- 1Department of Civil and Environmental Engineering, Norges teknisk-naturvitenskapelige universitet (NTNU), Trondheim, Norway
- 2Architecture, Materials and Structures, SINTEF Community, Trondheim, Norway
Sufficient airtightness of a building envelope is important both to ensure the overall energy efficiency of a building and to prevent moisture-related damage to the structure. Air leakages typically occur in the context of joints and perforations in vapor barriers installed inside walls and roofs. It is essential to give proper attention to details to achieve sufficient airtightness of building envelopes and joint’s durability. Sealing such building details with durable solutions is essential for ensuring sufficient airtightness overall. In recent years, adhesive tapes have increasingly been used for this application. However, there remains uncertainty regarding its performance in the long-term. The study offers an overview of the current state of the art by incorporating findings from a literature review including an analysis of established methods currently being used for evaluation of tape joint durability, as well as other experimental test methods. The aim of research presented in this paper is to contribute to the development of a test method with sufficient accuracy, reproducibility, and repeatability to be used in the development and certification of tape products and systems. Although the method in development displays limitations in terms of reproducibility, it is regarded as a promising concept. Through further development, the method is believed to be suitable for potential integration into wider evaluation programs addressing adhesive tape durability, supplementary to existing methods.
1 Introduction
1.1 Background
In the face of climate change, the construction industry is facing increasingly stringent energy efficiency requirements. In the EU, buildings were responsible for 40% of the total energy consumption and 36% of greenhouse gas emissions as of 2020 (European Commission, 2020). In Norway, the building stock accounts for around a third of domestic energy consumption and 40% of greenhouse gas emissions (Forskningsradet, 2021).
The European Union (EU) initiated the Energy performance of buildings directive (EPBD) to provide a legislative framework for promoting energy efficiency in buildings. Among its stated goals is to “achieve a highly energy efficient and decarbonized building stock by 2050” (European Commission, 2021). The latest proposal for a revision of the EPBD from 2021 establishes a vision for achieving a zero-emission building stock by 2050. In Norway, technical requirements regarding energy efficiency are defined in the Regulations on technical requirements for construction works, i.e., TEK, with its newest edition TEK17 taking effect in 2017 (Direktoratet for byggkvalitet, 2017). TEK is guided by EPBD in posing stricter requirements to the overall energy efficiency of buildings and emphasizing building airtightness in Norway as shown in Table 1. The purpose of posing requirements for building airtightness is to prevent leakages of cold outdoor air into the building, as well as humid indoor air from leaking into the internal structures of the building envelope. Sufficient airtightness is thus important both to ensure the overall energy efficiency of a building, and to prevent moisture-related damage to the structure, like mold and rot. Air and vapor barriers are installed in walls and roofs of buildings to prevent air from penetrating through the structure. Air leakages typically occur in the context of joints and penetrations in these barriers. It is thus essential to give proper attention to these details, both at the design stage and during construction, to achieve a sufficient airtightness. In recent years, adhesive tapes have become a trendy way of air sealing joints and penetrations in the building envelope. Early on, these tapes had a reputation for having poor adhesive properties and durability. More recently, along with further product development, adhesive tapes have been recognized for their ability to provide adequate airtightness, among others, by Skogstad et al. (2010). The use of tape also allows for innovative solutions, along with a simple and quick application, making it a highly convenient option for air sealing details. However, as adhesive tapes constitute a relatively new way of air sealing a building, there are concerns and uncertainties regarding the long-term durability of products and solutions to be used. Current evaluation methods used for certification of products and systems are primarily based on assessing the mechanical and adhesive properties of products rather than addressing the airtightness directly.
1.2 Existing experimental test methods
Fufa et al. describe a lack of reliable test procedures for tapes used in building applications and express the need for new methods to evaluate the durability of products’ performance (Fufa et al., 2017). Efforts to develop new test procedures for adhesive tapes have resulted in a range of methods, using different layouts, scales, and substrate materials. Some studies combine the evaluation of airtightness with the measuring of the mechanical tapes’ properties such as a peel and shear resistance. The developed experimental methods take different approaches to evaluate the durability of tapes. Most apparent is the difference in how the standardized methods mainly rely on quantifying adhesive properties, while the experimental methods assess airtightness. The methods differ in several ways but also share common features. Table 2 provides an overview comparing some of their aspects.
The methods developed by Antonsson (2017) and Ylmén et al. (2012) simulate building components with realistic dimensions, making the tests and ageing processes highly representative. However, a full scale testing can be cost and time consuming. Issues with reproducibility have also led to questions whether the full-scale methods are assessing the quality of implementation rather than product properties according to Leprince et al. (2017). Studies conducted by Antonsson and Ylmén et al. only involved testing one single specimen of each configuration, making it difficult to conclude on the reproducibility of the two methods. Møller and Rasmussen (2020) and Van Linden and Van den Bossche (2017) were able to test more samples, making it easier to evaluate the reproducibility of their methods. Reduction of scale may, on the other hand, cause the results to be less representative. Nevertheless, both Ylmén et al. and Møller and Rasmussen concluded that there is no clear correlation between airtightness and mechanical properties, such as peel and shear resistance. Despite their differing test-scales, both studies found that the peel and shear resistance tend to improve after accelerated ageing while the airtightness deteriorates. Still, some observations may seem counterintuitive when compared to other studies: while Van Linden and Van den Bossche found that the airtightness of taped joints depended on the substrate, Sletnes and Frank (2020) found that peel and shear resistance varied more between different tapes than between different substrates. Out of the evaluation methods mentioned, Van Linden and Van den Bossche are the only ones addressing airtightness using concrete as a substrate. All the mentioned methods except the one of Van Linden and Van den Bossche (2017) include adhesive tape joints linking two or more varied materials, for instance wood and PE membrane or wood and concrete. Varied materials undergo different dimensional changes in response to varying temperature and moisture content, which might lead to skewed deformation and tension in the tape. This can in turn affect adhesive properties or airtightness, according to Antonsson (2017). Studying this phenomenon in isolation would be relevant to better understand how the airtightness of tape joints evolves in the long-term.
