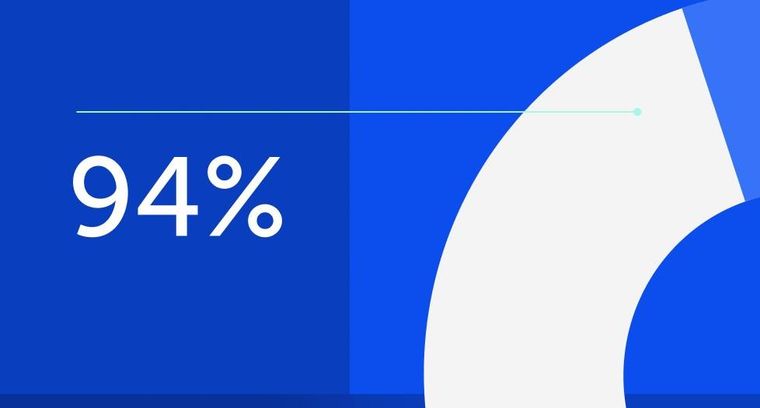
94% of researchers rate our articles as excellent or good
Learn more about the work of our research integrity team to safeguard the quality of each article we publish.
Find out more
ORIGINAL RESEARCH article
Front. Energy Res., 02 September 2022
Sec. Carbon Capture, Utilization and Storage
Volume 10 - 2022 | https://doi.org/10.3389/fenrg.2022.994220
In recent years, with the rapid development of biomass combustion power generation and heat generation as the main application industry, the amount of byproduct biological ash is also increasing year by year. How to effectively utilize the biological ash in a more green, environmental friendly and economic way has become a research hotspot. In view of the problem that the mechanical properties of the cement stone decreased when the conventional latex was used as the toughening agent, based on the introduction of high dispersive composite modified fiber to enhance the toughness of the cement stone, this paper analyzed the physical and chemical properties and application status of the biological ash, and further explored the influence and role of the biological ash as the cement stone admixture on the high-temperature mechanical properties of the composite fiber cement stone Mechanism. The results show that when the dosage of biological ash is in the range of 0–10% (wt%), it has little effect on the basic slurry properties of cement stone, and has a certain preventive effect on the gas channeling of cement stone. In the analysis of comprehensive mechanical properties, the activated biological ash can enhance the compactness of cement matrix under high temperature by reducing the Ca/Si ratio through the secondary pozzolanic effect, stimulate the formation of a large number of hydration products, and strengthen the later strength growth rate of cement. The high temperature resistance of cement paste can be effectively improved by hybrid high dispersion composite fiber.
Biomass energy is a kind of renewable and clean energy with abundant resources, which accounts for nearly 2/3 of all renewable energy in the world, and it is almost sulfur-free. It can achieve zero emission of CO2 in the total amount of combustion utilization, which provides an effective way to solve the current energy crisis and environmental problems (Antar et al., 2021; Siwal et al., 2021; Wareing et al., 2021; Ning et al., 2021). At present, many countries have increased the research and development of biomass energy. The so-called biomass refers to all the substances in the organic matter, except the fossil fuel, which can be regenerated from animals and plants (Popp et al., 2021; Kartik et al., 2021). Biomass can obtain many kinds of energy products such as gas, liquid and solid through thermochemical conversion technology. After thermochemical conversion and utilization, the residual inorganic material is biomass ash, which is produced in many countries every year (Ashokkumar et al., 2022). Vassilev et al. (2013) estimated that 476 million tons of ash are produced by direct combustion of biomass every year, which is similar to the amount of coal ash (780 million tons). At present, the main treatment method for biological ash is landfill, which not only has high cost, but also causes a large amount of waste of resources and serious pollution to the environment. Therefore, how to use bio ash in a more green, economical and simple way still needs a lot of research. At present, the sources of biomass fuel for producing biological ash are roughly divided into four categories: agricultural biomass, i.e. the residues after the receipt and processing of crops, such as straw, rice husk and wheat straw (Petrella et al., 2022). forest biomass, i.e. the residues of forest products, such as wood cuttings, sawdust, bark and conifers, wood blocks, etc (Noë et al., 2021), energy crops, such as short-term rotation crops, fast-growing forests, etc (Nathan and Goretty, 2018; Ameray et al., 2021).
