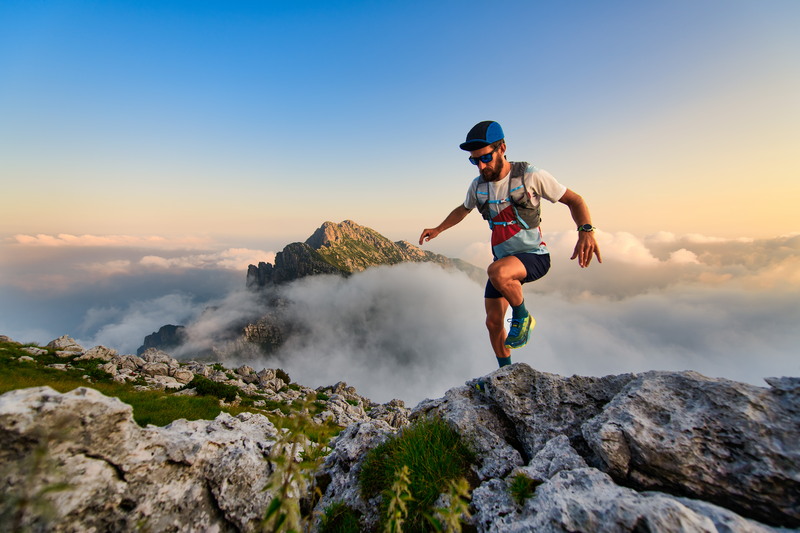
94% of researchers rate our articles as excellent or good
Learn more about the work of our research integrity team to safeguard the quality of each article we publish.
Find out more
ORIGINAL RESEARCH article
Front. Built Environ. , 11 March 2021
Sec. Construction Management
Volume 7 - 2021 | https://doi.org/10.3389/fbuil.2021.520154
This article is part of the Research Topic Systems for Construction Management View all 6 articles
Purpose: The research goal was to investigate the main barriers faced by a large Brazilian construction company in their efforts to thoroughly implement BIM. This study focused on the analysis of understanding the barriers to BIM adoption and the usage of 3/4 dimensions (3D/4D) on the development of an infrastructure project.
Research methodology: The research methodology was exploratory and qualitative, carried out through a single-case study approach made upon bibliographical research, company document analysis, project document analysis, interviews, informal conversations, and observations. The research methodology was developed in six months (from June to December 2019) divided into three main phases: phase 1: definition and design; phase 2: preparation and collection; phase 3: data analysis and conclusion. Data collection was developed using a semistructured research protocol with two different semistructured questionnaires: the first questionnaire aimed at collecting data regarding BIM implementation in the company’s organizational context; the second one focused on the understanding of BIM adoption in the project and on the investigation of the main barriers related to the usage of 3D and 4D modeling in the project studied.
Findings: Regarding BIM implementation in the company, although the company studied is a construction company in the infrastructure sector, BIM was considered more efficient in the design phase and flawed in the construction phase. Findings have shown that BIM has improved the information management of the design itself and its interface with the construction phase. In relation to the usage of BIM in the project, a more collaborative work environment was noticed due to the effectiveness of communication between the design and construction teams on the job site. With respect to the usage of 3D/4D modeling in the project studied, the difficulties in extracting information from the 3D model have disabled the usage of 4D modeling during the construction phase. Therefore, the difficulties reported were identified as an opportunity to map deficiencies in the BIM model in order to define parameters for the new project proposals and to automate the process of receiving the model and checking for inconsistencies or lack of information.
Implications for Research and Practice: The case study is an example that BIM as a technological tool is not able to promote an integrated design and construction interface by itself. It is necessary to integrate BIM as an integrated process with structured management methods and tools. From our perspective, we understand that contracts should change, including construction stakeholders in the very beginning of the design process fostering collaboration across stakeholders such as designers, design and construction managers, suppliers, and subcontractors, thereby achieving a higher level of improvement potentially carried on by the new technologies allied to management practices. With regard to the nature of this article, it is important to make it clear that the results from this study were based on the Brazilian construction industry only.
Limitations: The research is a single-case study; therefore, the findings cannot be generalized. Most of the data were dependent on the interviewees’ self-reported perceptions. We suggest new studies should be conducted with other construction companies in the Brazilian context, comparing companies with different organizational structures and sizes and other types of projects.
BIM (building information modeling) has become a common process and technology used in the management of construction projects (Puolitaival and Forsythe, 2016). Considered not only a technology but also a project management tool and process, BIM consisted of all aspects, disciplines, and systems of a facility within a model, with which all stakeholders (owners, architects, engineers, contractors, subcontractors, and suppliers) can collaborate more accurately and efficiently than traditional processes (Succar, 2009; Azhar et al., 2012; Succar and Kassem, 2015).
Construction companies focused on infrastructure projects have been adopted BIM as a valuable alternative for highly complex projects to minimize problems commonly found in the design and construction phases. Even though BIM has been continually expanding its functionality in the construction industry since its inception in the 1970s, it has not been fully exploited, even in leading contexts.
Mostly, there is a higher level of awareness of BIM in the United Kingdom, Canada, Finland, and New Zealand than that in developing countries (Gu and London, 2010; Ghaffarianhoseini et al., 2017). The United Kingdom Government developed an approach to implementing BIM in the United Kingdom, namely, United Kingdom BIM framework. This framework provides resources in the form of standards, guidance, information protocol, and learning outcomes to support individuals and organizations in the United Kingdom to understand the fundamental principles of information management with BIM (UK BIM Framework, 2020).
A study developed by Cao et al. (2015) has shown an overview of BIM practices in China in the last decade and confirmed that BIM adoption had been clearly extended from the architectural design stage to the construction stage. Despite the fast development of BIM, the effectiveness in practice is constrained by the current contractual arrangements and traditional practices. There is a reluctance to change traditional practices and current procedures by the professionals to adopt BIM. In general, projects are more focused on individual benefits instead of the delivery of integrated project solutions (Migilinskas et al., 2013; Love et al., 2014).