1.3 Motivation
The usefulness and validity of these established evaluation methods may seem to depend on the existence of a direct correlation between the airtightness and adhesion of the tape joints. However, research results have suggested otherwise, as while adhesive properties in many cases remain unchanged or even improved over time, the airtightness is in most cases reduced, according to Møller and Rasmussen (2020). The uncertainty has led research communities to recognize the need for new test methods. The Norwegian institute of applied research (SINTEF) initiated the research project TightEN in 2019 to increase experience and knowledge regarding the airtightness and long-term durability of sealing systems utilizing adhesive tapes (SINTEF, 2019). Research and results presented in this paper focus on evaluating the usefulness of a medium-scale test method for assessing the airtightness of joints sealed with adhesive tapes. The aim is to contribute to the development of test methods with sufficient accuracy, reproducibility, and repeatability to be used in the development and certification of tape products and systems in the future.
With further improvement, the proposed experimental method in development is considered applicable as a means of evaluating the durability of adhesive tapes as part of product development or certification. In the context of separate tape evaluation, the method could potentially constitute a supplementary test to currently established evaluation methods. Durability of tensile strength, peel and shear resistance is regarded as important to ensure the joint can withstand mechanical strains over time. However, a direct assessment of the actual airtightness is deemed beneficial to ensure the products fulfill their purpose of air sealing building envelopes in the long term.
The authors believe that an improved version of this method can achieve satisfactory precision in determining specimen leakage rates by incorporating improvements aimed at minimizing system leakage rates. In terms of durability evaluation criteria, it is considered more suitable to establish absolute threshold values for permeability before and after ageing, in contrast to current guidelines for peel and shear resistance evaluation, in which durability is evaluated based on relative change in material properties after artificial ageing.
2 Theory
This section, divided into three subsections, provides the theoretical background of this study. It starts with definitions of airtightness, Section 2.1, and airtightness in practice, Section 2.2, followed by reviews of the current technical regulations in Norway, Section 2.3.
2.1 Airtightness
Air enters and leaves buildings through ventilation or infiltration. In modern buildings, ventilation is often provided through balanced ventilation with heat recovery which makes the air flow predictable and controllable. Modern ventilation systems also make it possible for heat batteries to reclaim energy from the exhaust air to limit heat losses, according to Thue (2016). Thue defines infiltration as air flowing in and out of a building as a result of leakages in the building envelope. Unlike ventilation, air leakages constitute undesirable and uncontrollable movement of cold outdoor air through openings in the building envelope, for instance, a punctured air barrier can allow cold outdoor air to penetrate into a layer of insulation, subsequently reducing its insulating properties. Chilly air can also penetrate further, into occupied space, causing excessive heat loss and thermal discomfort for building occupants. Likewise, humid indoor air can leak into the insulation through holes in the vapor barrier, entailing risks of condensation and consequentially the formation of mold and rot. Ensuring the building envelope is airtight is thus important to reduce unwanted leakages and consequential excessive heat loss and risk of damage to the structure, according to Blom and Uvsløkk (Blom and Uvsløkk). Infiltration is driven by differences in air pressure,
2.2 Airtightness in practice
An air barrier is normally situated on the exterior of the timber framing and insulation, preventing cold outdoor air from entering the layers of insulation and thus reducing its insulating properties. This layer must be sufficiently airtight to prevent air from penetrating it, but at the same time allow for vapor diffusion so that moisture can dry out. Along with the exterior wall cladding, those diffusion open, yet airtight barriers serve the purpose of preventing rain from entering the wall. The cladding provides weather protection as a rain-tight exterior layer, creating a ventilated and drained cavity between the air barrier and the cladding. Air barriers can be comprised of a range of varied materials, usually in the form of boards or membranes. A vapor barrier is normally installed on the interior side of an internal wall structure with the intent of preventing humid indoor air from entering the thermal insulation where it might condensate as a result of lower temperatures inside the exterior wall construction. Vapor barriers typically consist of polymer sheets, such as polyethylene (PE) foils and are highly vapor resistant, unlike the exterior air barrier, according to Blom and Uvsløkk (Blom and Uvsløkk). Vapor diffusion resistance of barrier products can be quantified through Sd values. The Sd value of a barrier corresponds to the thickness of an air layer required to achieve the equivalent vapor resistance. Vapor barriers must have a relatively high Sd value to prevent moisture from infiltrating the wall structure, while air barriers typically have alower Sd, allowing any moisture inside the structure to escape. This principle is illustrated in Figure 1, according to Geving et al. SINTEF recommends an Sd < 0.5 m for air barriers, and Sd > 10 m for vapor barriers. These limit values are in turn used by SINTEF to define products as air or vapor barriers. PE foils used as vapor barriers today typically have a thickness of 0.15 mm, achieving Sd values of around 70 m.
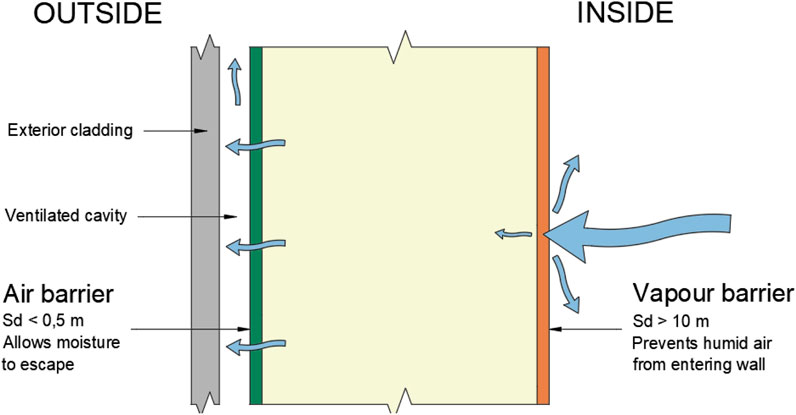
Figure 1. Diffusion in exterior wall construction with recommended Sd values (Geving et al., 2020).
