- ICSM, Univ Montpellier, CEA, CNRS, ENSCM, Marcoule, Bagnols-sur-Cèze, France
We show hereby that recycling of NdFeB permanent magnets by selective leaching and precipitation is possible, using an electrolyte as hydrotrope, thus avoiding the need of any specific extractant molecules. We analyse the yield of the extractant-free process and show that the non toxic formulation of Sodium Salicylate and ethylacetate used as diluent and choosing the optimal tie-line in a ternary phase diagram allows extraction using any type of acid in the aqueous phase. Iron is well separated from rare earths and the product can be recovered directly form the fluid used in separation by oxalic acid precipitation.
1 Introduction
NdFeB permanent magnets have been commercially available since the mid-1980s (Gutfleisch et al., 2011; Croat et al., 1984; Buschow, 1994; Filippas et al., 2021). With a much higher magnetic force than magnets of previous generations (ferrite, SmCo), they are gaining ground due to the increasing importance of miniaturization in many applications (Yang et al., 2017). The chemical composition of NdFeB magnets varies considerably, depending on the specific application, but in principle, all NdFeB magnets are composed of a tetragonal Nd2Fe14B crystal structure (Zhang et al., 1988). They are composed of around 30% Nd, 64% Fe and 0.5% B (Mochizuki et al., 2013; Behera and Parhi, 2016). Surrounded by an Nd-rich grain boundary, other rare earths found in the grain boundary are Dy, Gd, Pr and Tb (Binnemans et al., 2013). Other elements, including Al, Co., Cu, Mo, Nb, Ti, V and Zr, may also be present in trace amounts (<1%). The addition of certain elements is directly linked to the improvement of certain properties. To this end, small quantities of Dy and Tb are added to increase the magnet’s intrinsic coercivity and anisotropy, as well as its high-temperature performance. Gadolinium is added to increase the temperature coefficient, while Cu and Al are added to improve magnet sintering (Yang et al., 2017). Then, Cobalt is added to increase the temperature at which the magnet loses its magnetic properties (Riano and Binnemans, 2015). In addition, nickel-based coatings are used to protect the surface of NdFeB magnets from corrosion (Li et al., 2009).
After dismantling, hydrogen decrepitation and grinding, Rare Earth Elements (REEs) recovery from NdFeB magnets can be achieved by hydrometallurgical, pyrometallurgical or biohydrometallurgical methods (Kumari and Sahu, 2023; Habibzadeh et al., 2023; Chung et al., 2022; Polyakov and Sibilev, 2015; Emil-Kaya et al., 2022; Zhang et al., 2020; Kucuker et al., 2017; Walton et al., 2015; Okabe et al., 2003; Saito et al., 2003). Processes such as oxidation (Stopic et al., 2022; Emil-Kaya et al., 2023), carbonylation (Miura et al., 2008; Itoh et al., 2009), chlorination using NH4Cl (Itoh et al., 2007), molten magnesium metal technique (Takeda et al., 2006), chemical vapor transport (Murase et al., 1995) and leaching using a mineral acid (Emil-Kaya et al., 2022; Uysal et al., 2023; Yang et al., 2017; Borra et al., 2015; Wu et al., 2014; Yoon et al., 2014; Rabatho et al., 2013) have been investigated for substantial REEs recovery. However, due to the drawbacks of pyrometallurgical methods, including high energy consumption and low selectivity, the hydrometallurgical leaching was often proposed for rare earth metal extraction. To date, acidic, alkaline and ammoniacal reagents have been used for REE leaching from WEEE. Although the use of mineral acids (sulfuric, nitric and hydrochloric acid), ammonia and NaOH is more common in the development of hydrometallurgical leaching processes, these reagents also produce environmentally hazardous and toxic gases during leaching. Furthermore, the acid- or alkali-based leach solution generated after leaching is not generally recycled, resulting in a loss of reagents (Rabatho et al., 2013; Yoon et al., 2014; Borra et al., 2015). Therefore, due to low energy consumption, low toxic gas emissions, low waste generation and recyclable nature, adaptations of green organic reagents are well used for rare earth metal leaching (Borra et al., 2015). Thus, the leaching of REEs with various organic and inorganic acids has been studied by many researchers (Onal et al., 2020; Wu et al., 2014; Yoon et al., 2014; Borra et al., 2015). Lyman et al. developed a process involving the recovery of REE by leaching magnetic scrap with H2SO4, followed by the precipitation of rare earth salts (Lyman and Palmer, 1993). A kinetic study of neodymium leaching from NdFeB magnet waste was carried out with H2SO4 and almost all (∼99.99%) of the amount of Nd was recovered in the aqueous phase (Yoon et al., 2014). A comparative study of the leaching of La, Nd and Lu from bauxite residues was reviewed by Borra et al. Different mineral acids (nitric, hydrochloric, sulphuric) and organic acids (citric, acetic acid, methanesulfonic) were investigated with a quantitative dissolution of Neodymium and Dysprosium with H2SO4 (Borra et al., 2015).
Since these acids also dissolve high quantities of Fe, particular attention has been paid to the development of selective processes. After processing a sulfate mixture with H2SO4 (12–16 M), drying and high-temperature treatment, the resulting magnet powder is leached in demineralized water, leading to >95% REE recovery, while Fe remains in the solid residue as a sulfate salt (Onal et al., 2017). In 2014, the leaching of NdFeB magnet waste using H2SO4 at different temperatures and concentrations was studied with optimal conditions operated with a 3 mol.L-1 solution at 70°C in 4 h (Yoon et al., 2014). In 2013, a study using solutions of H2SO4, HCl, HNO3 and NaOH was conducted Lee et al., 2013). HCl and H2SO4 showed the best leaching performance. Optimum conditions were a solid/liquid ratio of 20 g.L-1, a leaching time of 15 min and concentrations of 3 mol.L-1 HCl and 1.5 mol.L-1 of H2SO4. As far as we know, most research to date has been carried out using strong mineral acids for leaching (Gergoric et al., 2017; Onal et al., 2017; Parhi et al., 2016).
Although the use of mineral acids and their mixtures showed good performance, there is still the issues of regeneration, release of toxic gases during the leaching, and the inconvenience of handling a high-concentration acid in an industrial-scale operation. Ground-breaking improvements are still needed to satisfy more and more stringent requirements on the environmental impact of metal waste leaching.
Therefore, we focus here on leaching using weak organic acids. Acetic acid has been shown to be effective in leaching precious metals and rare earths from several sources (Murase et al., 1995; Behera and Parhi, 2016; Zhu et al., 2013). The kinetics of Nd extraction from NdFeB waste using this acid has been detailed by Behera and Parhi, (2016) who showed that acid concentrations above 0.4 mol.L-1 at 800 rpm, 1% S/L ratio and 308 K was effective conditions in leaching Nd and Fe. However, in this study, little attention has been paid to the recovery of other REEs, meaning that no detailed studies of kinetics or temperature dependence have been carried out for essential REEs such as Dy and Pr in waste. The behaviour of other impurities such as Fe, B and Co. during the leaching process has not been fully addressed either. Based on the various characteristics of a ternary H2O/NaSal/AcOEt system previously determined (Figure 1), (El Maangar et al., 2020) we propose here a new and eco-compatible process for recovering REEs from NdFeB magnets.
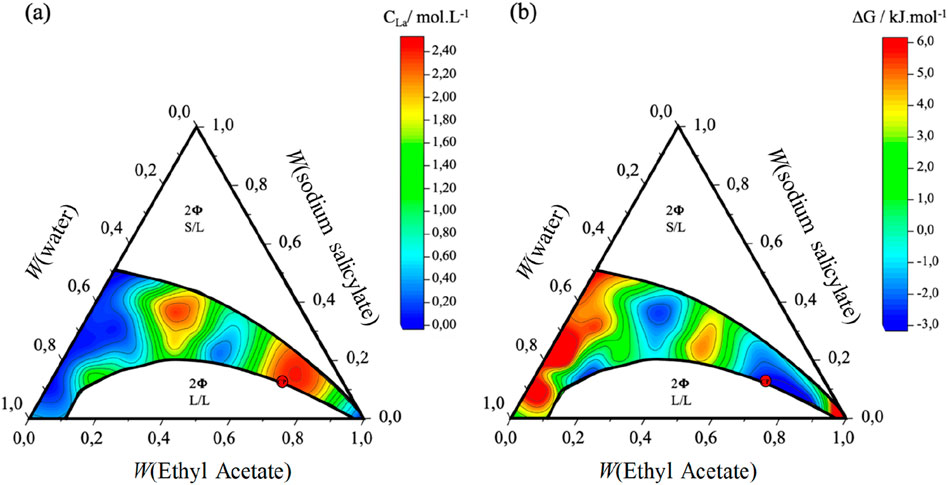
Figure 1. (A) Solubilization map of lanthanum salts in the ternary system consisting of H2O/NaSal/AcOEt. (B) Corresponding map translated into transfer Gibbs energy from solid state to the state as dissolved in a ternary fluid based on an hydrotrope (reproduced from El Maangar et al., 2020, with permission).