The lack of collaboration among stakeholders and the difficulties in the management and information exchange of the project still constitute a big challenge for the construction industry. As stated by Chen et al. (2020), “as BIM systems have an inherent capability to well connect professionals by collecting and sharing constant accurate data and information among all stakeholders, the adoption is therefore recommended for the project team to effectively tackle the challenge on professional competences.”
BIM is new to many companies, and the adoption is consequently challenging itself. Challenges include unstructured processes that often lead to time and cost overruns (Grytting et al., 2017). Despite the advances in construction management methods and systems over the previous decades, project managers still face a variety of problems related to the management of partial and heterogeneous data and the manipulation of information (Francis, 2013).
In Brazil and other developing countries, there are many initiatives being developed aiming at the adoption of BIM in the construction sector. However, BIM adoption requires a significant change in the way construction businesses operate at almost every level within a building process (Arayici et al., 2011). According to Succar et al. (2013), BIM requires a continuous and long process that needs to be improved step by step encompassing all BIM stages and new strands of expertise for all disciplines compared to more traditional projects.
Therefore, the research goal was to investigate the main barriers faced by a large Brazilian construction company in their efforts to implement BIM thoroughly. This study focused on the analysis of understanding the barriers to BIM adoption and the usage of 3/4 dimensions (3D/4D) on the development of an infrastructure project. Our findings have shown BIM adoption in the company’s projects has matured together with BIM implementation process in the company itself. Although BIM was not fully used in this case, the 3D model has brought constructive advantages by enhancing the visualization of project interferences and parts and optimizing the construction works.
The article is structured as follows: firstly, we introduce the research topic by presenting the main research gaps and the research goal. Secondly, we contextualize the literature review by discussing BIM adoption in the Brazilian context and the benefits of 3D/4D modeling in BIM adoption. Thirdly, we outline the research methodology and data collection process. After, we present a case study by detailing the information regarding the company and the project selected. Then, we show the results of BIM implementation in the company, BIM adoption in the project, and the barriers to BIM adoption and of 3D/4D BIM modeling in the project. Finally, we conclude by presenting research achievements, limitations, and recommendations for future works.
In order to answer the research goal and understand the current research of BIM adoption, we structured the literature review in two main subtopics as follows. In the first subtopic, we present an overview regarding the scenario of BIM adoption in Brazil, and in the second one, we comment on the benefits of 3D/4D modeling in BIM adoption.
In Brazil, construction companies are looking for the best strategies for BIM adoption into their processes. The main obstacles are related to the need of changing the work culture and practices, the scarcity of understanding of the stakeholders’ roles and responsibilities, the lack of knowledge about processes and workflows, and the high investment in training required for learning BIM skills (Hartmann and Fischer, 2007; Singh et al., 2011; Khosrowshahi and Arayici 2012; Mahalingam et al., 2015; Olawumi et al., 2018).
BIM adoption is a long path and depends on many aspects such as adequate methodology, trained personnel, availability of technology, and industry policies (Akintola et al., 2017). According to Abaurre et al. (2011), there are several project and work process issues inherent to the Brazilian civil engineering production chain; therefore, this can impact BIM adoption in this country’s companies.
In 2017, the Brazilian Government created a strategic committee dedicated to BIM adoption, namely, CE-BIM, to diffuse its usage in the construction sector through modernization and digital transformation. Based on a Federal Decree, in 2018, the Brazilian Government has established the BIM BR Strategy as a national plan 2018–2028 of BIM dissemination, systematized by purposes, objectives (indicators and milestones), and actions. Nine main objectives were defined to achieve the expected results (Brasil, 2018):
1. Spread BIM concepts and their benefits
2. Coordinate the structuring of the public sector for BIM adoption
3. Create conditions for public and private investments in BIM
4. Encourage BIM training
5. Propose normative parameters for BIM-based procurement and public bidding
6. Develop technical standards, guides, and specific protocols for BIM adoption
7. Develop a platform and a BIM national library
8. Encourage the development and the usage of new technologies related to BIM
9. Encourage market competition through neutral standards of BIM interoperability.
The CE-BIM has proposed a BIM BR roadmap to be developed in 10 years, from 2018 to 2028 in three main phases. All three phases involve the development of architectural and engineering projects for new constructions, extensions, and retrofits:
• Phase 1 (from January 2021): BIM adoption in the design phase, usage of BIM models for clash detections among disciplines such as structure, electricals, hydraulics, HVAC (heating, ventilation, and air condition); quantitative take-offs; graphic documentation
• Phase 2 (from January 2024): BIM adoption in the design and construction phases, project planning, management, and procurement of the construction phase and the design as-built model
• Phase 3 (from January 2028): BIM adoption in the whole building life cycle phases (design, construction, and operation/maintenance) and also considering the development of BIM models for facility management
In addition to the Brazilian Government initiative, the Brazilian Association of Technical Standards—ABNT—has defined a set of six technical standards related to BIM, including modeling object requirements, guidelines for libraries, system classification, and information management in construction. Furthermore, the Brazilian Chamber of the Construction Industry—CBIC—has elaborated a guide named BIM Implementation Collection for Builders and Developers; the aims of this document are as follows (CBIC—Câmara Brasileira Da Indústria Da Construção, 2016):
• Develop a clear understanding of BIM usage by giving orientations regarding this matter for construction companies and developers
• Clarify, influence, and facilitate a common technological platform between all construction stakeholders
In April 2020, a new Federal Decree nº 10.306 by the Brazilian Government reestablished the sector policy regarding BIM, reinforcing its importance, assuring the relevance to proceed with the usage of BIM and establishing that the public federal administration entities must employ BIM directly or indirectly in civil engineering works and services (Presidência, 2020). Allied to the Brazilian Government, associations and syndicates from the construction sector have been making many efforts toward BIM adoption in the construction sector. Likewise, academia and research labs are developing studies attempting to better incorporate BIM into the Brazilian context.