Joints between the separate sheets of a barrier membrane itself are critical, along with penetrations in the building envelope which may be intentional, as for plumbing and electrical works, or accidental, resulting from ruptures occurring during construction or in the operational phase. Manufacturers offer adhesive pipe sleeves for sealing intentional penetrations in air and vapor barriers, according to Blom and Uvsløkk (Blom and Uvsløkk). Figure 2 highlights some of the details of a building envelope in which air leakages typically occur. The figure outlines in red, an imaginary, continuous airtight layer. Sealing critical points is essential to achieve the continuity of the airtight barriers, thus ensuring the overall airtightness of the building. There are several options for sealing joints and connections, such as clamping, sealants and using adhesive tapes.
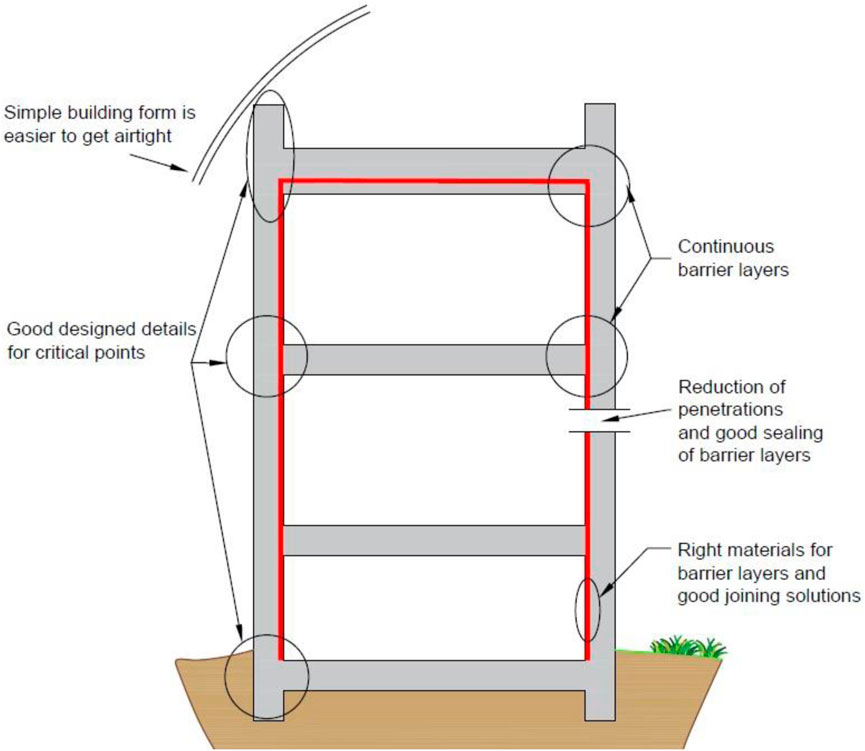
Figure 2. Critical details concerning air leakages in a building envelope (Geving, 2021).
Adhesive tapes can be used as the primary way of sealing and as reinforcement of clamped joints, helping to provide continuity in the barrier layers. Figure 3 illustrates a practical application of adhesive tape on a vapor barrier membrane in walls and a ceiling of a timber frame house. Adhesive tapes can be used to join boards and sheets of membrane together, and to connect these to other building components, such as floors and ceilings, according to Boberach (2022). Rigid boards can be joined by a simple connection, while joining two sheets of membrane requires the sheets to overlap, according to DIN, (2011). This principle is illustrated in Figure 4 which shows a vertical cross section of an exterior wall, where rigid gypsum boards constitute the air barrier, and a PE membrane makes up the vapor barrier.
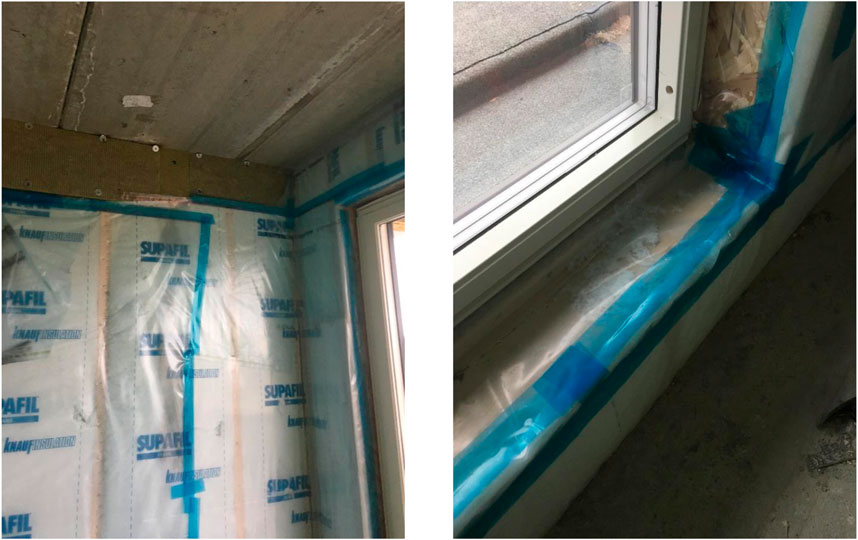
Figure 3. Adhesive tape is used to join sheets of vapor barrier membrane, and to connect the membrane to the timber frame (Photo: Geving S., SINTEF Community).
For the use of tape to be successful, it is important that the products’ performance and durability is accurately assessed and documented. The airtightness of a joint or opening sealed by tape is affected by several different parameters, such as type of substrate, and its resilience to moisture, changes in temperature or relative humidity, exposure to UV radiation, chemical compounds, and dust. These conditions may affect the function of deterioration by causing dimensional change, material fatigue or oxidation. Factors can also combine in ways leading to synergistic effects, accelerating the deterioration of the tape’s airtightness even further, according to Ylmén et al. (2012). It is therefore important that tapes are tested in realistic and relevant conditions, to examine how the products react to different climate conditions, including frost, moisture, heat, and exposure to sun. Previous research also suggests that conditions of installation can have a major impact on the airtightness of tape joints, according to Antonsson (2017).
