- 1Key Laboratory of Gas and Fire Control for Coal Mines, China University of Mining and Technology, Ministry of Education, Xuzhou, China
- 2School of Safety Engineering, China University of Mining and Technology, Xuzhou, China
Coal and gas outburst is an extremely serious dynamic phenomenon involving the comprehensive action of many factors, and remains a major disaster that needs to be solved in coal mine production. Considering the significant influence of moisture content on coal and gas outburst, it is necessary to carry out experimental research on coal and gas outburst under different moisture content conditions. The coal of the serious outburst coal seam in the Luling coal mine, which has had several coal and gas outburst accidents, was selected as the experimental sample. Firstly, the gas desorption law and outburst index characteristics of coal under different moisture content were studied, and the influence of moisture content on gas outburst parameters of coal was obtained. Then, the simulation tests of coal and gas outburst under different moisture content were carried out by using a triaxial coal and gas outburst simulation test system. Based on the above experimental research, the influence of moisture on coal and gas outburst was summarized, and the energy calculation and prevention countermeasures of coal and gas outburst under different moisture content conditions were carried out. With the increase of moisture content, the adsorption constant a, the initial velocity of gas diffusion Δp, and the gas desorption index of drill cuttings K1/Δh2 decrease, but the Protodyakonov coefficient f increases, all of which have an exponential relation to moisture content. Meanwhile, with the increase of moisture content, the threshold of coal and gas outburst pressure increases, and the intensity and energy of outburst decrease. At 0.45 MPa pressure, the outburst of 1.47% moisture content is the most serious, the outburst of 5% moisture content is weakened, while the outburst of 10% moisture content is not triggered. Five percent moisture content can be used as a critical index of hydraulic measures to prevent coal and gas outburst in No. 8 coal seam of the Luling coal mine. This research can provide new insights into the theoretical study of coal and gas outburst in serious outburst coal seams and the control of coal and gas outburst by hydraulic measures.
1 Introduction
With the growth of coal mining in China, factors such as geostress, gas pressure, geological structure, and mining activities are changing constantly. Coal seam gas has become the key factor that constrains safe and efficient production of Chinese deep coal mines (Cheng et al., 2011; Wang et al., 2012; Chen et al., 2022). The damage caused by coal and gas outburst dynamic disasters is increasing day by day. At present, coal and gas outburst accidents have become the focus of attention (Cheng and Pan, 2020; Wang L. et al., 2020). Coal and gas outburst involves injecting a large amount of coal/rock and gas into the mining working face over a short time. The coal rock is injected from several tons to tens of thousands of tons, and the gas is emitted from hundreds to millions of cubic meters, which may lead to a series of disasters such as gas explosion (Beamish and Crosdale, 1998; Zhao et al., 2016; Zhi and Elsworth, 2016). Since the first outburst accident was recorded in the Isaac Coal Mine, France, in 1834, tens of thousands of outburst accidents have happened all over the world (Shepherd et al., 1981; Wang et al., 2013; Tu et al., 2021). In the past decades, coal and gas outburst, as one of the most destructive disasters in China’s coal production, has caused serious economic losses and casualties (Cheng et al., 2011; Wang et al., 2017b; Cheng and Pan, 2020). According to incomplete statistics, there are more than 1,000 mines with strong coal and gas outburst danger in China. In the recent 20 years, there have been nearly 500 outburst accidents and more than 3,000 deaths (Sun, 2014; Zhang et al., 2021). Although coal and gas outburst accidents have been effectively controlled in recent years, they are still at a relatively high level and have become more and more prominent in coal mine accidents. From April to June 2021, four coal and gas outburst accidents happened in succession in China, causing 18 deaths. This shows that coal and gas outburst remains a major disaster that needs to be solved in China’s coal mine production.
Coal and gas outburst is a very destructive and complex coal/rock dynamic process (Black, 2019). It is generally believed that the trigger of outburst is related to geological structure, coal properties, gas pressure, stress state, and other factors (Díaz Aguado and González Nicieza, 2007; Jin et al., 2018; Tu et al., 2021). Moisture is one of the most important factors that influence gas seepage and coalbed methane extraction (Ding and Yue, 2018). Generally, moisture in the coal seam will inhibit gas desorption, diffusion, and seepage, and greater moisture content generates lower outburst risk (Fan et al., 2017). Hydraulic measures are important technical measures that deal with gas hazards, such as coal seam water injection, hydraulic flushing, hydraulic slotting, and hydraulic fracturing (Lu et al., 2017; Zhang et al., 2017; Yan et al., 2019; Zhao et al., 2020). The implementation of hydraulic measures will increase the moisture content of coal seam while relieving in situ stress and improving gas drainage efficiency (Yang et al., 2019; Yi et al., 2021). The difference in moisture content affects the adsorption and desorption capacity of coal and then affects the outburst parameters and gas outburst capacity of coal (Pan et al., 2010; Wang K et al., 2021). Coal has a stronger adsorption capacity for water molecules than methane molecules (Zhang and Sang, 2009; Wang H et al., 2021). The affinity between methane molecules and the coal molecule is reduced, and methane molecules are less aggregated around the coal molecule because of the presence of water molecules (Meng et al., 2020). Matrix pores are the main storage space for methane (Fan et al., 2021; Zhang et al., 2022) and water molecules enter matrix pores of coal body by capillary suction and mainly act on micropore fractures. If the pressure difference between the inside and outside of pores cannot overcome the capillary force, water will block the gas desorption path and reduce the gas desorption capacity of coal, resulting in the water lock effect (Hao et al., 2018; Liu et al., 2019; Qin et al., 2020). After the implementation of hydraulic measures, the moisture content of coal seam increases and the permeability decreases, which has a restraining effect on gas emission and will result in the change of desorption-induced strains (Chen et al., 2012).
However, most of the studies focus on the influence of different moisture content on gas adsorption/desorption in coal (Zhang et al., 2011; Chen and Cheng, 2014; Wang et al., 2017a; Hao et al., 2018; Zhao et al., 2018; Liu et al., 2019; Qin et al., 2019; Yao et al., 2020). There are still different views on the influence of moisture on the characteristics of gas adsorption and desorption in the coal industry, which is highly controversial. At present, most studies conducted are single studies, and water studies and coal and gas outburst experiments are separate. There are relatively few studies that examine the law of coal and gas outburst intensity under different moisture content conditions and the key control indexes of coal and gas outburst prevention under hydraulic measures combined with coal and gas outburst simulating tests. Most coal and gas outburst simulating tests are used to focus on the mechanism and characteristics of gas outburst, while moisture content experiments are used to study the characteristics and microscopic characteristics of coal body. In addition, the process of hydraulic measures implemented on site shows that too little water is not conducive to gas control, and too much water can lead to difficult gas extraction and environmental pollution. In addition, the process of hydraulic measures implemented on site shows that too little water is not conducive to controlling gas, while too much water will lead to gas extraction difficulty and environmental pollution. It is particularly important to select a suitable water content index for specific coal seam in hydraulic measures, but there is no unified method at present. Therefore, it is necessary to study the influence of moisture on the gas outburst parameters, the energy of coal and gas outburst, and the selection of key moisture content index in hydraulic measures, which is of great significance for preventing gas disasters and guiding the field production in coal mines.