In the past decade, there have been significant advances in construction-related collaborative technologies. Considered an innovative process and efficient technology, BIM manages project information from design to construction and operation in a collaborative way (Donato et al., 2017). BIM promises the integration of information by combining geometric and nongeometric information in a comprehensive model that accommodates all aspects of the construction (Koutamanis, 2017).
In the article by Chong et al. (2016), BIM can be used to create and manage geospatial information such as site setting and transport network representation, site logistics, equipment and material usage planning, project scheduling, work progress monitoring, construction inspection, and quality assurance. Once the BIM model stores all information regarding construction requirements that can be integrated into the model, it assists cash flow management, safety, and on-site control where simulations can show potential safety hazards.
According to Sacks et al. (2018), the 3D BIM model is a representation of the building through object-based parametric modeling. In other words, the elements are composed of more than just the geometry, but also parameters, requirements, nongeometric information, a set of relations, and rules to control the parameters, which allow practical and automatic changes. The 3D BIM model can improve productivity, stakeholders’ comprehensive understanding of the project, and a collaborative assembly of a federal model.
CBIC—Câmara Brasileira Da Indústria Da Construção (2016) highlighted that not every 3D model is a BIM model because there is some information that must be embedded on the model, other than just the geometry. For instance, there are many types of 2D software that simulate the 3D model, but the objects are not parametric; then, it is not possible to manipulate this model for further purposes such as cost estimating or simulating scenarios.
The development of a 3D model is of the utmost importance to further crucial uses such as model control and planning, which enables collaboration and decreases layout errors and model coordination through clash detection prior to construction. The 4D BIM model is a combination of the 3D model with scheduling to represent the construction timeline to be followed, all the activities and their duration, and the work planning. Therefore, the 4D enables deadline and production monitoring, progress control, and a virtual construction prior to the real work (Suzuki and Santos, 2015; CBIC—Câmara Brasileira Da Indústria Da Construção, 2016).
During the design phase, 3D and 4D modeling techniques can be used to simulate the construction process through the BIM model and detect operation succession errors and space use conflicts (Francis, 2019). As more information becomes available over time and the level of risk decreases, it becomes much easier to make better-informed decisions according to the status of the project or based on the available budget (Francis and Miresco, 2016).
Moreover, the 4D model can also be used during construction to show permanent and temporary facilities, according to the schedule and spaces, enabling site management (BIM Project Execution Planning Guide, 2019). The schedule integration with the 3D BIM model also allows space management and tracking, allocating and managing resources and spaces during and after construction. Current scheduling methods do not account for spatiotemporal constraints, which lead to less than optimal scheduling. This failure causes problems that affect the project’s duration and cost (Francis, Miresco and Le Meur, 2019).
There is still limited bibliography reporting BIM adoption in infrastructure projects. Mainly, the difficulties in BIM adoption stem from the construction industry fragmentation. The necessity of the change of work culture and practices, lack of understanding of the stakeholders’ roles and responsibilities, lack of knowledge about processes, and high investment in training are some of the constraints faced by the construction companies in BIM adoption.
The research methodology was exploratory and qualitative, through a holistic and single-case study (Silva and Menezes, 2005). Based on a literature review, single-case studies aim to understand the experience of a company deeply and holistic case studies investigate an organization or a program through a global approach (Yin, 2015). The case study method was chosen due to the need to understand the research topic through a broad description and a deep analysis (Yin, 2015). The units of analysis were project, company, and people, and the geographical scope of the study was national. The research methodology was developed in three main phases described as follows:
• Phase 1: Definition and design: the research began by defining the research goal, reviewing the literature regarding the research topic, and selecting the company for the study. Then, we concentrated on developing the research protocol and making the first contact with the company selected.
• Phase 2: Preparation and collection: phase 2 started by reviewing the research protocol to prepare for data collection. Additionally, we presented the research goal for the company and defined the project to be studied and the key stakeholders to be interviewed. During the data collection process, we first analyzed information about the company and documents related to the project, such as contract, project scope and schedule, and design deliverables. Second, we interviewed the company’s stakeholders.
• Phase 3: Data analysis and conclusion: phase 3 focused on data analysis obtained during the data collection process and results discussion. In conjunction with the company documents, project analysis, and interviews, we had informal conversations and made observations. Lastly, we concluded the study by presenting achievements and recommendations for the research topic.
Data collection was retrospective and developed from June to December of 2019 and gathered using a semi-structured research protocol. The research protocol contained two different semi-structured questionnaires, as can be seen in the Appendix of the article, which were applied through interviews with key stakeholders according to their position in the company and their participation in the project selected for the study.
The first questionnaire focused on collecting data related to BIM implementation in the company’s organizational context. This questionnaire was applied to the stakeholders who had participated actively in the implementation process. The second questionnaire focused on the understanding of BIM adoption in the project and on the investigation of the main barriers related to the usage of 3D and 4D modeling in the project studied. For these interviews, we spoke to stakeholders who were involved in the design and construction phases of the project but may not have participated in the BIM adoption process in the company. Table 1 shows a brief description of the participating stakeholders of the study.
The study sources of evidence were documents, projects, interviews, informal conversations, and observations. Most of the data were obtained from the interviews. According to Blumberg et al. (2011), interviews provided rich data collection by allowing an expansion and clarification of questions and answers during the interview process.
In this case, the interview process was oriented by the research protocol using the semi-structured questionnaires, with clarifications being made by using complementary questions throughout the interviews when necessary. Annotations were made and the interviews were recorded and transcribed for content data analysis. Interviewees were informed that the responses were completely anonymous and confidential, and each one signed a consent form.
The company selected for this study is a relevant and well-known multinational Brazilian construction company with over 70 years of experience in the infrastructure sector. Since 1948, the company has developed more than 900 projects such as industrial, infrastructure, energy, oil, gas, and urban mobility projects all over Brazil and in more than 40 countries. The company’s technical capacity goes beyond the execution of construction projects, including the design of projects, purchases, manufacturing and assembly, project management, and contracts.
