anatomical wooden structure and its properties. Therefore, influences of existing structural properties cannot be subsequently changed by incising, which indicates why warping of Beech sleepers is not positively influenced by incising.
The penetration of fluids into wood takes place primarily in longitudinal direction (Côté, 1963). Fluid movements in transverse direction are generally more difficult (Murmanis and Chudnoff, 1979). Punching in the incision creates new axial surfaces, which enables longitudinal penetration. Penetration up to the depth of the incision is facilitated and thus simultaneously leading to an improved uptake of the preservative. The missing influence of the gross weight on the uptake of the preservative can be explained by the dwell time of the specimens in the oil during the pressure phase. This may have resulted in drying of the upper layers and therefore led to a balance between the gross densities.
The required degree of seasoning (MC) before the second impregnation was of great importance for the quality of the impregnation with the alternative oily preservative. The negative retention of the alternative oily preservative for sleepers with an average gross weight of 1,123 kg/m3 can be explained by a weight loss during the second impregnation. The quantity of water released during impregnation exceeded the amount of absorbed oily preservative. The sleepers became lighter. Broese van Groenou and Bellmann (1958) made similar experiences with the creosote impregnation of wet Beech sleepers. Since oily products are not water-soluble, free water or aqueous preservatives act as an impassable barrier in the cell cavities and prevent the penetration of oily preservatives. The areas to be impregnated should have a MC below fiber saturation, ideally less than 20% (Leiße, 1992). From a gross weight of 950 kg/m3, moisture levels required by Leiße (1992) have most likely been reached in the peripherical areas of the Beech sleepers. Penetration of the alternative oily preservative is possible. Since there is no significant increase in the retention despite the decreasing gross weight, the retention and penetration depth can be further modified by means of optimization of the impregnation parameters.
The current study showed that the mechanical pre-treatment of the Beech sleepers by incising has a positive effect on the following:
• Check formation before impregnation with regard to check length, width, and depth.
• Penetration depth and retention of an alternative oily preservative in the area of incisions.
The incising pattern used in this test setup did not reduce the drying speed until the required degree of seasoning for impregnation was reached. Furthermore, there was no influence on the moisture distribution within the sleeper or the dimensional stability. Whether this can be achieved by changing the incising pattern needs to be evaluated in further investigations. It became evident that before the second impregnation with the alternative oily preservative, a re-drying of the sleepers to a target gross weight of ≤950 kg/m3 is necessary. In this way a homogeneous distribution of the alternative oily preservative in the peripheral area can be achieved.
The raw data supporting the conclusions of this article will be made available by the authors, without undue reservation.
MS, AH, CB, and HM contributed to conception and design of the study. MS and CB performed the work and organized the database and wrote the first draft of the manuscript. All authors contributed to manuscript revision and approved the submitted version.
MS and AH are employed by Fürstenberg-THP GmbH.
The remaining authors declare that the research was conducted in the absence of any commercial or financial relationships that could be construed as a potential conflict of interest.
All claims expressed in this article are solely those of the authors and do not necessarily represent those of their affiliated organizations, or those of the publisher, the editors and the reviewers. Any product that may be evaluated in this article, or claim that may be made by its manufacturer, is not guaranteed or endorsed by the publisher.
The authors gratefully acknowledge the Federal Ministry of Economics and Energy (BMWi) for funding the research project “SysSchwelle – Entwicklung und Marktführung einer innovativen F-Systemschwelle” (funding code: ZF 4279205CM7 and ZF 4473801CM7) as part of the Central Innovation Programme for Medium-Sized Companies (ZIM).
Becker, G., and Beimgraben, T. (2001). Stresses in Beech – Occurrence and Relevance of Growth Stresses in Beech (Fagus sylvatica L.) in Central Europe; Final Report of EU FAIR-Project CT 98-3606, Edited by the Institute of Forest Utilization and Work Science. Freiburg im Breisgau: Universität Freiburg i. Brsg.
Beimgraben, T. (2002). Auftreten von Wachstumsspannungen im Stammholz der Buche (Fagus sylvatica L.) und Möglichkeit zu deren Verminderung. Dissertation Albert Ludwigs. Freiburg im Breisgau: Universität Freiburg i. Brsg, 225.