A total of 26 coal and gas outburst accidents happened in the Luling coal mine in Anhui Province, China, with a high frequency and a high intensity of gas outburst. Among them, the one with the largest outburst intensity happened in No. 8 coal seam on April 7, 2002. A total of 10,500 t of coal/rock were injected, and 1.23 million m3 of gas was emitted, resulting in 13 deaths (Wang L. et al., 2020). Therefore, the test coal sample was taken from No. 8 coal seam in the Luling coal mine in view of its strong outburst risk. In this paper, based on the study of the outburst physical parameters of coal sample under different moisture content, the influence of different moisture content on gas desorption of coal was explored. The influence of moisture content on the gas outburst parameters of coal and the intensity of coal and gas outburst were studied by combining various experimental devices. Then, the simulation tests under different moisture content were carried out using the simulation test system to explore the influence of moisture on the laws and characteristics of coal and gas outburst. The characteristics of coal and gas outburst under different moisture content conditions and the key moisture content index of coal and gas outburst prevention under hydraulic measures were analyzed in the end. With this study, the relevant laws of coal and gas outburst dynamic disasters of strong outburst coal with different moisture content can be further understood. It is hoped that this study can provide technical guidance for hydraulic measures to prevent and control coal and gas outburst dynamic disasters.
2 Materials and Methods
2.1 Coal Samples Preparation
The Luling coal mine is located in Huaibei Coalfield, Anhui Province, China. It has been affected by many geological tectonic movements, resulting in extremely complex geological environment and tectonic features. The in situ stress in the Luling coal mine is concentrated because it is located near the top of the lateral arc. No. 8 coal seam is the main mining seam, the roof of which is fine sandstone/mudstone and the floor is mudstone (Wang L. et al., 2020). The complex environment seals the gas in the coal seam, resulting in high gas content and pressure. In addition, because of the large number of folds and faults, the local thickness of No. 8 coal seam varies greatly, which increases the risk of coal and gas outburst. There have been many outburst accidents in No. 8 coal seam, which has strong outburst risk. Therefore, coal samples were extracted from a working face of No. 8 coal seam in the Luling coal mine in this study.
The independent variable of this study is moisture content, so coal samples with different characteristic parameters need to be prepared. According to different experimental requirements, coal samples with corresponding particle size were crushed and screened. The drying oven was used to fully dry the coal samples. Then, the dry coal samples were saturated with distilled water for 3 days by the vacuum water saturation instrument for them to fully absorb water. After that, the wet coal samples were taken out and water drops on the surface of the coal particles were adsorbed using filter paper. Then, the vacuum drying oven was used to dry the sample sieves containing the coal samples to obtain different moisture content by controlling the drying time. Finally, the sieves were taken out and the coal samples therein were stored in the sealing bag, successively.
2.2 Gas Outburst Parameter Determination of Coal With Different Moisture Content
2.2.1 Adsorption Constant a
Coal is a porous medium with a large number of fractures and pores in its interior, which provide sufficient space for gas adsorption. The relationship between gas adsorption and gas pressure can be represented as Eq. 1:
Where
Adsorption constant a of coal samples was measured according to the China National standard MT-T 752-1997 via an HCA gas adsorption experimental device, as shown in Figure 1A. The particle size of coal samples with different moisture content used in the experiment is 0.2–0.25 mm and the mass is 50 g.
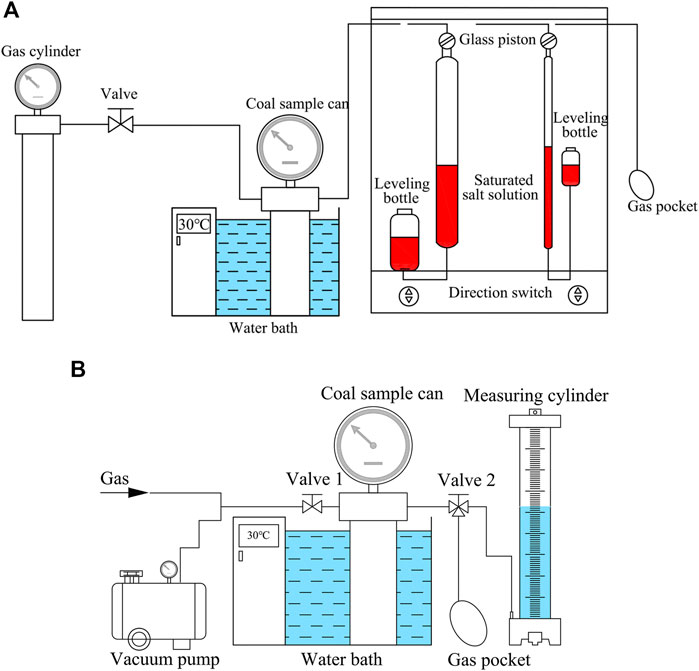
FIGURE 1. Schematic of the gas adsorption/desorption experimental devices. (A) HCA gas adsorption experimental device. (B) FM-1 gas isothermal desorption device.
2.2.2 Protodyakonov Coefficient f
The Protodyakonov coefficient, f value, of coal samples (hereafter referred to as f) was determined according to the China National standard GB/T 23561.12-2010. The particle size of coal samples with different moisture content is 1–3 mm and the mass is 50 g. It is generally believed that the f of intact coal is in the range of 0.75–1.5. When f is less than 0.5, the coal properties indicate a risk of a coal and gas outburst. When f is less than 0.3, this coal is considered to be strong outburst risk (Wang C et al., 2020).
2.2.3 Initial Velocity of Gas Diffusion
The initial velocity of gas diffusion (hereafter referred to as Δp) was determined according to the China National standard AQ1080-2009 via a WT-1 gas diffusion velocity analyzer. The particle size of coal samples with different moisture content is 0.2–0.25 mm.
2.3 Gas Desorption Experiment of Coal With Different Moisture Content
Gas desorption capacity of coal has an important influence on the generation and development of coal and gas outburst. The moisture content greatly affects the gas desorption capacity of coal. Therefore, it is of fundamental and important significance to study the gas desorption characteristics of strong outburst coal under different moisture content conditions. Gas desorption experiments were carried out under the adsorption equilibrium pressure of 0.74, 1, 2, 3, and 4 MPa via a FM-1 gas isothermal desorption device, as shown in Figure 1B (Zhao et al., 2016). The particle size of coal samples is 1–3 mm and the moisture content of coal used in the experiment are 1.68%, 3.42%, 5.19%, and 6.81%, respectively. After converting the measured data into standard data, the desorption curve was drawn.