2.3 Norwegian regulations
Norwegian construction projects must meet the Regulations on technical requirements for construction works, TEK17. This building code determines requirements regarding a building’s overall energy efficiency, including its airtightness through upper limit values concerning the air change rate, n50. The air change rate is herein defined as the volumetric air flow,
All Norwegian building projects, including total renovation, must be built according to the minimum requirements in TEK17. Buildings can be built with an even higher level of energy efficiency than required by TEK17. This can be achieved by designing the building according to the Passive House Standards NS3700 or NS3701, for residential and non-residential buildings respectively (Standard Norge and NS 3700, 2013; Standard Norge and NS 3701, 2012). Table 1 shows the different requirements regarding airtightness that are relevant to the construction of new buildings and total renovation of existing buildings in Norway. From 1 January 2013, the air leakage rates of new buildings are required to be verified by an independent controller in Norway, according to Direktoratet for byggkvalitet (Direktoratet for byggkvalitet, 2012). Verification can be carried out by performing the blower-door test described in the NS-EN ISO 9972:2015 standard, according to SINTEF (Byggforsk, 2014).
3 Material and methods
An experimental method has been under development to evaluate the air permeability and durability of joints sealed with adhesive tapes. The method in development is presented in Section 3.1. The procedure used to collect and analyze data is inspired by NS-EN 12114:2000 (Standard Norge, 2000). The reproducibility, repeatability and accuracy of the method is assessed through a measurement program described in Section 3.2. The program involves measuring the air permeability of specimens from six different material samples. Each test sample consists of a given combination of one adhesive tape and a substrate. Test samples and specimens are described in Section 3.2.2. Specimens are tested before and after artificial ageing to assess whether the test setup is suitable for evaluating the durability of adhesive tapes. The ageing procedures are described in Section 3.4. Parallelly to the air permeability evaluation, the same material samples are tested for peel resistance in accordance with the national standard NS-EN 12316-2:2013 (Standard Norge, 2013b). The peel resistance measurements are conducted on non-aged and artificially aged test specimens, exposed to the same ageing procedure as the corresponding air permeability specimens. The purpose of performing standardized peel resistance measurements of the material samples is to examine how the durability evaluation from the method in development compares to a test method, i.e., NS-EN 12316-2:2013 (Standard Norge, 2013b). Results from the two methods are compared to observe whether there is a correlation between the air permeability and adhesive properties of the materials.
3.1 Air permeability test method
Experiments are conducted using a test rig in the laboratories of SINTEF Community. A schematic drawing of the setup is shown in Figure 5. The setup includes a box-shaped test stand made of welded-together steel plates into which a test specimen is installed, creating an enclosed volume. The test stand is pressurized while measuring the supplied air flow rate using one of three flow meters. Flow meters are enumerated 1, 2, 3, and can measure flow rates within the ranges 0 - 0.4, 0 - 10 and 0–100 L/min, respectively.
3.1.1 Test stand
The test stand consists of a box welded together from three steel plates, 2 mm thick, leaving one side open for mounting test samples. The box is outfitted with 50 mm flanges pointing outwards from said opening. The flanges act as support for the test samples and allow for the fastening of clamps. The test stand is designed with dimensions allowing test samples to fit inside the heat chamber used for artificial ageing at SINTEF Community. A stylized cross section of the assembled test stand with a test sample installed in it is shown in Figure 6, Figure 7.
3.1.2 Data collection
Data collection is conducted in accordance with the test procedure described in NS-EN 12114:2000 (Standard Norge, 2000). The measuring begins with pressurizing the test stand with compressed air through the pressurization rig, creating a positive pressure on its inside. The air flow is regulated manually, until the pressure difference rests at one of several predetermined levels. Pressure steps are determined according to Annex A of NS-EN 12114:2000 (Standard Norge, 2000). 100 Pa is used as the highest pressure difference
This formula gives the following seven pressure steps: 10, 15, 22, 32, 46, 68, 100 Pa. Three pulses of pressurization equal to 110 Pa (10% greater than
The leakage through the sample can be further divided into joint and substrate leakage as shown in Equation 4.
If the substrate is considered airtight, the substrate leakage is neglected. Figure 7 illustrates the diverse types of leakages.
The measured air leakage rates are corrected for reference conditions according to NS-EN 12114:2000 if the following laboratory conditions are not met: 18°C–22°C air temperature, 100–102 KPa atmospheric pressure, 25%–50% relative humidity. The corrected leakage rate
3.1.3 Data processing
The recorded air leakage rate
Further subtracting the substrate leakage results in the leakage through the joints, as shown in Equation 7.
The substrate leakage of a given sample is evaluated by implementing the previously described measurement procedure on an intact piece of the associated substrate, free from cuts and tape joints. The intact substrate is tested before and after artificial ageing, parallelly to the sample with tape joints. PE foil is considered practically airtight, hence
The data sets containing the reference measurements
Workflow for the test procedure is presented in Supplementary Appendix.
3.2 Measurement program
The measurement program is planned out with the intention of assessing the accuracy, reproducibility, and repeatability of the test method, and it includes following actions: 1) the test stand leakage evaluation, 2) the choice of material samples and evaluation, 3) identical parallel specimens’ testing, 4) the repeatability evaluation, and 5) the comparison to peel resistance. 1) The test stand leakage evaluation is performed by installing a sheet of PE foil over the test stand’s opening, before pressurizing the test stand until a steady pressure difference of 100 Pa is achieved. The air flow rate going into the test stand is simultaneously recorded under the assumption that the PE foil is airtight. The recorded flow rate is consequently assumed to be equal to the system leakage. This test procedure is repeated, varying the number of clamps to assess how this affects the system leakage rate. The test starts out using eight clamps (see Figure 8) before the test is repeated using 12 clamps. 2) The material test samples used in these experiments consist of combinations of three commercially available tape products and two different substrates, as shown in Table 4. The tapes chosen for the samples include a universal tape T1 for use in both air and vapor barriers, an air barrier tape T2 and a duct tape T3. Both T1 and T2 have received Technical Approval from SINTEF for their respective areas of use. The duct tape, T3, is developed for sealing applications in HVAC systems (heating, ventilating, air conditioning) and has not received any Technical Approval from SINTEF for use in either air or vapor barrier systems.
Different substrates are chosen to observe how the air permeability of the tapes varies depending on the surface it is adhered to. Some substrates, such as PE foil are practically airtight, making it easier to measure an isolated joint leakage. For substrates that are more air permeable, it is necessary to measure and subtract the leakages going through the substrate itself before obtaining the joint leakage. Both air barrier materials and PE membranes constitute standard substrates in the context of SINTEF Technical Approval and are among the end-use substrates with which adhesive tapes are typically used. Because of this, they were considered the most relevant substrates, along with wood and concrete.