2 Experimental section
2.1 Materials
Ethyl acetate (EA) (N99.9%) and sodium salicylate (NaSal) (N99.5%) were respectively purchased from Merck (Darmstadt, Germany) and Sigma Aldrich (Darmstadt, Germany). 70% nitric acid was bought from Fischer, 62% sulphuric acid and 37% acid chloride and oxalic acid were purchased from Sigma Aldrich. All chemicals were used without further purification.
2.2 Phase diagrams, tine-lines
The determination of the existence of a monophasic and biphasic domains as well as tine-lines in the biphasic in the ternary water/sodium salicylate/ethyl acetate mixture was performed using a static and dynamic process, previously described (El Maangar et al., 2020). As can be seen in Figure 1, the two domains with the highest solubilities are observed first as usual near the critical point (red dot), but also in the Prenucleation cluster region that is close to the S/L phase separation line when 35% of NaSal as hydrotrope is used.
2.3 Density measurement and tie-line determination in the miscibility gap
Solution densities were determined using a vibrating tube density meter (DMA 5000 M, Anton Paar, Austria) at (25 ± 0.005) °C with a nominal precision of ±5·10−6 g.mL-1. Calibration was performed using air and pure water at 25 °C. At the beginning and at the end of each day, calibration was checked using pure water and between each measurement against air (maximum deviation: ±5·10−5 g.mL-1)
2.4 Leaching experiments
After determining the chemical composition of the waste, leaching experiments were carried out using the ternary H2O/NaSal/AcOEt. In order to compare the performance of this new system with conventional leaching systems, leaching experiments using strong inorganic acids were also carried out in parallel. Sulfuric acid, hydrochloric acid and nitric acid were thus studied at various concentrations. Leaching is carried out in thermostatically-controlled reactors, with stirring to adjust the temperature to the needs of each experiment. 10 mL of a ternary solution of water, NaSal and AcOEt of the desired composition, or an inorganic acid of the desired concentration for comparison experiments, is added to the reactor. Once the operating temperature has been reached, the magnet powder is added to the solution at the desired S/L ratio. After a pre-defined leaching time, the leachate is filtered. Metal concentrations in the leachate are determined using an X-ray fluorescence spectrometer (XRF) and ICP-OES. The aim of the various tests carried out is to study the leaching of the different REEs making up NdFeB magnet powder, namely, Nd, Pr, Dy and Fe, accor ding to different parameters: (i) the composition of the leaching solution, (ii) the stirring rate, (iii) the S/L ratio, (iv) the leaching time and (v) the operating temperature. During the leaching experiments, one of the parameters was modified while the others were kept constant. To ensure reproducibility, leaching experiments are repeated three times, and the experimental error was found to be ±2%. Leaching efficiency E (%) is defined in Equation 1 as follows:
2.5 X-ray fluorescence (XRF) measurements
A commercial XRF spectrometer model SPECTRO XEPOS (AMETEK) is used, and liquid samples are placed in 6 mm diameter cups, the base of which is made of a 4 μm-thick film of ProleneTM. ProleneTM is a high X-ray transmission material marketed by Ethicon Inc. The XRF spectrometer analyzes a series of eleven cups using a rotating carousel that positions the samples above the so-called “inverse optics” section. Inverse optics enable the analysis of liquids, as the area illuminated by the X-rays is flat. In this instrument, it is possible to place 25 mm diameter analysis cups to illuminate a larger surface and thus recover a stronger fluorescence signal, which is useful in the case of highly diluted samples. In order to prepare for the integration of a measurement on a microfluidic device and minimize sample volumes, our choice 6 mm diameter cups.
2.6 ICP-OES
Elements-f and iron are measured by ICP-OES (Inductive Coupled Plasma - Optical Emission Spectroscopy). The commercial instrument used for this study is a SPECTRO ARCOS ICP-OES, equipped with a circular detector consisting of 32 linearly aligned CCDs, each with a resolution of 3,648 pixels covering wavelengths from 130 to 770 nm. Detector resolution is 8.5 p.m. from 130 to 340 nm and 15 p.m. from 340 to 770 nm, with an intensity dynamic range of eight orders of magnitude. The CCDs are read simultaneously and a complete spectrum is generated in less than 2 seconds. The circular polychromator (Paschen-Runge design, optical components; MgF2, Zerodur structure) has a focal length of 750 mm. Thermal excitation is created by a radio-frequency generator operating at a frequency of 27.12 MHz, with power adjustable from 0.7 to 1.7 kW with 70% efficiency and 0.1% stability.
3 Results and discussion
3.1 Elemental composition of WEEE
NdFeB magnet powder was used as the NdFeB waste stream in its original form (as received, particle size <1 mm). The particles are sieved to the desired size fraction so as to fix the particle size range throughout the leaching study, unless otherwise specified. To determine the total elemental composition, 1 g of NdFeB powder is dissolved in 10 mL aqua regia (VHCl, conc: VHNO3,conc = 3 : 1) at 80°C ± 1°C for 8 h. The solution was then filtered through polypropylene filters (0.45 μm, VWR). No residue was observed on the filter paper after filtration of the solution. The composition of the prepared solution was measured using ICP-OES and XRF. The concentrations obtained are converted into mass percentages of the elements in the powders. All experiments were carried out in triplicate to guarantee the statistical reliability of the results.
Table 1 shows the composition of the magnet powder that was used in the leaching experiments. The most abundant rare earth in magnet powder is Nd, with around 25% in mass fraction, followed by Pr with 3.4% and Dy with around 2.4% in mass fraction. The main constituent of NdFeB powder is Fe, which accounts for around 60% of the waste mass. Other impurities, including Co. and B, were also found in mass percentages of around 1%, as well as Ni (around 0.4%), which is commonly found in NdFeB coating (Li et al., 2009). The composition determined here corresponds to the REE content and other constituent elements of NdFeB magnets found in industrial fluxes (Binnemans et al., 2013; Yang et al., 2017; Tunsu et al., 2015). The difference from 100% can be attributed to experimental errors or un-analysed elements.

Table 1. Elemental composition, in weight fraction, of NdFeB powder totally dissolved in aqua regia for 6 h at 80°C ± 1°C and S/L = 0.1 : 10 g.mL-1.
3.2 Influence of the composition
In order to determine the optimum operating conditions for leaching, the first variable studied was the composition of the ternary H2O/NaSal/AcOEt leaching system. Leaching tests were carried out at different compositions in the monophasic region of the phase diagram (see Figure 1), maintaining the leaching step for 5 h at a temperature of 25°C. The S/L ratio is maintained at 0.2 g of magnet powder per 10 mL of ternary solution, and the stirring rate at 700 rpm. The starting compositions of the leaching solutions used are shown in the phase diagram in Figure 2 and summarized in Supplementary Table S1). Each experiment was performed 3 times and pH values before and after leaching also measured. Figure 2 shows the variation in leaching yields for Dy, Nd and Fe as a function of the mass fraction of ethyl acetate in the binary water/ethyl acetate mixture, α where α is defined in Equation 2 as:
with wEA and wwater are the mass fraction of AcOEt and water in the ternary mixture.
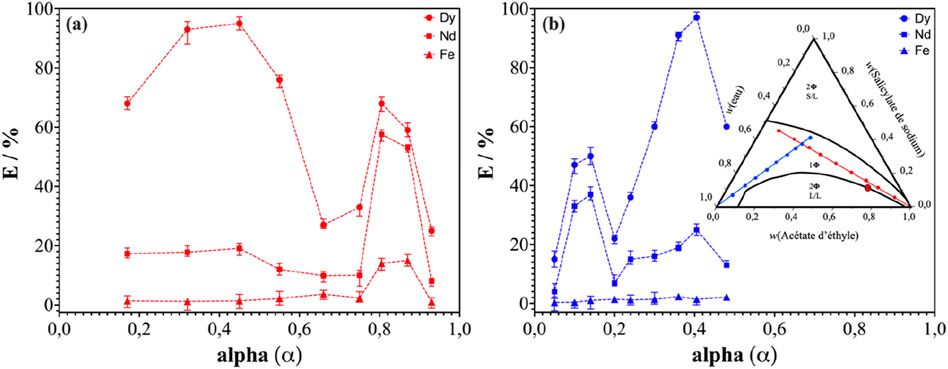
Figure 2. Effect of the composition of the ternary system water/NaSal/EtOAc on the leaching efficiency of Nd, Dy and Fe. Water rich ternary solutions are shown as blue point in a dilution line, while solvent rich are shown in red. α is defined as classically for classical microemulsions: α is the amount of solvent (AcOEt) in the total (water plus AcOEt), not taking into account the hydrotrope. The temperature is maintained at 25°C ± 1°C, magnetic stirring at 700 rpm and the S/L ratio at 1: 50 g.mL-1. (A): dilution line with ethyl acetate. (B) dilution line with water.
