- 1College of Materials Science and Engineering, Zhejiang University of Technology, Hangzhou, China
- 2Zhejiang Meidu Hitrans Lithium Battery Technology Co., Ltd, Shaoxing, China
- 3Institute of Optoelectronic Materials and Devices, China Jiliang University, Hangzhou, China
- 4SolaXPower Network Technology (Zhejiang) Co., Ltd, Hangzhou, China
- 5Hengdian Group DMEGC Magnetics Co. Ltd, Dongyang, China
- 6Department of Cell Research and Development, Farasis Energy Inc., Hayward, CA, United States
- 7Materials Science and Engineering Program & Texas Materials Institute, The University of Texas at Austin, Austin, TX, United States
- 8State Key Laboratory of Advanced Technology for Materials Synthesis and Processing, Wuhan University of Technology, Wuhan, China
Ni-rich layered transition-metal oxides with high specific capacity and energy density are regarded as one of the most promising cathode materials for next generation lithium-ion batteries. However, the notorious surface impurities and high air sensitivity of Ni-rich layered oxides remain great challenges for its large-scale application. In this respect, surface impurities are mainly derived from excessive Li addition to reduce the Li/Ni mixing degree and to compensate for the Li volatilization during sintering. Owing to the high sensitivity to moisture and CO2 in ambient air, the Ni-rich layered oxides are prone to form residual lithium compounds (e.g. LiOH and Li2CO3) on the surface, subsequently engendering the detrimental subsurface phase transformation. Consequently, Ni-rich layered oxides often have inferior storage and processing performance. More seriously, the residual lithium compounds increase the cell polarization, as well as aggravate battery swelling during long-term cycling. This review focuses on the origin and evolution of residual lithium compounds. Moreover, the negative effects of residual lithium compounds on storage performance, processing performance and electrochemical performance are discussed in detail. Finally, the feasible solutions and future prospects on how to reduce or even eliminate residual lithium compounds are proposed.
Introduction
Although LiCoO2 is one of the earliest successfully commercialized cathode materials, with a low energy density, high cost and toxicity, it is not suitable to be applied as a power battery material (Lu et al., 2019; Xian et al., 2020; Cheng et al. 2020). By substituting cobalt (Co) with nickel (Ni), LiNiO2 has a similar layered crystal structure to LiCoO2. However, it possesses a larger energy density and costs less (Ohzuku et al., 1993; Deng et al., 2019; Mu et al., 2020). Unfortunately, due to the large cation mixing degree during synthesis (preparing stoichiometry LiNiO2 is actually difficult) and extreme air sensitivity, the practical application of LiNiO2 is very challenging (Liu et al., 2007; Manthiram et al., 2016; Das et al., 2017). In this respect, substituting the fractional Ni atoms in LiNiO2 with other metallic elements, Ni-rich layered oxide materials (LiNixMyO2, M = Co, Mn, Al, x + y = 1 and x ≥ 0.6) will be more stable than pristine LiNiO2 (ChongYoon et al., 2015; Manthiram et al., 2017; Li et al., 2018; Ryu et al., 2018; Zhang et al., 2019c). Taking NCM (LiNixCoyMnzO2) materials as an example, through replacing some Ni atoms at the 3b site with Co and Mn, with a favorable synergistic effect, they exhibit equalizing performance, where Ni is the main capacity provider with two redox couples including Ni2+/Ni3+ and Ni3+/Ni4+, Co3+ is beneficial in suppressing Li/Ni mixing and enhances systematic ionic conductivity, furthermore, Mn4+ can also stabilize the lattice structure and improve thermal stability (Deng and Manthiram, 2011; Liang et al., 2016; Masoumi et al., 2017). However, with the increase of Ni content, some intrinsic defects originating from LiNiO2 are prone to be more obvious, such as: Li/Ni cation mixing, air sensitivity, serious slurry gelation, and unwanted gas evolution, which should be solved urgently before their large-scale application (Park et al., 2016; Zhao et al., 2017; Kim et al., 2019a; Duan et al., 2019; Zhang, 2020).
Li/Ni mixing is one of the characteristic defects of Ni-rich layered oxides since Ni2+ (0.69 Å) and Li+ (0.76 Å) have a similar ionic radius, and Ni2+ is difficult to fully oxidized into Ni3+ during the sintering synthesis process. In order to minimize the Li/Ni mixing degree, the synthesis process needs to be carried out under an oxygen atmosphere by adding an excessive Li source (Wu et al., 2015; Park and Choi, 2018; Li et al., 2019a; Zhang et al., 2019b). However, after sintering, the residual lithium remains on the surface of the final product, which is prone to absorbing and reacting with moisture and carbon dioxide (CO2) in air. Therefore, residual lithium compounds spontaneously generate (Cho et al., 2014). In addition, the external Ni3+ ions with high chemical activity have a tendency to be reduced into Ni2+, together with the lattice oxygen release, the growth of residual lithium compounds, and the surface phase transition during air exposure (Jo et al., 2014b; Tian et al., 2018; Yang et al., 2019a). Those are the main reasons why residual lithium compounds increase on the surface of Ni-rich cathode materials with an air exposure time extension.
Furthermore, the formation of residual lithium compounds not only influences the electrode preparation, but also results in capacity fading and is a safety hazard. During the electrode slurry preparation, the high alkaline Ni-rich cathode materials (pH ≈ 11) will give rise to polyvinylidene fluoride (PVDF) degradation and slurry gelation, thus worsening the processability of the electrode slurry (Ross et al., 2000). Another issue is that due to the intrinsic insulation of surface impurities, the Li+ diffusion is seriously restricted, leading to the increased cell polarization and inferior cycling performance (Chen et al., 2019; Wang et al., 2019). Moreover, the electrochemical decomposition of residual lithium compounds will cause cell swelling and localized heating, which are potential safety risks in its practical application (Min et al., 2017; Mao et al., 2019; Renfrew et al., 2019). As a consequence, how to effectively reduce surface residual lithium compounds of Ni-rich cathode materials, has become a current research hotspot.
Up to now, various strategies have been put forward to overcome the aforementioned issues, such as a washing process, secondary sintering, surface coating, heterogeneous doping and slurry additives, which will be introduced later. In addition, recently, Renfrew et al. found that, up to 4.8 V vs Li/Li+ on the first charge, the decomposition of residual lithium compounds was the main source of CO and CO2 evolution, not the electrolyte decomposition (Renfrew and McCloskey, 2017). They also suggested that oxygen evolution from the lattice of Ni-rich layered oxides decreased after removing partial residual Li2CO3, implying that the residual lithium impurities may facilitate the generation of oxygen, which is different from what we knew before, that lattice oxygen release originates from an irreversible H2 to H3 phase transition (Flores et al., 2020). Therefore, understanding the origin of residual lithium compounds and the possible solutions of how to remove them appear to be particularly necessary.
SOURCES OF RESIDUAL LITHIUM COMPOUNDS
Excessive Addition of Lithium in Synthesis
For the purpose of gaining Ni-rich layered oxides, the transition metal hydroxide precursor, usually prepared by a co-precipitation method, is uniformly mixed with a lithium source (e.g. lithium hydroxide and lithium carbonate) and sintered in high temperature at oxygen atmosphere for a period of time. The sintering temperature must be higher than the melting point of the lithium sources. For example, LiOH, the most commonly used lithium source, with a melting point lower than 500°C, is basically sintered above 750°C with a Ni-rich hydroxide precursor. Therefore, the volatilization of lithium during sintering should be taken into consideration. Moreover, due to the similar radius of Li+ (0.76 Å) and Ni2+ (0.69 Å), if the ratio of lithium and the precursor is 1, the Li+/Ni2+ cation mixing will be severe. To reduce the impact of this defect, Arai et al. demonstrated that excessive lithium addition was beneficial to suppress cation mixing so that the resultant Ni-rich materials remained a well-ordered layered structure with ameliorative cycling performance (Arai et al., 1995). For those reasons, in order to compensate for the lithium volatilization at high temperature and to reduce the cation mixing degree, it is necessary to introduce excessive lithium, which normally ranges from 1% to 5%. However, the mass of excess lithium addition is highly related to the sintering temperature and sintering time (Wang et al., 2017; Kong et al., 2019). As a result, after sintering, a part of unreacted lithium remains on the surface mainly in the form of lithium oxide (Li2O). It is worth noting that the lithium oxide on the surface is chemically unstable, and tends to absorb and react with moisture and CO2 in air to further form residual lithium compounds, including LiOH, LiHCO3, and Li2CO3. Cho et al. also reported that, if too much residual lithium (Li2O) remained on the surface of the final product after calcination, LiOH would be the major constituent part (Cho et al., 2014). The total reactions of residual lithium and air can be described as Equation 1-3:
Air Sensitivity
Apart from the formation of Li2O after sintering, with a strong alkaline surface, Ni-rich cathode materials are also intrinsically sensitive to moisture and CO2, forming residual lithium compounds on the surface during the unavoidable air contact. However, the surface degradation mechanisms of Ni-rich cathode materials exposed to ambient air still remains controversial, which can be mainly divided into two kinds: a redox reaction mechanism and a proton–lithium exchange mechanism.
By comparing the amounts of surface impurities on LiNixCoyMnzO2 with different Ni contents, Noh et al. found more carbonates and hydroxides grew on the higher Ni content cathode surface (Noh et al., 2013), revealing that the formation of surface residual lithium compounds was related to surface Nickel ions. Similarly, on the basis of density functional theory (DFT) calculation, Qian et al. promoted that with the increase of Ni content, the charge transfer ability and moisture adsorption energy of Ni-rich layered oxides were prone to being more robust (Qian et al., 2019), suggesting that the growth of Li2CO3 in high Ni content cathodes was faster than it is in a low Ni content one (Figure 1A). As a matter of fact, in view of the crystal field theory, Ni3+ at the octahedral site with an electron configuration of t2g6eg1 is not stable and is prone to giving rise to the Jahn-Teller (J-T) effect, inducing lattice distortion, while Ni2+ with an electron configuration of t2g6eg2 is an inactive J-T ion (Figure 1B) (Kong et al., 2018; Kim et al., 2019b). The chemical active Ni3+ ions therefore tend to be converted to Ni2+, which could alleviate local lattice distortion of Ni-O octahedral and can release partial residual stress and reduce system energy at the same time. Furthermore, the reduction reaction of Ni3+ will accelerate the production of highly active oxygen species (Xiao and Sun, 2018). Consequently, when Ni-rich layered oxides are exposed to ambient air, the active oxygen species will react with the absorbed moisture and CO2 to form hydroxyl and carbonate species, along with the release of lattice oxygen to form oxygen gas. The formed hydroxyl and carbonate species react with lithium ions from host material and finally generate residual lithium compounds (mainly LiOH and Li2CO3), together with the phase transition from a layered structure to a NiO-like rock-salt structure (Huang et al., 2019a; Martinez et al., 2020). The total reaction can be expressed as the following equations:
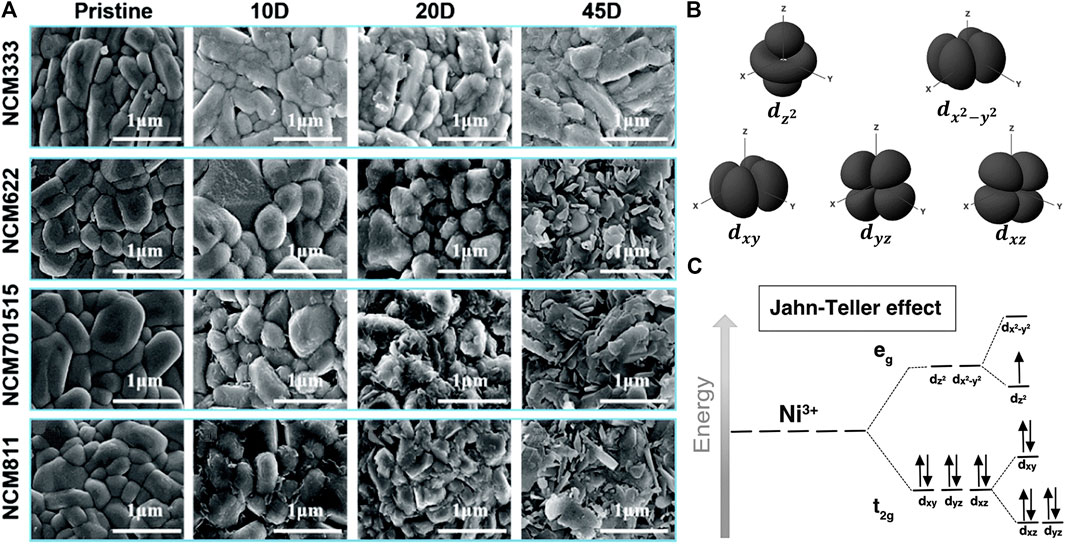
FIGURE 1. (A) SEM images of NCM333, NCM622, NCM701515, and NCM811 after 0, 10, 20, and 45 days of storage (from left to right, respectively) at 25°C and 40% relative humidity. Adapted from [Qian et al., 2019] with permission from Royal Society of Chemistry. (B) and (C) Illustration of the Jahn- Teller effect of NiO6 with energy splitting in an octahedral complex. Adapted from [Kim et al., 2019b] with permission from Royal Society of Chemistry.