3.3 Peel resistance test
Peel resistance is measured in accordance with the Norwegian national standard NS-EN 12316-2:2013 (Standard Norge, 2013b). The measurements are performed in the laboratories of SINTEF Byggforsk, in line with their accredited test procedure. The tests utilize a Zwick/Roell Z010 Material Tensile Testing Machine, see Figure 9. During the test, the substrate and tape are fastened to the lower and upper grip, respectively.
The upper grip pulls upwards, which results in the tape gradually being peeled off the substrate. The grip moves at a constant speed of 100 mm/min while the peeling force is continually measured and logged by a load cell. The test continues until the joint fails.
When a test is completed, the failure mode is recorded as one of the following: A: Peeling of joint - failure of adhesive. B: Break outside of joint - failure of substrate or tape backing material. C: Delamination of sheet - separation of material layers parallel to the joint. The maximal peel resistance of the specimen is recorded, while a computer automatically calculates its average peel resistance in accordance with NS-EN 12316-2:2013 (Standard Norge, 2013b).
3.4 Ageing procedures
In the context of Technical Approval, test samples can be exposed to different procedures for accelerated ageing depending on a specific product’s area of use. In this study, the artificial ageing procedure varies depending on the substrate material: in a manner inspired by guidelines for vapor barriers where PEF constitutes the substrate and, in a manner, like the guidelines for air barriers where ROM constitutes the substrate, according to the Technical Approval of SINTEF (SINTEF, 2022).
3.4.1 Heat chamber
The material samples which include PEF as substrate are artificially aged in a ventilated heat chamber at 70°C for 6 weeks. The heat chamber warms up the ambient laboratory air, resulting in a relatively low humidity inside the chamber. The air permeability specimens hang vertically inside the heat chamber to prevent the different specimens from interfering with each other during the ageing procedure, while the peel resistance specimens were laid horizontally inside another and identical heat chamber, see Figure 10.
3.4.2 Climate simulator
Accelerated ageing of the ROM samples is performed using the method NT BUILD 495 over the course of 6 weeks, where samples are exposed to UV light, heat, water, and frost to simulate climatic strains (Nordtest, 2000), see Figure 11. NT BUILD 495 is included in the standard procedure for artificial ageing of air barrier tapes and systems during Technical Approval, in which peel and shear resistance samples are exposed to the climate simulator for 2 weeks, followed by 12 weeks of heat ageing (SINTEF, 2022).
4 Results
The following sections present results from the measurement program used to evaluate the suitability of the test method in development.
4.1 Test stand leakage
The test stand leakage evaluation was performed on two different dates: 24.03.2023 and 12.04.2023. On both occasions, the test procedure was performed through two separate measurement series. The first two measurement series were performed prior to testing the material samples, and thus constituted the earliest utilization of the test stand. The subsequent measurement series was performed 3 weeks later. During these 3 weeks, the test stand had already been used to measure air permeability rates of non-aged material samples through 15 separate measurement series. Figure 12 illustrates results from the test stand leakage evaluation, showing the leakage rate at a 50 Pa pressure difference,
4.2 Air permeability tests
Air permeability evaluation of material samples was performed in accordance with the previously described measurement program, using 12 clamps for sealing the specimens during tests.
4.2.1 Material samples durability
Specimens were tested according to the same procedure before and after artificial ageing to determine the durability of joint permeability. All artificially aged specimens were conditioned in the laboratory at (23 ± 2) °C and 48% RH for more than 48 h prior to performing the tests. Figure 13 shows the results from the durability evaluation expressed as average air permeability at 50 Pa, before and after ageing. The calculated average values do not consider specimens which deviated significantly from the other parallel specimens, including T1-PEF-A, T1-PEF-D and T2-PEF-C. These neglected specimens are nevertheless addressed later, as part of the reproducibility evaluation in Section 4.2.2. All parallel specimens of sample T3-PEF and T3-ROM failed after artificial ageing, as illustrated by the hatched bars in Figure 13. For illustrative purposes, the height of these bars is not representative of the actual permeability of the failed specimens. The dashed line in the chart corresponds to the passive house threshold of 0.048 m³/mh, as described by Van Linden and Van den Bossche (2017).
A horizontal line corresponds to the aforementioned passive house threshold. The height of bars representing failed specimens does not correspond to the actual permeability. Table 5 shows relative changes in air permeability after artificial ageing for four settings of two of the selected to be tested tapes (T1 and T2) in combination with the two different substrates (PEF and ROM).
All the material samples become more air permeable after artificial ageing. However, the increase is more significant among the PEF samples. While the PEF samples are comparatively less permeable before ageing, they eventually surpass the permeability rates of the ROM samples when tested after the ageing process. All material samples are within the passive house threshold prior to ageing, but only T1-ROM and T2-ROM remain airtight enough to stay below this threshold in artificially aged condition. Table 5 shows the relative change in air permeability among the material samples, not including the failed T3-PEF and T3-ROM.
4.2.2 Reproducibility
Figure 14 shows the estimated mean joint permeability
Figure 15 shows the estimated air permeability rates of specimens after 6 weeks of artificial ageing at 50 Pa. T3-PEF and T3-ROM are not included, as they failed during the ageing process. Specimens T1-PEF-D, T2-PEF-C were not exposed to artificial ageing due to time constraints. In the chart, a dashed horizontal line marks the passive house threshold, while a solid line indicates the upper limit for what is considered “good airtightness” at 0.238 m³/m∙h according to Van Linden and Van den Bossche (2017). Apart from T1-PEF-A and the failed T3-PEF and T3-ROM specimens, other specimens retain “good” airtightness after ageing. Like the non-aged measurements, the permeability rates of the PEF samples vary significantly between parallel specimens, while ROM samples provide more consistent results. When comparing individual parallel specimens, those which were permeable initially likewise became increasingly more permeable after ageing. In specimens with air permeability
4.2.3 Repeatability
The repeatability evaluation featured air permeability measurements of three specimens, each tested through three separate measurement series in non-aged condition. Figure 16 shows the estimated mean joint permeability
4.2.4 Visual inspection of specimens
Specimens were visually inspected before and after performing the ageing procedures to observe and map imperfections in specimens which may have impacted air permeability measurement results as shown for the test set up T3-ROM-A in Figure 17. In this case, both specimens of the T3-ROM sample were taken out of the climate simulator after 12 days after a visual inspection. The tape was separated from the substrate in several local points along the joints. The failure appears to have occurred within the adhesive, as the adhesive was still attached partly to the substrate and partly to the backing material. The specimens were tested to determine the leakage rates, but in both cases, an air flow rate of 6 m3/h was not sufficient to elevate the pressure difference ΔP beyond 3 Pa. Because of this, both T3-ROM specimens were deemed as failed tests after artificial ageing.