Bleile, K. (2006). Vorkommen und Analyse von Zugholz bei Buche (Fagus sylvatica L.) als Ursache von Spannungen im Rundholz und Verwerfungen des Schnittholzes. Dissertation, Albert-Ludwigs. Freiburg im Breisgau: Universität Freiburg i. Brsg, 174.
Brient, J. A., Manning, M. J., and Freeman, M. H. (2020). Copper naphthenate – protecting America’s infrastructure for over 100 years and its potential for expanded use in Canada and Europe. Wood Mater. Sci. Eng. 15, 368–376. doi: 10.1080/17480272.2020.1837948
Brischke, C., and Lampen, S. C. (2014). Resistance based moisture content measurements on native, modified and preservative treated wood. Eur. J. Wood Wood Prod. 72, 289–292. doi: 10.1007/s00107-013-0775-3
Broese van Groenou, H. (1983). Kesseldruckimprägnierung mit Steinkohlenteeröl. Holzals Rohund Werkstoff 41, 505–508. doi: 10.1007/BF02608175
Broese van Groenou, H., and Bellmann, H. (1958). Zur Frage der Imprägnierung feuchter Buchenschwellen. Holzals Rohund Werkstoff 16, 229–233. doi: 10.1007/BF02618117
Burnes, J. D. (1923). “Experiment to determine the effect of perforations upon the checking of northern white cedar and western red cedar after treatment,” in Proceedings of the 19th Annual Meeting American Wood-Preservers Association, 263–268.
Côté, W. A. J. R. (1963). Structural Factors affecting the permeability of wood. J. Polym. Sci. Part C 2, 231–242. doi: 10.1002/polc.5070020122
DIN 68811 (2007). Imprägnierung von Eisenbahnschwellen aus Holz mit Kreosot (Steinkohlenteeröl). Berlin: Beuth.
Du, Q. P., Geissen, A., and Noack, D. (1991). Die Genauigkeit der elektrischen Holzfeuchtemessung nach dem Widerstandsprinzip. Holzals Rohund Werkstoff 49, 1–6. doi: 10.1007/BF02627523
Edscorn, K. C., and Davis, D. D. (1989). Survey of Wooden Crosstie Tests, Volume I. Association American Railroads Research and Testing Department Brief R-744. Chicago IL: AAR Technical Centre.
EN 350 (2016). Durability of Wood and Wood-Based Products—Testing and Classification of the Durability to Biological Agents of Wood and Wood-Based Materials. Brussels: CEN.
Evans, P. D. (2016). The effects of incising on the checking of wood: a review. Int. Wood Prod. J. 7, 12–25. doi: 10.1080/20426445.2015.1112936
Fang, C., Clair, B., Gril, J., and Liu, S. (2008). Growth stresses are highly controlled by the amount of g-layer in poplar tension wood. Int. Assoc. Wood Anatom. J. 29, 237–246. doi: 10.1163/22941932-90000183
Harkom, J. F. (1932). “Experimental treatment of hardwood ties,” in Proceedings of the 28th Annual Meeting American Wood-Preservers’ Association, 269–282.
Hill, L. L. (1923). “Report of Committee 5-5-2-Non-pressure treatment of poles,” in Proceedings of the 19th Annual Meeting American Wood-Preservers’ Association, 250–253.
Keey, R. B., Langrish, T. A. G., and Walker, J. C. F. (2000). Kiln-Drying of Lumber. Berlin: Springer, 325. doi: 10.1007/978-3-642-59653-7
Leiße, B. (1992). Holzschutzmittel im Einsatz: Bestandteile, Anwendungen, Umweltbelastungen. Wiesbaden und Berlin: Bauverlag GmbH, 224.
Meierhofer, U. A. (1986). Witterungsverhalten von salz- und öl-imprägniertem Brettschichtholz. Holzals Rohund Werkstoff 44, 173–177. doi: 10.1007/BF02611287
Morrell, J. J., Gupta, R., Winandy, J. E., and Riynato, D. S. (1998). Effect of Incising and preservative treatment on shear strength of nominal 2-inch lumber. Wood Fiber Sci. 30, 374–381.
Morrell, J. J., and Winandy, J. E. (1987). Incising practises used to improve preservative treatment in western species: a preliminary survey. Proc. Am. Wood Preservers Assoc. 83, 400–404.