The company’s organizational structure is mainly formed by nine corporative units/departments: finances, planning and risk business, juridical, engineering, management center, supply chain, people management, excellence and innovation, and equipment. With more than 10 thousand employers (office and construction team), the company has five offices located in Brazil and six offices abroad. There are two main headquarters, one placed in the city of Rio de Janeiro and another one in São Paulo, Brazil.
The company holds several national and international awards and certifications, such as ISO 9001, ISO 14001, ISO 19600, OHSAS 18001, AS 8000, SGQ: Sistema de Gestão da Qualidade, SGI: Sistema de Gestão Integrado, and PBQP-H: Programa Brasileiro da Qualidade e Produtividade do Habitat (in Portuguese)1. In 2018, due to market demand and considering the company's previous experience with BIM, the head of the company established BIM adoption as a fundamental part of the company’s strategic planning for the following three years (from 2018 to 2020). Therefore, BIM adoption is an ongoing process in the company. The project selected for this study is a pilot project of an initial BIM adoption detailed as follows.
The project is a Brazilian consortium of an Engineering, Procurement, and Construction (EPC) contract tasked to execute a thermoelectric power plant for liquefied natural gas (LNG) storage. The project is being developed by two main contractors and one engineering subcontractor, a Spanish outsourced engineering company, which is responsible for the design. The company selected for this study is one of the contractors in charge of the management of design and construction teams and the execution of the thermoelectric power plant.
In November 2017, the project contract was signed and the first mobilizations for construction started in March of 2018. The expected deadline for starting to deliver energy is at the beginning of 2021. At the time of data collection, the project stage was at electromechanical assembly and testing the plant’s commissioning. The project’s scope consists of design, procurement, and providing of all equipment, installations, construction, commissioning, and start-up. The development of the thermoelectric power plant involved six main disciplines: civil, metallic, mechanic, pipeline, electric, and instrumentation.
The project is being built in a 15,700 ha area located in the city of São João da Barra, north of Rio de Janeiro state in Brazil. The thermoelectric power plant is a combined cycle gas turbine (CCGT) with 1238 MW net installed capacity and a configuration of 3 × 3 × 1 (3 gas turbines, 3 HRSGs, and 1 steam turbine). The gas turbines will have a single fuel capability with natural gas and the steam exhausting from the steam turbine will be condensed through a seawater cooling tower system. Figures 2,3 illustrate the project chosen for this study.
The research results were collected from different sources during the study and are presented in the following topics. The sources of data collection were the company’s documents, the project studied, interviews, and informal conversations with the company’s stakeholders and observations.
In 2008, the company started the first initiatives using 3D modeling in industrial projects. In 2017, motivated by the need for a more integrated and collaborative process, BIM has become a fundamental part of the company’s strategic planning for the following three years (from 2018 to 2020). Therefore, BIM was incorporated into the company’s strategic plan with the purpose of delivering more value to clients through a digital model and developing a more integrated process able to manage project information and stakeholders in all project phases.
Thus, the company decided to use BIM through Autodesk Revit software. Despite the ownership of the right tools, by that time, they have never learned about BIM, what it represented, what is possible to achieve with its usage, how to implement it correctly, or how to work with the software. Consequently, this first practical attempt without planning did not bring the results that the company + hoping for. On the other hand, it served to represent the magnitude of BIM and the implementation process.
At the beginning of the implementation process, only the engineering department was involved and a team of 8–10 professionals was created to implement BIM. The team was divided into two different BIM approaches. The first one focused on the development of BIM interfaces and the second one on the expansion of BIM adoption subdivided into BIM for proposals and BIM for construction applications.
Since then, many efforts have been made to spread BIM as a work process and culture from the engineering department to other departments of the company. Therefore, the engineering department has been working on the involvement of the strategic, automation, and construction departments together with the head of the company. BIM implementation process was planned to be applied in three main phases:
• Phase 1: Structuring phase (2018): this phase focused on BIM structuring at the organizational level of the company by understanding first how BIM could be integrated into the company workflow learning from BIM practices developed by companies abroad.
• Phase 2: Training phase (2019): this phase concentrated on professional training of some company’s employees along with consulting BIM experts during the implementation process. The company's goal was first to have a couple of professionals with BIM skills who could disseminate the knowledge learned for others.
• Phase 3: Implementing phase (2020): this phase has been dedicated to implementing BIM in pilot projects divided into proposals and construction applications. Since then, six pilot studies of proposal and seven of construction applications have been conducted by the company.
However, the implementation did not follow exactly as planned. The training and structuring phases happened in parallel in 2018 and the first pilot project began in 2019, without the conclusion of phases 1 and 2. The practical usage of BIM was demanded by the company’s president because there was anticipation to see how it works and its results.
The BIM implementation team divided the first year into three different stages: 1) learning and understanding; 2) investigation and diagnostic; 3) roadmap. For the first phase, the primary purpose was to study about BIM since they did not have any knowledge about it at the time. For instance, they gathered information from books, papers, webinars, courses, and benchmarking about BIM.
It was important so they could understand about the BIM process, how to implement it, and the possible benefits and then they would be able to structure an implementation plan for the company. Additionally, some of the team members were volunteers, employees who believe in the BIM benefits and wanted to help the company through this process. Consequently, these volunteers had to divide their times between the daily routine and the implementation project.
Moreover, the company promoted BIM speeches for a year, inviting a BIM specialist to talk about different subjects. The main purpose of this initiative was to empower the employees regarding this matter. Similarly, the team members also started taking BIM courses to learn more and be able to correctly plan the BIM rollout in the company. Another important goal was to overcome the employees’ resistance to change because BIM poses a great challenge to them since it requires a lot of learning, structuring, and practice.
Subsequently, the BIM team decided to investigate what was the company’s structure for collecting and sharing information to see if they could adequate what they already had with the BIM process. At this stage, they also aimed at identifying the best uses of BIM for the company, focusing on their type of construction and their necessity. Therefore, they decided to have conversations with employees from different areas of the company to comprehend how this new process could contribute to their daily routine and improve the quality of their final product. Consequently, they were able to define the strategic uses of BIM, what they needed to develop to achieve the best results with BIM implementation, and also review their processes to improve their methods and workflow.