4.3 Peel resistance measurement
Peel resistance measurements were performed on non-aged specimens, and specimens exposed to artificial ageing for 6 weeks. Results from the tests are expressed as the average peel resistance across five parallel specimens from each material sample, calculated according to NS-EN 12316-2:2013 (Standard Norge, 2013b). Results from the measurements are presented in Figure 18 with error bars representing standard deviations.
Average peel resistance measured among the non-aged specimens ranged from 15 to 41 N/50 mm for the PEF samples, and 14–36 N/50 mm for the ROM samples. On both substrates, T2 displayed a peel resistance approximately two times higher than that of T1 and T3. Following the heat ageing procedures, the PEF samples exhibited a moderate increase in peel resistance, while all ROM samples experienced a decrease in peel resistance after undergoing ageing in the climate simulator, as shown in Table 6.
Table 7 shows the most prevalent failure mode of each material sample. All non-aged specimens failed due to adhesive failure, i.e., mode A. Among the artificially aged specimens, failure mode A was still predominant, although the T2-PEF specimens failed due to delamination of sheet, i.e., mode C.
5 Discussion
In terms of airtightness durability, the tape T3 exhibited the poorest performance among the tapes on both substrates as all its associated specimens failed during the artificial ageing procedure. Since T3 is a tape not developed or certified for permanent application in air or vapor barrier systems, the failure of the T3-PEF and T3-ROM specimens can be regarded as an indication that the method in development is able to detect unsuitable tapes. In contrast, the peel resistance results alone did not provide sufficient grounds to conclude that T3 is unsuitable. As none of the material samples displayed a peel resistance reduction larger than 50% after ageing, all tapes have sufficient adhesion to the substrates to meet the durability requirements outlined in the SINTEF Technical Approval (SINTEF, 2022) guidelines for air and vapor barrier tapes. It is, however, important to acknowledge that the aging procedures employed in this study deviated to some extent from those specified in the SINTEF guidelines. Furthermore, the guidelines require testing of peel resistance to more substrate materials. The method in development can be considered a medium-scale test method as it constitutes a compromise, in terms of complexity, between the standardized peel, shear and tensile tests, and the full-scale methods presented in Section 1: Introduction. The permeability test method is considered less reliable in quantifying properties inherent to various product combinations compared to the peel resistance test, NS-EN 12316-2 (Standard Norge, 2013b), as the permeability estimates appears to depend heavily on the implementation quality of individual specimens. Nevertheless, by measuring air permeability directly, the method in development does not rely on a supposed correlation between airtightness, and mechanical or adhesive properties. As the main purpose of an adhesive tape in this context is to provide airtightness, the concept of measuring air permeability directly is considered a potentially more valid approach to product evaluation.
The method in development can be considered a medium-scale test method as it constitutes a compromise, in terms of specimen size and complexity, between the standardized peel, shear and tensile tests, and the full-scale methods presented in Section 1: Introduction. The permeability test method is considered less reliable in quantifying properties inherent to various product combinations compared to the peel resistance test, NS-EN 12316-2, as the permeability estimates appear to depend heavily on the implementation quality of individual specimens. Nevertheless, by measuring air permeability directly, the method in development does not rely on a supposed correlation between airtightness, and mechanical or adhesive properties. As the main purpose of adhesive tape in this context is to provide airtightness, the concept of measuring air permeability directly is considered a potentially more valid approach to product evaluation.
The proposed method is less complex compared to the full-scale methods utilized by Antonsson (2017) and Ylmén et al. (2012), as it only assesses individual barriers without considering components such as windows, timber framing or pipe penetrations. The reduction of scale and complexity is regarded as beneficial for time and cost efficiency in performing tests, and potentially also regarding reproducibility. Still, this scale reduction and simplification of specimens may cause relevant ageing mechanisms and factors to be disregarded, rendering the test less representative of realistic conditions. The ageing procedure performed on the PEF peel resistance specimens deviates from the SINTEF Technical Approval (SINTEF, 2022) guidelines for vapor barrier tapes, as it did not include exposure to UV radiation for 48 h prior to heat ageing. In addition, the duration of the heat ageing procedure was only half of the 12 weeks used during durability evaluation in Technical Approval. As for the ROM samples, current guidelines for Technical Approval of air barrier tapes demand only 2 weeks in NT BUILD 495 (Nordtest, 2000) as opposed to 6. According to the guidelines, air barrier tapes must undergo additional heat ageing for 24 weeks. The measurement program exclusively involved specimens with joints composed of simple tape joints used to cover cuts in membranes, thus not accounting for overlapping joints. Overlapping joints are believed to potentially exhibit different responses, compared to simple joints, to both climatic strains during artificial ageing and to mechanical strains induced by pressurization during the measurement procedure. Moreover, as specimens were exclusively subjected to positive differential pressure, the impact of negative pressure differences on permeability rates remains unexplored.
6 Limitations
Due to the relatively small number of parallel specimens, the results obtained from the air permeability and durability evaluation of the material samples are considered uncertain.
The accuracy of the permeability measurements is negatively impacted by relatively large and fluctuating system leakage rates which were observed across the various measurement series. In its current form, the test method shows limitations in its ability to provide accurate quantification of air permeability in relatively airtight samples. However, it is still considered suitable for detecting significant increases in air permeability after ageing.