Leaching tests were carried out on two different dilution lines in the single-phase region of the system under consideration (Figure 2B). The composition of the system plays an important role in the leaching efficiency of REEs from NdFeB powder. Dy and Nd leaching was maximal for an α value equal to 0.42. This yield then remained stable for α values between 0.38 and 0.45 on the dilution line with AcOEt (red dilution line, Figure 2A) and between 0.36 and 0.42 on the dilution line with water (blue dilution line, Figure 2B). This range of α values, corresponds to the region where Pre-Nucleation clusters (NPCs) are observed (see Supplementary Figure S1) (El Maangar et al., 2020). The maximum leaching yield for α = 0.42 corresponds to a mass fraction composition of the ternary solution of 21% ethyl acetate, 39% sodium salicylate and 40% water. Regarding the leaching yield of praseodymium, the same behaviour as for neodymium was observed, with a yield reaching a maximum value at the same composition. Furthermore, these results showed that the leaching efficiency of Fe was very low, whatever the composition of the ternary solution. In Figure 2A, a local efficiency maximum was identified in the AcOEt-rich region, which was found at α = 0.8. It should be noted that this value of α corresponds to the region close to the critical point where critical fluctuations (CF) are dominant. Similarly for Figure 2B, on the water-rich side, and at α = 0.14, a local maximum was found. This region corresponds to the Pre-Ouzo (PO) region where e/h aggregates were identified.
These results are in line with the solubilization regimes previously identified and reported (El Maangar et al., 2020). The presence of cohesive aggregates, whether critical pre-nucleation (CPN) or pre-ouzo (PO), systematically increases the yield of leaching. This can be understood by applying the “ienaic” decomposition of the molecular forces involved in the phase transfer, originally designed to understand LL separation yields, to the case of solid/liquid transitions (Špadina et al., 2021; Špadina et al., 2022). An interesting result was the selectivity of dysprosium over neodymium and iron in the CPN region (i.e., α = 0.42), which is not the case in the FC region.
Leaching experiments with strong inorganic acids are carried out, in order to compare the results obtained with those of the H2O/NaSal/AcOEt ternary system. Figure 3 shows the results of leaching NdFeB powder using 2 mol.L-1 HNO3, 2 mol.L-1 H2SO4 and 2 mol.L-1 HCl under the same operating conditions as the experiments reported in Figure 2. Inorganic acids proved highly effective in leaching REEs from NdFeB powder. All elements were dissolved in yields of over 83% after 5 h in all the acids used. Increasing the acid concentration up to 5 mol.L-1 did not result in a significant increase in the amount of REE leached. It is important to note that in all inorganic acids, the addition of NdFeB powder to the leaching solutions caused an exothermic reaction due to high oxidation conditions, as well as NO2 off-gassing in the case of HNO3. Similar effects have been observed in previous work (Yoon et al., 2014; Gergoric et al., 2018), suggesting roasting to remove this problem, also leading to lower heat and gas releases during leaching of REE oxides. In addition to REE, other elements contained in the NdFeB magnet were also leached using all the above-mentioned inorganic acids, namely, iron, boron and cobalt. No selectivity was obtained between the elements, either inter-REEs or between REEs and other elements (i.e., , B, Co. and Fe).
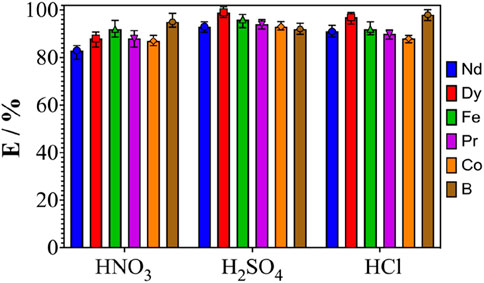
Figure 3. Effect of acid nature (HNO3, H2SO4 and HCl) on the leaching efficiency of Nd, Dy, Fe, Pr, Co. and B. The temperature is maintained at 25°C ± 1°C, magnetic stirring at 700 rpm and the S/L ratio at 1: 50 g.mL-1. The acid concentration is 2 mol.L-1.
Based on the determination of the distribution coefficient KDi = (Cl/Cs)i.V/m with Cl the concentration of the considered element i in the leachate of a volume V and Cs the concentration in the solid residue of mass m after leaching, Figure 4 shows the separation factor (KDDy/KDi) of the leaching of dysprosium in relation to two other rare earths in the magnet (Nd and Pr) and iron, for the H2O/NaSal/AcOEt system and for three inorganic acids. Figure 4A shows the results for the ternary H2O/NaSal/AcOEt system in three different compositions. The leaching solution compositions chosen correspond to the compositions where the overall maximum in leaching efficiency as well as the two local maxima were already identified in Figure 2. These three maxima were found, respectively, in three different regions of the phase diagram FC, CPN and PO (see Supplementary Figure 1). A very slight selectivity of Dy, compared to Nd and Pr, was observed in the case of leaching in the region close to the critical point (FC) as well as in the pre-Ouzo region (PO). This selectivity increased significantly in the CPN region, from SFDy/Nd of 1.7 for the PO point to SFDy/Nd of 62.5 for the CPN point. This was linked to the solubilization mechanisms previously discussed (El Maangar et al., 2020). All three compositions showed significant iron selectivity (15.6 for FC, 1,535 for CPN and 98.6 for PO).
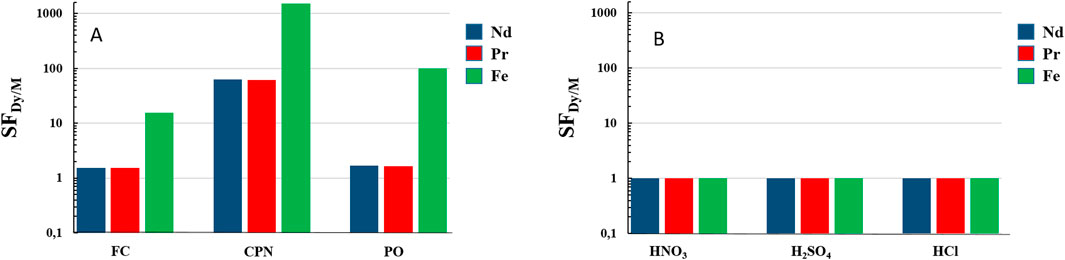
Figure 4. Selectivity coefficient of dysprosium with respect to neodymium, praseodymium and iron. (A) for the H2O/NaSal/AcOEt system at three different compositions corresponding to the three FC, CPN and PO regimes. (B) for three strong inorganic acids at 2 M: HNO3, H2SO4 and HCl.
Figure 4B shows the selectivity results for HNO3, H2SO4 and HCl. All selectivity coefficients were close to one and no selectivity was observed for these acids. In this case, the NdFeB powder was simply “ put into solution “ These results reinforce the interest in the H2O/NaSal/AcOEt system for the selective leaching of REEs in energy-as well as effluent-efficient processes, making it possible to close the REEs life cycle under favourable conditions in terms of cost and eco-compatibility. For example, a ternary mass composition of 21% ethyl acetate, 39% sodium salicylate and 40% water was recommended for efficient, selective REE recovery from NdFeB powder. This composition was used for the following experiments.
3.3 Study of the solid/liquid ratio
The S/L ratio is a key parameter in characterizing waste leaching behaviour. This is the ratio between the mass of the solid to be leached and that of the liquid (i.e., the leaching solution). The leaching of NdFeB powder as a function of the S/L ratio in the range from 1:10 to 1:100 g.mL-1 was thus studied. The volume of the leaching solution was kept at 10 mL in all cases, and the mass of the NdFeB powder varied. The powder samples were dissolved in the H2O/NaSal/AcOEt mixture in a composition of 21% AcOEt, 39% NaSal and 40% H2O for 5 h. The stirring speed was kept constant at 800 rpm, and the temperature maintained at 25°C ± 1°C. The leaching efficiencies of Nd, Dy and Fe with the ternary H2O/NaSal/AcOEt are presented in Figure 5. The variation of the S/L ratio had significant effects on the leaching efficiencies of the elements present. Dy leaching increased from 80.3% to 99.7% with the decrease of S/L ratio from 1:10 to 1:100 g mL-1, respectively. Dy showed maximum effectiveness from the S/L ratio of 1:50 g.mL-1 which remains almost constant for lower S/L ratios. The leaching of Nd was significantly affected by the variation of the S/L ratio. Nd leaching increased from 20.1% ± 1.38% at 1:10 g.mL-1 to 70.4% ± 2.10% at 1:100 g.mL-1. Varying the S/L ratio from 1:10 to 1:60 g mL-1 did not affect the Fe leaching efficiency (∼1%). However, the S/L ratio had a considerable effect on the Fe leaching efficiency from a ratio of 1:60 g.mL-1. Iron was leached at 2.3% ± 1.8% at 1: 60 g.mL-1 and at 18.1% ± 2.69% at 1: 100 g.mL-1.
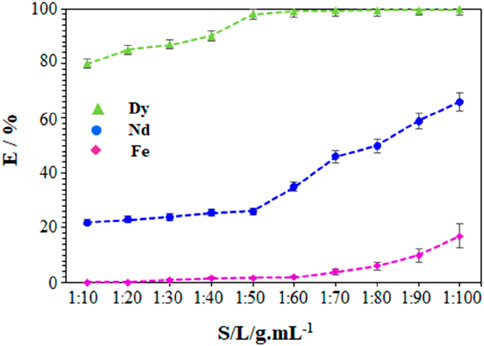
Figure 5. Dependence of the amount of leached metals versus the S/L ratio at 25°C ± 1°C, using a composition of 21% AcOEt, 39% NaSal and 40% H2O, with stirring at 800 rpm for 5 h.