With the acceleration of industrialization and the shortage of energy and resources, the effective use of biomass renewable resources is strongly advocated by the state. In the field of oil well cementing, due to the need to use a large number of Portland cement for downhole formation sealing operations, and the production of Portland cement accounts for 8% of greenhouse gas emissions, which greatly aggravates the environmental pollution. At present, the management and utilization of solid waste has been studied as a method to minimize environmental impact (Bildirici, 2019). Therefore, more and more researches on the replacement of Portland cement with industrial waste have emerged. Her et al. (2021) selected oyster shell powder and fan shell powder to replace limestone in cement clinker. Through comparison with conventional Portland cement, it was found that these two kinds of added shell powder cement formed C3S, C2S, C3A and C4AF compounds, and the main hydration products were C-S-H gel and calcium hydroxide, which was the same as Portland cement. Niu and Kim (2022) pretreated the surface of corn straw with siliceous solution to prevent the hydrolysis of cellulose sugar and reduce the water absorption capacity of corn straw. It is found that corn straw can effectively reduce the consumption of cement materials and improve the thermal insulation and energy saving effect of buildings. Amin et al. (2021) explored the effect of the synergistic use of nano cotton stalk ash (NCSA) and palm leaf ash (PLA) on the properties of Portland cement, and found that the mechanical properties of cement slurry added with 5% NCSA and 20% PLA were the best at 90 days Jaitanong and Chaipunti. (2015) studied the structure and properties of Portland cement (PC), natural latex and rice husk ash (RHA) composites. It was found that at the same water cement ratio of 0.5, the compressive strength of PC-RHA with 20% rice husk ash (the most appropriate amount) increased by 36.4 and 38.3% respectively in 3ays and 14days, compared with the same PC, but the compressive strength of the cement stone decreased to a certain extent after adding latex. Mahmuda et al. (2020) studied the influence of different amount of straw ash on the performance of cement stone. It was found that the average compressive strength of cement stone samples mixed with 10, 20 and 30% straw ash was 15.82, 20.17 and 27.32 kN respectively under 7days curing, while the compressive strength of the pure slurry was only 13.53 kN. It is believed that this is due to the formation of amorphous silica from straw ash and Portland cement, which improves the compressive strength. Shar et al. (2020) used wheat straw ash as a cement substitute in concrete to test the compressive strength. It was found that with the increase of the amount of wheat straw ash, the compressive strength of cement stone increased continuously, reaching the maximum at about 10%. A large number of previous experimental research results have shown that bio-ash materials have a strong feasibility as a substitute for cement in conventional Portland cement, and can show a certain performance improvement effect, but such studies are mostly carried out under the conditions of low temperature and normal pressure, and there are relatively few researches under the conditions of high temperature and pressure, and most of them are carried out based on civil engineering experimental standards, and the reference surface is relatively narrow. In order to improve its universality and expand its engineering application scope. This paper is based on the systematic evaluation plan in the petroleum field and the current domestic bio-ash waste-rice straw ash. In order to cope with the primary defects of insufficient toughness and excessive brittleness of cement stone, it is also to solve the poor tolerance of high temperature natural latex mixed with cement stone (Al-Khafaji et al., 2021; Buritatum et al., 2021), the modified temperature-resistant latex has high pollution and high-temperature strength attenuation, and carried out experimental research on high-temperature and high-pressure activated straw ash hybrid high-strength crack-resistant glass fiber/carbon fiber composite materials. Through the evaluation standard of oil well cement stone, the systematic experimental evaluation and microscopic image analysis of cement stone are carried out. The purpose is to study the mechanical properties of rice straw ash cement stone mixed with two-component fiber toughened materials at high temperature, and to provide some reference and guidance for the follow-up work.
Jiahua G-grade oil well cement, density 3.12–3.15 g/cm3, the chemical composition is shown in Table 1, purchased in Jiahua Special Cement Co., Ltd.; 300mesh silicon powder, density 2.6 g/cm3-2.7 g/cm3, particle size report as shown in Figure 1, purchased in Henan Huarong Silicon Powder Material Co., Ltd.; High-strength A-grade alkali-free high-dispersion glass fibers (Figure 2, Right), purchased in Taowu Fiberglass Factory; 3 mm carbon fiber (Figure 2, Left), purchased in Shanghai Lishuo Composite Material Technology Co., Ltd.; Nano-liquid silicon, defoamer X66L, fluid loss agent CG80L, dispersant CF43L are all from Jingzhou Jiahua Technology Co., Ltd.; Biological ash (Figure 2, Middle), the chemical composition is shown in Table 2, purchased and placed in Hongke Insulation Material Factory, Dacheng County, Hebei Province; Na2SO4, industrial grade, purchased in Jinan Hongde Chemical Co., Ltd.; NaOH, analytically pure, purchased in Henan Tongxing Wanxin Environmental Protection Technology Co., Ltd.
FIGURE 2. Experimental bio-ash and fiber materials (Left: carbon fiber; middle: bio-ash; right: alkali-free high-dispersion fiber).