Due to time constraints, the accelerated ageing procedures were not performed for as long as required by SINTEF protocols for Technical Approval. Hence, the results of this study are not directly comparable to SINTEF research. Nevertheless, this time difference is not believed to have affected the general trends observed during the durability evaluation.
The design and dimensions of the test samples differ from in situ conditions, and it must be taken into consideration that the materials may respond differently as a result of this, both during pressurization and ageing. Weighing down the test specimens may have induced mechanical tensions in the materials which differ from what would be observed for instance in a vapor barrier mounted in a wall.
7 Conclusion
Sufficient airtightness in buildings is essential to meet increasingly stringent energy efficiency requirements, and to prevent damages and issues arising from moisture transfer. In order to achieve this, it is crucial to seal joints, connections, and penetrations in the building envelope, using solutions and products with satisfactory performance in long-term. For this purpose, a test method was developed as part of this study, to assess the durability of adhesive tapes based on air permeability.
Basing on results from the measurement program, the test method appears capable of measuring permeability rates with sufficient accuracy to distinguish different material combinations from each other, provided test specimens are prepared in a uniform manner. However, permeability rate estimates depended heavily on the implementation quality of individual specimens, making it difficult to determine what share of the leakages could be attributed to inherent product properties as opposed to the quality of workmanship. This impacted reproducibility negatively, in particular across material samples involving flexible substrates. The degradation of airtightness observed after ageing in the permeability test was not consistent with the durability evaluation based on peel resistance measured according to NS-EN 12311-2 (Standard Norge, 2013a). While all material samples experienced significant increase in air permeability after ageing, the parallel peel resistance measurements provided a significantly more optimistic durability assessment. Nevertheless, the results obtained from the method in development appear to correlate with those obtained from other experimental approaches that assess air permeability. With further improvement, the method presented in this paper is considered applicable as a mean of evaluating the durability of adhesive tapes as part of product development or certification. In the context of separate tape evaluation, the method could potentially constitute a supplementary test to currently established evaluation methods, NS-EN 12311-2 (Standard Norge, 2013a), NS-EN 12316-2 (Standard Norge, 2013b) and NS-EN 12317-2 (Standard Norge, 2010).
The test stand is considered highly configurable, as it allows for the specimen layout to be altered, for instance by utilizing solid boards as substrates and including additional components, such as adhesive pipe collars. This versatility makes it possible to perform permeability tests on the same standard substrates used in Technical Approval of air and vapor barrier tapes. Furthermore, specimens can be inverted, enabling exposure to both positive and negative pressure differences. While the test method in its current form might not be capable of accurately determining the air permeability and durability of joints, it is believed that an improved version can achieve satisfactory precision in determining specimen leakage rates by incorporating improvements aimed at minimizing system leakage rates. The permeability of a specimen as a whole, expressed as leakage per unit area, can then be used for comparison against predefined threshold values. In terms of durability evaluation criteria, it is considered more suitable to establish absolute threshold values for permeability before and after ageing, in contrast to current guidelines for peel and shear resistance evaluation, in which durability is evaluated based on relative change in material properties after artificial ageing.
Despite limitations, the test method is considered a viable approach to durability evaluation of air and vapor barrier tapes in the context of product development and certification. Through further development and improvement, the method in development is considered to have the potential for integration into a wider test program, such as the SINTEF Technical Approval of tape products. Here, the method could potentially be implemented as a supplementary evaluation to already established methods, such as NS-EN 12311-2, NS-EN 12316-2 and NS-EN 12317-2.
8 Future work
Although the method in development displays limitations, a further development is believed to be suitable for potential integration into wider evaluation programs supplementary to existing methods. For further work following aspects to include are proposed:
• Seek confirmation of results by testing more material samples and specimens.
• Perform tests on specimens using both positive and negative differential pressures.
• Look deeper into the relation between artificial and natural ageing.
• Run parallel tests on products in a full-scale.
• Perform tests on tape joints between two different substrate materials.
Data availability statement
The original contributions presented in the study are included in the article/Supplementary Material, further inquiries can be directed to the corresponding author.
Author contributions
TKL: Conceptualization, Data curation, Formal Analysis, Investigation, Methodology, Resources, Validation, Visualization, Writing–original draft. SG: Conceptualization, Data curation, Formal Analysis, Funding acquisition, Methodology, Resources, Supervision, Validation, Visualization, Writing–review and editing. BDH: Conceptualization, Data curation, Formal Analysis, Funding acquisition, Methodology, Project administration, Resources, Supervision, Validation, Visualization, Writing–original draft, Writing–review and editing.
Funding
The author(s) declare that financial support was received for the research, authorship, and/or publication of this article. The Research Council of Norway financially supported this research. Open Access Funding was provided by Norges teknisk-naturvitenskapelige universitet (NTNU).
Acknowledgments
Research results presented in this paper are part of MSc thesis by Tore Kolstad Linløkken, Development of a test method for evaluating durability of adhesive tapes in construction (Linløkken, 2023), completed 2023 at the Department of Civil and Environmental Engineering at Norges teknisk-naturvitenskapelige universitet (NTNU). The authors would like to thank our colleagues from SINTEF, within the research project TightEN (project no. 102020444-2), who provided expertise that assisted the research.
Conflict of interest
The authors declare that the research was conducted in the absence of any commercial or financial relationships that could be construed as a potential conflict of interest.
Publisher’s note
All claims expressed in this article are solely those of the authors and do not necessarily represent those of their affiliated organizations, or those of the publisher, the editors and the reviewers. Any product that may be evaluated in this article, or claim that may be made by its manufacturer, is not guaranteed or endorsed by the publisher.
Supplementary material
The Supplementary Material for this article can be found online at: https://www.frontiersin.org/articles/10.3389/fbuil.2024.1411586/full#supplementary-material
References
Antonsson, U. (2017). Lufttäta klimatskal under verkliga förhållanden. Technical report, RISE, 2017. FULLTEXT01.pdf (diva-portal.org).
Blom, P., and Uvsløkk, S. (2012). Bygg tett! Prosjektrapport 98, technical report, SINTEF Byggforsk. Prosjektrapport98.pdf (unit.no).
Boberach, C. (2022). Development of a test procedure for determining air permeability of adhesive tapes for air barriers in lightweight construction.