Many studies have shown that decreasing the S/L ratio increases leaching efficiency, because there is more liquid to dissolve the metals in the solid (Behera and Parhi, 2016; Onal et al., 2020). The results obtained correlate with this. The dissolution of Dy can reach up to 99.7% for the S/L ratio of 1: 100 g mL-1. The results obtained for the leaching of Dy show the ability to achieve excellent dissolution levels with a ternary mixture based on hydrotropes, usually observed only upon leaching with strong inorganic acids. However, the reduction in the S/L ratio leads to a significant reduction in the selectivity of Dy relative to Nd as well as relative to Fe. Considering a balance between leaching efficiency and separation factor (SDy/Nd and SDy/Fe), an S/L ratio of 1:50 g.mL-1 is an optimum for the design of new selective leaching process.
3.4 Leaching kinetics
Leaching tests were carried out as a function of time varying from 1 h to 30 h using the leaching solution with the optimal composition (i.e., 21% AcOEt, 39% NaSal and 40% H2O) at 25°C ± 1 °C. The stirring rate was kept constant at 800 rpm, and the S/L ratio was set at 1:50 g mL-1. Each point on the kinetic curve representing the percentage of REE or Fe is represented as the average of the three replicas of an experiment. Figure 6 shows the variation in leaching yield of Nd, Pr, Dy and Fe as a function of leaching time.
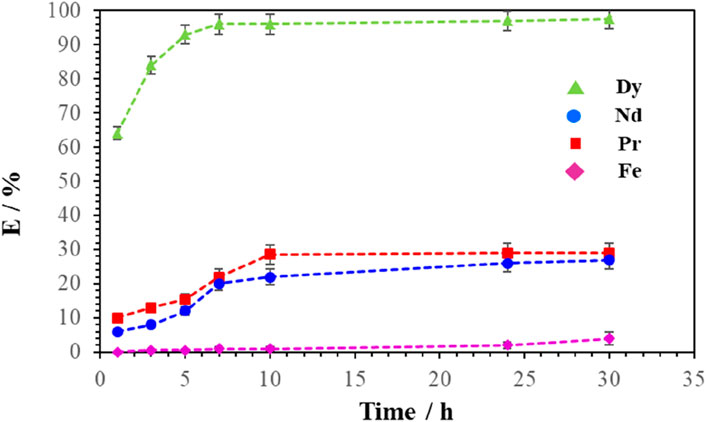
Figure 6. Effect of leaching time on the leaching efficiency of Nd, Pr, Dy and Fe. The temperature was maintained at 25°C ± 1°C, magnetic stirring at 800 rpm, and the S/L ratio at 1: 50 (g.mL-1).
As shown in Figure 6, the leaching of Dy in the ternary leaching solution was rapid compared to that of Nd, Pr and Fe. Indeed, the leaching yield of Dy reached 94% after 5 h while the leaching yield light REEs (Nd and Pr) did not exceed 15%. The yield of light REEs then continued to increase slowly to reach a level of approximately 25% after 24 h. This difference in leaching kinetics accentuated the interest in the selective leaching of Dy compared to Nd, Pr and Fe obtained with ternary solutions of water, ethyl acetate and sodium salicylate. The selective recovery of Dy relative to Nd, Pr and Fe was maximum after 3–5 h. The optimal time to selectively recover Dy from Nd, Pr and Fe was therefore around 5 h. These tests showed that the Fe remained almost insoluble despite the increase in the treatment time to 30 h. The residue obtained after leaching in the ternary solution was enriched in Nd, Pr and Fe. This residue could therefore be leached for a second time under conditions favoring the leaching of Nd and Pr in order to selectively extract Nd and Pr with respect to Fe.
Supplementary Figure S2 in presents the results of the leaching kinetics of NdFeB powder using the inorganic acids studied (i.e., HNO3, H2SO4 and HCl) at 2 mol.L-1. Unlike the ternary leaching system, leaching time did not play a significant role in the leaching process with these inorganic acids, since most REEs were completely leached after 1 h and reached a leaching efficiency of over 90% after 2 h. In addition to REEs, other elements in the NdFeB magnet were also leached using all the mentioned acids and without any selectivity.
3.5 Temperature effect
In order to determine the effect of temperature, tests were carried out between 10°C and 80°C. The composition of the ternary mixture was maintained at 21% AcOEt, 39% NaSal and 40% H2O and the S/L ratio at 1:50 g.mL-1. Figure 7 represents the leaching yields as a function of leaching time for four temperatures (20, 40, 60°C and 70°C) and for leaching times ranging from 1 h to 30 h. For a leaching time equal to 24 h, Figure 7 shows that increasing the temperature from 20°C to 40°C leads to a significant increase in the leaching efficiency, especially for neodymium (Figure 7A). An efficiency gain of around 60% was observed in the case of Nd at 40°C compared to 20°C. Metal leaching reactions are largely endothermic and therefore, they are favoured by higher temperatures that shift the equilibrium in favour of dissolution (Behera and Parhi, 2016; Yoon et al., 2014). The downside is that all elements (Nd, Pr, Dy, Fe and Co.) follow this trend, so the dissolution rates of Fe and other unwanted elements also increased with temperature. In the case of dysprosium, very little change was observed since the conditions already allowed leaching greater than 90% at room temperature.
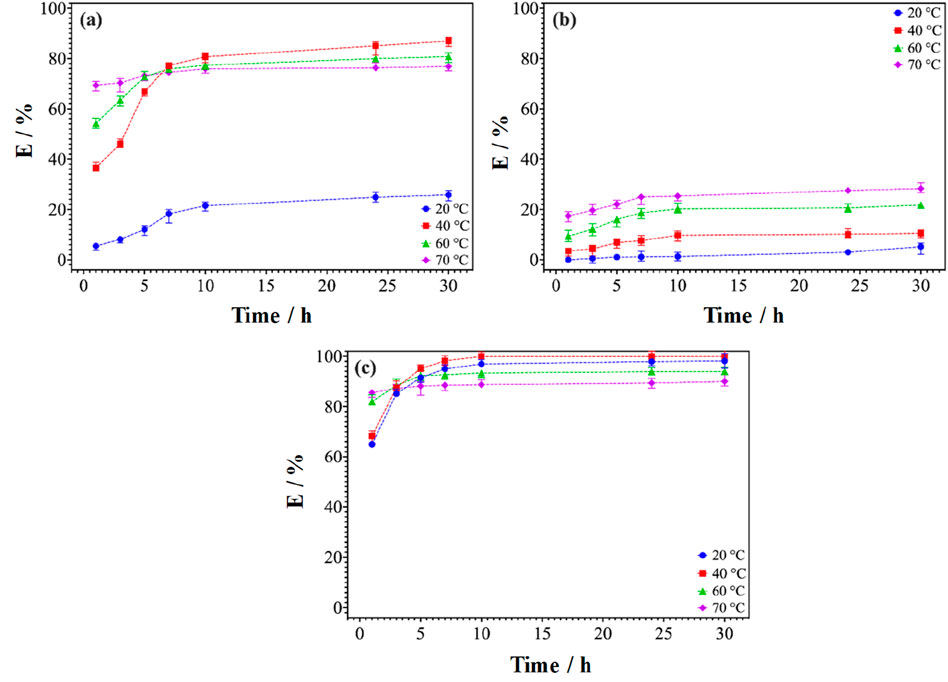
Figure 7. Leaching kinetics of (A) Nd, (B) Fe and (C) Dy at different temperatures. The S/L ratio is 1:50 (g.mL-1), the stirring speed was 800 rpm.
Unlike Nd and Fe, where increasing the temperature from 20°C to 40°C resulted in an increase in leaching efficiency. The other elements (Co. and B) were not leached quantitatively. The greatest increase in efficiency was observed for Nd, where the leaching efficiency increased from 25% at room temperature to 83% at 40°C ± 1°C. By further increasing the temperature from 40°C to 70°C, an opposite trend was observed, since the efficiency decreased significantly with increasing temperature. This phenomenon could be explained by the disappearance of CPN aggregates, responsible for the efficiency of dissolution in this region of the phase diagram (Figure 1).
In order to verify this, SWAXS experiments were performed for the CPN sample at different temperatures. Indeed, as shown in Figure 8, the characteristic peak of CPN aggregates located at q = 2.5 nm-1 at 20°C disappears by increasing the temperature from 20°C to 70°C. This disappearance of structuring at elevated temperatures is likely due to the low boiling point of ethyl acetate at which solvent structuration fades out. With this destructuration and loss of volume, the leaching power of the solution decreases and leaching is less effective.
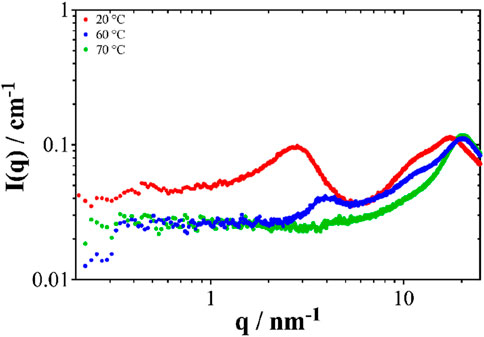
Figure 8. SWAXS spectra at different temperatures of the sample with the following composition: 21% EA, 39% NaSal and 40% water. The aggregates disappear at high temperature.