2.4 Coal and Gas Outburst Analogical Simulating Test Under Different Moisture Content
The triaxial coal and gas outburst simulation test system was designed and completed by the research team according to the similarity theory, which satisfies the geometric similarity, motion similarity, and dynamic similarity (Tu et al., 2016; Lei et al., 2020). It is mainly composed of four systems: outburst chamber, loading system, data collection system, and gas injection/vacuum pumping system, as shown in Figure 2. The interior space size of the outburst chamber is designed to be 250 × 250 × 310 mm, and the wall thickness is about 80 mm. An outburst port of approximately 50 mm diameter is set in the front of the chamber, and a gas injection/exhaust port is set in the front right of the chamber. For safety reasons, CO2 was used in place of explosive CH4. The ambient temperature was 25°C; the triaxial loading pressures for
1) Coal sample preparation—the coal sample with the corresponding moisture content was prepared, and the particle size of coal was 0.25–0.5 mm.
2) Coal briquette pressing—the outburst chamber was filled with coal sample after the coal sample preparation was completed. Then, the coal sample in the chamber was preliminarily compacted horizontally using the loading system. After adding the appropriate amount of coal samples to the chamber, the press was increased to 48 MPa for secondary pressing and the loading time was kept for 40 min. In this way, the coal briquette will be pressed successfully according to previous studies.
3) Vacuum pumping/gas charging—after confirming that the chamber was sealed, it was vacuumed for 12 h. Then, CO2 was injected into the chamber for at least 48 h to make it fully adsorbed and balanced to the target pressure.
4) Outburst preparation—a loading stress of
5) Outburst induced—the plug of the outburst port was removed, causing the outburst.
6) Data acquisition—the key parameters were obtained from the test site.
3 Results and Analysis
3.1 Gas Outburst Parameter Characteristics
The adsorption constant a, f, and Δp of coal samples with a moisture content of 1.68%, 3.42%, 5.19%, and 6.81% were determined, as shown in Figure 3. The curves in Figure 3 were obtained by fitting data points, and their goodness of fit were all above 0.99.
3.1.1 Results of Adsorption Constant a
Figure 3 illustrates that the adsorption constant a of coal decreases with the increase of moisture content. This indicates that the limit adsorption capacity of gas decreases due to the moisture of coal. In addition, with the increase of moisture content, the decline curve tends to flatten and the rate decreases. It is highly probable that the adsorption constant a will not change with the further increase of moisture content. The main reason for the above results is that the fractures and pores of coal are filled with water, which affects the adsorption of gas in three aspects: 1) A part of the decomposed water and free water in the coal body combine with the coal structure surface through acting force, occupying a certain amount of adsorption space on the coal structure surface. This reduces the effective space for gas adsorption to a certain extent, leading to the decrease in the amount of adsorbed gas. 2) Some fractures and pores in the coal body are very narrow, and free water cannot reach its interior. However, some water will enter into these narrow fractures and pores in the form of water vapor, which will form a competitive relationship with CH4, resulting in a decrease in the amount of adsorbed gas. 3) The influence of moisture on the adsorption characteristics of coal will be greatly weakened after the coal is saturated with water (Yang et al., 2017).
3.1.2 Results of Protodyakonov Coefficient f
f can represent the ability of coal to resist outburst (Xue et al., 2014). The smaller the value of f, the lower the strength of coal and the higher the deformability. This means that coal and gas outburst is more dangerous (Fan et al., 2020). It can be seen from Figure 3 that the f increases with the increase of moisture content, and the increase rate gradually decreases and tends to be gentle. The internal friction angle decreases linearly with the increase of moisture content while the cohesion increases parabolically with the increase of moisture content, which is beneficial to the consolidation of the coal body (Wang H et al., 2021). The more moisture content in the coal, the harder it is to be crushed, and the lower the risk of coal and gas outburst.
3.1.3 Results of Initial Velocity of Gas Diffusion
Δp is one of the important indicators for discriminating coal and gas outburst risk. It characterizes the microstructure of coal and indicates the gas emission capacity of coal, which greatly affects the intensity of coal and gas outburst. It can be used individually or combined with other parameters to predict the outburst risk tendency of coal seams (Zhou et al., 2019). As can be seen from Figure 3, Δp decreases with the increase of moisture content, and shows a gradual decrease and flattening trend, which is similar to the change law of the adsorption constant a of coal. This shows that water has a significant inhibitory effect on gas emission. After water molecules enter the fractures and pores of coal body, the water lock effect is generated, which hinders the movement of methane molecules, resulting in the decrease of gas desorption amount per unit time and the decrease of desorption rate. This is consistent with the findings of others (Wang et al., 2017a; Wang et al., 2018).
3.2 Gas Desorption Characteristics
The desorption curves of coal with different moisture content at the equilibrium pressure of 0.74, 1, 2, 3, and 4 MPa are shown in Figure 4.
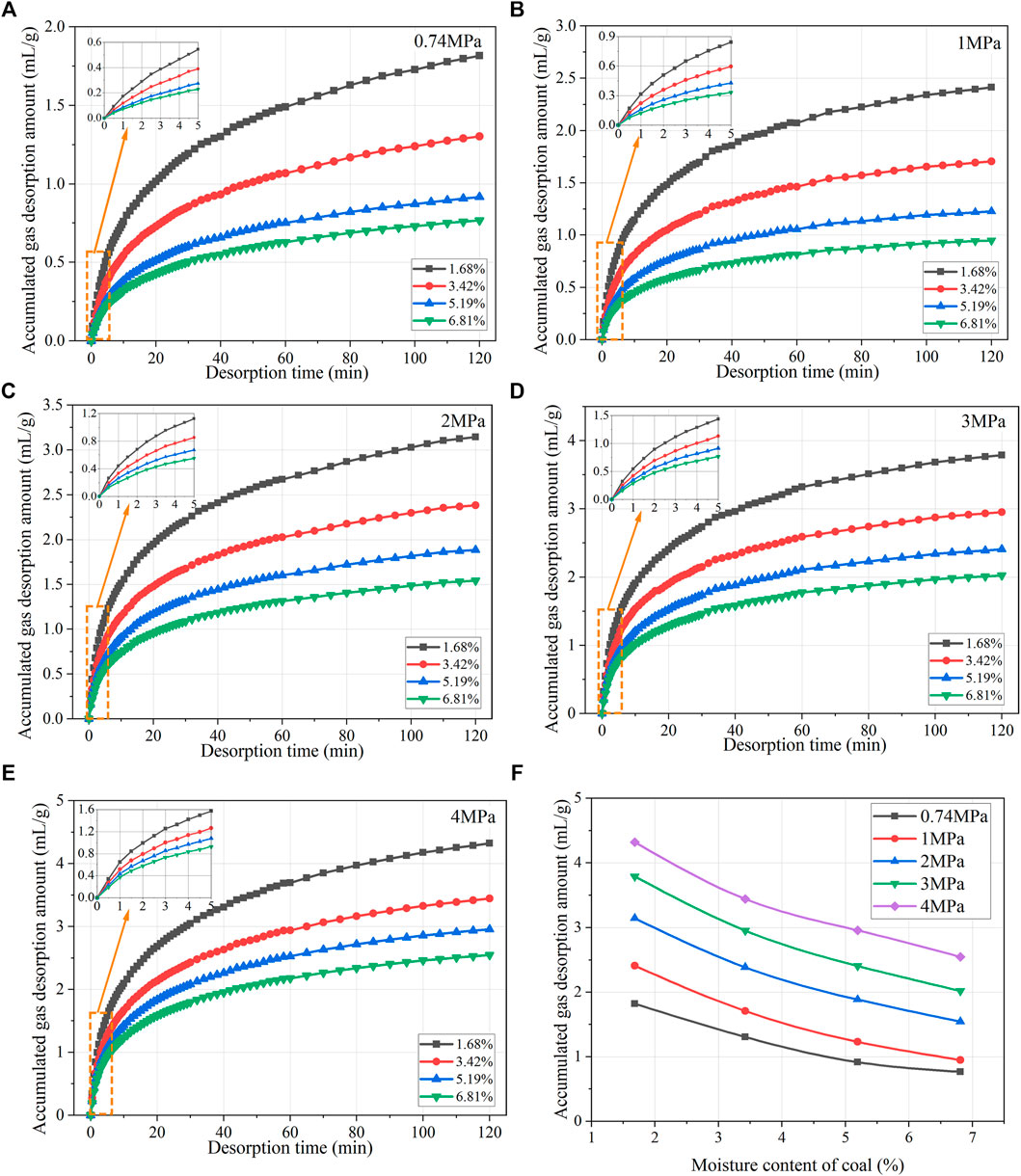
FIGURE 4. Gas desorption curves of coal samples with different moisture content at different adsorption equilibrium pressure. (A) Equilibrium pressure of 0.74 MPa. (B) Equilibrium pressure of 1 MPa. (C) Equilibrium pressure of 2 MPa. (D) Equilibrium pressure of 3 MPa. (E) Equilibrium pressure of 4 MPa. (F) Accumulated gas desorption amount.