As they were leading this work front, it was clear that they were not obtaining all the information that they needed to develop the best environment to implement BIM. Thus, added to the fact that the company’s president was expectantly waiting to see the practical usage of BIM and get its benefits, the group decided to begin a few pilot projects.
Throughout the BIM implementation process, interviewees reported the mains difficulties were related to the following:
• BIM concept misunderstanding as methodology and work process
• Lack of trained professionals with BIM skills
• Lack of digital materials and standards in the infrastructure sector
• Work culture resistance in redesigning the workflow and in the adoption of new technologies
• High investment in training and acquisition of hardware and software
However, many changes have been made in the company’s policies and were process-oriented by BIM implementation process, including new standards, guidelines, manuals, and procedures. Along with the process, the company has also understood that BIM demands a change in the very beginning of the process, in the contracting phase of the project. There is a need for change in the way how design has been contracted to be developed in BIM. Results have shown that the new project’s contracts are being detailed according to the level of development (LOD) by discipline, and the usage of BIM is being defined in the project scope conforming to the design typology and complexity.
During the interviews, two stakeholders were asked to rank the most impact category (process, people, and technology) by BIM. The first stakeholder categorized process as the first most impacted category, people as the second, and technology as the last one. The second stakeholder ranked first people, second process, and third technology as the category most impacted by BIM implementation in the company. These results suggest the importance of developing a more structured process and trained professionals able to adapt to new technologies such as BIM. As stated by Grytting et al. (2017), BIM challenges include unstructured processes that often lead to time and cost overruns.
Lastly, although the company studied is a construction company in the infrastructure sector, BIM was considered more efficient in the design phase and flawed in the construction phase. According to the interviewees, BIM has improved the information management of the design itself and its interface with the construction phase. The operation phase was not considered once the company does not work with facility management contracts. Finally, interviewees were interrogated to classify on a scale from one to five BIM implementation status in the company. Considering that one is initial and five is optimized, they classified the BIM level of maturity between levels 2 and 3, justifying that BIM is an ongoing implementation process in the company.
The case study is an example of a pilot project using BIM during its implementation process in the company. In this case, BIM was not fully used as an integrated process; however, the 3D model was developed through a PDMS (Plant Design Management System) software. Due to the high complexity of industrial projects, the development of 3D models is a common procedure practiced by the design offices in the market in this kind of project typology. In the project studied, the 3D model was subcontracted to be developed since the beginning of the design phase (conception stage). Therefore, according to the interviewed professionals, this was the main reason for the company to choose this project; otherwise, if they had received it in 2D, they would have to spend a lot of time modeling it.
Even though the company chose this pilot project specifically because they had already received the 3D model, they realized that it was not enough. The model was not prepared for the 4D aimed by the construction company since the information added to it was not enough. Consequently, the company’s engineers spent a lot of time and effort to refine the 3D model for the use they needed.
As cited before, the project is an EPC contract between two main contractors and one subcontractor, and the company studied was responsible for the design management, the procurement, the providing of equipment, installations, construction, commissioning, and the project start-up. Because of intellectual property information from the other contractor, the project did not have a common database with shared information. Thus, each company developed its own database, and the model management and integration were done by the company studied through Navisworks software, a 3D model review software for architecture, engineering, and construction.
For every project stage, from the design to the construction phase, a team of professionals has been working on the information management of the design in consonance with the construction needs. Since the preconstruction phase, a dedicated team was mobilized to the construction site to deal with problems during construction, floating from 15 to 25 professionals according to the construction stage. The professionals were allocated by design discipline and guided by a “Job Leader” in order to bring better solutions toward design constructability allied to construction planning and schedule.
In relation to the usage of BIM in the project, interviewees said that they experienced a more collaborative work environment due to the effectiveness of communication between the design and construction teams on the job site. Additionally, it was noticed that the design team has been able to deliver all the drawings allied to the construction demands diminishing the lack of integration between the design and construction phases. Yet, according to the project engineering manager (participant 4), BIM as a technological tool was not able to promote an integrated design and construction interface by itself. It is necessary to integrate BIM as an integrated process with structured management methods and tools.
During the construction phase, it was noticed that BIM had brought an improvement in the design quality and project constructability. According to the interviewee’s answers, a more significant participation of the designers was observed in the job site developing design solutions on time with the construction planning. As a result, interviewees responded that they have been receiving positive feedback from the clients concerning design quality through a better project visualization provided by the usage of BIM. Lastly, BIM was not used to develop the project of site layout and safety. To conclude, during the interview, interviewees three and four were asked to classify the BIM level of maturity in the project studied. On a scale from 1 (initial) to 5 (optimized), both of them classified the project between levels 2 and 3.
The usage of BIM in the project was limited to the 3D model and punctual initiative of a 4D modeling in the cooling tower’s thermoelectric plant. Results have shown the 4D model promoted more integration between the planning and construction teams if compared with the engineering team. During the pilot study, the main barriers to BIM adoption and 3D/4D modeling in the project studied were as follows:
• Lack of knowledge and skills from the subcontractor company responsible for the design concerning the constructability
• Lack of information in the 3D model disabling the development of the other dimensions such as 4D or 5D
• Lack of definition concerning the usage of BIM in the design process and its relationship with construction
• Short time for design development, verification, detailing, and refinement due to the contract type for EPC
• Lack of interest from the client to contract the project developed in BIM due to time and cost increasing
• Difficulties in developing the project with contractors located in different countries
• Difficulties in having a shared model with a common database because of intellectual properties reasons
With respect to the usage of 3D/4D modeling in the project studied, the difficulties in extracting information from the 3D model have disabled the usage of 4D modeling during the construction phase. Many adjustments were made in the 3D model to run the pilot study of 4D modeling in the cooling tower’s thermoelectric plant. Therefore, the difficulties reported during the pilot study were identified as an opportunity to map deficiencies in the BIM model in order to define parameters for the new project proposals and to automate the process of receiving the model and checking for inconsistencies or lack of information.