Although leaching efficiency was optimal at 40°C, the selectivity between Dy and Nd decreased drastically with increasing temperature (see Supplementary Figure S3). Praseodymium has a similar behaviour to Nd. For these reasons, a temperature of 20°C will be maintained for the selective recovery of Dy with respect to Nd, Pr and Fe, while for the recovery of Didymium (Nd and Pr), a temperature of 40°C will be preferred. Furthermore, it should be noted that Fe remained almost insoluble under these leaching conditions, regardless of the temperature used.
3.6 Recovery of REE by selective precipitation from the ternary leach solution
After leaching with the H2O/NaSal/AcOEt formulation, the corresponding leachate must be re-extracted. Because the starting materials in the manufacturing of NdFeB magnets are REE oxides, so the final product of the recycling loop should also be REE oxides. Oxalic acid (C2H2O4) is used for the precipitation of REEs in most processes, because it forms very stable complexes with them that are insoluble in water. These complexes have very low solubility constants (4.51032 < Ks < 5.1030) (Chung et al., 1998), which makes it possible to obtain pure oxides after combustion. Precipitation in the form of hydroxide is another opportunity which can nevertheless be considered. However, we did not study it in our case due to the presence of organic substances (sodium salicylate and ethyl acetate) in the leaching solution (Couillard and Mercier, 1992; Barbaroux et al., 2011). The use of the H2O/NaSal/AcOEt ternary solution as a leaching agent induces an increase in the organic matter content in the leaching solution. However, no information was available in the literature on the behavior of REEs precipitation by oxalic acid in the presence of high NaSal and AcOEt contents. The aim of this study was to explore the influence of NaSal and AcOEt on the precipitation of REEs by oxalic acid. For this, preliminary precipitation experiments were carried out on ternary leaching solutions in a synthetic medium. Metal speciation has been modified by the addition of oxalic acid to a solution containing rare earths and NaSal. In this environment, at least three competing reactions could occur: the complexation reaction of REEs with NaSal, the deprotonation reaction of oxalic acid and finally the precipitation reaction of REE oxalates. As the complexes formed by NaSal and REEs in the H2O/NaSal/AcOEt ternary were not studied in this work, we did not have information on speciation in this environment. However, to promote precipitation, the REE3+ and Ox2- form (i.e., C2O42-) is preferred to form the (Ox)3(REE)2 precipitate which means that conditions where the pH values are fixed between 4.2 and eight is preferred. To test the feasibility of precipitation from the ternary leaching solution, synthetic ternary solutions of H2O/NaSal/AcOEt (H2O: 40%, NaSal: 39% and AcOEt: 21%) containing laboratory grade neodymium (representative element of NdFeB magnets) at a concentration of 10 mmol.L-1 were prepared. A pH adjustment is carried out with a 1 mol.L-1 nitric acid solution. Then, oxalic acid in stoichiometry with NaSal was added to the solution at different pH values ranging from two to 7.
The mixtures were stirred for 2 h, at 800 rpm and at room temperature. Then, they were centrifuged and the neodymium content remaining in the ternary solution is measured by XRF before and after precipitation. The precipitation percentage (% P) of neodymium was calculated according to the following formula 3:
Where [Nd]initial and [Nd]final are, respectively, the initial and final concentration of neodymium in the ternary solution before and after precipitation.
Figure 9 shows the precipitation yield (% P) of neodymium as a function of the pH of the solution. Total precipitation of neodymium in the form of oxalates was obtained at a pH range from two to 4 (% p = 99%). At pH > 4, a significant decrease in the precipitation yield was observed. This result could be attributed to the complex of neodymium with the salicylate Ndx(Sal)y, which probably became predominant. It should be noted that the amount of excess oxalic acid relative to neodymium greatly influenced the stability of the Nd oxalate precipitate. The higher this excess, the more the precipitate appeared at higher pH and the greater the precipitation yield. To conclude, the precipitation of neodymium in the form of oxalates was possible at pH values below 4, despite the presence of organic molecules in the solution resulting from the initial leaching.
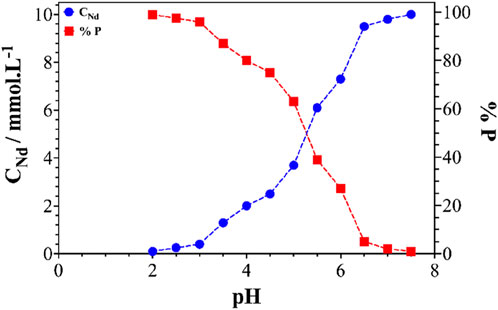
Figure 9. Concentration of neodymium in the solution after precipitation (●) and percentage precipitation of neodymium (■), as a function of pH of a solution containing 10 mmol.L-1 neodymium.
The ternary solution generated after precipitation can be reused for further leaching experiments. However, oxalic acid should not remain in this phase, as this would decrease the rare earth leaching percentage due to the formation of rare earth oxalate salts in a leaching experiment. This can only be avoided if the precipitation reaction is complete and no oxalic acid is anymore present in the ternary leaching phase after precipitation. In order to verify this, precipitation experiments at different amounts of oxalic acid were carried out at pH = 3. Figure 10 shows the precipitation yield (%P) as a function of the n(oxalic acid)/n(Nd) ratio. The amount of neodymium precipitated from the H2O/NaSal/AcOEt solution increased linearly toward 100% at an oxalic acid/nNd value of 2.2. This means that a significant amount of oxalic acid dissolved in the solution was still present. This could present an issue in practice for reusing the leaching phase in a new leaching experiment. In our case, no precipitation of sodium oxalate was observed for similar mixtures without metals, proving that the precipitate was pure. The precipitate obtained could be washed with deionized water to remove traces of NaSal and AcOEt. Then, it could be calcined at the temperature necessary to calcine the rare earth oxalates and obtain rare earth oxides (i.e., between 600°C and 1,000°C) (Jha et al., 2016; Chi et al., 2000).
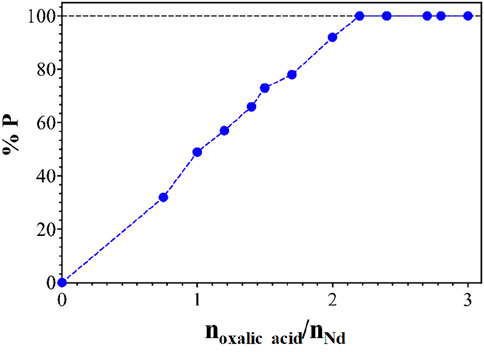
Figure 10. Percentage of precipitation (% P) as a function of the molar ratio of oxalic acid added to the CPN solution containing neodymium. The CPN phase contains 10 mol.L-1 of Nd and in mass fraction: 21% EA, 39% NaSal and 40% water.
3.7 Proposed flowsheet
By integrating the main useful characteristics of the different parts described previously, a new process combining two selective leaches followed by oxalic acid precipitation could be applied to NdFeB magnets, as described in Figure 11. The NdFeB magnet recycling process includes 10 steps (2 × 5 steps). A first series of steps makes it possible to separate the dysprosium from the light rare earths (Nd and Pr) and iron where the solid powder of the NdFeB magnet is leached (step A) for 3 h at 20°C with stirring at 800 rpm and at an S/L ratio of 1:50 g.mL-1, using the leaching solution composed of 21% AcOEt, 39% NaSal and 40% water. The leaching residue is separated from the leachate by filtration (step B). We thus obtain a leachate enriched in Dy, with a mass composition of 43.3% Dy, 39.1% Nd, 12.4% Fe and 5.2% Pr since in these experimental conditions, 88% of Dy, 8% of Pr and Nd and 1% of Fe were dissolved from the initial composition of the magnet powder (Table 1). Unfortunately, approximately 10% of the leach solution was lost in this process due to liquid absorption into the filter pores and into the leach residue. Specialized equipment, such as a full bowl centrifuge, can significantly reduce these losses. Then the leachate can be precipitated (step C) in the form of oxalates by adding oxalic acid, after adjusting the pH of the solution to pH = 3. The precipitation is carried out at 20°C with constant stirring. It is best to avoid adding excess oxalic acid in this step to avoid precipitation of rare earths in the following leaching step. After filtration of the solution resulting from the precipitation step (step D), the oxalates are then calcined (step E) to recover a dysprosium enriched oxide at the end of the process. Assuming that all the elements present precipitate as oxalate, two further sequences of dissolution/filtration/precipitation of the oxides obtained after calcination would yield dysprosium at 99.4% purity, with an overall mass yield of around 68%. The ternary solution can be reused as a leaching solution for new NdFeB oxide powder. In this way, rare earth losses in the precipitation stage are also avoided because the remaining rare earths are reinjected into the process feed.