Except for the formation of Li2CO3 and LiOH, LiHCO3 is also considered to be a residual lithium compound which may be produced by the reaction between LiOH and CO2 under ambient atmosphere.
In addition, the composition and content of residual lithium compounds are extremely concerned with the temperature, moisture, and CO2 concentration around the storage environment. Thus, the reaction between Ni-rich layered oxide cathodes and ambient atmosphere are more complicated in different conditions. Faenza et al. indicated that moisture was essential for the formation of residual lithium compounds at room temperature, suggesting that Ni-rich layered oxide materials should be stored in a cool and moisture-free space to suppress the spontaneous formation of residual impurities (Faenza et al., 2017). Whereas Shizuka et al. reported that Li1.040Ni0.80Co0.15Al0.05O2 (NCA) could react with pure CO2 to form Li2CO3 at 400°C, without the participation of moisture (Shizuka et al., 2007). Furthermore, Cho et al. demonstrated that if too much residual lithium (Li2O) remains on the surface of the final product after calcination, LiOH will be the major constituent part (Cho et al., 2014). Apart from the residual compounds and various absorbed species, Chen et al. found a delithiation layer existing on the subsurface of LiNi0.6Co0.2Mn0.2O2 (NCM622) stored at 55°C with 80% relative humidity, which implied that the extraction of lithium from host material to surface region really occurred (Chen et al., 2017b). In conclusion, the surface degradation of Ni-rich layered oxides during air exposure are driven by the reduction of chemical active Ni3+ to more stable Ni2+, causing the release of lattice oxygen and the formation of residual lithium compounds on the surface. Owing to the consumption of surface lattice lithium, a NiO-like rock-salt phase layer and a delithiation layer are also generated. Surface coating combined with surface doping, an effective method to stabilize the layered structure and reduce surface reactivity of the active material, has been widely reported to enhance the air stability of Ni-rich layered oxides, which will be subsequently discussed.
Except for the above-mentioned redox mechanism, the additional proton–lithium exchange mechanism has also been proposed, which is supposed to take place in the near surface regions in concert with redox reactions (Shkrob et al., 2017; Toma et al., 2020). The released H+ from surface absorbed water molecular exchanges with the out-migration Li+ and occupy Li+ site, form residual lithium compounds. The H+/Li+ exchange mechanism can be described with the following equations:
Exposing LiNi0.5Co0.2Mn0.3O2 (NCM523) to humid air, Shkrob et al. provided some evidence for a proton–lithium exchange mechanism (Shkrob et al., 2017). First, the contraction of c lattice was observed by XRD, which was mainly attributed to the stronger interaction force between H+ and lattice oxygen. Subsequently, the partial capacity recovery has been detected during several initial charging/discharging cycles since the H+ intercalation was reversible and could be replaced by Li+ again in electrochemical (de)lithiation.
Although the proton–lithium exchange mechanism indicates that moisture is necessary to start the degradation of Ni-rich layered oxides, it cannot explain the acceleration effect of high Ni content on the growth rate of residual lithium compounds. Therefore, the H+/Li+ exchange mechanism is considered to play a minor role in surface degradation of Ni-rich cathode during air exposure, which usually emerges at the primary stage of air exposure.
Negative Effects of Residual Lithium Compounds
The formation of residual lithium compounds not only puts forward a strict requirement of storage atmosphere for Ni-rich cathode materials, but also sets great challenges for the subsequent slurry processing, cycling performance, and safety issues. In this section, the negative effects of residual compounds are analyzed.
Increase Storage Costs
As shown by the spontaneous growth of detrimental residual lithium compounds on the surface of Ni-rich cathode materials during air exposure, it is inappropriate to store Ni-rich cathode materials in ambient air. Generally, for practical application, Ni-rich cathode materials are stored under vacuum or inert atmosphere conditions, which significantly enhance the storage cost to some extent, leading to inconveniences in production and application. Recently, Faenza et al. compared the growth of residual lithium compounds on LiNi0.8Co0.15Al0.05O2 stored at different conditions for 2 weeks, including ambient air, dry CO2 with less 10 ppm H2O, pure argon (Ar) and a dry room (with dew point about -35°C) (Faenza et al., 2017). The results clearly demonstrate that the formation of residual lithium compounds can be effectively suppressed when the sample is stored in a dry room with a low moisture content. It is therefore suggested that Ni-rich layered oxides are stored at a very low relative humidity condition. Additionally, in order to reduce storage requirements and cost, some surface modifications need to be conducted, such as surface coating and doping, which will be discussed later.
Slurry Processing Performance Deterioration
Poly(vinylidene fluoride) (PVDF) is the most used binder for the preparation of a cathode slurry. Generally, PVDF can be fully dissolved in N-methyl-2-pyrrolidone (NMP) solution, but it is insoluble in an aqueous solution. It is worth noting that PVDF is prone to a defluorination reaction under an alkaline condition (Ross et al., 2001). As a result, when it encounters a Ni-rich cathode, strong alkaline residual lithium compounds, such as LiOH, can react with PVDF, thereby causing PVDF degradation, reducing the cohesiveness of slurry, and generating H2O simultaneously. Additionally, PVDF will be rapidly condensed and gelatinized in water, severely deteriorating the slurry processing performance. In fact, slurry is unavoidably exposed to air, making alkaline slurry prone to absorbing the moisture from air, which will make the slurry fabrication difficult. Hence, the air humidity should be strictly controlled in the manufacturing plant to reduce the harmful effects of moisture absorption.
Electrochemical Degradation
As mentioned above, Ni-rich cathode materials exposed to ambient air may cause severe surface degradation, consuming Li+ from host materials, further leading to the formation of the delithiation layer, the rock-salt cubic phase layer, and the residual lithium compounds layer. As a result, the loss of Li from host material directly triggers the initial capacity fading. Even worse, being covered by poor ionic/electron conductivity impurities and subsurface rock-salt cubic phase layer, the Li+ diffusion in the interface of the cathode and electrolyte will be significantly suppressed. As a consequence, the charge transfer resistance increases so drastically that battery polarization obviously intensifies, further cutting down discharge capacity and worsening rate performance. By coating LiNi0.7Mn0.3O2 with a Li2O layer, Cho et al. simulated the effect of residual lithium compounds growing on the surface of Ni-rich cathode materials (Cho et al., 2014). They indicated that a larger irreversible capacity with limited discharge capacity emerged in LiNi0.7Mn0.3O2, which was attributed to the suppressed Li+ diffusion by insulating the Li2O layer. In addition, the electrochemical reaction heterogeneity caused by surface insulating the Li2CO3 film was reported, which was demonstrated by the splitting of the (003) reflection using the in-situ XRD analysis as presented in Figure 2A (Grenier et al., 2017). In a further step, Qian et al. proposed that the reaction heterogeneity that originated from different energy barriers and activation energies for (de)lithiation of individual particles was due to the uneven growth of residual lithium compounds (Figure 2B) (Qian et al., 2019). More seriously, the augment of impedance may lead to the accelerated localized heating, which increases the risk of catastrophically destroying the batteries or igniting the liquid organic electrolyte. For this reason, safety issues derived from the formation of insulating residual lithium compounds should be taken seriously.
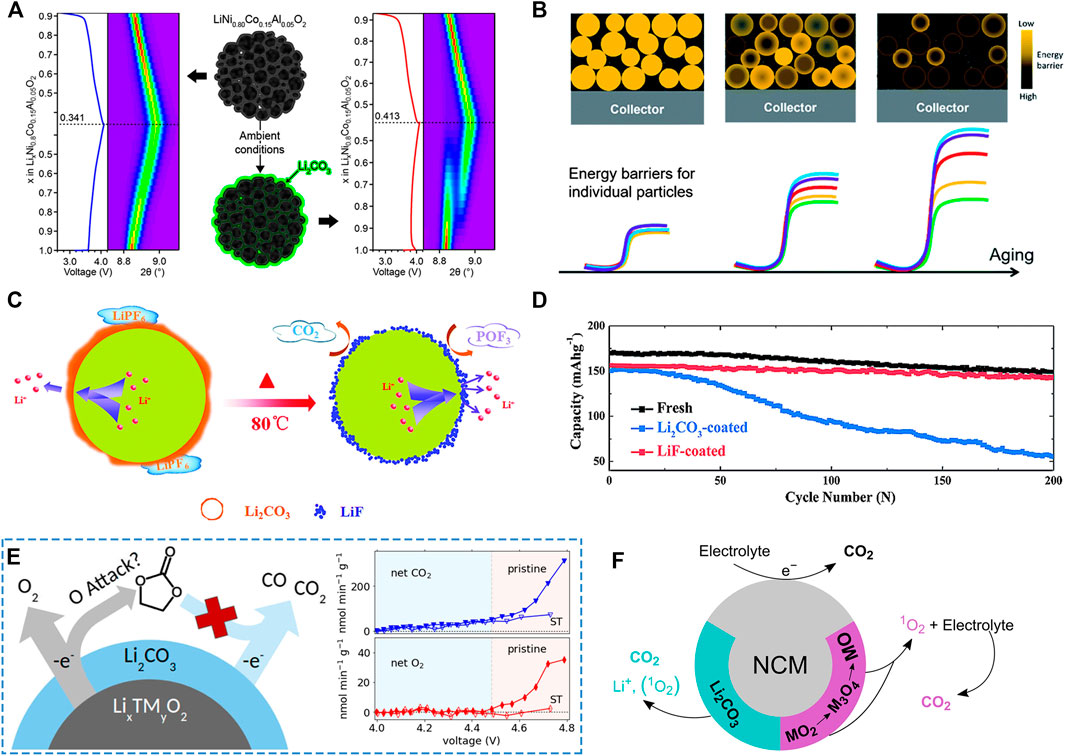
FIGURE 2. (A) The splitting of the (003) reflection of LiNi0.8Co0.15Al0.05O2 after air exposure. Adapted from [Grenier et al., 2017] with permission from American Chemical Society. (B) Schematic diagram of the energy barrier evolution with aging; the different colors of the lines represent different energy barriers from different particles. Adapted from [Qian et al., 2019] with permission from Royal Society of Chemistry. (C) Scheme illustration of the surface reaction of Li2CO3-coated material in LiPF6 electrolyte and (D) Cyclic stability of fresh, Li2O coated, LiF coated NCM811 at 1 C. Adapted from [Bi et al., 2016] with permission from Royal Society of Chemistry. (E) Gas evolution (O2 and CO2) for pristine (untreated) and surface treated (ST) 18O-NMC, showing attenuation of both the CO2 and O2 evolution rates after removal of a portion of Li2CO3. Adapted from [Renfrew and McCloskey, 2017] with permission from American Chemical Society.) (F) Scheme illustration of the origin of CO2 during cycling of Ni-rich layered NCM cathodes, including the decomposition of Li2CO3, chemical and electrochemical oxidation of electrolyte. Adapted from [Hatsukade et al., 2018] with permission from American Chemical Society.