The relationship between the accumulated gas desorption amount and desorption time is a monotonically increasing parabola (Figure 4). In the initial period of gas desorption, the gas desorption amount is large and the desorption rate is fast. With the passage of time, the desorption rate decreases and the desorption amount gradually flattens out. With the increase of adsorption equilibrium pressure, the accumulated gas desorption amount of coal samples with different moisture content increases. Under the same adsorption equilibrium pressure, the desorption curve of coal samples with higher moisture content is always below that of coal samples with lower moisture content, indicating that the desorption amount decreases with the increase of moisture content in the coal.
Figure 4F shows the relationship between the gas desorption amount and moisture content in 120 min under different pressures. With the increase of moisture content, the gas desorption amount in 120 min decreased gradually. In general, the desorption quantity decreases greatly in the initial increasing stage of moisture content. With the increase of moisture content, the decrease of desorption capacity decreases gradually. This law is more obvious at lower adsorption equilibrium pressure because the influence factors of pressure on gas desorption is weakened.
3.3 Coal and Gas Outburst Characteristics
3.3.1 Test Results of Coal and Gas Outburst Simulation
The tests in Table 1 were carried out under the same environmental conditions, and the results are shown in Table 2. The test results are divided into two cases: outburst and no outburst. For the outburst case, the coal powder thrown out has the same shape (spindle distribution), showing a wide shape in the middle of the two ends of the tip (Figure 5).
The test results show that the change of gas pressure and moisture content greatly affects the trigger and intensity of coal and gas outburst. It can be found that gas pressure threshold exists in the trigger of coal and gas outburst, and moisture content will greatly affect the pressure threshold (Ding and Yue, 2018; Lei et al., 2020). With the increase of moisture content, the threshold of gas pressure increases and the intensity of outburst decreases. Outburst was triggered at a gas adsorption equilibrium pressure of 0.35 and 0.45 MPa when the moisture content was 1.47%, while the coal with a moisture content of 5% was only triggered at a pressure of 0.45 MPa, and the amount of coal powder thrown out was relatively less. The coal with a moisture content of 10% did not even trigger outburst at a pressure of 0.45 MPa.
The characteristics of residual briquette after outburst are also significantly different, as shown in Figure 6. The outburst hole of the coal with 5% moisture content was complete and round. The residual coal in the chamber was relatively complete and less broken. When the moisture content was 1.47% and the gas pressure was 0.35 MPa, the outburst hole was larger and more fractures appeared on the surface and inside of the residual briquette. When the moisture content was 1.47% and the gas pressure was 0.45 MPa, the damage to the residual briquette was the most serious, and most of the coal in the chamber was broken.
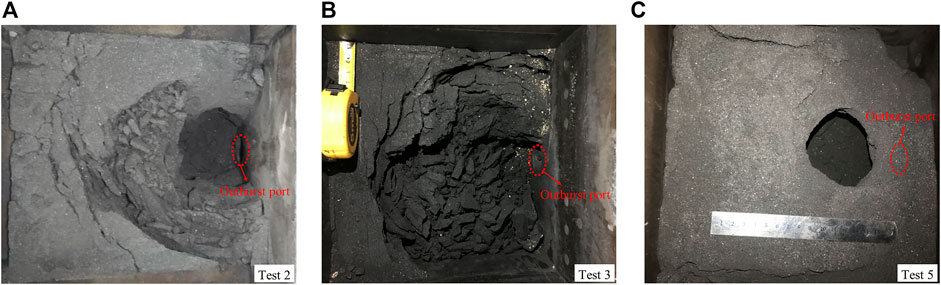
FIGURE 6. Outburst hole characteristics of different simulation tests. (A) Test 2: 1.47% moisture content and 0.35 MPa pressure. (B) Test 3: 1.47% moisture content and 0.45 MPa pressure. (C) Test 5: 5% moisture content and 0.45 MPa pressure.
3.3.2 Characteristics of Coal and Gas Outburst Process
When the outburst was triggered, the high-pressure gas carrying coal in the chamber was jetted out rapidly, and the duration was very short, only about 1 s. The two-phase gas–solid mixtures caused by the outburst propagated as shock waves and flows from the sources (Zhou et al., 2020). The entire outburst process was divided into four stages: preparation, trigger, development, and termination (Zhao et al., 2016). Figure 7 shows the typical motion state in the outburst process of test 3. In the outburst trigger stage, the coal was broken and thrown out under the action of high-pressure gas and stress. At this time, the mass and velocity of the thrown coal were increasing. The free gas in the chamber had enough energy to break, transport, and throw away the coal. During the outburst development stage, the mass and velocity of the thrown coal were relatively stable because the desorption gas was converted into free gas to supplement energy. At the outburst termination stage, the effect of gas and stress was not able to further break down and throw out the coal, so the mass and velocity of the thrown coal decreased, and finally the outburst came to an end. The whole outburst process experienced three periods: acceleration period, stabilization period, and attenuation period. The three stages are closely related to the energy of coal destruction and migration.
3.3.3 Distribution Characteristics of Coal Powder
After each outburst, the coal powder scattered on the ground was weighed to obtain the distance distribution, as shown in Figure 8. The distance between the thrown coal powder and the outburst port in a test was divided into five zones equally: zones Ⅰ, Ⅱ, Ⅲ, Ⅳ, and Ⅴ. The mass and proportion of the outburst coal powder in each zone are shown in Table 3.