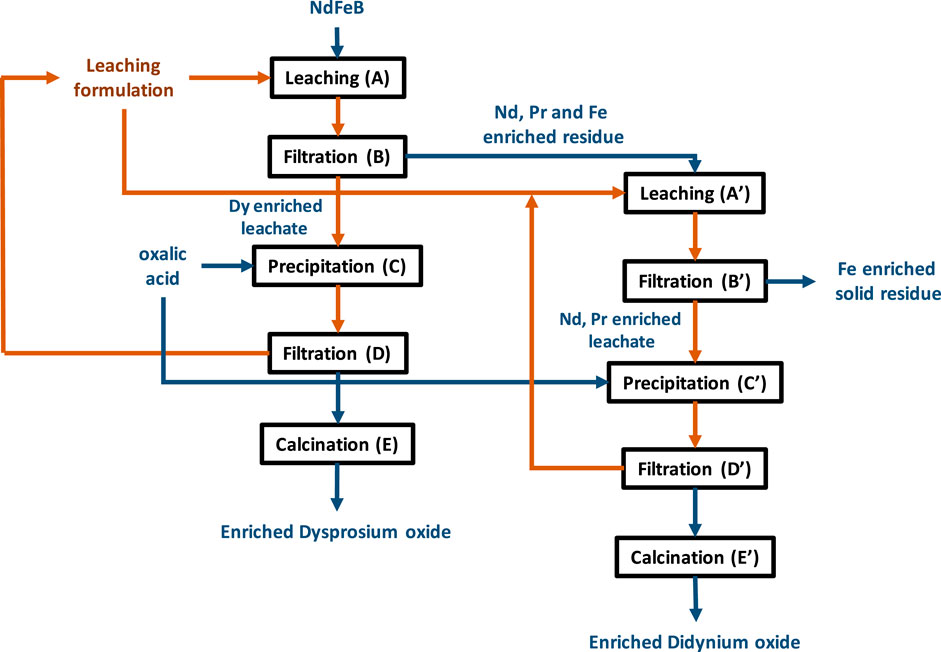
Figure 11. Schematic of the proposed process for the recycling of NdFeB permanent magnets by selective leaching. Blue arrows: solid flows. Brown arrows: liquid flows.
The second series of steps makes it possible to separate the Nd and Pr from the Fe. The solid residue from the first step (step B) of the process is leached (step A′) in the ternary leaching solution for 5 h, at a temperature of 40°C at an S/L ratio of 1:50 g.mL-1. At the end of the filtration step (step B′), a leachate enriched in Nd and Pr is obtained of a mass composition of 71.8% Nd, 17.4% Fe, 9.6% Pr and 1.2% Dy. The didymium is then precipitated (step C′) using oxalic acid and using the same operating conditions as step C. After filtration (step D′), the didymium oxalates are then calcined (step E′) to obtain enriched didymium oxide. The solid residue from this second selective leaching mainly contains Fe in the form of Fe2O3, which can be used in the production of pigments, for example.
4 Conclusion
The recovery of rare earths from end-of-life materials is beneficial both economically and environmentally. However, the overall recovery rate is low due to the lack of an efficient and clean recovery method. The state-of-the-art recovery process, based on hydrometallurgical methods such as liquid-liquid extraction, is a heavy burden on the environment. In addition to the emission of volatile solvents and residual gases such as ammonia, the inorganic acids adopted in full leaching and liquid-liquid extraction procedures contribute significantly to ozone depletion, human toxicity potential, marine aquatic ecotoxicity potential, eutrophication, greenhouse gas emissions and material costs of the total hydrometallurgical process (Zaimes et al., 2015; Iannicelli-Zubiani et al., 2017; Norgate and Jahanshahi, 2011). The method we proposed to test in this work consisted in replacing the acids classically used in NdFeB magnet leaching processes by more eco-friendly formulations, such as hydrotrope-based formulations (Kunz et al., 2016; Gaikar and Sharma, 1986), which on the one hand enable selective leaching (Yoon et al., 2015; Binnemans and Jones, 2017) and on the other hand dispense with the subsequent liquid/liquid extraction steps. As the target metals are selectively dissolved from the solid materials, the liquid-liquid extraction procedure is not necessary, paving the way for compact and more eco-compatible processes, drastically reducing the significant secondary chemical waste (Bandara et al., 2016; Dupont and Binnemans, 2015). Ternary systems comprising a short-chain amphiphilic molecule called a “hydrotrope” and two immiscible fluids are considered powerful solubilization media avoiding the use of conventional surfactants (Klossek et al., 2012; Fischer et al., 2015; Schöttl et al., 2014). In this study, we consider the ternary mixture of water, sodium salicylate (NaSal) and an eco-compatible diluent, ethyl acetate (AcOEt), as a solubilization system. NaSal is a widely used electrolyte as a solubilizing agent in the pharmaceutical (Revathi et al., 2010; Nidhi et al., 2011; Maheshwari, 2006; Maheshwari et al., 2008; Hersey and Jackson, 1987) and personal care (Merinville et al., 2010; Elewa and Zouboulis, 2014) industries, notably for solubilizing hydrophobic dyes, flavors, fragrances or active molecules in water. For use in hydrometallurgy, (NaSal) offers a number of advantages, including its ability to complex rare earths and its non-toxicity. AcOEt is a biobased “green” solvent with a boiling point of 77°C, a flash point of 4°C and a partial vapour pressure of 10 kPa at room temperature. It is used as an effective solvent for phenols (Salagoïty-Auguste and Bertrand, 1984; Bonilla et al., 1999) and also used in the pharmaceutical industry as a non-toxic solvent (Young et al., 1979).
Finally, the compatibility of oxalic acid with the ternary mixture NaSal/H2O/AcOEt enables the sequential precipitation of rare earths present in the leaching medium, which can then be recycled. This may open up a completely new general avenue for reducing toxic effluents in hydrometallurgy and recycling.
Data availability statement
The raw data supporting the conclusions of this article will be made available by the authors, without undue reservation.
Author contributions
AE: Writing–original draft, Conceptualization, Data curation, Formal Analysis, Investigation, Software. CF: Data curation, Investigation, Software, Visualization, Writing–original draft. SP-R: Conceptualization, Supervision, Validation, Writing–original draft, Writing–review and editing. TZ: Conceptualization, Funding acquisition, Project administration, Supervision, Validation, Writing–original draft.
Funding
The author(s) declare that financial support was received for the research, authorship, and/or publication of this article. The author(s) declare that financial support was received for the research, authorship, and publication from the CNRS through the international Research Project “NISI” program, the European project ERC-32915 “REE-CYCLE” 2013-2018 and the Agence Nationale de la Recherche under the France 2030 program, reference “ANR-22-PERE-0003”.
Conflict of interest
The authors declare that the research was conducted in the absence of any commercial or financial relationships that could be construed as a potential conflict of interest.
Publisher’s note
All claims expressed in this article are solely those of the authors and do not necessarily represent those of their affiliated organizations, or those of the publisher, the editors and the reviewers. Any product that may be evaluated in this article, or claim that may be made by its manufacturer, is not guaranteed or endorsed by the publisher.
Supplementary material
The Supplementary Material for this article can be found online at: https://www.frontiersin.org/articles/10.3389/fceng.2024.1420008/full#supplementary-material
References
Bandara, H. M. D., Field, K. D., and Emmert, M. H. (2016). Rare earth recovery from end-of-life motors employing green chemistry design principles. Green Chem. 18, 753–759. doi:10.1039/C5GC01255D
Barbaroux, R., Mercier, G., Blais, J. F., Morel, J. L., and Simonnot, M. O. (2011). A new method for obtaining nickel metal from the hyperaccumulator plant Alyssum murale. Sep. Purif. Technol. 83, 57–65. doi:10.1016/j.seppur.2011.09.009
Behera, S. S., and Parhi, P. K. (2016). Leaching kinetics study of neodymium from the scrap magnet using acetic acid. Sep. Purif. Technol. 160, 59–66. doi:10.1016/j.seppur.2016.01.014
Binnemans, K., and Jones, P. T. (2017). Solvometallurgy: an emerging branch of extractive metallurgy. J. Sustain. Metal. 3, 570–600. doi:10.1007/s40831-017-0128-2
Binnemans, K., Jones, P. T., Blanpain, B., Van Gerven, T., Yang, Y., Walton, A., et al. (2013). Recycling of rare earths: a critical review. J. Clean. Prod. 51, 1–22. doi:10.1016/j.jclepro.2012.12.037
Bonilla, F., Mayen, M., Merida, J., and Medina, M. (1999). Extraction of phenolic compounds from red grape marc for use as food lipid antioxidants. Food Chem. 66, 209–215. doi:10.1016/S0308-8146(99)00046-1
Borra, C. R., Pontikes, Y., Binnemans, K., and Van Gerven, T. (2015). Leaching of rare earths from bauxite residue (red mud). Min. Eng. 76, 20–27. doi:10.1016/j.mineng.2015.01.005
Buschow, K. H. J. (1994). Trends in rare earth permanent magnets. Ieee. Trans. Magn. 30, 565–570. doi:10.1109/20.312337
Chi, R., Zhu, G., Zhou, Z., and Xu, Z. (2000). A novel process for recovering rare earth from weathered black earth. Metal. Mater. Trans. B 31, 191–196. doi:10.1007/s11663-000-0144-6
Chung, D. Y., Kim, E. H., Lee, E. H., and Yoo, J. H. (1998). Solubility of rare earth oxalate in oxalic and nitric acid media. J. Ind. Eng. Chem. 4, 277–284.