Furthermore, the presence of residual lithium compounds at the interface of electrode and electrolyte could also cause adverse reactions with the LiPF6-based electrolyte, generating CO2 gas and LiF (Figure 2C). In order to confirm the influence of surface LiF and Li2CO3 on the performance of Ni-rich cathode materials, Bi et al. compared the electrochemical performance of both Li2CO3-coated and LiF-coated LiNi0.8Co0.1Mn0.1O2 (NCM811) (Bi et al., 2016). As shown in Figure 2D, the surface Li2CO3 coating layer had a severely negative impact on the cycling stability while it was negligible for the surface LiF coating, which could be attributed to the decomposition of Li2CO3 reacting with the electrolyte. This reaction can be described as follows:
In fact, Li2CO3 is mainly in the form of the amorphous state, and its electrochemical stability is very poor, which is easily decomposed at a high potential (Wang et al., 2018). Hatsukade et al. employed an isotope labeling method to investigate the origins of CO2 during the cycling of LiNi0.6Co0.2Mn0.2O2 (NCM622) (Hatsukade et al., 2018). The CO2 formation at the first charge process was attributed to the surface Li2CO3 decomposition at high potential. However, with prolonged cycling and the decrease of surface Li2CO3, CO2 stemming from the chemical oxidation (with lattice oxygen) and electrochemical oxidation at high potential of electrolyte solvent became dominant (Figure 2F). In addition, there is an ambiguous understanding on whether the decomposition of Li2CO3 will produce oxygen simultaneously, because oxygen may also originate from lattice. In this respect, the oxidation of Li2CO3 has already been studied in Li-air cells (Mahne et al., 2018), producing O2 and CO2, which can be described as follows:
Subversively, Renfrew et al. observed the CO2/CO emission caused by the decomposition of residual Li2CO3 during the first charge, and the oxygen evolution from the lattice of Ni-rich cathode materials also decreased after removing a portion of surface Li2CO3 (Renfrew and McCloskey, 2017), suggesting that the oxidation of Li2CO3 is related to the lattice oxygen release (Figure 2E). Inspired by this research, quantitative studies of the influence of surface impurities on the structure evolution of Ni-rich cathode materials during the cycling tests are needed. Although the decomposition mechanism of Li2CO3 is not fully understood, the decomposition of Li2CO3 reduces the Coulombic efficiency of the initial several cycles. It also highlights the seriousness of safety issues, such as increasing batteries’ internal pressure and heat generation.
Moreover, the CO2 stemming from the decomposition of Li2CO3 and electrolyte solvents can react with LiOH to reformate trace H2O and Li2CO3 (Robert et al., 2015). Even worse, the trace H2O is harmful to electrolyte salt, resulting in the decomposition of LiPF6 and the formation of HF and other by-products. This process can be expressed as follows:
The resultant HF is detrimental to the electrochemical performance of Lithium-ion batteries. On the one hand, HF accelerates the decomposition of surface impurities including Li2CO3 and LiOH. On the other hand, HF corrodes the surface of Ni-rich cathode materials to promote the dissolution of transition metal ions, especially Ni ion, leading to rapid capacity loss and surface degradation. Moreover, after the removal of surface impurities, a greater electrochemically active surface will be exposed to the electrolyte, which will further boost the dissolution of transition metal ions and the decomposition of electrolyte solvent at high potential (Kleiner et al., 2015; Kim et al., 2016; Liang et al., 2019).
Challenges and Solutions to Residual Lithium Compounds
To avoid the adverse effects of residual lithium compounds on powder storage, slurry processing and electrochemical performance of Ni-rich cathode materials, numerous methods are conducted to remove the surface impurities and to enhance the air-storage stability.
Washing & Annealing Process
Washing with water is widely applied in practical industrial manufacturing to eliminate the detrimental residual lithium compounds. To be specific, the alkaline Ni-rich cathode materials are stirred in deionized water to remove surface residual lithium compounds and dried at a high temperature in an air-free atmosphere after filtration, which is called the washing & annealing process (Kim et al., 2018). The concentration of residual lithium compounds and powder pH value can be effectively reduced after washing. As a consequence, gas evolution of the washed cathode materials is significantly suppressed during the charging process. Furthermore, after the washing and annealing process, the cycling performance and capacity retention are dramatically improved with a slight initial discharge capacity decline.
However, it should be mentioned that the capacity degradation of Ni-rich cathode materials may be accelerated after the washing process owing to an improper annealing temperature. As Xiong et al. reported, NCM811 annealed at 300°C after washing exhibited the worst specific capacity and cycling stability compared to the washed or non-washed sample annealed at 700°C (Xiong et al., 2013). Except for water washing, a faintly acidic solution is also a substitution (Park et al., 2017; Xu et al., 2017; Wu et al., 2018). Park et al. compared two kinds of solvents, de-ionized water and diluted nitric acid with a solvent evaporation process. They suggest that the diluted nitric acid eliminates surface residual compounds more efficiently than de-ionized water. The sample treated with diluted nitric acid exhibited the superior cycling performance (Park et al., 2017). Analogously, compared to water washing, mild polyaniline (PANI) could also be utilized as a solvent to remove residual impurities, and to synchronously form a protective layer on the surface, which greatly enhances the surface stability of Ni-rich cathode materials (Xu et al., 2017). In addition to the above washing solvents, alcohol washing is a “compromise” process, which can reduce the lithium residue and does not destroy the surface structure (Cao et al., 2019). However, the solubility of LiOH and Li2CO3 in ethanol is low, which should be further improved. Apart from annealing temperature and washing solvent, the electrochemical performance of washed materials is closely related to the powder-to-solvent ratio and washing time, which is a complex technical method.
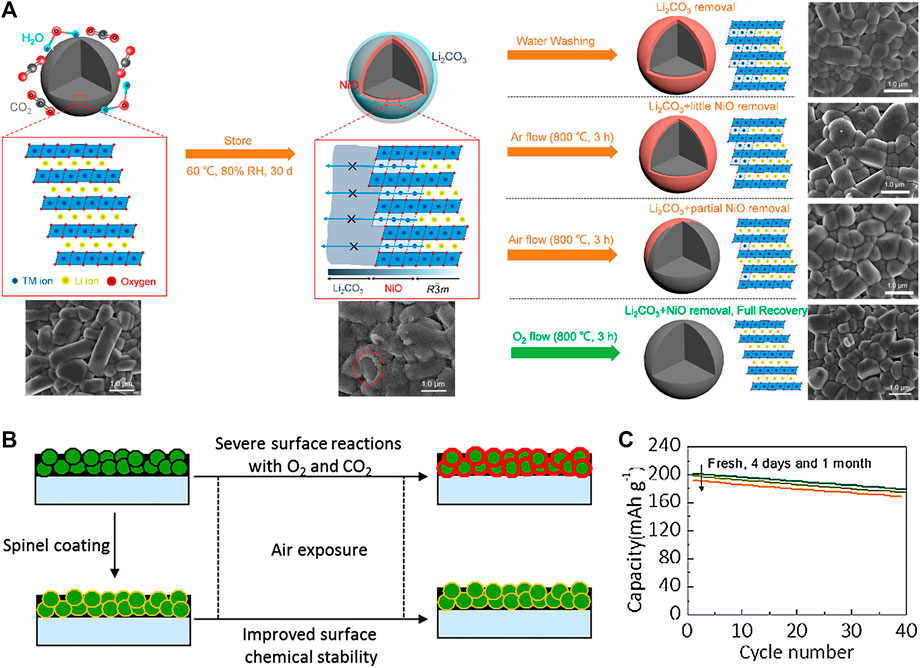
FIGURE 3. (A) Scheme illustration of the failure and recovery behaviors of the stored NCM701515 with the structure and surface morphology evolution. Adapted from [Huang et al., 2019a] with permission from American Chemical Society. (B) Schematic view of the effect of spinel LiMn1.9Al0.1O4 coating on the Ni-rich layered oxide surface and (C) The cycling performance of spinel LiMn1.9Al0.1O4 modified sample after air exposure. Adapted from [Oh et al., 2016] with permission from Royal Society of Chemistry.
Although the residual lithium compounds and powder pH can be effectively reduced by the washing process, the washed Ni-rich cathode materials are more air sensitive than non-washed materials because of more chemically active surfaces (Xiong et al., 2013; Kim et al., 2018). After being exposed to the air for the same time, a thicker amorphous residual lithium layer is formed on the surface of washed Ni-rich cathode materials (Jo et al., 2016). During the formation of an amorphous residual lithium layer, a part of lithium on the subsurface of Ni-rich cathode materials will be extracted from the host structure along with the increased cationic disorder. As a result, a rock-salt NiO-like surface is generated, which significantly deteriorates the electrochemical performance of Ni-rich cathode materials. Therefore, taking air sensitivity of washed Ni-rich cathode materials into consideration, it is very important to store them in an air free- or humidity and CO2 controlled conditions. Moreover, in practical application, washing treatment is generally combined with other treatments such as surface coating, aiming to prevent a chemically unstable surface from ambient air. In addition, due to the generation of waste water, the increased processing time and capital cost of waste water treatment should also be considered, and still remains a huge challenge for its practical implementation.
Secondary Sintering
Secondary sintering is similar to the annealing process after washing. However, compared to the washing process, secondary sintering does not involve the generation of waste water, which is a solid phase reaction process mainly including the decomposition of residual lithium compounds and surface reconstruction. In order to decompose the residual lithium compounds sufficiently, the sintering temperature is usually increased to the initial sintering temperature, sometimes even higher. It is important to note that the evaporation of Li2O should be taken into account to reduce capacity loss, so that the secondary sintering time is not long. Furthermore, calcination atmosphere is another factor effecting secondary sintering as well. According to previous literature reported by Jo and co-workers [Ross et al., 2001], for freshly sintered or few surface residual impurities materials, when being reheated in air atmosphere, a sintering temperature between 200°C and 400°C is optimal, otherwise the structural integrity will be destroyed at a higher temperature.
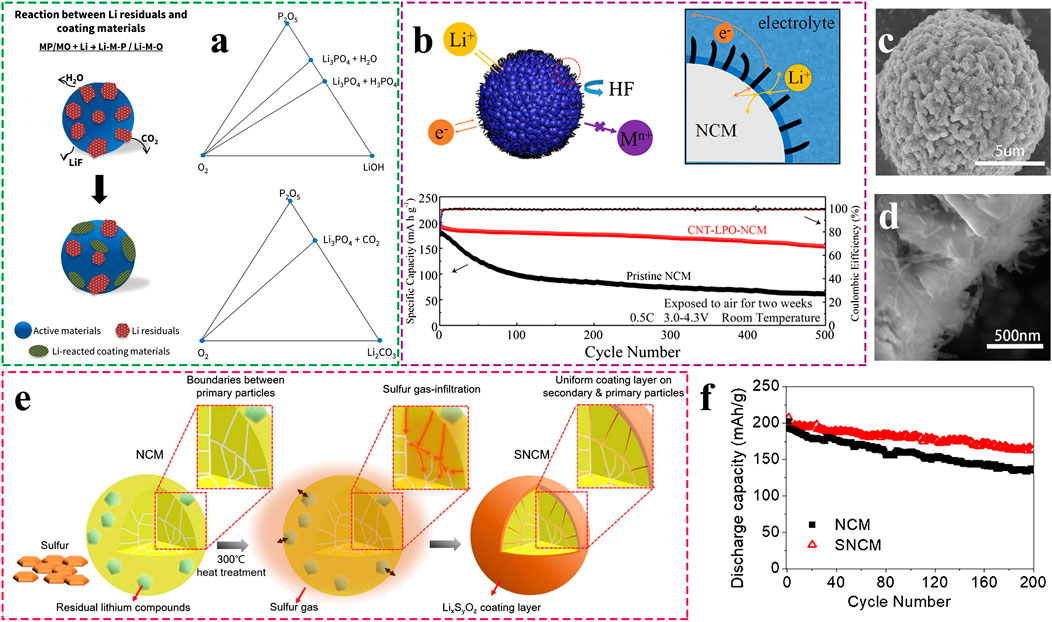
FIGURE 4. (A) Schematic views of the Li-reactive coating process and phase diagram for P2O5−LiOH/Li2CO3−O2. Adapted from [Min et al., 2017] with permission from American Chemical Society. (B) Schematic diagrams of the working mechanism of CNT& Li3PO4 coating layer and cycling stability of CNT& Li3PO4 coated sample compared to pristine and (C and D) SEM images of the CNT& Li3PO4 coated sample. Adapted from [Yang et al., 2019c] with permission from American Chemical Society. (E) Schematic views of the sublimation-induced gas-reacting process on the surface and inside of the secondary particles and (F) The improved cycling performance of surface LixSyOz coated sample. Adapted from [Kim et al., 2020] with permission from American Chemical Society.