The composition of the experimental formula designed by the Institute is shown in Table 3, and the fixed water cement ratio is 0.44. The activator used is the combination of sodium sulfate and NaOH. As an alkali activator, the dosage of sodium sulfate is 0.01–0.03% of the weight of cement ash, and the modulus ratio of Na2SO4: NaOH is 1:3. In the formula combination, ccs-0 is the basic reference sample without fiber and biological ash, while CCS-1, CCS-2, CCS-3 and CCS-4 are composite fiber hybrid biological ash test samples with 0, 3, 5 and 10% biological ash respectively.
1) Rheological property test
According to the oil industry standard SY/T5546-92 ″Test Method for Application Performance of Oil Well Cement” and API specification “Standard and Test Specification for Oil Well Cement Material”, the shear stress at different rotational speeds is measured, and its average value is measured many times.
2) Water loss test
Within 1 minute after the preparation of the cement slurry, the cement slurry is poured into the slurry cup of the Atmospheric pressure thick meter (Qingdao Senxin Mechanical and Electrical Equipment Co., Ltd.). The cement slurry is heated to 93 °C within 20 min. After mixing, the cement slurry was poured into the ZH10766 High Temperature and High Pressure Water Loss Instrument (Beijing Zhonghui Tiancheng Technology Co., Ltd.) to test the water loss of the cement slurry at 93 °C, 6.9 MPa for 30 min.
3) Thickening time test
Using TG-8040DA pressure thickening meter (Shenyang Tiger Petroleum Instrument Manufacturing Co., Ltd.) to test the time when the consistency of cement slurry reaches 100 Bc (Bearden units of Consistency—Consistency unit of cement slurry) at 180 °C × 80 MPa, that is, the time of cement slurry thickening. The starting point is the point where the consistency value suddenly changes, the ending point is the consistency value of 100 Bc, and the interval time is the conversion time.
4) Mechanical properties testing
Compressive strength and elastic modulus of cement paste are tested by HY-20080 computer-controlled electronic universal material tester (Shanghai Hengyi Precision Instrument Co., Ltd.) with sample size of 50.8 × 50.8 × 50.8 mm; The flexural strength test fixture of universal testing machine is used. The sample size is 40 × 40 × 160 mm. All samples after preparation are placed in a high-temperature pressurized curing kettle for curing at 180 °C and 21 MPa.
The design of the experimental formula is based on the two-component toughened fiber. The fluidity of the cement slurry will be affected due to the incorporation of the fiber, because the dry chopped fiber is easy to have a large friction force between the fibers, so by controlling the fiber addition (Ralph et al., 2019; Hasan et al., 2021), the total addition is ensured to be less than 0.3%, and the hybrid fiber material is also modified to a certain extent. This includes fiber surface pretreatment and modification.
1) Fiber surface pretreatment
The surface of the fiber will remain some oil agent used in the production, which will affect the wetting effect of the dispersant on the fiber surface. Therefore, the surface of the fiber needs to be pretreated to remove the impurities on the fiber surface. Here, 35% acetone solution is used as the fiber solvent, and magnetic stirring is carried out at room temperature for 12 h. The fiber after filtration is separated and washed with distilled water After heating and refluxing for about 2h, take it out for drying.
2) Fiber dispersion treatment
Put a proper amount of pretreated composite short cut fiber in a 1,000 ml beaker, add 500 ml of purified water, mix continuously at 800 r/min, at the same time, add a certain dose of (1.2 g/500 ml) hydroxyethyl cellulose (HEC) until all HEC are dissolved, and then further increase the speed to 1000r/min, continue to mix for 30 min, keep the composite fiber in the solution state for standby, in the preparation time of cement slurry, the root According to the amount of solvent in the composite fiber dispersion, the water demand of cement slurry is reduced in equal proportion to ensure the accuracy of the experiment.
Before the analysis experiment, select the cement stone fragments after the compression test, select the middle part to soak in anhydrous ethanol to prevent the sample from further hydration, then dry the sample at 60 °C, grind it into powder and reserve a small sample for XRD, SEM-EDS and thermosgravimetry analysis. The main purpose of micro test is to explore the exciting effect of activator and the change of internal structure of biological ash cement under high temperature.
1) Scanning electron microscope
Hitachi S-4800 field emission scanning electron microscope (SEM) is used in this paper. The acceleration voltage of electron beam is 15 kV. The test sample used is broken cement flake under the compressive strength test. By observing the sample at different magnification and combining with EDS scanning, the distribution form and phase composition of various components in the fracture surface of cement paste can be determined.
2) Thermogravimetric Analysis (TG) analysis
TGA/SDTA 851e is used in this test, the heating rate is 10°/min, the temperature rise range is 0–800°C, and the atmosphere used in the test is nitrogen.