Chung, H., Stopic, S., Emil-Kaya, E., Gürmen, S., and Friedrich, B. (2022). Recovery of rare earth elements from spent NdFeB-magnets: separation of iron through reductive smelting of the oxidized material (second part). Metals. 12 (10), 1615. doi:10.3390/met12101615
Couillard, D., and Mercier, G. (1992). Precipitations selectives des metaux solubilises biologiquement de boues aerobies d’epuration. Can. J. Chem. Eng. 70, 1021–1029. doi:10.1002/cjce.5450700526
Croat, J. J., Herbst, J. F., Lee, R. W., and Pinkerton, F. E. (1984). High-energy product Nd-Fe-B permanent magnets. Appl. Phys. Lett. 44, 148–149. doi:10.1063/1.94584
Dupont, D., and Binnemans, K. (2015). Rare-earth recycling using a functionalized ionic liquid for the selective dissolution and revalorization of Y 2 O 3:Eu 3+ from lamp phosphor waste. Green Chem. 17, 856–868. doi:10.1039/C4GC02107J
Elewa, R., and Zouboulis, C. C. (2014). Molecular mechanisms of action of topical antiaging compounds. J. Egyp. Women’s Derm. Soc. 11 (2), 73–78. doi:10.1097/01.EWX.0000446076.96563.ab
El Maangar, A., Degot, P., Huber, V., Causse, J., Berthault, P., Touraud, D., et al. (2020). Pre-nucleation cluster formation upon ethyl acetate addition to an aqueous solution of an anionic hydrotrope. J. Mol. Liq. 310, 113240. doi:10.1016/j.molliq.2020.113240
Emil-Kaya, E., Polat, B., Stopic, S., Gürmen, S., and Friedrich, B. (2023). Recycling of NdFeB magnets employing oxidation, selective leaching, and iron precipitation in an autoclave. RSC Adv. 13 (2), 1320–1332. doi:10.1039/d2ra06883d
Emil-Kaya, E., Stopic, S., Gürmen, S., and Friedrich, B. (2022). Production of rare earth element oxide powders by solution combustion: a new approach for recycling of NdFeB magnets. RSC Adv. 12 (48), 31478–31488. doi:10.1039/d2ra05876f
Filippas, A., Sempros, G., and Sarafidis, C. (2021). Critical rare earths: the future of Nd and Dy and prospects of end-of-life product recycling. Mater. Today Proc. 37, 4058–4063. doi:10.1016/j.matpr.2020.09.210
Fischer, V., Marcus, J., Touraud, D., Diat, O., and Kunz, W. (2015). Toward surfactant-free and water-free microemulsions. J. Colloid Interface Sci. 453, 186–193. doi:10.1016/j.jcis.2015.04.069
Gaikar, V. G., and Sharma, M. M. (1986). Extractive separation with hydrotropes. Solv. Extr. Ion. Exch. 4, 839–846. doi:10.1080/07366298608917896
Gergoric, M., Ekberg, C., Foreman, M. R. S. J., Steenari, B.-M., and Retegan, T. (2017). Characterization and leaching of neodymium magnet waste and solvent extraction of the rare-earth elements using TODGA. J. Sustain. Metal. 3, 638–645. doi:10.1007/s40831-017-0122-8
Gergoric, M., Ravaux, C., Steenari, B.-M., Espegren, F., and Retegan, T. (2018). Leaching and recovery of rare-earth elements from neodymium magnet waste using organic acids. Metals. 8, 721. doi:10.3390/met8090721
Gutfleisch, O., Willard, M. A., Bruck, E., Chen, C. H., Sankar, S. G., and Liu, J. P. (2011). Magnetic materials and devices for the 21st century: stronger, lighter, and more energy efficient. Adv. Mater. 23 (7), 821–842. doi:10.1002/adma.201002180
Hersey, S. J., and Jackson, R. T. (1987). Effect of bile salts on nasal permeability in vitro. J. Pharm. Sci. 76, 876–879. doi:10.1002/jps.2600761206
Habibzadeh, A., Kucuker, M. A., and Gökelma, M. (2023). Review on the parameters of recycling NdFeB Magnets via a hydrogenation Process. ACS Omega. 8, 17431–17445. doi:10.1021/acsomega.3c00299
Iannicelli-Zubiani, E. M., Giani, M. I., Recanati, F., Dotelli, G., Puricelli, S., and Cristiani, C. (2017). Environmental impacts of a hydrometallurgical process for electronic waste treatment: a life cycle assessment case study. J. Clean. Prod. 140, 1204–1216. doi:10.1016/j.jclepro.2016.10.040
Itoh, M., Miura, K., and Machida, K. (2007). A novel process of resource recovery from rare earth magnet scrap using carbonylation reaction and recycle as electromagnetic wave absorber. J. Ceram. Soc. Jpn. 115, 628–632. doi:10.2109/jcersj2.115.628
Itoh, M., Miura, K., and Machida, K. (2009). Novel rare earth recovery process on Nd–Fe–B magnet scrap by selective chlorination using NH4Cl. J. Alloys Compd. 477 (1-2), 484–487. doi:10.1016/j.jallcom.2008.10.036
Jha, M. K., Kumari, A., Panda, R., Kumar, J. R., Yoo, K., and Lee, J. Y. (2016). Review on hydrometallurgical recovery of rare earth metals. earth Met. Hydrometall. 165, 2–26. doi:10.1016/j.hydromet.2016.01.035
Klossek, M. L., Touraud, D., Zemb, T., and Kunz, W. (2012). Structure and solubility in surfactant-free microemulsions. ChemPhysChem 13, 4116–4119. doi:10.1002/cphc.201200667
Kucuker, M. A., Wieczorek, N., Kuchta, K., and Copty, N. K. (2017). Biosorption of neodymium on Chlorella vulgaris in aqueous solution obtained from hard disk drive magnets. PLoS One 12 (4), e0175255. doi:10.1371/journal.pone.0175255
Kumari, A., and Sahu, S. K. (2023). A comprehensive review on recycling of critical raw materials from spent neodymium iron boron (NdFeB) magnet. Sep. Pur. Technol. 317, 123527. doi:10.1016/j.seppur.2023.123527
Kunz, W., Holmberg, K., and Zemb, T. (2016). Hydrotropes. Curr. Opin. Colloid and Interface Sci. 22, 99–107. doi:10.1016/j.cocis.2016.03.005
Lee, C.-H., Chen, Y.-J., Liao, C.-H., Popuri, S. R., Tsai, S.-L., and Hung, C.-E. (2013). Selective leaching process for neodymium recovery from scrap Nd-Fe-B magnet. Metal. Mat. Trans. A 44, 5825–5833. doi:10.1007/s11661-013-1924-3
Li, Q., Yang, X., Zhang, L., Wang, J., and Chen, B. (2009). Corrosion resistance and mechanical properties of pulse electrodeposited Ni–TiO2 composite coating for sintered NdFeB magnet. J. Alloys Compd. 482 (1-2), 339–344. doi:10.1016/j.jallcom.2009.04.014
Lyman, J. W., and Palmer, G. R. (1993). Recycling of rare earths and iron from NdFeB magnet scrap. High. Temp. Mater. Process. 11, 175–188. doi:10.1515/HTMP.1993.11.1-4.175
Maheshwari, R. K. (2006). A novel application of hydrotropic solubilization in the analysis of bulk samples of ketoprofen and salicylic acid. Asian J. Chem. 18, 393–396.
Maheshwari, R. K., Chavada, V., Varghese, S., and Shahoo, K. (2008). Analysis of bulk sample of salicylic acid by application of hydrotropic solubilization method. Indian J. Pharm. Sci. 70, 823–825. doi:10.4103/0250-474X.49135
Merinville, E., Byrne, A. J., Rawlings, A. V., Muggleton, A. J., and Laloeuf, A. C. (2010). Original Contribution: three clinical studies showing the anti-aging benefits of sodium salicylate in human skin. J. Cosmet. Dermatol. 9, 174–184. doi:10.1111/j.1473-2165.2010.00506.x
Miura, K., Itoh, M., and Machida, K.-I. (2008). Extraction and recovery characteristics of Fe element from Nd–Fe–B sintered magnet powder scrap by carbonylation. J. Alloys Compd. 466 (1-2), 228–232. doi:10.1016/j.jallcom.2007.11.013
Mochizuki, Y., Tsubouchi, N., and Sugawara, K. (2013). Selective recovery of rare earth elements from Dy containing NdFeB magnets by chlorination. ACS Sustain. Chem. Eng. 1, 655–662. doi:10.1021/sc4000187
Murase, K., Machida, K., and Adachi, G. (1995). Recovery of rare metals from scrap of rare earth intermetallic material by chemical vapour transport. J. Alloys Compd. 217 (2), 218–225. doi:10.1016/0925-8388(94)01316-A
Nidhi, K., Indrajeet, S., Khushboo, M., Gauri, K., and Sen, D. J. (2011). Hydrotropy: a promising tool for solubility enhancement: a review. IJDDR. 3, 26–33.