Recently, Huang et al. conducted secondary sintering on the degraded LiNi0.70Co0.15Mn0.15O2 under various atmospheres at a high temperature (800°C) (Figure 4A) (Huang et al., 2019a). To get the degraded sample, the aging process was carried out at 60°C and 80% relative humidity for 30 days, in which a residual lithium compound layer, mainly composed of Li2CO3 with ∼90 nm thickness, was detected on the surface with a NiO-like layer formed at the near surface region. Successfully, the degraded LiNi0.70Co0.15Mn0.15O2 re-sintered at 800°C under flowing oxygen atmosphere for 3 h, exhibited a comparable electrochemical performance to the pristine one. Interestingly, after high temperature calcination under oxygen atmosphere, the surface impurities layer and NiO-like layer disappeared, and the surface was reconstructed to the layered structure. However, under other atmospheres such as air and argon, the surface structure can barely recover to the original layered structure and a NiO-like layer still remains, indicating that the oxidizing atmosphere is necessary for the reversion of degraded materials during the secondary sintering treatment.
Slurry Additives
Some additives are often added into slurry to reduce residual lithium compounds and slurry pH, thereby meliorating slurry processability. In detail, the additives should be moderate so that they only react with surface impurities without other undesirable side effects. This strategy is considered to be one of the most convenient methods for practical manufacturing. For instance, LiPF6 is adopted as a slurry additive to wipe off alkaline residual lithium compounds in NCM811 slurry, finally forming into LiF and Li3PO4 (Zhang et al., 2019d). With 0.5–1.0 wt. % LiPF6 addition (versus the mass of NCM811), the cycling stability and rate capacity of NCM811-Li cells are improved, which can be attributed to the formation of stable LiF and Li3PO4 and the decrease of insulating residual impurities.
Surface Coating
Although the surface residual impurities and lithium compounds can be removed after washing or secondary sintering treatment, the air sensitivity of Ni-rich cathode materials still cannot be fully solved. Therefore, Ni-rich cathode materials should be strictly stored in an atmosphere-controlled condition to avoid contact with H2O and CO2. In order to overcome this problem, various surface modification methods are developed. In this respect, surface coating is one of the most widely used methods in laboratory investigation. Generally, surface coating layers can not only enhance the air-storage stability of Ni-rich cathode materials, but also protect Ni-rich cathode materials from HF corrosion and detrimental side reactions with electrolyte at high potential. Up to now, various surface coating agents have been adopted to reduce the residual lithium impurities and to enhance the air storage stability of Ni-rich cathode materials, including phosphates (Jo et al., 2014a; Chen et al., 2017a; Min et al., 2018; Fan et al., 2019; Zou et al., 2020), fluoride (Dai et al., 2019; Huang et al., 2019b), conducting polymers (Sun et al., 2018; Gan et al., 2019; Yang et al., 2019b), and metallic oxides (Min et al., 2018; Zhao et al., 2018; Becker et al., 2019; Ho et al., 2020; Mo et al., 2020; Zhao et al., 2020). However, the formation mechanisms and functions of these coating layers are quite different, and need to be further investigated.
First, a coating layer can be physically formed on the Ni-rich cathode surface without reacting with residual lithium compounds. This kind of coating layer is electrochemically stable and nonreactive with electrolytes. As shown in Figure 3B, C, the air-storage stability of LiNi0.7Co0.15Mn0.15O2 coated with chemically stable spinel LiMn1.9Al0.1O4 is significantly improved. After being exposed to ambient air for 1 month, the capacity retention of the LiMn1.9Al0.1O4 coated LiNi0.7Co0.15Mn0.15O2 sample is compared to the fresh one (Oh et al., 2016). In addition, MnO2 coated LiNi0.8Co0.15Al0.05O2 can effectively prevent LiNi0.8Co0.15Al0.05O2 from absorbing the moisture and CO2 in air atmosphere and the HF erosion during long-term cycling (Zhao et al., 2018). Furthermore, TiO2 (Mo et al., 2020), ZrO2 and other oxides are also employed to construct protective layers on the surface of the Ni-rich cathode to decrease air sensitivity.
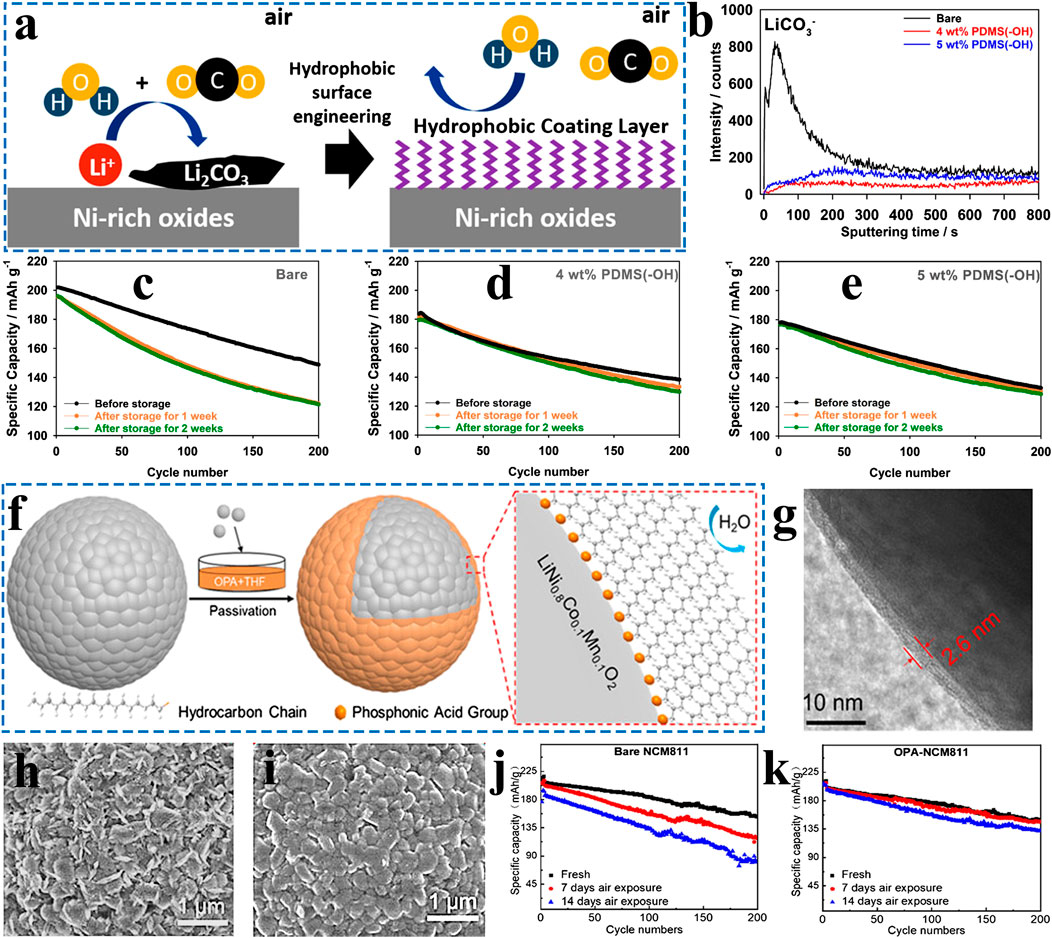
FIGURE 5. (A) Schematic drawing of the function of surface hydrophobic coating layer and (B) TOF-SIMS depth profiles of LiCO3− for bare, 4 wt. % PDMS(−OH)-grafted, and 5 wt. % PDMS(−OH)-grafted LiNi0.8Co0.1Mn0.1O2 powder samples after storage in a humidity chamber at 50% RH and 25°C for 1 week. (C-E) Cycling performances of bare, 4 wt. % PDMS(−OH)-grafted, and 5 wt. % PDMS(−OH)-grafted LiNi0.8Co0.1Mn0.1O2 after being exposed to a humidity chamber at 50% RH and 25°C, respectively. Adapted from [Doo et al., 2019] with permission from American Chemical Society. (F) Schematic illustration of the preparation process of OPA-coated NCM811 and (G) TEM images of OPA-coated NCM811; SEM images of (H) bare NCM811 and (I) OPA-coated NCM811 after 14-day air exposure; Cycling performance of (J) bare NCM811 and (K) OPA-coated NCM811 after different air exposure durations. Adapted from [Gu et al., 2020] with permission from American Chemical Society.
Moreover, the coating layers can be formed in-situ on the surface of Ni-rich cathode materials via chemical reactions between coating media and residual lithium compounds, which could eliminate surface impurities as well as form a functional film on the surface. For example, H3PO4 (Jo et al., 2014a; Min et al., 2017; Yang et al., 2019c), an acidic coating media, can react with the residual lithium compounds, such as LiOH and Li2CO3 to form a Li3PO4 coating layer, which has been verified to effectively enhance the surface stability of Ni-rich cathode materials. Due to the reduced surface insulating impurities and high ionic conductivity of newly generated Li3PO4, the capacity retention and rate capability of Li3PO4-coated NCM622 are greatly improved (Jo et al., 2014a). Additionally, Li3PO4 reacts with trace water in electrolytes to suppress the formation of HF, thereby preventing electrode erosion, which can be described as follows:
Furthermore, Min et al. investigated metal phosphates and metal oxides reacted with residual lithium compounds using a hybrid functional theory calculation (Min et al., 2017). As shown in Figure 4A, metal phosphates could effectively reduce both LiOH and Li2CO3, whereas metal oxides tend to react with LiOH more, in which P2O5 may be an optimal choice. In a further step, Yang et al. constructed a four-phase cathode electrolyte interface on NCM811, as described in Figure 4B (Yang et al., 2019c). The phosphoric acid reacted with surface residual lithium compounds to form an ionic conductive Li3PO4 layer, and carbon nanotubes were coated on the surface to penetrate through the Li3PO4 layer (Figure 4C, D). Thus, the ionic conductivity and electronic conductivity of NCM811 were both enhanced, leading to the greatly improved rate performance and capacity retention after surface modification. More importantly, even after being exposed to high moist air for 2 weeks, the modified sample could still deliver 154.2 mA h g−1 at 0.5 C after 500 cycles (Figure 4B).
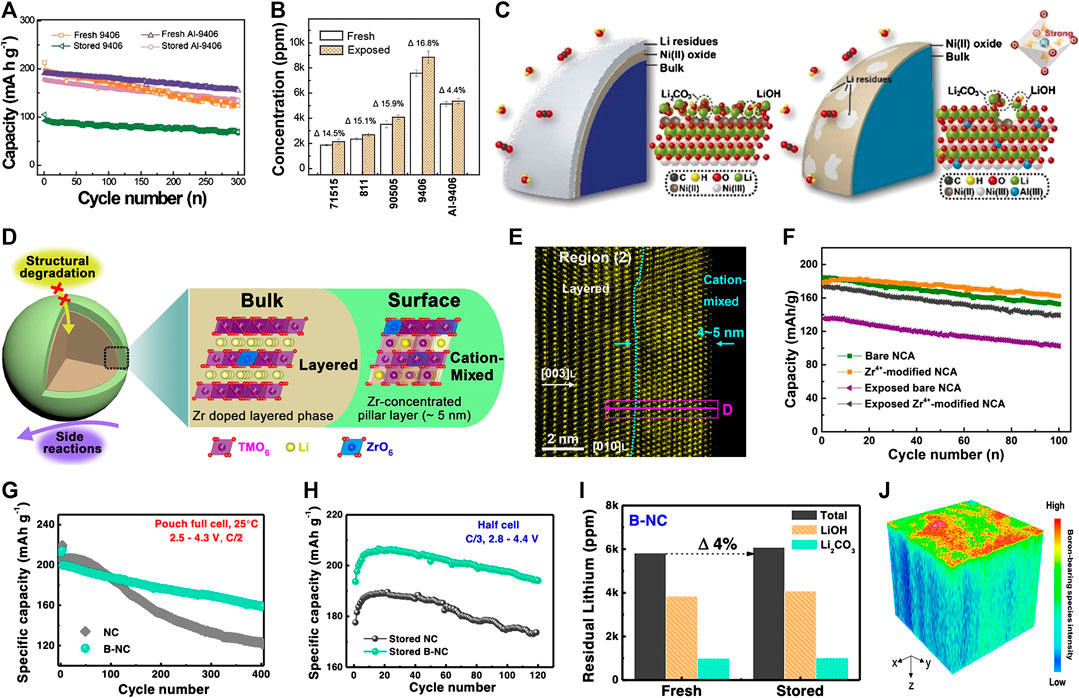
FIGURE 6. (A) Cycling performance curves of pristine and Al doping modified material before and after air storage for 30 days and (B) Concentration of residual lithium species on Ni-rich cathode with various Ni contents before and after air exposure for 30 days and (C) Schematic illustration of the mechanism of Al-doping in improving air stability of Ni-rich cathode. Adapted from [You et al., 2018] with permission from Wiley-VCH Verlag GmbH &Co. KGaA, Weinheim. (D) Schematic view of the surface structure of Zr doped Ni-rich cathode with its functions during cycling and (E) HAADF−STEM image as an evidence of the formation of cation mixed layer. Adapted from [Han et al., 2018] with permission from American Chemical Society. (F) Cycling performances of both bare and Zr4+ modified NCA before and after air exposure, indicating enhanced cycling stability and air stability of Zr doped NCA. Adapted from [Lai et al., 2019] with permission from Elsevier. (G) Cycling performance comparison of LiNi0.94Co0.06O2 before and after B2O3 doping in pouch full cell with graphite anode cycled between 2.5 and 4.3 V at 25°C and (H) Cycling performance comparison of the 30-day stored LiNi0.94Co0.06O2 before and after B2O3 doping in half cell and (I) Residual lithium content changes of the fresh and 30-day air-stored B2O3 doped LiNi0.94Co0.06O2 and (J) TOF-SIMS three dimension depth profiling of Box− (x = 1 or 2) species in the fresh B2O3 doped particle. Adapted from [Xie et al., 2019] with permission from American Chemical Society.