Byggforsk (2014). SINTEF, 474.624 Luftlekkasjemåling av bygninger. Hensikt og vurdering. Available at: https://www.byggforsk.no/dokument/4126/luftlekkasjemaaling_av_bygninger_hensikt_og_vurdering (Accessed: January 2024).
DIN 4108-7:2011-01 (2011). Thermal insulation and energy economy in buildings part 7: air tightness of buildings – requirements, recommendations and examples for planning and performance.
Direktoratet for byggkvalitet (2012). Disse kontrollområdene omfattes av obligatorisk uavhengig kontroll. Available at: https://dibk.no/saksbehandling-tilsyn-og-kontroll/Hvilke-kontrollomrader-omfattes-avobligatorisk-uavhengig-kontroll/ (Accessed: January 2024).
Direktoratet for byggkvalitet (2017). Byggteknisk forskrtift TEK17. Byggteknisk forskrift (TEK17) med veiledning - Direktoratet for byggkvalitet (dibk.no).
European Commission (2020). In focus: energy efficiency in buildings. Available at: https://commission.europa.eu/news/focus-energy-efficiency-buildings-2020-02-17_en (Accessed: January 2024).
European Commission (2021). Energy performance of buildings directive. Energy performance of buildings directive (europa.eu) (Accessed: January 2024).
Forskningsradet (2021). Forskningsrådet, Bygger bedre kunnskap for en mer bærekraftig byggebransje. Available at: https://www.forskningsradet.no/sok-om-finansiering/hvem-kan-soke-om-finansiering/naringsliv/prosjekter-naringslivet/bygger-bedre-kunnskap-for-en-mer-barekraftig-byggebransje/ (Accessed: January 2024).
Fufa, S. M., Labonnote, N., Frank, S., Rüther and, P., and &Jelle, B. P. (2017). Durability evaluation of adhesive tapes for building applications, Construction and Building Materials. Durability evaluation of adhesive tapes for building applications - ScienceDirect
Geving, S., Bergheim, E., and Gullbrekken, L. (2020). Bruk av eldre sperresjikt ved etterisolering. Available at: https://sintef.brage.unit.no/sintef-xmlui/bitstream/handle/11250/2647762/Pages%2Bfrom%2BByggeindustrien_03.pdf?sequence=1&isAllowed=y (Accessed: January 2024).
Leprince, V., Moujalled, B., and Litvak, A. (2017). Durability of building airtightness, review, and analysis of existing studies, 38th AIVC Conference. Nottingham UK. Durability of building airtightness, review and analysis of existing studies AIVC.
Linløkken, T. K. (2023). Development of a test method for evaluating durability of adhesive Tapes in construction. NTNU Open.
Møller, E., and Rasmussen, T. (2020). Testing joints of air and vapor barriers, do we use relevant testing methods? Aalborg University's Research Portal aau.dk.
Nordtest (2000). Building materials and components in the vertical position: exposure to accelerated climatic strains. N. T. Build. 495. Available at: http://www.nordtest.info/wp/2000/11/21/building-materials-and-components-in-the-vertical-position-exposure-to-accelerated-climatic-strains-nt-build-495/ (Accessed: January 2024).
SINTEF (2019). Durable adhesive airtight solutions for energy effective building envelopes. Available at: https://www.sintef.no/prosjekter/2019/tighten/ (Accessed: January 2024).
SINTEF (2022). SINTEF technical approval. Available at: https://www.sintefcertification.no/portalpage/index/56 (Accessed: January 2024).
Skogstad, H. B., Kvalvik, M., and Jelle, B. P. (2010). “Bruk tape med varig heft,” in Unngå byggskader – sitter tapen? Bruk tape med varig heft - SINTEF.
Sletnes, M., and Frank, S. (2020). Performance, and durability of adhesive tapes for building applications. From product documentation to scientific knowledge (and back again). XV International Conference on Durability of Building Materials and Components.
Standard Norge (2000). NS-EN 12114, Thermal performance of buildings air permeability of building components and building elements Laboratory test method.
Standard Norge (2010). NS-EN 12317-2, Flexible sheets for waterproofing Determination of shear resistance of joints Part 2: plastic and rubber sheets for roof waterproofing.
Standard Norge (2013a). NS-EN 12311-2, Flexible sheets for waterproofing Determination of tensile properties Part 2: plastic and rubber sheets for roof waterproofing.
Standard Norge (2013b). NS-EN 12316-2, Flexible sheets for waterproofing Determination of peel resistance of joints Part 2: plastic and rubber sheets for roof waterproofing.
Standard Norge, NS 3700 (2013). Criteria for passive houses and low energy buildings – residential buildings.
Standard Norge, NS 3701 (2012). Criteria for passive houses and low energy buildings – non-residential buildings.
Van Linden, S., and Van den Bossche, N. (2017). Airtightness of sealed building joints: comparison of performance before and after artificial ageing, Building and Environment. Airtightness of sealed building joints: Comparison of performance before and after artificial ageing - ScienceDirect.
Keywords: airtightness durability, building envelope, experimental test method, durability of joints, adhesive tapes
Citation: Linløkken TK, Geving S and Hrynyszyn BD (2024) Development of a test method for adhesive tapes certification and application. Front. Built Environ. 10:1411586. doi: 10.3389/fbuil.2024.1411586
Received: 03 April 2024; Accepted: 21 October 2024;
Published: 18 December 2024.
Edited by:
Wenrui Yang, East China University of Technology, ChinaReviewed by:
Dimitrios Kraniotis, Oslo Metropolitan University, NorwayShahryar Habibi, University of Ferrara, Italy
Copyright © 2024 Linløkken, Geving and Hrynyszyn. This is an open-access article distributed under the terms of the Creative Commons Attribution License (CC BY). The use, distribution or reproduction in other forums is permitted, provided the original author(s) and the copyright owner(s) are credited and that the original publication in this journal is cited, in accordance with accepted academic practice. No use, distribution or reproduction is permitted which does not comply with these terms.
*Correspondence: Bozena Dorota Hrynyszyn, Ym96ZW5hLmQuaHJ5bnlzenluQG50bnUubm8=