3) Diffraction of x-rays (XRD) test
Different types of cement stone powder samples were tested by D8 AVANCE diffractometer in Germany. The cement stone samples were grinded into 320 mesh size powder, about 40 μm the measurement mode was continuous scanning, the scanning speed was 5°/min, the scanning range was 5–70°, the diffractometer used was Cu target, the wavelength was 1.54056 λ.
4) Mercury intrusion porosimetry (MIP) test
The pore structure of hardened cement sample was analyzed by pore structure analyzer. The pressure range was 0.5–60000 Psi, and the pore size range was 0.0035–200 μm. Before preparing the sample, select the cement sample block which is damaged by mechanical test and close to the center of the sample under the curing age of 21 days of hydration, break it into small pieces with volume less than 1 cm3, then immediately put it into anhydrous ethanol to stop the hydration, and place the sample in a 65°C vacuum drying oven to dry to constant weight.
The fluidity test of cement slurry is one of the most important links in the design of cementing slurry. The fluidity directly determines the difficulty of pumping cement slurry to the well. If the fluidity of cement slurry is too bad, the pumping efficiency will be reduced, the pumping power consumption will be greatly increased, and the construction cost will be increased to a certain extent. The fluid loss of slurry is the key parameter to reflect the water retention performance of cement slurry, so as to ensure that the density of cement slurry will not be reduced due to water loss in the sealing operation under the formation, resulting in that the cement can-not balance the formation pressure. Therefore, the experiment test first conducted an experimental evaluation on the fluidity of cement slurry, and the evaluation results are shown in Figure 3. It can be seen from the figure that the incorporation of hybrid fiber has little effect on the convective denaturation, which is attributed to the lower fiber addition and better modification effect. With the increase of shear rate, the shear force of cement slurry increases gradually, which means that the fluidity of the slurry of composite fiber hybrid biological ash cement slurry system decreases with the increase of the content of biological ash. In addition, with the increase of the content of biological ash, the filtration of cement slurry decreases gradually, which can play a certain role in reducing water loss. This is because the fine grinding biological ash itself has a low particle fineness, so it can fill up the small pores in the mud cake in the test of the leakage of the cement slurry. In addition, because the biological ash has a certain water absorption capacity, to a certain extent, it reduces the water cement ratio of the cement slurry, so it will have a certain impact on the fluidity of the cement slurry, but because the fine is used in this experiment The smaller the particle size is, the smaller the ability of absorbing water is. As a result, the larger the unabsorbed water is in the cement slurry mixed with the composite fiber, so the fluidity is not affected.
The test of cement paste thickening time can truly reflect the state change of cement paste when it starts to thicken to the consistency when it reaches the setting under certain temperature and pressure conditions after the completion of mixing, so as to achieve a better sealing of cement paste at the specified temperature, pressure and time. The thickening time of cement slurry samples CCS -0, CCS-1, CCS-2, CCS-3 and CCS-4 under different biological ash dosage was tested in the laboratory. The experimental conditions were 180°C, 80 MPa.
As shown in Figure 4, When the amount of biological ash is low (<3%), it has little effect on the thickening time of cement slurry, but it will shorten the thickening transition time, among which, CCS-1 will reduce the thickening transition time by about 25% compared with CCS-0; when the amount of biological ash continues to increase to more than 3%, the thickening time will be significantly reduced, among which CCS-2, CCS-3 and CCS-4 will reduce the thickening time by nearly 16.4, 34.2 and 47.3% compared with ccs-0, respectively Compared with CCS-0, the transition time was reduced by 8, 41.7 and 75.2% respectively. On the one hand, the increase of biological ash content reduces the overall water cement ratio of cement slurry system to a certain extent, which affects the hydration process of cement slurry. On the other hand, it is because the dissolution of Si and Al in the slurry is affected, the polymerization degree is accelerated, and the thickening time and the thickening transition state time are reduced.
Mechanical property test is an important factor to evaluate the quality of cement stone. Through the use of universal mechanical testing machine, the compressive strength tests of cement stone samples CCS-0, CCS-1, CCS-2, CCS-3 and CCS-4 are carried out, and the test results are shown in Figure 5. Through comparative analysis, it can be found that the compressive strength of cement paste increases slowly with the increase of the amount of biological ash within 10%. The compressive strength of CCS-1 samples at 1, 7 and 28d was 2.1, 2.8 and 3.5% higher than that of CCS-0 respectively. CCS-2 increased by 4.3, 4.7 and 5.6% respectively. CCS-3 increased by 6.1, 6.5 and 7.6% respectively. CCS-4 increased by 11.3, 10.2 and 11.5% respectively. Secondly, in terms of intensity development, CCS-0 develops rapidly in 7d, with a growth rate of 15.7%, but the intensity growth is greatly reduced after 28d, with a growth rate of only 4.6% compared with 7d. Taking 10% CCS-4 samples as an example, the strength growth ratio at 7 and 28d was 14.4 and 21.1%, respectively. The reason is that the hydration activity of biological ash is weaker than that of cement, and the hydration speed is slower than that of cement. Therefore, the overall compressive strength of cement stone decreases with the increase of dosage, and the early strength is affected. However, with the increase of curing age, the hydration of this part is gradually completed, so the strength of cement stone will increase significantly after 28 days.