ptApart from the liquid-solid reaction, the gas-solid reaction is also employed to eliminate surface impurities, which could essentially avoid the generation of waste water. As illustrated in Figure 4E, the pioneering work (Kim et al., 2020) reported by Kim and co-works presented a novel sublimation-induced gas-reacting (SIGR) process on NCM811. The gas-phase sulfur (S) reacted with residual lithium compounds at a low temperature of 300°C and in-situ constructed a LixSyOz coating layer. Remarkably, the LixSyOz phases uniformly generated on the surface of secondary particles, as well as in the boundaries between internal primary particles. Consequently, the SIGR-treated NCM811 exhibited improved cycling stability, which were mainly attributed to the protected surface and suppressed anisotropic volume changes during (de)lithiation (Figure 4F).
Since moisture is one of the essential conditions for the formation of residual lithium compounds, thereby constructing a hydrophobic layer tightly coated on the cathode surface is highly expected to overcome this intractable issue (Doo et al., 2019; Gu et al., 2020). The modified hydrophobic surface effectively blocks the direct contact between moisture and the chemically unstable surface of Ni-rich cathode materials, further suppressing the formation of residual lithium compounds. Till now, various organic molecules are adopted as surface coating materials for modifying Ni-rich cathode materials. As shown in Figure 5A-E, hydrophobic polydimethylsiloxane (PDMS) coated NCM811, with a strong M−O−Si covalent bond, exhibited the enhanced air storage stability (Doo et al., 2019). Additionally, octadecyl phosphate (OPA) can be utilized to form a hydrophobic self-assembled monolayer on the surface of Ni-rich cathode materials to improve air-storage stability (Figures 5F-K) (Gu et al., 2020).
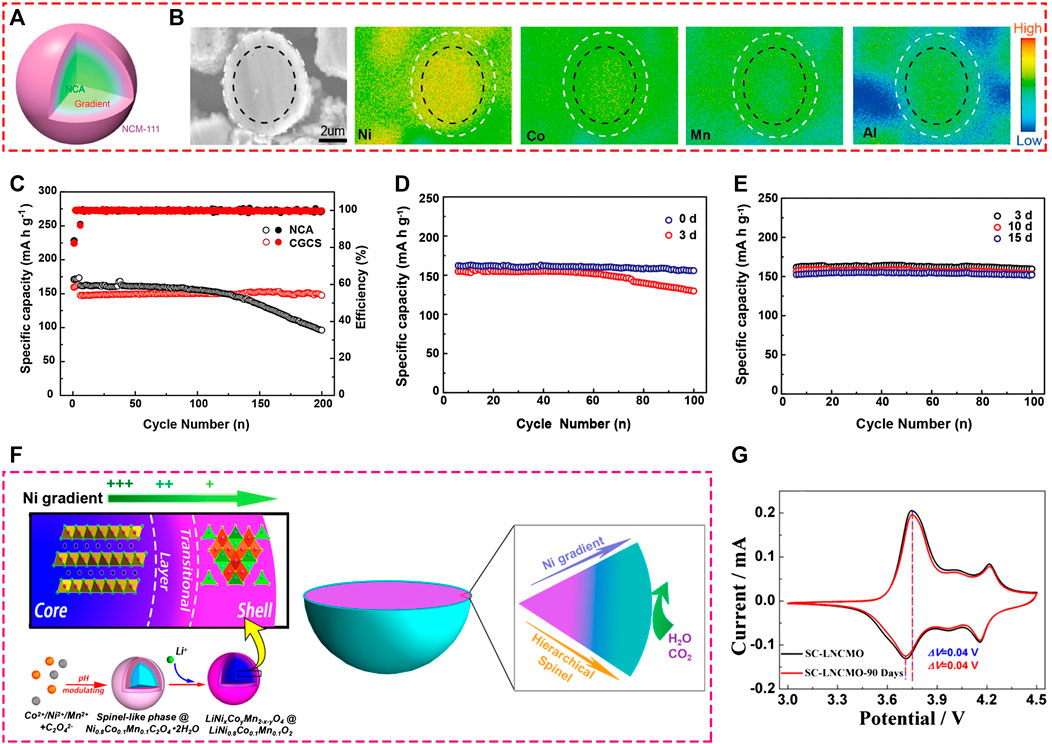
FIGURE 7. (A) Schematic view of the concentration-gradient core-shell structure cathode (CGCS) material; (B) Cross-sectional image of CGCS and corresponding element maps of Ni, Co, Mn, and Al; (C) Cycling performance comparison of pristine NCA and CGCS between 3.0 and 4.3 V; Cycling performance of (D) pristine NCA and (E) CGCS after air exposure with a relative humidity of about 30% for different numbers of days between 3.0 and 4.3 V. Adapted from [Shi et al., 2017] with permission from American Chemical Society. (F) Schematic view of the core-shell structure and preparation process of gradient Ni-rich cathode material; (G) CV curves for gradient Ni-rich cathode material before and after 90-days air exposure. Adapted from [Zhang et al., 2017] with permission from American Chemical Society.
Unfortunately, hydrophobic organic coating layers can only improve the storage property, but it has no obvious improvement in electrochemical performance. Meanwhile, the organic surface coating layer may dissolve into organic electrolyte during the long-term cycling. Even worse, the organic surface coating layers may be oxidized at high voltage, which will deteriorate the electrochemical performance of batteries, such as battery swelling, a thick solid electrolyte interface (SEI) layer and increased polarization.
Doping
Doping is another important strategy to enhance surface chemical and structural stability of Ni-rich cathode materials. By incorporating a small amount of cationic or anionic atoms into the crystal lattice of Ni-rich cathode materials, the air stability is significantly improved. The functions of cationic doping can be classified into two types. One type is the forming a strong covalent bond between doping cation and lattice oxygen to boost lattice structure and to suppress the loss lattice oxygen (You et al., 2018; Huang et al., 2019c). For example, You et al. successfully introduced a small amount of Al3+ into the surface lattice of LiNi0.94Co0.06O2 by sintering a mixture of LiOH and precursor coated with Al(OH)3 at a high temperature (You et al., 2018). The Al-doped LiNi0.94Co0.06O2 exhibited superior storage stability and capacity retention compared to the pristine one (Figure 6A, B). The enhanced surface lattice stability is mainly attributed to the robust Al-O bond (Figure 6C). Moreover, some high valent cations are doped to reduce the content of surface active Ni3+ (being reduced to stable Ni2+ to keep charge balance) (Han et al., 2018; Lai et al., 2019). As displayed in Figure 6D, E cation-mixed nanolayer with ∼5 nm thickness forms on the surface of NCM811 after doping Zr4+, in which Zr4+ ions occupy the transition metal site and increase the amount of Ni2+ to maintain the charge balance (Han et al., 2018). Owing to the highly reactive Ni3+ ions that are effectively reduced, the air-storage stability of NCM811 is improved. Similarly, Lai et al. demonstrated that the air-storage stability of LiNi0.815Co0.15Al0.035O2 can be significantly improved after 1% nano-ZrO2 doping (Figure 6F) (Lai et al., 2019).
Anions doping, such as boron-based polyanion doping, has been verified as an effective strategy to improve the air-exposure stability of the Ni-rich cathode. It is worth noting that the discharge capacity, cycling retention, and air exposure stability are simultaneously strengthened. However, the working mechanism of the boron-based polyanion doped Ni-rich cathode is seldomly investigated (Park et al., 2018; Zhang et al., 2019a; Yang et al., 2020). Recently, Xie et al. promoted a boron spatial distribution of the B2O3 doped LiNi0.94Co0.06O2 cathode material, in which BOx−/LiBO2− species mainly existed on the surface and boron ions (B3+) infiltrated into the host lattice in the tetrahedral interstitial sites of oxygen packing. (Figure 6J) (Xie et al., 2019). The surface species were related to the formation of electrochemically stable cathode electrolyte interface (CEI), and the boron doping could effectively enhance the oxygen lattice stability, thus excellent performances were achieved after boron doping (Figures 6G, H, I).
Furthermore, the combination of doping strategy and surface coating technology is considered to be a promising method to improve overall performance of Ni-rich cathode materials. For instance, Li et al. reported the La/Al co-doping and La2O3 coating co-modified NCM811 Ni-rich cathode (Li et al., 2019b). The La and Al doped into the inner lattice play the role of a pillar, which could enhance the structural stability as well as suppress the phase transition. Furthermore, Ni concentrations decrease in the La-Al co-doped layer in the subsurface region, Additionally, the surface La2O3 coating protects the Ni-rich cathode from the detrimental reaction with air and electrolyte. Thus, the air storage stability and cycling performance are effectively improved. Moreover, the cycling performance and air storage stability of NCM811 could be successfully enhanced via the combination strategy of Li2ZrO3 coating and Zr4+ doping. The surface Li2ZrO3 protective layer as a good Li+ conductor can suppress a surface side reaction as well as improve the Li-ion diffusion rate. More importantly, Zr4+ doping can stabilize the structural stability and reduce oxygen loss. In this way, the overall performance of NCM811 is improved. (Zhai et al., 2020).
Gradient Materials
It is widely accepted that the air-storage stability and thermal property of Ni-rich cathode materials are negatively related to the Ni concentration. In other words, the air storage stability can be improved by decreasing Ni concentration. However, this strategy will cause the capacity declination. So, can we reach an optimal equilibrium point where both relatively high discharge capacity and stable air-storage performance exist? Constructing gradient materials, with low a Ni concentration outer surface and high Ni content inner core, provides the answer. By changing the proportion of transition metal ions at different periods of coprecipitation, Shi et al. synthesized a surface concentration-gradient spherical Ni-rich cathode material with diverse elemental composition, in which the core inside was LiNi0.80Co0.15Al0.05O2 and the surface was composed of LiNi1/3Co1/3Mn1/3O2 (Figures 7A, B) (Shi et al., 2017). Compared to the pristine LiNi0.80Co0.15Al0.05O2, the gradient material presented significantly enhanced air stability (Figures 7D, E) and excellent cycling performance (Figures 7C).
Moreover, depending on the different precipitation pH values for transition metal ions, a gradient precursor can be generated by regulating co-precipitation pH as well. Figure 7F illustrates the gradient Ni-rich cathode material consisting of a layer-structure LiNi0.8Co0.1Mn0.1O2 core, gradient Ni concentration interlayer, and spinel-like LiNixCoyMn2-x-yO4 shell (Zhang et al., 2017). Due to the reduced Ni concentration and the formation of an air-stable spinel layer in the surface region, the gradient Ni-rich cathode material presents greatly improved long-term air storage stability (Figure 7G).
Summary and Perspectives
In this review, the origins and negative effects of residual lithium compounds on air storage performance, processing performance, and electrochemical performance of Ni-rich cathode materials were analyzed. Owing to the residue lithium and chemical active Ni3+ on the surface, Ni-rich cathode materials are chemically sensitive to moisture and CO2. Residual lithium compounds generate on the surface during air exposure, which have adverse effects on the processing and electrochemical performance of Ni-rich cathode materials. Residual lithium compounds with a strong alkaline feature will cause the decomposition of PVDF and lead to the gelation of the cathode slurry. In addition, due to the insulating impurities on the surface, the Li+ diffusion in the interface of the cathode and electrolyte will be suppressed and battery polarization will increase. Even worse, at the cost of consuming Li+ from host materials, the structure near the surface region of Ni-rich cathode materials is deteriorated, as well as the electrochemical performance. It is worth noting that the existence of Li2CO3 has negative effects on the cycling stability of Ni-rich cathode materials. Quantitative studies related to the mechanism of the effect of Li2CO3 on the electrochemical performance of Ni-rich cathode materials are therefore still required. In addition, under high temperature and high voltage (≥ 55°C, > 4.3 V), the mechanism of CO2 production and its influence on electrochemical performance should be further studied.