Norgate, T., and Jahanshahi, S. (2011). Assessing the energy and greenhouse gas footprints of nickel laterite processing. Miner. Eng. 24, 698–707. doi:10.1016/j.mineng.2010.10.002
Okabe, T. H., Takeda, O., Fukuda, K., and Umetsu, Y. (2003). Direct extraction and recovery of neodymium metal from magnet scrap. Mater. Trans. 44 (4), 798–801. doi:10.2320/matertrans.44.798
Onal, M. A. R., Aktan, E., Borra, C. R., Blanpain, B., Van Gerven, T., and Guo, M. (2017). Recycling of NdFeB magnets using nitration, calcination and water leaching for REE recovery. Hydrometallurgy. 167, 115–123. doi:10.1016/j.hydromet.2016.11.006
Onal, M. A. R., Dewilde, S., Degri, M., Pickering, L., Saje, B., Riano, S., et al. (2020). Recycling of bonded NdFeB permanent magnets using ionic liquids. Green Chem. 22, 2821–2830. doi:10.1039/D0GC00647E
Parhi, P. K., Sethy, T. R., Rout, P. C., and Sarangi, K. (2016). Separation and recovery of neodymium and praseodymium from permanent magnet scrap through the hydrometallurgical route. Sep. Sci. Technol. 51, 2232–2241. doi:10.1080/01496395.2016.1200087
Polyakov, E. G., and Sibilev, A. S. (2015). Recycling rare-earth-metal wastes by pyrometallurgical methods. Metallurgist. 59 (5), 368–373. doi:10.1007/s11015-015-0111-8
Rabatho, J. P., Tongamp, W., Takasaki, Y., Haga, K., and Shibayama, A. (2013). Recovery of Nd and Dy from rare earth magnetic waste sludge by hydrometallurgical process. J. Mater. Cycles Waste Manag. 15, 171–178. doi:10.1007/s10163-012-0105-6
Revathi, R., Ethiraj, T., Saravanan, V. S., Ganeshan, V., Saranya, V., and Sengottuvel, T. (2010). New spectroscopic determination of nifedipine using hydrotropic solubilization. Int. J. Pharm. Pharm. Sci. 2, 74–76.
Riano, S., and Binnemans, K. (2015). Extraction and separation of neodymium and dysprosium from used NdFeB magnets: an application of ionic liquids in solvent extraction towards the recycling of magnets. Green Chem. 17, 2931–2942. doi:10.1039/C5GC00230C
Saito, T., Sato, H., Ozawa, S., Yu, J., and Motegi, T. (2003). The extraction of Nd from waste Nd–Fe–B alloys by the glass slag method. J. Alloys Compd. 353, 189–193. doi:10.1016/S0925-8388(02)01202-1
Salagoïty-Auguste, M.-H., and Bertrand, A. (1984). Wine phenolics—analysis of low molecular weight components by high performance liquid chromatography. J. Sci. Food Agric. 35, 1241–1247. doi:10.1002/jsfa.2740351116
Schöttl, S., Marcus, J., Diat, O., Touraud, D., Kunz, W., Zemb, T., et al. (2014). Emergence of surfactant-free micelles from ternary solutions. Chem. Sci. 5, 2949–2954. doi:10.1039/C4SC00153B
Špadina, M., Dourdain, S., Rey, J., Bohinc, K., Pellet-Rostaing, S., Dufrêche, J.-F., et al. (2022). How acidity rules synergism and antagonism in liquid–liquid extraction by lipophilic extractants—Part II: application of the ienaic modelling. Solvent Extr. Ion. Exch. 40 (1and2), 106–139. doi:10.1080/07366299.2021.1899614
Špadina, M., Dufreche, J.-F., Pellet-Rostaing, S., Marčelja, S., and Zemb, T. (2021). Molecular forces in liquid–liquid extraction. Langmuir. 37 (36), 10637–10656. doi:10.1021/acs.langmuir.1c00673
Stopic, S., Polat, B., Chung, H., Emil-Kaya, E., Smiljani, S., Gürmen, S., et al. (2022). Recovery of rare earth elements through spent NdFeB magnet oxidation (first part). Metals. 12 (9), 1464–1476. doi:10.3390/met12091464
Takeda, O., Okabe, T. H., and Umetsu, Y. (2006). Recovery of neodymium from a mixture of magnet scrap and other scrap. J. Alloys Compd. 408-412, 387–390. doi:10.1016/j.jallcom.2005.04.094
Tunsu, C., Petranikova, M., Gergorić, M., Ekberg, C., and Retegan, T. (2015). Reclaiming rare earth elements from end-of-life products: a review of the perspectives for urban mining using hydrometallurgical unit operations. Hydrometallurgy. 156, 239–258. doi:10.1016/j.hydromet.2015.06.007
Uysal, E., Al, S., Emil-Kaya, E., Stopic, S., Gürmen, S., and Friedrich, B. (2023). Hydrometallurgical recycling of waste NdFeB magnets: design of experiment, optimisation of low concentrations of sulphuric acid leaching and process analysis. Can. Metall. 62, 107–118. doi:10.1080/00084433.2022.2058152
Walton, A., Yi, H., Rowson, N. A., Speight, J. D., Mann, V. S. J., Sheridan, R. S., et al. (2015). The use of hydrogen to separate and recycle neodymium– iron–boron-type magnets from electronic waste. J. Clean. Prod. 104, 236–241. doi:10.1016/j.jclepro.2015.05.033
Wu, Y., Yin, X., Zhang, Q., Wang, W., and Mu, X. (2014). The recycling of rare earths from waste tricolor phosphors in fluorescent lamps: a review of processes and technologies. Resour. Conserv. Recycl. 88, 21–31. doi:10.1016/j.resconrec.2014.04.007
Yang, Y., Walton, A., Sheridan, R., Guth, K., Gauss, R., Gutfleisch, O., et al. (2017). REE recovery from end-of-life NdFeB permanent magnet scrap: a critical review. J. Sustain. Metal. 3, 122–149. doi:10.1007/s40831-016-0090-4
Yoon, H.-S., Kim, C.-J., Chung, K., Jeon, S., Park, I., Yoo, K., et al. (2015). The effect of grinding and roasting conditions on the selective leaching of Nd and Dy from NdFeB magnet scraps. Metals 5, 1306–1314. doi:10.3390/met5031306
Yoon, H.-S., Kim, C.-J., Chung, K. W., Lee, S.-J., Joe, A.-R., Shin, Y.-H., et al. (2014). Leaching kinetics of neodymium in sulfuric acid from E-scrap of NdFeB permanent magnet. Korean J. Chem. Eng. 31, 706–711. doi:10.1007/s11814-013-0259-5
Young, K. H., Bullock, S. L., Melvin, D. M., and Spruill, C. L. (1979). Ethyl acetate as a substitute for diethyl ether in the formalin-ether sedimentation technique. J. Clin. Microbiol. 10 (6), 852–853. doi:10.1128/jcm.10.6.852-853.1979
Zaimes, G. G., Hubler, B. J., Wang, S., and Khanna, V. (2015). Environmental life cycle perspective on rare earth oxide production. ACS Sustain. Chem. Eng. 3, 237–244. doi:10.1021/sc500573b
Zhang, Y., Gu, F., Su, Z., Liu, S., Anderson, C., and Jiang, T. (2020). Hydrometallurgical recovery of rare earth elements from NdFeB permanent magnet scrap: a review. Metals 10 (6), 841–875. doi:10.3390/met10060841
Zhang, Y. D., Budnick, J. I., Potenziani, I. I. E., Pedziwiatr, A. T., Wallace, W. E., and Panissod, P. (1988). An NMR study of tetragonal Nd2Fe14B and Nd2Fe14−xCoxB. J. Appl. Phys. 63 (8), 719–721. doi:10.1063/1.340646
Keywords: leaching, critical fluctuations, sodium salicylate, solubilisation, pre-nucleation clusters, lanthanides, NdFeB, hydrotropes
Citation: El Maangar A, Fleury C, Pellet-Rostaing S and Zemb T (2024) Leaching and recycling of NdFeB permanent magnets using ionic non-toxic hydrotropes instead of extractants. Front. Chem. Eng. 6:1420008. doi: 10.3389/fceng.2024.1420008
Received: 19 April 2024; Accepted: 04 September 2024;
Published: 18 September 2024.
Edited by:
Juan Gabriel Segovia Hernandez, University of Guanajuato, MexicoReviewed by:
Julien Estager, Centre of Technological Resources in Chemistry (CERTECH), BelgiumZeferino Gamino-Arroyo, University of Guanajuato, Mexico
Copyright © 2024 El Maangar, Fleury, Pellet-Rostaing and Zemb. This is an open-access article distributed under the terms of the Creative Commons Attribution License (CC BY). The use, distribution or reproduction in other forums is permitted, provided the original author(s) and the copyright owner(s) are credited and that the original publication in this journal is cited, in accordance with accepted academic practice. No use, distribution or reproduction is permitted which does not comply with these terms.
*Correspondence: Stéphane Pellet-Rostaing, c3RlcGhhbmUucGVsbGV0LXJvc3RhaW5nQGNlYS5mcg==; Thomas Zemb, dGhvbWFzLnplbWJAaWNzbS5mcg==