In view of the composite fiber mixed in the cement slurry formulation system, the effect of biological ash on the flexural strength of the fiber composite cement slurry system was also studied in the experiment, and the experimental results are shown in Figure 6. It can be seen in the figure that the development trend of flexural strength and compressive strength of composite fiber hybrid biological ash cement stone is consistent, showing a stable growth trend with the growth of curing age. The bending strength of CCS-1 samples at 1, 7ays and 28d was 12.7, 17.5 and 16.8% higher than that of CCS-0 respectively. CCS-2 increased by 14, 19.8 and 21.2% respectively. CCS-3 increased by 15.8, 21.8 and 24.8% respectively. CCS-4 increased by 19.8, 26.4 and 28.3% respectively. In the aspect of flexural strength development, the strength of CCS-0 developed rapidly in 7d, with a growth rate of 7.7%. After 28d, the flexural strength increased slowly, with a growth rate of only 2.1% in 7d. Taking 10% CCS-4 samples as an example, the strength growth ratio at 7ays and 28d was 13.6 and 3.7%, respectively. The reason is that the hydration activity of the biological ash is weaker than that of the cement, and the hydration speed is slower than that of the cement. Therefore, the overall compressive strength of the cement stone decreases with the increase of the dosage, and the early strength is affected. However, with the increase of the curing age, the hydration of this part is gradually completed. In addition, due to the presence of activated silica and activated alumina in the biological ash, it will also produce a certain geopolymer gel under the condition of alkaline activator, so the strength of the cement stone after 28days will be more great growth (compared to cement paste stone).
In Figure 7, XRD analysis was carried out on the samples of cement paste and fiber hybrid biological ash, and the same time, 5% phenolphthalein-alcohol solution was used to titrate the cement paste profile. Through the comparison, it can be found that the main products in the samples are SiO2, calcium hydroxide (OH), Ca1.5·SiO3.5·xH2O, Ca3SiO5 and gismondine. Among them, SiO2 mainly comes from the addition of silica powder, in order to avoid the high temperature strength degradation of cement. It can be seen from the comparison that the characteristic peak of cement sample with fiber mixed biological ash has changed to some extent compared with that of cement sample with pure slurry. Among them, there are obvious CH characteristic peaks in CCS-0, but with the addition of biological ash, the CH characteristic peaks weaken significantly, which shows that part of CH is consumed. This is because in addition to the reaction between the addition of SiO2 and CH in the cement stone, the SiO2, Al2O3 and other silicate glasses in the biological ash react with the alkaline activator CH produced in the cement stone to generate hydrated silicon Calcium carbonate and other gel, reinforced cement matrix colleagues also dissipated part of CH. The results of phenolphthalein titration showed that with the increase of the dosage of biological ash, the basic components in cement decreased gradually, and the discoloration degree of phenolphthalein decreased gradually, which was consistent with the test results of XRD.
Figure 8 shows the thermogravimetric analysis results of CCS-2 and CCS-0, respectively. The results show that the weight of CCS-0 sample changes obviously in the temperature range of 400–550°C and 550–700°C. At the same time, according to the mass loss shown in the thermogravimetric curve, the content of CH in the cement stone can be calculated. The specific formula is as follows:
Where 74, 18 are the molar masses of CH, H2O.
Among them, in the range of 400–550°C, the weight attenuation ratio of cement paste due to the removal of structural water by CH is 4.06%, and its CH content is 16.69w/%. By comparing the CH content of CCS-2 samples, we can see that with the addition of biological ash, the content of CH in cement paste decreases. When the content of biological ash is 7%, the content of CH in the samples has decreased from 16.69w/% to 14.84w/%, and with the addition of biological ash, the content of CH in the samples has decreased from 16.69w/% to 14.84w/%, With the gradual progress of cement hydration, the SiO2 in the biological ash reacts with the OH and C-S-H gels in the hydration product to produce a pozzolanic reaction, which further formed low alkalinity C-S-H gel, and the change of CH content can reflect the extent of pozzolanic reaction in the side. However, the decomposition of carbonate (CaCO3) is from 550 to 700°C. For the appearance of calcium carbonate, the main reason is that the calcium hydroxide produced by cement hydration migrates to the surface with water, and the calcium hydroxide precipitates after water evaporation, and then reacts with carbon dioxide in the air to form calcium carbonate. In general, the addition of biological ash improves the thermal decomposition of cement paste, which also verifies that the mechanical properties of cement paste continue to strengthen with the increase of the amount of biological ash (<10%) at high temperature.