Most of the coal powder was concentrated in zones Ⅲ, Ⅳ, and Ⅴ, while the distribution in zones I and Ⅱ was rare, the sum of which was less than 15%. This phenomenon indicates that there is enough energy in the chamber to break a large amount of coal and throw it out for a long distance in the early and middle stage of the outburst. With the continuous development of the outburst process, the energy is consumed greatly, and only a small part of the coal is broken and thrown out for a short distance. Finally, the outburst process terminates, which is also consistent with the outburst process analysis.
Compared with tests 3 and 5, when the moisture content of coal increased from 1.47 to 5%, the mass proportion of coal powder in zones Ⅲ and Ⅳ increased significantly, while that in zones Ⅴ decreased by 8.31%. In addition, the maximum distance of coal ejection was shortened by 4.67 m. The moisture content of coal has a great influence on the distance and distribution of the outburst coal powder. With the increase of moisture content, the bonding between coal particles increases (Wang H et al., 2021). Since coal rock mass is a porous medium, its internal pores and fractures are filled by water molecules, which increases the density of a single coal particle, so the thrown coal powder becomes more concentrated.
4 Discussion
4.1 Energy Analysis of Coal and Gas Outburst
The complete coal and gas outburst process goes through four stages: the preparation stage, the trigger stage, the development stage, and the termination stage. The energy required for outburst changes constantly at each stage. In the preparation stage, gas pressure and stress fully compress the skeleton of coal, resulting in a large amount of elastic potential of coal (Tu et al., 2021). In addition, 90% of the gas in coal is in the adsorption state and has great expansion potential. In the trigger stage, the equilibrium state of the coal body is broken, the free gas and stress release energy quickly to do work on the coal body, and the outburst accident is triggered (Hou et al., 2021). In the development stage, adsorbed gas with high pressure gradient can be desorbed quickly to supplement energy, and the coal body is continuously stripped, broken and thrown out by free gas. For the simulation test of coal and gas outburst in this study, the algorithm for defining energy is shown in Eq. 2 (Guo, 2014). In the outburst simulation test, coal and gas are thrown into free open space, which is different from the coal and gas thrown into the roadway in the actual coal and gas outburst. The energy calculated by this method is also different from the actual outburst energy, but the energy variation trend is consistent.
Where
Figure 9 shows the variation characteristics of outburst energy per unit distance in different tests. The outburst energy of the three tests increased first and then decreased with the distance of coal powder thrown out. The calculated outburst energy was mainly concentrated in the rear, indicating that the outburst energy is large in the early and middle period of outburst, which can break the coal body and throw it to a long distance. The total energy of outburst in tests 2, 3, and 5 was 29.8554, 62.0029 and 27.5826 kg·m, respectively. The total outburst energy in test 3 was the largest. With the decrease of moisture content and gas pressure, the total outburst energy and outburst intensity decreased. Compared with tests 3, the total energy in test 5 was reduced by 34.4203 kg·m.
4.2 Effect of Moisture on Coal and Gas Outburst
The gas desorption index of drill cuttings K1 and Δh2 are indicators to predict and judge the risk of coal and gas outburst through the correlation law of gas adsorption and desorption of coal, which are widely used in gas prevention and control technology in China. K1 reflects the gas desorption amount of coal in the first 1 min, and Δh2 reflects the gas desorption amount within 4–5 min (State Administration of Work Safety, 2019; Wang F et al., 2020). K1 and Δh2 can be obtained by intercepting the corresponding data of gas desorption experiment in Section 3.2, which can further analyze the risk of coal and gas outburst, as shown in Figure 10. When the gas adsorption equilibrium pressure is 4 MPa and the moisture content is 1.68%, K1 and Δh2 are the largest. When the gas pressure is the same, K1 and Δh2 decrease and tend to be gentle with the increase of moisture content of coal, showing an exponential law. The gas outburst parameter experimental results show that with the increase of moisture content, the adsorption constant a of coal decreases and the limit adsorption amount of gas decreases. The f of coal increases, and the coal body strength increases, thus increasing the energy threshold required by coal and gas outburst. The desorption capacity of gas decreases as the Δp decreases. All of them have an exponential relation to moisture content. The results of gas desorption experiments show that with the increase of moisture content, the accumulated gas desorption amount and the initial desorption rate decrease obviously. All the above laws indicate that the increase of moisture content weakens the risk of coal and gas outburst. According to the variation law of each parameter with moisture content, it can be predicted that there is a certain limit of moisture content. When the moisture content exceeds its value, the increase of coal seam solidity coefficient and the decrease of gas desorption velocity will no longer be obvious. Meanwhile, the adsorption constant a, f, Δp, K1, and Δh2 of coal will not change significantly, but remain roughly stable at a certain value.
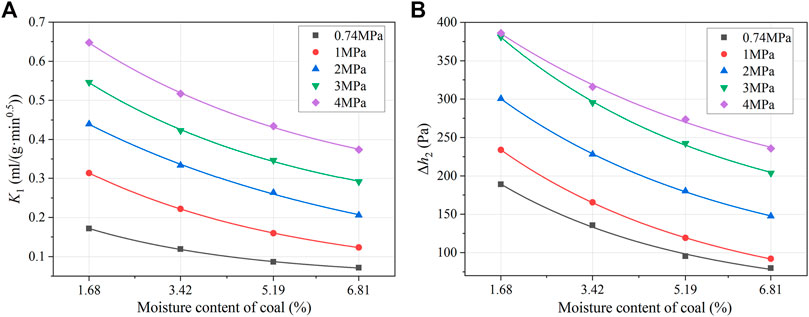
FIGURE 10. Effect of different moisture content of coal on K1 and Δh2. (A) Effect on K1. (B) Effect on Δh2.
When the moisture content of coal is low, a large amount of adsorbed gas is desorbed into free gas, and the intensity of coal and gas outburst is large. On the contrary, when the moisture content increases, the water lock effect makes the desorption amount of coal decrease greatly. Moreover, the coal body plasticity increases, elasticity decreases, and the ability to resist damage also increases, which weakens the possibility of outburst. In the coal mine site, the stress concentration zone of the working face is transferred to the depth of the coal seam, so as to reduce the stress in front of the working face. At the same time, water will have an obvious blocking effect on gas migration, which can reduce the risk of outburst. Therefore, the risk of coal and gas outburst decreases with the increase of moisture content, and the outburst may not be triggered when the moisture content increases to a critical value.
4.3 Key Indexes of Coal and Gas Outburst Prevention Under Hydraulic Measures
Hydraulic measures can reduce the outburst risk of coal seam to a large extent and escort the smooth development of mining face. In the process of gas control in coal mine site, too little water is not conducive to control the risk of coal and gas outburst. However, too much water will lead to the water lock effect (Hao et al., 2018; Liu et al., 2019; Qin et al., 2020), making it difficult for gas to be pre-extracted, which is also not conducive to the prevention and control of coal and gas outburst. Table 4 shows the critical value of outburst risk index commonly used in China (State Administration of Work Safety, 2019). In this study, the gas outburst parameters of No. 8 coal seam in the Luling coal mine under different moisture content were obtained. According to the fitting formula in Figure 3, when the moisture content is greater than 5%, the Δp is <10 and the f is >0.5. Figure 11 shows the Δh2 fitting curve of coal with a moisture content of 5.19% under different gas pressures. When the gas pressure is 0.74 MPa, Δh2 is 98.34 Pa, far less than the critical value of 160 Pa. The simulation test of coal and gas outburst also shows that it is more difficult to outburst when the moisture content of coal is greater than 5%. Therefore, it can be inferred that in No. 8 coal seam of the Luling coal mine, the coal body moisture content interval of hydraulic measures for coal and gas outburst should be greater than 5%. Therefore, 5% moisture content of coal body can be used as a critical index of hydraulic measures to prevent coal and gas outburst in No. 8 coal seam of the Luling coal mine.