Although BIM was not fully used in this case, the 3D model has brought constructive advantages, enhancing the visualization of project interferences and parts and optimizing the construction works. Finally, the usage of BIM in the company’s projects is maturing together with BIM implementation process in the company itself. Thus, many other pilot studies have been developed to build common knowledge about BIM in the company by trial and error. In this process, proposal requirements were adjusted, and the BIM execution plan (BEP) is being developed for the new company’s projects. As said by Turk (2016), the usage of BIM in the construction industry is growing as the technology matures.
To ensure that fundamental matters are taken into consideration during BIM adoption and to avoid barriers during this process, the Pennsylvania State University established an extensive planning detailed design regarding the project execution with BIM, defining BIM uses for the company and its projects according to the company’s strategy. Also, the guide orients BIM implementation process mapping and progress monitoring and developing infrastructure to support the whole process, such as communication procedures, technology development, and the form of the contracts (BIM Project Execution Planning Guide, 2019).
The research has achieved the goal of investigating a case of BIM implementation in a large construction company in Brazil and also analyzing the experience concerning the usage of 3D and 4D modeling by reporting the barriers they faced and how they overcame the situation. BIM is new to many companies, and the implementation is consequently challenging itself. In Brazil, the reality is not different, and the usage of BIM still being premature especially in the infrastructure sector. There is a lack of policies, standards, and guides, which should be developed from the government sphere in order to bring more quality to the construction industry due to the relevance of this sector for the economic development in the country.
The construction industry is a complex and fragmented environment and construction companies still face problems related to the management data and information. The barriers related to BIM are not the only constraints faced by the construction industry in the Brazilian context. The lack of knowledge concerning project and process management is also a reality experimented by the construction environment. In the case studied, many decisions that could be solved during the design phase were postponed to the construction phase due to the parallelism of design and construction activities faced by highly complex projects such as infrastructure and industrial projects in EPC contracts.
Based on that, we observed the importance of promoting a collaborative and integrated work environment with an effective interaction between stakeholders. Therefore, we suggest design players work together with the construction team in order to mitigate problems related to project fragmentation and to improve project’s constructability, performance, and quality. We also recognized the necessity of the construction players who started to work with the design team at the very beginning of the design phase, bringing their experience and knowledge about constructability and inputting information in the BIM model during the design and planning phase allied to the construction needs.
By acknowledging that BIM implementation is a continuous and long process, we did not expect a different result due to the short period of time of BIM implementation in the company. We also recognize the efforts through a very well-structured plan that the company has been applying toward BIM implementation by spreading the BIM concept as a work culture of a holistic process and not only as an isolated technological tool.
Moreover, the 3D model development must consider all fundamental information for further uses, such as scheduling and cost estimating. The civil engineering environment is fragmented, and construction companies act differently based on their needs on the project and construction. Thus, the efficiency of BIM depends not only on the BIM itself but also on the management of the design and construction interface by promoting a more collaborative work environment among stakeholders.
With respect to BIM adoption and 3D/4D modeling, we realize that BIM itself is not able to bring improvements to the project construction. There is a necessity to advance the development of construction management methods, which can be able to diminish the lack of integration between design and construction phases and provide a collaborative project environment among design and construction players working together at the “same page”. From the interviewees' viewpoint, there is a misunderstanding concerning the BIM concept among professionals in the construction sector. Some of them interpret BIM as a 3D model for data visualization and project interferences and not a methodology or process to be used through all project life cycle phases.
Lastly, besides the complexity of the project studied and the company’s relevance in the construction industry in Brazil, this research has some limitations of the methodological approach. First, as a single-case study, the findings cannot be generalized. Second, this study was dependent on the interviewees’ self-reported perceptions. Third, new studies should be conducted with others construction companies, comparing them from the perspective of another project and a different company’s organizational structure. An interesting area for future research could be an investigation of BIM usage in other project typologies or BIM implementation in the public sector.
The datasets generated for this study are available on request to the corresponding author.
Ethical review and approval was not required for the study on human participants in accordance with the local legislation and institutional requirements. Written informed consent from the participants was not required to participate in this study in accordance with the national legislation and the institutional requirements.
All authors have contributed to the development of this research. AA: Structured and developed the whole article. Firstly, reviewed the literature, designed the methodology and collected the data. Secondly, analyzed the data and discussed the findings. Thirdly, conclude the article presenting achievements, limitations and future works. RF: Collected part of the data and wrote the article together with AA. SM: Made contact with the company, revised the article, and wrote part of the conclusions.
This study was financed in part by the Coordenação de Aperfeiçoamento de Pessoal de Nível Superior—Brasil (CAPES)—Finance Code 001.
The authors declare that the research was conducted in the absence of any commercial or financial relationships that could be construed as a potential conflict of interest.
We would like to thank the company selected for giving all the necessary support and data for the development of this research. Even more, we thank all the interviewees, without whom this study would not have been possible.
1. When did the company become interested in BIM?
2. What were the motivations that led the company to implement BIM?
3. What were the main barriers and difficulties during the implementation process?
4. Who led the implementation? What were the main stakeholders involved?
5. What were the changes made in the company policy and processes with BIM implementation?
6. Has the design management process changed with the implementation of BIM?
7. Does the company use any kind of method or tool for preconstruction phase that promotes a better integration between design and construction phases?
8. Has the project documentation and bid preparation (contracting procedure) changed with BIM?
9. Among the categories (1) technology, (2) processes and (3) people, which one do you consider that the company has been the most impacted by BIM? Tell me about.
10. What were the changes in technology (software and hardware) with the BIM implementation?
11. Which phase (design, construction, and operation) do you consider that BIM is more effective for the company? Could you specify a subphase?
12. And in the opposite way, which phase (design, construction, and operation) do you consider that BIM is less effective in the company? Could you specify a subphase?