The pore structure of cement stone is closely related to its physical and mechanical properties, and therefore it is also an important performance index to determine the quality of cement stone. By selecting specific experimental samples CCS-0 and CCS-2 for mercury injection test, the experimental results are shown in Figure 9; Table 4. Where, the porosity of CCS-2 in the cement sample of bio ash hybrid composite fiber is significantly lower than that of CCS-0, the porosity is 20.06%, and the decrease ratio is 15.99%. According to the pore size distribution diagram, the pore size of CCS-2 less than 0.02 μm is significantly higher than that of CCS-0. This may be attributed to the plugging of the cementitious material formed by the alkaline excitation of the biological ash. At the same time, the main component of the biological ash is SiO2, which is equivalent to improving the Si/Ca ratio in the cement slurry system to a certain extent, promoting its pozzolanic effect and improving the compactness of the cement matrix.
Figures 10, 11 is the SEM and EDS analysis results of CCS-4 sample (composite fiber mixed with 10% bio-ash cement stone sample) for hydration 3d. The observation shows that the cement stone hardened body The cross section at 400 μm can clearly observe the glass fiber and carbon fiber interspersed at the cross section. at the same time, it can also be observed that the fragmented silicon powder is scattered on the cross section Figures 10A,B, the cement stone has a relatively high density, and almost no cracks. Continue to enlarge the magnification to below 10 μm. Observation of the overall morphology shows that a large amount of hydration products are plugged between the silica powder and the cement stone matrix. Among them, only a small amount of square crystal CH appears, which is consistent with the XRD test analysis results. According to the EDS analysis results of the hydration products, taking the measurement point A as an example, the content of Ca, O and Si atoms in the needle-shaped and granular hydration products is relatively high, and the contents are 15.53, 73.81 and 8.84%, respectively. The mass percentages are 29.65, 56.26 and 11.83%, respectively. It is precisely because of the presence of this hydrated gelatinous substance that the strength of the cement stone in the later period has been greatly improved. These gelled substances greatly enhance the internal structure of the cement stone by crosslinking with other components in the silica powder cement stone matrix force.
To solve the problem that the conventional latex as a toughener added to cement stone is not resistant to high temperature, resulting in a significant decrease in the high-temperature mechanical properties of the cement stone, the high-temperature modification and toughening of the oil well cement stone is achieved by using glass fiber/carbon fiber composite blending. At the same time, the introduction of the most common bio-ash waste in China and the use of alkaline activator, through the comprehensive performance research of bio-ash hybrid glass/carbon fiber composite cement stone, and a series of characterization evaluations that can be implemented:
(1) In the basic performance test, it can be found that at less than 10% dosage, different amounts of bio-ash have little effect on the rheology of cement slurry mixed with modified composite fiber, which can ensure that the cement slurry has a good Pumping effect. In addition, with the increase in the amount of bio-ash, the water loss of cement slurry decreases, which effectively avoids weight loss and gas channeling accidents caused by excessive water loss when the cement slurry returns in the wellbore. In addition, in the thickening test, with the increase of the amount of biological ash, the thickening time and the transition time will be shortened to a certain extent, which is extremely beneficial to the prevention of gas channeling.
(2) After testing the compressive strength and flexural strength of cement stone separately, it can be seen that the bio-ash hybrid composite fiber has a certain improvement effect on the mechanical properties of the cement stone. On the basis of ensuring the rheology of the cement slurry foundation, the amount of fiber is fixed It was found that with the increase of the amount of bio-ash, the compressive strength of cement stone gradually increased. The compressive strength of cement stone at 7 and 28d under the condition of 10% bio-ash and 0.4% composite fiber was 14.4% and 21.1 respectively. %, the test sample mixed with biological ash has a higher strength growth rate in the later period. In the bending strength test, it can be found that the incorporation of fibers plays a major role in improving the bending strength, and biological ash plays an auxiliary role in strengthening.
(3) In the discussion of the mechanism of bio-ash hybrid composite fiber reinforced cement stone, on the basis of ensuring good rheology, the composite fiber penetrates the cement stone matrix cross section inside the cement stone, dissipating part of the cement stone fracture Stress, which strengthens the bending resistance of the cement stone. For the high temperature cement stone test, the biological ash waste that plays a major role dissipates the internal component CH of the cement stone through the secondary pozzolanic effect, and cooperates with the cement matrix The generated large amount of hydrated calcium silicate gel material reduces the heat loss of the main components of the cement stone and strengthens the high-temperature mechanical properties of the cement stone.