Since Ni-rich cathode materials will deteriorate during the long-term air exposure, one option is to store them in a vacuum or in an inert atmosphere. However, this strategy will increase the cost of storage, and it is not convenient for production and application. Instead, storing them in a low relative humidity condition seems more practical. To remove surface residual lithium compounds, new types of cleaning agents that can effectively remove lithium residue, but not destroy the surface structure, should be further screened. Furthermore, washing combined with an annealing process and secondary sintering are widely implemented in large-scale application. The washing time and powder-to-solvent ratio should be systematically studied to obtain an optimal design. Moreover, the washing process always takes place in conjunction with surface coating to overcome the disadvantages as Ni-rich cathode materials are more sensitive to air after washing. Secondary sintering is preponderant in the reversion of the severely degraded Ni-rich materials, in which sintering temperature and time should be carefully controlled.
Although the surface residual impurities and lithium compounds can be removed after washing or secondary sintering treatment, the intrinsic air sensitivity of Ni-rich cathode materials still cannot be fully solved. Combining a doping strategy and surface coating technology is one useful solution to reinforce the air storage stability of Ni-rich cathode materials. In future studies, it is important to enhance the lattice matching of the doping and coating interface and to develop a facile method for large-scale production. Another solution is constructing gradient materials with low Ni concentration at the outer surface. We believe that this review provides an in-depth understanding of the residual lithium compounds in Ni-rich cathode materials.
Author Contributions
AC: Writing --original draft preparation. KW: Writing --original draft preparation. JL: Writing --original draft preparation. QM: Writing --Reviewing and Editing. ZX: Visualization. DZ: Writing --Reviewing and Editing. GW: Visualization. PL: Writing --original draft preparation. JH: Writing --Reviewing and Editing. YY: Writing --Reviewing and Editing. YX: Conceptualization, Supervision.
Conflict of Interest
Author QM was employed by the company Zhejiang Meidu Hitrans Lithium Battery Technology Co., Ltd. Author DZ was employed by the company SolaXPower Network Technology (Zhejiang) Co., Ltd. Author GW was employed by the company Hengdian Group DMEGC Magnetics Co. Ltd. Author PL was employed by the company Farasis Energy Inc.
The remaining authors declare that the research was conducted in the absence of any commercial or financial relationships that could be construed as a potential conflict of interest.
Funding
This work was supported by the China Postdoctoral Science Foundation (2020M671785 and 2020T130597), the National Natural Science Foundation of Zhejiang Province (LY18E020009, LY21E020005 and 2020C01130) the Open Research Program of Engineering Research Center of Pharmaceutical and Chemical Waste Recycling & Comprehensive Utilization of Zhejiang Province (XHLY2019-4), and the Zhejiang Xinmiao Talents Program (2020R403043).
References
Arai, H., Okada, S., Ohtsuka, H., Ichimura, M., and Yamaki, J. (1995). Characterization and cathode performance of Li1-xNi1+xO2 prepared with the excess lithium method. Solid State Ionics. 80(3-4), 261-269. doi:10.1016/0167-2738(95)00144-u
Becker, D., Borner, M., Nolle, R., Diehl, M., Klein, S., Rodehorst, U., et al. (2019). Surface modification of Ni-rich LiNi0.8Co0.1Mn0.1O2 cathode material by tungsten oxide coating for improved electrochemical performance in lithium-ion batteries. ACS Appl. Mater. Interfaces. 11(20), 18404-18414. doi:10.1021/acsami.9b02889
Bi, Y., Wang, T., Liu, M., Du, R., Yang, W., Liu, Z., et al. (2016). Stability of Li2CO3 in cathode of lithium ion battery and its influence on electrochemical performance. RSC Adv. 6(23), 19233-19237. doi:10.1039/c6ra00648e
Cao, C. H., Zhang, J., Xie, X. H., and Xia, B. J. (2019). A novel method for the modification of LiNi0.8Co0.15Al0.05O2 with high cycle stability and low pH. J. Solid State Electrochem. 23(5), 1351-1358. doi:10.1007/s10008-019-04216-6
Chen, S., He, T., Su, Y., Lu, Y., Ban, L., Chen, L., et al. (2017a). Ni-rich LiNi0.8Co0.1Mn0.1O2 oxide coated by dual-conductive layers as high performance cathode for lithium-ion batteries. ACS Appl. Mater. Interfaces. 9(35), 29732-29743. doi:10.1021/acsami.7b08006
Chen, T., Wang, F., Li, X., Yan, X., Wang, H., Deng, B., et al. (2019). Dual functional MgHPO4 surface modifier used to repair deteriorated Ni-Rich LiNi0.8Co0.15Al0.05O2 cathode material. Appl. Surf. Sci. 465, 863-870. doi:10.1016/j.apsusc.2018.09.250
Chen, Z., Wang, J., Huang, J., Fu, T., Sun, G., Lai, S., et al. (2017b). The high-temperature and high-humidity storage behaviors and electrochemical degradation mechanism of LiNi0.6Co0.2Mn0.2O2 cathode material for lithium ion batteries. J. Power Sources. 363, 168-176. doi:10.1016/j.jpowsour.2017.07.087
Cheng, T., Ma, Z. T., Qian, R. C., Wang, Y. T., Cheng, Q., Lyu, Y. C., et al. (2020). Achieving stable cycling of LiCoO2 at 4.6 V by multilayer surface modification. Adv. Funct. Mater. doi:10.1002/adfm.202001974
Cho, D.-H., Jo, C.-H., Cho, W., Kim, Y.-J., Yashiro, H., Sun, Y.-K., et al. (2014). Effect of residual lithium compounds on layer Ni-rich Li[Ni0.7Mn0.3]O2. J. Electrochem. Soc. 161(6), A920-A926. doi:10.1149/2.042406jes
Yoon, C. S., Choi, M. H., Lim, B-B., Lee, E-J., and Sun, Y-K. (2015). Review—high-capacity Li[Ni1-xCox/2Mnx/2]O2 (x = 0.1, 0.05, 0) cathodes for next-generation Li-ion battery. J. Electrochem. Soc. 162 (14), A2483-A2489. doi:10.1149/2.0101514jes
Dai, S. C., Yan, G. J., Wang, L., Luo, L. M., Li, Y. P., Yang, Y. T., et al. (2019). Enhanced electrochemical performance and thermal properties of Ni-rich LiNi0.8Co0.1Mn0.1O2 cathode material via CaF2 coating. J. Electroanal. Chem. 847. doi:10.1016/j.jelechem.2019.113197
Das, H., Urban, A., Huang, W., and Ceder, G. (2017). First-principles simulation of the (Li–Ni–vacancy)O phase diagram and its relevance for the surface phases in Ni-rich Li-ion cathode materials. Chem. Mater. 29(18), 7840-7851. doi:10.1021/acs.chemmater.7b02546
Deng, T., Fang, X., Cao, L., Chen, J., Hou, S., Ji, X., et al. (2019). Designing in-situ-formed interphases enables highly reversible cobalt-free LiNiO2 cathode for Li-ion and Li-metal batteries. Joule. 3(10), 2550-2564. doi:10.1016/j.joule.2019.08.004
Deng, Z. Q., and Manthiram, A. (2011). Influence of cationic substitutions on the oxygen loss and reversible capacity of lithium-rich layered oxide cathodes. J. Phys. Chem. C. 115(14), 7097-7103. doi:10.1021/jp200375d
Doo, S. W., Lee, S., Kim, H., Choi, J. H., and Lee, K. T. (2019). Hydrophobic Ni-rich layered oxides as cathode materials for lithium-ion batteries. ACS Appl. Mater. Interfaces. 2(9), 6246-6253. doi:10.1021/acsaem.9b00786
Duan, Y., Yang, L., Zhang, M.-J., Chen, Z., Bai, J., Amine, K., et al. (2019). Insights into Li/Ni ordering and surface reconstruction during synthesis of Ni-rich layered oxides. J. Mater. Chem. A. 7(2), 513-519. doi:10.1039/c8ta10553g
Fan, Q., Yang, S., Liu, J., Liu, H., Lin, K., Liu, R., et al. (2019). Mixed-conducting interlayer boosting the electrochemical performance of Ni-rich layered oxide cathode materials for lithium ion batteries. J. Power Sources. 421, 91-99. doi:10.1016/j.jpowsour.2019.03.014
Flores, E., Novák, P., Aschauer, U., and Berg, E. J. (2020). Cation ordering and redox chemistry of layered Ni-rich LixNi1–2yCoyMnyO2: an operando Raman spectroscopy study. Chem. Mater. 32(1), 186-194. doi:10.1021/acs.chemmater.9b03202
Gan, Q., Qin, N., Zhu, Y., Huang, Z., Zhang, F., Gu, S., et al. (2019). Polyvinylpyrrolidone-induced uniform surface-conductive polymer coating endows Ni-rich LiNi0.8Co0.1Mn0.1O2 with enhanced cyclability for lithium-ion batteries. ACS Appl. Mater. Interfaces. 11(13), 12594-12604. doi:10.1021/acsami.9b04050
Grenier, A., Liu, H., Wiaderek, K. M., Lebens-Higgins, Z. W., Borkiewicz, O. J., Piper, L. F. J., et al. (2017). Reaction heterogeneity in LiNi0.8Co0.15Al0.05O2 induced by surface layer. Chem. Mater. 29(17), 7345-7352. doi:10.1021/acs.chemmater.7b02236
Gu, W., Dong, Q., Zheng, L., Liu, Y., Mao, Y., Zhao, Y., et al. (2020). Ambient air stable Ni-rich layered oxides enabled by hydrophobic self-assembled monolayer. ACS Appl. Mater. Interfaces. 12(1), 1937-1943. doi:10.1021/acsami.9b20030
Han, B., Xu, S., Zhao, S., Lin, G., Feng, Y., Chen, L., et al. (2018). Enhancing the structural stability of Ni-rich layered oxide cathodes with a preformed Zr-concentrated defective nanolayer. ACS Appl. Mater. Interfaces. 10(46), 39599-39607. doi:10.1021/acsami.8b11112
Hatsukade, T., Schiele, A., Hartmann, P., Brezesinski, T., and Janek, J. (2018). Origin of carbon dioxide evolved during cycling of nickel-rich layered NCM cathodes. ACS Appl. Mater. Interfaces. 10(45), 38892-38899. doi:10.1021/acsami.8b13158
Ho, V. C., Jeong, S., Yim, T., and Mun, J. (2020). Crucial role of thioacetamide for ZrO2 coating on the fragile surface of Ni-rich layered cathode in lithium ion batteries. J. Power Sources. 450. doi:10.1016/j.jpowsour.2019.227625
Huang, B., Liu, D., Qian, K., Zhang, L., Zhou, K., Liu, Y., et al. (2019a). A simple method for the complete performance recovery of degraded Ni-rich LiNi0.70Co0.15Mn0.15O2 cathode via surface reconstruction. ACS Appl. Mater. Interfaces. 11(15), 14076-14084. doi:10.1021/acsami.8b22529
Huang, J. L., Du, K., Peng, Z. D., Cao, Y. B., Xue, Z. C., Duan, J. G., et al. (2019b). Enhanced high-temperature electrochemical performance of layered nickel-rich cathodes for lithium-ion batteries after LiF surface modification. Chemelectrochem. 6(21), 5428-5432. doi:10.1002/celc.201901505
Huang, Y., Liu, X., Yu, R., Cao, S., Pei, Y., Luo, Z., et al. (2019c). Tellurium surface doping to enhance the structural stability and electrochemical performance of layered Ni-rich cathodes. ACS Appl. Mater. Interfaces. 11(43), 40022-40033. doi:10.1021/acsami.9b13906