13. The usage of BIM can be changed according to the project typology / category?
14. What is the client`s feedback regarding the usage of BIM in the company`s projects?
15. On a scale of 1 to 5, how do you classify the company's BIM maturity level?
1. Did BIM change the project`s scope?
2. Has BIM positively or negatively interfered in the project cost and duration?
3. Did BIM improve project quality and performance? If so, could you give some examples?
4. At which project`s phase BIM has been implemented in the project life cycle?
5. Do you believe that BIM was integrated into the process in a holistic or in an isolated way?
6. Do you believe that BIM allowed the designer to “get closer” to the construction site?
7. Do you believe that BIM enhanced the project’s constructability?
8. Do you believe that BIM has improved communication between the design and construction team?
9. In your opinion, what are the main gaps related to BIM at the design phase?
10. In your opinion, what are the main gaps related to BIM in the construction phase?
11. In your opinion, how could BIM improve the integration between design and construction phases?
12. What were the main difficulties during the development of the BIM model at the design phase?
13. How did the clash detection (BIM) model verification process occur to validate information consistency across project disciplines?
14. What were the main challenges to the management of information flow during construction?
15. Does the company has continuously updated the BIM model as changes happened during construction? so, could you tell more about the steps in this process?
16. If so, the BIM model was updated by a specific stakeholder or team?
17. What were the BIM dimensions developed in the model?
18. On a scale of 1 to 5, how do you classify the BIM level of maturity (detailing) of the model?
19. Using the BIM model, it was possible to:
Note: If affirmative, please cite examples:
19.1 Increase the accuracy and reliability of design data
19.2 Collaboration in design, construction, engineering, and facility management stakeholders
19.3 Ensuring effective communication among project participants
19.4 Enhancing exchange of information and knowledge management
19.5 Reduced claims or litigation (risks)
19.6 Improve site layout, planning and site safety
19.7 Improve coordination and planning of construction works
19.8 Integrating project documentation/bid preparation?
19.9 Synchronization of procurement with design and construction
19.10 Providing BIM models for offsite prefabrication
19.11 Providing better implementation of lean construction, green sustainability and IPD
1Quality management system; SGI: Integrated Management System, and PBQP-H: Brazilian Habitat Quality and Productivity Program.
Abaurre, M. W., Manzione, L., and Melhado, S. B. (2011). Desafios para a implementação do processo de projeto colaborativo: análise do fator humano. V Encontro Brasileiro de Tecnologia de Informação e Comunicação na Construção: BIM – modelando a construção do futuro—TIC 2011: proceedings of the TIC 2011. Ago 4-5. Brazil: Salvador, 1–12.
Akintola, A., Venkatachalam, S., and Root, D. (2017). New BIM roles’ legitimacy and changing power dynamics on BIM-enabled projects. J. Construct. Eng. Manag. 143, 9. doi:10.1061/(ASCE)CO.1943-7862.0001366
Arayici, Y., Coates, P., Koskela, L., Kagioglou, M., Usher, C., and O’Reily, K. (2011). Technology adoption in BIM implementation for lean architectural practice. Autom. ConStruct. 20, 189–195. doi:10.1016/j.autcon.2010.09.016
Azhar, S., Khalfan, M., and Maqsood, T. (2012). Building information modeling (BIM): now and beyond. Constr. Econ. Build. 12, 15–28. doi:10.5130/ajceb.v12i4.3032
BIM Project Execution Planning Guide (2019). BIM project execution planning GuideVersion 2.2. 2019. Pennsylvania, PA: Pennsylvania State University Available at: https://www.bim.psu.edu/bim_pep_guide/ (Accessed November 08, 2020).
Blumberg, B., Cooper, D. R., and Schindler, P. S. (2011). Business research methods. Berkshire. 3rd Edn. Pennsylvania, NY: McGraw-Hill Higher Education, 656.
Cao, D., Wang, G., Li, H., Skitmore, M., and HuangT Zhang, W. (2015). Practices and effectiveness of building information modeling in construction projects in China. Autom. Constr. 49, 13–122. doi:10.1016/j.autcon.2014.10.014
CBIC—Câmara Brasileira Da Indústria Da Construção (2016). Fundamentos BIM—parte 1: implantação do BIM para construtoras e incorporadoras. Brazil. https://cbic.org.br/faca-o-download-da-coletanea-bim-no-site-da-cbic/ (Accessed November 08, 2020).
Chen, Z., Agapiou, A., and Li, H. (2020). A benefits prioritization analysis on adopting BIM systems against major challenges in megaproject delivery. Front. Built Environ. 6, 26. doi:10.3389/fbuil.2020.00026
Chong, H. Y., Lopez, R., Wang, J., Wang, X., and Zhao, Z. (2016). Comparative analysis on the adoption and use of BIM in Road infrastructure projects. J. Manag. Eng. 32, 6. doi:10.1061/(ASCE)ME.1943-5479.0000460
Donato, V., Lo Turco, M., and Bocconcino, M. M. (2017). BIM-QA/QC in the architectural design process. Architect. Eng. Des. Manag. 14, 1–16. doi:10.1080/17452007.2017.1370995
Francis, A., Miresco, E., and Le Meur, E. (2019). Spatiotemporal chronographical modeling of procurement and material flow for building projects. Adv. Comput. Des. 4, 2. doi:10.12989/acd.2019.4.2.119
Francis, A., and Miresco, E. (2016). Simulation of execution alternatives using chronographic scheduling logic. J. Civ. Eng. 5, 1–8. doi:10.5963/JCES0501001
Francis, A. (2019). Chronographical spatiotemporal scheduling optimization for building projects. Frontiers in Built Environment 5, 1–14. doi:10.3389/fbuil.2019.00036
Francis, A. (2013). The Chronographical approach for construction project modeling. MPAL. 166, 188–204. doi:10.1680/mpal.12.00009
Ghaffarianhoseini, A., Tookey, J., Ghaffarianhoseini, A., Naismith, N., Azhar, S., Efimova, O., et al. (2017). Building Information Modeling (BIM) uptake: clear benefits, understanding its implementation, risks, and challenges. Renew. Sustain. Energy Rev. 75, 46–1053. doi:10.1016/j.rser.2016.11.083
Grytting, I., Svalestuen, F., Lohne, J., Sommerseth, H., Augdal, S., and Lædre, O. (2017). Use of LoD decision plan in BIM-projects. I creative construction conference 2017: proceedings of the I creative construction conference. Primosten, Croatia: Elsevier, 407–414.