(4) The implementation of this work plays a vital role in mitigating environmental pollution and reducing costs and increasing efficiency. On the one hand, it avoids the use of latex and other high-temperature polluting cement stone toughening raw materials, and effectively uses domestic Large amounts of bio-ash (rice straw ash) waste. On the other hand, the waste bio-ash raw materials used in this work are inexpensive, have a wide range of raw material sources, and are extremely difficult to obtain.
In this research work, the scheme design of bio ash composite fiber cement is carried out for high temperature environment (180°C), and more experimental studies will be carried out at temperature (40°C, 80°C, 120°C) in the future, so as to more comprehensively grasp the application scope and performance change relationship of bio ash composite fiber cement.
The original contributions presented in the study are included in the article/supplementary material further inquiries can be directed to the corresponding author.
YZ investigated and processed the data, pointed out the framework of the paper, made a summary and analysis, and completed the writing of the article. YZ, JW and XY reviewed the paper and supported the project.
The authors would like to acknowledge the Doctoral Fund Project of Chongqing Institute of Industry and Technology (Grant No. 2022G2YBS2K2-12).
The authors declare that the research was conducted in the absence of any commercial or financial relationships that could be construed as a potential conflict of interest.
All claims expressed in this article are solely those of the authors and do not necessarily represent those of their affiliated organizations, or those of the publisher, the editors and the reviewers. Any product that may be evaluated in this article, or claim that may be made by its manufacturer, is not guaranteed or endorsed by the publisher.
Al-Khafaji, Z., Falah, M., Shubbar, A., Nasr, M. S., Al-Mamoori, S. F., Alkhayyat, A., et al. (2021). The impact of using different ratios of latex rubber on the characteristics of mortars made with GGBS and Portland cement. IOP Conf. Ser. Mat. Sci. Eng. 1090 (1), 1–11. doi:10.1088/1757-899X/1090/1/012043
Ameray, A., Bergeron, Y., Valeria, O., Montoro Girona, M., and Cavard, X. (2021). Forest carbon management: A review of silvicultural practices and management strategies across boreal, temperate and tropical forests. Curr. For. Rep. 7 (4), 245–266. doi:10.1007/s40725-021-00151-w
Amin, M., Zeyad, A., Tayeh, B., and Saad Agwa, I. (2021). Effects of nano cotton stalk and palm leaf ashes on ultrahigh-performance concrete properties incorporating recycled concrete aggregates. Constr. Build. Mater. 302 (10), 1–14. doi:10.1016/j.conbuildmat.2021.124196
Antar, M., Lyu, D., Nazari, M., Shah, A., Zhou, X., and Smith, D. L. (2021). Biomass for a sustainable bioeconomy: An overview of world biomass production and utilization. Renew. Sustain. Energy Rev. 139 (4), 1–18. doi:10.1016/j.rser.2020.110691
Ashokkumar, V., Venkatkarthick, R., Jayashree, S., Chuetor, S., Dharmaraj, S., Kumar, G., et al. (2022). Recent advances in lignocellulosic biomass for biofuels and value-added bioproducts-A critical review. Bioresour. Technol. 344 (1), 1–15. doi:10.1016/j.biortech.2021.126195
Bildirici, M. (2019). Cement production, environmental pollution, and economic growth: evidence from China and USA. Clean. Technol. Environ. Policy 21 (4), 783–793. doi:10.1007/s10098-019-01667-3
Buritatum, A., Horpibulsuk, S., Udomchai, A., Suddeepong, A., Takaikaew, T., Vichitcholchai, N., et al. (2021). Durability improvement of cement stabilized pavement base using natural rubber latex. Transp. Geotech. 28 (5), 1–9. doi:10.1016/j.trgeo.2021.100518
Hasan, K., Horváth, P., and Alpár, T. (2021). Lignocellulosic fiber cement compatibility: a state of the art review. J. Nat. Fibers 2021 (2), 1–26. doi:10.1080/15440478.2021.1875380
Her, S., Park, T., Zalnezhad, E., and Bae, S. (2021). Synthesis and characterization of cement clinker using recycled pulverized oyster and scallop shell as limestone substitutes. J. Clean. Prod. 278 (1), 1–13. doi:10.1016/j.jclepro.2020.123987
Jaitanong, N., and Chaipunti, T. (2015). Physical and mechanical properties of cement/natural rubber latex/rice husk ash composites. Appl. Mech. Mater. 804 (10), 124–128. doi:10.4028/www.scientific.net/amm.804.124amm.804.124