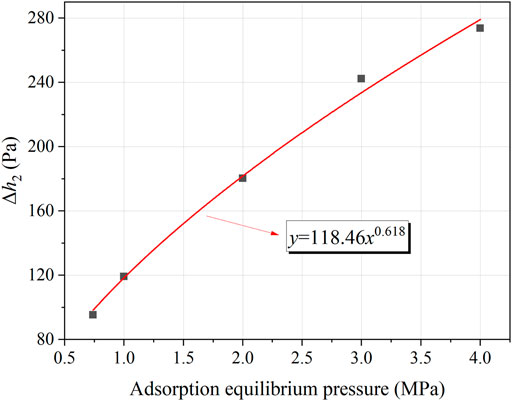
FIGURE 11. Fitting curve of adsorption equilibrium pressure effect on the Δh2 of coal with 5.19% moisture content.
5 Conclusion
In this study, we systematically studied the gas outburst parameters and gas desorption characteristics of the strong outburst coal under different moisture content in No. 8 coal seam of the Luling coal mine. Additionally, the coal and gas simulation tests under different moisture content were carried out using the simulation test system to explore the influence of moisture on the law and characteristics of coal and gas outburst. The main conclusions are as follows:
1) With the increase of moisture content, the adsorption constant a, the initial velocity of gas diffusion Δp, and the gas desorption index of drill cuttings K1 and Δh2 of coal decrease, but the Protodyakonov coefficient f of coal increases. Meanwhile, the accumulated gas desorption amount and the initial desorption rate decrease obviously. All of them have an exponential relation to moisture content. Increasing the moisture content of strong outburst coal is beneficial to reduce the outburst risk.
2) The entire outburst process is divided into four stages: preparation, trigger, development, and termination. The change of moisture content greatly affects the characteristics and energy of coal and gas outburst. With the increase of moisture content from 1.47% to 5%, the threshold of gas pressure increases and the intensity of outburst decreases, the amount of coal powder thrown out is relatively less, and the maximum distance of coal ejection is shortened by 4.67 m. Furthermore, the total outburst energy decreases by 34.4203 kg·m.
3) The coal and gas outburst may not be triggered when the moisture content increases to a critical value. When the moisture content of the strong outburst coal is greater than 5%, Δp is <10, f is >0.5, and Δh2 is < 160 Pa, which indicate that the risk of outburst is greatly reduced. Therefore, 5% moisture content of coal body can be used as a critical index of hydraulic measures to prevent coal and gas outburst in No. 8 coal seam of the Luling coal mine.
Data Availability Statement
The raw data supporting the conclusion of this article will be made available by the authors, without undue reservation.
Author Contributions
ZL: Writing, Conceptualization, Methodology and Analysis. LW: Validation, Resources and Funding acquisition. ML: Investigation and Data curation. YL: Investigation. HW: Supervision and Review. QL: Review and Resources.
Funding
This research was supported by the National Natural Science Foundation of China (Nos 51974300 and 52174216), the Fundamental Research Funds for the Central Universities (Nos 2021YCPY0206 and 2020ZDPY0224), the Postgraduate Research and Practice Innovation Program of Jiangsu Province (KYCX21_2476), and a project funded by the Priority Academic Program Development of Jiangsu Higher Education Institutions.
Conflict of Interest
The authors declare that the research was conducted in the absence of any commercial or financial relationships that could be construed as a potential conflict of interest.
Publisher’s Note
All claims expressed in this article are solely those of the authors and do not necessarily represent those of their affiliated organizations, or those of the publisher, the editors, and the reviewers. Any product that may be evaluated in this article, or claim that may be made by its manufacturer, is not guaranteed or endorsed by the publisher.
References
Beamish, B. B., and Crosdale, P. J. (1998). Instantaneous Outbursts in Underground Coal Mines: An Overview and Association with Coal Type. Int. J. Coal Geology. 35 (1), 27–55. doi:10.1016/S0166-5162(97)00036-0
Black, D. J. (2019). Review of Coal and Gas Outburst in Australian Underground Coal Mines. Int. J. Mining Sci. Tech. 29 (6), 815–824. doi:10.1016/j.ijmst.2019.01.007
Chen, D., Pan, Z., Liu, J., and Connell, L. D. (2012). Modeling and Simulation of Moisture Effect on Gas Storage and Transport in Coal Seams. Energy Fuels 26 (3), 1695–1706. doi:10.1021/ef2014327
Chen, X., and Cheng, Y. (2014). Influence of the Injected Water on Gas Outburst Disasters in Coal Mine. Nat. Hazards 76 (2), 1093–1109. doi:10.1007/s11069-014-1535-3
Chen, J., Zhu, C., Du, J., Pu, Y., Pan, P., Bai, J., et al. (2022). A Quantitative Pre-warning for Coal Burst Hazardous Zones in a Deep Coal Mine Based on the Spatio-Temporal Forecast of Microseismic Events. Process Safety and Environmental Protection 159, 1105–1112. doi:10.1016/j.psep.2022.01.082
Cheng, Y.-P., Wang, L., and Zhang, X.-L. (2011). Environmental Impact of Coal Mine Methane Emissions and Responding Strategies in China. Int. J. Greenhouse Gas Control. 5 (1), 157–166. doi:10.1016/j.ijggc.2010.07.007
Cheng, Y., and Pan, Z. (2020). Reservoir Properties of Chinese Tectonic Coal: A Review. Fuel 260, 116350. doi:10.1016/j.fuel.2019.116350
Díaz Aguado, M. B., and González Nicieza, C. (2007). Control and Prevention of Gas Outbursts in Coal Mines, Riosa-Olloniego coalfield, Spain. Int. J. Coal Geology. 69 (4), 253–266. doi:10.1016/j.coal.2006.05.004
Ding, Y., and Yue, Z. Q. (2018). An Experimental Investigation of the Roles of Water Content and Gas Decompression Rate for Outburst in Coal Briquettes. Fuel 234, 1221–1228. doi:10.1016/j.fuel.2018.07.143
Fan, C., Li, S., Elsworth, D., Han, J., and Yang, Z. (2020). Experimental Investigation on Dynamic Strength and Energy Dissipation Characteristics of Gas Outburst‐prone Coal. Energy Sci Eng 8 (4), 1015–1028. doi:10.1002/ese3.565
Fan, C., Li, S., Luo, M., Du, W., and Yang, Z. (2017). Coal and Gas Outburst Dynamic System. Int. J. Mining Sci. Tech. 27 (1), 49–55. doi:10.1016/j.ijmst.2016.11.003
Fan, C., Yang, L., Wang, G., Huang, Q., Fu, X., and Wen, H. (2021). Investigation on Coal Skeleton Deformation in CO2 Injection Enhanced CH4 Drainage from Underground Coal Seam. Front. Earth Sci. 9. doi:10.3389/feart.2021.766011
Guo, P. (2014). Research on Laminar Spallation Mechanism of Coal and Gas Outburst Propagation [D]. Xuzhou, Jiang su: China University of mining and technology.