Gu, N., and London, K. (2010). Understanding and facilitating BIM adoption in the AEC industry. Autom. Constr. 19, 988–999. doi:10.1016/j.autcon.2010.09.002
Hartmann, T., and Fischer, M. (2007). Applications of BIM and hurdles for widespread adoption of BIM2007AISC-ACCL eConstruction Roundtable Event Report, Stanford, CA: CIFE.
Khosrowshahi, F., and Arayici, Y. (2012). Roadmap for implementation of BIM in the United Kingdom construction industry. J. Eng. Constr. Archit. Manag. 19, 610–635. doi:10.1108/09699981211277531
Koutamanis, A. (2017). Briefing and building information modeling: potential for integration. Int. J. Architect. Comput. 15, 119–133. doi:10.1177/1478077117714914
Love, P. E. D., Matthews, J., Simpson, I. S., Hill, A., and Olatunji, O. A. (2014). A benefits realization management building information modeling framework for asset owners. Autom. Constr. 37, 1–10. doi:10.1016/j.autcon.2013.09.007
Mahalingam, A., Yadav, A. K., and Varaprasad, J. (2015). Investigating the role of lean practices in enabling BIM adoption: evidence from two Indian cases. J. Const. Eng. Manag. 141 (7), 05015006. doi:10.1061/(ASCE)CO.1943-7862.0000982
Migilinskas, D., Popov, V., Juocevicius, V., and Ustinovichius, L. (2013). “The benefits, obstacles and problems of practical BIM implementation,” in 11th international conference on modern building materials, structures and TechniquesProceedings of the MBMST 2013. May 16-17 (Vilnius, Lithuania: MBMSTProcedia Engineering), 767–774.
Olawumi, T. O., Chan, D. W. M., Wong, J. K. W., and Chan, A. P. C. (2018). Barriers to the integration of BIM and sustainability practices in construction projects: a Delphi survey of international experts. J. Build. Eng. 20, 11. doi:10.1016/j.jobe.2018.06.017
Presidência, da. República. (2020). Decreto Nº 10.306, de 2 de Abril de 2020. http://www.planalto.gov.br/ccivil_03/_ato2019-2022/2020/decreto/D10306.htm (Accessed November 8, 2020).
Puolitaival, T., and Forsythe, P. (2016). Practical challenges of BIM education. Struct. Surv. 34, 15. doi:10.1108/SS-12-2015-0053
Sacks, R., Eastman, C., Lee, G., and Teicholz, P. (2018). BIM handbook: a guide to building information modeling for owners, designers, engineers, contractors and facility managers. 3rd Edn. New Jersey: John Wiley & Sons, 682.
Silva, E. L., and Menezes, E. M. (2005). Metodologia da Pesquisa e Elaboração de Dissertação. 4th Edn. Florianópolis: UFSC, 2005, 138.
Singh, V., Gu, N., and Wang, X. (2011). A theoretical framework of a BIM-based multi-disciplinary collaboration platform. Autom. Constr. 20, 134–144. doi:10.1016/j.autcon.2010.09.011
Succar, B., and Kassem, M. (2015). Macro-BIM adoption: conceptual structures. Autom. Constr. 57, 64–79. doi:10.1016/j.autcon.2015.04.018
Succar, B., Sher, W., and Williams, A. (2013). An integrated approach to BIM competency assessment, acquisition, and application. Autom. Constr. 35, 174–189. doi:10.1016/j.autcon.2013.05.016
Succar, B. (2009). Building information modeling framework: a research and delivery foundation for industry stakeholders. Autom. Constr. 18, 357–375. doi:10.1016/j.autcon.2008.10.003
Suzuki, R. T., and Santos, E. T. (2015). Planejamento 4D no Brasil: levantamento orientado à percepção de resultados pelos diversos “stakeholders” da construção. VII Encontro Brasileiro de Tecnologia de Informação e Comunicação na Construção—edificações, Infraestrutura e Cidade: do BIM ao CIM. TIC 2015: proceedings of the TIC 2015. Recife, Brazil: Blucher Engineering Proceedings, 168–178.
Turk, Z. (2016). Ten questions concerning building information modeling. Build. Environ. 107, 274–284. doi:10.1016/j.buildenv.2016.08.001
UK BIM Framework (2020). UK BIM framework Available at: https://ukbimframework.org/standards-guidance/ (Accessed November 11, 2020).
Keywords: BIM-building information modeling, BIM adoption, construction management, construction company, infrastructure project
Citation: Arrotéia AV, Freitas RC and Melhado SB (2021) Barriers to BIM Adoption in Brazil. Front. Built Environ. 7:520154. doi: 10.3389/fbuil.2021.520154
Received: 14 December 2019; Accepted: 25 January 2021;
Published: 11 March 2021.
Edited by:
Zhen Chen, University of Strathclyde, United KingdomReviewed by:
Heap Yih Chong, Curtin University, AustraliaCopyright © 2021 Arrotéia, Freitas and Melhado. This is an open-access article distributed under the terms of the Creative Commons Attribution License (CC BY). The use, distribution or reproduction in other forums is permitted, provided the original author(s) and the copyright owner(s) are credited and that the original publication in this journal is cited, in accordance with accepted academic practice. No use, distribution or reproduction is permitted which does not comply with these terms.
*Correspondence: Aline V. Arrotéia, aline.arroteia@usp.br
Disclaimer: All claims expressed in this article are solely those of the authors and do not necessarily represent those of their affiliated organizations, or those of the publisher, the editors and the reviewers. Any product that may be evaluated in this article or claim that may be made by its manufacturer is not guaranteed or endorsed by the publisher.
Research integrity at Frontiers
Learn more about the work of our research integrity team to safeguard the quality of each article we publish.