Jo, C.-H., Cho, D.-H., Noh, H.-J., Yashiro, H., Sun, Y.-K., and Myung, S. T. (2014a). An effective method to reduce residual lithium compounds on Ni-rich Li[Ni0.6Co0.2Mn0.2]O2 active material using a phosphoric acid derived Li3PO4 nanolayer. Nano Res. 8(5), 1464-1479. doi:10.1007/s12274-014-0631-8
Jo, J. H., Jo, C.-H., Yashiro, H., Kim, S.-J., and Myung, S.-T. (2016). Re-heating effect of Ni-rich cathode material on structure and electrochemical properties. J. Power Sources. 313, 1-8. doi:10.1016/j.jpowsour.2016.02.015
Jo, M., Noh, M., Oh, P., Kim, Y., and Cho, J. (2014b). A new high power LiNi0.81Co0.1Al0.09O2 cathode material for lithium-ion batteries. Adv. Energy Mater. 4(13), 1301583. doi:10.1002/aenm.201301583
Kim, J. H., Ryu, H. H., Kim, S. J., Yoon, C. S., and Sun, Y. K. (2019a). Degradation mechanism of highly Ni-rich Li[NixCoyMn1-x-y]O2 cathodes with x > 0.9. ACS Appl. Mater. Interfaces. 11(34), 30936-30942. doi:10.1021/acsami.9b09754
Kim, J., Lee, H., Cha, H., Yoon, M., Park, M., and Cho, J. (2018). Prospect and reality of Ni-rich cathode for commercialization. Adv. Energy Mater. 8(6), 1702028. doi:10.1002/aenm.201702028
Kim, J., Lee, J., Bae, C., and Kang, B. (2020). Sublimation-induced gas-reacting process for high-energy-density Ni-rich electrode materials. ACS Appl. Mater. Interfaces. 12(10), 11745-11752. doi:10.1021/acsami.0c00038
Kim, N. Y., Yim, T., Song, J. H., Yu, J.-S., and Lee, Z. (2016). Microstructural study on degradation mechanism of layered LiNi0.6Co0.2Mn0.2O2 cathode materials by analytical transmission electron microscopy. J. Power Sources. 307, 641-648. doi:10.1016/j.jpowsour.2016.01.023
Kim, T., Song, W., Son, D.-Y., Ono, L. K., and Qi, Y. (2019b). Lithium-ion batteries: outlook on present, future, and hybridized technologies. J. Mater. Chem. A. 7(7), 2942-2964. doi:10.1039/c8ta10513h
Kleiner, K., Melke, J., Merz, M., Jakes, P., Nagel, P., Schuppler, S., et al. (2015). Unraveling the degradation process of LiNi0.8Co0.15Al0.05O2 electrodes in commercial lithium ion batteries by electronic structure investigations. ACS Appl. Mater. Interfaces. 7(35), 19589-19600. doi:10.1021/acsami.5b03191
Kong, D., Zhang, M., Xiao, Y., Hu, J., Zhao, W., Han, L., et al. (2019). Insights into the structural evolution and Li/O loss in high-Ni layered oxide cathodes. Nano Energy. 59, 327-335. doi:10.1016/j.nanoen.2019.02.059
Kong, F., Liang, C., Longo, R. C., Zheng, Y., and Cho, K. (2018). Atomic-scale understanding of non-stoichiometry effects on the electrochemical performance of Ni-rich cathode materials. J. Power Sources. 378, 750-758. doi:10.1016/j.jpowsour.2018.01.008
Lai, Y., Wu, J., Tang, Y., Shang, G., Yang, X., Fan, H., et al. (2019). Alleviating the air sensitivity of nickel-rich LiNi0.815Co0.15Al0.035O2 cathode by Zr4+-modification for Li-ion batteries. Ceram. Int. 45(11), 14270-14277. doi:10.1016/j.ceramint.2019.04.136
Li, H. Y., Li, J., Zaker, N., Zhang, N., Botton, G. A., and Dahn, J. R. (2019a). Synthesis of single crystal LiNi0.88Co0.09Al0.03O2 with a two-step lithiation method. J. Electrochem. Soc. 166(10), A1956-A1963. doi:10.1149/2.0681910jes
Li, W., Liu, X., Celio, H., Smith, P., Dolocan, A., Chi, M., et al. (2018). Mn versus Al in layered oxide cathodes in lithium-ion batteries: a comprehensive evaluation on long-term cyclability. Adv. Energy Mater. 8(15), 1703154. doi:10.1002/aenm.201703154
Li, Y.-C., Xiang, W., Xiao, Y., Wu, Z.-G., Xu, C.-L., Xu, W., et al. (2019b). Synergy of doping and coating induced heterogeneous structure and concentration gradient in Ni-rich cathode for enhanced electrochemical performance. J. Power Sources. 423, 144-151.https://doi.org/10.1016/j.jpowsour.2019.03.073
Liang, C., Kong, F., Longo, R. C., Kc, S., Kim, J.-S., Jeon, S., et al. (2016). Unraveling the origin of instability in Ni-rich LiNi1-2xCoxMnxO2 (NCM) cathode materials. J. Phys. Chem. C. 120(12), 6383-6393. doi:10.1021/acs.jpcc.6b00369
Liang, L., Zhang, W., Zhao, F., Denis, D. K., Zaman, F. u., Hou, L., et al. (2019). Surface/interface structure degradation of Ni‐rich layered oxide cathodes toward lithium‐ion batteries: fundamental mechanisms and remedying strategies. Adv. Mater. Interfaces. 7(3), 1901749. doi:10.1002/admi.201901749
Liu, H., Yang, Y., and Zhang, J. (2007). Reaction mechanism and kinetics of lithium ion battery cathode material LiNiO2 with CO2. J. Power Sources. 173(1), 556-561. doi:10.1016/j.jpowsour.2007.04.083
Lu, Y., Zhang, Q., and Chen, J. (2019). Recent progress on lithium-ion batteries with high electrochemical performance. Sci. China Chem. 62(5), 533-548. doi:10.1007/s11426-018-9410-0
Mahne, N., Renfrew, S. E., McCloskey, B. D., and Freunberger, S. A. (2018). Electrochemical oxidation of lithium carbonate generates singlet oxygen. Angew. Chem. Int. Ed. 57(19), 5529-5533. doi:10.1002/anie.201802277
Manthiram, A., Knight, J. C., Myung, S.-T., Oh, S.-M., and Sun, Y.-K. (2016). Nickel-rich and lithium-rich layered oxide cathodes: progress and perspectives. Adv. Energy Mater. 6(1), 1501010. doi:10.1002/aenm.201501010
Manthiram, A., Song, B., and Li, W. (2017). A perspective on nickel-rich layered oxide cathodes for lithium-ion batteries. Energy Storage Mater. 6, 125-139. doi:10.1016/j.ensm.2016.10.007
Mao, C., Ruther, R. E., Geng, L., Li, Z., Leonard, D. N., Meyer, H. M., et al. (2019). Evaluation of gas formation and consumption driven by crossover effect in high-voltage lithium-ion batteries with Ni-rich NMC cathodes. ACS Appl. Mater. Interfaces. 11(46), 43235-43243. doi:10.1021/acsami.9b15916
Martinez, A. C., Grugeon, S., Cailleu, D., Courty, M., Tran-Van, P., Delobel, B., et al. (2020). High reactivity of the nickel-rich LiNi1-x-yMnxCoyO2 layered materials surface towards H2O/CO2 atmosphere and LiPF6-based electrolyte. J. Power Sources. 468, 228204. doi:10.1016/j.jpowsour.2020.228204
Masoumi, M., Cupid, D. M., Reichmann, T. L., Chang, K., Music, D., Schneider, J. M., et al. (2017). Enthalpies of formation of layered LiNixMnxCo1-2xO2 (0 ≤ x ≤0.5) compounds as lithium ion battery cathode materials. Int. J. Mater. Res. 108(11), 869-878. doi:10.3139/146.111553
Min, K., Park, K., Park, S. Y., Seo, S.-W., Choi, B., and Cho, E. (2018). Residual Li reactive coating with Co3O4 for superior electrochemical properties of LiNi0.91Co0.06Mn0.03O2 cathode Material. J. Electrochem. Soc. 165(2), A79-A85. doi:10.1149/2.0341802jes
Min, K., Seo, S.-W., Choi, B., Park, K., and Cho, E. (2017). Computational screening for design of optimal coating materials to suppress gas evolution in Li-ion battery cathodes. ACS Appl. Mater. Interfaces. 9(21), 17822-17834. doi:10.1021/acsami.7b00260
Mo, Y., Guo, L., Jin, H., Du, B., Cao, B., Chen, Y., et al. (2020). Improved cycling stability of LiNi0.6Co0.2Mn0.2O2 through microstructure mum consolidation by TiO2 coating for Li-ion batteries. J. Power Sources. 448, 227439. doi:10.1016/j.jpowsour.2019.227439
Mu, L., Kan, W. H., Kuai, C., Yang, Z., Li, L., Sun, C.-J., et al. (2020). Structural and electrochemical impacts of Mg/Mn dual dopants on the LiNiO2 cathode in Li-metal batteries. ACS Appl. Mater. Interfaces. 12(11), 12874-12882. doi:10.1021/acsami.0c00111
Faenza, Nicholas. V., L. B., , Lebens-Higgins, Zachary. W., Plitz, Irene., Pereira, Nathalie., Piper, Louis. F. J., et al. (2017). Growth of ambient induced surface impurity species on layered positive electrode materials and impact on electrochemical performance. J. Electrochem. Soc. 164(14), A3727-A3741. doi:10.1149/2.0921714jes
Noh, H.-J., Youn, S., Yoon, C. S., and Sun, Y.-K. (2013). Comparison of the structural and electrochemical properties of layered Li[NixCoyMnz]O2 (x = 1/3, 0.5, 0.6, 0.7, 0.8 and 0.85) cathode material for lithium-ion batteries. J. Power Sources. 233, 121-130. doi:10.1016/j.jpowsour.2013.01.063
Oh, P., Song, B., Li, W., and Manthiram, A. (2016). Overcoming the chemical instability on exposure to air of Ni-rich layered oxide cathodes by coating with spinel LiMn1.9Al0.1O4. J. Mater. Chem. A. 4(16), 5839-5841. doi:10.1039/c6ta01061j
Ohzuku, T., Ueda, A., and Nagayama, M. (1993). Electrochemistry and structural chemistry of LiNiO2 (R(3)m) for 4 volt secondary lithium cells. J. Electrochem. Soc. 140(7), 1862-1870. doi:10.1149/1.2220730
Park, J.-h., Park, J.-k., and Lee, J.-w. (2016). Stability of LiNi0.6Mn0.2Co0.2O2 as a cathode material for lithium-ion batteries against air and moisture. Bull. Korean Chem. Soc. 37(3), 344-348. doi:10.1002/bkcs.10679
Park, K.-J., Jung, H.-G., Kuo, L.-Y., Kaghazchi, P., Yoon, C. S., and Sun, Y.-K. (2018). Improved cycling stability of Li[Ni0.90Co0.05Mn0.05]O2 through microstructure modification by boron doping for Li-ion batteries. Adv. Energy Mater. 8(25), 1801202. doi:10.1002/aenm.201801202
Park, K., and Choi, B. (2018). Requirement of high lithium content in Ni-rich layered oxide material for Li ion batteries. J. Alloys Compd. 766, 470-476. doi:10.1016/j.jallcom.2018.06.135
Park, K., Park, J. H., Hong, S. G., Choi, B., Heo, S., Seo, S. W., et al. (2017). Re-construction layer effect of LiNi0.8Co0.15Mn0.05O2 with solvent evaporation process. Sci. Rep. 7. doi:10.1038/srep44557
Qian, K., Huang, B., Liu, Y., Wagemaker, M., Liu, M., Duan, H., et al. (2019). Increase and discretization of the energy barrier for individual LiNixCoyMnyO2 (x + 2y =1) particles with the growth of a Li2CO3 surface film. J. Mater. Chem. A. 7(20), 12723-12731. doi:10.1039/c9ta01443h
Renfrew, S. E., Kaufman, L. A., and McCloskey, B. D. (2019). Altering surface contaminants and defects influences the first-cycle outgassing and irreversible transformations of LiNi0.6Mn0.2Co0.2O2. ACS Appl. Mater. Interfaces. 11(38), 34913-34921. doi:10.1021/acsami.9b09992
Renfrew, S. E., and McCloskey, B. D. (2017). Residual lithium carbonate predominantly accounts for first cycle CO2 and CO outgassing of Li-stoichiometric and Li-rich layered transition-metal oxides. J. Am. Chem. Soc. 139(49), 17853-17860. doi:10.1021/jacs.7b08461