Hao, D., Zhang, L., Ye, Z., Tu, S., and Zhang, C. (2018). Experimental Study on the Effects of the Moisture Content of Bituminous Coal on its Gas Seepage Characteristics. Arabian J. Geosciences 11 (15). doi:10.1007/s12517-018-3758-1
Hou, W., Wang, H., Yuan, L., Wang, W., Xue, Y., and Ma, Z. (2021). Experimental Research into the Effect of Gas Pressure, Particle Size and Nozzle Area on Initial Gas-Release Energy during Gas Desorption. Int. J. Mining Sci. Tech. 31 (2), 253–263. doi:10.1016/j.ijmst.2021.01.002
Jin, K., Cheng, Y., Ren, T., Zhao, W., Tu, Q., Dong, J., et al. (2018). Experimental Investigation on the Formation and Transport Mechanism of Outburst Coal-Gas Flow: Implications for the Role of Gas Desorption in the Development Stage of Outburst. Int. J. Coal Geology. 194, 45–58. doi:10.1016/j.coal.2018.05.012
Lei, Y., Cheng, Y., Ren, T., Tu, Q., Shu, L., and Li, Y. (2020). The Energy Principle of Coal and Gas Outbursts: Experimentally Evaluating the Role of Gas Desorption. Rock Mech. Rock Eng. 54 (1), 11–30. doi:10.1007/s00603-020-02246-5
Liu, Y., Feng, G., Zuo, W., Liu, M., and Mitri, H. S. (2019). The Law and Mechanism of Dynamic Methane Diffusion from Coal Particles under Different Moisture Content. Arabian J. Geosciences 12 (24). doi:10.1007/s12517-019-4919-6
Lu, Y., Ge, Z., Yang, F., Xia, B., and Tang, J. (2017). Progress on the Hydraulic Measures for Grid Slotting and Fracking to Enhance Coal Seam Permeability. Int. J. Mining Sci. Tech. 27 (5), 867–871. doi:10.1016/j.ijmst.2017.07.011
Meng, J., Li, S., Niu, J., Meng, H., Zhong, R., Zhang, L., et al. (2020). Effects of Moisture on Methane Desorption Characteristics of the Zhaozhuang Coal: experiment and Molecular Simulation. Environ. Earth Sci. 79 (1). doi:10.1007/s12665-019-8788-9
Pan, Z., Connell, L. D., Camilleri, M., and Connelly, L. (2010). Effects of Matrix Moisture on Gas Diffusion and Flow in Coal. Fuel 89 (11), 3207–3217. doi:10.1016/j.fuel.2010.05.038
Qin, H., Wei, J., Li, D., and Li, S. (2019). Experimental Investigation on the Release Rule of the Gas Expansion Potential of Loaded Water-Filled Soft Coal. Math. Probl. Eng. 2019, 1–9. doi:10.1155/2019/1085296
Qin, Y., Su, W., Tian, F., and CHen, Y. (2020). Research Status and Development Direction of Microcosmic Effcet under Coal Seam Water Injection. J. China Univ. Mining Tech. 49 (03), 428–444. doi:10.13247/j.cnki.jcumt.001148
Shepherd, J., Rixon, L. K., and Griffiths, L. (1981). Outbursts and Geological Structures in Coal Mines: A Review. Int. J. Rock Mech. Mining Sci. Geomechanics Abstr. 18 (4), 267–283. doi:10.1016/0148-9062(81)91192-x
State Administration of Work Safety (2019). Detailed Rules for Prevention and Control of Coal and Gas Outburst. Beijing: China Coal Industry Publishing House.
Sun, Q. (2014). Research on Status Quo and Prevention Countermeasures of Coal Mine Gas Disaster in China. China Coal 40 (03), 116–119. doi:10.19880/j.cnki.ccm.2014.03.027
Tu, Q., Cheng, Y., Guo, P., Jiang, J., Wang, L., and Zhang, R. (2016). Experimental Study of Coal and Gas Outbursts Related to Gas-Enriched Areas. Rock Mech. Rock Eng. 49 (9), 3769–3781. doi:10.1007/s00603-016-0980-6
Tu, Q., Cheng, Y., Xue, S., Ren, T., and Cheng, X. (2021). Energy-limiting Factor for Coal and Gas Outburst Occurrence in Intact Coal Seam. Int. J. Mining Sci. Tech. 31 (4), 729–742. doi:10.1016/j.ijmst.2021.05.009
Wang, C., Cheng, Y., Yi, M., Lei, Y., and He, X. (2020). Powder Mass of Coal after Impact Crushing: A New Fractal-Theory-Based Index to Evaluate Rock Firmness. Rock Mech. Rock Eng. 53 (9), 4251–4270. doi:10.1007/s00603-020-02174-4
Wang, C., Yang, S., Li, J., Li, X., and Jiang, C. (2018). Influence of Coal Moisture on Initial Gas Desorption and Gas-Release Energy Characteristics. Fuel 232, 351–361. doi:10.1016/j.fuel.2018.06.006
Wang, F., Liang, Y., Sun, Z., Li, L., and Li, X. (2020). Determination of the Sensitivity index and its Critical Value for Outburst Risk Prediction: A Case Study in Fuxiang Mine, China. Adsorption Sci. Tech. 38 (9-10), 502–527. doi:10.1177/0263617420963735
Wang, H., Cheng, Y., and Yuan, L. (2013). Gas Outburst Disasters and the Mining Technology of Key Protective Seam in Coal Seam Group in the Huainan coalfield. Nat. Hazards 67 (2), 763–782. doi:10.1007/s11069-013-0602-5
Wang, H., Tao, Y., Wang, D., Sun, X., Gao, J., and Loupasakis, C. (2021). Experimental Study on Mechanical Properties of Briquette Coal Samples with Different Moisture Content. Geofluids 2021, 1–11. doi:10.1155/2021/6634378
Wang, K., Dong, H., Guo, Y., Zhao, W., Shao, B., Yan, Z., et al. (2021). Gas Drainage Performance Evaluation in Coal under Non-uniform Stress with Different Moisture Content: Analysis, Simulation and Field Verification. Fuel 305, 121489. doi:10.1016/j.fuel.2021.121489
Wang, L., Chen, E.-t., Liu, S., Cheng, Y.-p., Cheng, L.-b., Chen, M.-y., et al. (2017a). Experimental Study on the Effect of Inherent Moisture on Hard Coal Adsorption-Desorption Characteristics. Adsorption 23 (5), 723–742. doi:10.1007/s10450-017-9889-y
Wang, L., Liu, S., Cheng, Y., Yin, G., Zhang, D., and Guo, P. (2017b). Reservoir Reconstruction Technologies for Coalbed Methane Recovery in Deep and Multiple Seams. Int. J. Mining Sci. Tech. 27 (2), 277–284. doi:10.1016/j.ijmst.2017.01.026