Kartik, A., Akhil, D., Lakshmi, D., Panchamoorthy Gopinath, K., Arun, J., Sivaramakrishnan, R., et al. (2021). A critical review on production of biopolymers from algae biomass and their applications. Bioresour. Technol. 329 (6), 1–11. doi:10.1016/j.biortech.2021.124868
Mahmuda, A., Tjaronge, M., and Amiruddin, A. (2020). The potential utilization of rice straw ash as cement replacement in mortar material. IOP Conf. Ser. Earth Environ. Sci. 419 (10), 1–7. doi:10.1088/1755-1315/419/1/012037
Nathan, W., and Goretty, D. (2018). Supplying renewable energy for Canadian cement production: Life cycle assessment of bioenergy from forest harvest residues using mobile fast pyrolysis units. J. Clean. Prod. 175 (2), 237–250. doi:10.1016/j.jclepro.2017.12.040
Ning, P., Yang, G., Hu, L., Sun, J., Shi, L., Zhou, Y., et al. (2021). Recent advances in the valorization of plant biomass. Biotechnol. Biofuels 14 (1), 1–22. doi:10.1186/s13068-021-01949-3
Niu, B., and Kim, B. (2022). Method for manufacturing corn straw cement-based composite and its physical properties. Materials 15 (9), 1–18. doi:10.3390/ma15093199
Noë, J., Erb, K., Matej, S., Magerl, A., Bhan, M., and Gingrich, S. (2021). Altered growth conditions more than reforestation counteracted forest biomass carbon emissions 1990–2020. Nat. Commun. 12 (1), 1–10. doi:10.1038/s41467-021-26398-2
Petrella, A., De Gisi, S., Di Clemente, M., Todaro, F., Ayr, U., Liuzzi, S., et al. (2022). Experimental investigation on environmentally sustainable cement composites based on wheat straw and perlite. Materials 15 (2), 1–22. doi:10.3390/ma15020453
Popp, J., Kovács, S., Oláh, J., Diveki, Z., and Balazs, E. (2021). Bioeconomy: Biomass and biomass-based energy supply and demand. New Biotechnol. 60 (1), 76–84. doi:10.1016/j.nbt.2020.10.004
Ralph, C., Lemoine, P., Boyd, A., Archer, E., and McIlhagger, A. (2019). The effect of fibre sizing on the modification of basalt fibre surface in preparation for bonding to polypropylene. Appl. Surf. Sci. 475 (1), 435–445. doi:10.1016/j.apsusc.2019.01.001
Shar, I., Fareed, A., Memon, B., Bheel, N. D., Hussain, Z., and Dayo, A. A. (2020). “Use of wheat straw ash as cement replacement material in the concrete,” in International Conference on Sustainable Development in Civil Engineering, MUET, Pakistan, Dec 06-07 2019.
Siwal, S., Zhang, Q., Devi, N., Saini, A. K., Saini, V., Pareek, B., et al. (2021). Recovery processes of sustainable energy using different biomass and wastes. Renew. Sustain. Energy Rev. 150 (10), 1–23. doi:10.1016/j.rser.2021.111483
Vassilev, S., Baxter, D., Andersen, L., and Vassileva, C. G. (2013). An overview of the composition and application of biomass ash. Part 1. Phase–mineral and chemical composition and classification. Fuel 105 (3), 40–76. doi:10.1016/j.fuel.2012.09.041
Keywords: biomass, high temperature, cement, composite fiber, mechanical properties
Citation: Zhang Y, Wen J and Yin X (2022) Evaluation and high temperature strengthening mechanism of alkali activated biological-ash hybrid glass fiber-carbon fiber cement slurry system. Front. Energy Res. 10:994220. doi: 10.3389/fenrg.2022.994220
Received: 14 July 2022; Accepted: 01 August 2022;
Published: 02 September 2022.
Edited by:
Hailong Li, Central South University, ChinaReviewed by:
Muhammad Imran Rashid, University of Engineering and Technology, PakistanCopyright © 2022 Zhang, Wen and Yin. This is an open-access article distributed under the terms of the Creative Commons Attribution License (CC BY). The use, distribution or reproduction in other forums is permitted, provided the original author(s) and the copyright owner(s) are credited and that the original publication in this journal is cited, in accordance with accepted academic practice. No use, distribution or reproduction is permitted which does not comply with these terms.
*Correspondence: Yihang Zhang, THVja3l6aGFuZ3loQGZveG1haWwuY29t
Disclaimer: All claims expressed in this article are solely those of the authors and do not necessarily represent those of their affiliated organizations, or those of the publisher, the editors and the reviewers. Any product that may be evaluated in this article or claim that may be made by its manufacturer is not guaranteed or endorsed by the publisher.
Research integrity at Frontiers
Learn more about the work of our research integrity team to safeguard the quality of each article we publish.