Robert, R., Bünzli, C., Berg, E. J., and Novák, P. (2015). Activation mechanism of LiNi0.80Co0.15Al0.05O2: surface and bulk operando electrochemical, differential electrochemical mass spectrometry, and X-ray diffraction analyses. Chem. Mater. 27(2), 526-536. doi:10.1021/cm503833b
Ross, G. J., Watts, J. F., Hill, M. P., and Morrissey, P. (2000). Surface modification of poly(vinylidene fluoride) by alkaline treatment 1. The degradation mechanism. Polym. 41(5), 1685-1696. doi:10.1016/s0032-3861(99)00343-2
Ross, G. J., Watts, J. F., Hill, M. P., and Morrissey, P. (2001). Surface modification of poly(vinylidene fluoride) by alkaline treatment Part 2. Process modification by the use of phase transfer catalysts. Polym. 42(2), 403-413. doi:10.1016/s0032-3861(00)00328-1
Ryu, H.-H., Park, K.-J., Yoon, C. S., and Sun, Y.-K. (2018). Capacity fading of Ni-rich Li[NixCoyMn1–x–y]O2 (0.6 ≤ x ≤ 0.95) cathodes for high-energy-density lithium-ion batteries: bulk or surface degradation? Chem. Mater. 30(3), 1155-1163. doi:10.1021/acs.chemmater.7b05269
Shi, J.-L., Qi, R., Zhang, X.-D., Wang, P.-F., Fu, W.-G., Yin, Y.-X., et al. (2017). High-thermal- and air-stability cathode material with concentration-gradient buffer for Li-ion batteries. ACS Appl. Mater. Interfaces. 9(49), 42829-42835. doi:10.1021/acsami.7b14684
Shizuka, K., Kiyohara, C., Shima, K., and Takeda, Y. (2007). Effect of CO2 on layered Li1+zNi1-x-yCoxMyO2 (M =Al, Mn) cathode materials for lithium ion batteries. J. Power Sources. 166(1), 233-238. doi:10.1016/j.jpowsour.2007.01.013
Shkrob, I. A., Gilbert, J. A., Phillips, P. J., Klie, R., Haasch, R. T., Bareño, J., et al. (2017). Chemical weathering of layered Ni-rich oxide electrode materials: evidence for cation exchange. J. Electrochem. Soc. 164(7), A1489-A1498. doi:10.1149/2.0861707jes
Sun, B., El Kazzi, M., Müller, E., and Berg, E. J. (2018). Toward high-performance Li(NixCoyMnz)O2 cathodes: facile fabrication of an artificial polymeric interphase using functional polyacrylates. J. Mater. Chem. A. 6(36), 17778-17786. doi:10.1039/c8ta03954b
Tian, C., Lin, F., and Doeff, M. M. (2018). Electrochemical characteristics of layered transition metal oxide cathode materials for lithium ion batteries: surface, bulk behavior, and thermal properties. Acc. Chem. Res. 51(1), 89-96. doi:10.1021/acs.accounts.7b00520
Toma, T., Maezono, R., and Hongo, K. (2020). Electrochemical properties and crystal structure of Li+/H+ cation-exchanged LiNiO2. ACS Appl. Mater. Interfaces. 3(4), 4078-4087. doi:10.1021/acsaem.0c00602
Wang, C., Shao, L., Guo, X., Xi, X., Yang, L., Huang, C., et al. (2019). Air-induced degradation and electrochemical regeneration for the performance of layered Ni-rich cathodes. ACS Appl. Mater. Interfaces. 11(47), 44036-44045. doi:10.1021/acsami.9b11452
Wang, D., Kou, R., Ren, Y., Sun, C.-J., Zhao, H., Zhang, M.-J., et al. (2017). Synthetic control of kinetic reaction pathway and cationic ordering in high-Ni layered oxide cathodes. Adv. Mater. 29(39). doi:10.1002/adma.201606715
Wang, R., Wang, J., Chen, S., Gao, A., Su, Y., and Wu, F. (2018). Influence of atmosphere on electrochemical performance of LiNi0.8Co0.1Mn0.1O2 electrodes for Li-ion batteries. Mater. Sci. Eng. 301. doi:10.1088/1757-899x/301/1/012039
Wu, F., Tian, J., Su, Y., Wang, J., Zhang, C., Bao, L., et al. (2015). Effect of Ni2+ content on lithium/nickel disorder for Ni-rich cathode materials. ACS Appl. Mater. Interfaces. 7(14), 7702-7708. doi:10.1021/acsami.5b00645
Wu, N., Wu, H., Kim, J.-K., Liu, X., and Zhang, Y. (2018). Restoration of degraded nickel-rich cathode materials for long-life lithium-ion batteries. Chemelectrochem. 5(1), 78-83. doi:10.1002/celc.201700979
Xian, F., Li, J. D., Hu, Z. L., Zhou, Q., Wang, C., Lu, C. L., et al. (2020). Investigation of the cathodic interfacial stability of a nitrile electrolyte and its performance with a high-voltage LiCoO2 cathode. Chem. Commun. 56(37), 4998-5001. doi:10.1039/d0cc00049c
Xiao, B., and Sun, X. (2018). Surface and subsurface reactions of lithium transition metal oxide cathode materials: an overview of the fundamental origins and remedying approaches. Adv. Energy Mater. 8(29), 1802057. doi:10.1002/aenm.201802057
Xie, Q., Li, W., Dolocan, A., and Manthiram, A. (2019). Insights into boron-based polyanion-tuned high-nickel cathodes for high-energy-density lithium-ion batteries. Chem. Mater. 31(21), 8886-8897. doi:10.1021/acs.chemmater.9b02916
Xiong, X. H., Wang, Z. X., Yue, P., Guo, H. J., Wu, F. X., Wang, J. X., et al. (2013). Washing effects on electrochemical performance and storage characteristics of LiNi0.8Co0.1Mn0.1O2 as cathode material for lithium-ion batteries. J. Power Sources. 222, 318-325. doi:10.1016/j.jpowsour.2012.08.029
Xu, S., Du, C. Y., Xu, X., Han, G. K., Zuo, P. J., Cheng, X. Q., et al. (2017). A mild surface washing method using protonated polyaniline for Ni-rich LiNi0.8Co0.1Mn0.1O2 material of lithium ion batteries. Electrochim Acta. 248, 534-540. doi:10.1016/j.electacta.2017.07.169
Yang, H., Wu, H.-H., Ge, M., Li, L., Yuan, Y., Yao, Q., et al. (2019a). Simultaneously dual modification of Ni-rich layered oxide cathode for high-energy lithium-ion batteries. Adv. Funct. Mater. 29(13), 1808825. doi:10.1002/adfm.201808825
Yang, H., Wu, K., Hu, G., Peng, Z., Cao, Y., and Du, K. (2019b). Design and synthesis of double-functional polymer composite layer coating to enhance the electrochemical performance of the Ni-rich cathode at the upper cutoff voltage. ACS Appl. Mater. Interfaces. 11(8), 8556-8566. doi:10.1021/acsami.8b21621
Yang, S., Fan, Q., Shi, Z., Liu, L., Liu, J., Ke, X., et al. (2019c). Superior stability secured by a four-phase cathode electrolyte interface on a Ni-rich cathode for lithium ion batteries. ACS Appl. Mater. Interfaces. 11(40), 36742-36750. doi:10.1021/acsami.9b12578
Yang, W., Xiang, W., Chen, Y. X., Wu, Z. G., Hua, W. B., Qiu, L., et al. (2020). Interfacial regulation of Ni-rich cathode materials with an ion-conductive and pillaring layer by infusing gradient boron for improved cycle stability. ACS Appl. Mater. Interfaces. 12(9), 10240-10251. doi:10.1021/acsami.9b18542
You, Y., Celio, H., Li, J., Dolocan, A., and Manthiram, A. (2018). Modified high-nickel cathodes with stable surface chemistry against ambient air for lithium-ion batteries. Angew. Chem. Int. Ed. 57(22), 6480-6485. doi:10.1002/anie.201801533
Zhai, Y., Yang, W., Ning, D., Yang, J., Sun, L., Schuck, G., et al. (2020). Improving the cycling and air-storage stability of LiNi0.8Co0.1Mn0.1O2 through integrated surface/interface/doping engineering. J. Mater. Chem. A. 8(10), 5234-5245. doi:10.1039/c9ta13014d
Zhang, C., Xu, S., Han, B., Lin, G., Huang, Q., Ivey, D. G., et al. (2019a). Towards rational design of high performance Ni-rich layered oxide cathodes: the interplay of borate-doping and excess lithium. J. Power Sources. 431, 40-47. doi:10.1016/j.jpowsour.2019.05.048
Zhang, C. X., Xu, S., Han, B., Lin, G. X., Huang, Q., Ivey, D. G., et al. (2019b). Towards rational design of high performance Ni-rich layered oxide cathodes: the interplay of borate-doping and excess lithium. J. Power Sources. 431, 40-47. doi:10.1016/j.jpowsour.2019.05.048
Zhang, J., Yang, Z., Gao, R., Gu, L., Hu, Z., and Liu, X. (2017). Suppressing the structure deterioration of Ni-rich LiNi0.8Co0.1Mn0.1O2 through atom-scale interfacial integration of self-forming hierarchical spinel layer with Ni gradient concentration. ACS Appl. Mater. Interfaces. 9(35), 29794-29803. doi:10.1021/acsami.7b08802
Zhang, S., Ma, J., Hu, Z., Cui, G., and Chen, L. (2019c). Identifying and addressing critical challenges of high-voltage layered ternary oxide cathode materials. Chem. Mater. 31(16), 6033-6065. doi:10.1021/acs.chemmater.9b01557
Zhang, S. S., Chen, J., and Wang, C. S. (2019d). Elemental sulfur as a cathode additive for enhanced rate capability of layered lithium transition metal oxides. J. Electrochem. Soc. 166(4), A487-A492. doi:10.1149/2.0101904jes
Zhang, S. S. (2020). Problems and their origins of Ni-rich layered oxide cathode materials. Energy Storage Mater. 24, 247-254. doi:10.1016/j.ensm.2019.08.013
Zhao, J., Wang, Z., Wang, J., Guo, H., Li, X., Yan, G., et al. (2018). The role of a MnO2 functional layer on the surface of Ni-rich cathode materials: towards enhanced chemical stability on exposure to air. Ceram. Int. 44(11), 13341-13348. doi:10.1016/j.ceramint.2018.04.166
Zhao, J., Zhang, W., Huq, A., Misture, S. T., Zhang, B., Guo, S., et al. (2017). In Situ probing and synthetic control of cationic ordering in Ni-rich layered oxide cathodes. Adv. Energy Mater. 7(3), 1601266. doi:10.1002/aenm.201601266
Zhao, S. Y., Zhu, Y. T., Qian, Y. C., Wang, N. N., Zhao, M., Yao, J. L., et al. (2020). Annealing effects of TiO2 coating on cycling performance of Ni-rich cathode material LiNi0.8Co0.1Mn0.1O2 for lithium-ion battery. Mater. Lett. 265, 127418. doi:10.1016/j.matlet.2020.127418
Keywords: ni-rich cathode, air storage performance, residual lithium compounds, surface degradation, modification
Citation: Chen A, Wang K, Li J, Mao Q, Xiao Z, Zhu D, Wang G, Liao P, He J, You Y and Xia Y (2020) The Formation, Detriment and Solution of Residual Lithium Compounds on Ni-Rich Layered Oxides in Lithium-Ion Batteries. Front. Energy Res. 8:593009. doi: 10.3389/fenrg.2020.593009
Received: 09 August 2020; Accepted: 30 September 2020;
Published: 10 December 2020.
Edited by:
Zhan Lin, Zhejiang University, ChinaReviewed by:
Hailei Zhao, University of Science and Technology Beijing, ChinaHui Xia, Nanjing University of Science and Technology, China
Copyright © 2020 Chen, Wang, Li, Mao, Xiao, Zhu, Wang, Liao, He, You and Xia. This is an open-access article distributed under the terms of the Creative Commons Attribution License (CC BY). The use, distribution or reproduction in other forums is permitted, provided the original author(s) and the copyright owner(s) are credited and that the original publication in this journal is cited, in accordance with accepted academic practice. No use, distribution or reproduction is permitted which does not comply with these terms.
*Correspondence: Jiarui He, amlhcnVpLmhlQHV0ZXhhcy5lZHU=; Ya You, eW91eWFAd2h1dC5lZHUuY24=; Yang Xia, bmFub3NoaW5lQHpqdXQuZWR1LmNu