Wang, L., Lu, Z., Chen, D.-p., Liu, Q.-q., Chu, P., Shu, L.-y., et al. (2020c). Safe Strategy for Coal and Gas Outburst Prevention in Deep-And-Thick Coal Seams Using a Soft Rock Protective Layer Mining. Saf. Sci. 129, 104800. doi:10.1016/j.ssci.2020.104800
Wang, L., Xi, G., Keep, R. F., and Hua, Y. (2012). Iron Enhances the Neurotoxicity of Amyloid β. Transl. Stroke Res. 3 (1), 107–113. doi:10.1007/s12975-011-0099-8
Xue, S., Yuan, L., Wang, Y., and Xie, J. (2014). Numerical Analyses of the Major Parameters Affecting the Initiation of Outbursts of Coal and Gas. Rock Mech. Rock Eng. 47 (4), 1505–1510. doi:10.1007/s00603-013-0425-4
Yan, F., Xu, J., Lin, B., Peng, S., Zou, Q., and Zhang, X. (2019). Effect of Moisture Content on Structural Evolution Characteristics of Bituminous Coal Subjected to High-Voltage Electrical Pulses. Fuel 241, 571–578. doi:10.1016/j.fuel.2018.12.078
Yang, M., Yuan, M., Xu, L., Xu, S., Li, C., and Wang, Y. (2017). Research of the Influence of Moisture on Initial Speed of Methane Diffusion. Ind. Saf. Environ. Prot. 43 (04), 11–13. doi:10.3969/j.issn.1001-425X.2017.04.004
Yang, W., Wang, H., Zhuo, Q., Lin, B., Zhang, J., Lu, C., et al. (2019). Mechanism of Water Inhibiting Gas Outburst and the Field experiment of Coal Seam Infusion Promoted by Blasting. Fuel 251, 383–393. doi:10.1016/j.fuel.2019.04.064
Yao, Q., Zheng, C., Tang, C., Xu, Q., Chong, Z., and Li, X. (2020). Experimental Investigation of the Mechanical Failure Behavior of Coal Specimens with Water Intrusion. Front. Earth Sci. 7. doi:10.3389/feart.2019.00348
Yi, M., Wang, L., Liu, Q., Hao, C., Wang, Z., and Chu, P. (2021). Characteristics of Seepage and Diffusion in Gas Drainage and its Application for Enhancing the Gas Utilization Rate. Transp Porous Med. 137 (2), 417–431. doi:10.1007/s11242-021-01573-7
Zhang, C., Wang, E., Wang, Y., and Zhou, X. (2021). Spatial-temporal Distribution of Outburst Accidents from 2001 to 2020 in China and Suggestions for Prevention and Control. Coal Geology. Exploration 49 (4), 134–141. doi:10.3969/j.issn.1001-1986.2021.04.016
Zhang, G., Liu, X., Bi, Y., and Pu, W. (2011). Experimental Study of Penetrant Solution Impact on Gas Desorption. Proced. Eng. 26, 113–119. doi:10.1016/j.proeng.2011.11.2147
Zhang, H., Cheng, Y., Liu, Q., Yuan, L., Dong, J., Wang, L., et al. (2017). A Novel In-Seam Borehole Hydraulic flushing Gas Extraction Technology in the Heading Face: Enhanced Permeability Mechanism, Gas Flow Characteristics, and Application. J. Nat. Gas Sci. Eng. 46, 498–514. doi:10.1016/j.jngse.2017.08.022
Zhang, K. Z., Wang, S. L., Wang, L., Cheng, Y. P., Li, W., Han, X. W., et al. (2022). 3D Visualization of Tectonic Coal Microstructure and Quantitative Characterization on Topological Connectivity of Pore-Fracture Networks by Micro-CT. J. Pet. Sci. Eng. 208, 109675. doi:10.1016/j.petrol.2021.109675
Zhang, S., and Sang, H. (2009). Physical Chemistry Mechanism of Influence of Liquid Water on Coalbed Methane Adsorption. Proced. Earth Planet. Sci. 1 (1), 263–268. doi:10.1016/j.proeps.2009.09.042
Zhao, W., Cheng, Y., Jiang, H., Jin, K., Wang, H., and Wang, L. (2016). Role of the Rapid Gas Desorption of Coal Powders in the Development Stage of Outbursts. J. Nat. Gas Sci. Eng. 28, 491–501. doi:10.1016/j.jngse.2015.12.025
Zhao, W., Wang, K., Zhang, R., Dong, H., Lou, Z., and An, F. (2020). Influence of Combination Forms of Intact Sub-layer and Tectonically Deformed Sub-layer of Coal on the Gas Drainage Performance of Boreholes: a Numerical Study. Int. J. Coal Sci. Technol. 7 (3), 571–580. doi:10.1007/s40789-020-00317-0
Zhao, Y., Cao, S., Li, Y., Zhang, Z., Guo, P., Yang, H., et al. (2018). The Occurrence State of Moisture in Coal and its Influence Model on Pore Seepage. RSC Adv. 8 (10), 5420–5432. doi:10.1039/c7ra09346b
Zhi, S., and Elsworth, D. (2016). The Role of Gas Desorption on Gas Outbursts in Underground Mining of Coal. Geomech. Geophys. Geo-energ. Geo-resour. 2 (3), 151–171. doi:10.1007/s40948-016-0026-2
Zhou, A., Zhang, M., Wang, K., and Elsworth, D. (2020). Near-source Characteristics of Two-phase Gas-Solid Outbursts in Roadways. Int. J. Coal Sci. Technol. 8 (4), 685–696. doi:10.1007/s40789-020-00362-9
Keywords: coal and gas outburst, moisture content, gas desorption, hydraulic measures, simulation test
Citation: Lu Z, Wang L, Lv M, Lei Y, Wang H and Liu Q (2022) Experimental Study on Coal and Gas Outburst Risk in Strong Outburst Coal Under Different Moisture Content. Front. Earth Sci. 10:782372. doi: 10.3389/feart.2022.782372
Received: 24 September 2021; Accepted: 15 February 2022;
Published: 22 March 2022.
Edited by:
Jie Chen, Chongqing University, ChinaReviewed by:
Huafu Qiu, Xi’an University of Science and Technology, ChinaChaojun Fan, Liaoning Technical University, China
Zou Quanle, Chongqing University, China
Haifei Lin, Xi’an University of Science and Technology, China
Copyright © 2022 Lu, Wang, Lv, Lei, Wang and Liu. This is an open-access article distributed under the terms of the Creative Commons Attribution License (CC BY). The use, distribution or reproduction in other forums is permitted, provided the original author(s) and the copyright owner(s) are credited and that the original publication in this journal is cited, in accordance with accepted academic practice. No use, distribution or reproduction is permitted which does not comply with these terms.
*Correspondence: Liang Wang, wangliang@cumt.edu.cn; Qingquan Liu, cumtsafe@cumt.edu.cn