Morris, P. I., Morrell, J. J., and Ruddick, J. N. R. (1994). “A review of incising as a means of improving treatment of sawnwood,” in Proceedings of the IRG Annual Meeting, IRG/WP 94-40019 (Stockholm), 24.
Murmanis, L., and Chudnoff, M. (1979). Lateral flow in beech and birch as revealed by electron microscope. Wood Sci. Technol. 13, 79–87. doi: 10.1007/BF00368601
Neuhaus, H. (2009). Ingenieurholzbau. Grundlagen – Bemessung – Nachweise – Beispiele, 2nd Edn. Wiesbaden: Vieweg + Teubner GWV Fachverlage GmbH, 627.
Niemz, P., and Sonderegger, U. (2017). Holzphysik. Physik des Holzes und der Holzwerkstoffe. Munich: Carl Hanser Verlag GmbH und Co. KG, 580. doi: 10.3139/9783446445468
ÖBB Infra (2017). Gleis- und Weichenschwellen aus Holz. Technische Lieferbedingungen. 07.09.07. Oberbau/Anforderungen an Oberbaukomponente. Wien: ÖBB Infrastruktur AG.
Pfabigan, N., and Reitbauer, H. (2020). Eine Ära geht dem Ende zu – Alternative Imprägnierung als Chance für die Holzschwelle. ETR Eisenbahntechnische Rundschau 69, 68–72.
REACH (2006). Regulation (EC) No 1907/2006 of the European Parliament and of the Council of 18 December 2006 concerning the registration, evaluation, authorization and restriction of chemicals. Official J. Eur. Union 49:L396.
Scheiding, W., Grabes, P., Haustein, T., Haustein, V. H., Nieke, N., Urban, H., et al. (2016). Holzschutz: Holzkunde - Pilze und Insekten – Konstruktive und chemische Maßnahmen – Technische Regeln – Praxiswissen. München: Fachbuchverlag Leipzig im Carl Hanser Verlag, 296. doi: 10.3139/9783446448445
Schulz, G. (1971). Spannungs- und Schwindungserscheinungen bei Buchengleisschwellen und ihre Auswirkung auf die Spur. Die Holzschwelle 69, 3–19.
Schulz, G. (1987). Temperaturverlauf im Kessel und im Holz bei der Teerölimprägnierung von Buchenschwellen. Holzals Rohund Werkstoff 45, 27–34. doi: 10.1007/BF02612041
Suttie, E (2002). Client Report: State of the Art Review of Incising Pre-treatment Technology and its Potential for Enhancing the Value of UK Grown Spruce. BRE Client Report Number 208080. Watford: Building Research Establishment Ltd., 43.
Keywords: creosote, incising, moisture content monitoring, oily preservative, railway sleepers, ties
Citation: Starck M, Heidel A, Brischke C and Militz H (2022) Incising and Double Impregnation of Beech Sleepers—Investigation of an Alternative Preservation System for Wooden Railway Sleepers. Front. For. Glob. Change 5:814049. doi: 10.3389/ffgc.2022.814049
Received: 12 November 2021; Accepted: 31 March 2022;
Published: 27 April 2022.
Edited by:
Tamás Hofmann, University of West Hungary, HungaryReviewed by:
Türkay Türkoğlu, Muğla University, TurkeyCopyright © 2022 Starck, Heidel, Brischke and Militz. This is an open-access article distributed under the terms of the Creative Commons Attribution License (CC BY). The use, distribution or reproduction in other forums is permitted, provided the original author(s) and the copyright owner(s) are credited and that the original publication in this journal is cited, in accordance with accepted academic practice. No use, distribution or reproduction is permitted which does not comply with these terms.
*Correspondence: Christian Brischke, Y2hyaXN0aWFuLmJyaXNjaGtlQHVuaS1nb2V0dGluZ2VuLmRl
Disclaimer: All claims expressed in this article are solely those of the authors and do not necessarily represent those of their affiliated organizations, or those of the publisher, the editors and the reviewers. Any product that may be evaluated in this article or claim that may be made by its manufacturer is not guaranteed or endorsed by the publisher.
Research integrity at Frontiers
Learn more about the work of our research integrity team to safeguard the quality of each article we publish.